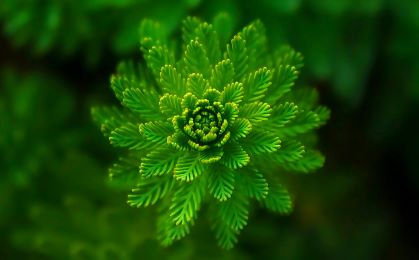
Contact Changfu Chemical Now!
+86 27 8439 6550 | +86 181 6277 0058
The Power of Silicone Rubber Coating: Benefits and Applications for Modern Industries
Introduction
In today’s world, materials used in industrial applications must meet the rigorous demands of durability, resistance, and adaptability. Among the many specialized coatings available, silicone rubber coating has emerged as a versatile solution across various sectors. Known for its exceptional properties, silicone rubbers offer unparalleled performance, whether for high-temperature applications, moisture resistance, or flexibility. This blog will delve into the benefits of silicone rubber coating and explore its diverse applications across modern industries, from electronics to aerospace.
What is Silicone Rubber Coating?
Silicone rubber coating is a protective layer made from silicone rubbers, a group of synthetic elastomers widely recognized for their outstanding thermal stability, flexibility, and electrical insulating properties. Silicone rubbers are typically composed of silicon, oxygen, carbon, and hydrogen atoms, and their molecular structure allows them to withstand extreme environmental conditions, including high heat, cold, moisture, and chemical exposure.
The primary advantage of silicone rubber coating is its ability to form a smooth, durable, and resilient protective layer on various surfaces. Unlike traditional coatings, silicone rubbers offer long-lasting performance in demanding environments, making them ideal for use in industrial and commercial applications. Silicone rubber coating differs from other coatings, such as epoxy or polyurethane, due to its superior flexibility, weather resistance, and non-reactive nature.
Key Benefits of Silicone Rubber Coating
1.Durability and Longevity
One of the most significant advantages of silicone rubber coating is its durability. Silicone rubbers are highly resistant to wear, tear, and environmental degradation, making them perfect for both outdoor and indoor applications. Whether used in automotive, aerospace, or electronics, silicone rubber coatings protect vital components from physical damage, scratches, and exposure to harsh chemicals or UV rays.
2.High Temperature Resistance
Silicone rubbers excel in extreme temperature environments. Unlike many other materials, silicone rubber coating can withstand both very high and low temperatures, typically ranging from -60°C to 230°C, depending on the specific formulation. This high temperature resistance makes silicone rubber coatings invaluable in industries such as automotive and aerospace, where parts must operate efficiently in hot, corrosive environments.
3.Waterproofing and Insulation
Silicone rubber coatings are highly effective at waterproofing surfaces, protecting sensitive electronic components, cables, and insulation from moisture damage. Whether used in marine applications, electronics, or construction, silicone rubber’s inherent waterproofing capabilities make it an essential material for any application where water exposure is a concern.
4.Chemical Resistance
Silicone rubbers are resistant to many chemicals, oils, solvents, and fuels. This property makes silicone rubber coating ideal for use in industries where chemical exposure is frequent, such as automotive, chemical processing, and manufacturing. The ability to resist degradation from aggressive substances significantly extends the life of coated parts and reduces maintenance costs.
5.Non-toxic and Food-Safe Properties
Another significant benefit of silicone rubber is its non-toxic nature, making it safe for applications in the medical and food industries. Silicone rubber coating is commonly used in medical devices, baby products, and food-related items, ensuring that products are both safe and effective. Silicone’s FDA approval for food contact makes it a popular choice for cookware, baking tools, and infant care products.
6.Flexibility and Conformability
The inherent flexibility of silicone rubbers enables the coating to conform to irregular shapes and surfaces. This adaptability makes silicone rubber coating ideal for coating components with intricate geometries or uneven surfaces, ensuring complete coverage and protection. The flexibility of the material also helps absorb impacts and reduce the risk of cracks or chips in the protective layer.
Applications of Silicone Rubber Coating in Modern Industries
1.Electronics and Electrical Systems
One of the most common uses of silicone rubber coating is in electronics and electrical systems. Silicone rubbers provide excellent insulation, protecting electrical components from moisture, dust, and heat. They are often used in printed circuit boards (PCBs), electrical wires, and connectors, offering both electrical insulation and environmental protection. In addition, silicone rubbers are used for heat dissipation in high-performance electronic devices, ensuring longevity and stability.
2.Automotive Industry
The use of silicone rubber in the automotive industry has revolutionized the manufacturing of seals, gaskets, and hoses, providing enhanced durability and resistance to extreme temperatures. In the automotive industry, silicone rubber coating plays a crucial role in sealing, insulation, and protection. Silicone rubbers are used in gaskets, seals, hoses, and engine components to prevent the ingress of dust, dirt, and liquids, ensuring that the vehicle operates smoothly. Additionally, silicone rubber coatings help with temperature regulation, preventing overheating of critical parts under the hood.
3.Medical Industry
The medical field relies heavily on the properties of silicone rubber coatings for the manufacture of medical devices, implants, and prosthetics. Silicone rubbers are biocompatible, flexible, and easy to sterilize, making them perfect for devices that come into contact with the human body. From catheters to surgical instruments, silicone rubbers are integral to ensuring safety, hygiene, and longevity in medical applications.
4.Aerospace
The aerospace industry demands materials that can withstand extreme conditions, and silicone rubber coatings meet these requirements. Silicone rubbers provide superior resistance to high temperatures, pressure, and radiation, making them ideal for use in aircraft and spacecraft components. Silicone rubber coatings are used for sealing, insulation, and protecting sensitive instruments in these high-stakes environments.
5.Consumer Goods
In consumer products, silicone rubber coating is used to create durable and safe coatings for everyday items such as cookware, baby products, and personal care items. Silicone rubber coatings are non-toxic, flexible, and resistant to staining and odors, making them ideal for items that require frequent cleaning and prolonged use.
6.Construction and Home Appliances
Silicone rubbers are widely used for weatherproofing applications, such as sealing windows, doors, and roofing materials. Silicone rubber coatings provide excellent insulation, reducing energy costs and enhancing the comfort of indoor environments. Additionally, silicone rubbers are used in home appliances like washing machines, refrigerators, and ovens to ensure long-lasting performance.
Silicone Rubber Coating in the Manufacturing Process
The application of silicone rubber coating in manufacturing is a critical process that requires precision and care to ensure optimal results. Several techniques are commonly used for applying silicone rubber coatings, including spraying, dipping, and brushing, each offering distinct advantages depending on the specific product and its requirements.
- Spraying is often used for large-scale production and complex parts, where the coating needs to cover irregular surfaces or intricate geometries. It allows for a smooth, even application, though it requires careful control to avoid over-spraying or waste.
- Dipping involves immersing the product into a bath of liquid silicone rubber, ensuring complete coverage, particularly for parts with consistent shapes or smaller, simpler designs. This method is ideal for items like seals, gaskets, and electrical components.
- Brushing is used for smaller quantities or when a more controlled application is required. It allows for the application of thicker layers where additional build-up is needed for enhanced protection.
Once the silicone rubber is applied, it is cured, typically using heat or ultraviolet (UV) light, which transforms the liquid into a solid, durable coating. During curing, manufacturers must carefully control temperature and timing to avoid inconsistencies in the final product.
Despite its many advantages, applying silicone rubber coatings does present challenges. Ensuring uniform coverage, managing curing times, and optimizing adhesion to various substrates are key factors that require attention. Advances in silicone formulations, along with more refined application techniques, have made the process more efficient and reliable, improving both productivity and product performance. Furthermore, innovations in materials and curing methods continue to reduce production times and costs while increasing the overall quality and longevity of silicone-coated products.
Innovative Developments and Future Trends
The silicone rubber coating industry is constantly evolving to meet the changing needs of modern manufacturing and technology. One of the most exciting innovations is the development of self-healing coatings, which have the ability to repair minor scratches or damage to the surface over time. This feature significantly extends the lifespan of coated products, reducing maintenance costs and enhancing durability.
Another growing trend is the rise of eco-friendly silicone rubbers, which are formulated to minimize their environmental impact without compromising performance. These formulations use sustainable raw materials and eco-conscious production processes, making them more attractive for industries aiming to reduce their carbon footprint.
Furthermore, silicone rubbers are being increasingly utilized in cutting-edge applications such as renewable energy technologies, including solar panels and wind turbines, where their heat resistance and flexibility play a crucial role. In the realm of 3D printing, silicone rubbers are being used to create highly durable, flexible prototypes and functional parts, opening up new possibilities for product development and design. As these innovations continue to emerge, silicone rubber coatings are poised to drive advancements in a wide range of industries.
Conclusion
Silicone rubber coating is a powerful, versatile solution that has revolutionized industries worldwide. Its durability, resistance to heat and chemicals, waterproofing capabilities, and flexibility make it an essential material for a wide range of applications. As industries continue to demand more efficient and reliable materials, silicone rubbers will undoubtedly remain at the forefront of innovation. Whether in electronics, automotive, medical devices, or aerospace, silicone rubber coating continues to enhance the safety, performance, and longevity of critical components and products.
Popular Silicon Compounds
Popular Silicon Compounds
Related News & Blog
Related News & Blog
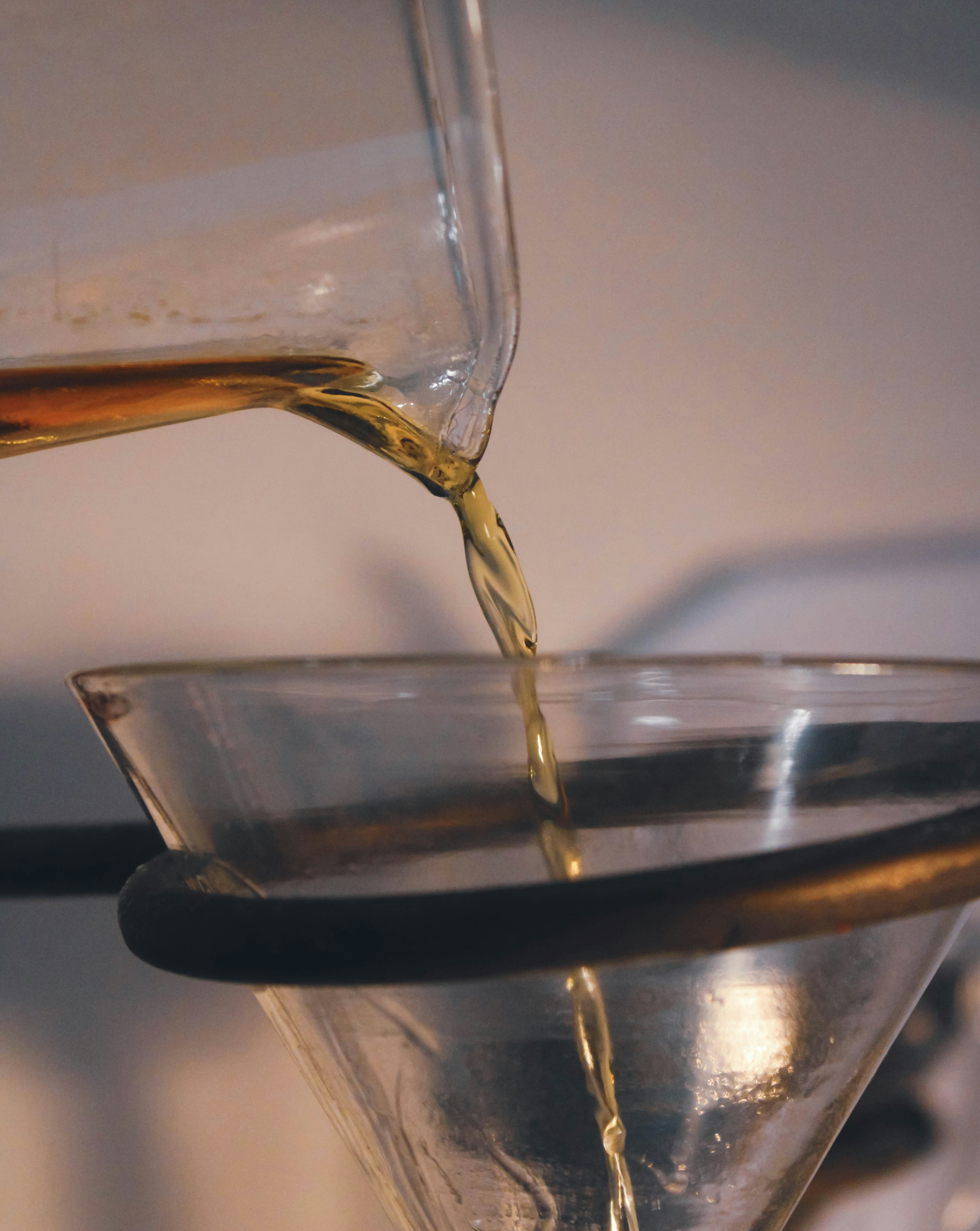
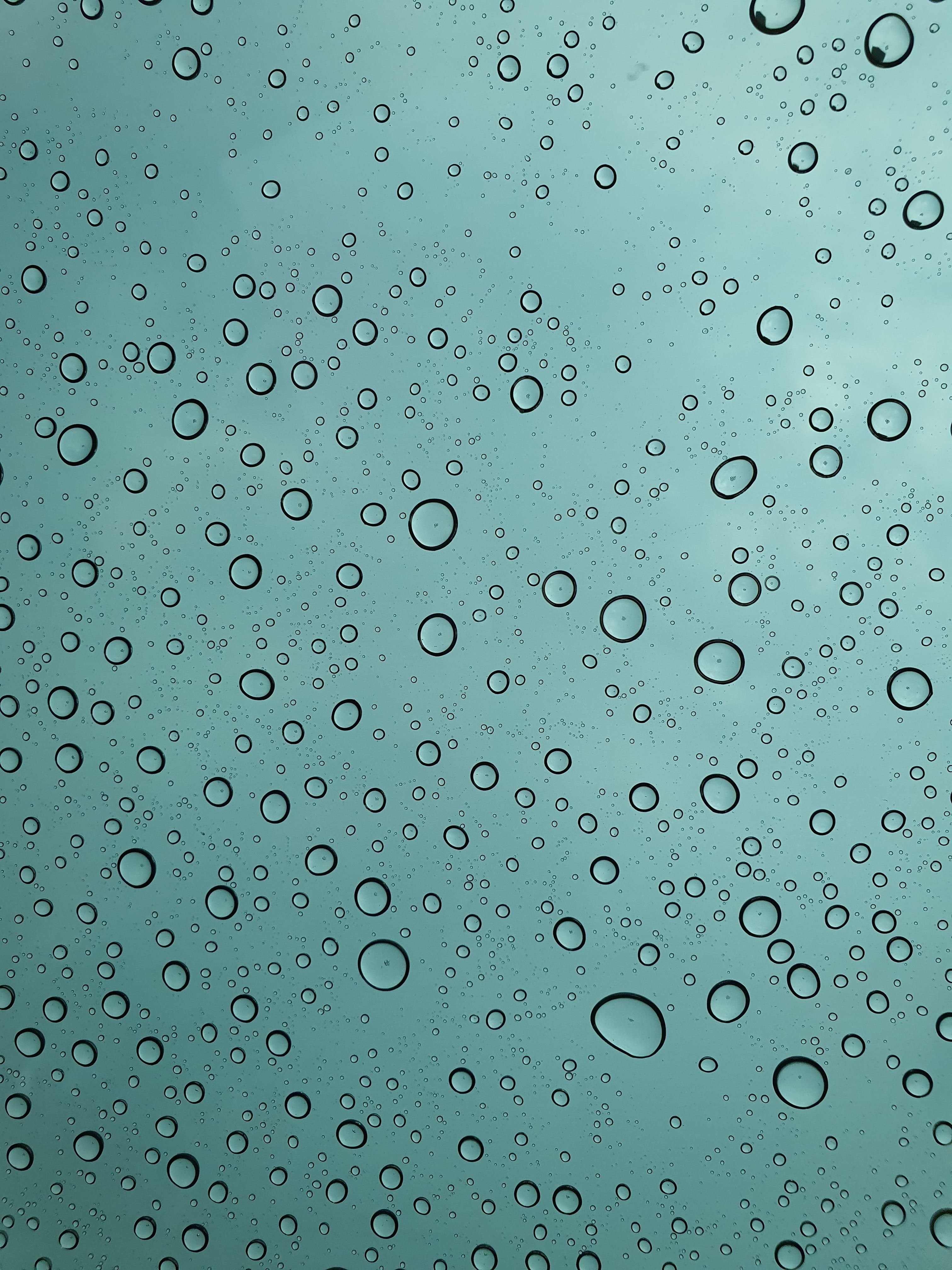
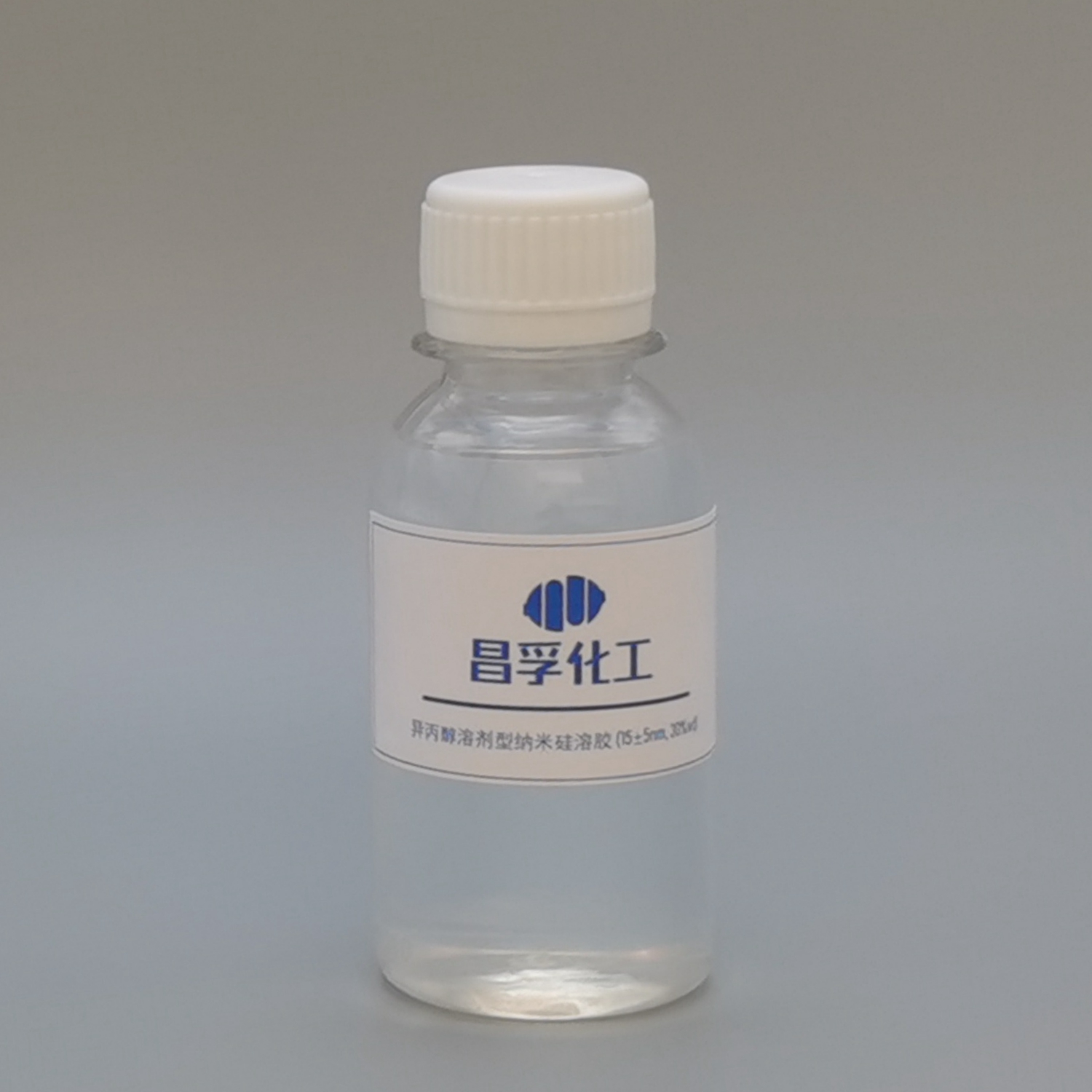
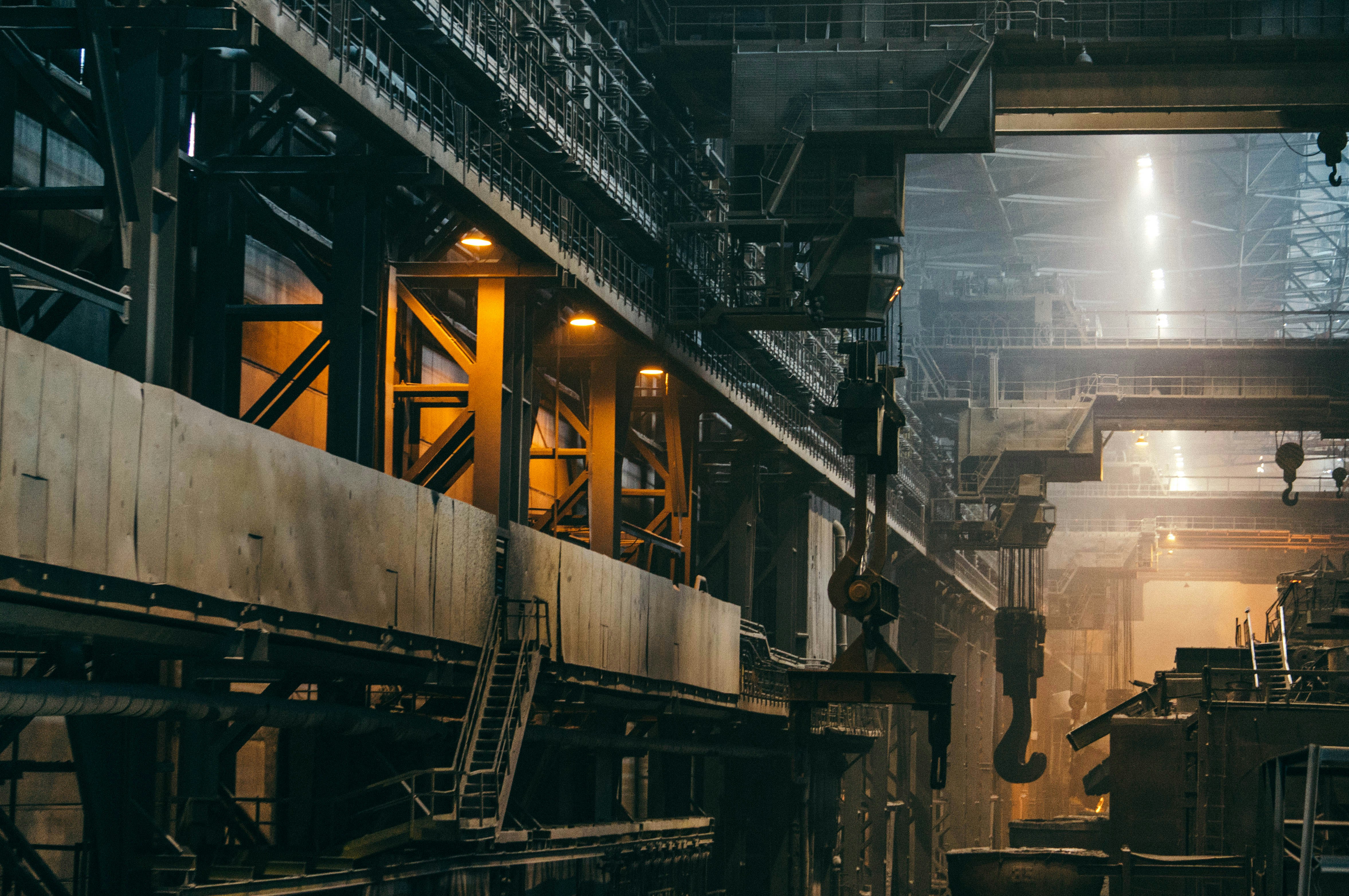
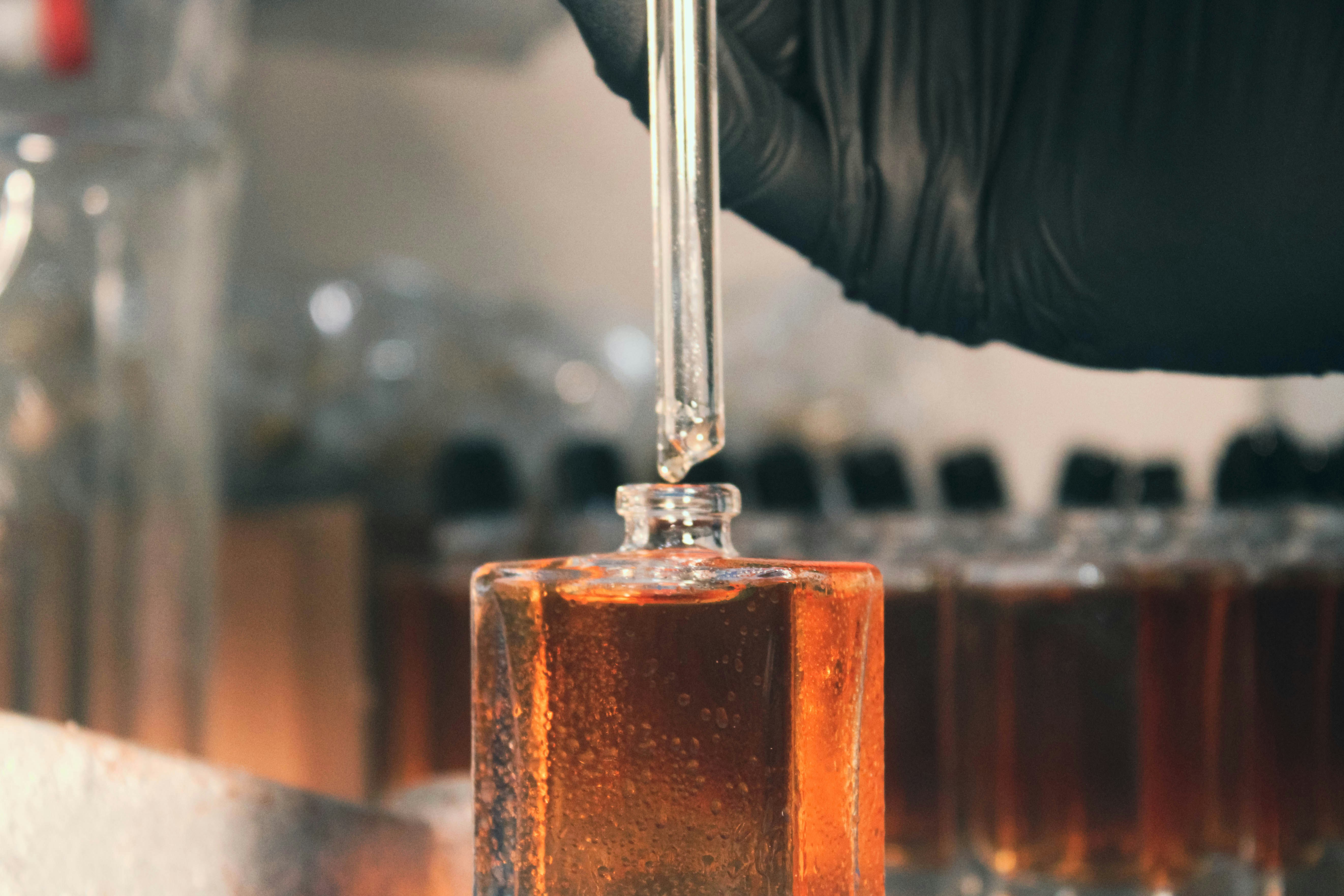
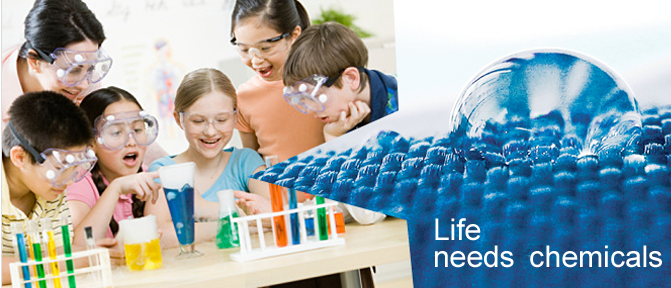

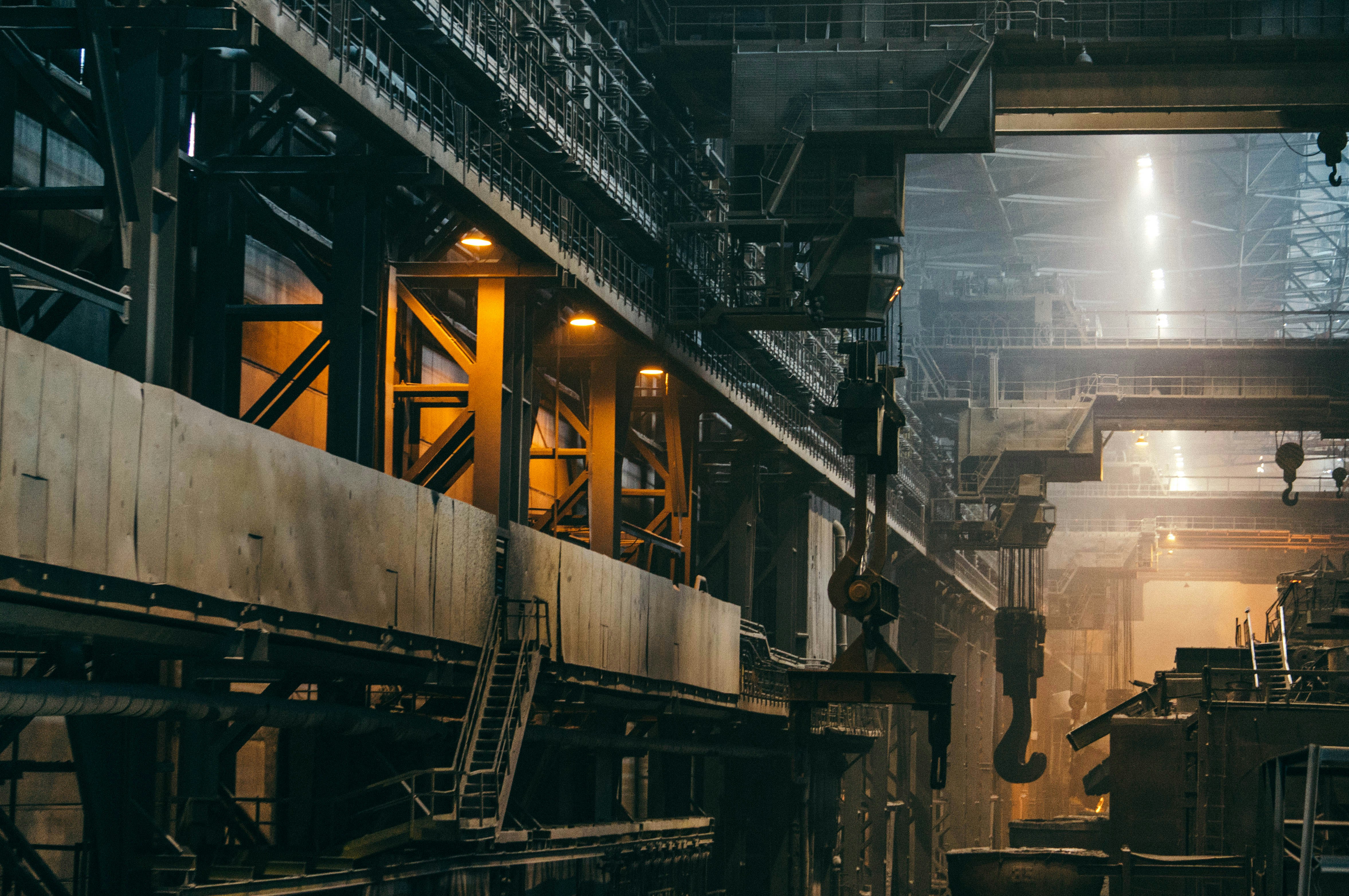
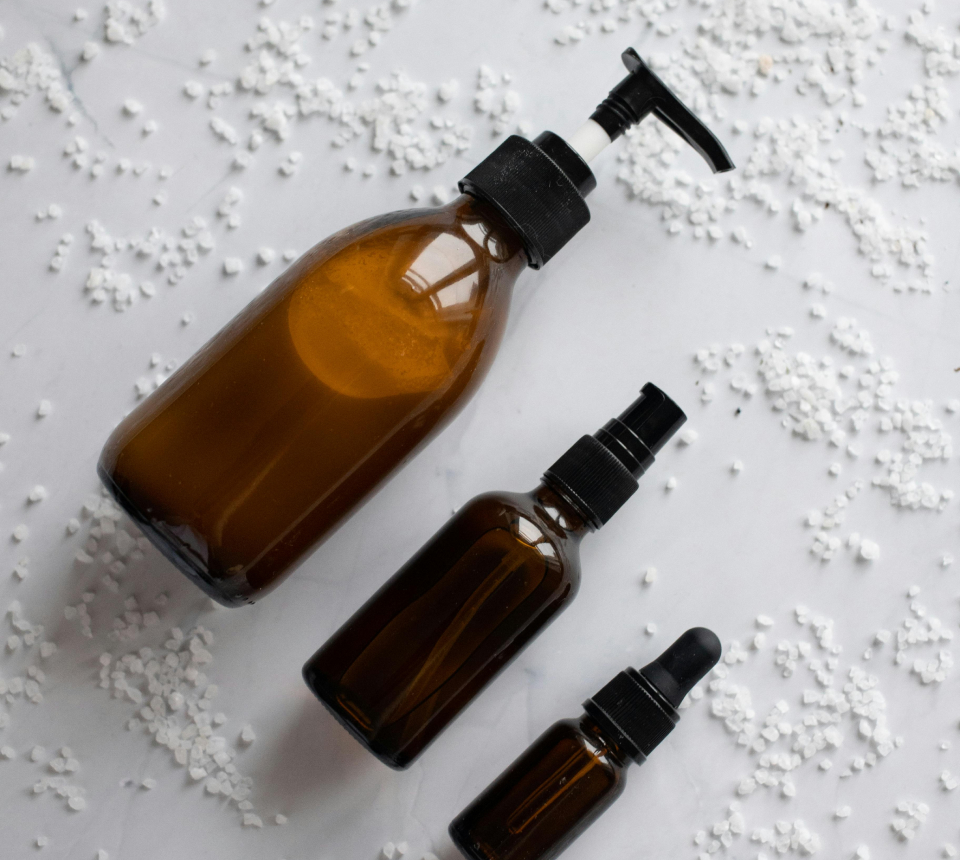
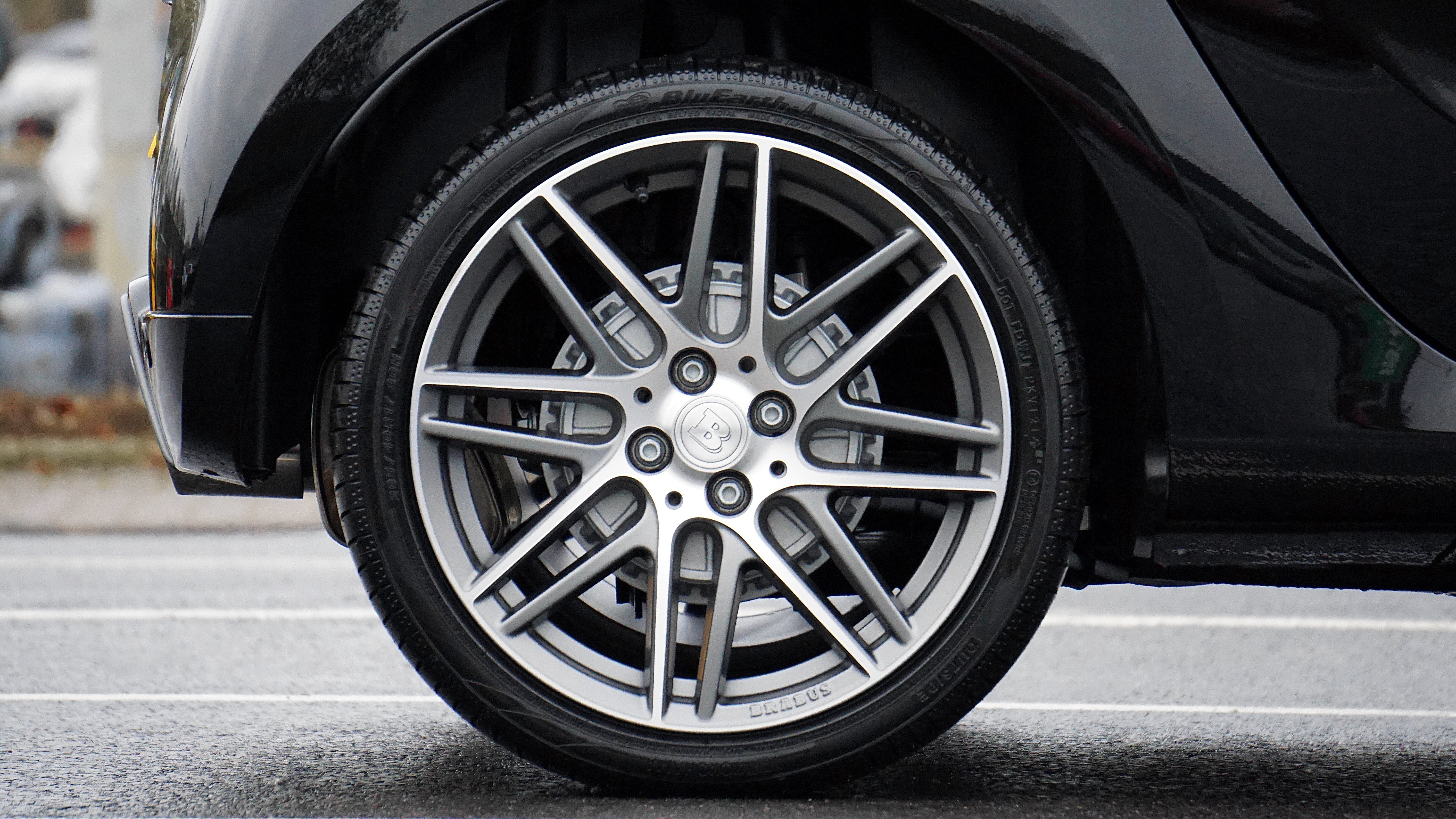
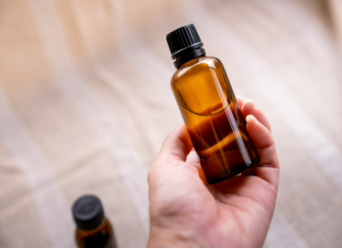
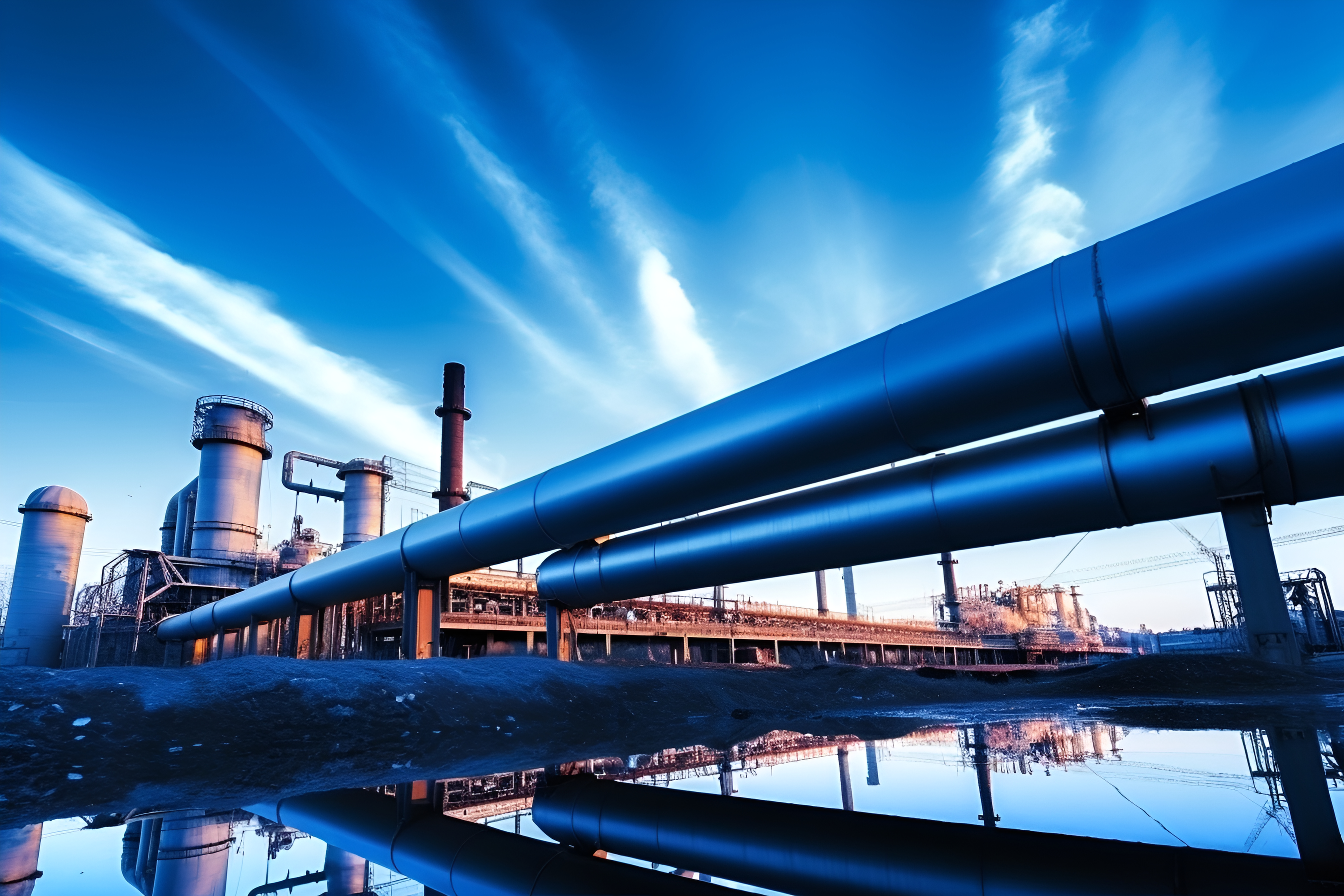

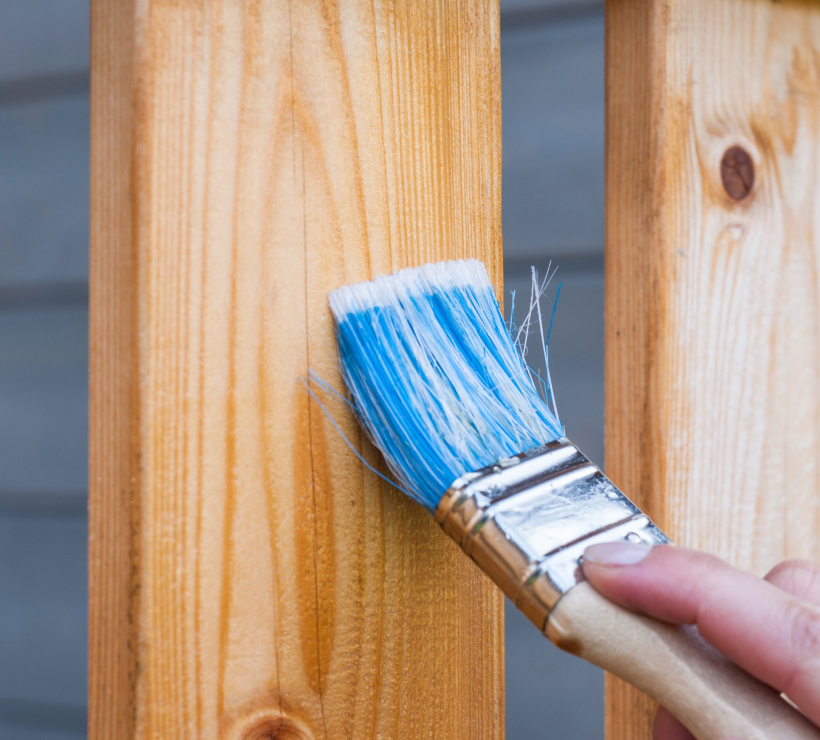
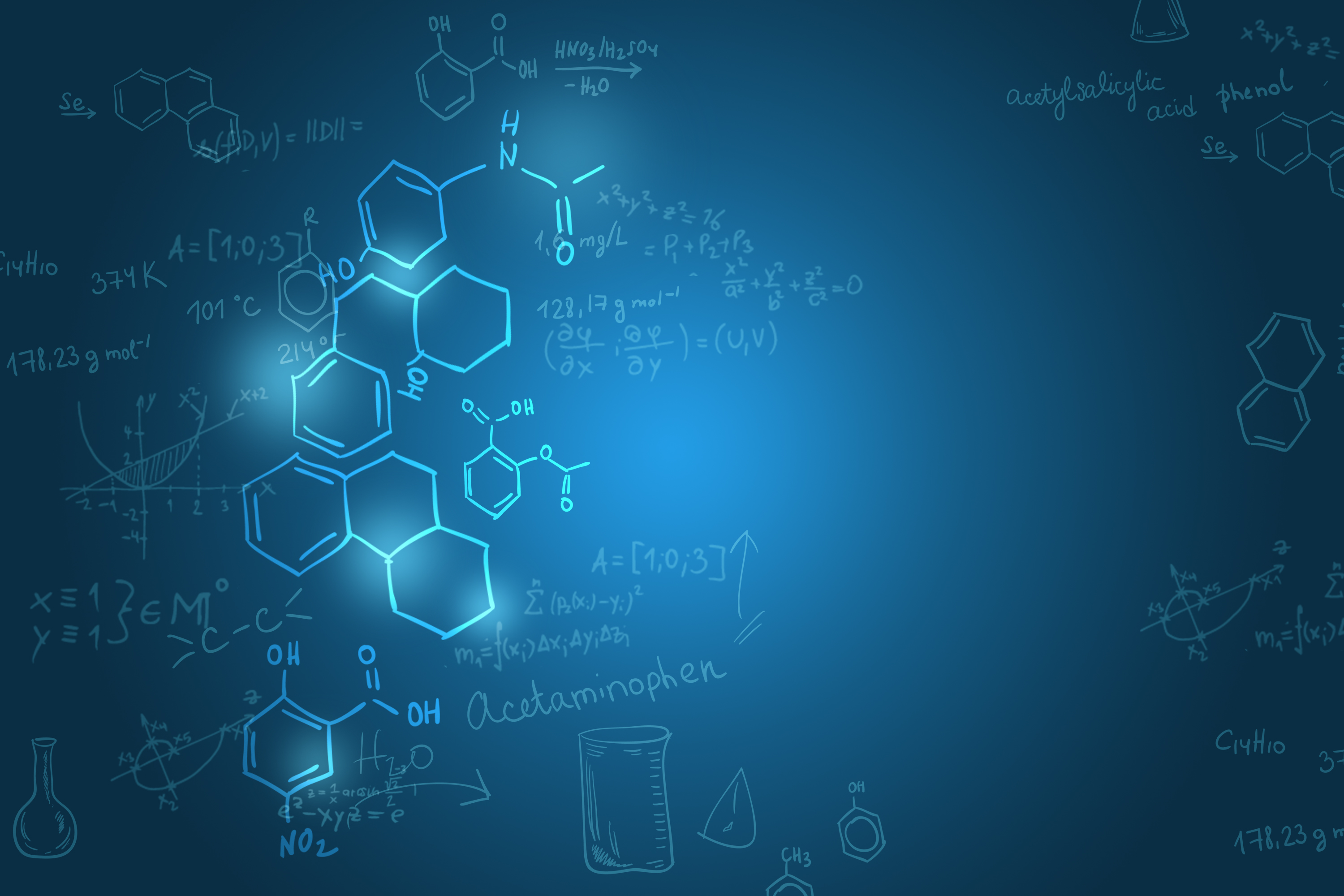
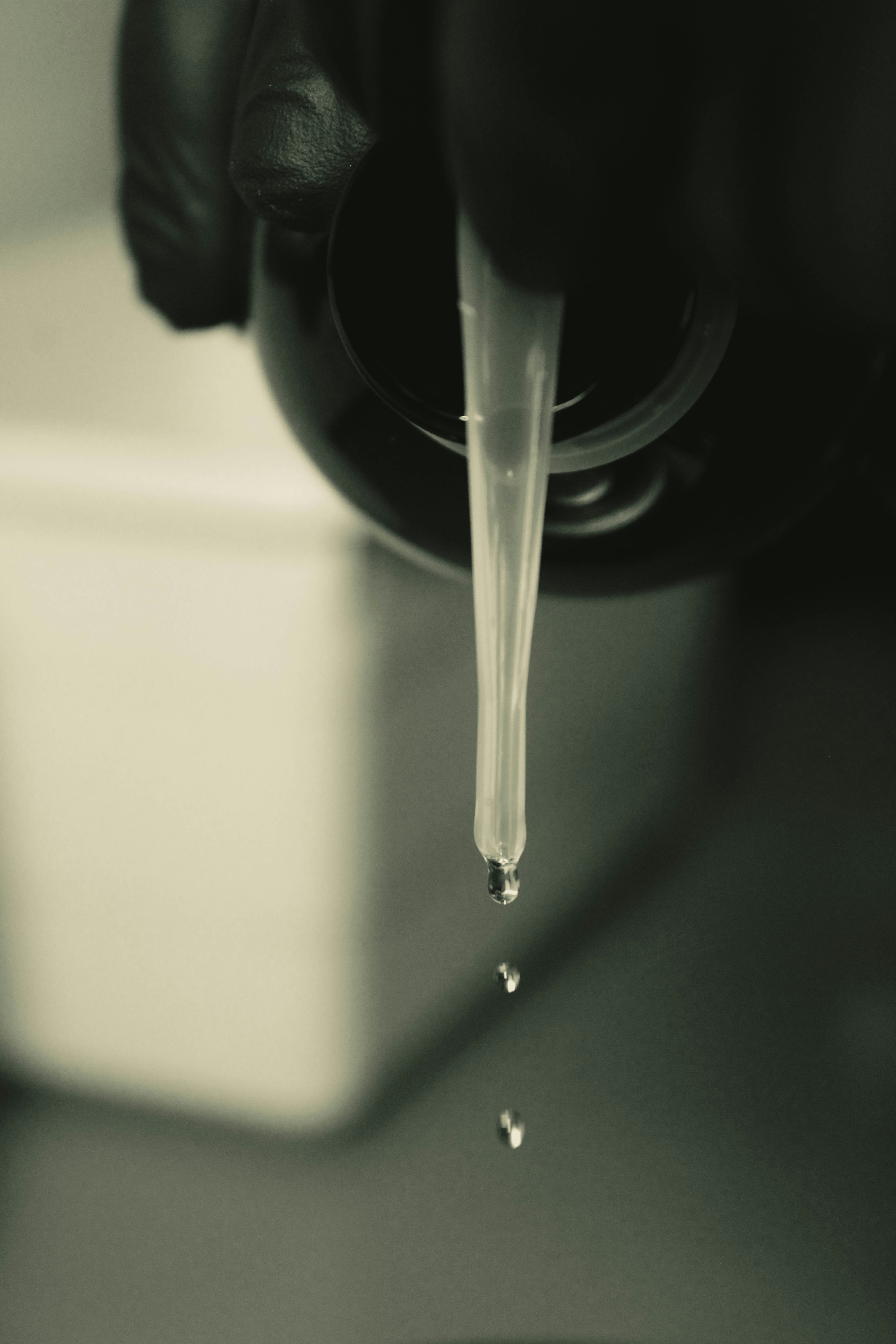
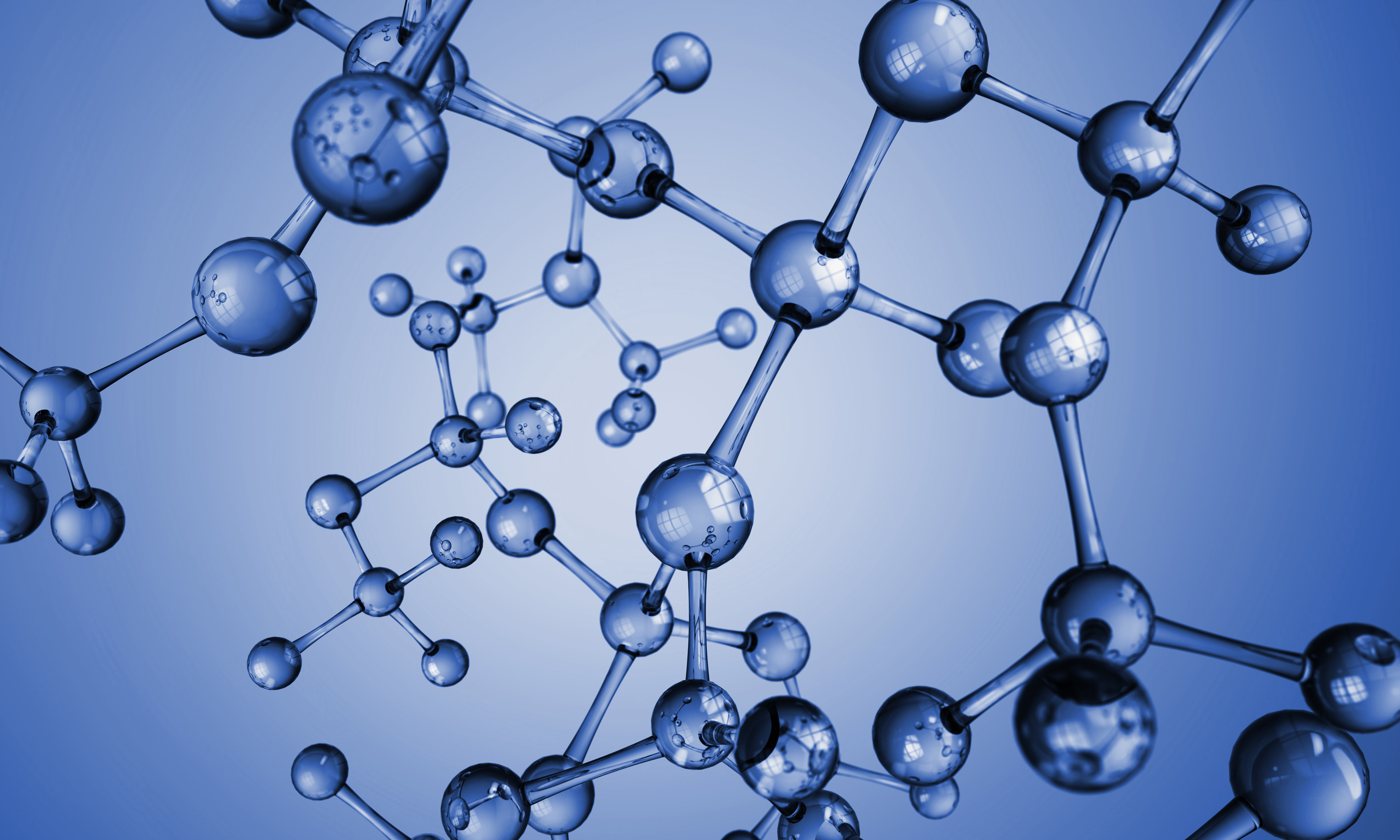
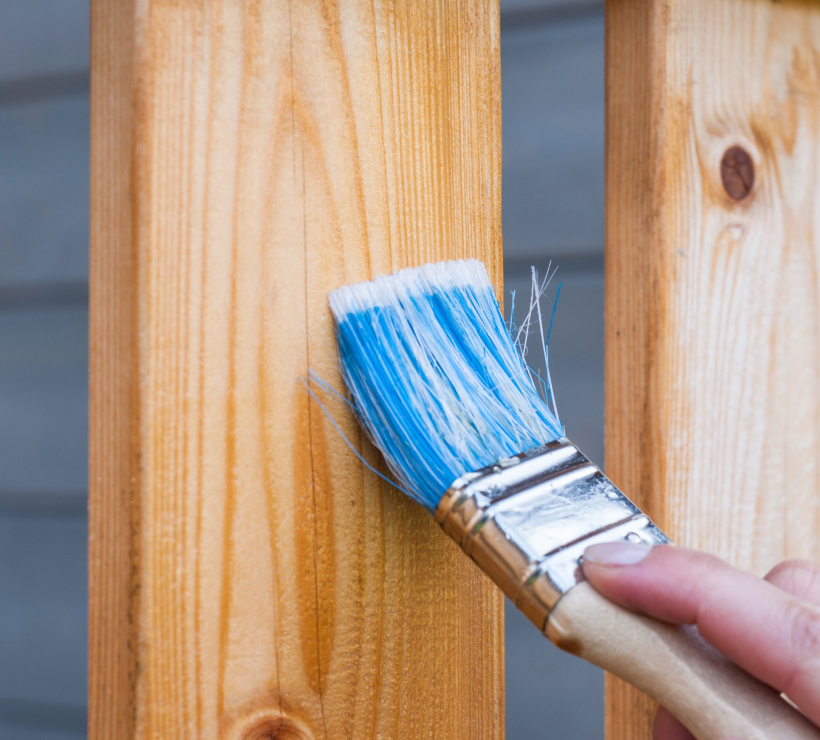

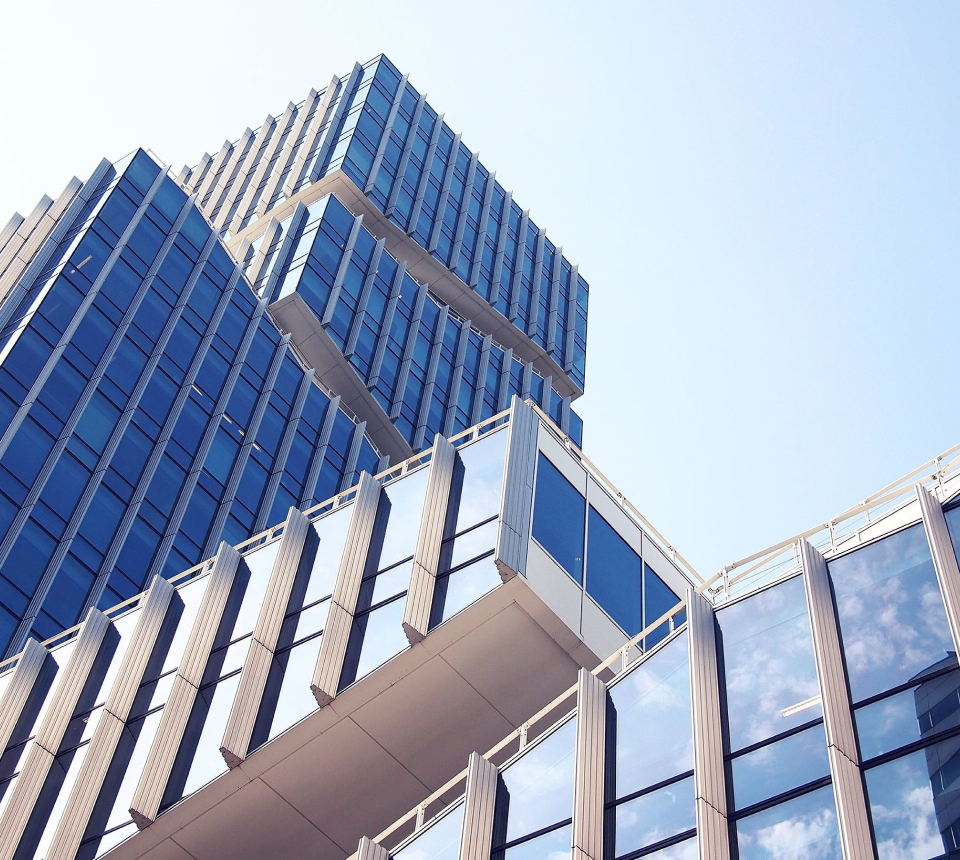
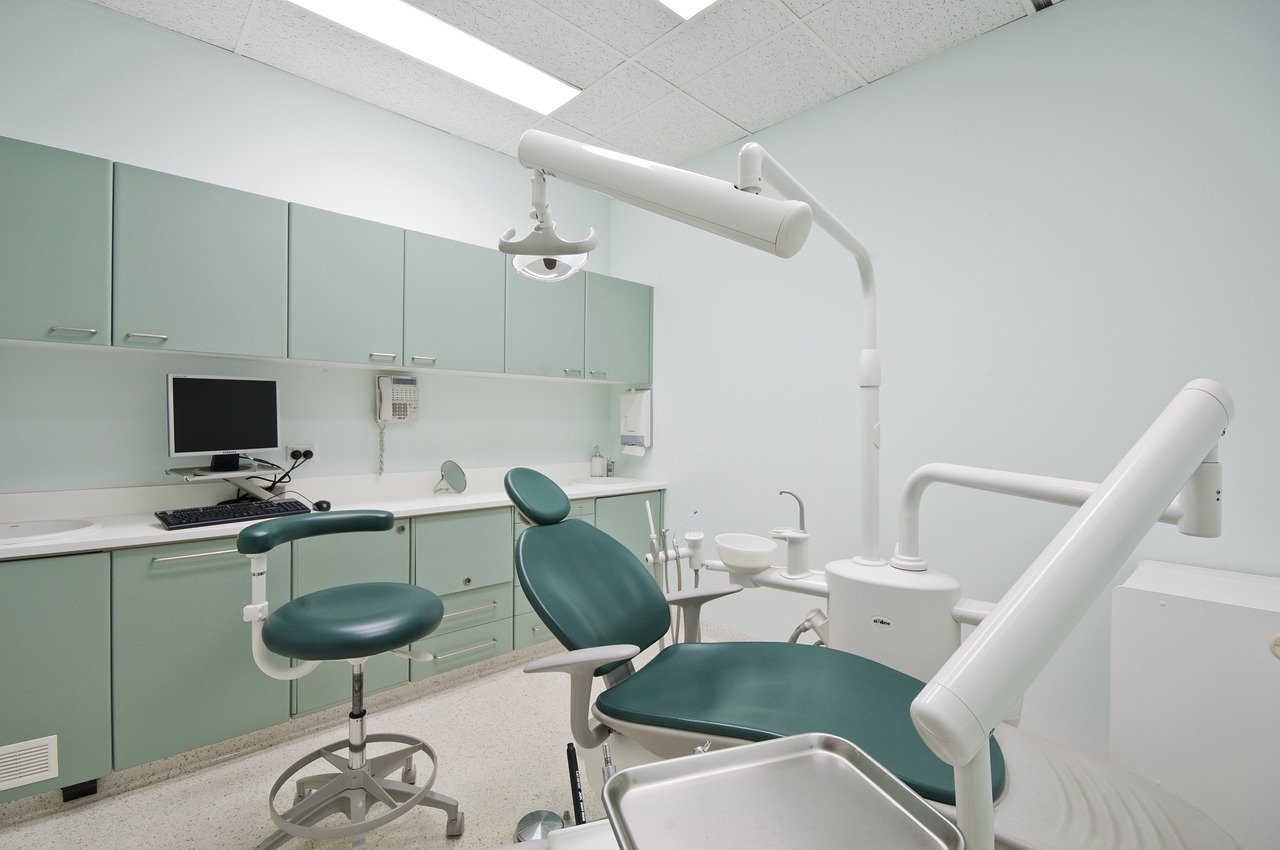
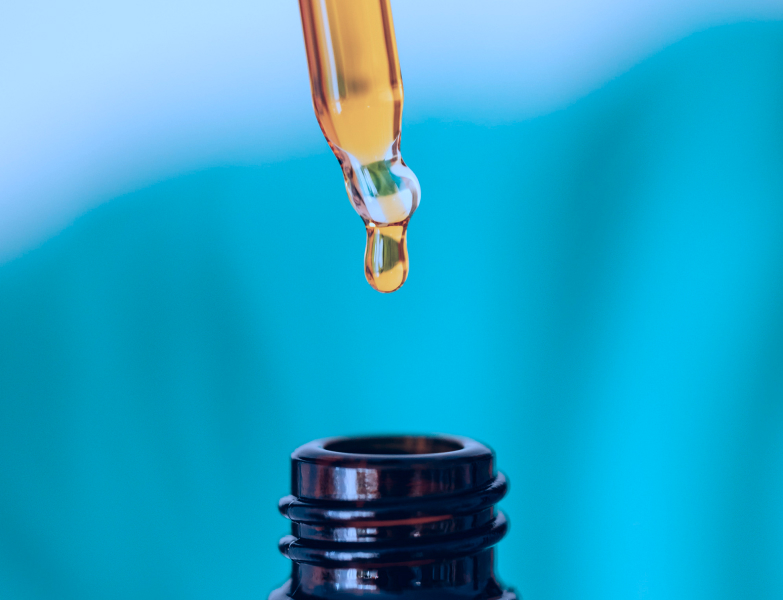
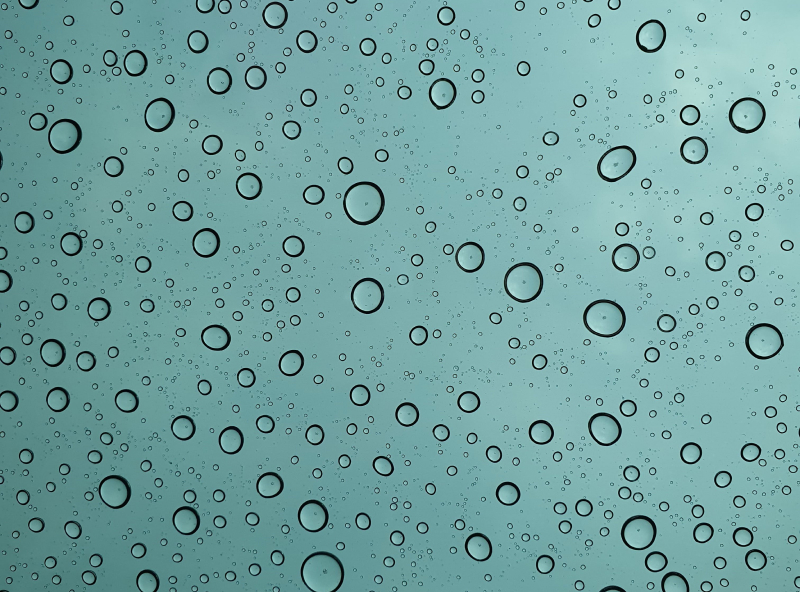
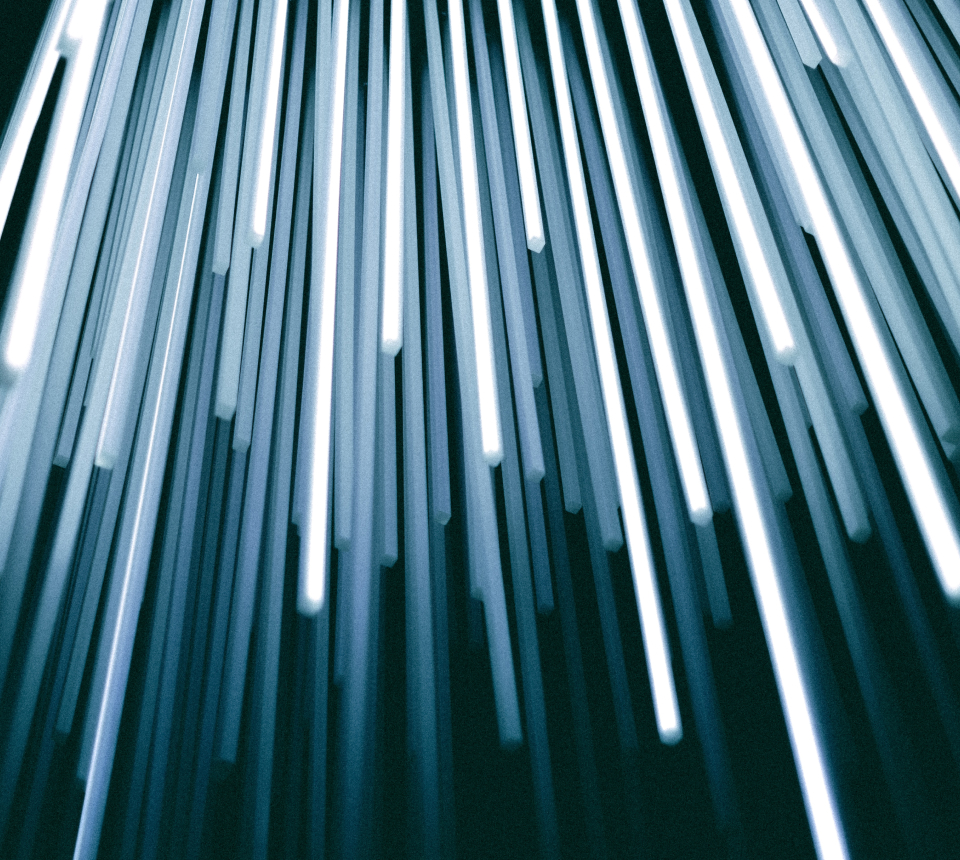
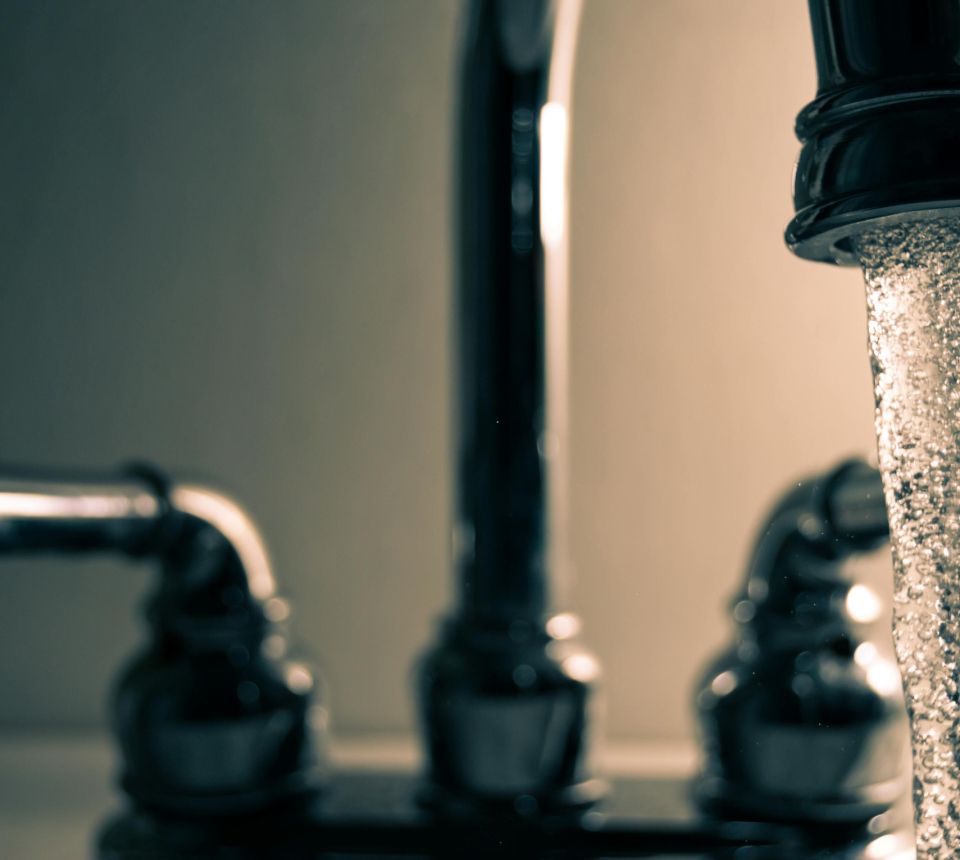
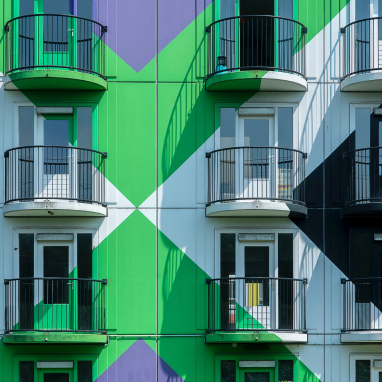
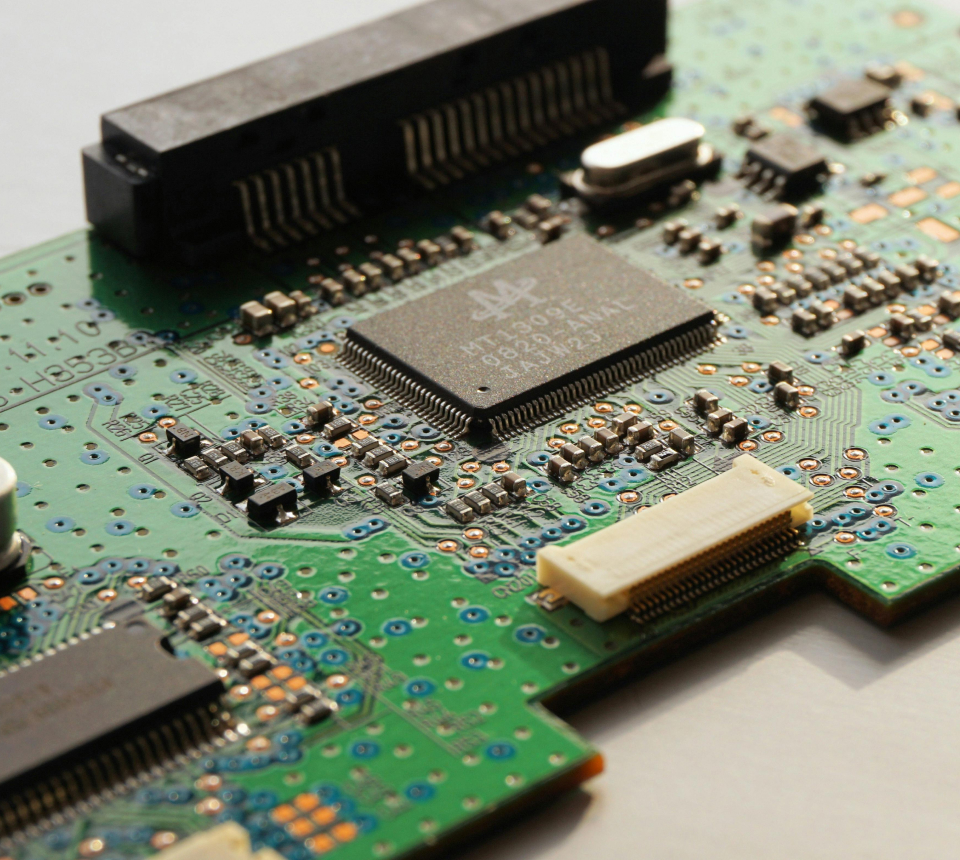
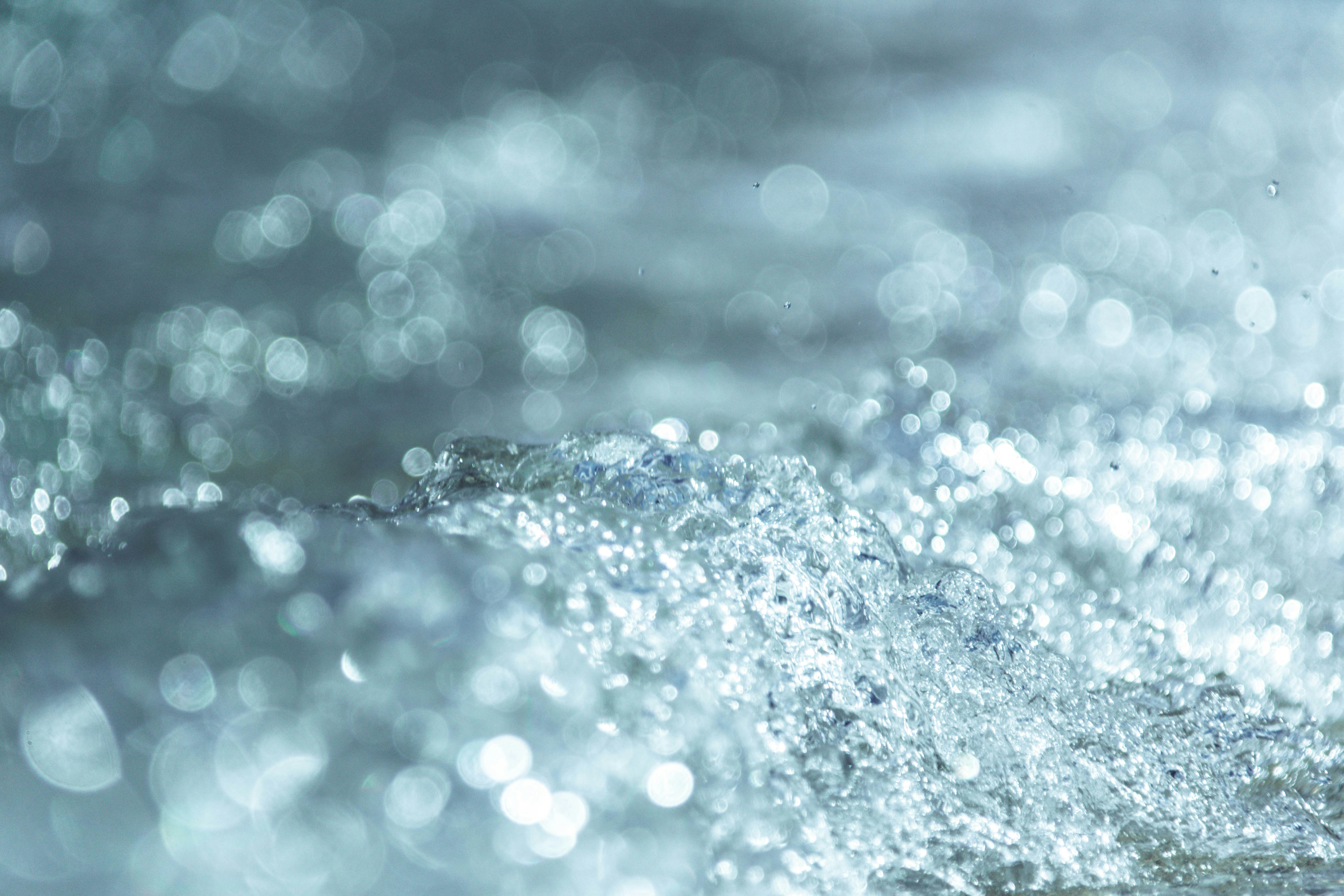
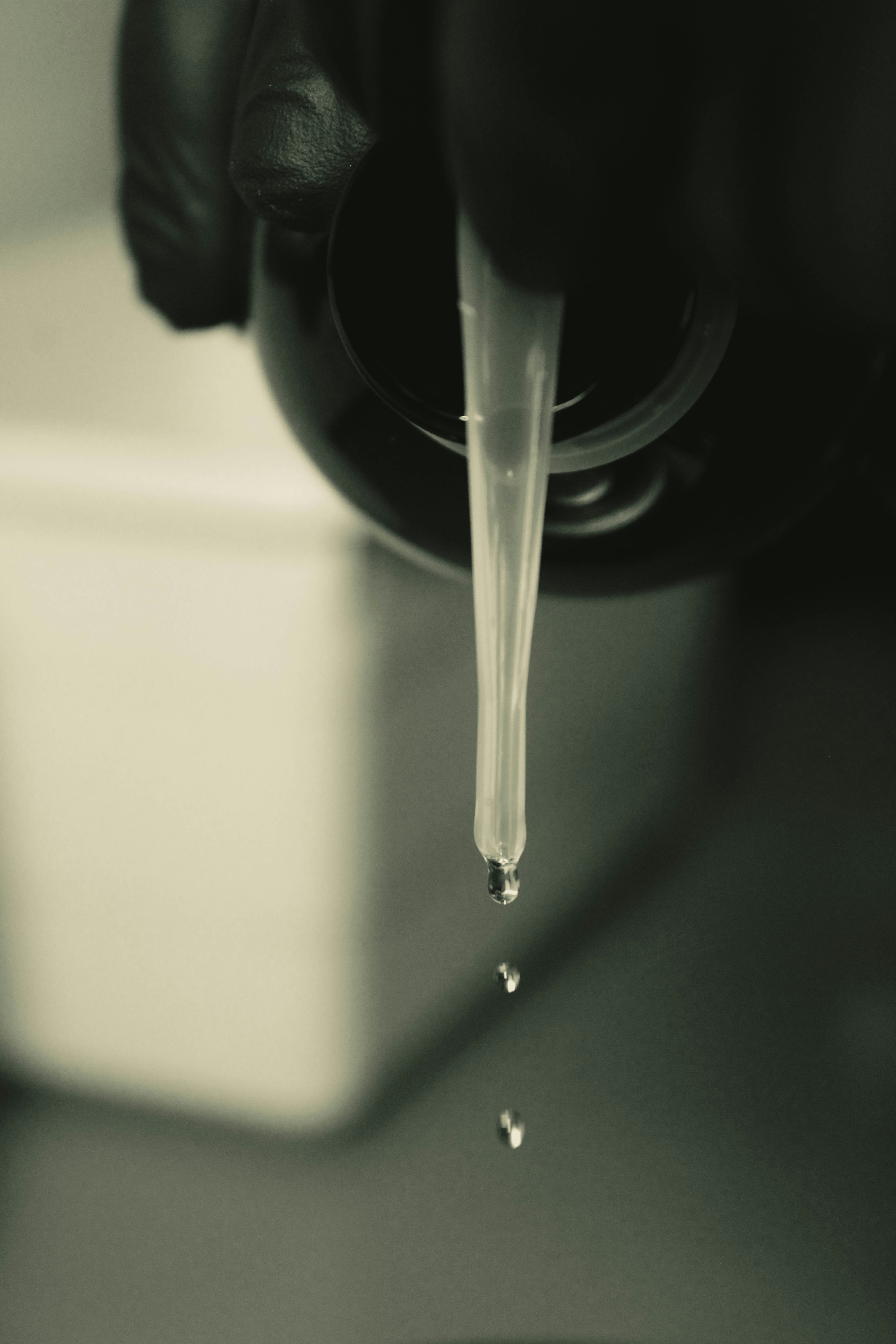
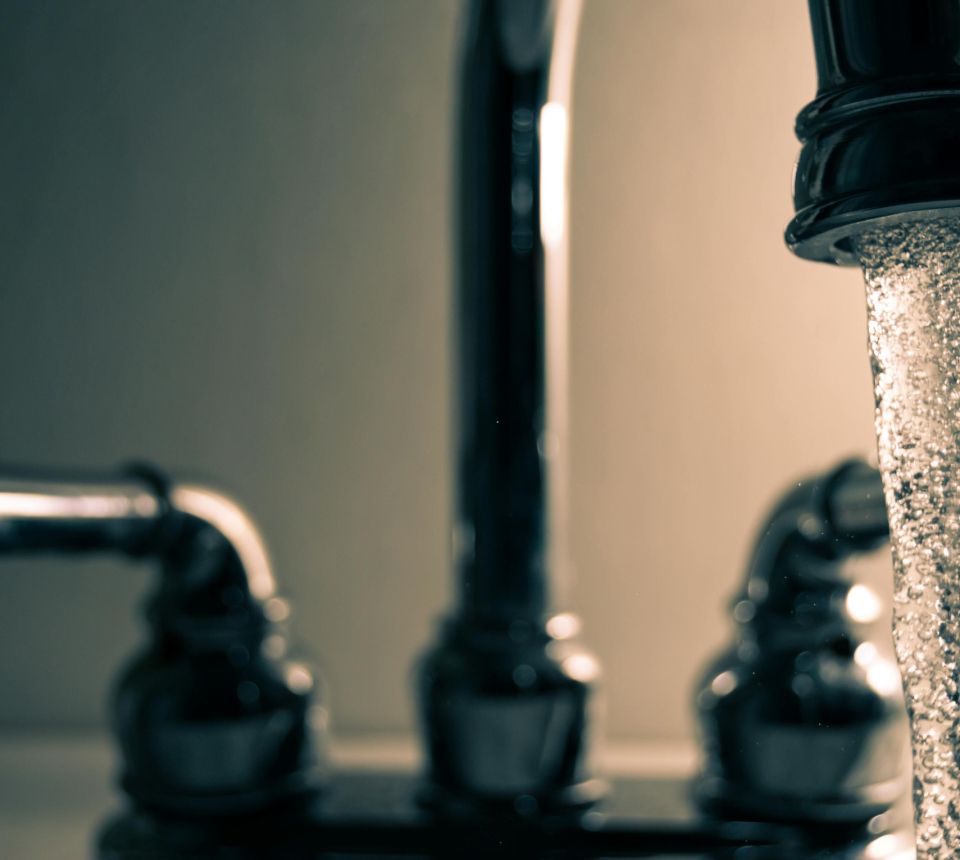
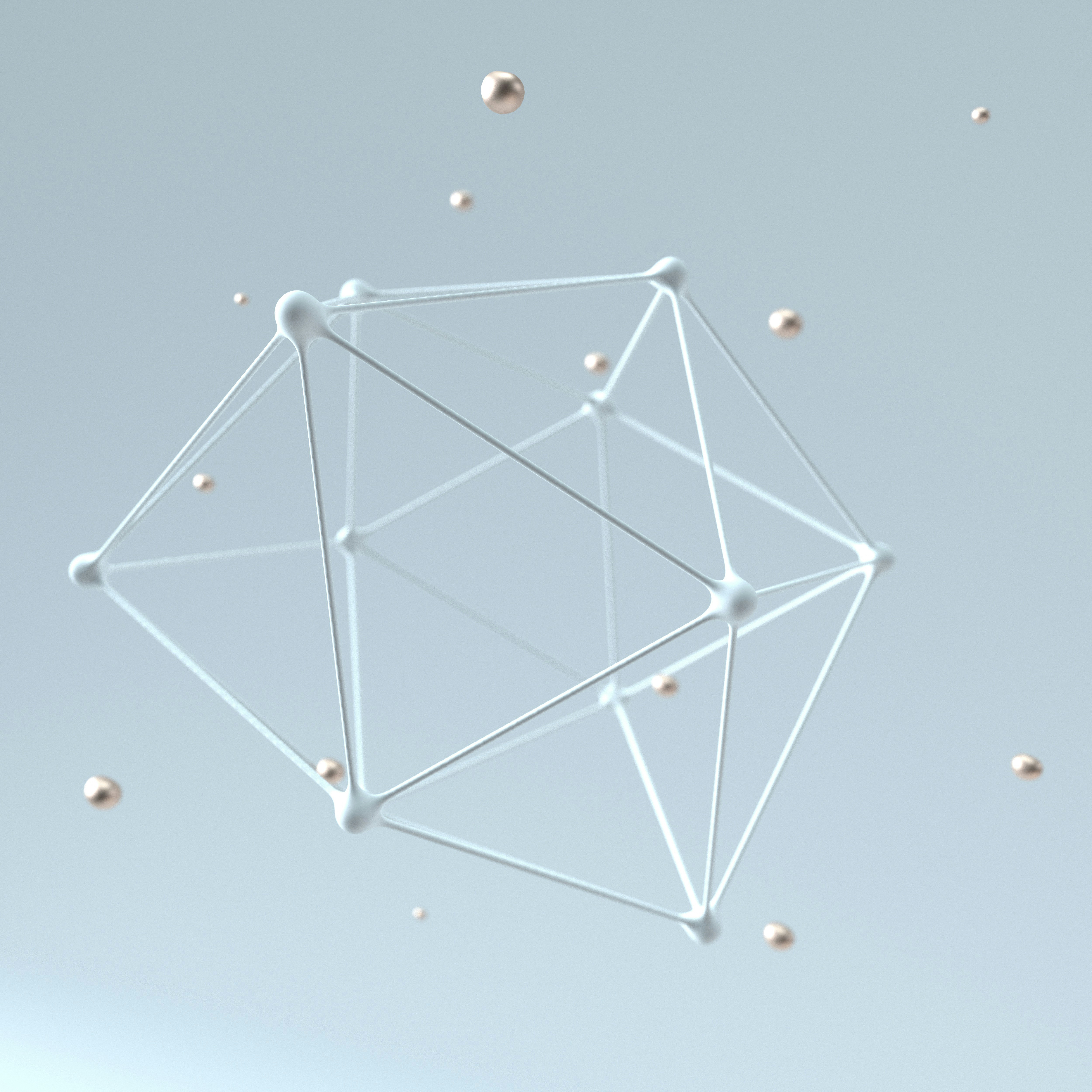
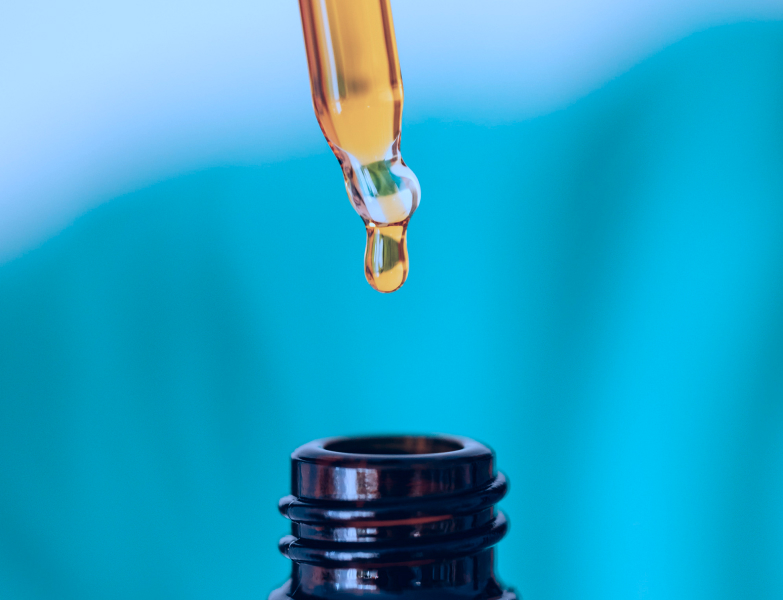
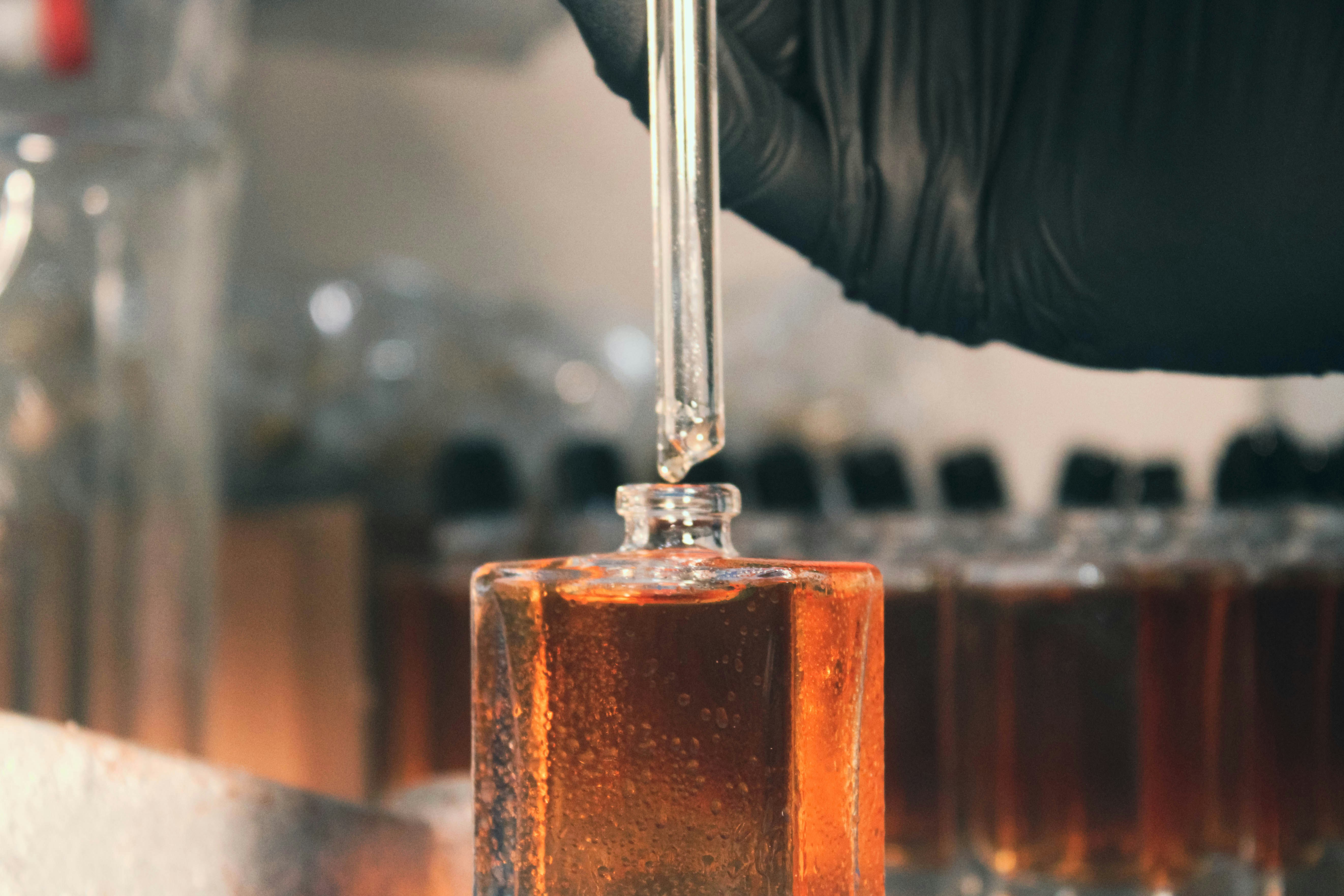
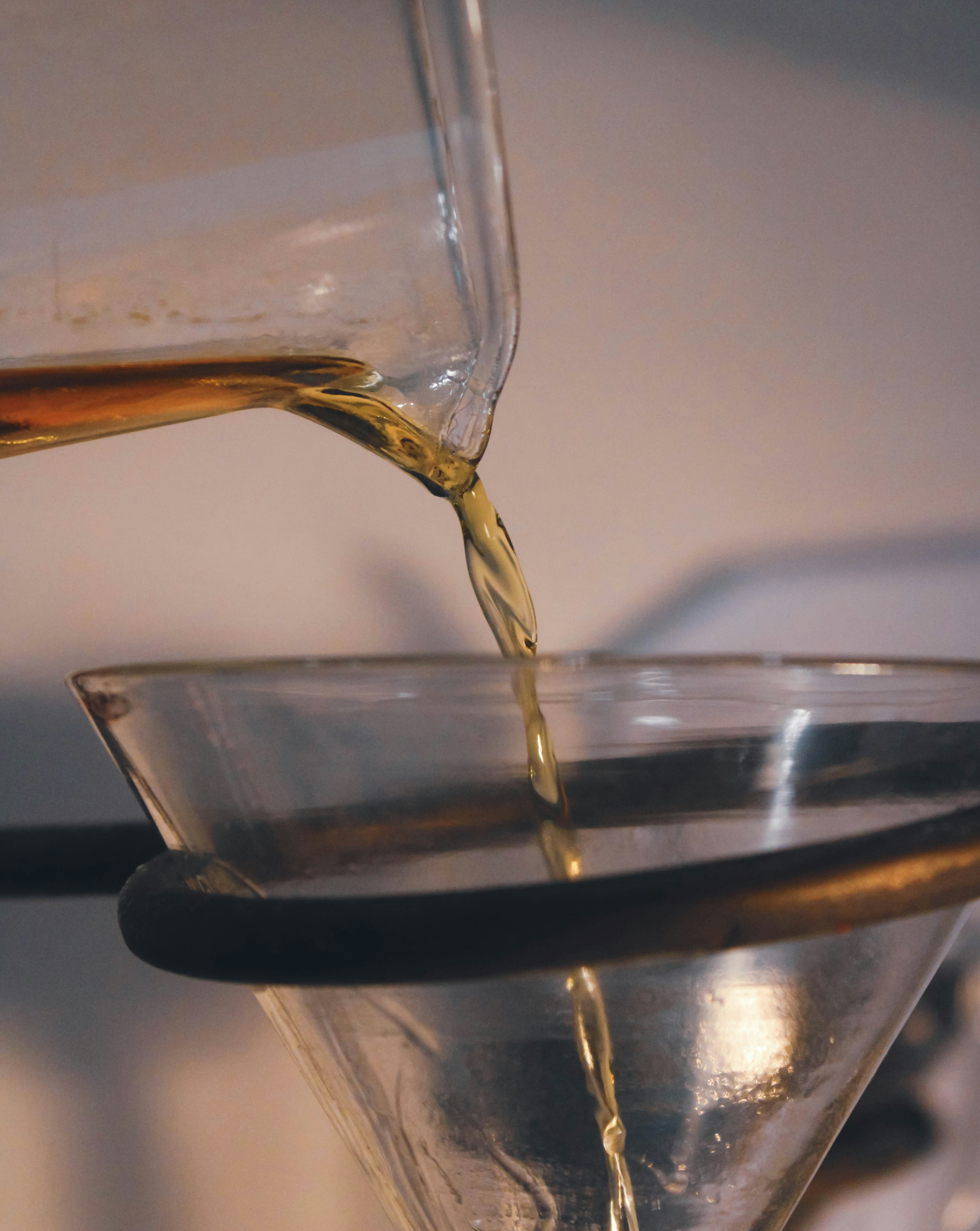
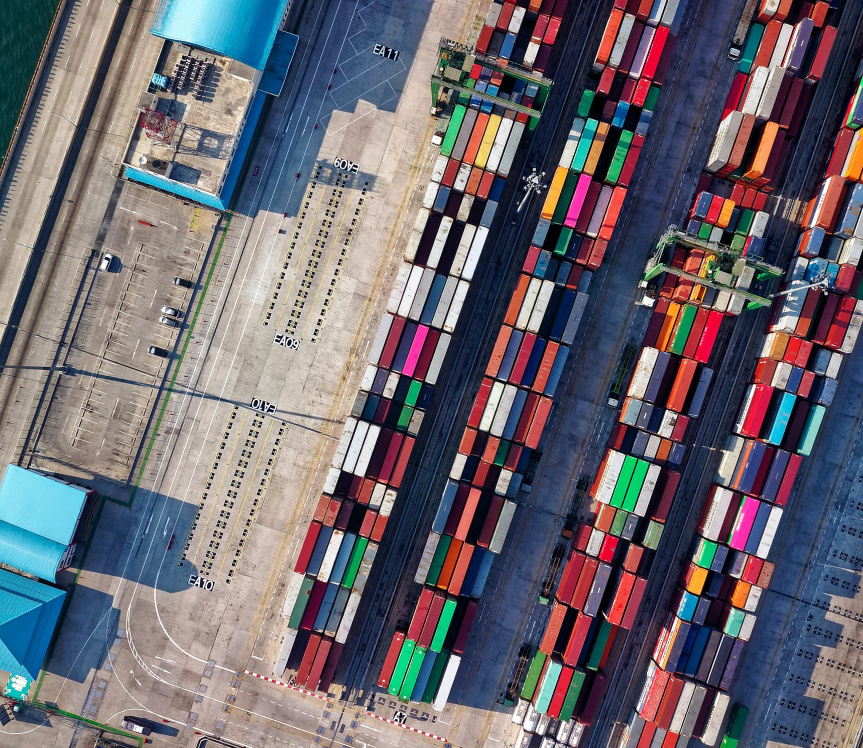
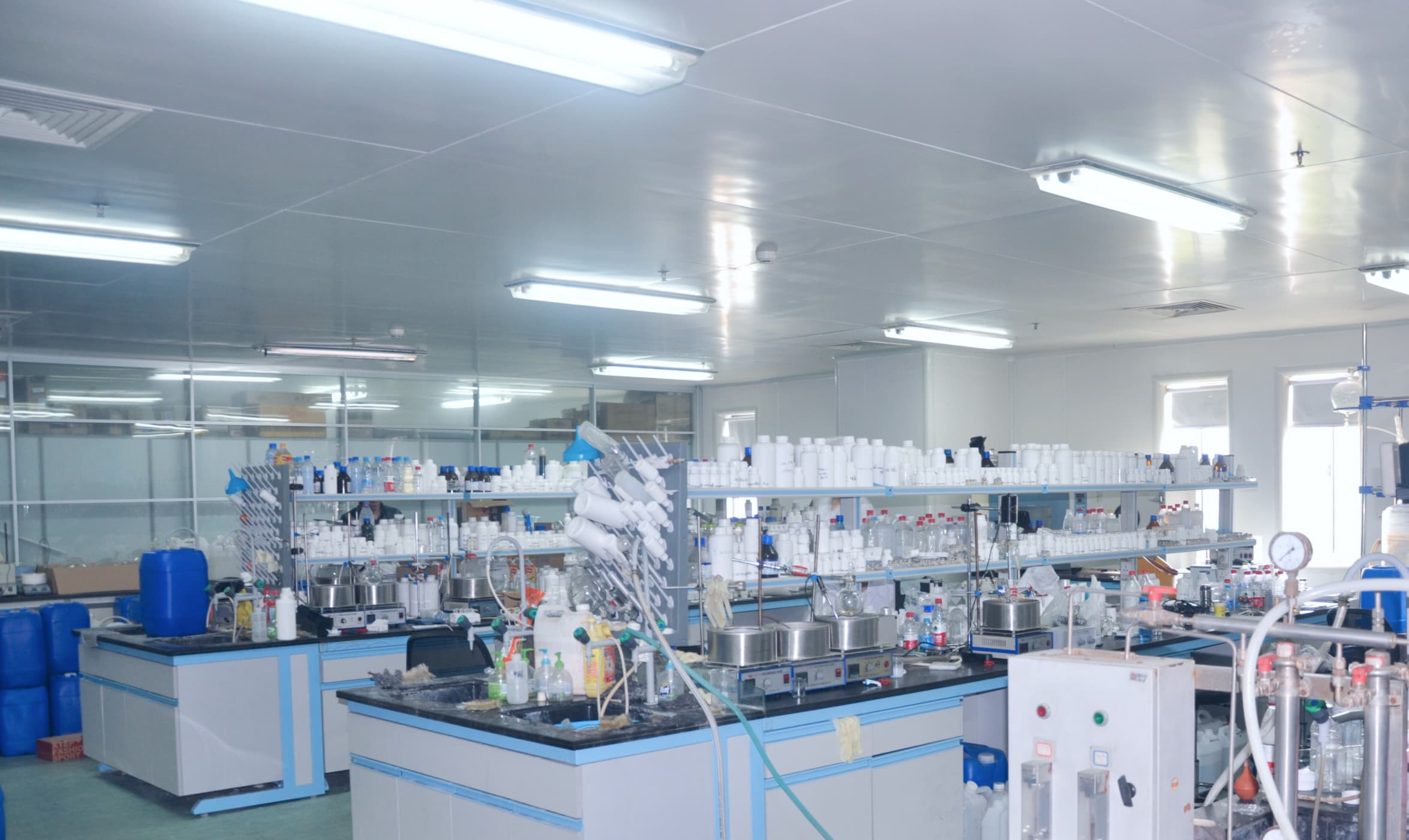
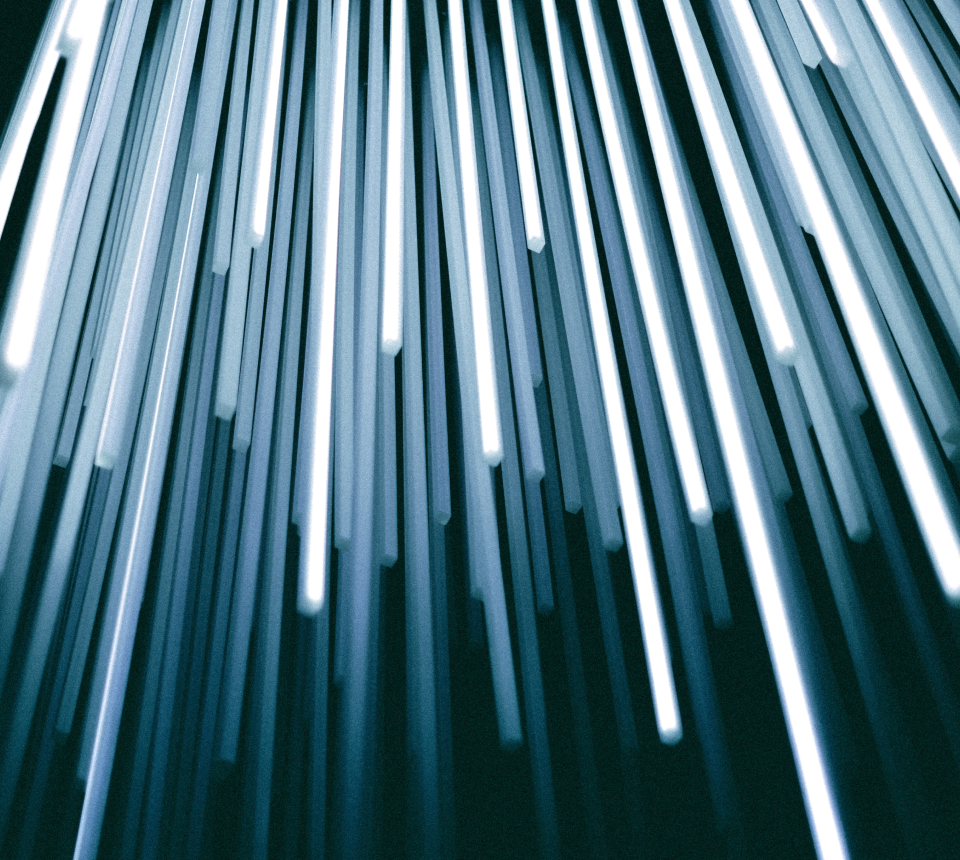
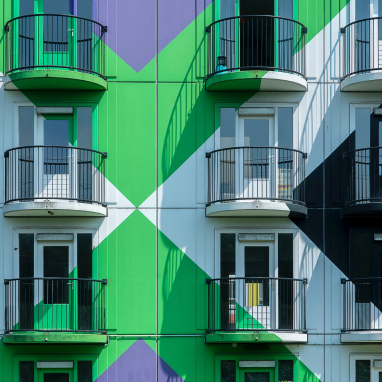
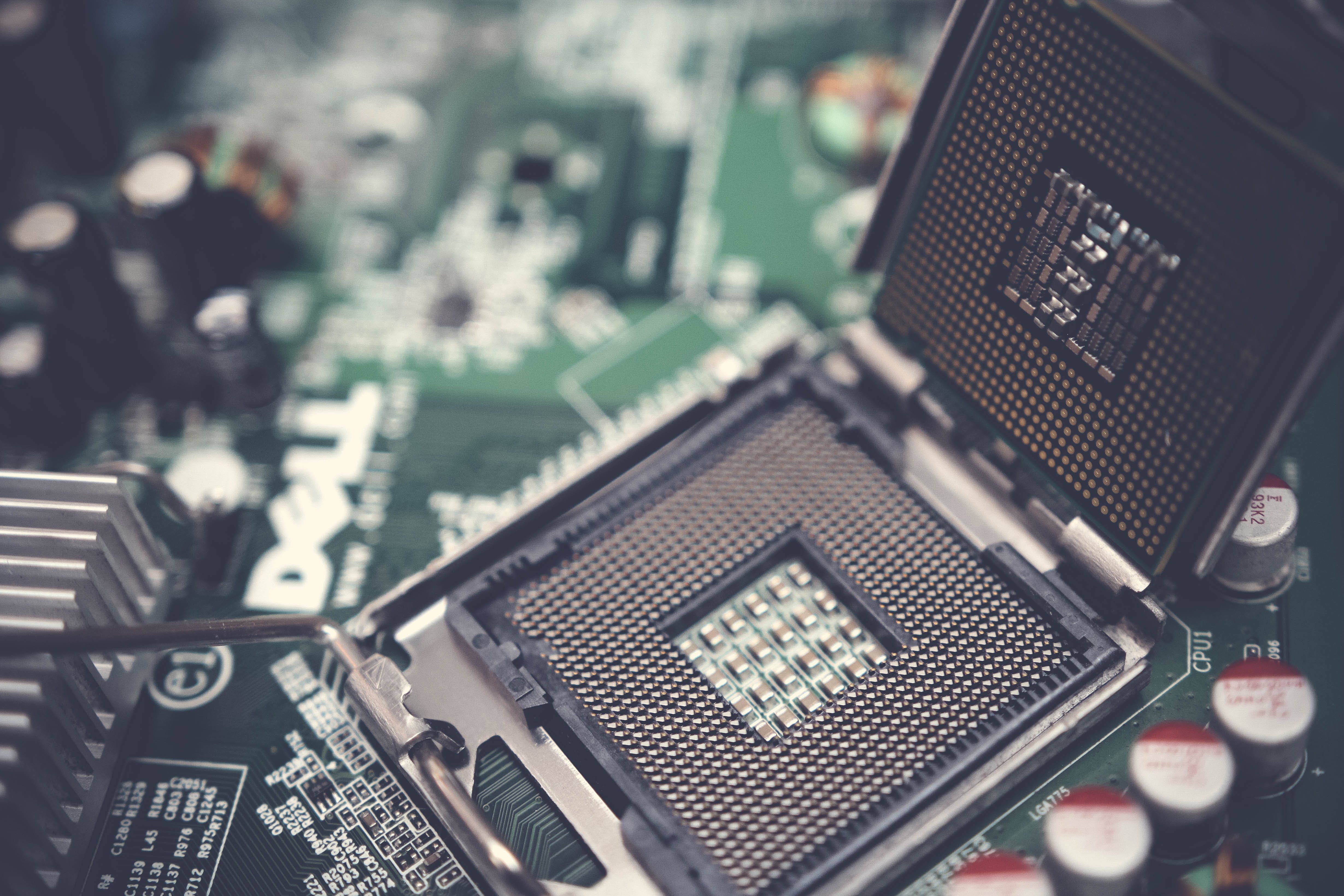
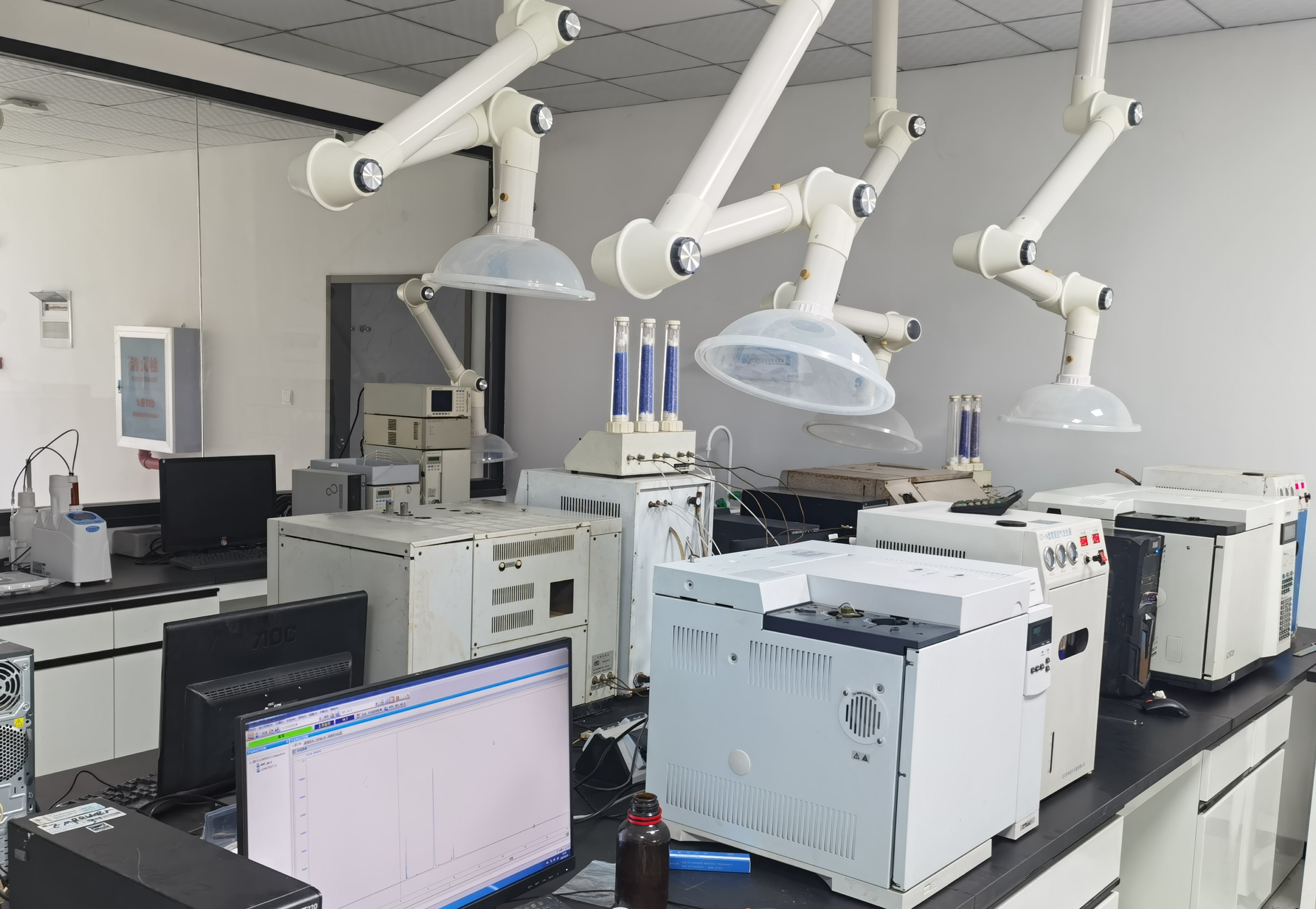
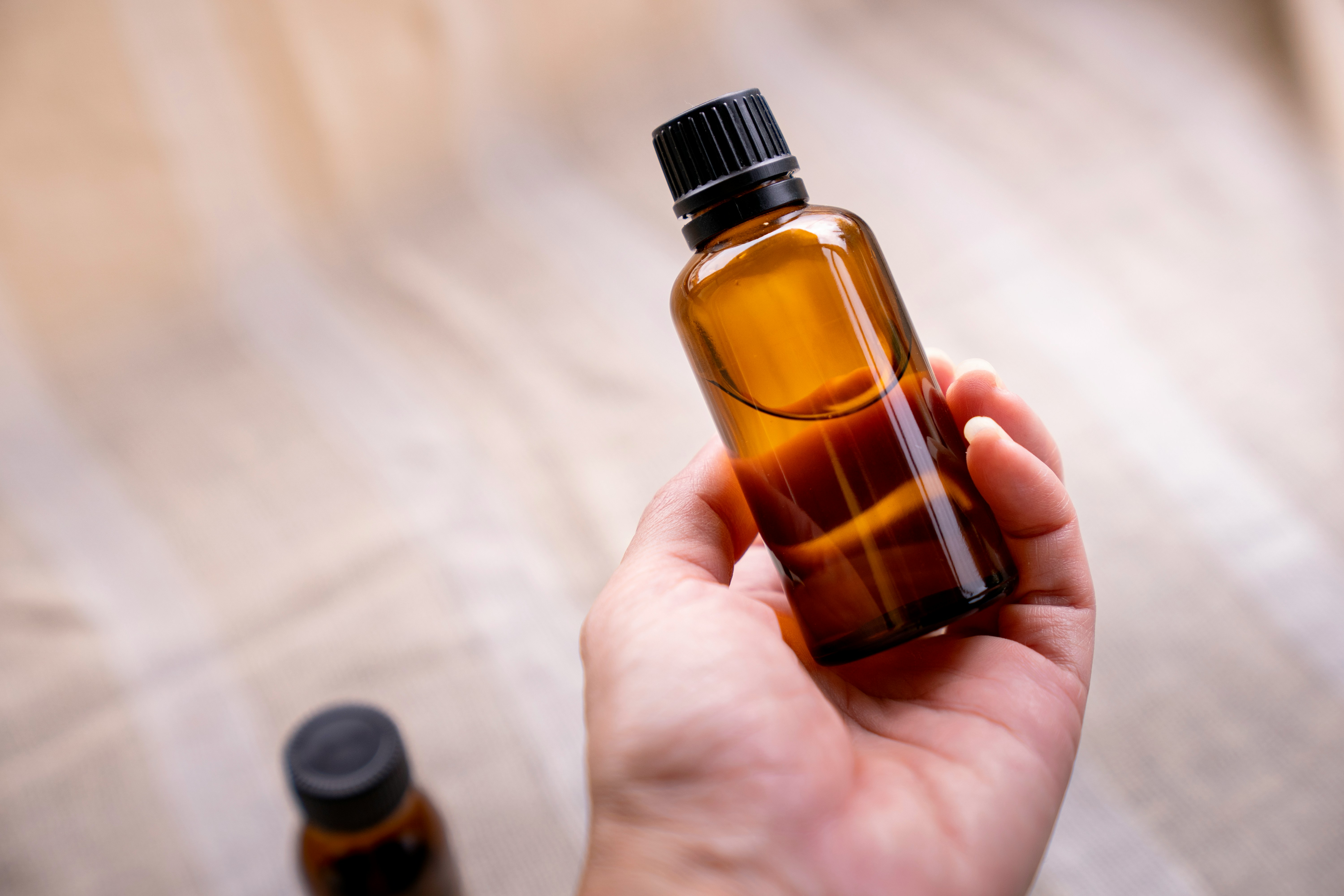
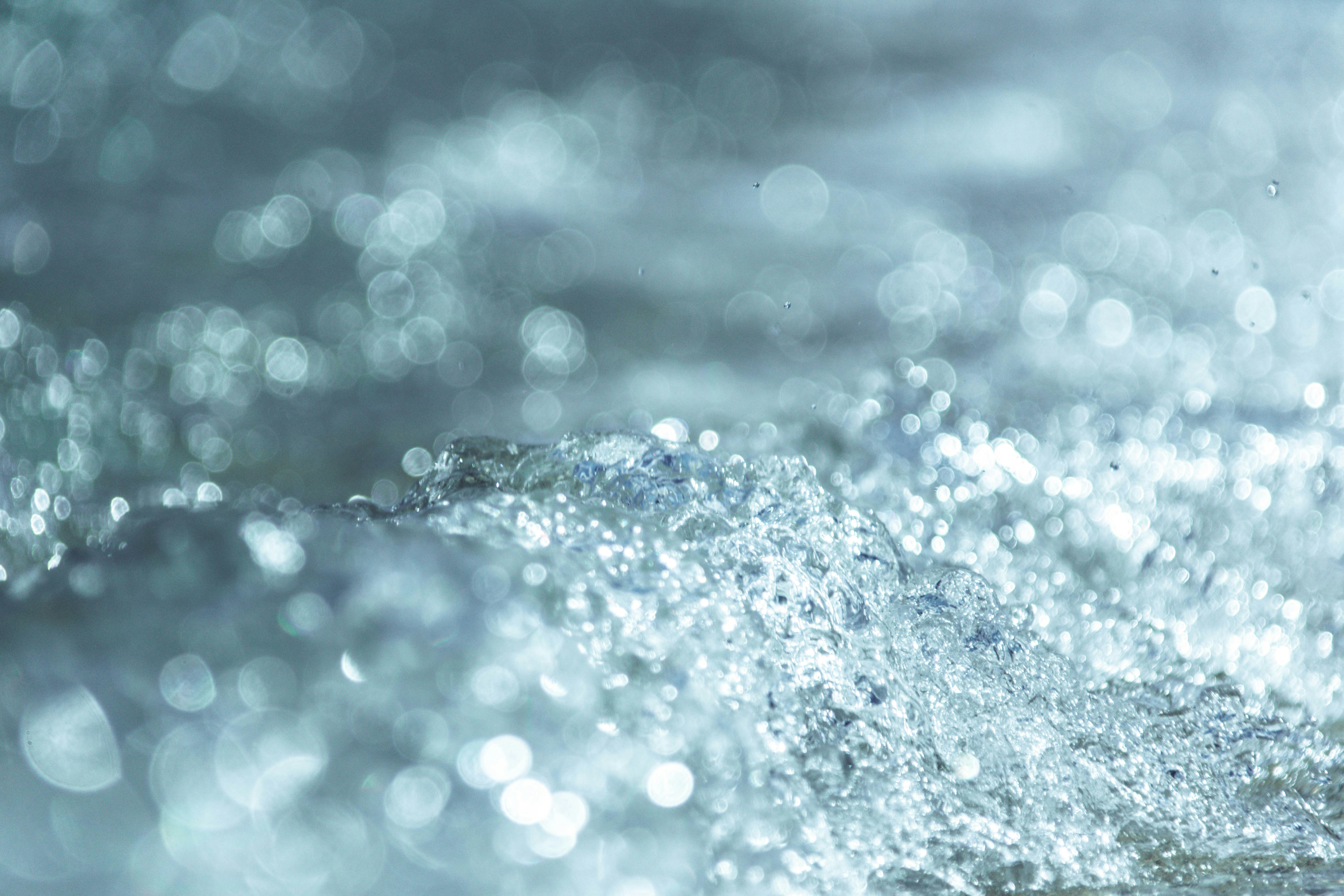
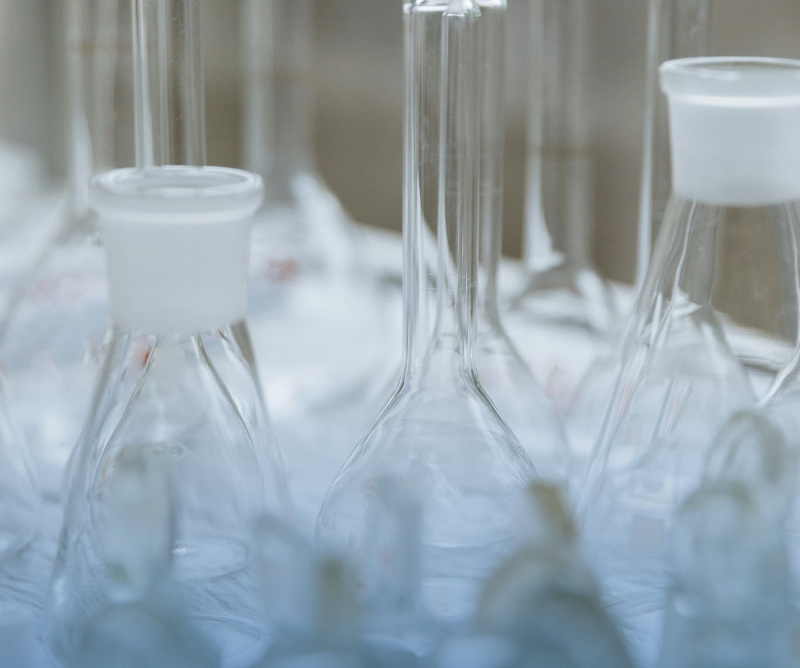
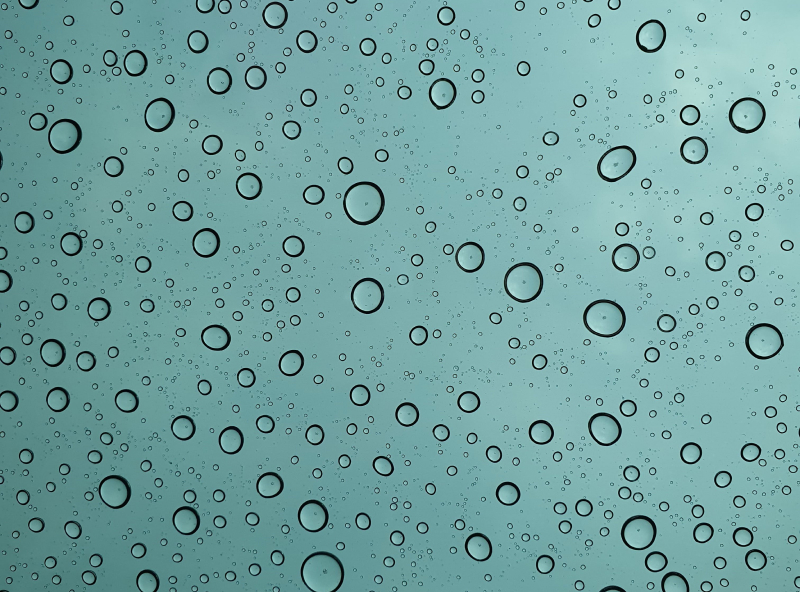
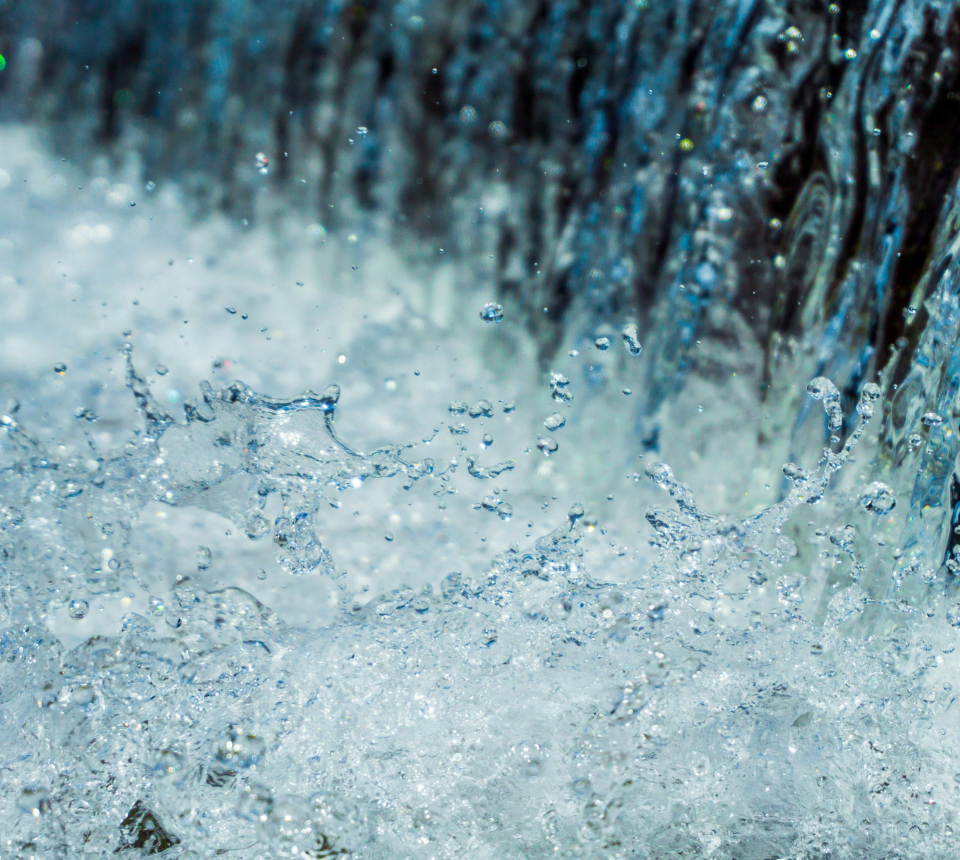
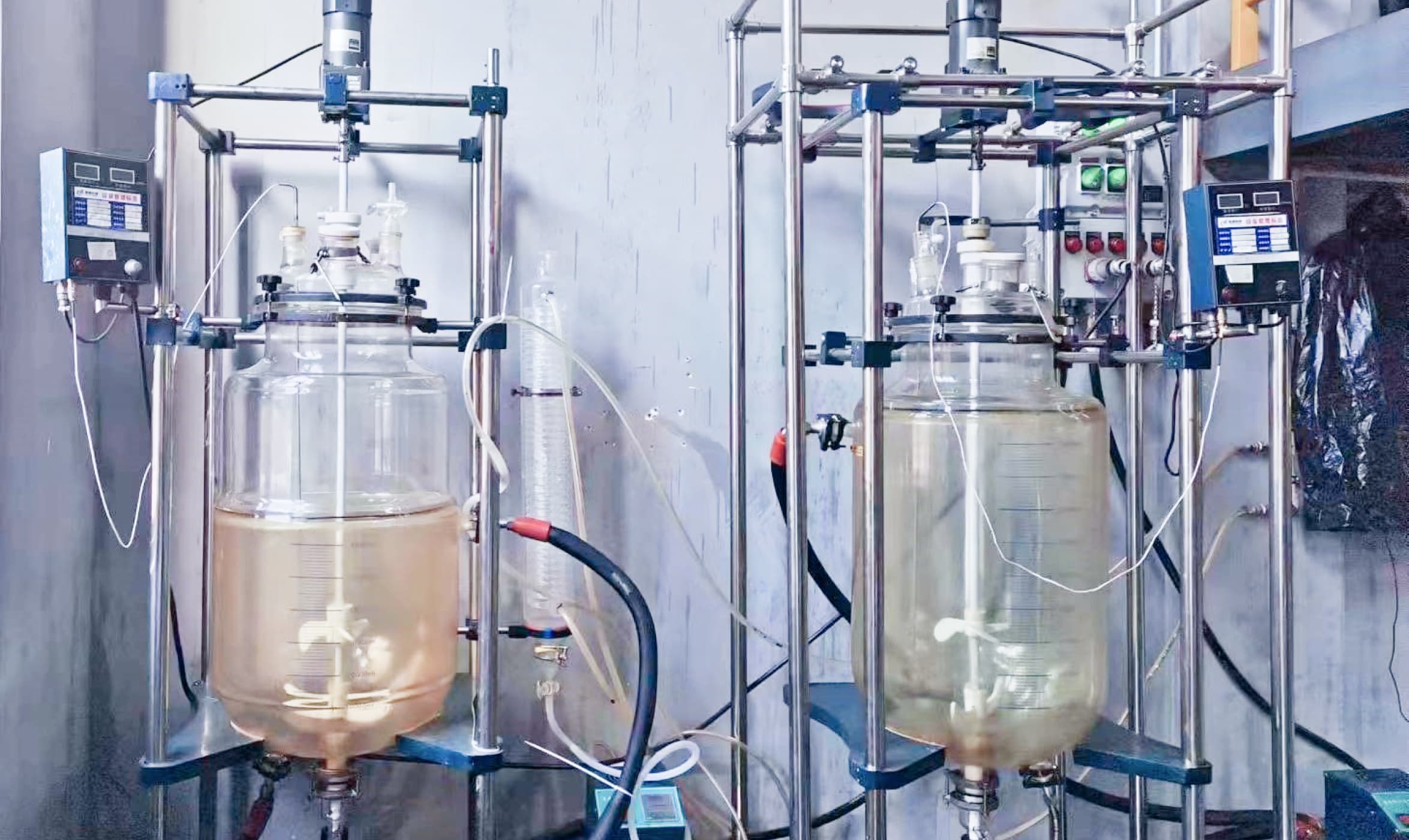
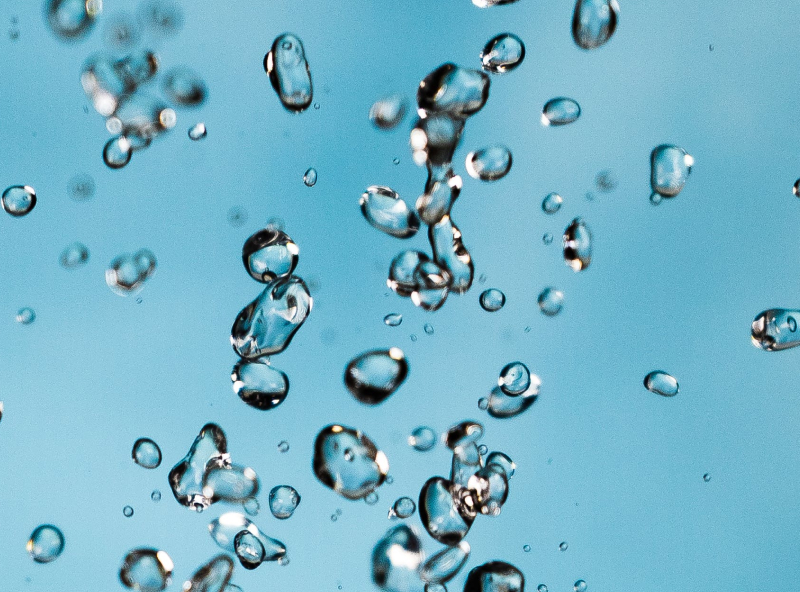
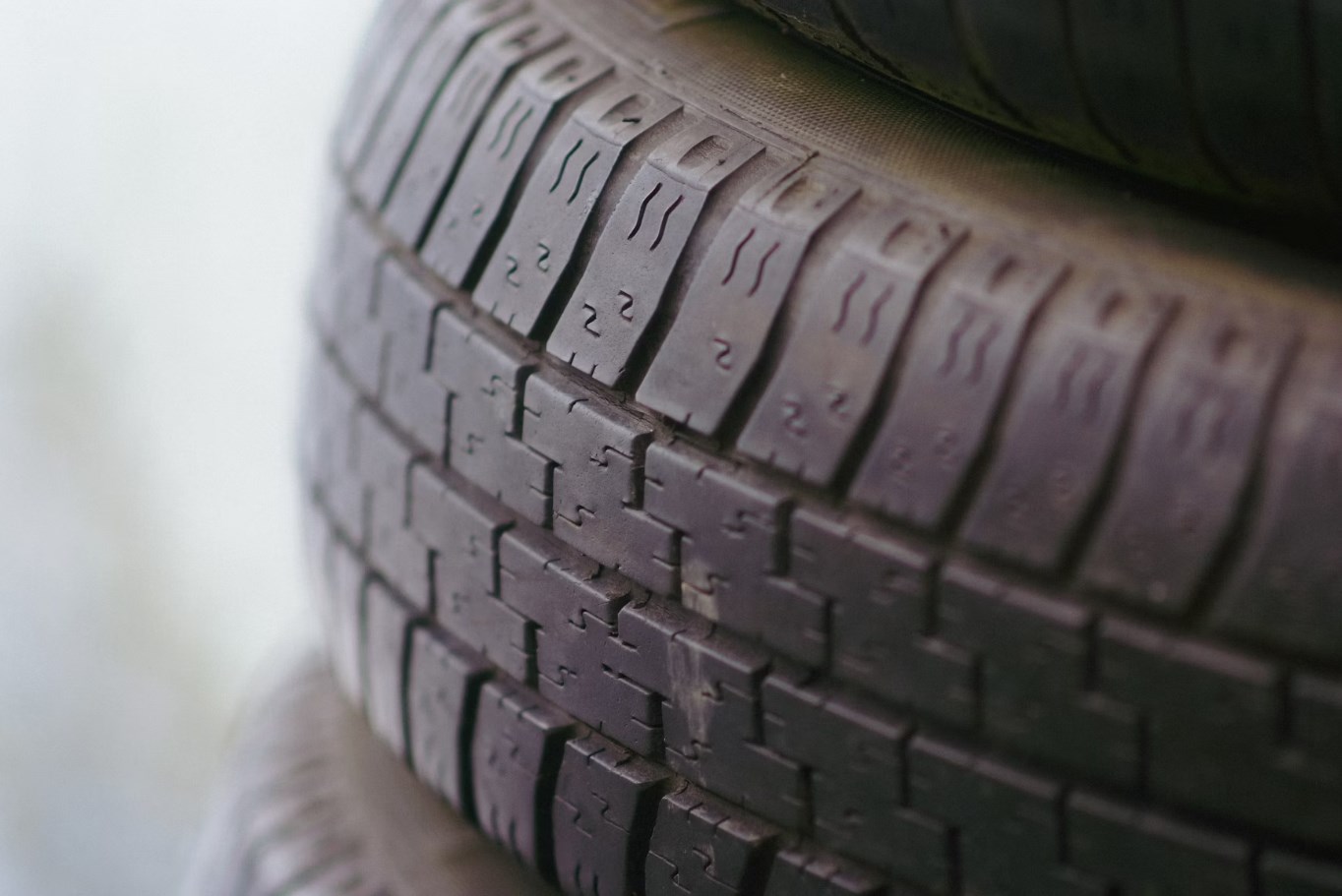
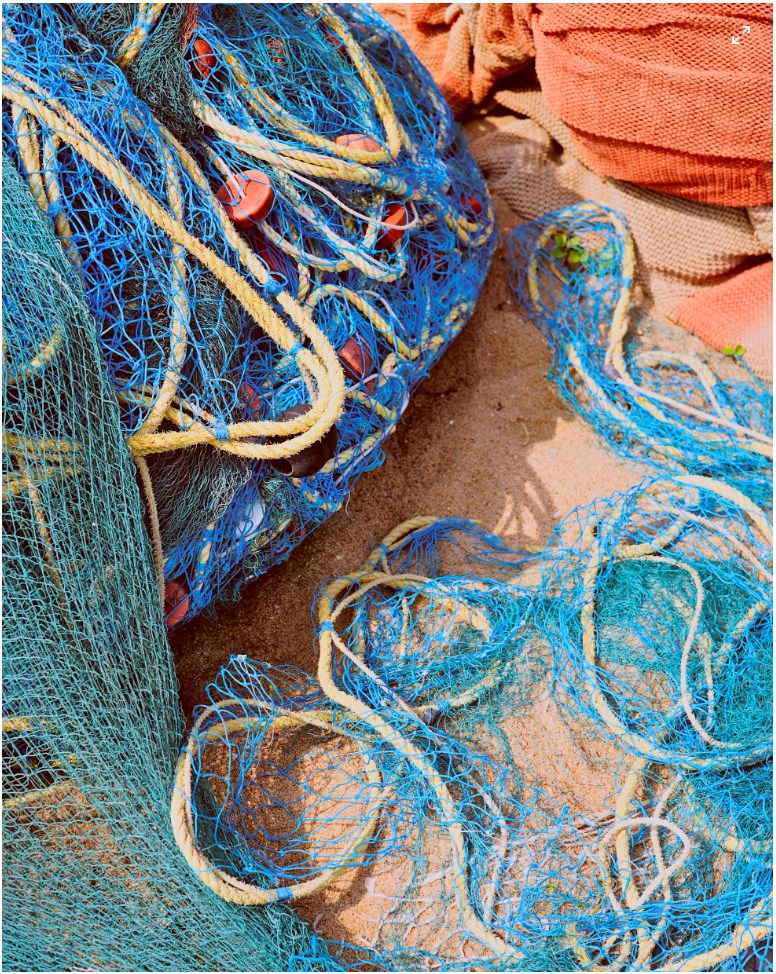
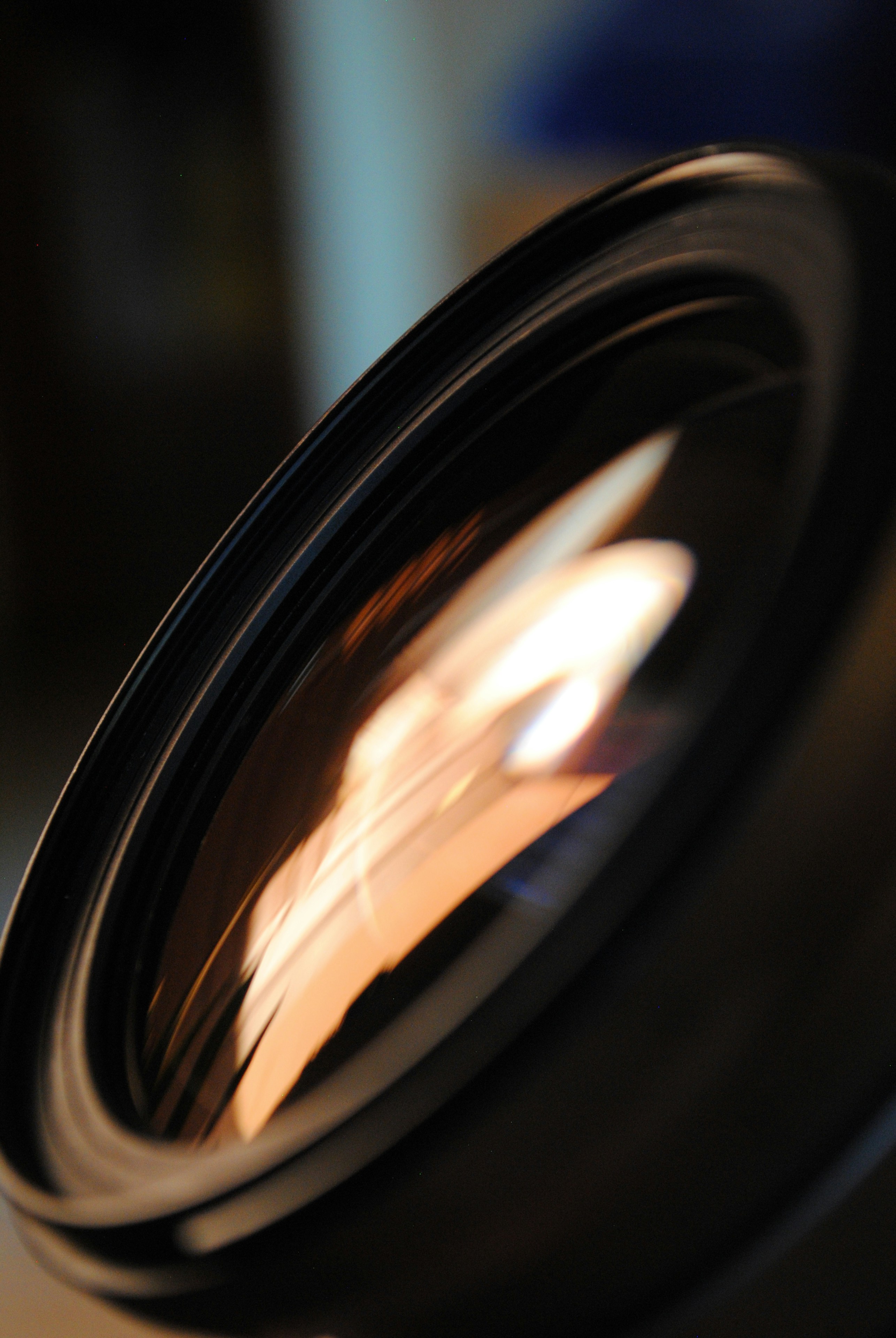
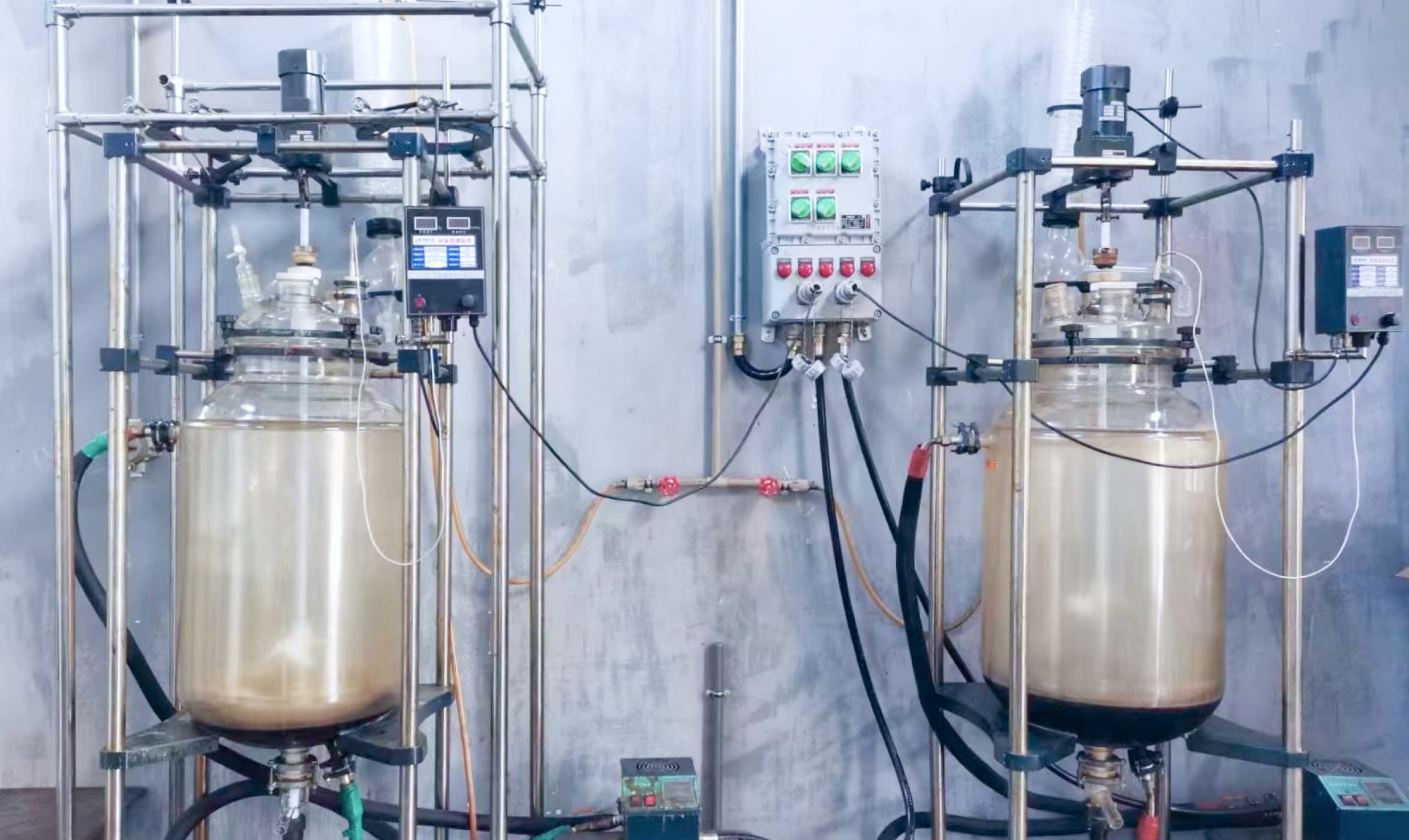
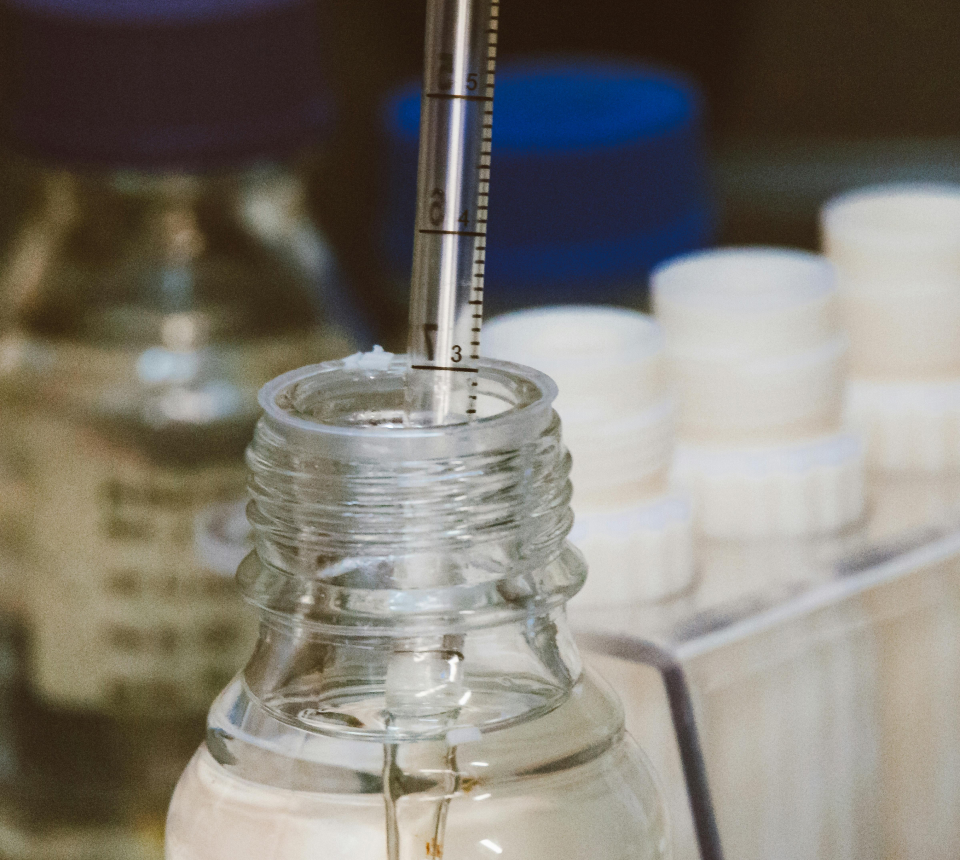
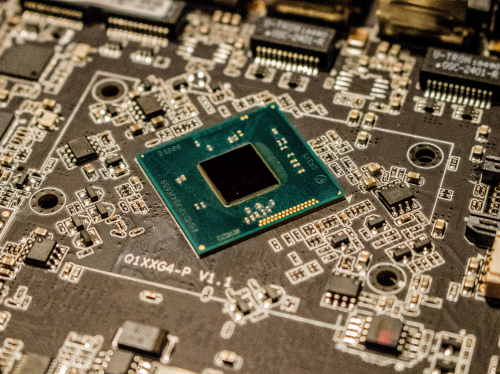
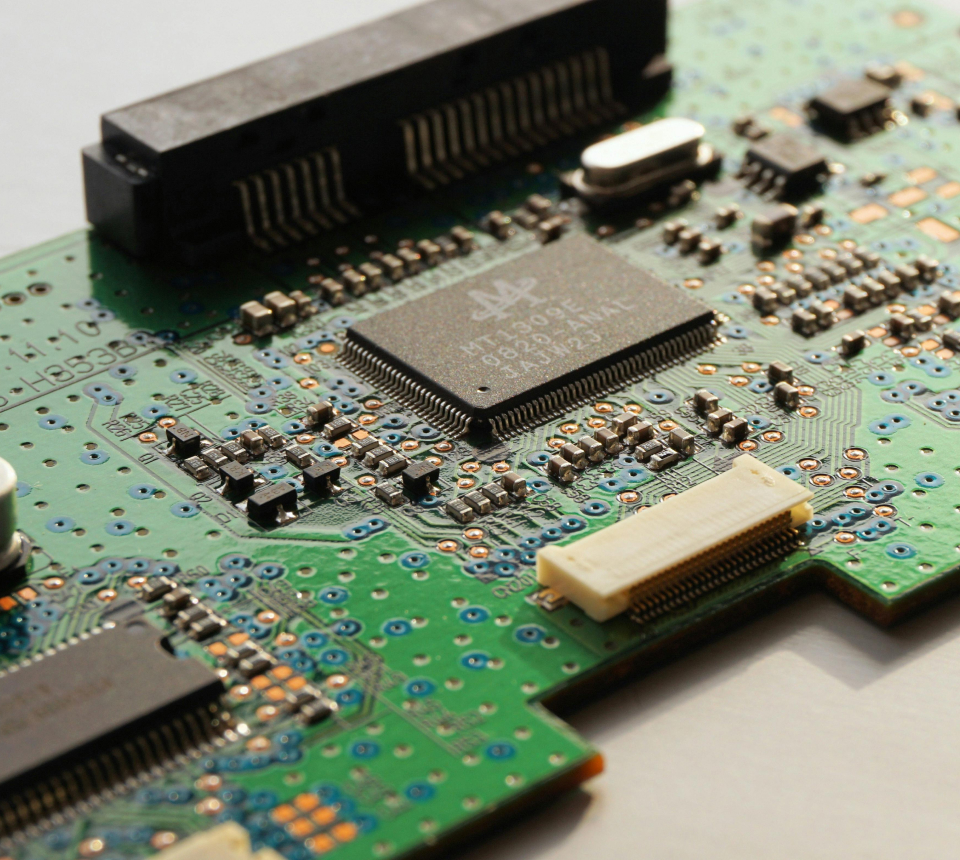
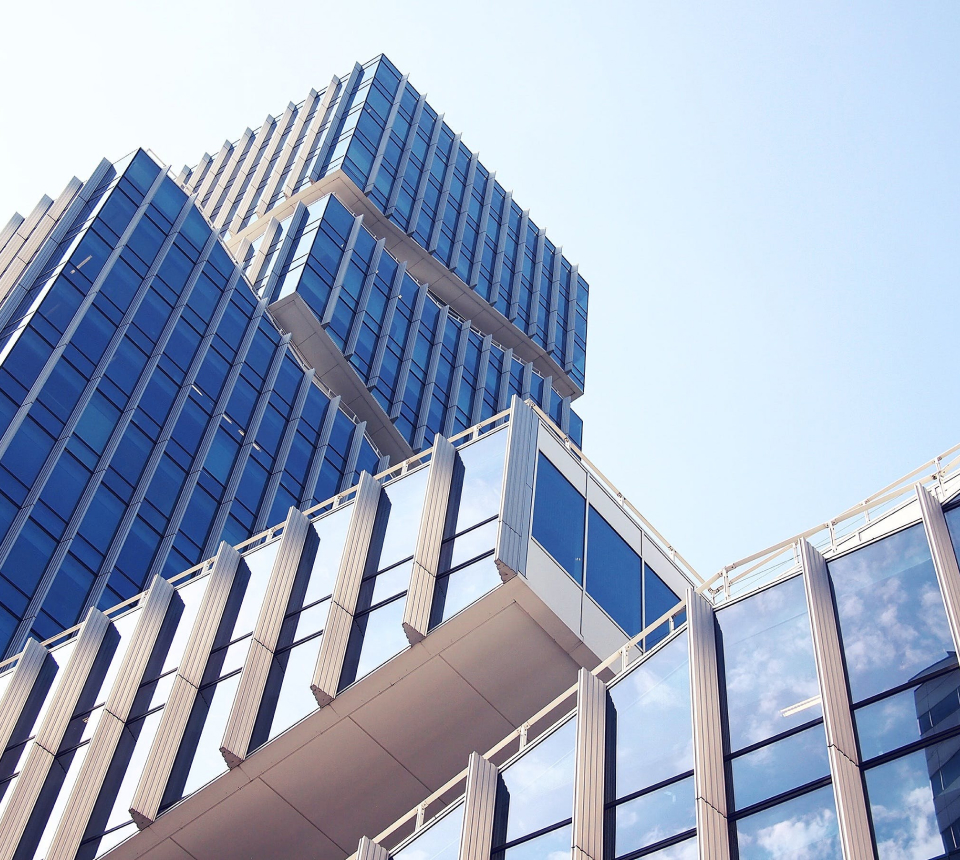
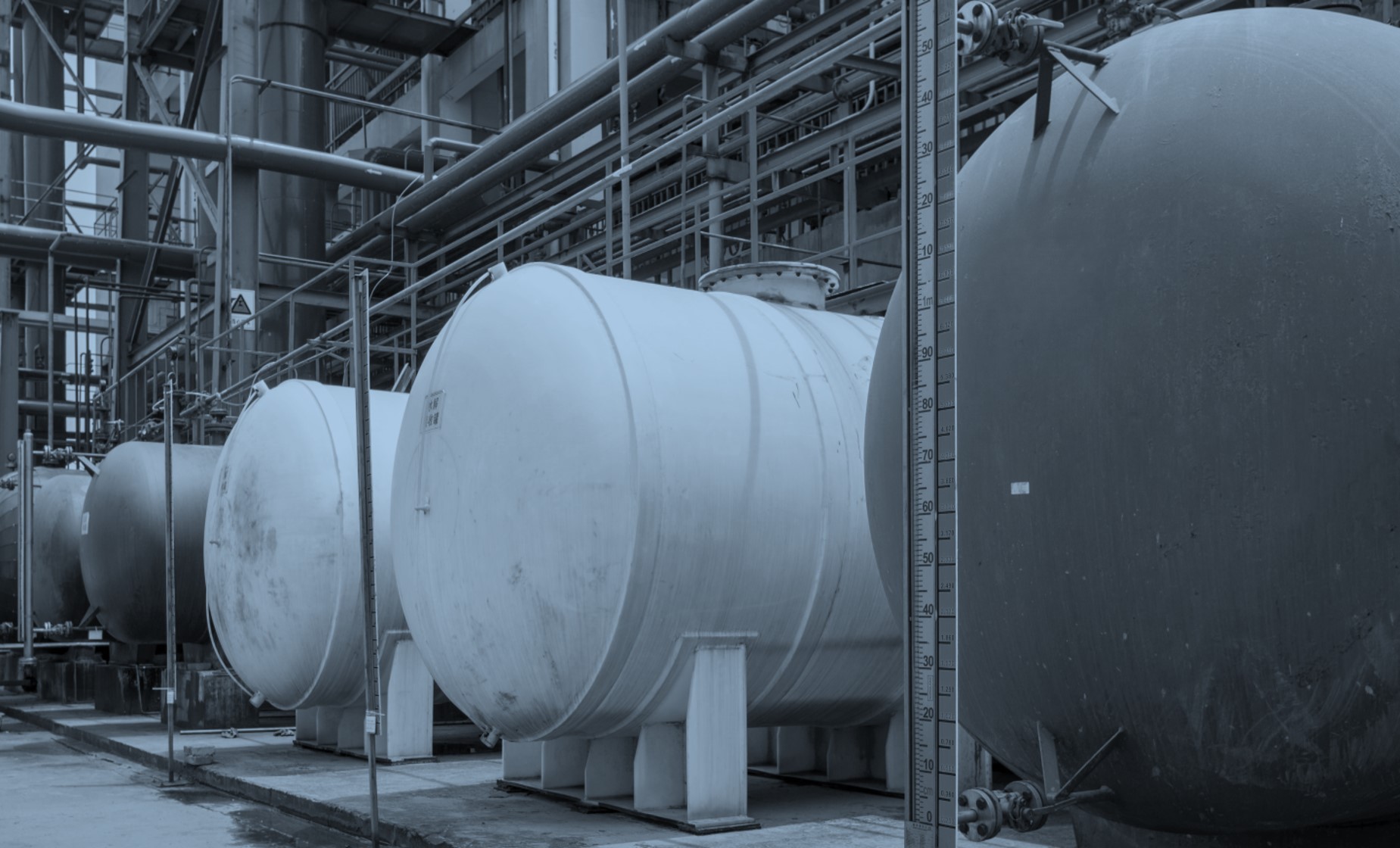
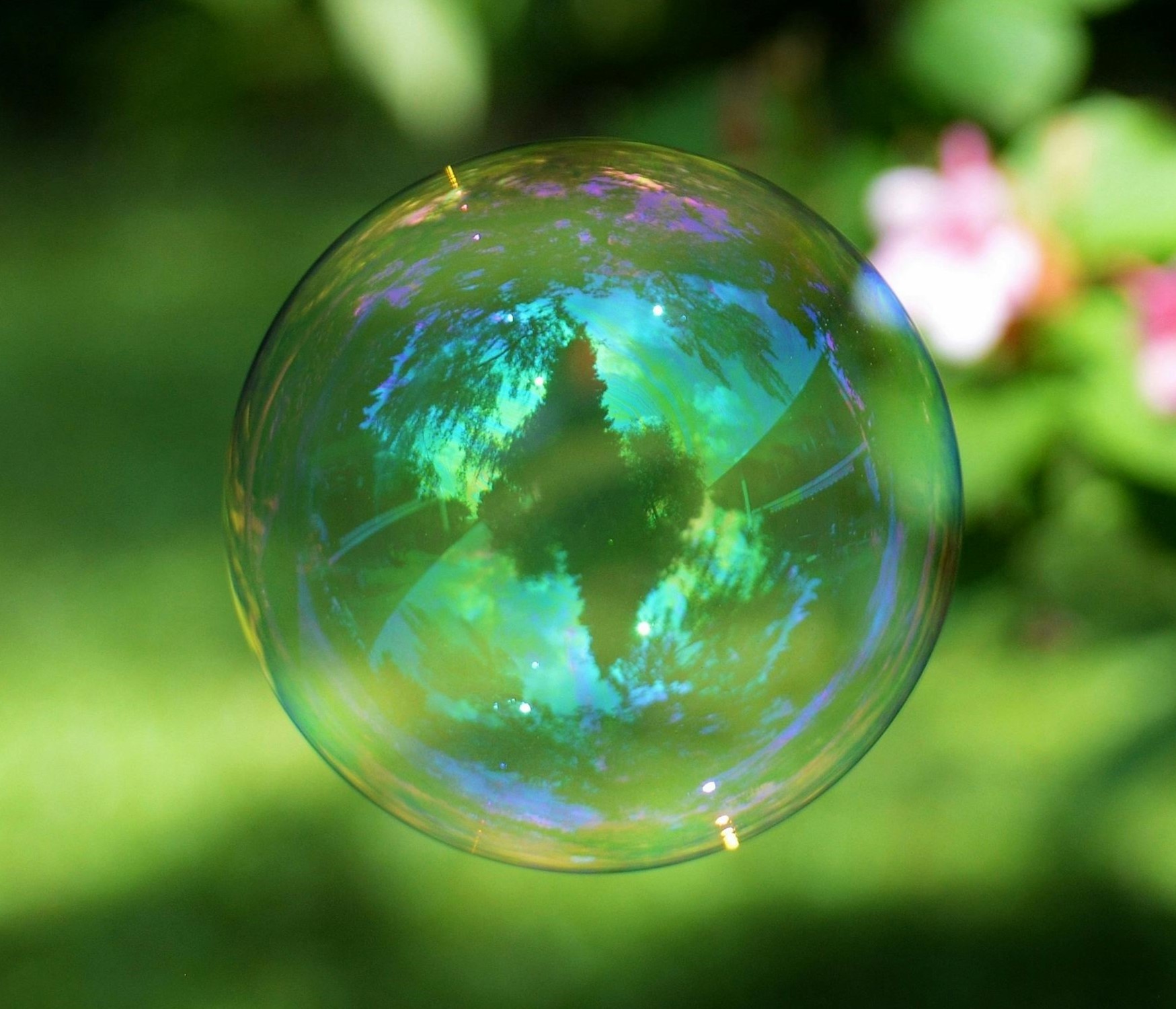
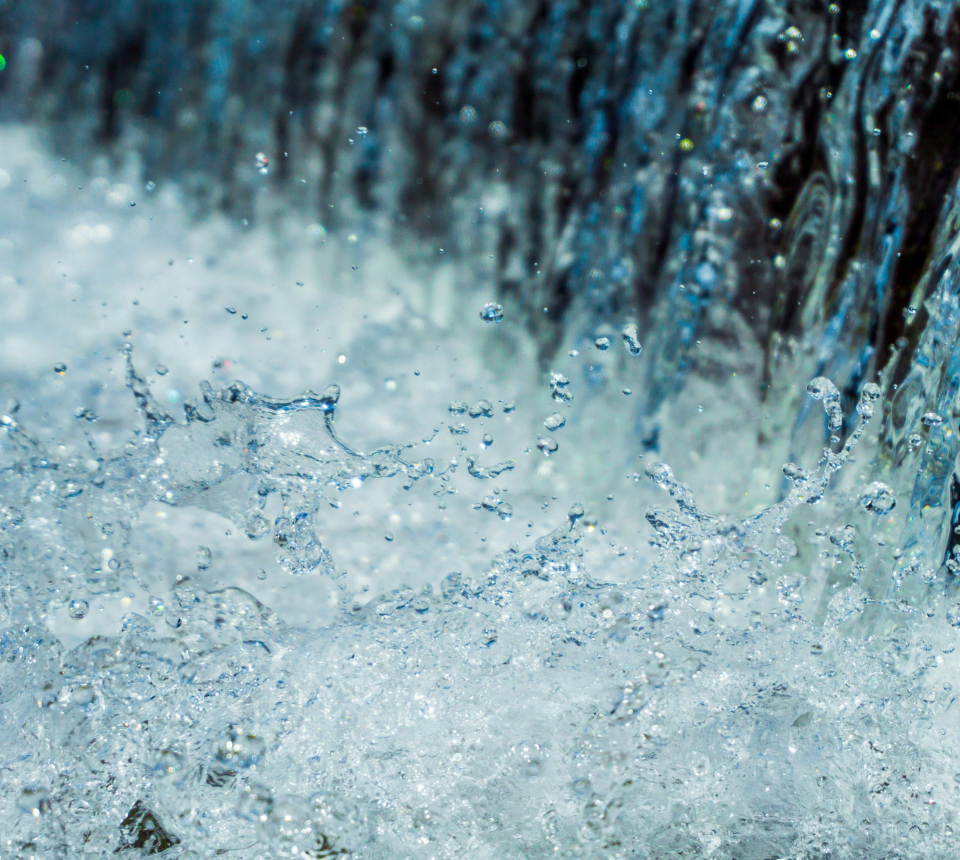
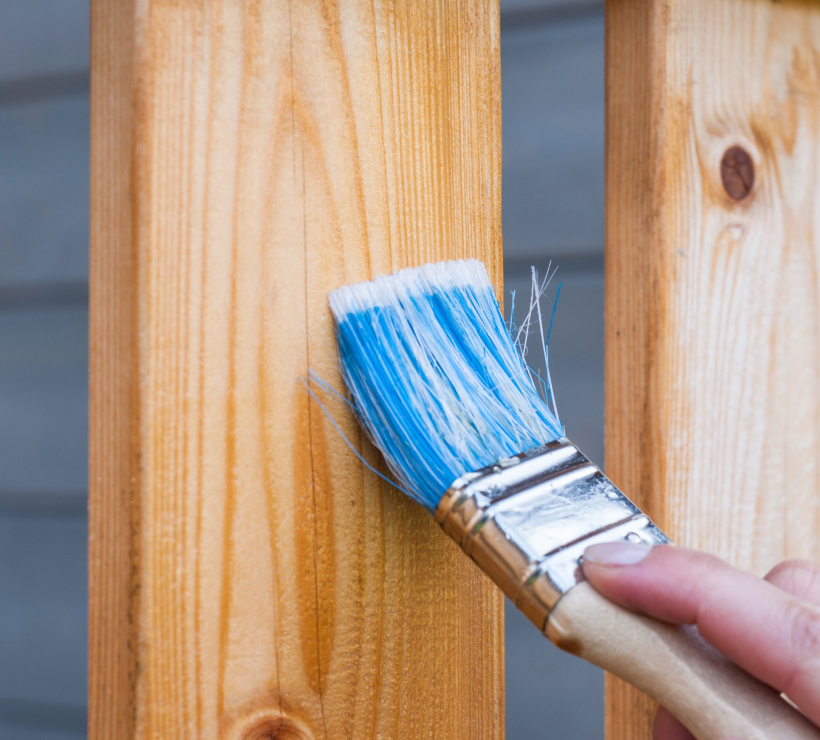

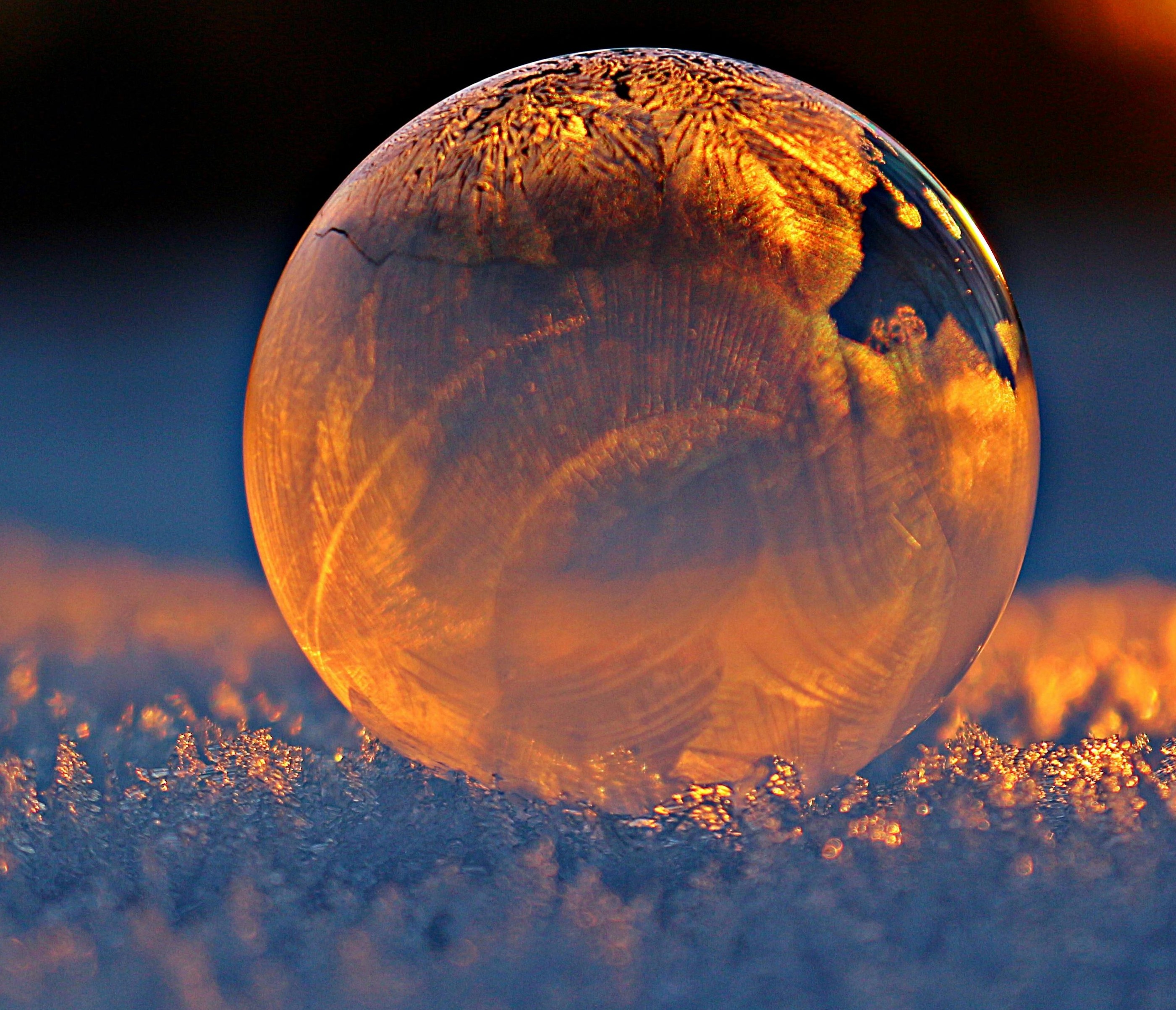
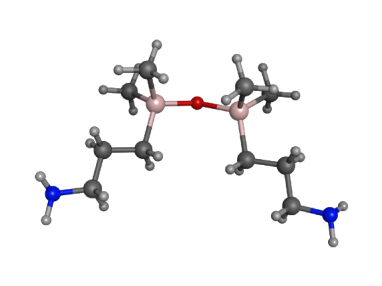
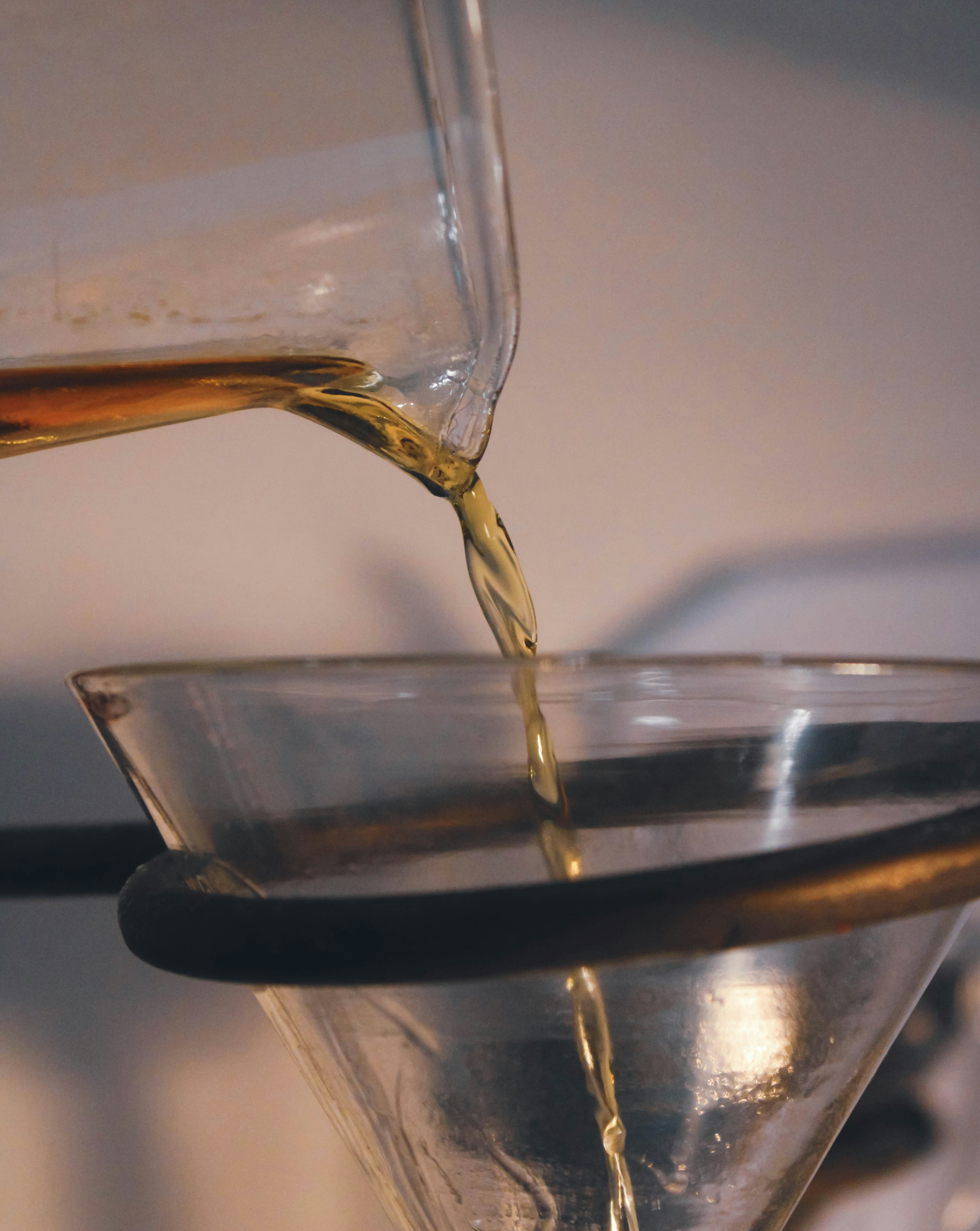
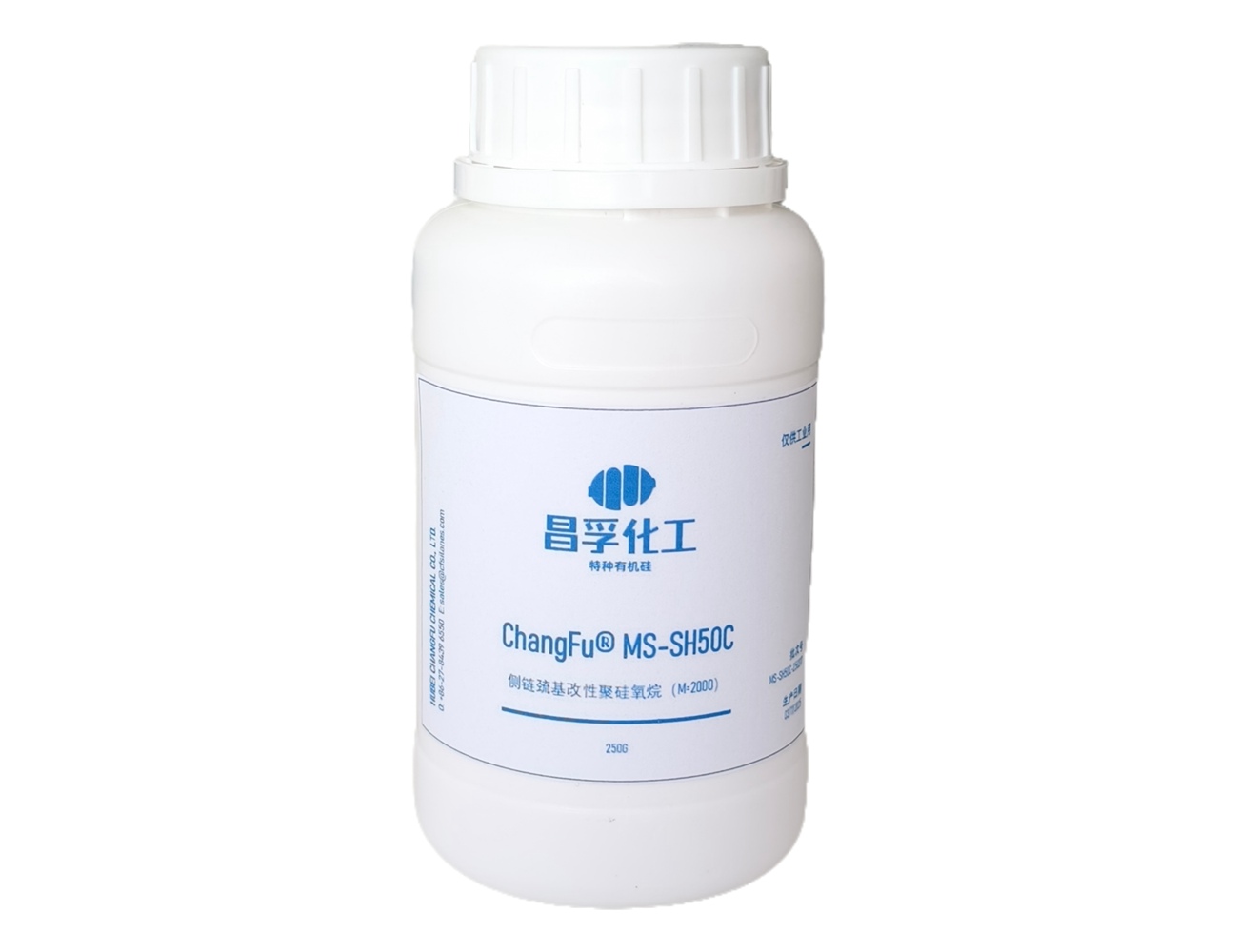
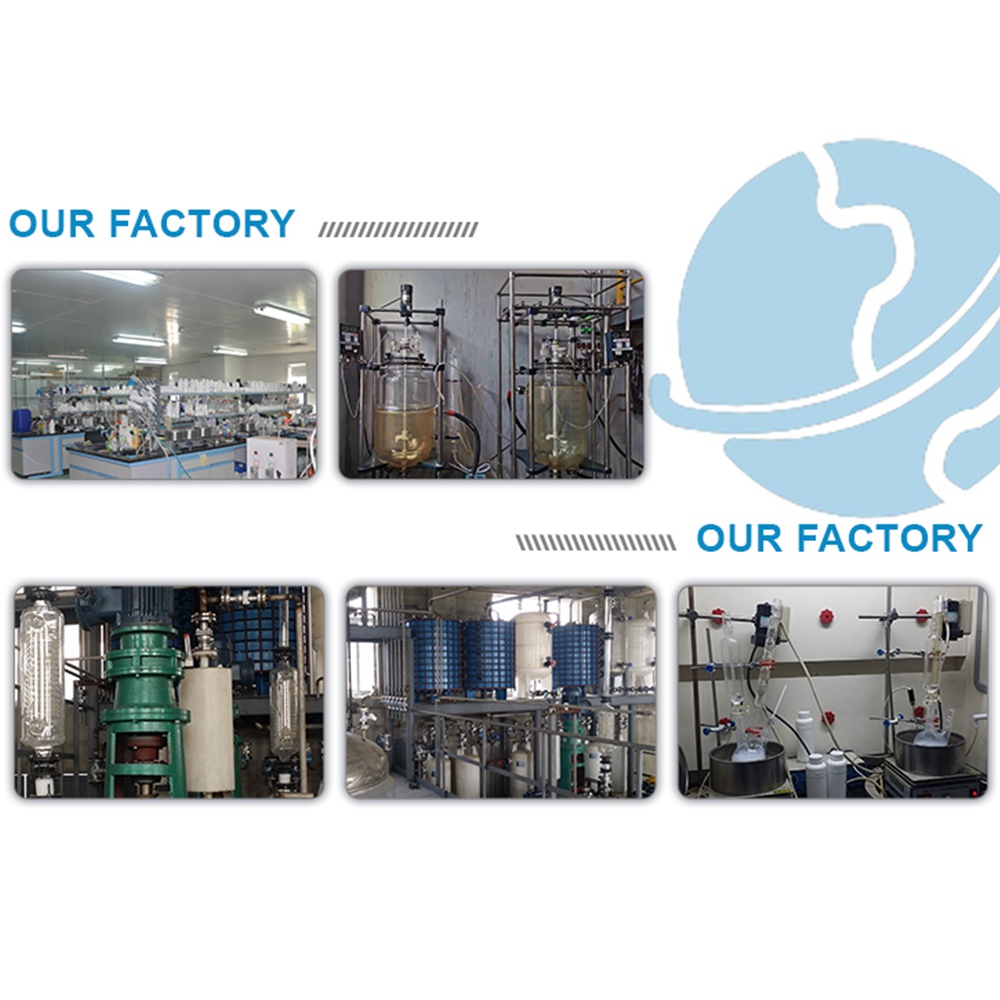
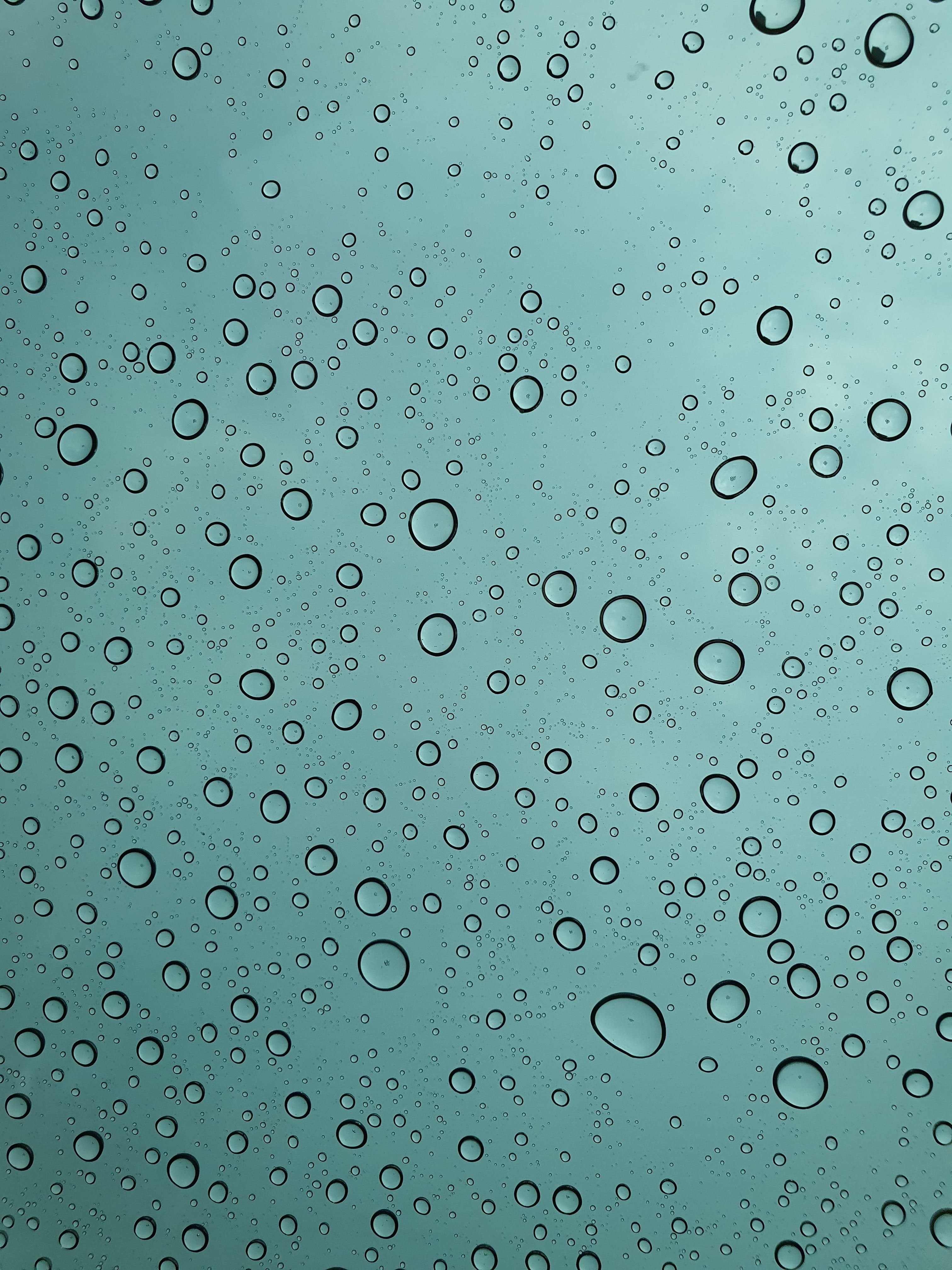
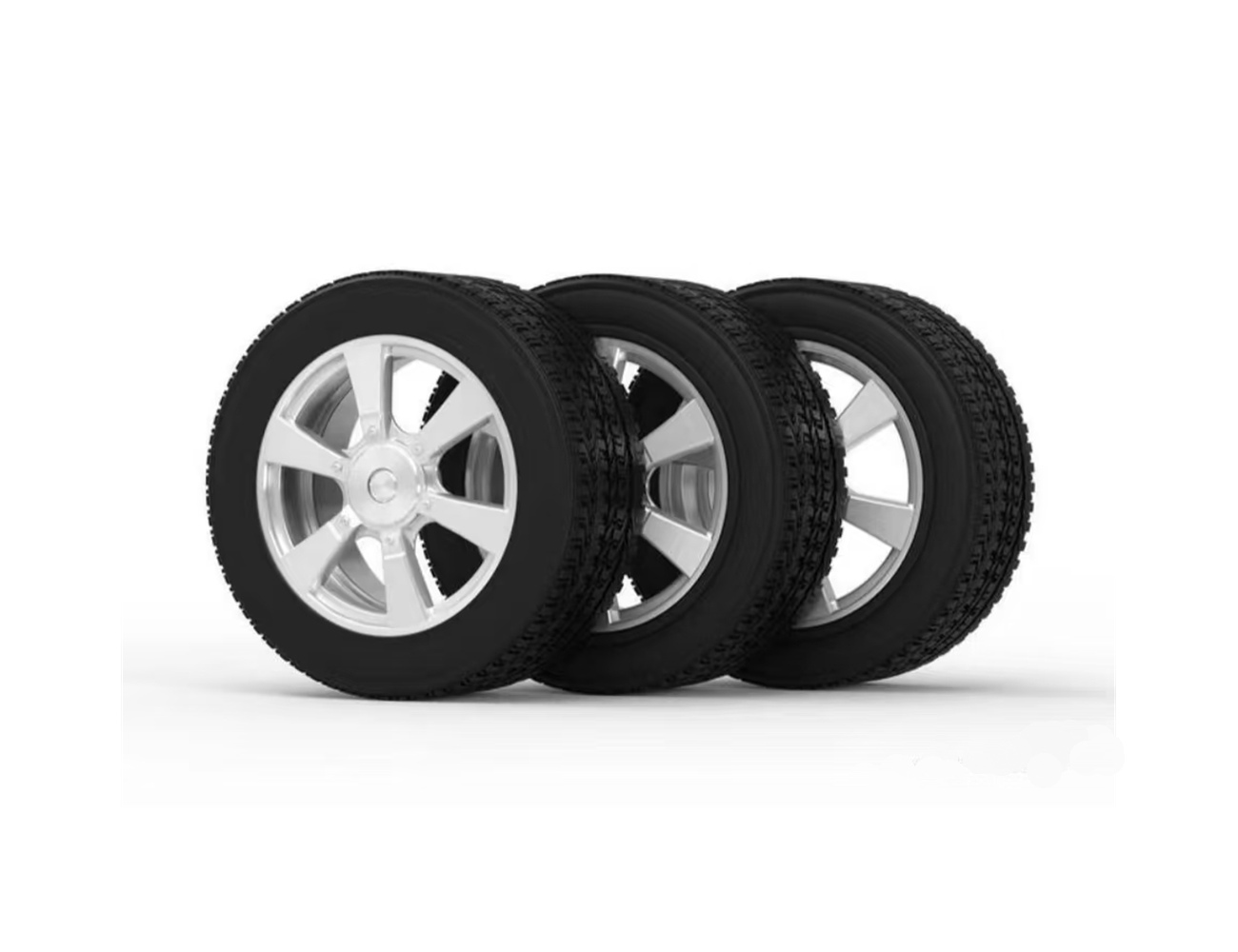
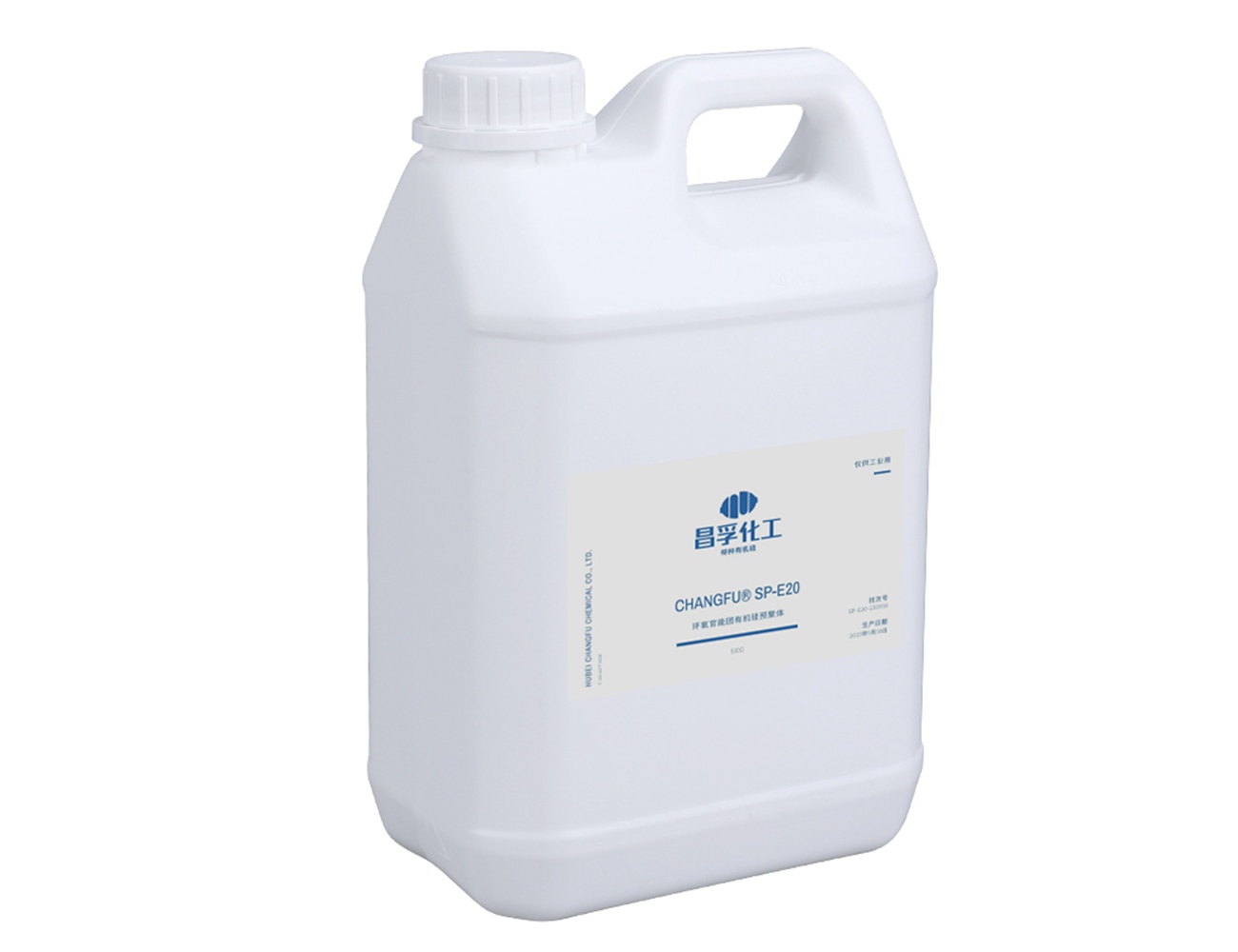
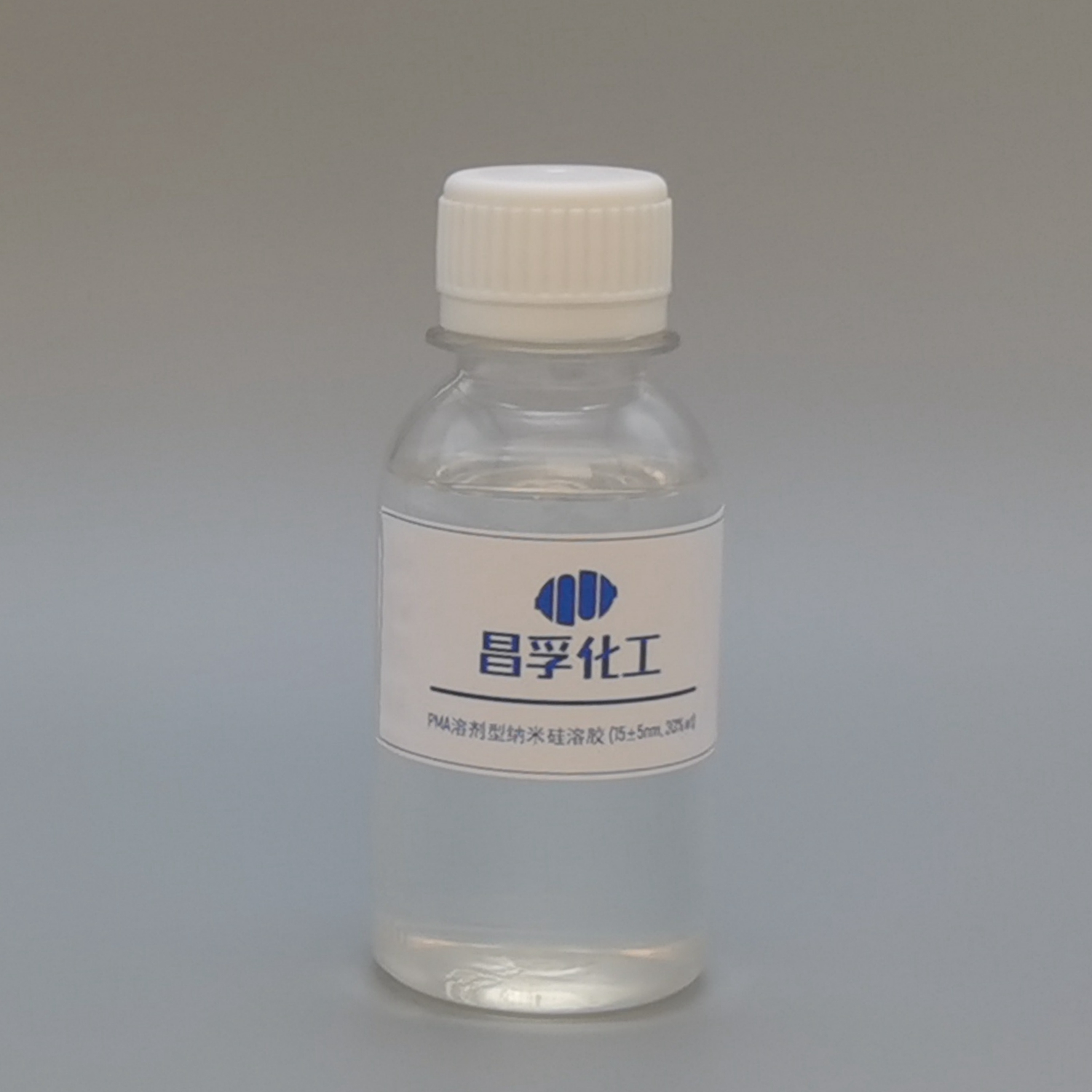
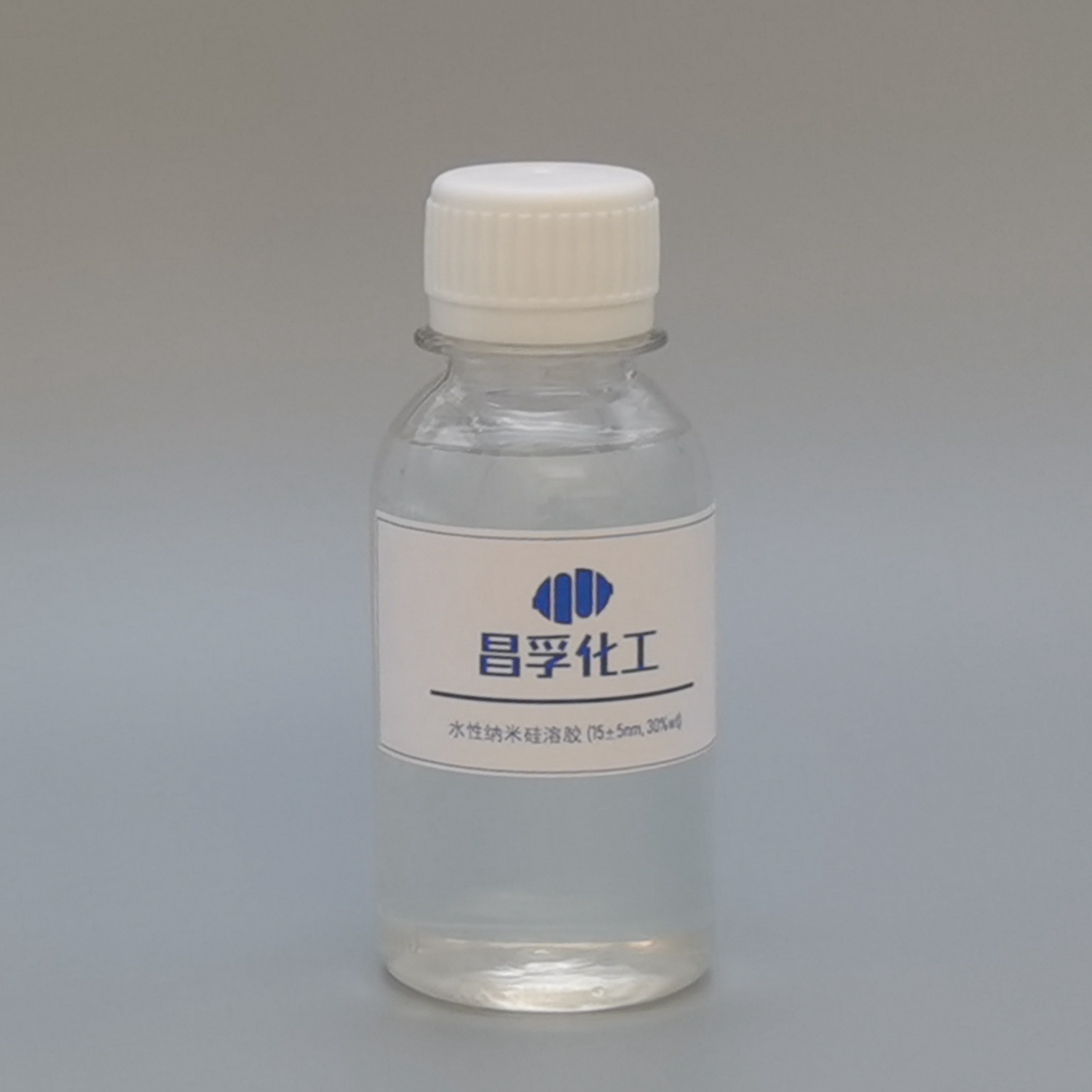
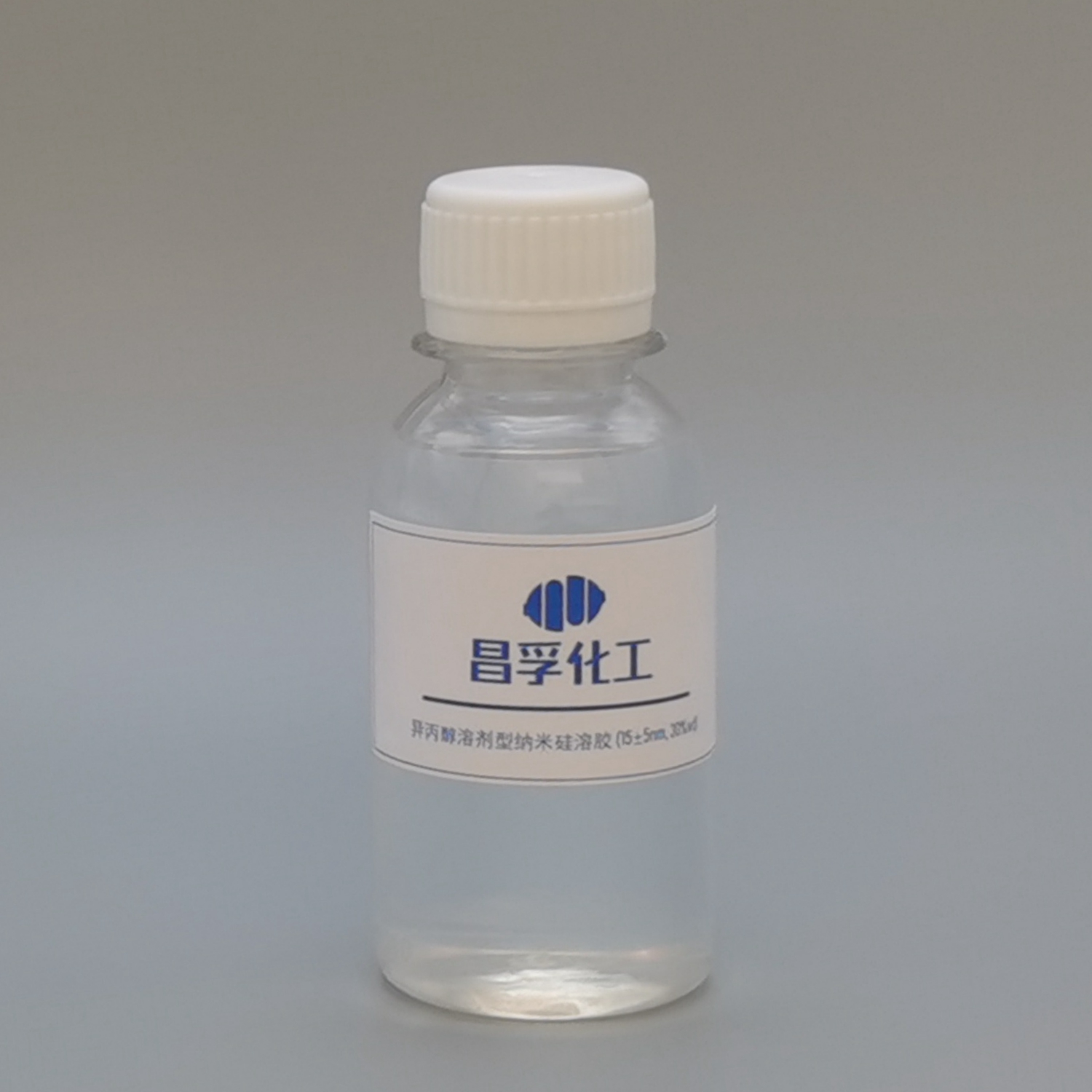
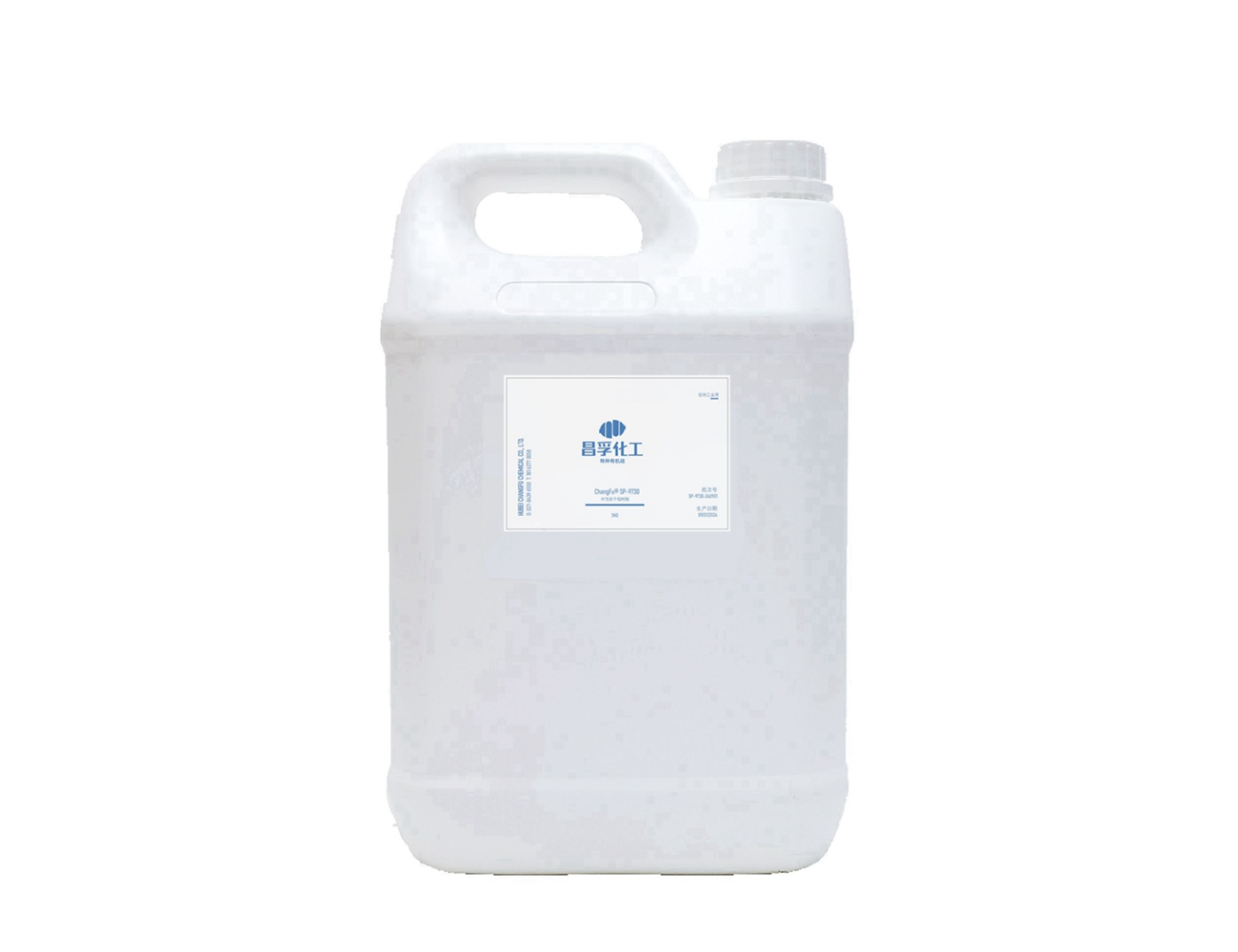
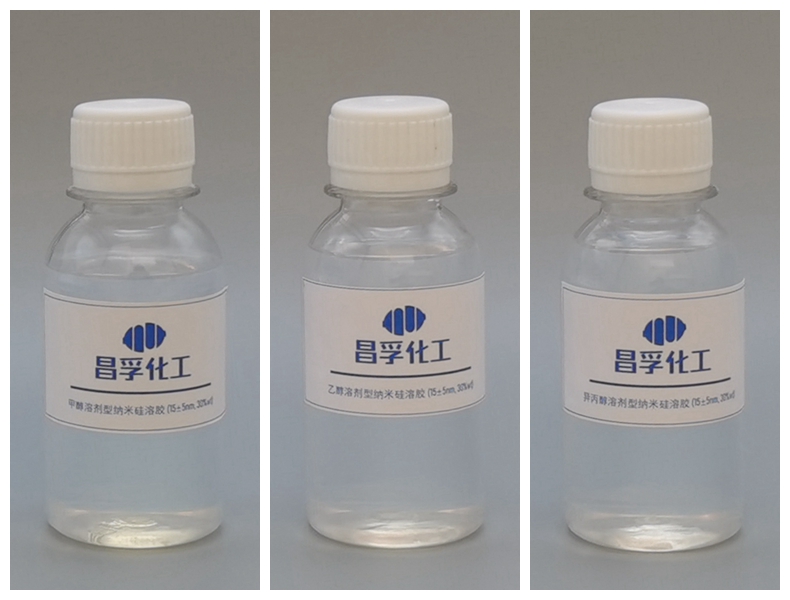
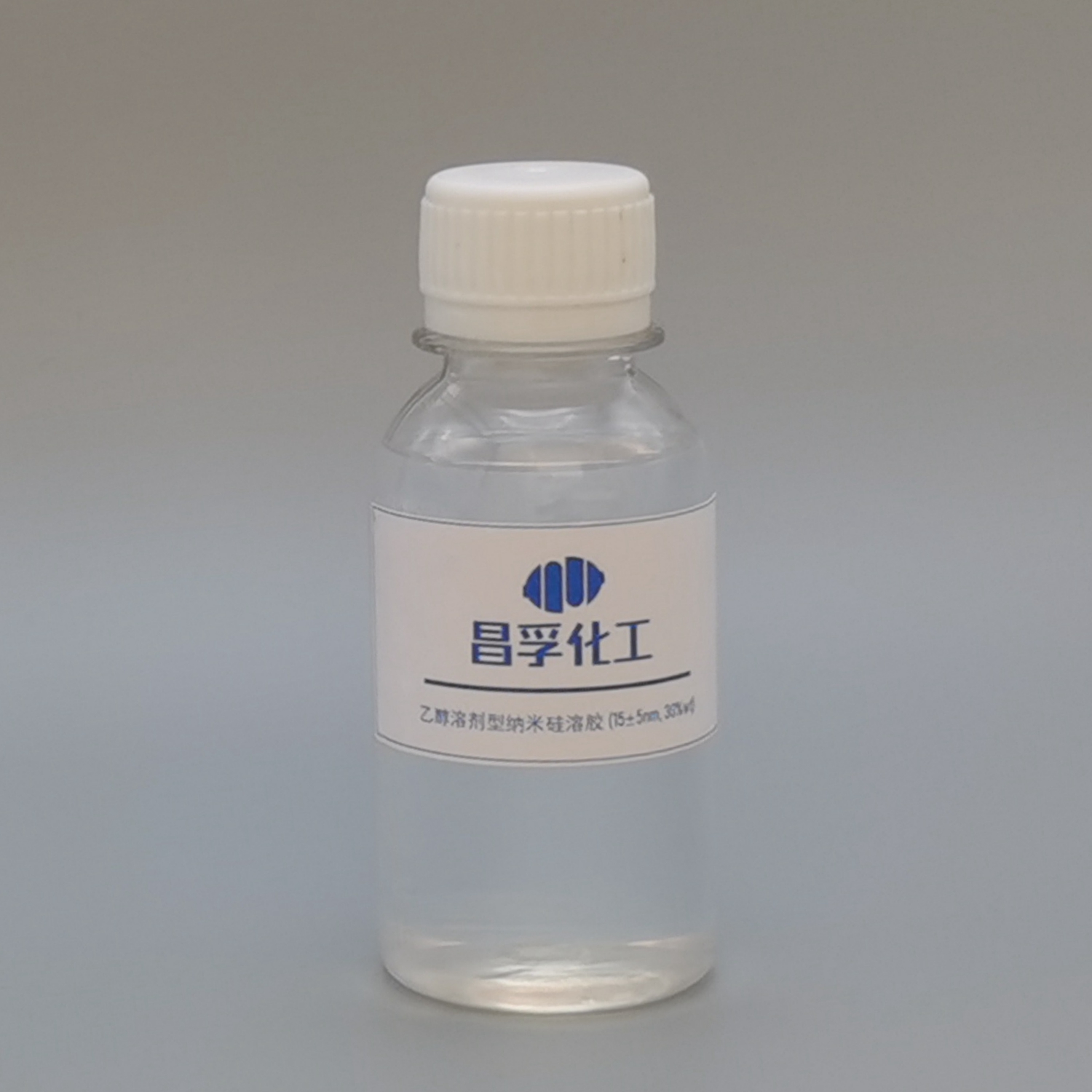
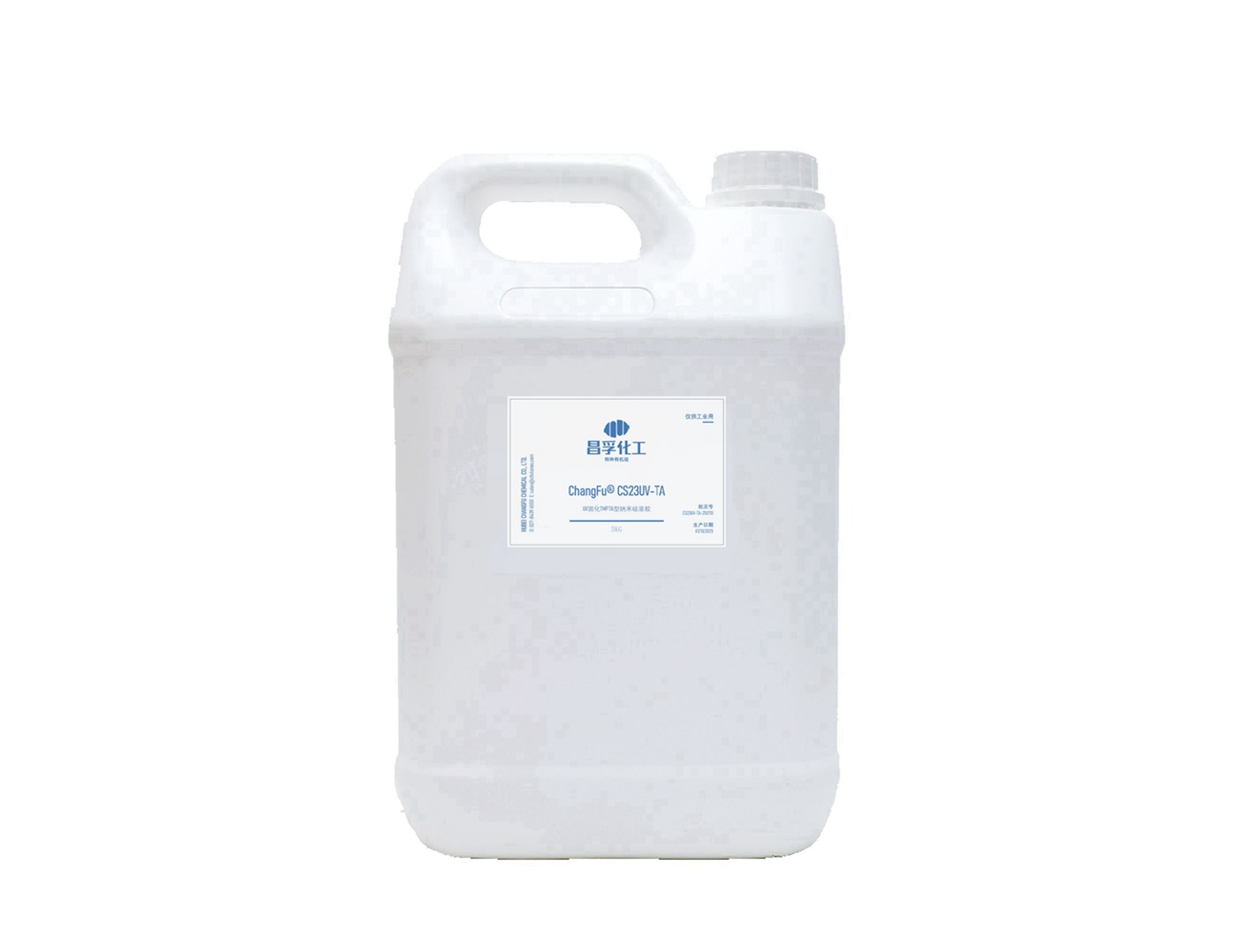
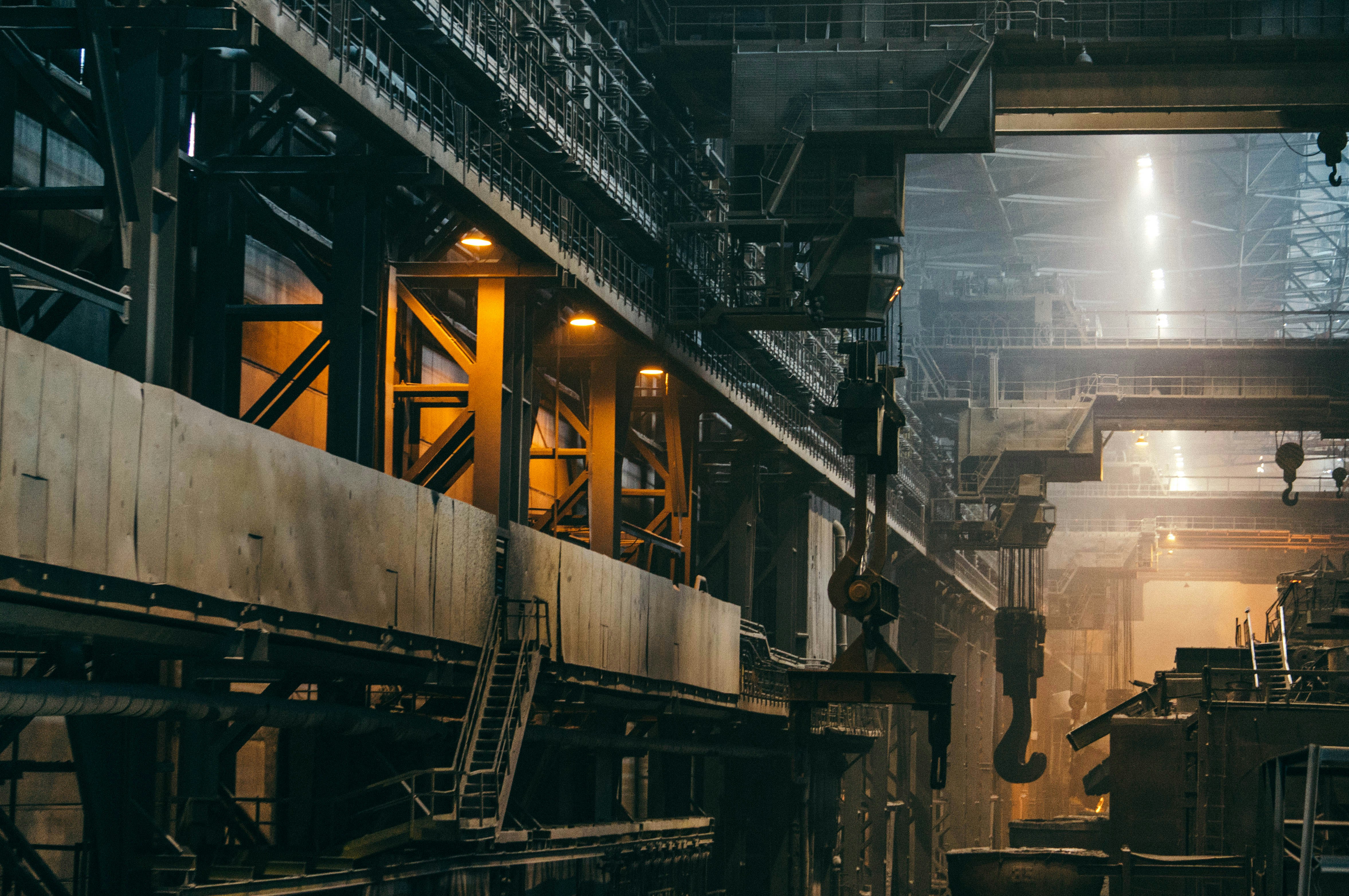
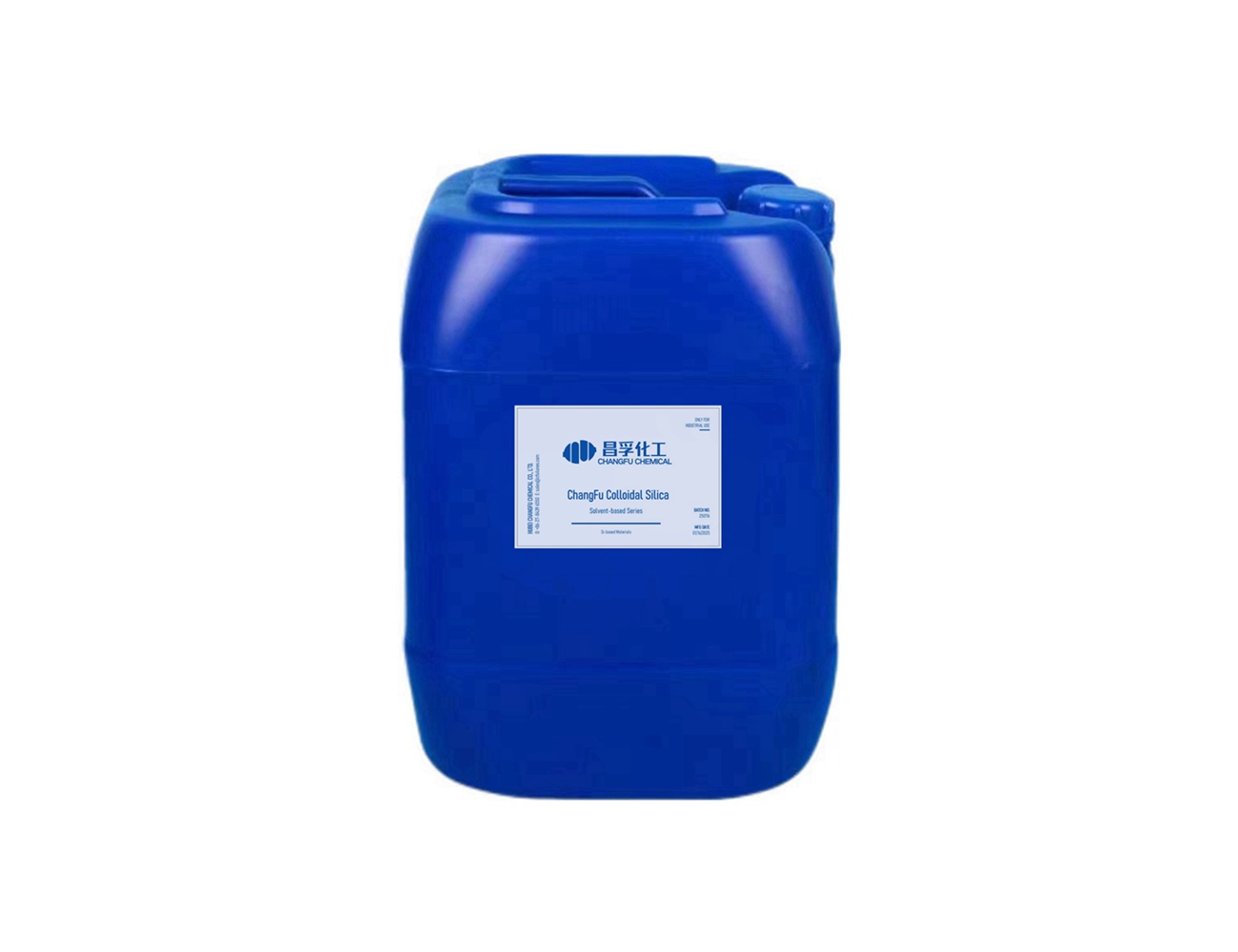
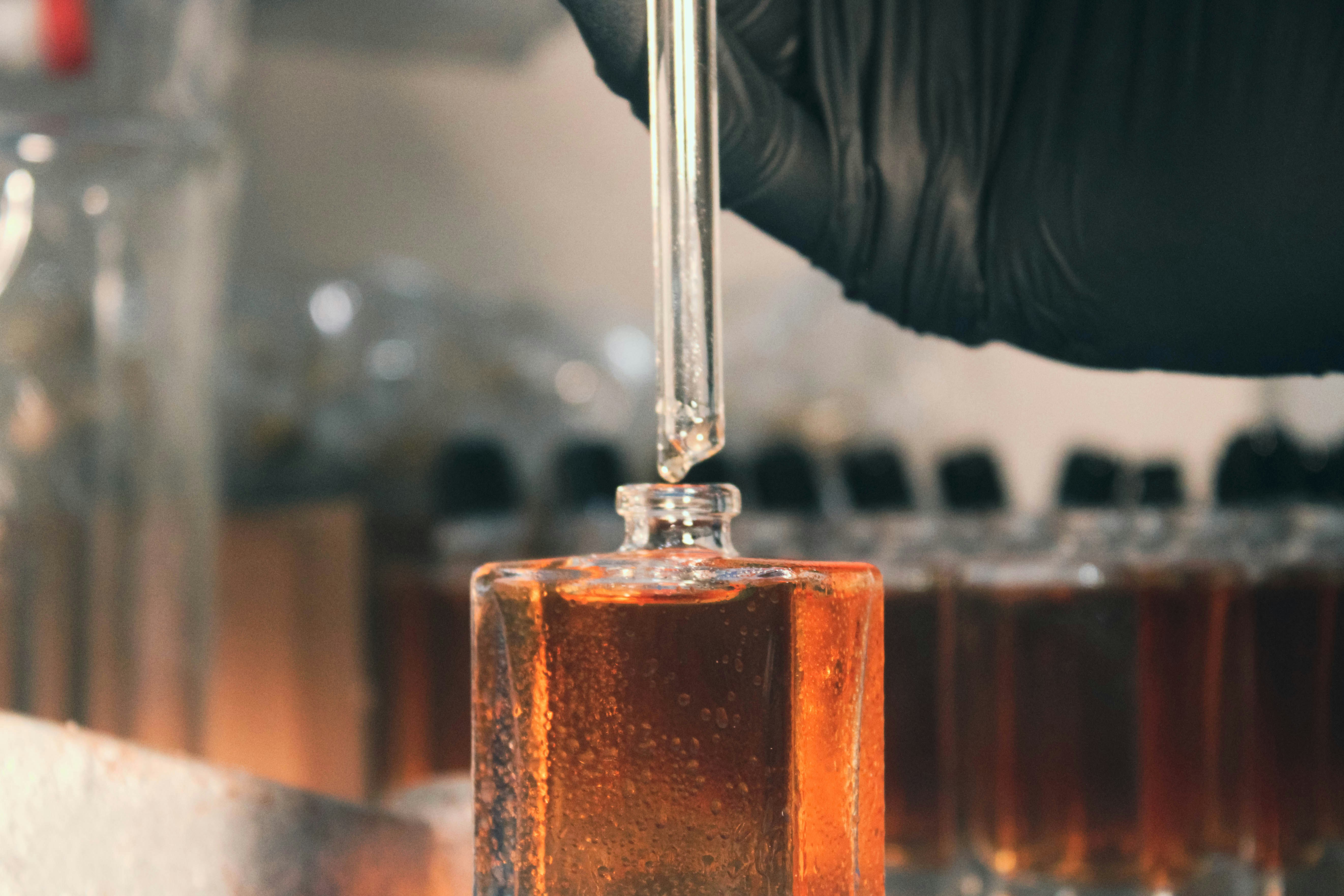
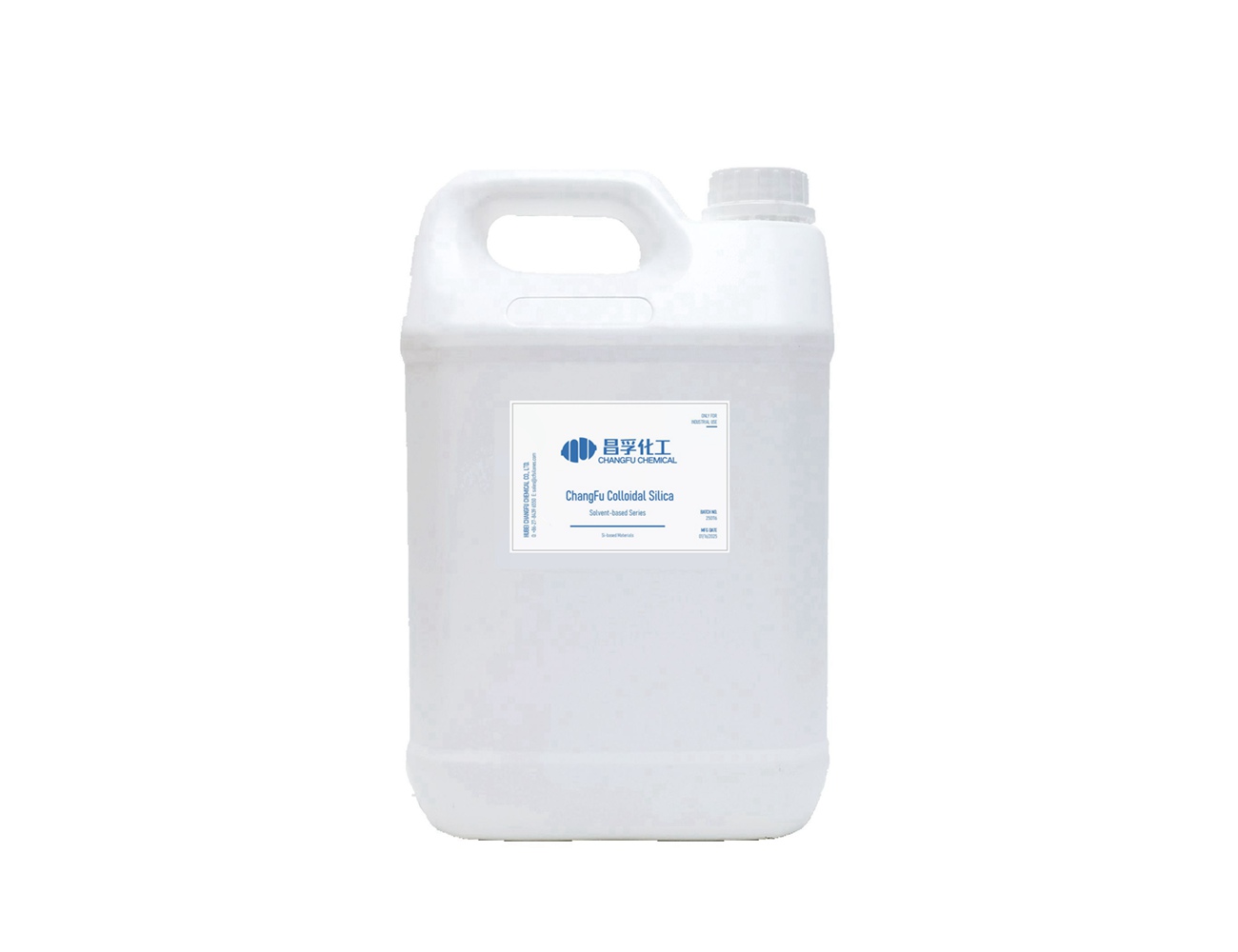
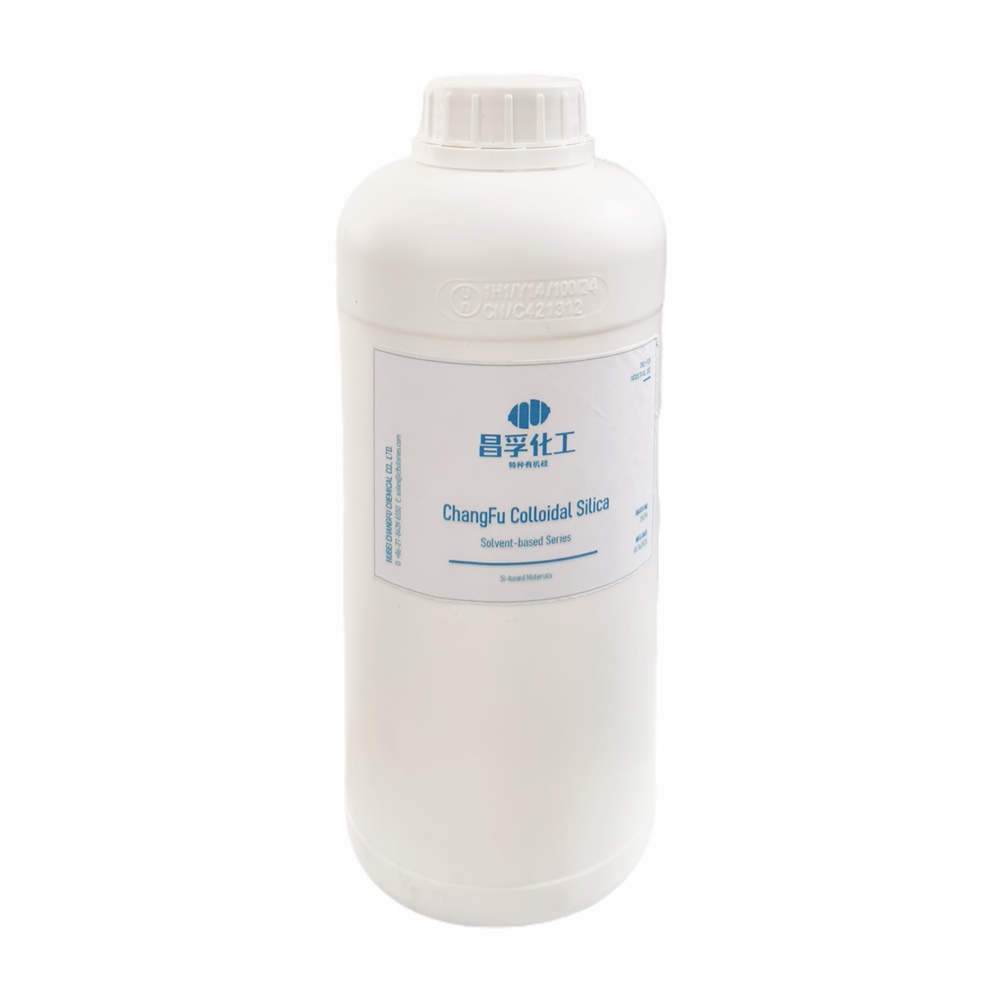
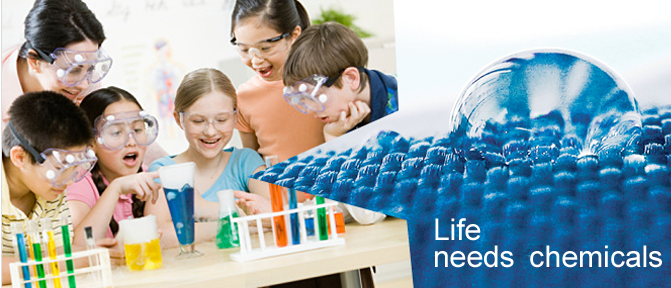


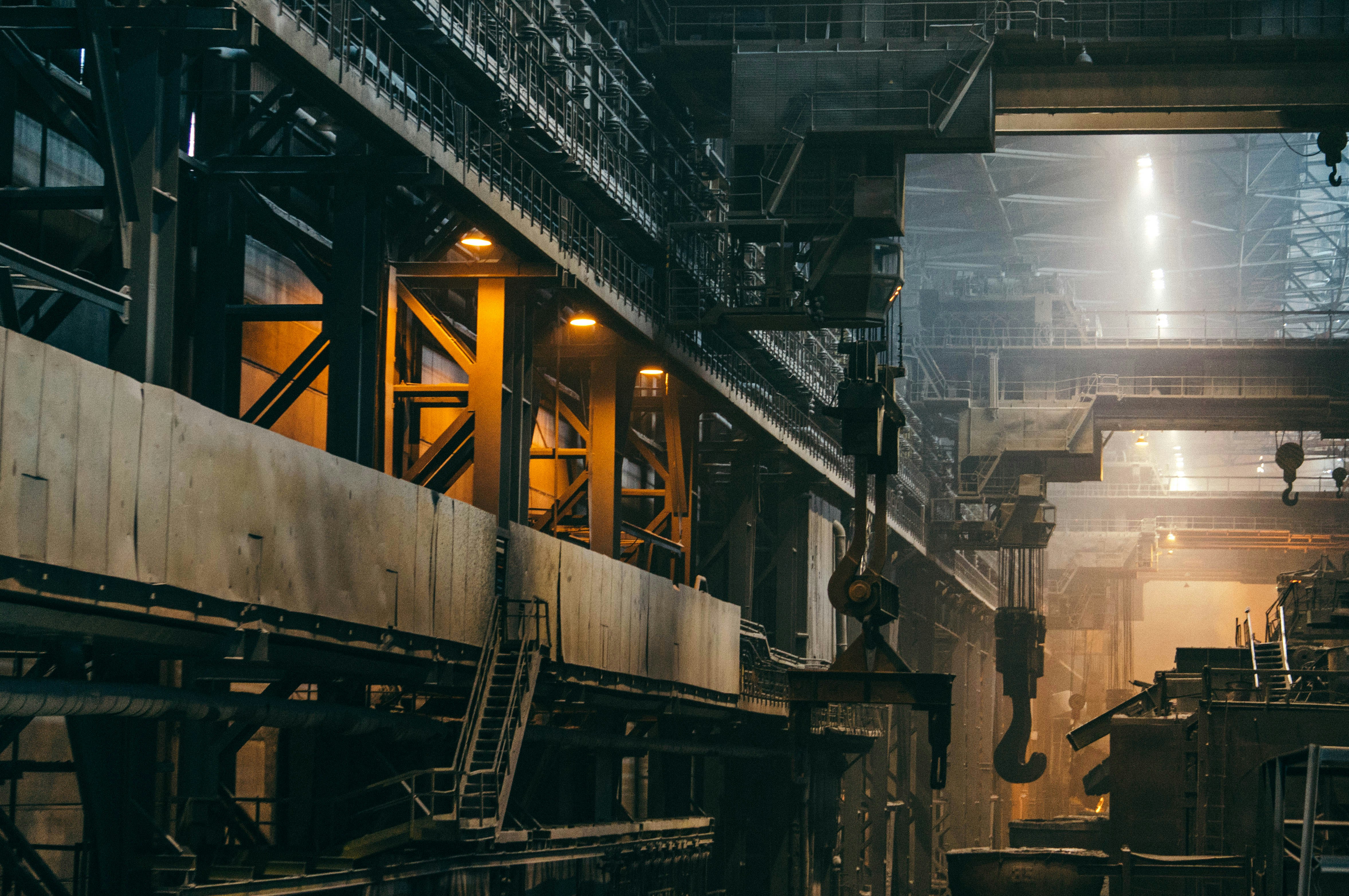
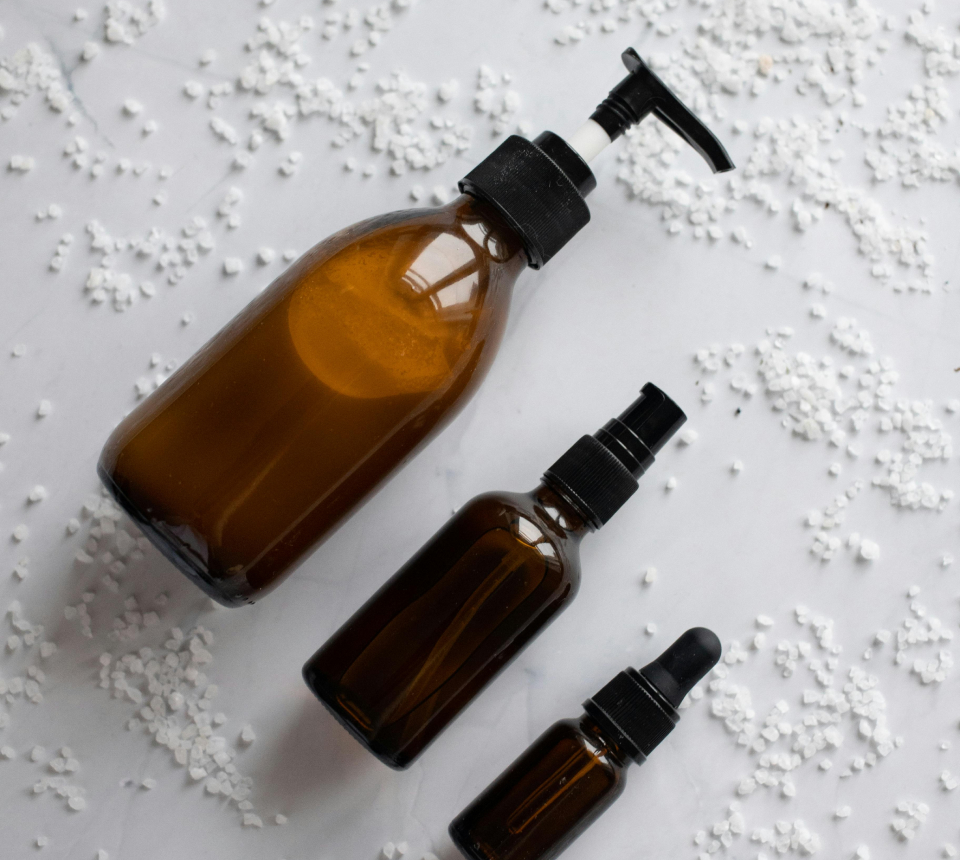
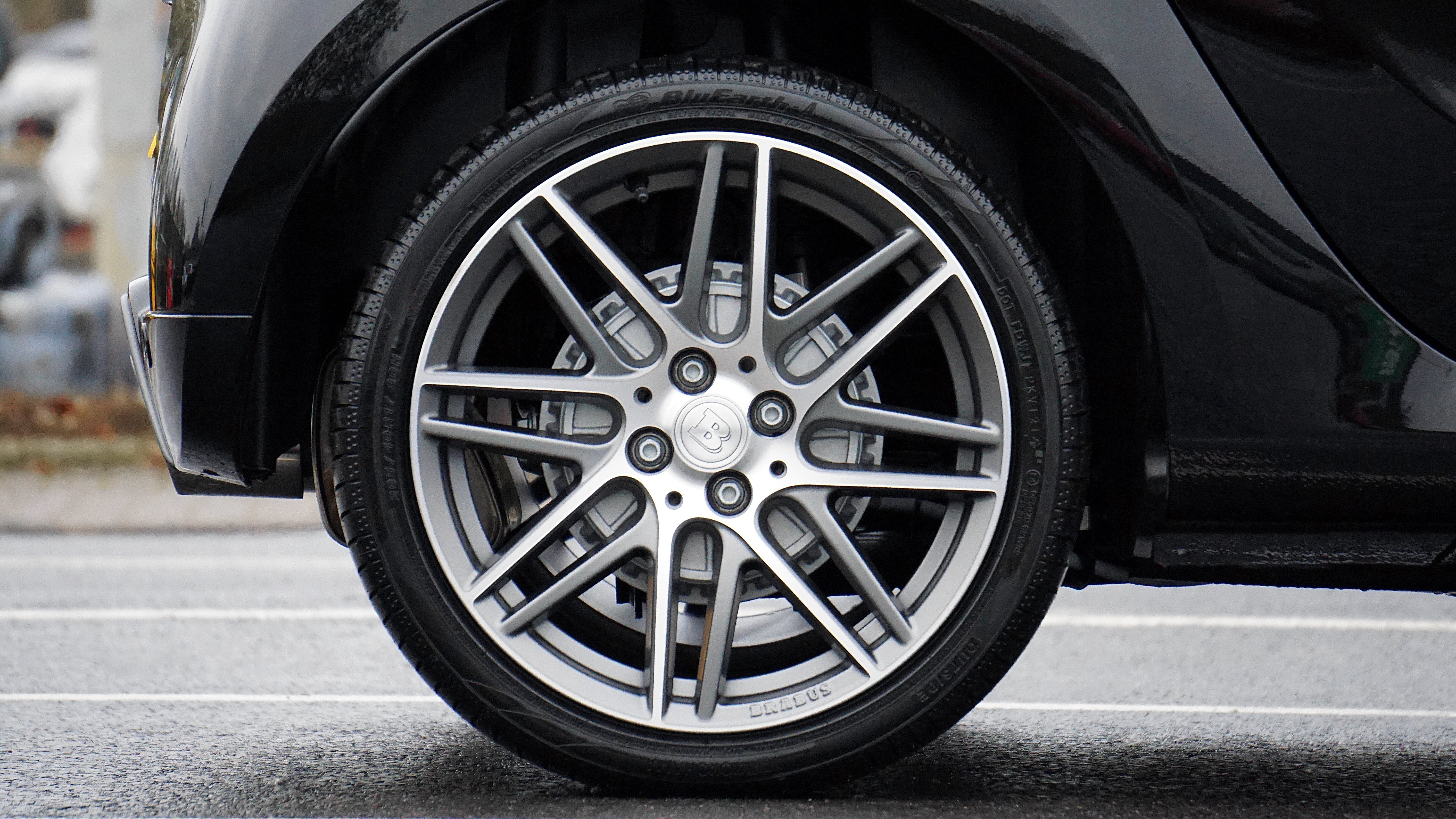
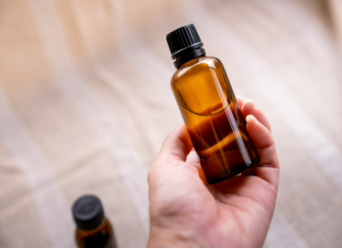
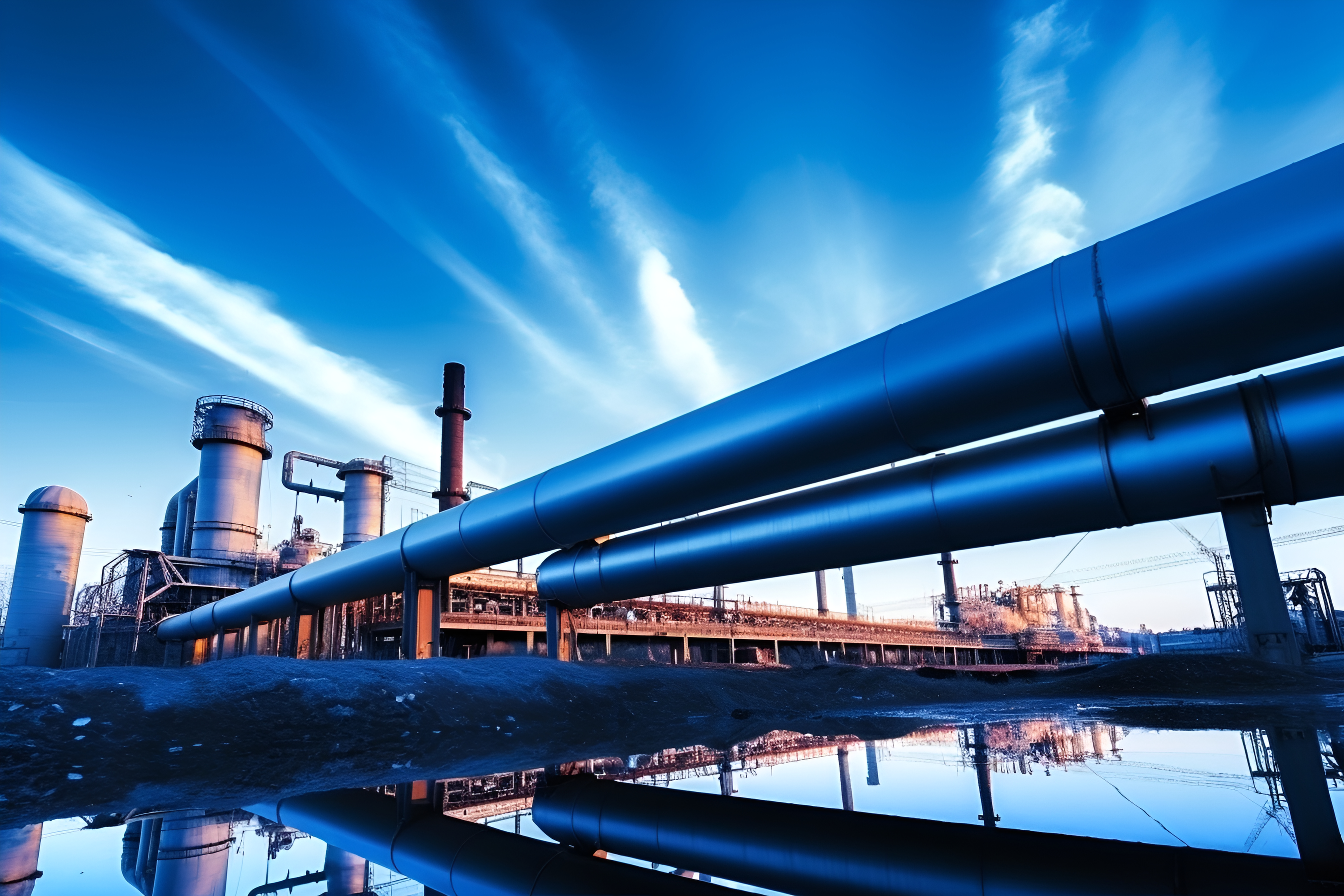

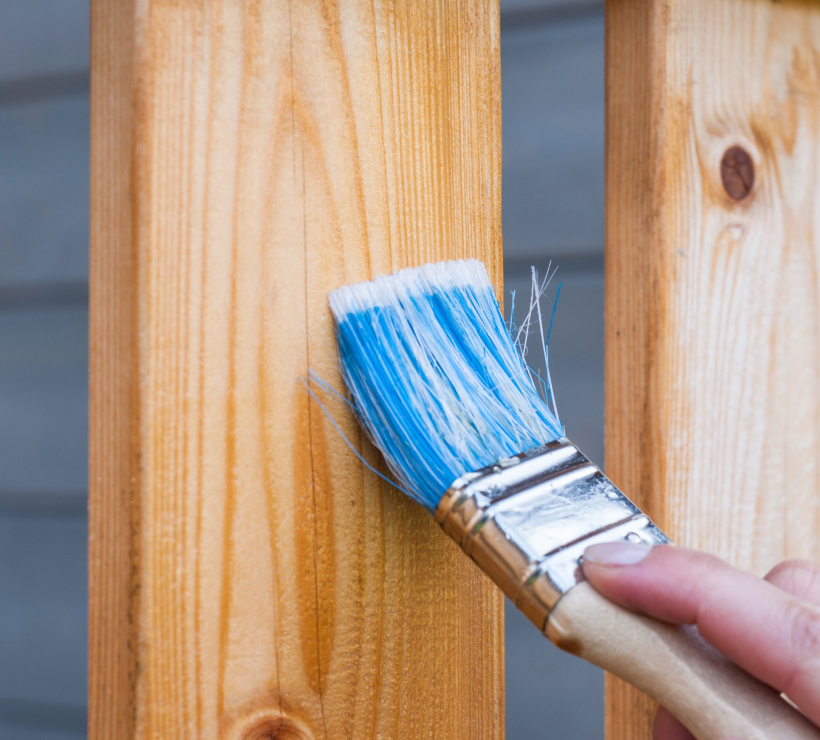
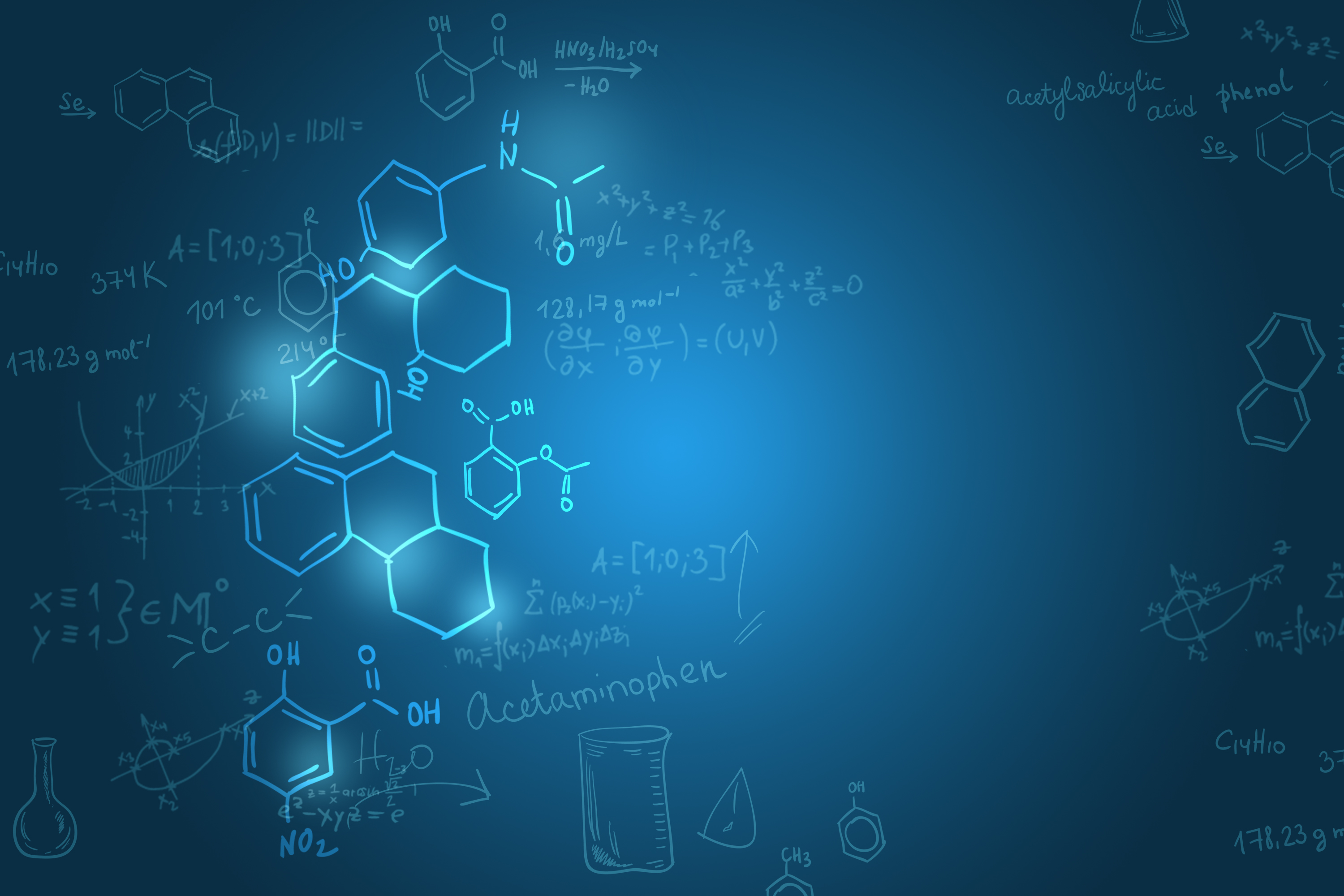
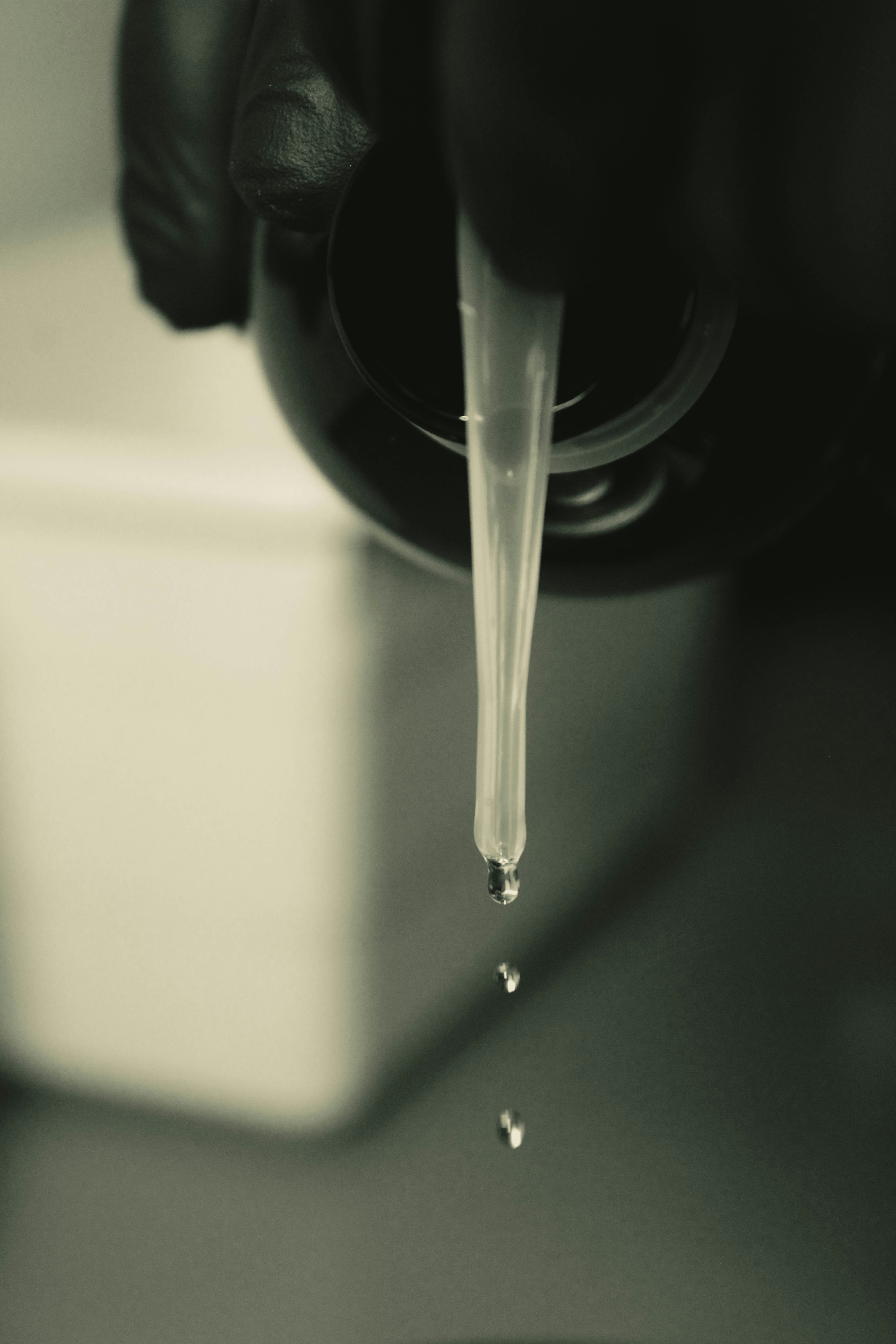
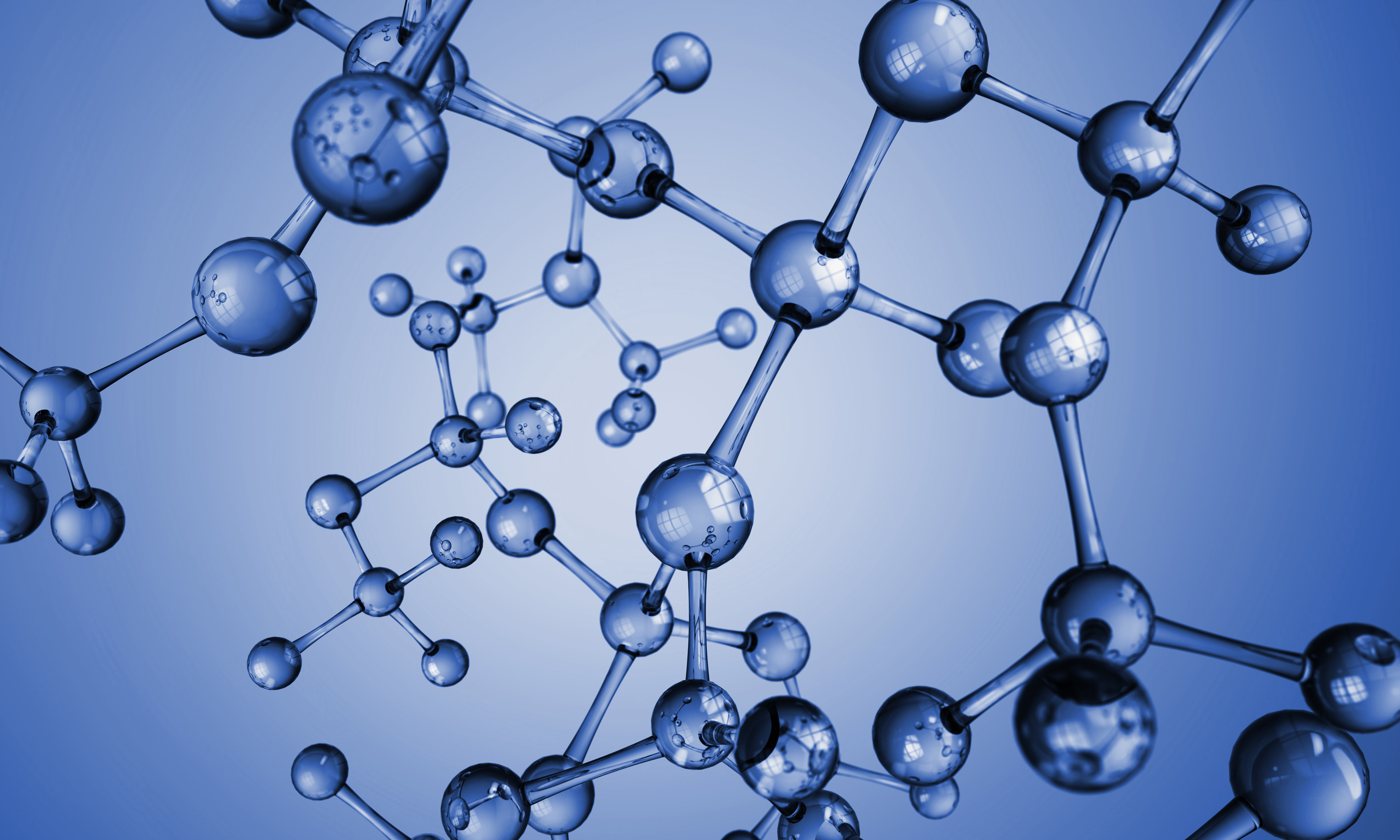
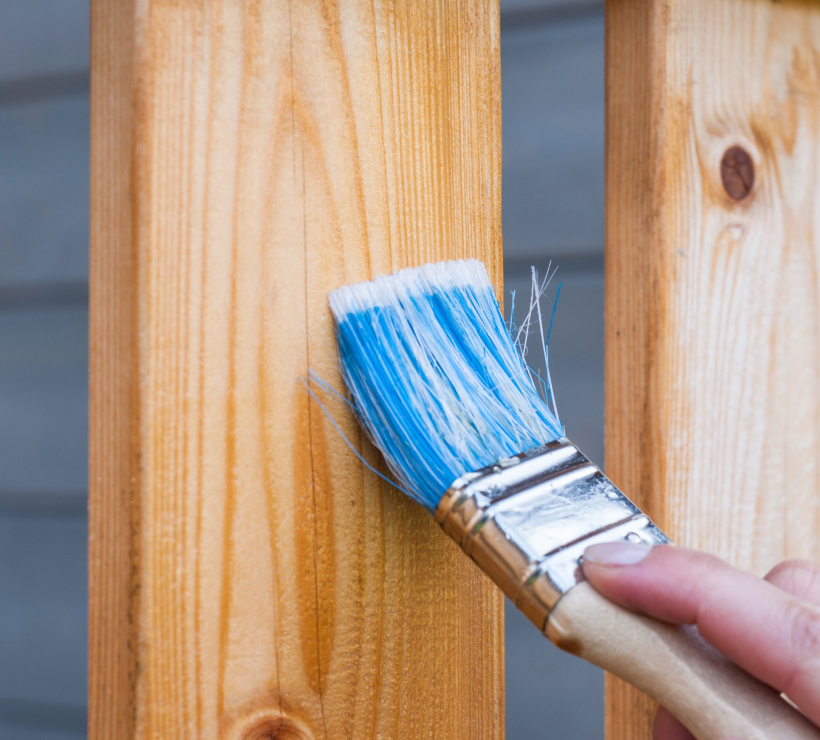

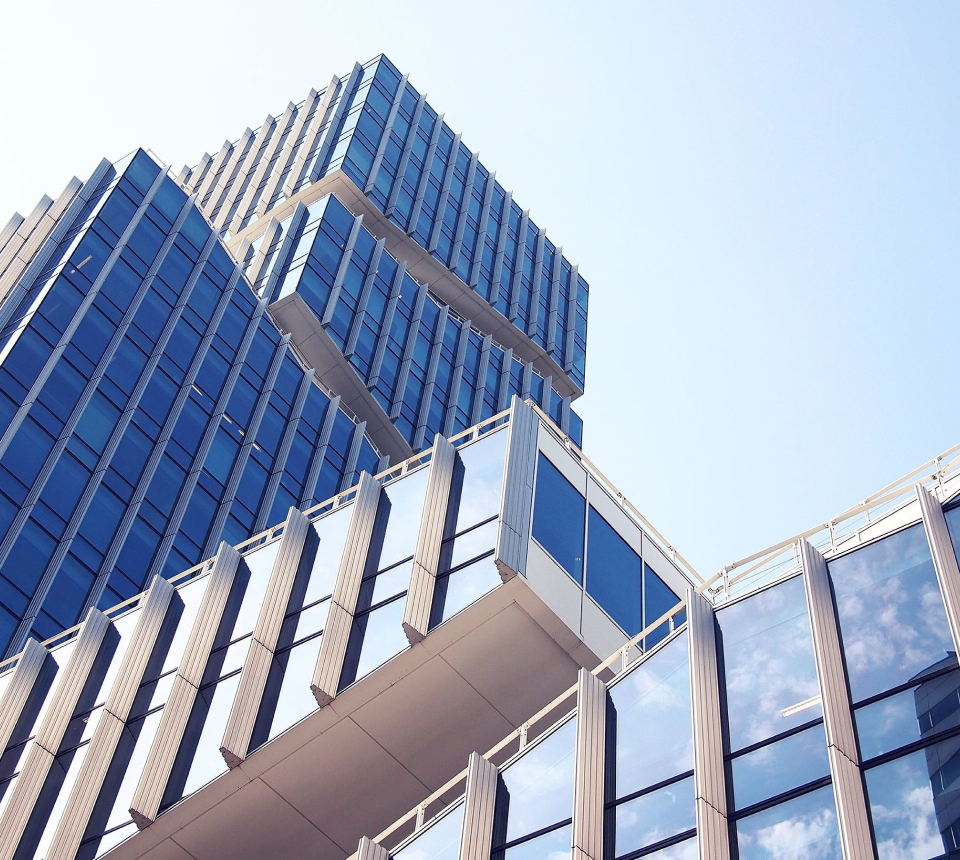
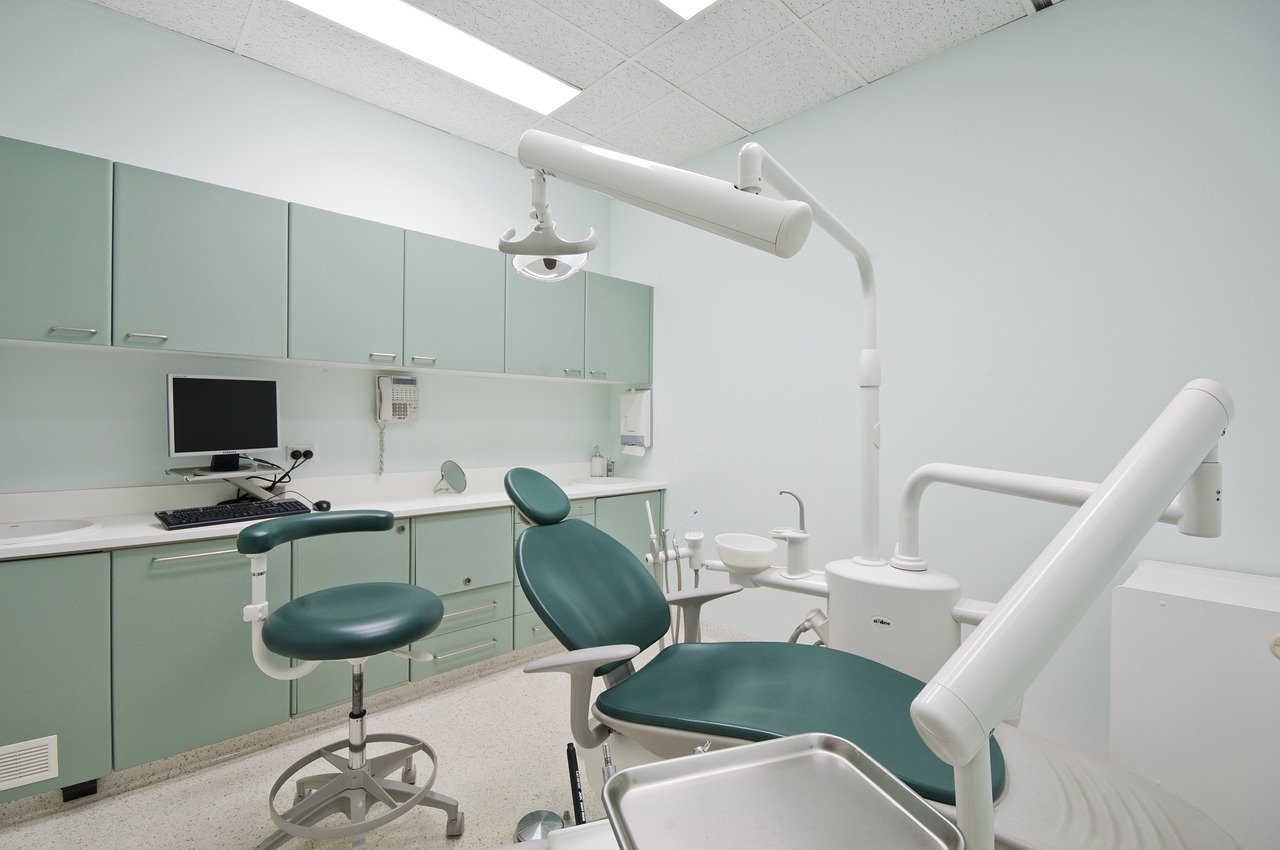
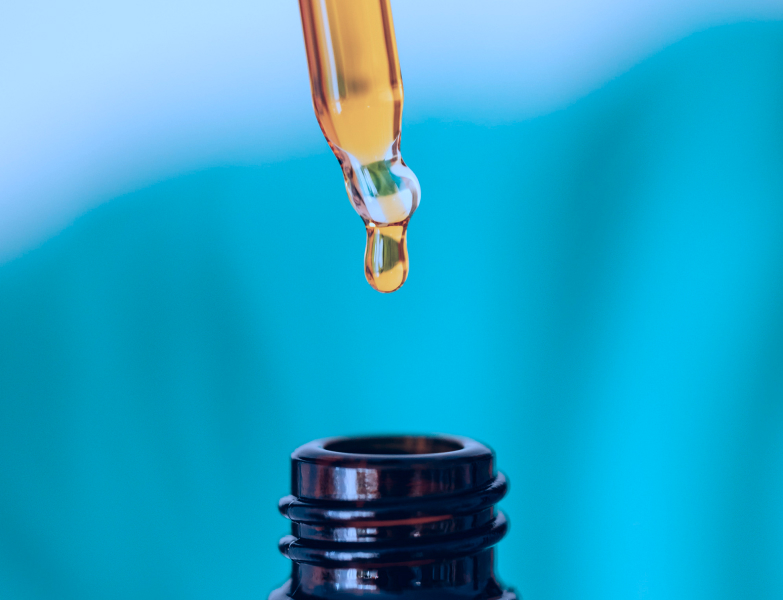
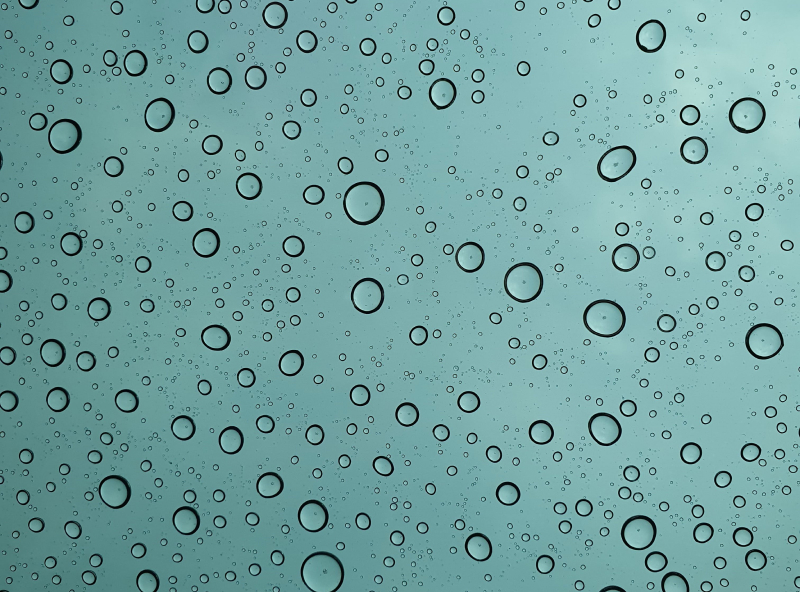
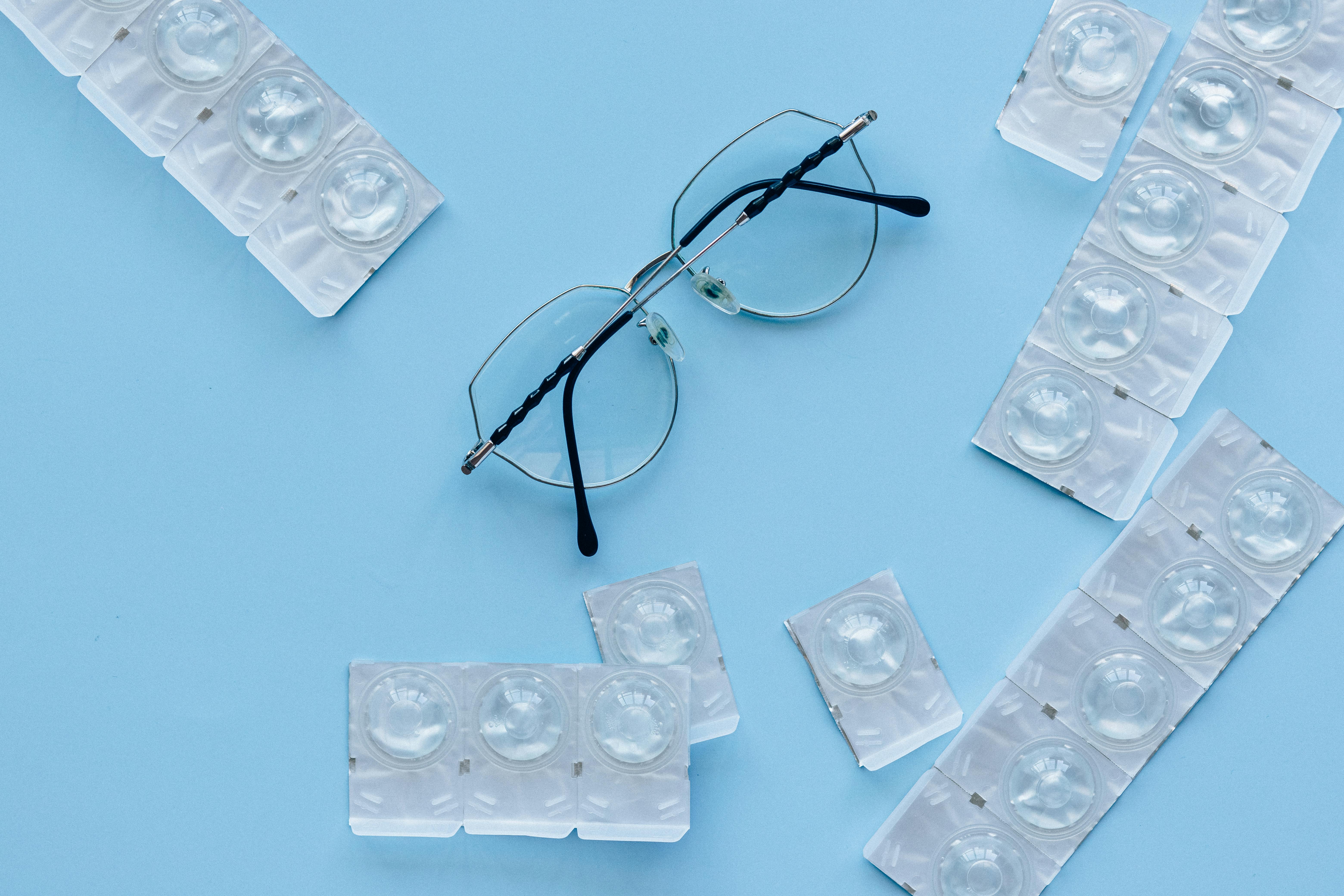
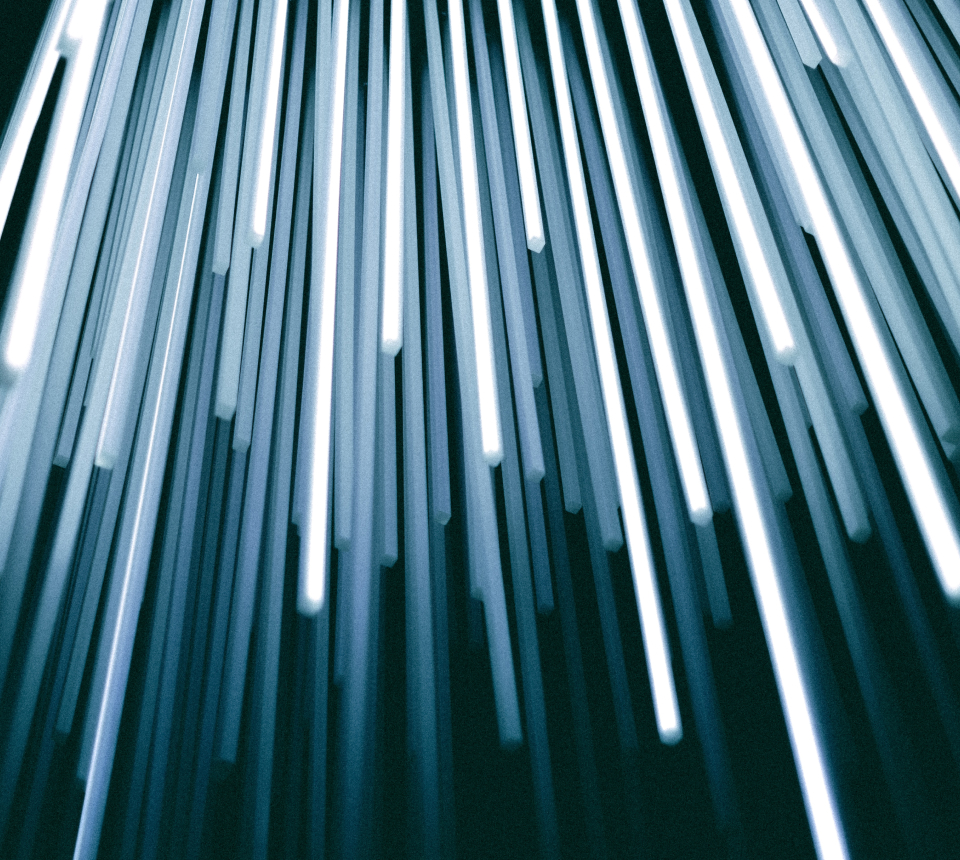
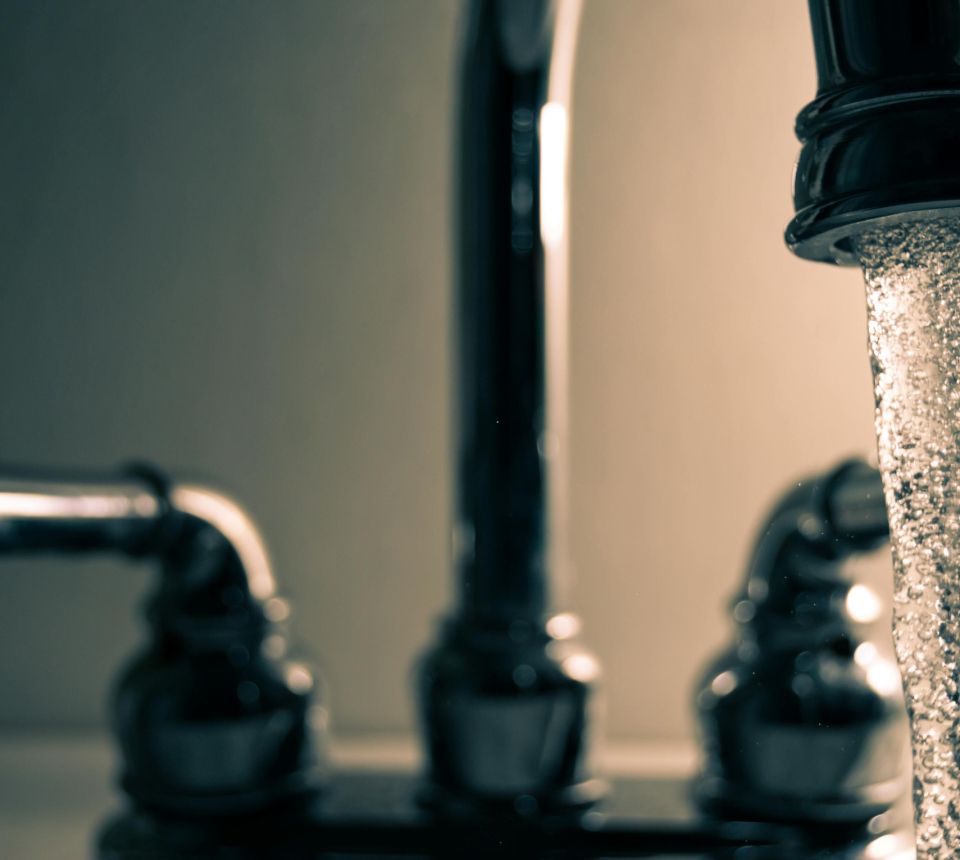
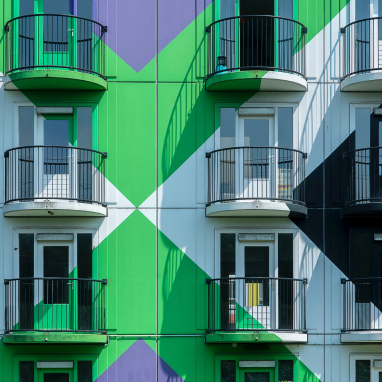
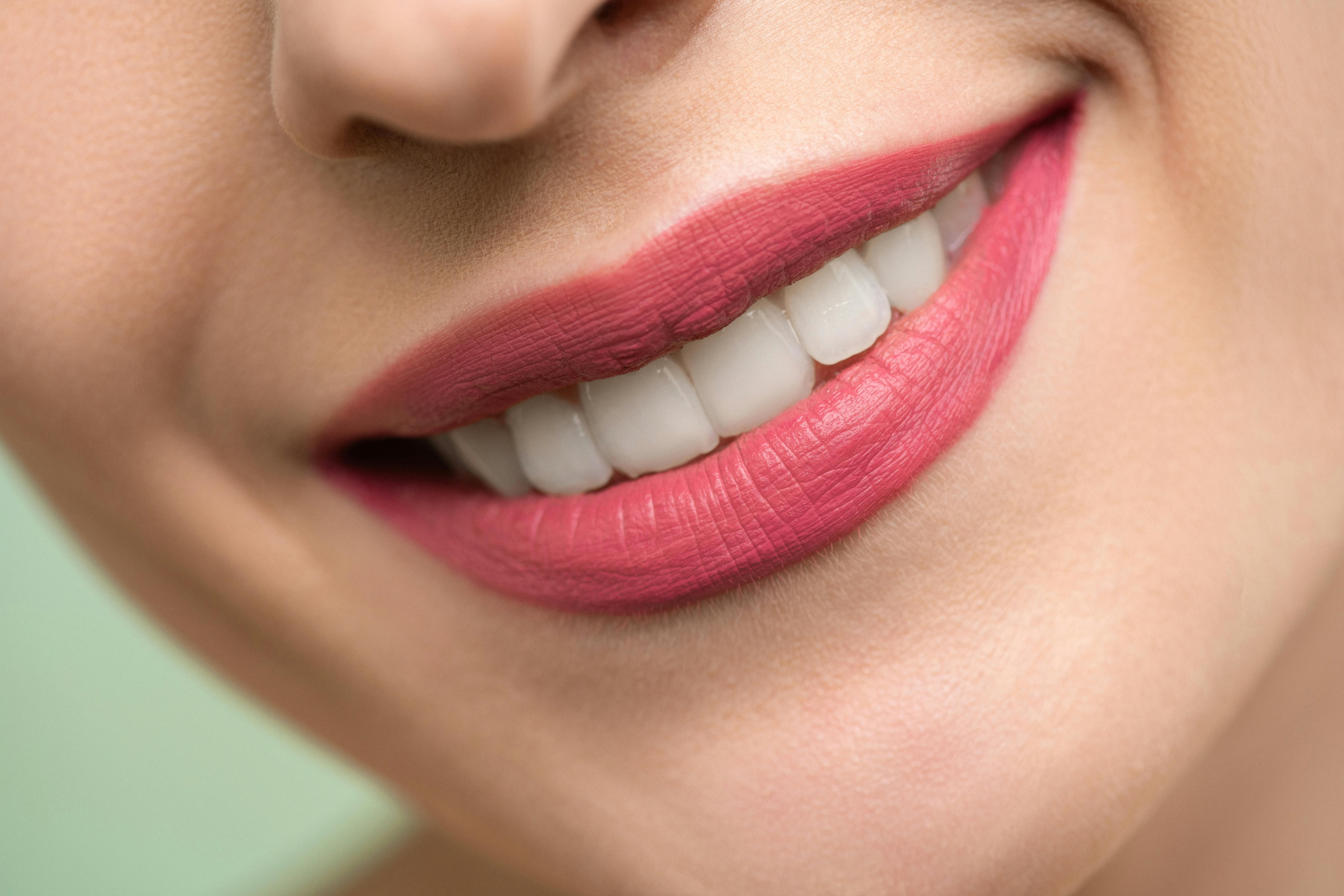
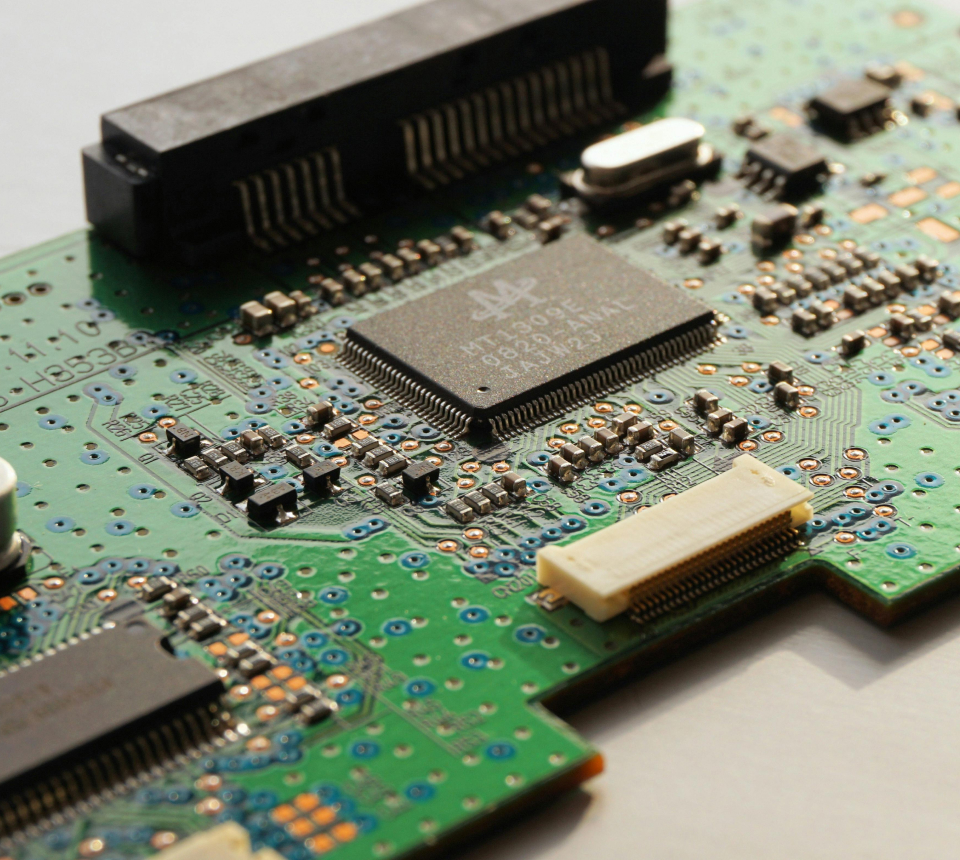
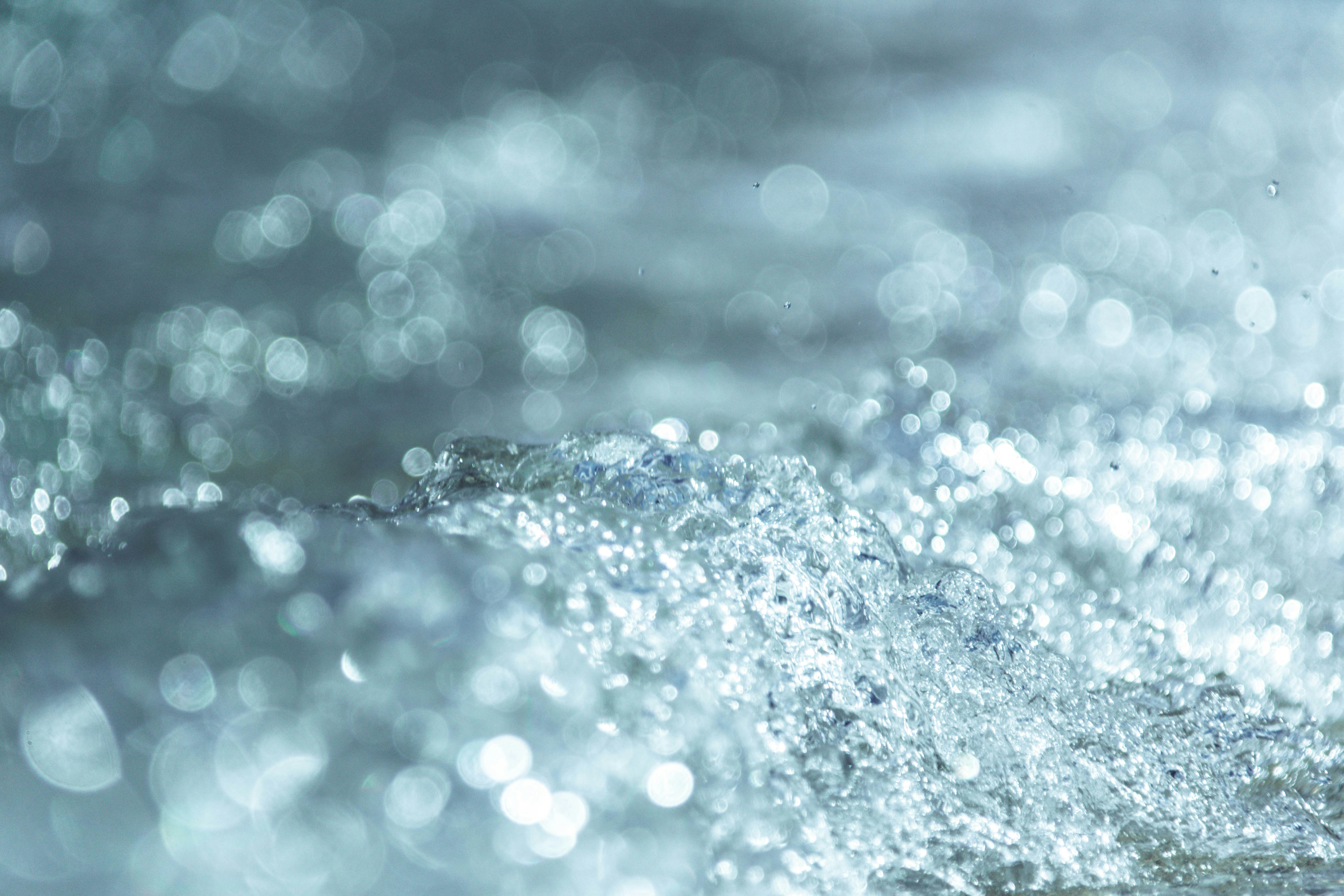
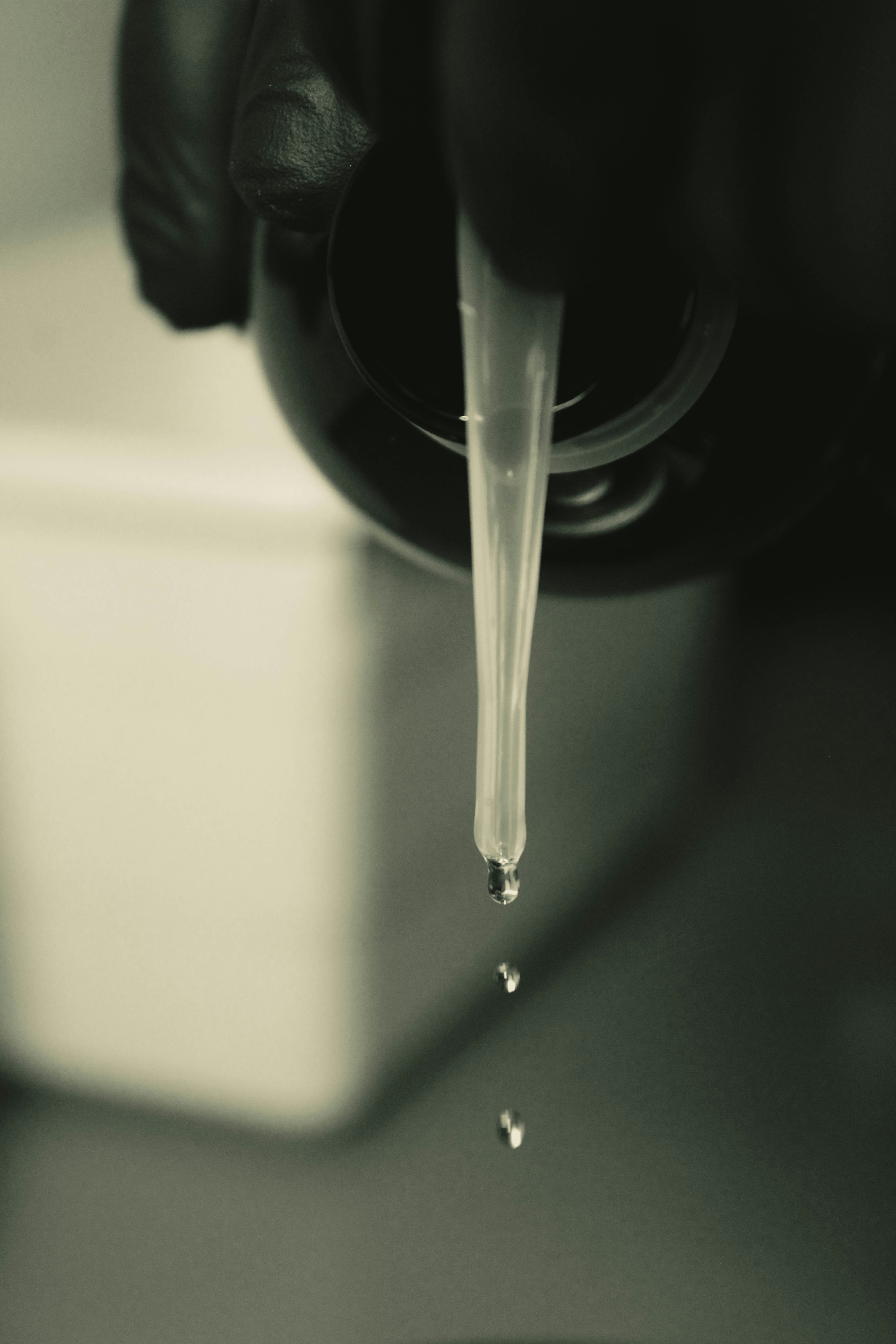
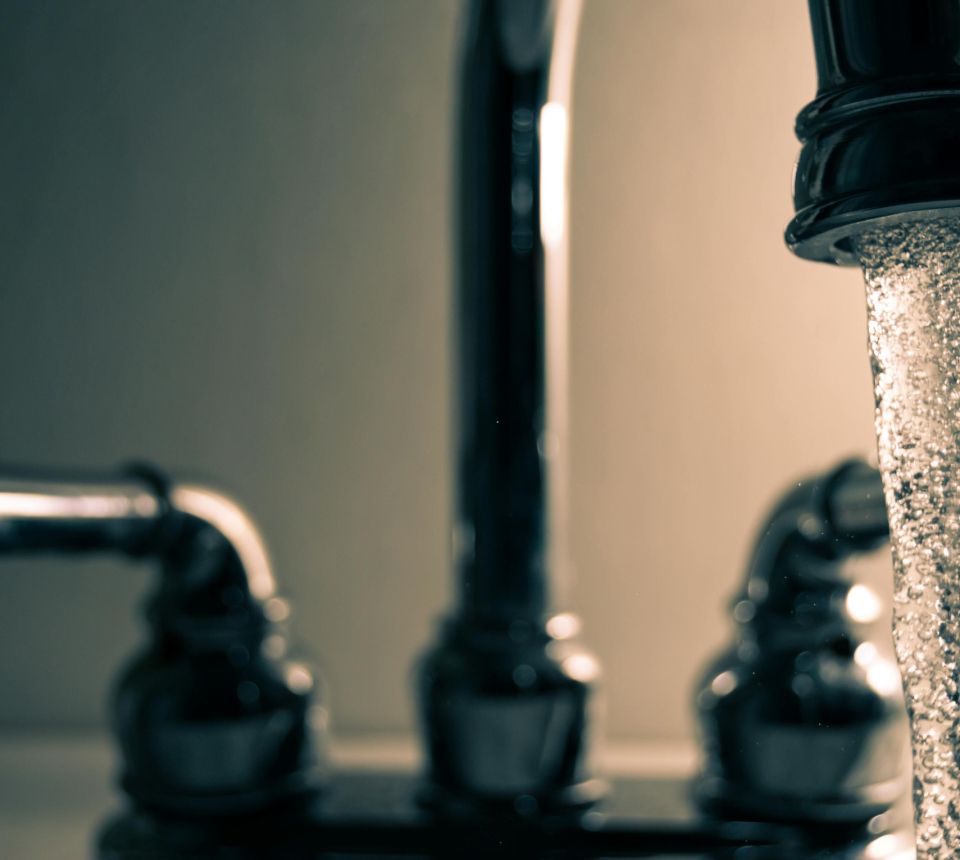
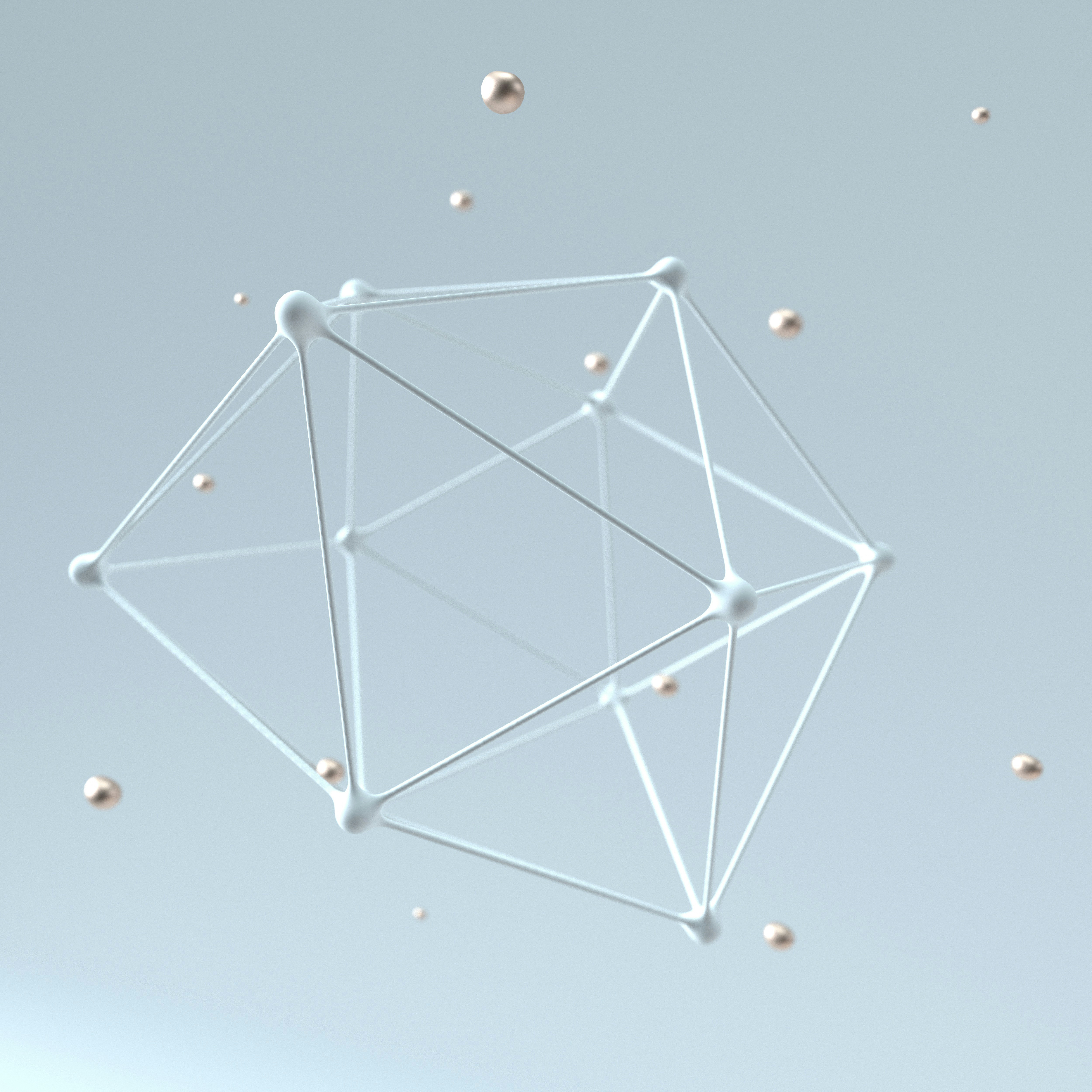
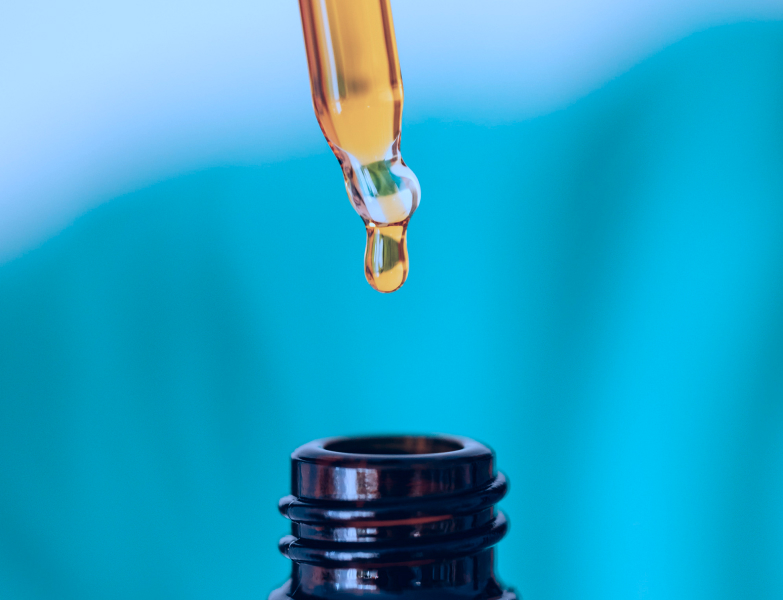
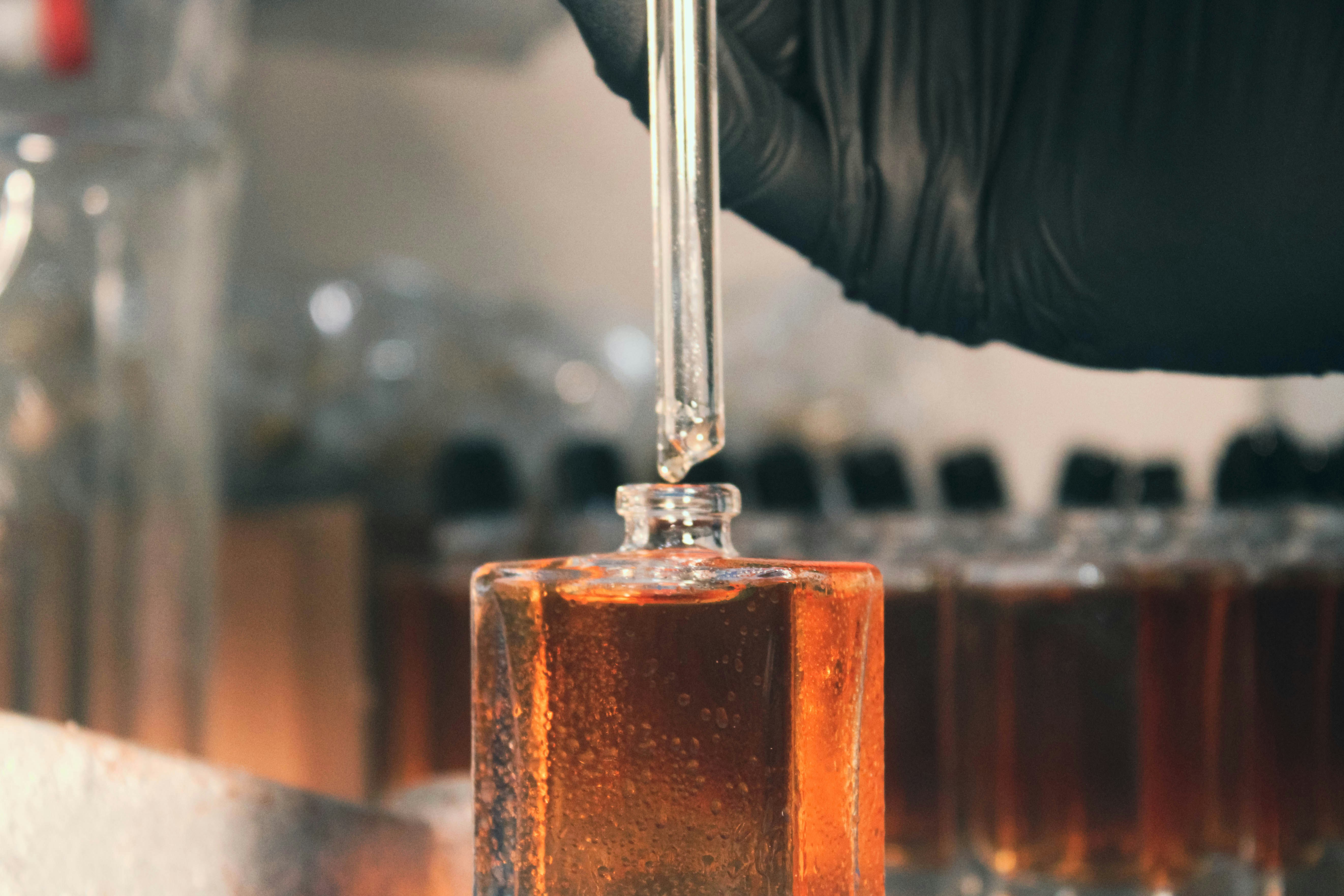
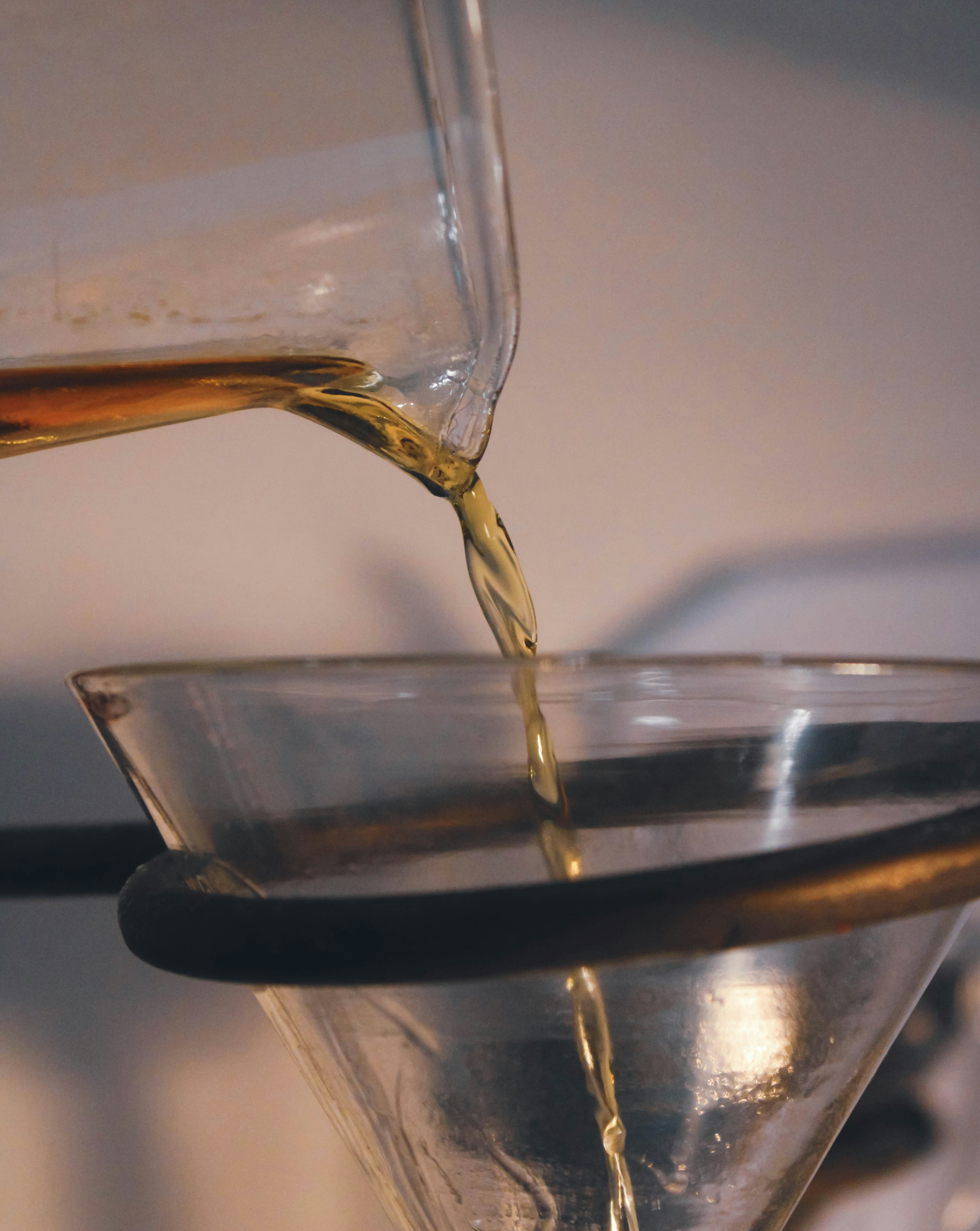
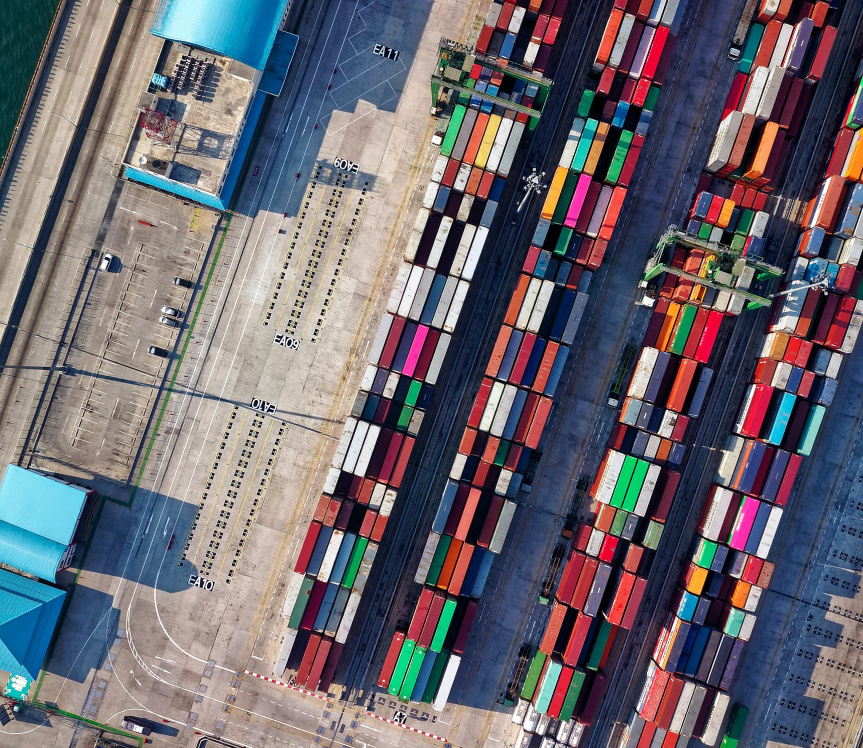
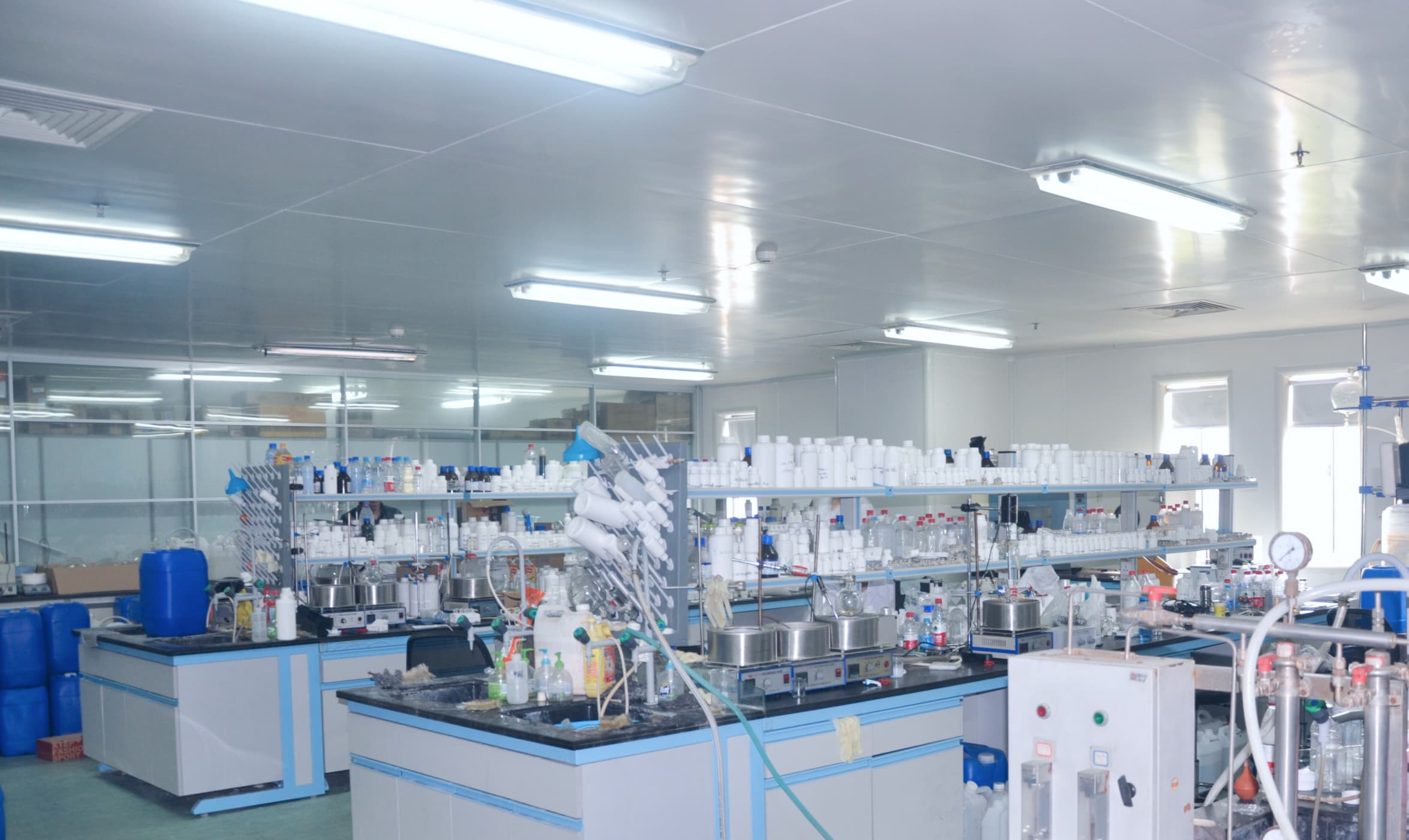
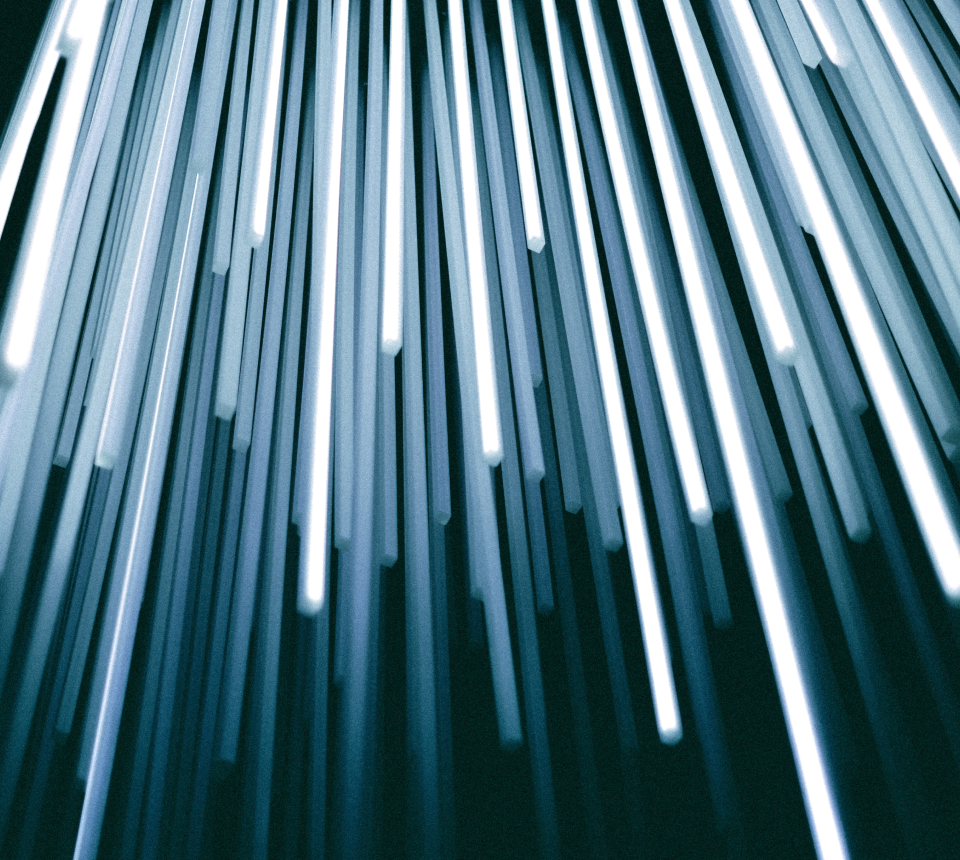
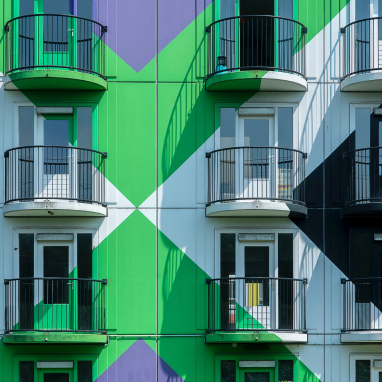
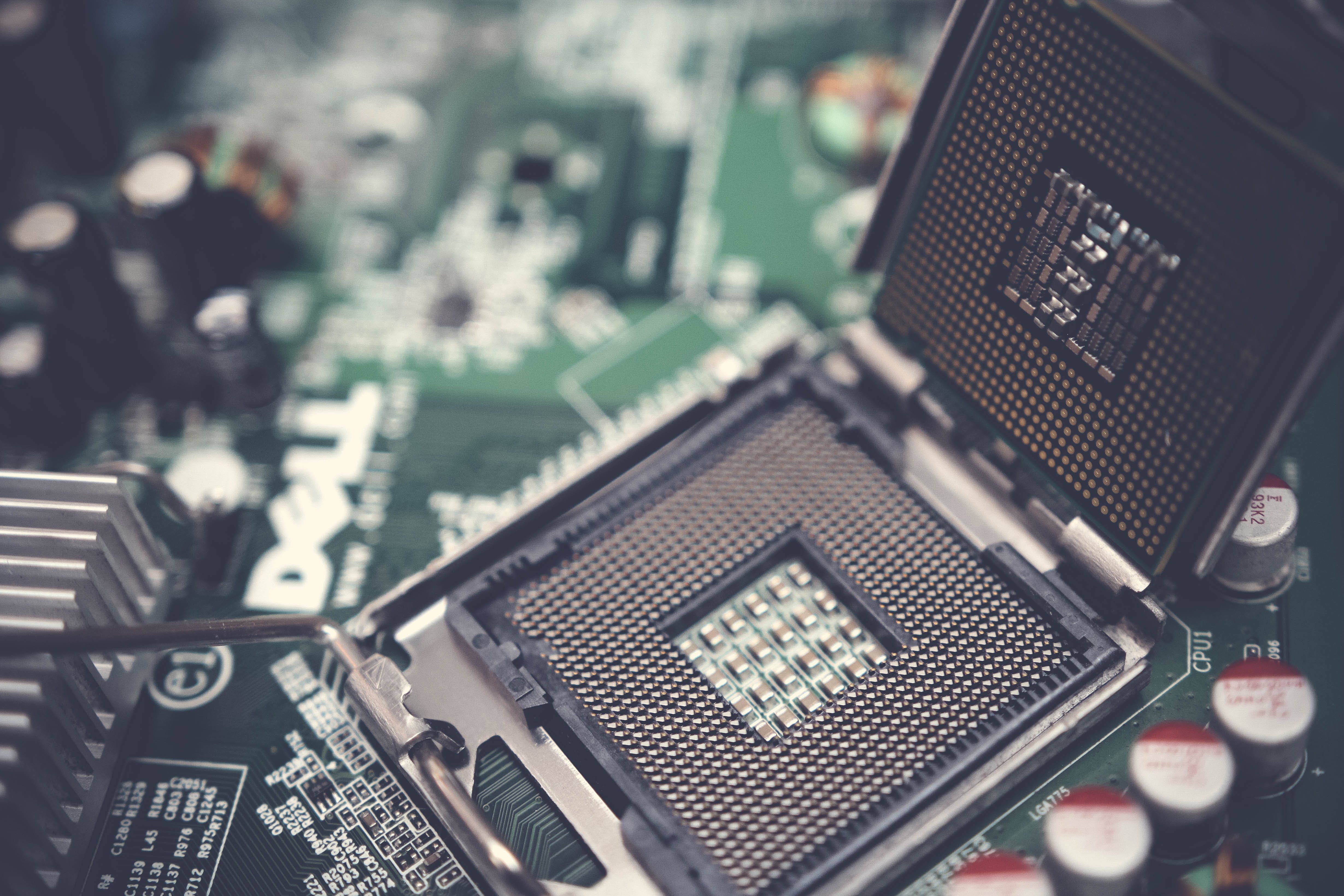
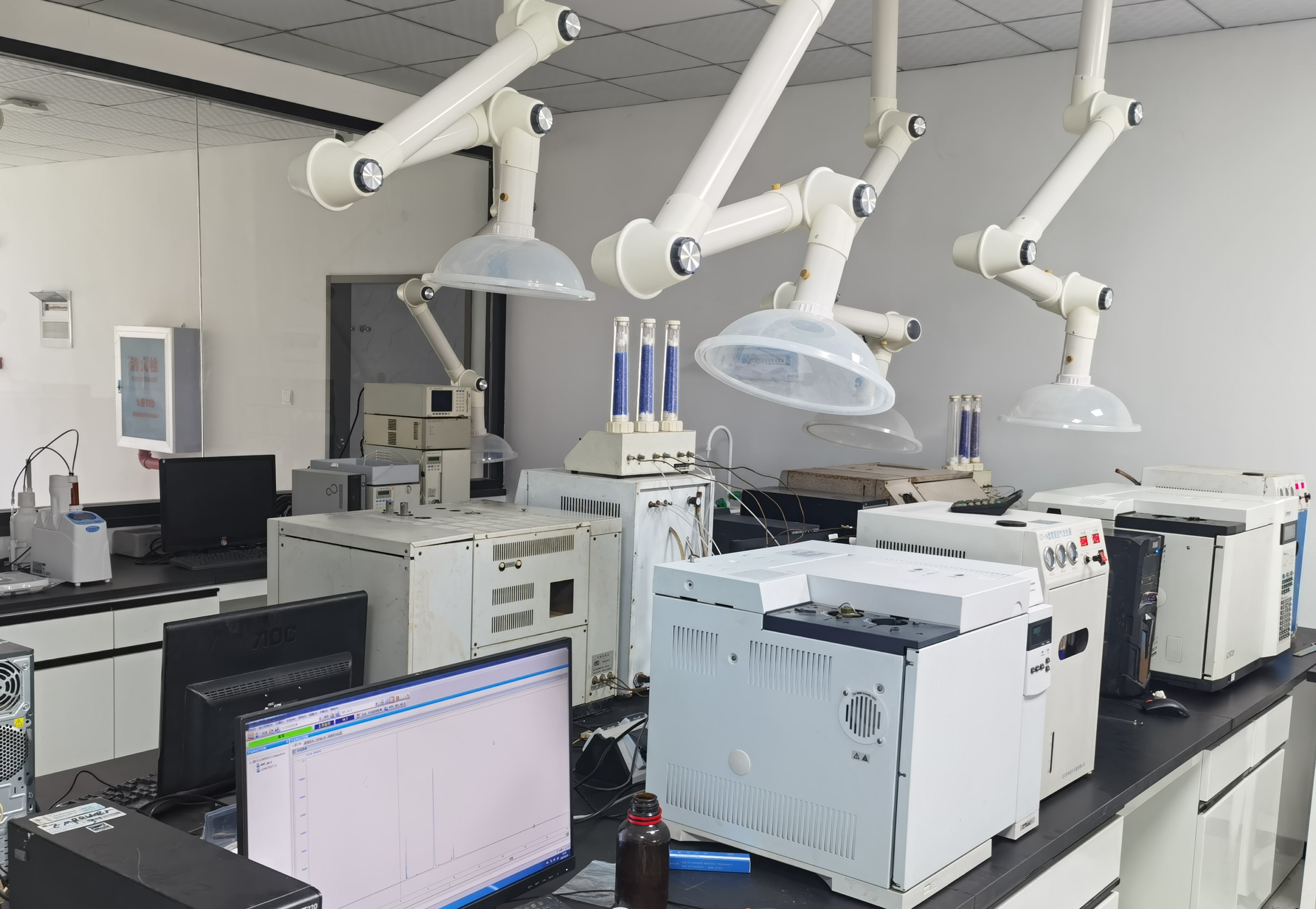
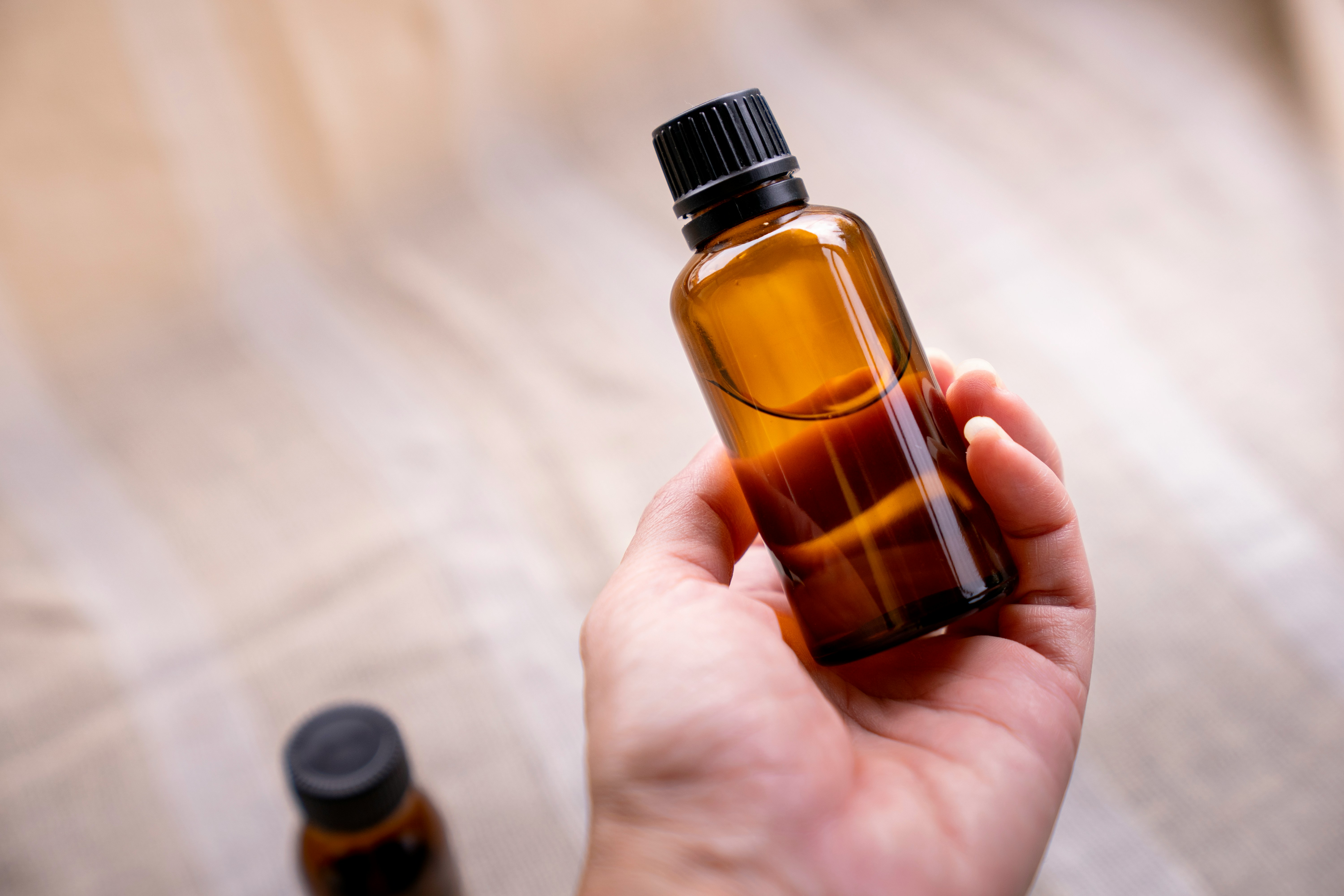
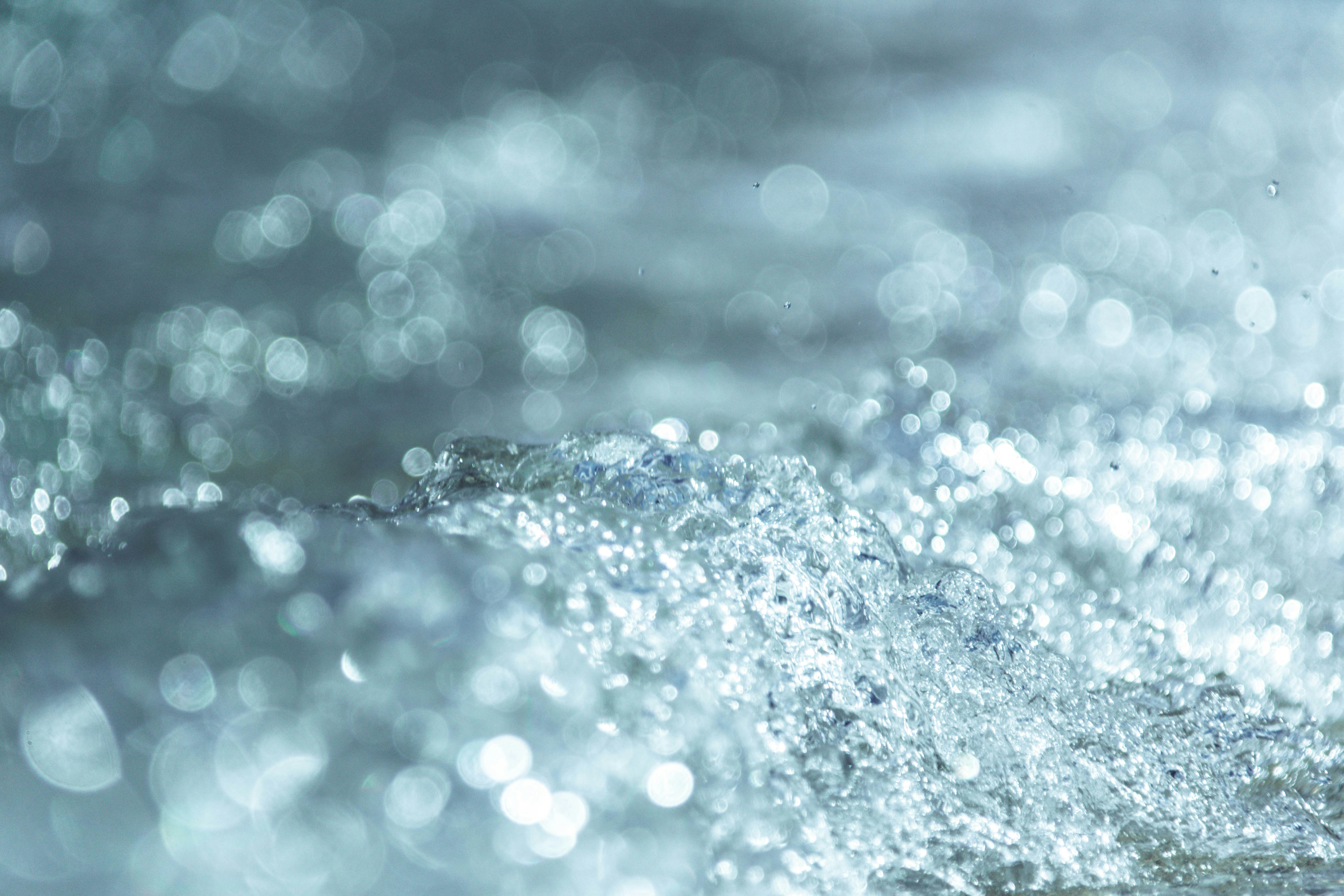
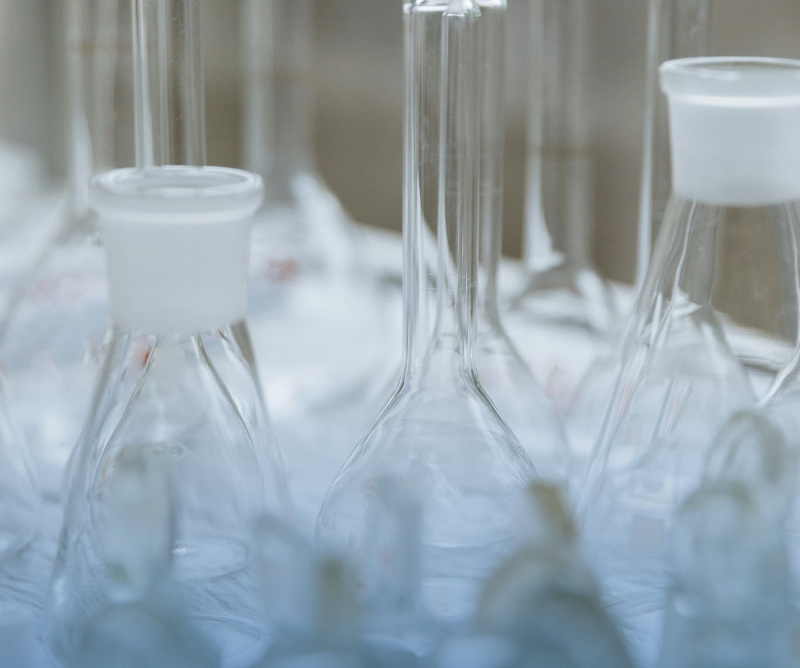
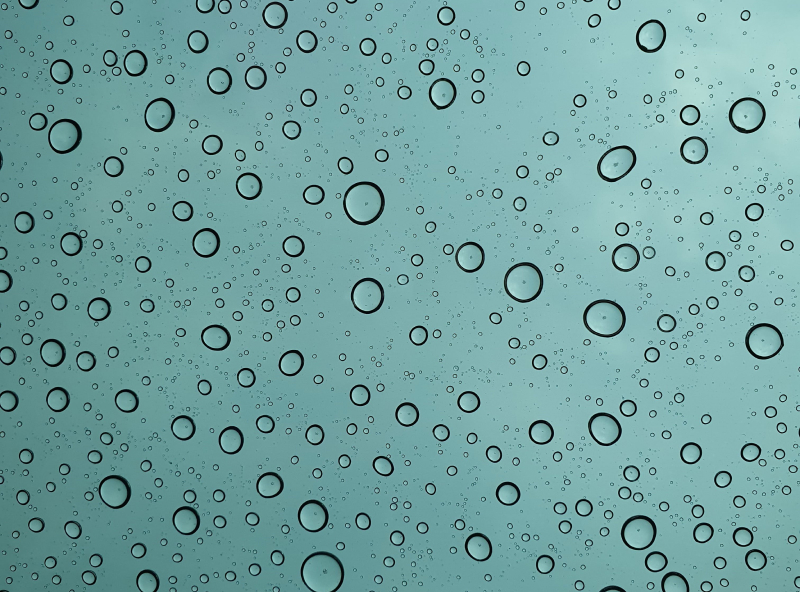
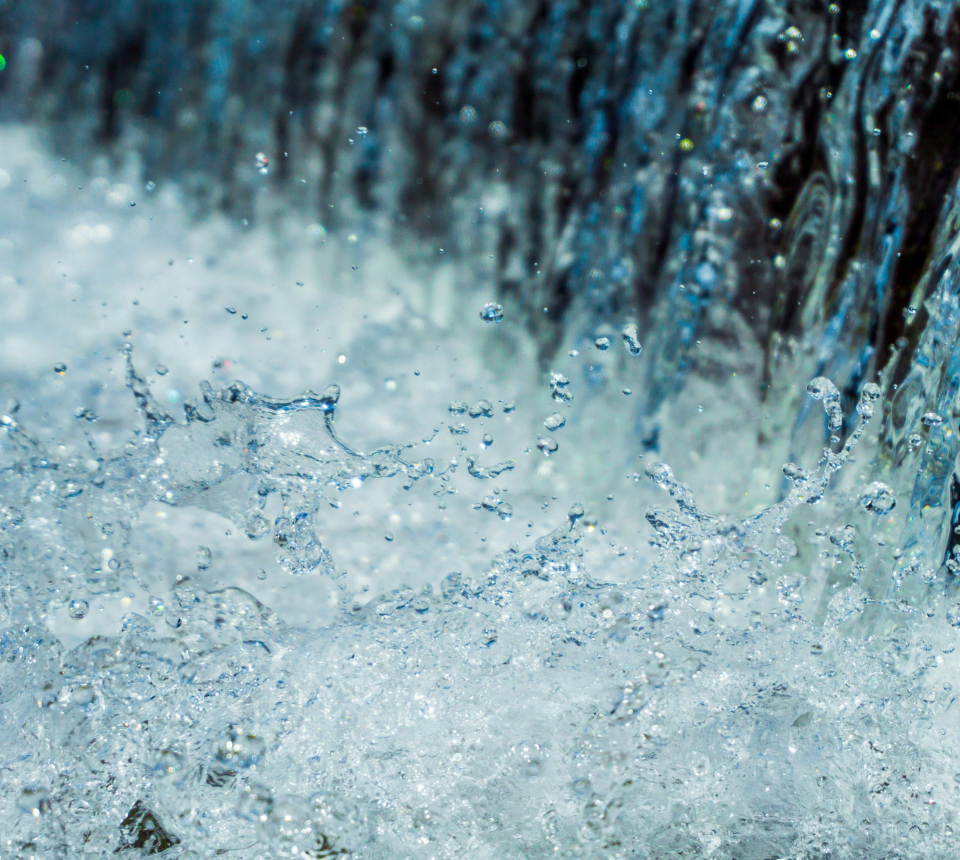
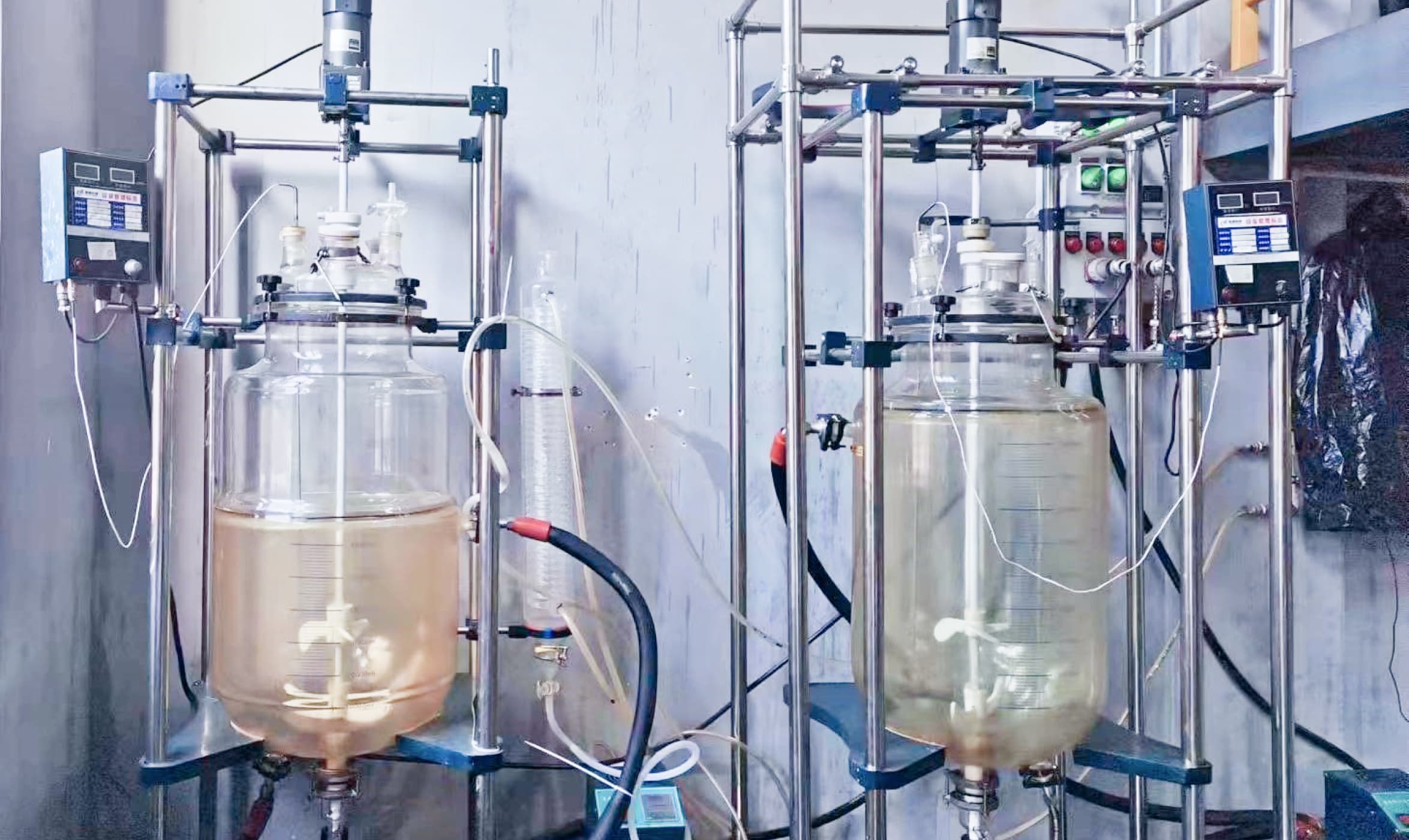
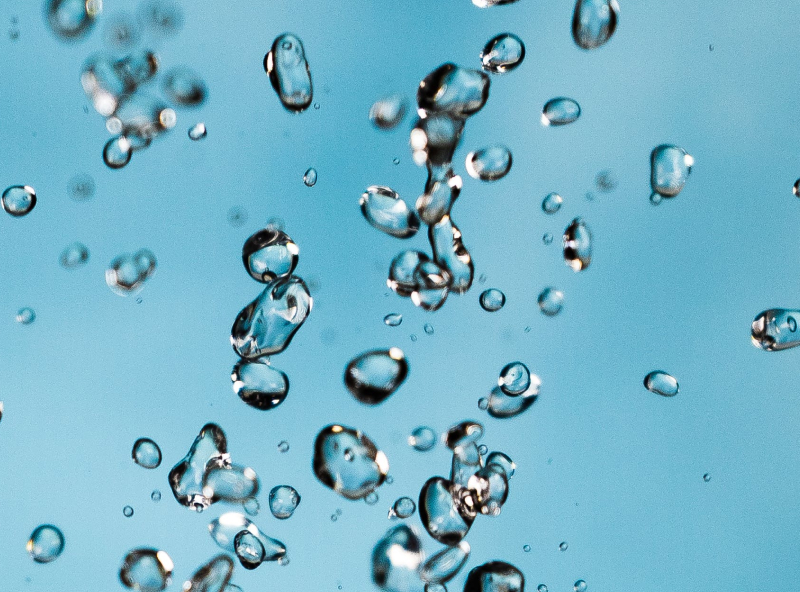
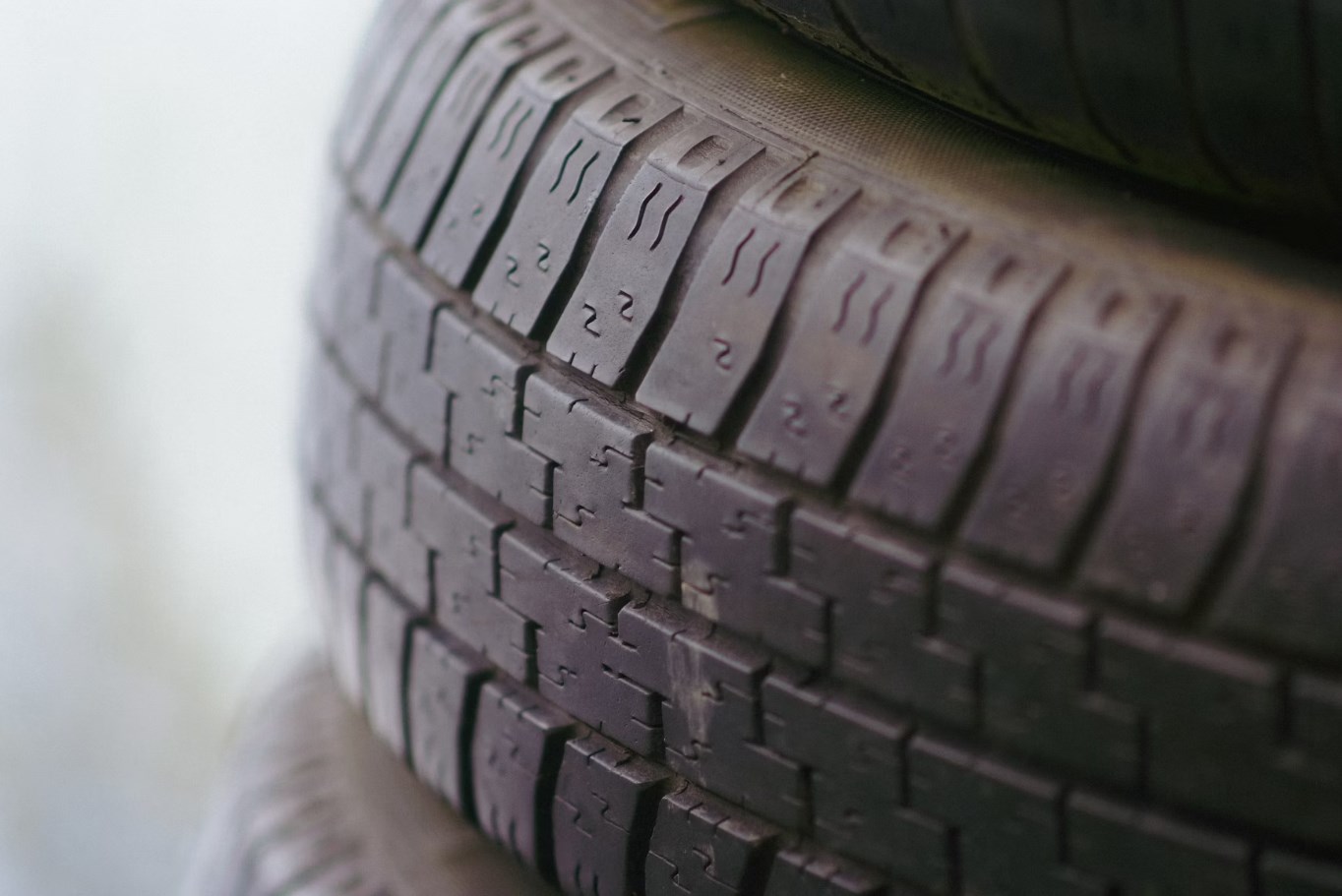
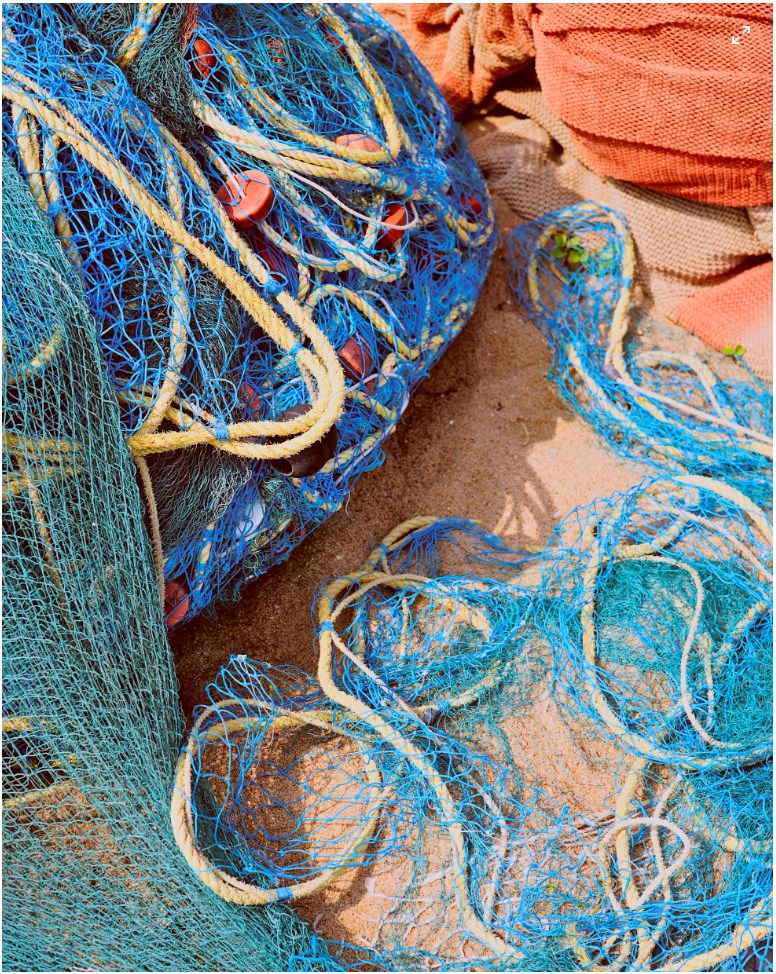
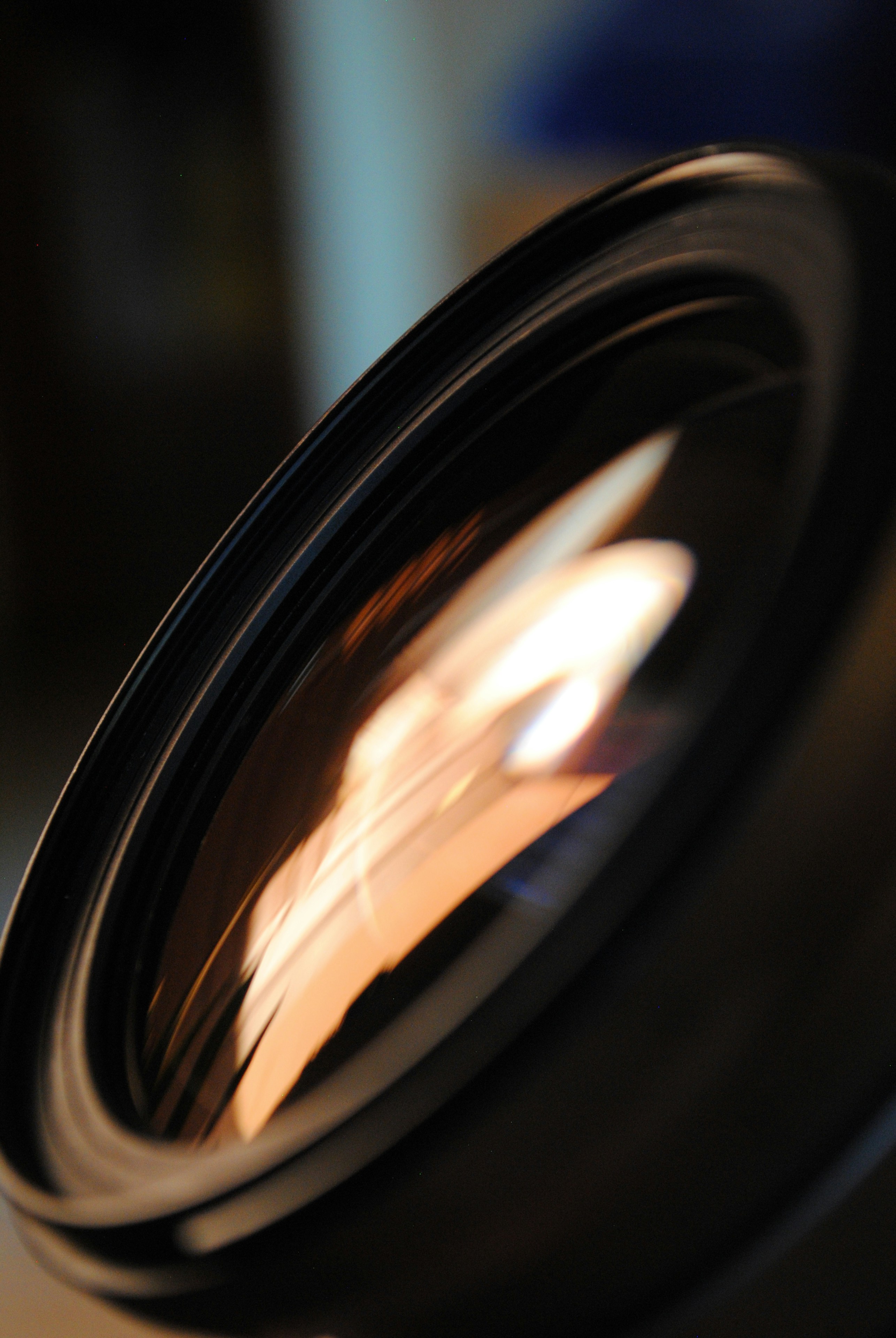
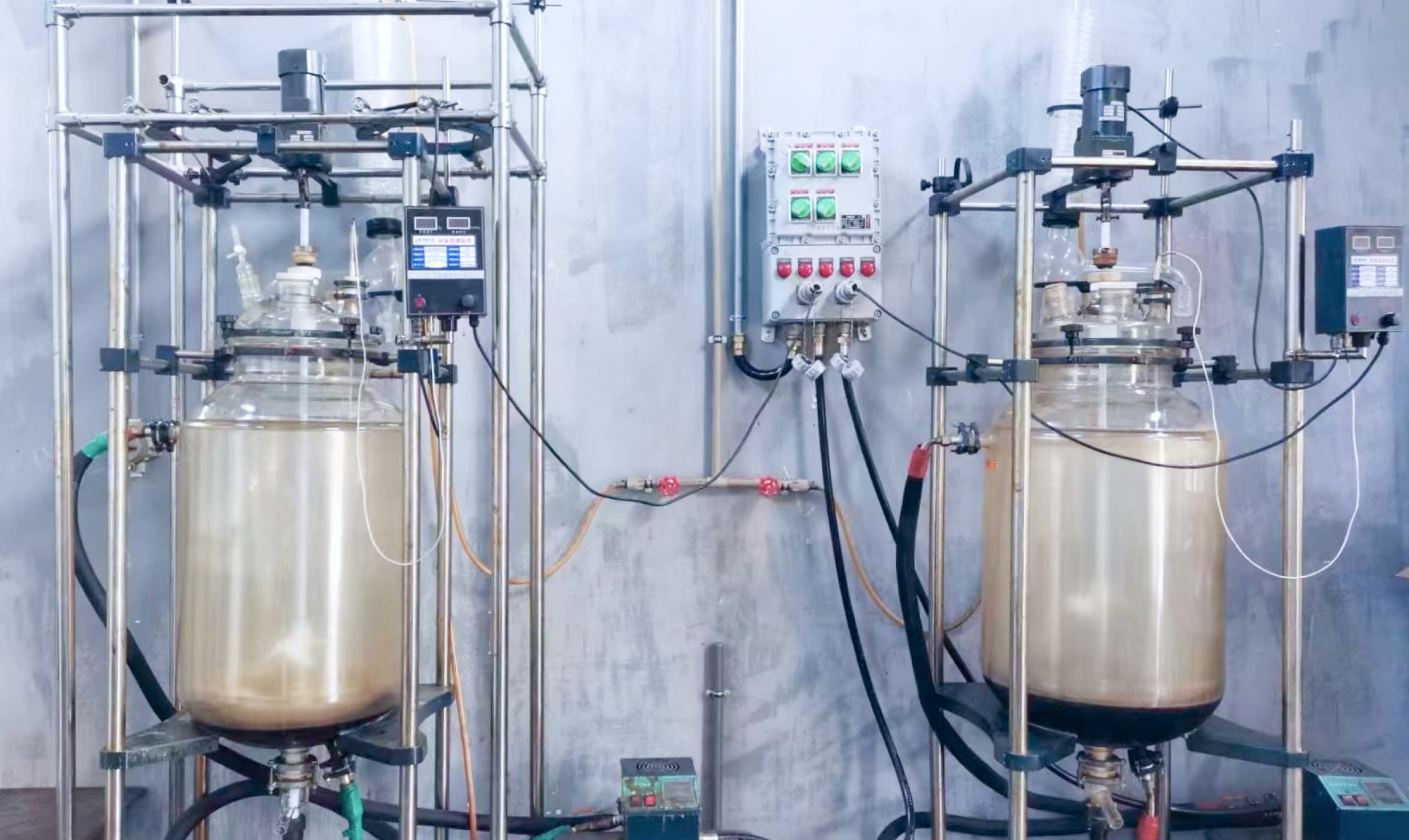
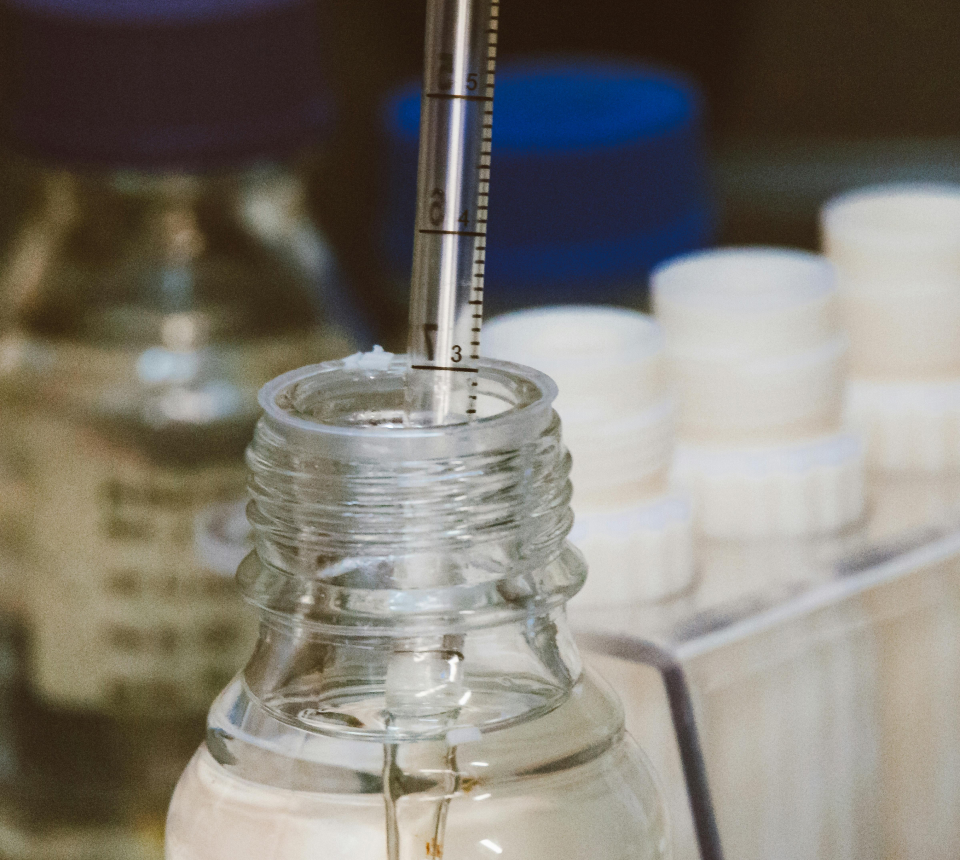
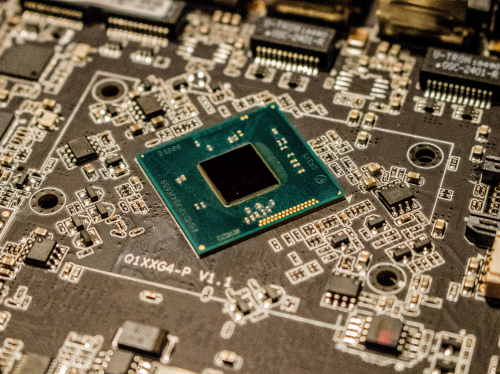
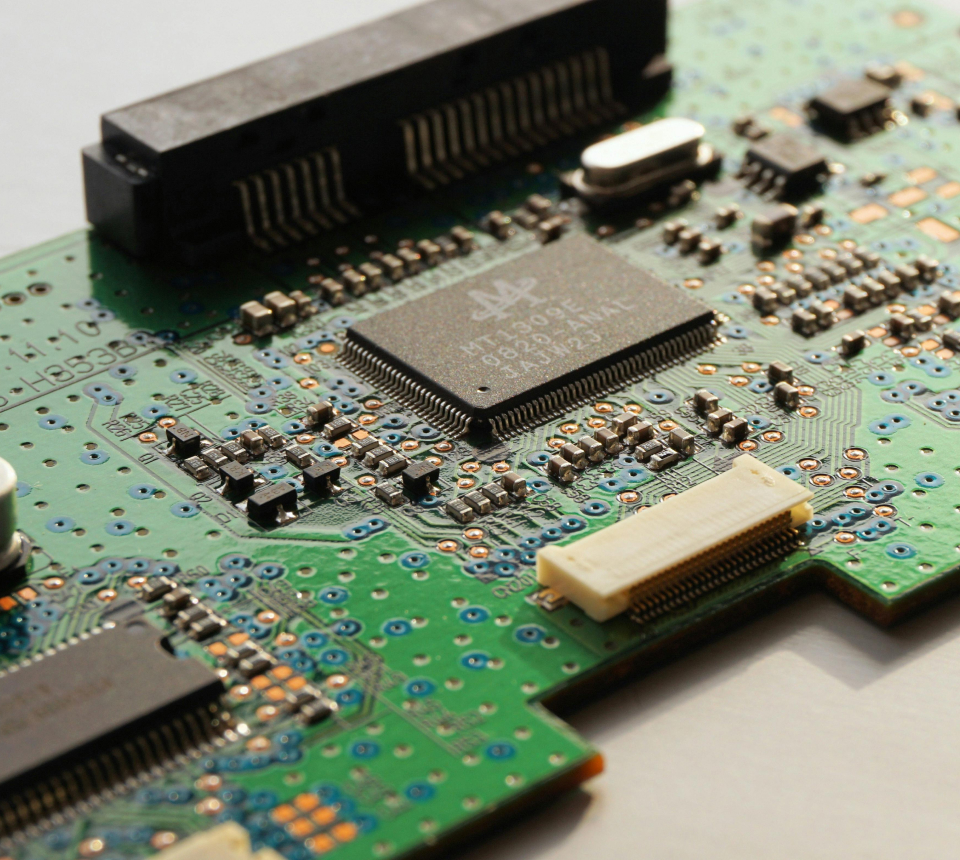
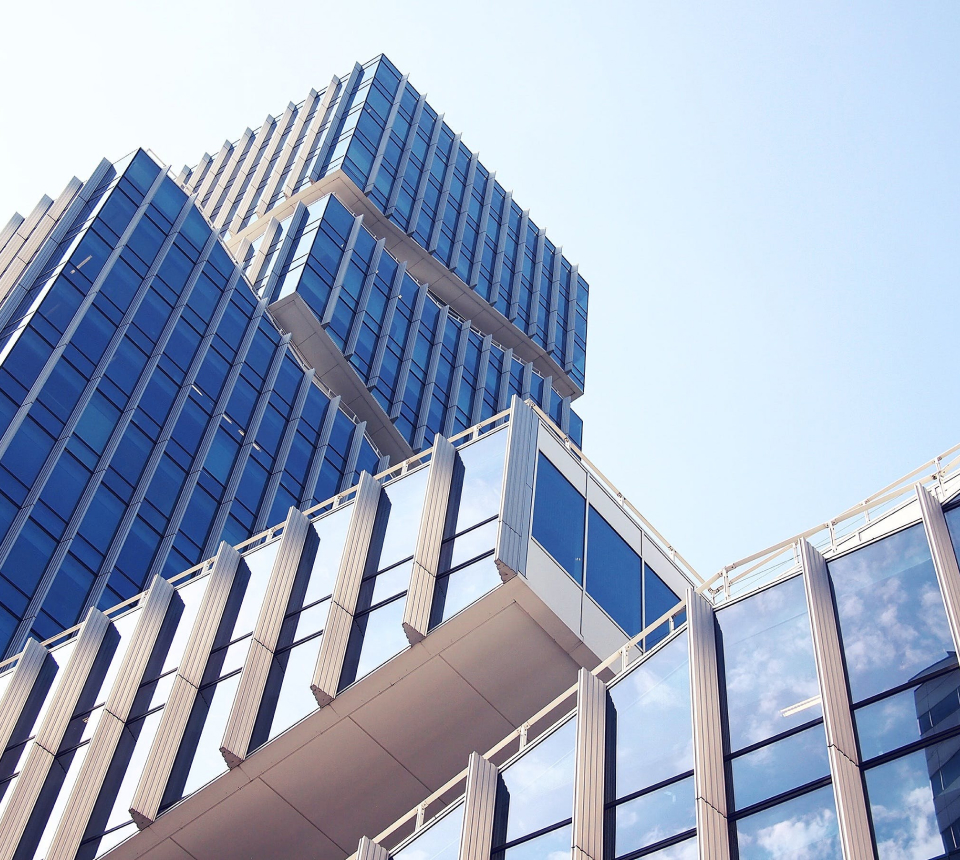
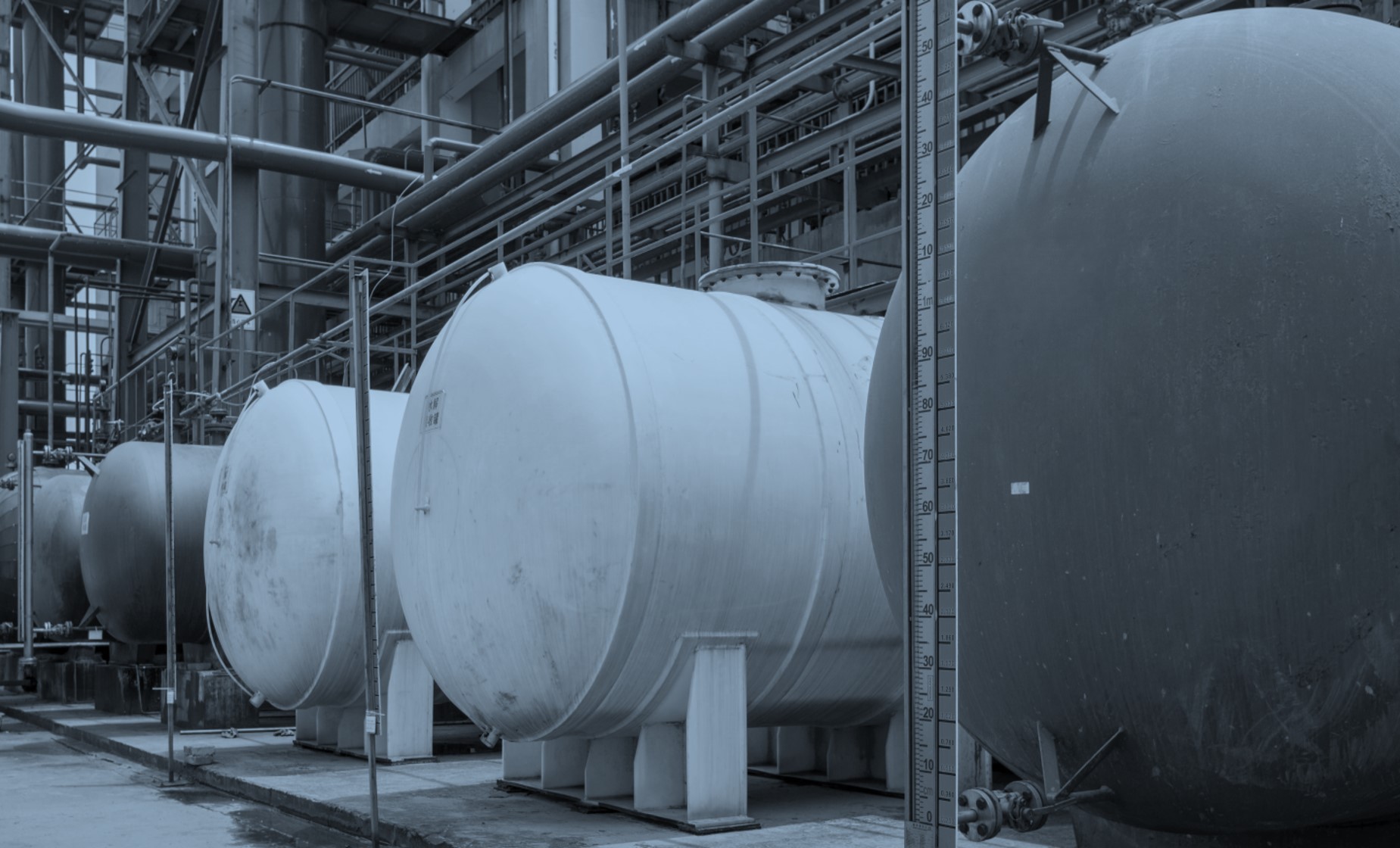
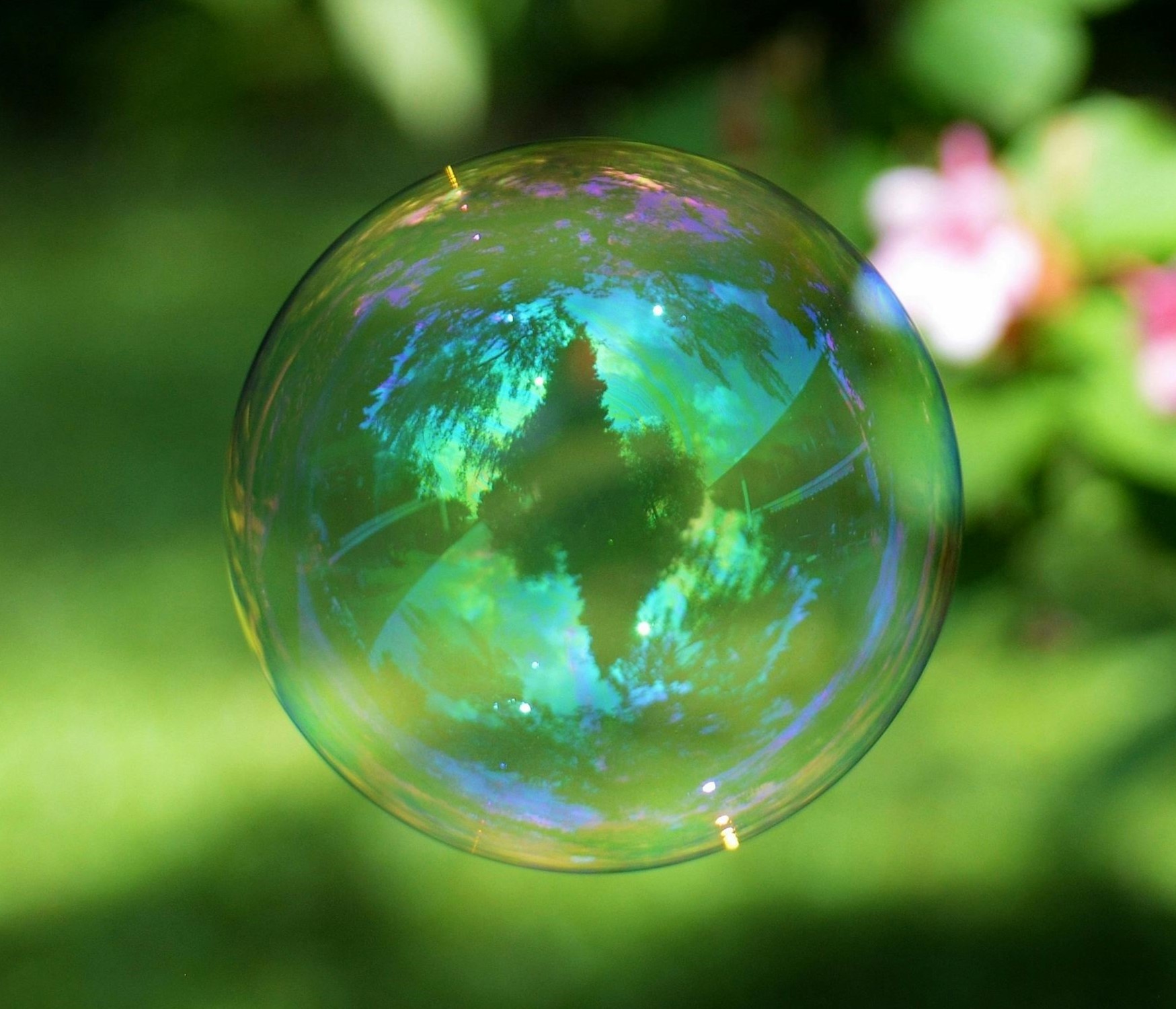
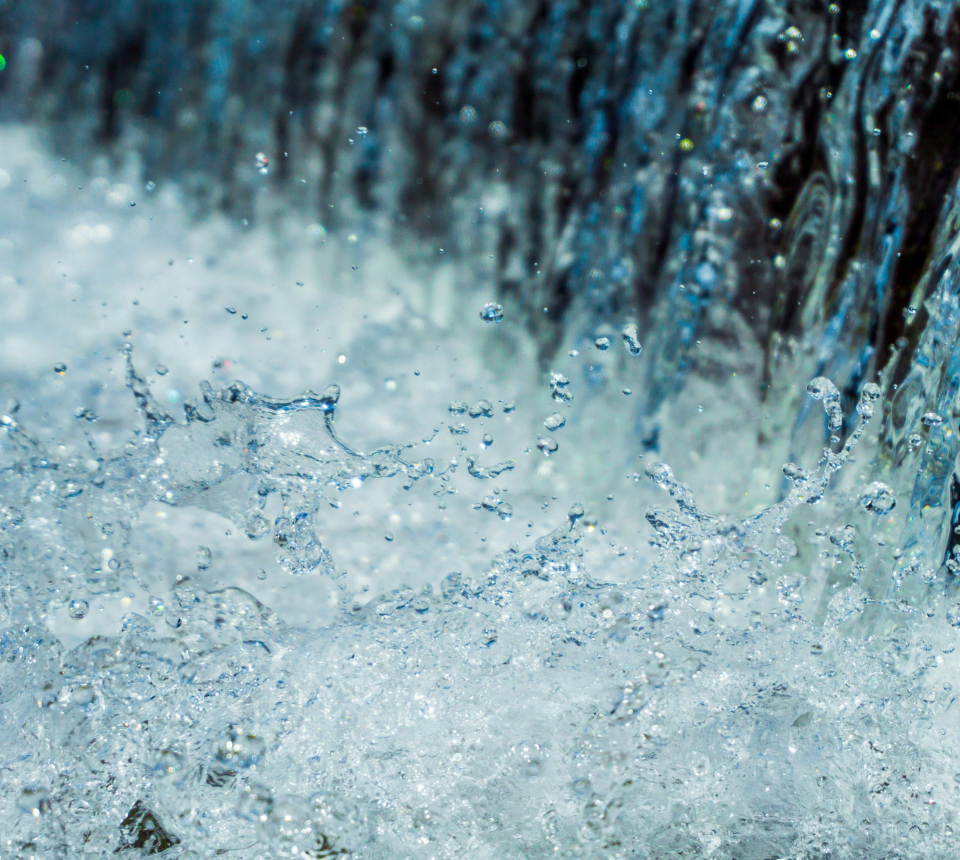
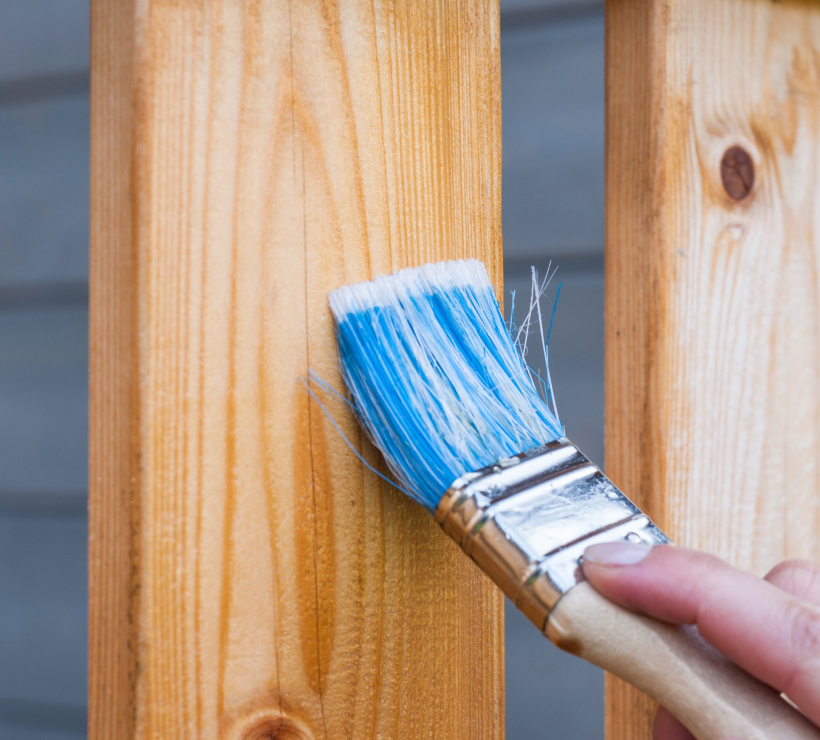

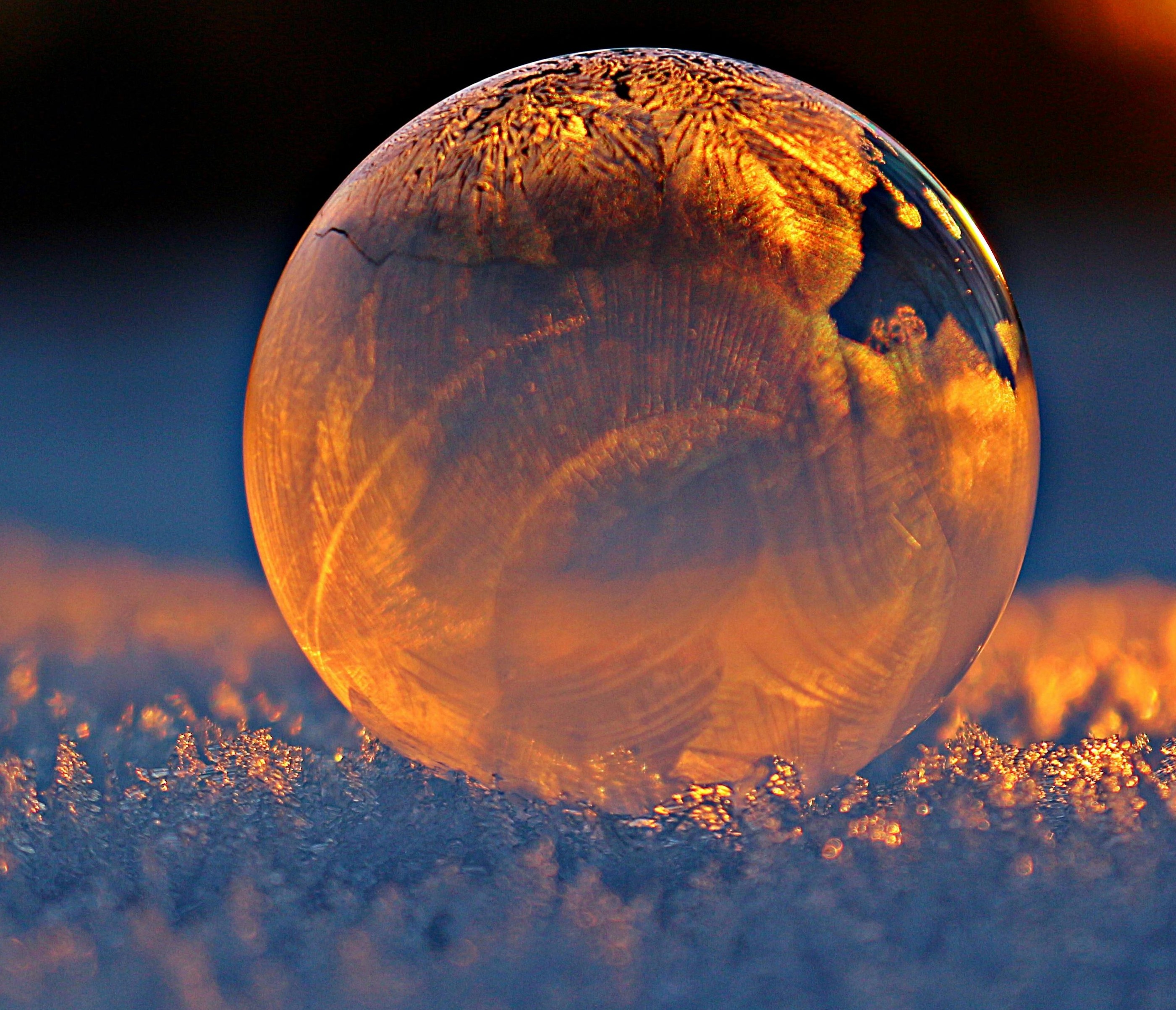
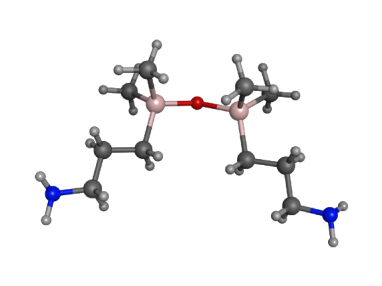
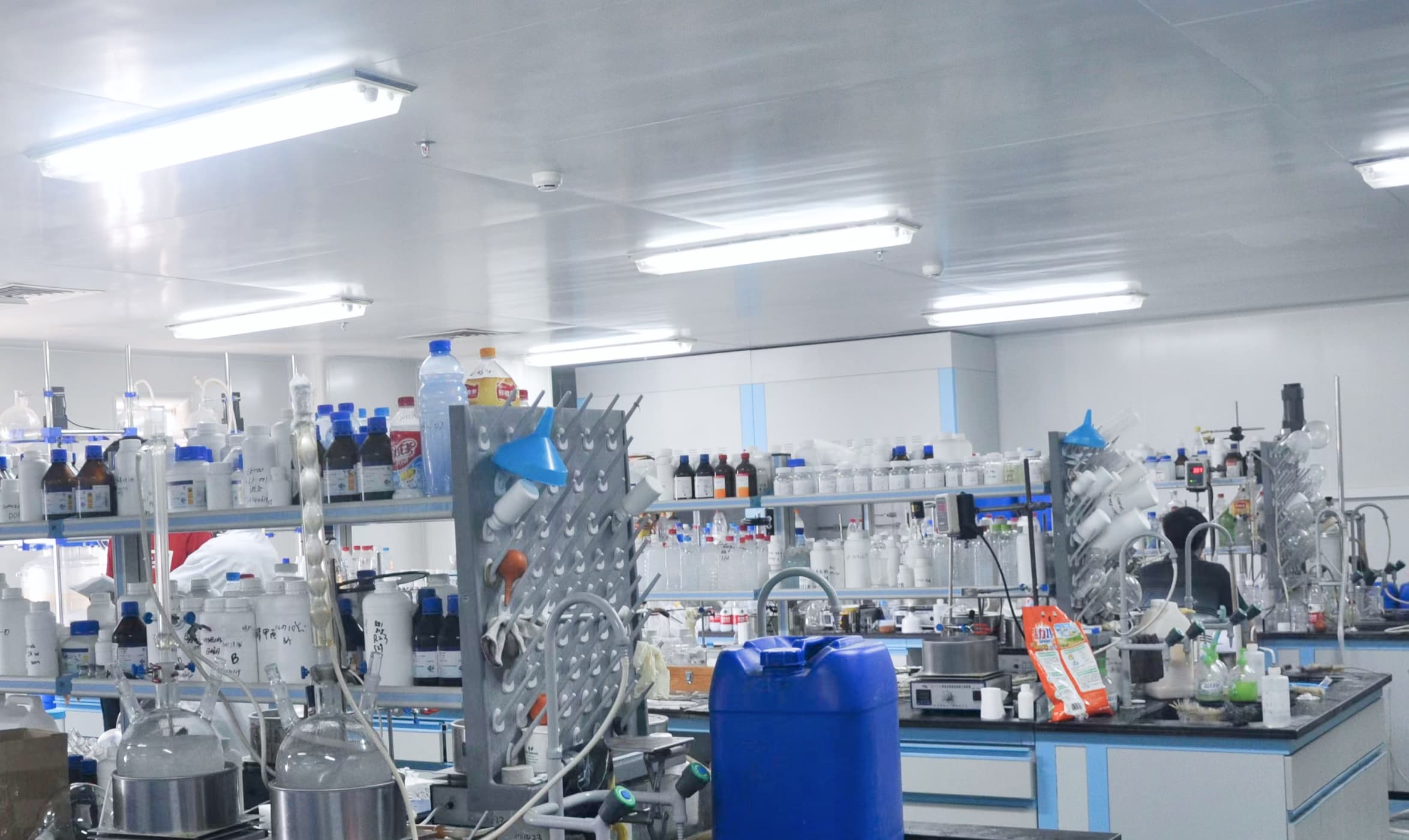
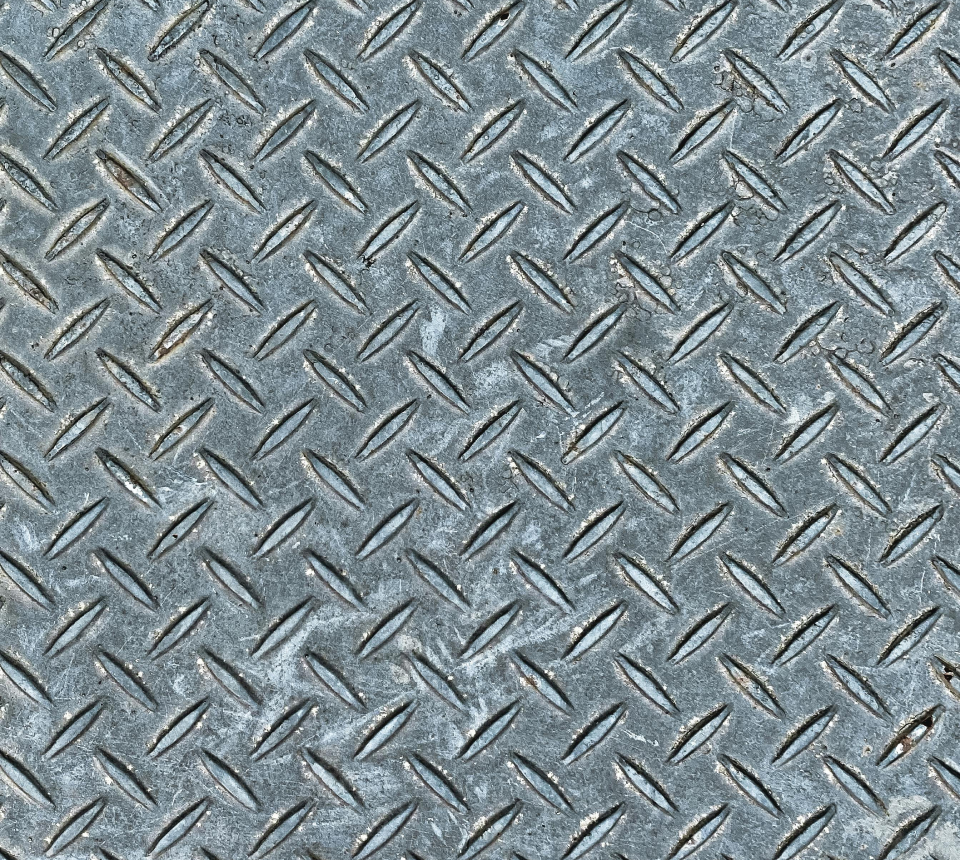
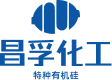
+86 27 8439 6550
+86 181 6277 0058
sales@cfsilanes.com
Optics Valley Bio-City
No. 666, Gaoxin Avenue
Hongshan District, Wuhan City
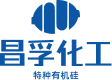
+86 27 8439 6550 | +86 181 6277 0058
sales@cfsilanes.com
Optics Valley Bio-City
No. 666, Gaoxin Avenue
Hongshan District, Wuhan City
Copyright © Hubei ChangFu Chemical Co., Ltd. All Rights