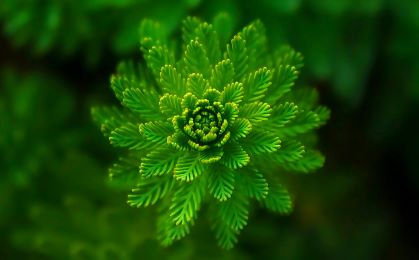
Contact Changfu Chemical Now!
+86 27 8439 6550 | +86 181 6277 0058
Understanding the Different Types of Silicone Additives and Their Functions
Introduction: The Role of Silicone Additives in Modern Industries
Silicone additives are a key component in the formulation of many chemical products, enhancing their performance, durability, and versatility across industries such as automotive, cosmetics, and food packaging.
Silicone additives are versatile and essential compounds used in a variety of industries to enhance the performance of materials and products. Derived from silicon, these additives are chemically stable, flexible, and offer a unique set of properties that make them indispensable in countless applications. Whether it's improving the durability of industrial coatings, enhancing the performance of rubber products, or even optimizing the processing of food packaging, silicone additives have proven their worth as multifunctional agents in a wide range of sectors.
In this blog, we will dive into the different types of silicone additives and their specific functions, exploring how these compounds are utilized across industries to improve product performance, safety, and sustainability.
What Are Silicone Additives?
Silicone additives are chemical compounds made from silicon, oxygen, carbon, hydrogen, and other elements. They are typically used in small amounts (often less than 1% of a formulation) to modify the properties of other materials, such as polymers, rubbers, coatings, lubricants, and more. These additives are designed to improve specific characteristics like flexibility, temperature resistance, water repellency, and surface properties.
These additives are essential for achieving high-performance results in various manufacturing processes, from automotive production to food packaging, and even in the cosmetics industry. Some common forms of silicone additives include emulsions, oils, resins, and rubber compounds.
Types of Silicone Additives and Their Functions
1.Silicone Surfactants
Function: Silicone surfactants are used primarily to modify the surface tension of liquids, which makes them ideal for use in emulsions and foams. These additives play a crucial role in improving wetting properties and enhancing the spreading of liquids over surfaces.
Applications:
- Cosmetics: Silicone surfactants are used in personal care products such as shampoos, conditioners, and lotions to improve spreadability and enhance product texture.
- Textiles: They are used to treat fabrics, making them water-repellent and improving the smoothness and softness of the material.
- Coatings: Silicone surfactants are often used in paints and coatings to improve the adhesion and uniformity of application.
By reducing the surface tension of liquids, these silicone additives help products maintain a more stable and consistent performance.
2. Silicone Oils
Function: Silicone oils are fluids that provide excellent lubrication properties. They are often used to enhance the performance of various materials, particularly in situations where high-temperature stability or water resistance is crucial.
Applications:
- Automotive: Silicone oils are often used as lubricants in automotive parts such as gaskets, seals, and engine components to reduce friction and wear.
- Electronics: These oils help in insulating and protecting electronic components from heat and moisture, extending the lifespan of devices.
- Cosmetics: Used in skin care and hair products, silicone oils provide a silky feel without feeling greasy, making them ideal for use in serums and conditioners.
Silicone oils are prized for their low volatility, which allows them to maintain their lubricating and protective properties even under extreme conditions.
3. Silicone Resins
Function: Silicone resins are hard, heat-resistant polymers that are often used as coatings or adhesives. They offer superior heat resistance, chemical stability, and durability, making them ideal for use in harsh environments. Silicone resins can also impart water repellency and resistance to UV degradation.
Applications:
- Coatings: Silicone resins are commonly used in industrial and automotive coatings to provide a high degree of durability, weather resistance, and temperature stability.
- Electronics: They are used to encapsulate electronic components, protecting them from environmental factors such as moisture, heat, and dust.
- Construction: Silicone resins are used in building materials like sealants and paints, ensuring the long-term protection of surfaces from harsh weather conditions.
The unique combination of properties, such as heat resistance, low surface energy, and water repellency, makes silicone resins indispensable in demanding environments.
4. Silicone Rubber Additives
Function: Silicone rubber additives are designed to improve the physical and mechanical properties of silicone rubber, such as its elasticity, tensile strength, and resistance to temperature extremes. These additives enhance the performance of silicone rubber in various industrial applications.
Applications:
- Automotive: Silicone rubber is widely used in automotive seals, gaskets, and hoses. Silicone rubber additives improve these parts' ability to withstand extreme temperatures and weathering, ensuring long-lasting performance.
- Medical Devices: In medical devices like seals for surgical instruments or prosthetics, silicone rubber additives improve biocompatibility and durability.
- Construction and Manufacturing: Silicone rubber gaskets and seals, enhanced with silicone additives, provide reliable resistance to water, chemicals, and temperature extremes in industrial applications.
These additives contribute to the overall flexibility, longevity, and safety of silicone rubber products.
5. Silicone Defoamers and Anti-Foaming Agents
Function: Silicone defoamers and anti-foaming agents are used to control and reduce foam formation in various processes, particularly in industrial settings. These additives help to prevent foam from interfering with manufacturing operations or product quality.
Applications:
- Paints and Coatings: Silicone defoamers are often added to paint formulations to prevent air bubbles from forming during application, ensuring a smooth, even finish.
- Food and Beverage Processing: In food production, silicone anti-foaming agents are used to reduce foam in products like juices, syrups, and sauces, improving the consistency and visual appeal of the final product.
- Industrial Processes: In processes such as pulp and paper production, silicone defoamers help to minimize foam in machines, improving efficiency and product quality.
By eliminating unwanted foam, silicone defoamers ensure smoother production processes and better-quality end products.
6. Silicone Antioxidants
Function: Silicone antioxidants are used to prevent oxidation in silicone products, especially when exposed to heat, UV radiation, or ozone. These additives help extend the shelf life of silicone-based products by preventing the degradation of the material over time.
Applications:
- Rubber and Elastomers: In automotive seals and industrial gaskets, silicone antioxidants protect against oxidation, maintaining the strength and flexibility of the rubber over long periods.
- Coatings and Paints: Used in paint formulations to enhance the durability and weather resistance of exterior coatings.
- Medical Devices: Silicone antioxidants help to preserve the integrity and safety of medical devices by preventing material degradation.
These antioxidants are essential for ensuring that silicone products maintain their properties and performance even under challenging conditions.
7. Silicone Crosslinking Agents
Function: Crosslinking agents are additives that help to chemically bond silicone molecules together, forming a stronger and more durable material. These agents are typically used to improve the structure and integrity of silicone elastomers, making them more resistant to heat, moisture, and other external factors.
Applications:
- Medical Devices: Silicone crosslinking agents are crucial in creating biocompatible materials for medical applications, such as implants or prosthetics.
- Electronics: They are used in encapsulation materials for electronic components to provide better protection against environmental elements like moisture and dust.
- Automotive Parts: Crosslinked silicone rubber is used for engine seals, electrical connectors, and weather-resistant gaskets, offering enhanced performance and reliability.
By improving the strength and resilience of silicone materials, crosslinking agents help create products that can endure harsher conditions.
Why Are Silicone Additives So Important?
Silicone additives play a pivotal role in the formulation of high-performance products across a range of industries. Their ability to modify and enhance the properties of materials—whether it’s improving water repellency, increasing temperature resistance, or adding flexibility—makes them indispensable in product development.
These additives are also crucial for meeting evolving consumer demands, including the need for sustainable, eco-friendly solutions. Many silicone additives are chemically stable and have low toxicity, making them safe for use in applications like food packaging, medical devices, and personal care products.
Moreover, with industries becoming increasingly global and diverse, silicone additives allow manufacturers to create versatile products that can withstand the rigors of various environmental conditions, from extreme heat to intense moisture, without compromising performance or longevity.
Conclusion: The Future of Silicone Additives
The use of silicone additives is expected to continue growing as industries look for ways to enhance the performance, safety, and sustainability of their products. As manufacturers seek to innovate and meet more complex demands, silicone additives will play a central role in improving product functionality and performance.
With ongoing research and development in silicone technologies, we are likely to see even more specialized additives designed to meet the unique needs of specific industries. From automotive to food processing, construction to electronics, silicone additives are poised to remain a cornerstone of product development in the years to come.
In conclusion, understanding the different types of silicone additives and their functions is crucial for industries seeking to improve the quality and performance of their products. By leveraging the unique properties of silicone additives, businesses can ensure their products meet the highest standards of efficiency, safety, and durability.
FAQs
1. What are silicone additives made from?
Silicone additives are typically made from silicon, oxygen, carbon, hydrogen, and other elements. These components create a stable and flexible compound suitable for a wide range of applications.
2. Are silicone additives eco-friendly?
Many silicone additives are considered eco-friendly due to their low toxicity and long-lasting properties. However, the environmental impact depends on the specific formulation and how it is used.
3. What industries use silicone additives the most?
Silicone additives are widely used in industries such as automotive, construction, electronics, medical devices, food packaging, and cosmetics.
4. Can silicone additives be used in food packaging?
Yes, silicone additives are commonly used in food packaging to enhance product durability, flexibility, and water resistance, ensuring that the packaging meets safety standards.
5. How do silicone additives improve product performance?
Silicone additives improve product performance by enhancing properties such as temperature resistance, flexibility, water repellency, and durability, making products more reliable and longer-lasting.
Popular Silicon Compounds
Popular Silicon Compounds
Related News & Blog
Related News & Blog
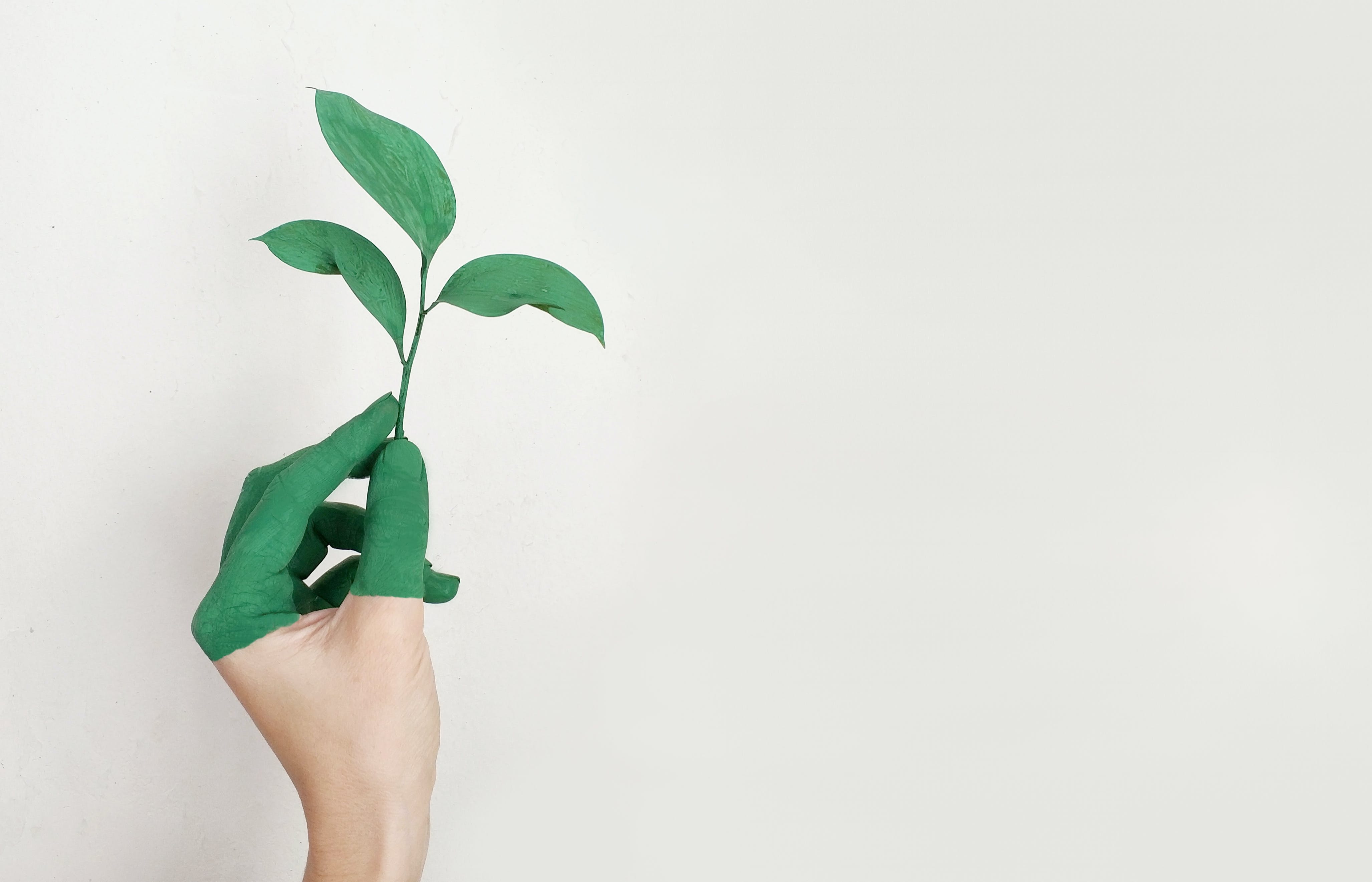
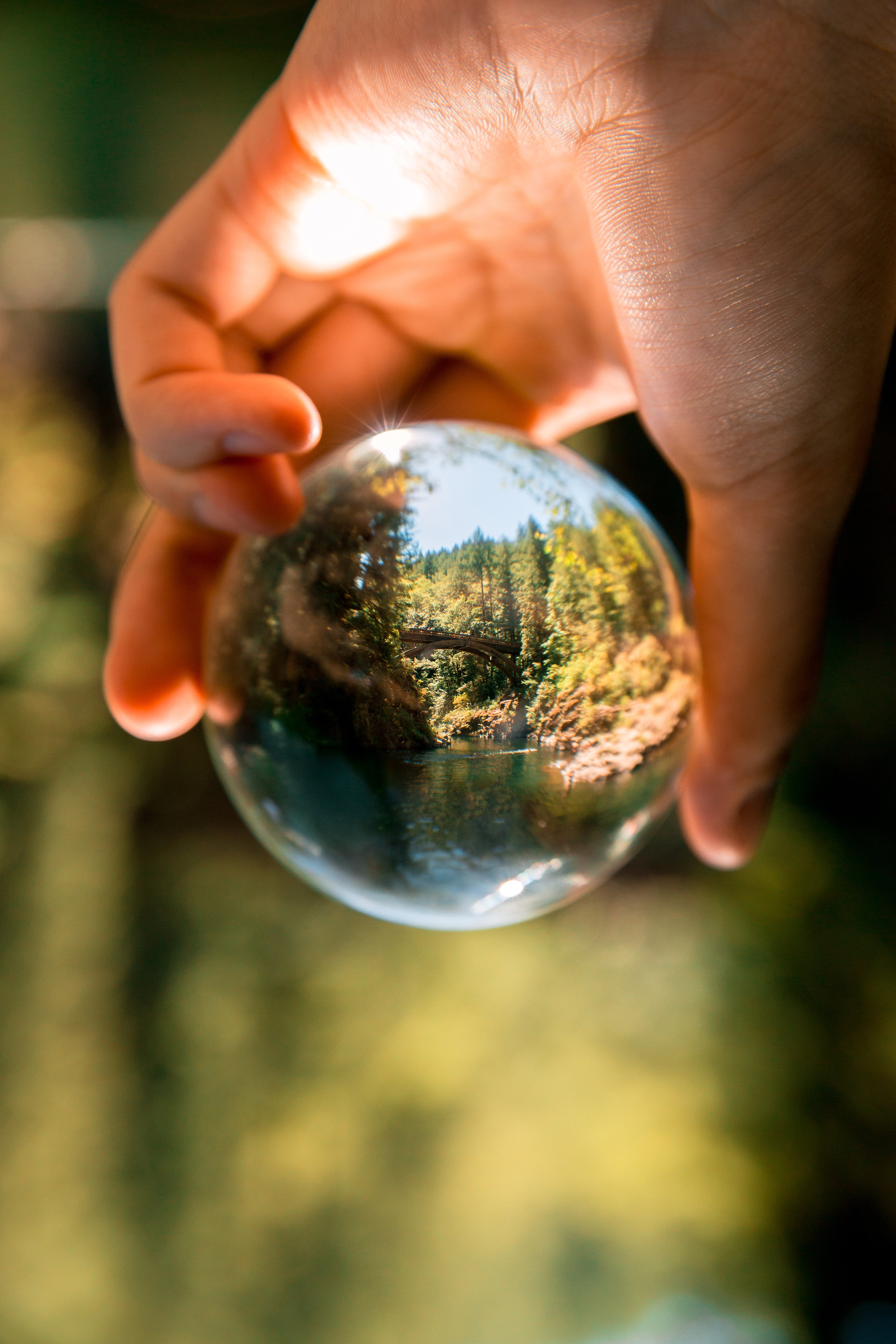
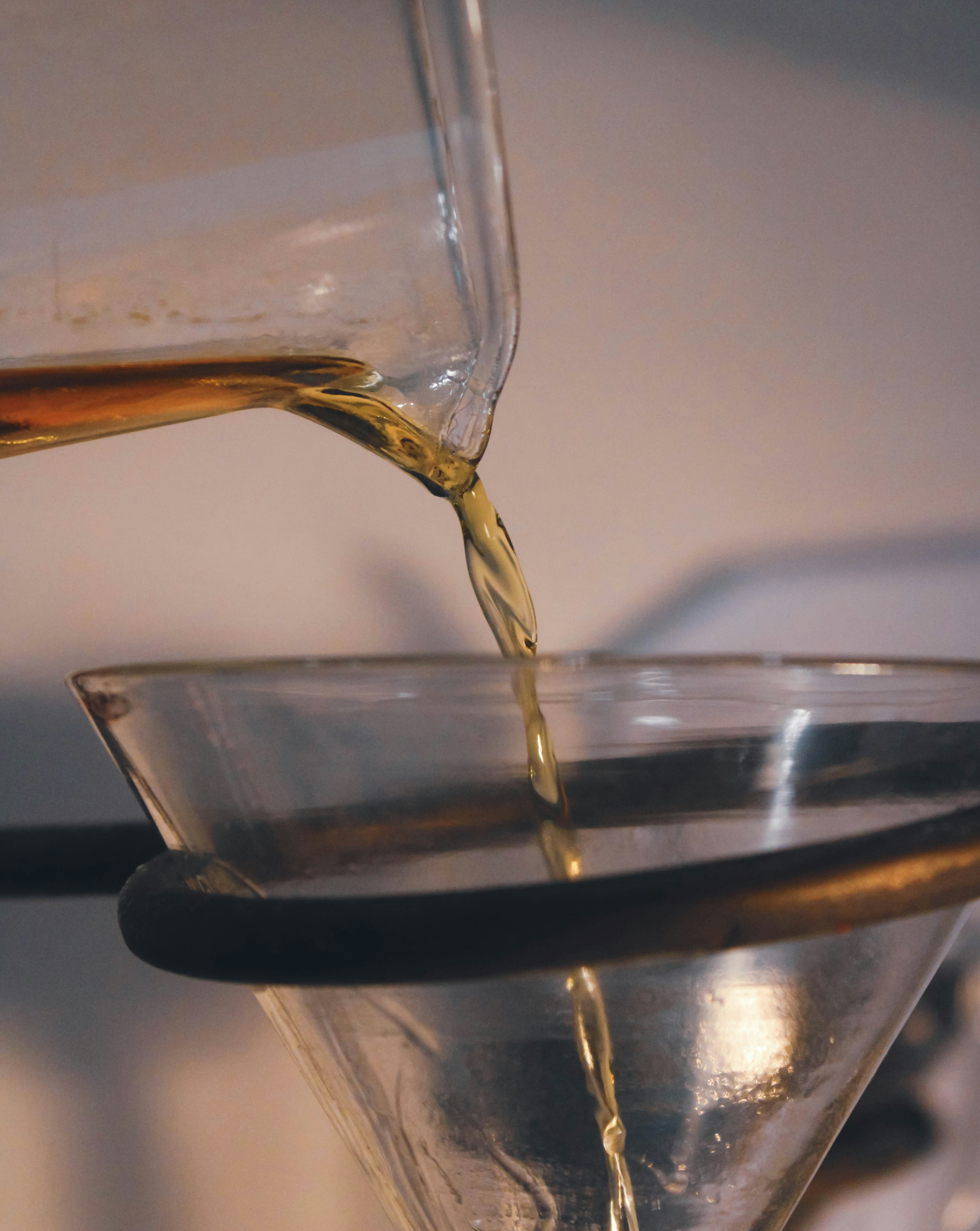
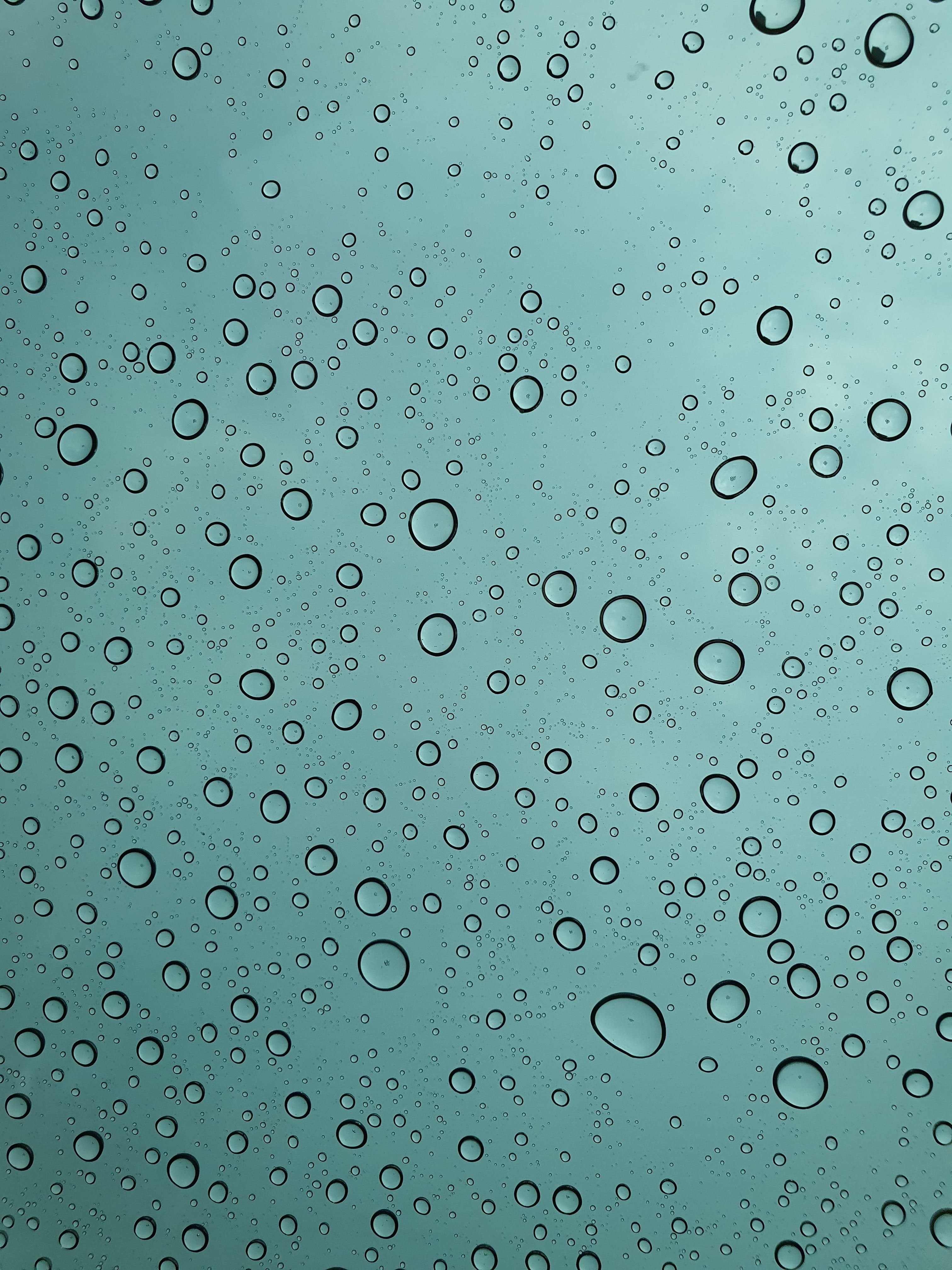
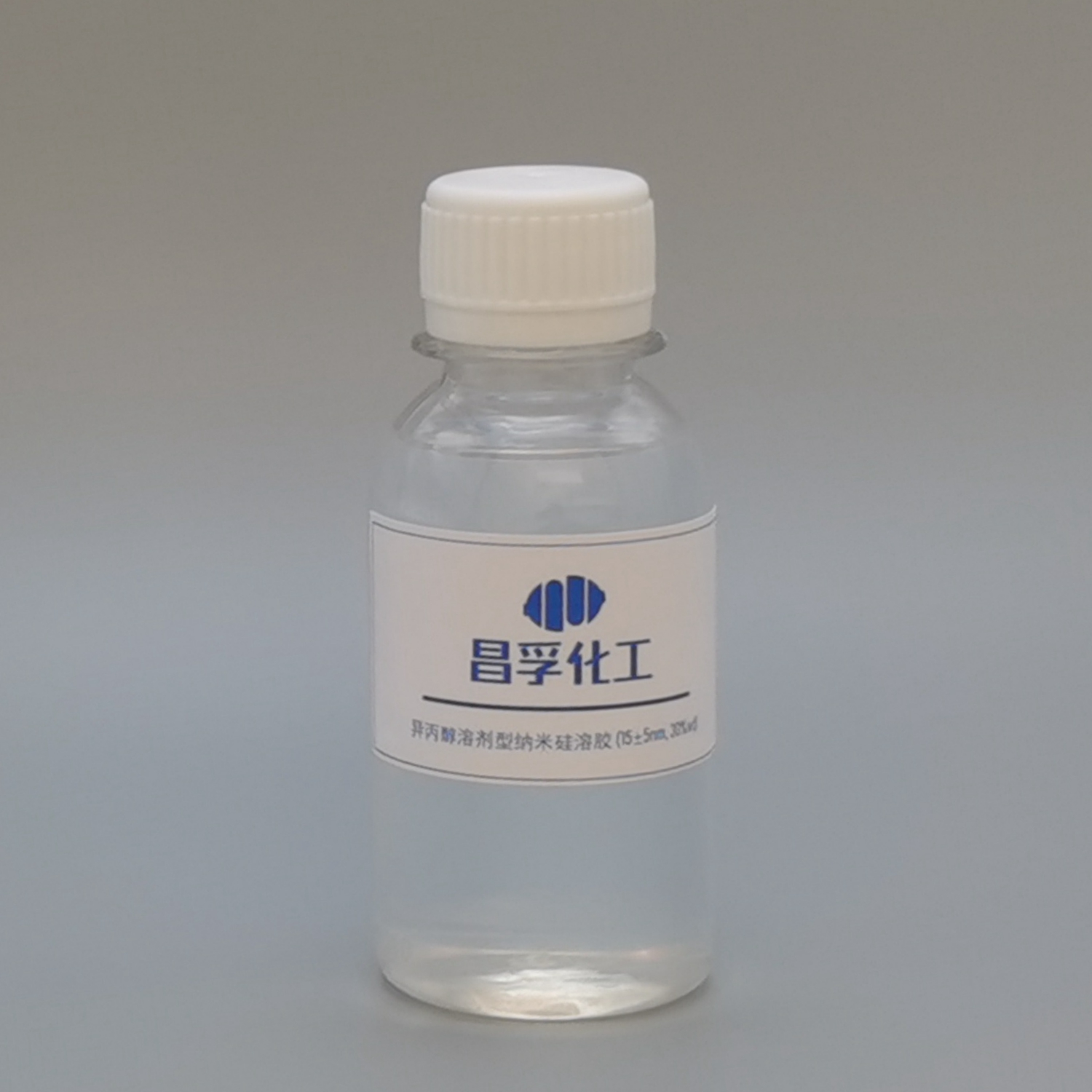
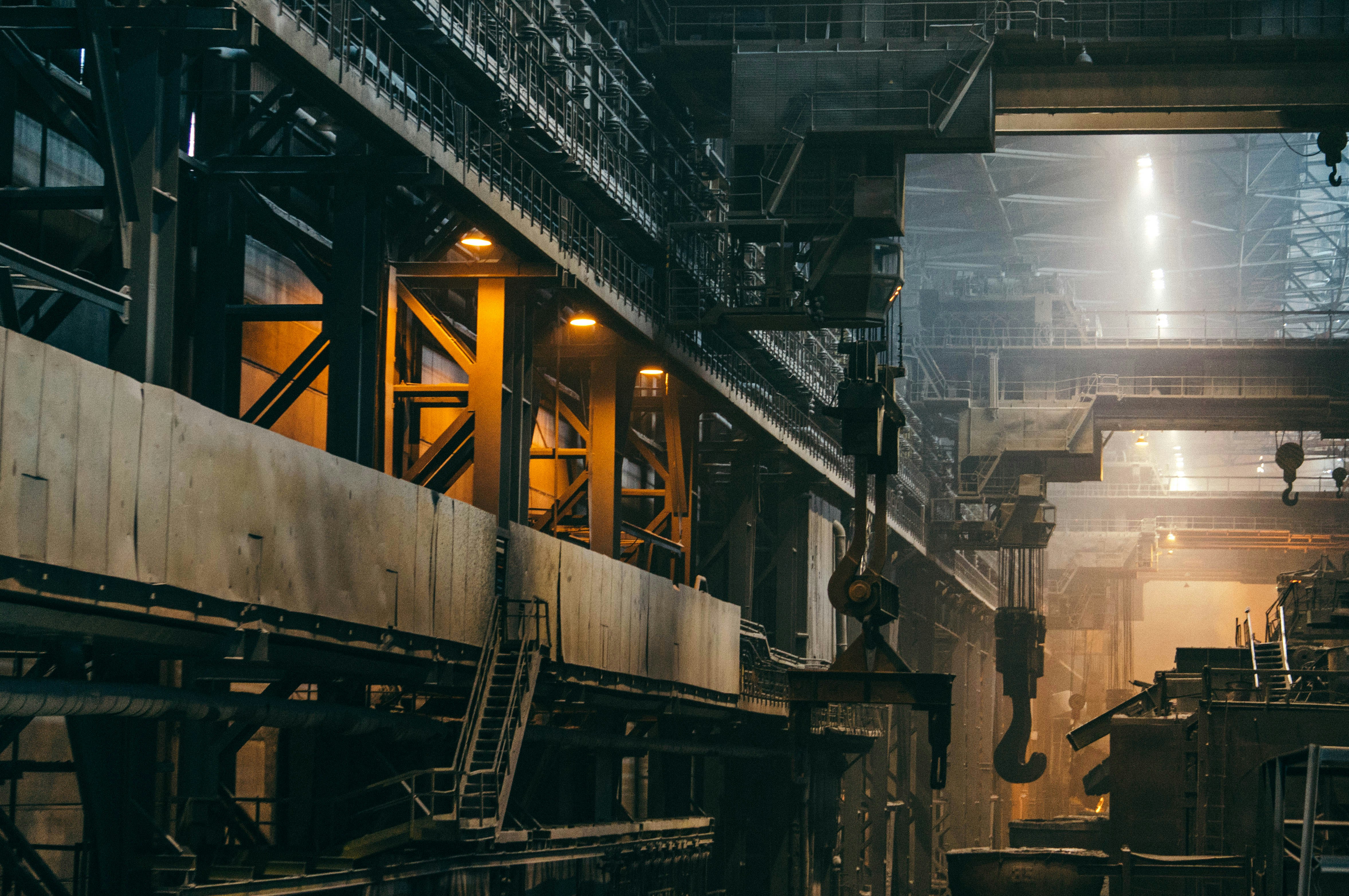
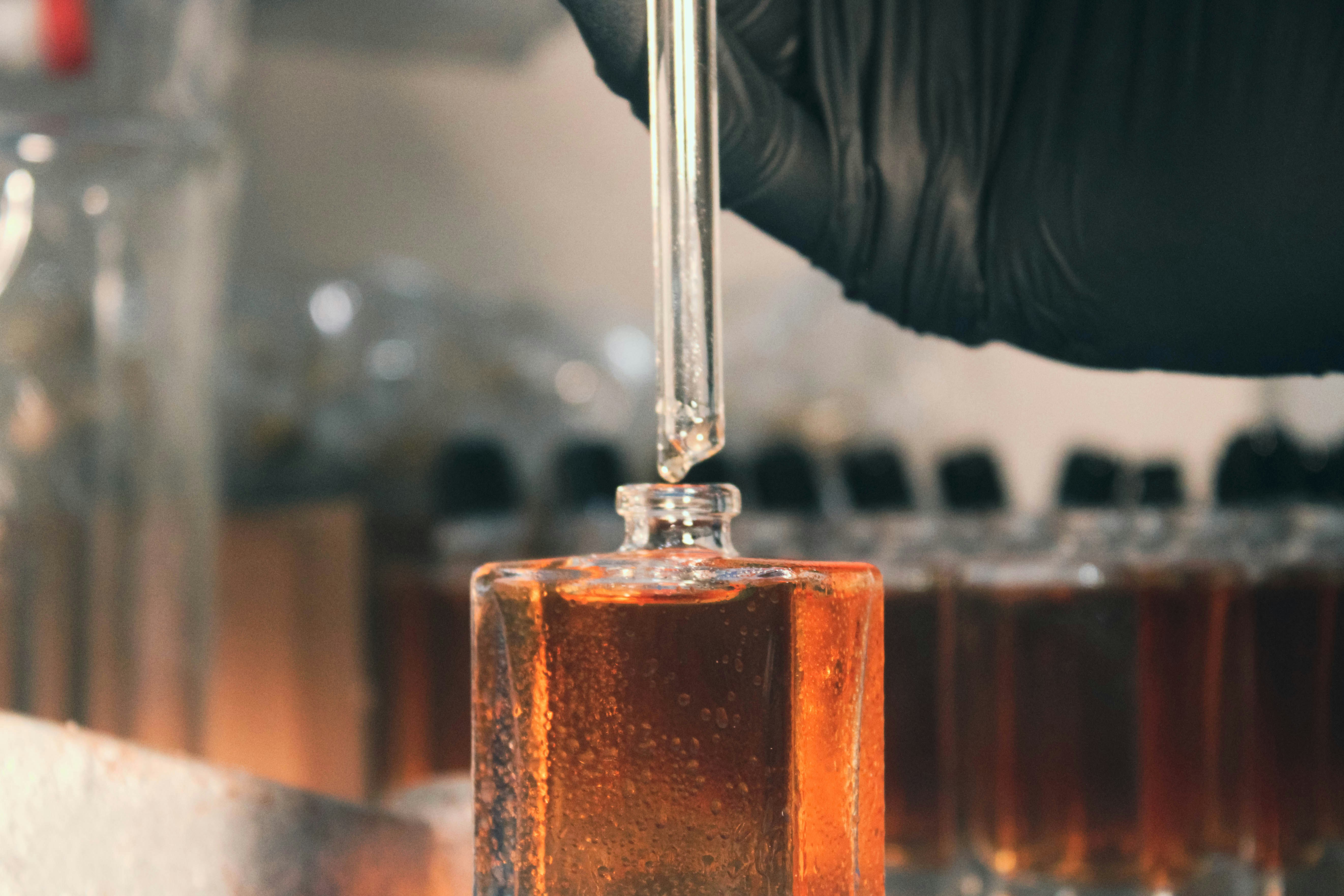
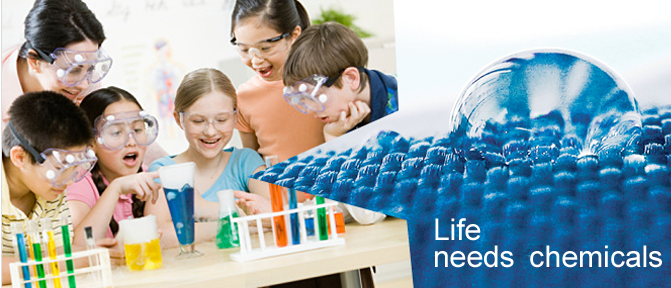

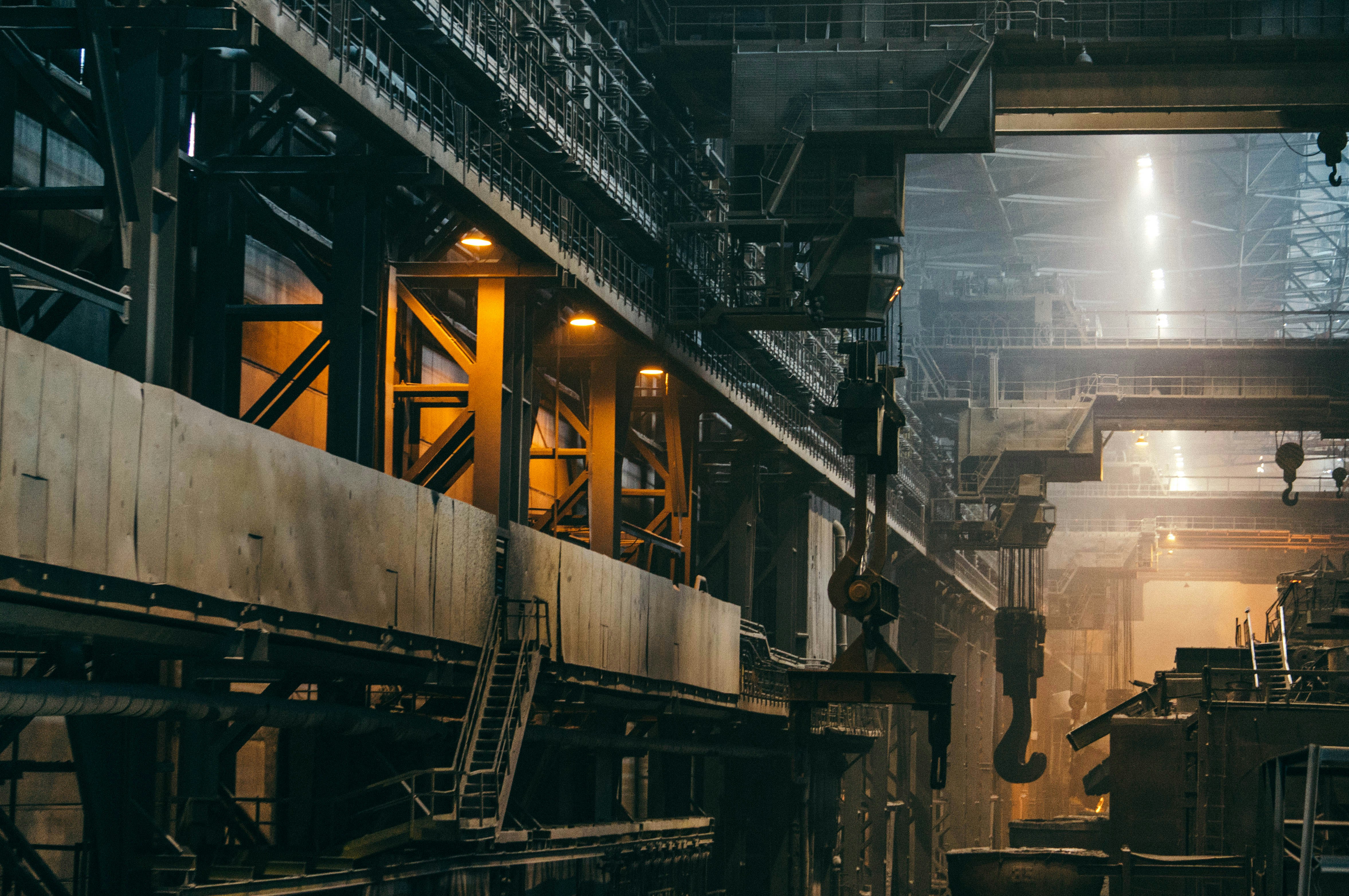
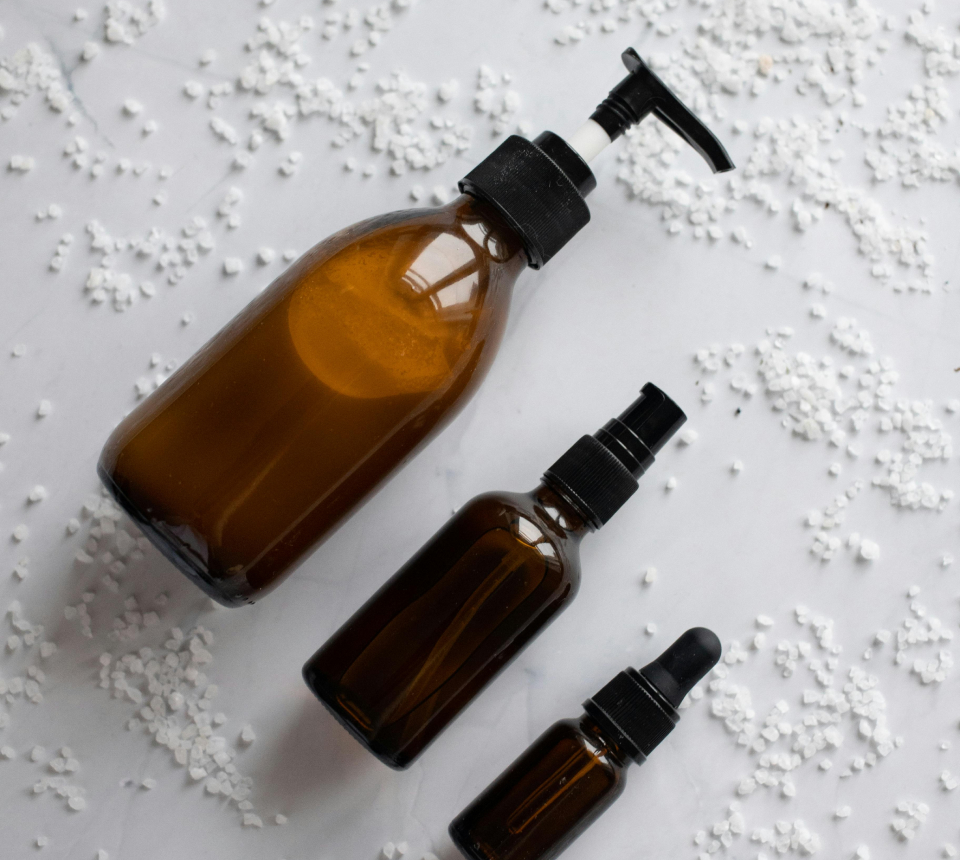
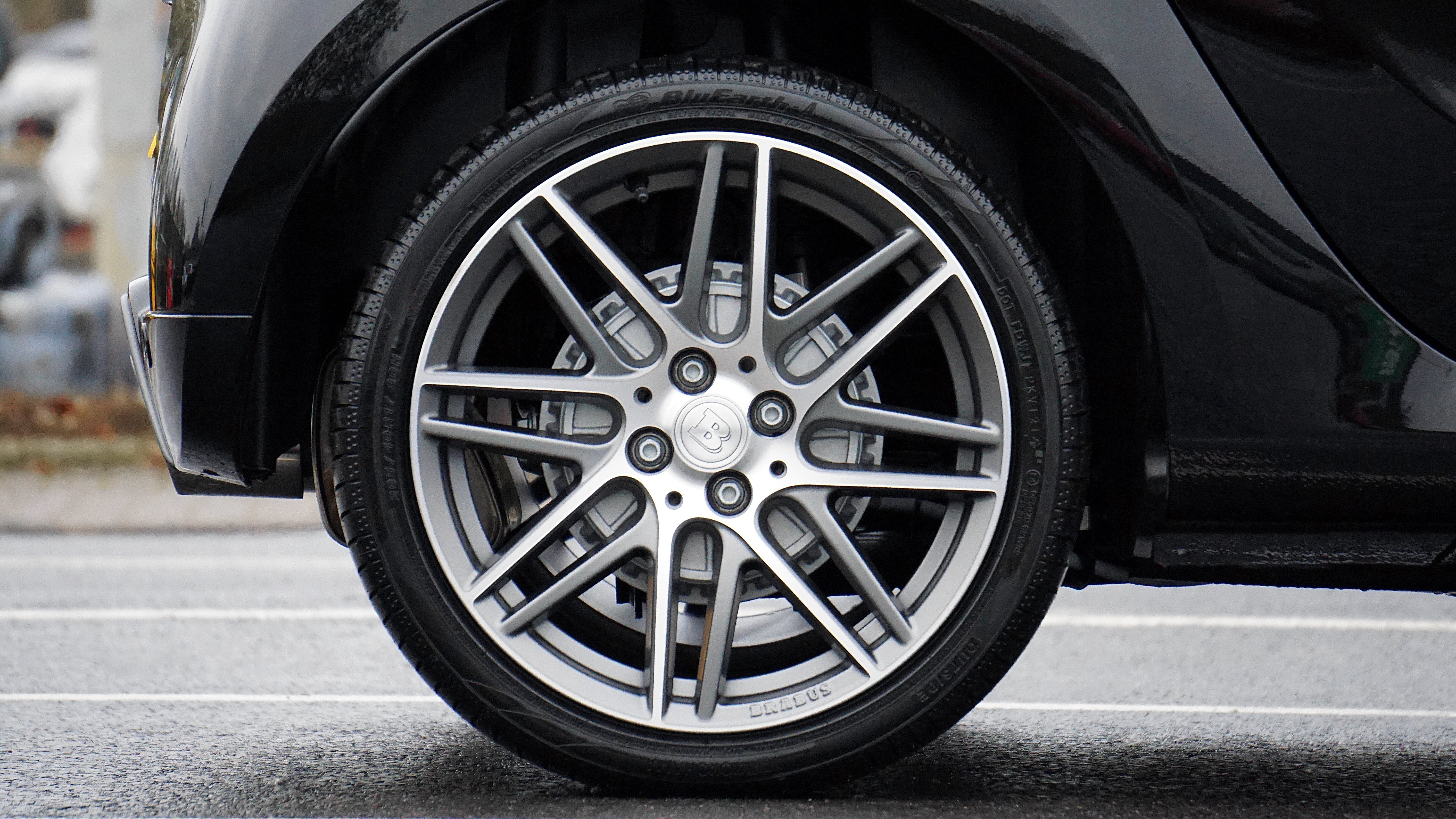
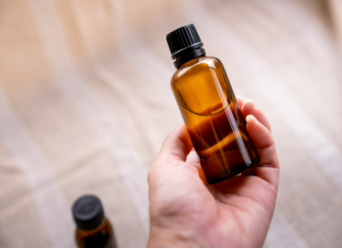
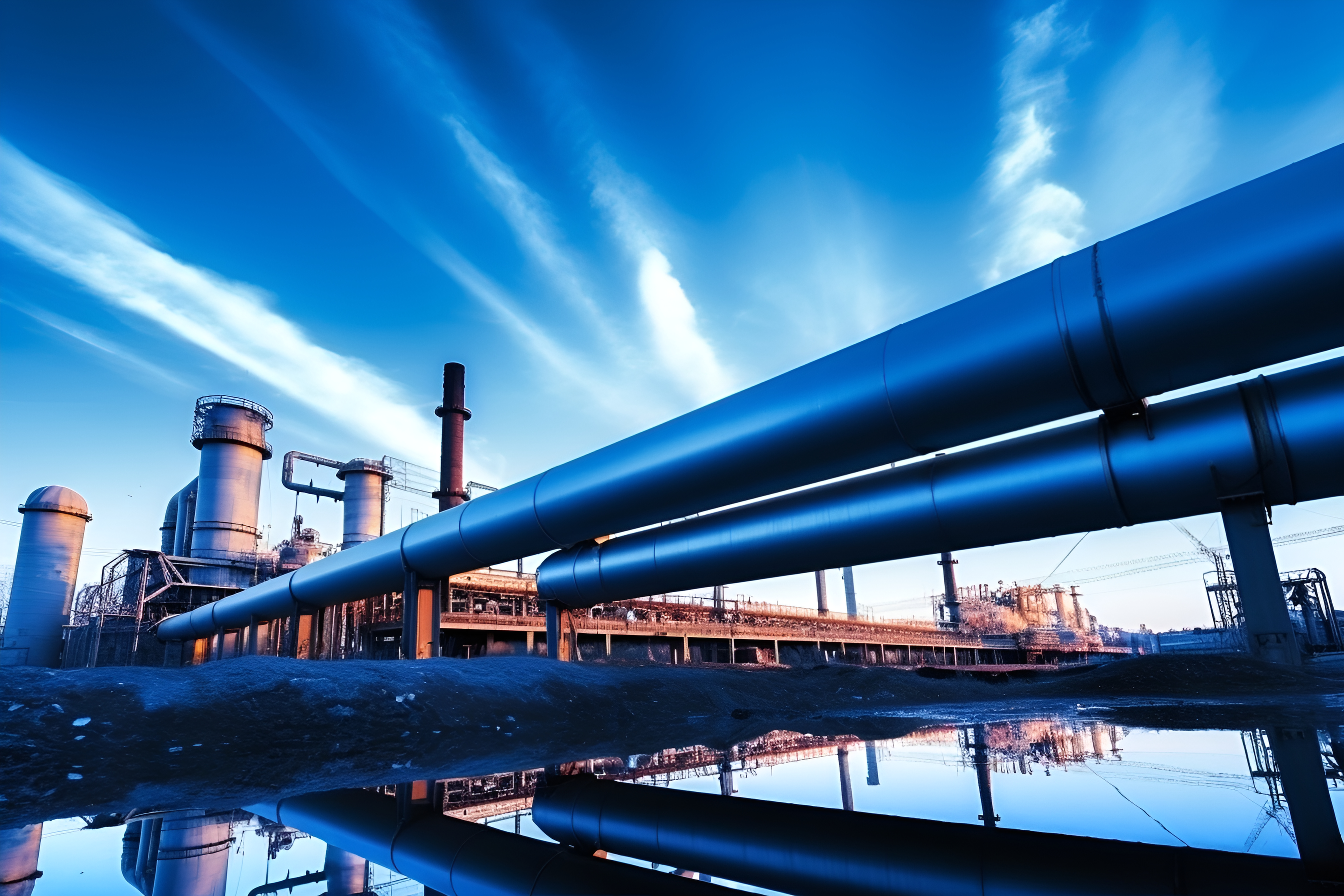

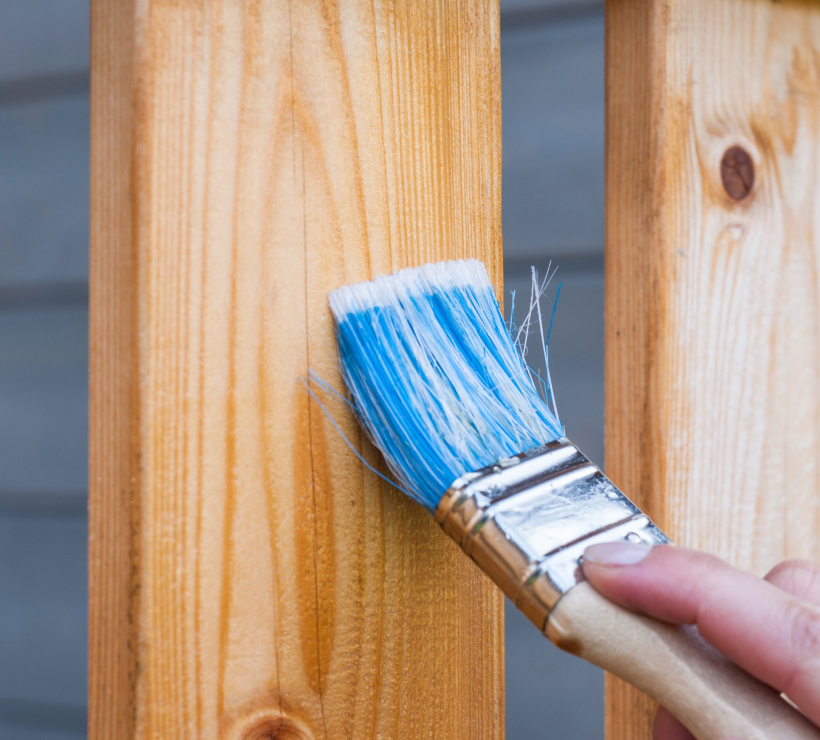
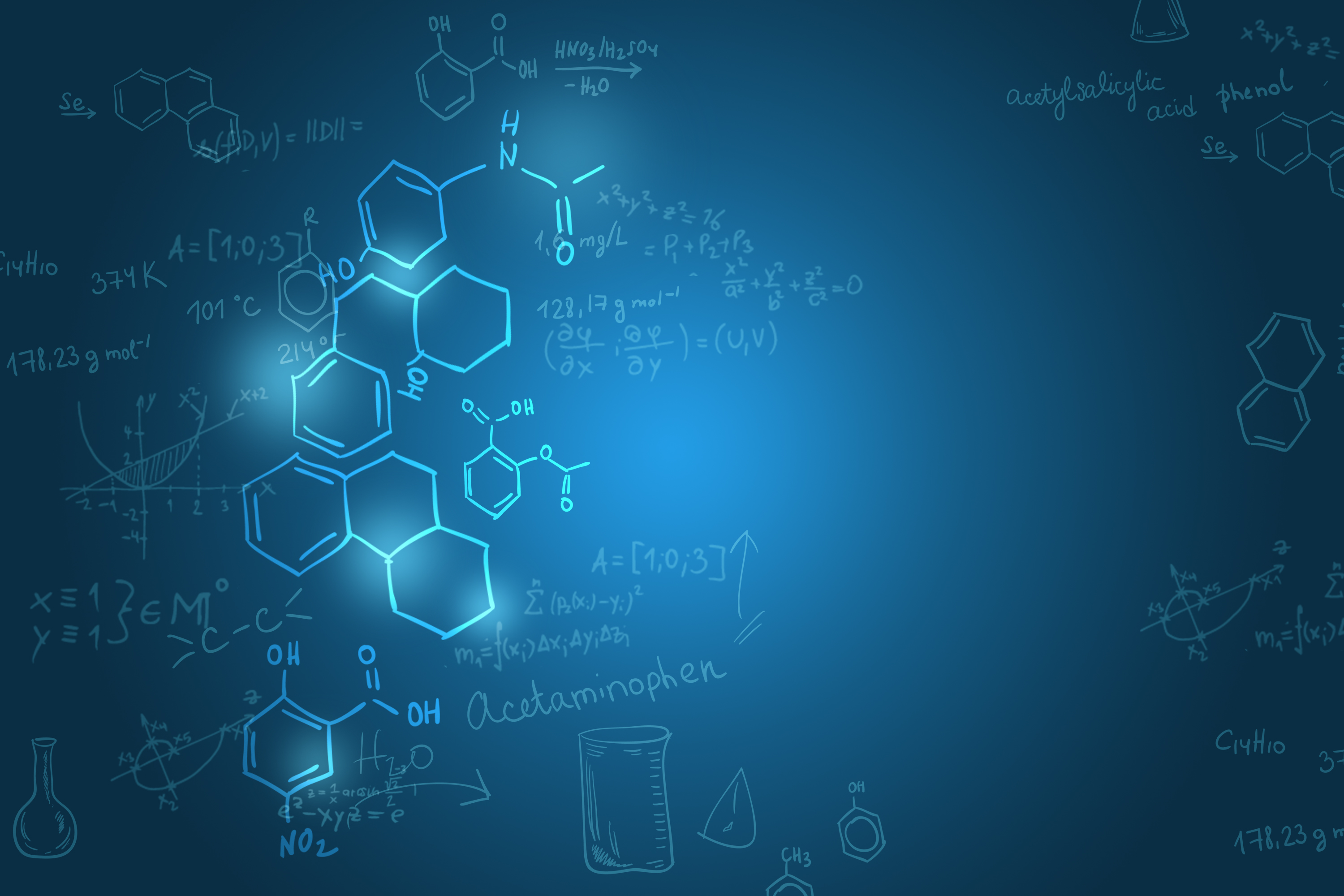
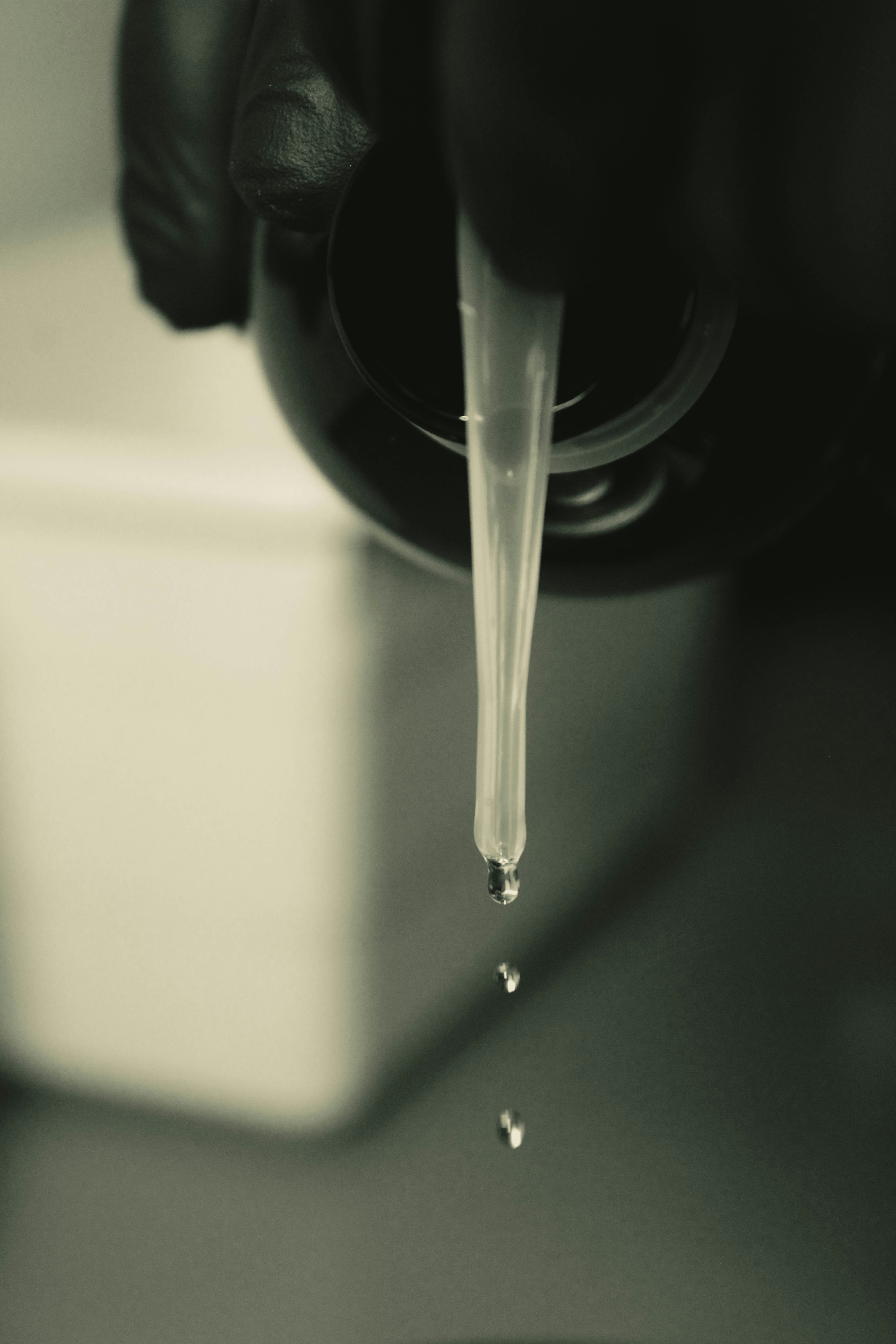
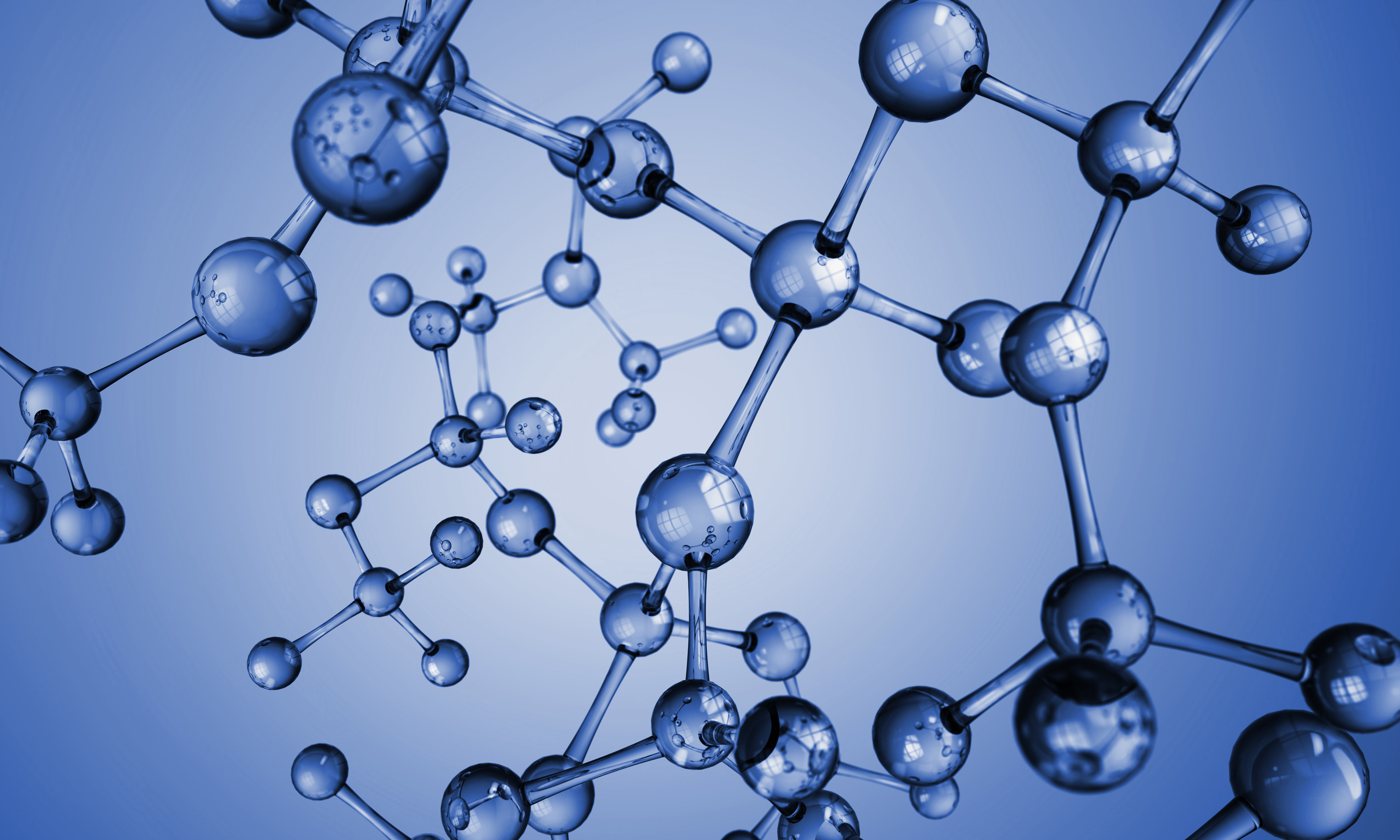
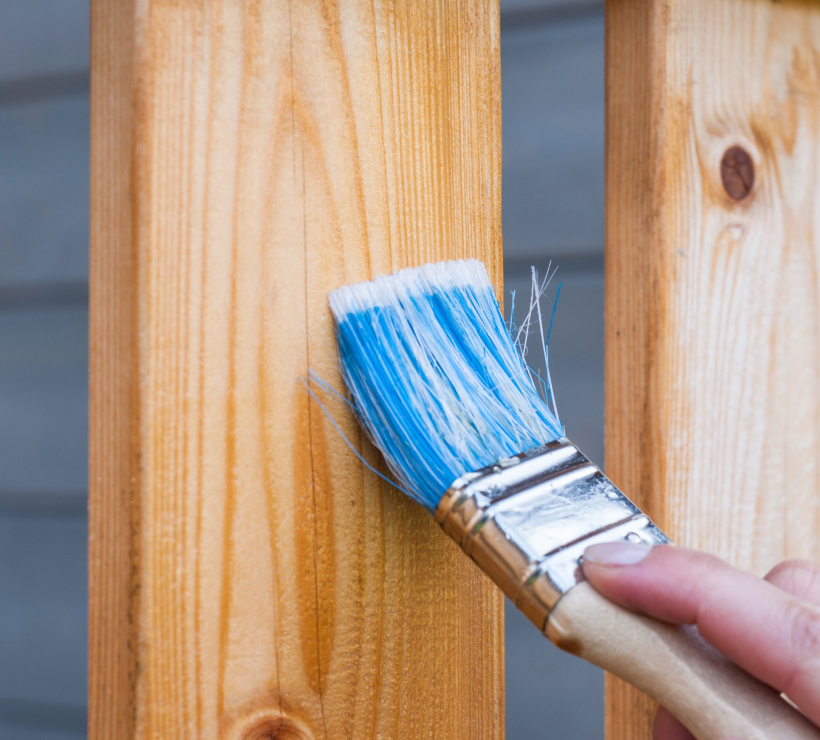

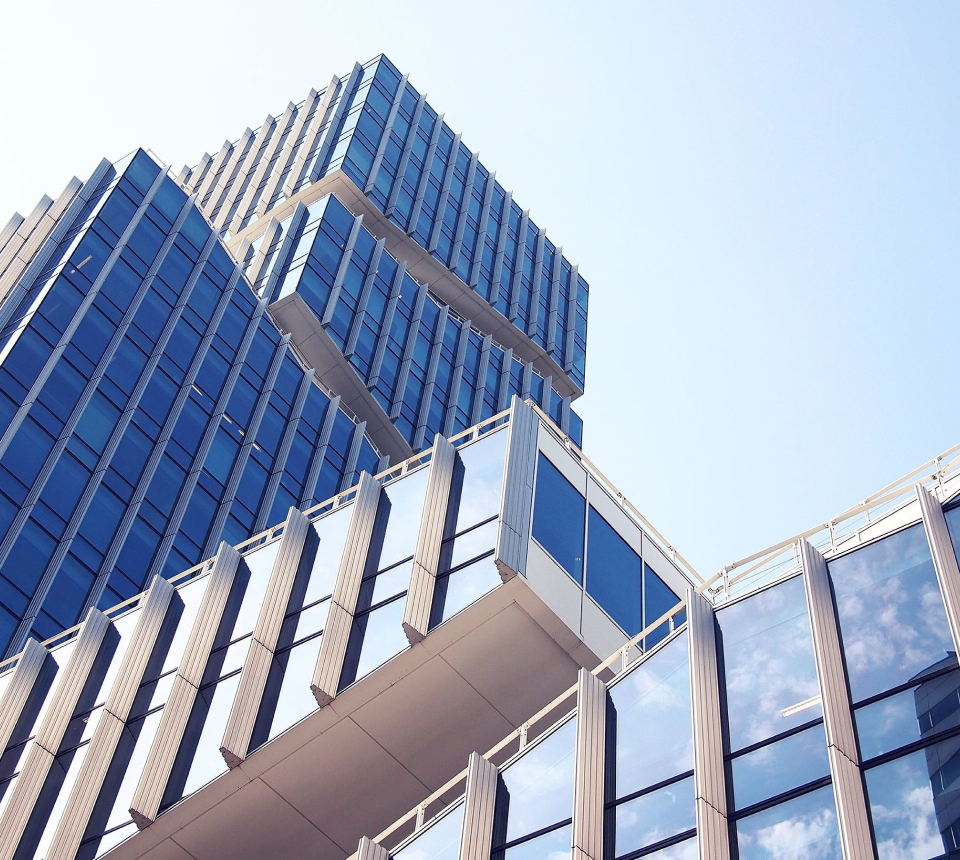
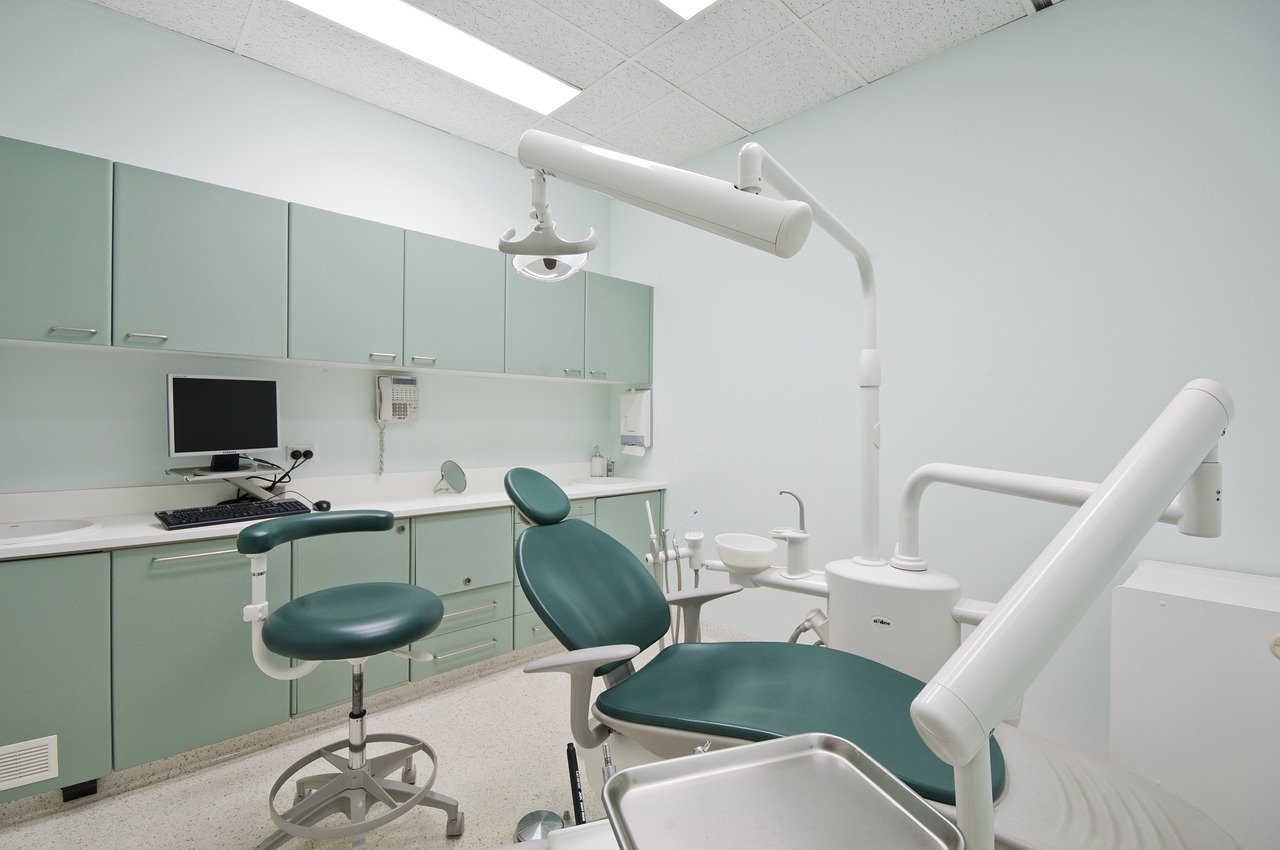
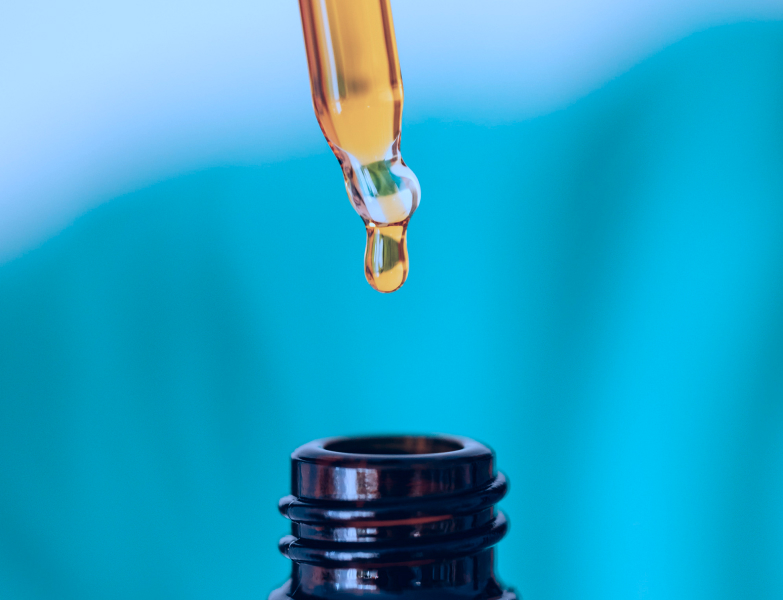
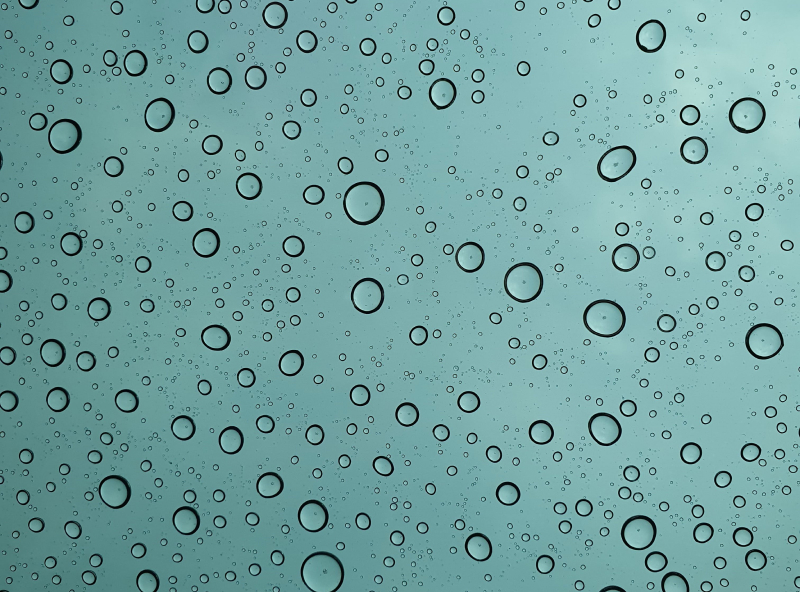
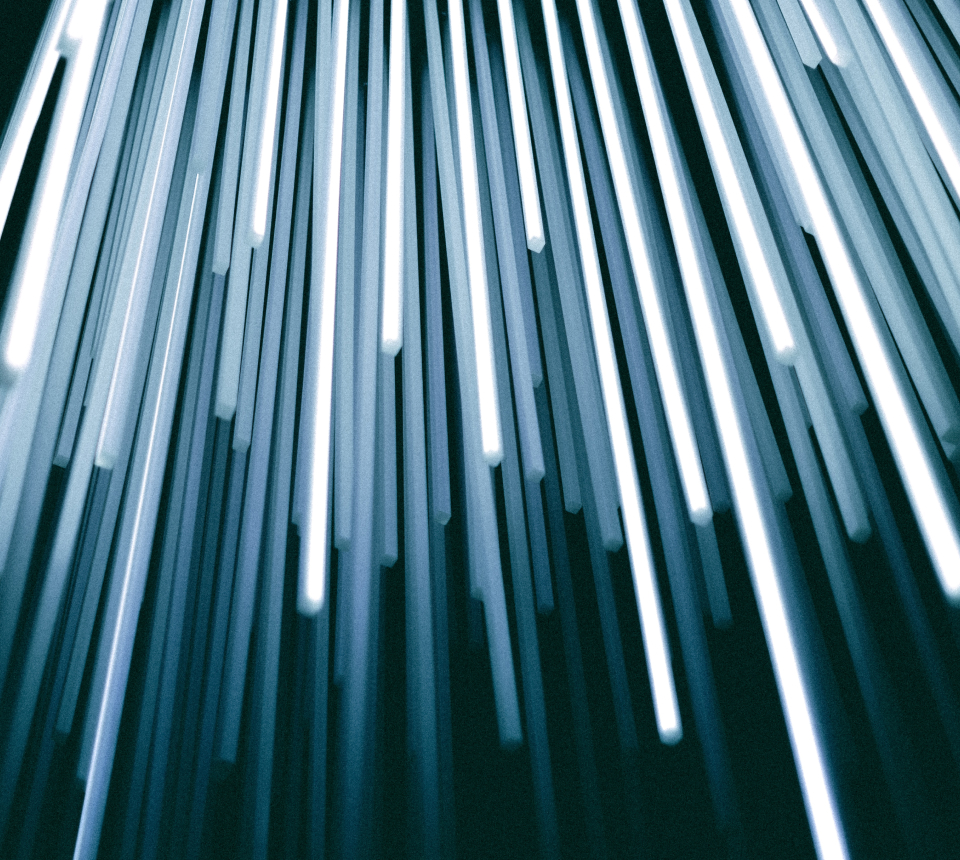
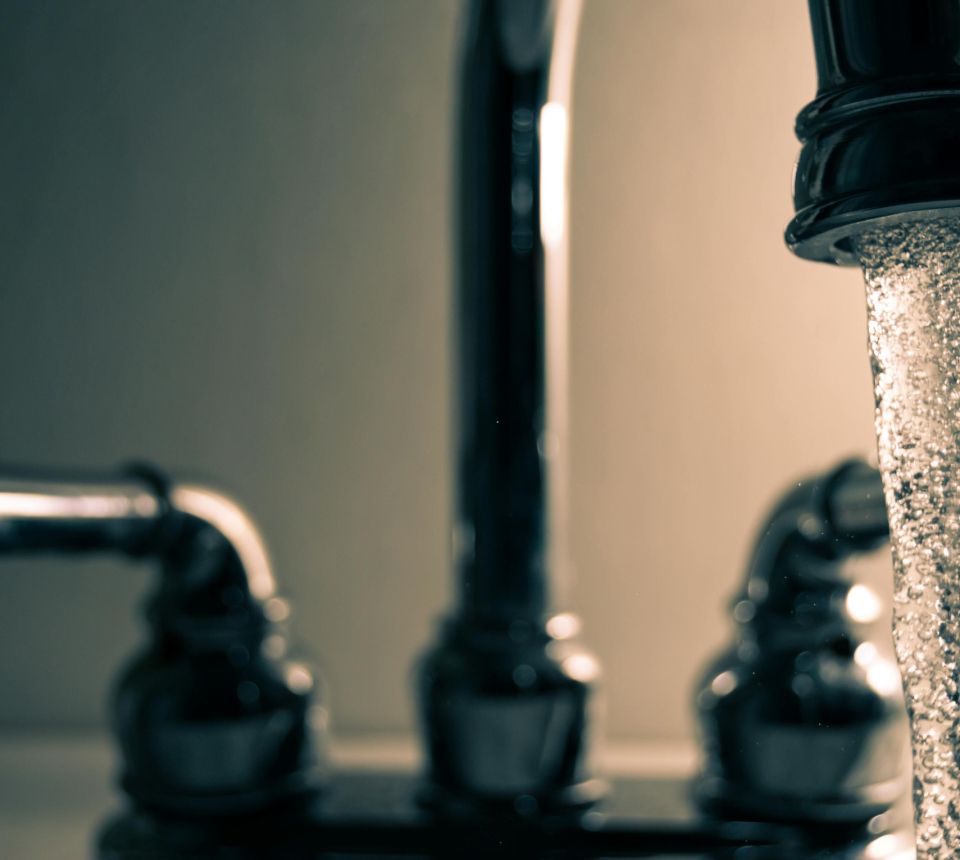
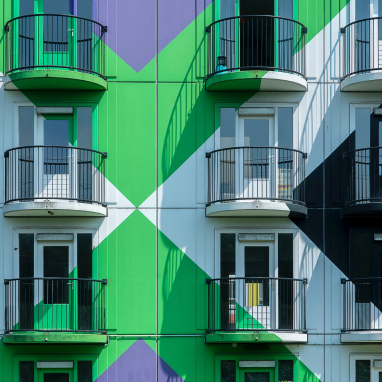
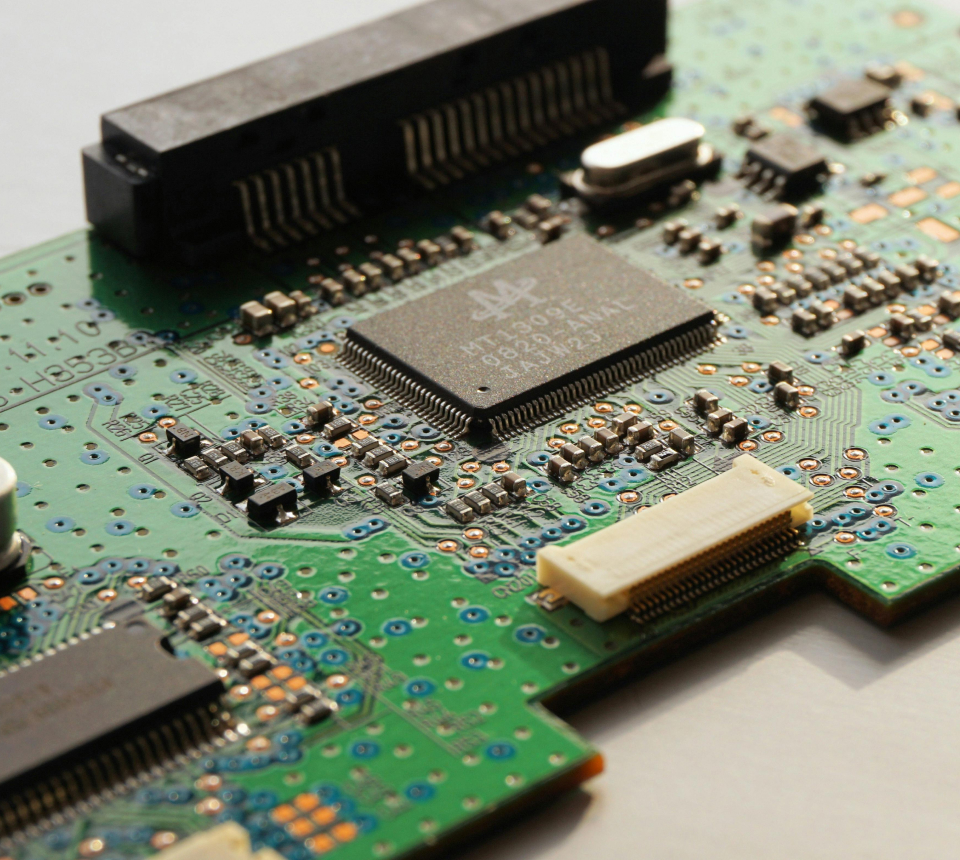
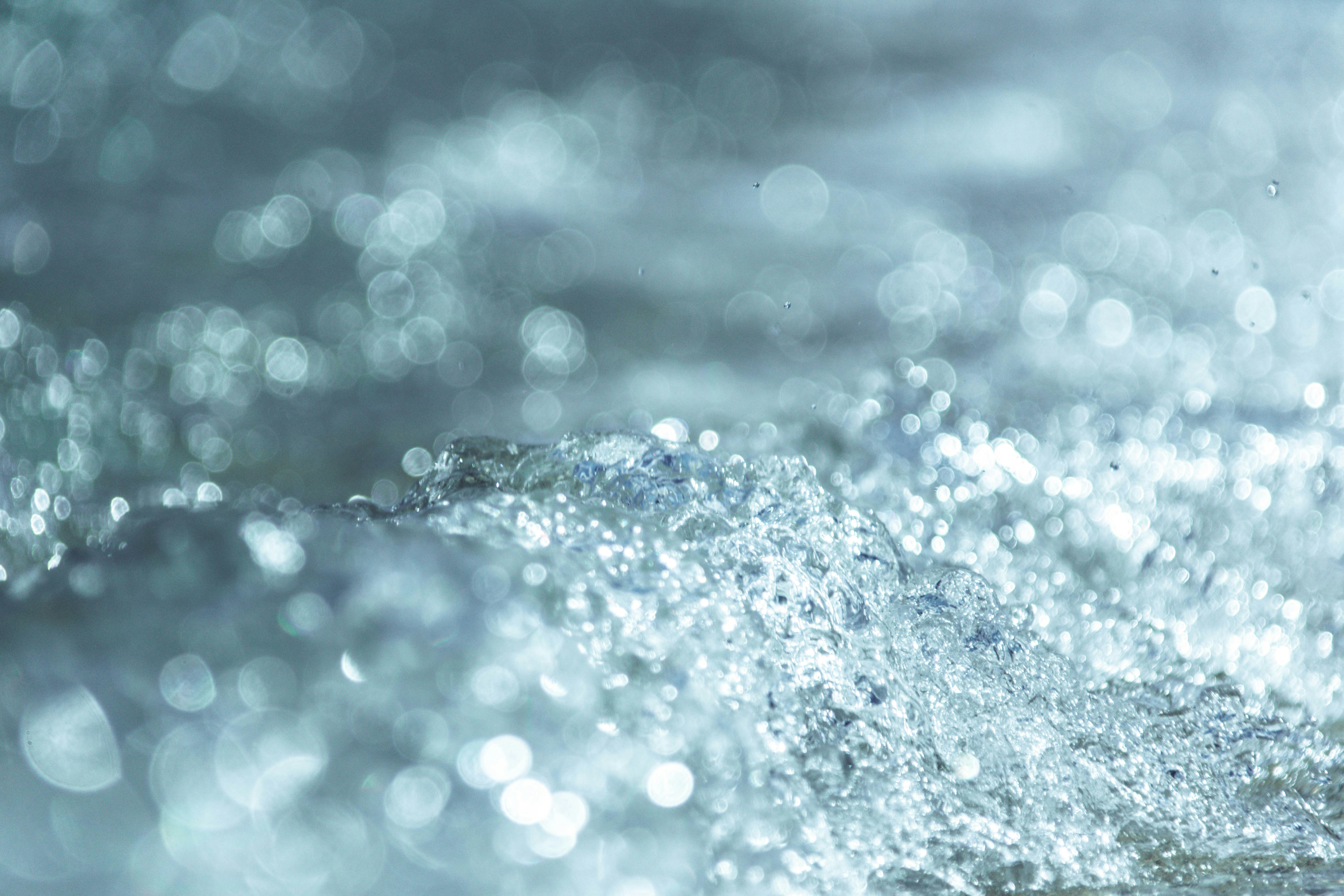
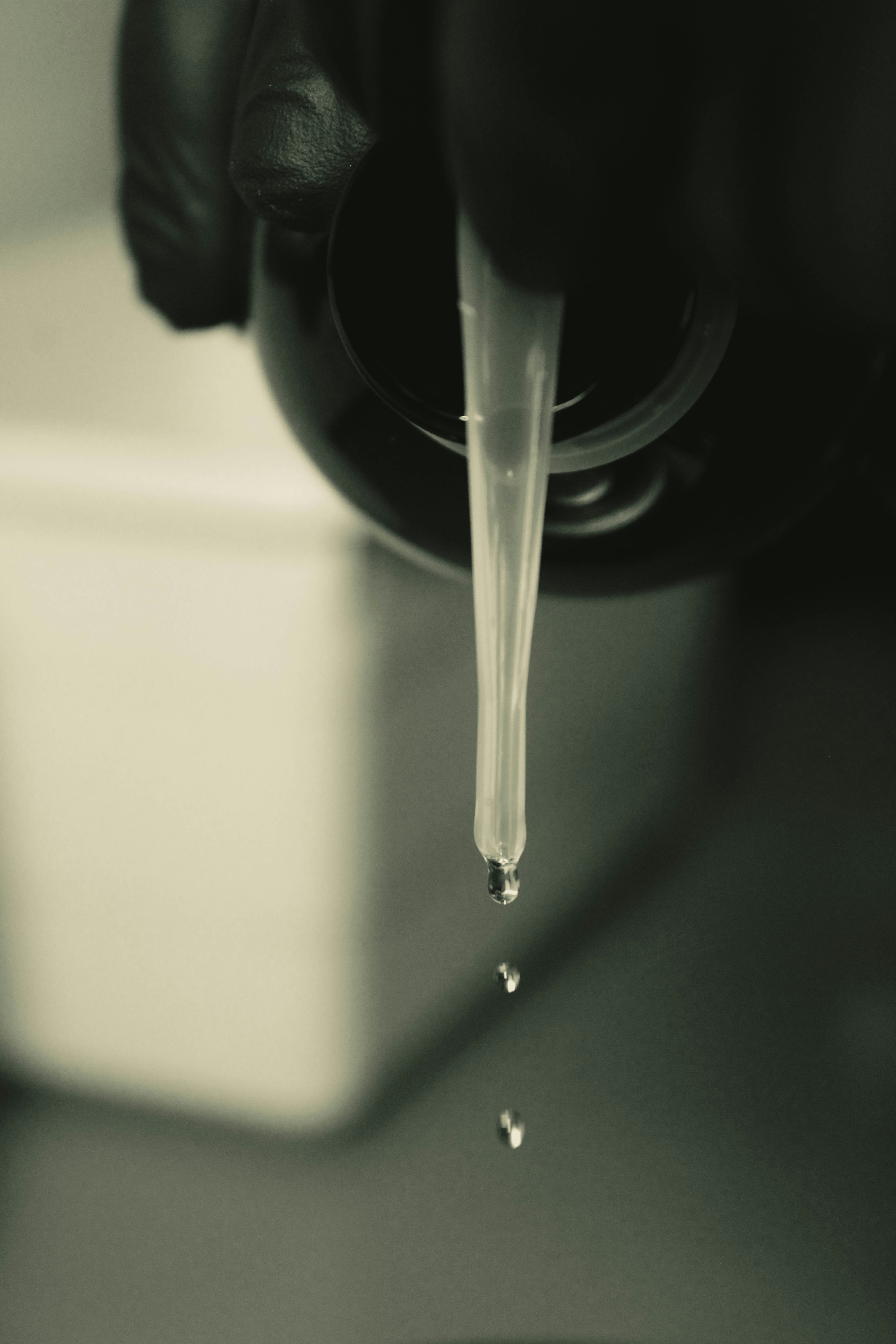
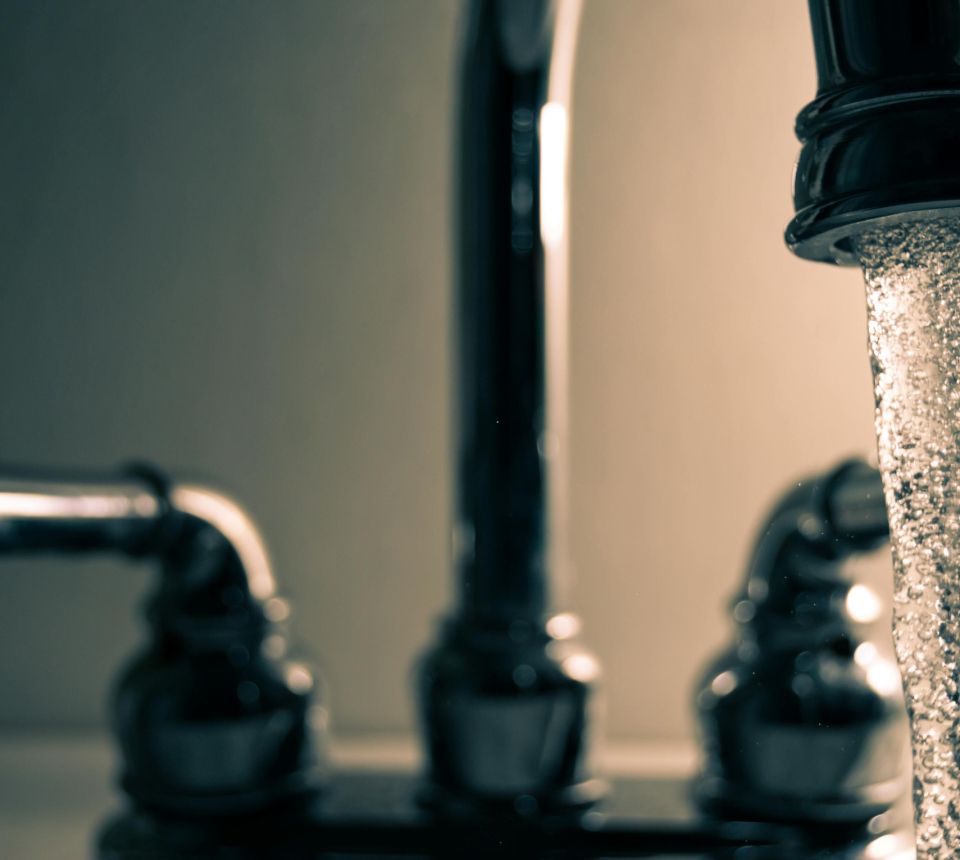
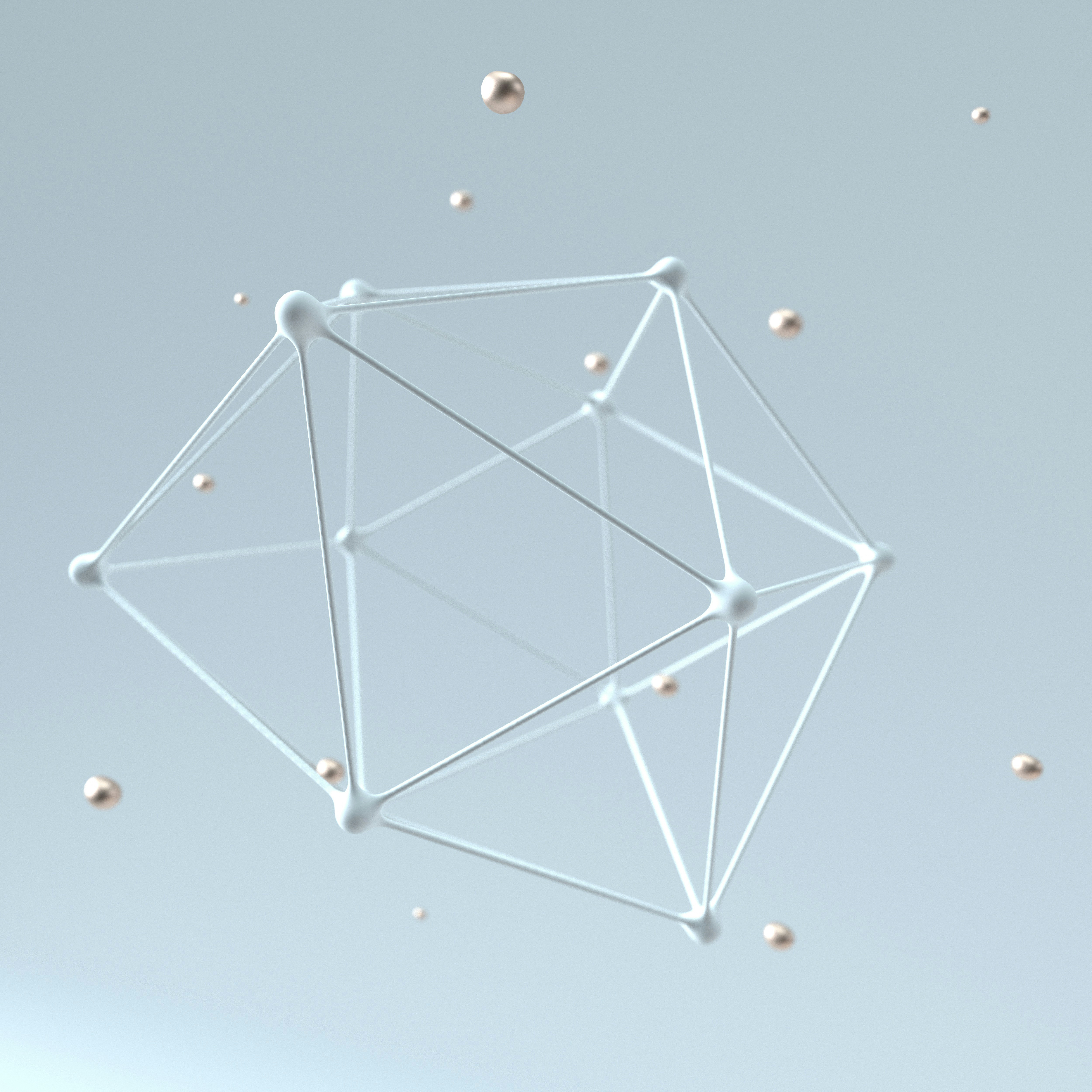
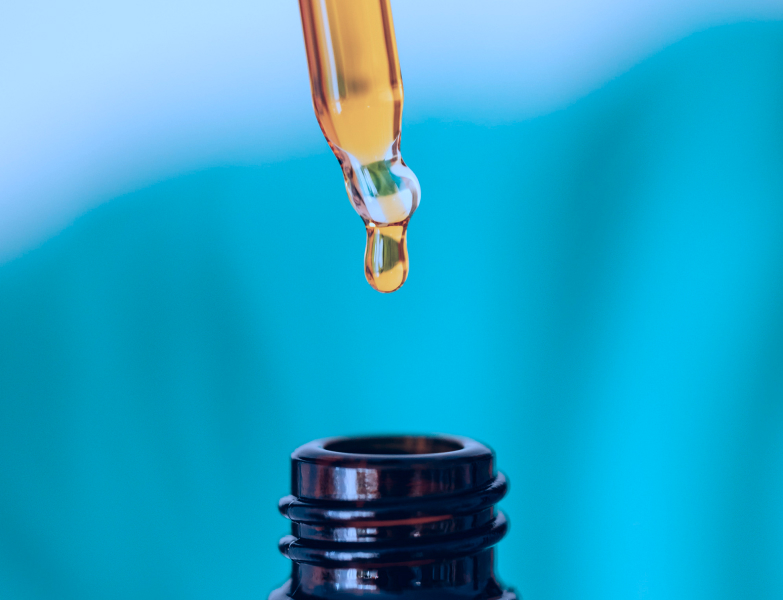
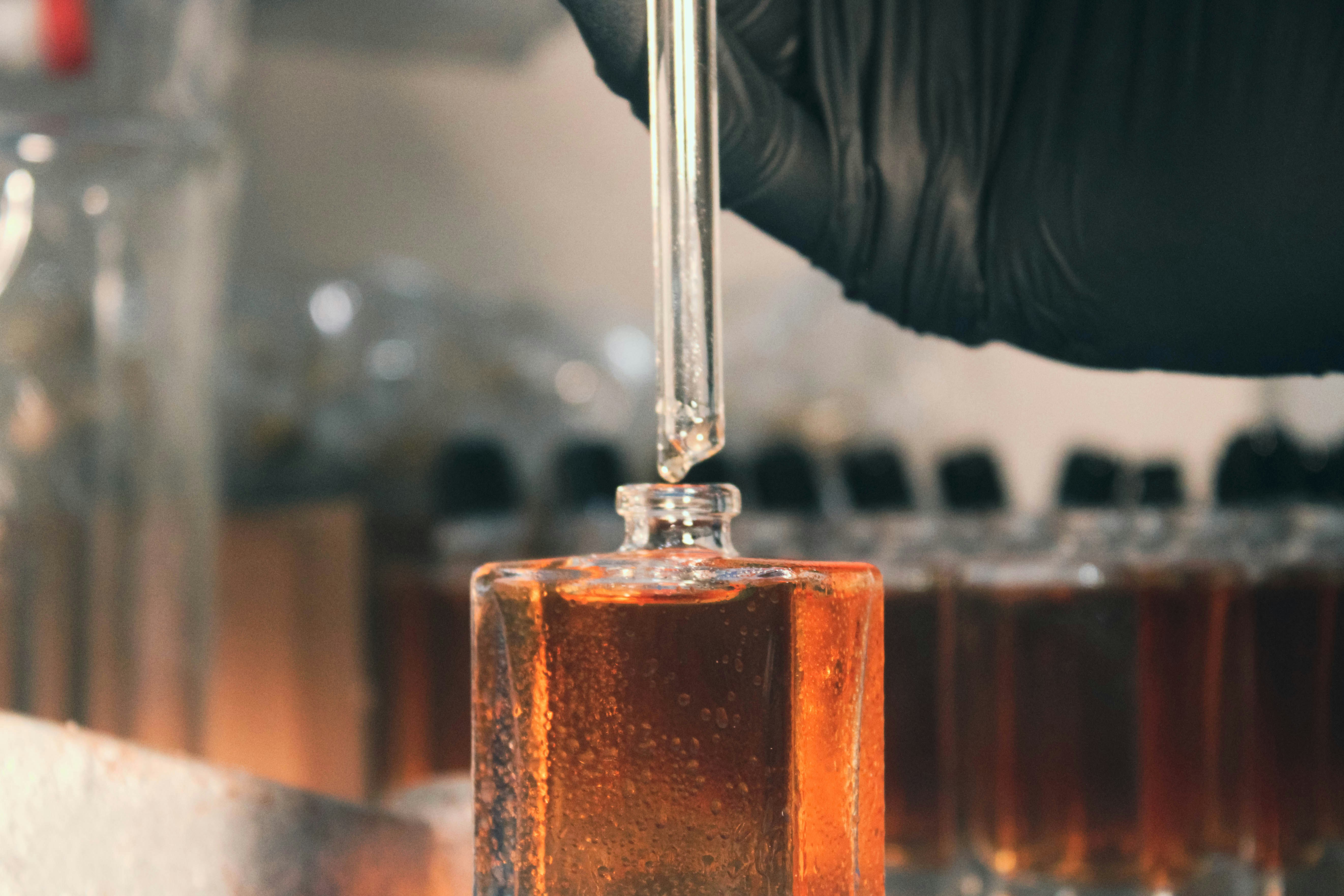
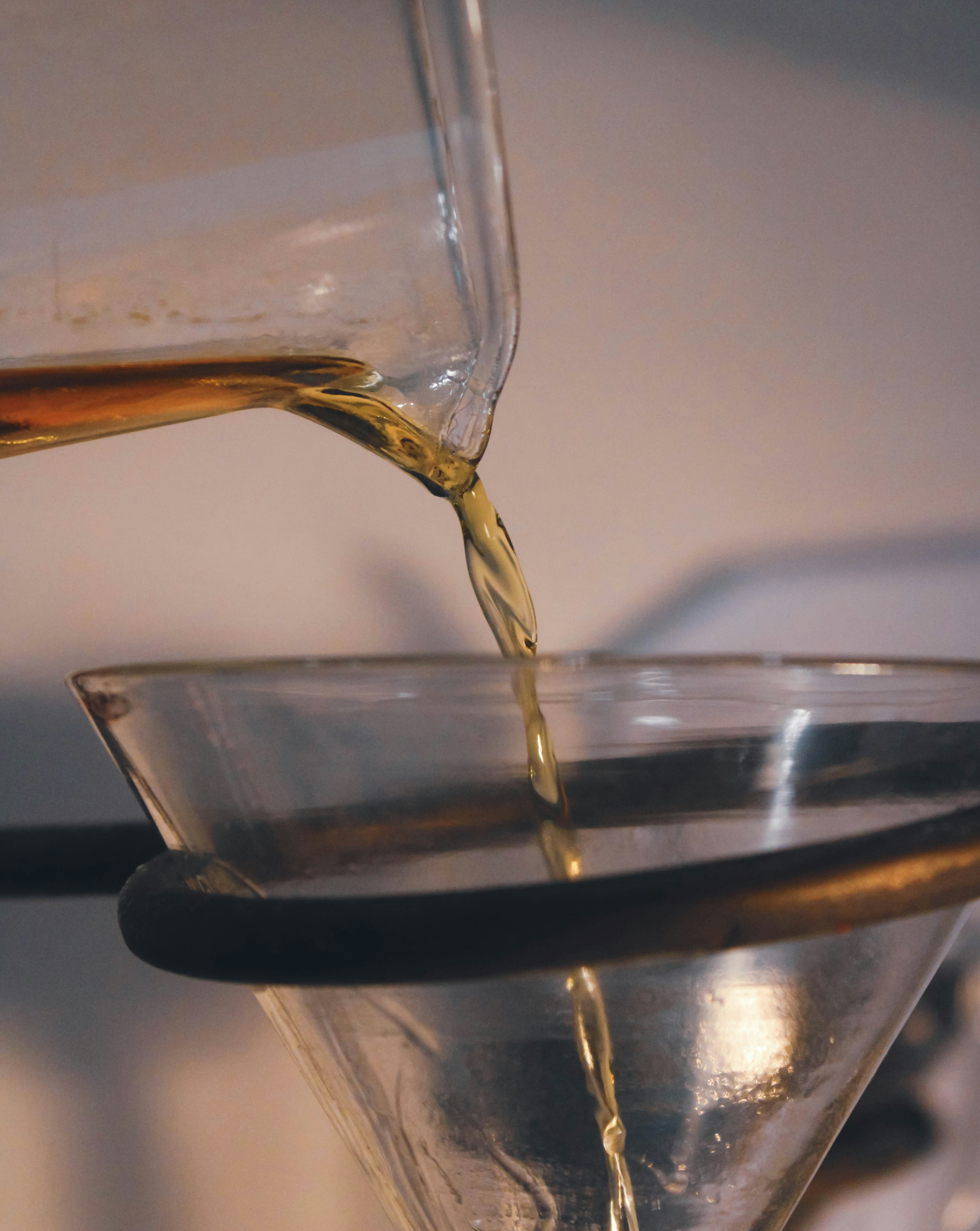
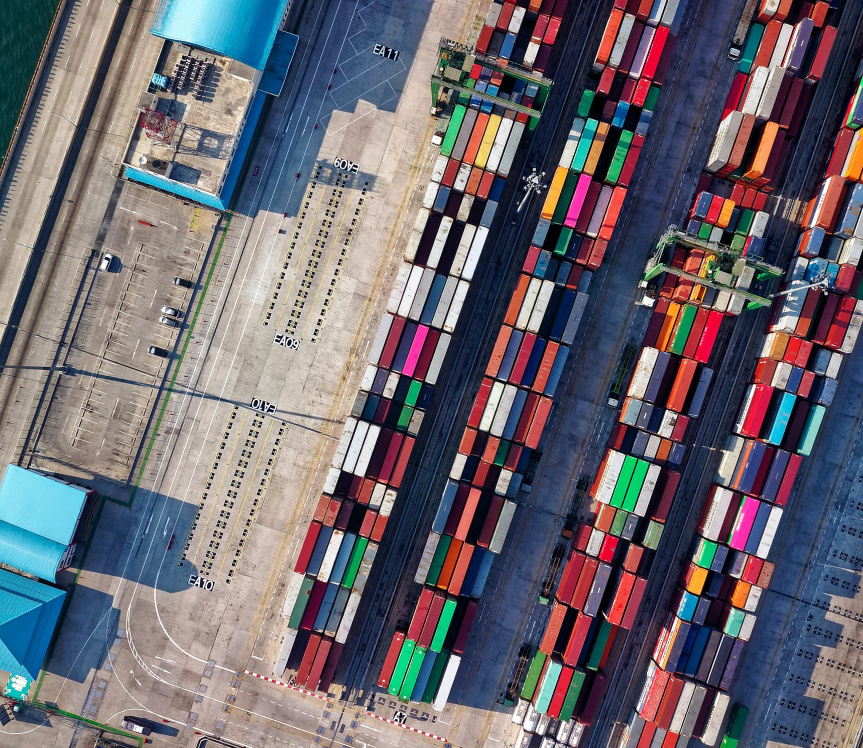
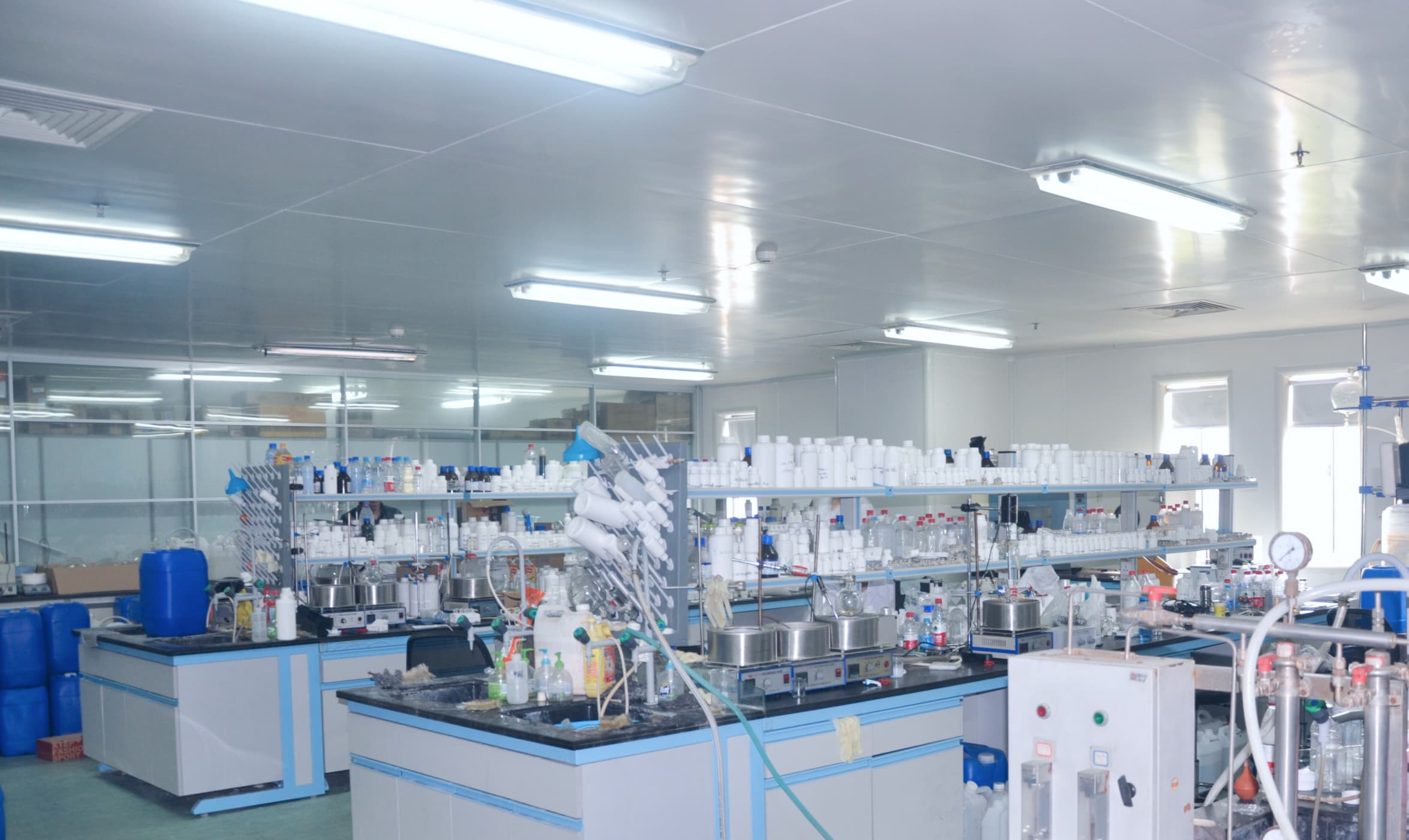
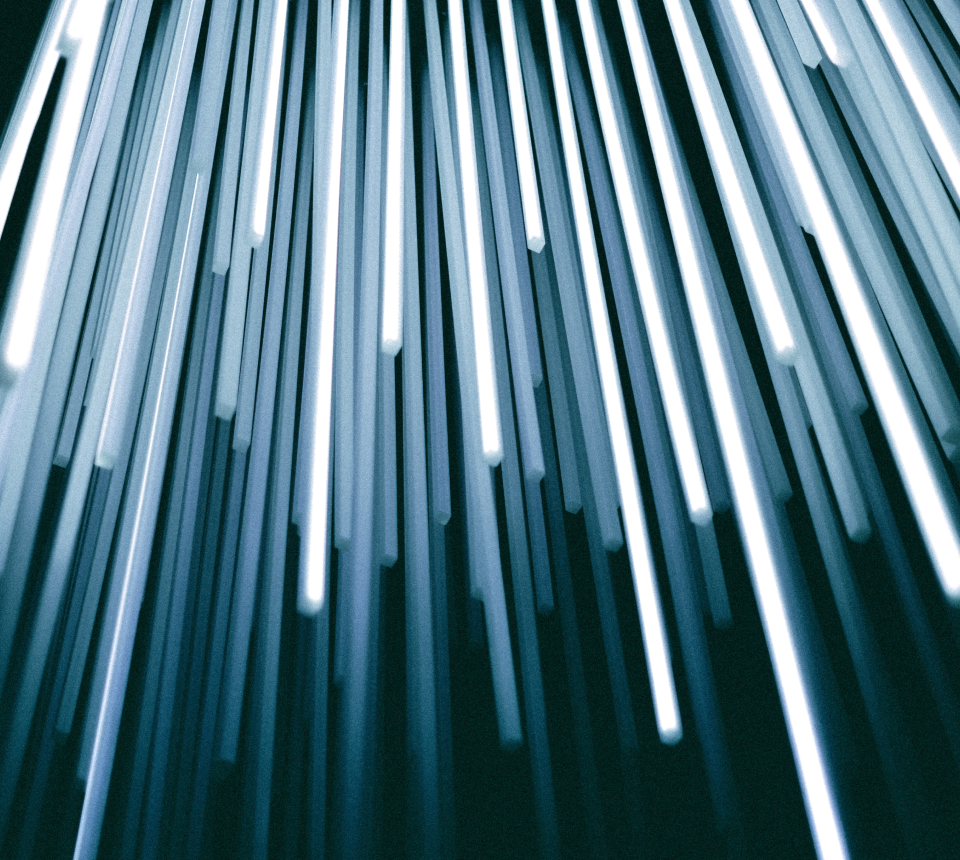
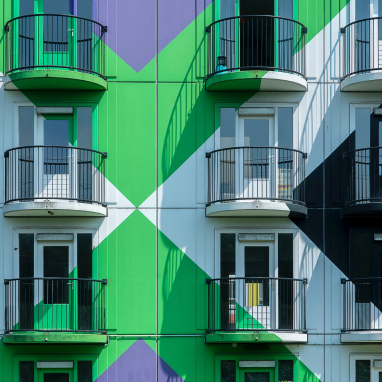
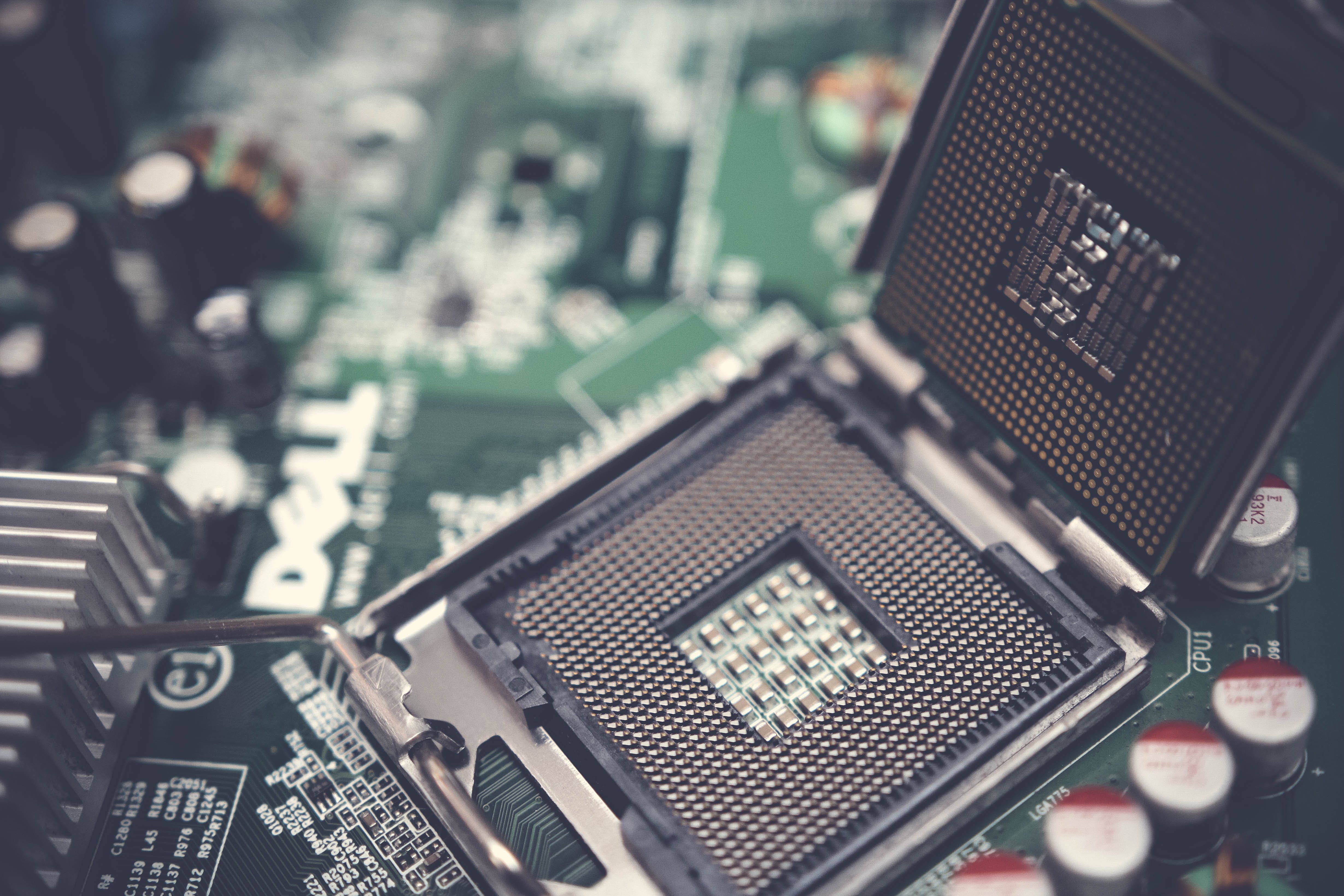
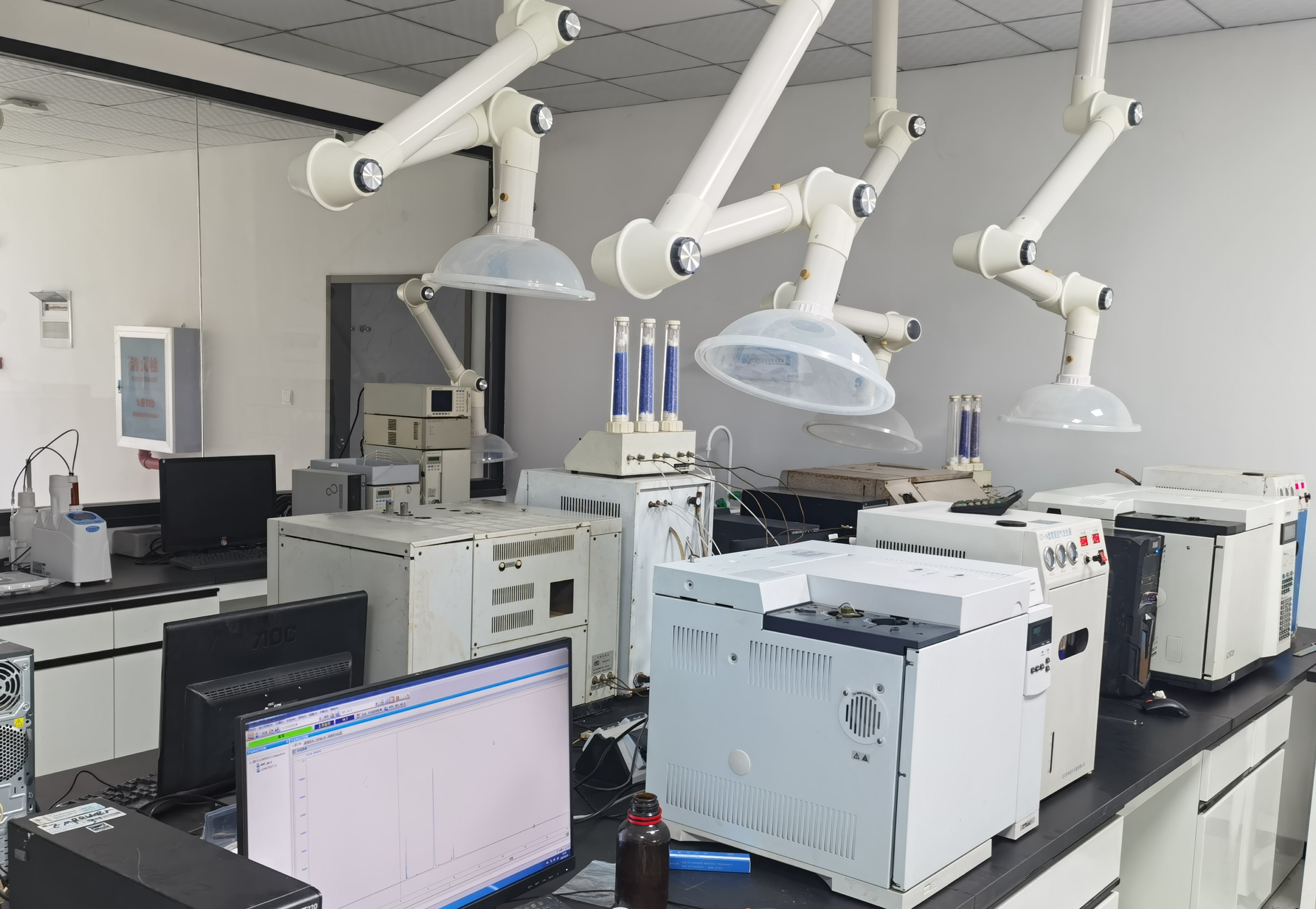
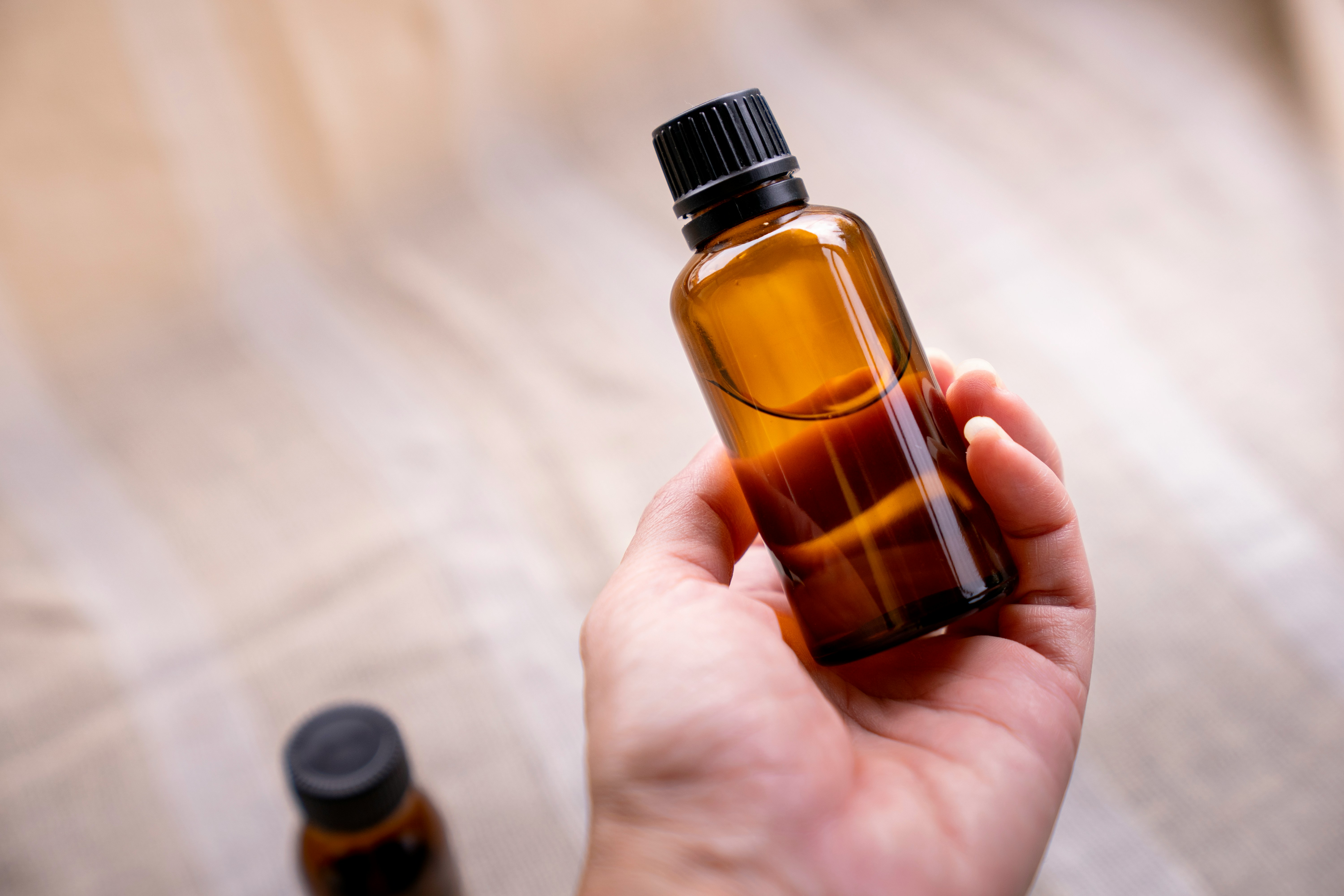
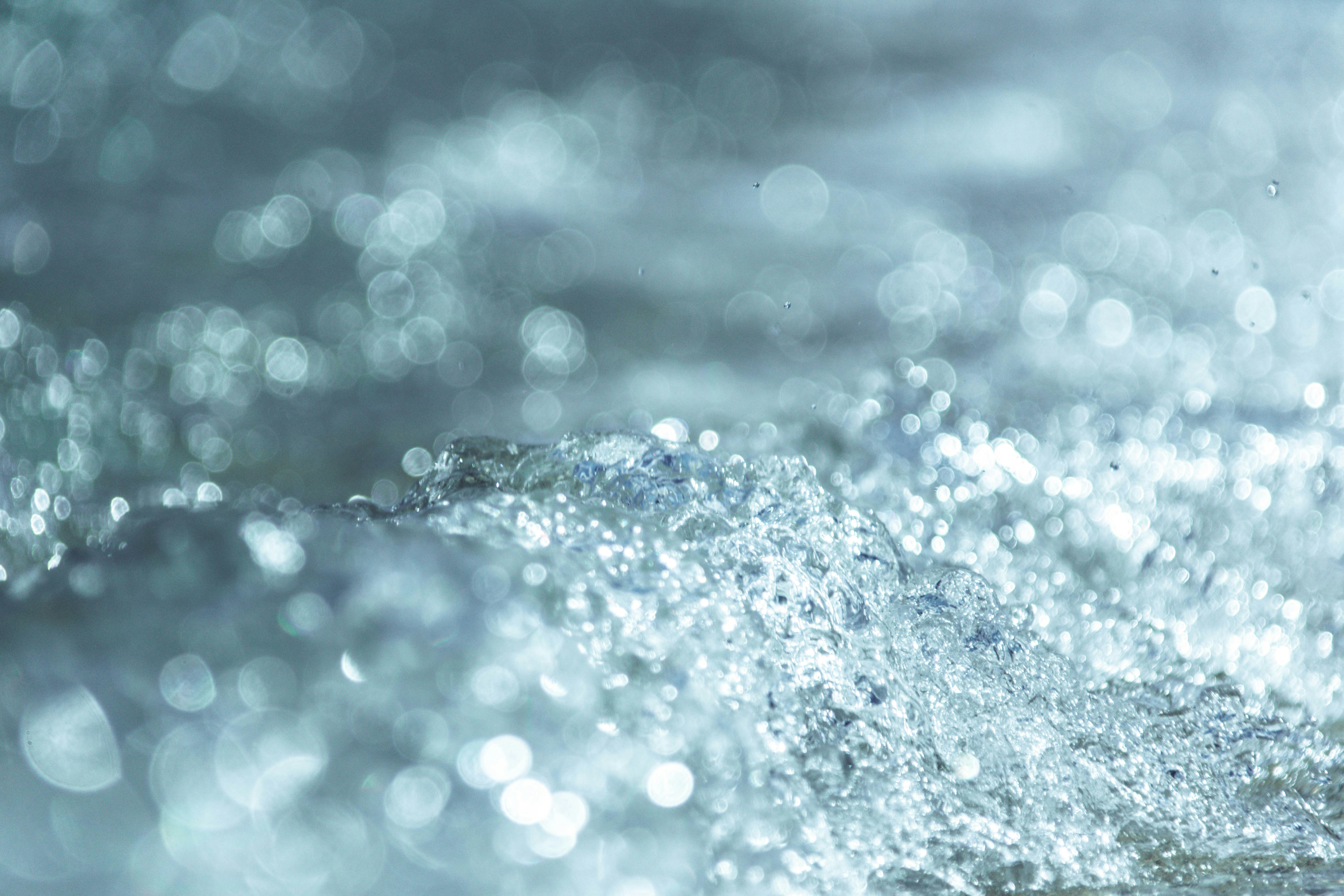
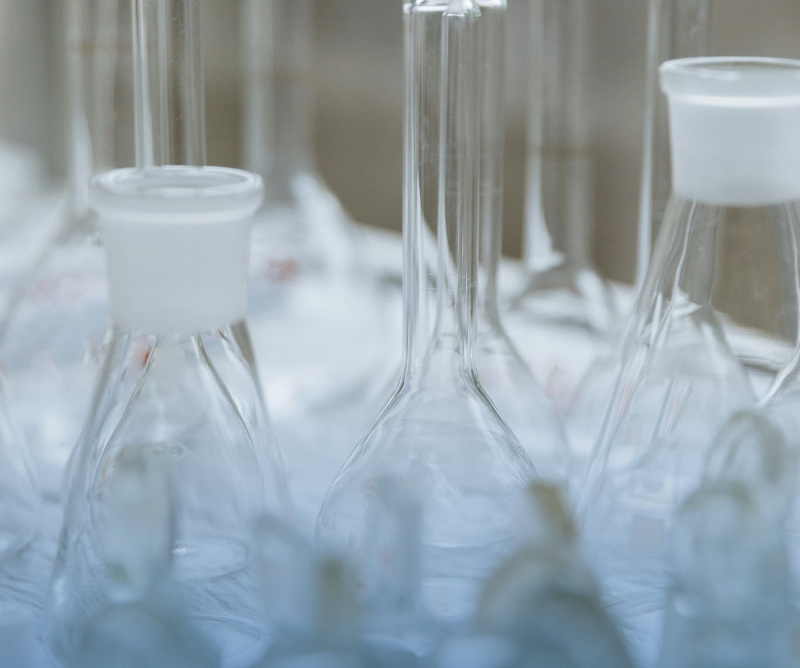
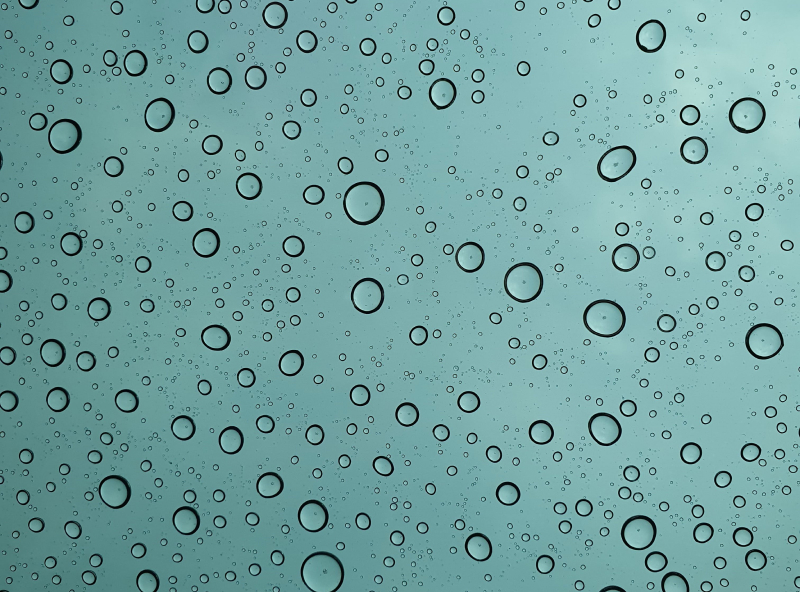
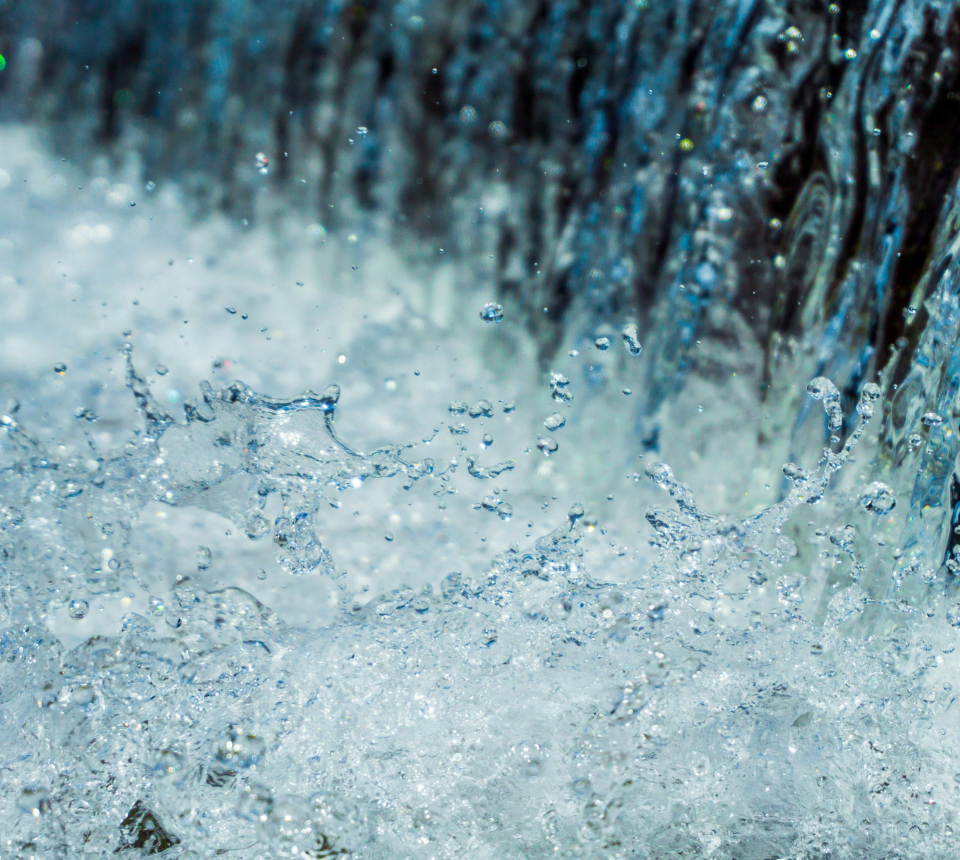
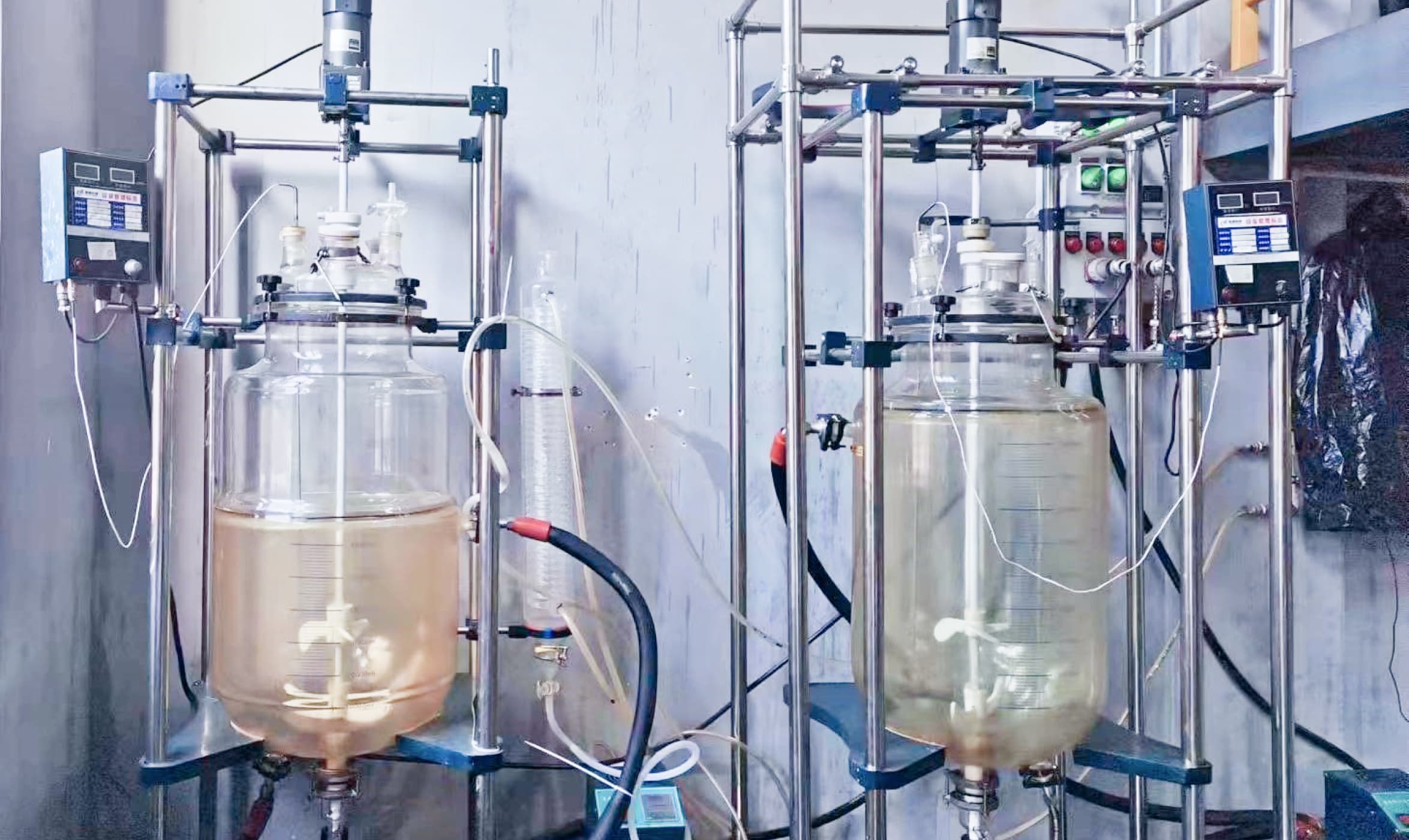
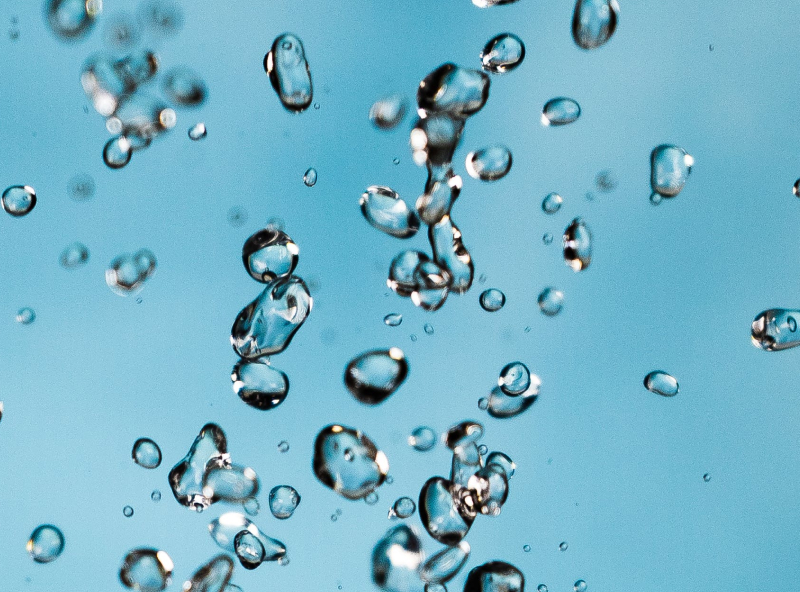
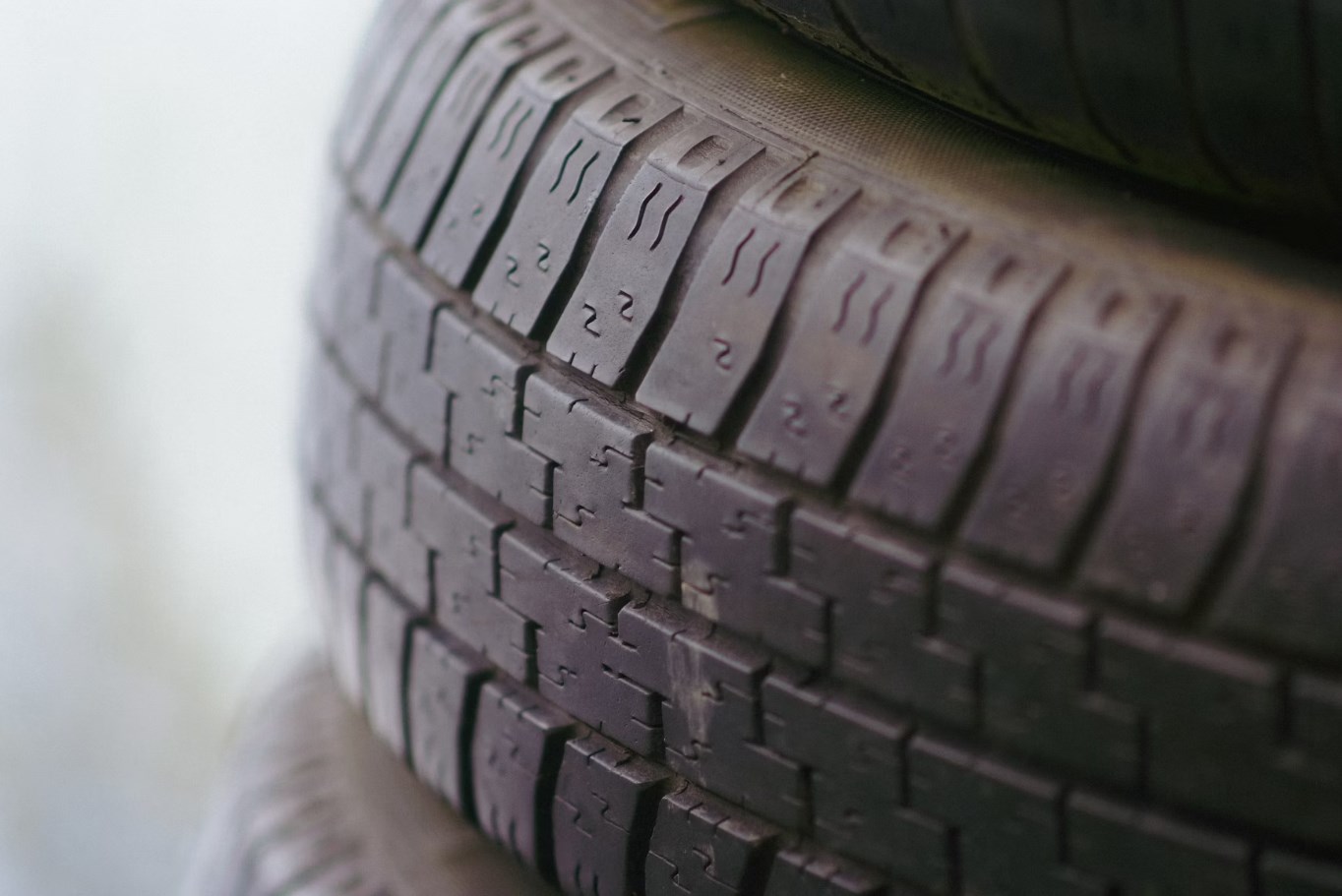
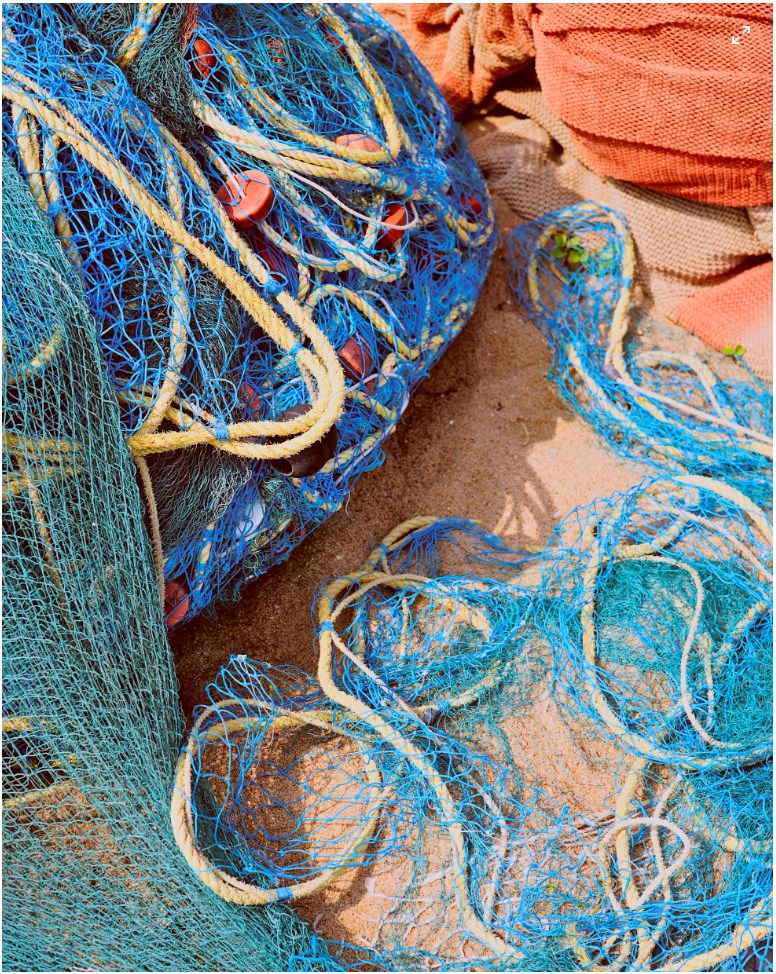
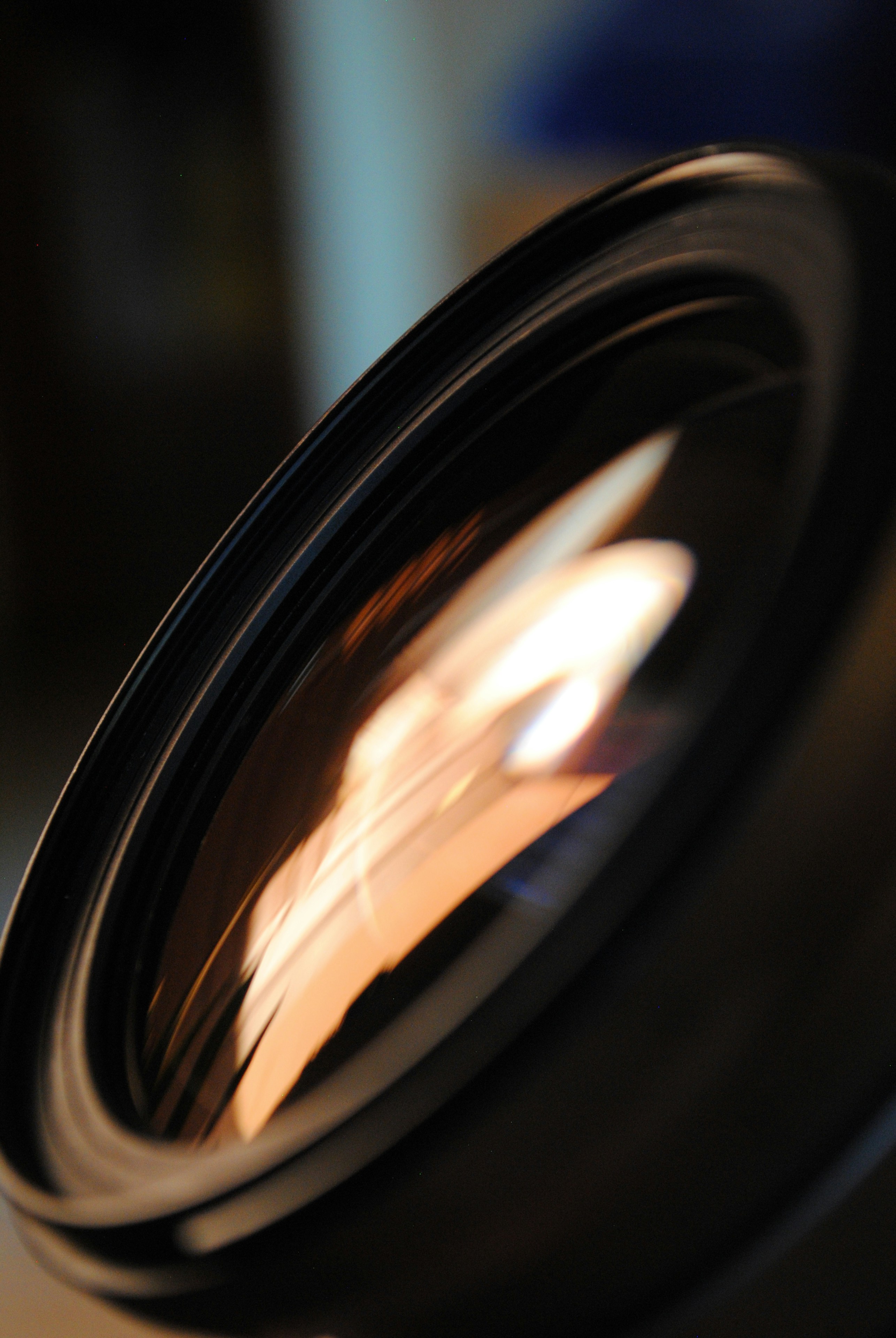
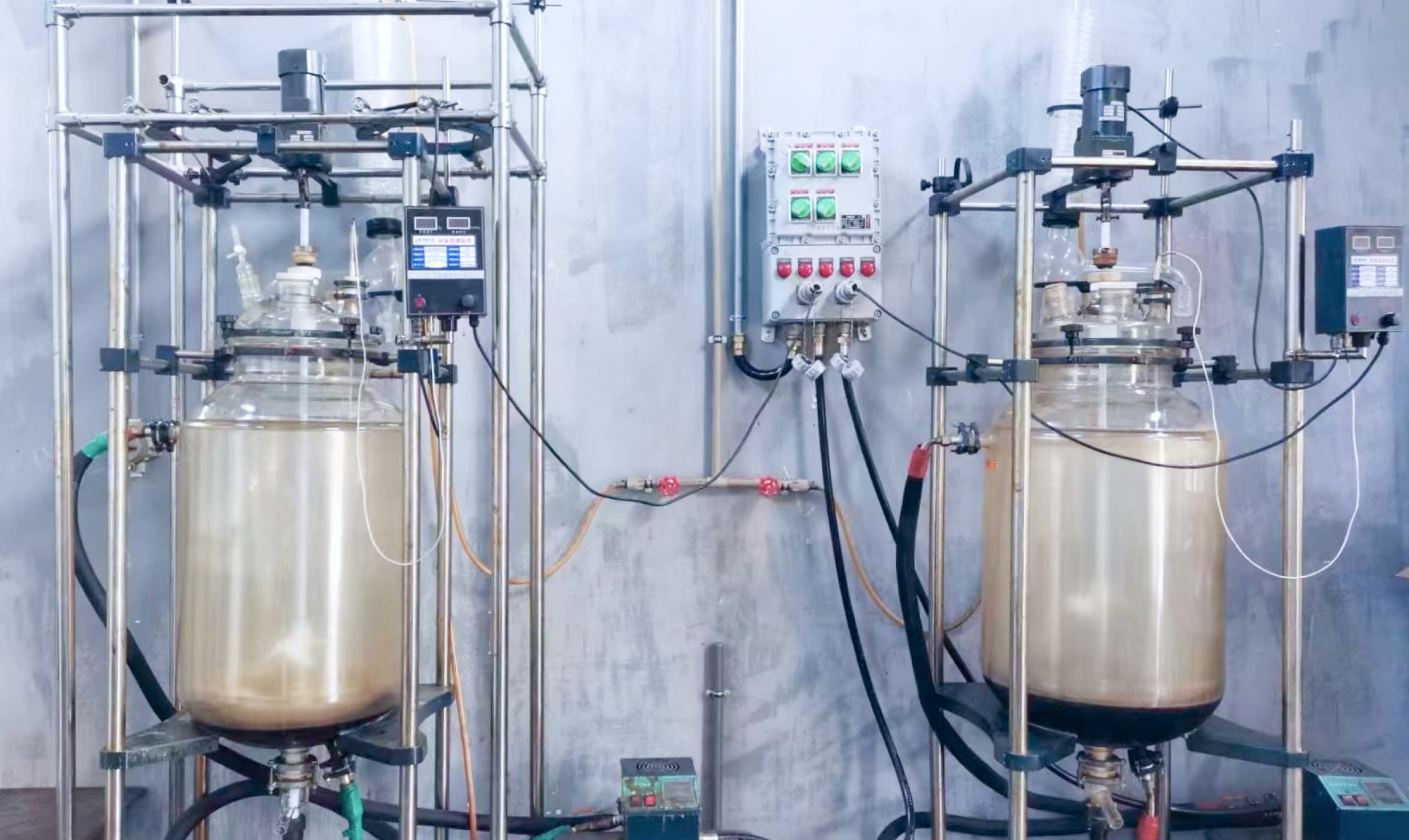
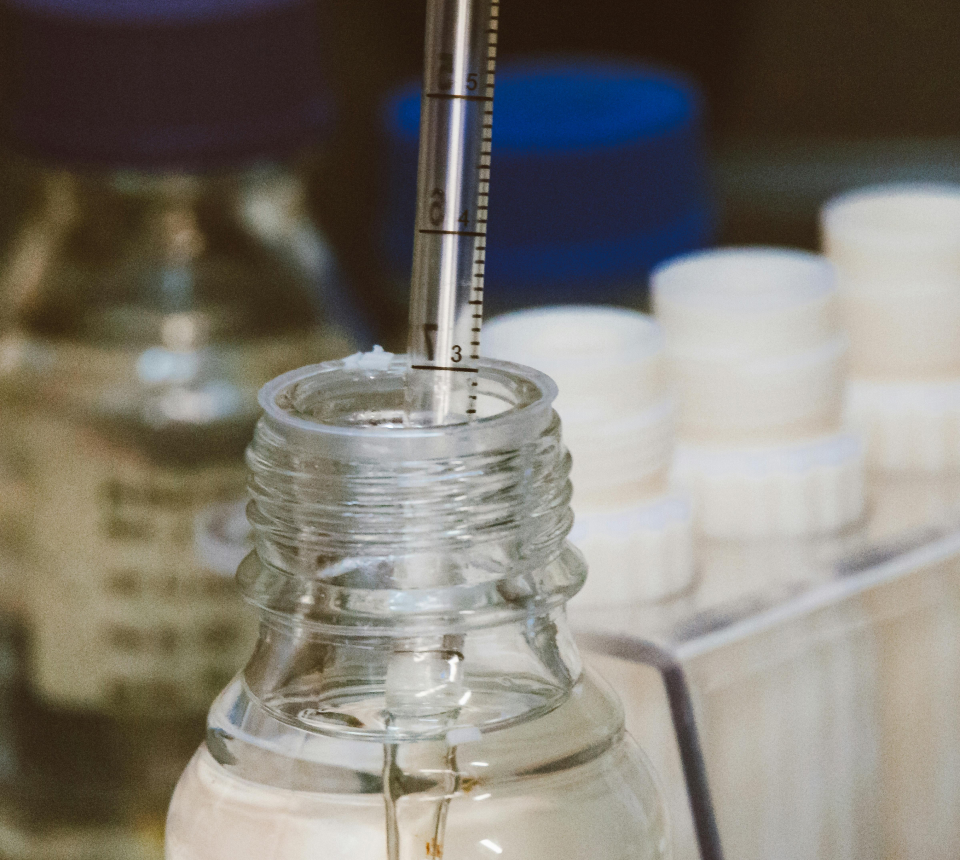
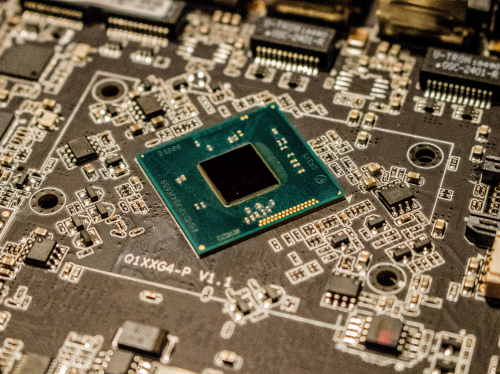
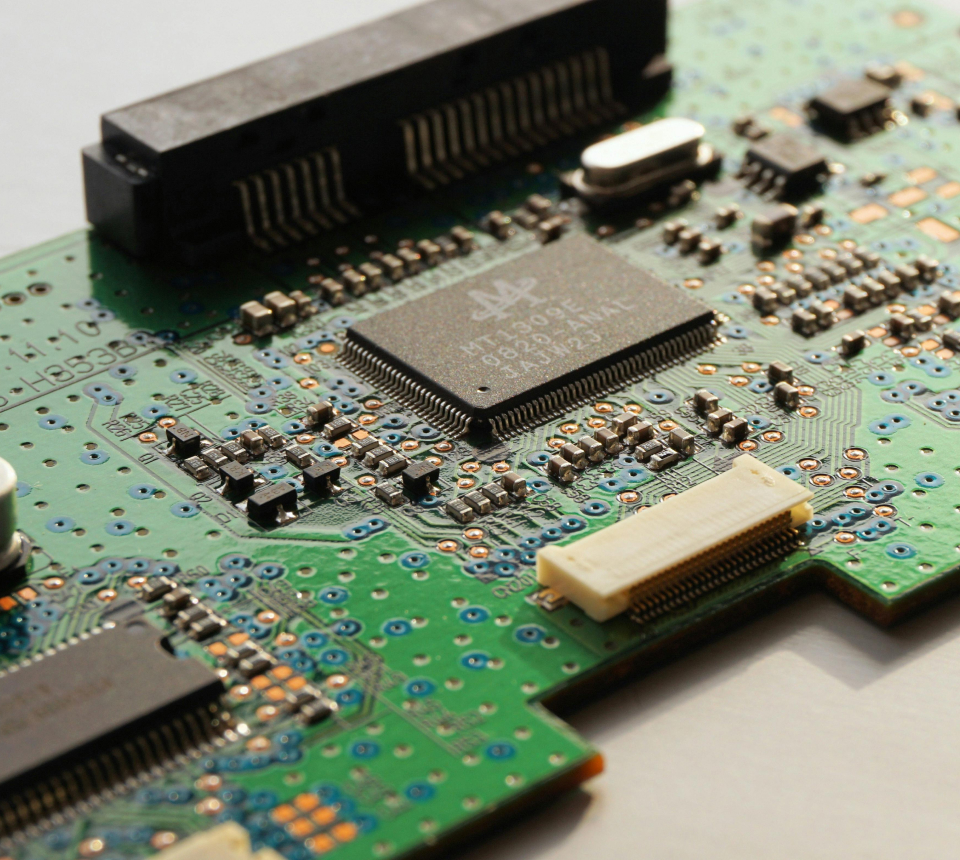
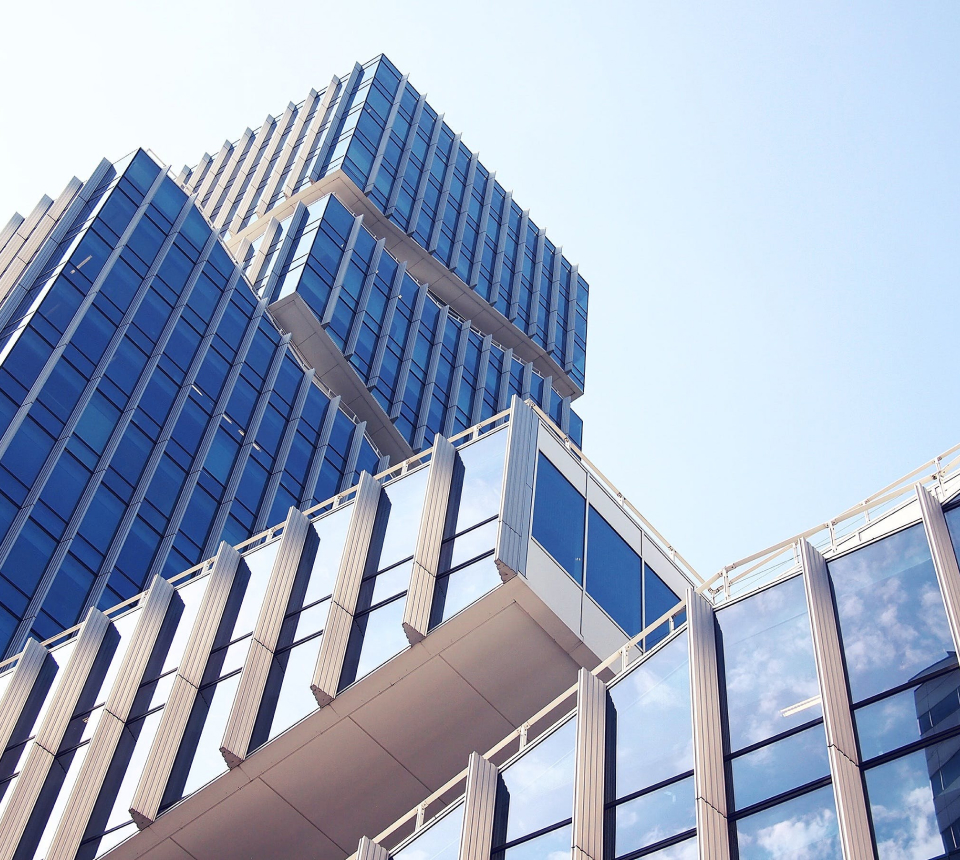
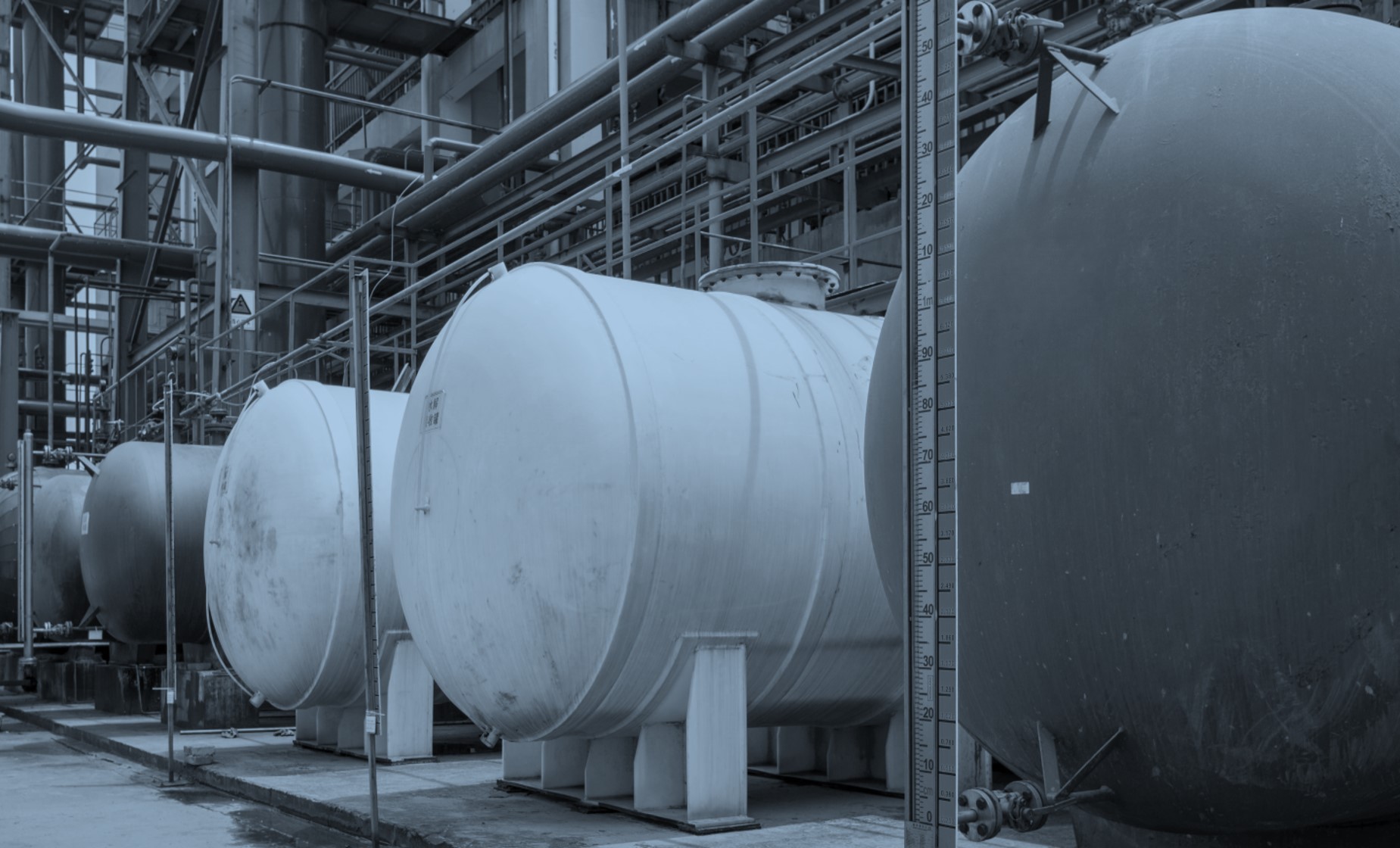
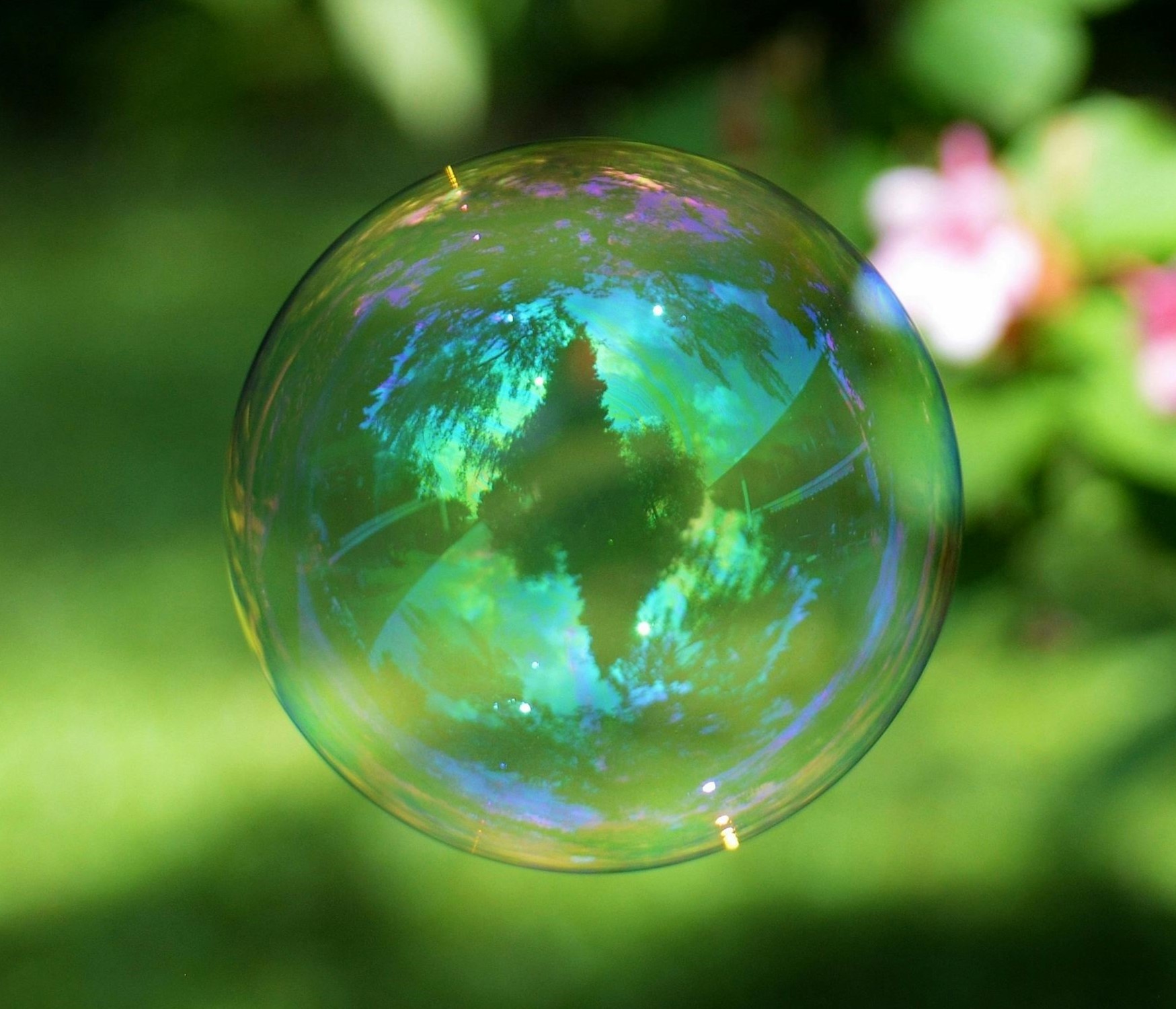
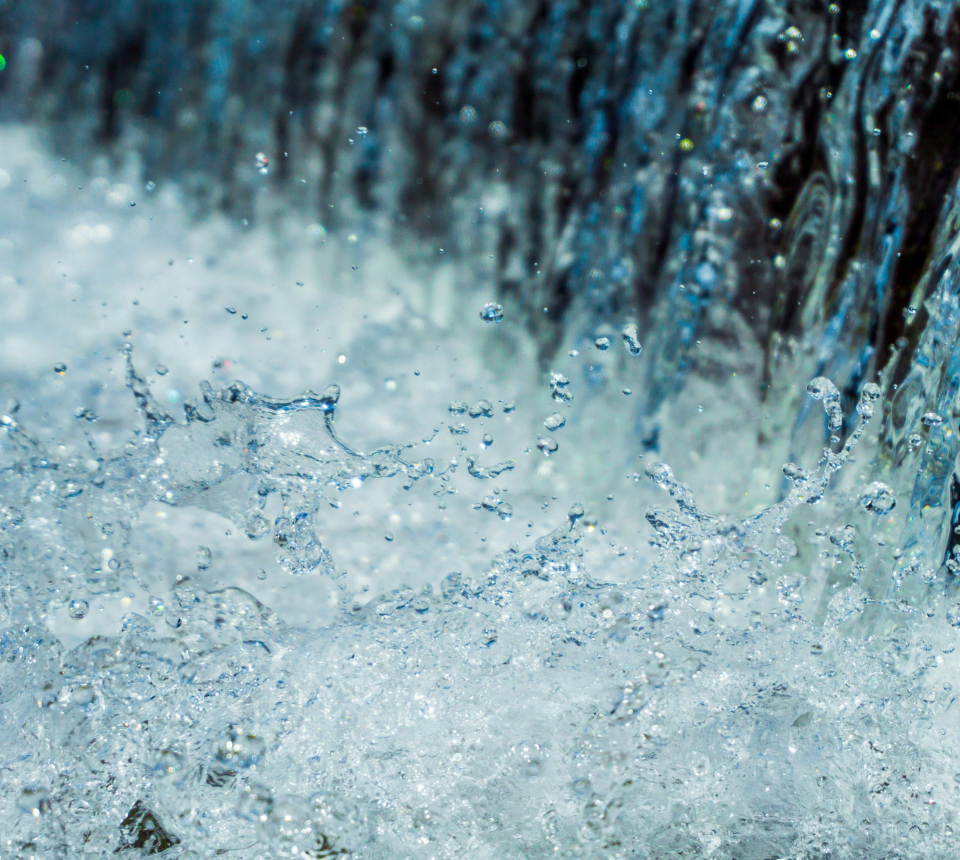
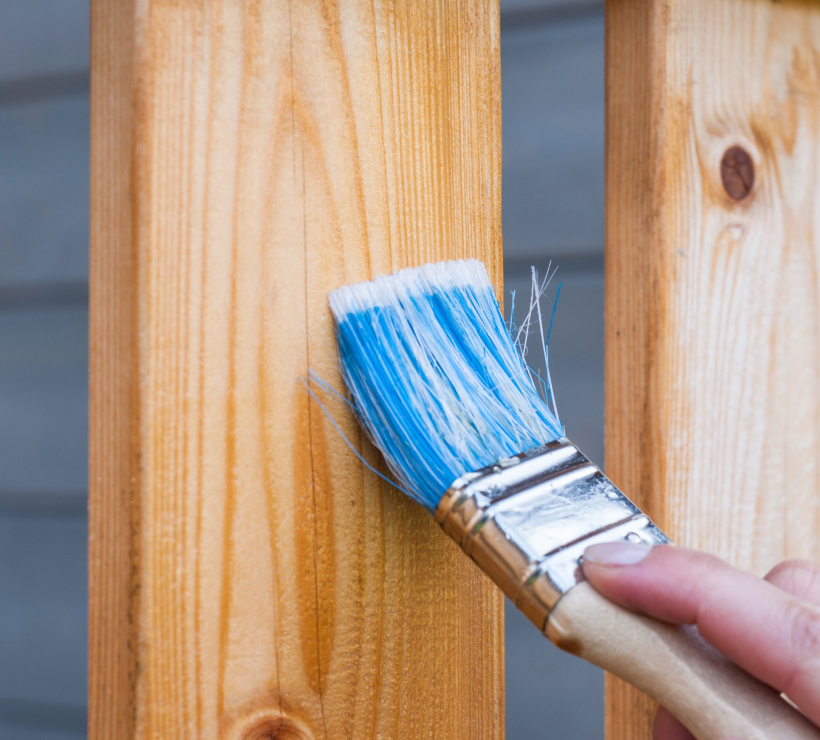

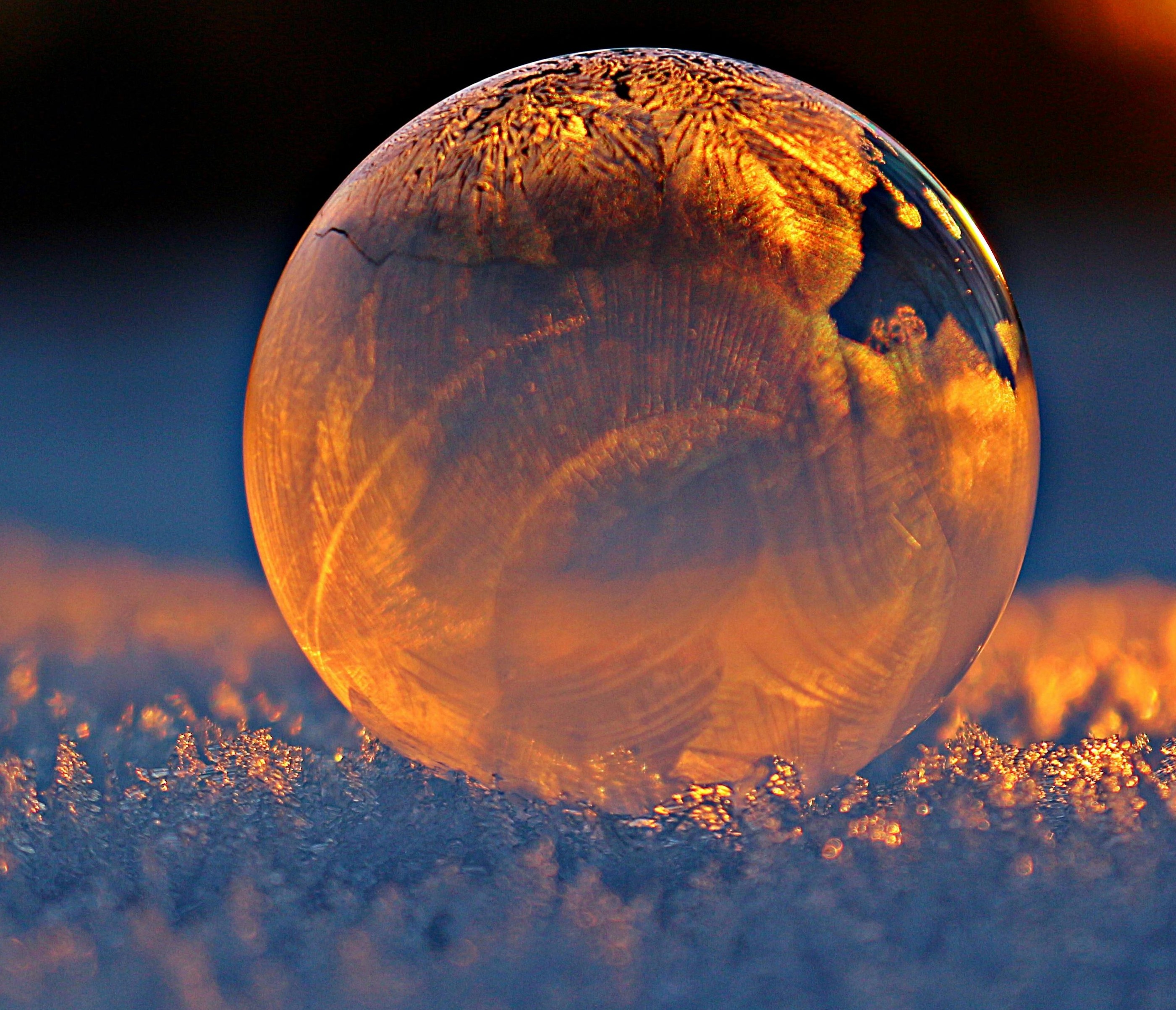
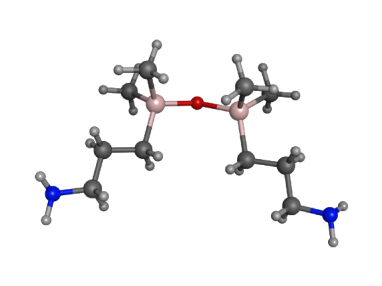
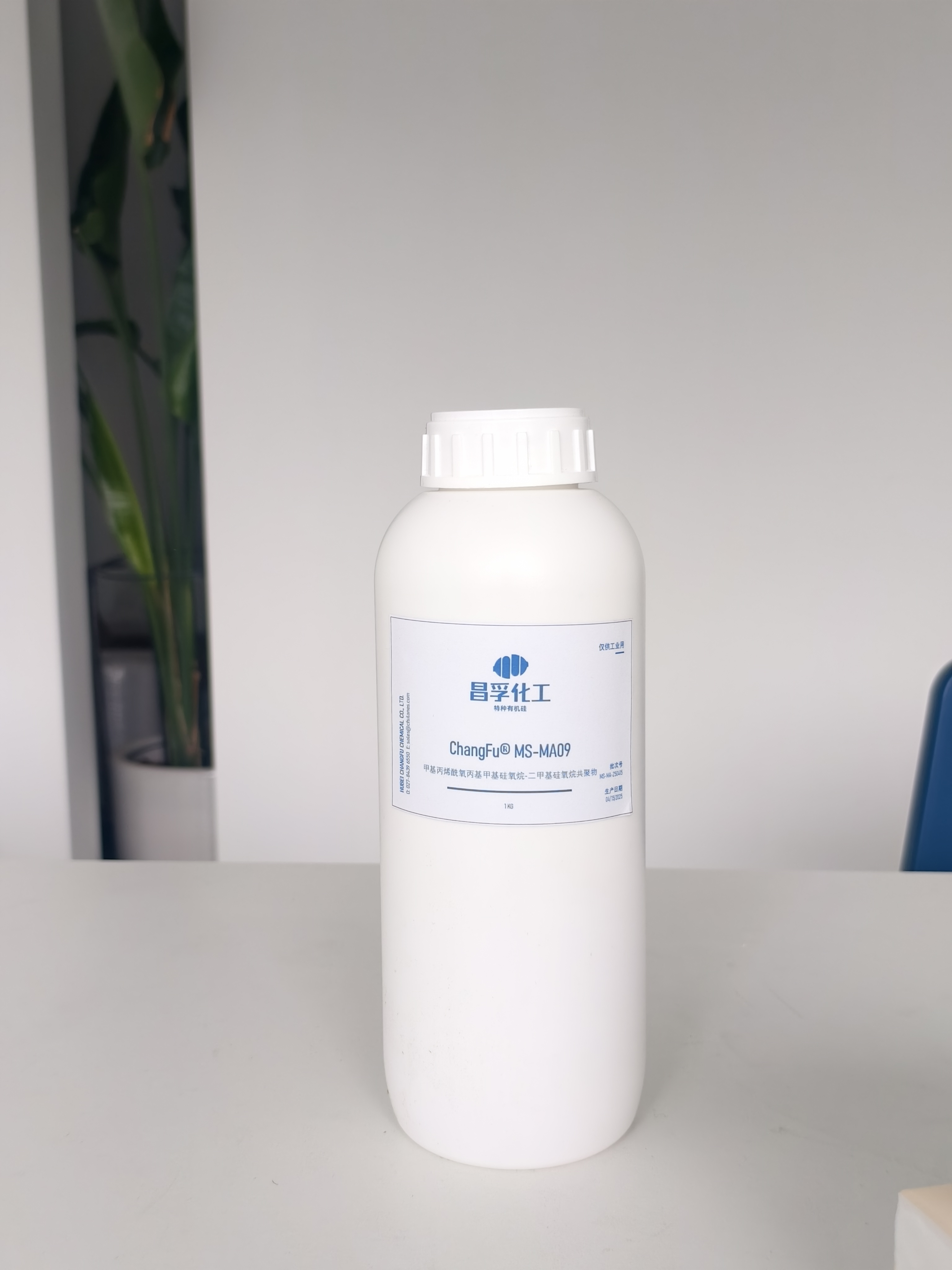
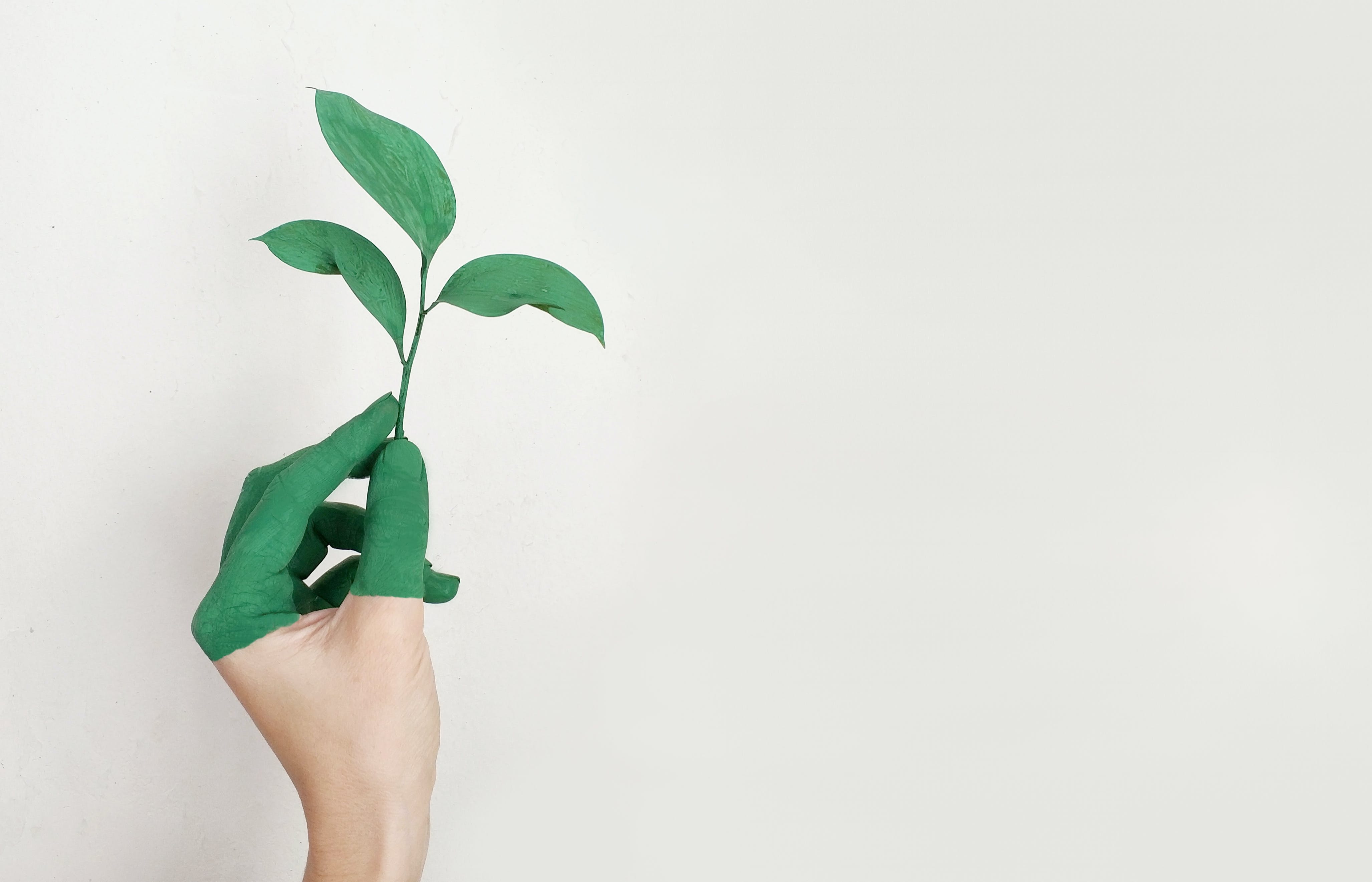
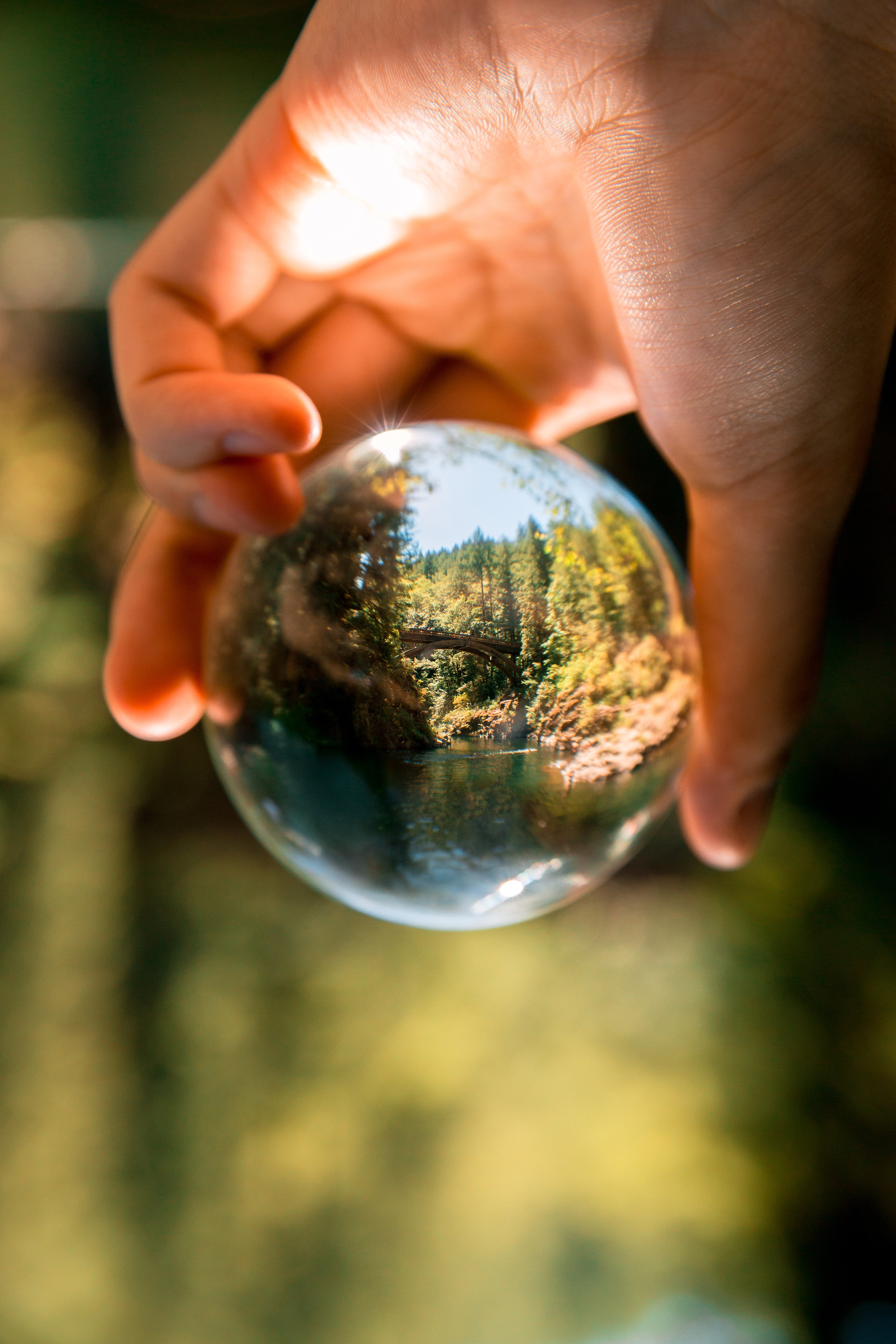
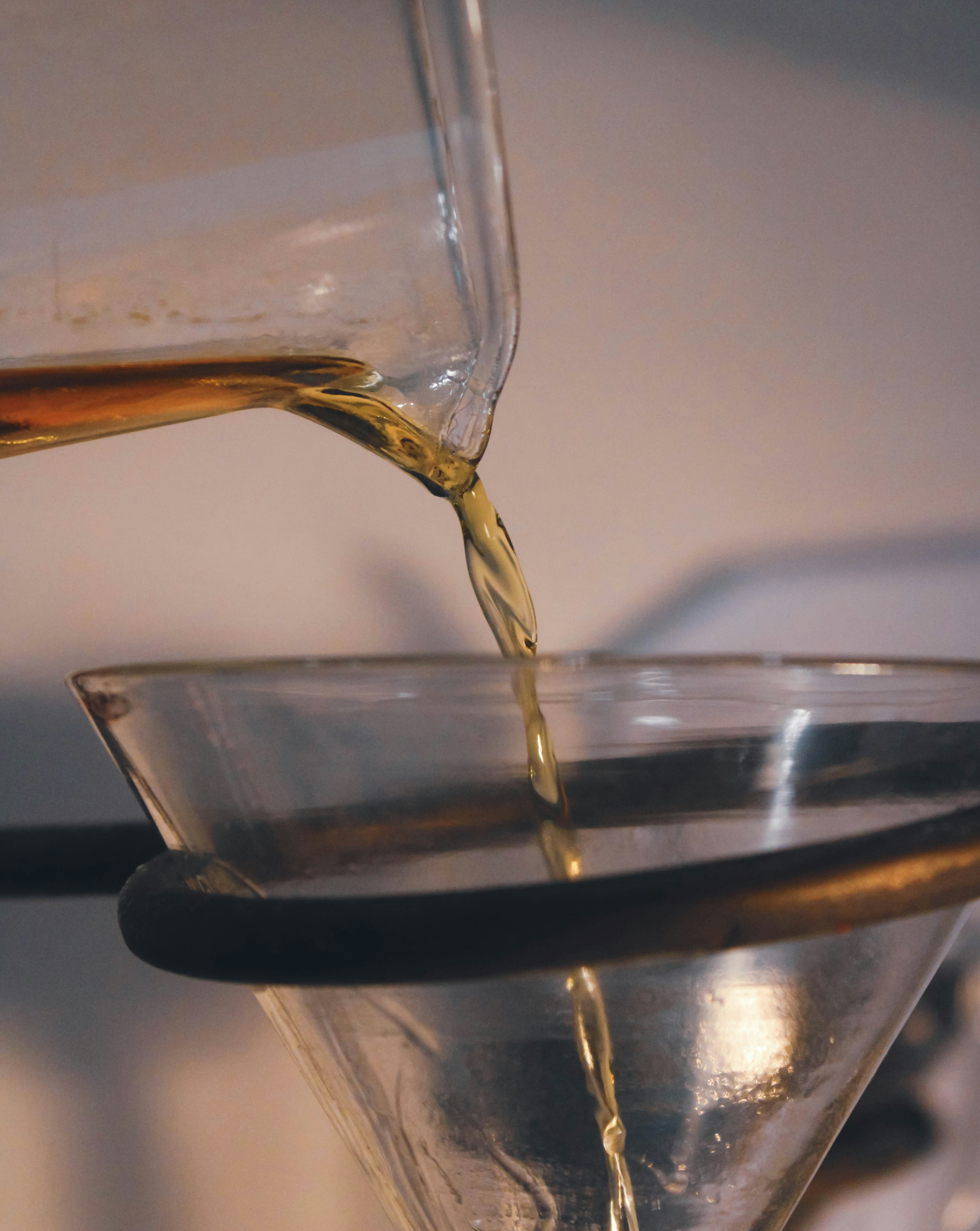
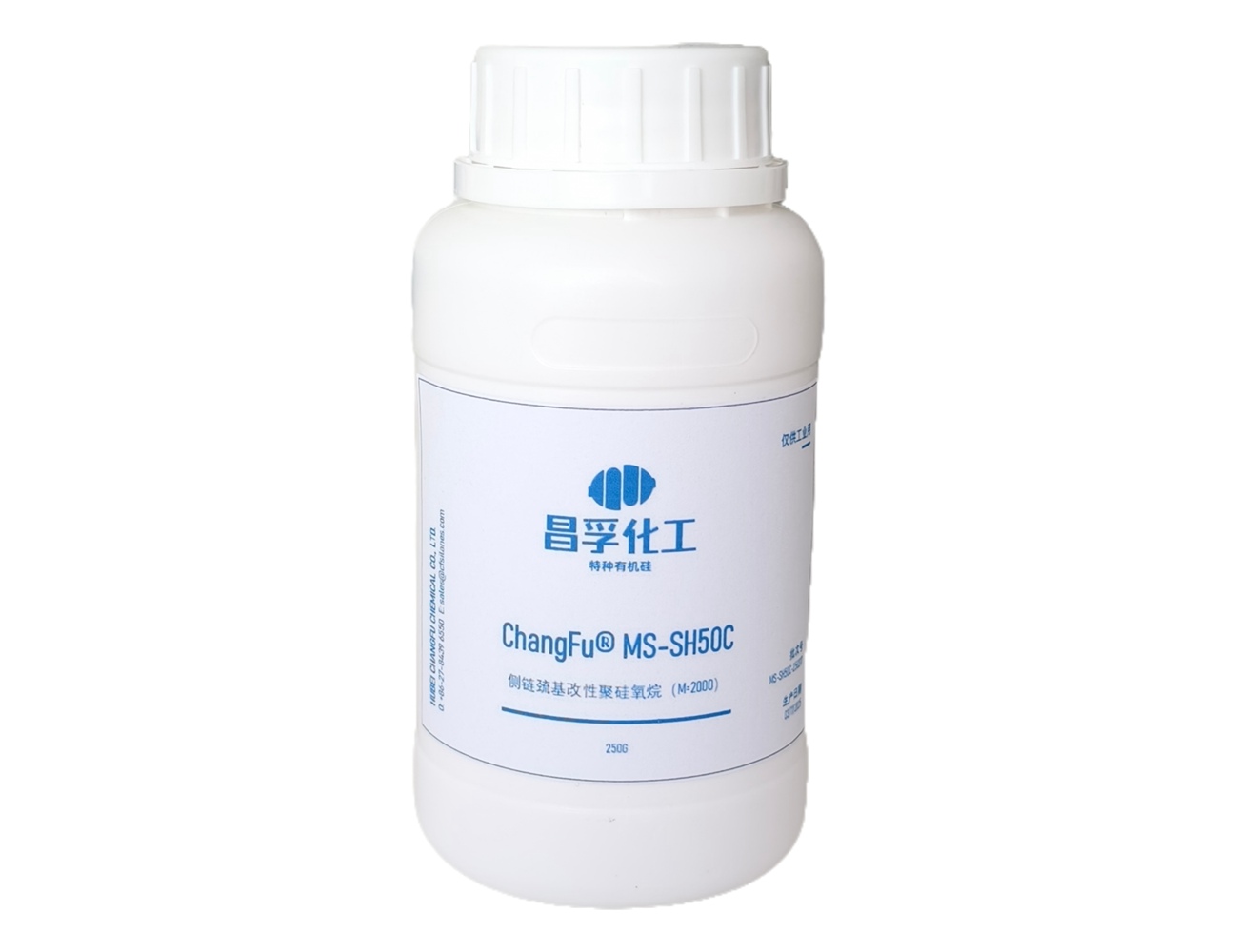
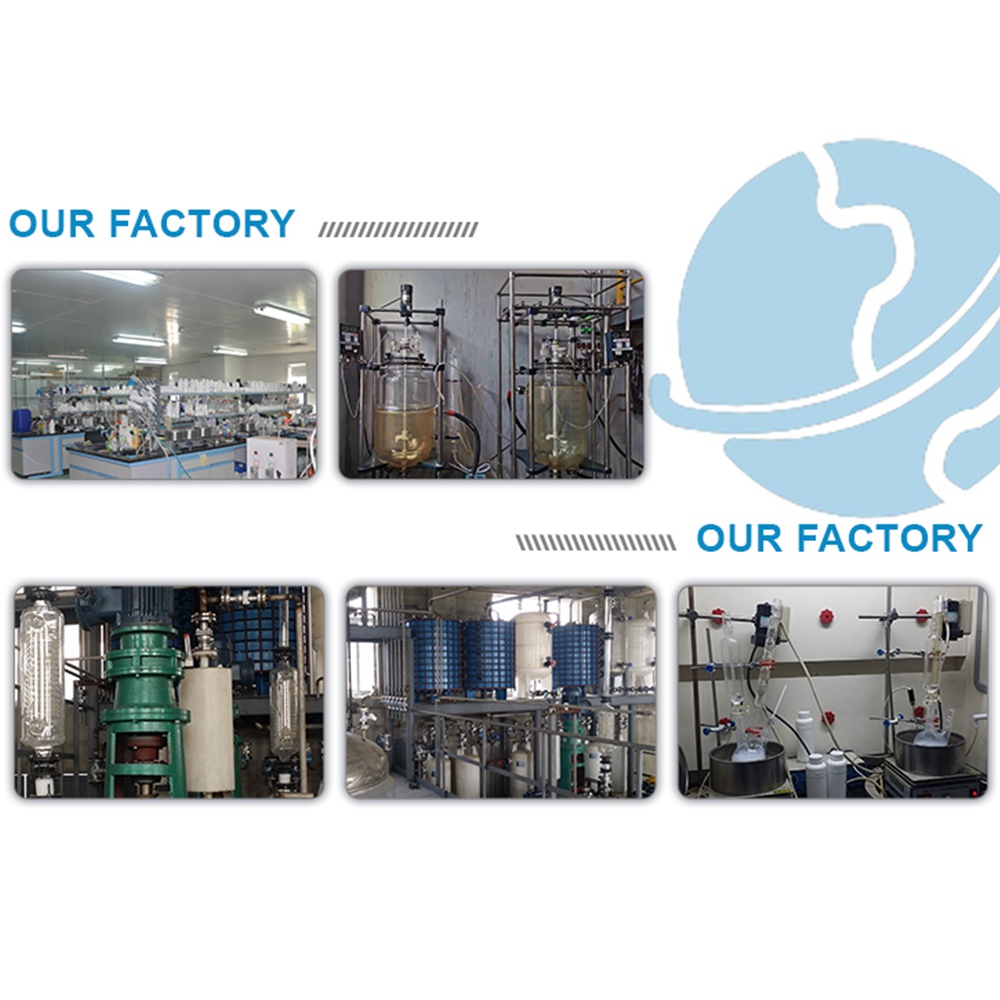
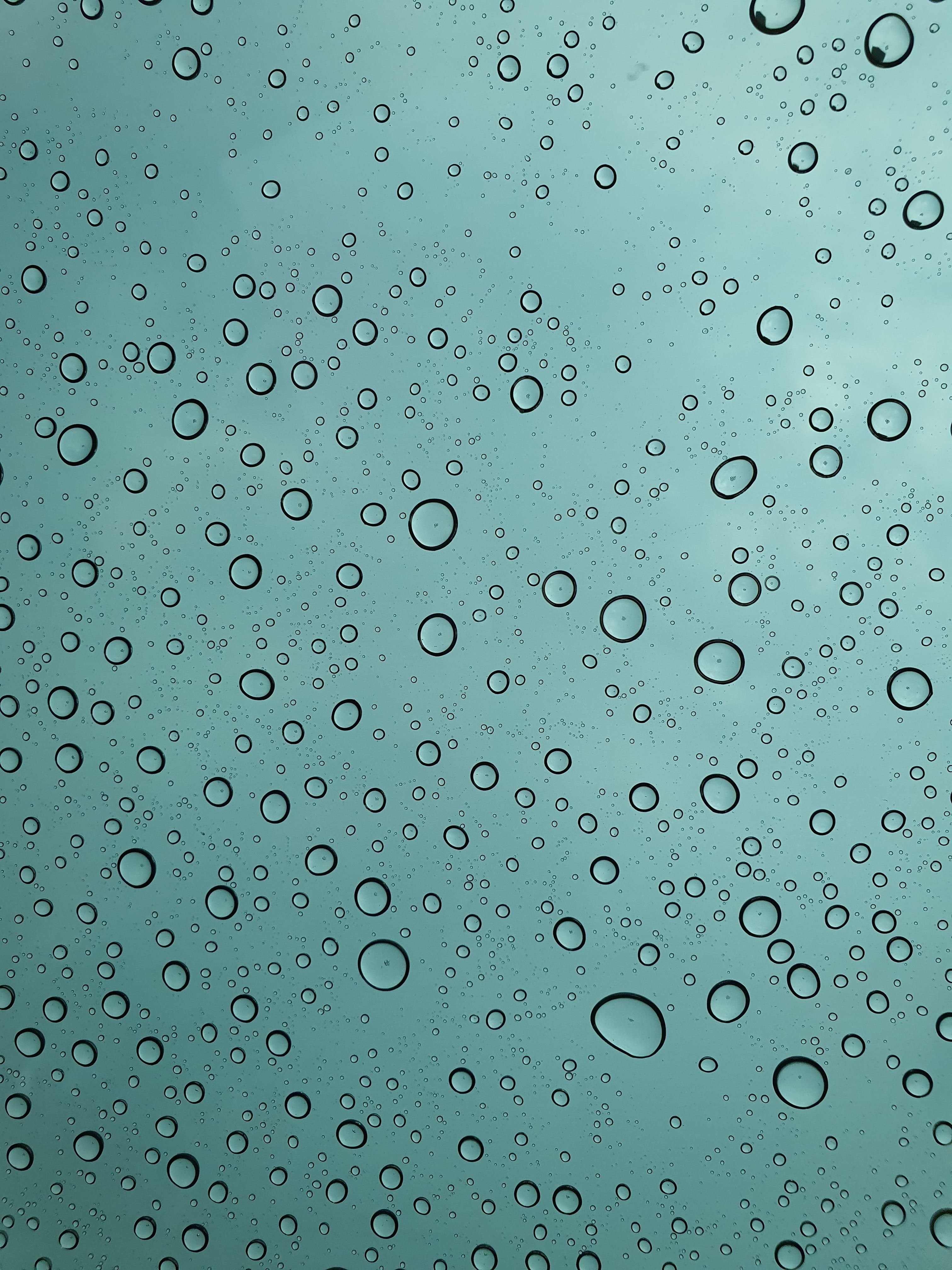
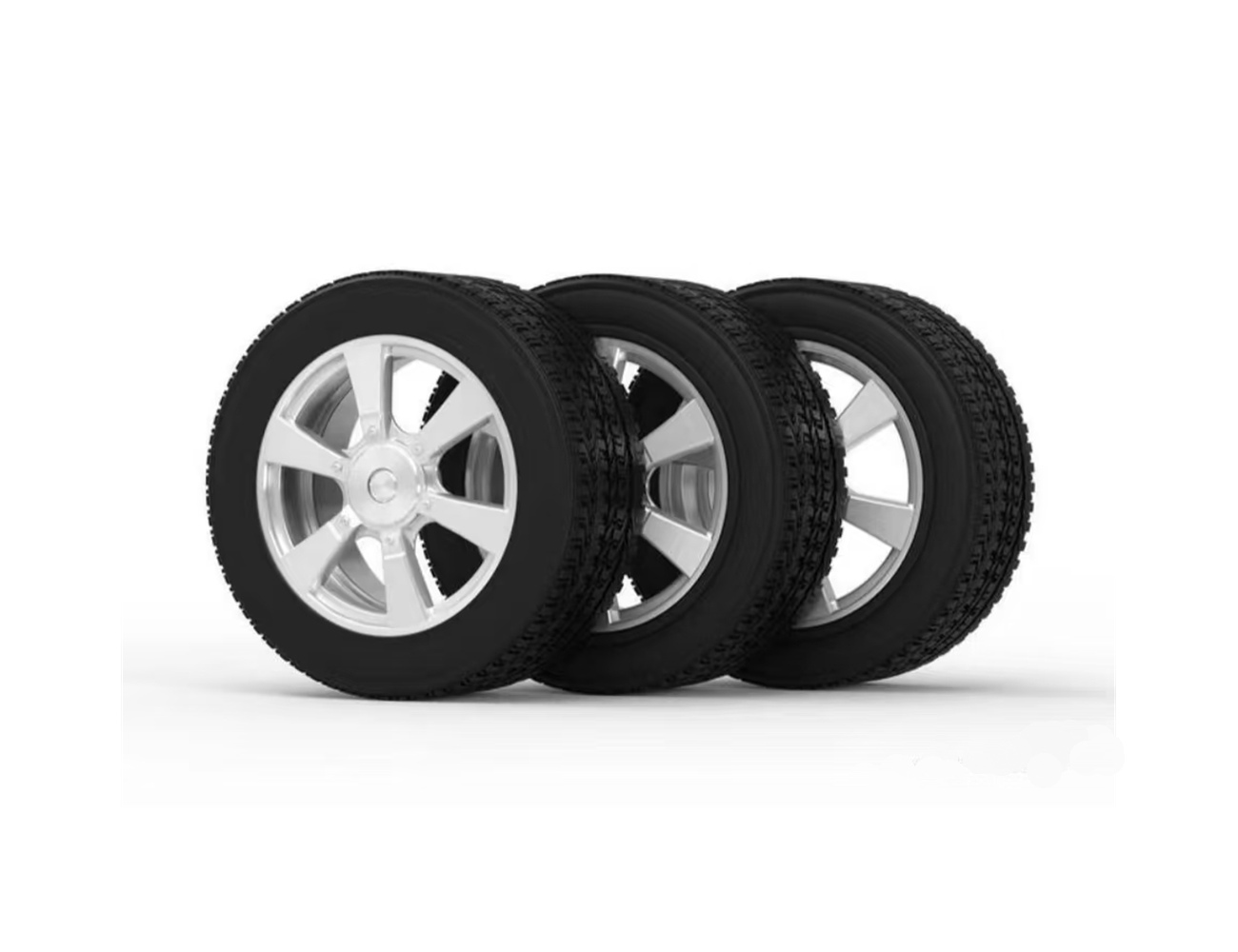
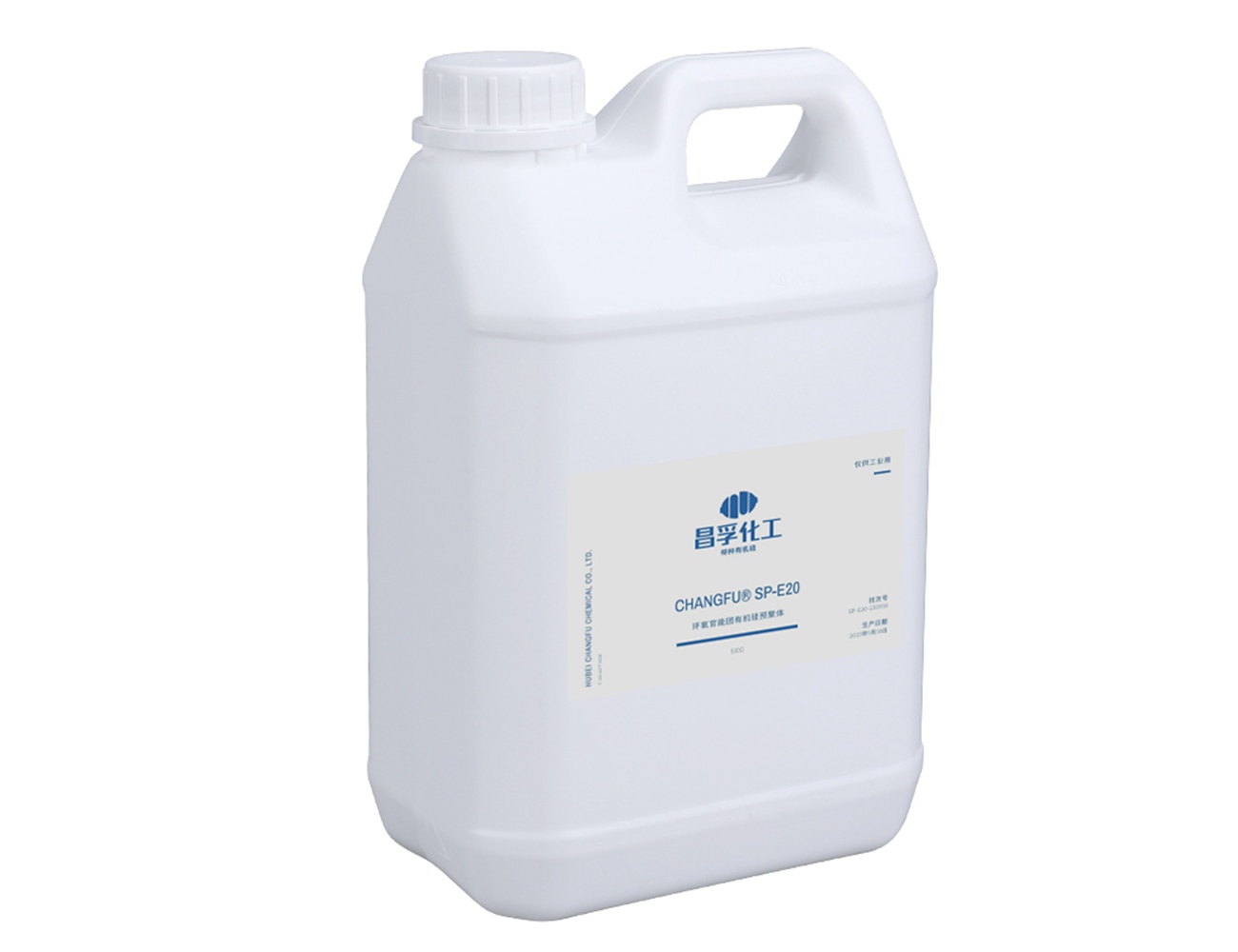
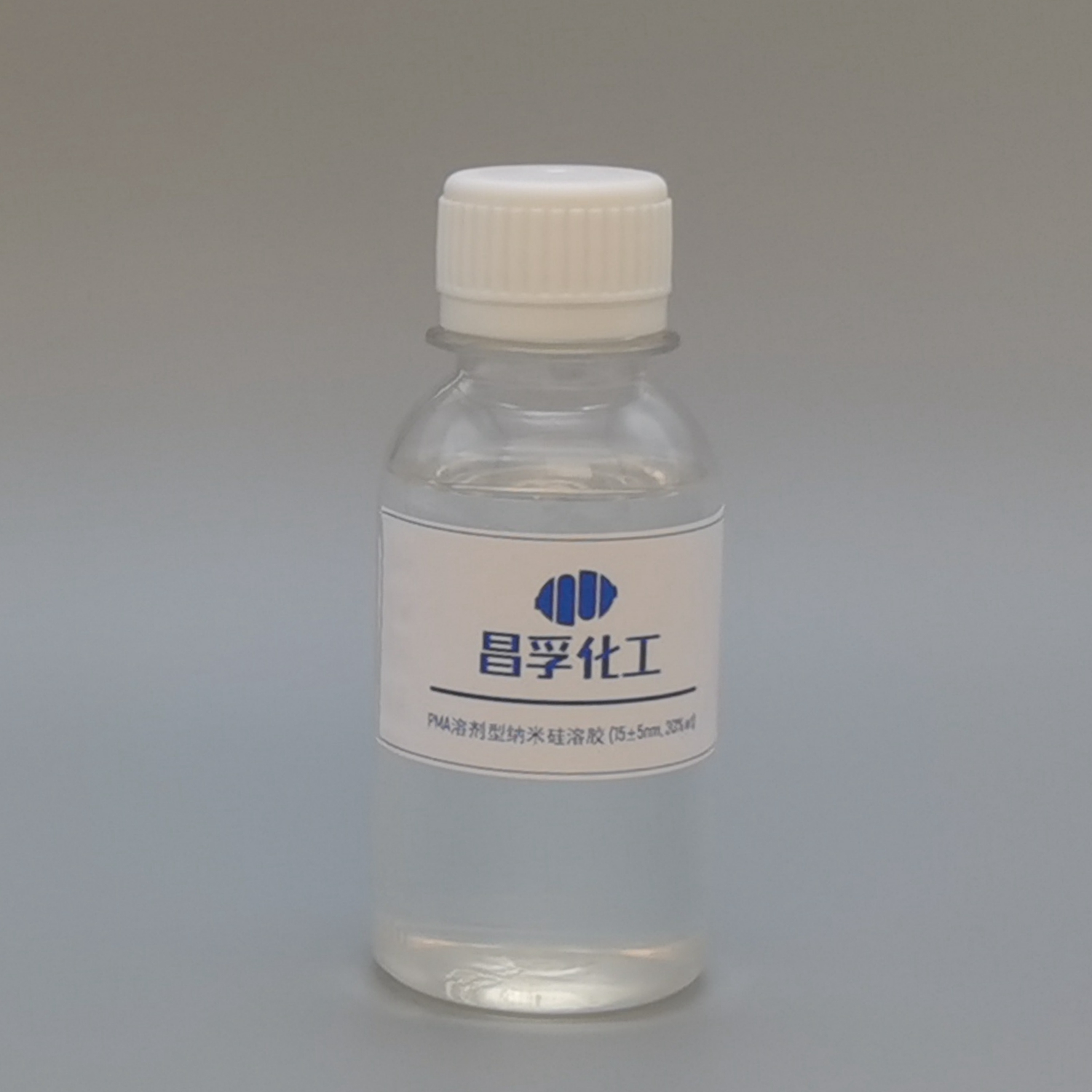
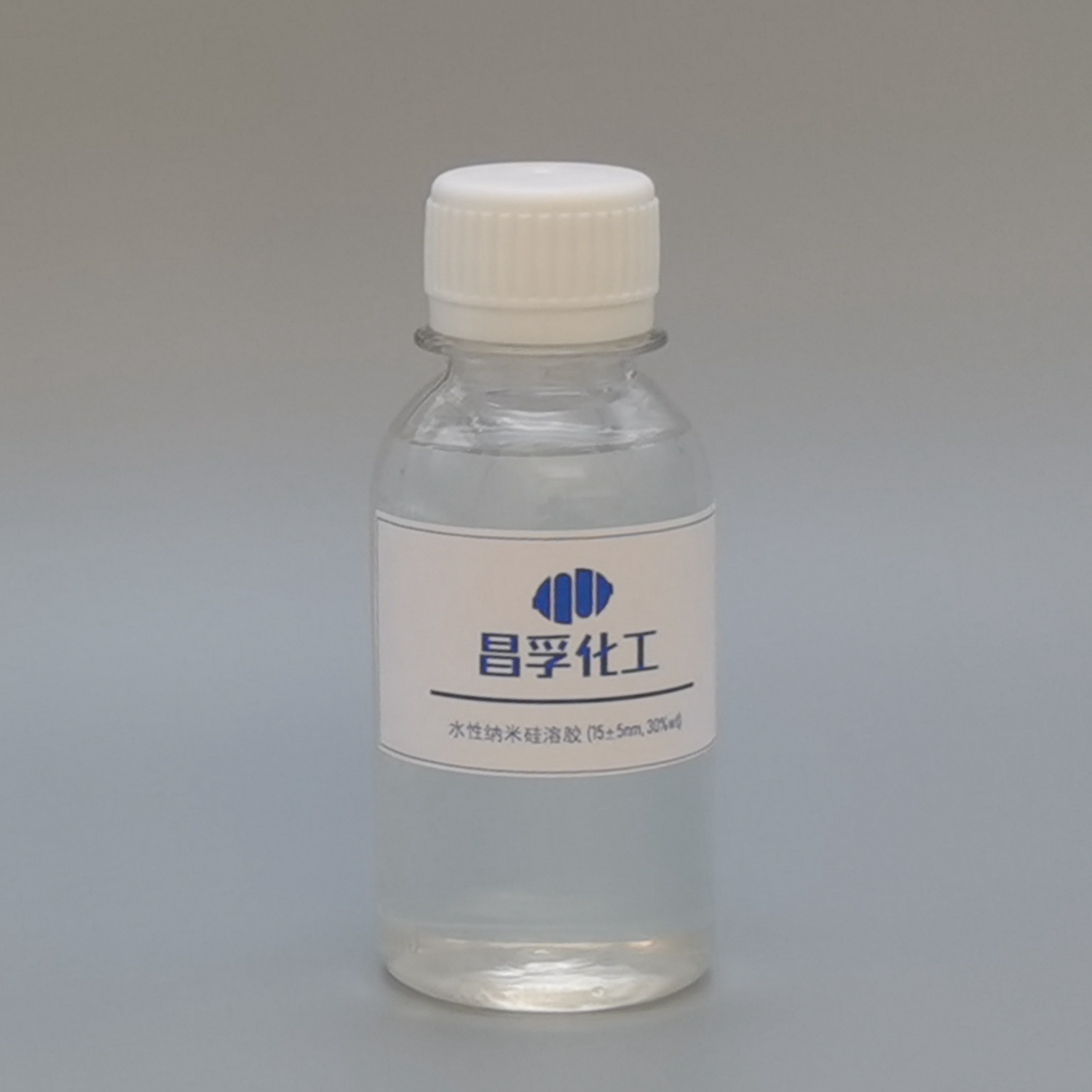
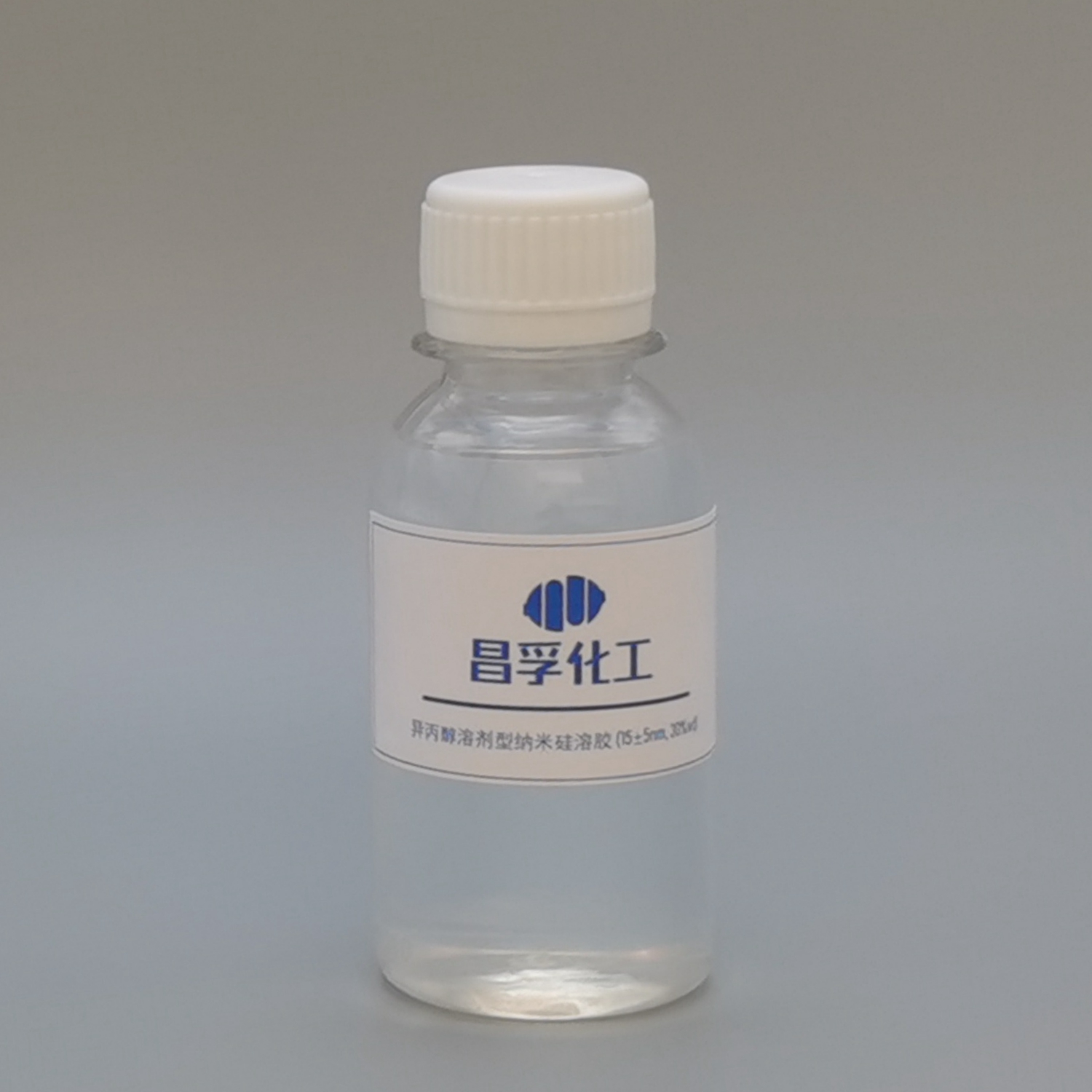
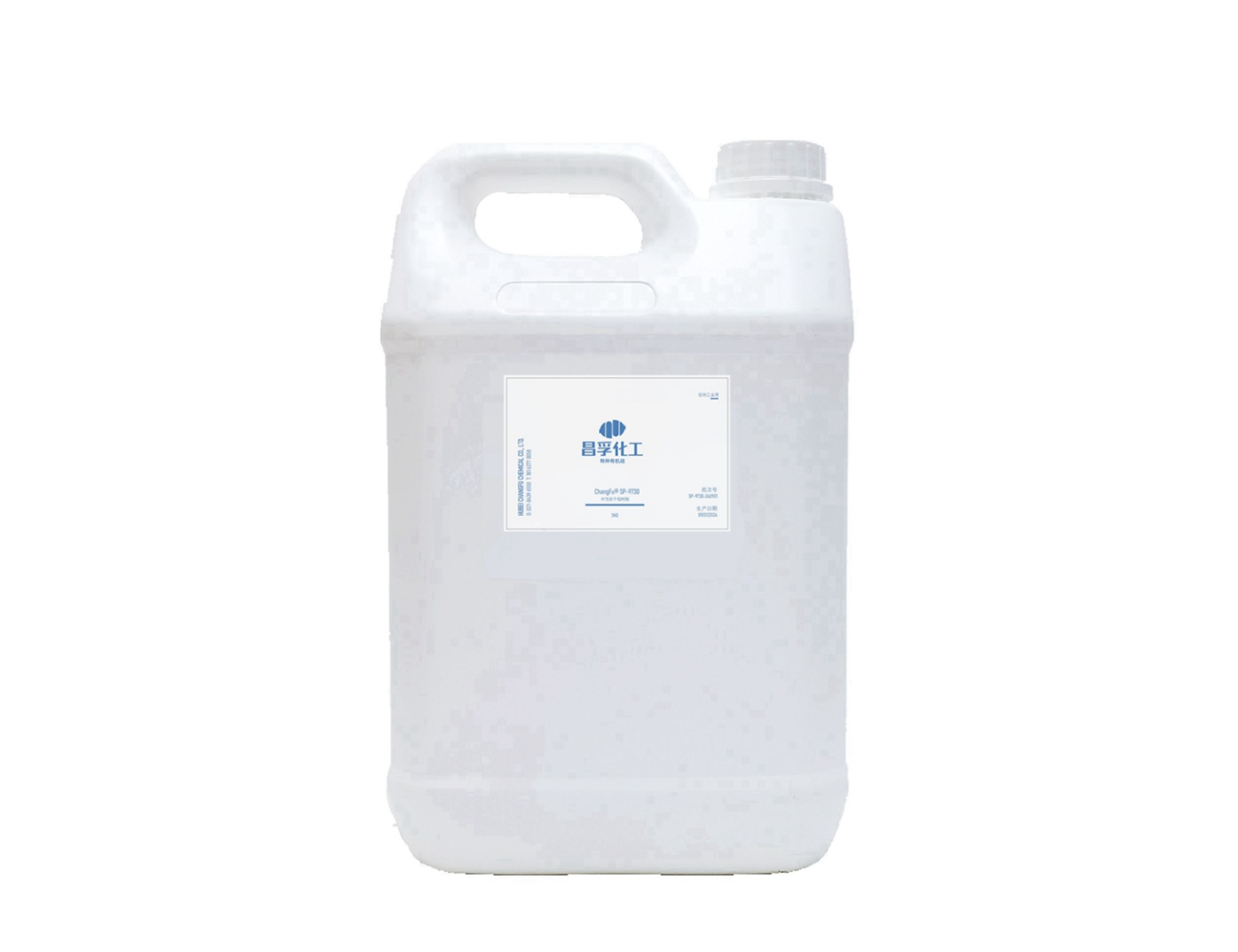
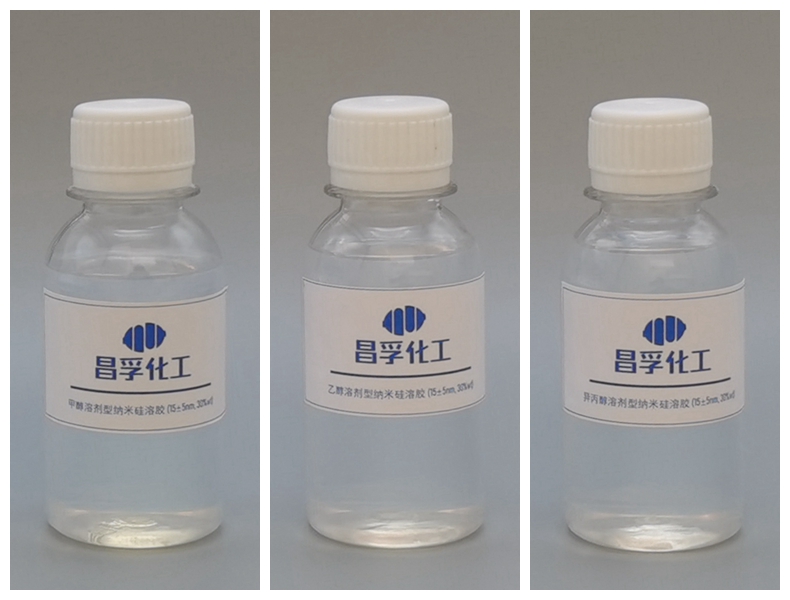
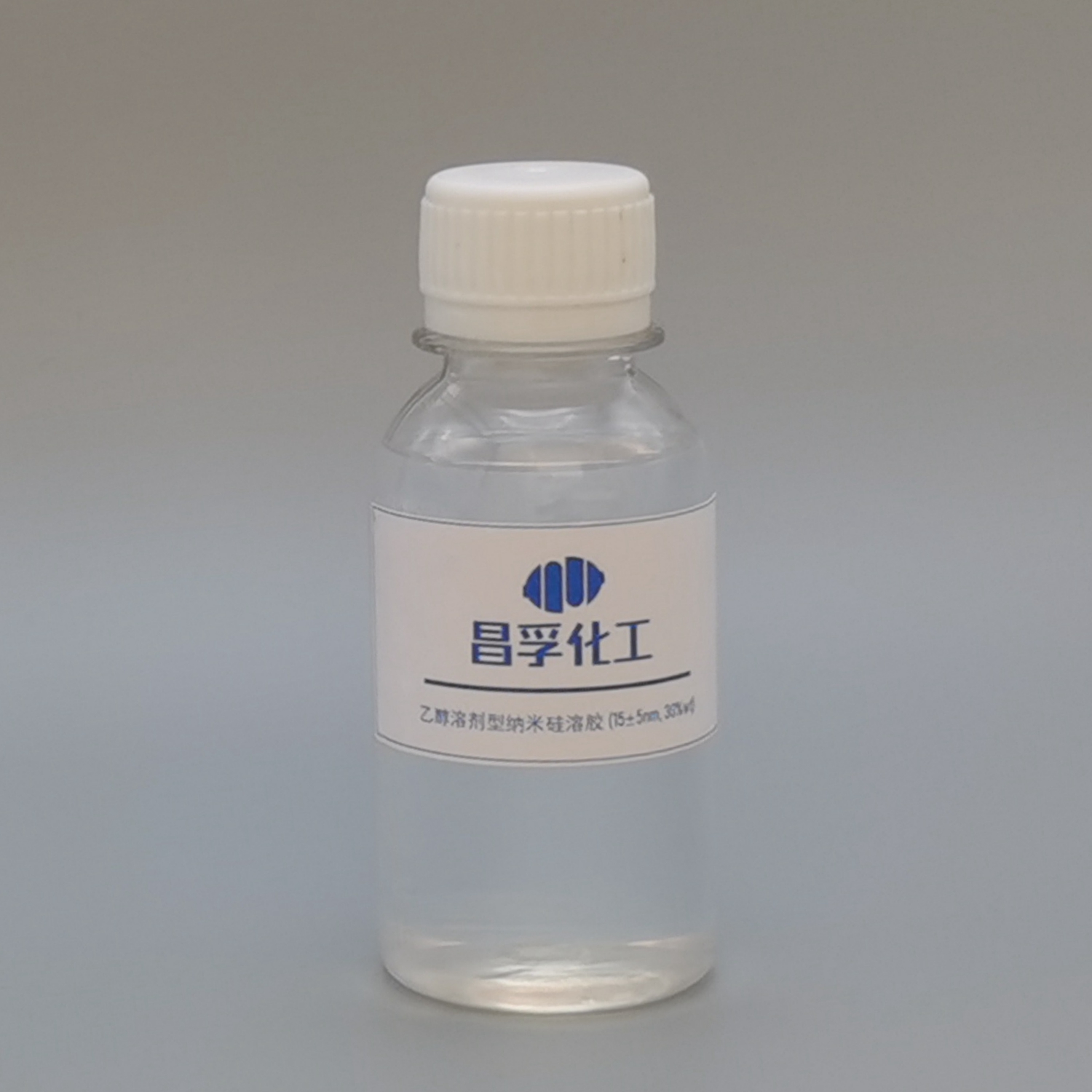
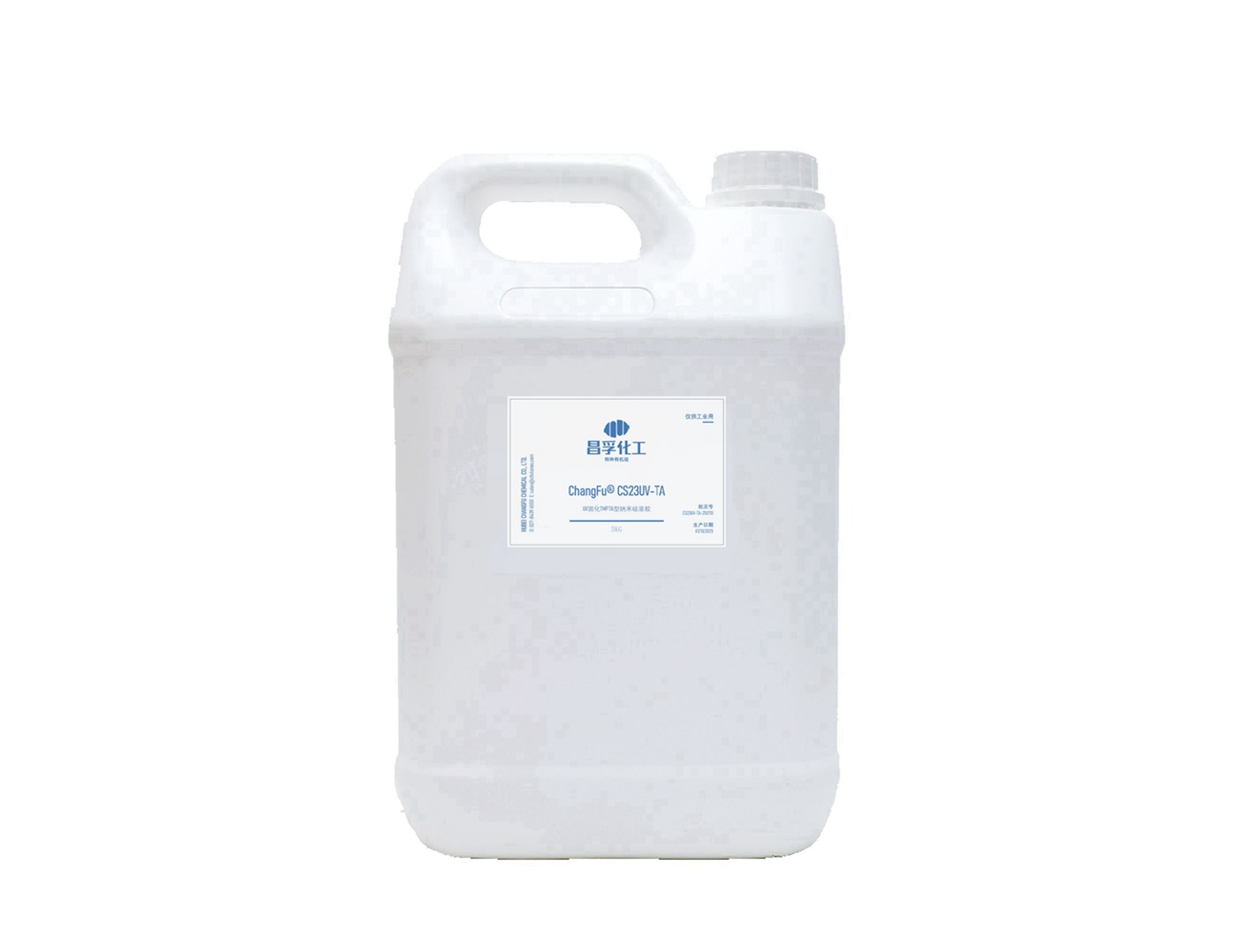
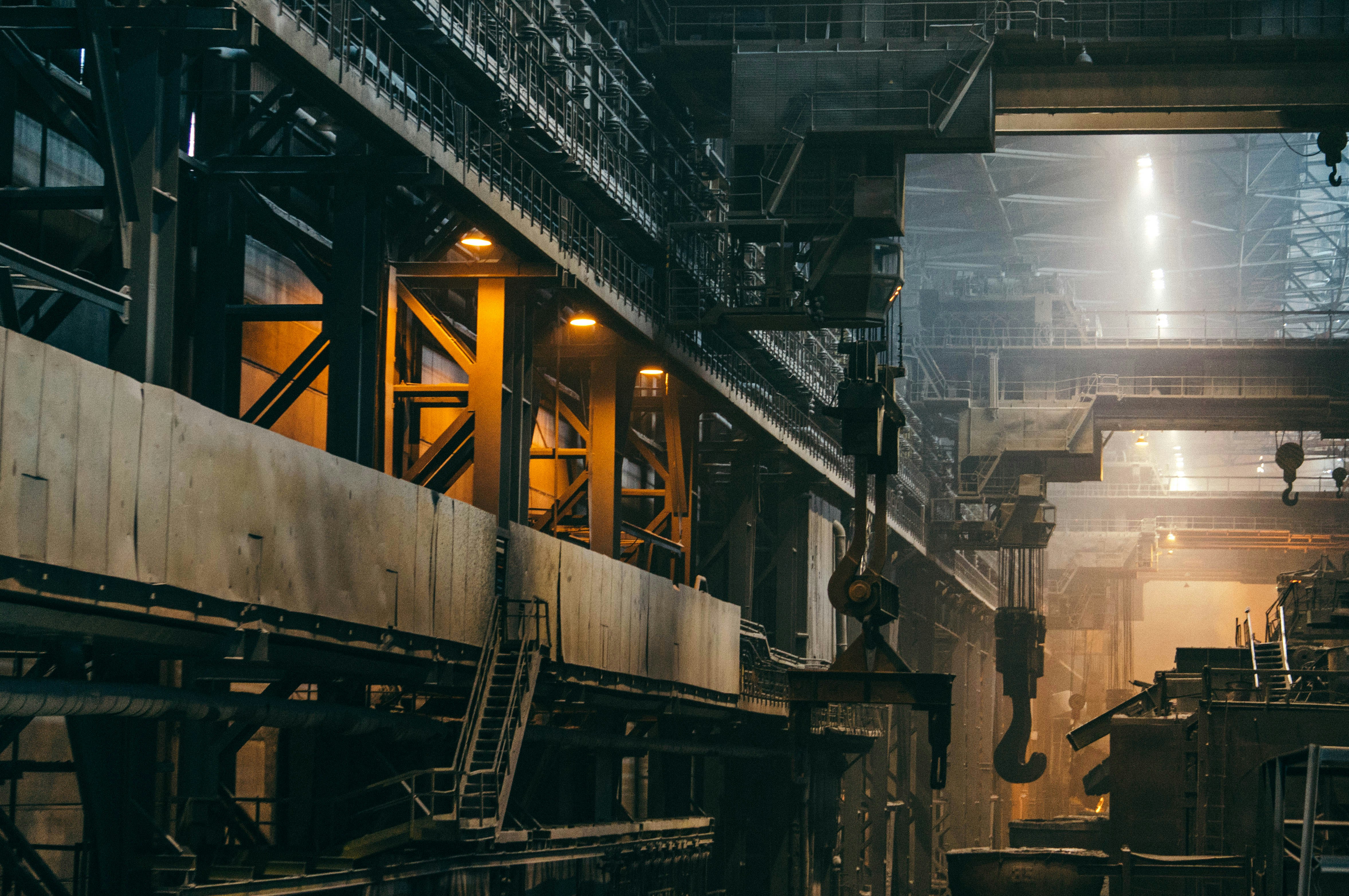
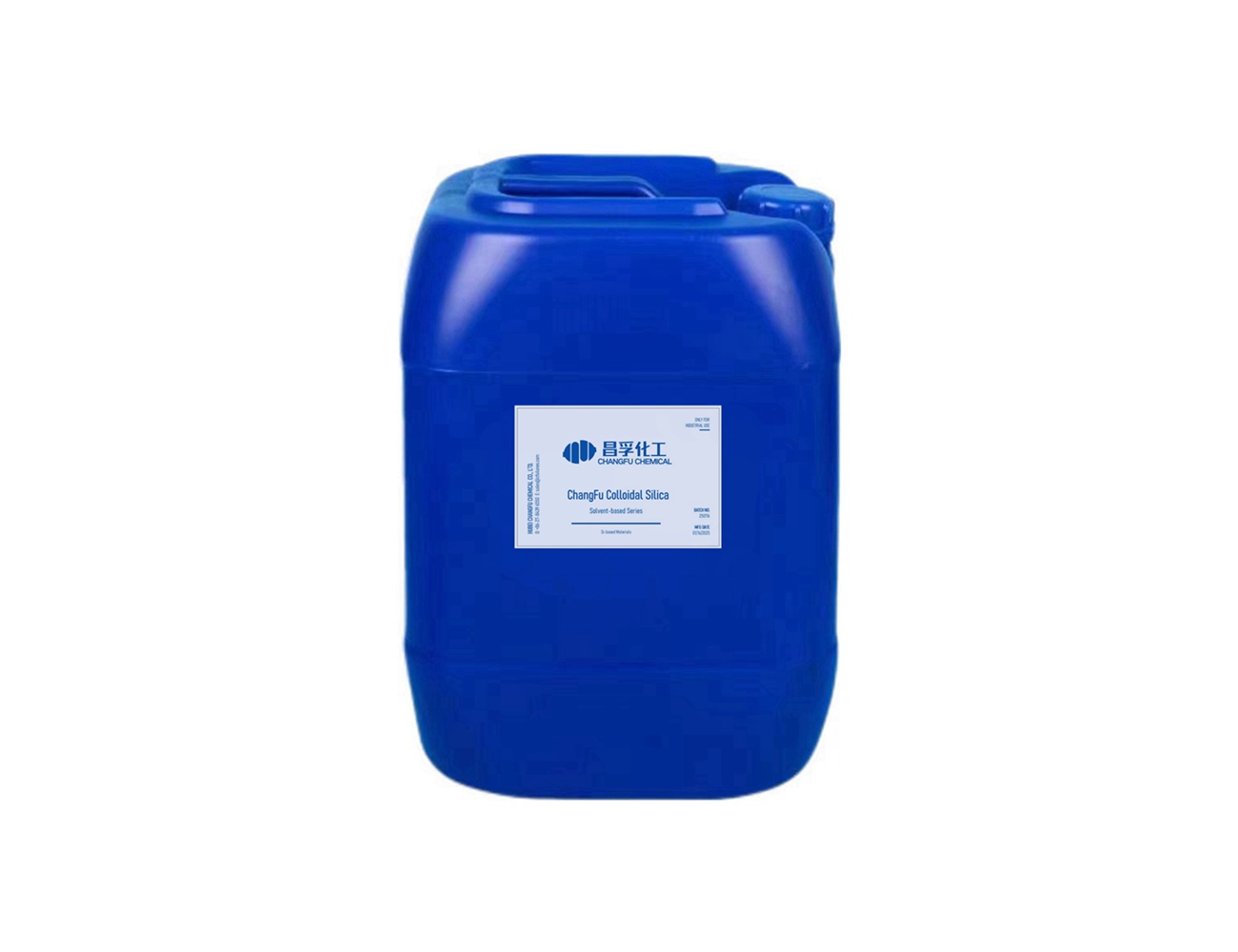
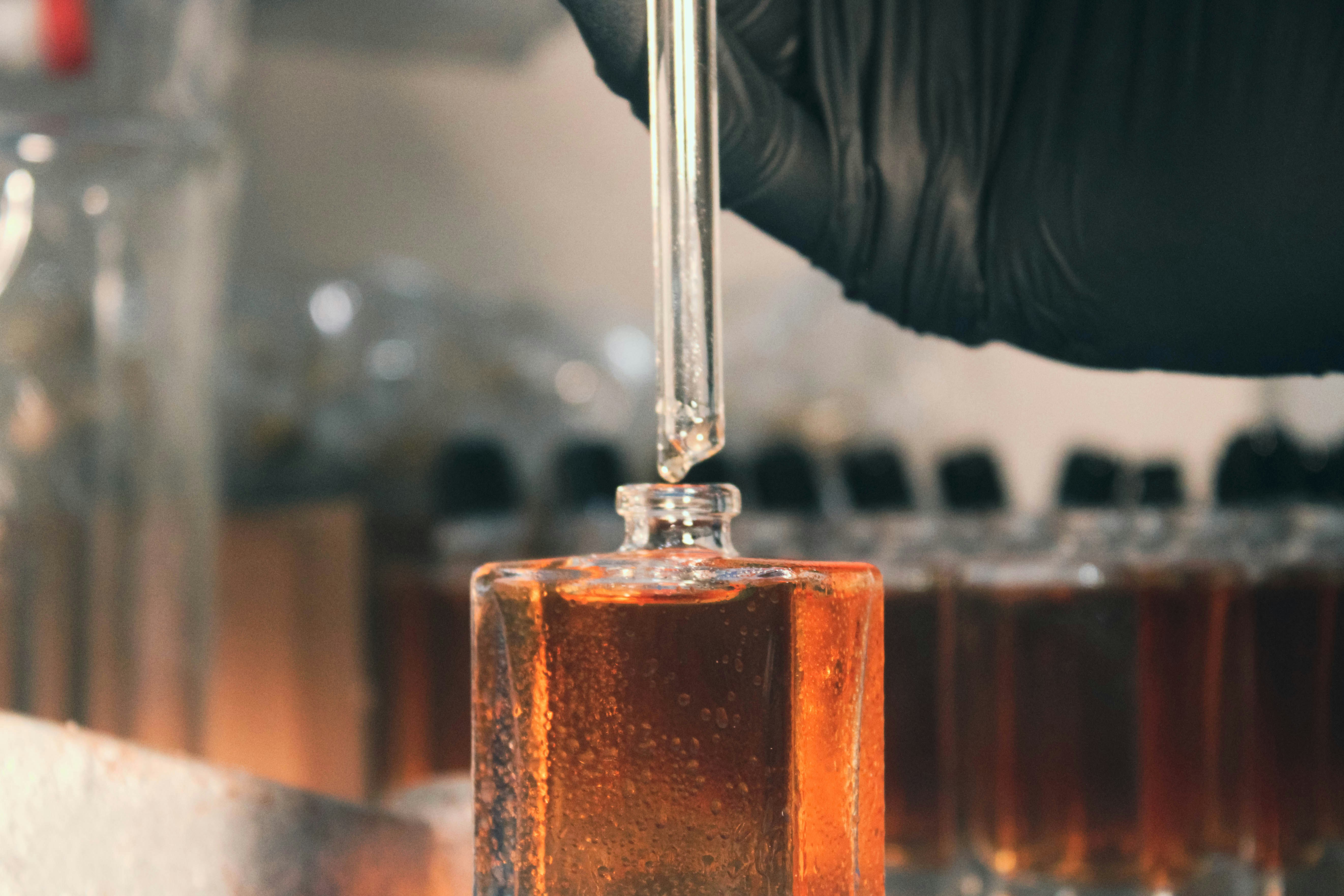
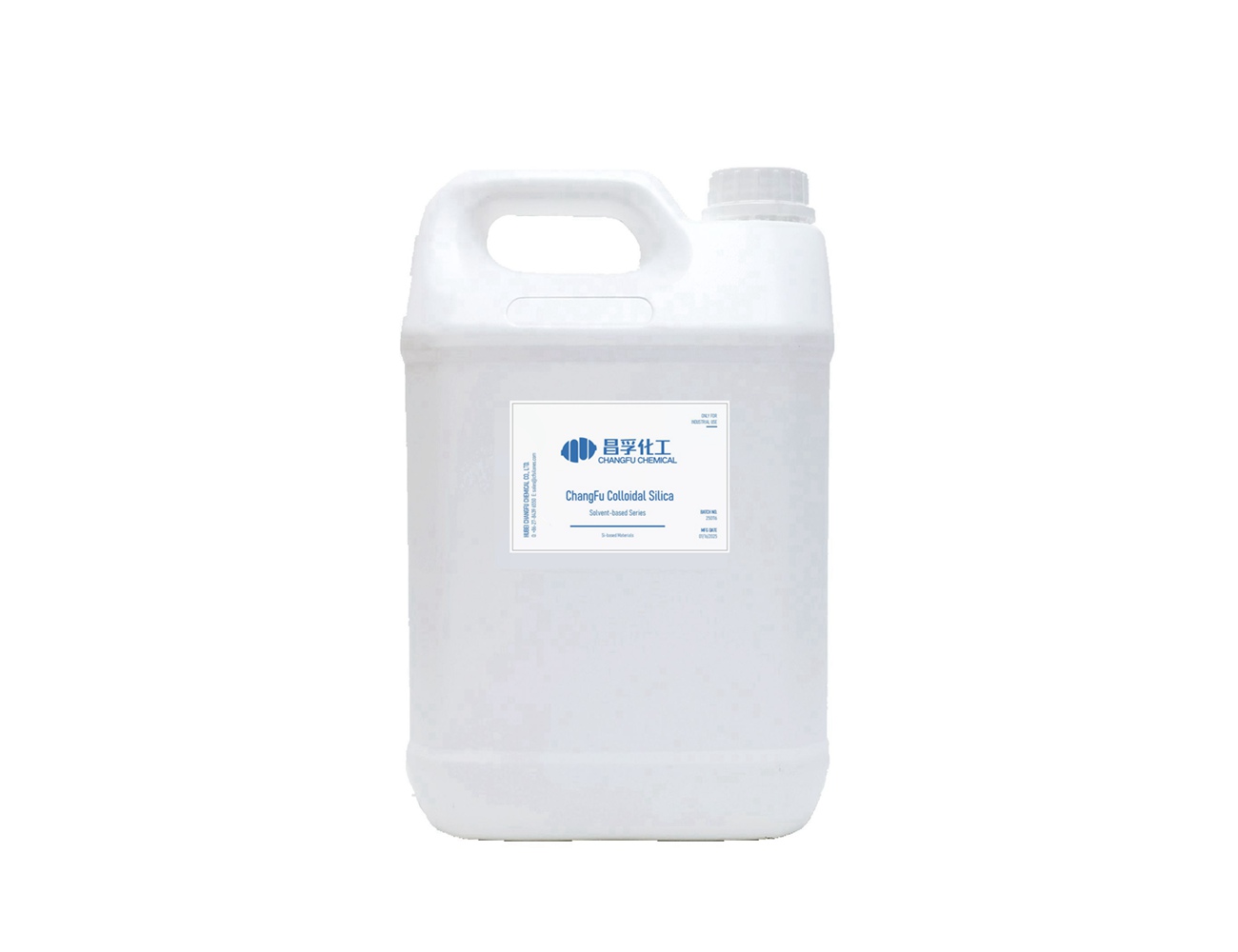
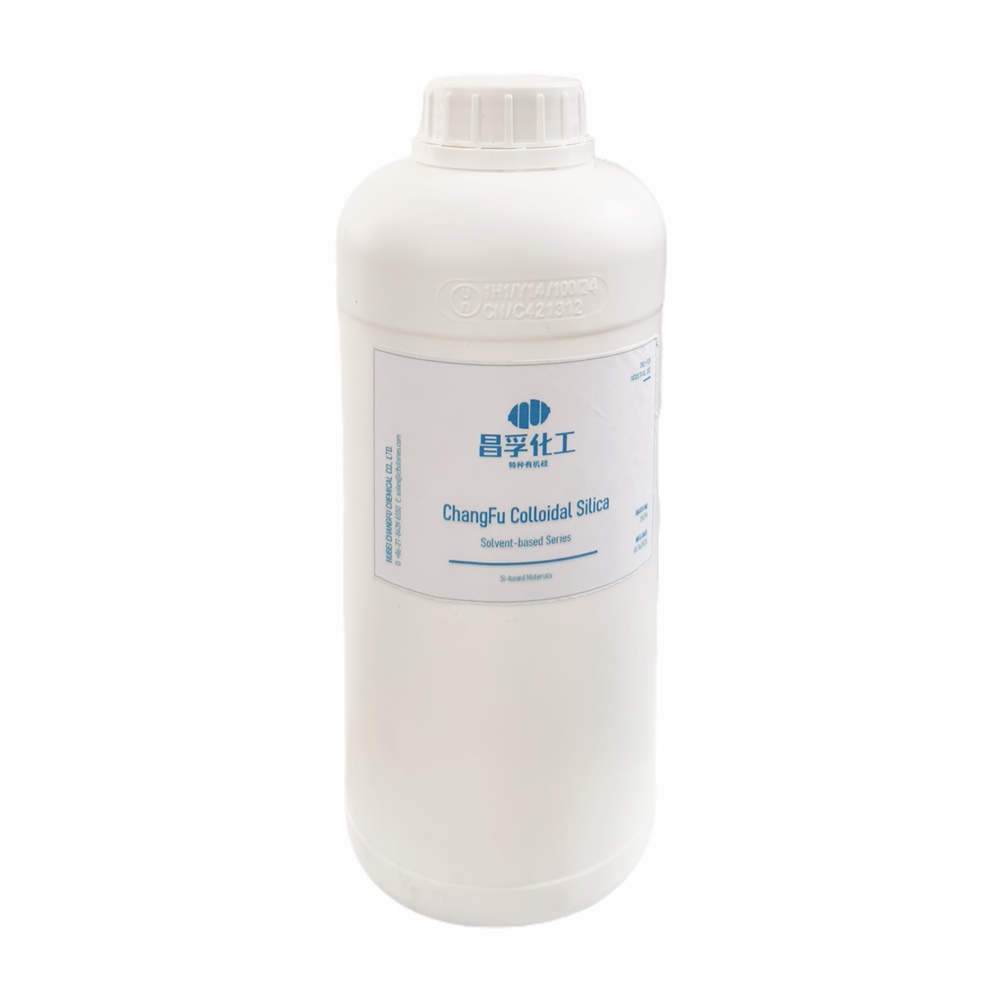
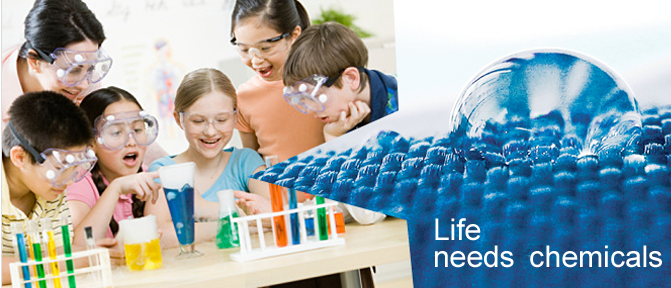


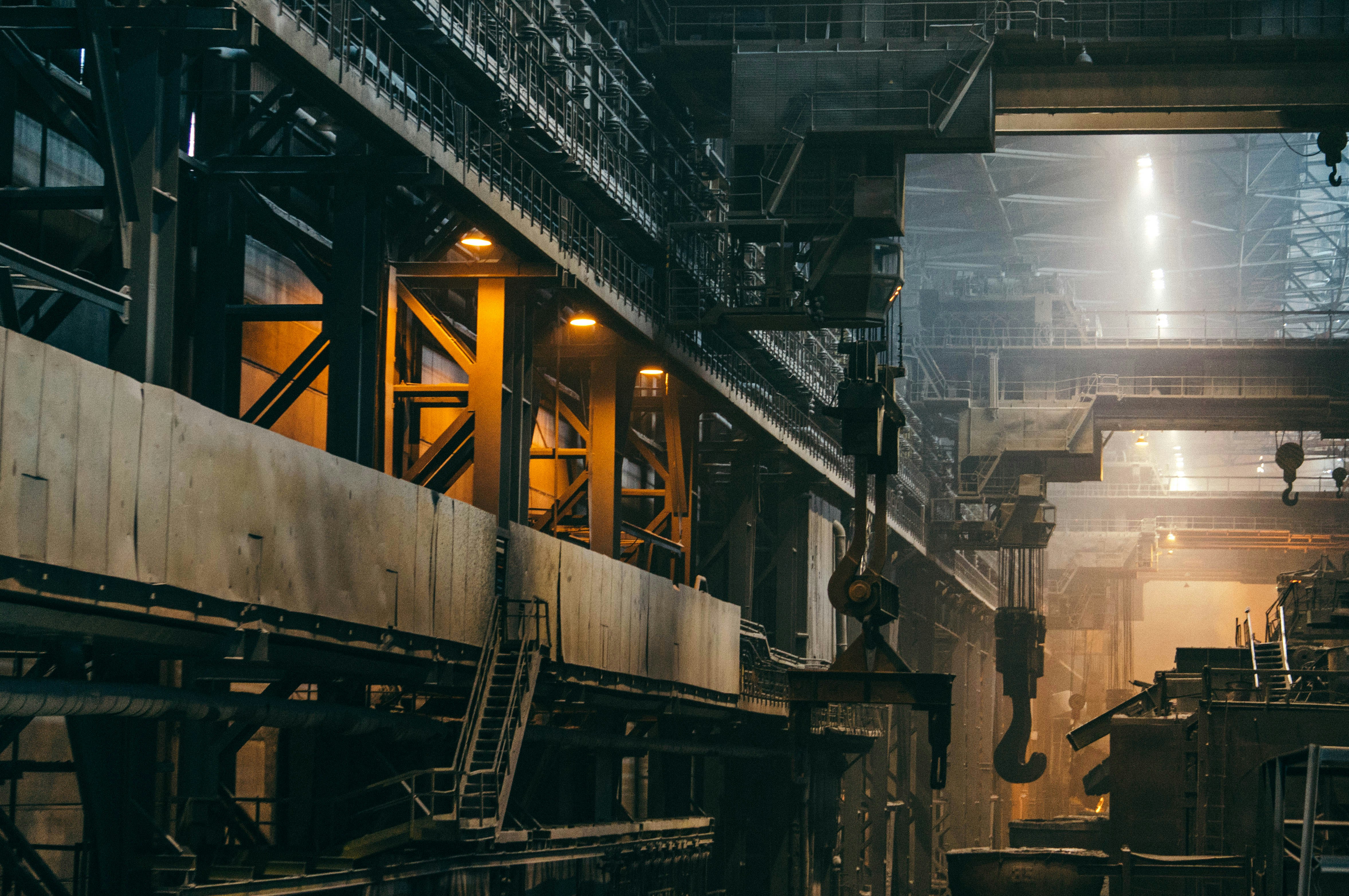
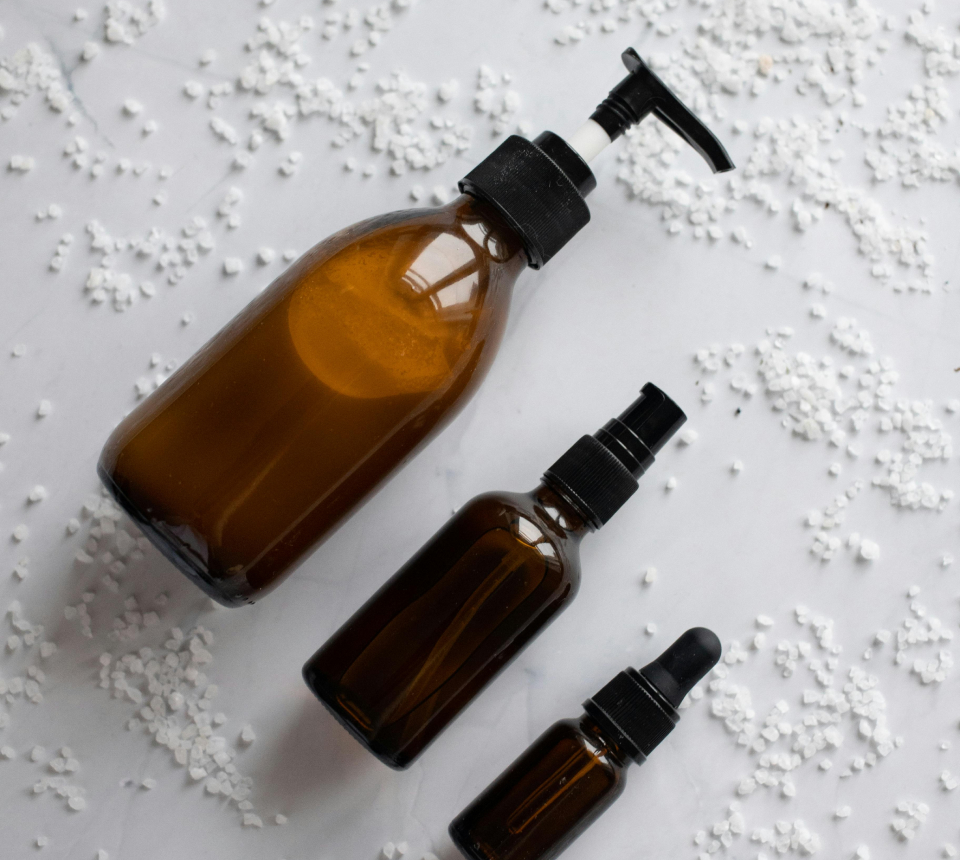
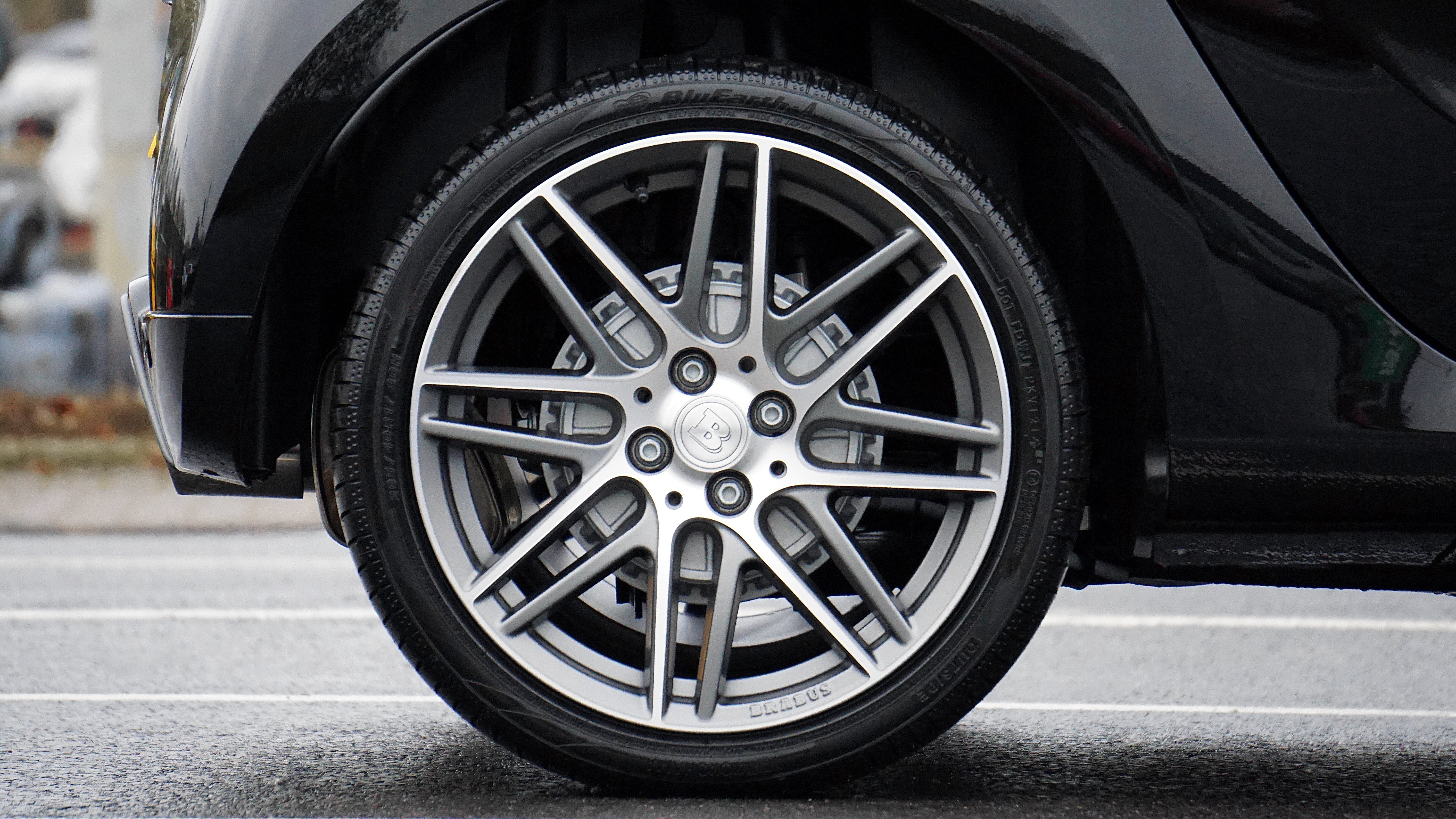
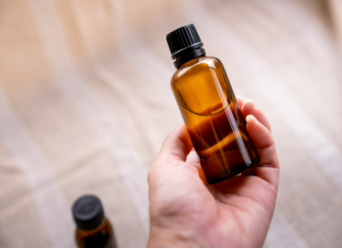
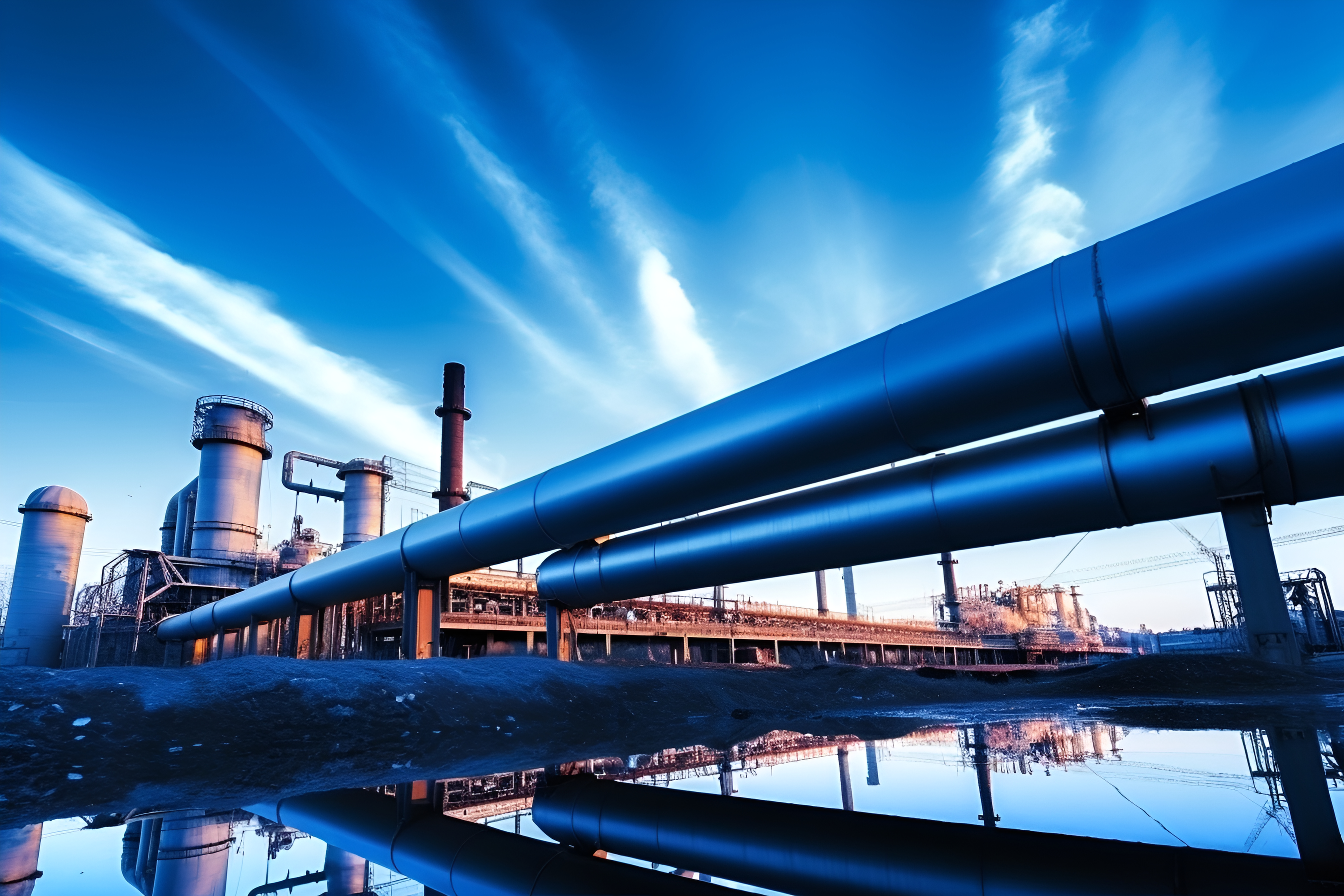

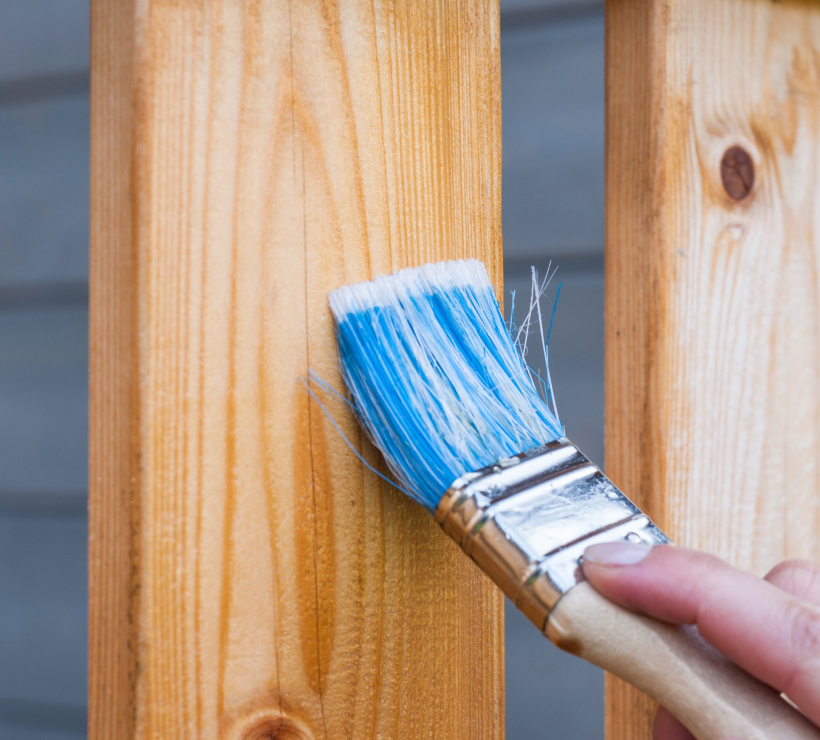
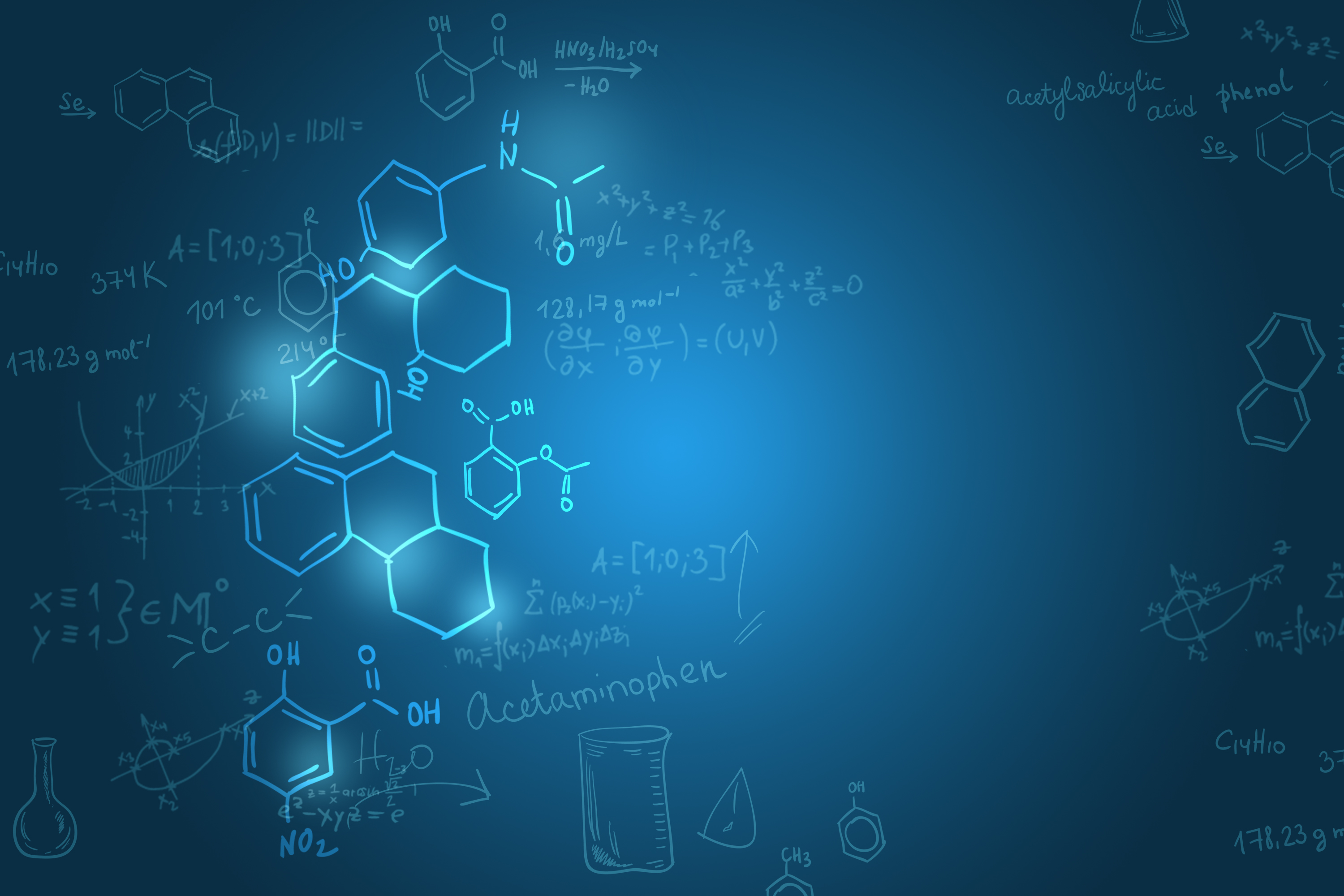
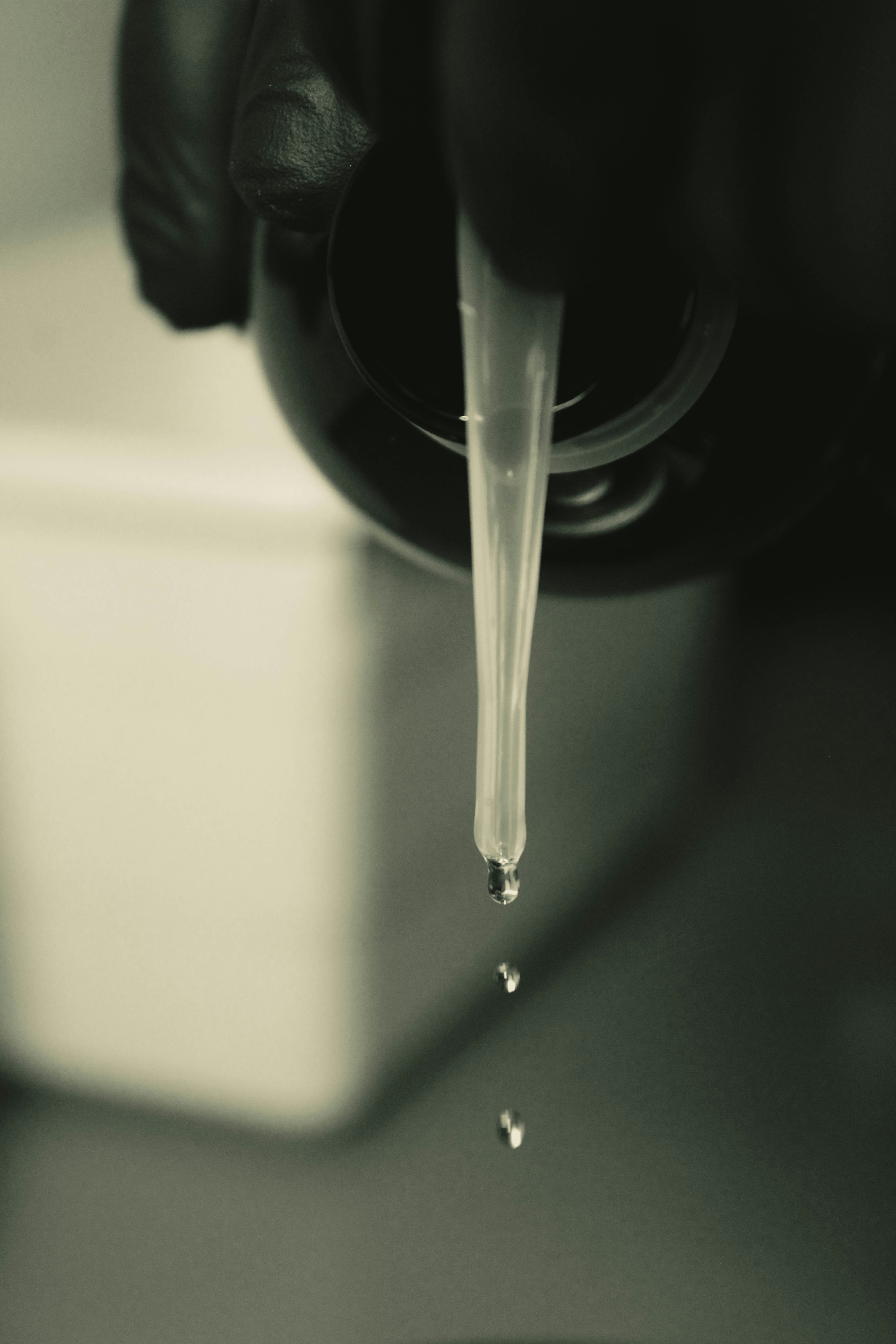
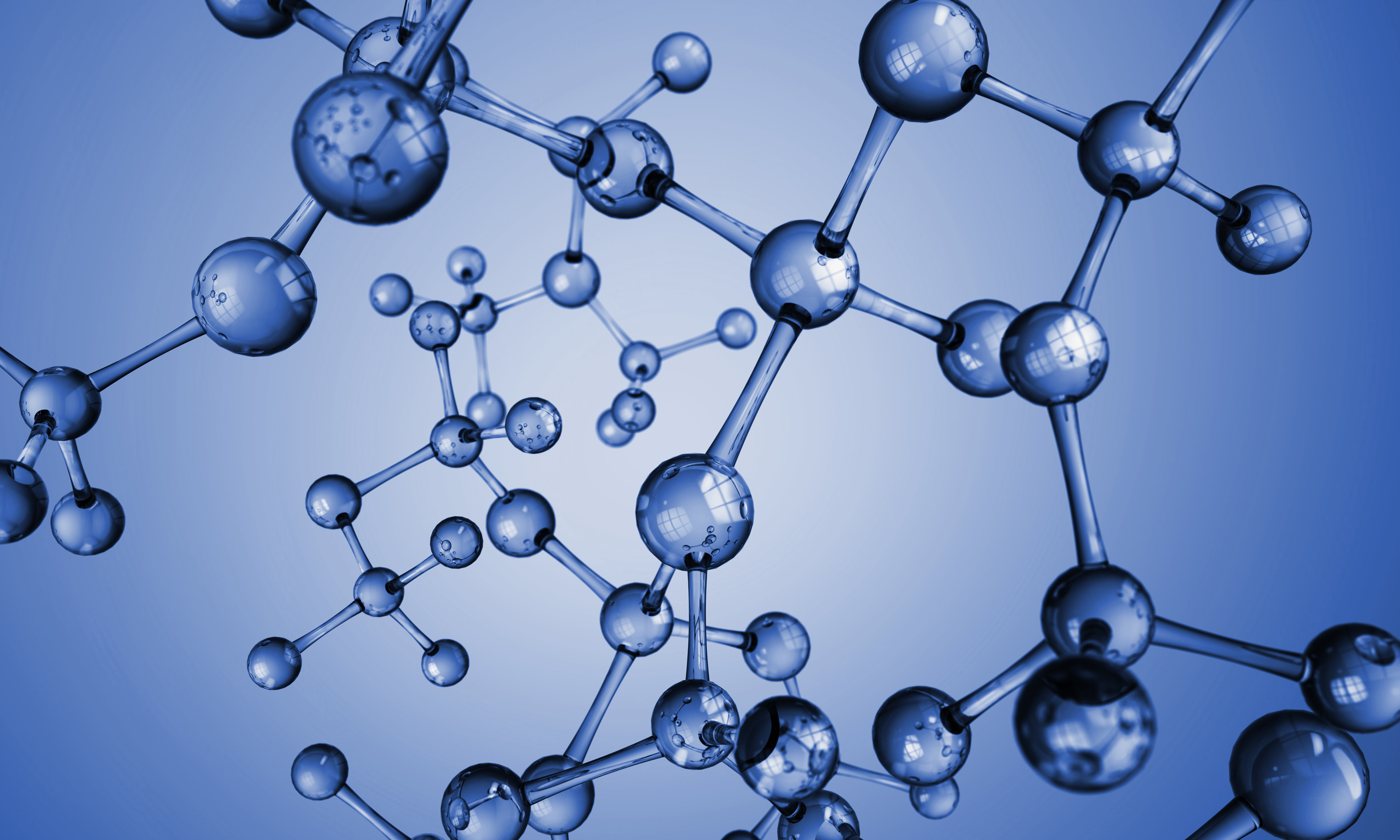
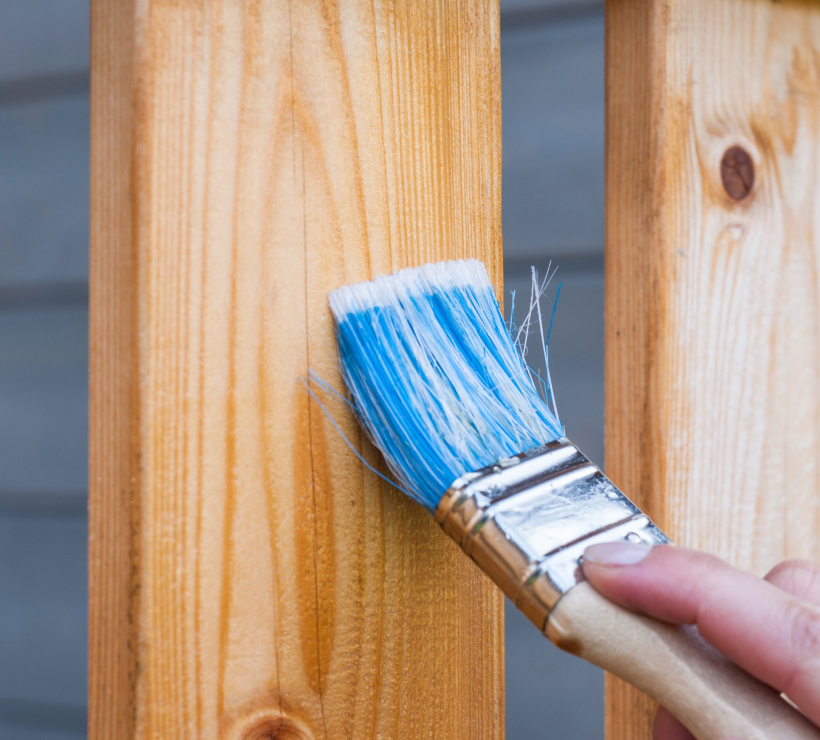

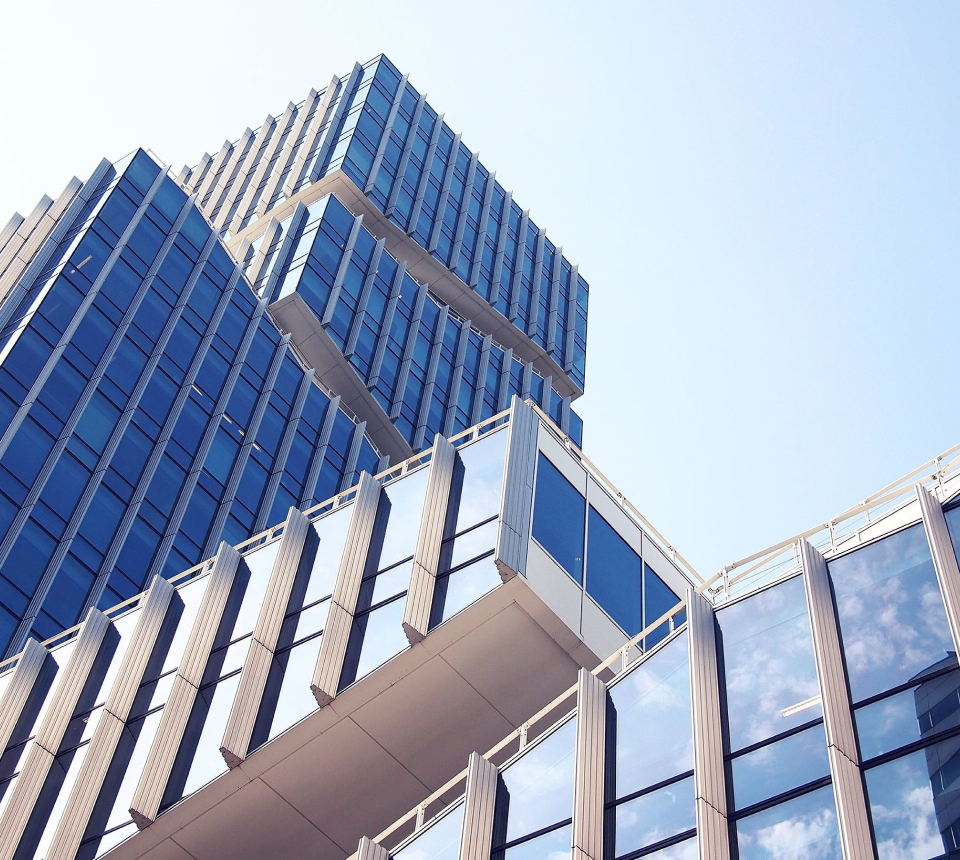
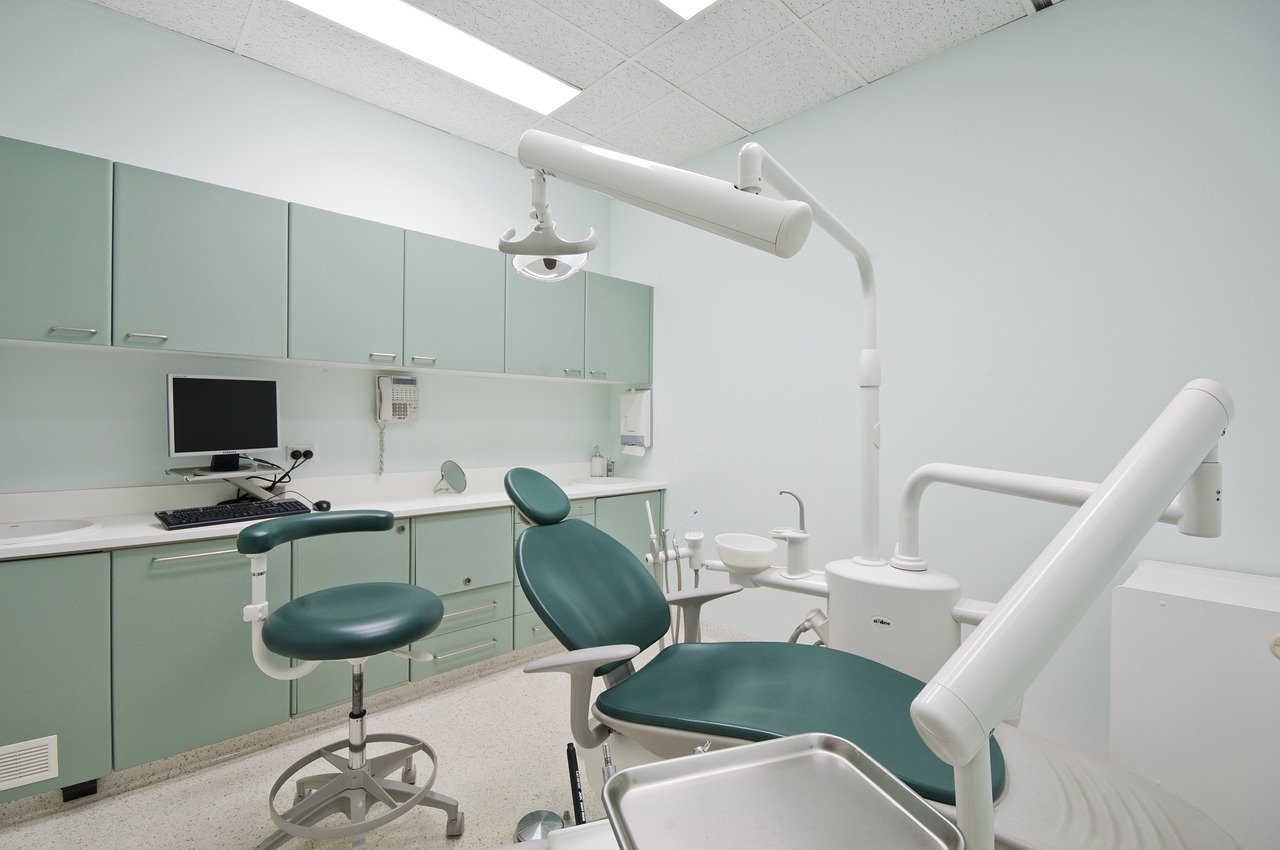
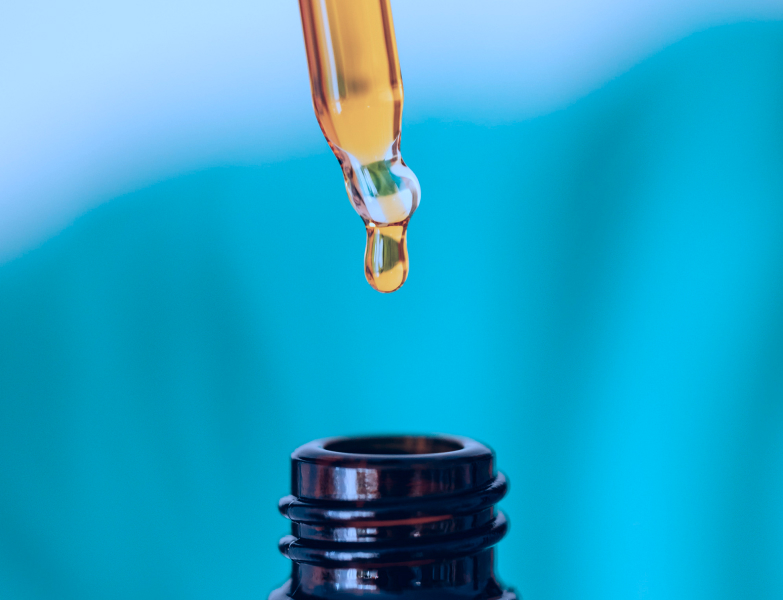
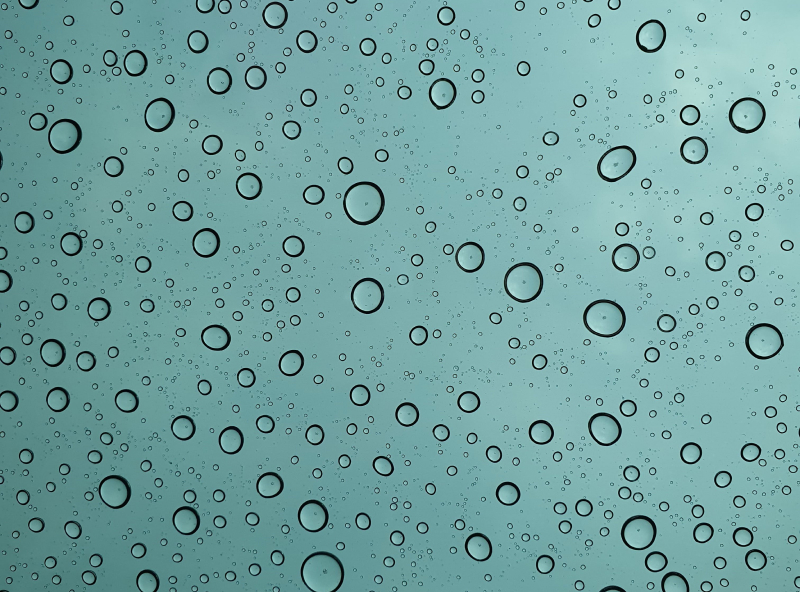
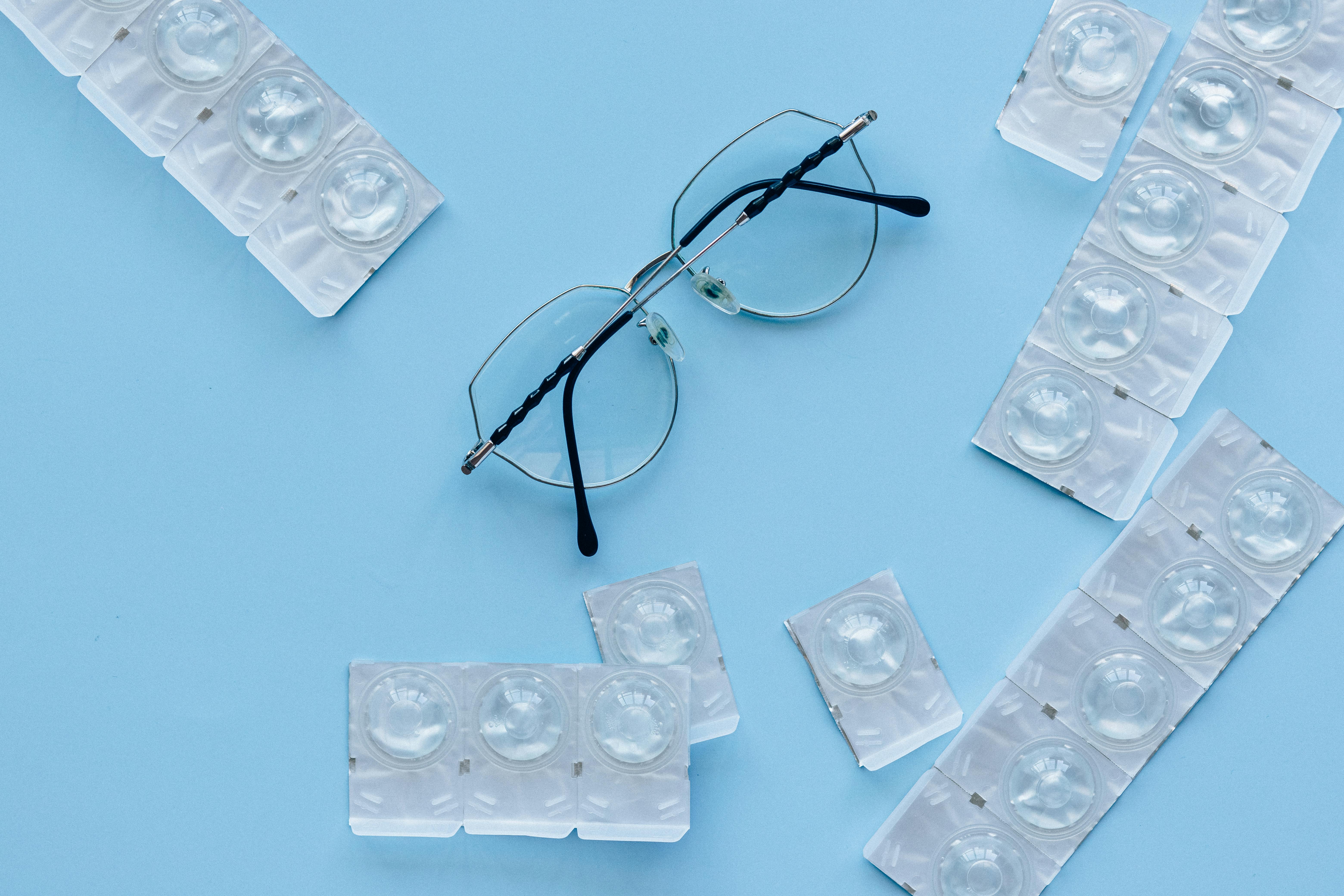
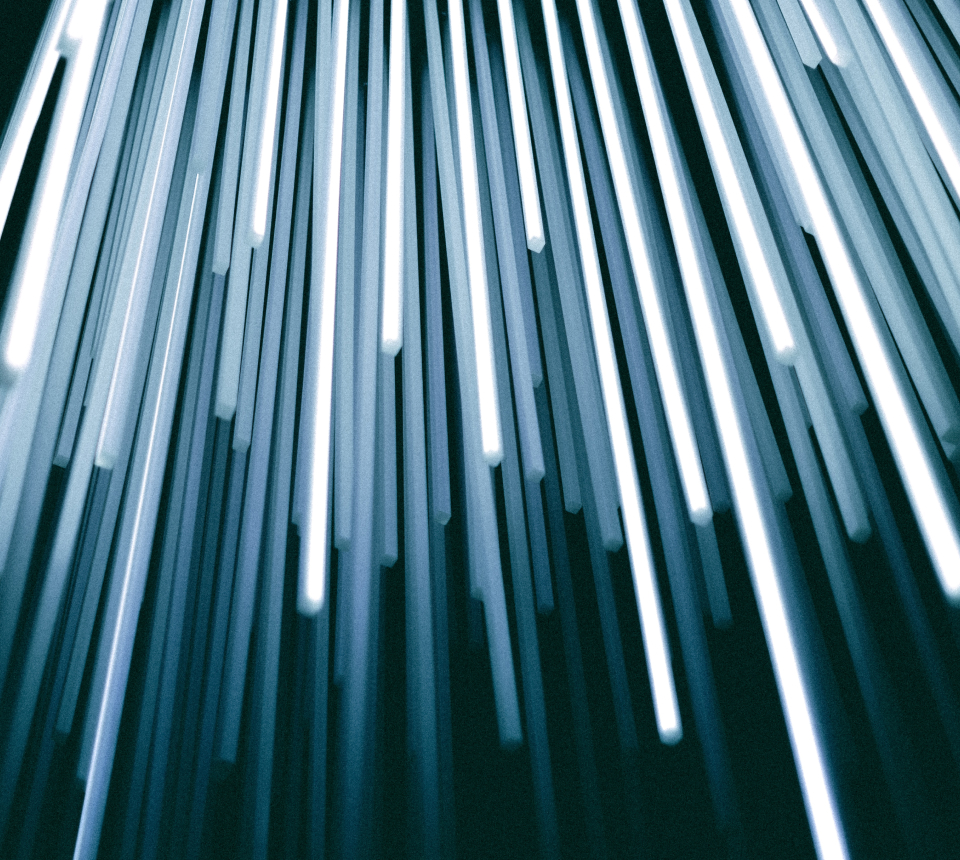
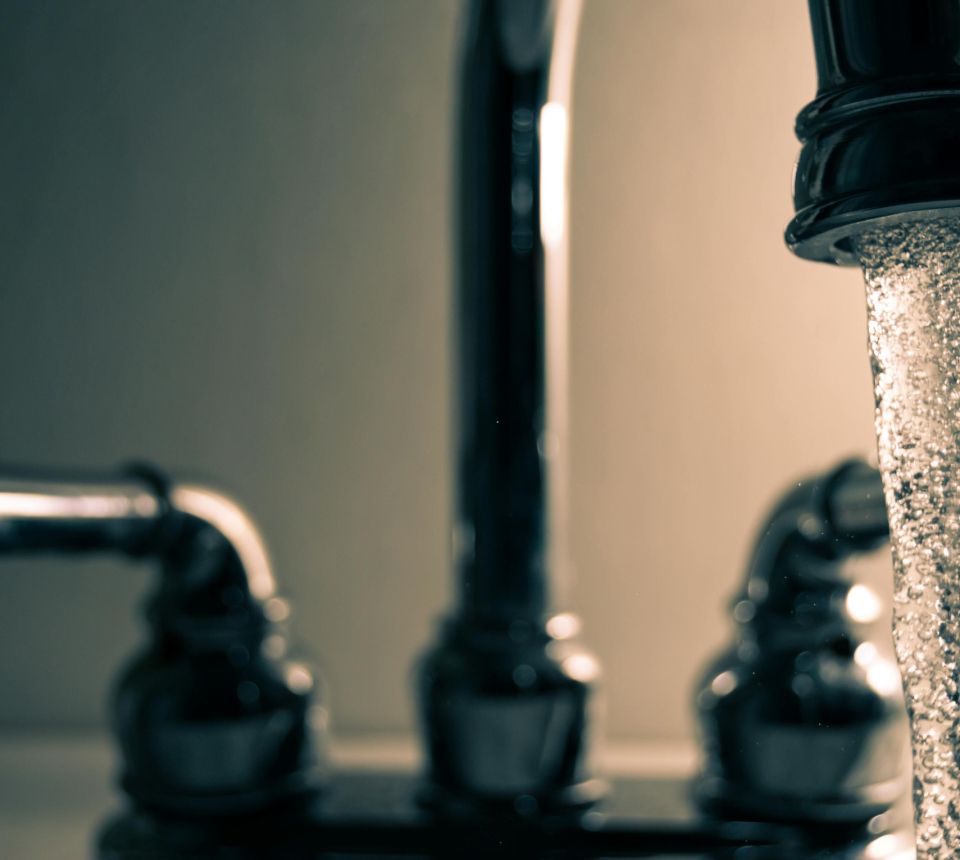
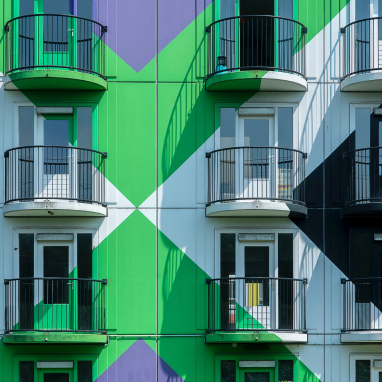
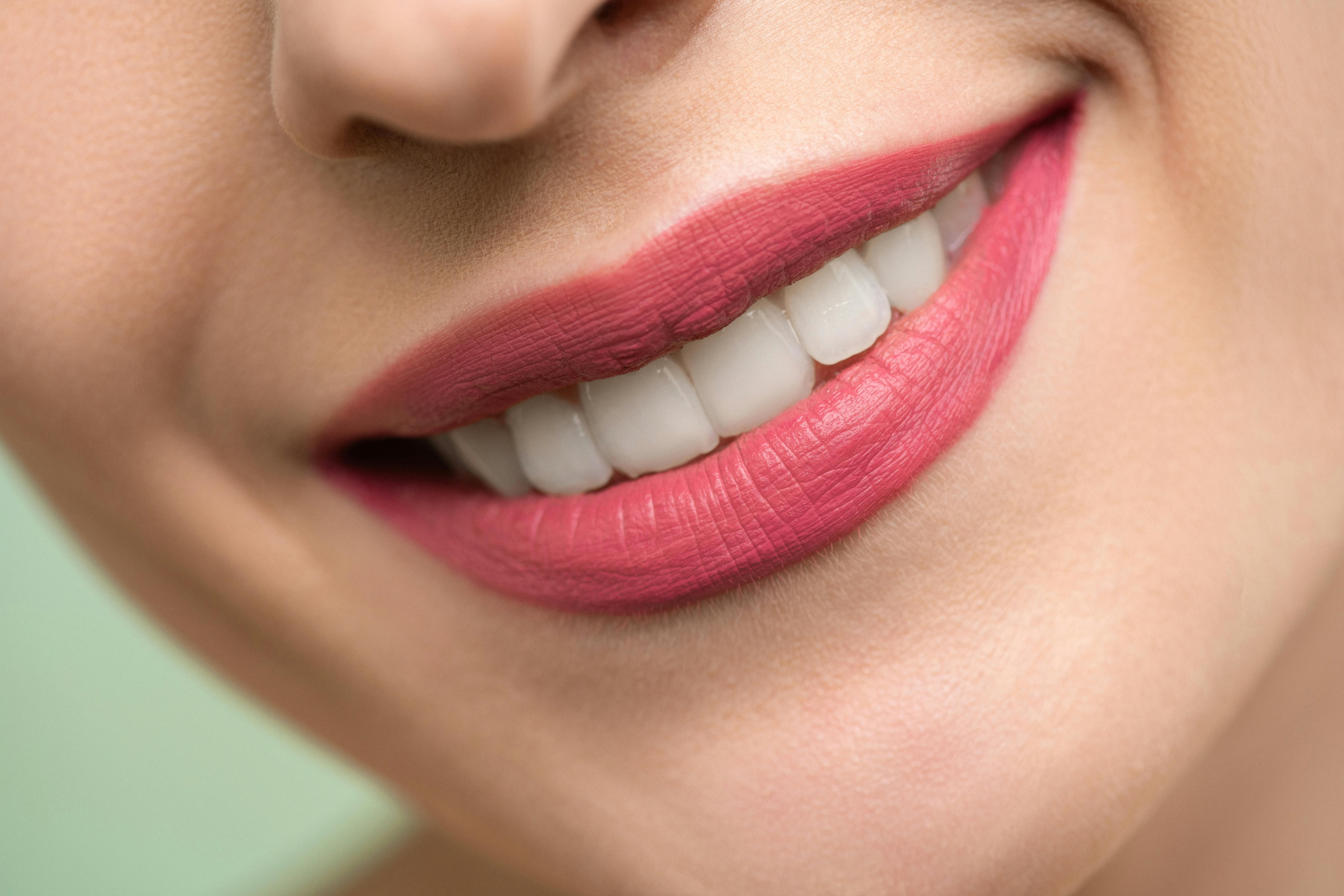
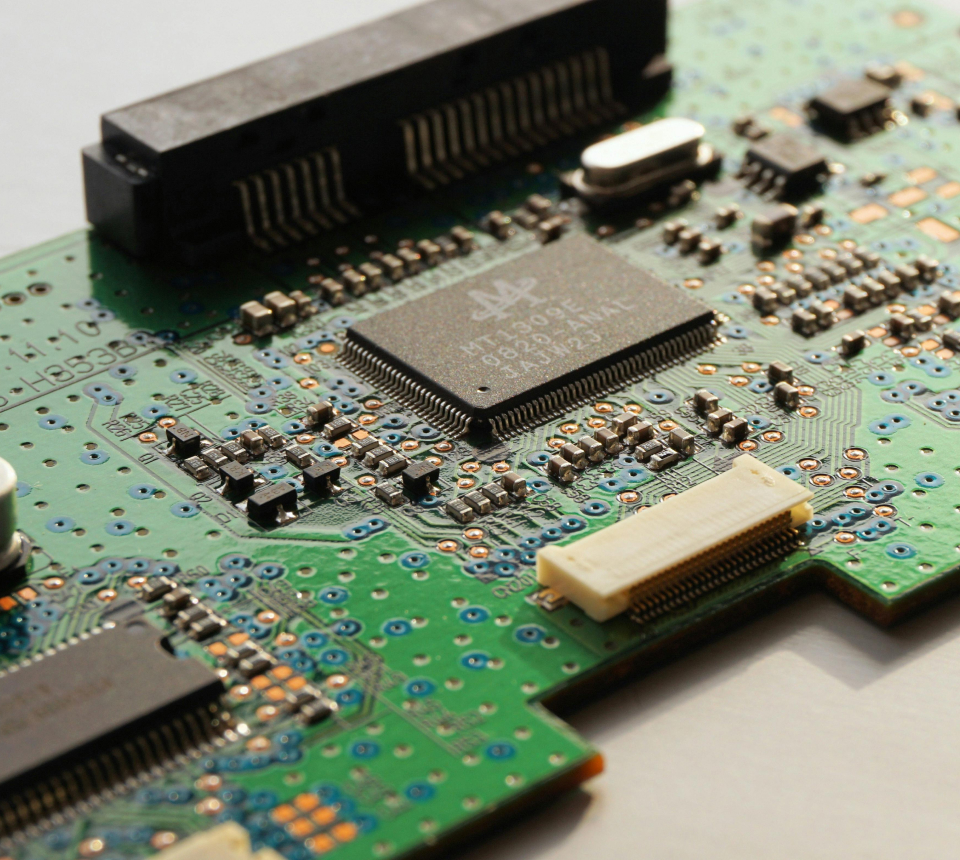
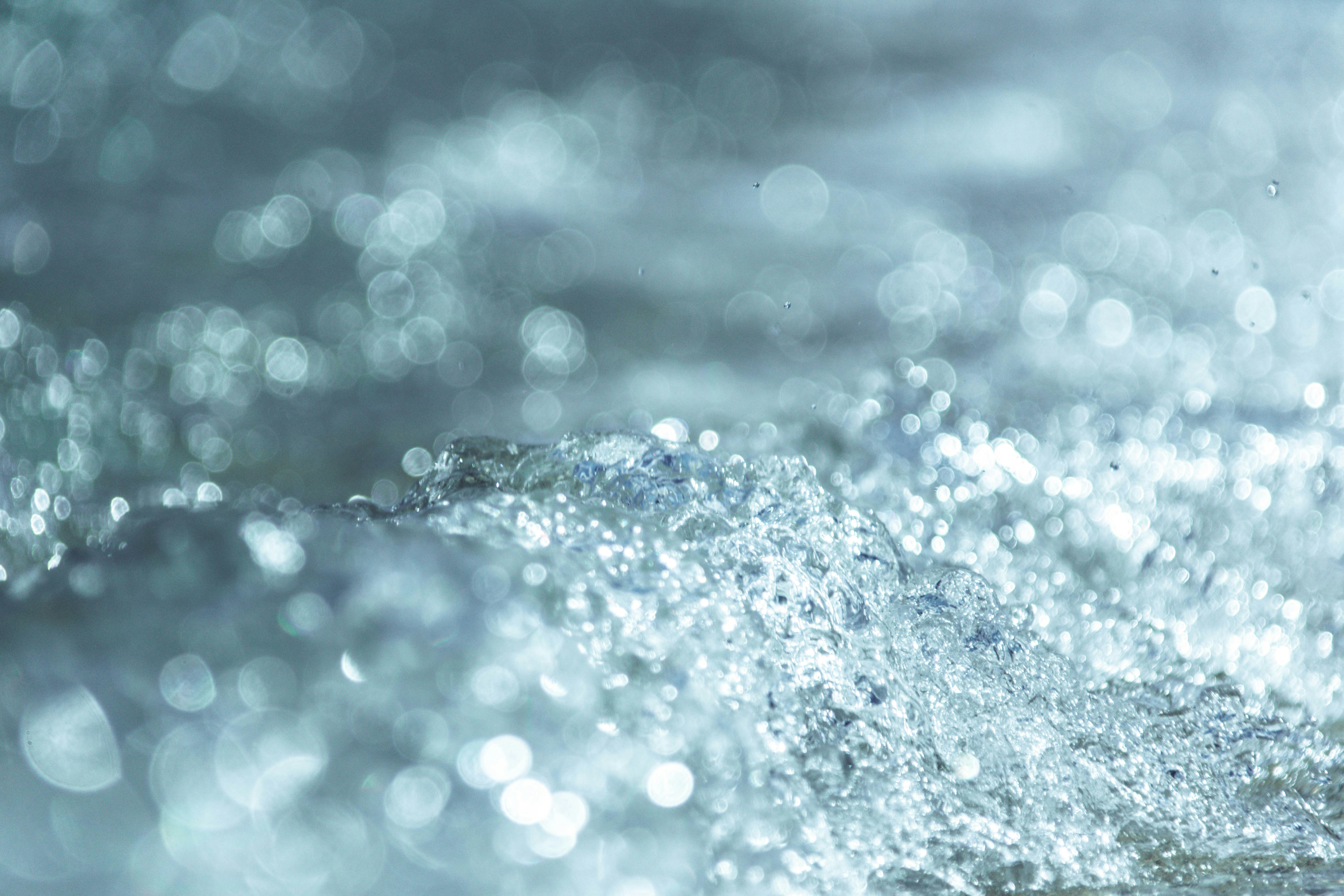
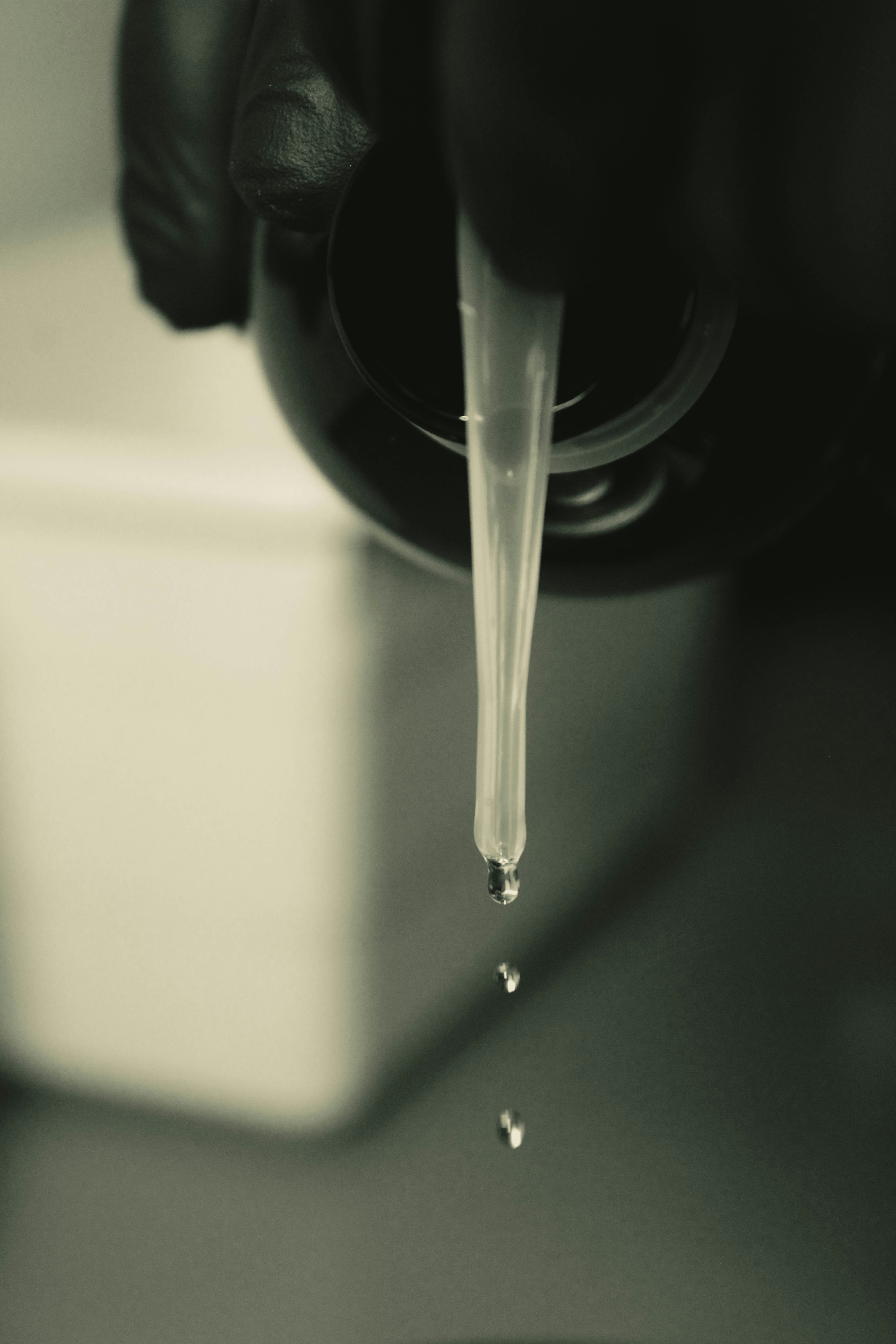
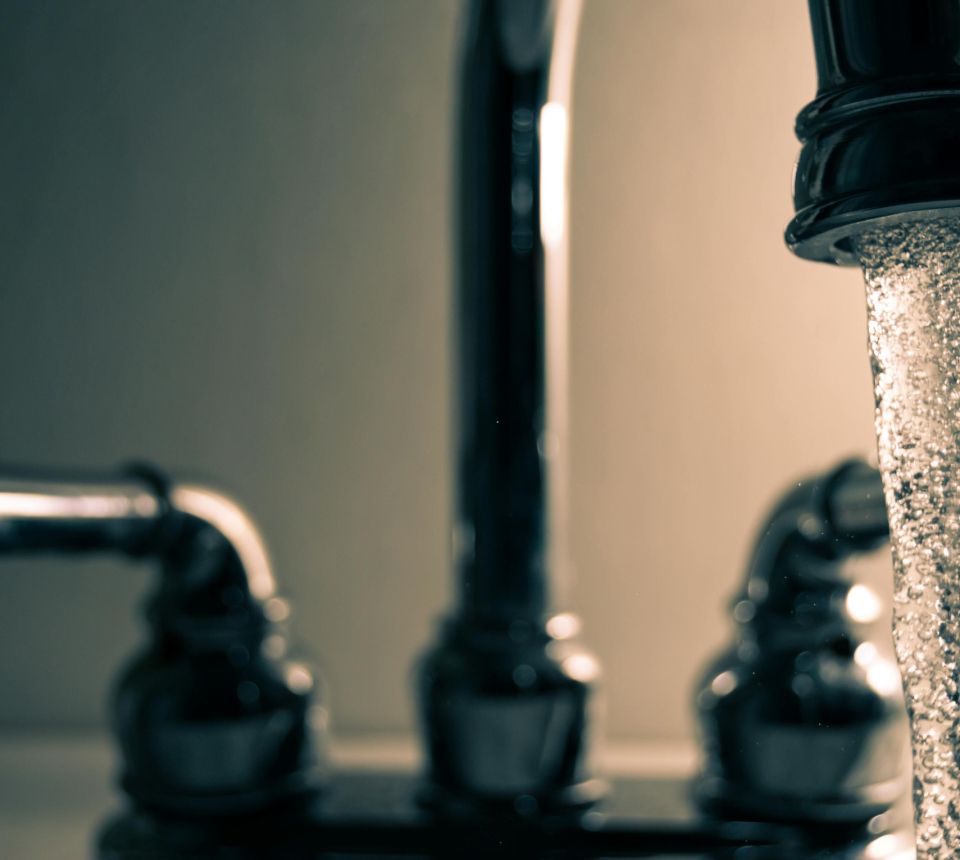
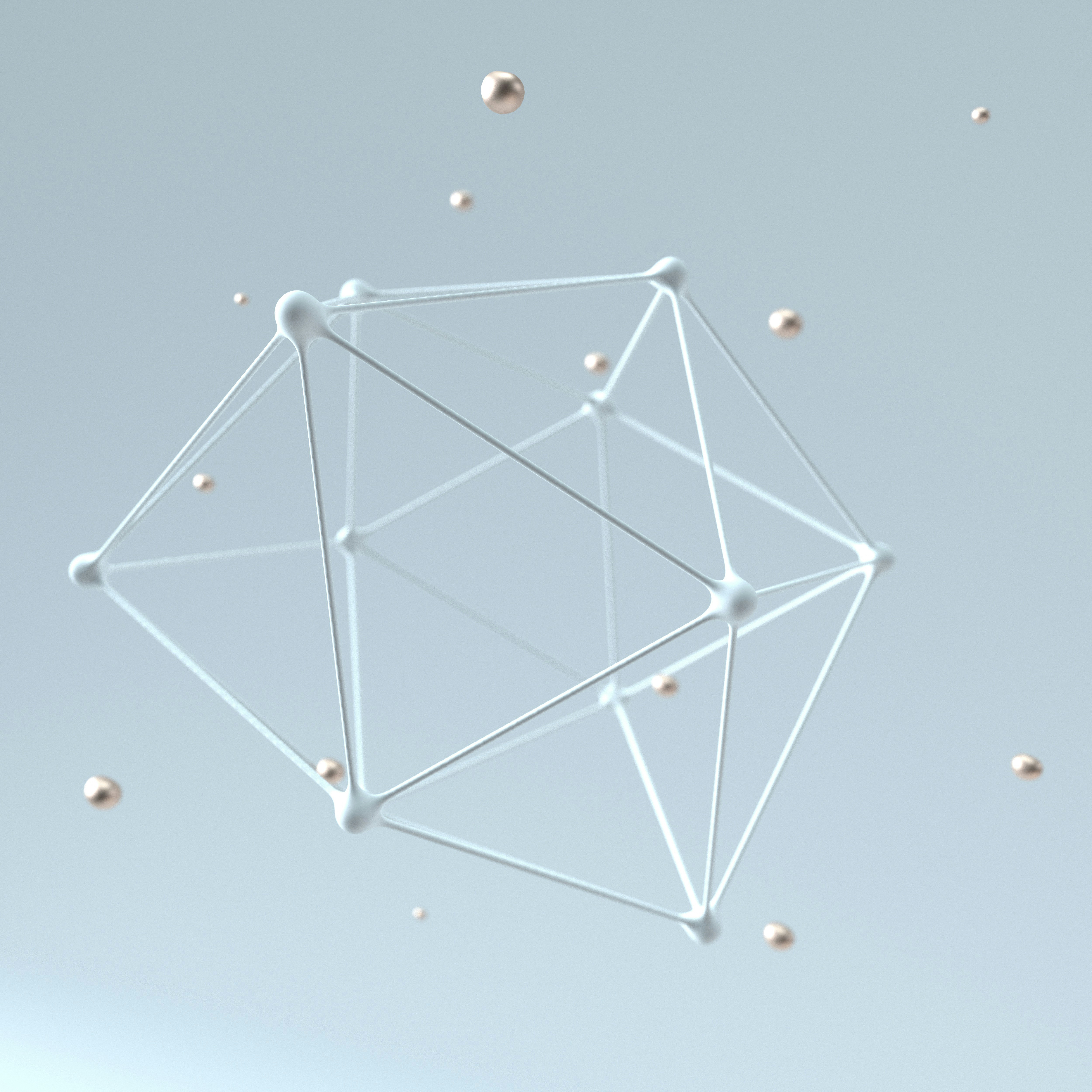
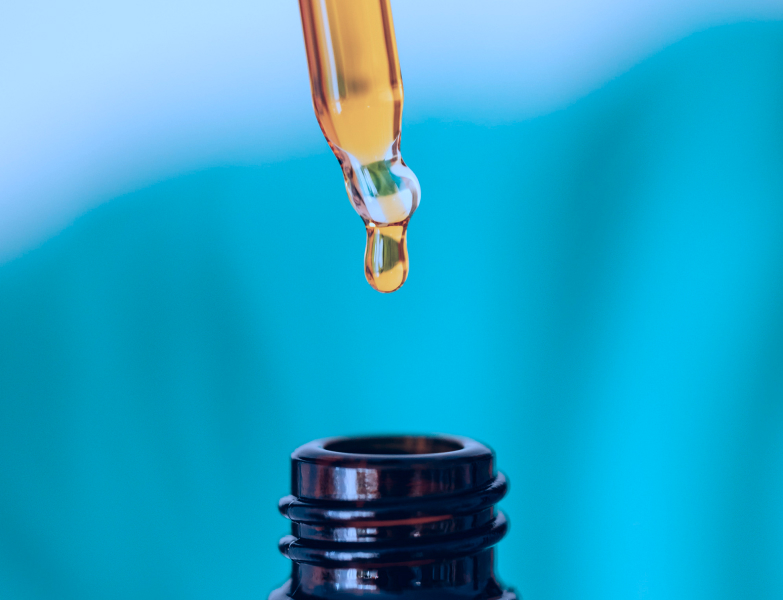
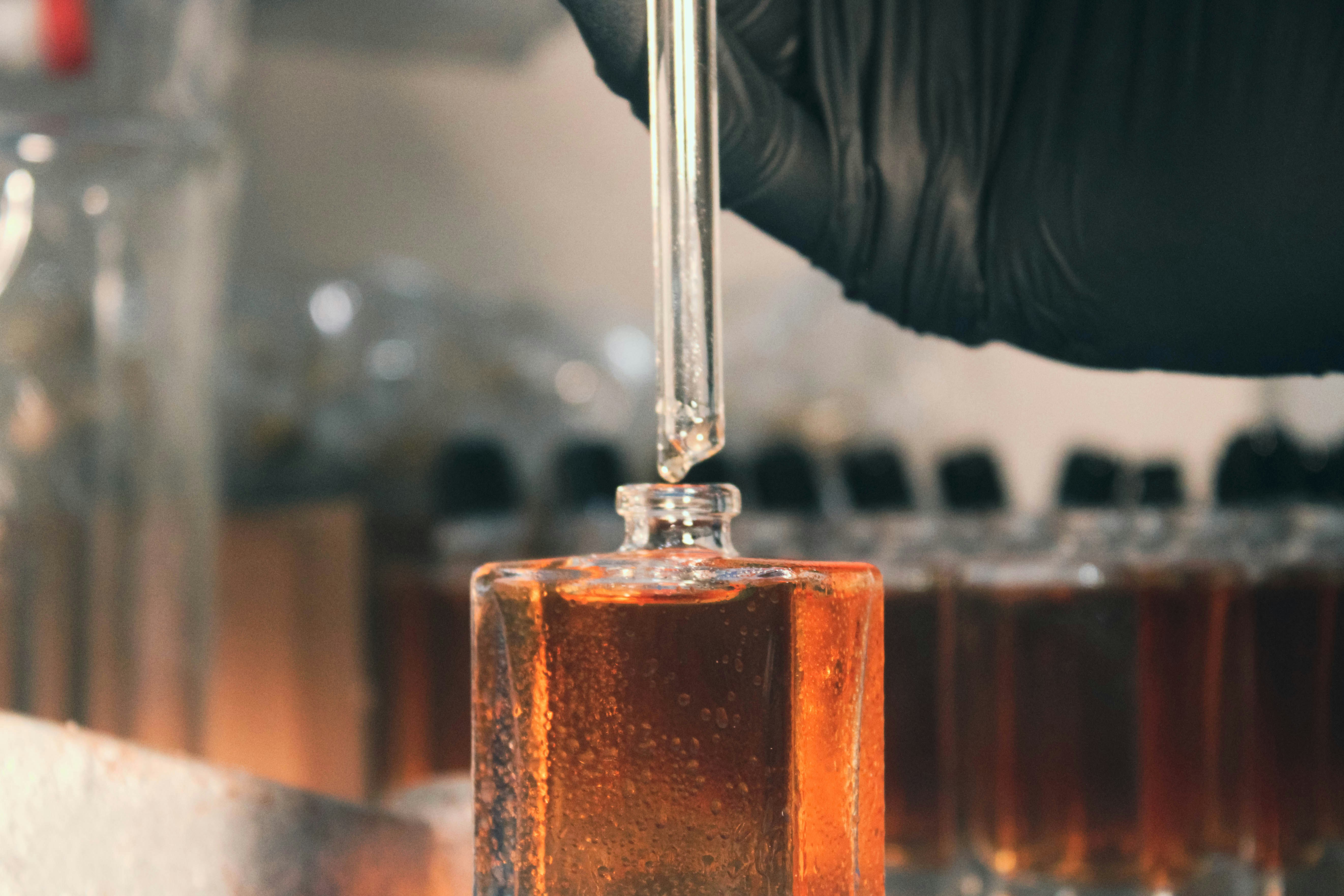
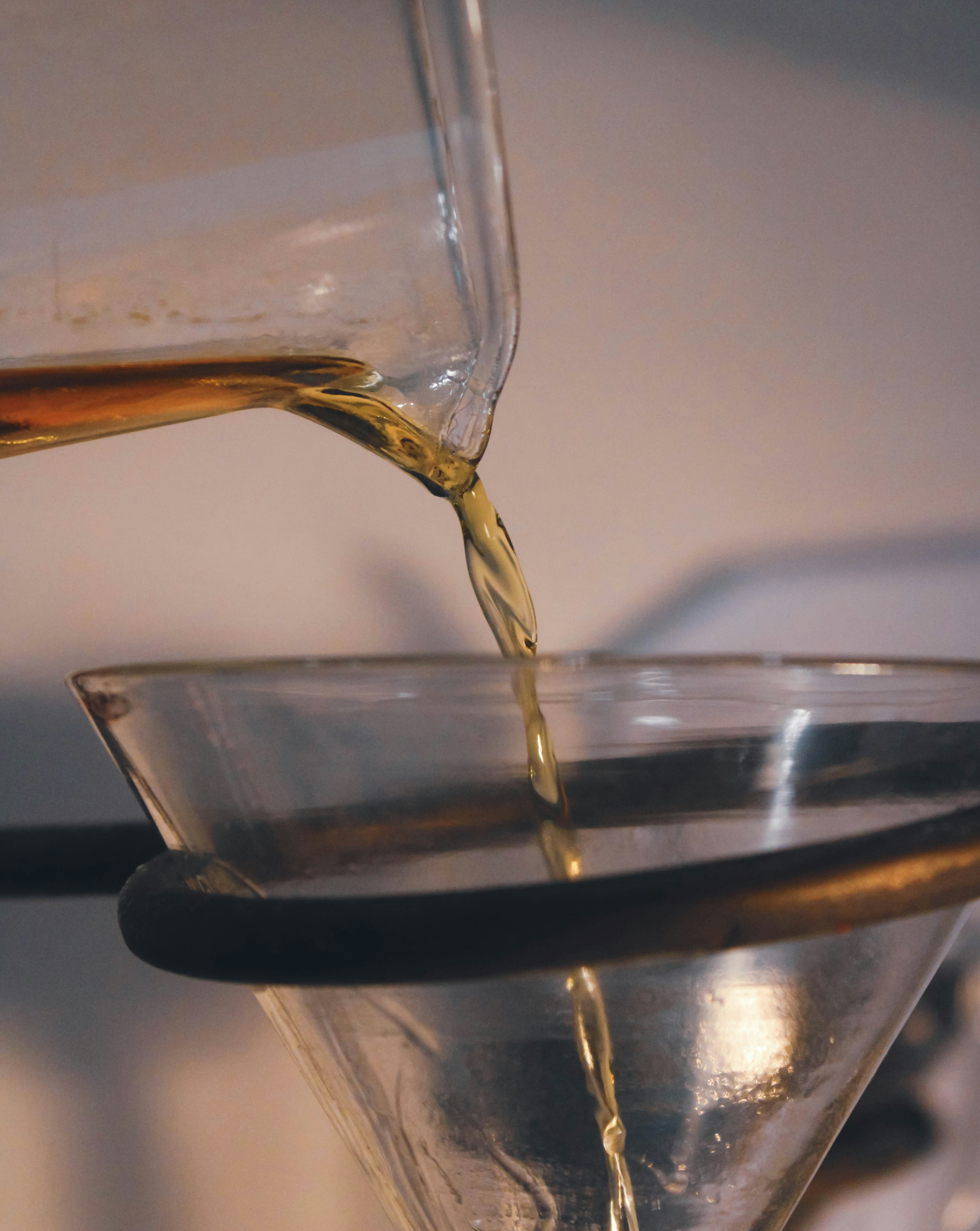
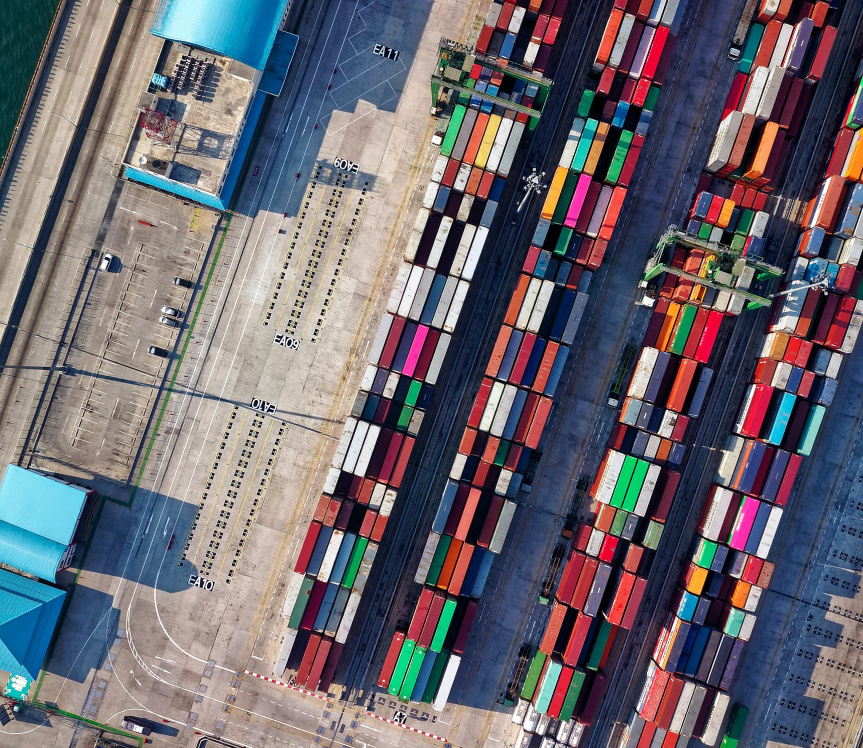
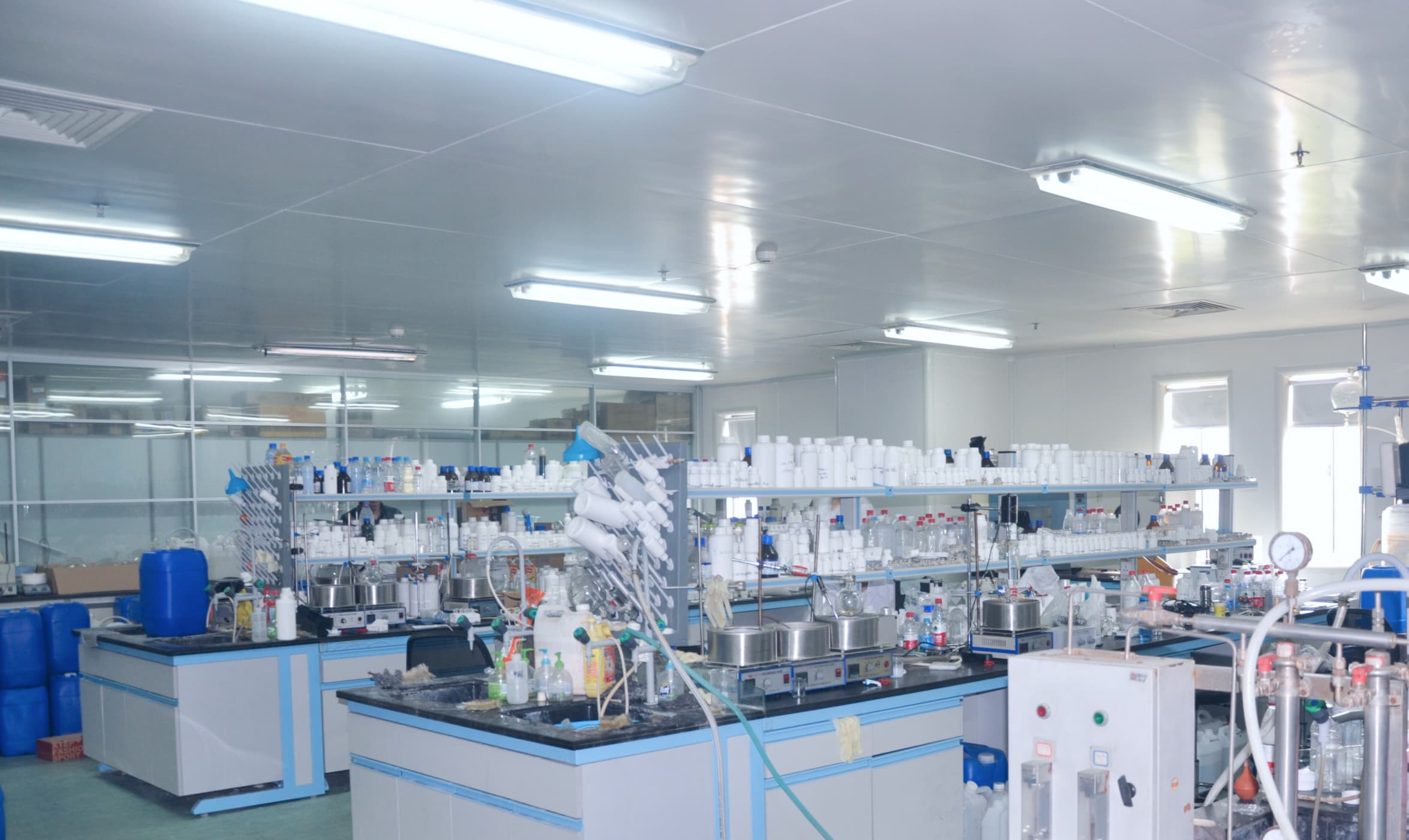
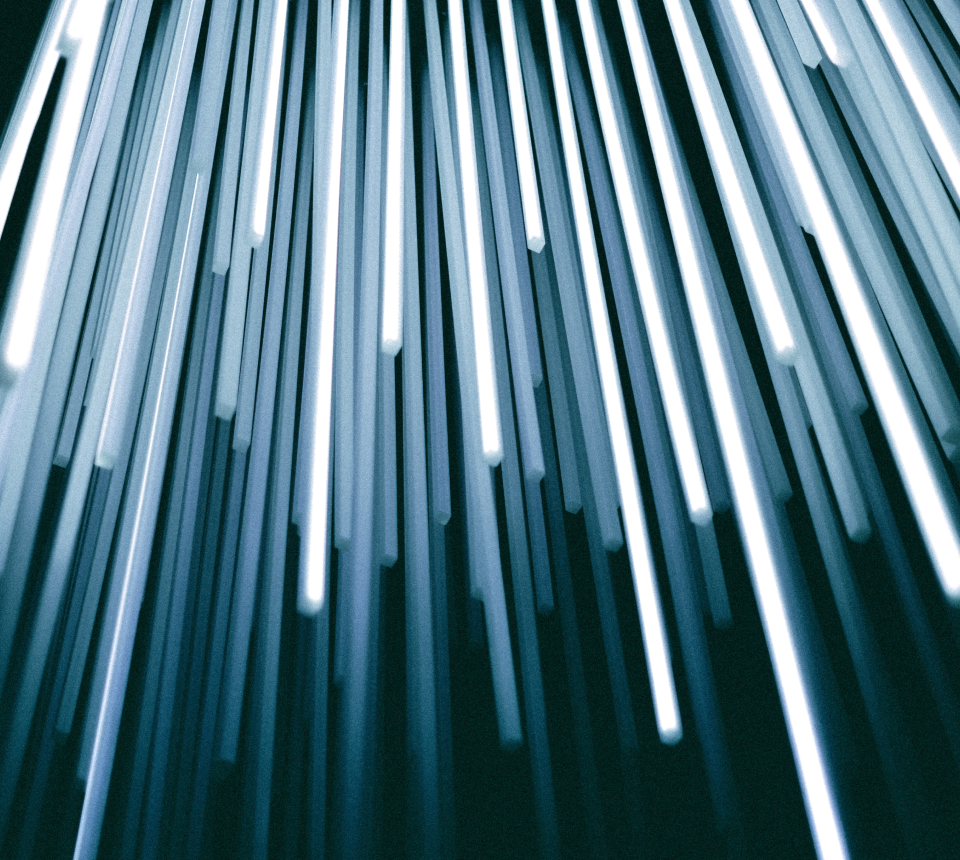
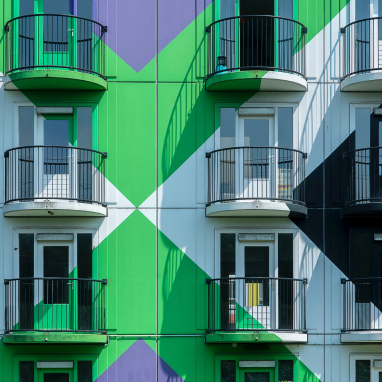
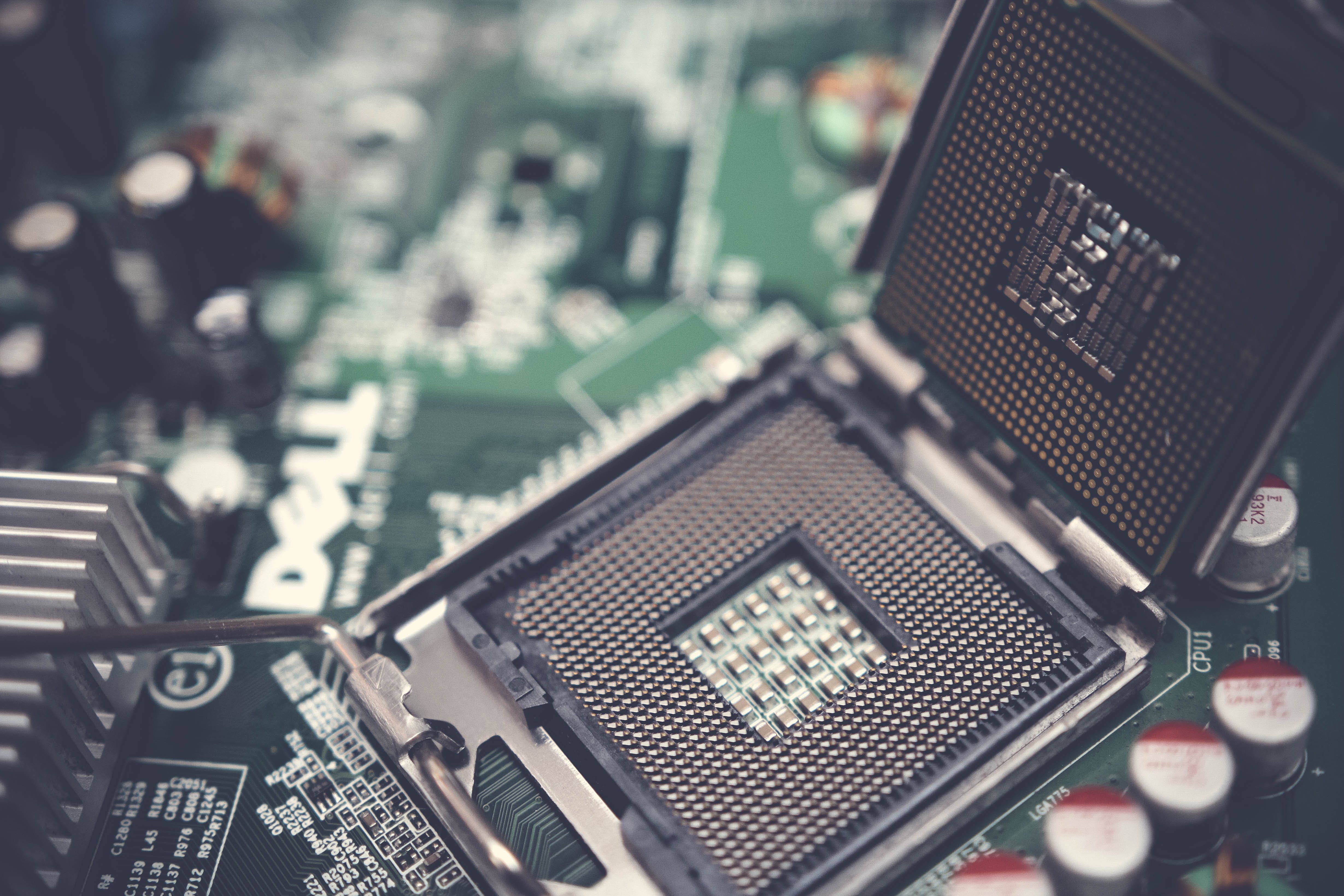
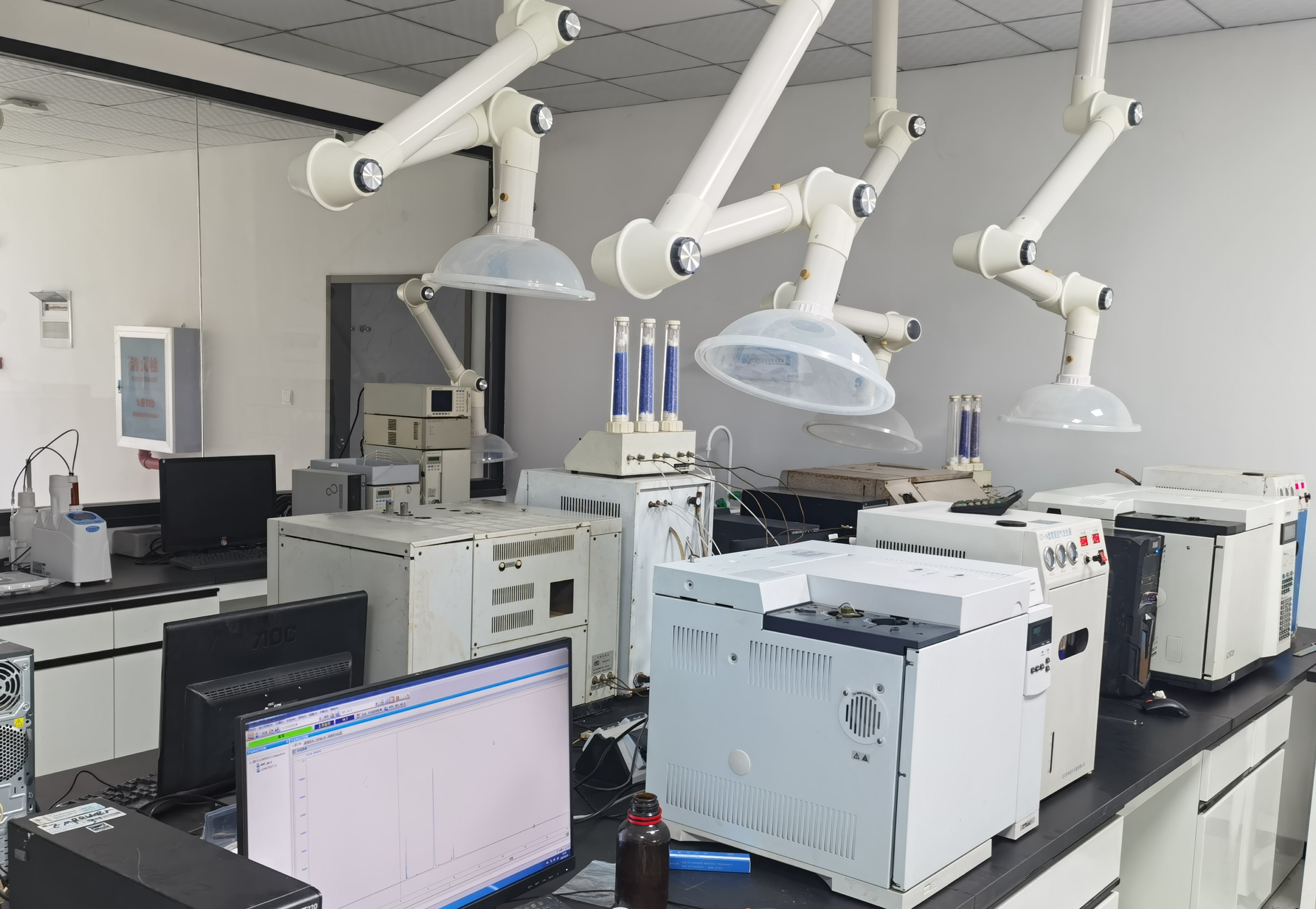
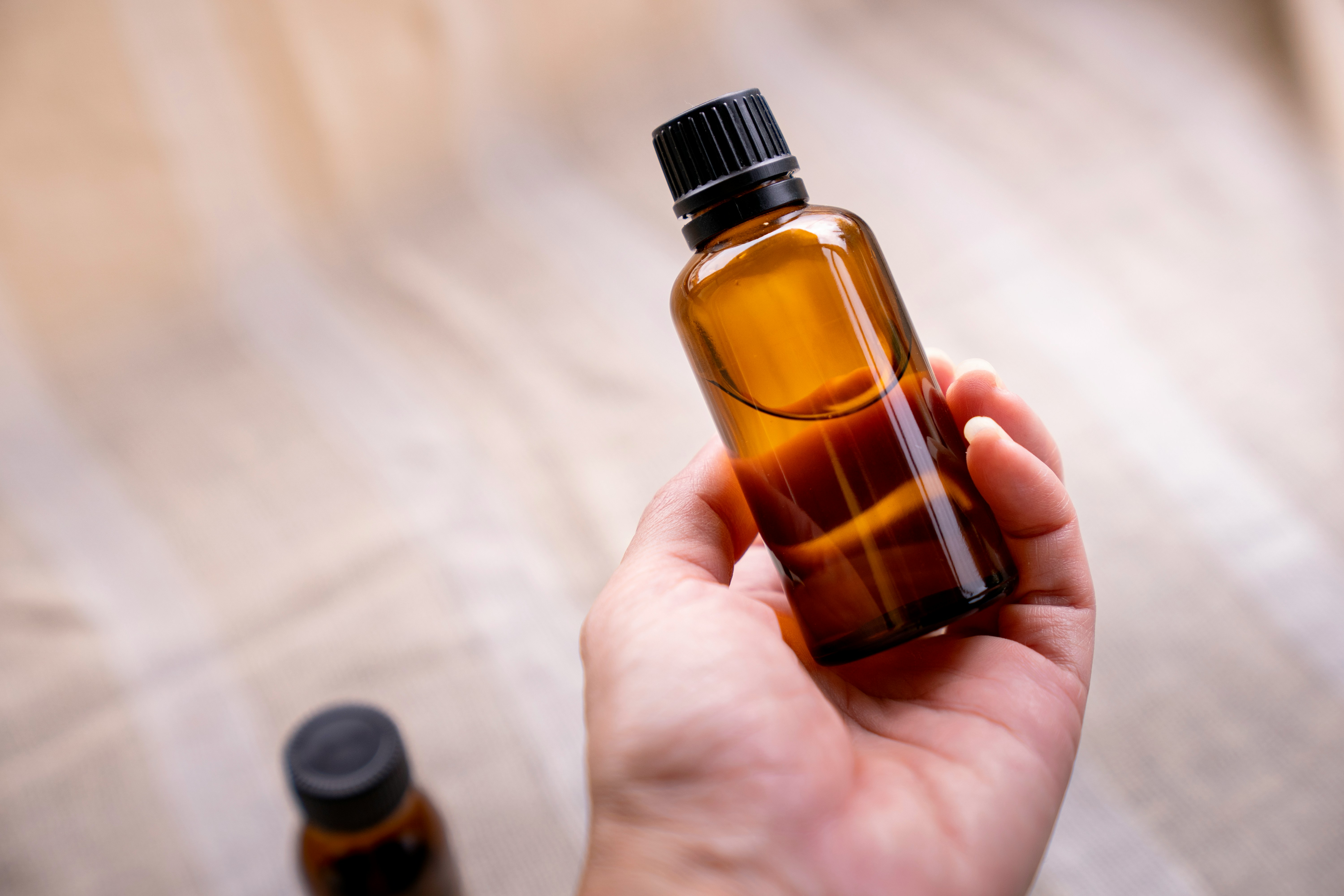
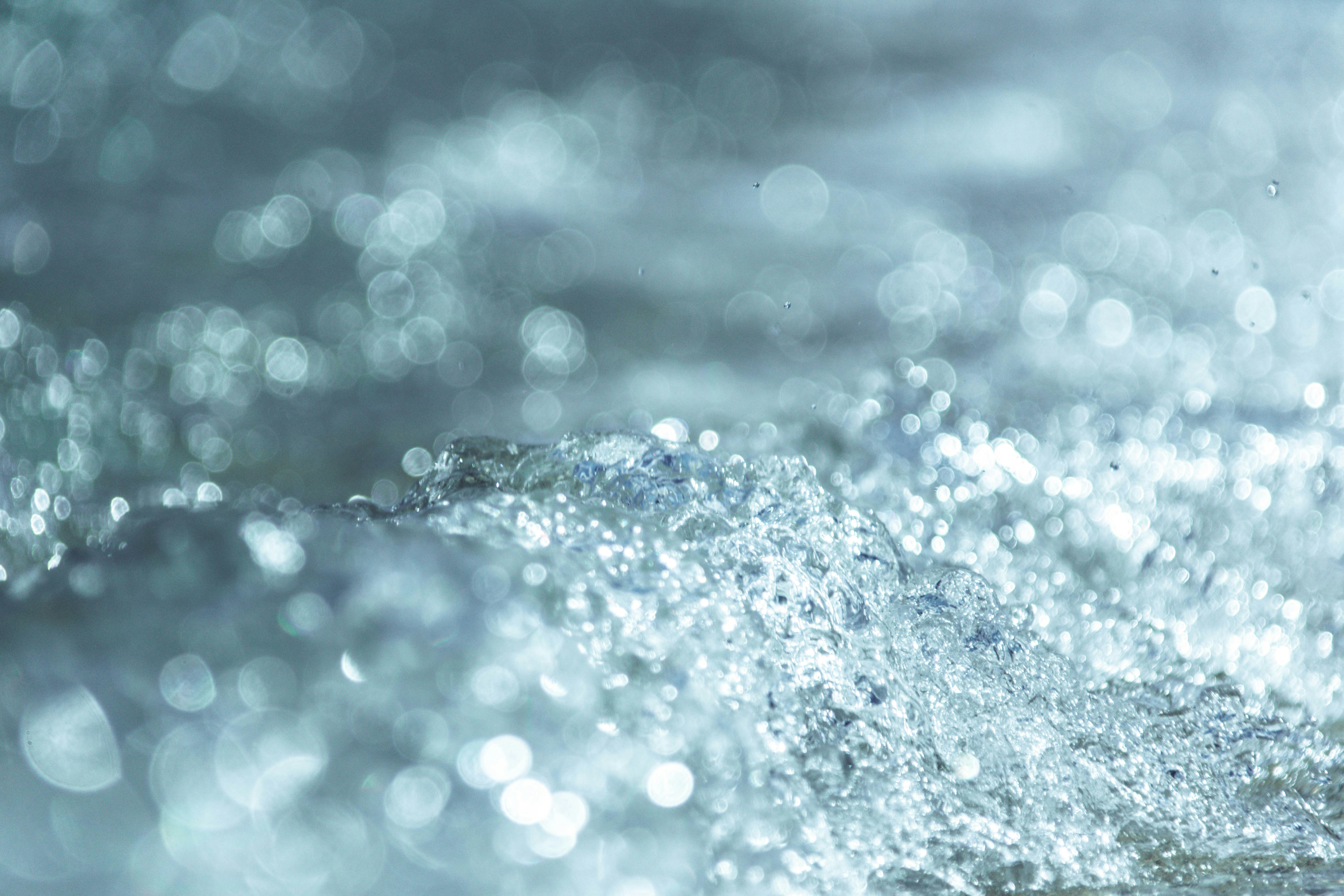
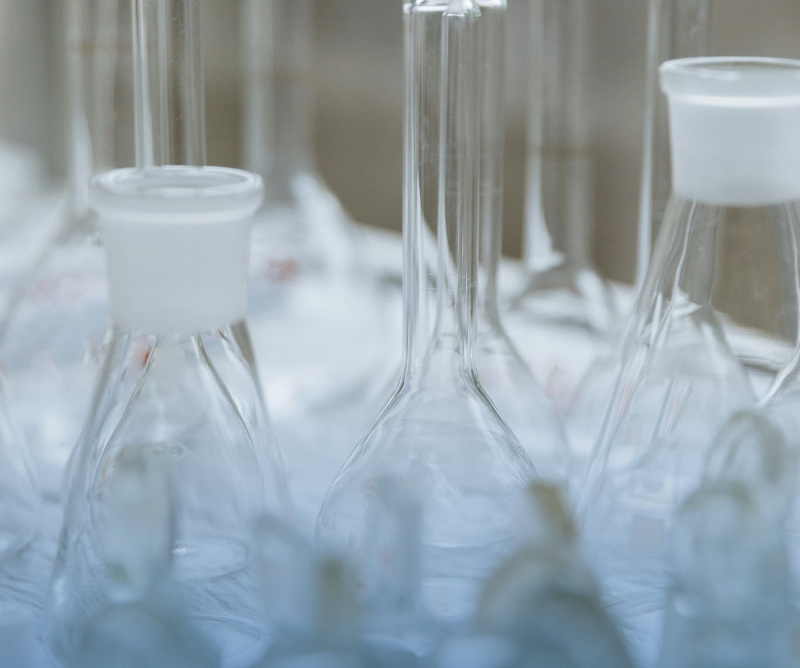
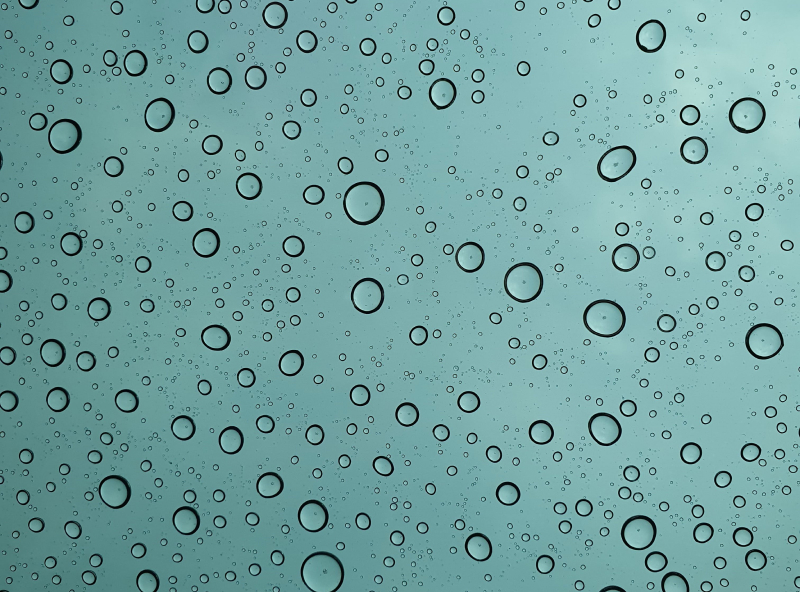
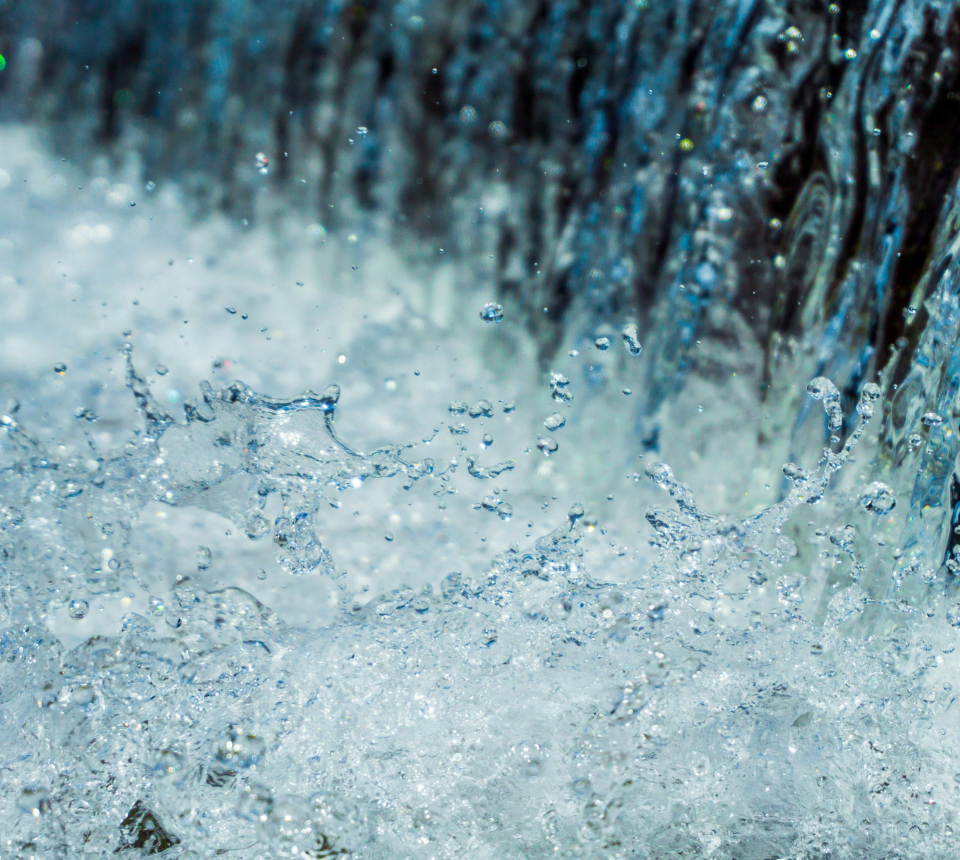
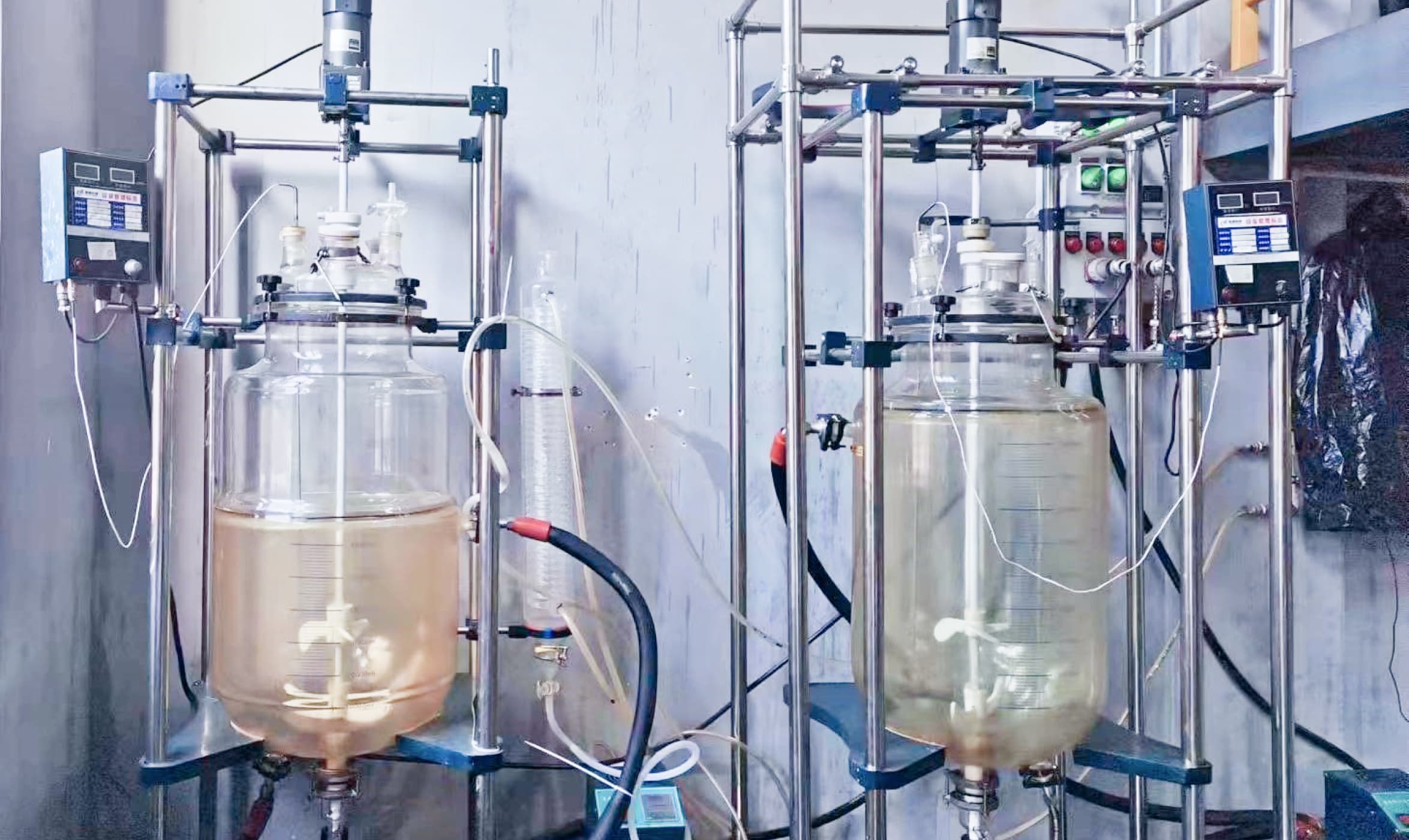
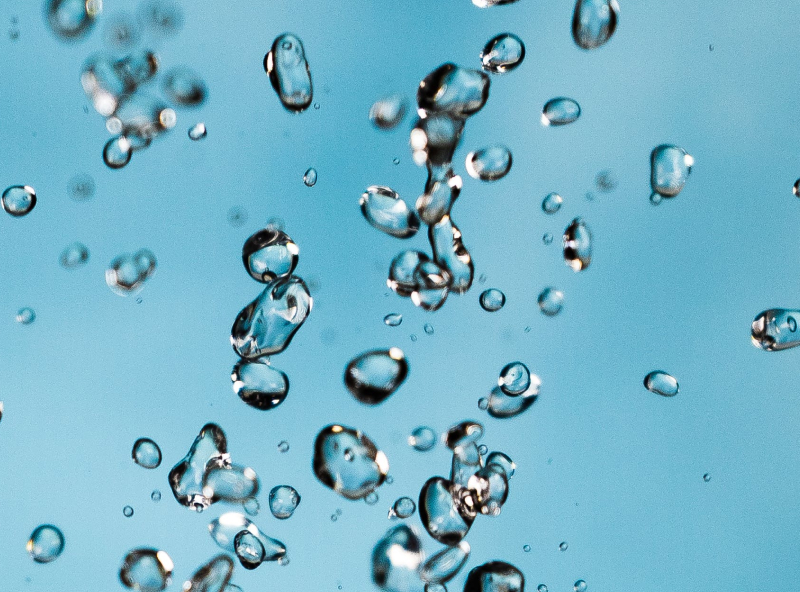
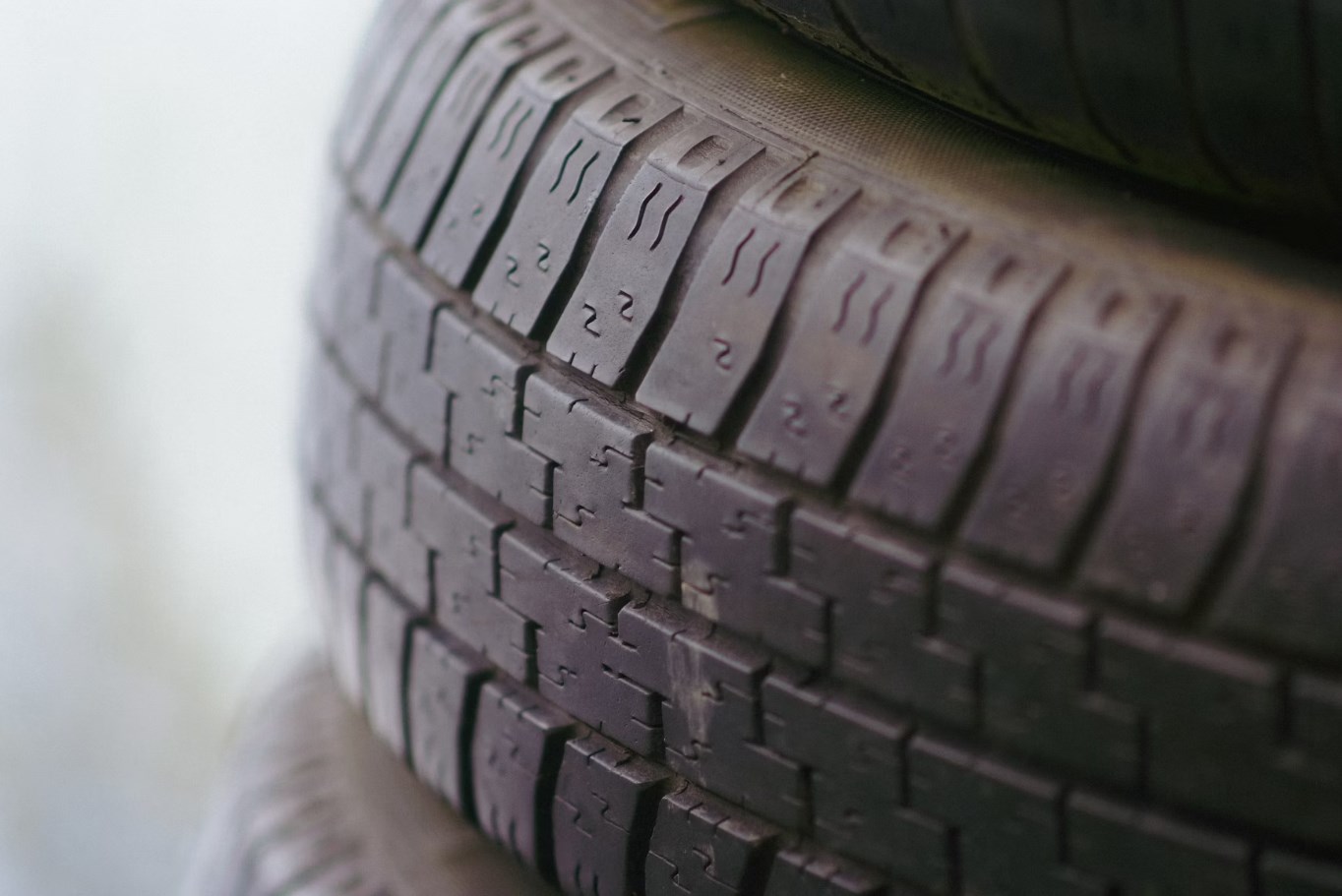
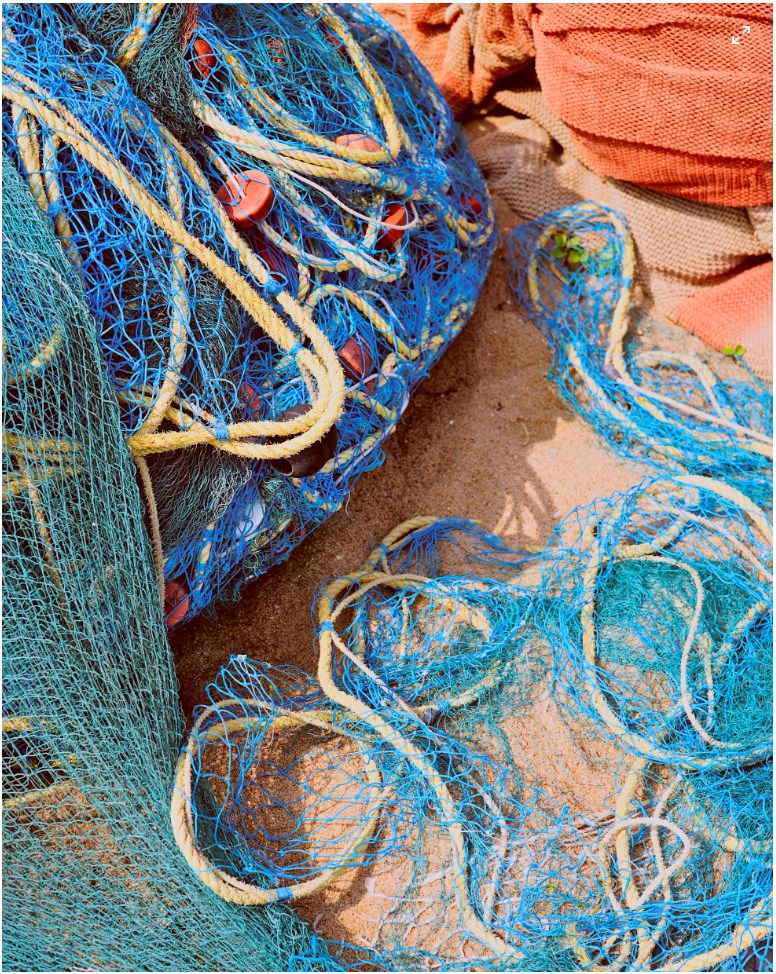
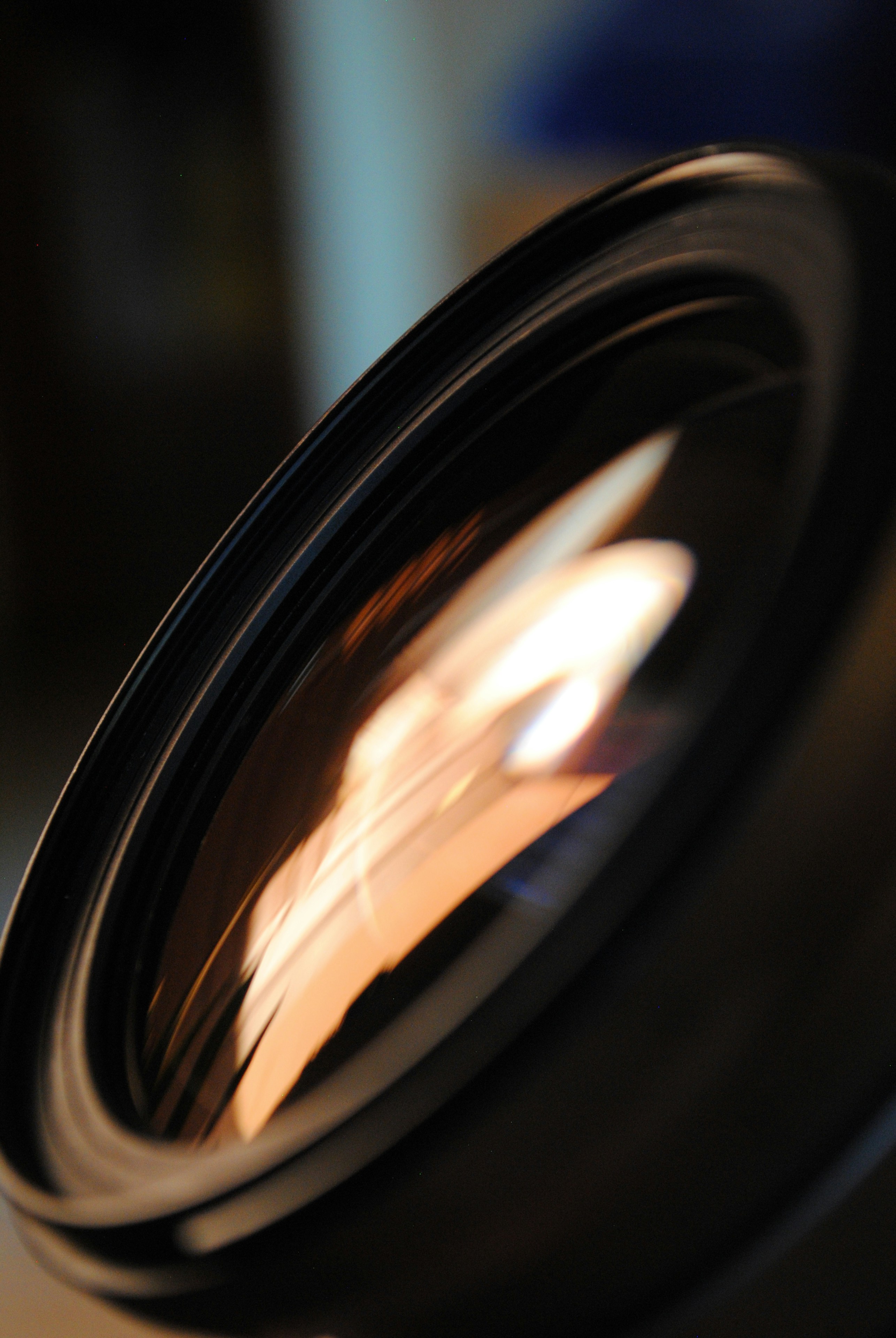
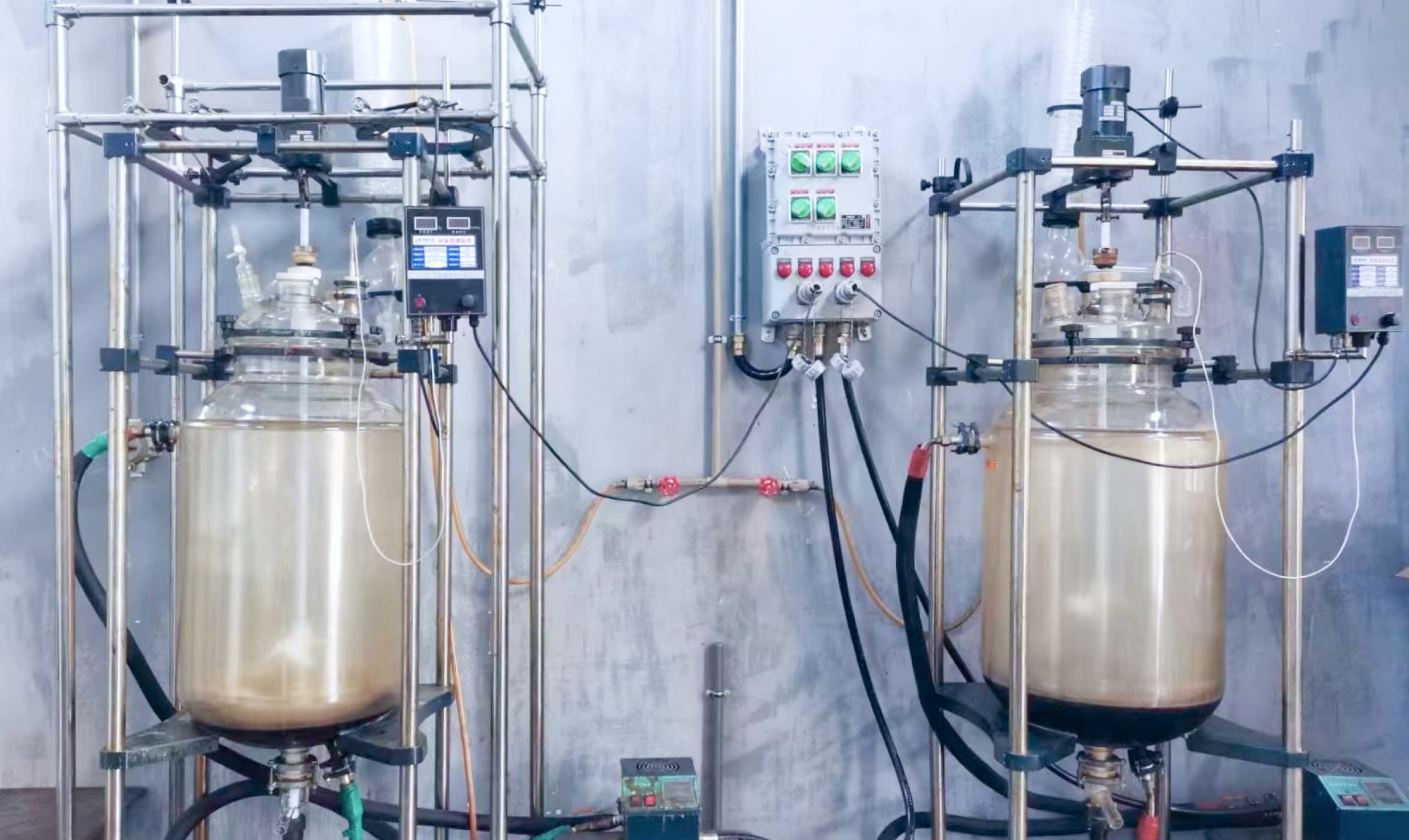
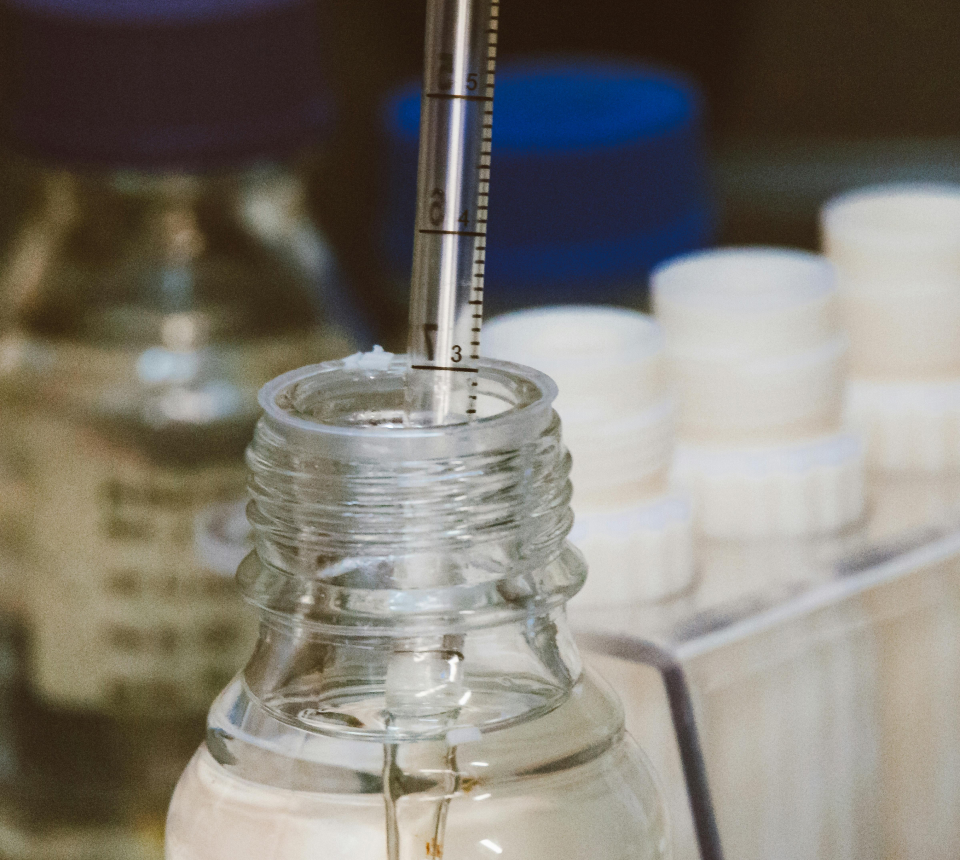
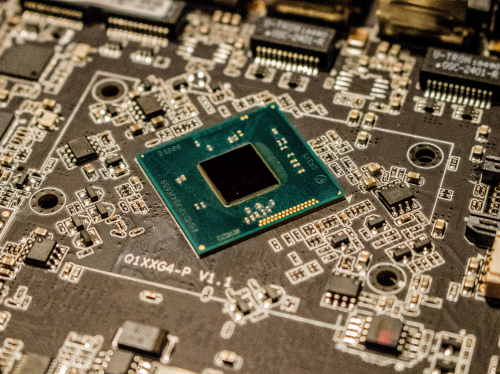
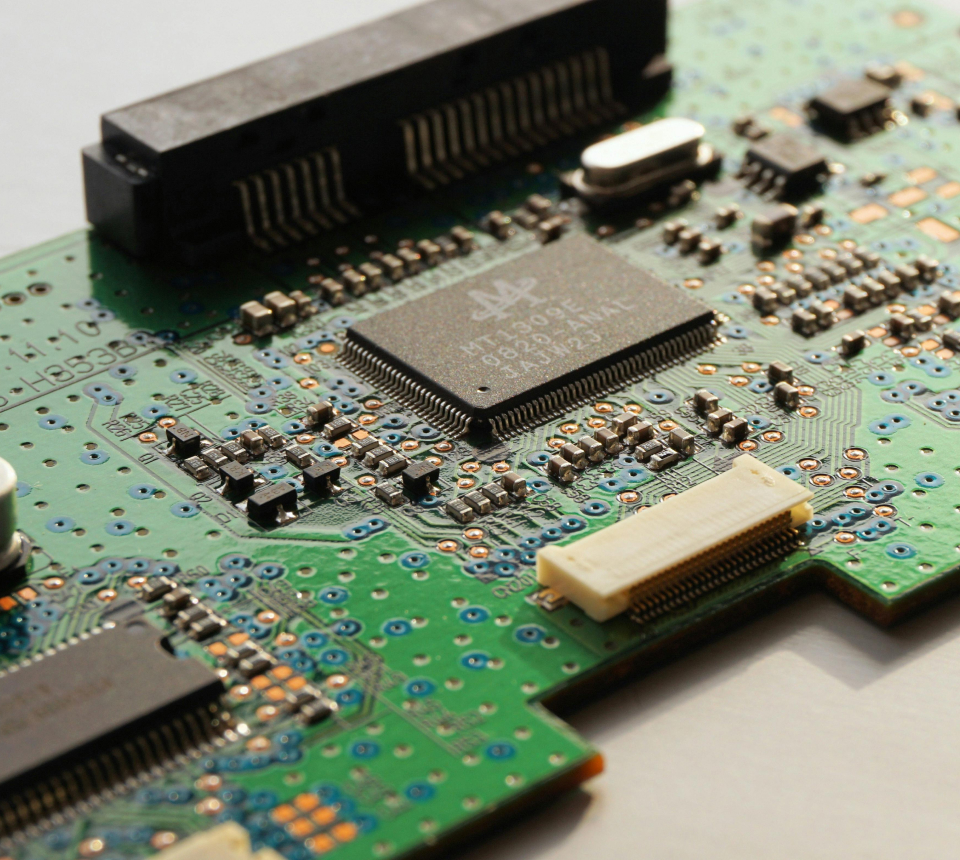
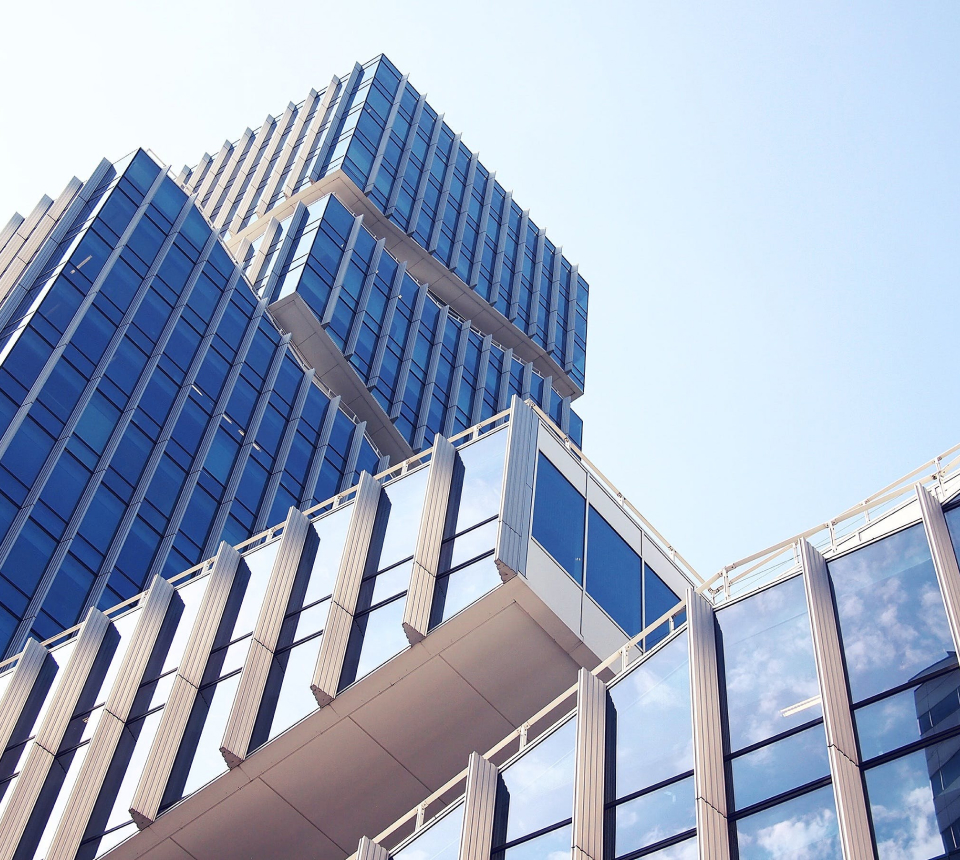
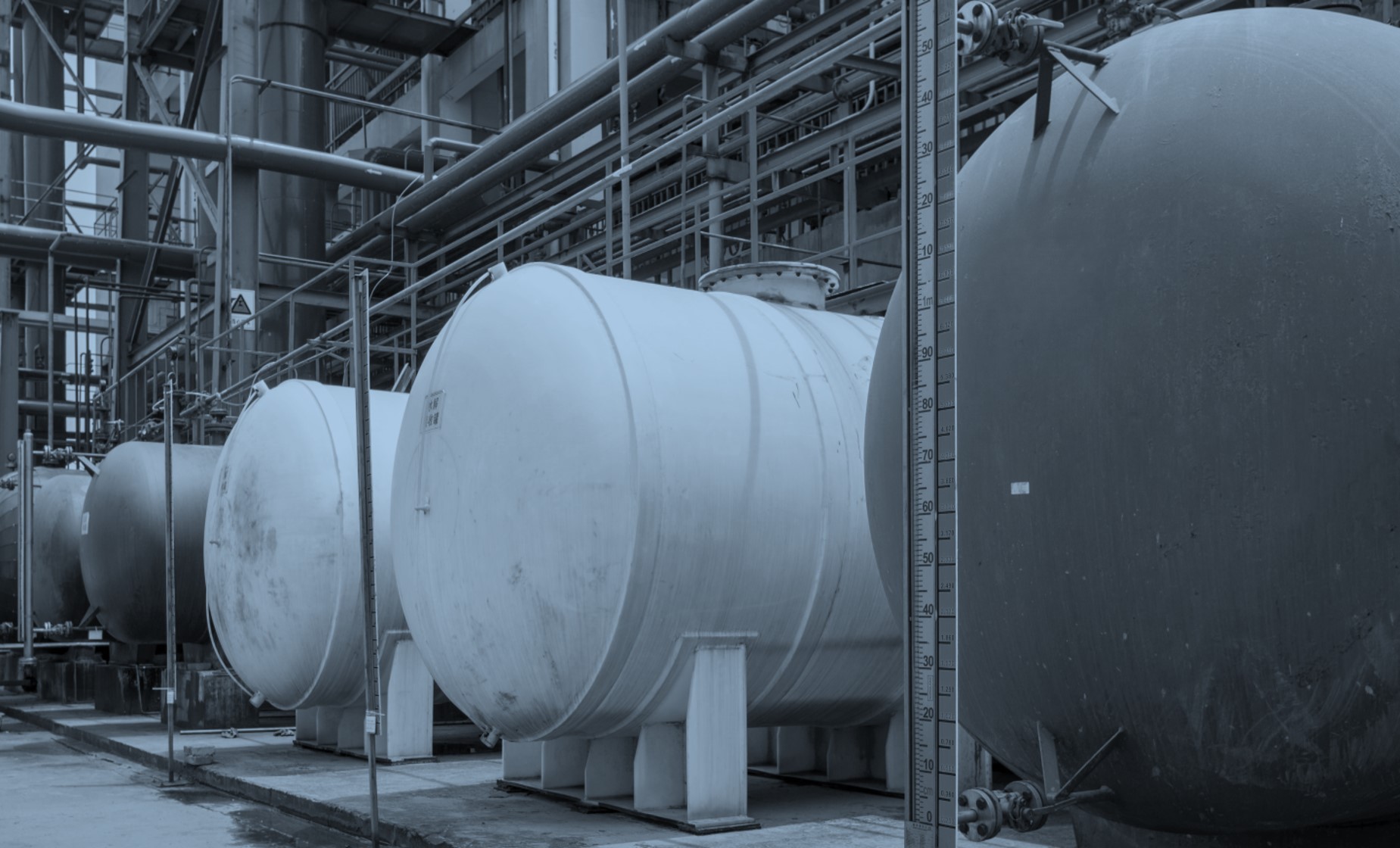
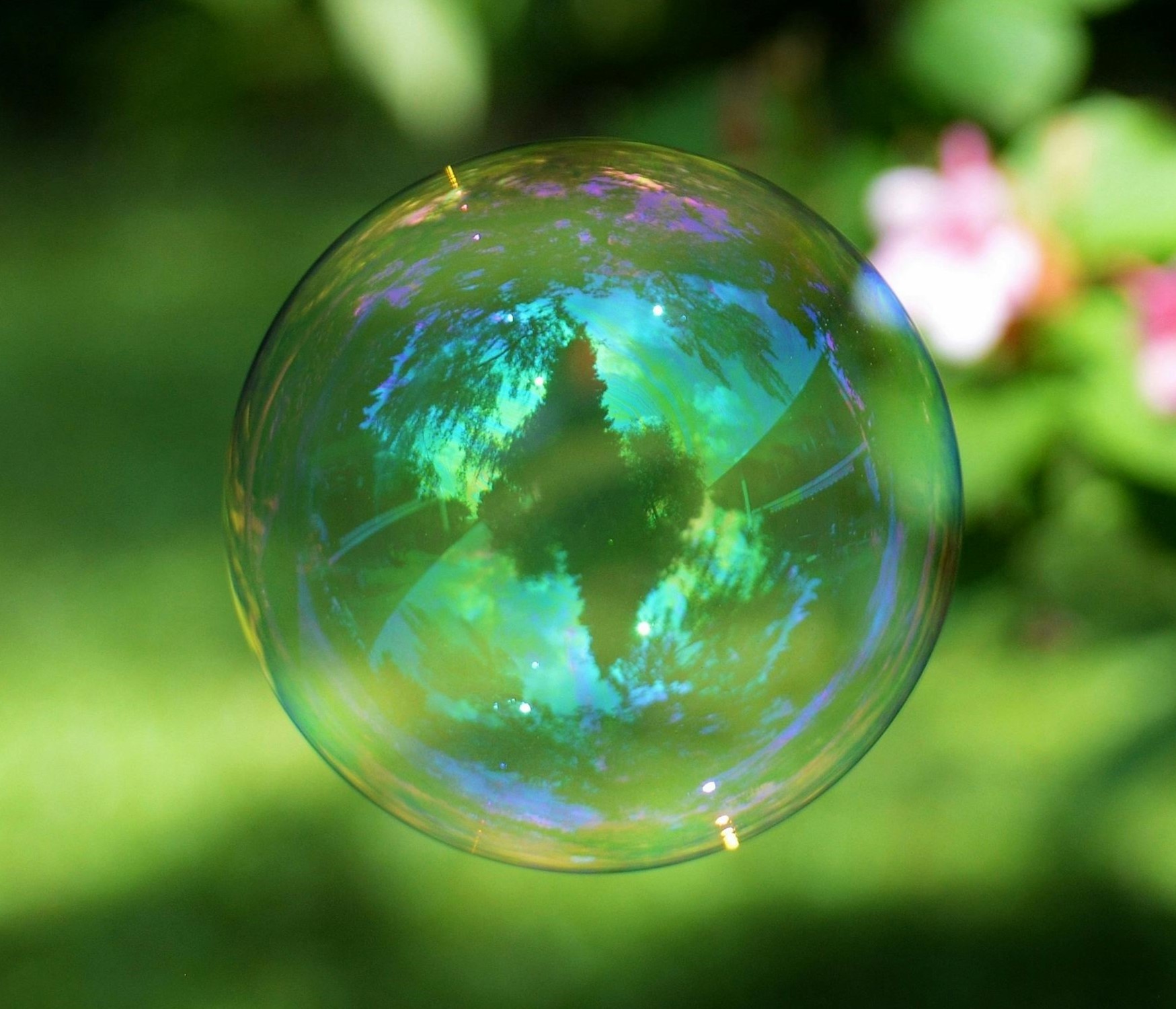
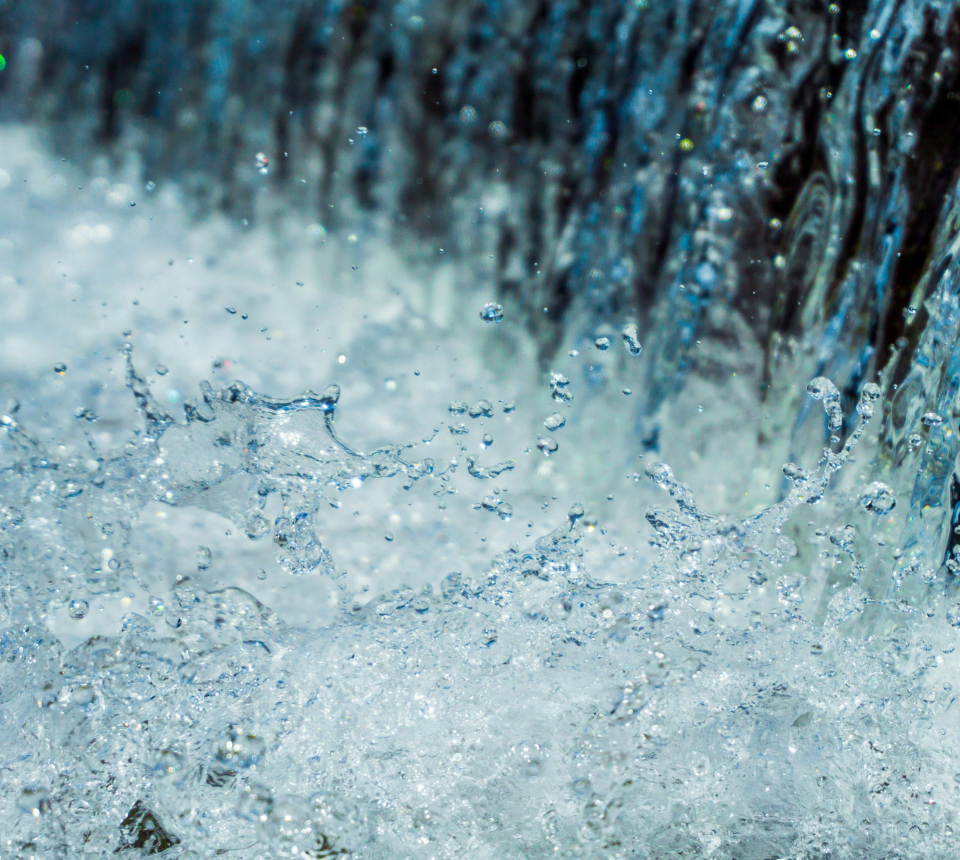
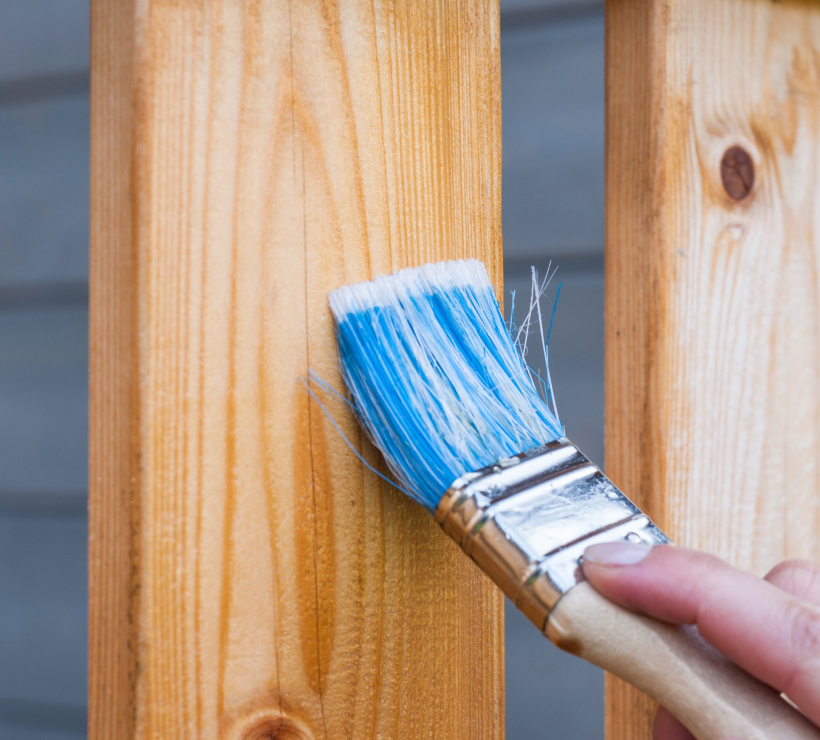

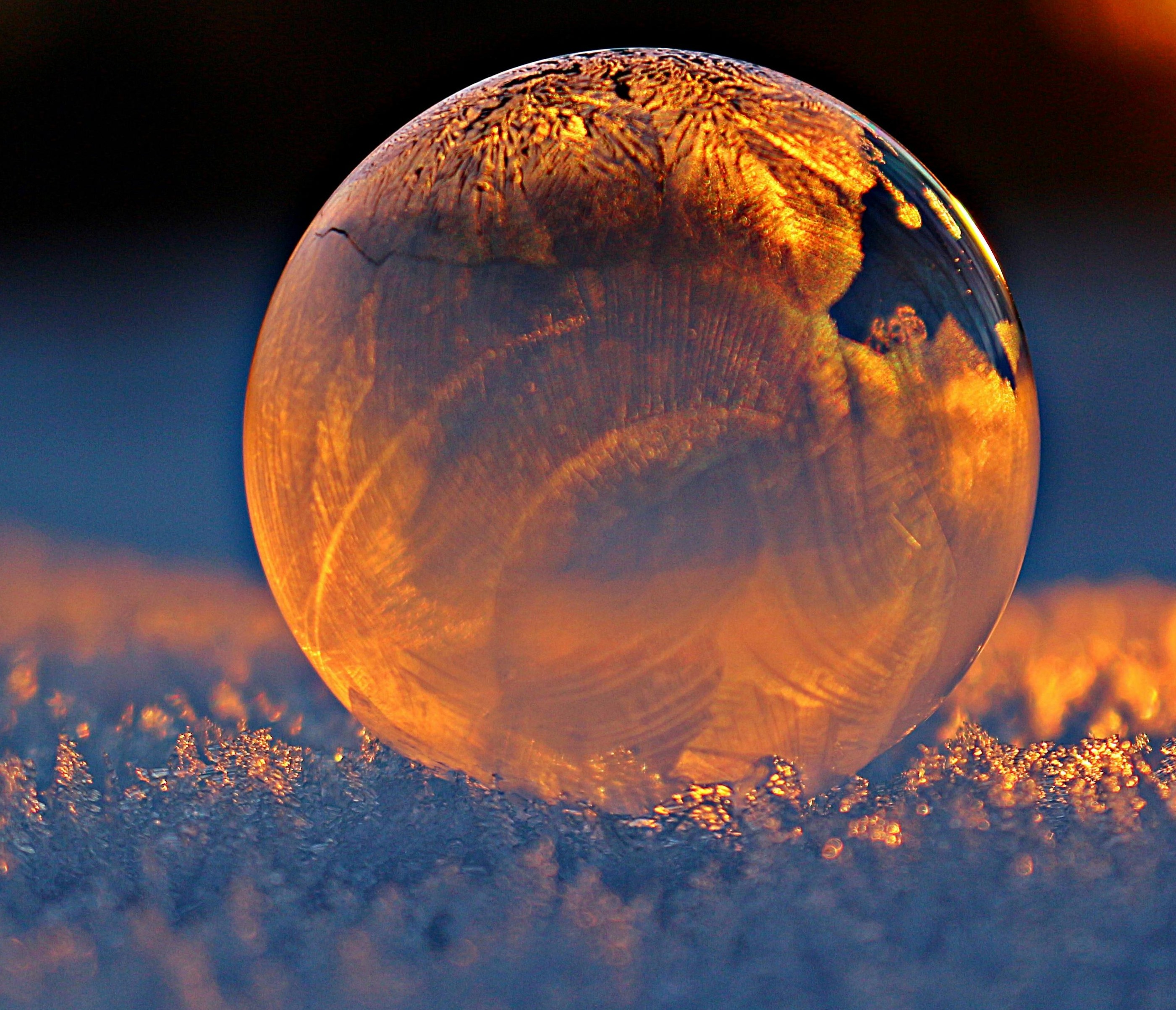
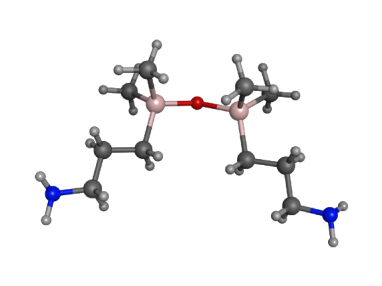
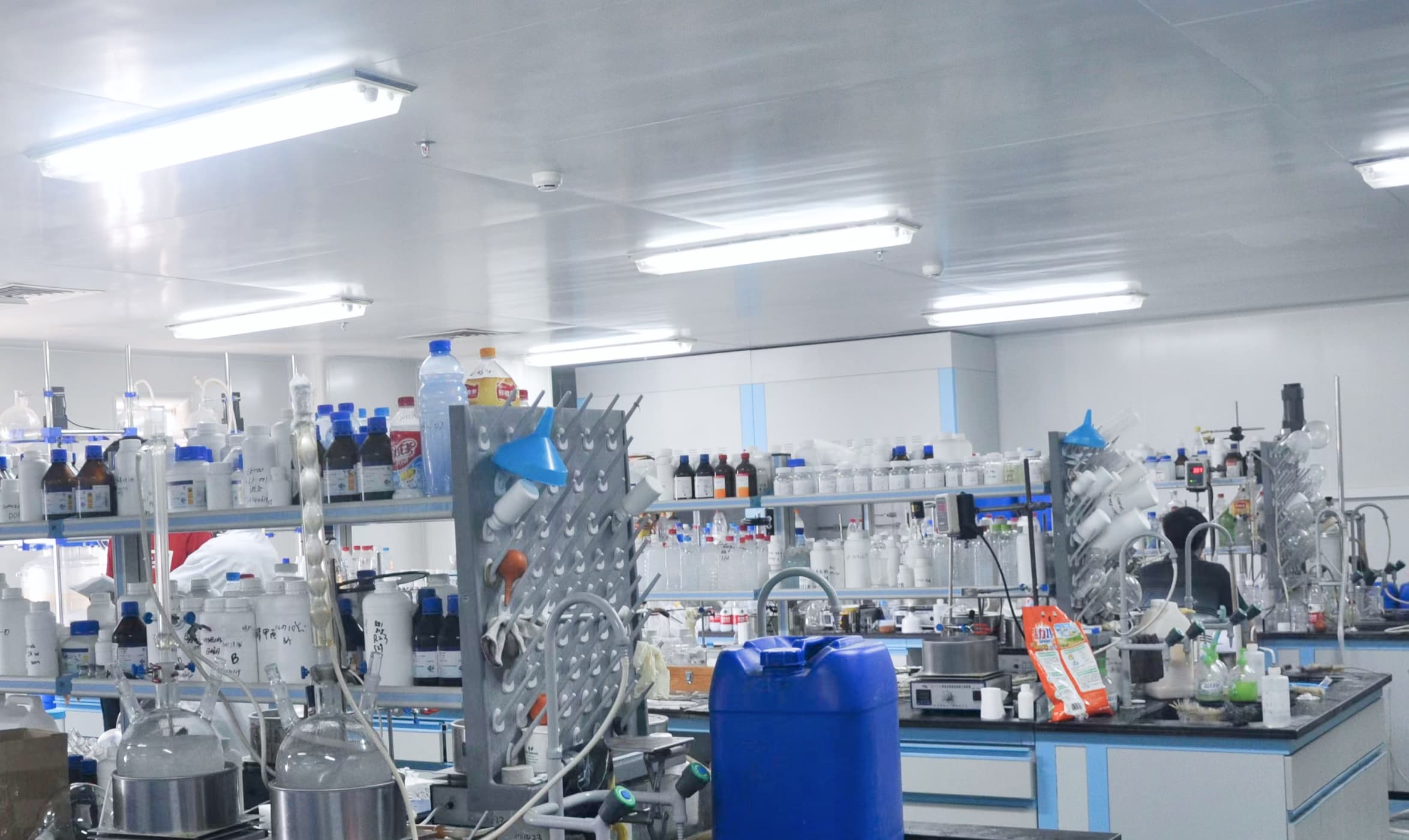
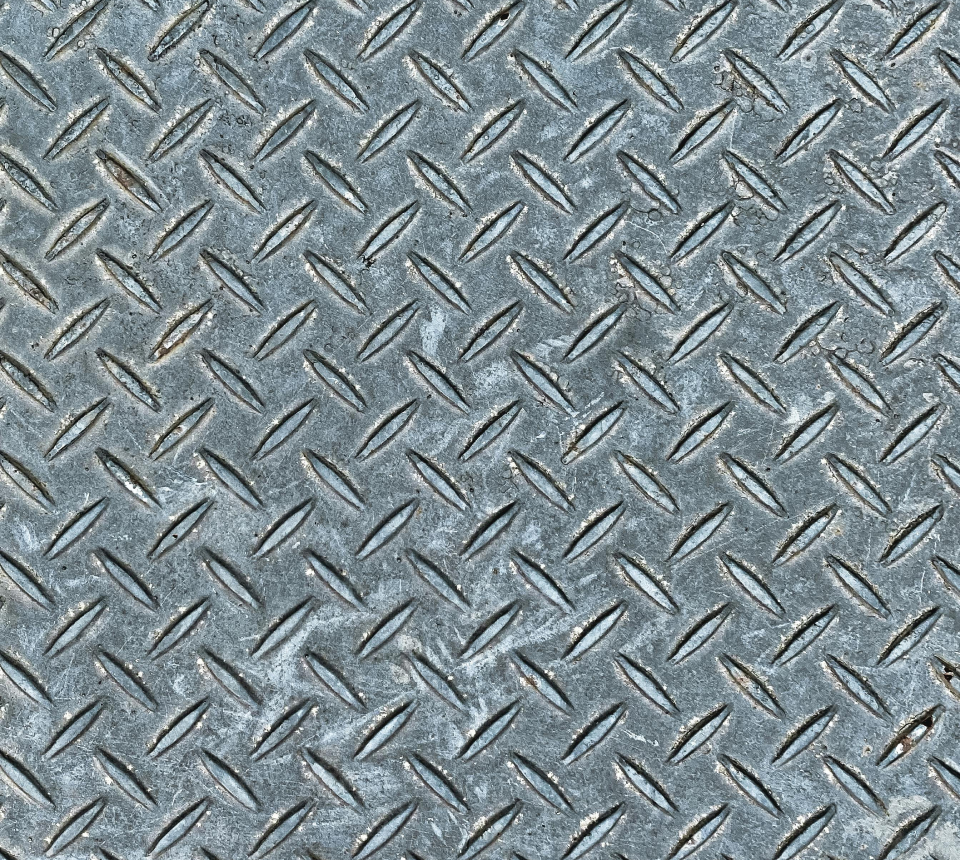
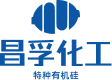
+86 27 8439 6550
+86 181 6277 0058
sales@cfsilanes.com
Optics Valley Bio-City
No. 666, Gaoxin Avenue
Hongshan District, Wuhan City
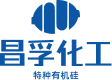
+86 27 8439 6550 | +86 181 6277 0058
sales@cfsilanes.com
Optics Valley Bio-City
No. 666, Gaoxin Avenue
Hongshan District, Wuhan City
Copyright © Hubei ChangFu Chemical Co., Ltd. All Rights