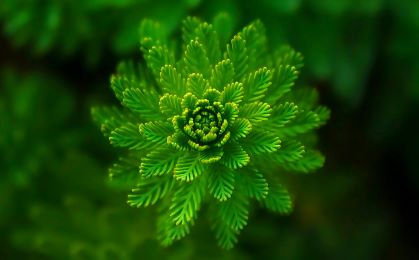
Contact Changfu Chemical Now!
+86 27 8439 6550 | +86 181 6277 0058
A Complete Guide to Silicone Release Coating
Silicone release coating is a crucial component in many industries, providing essential benefits in manufacturing, packaging, and processing. It plays a vital role in making products more efficient, durable, and easier to handle. This comprehensive guide will explore everything you need to know about silicone release coatings, from their composition and applications to the science behind their effectiveness. Additionally, we will look into the key differences between silicone release coatings and other release agents, providing you with valuable insights for your business or project.
What is Silicone Release Coating?
Silicone release coating refers to a thin layer of silicone-based material applied to a surface to create a non-stick effect, facilitating the easy removal of products from molds, carriers, or machinery. This type of coating is particularly effective in preventing adhesion, ensuring smooth surfaces that enhance the production process. Silicone release coatings are widely used in industries such as food packaging, automotive manufacturing, textiles, and medical device production.
The primary feature of silicone release coatings is their ability to prevent substances from sticking to the coated surface. By reducing friction and surface tension, these coatings provide a clean separation between the product and the mold or surface. The resulting smooth, non-stick finish is crucial for both ease of manufacturing and for maintaining product quality.
How Silicone Release Coating Works
At the heart of the silicone release coating's functionality lies the unique properties of silicone. Silicone, a polymer made from silicon, oxygen, and other elements, has exceptional chemical and thermal stability. When applied as a release coating, silicone creates a smooth, durable, and often hydrophobic (water-repelling) surface. This non-stick effect makes it ideal for use in a variety of manufacturing processes, where easy separation of materials is required.
Silicone release coatings work by forming a thin layer on the surface, which acts as a barrier between the product being processed and the surface it comes into contact with. Whether it’s a mold, conveyor belt, or packaging material, the silicone layer ensures that the product does not stick, thus reducing wear on machinery and improving the overall efficiency of the manufacturing process.
Types of Silicone Release Coating
There are several types of silicone release coatings, each designed to meet specific needs. Understanding the differences between these types is essential to selecting the right silicone release coating for your application.
1. Water-Based Silicone Release Coating
Water-based silicone release coatings are one of the most common and environmentally friendly options available. These coatings are easy to apply and can be used on a variety of surfaces, including paper, plastics, and textiles. They are particularly useful in industries that prioritize sustainability, as they have low volatile organic compound (VOC) emissions. Water-based silicone release coatings also offer excellent flexibility, which makes them suitable for a wide range of applications, such as food packaging and pharmaceutical industries.
2. Solvent-Based Silicone Release Coating
Solvent-based silicone release coatings are known for their fast drying times and superior performance in high-temperature environments. These coatings are typically used in situations where a thicker and more durable layer of silicone is needed. Solvent-based coatings can be applied to both rigid and flexible materials, making them versatile for use in industries like automotive manufacturing and electronics.
3. Silicone Release Coating for High-Temperature Applications
Some silicone release coatings are specially formulated to withstand extreme heat. These coatings are ideal for industries that involve high-temperature processes, such as the production of non-stick cookware, automotive parts, and even some electronics. Silicone release coatings for high-temperature applications are designed to maintain their non-stick properties even when exposed to temperatures above 300°C (572°F).
4. Silicone Release Coating for Food Packaging
Silicone release coatings used in food packaging are food-grade and comply with stringent regulatory standards to ensure they are safe for contact with consumables. These coatings are commonly used to line paper and cardboard packaging, particularly for products like baked goods, confectioneries, and frozen foods. The non-stick properties prevent food from adhering to the packaging, ensuring that products are easy to remove, while maintaining hygiene and product integrity.
Benefits of Using Silicone Release Coating
The application of silicone release coatings offers a number of key benefits that can significantly enhance manufacturing efficiency and product quality. Below are some of the most important advantages of silicone release coatings:
1. Reduced Adhesion
The primary benefit of silicone release coatings is their ability to reduce adhesion between surfaces. Whether you're working with molds, conveyor belts, or packaging materials, silicone release coatings ensure that products do not stick, reducing the need for manual intervention and improving overall production efficiency.
2. Increased Productivity
By preventing materials from sticking, silicone release coatings help speed up manufacturing processes. This leads to fewer disruptions, less downtime for equipment maintenance, and ultimately, higher productivity levels. The easy separation of products from molds and machinery means that the production process can proceed smoothly without any hindrances.
3. Improved Surface Quality
Silicone release coatings create a smooth and uniform surface that enhances the quality of the final product. This is particularly beneficial in industries where appearance is important, such as packaging and textiles. The non-stick properties of silicone also ensure that products are free from imperfections caused by sticking or tearing during manufacturing.
4. Cost Efficiency
Silicone release coatings can help reduce costs in the long term. By extending the lifespan of molds, machinery, and equipment, businesses can reduce maintenance costs and minimize the need for frequent replacements. Additionally, the improved productivity resulting from faster and smoother production processes can lead to increased profits.
5. Eco-Friendly Options
As mentioned earlier, some silicone release coatings are water-based and have low environmental impact. For businesses that prioritize sustainability, using eco-friendly silicone release coatings can be an important step in reducing the overall environmental footprint of their manufacturing processes.
Applications of Silicone Release Coating
Silicone use in manufacturing processes has become increasingly popular due to its ability to provide durable, non-stick surfaces that enhance efficiency and product quality across various industries. Silicone release coatings are used in a wide range of industries, thanks to their versatility and superior performance. Below are some of the key applications of silicone release coatings:
1. Food Packaging and Processing
In the food packaging industry, silicone release coatings are commonly used on paper and cardboard packaging to prevent food products from sticking to the surface. This is particularly useful for items such as baked goods, confectionery, and frozen foods. Silicone release coatings ensure that the products remain intact and easy to remove from their packaging, while also maintaining hygiene standards.
2. Automotive Manufacturing
In automotive manufacturing, silicone release coatings are used in a variety of processes, including molding, die-casting, and composite manufacturing. These coatings help prevent materials from adhering to molds, making the production process more efficient and reducing the risk of defects in the final product.
3. Medical Devices and Pharmaceuticals
Silicone release coatings are often used in the production of medical devices and pharmaceutical packaging. For example, they are applied to products such as adhesive bandages, medical tapes, and pharmaceutical blister packs. The non-stick properties ensure that the products can be easily removed from molds or packaging, without compromising their integrity.
4. Textiles and Non-Woven Fabrics
Silicone release coatings are also used in the textile industry to prevent fibers from sticking together during the manufacturing process. These coatings are applied to non-woven fabrics, where they facilitate the easy removal of materials from molds and rollers. They also help improve the appearance and texture of the final product.
5. Electronics and Electrical Manufacturing
In electronics, silicone release coatings are used in the production of components such as semiconductor wafers and printed circuit boards (PCBs). These coatings prevent adhesion during processes like etching and bonding, ensuring high-quality manufacturing and reducing the risk of defects.
Silicone Release Coating vs. Other Release Agents
While silicone release coatings are highly effective, they are not the only option available for preventing adhesion in manufacturing. There are several other types of release agents, each with its own strengths and weaknesses.
1. Wax-Based Release Agents
Wax-based release agents are commonly used in the molding industry. While they can provide a non-stick surface, they are not as durable as silicone release coatings and may require more frequent reapplication. Additionally, wax-based agents can leave residue on the surface, which may affect the final product's appearance.
2. PTFE (Teflon) Release Coatings
PTFE release coatings, made from polytetrafluoroethylene (Teflon), are known for their exceptional non-stick properties and ability to withstand high temperatures. However, they tend to be more expensive than silicone release coatings and may not offer the same level of versatility in different applications.
3. Fluoropolymer Release Agents
Fluoropolymer release agents are similar to silicone coatings in that they provide excellent non-stick properties. However, they are typically more expensive and may not be as effective in certain applications. They are often used in specialized industries such as aerospace and high-performance manufacturing.
Conclusion
Silicone release coatings are essential tools in modern manufacturing, offering a range of benefits that improve efficiency, product quality, and cost-effectiveness. From preventing adhesion to improving surface quality, silicone release coatings play a vital role in industries such as food packaging, automotive manufacturing, textiles, and medical device production. By understanding the different types of silicone release coatings, their applications, and how they work, you can make informed decisions that enhance your production processes and lead to better results.
Popular Silicon Compounds
Popular Silicon Compounds
Related News & Blog
Related News & Blog
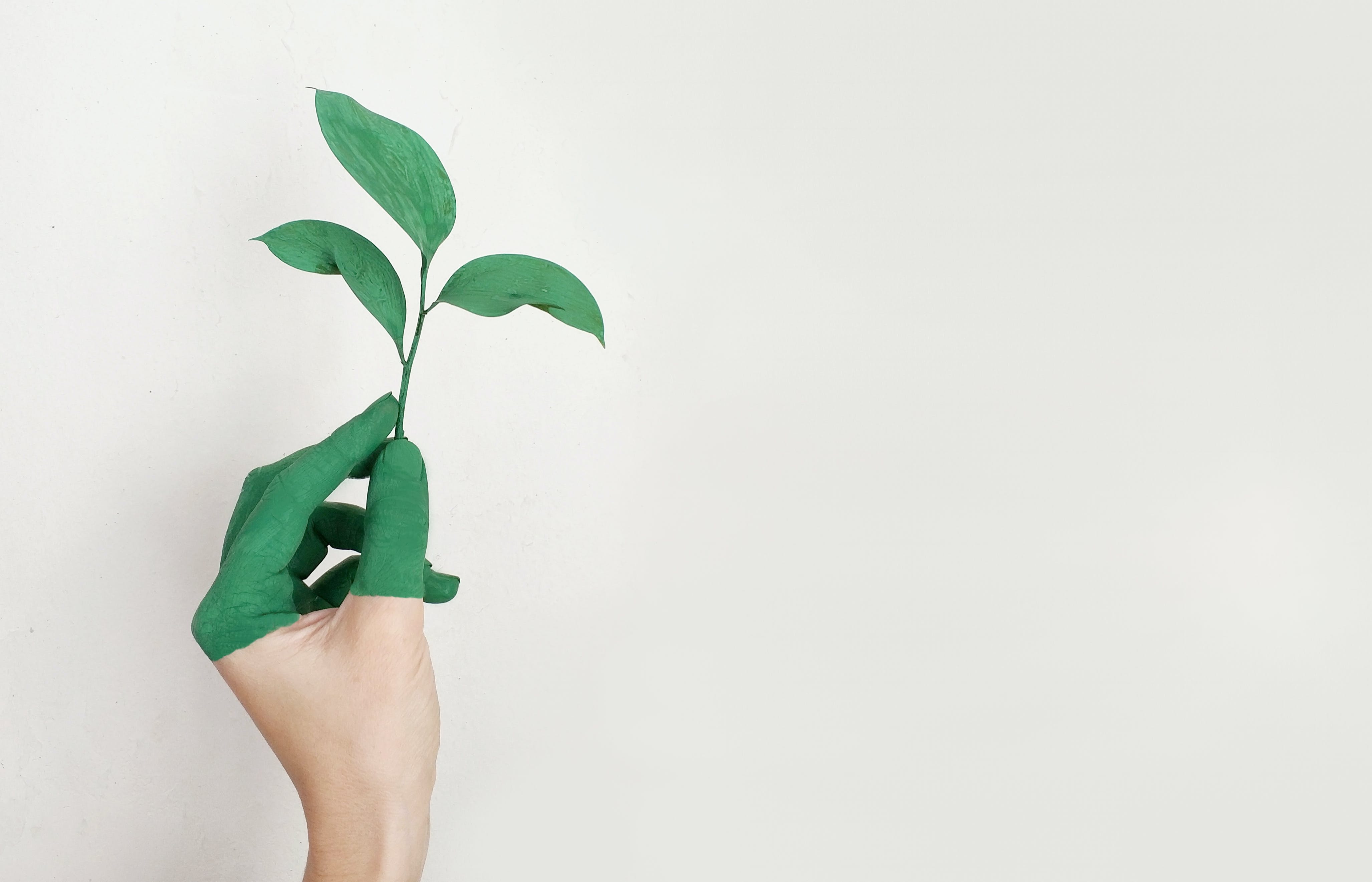
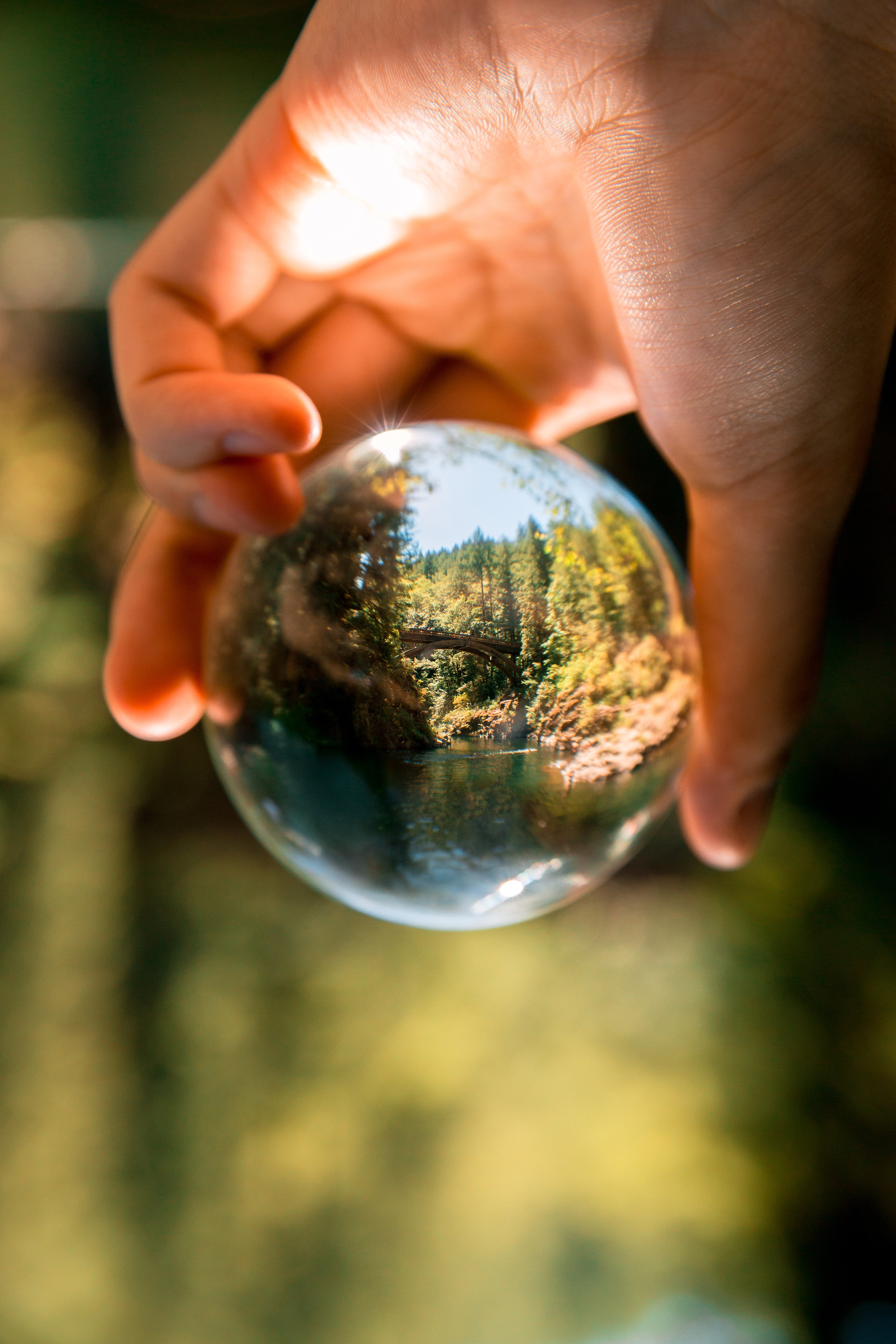
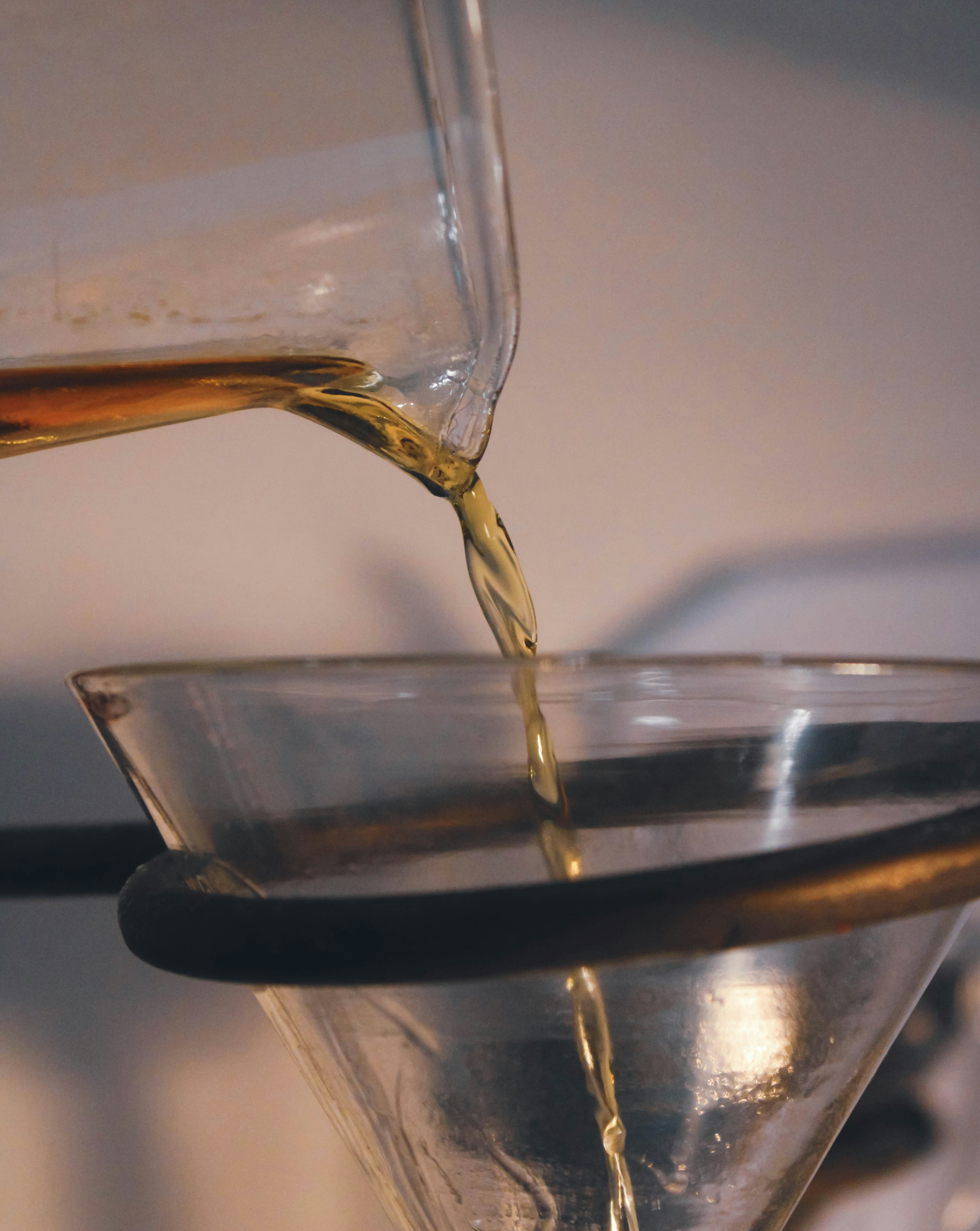
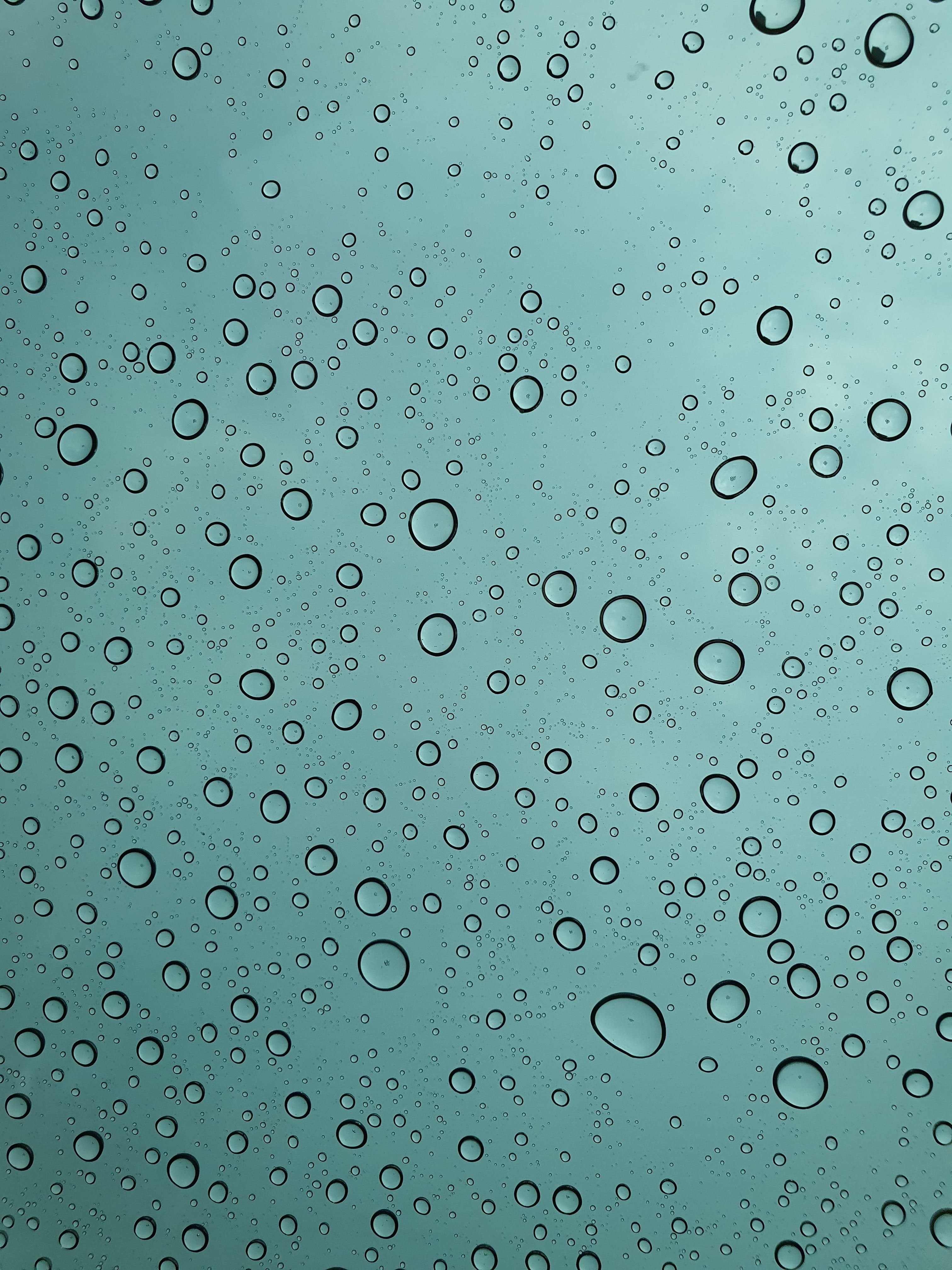
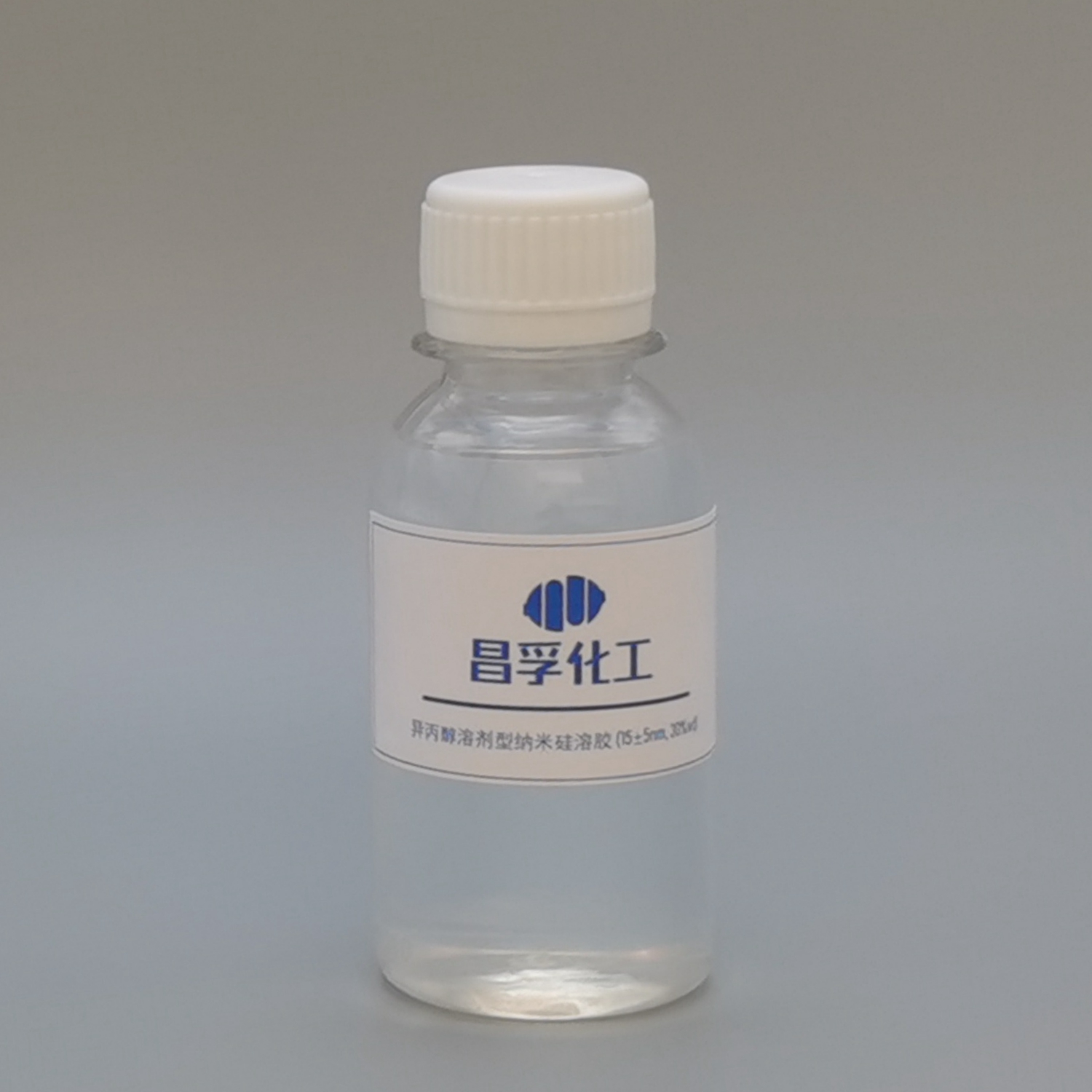
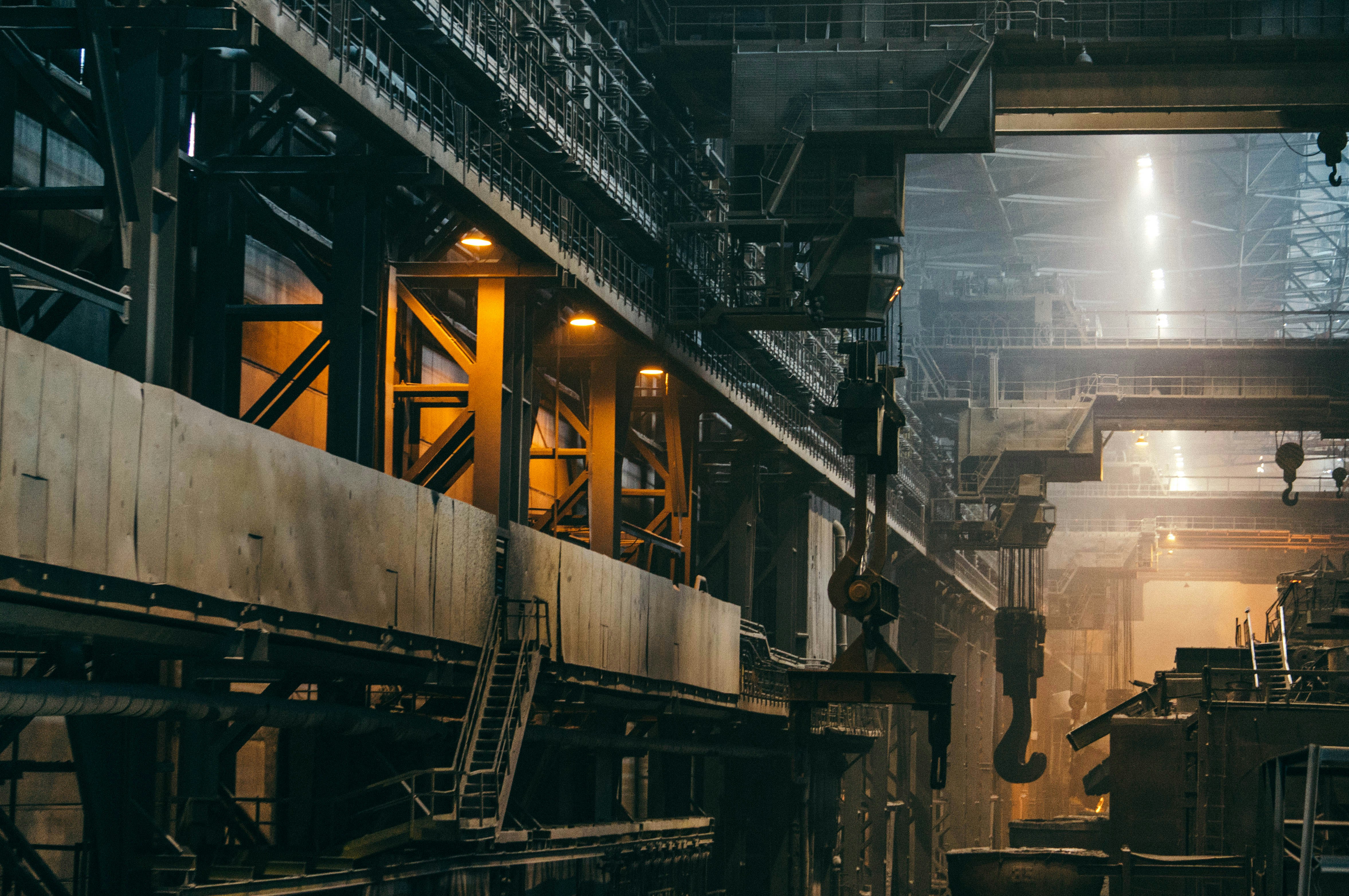
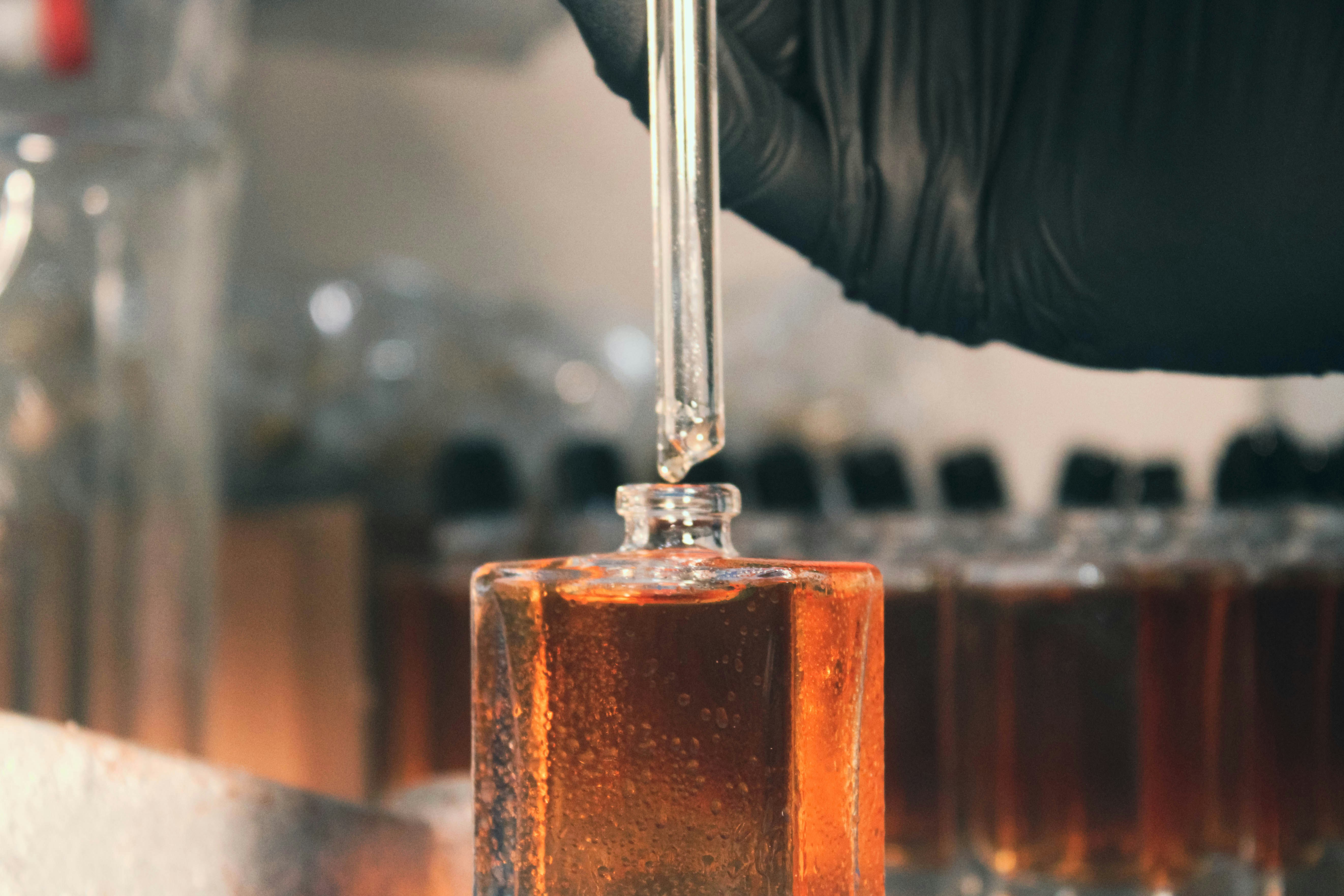
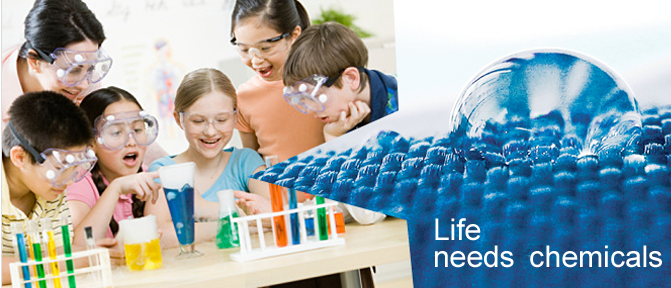

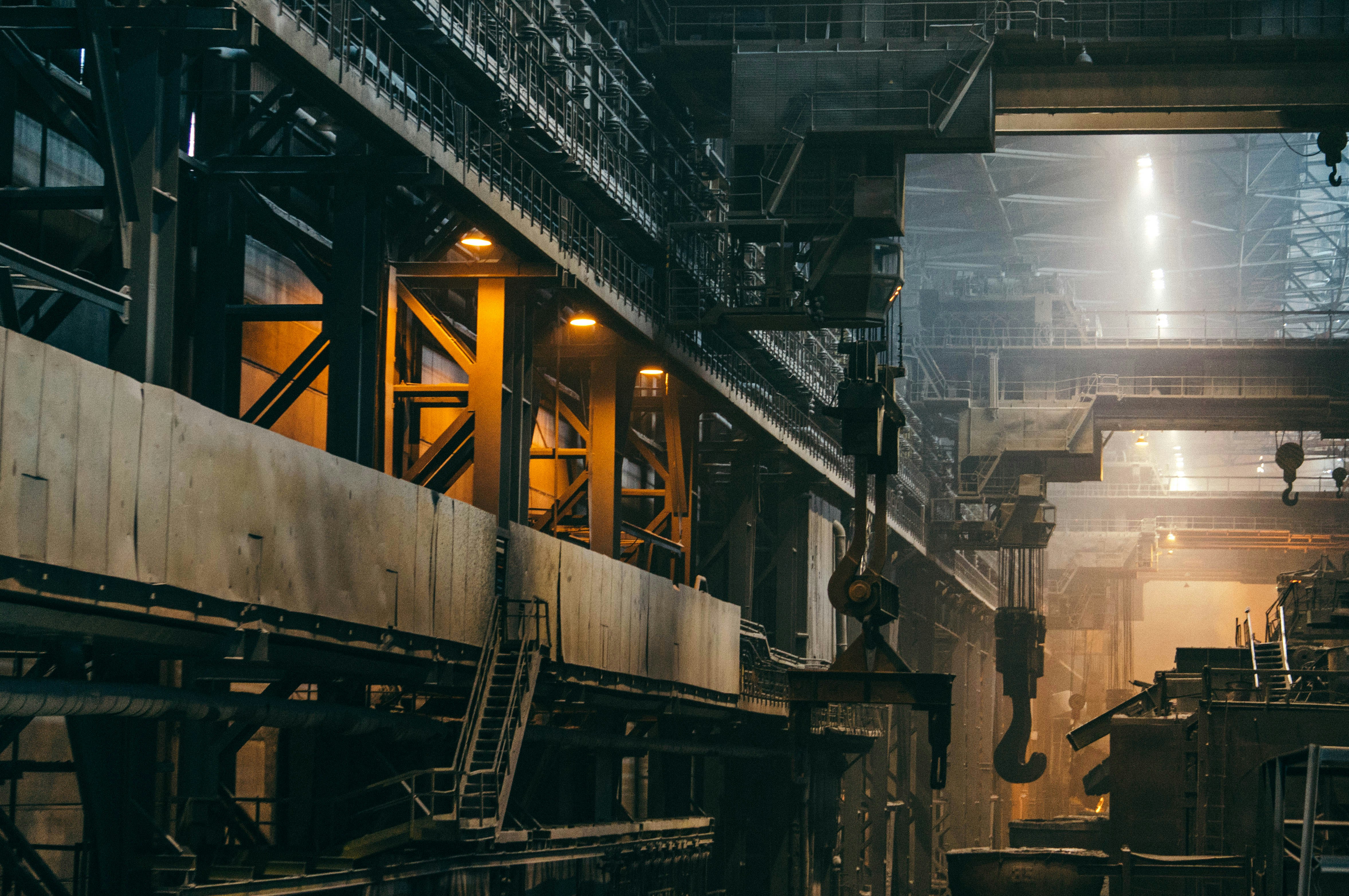
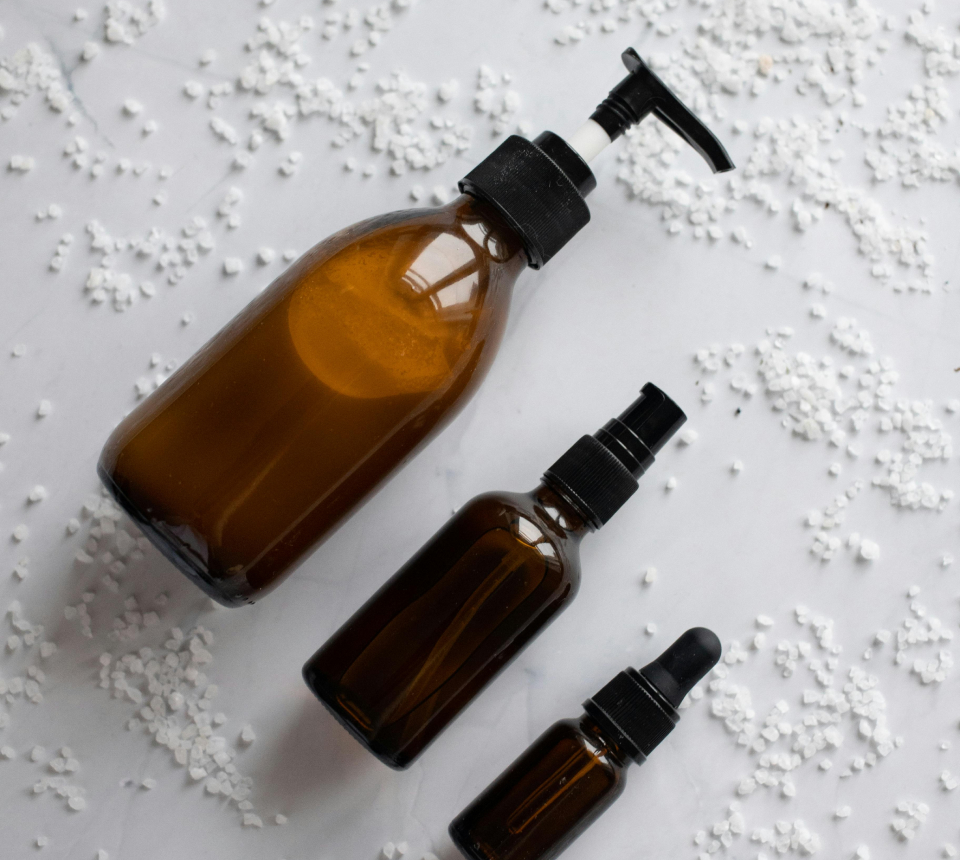
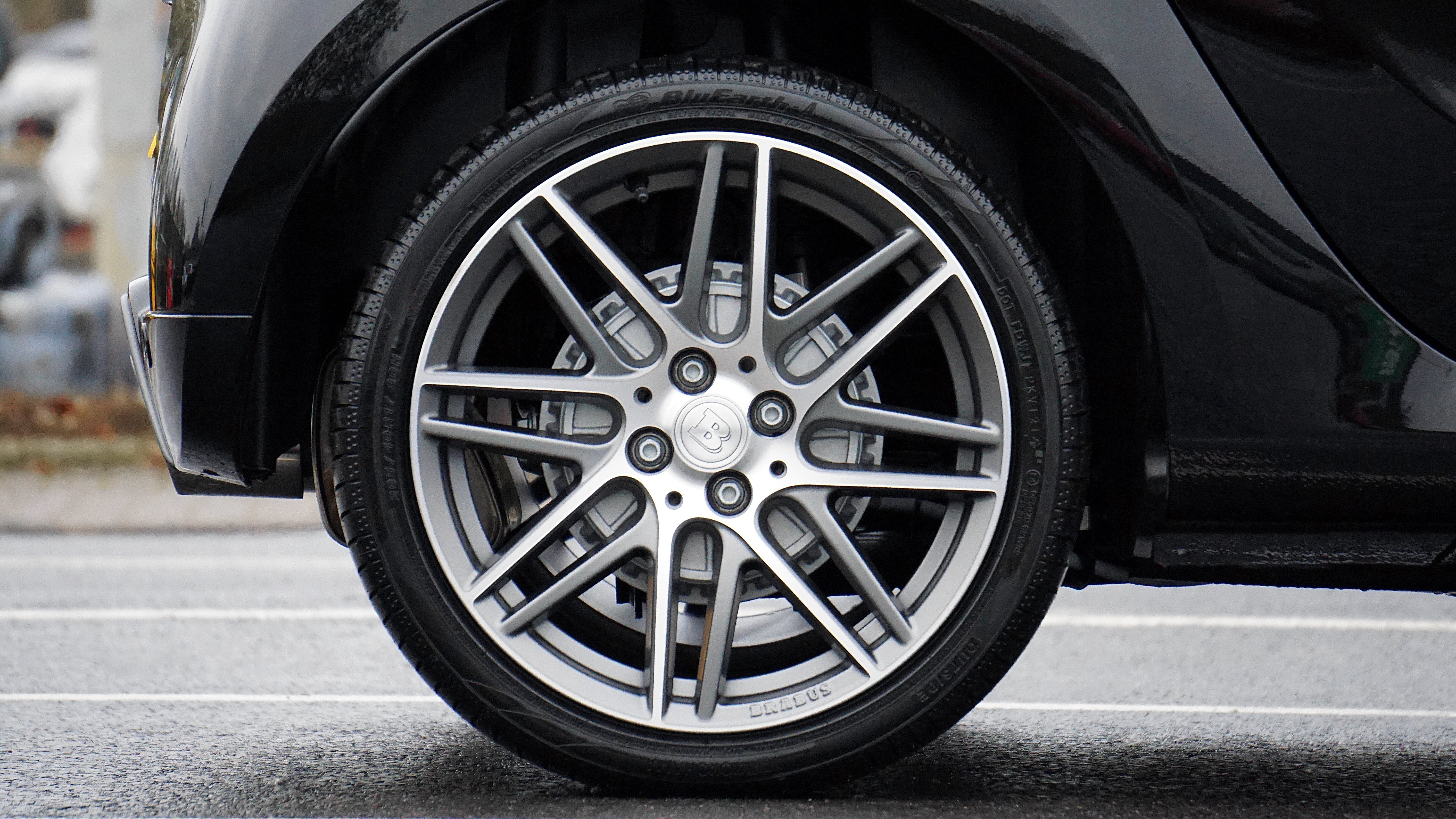
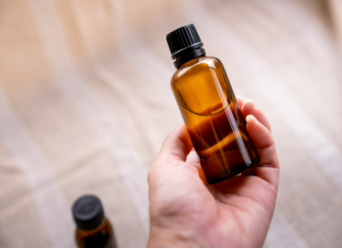
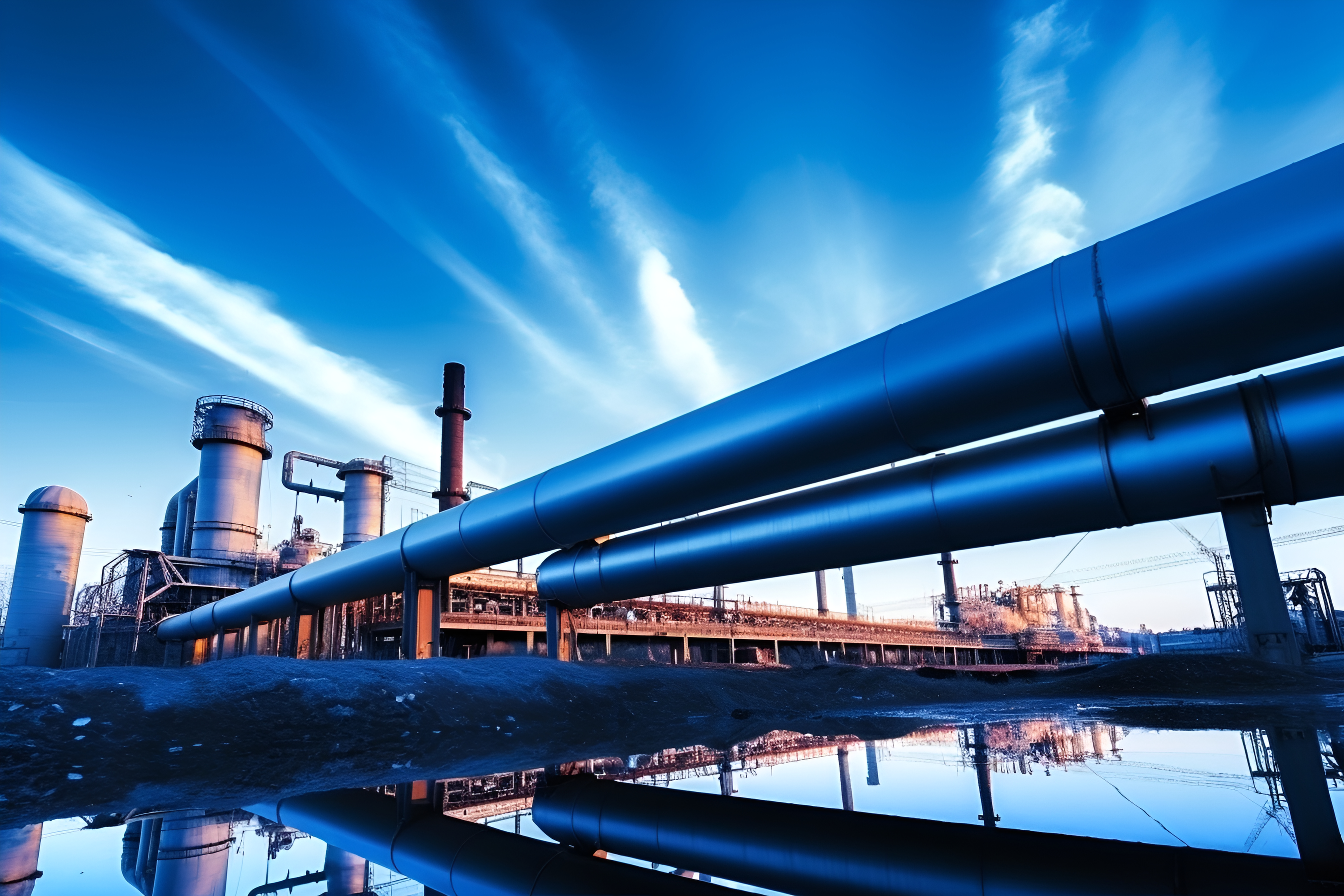

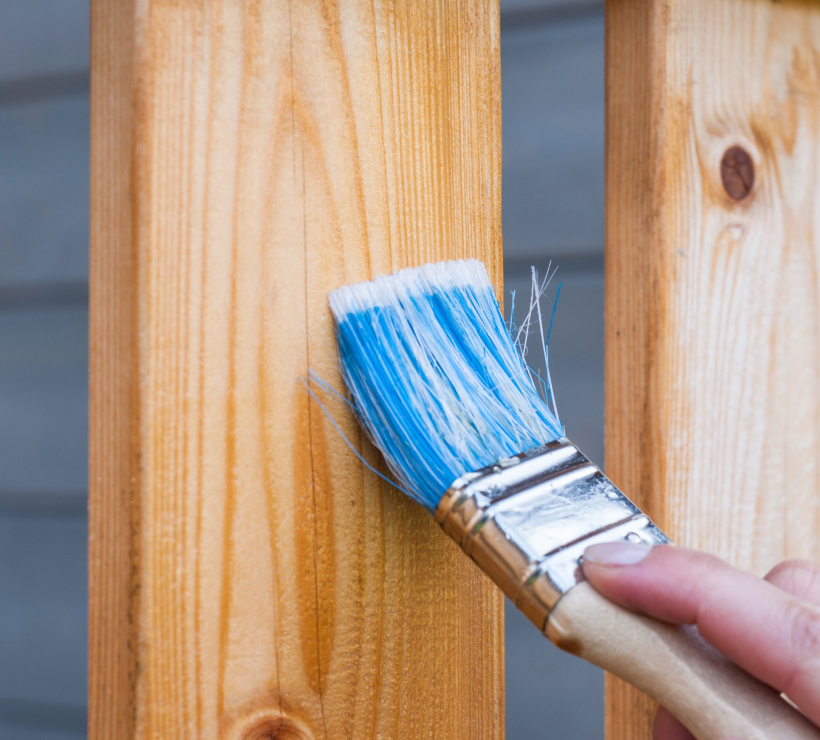
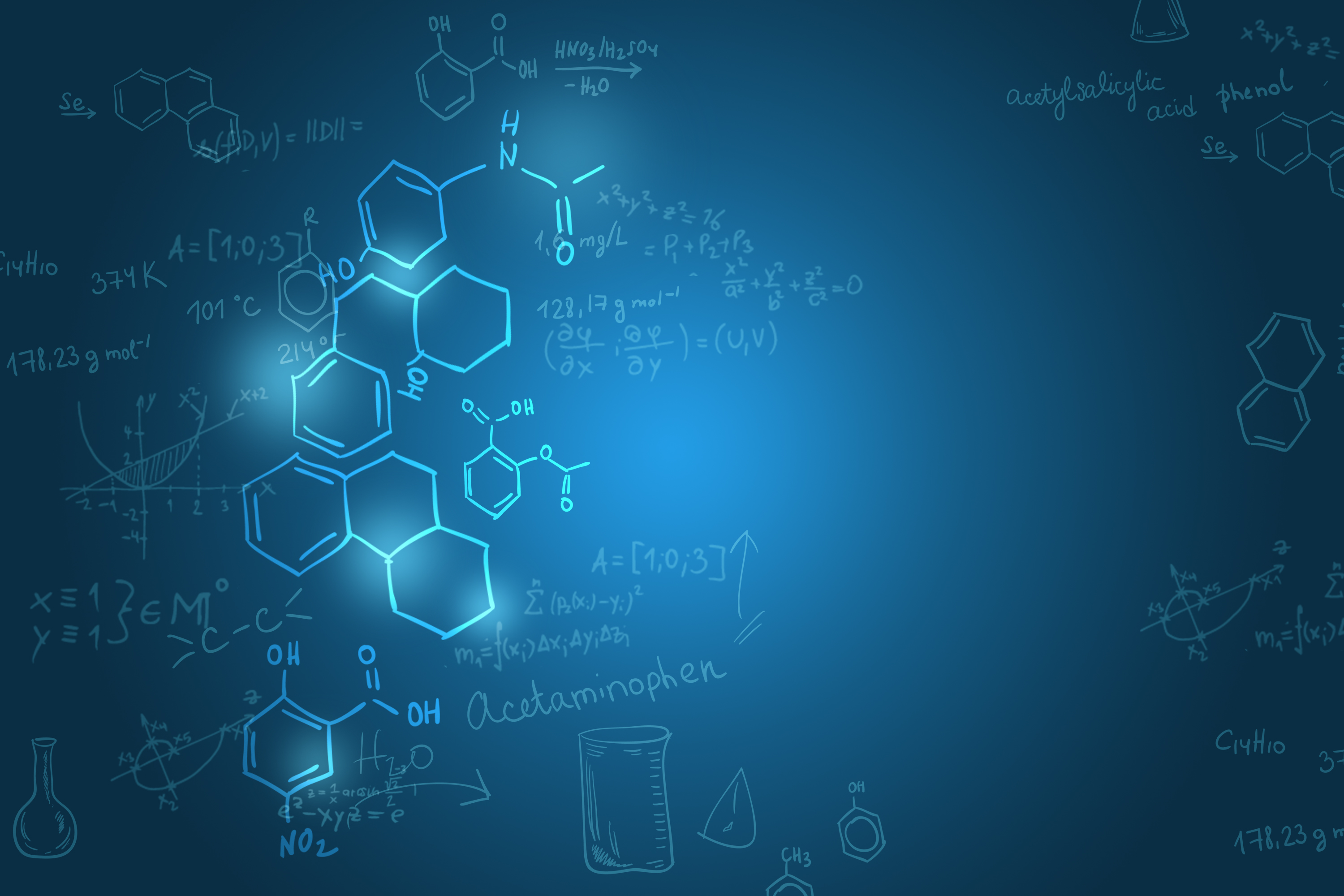
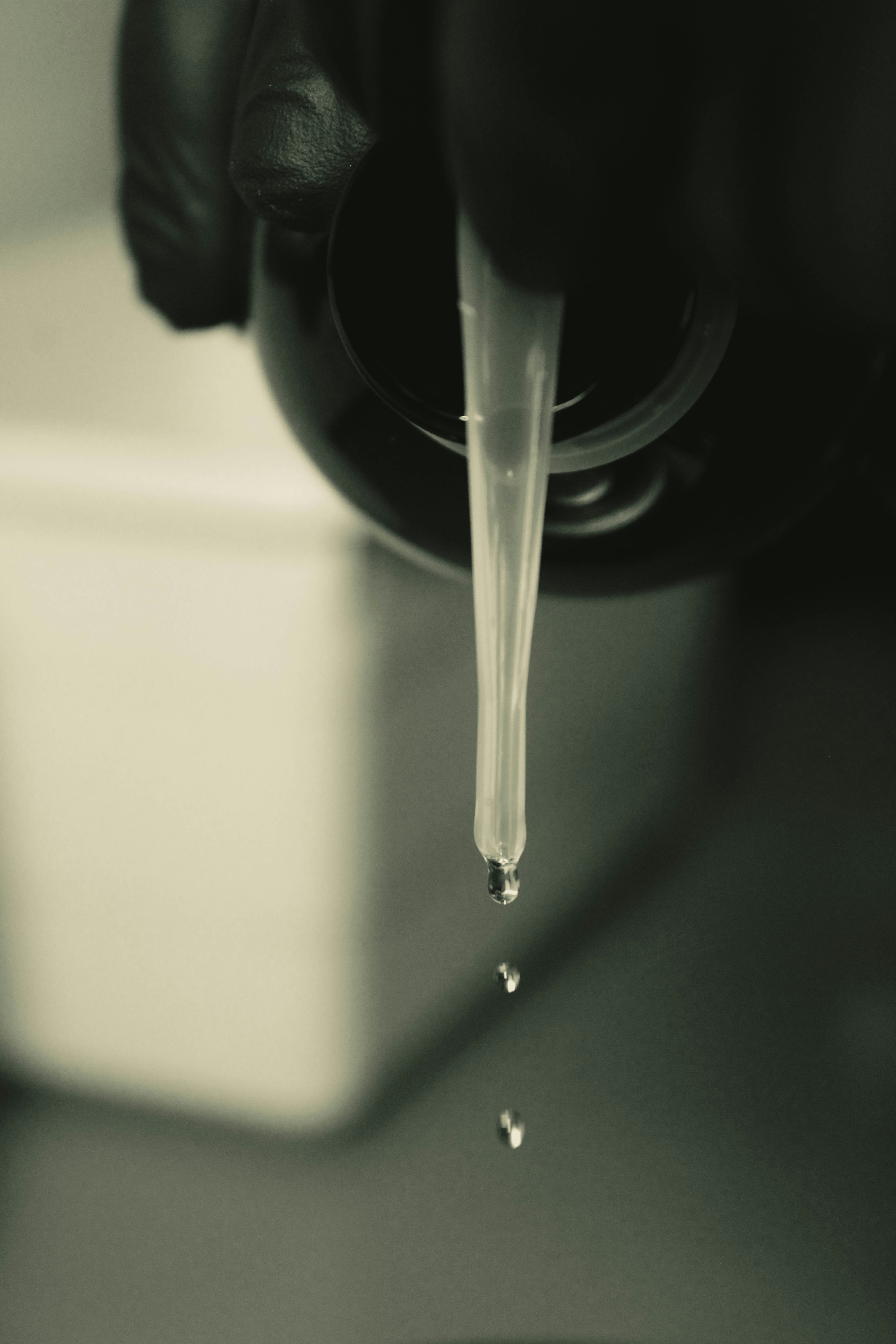
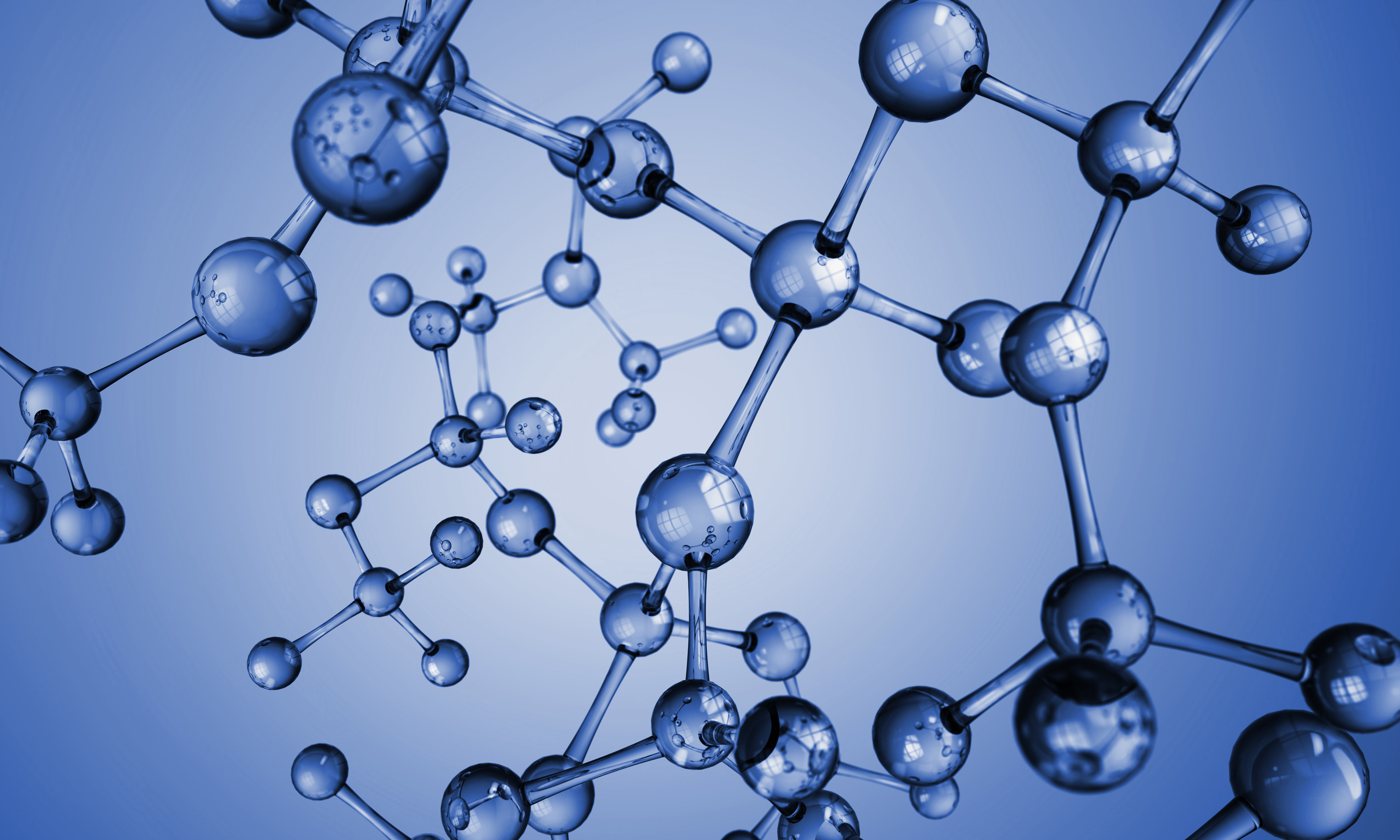
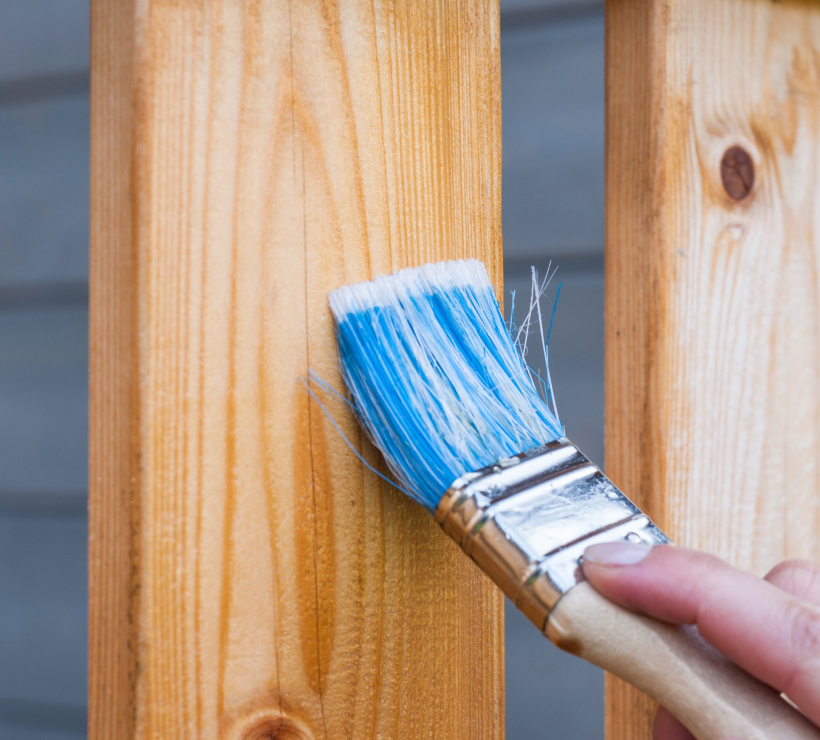

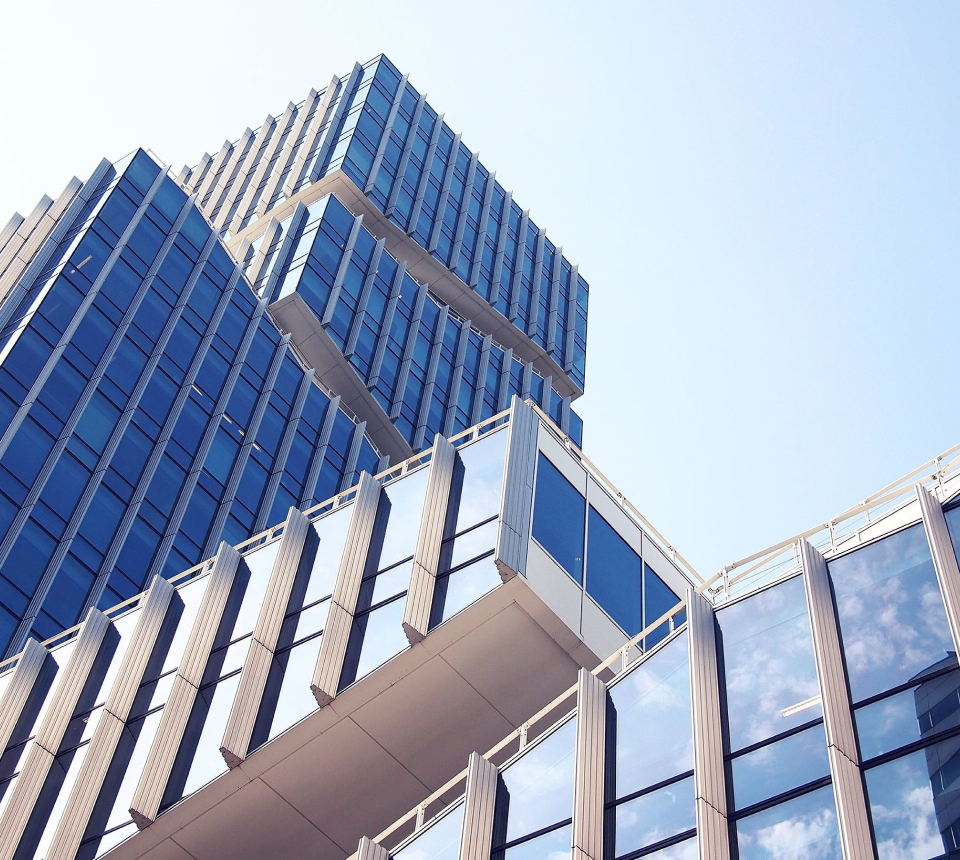
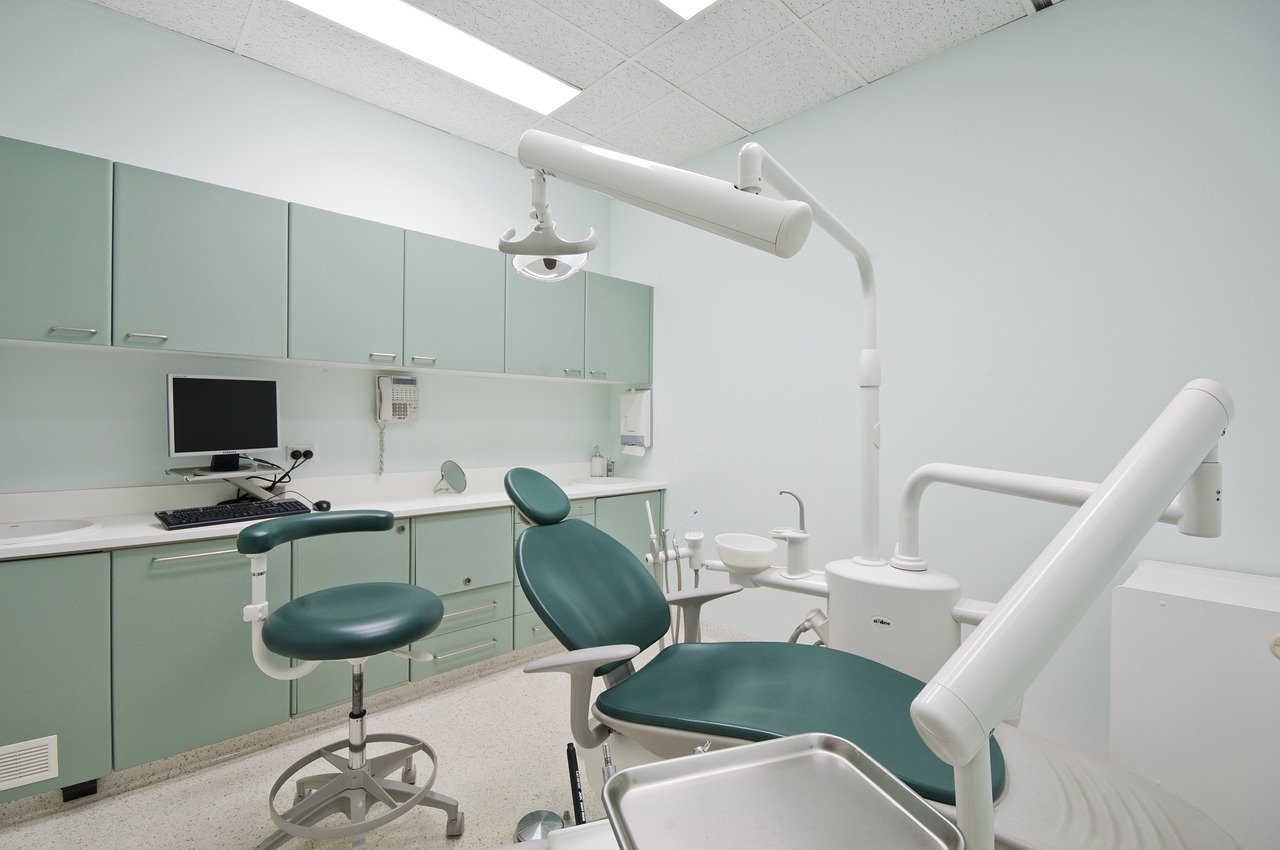
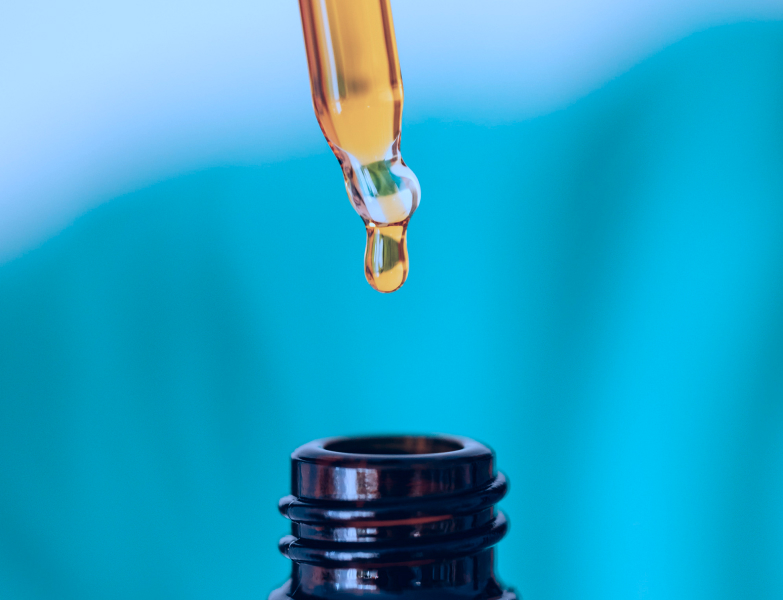
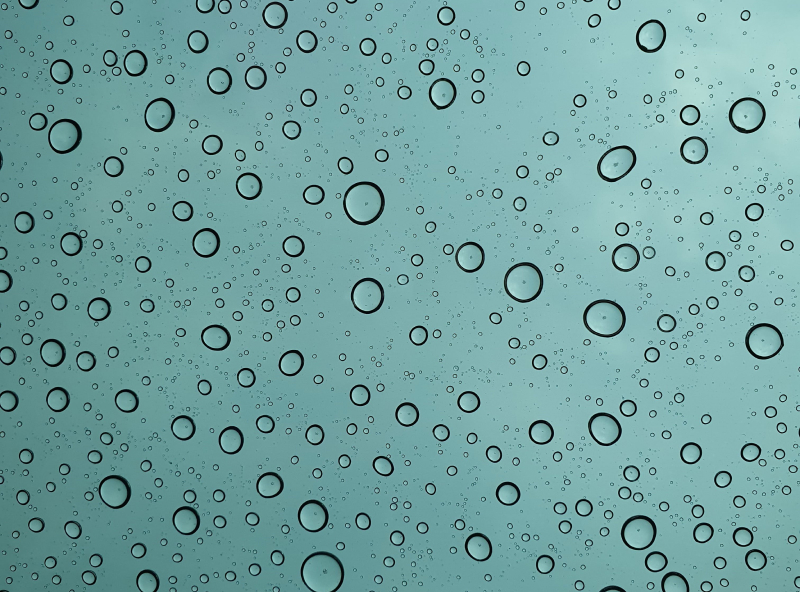
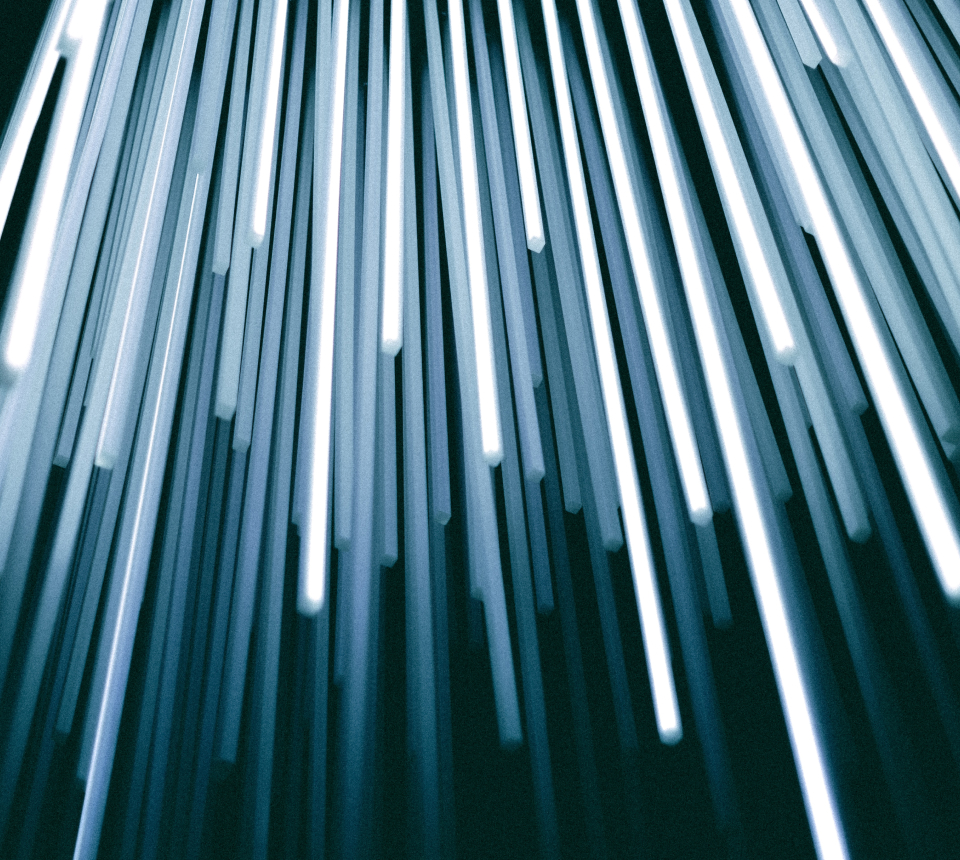
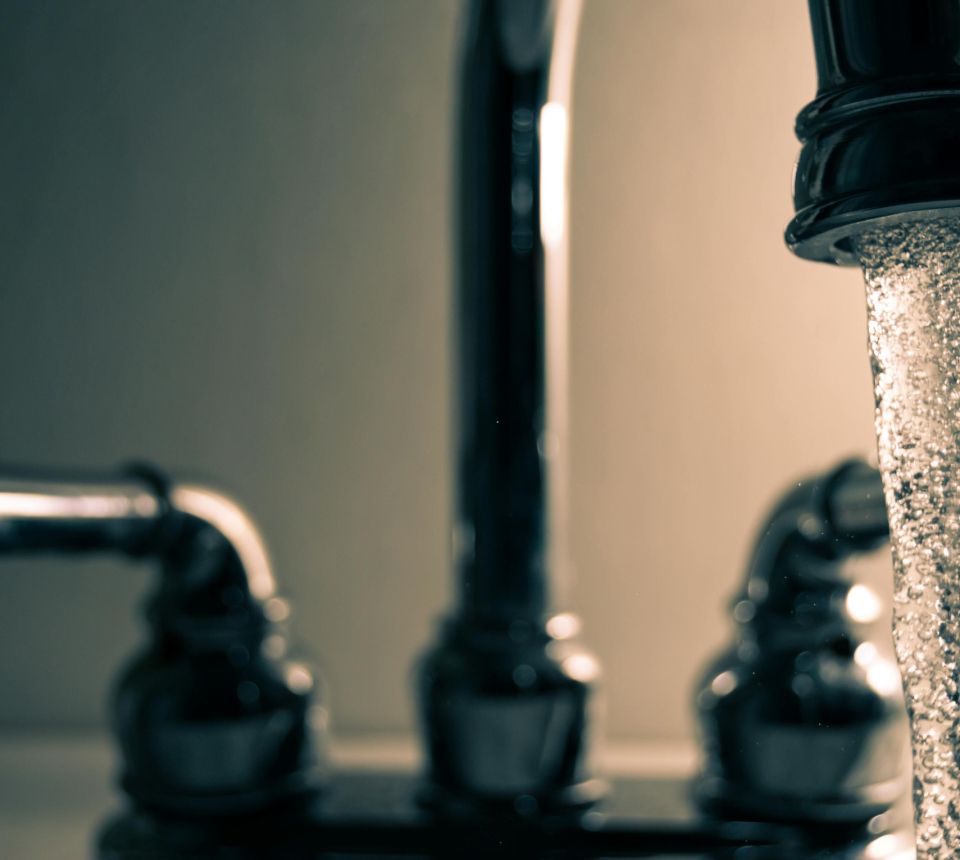
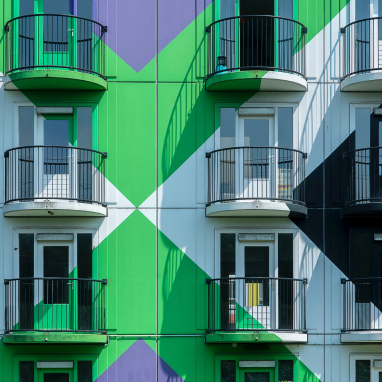
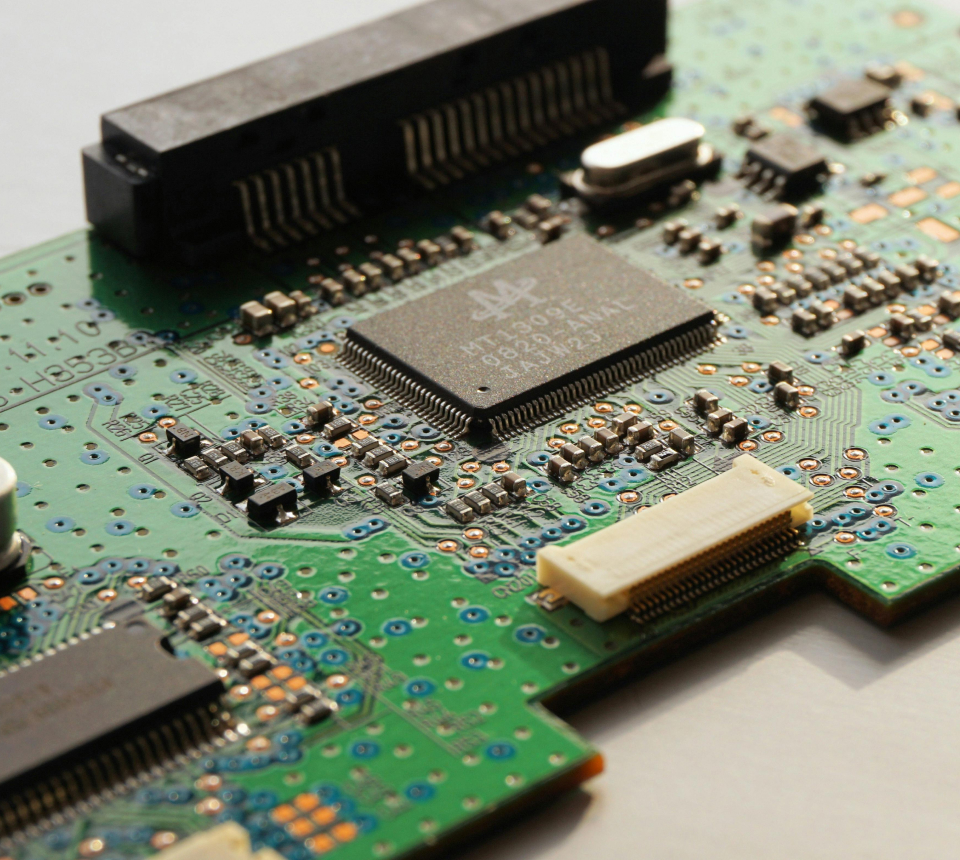
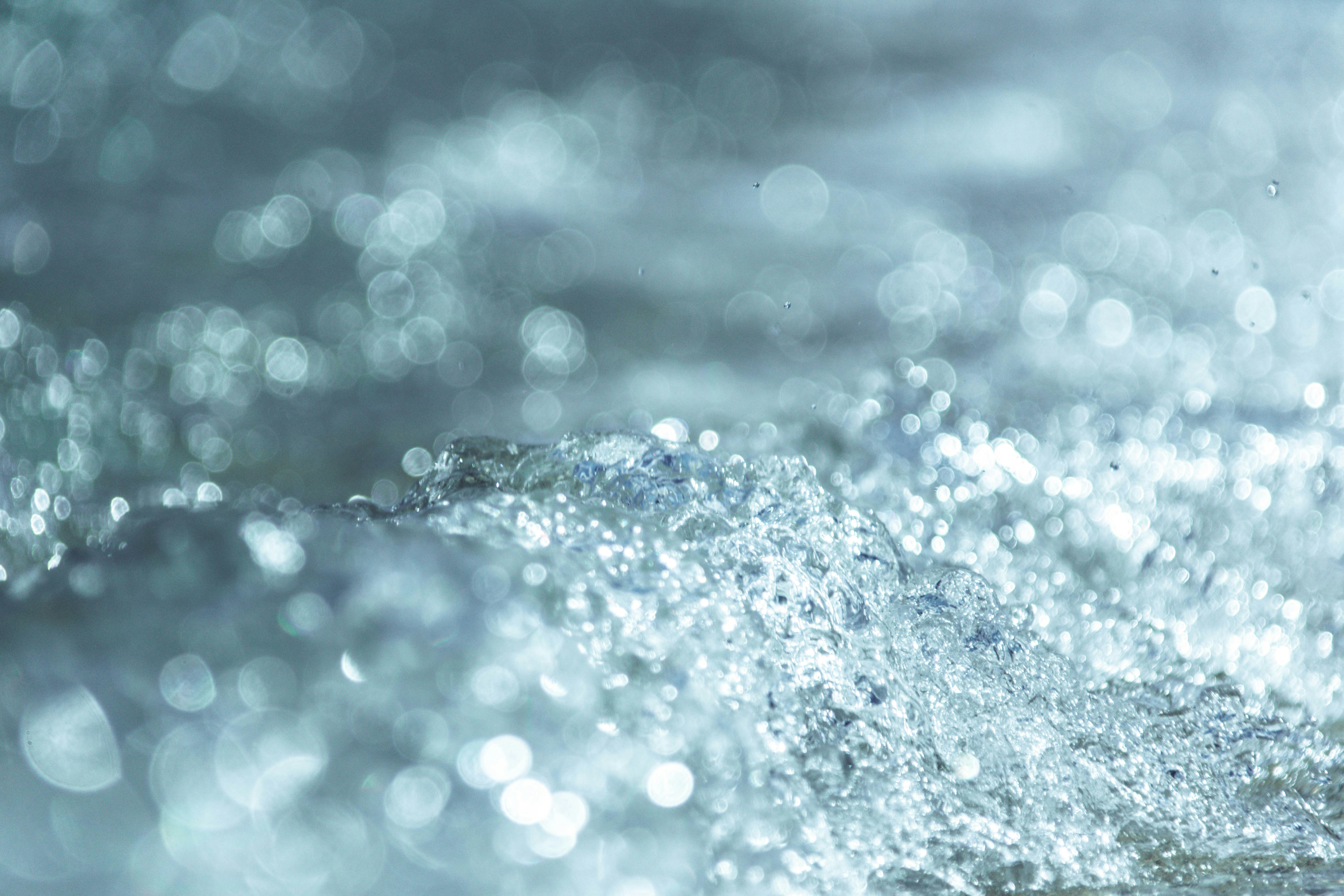
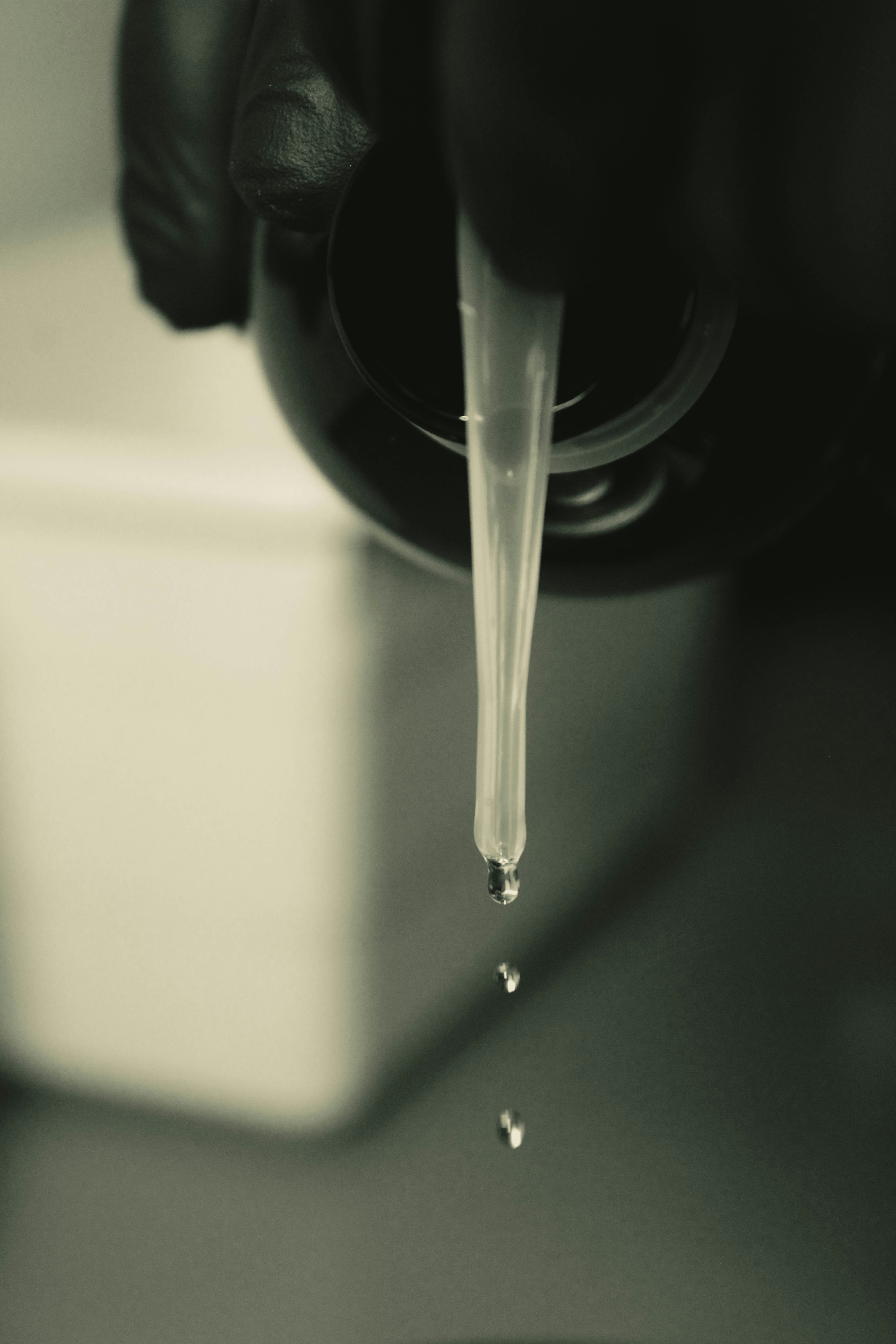
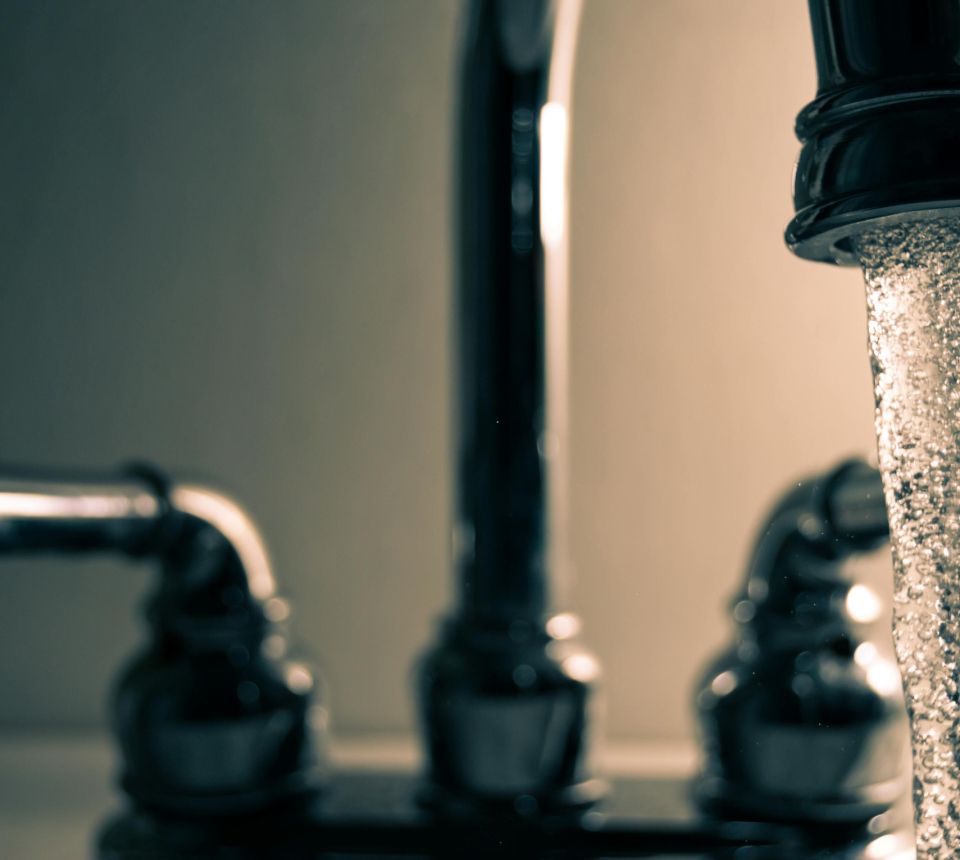
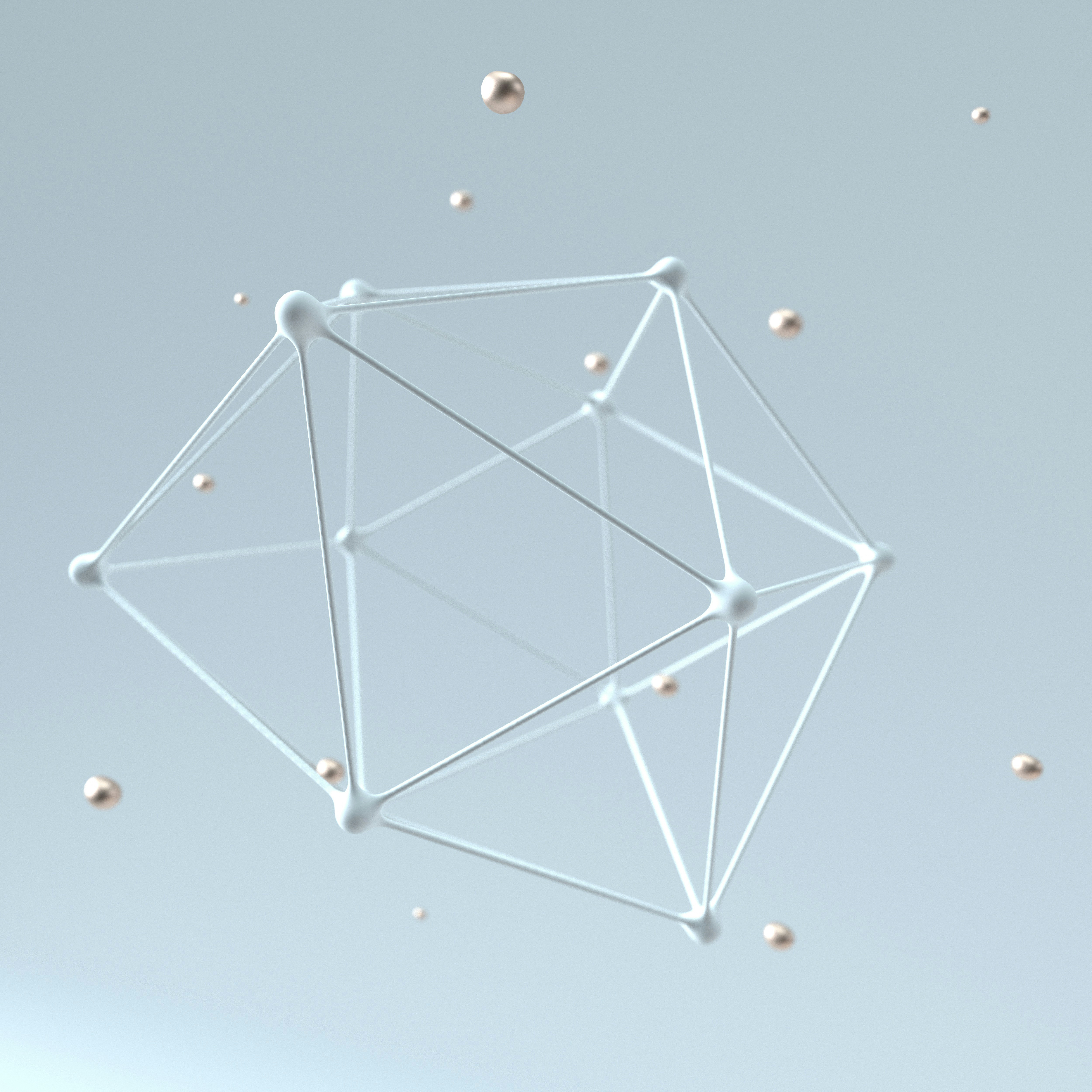
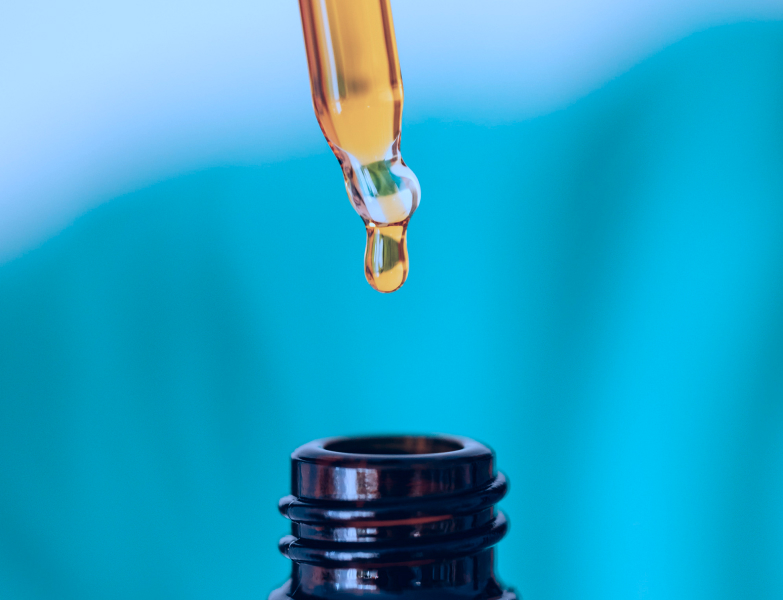
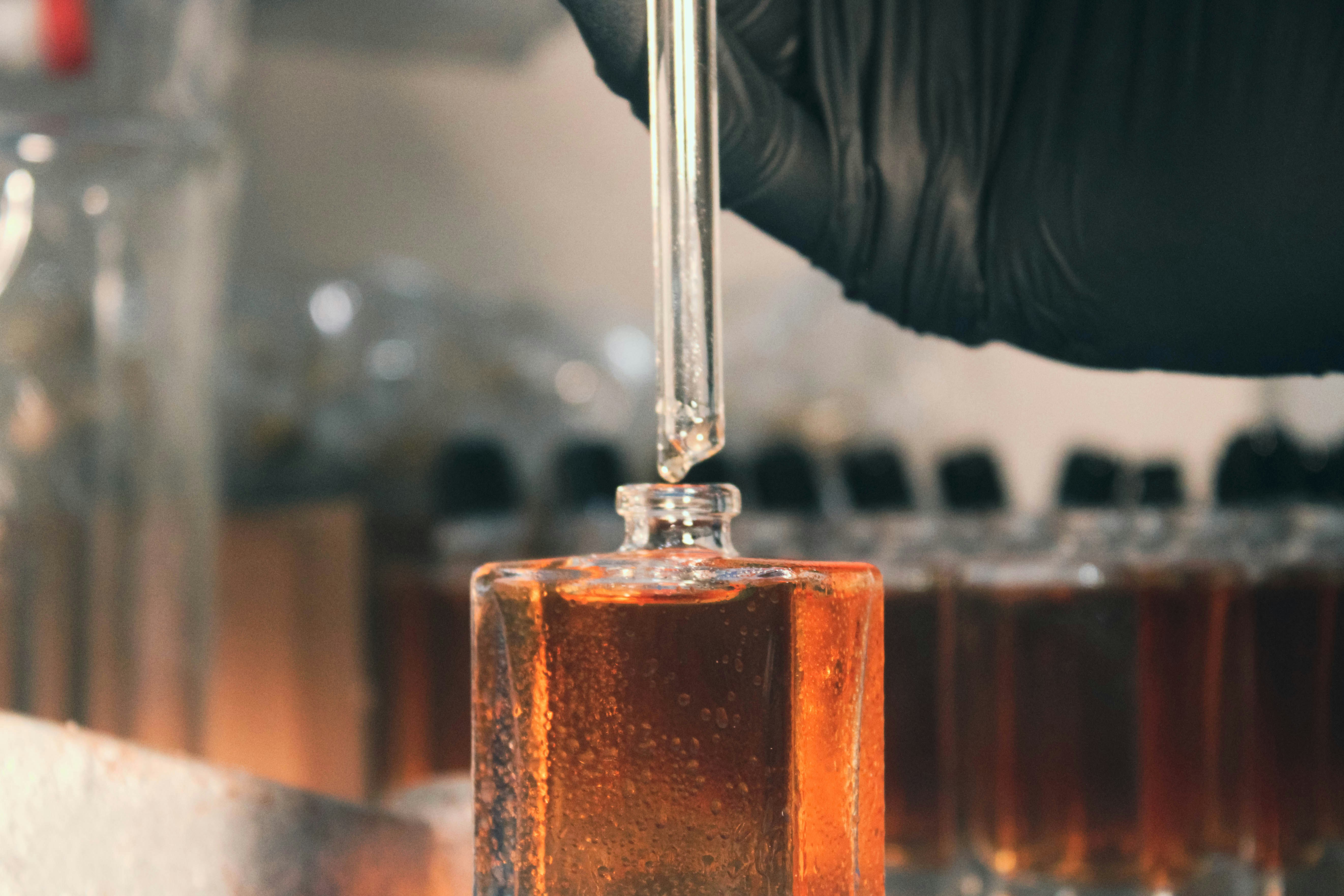
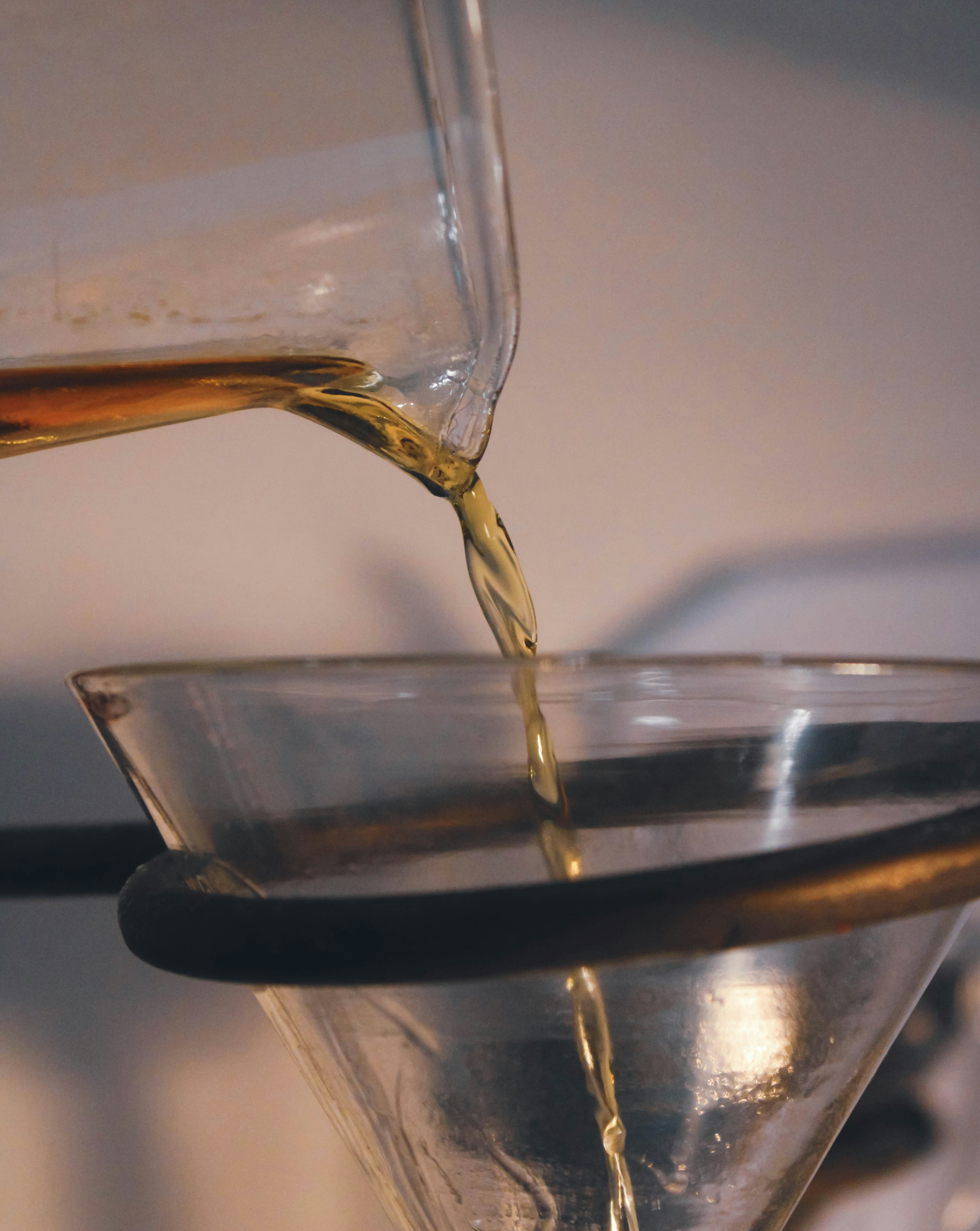
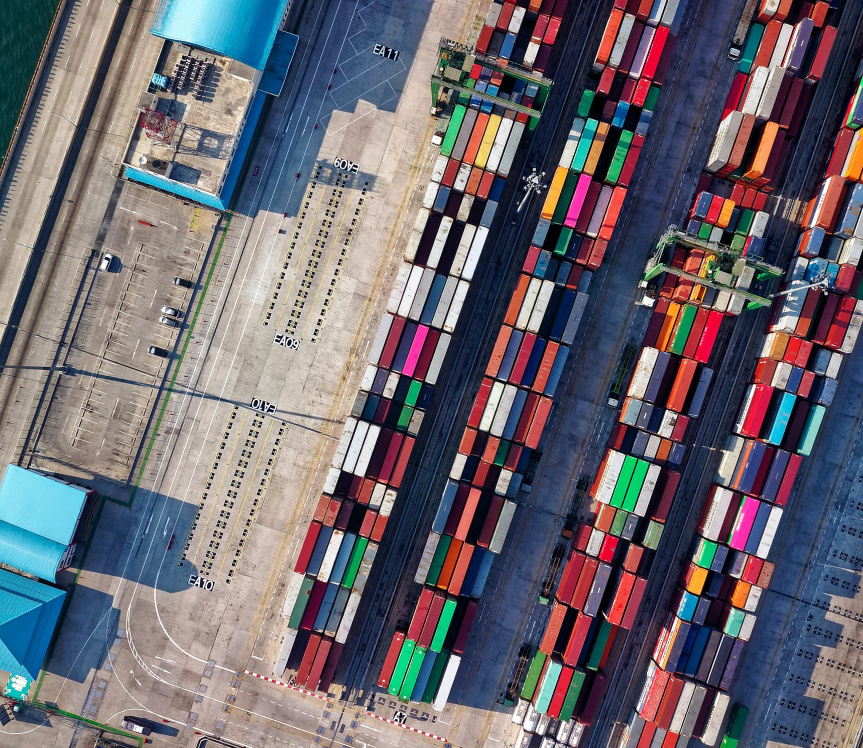
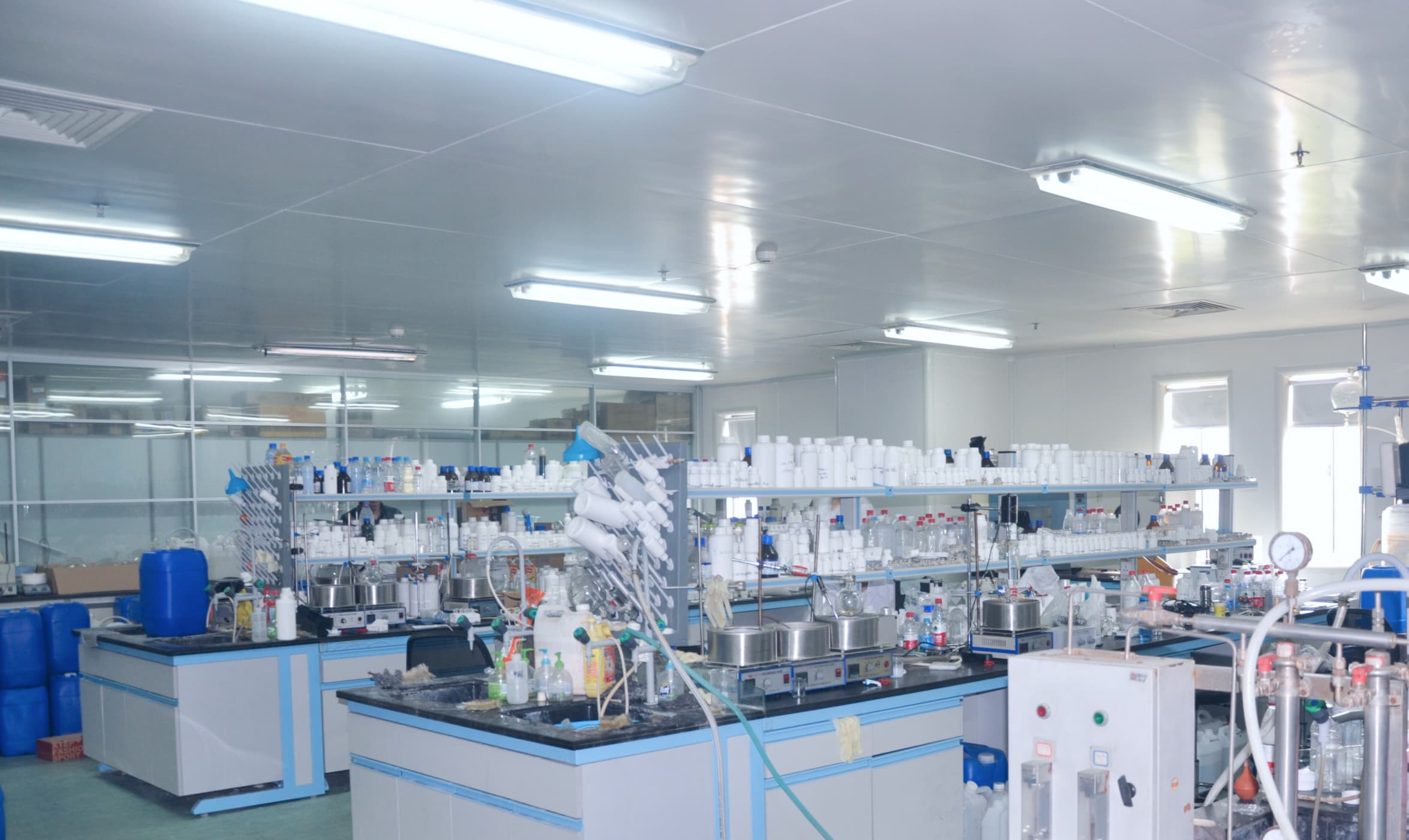
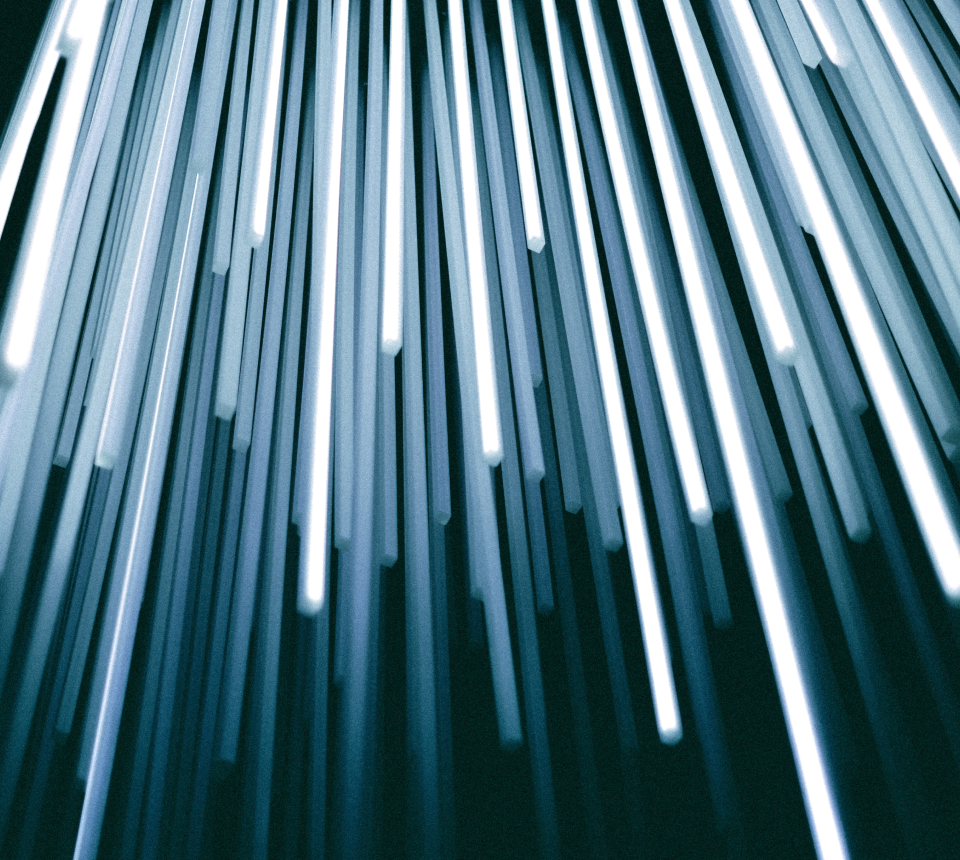
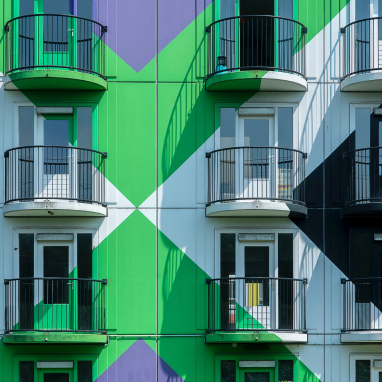
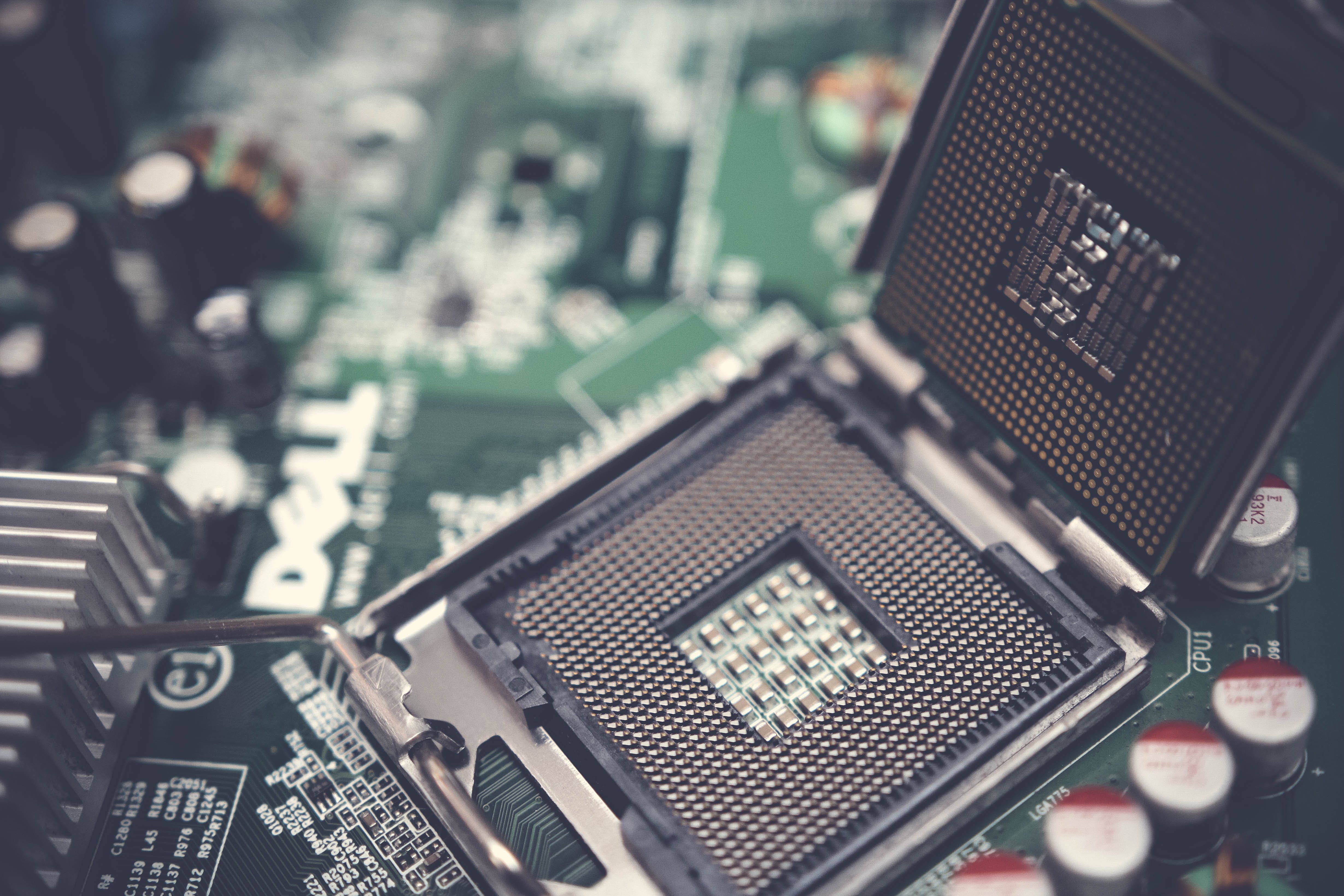
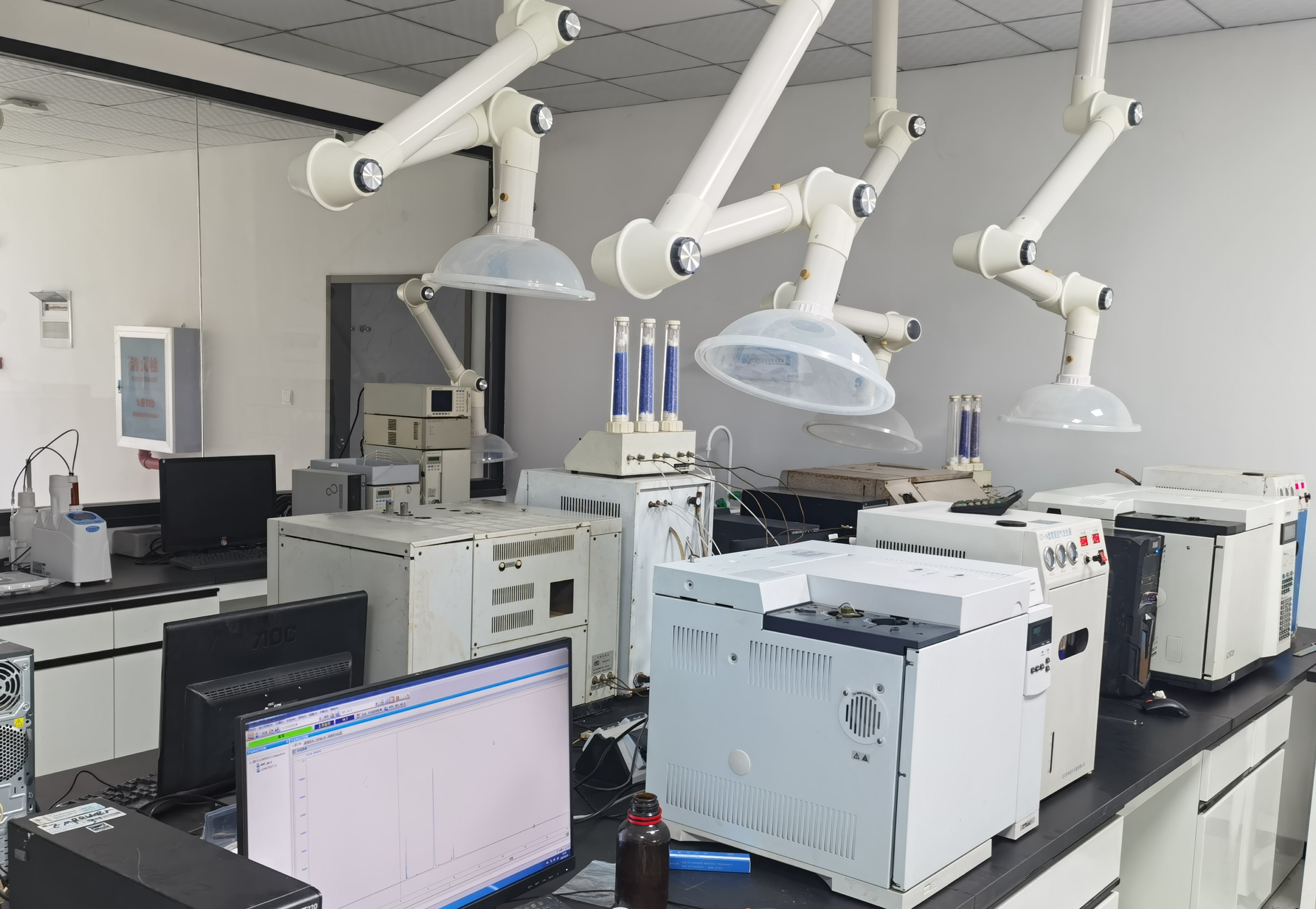
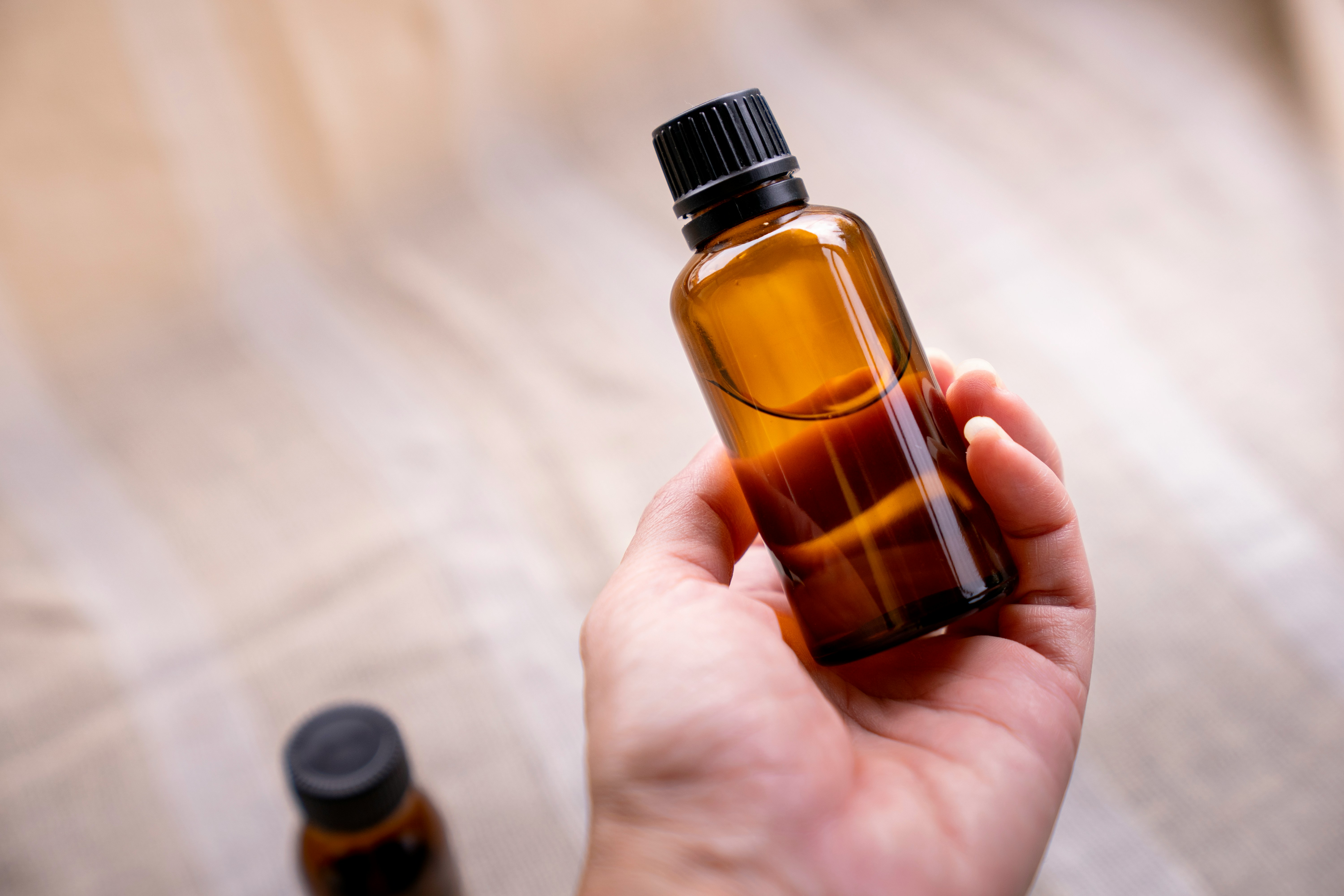
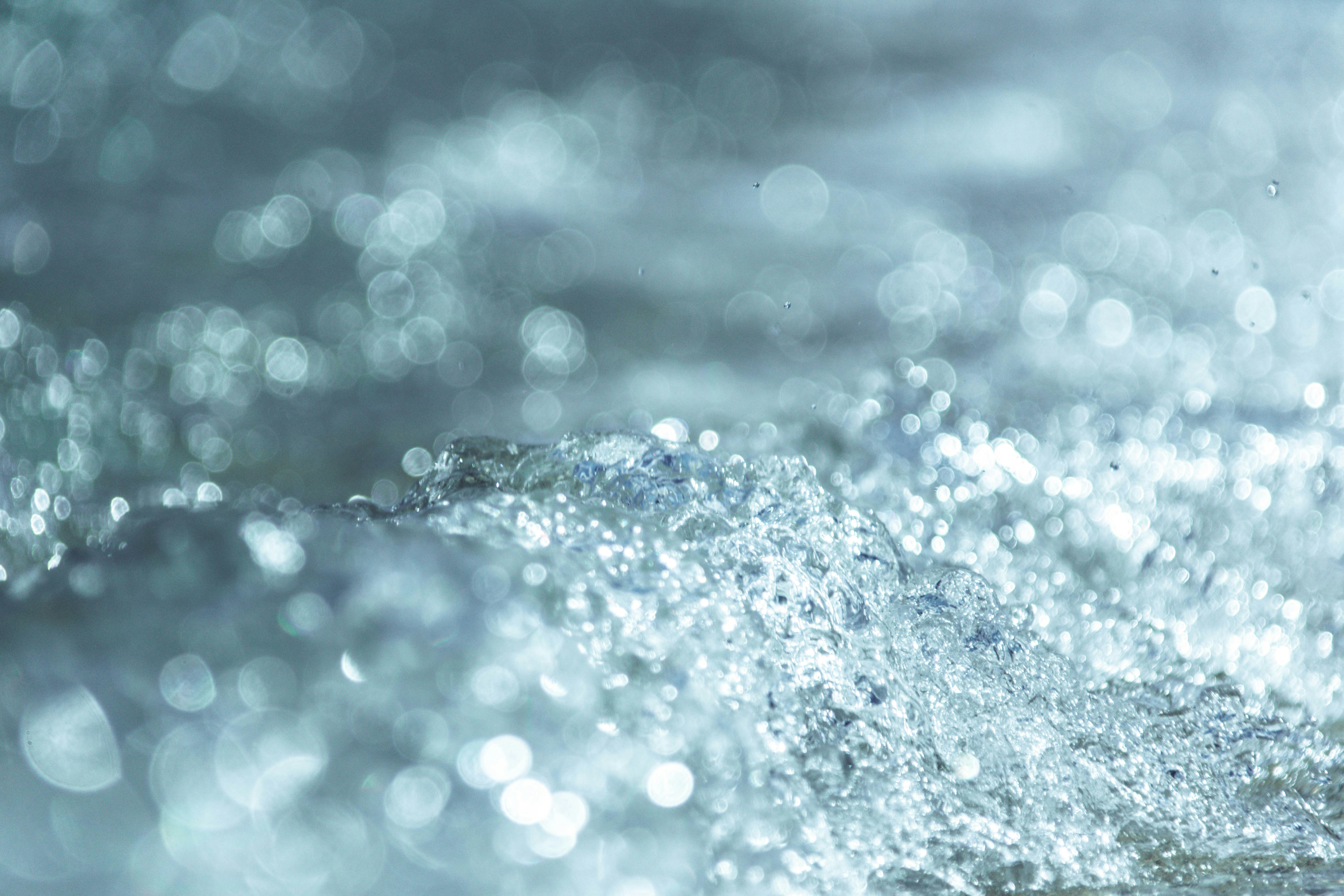
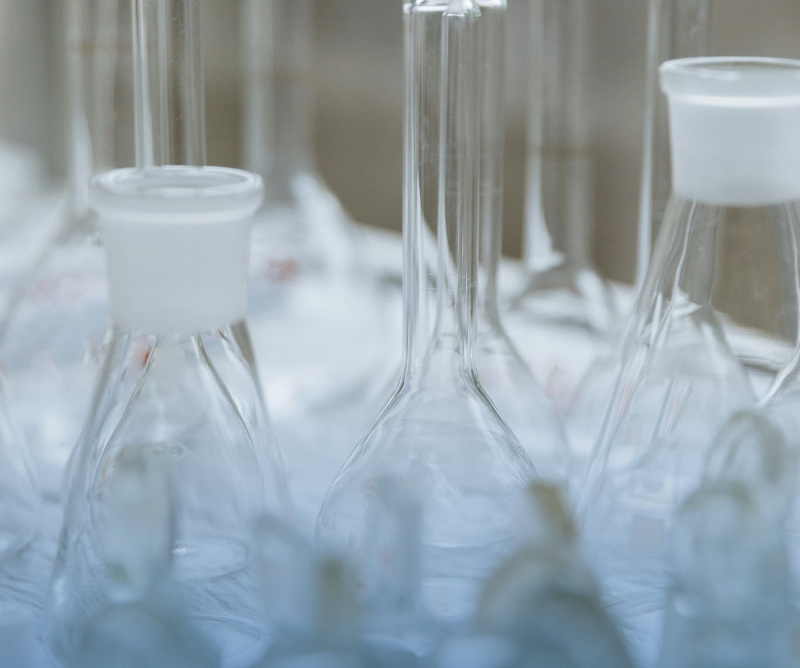
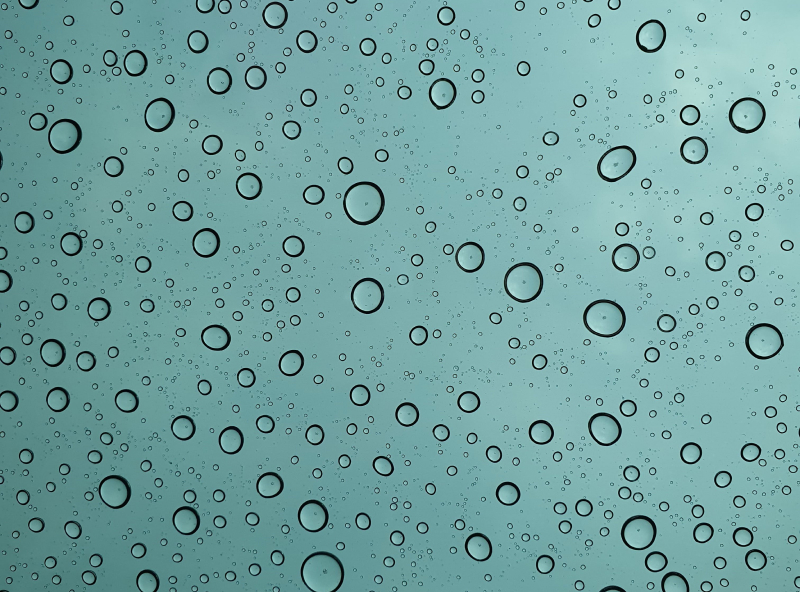
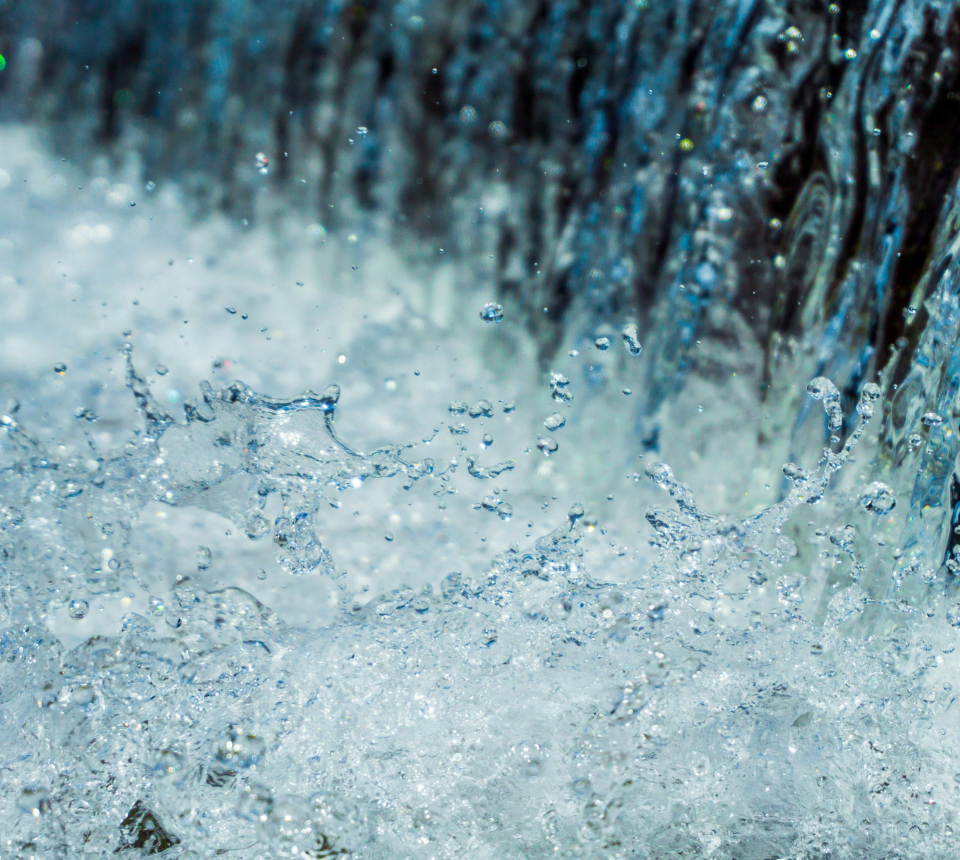
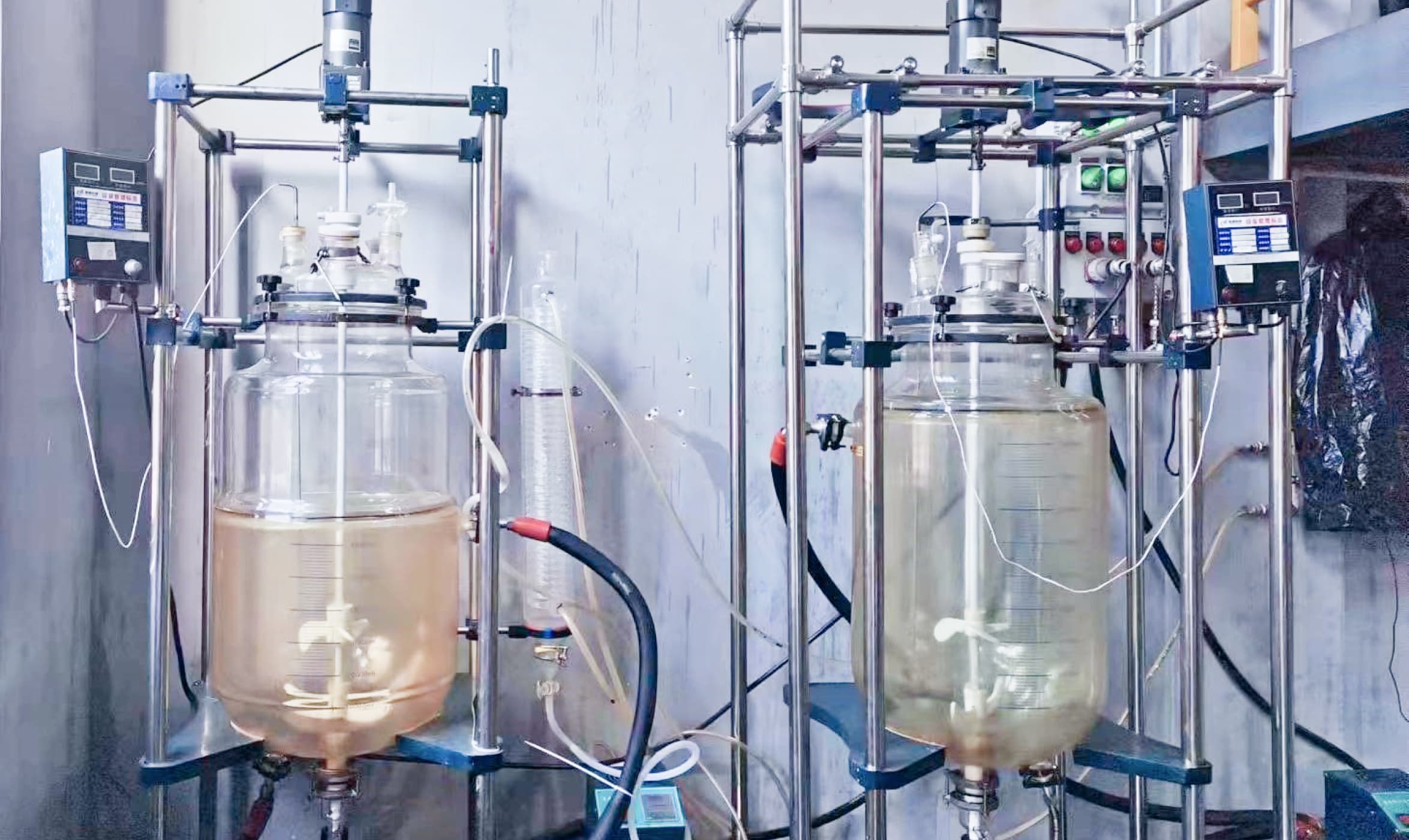
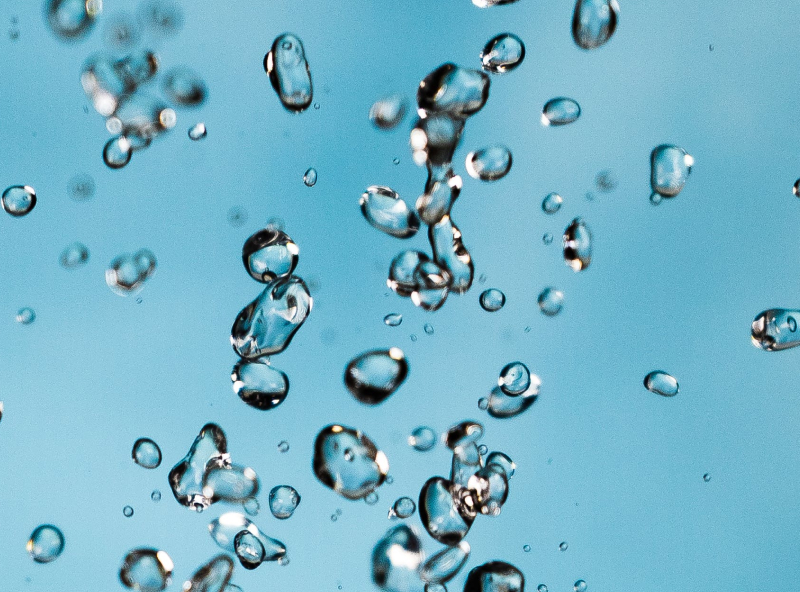
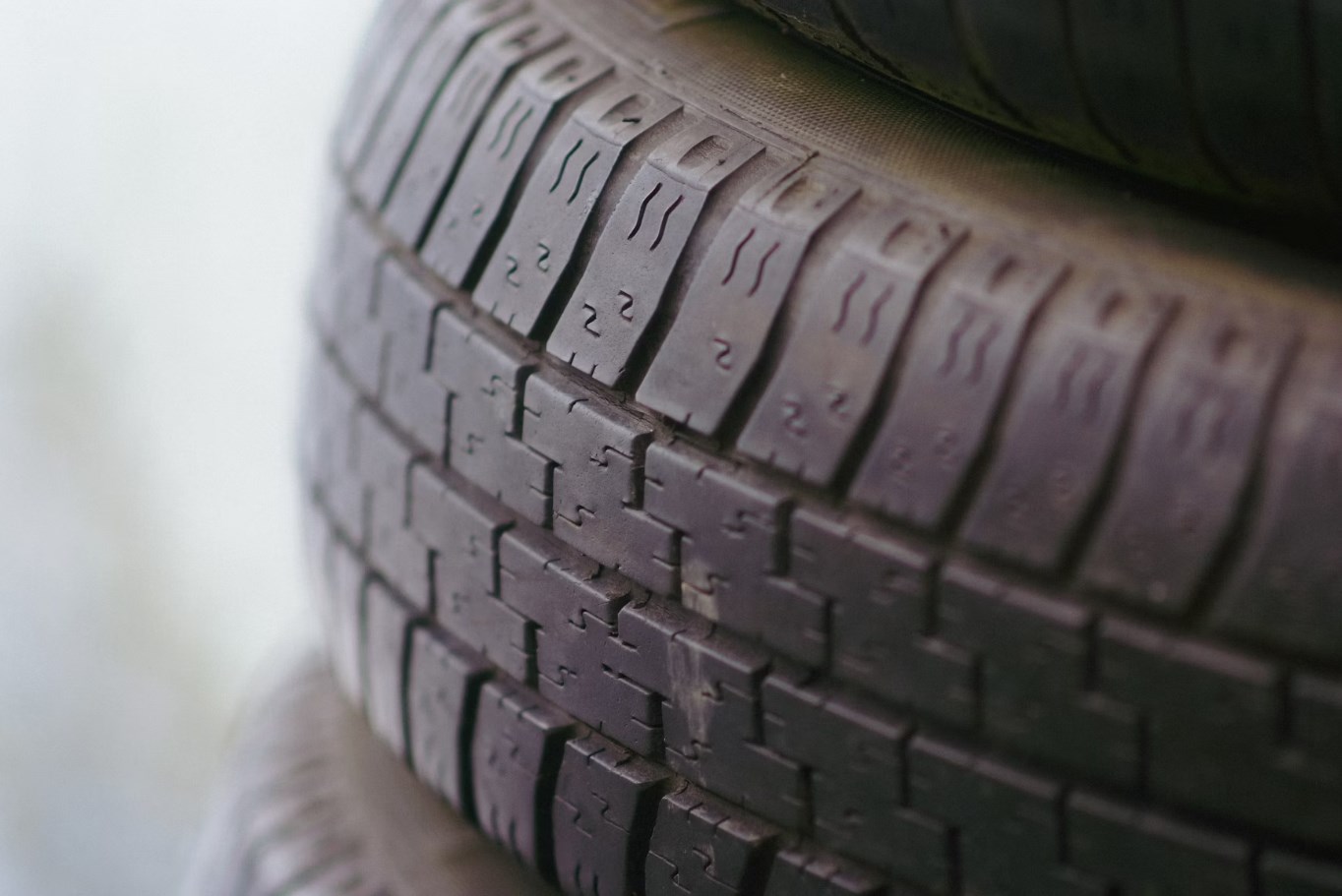
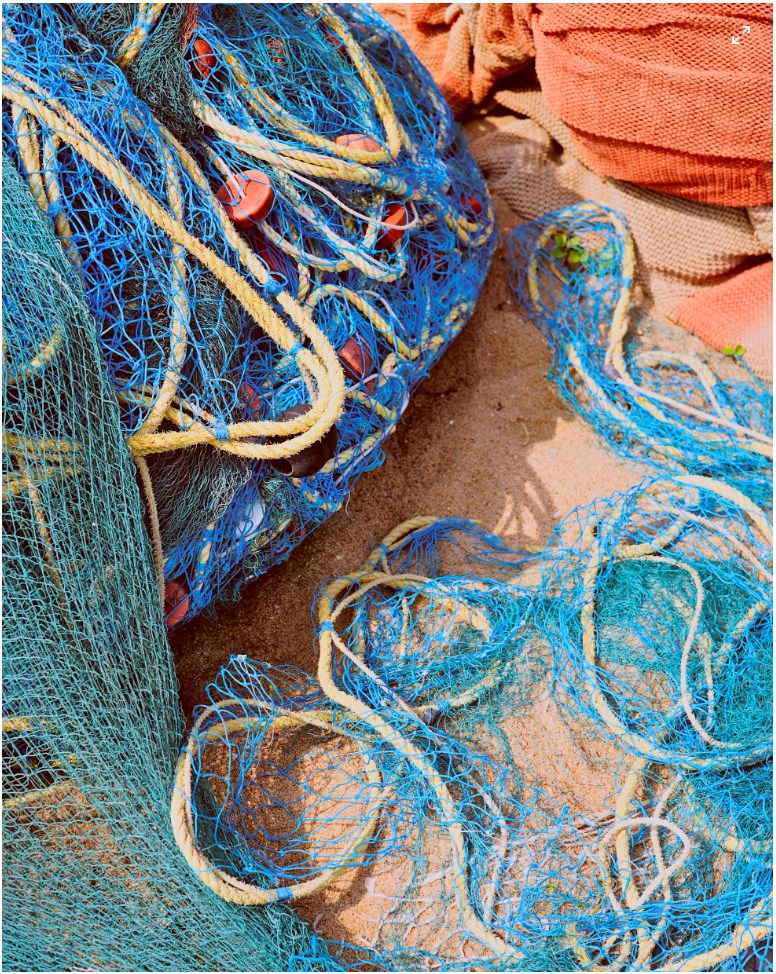
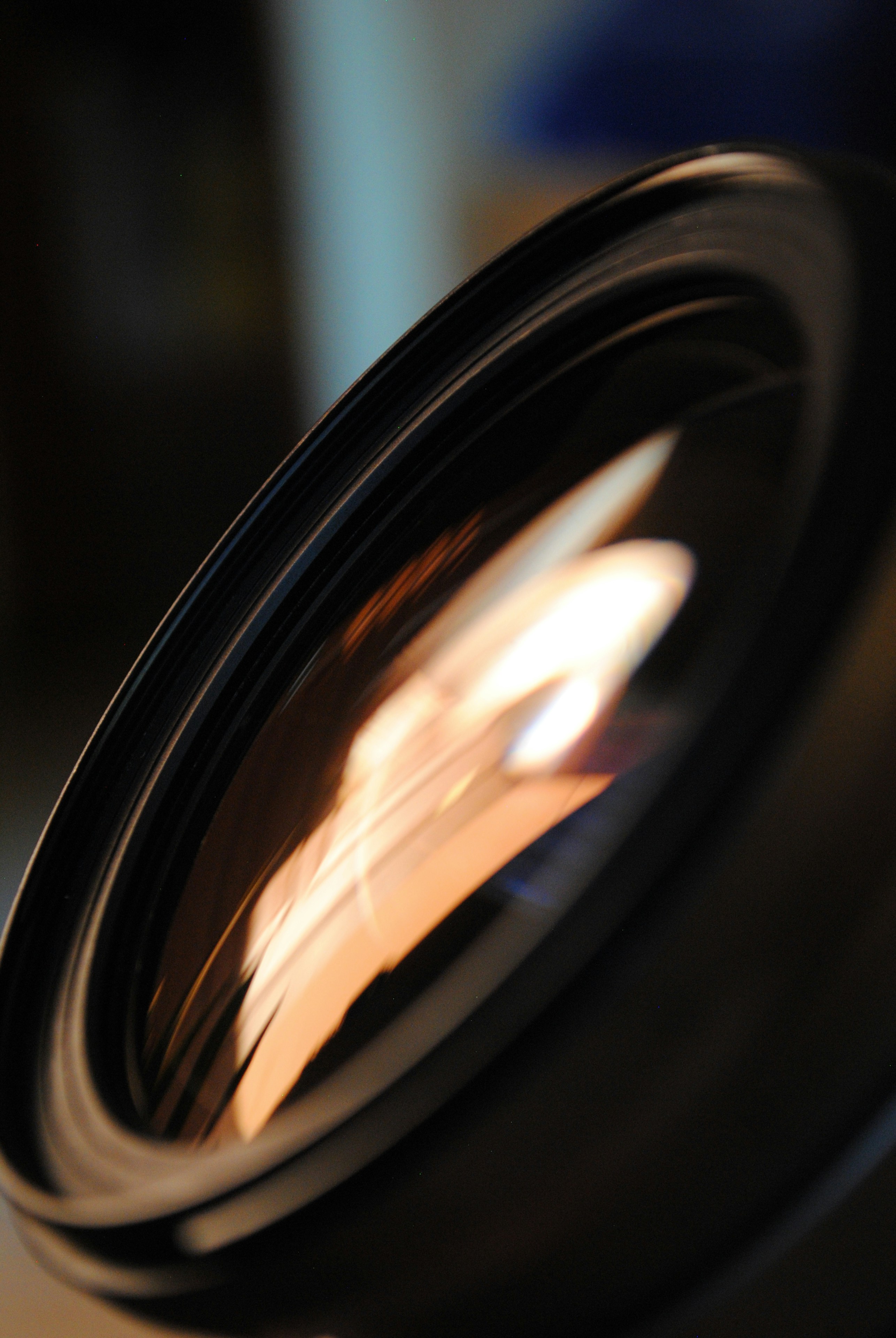
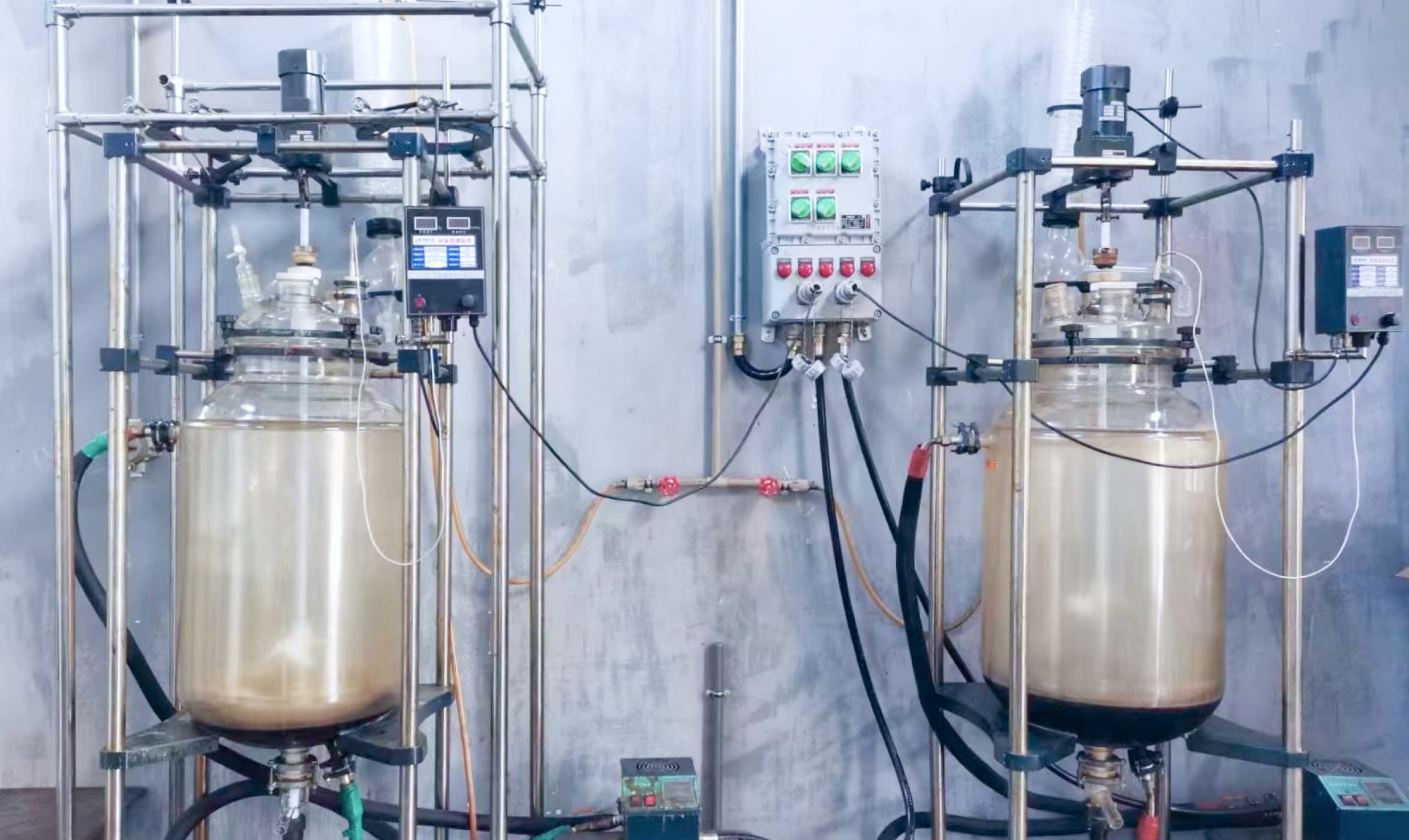
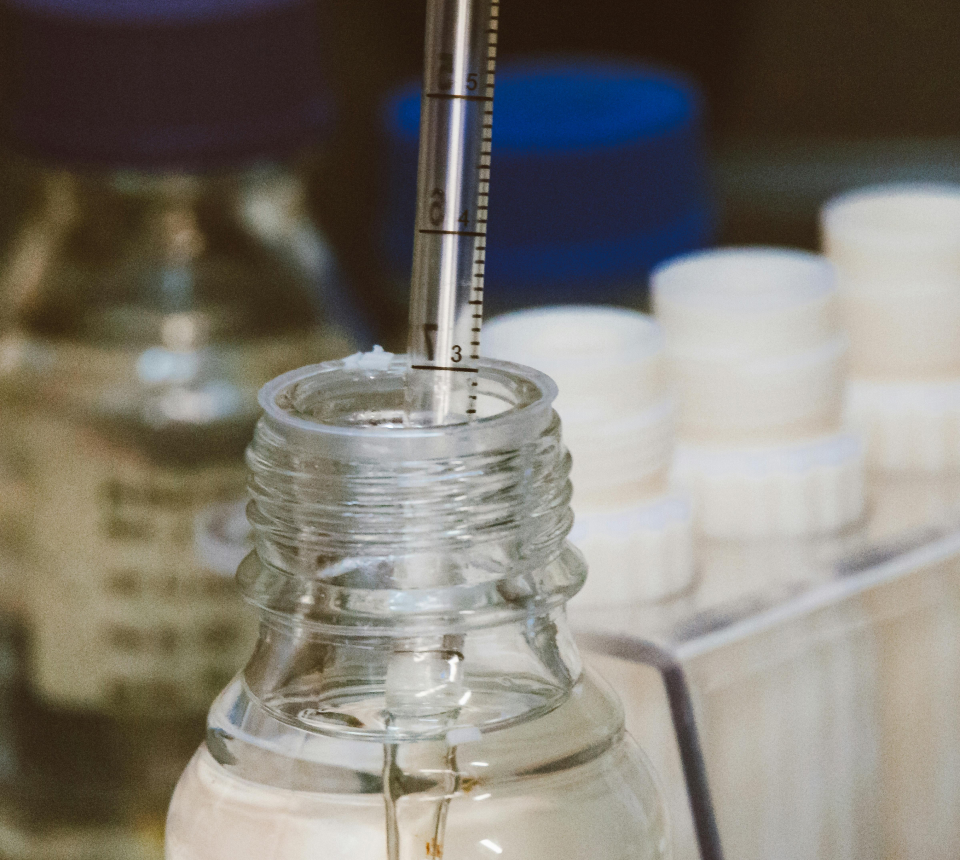
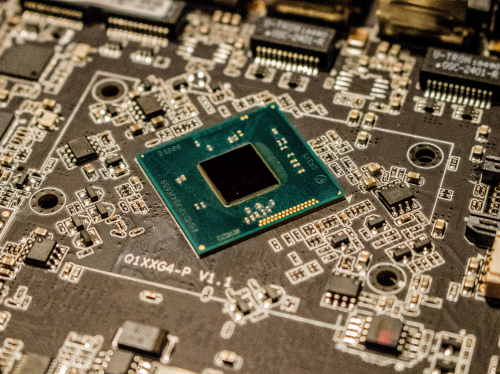
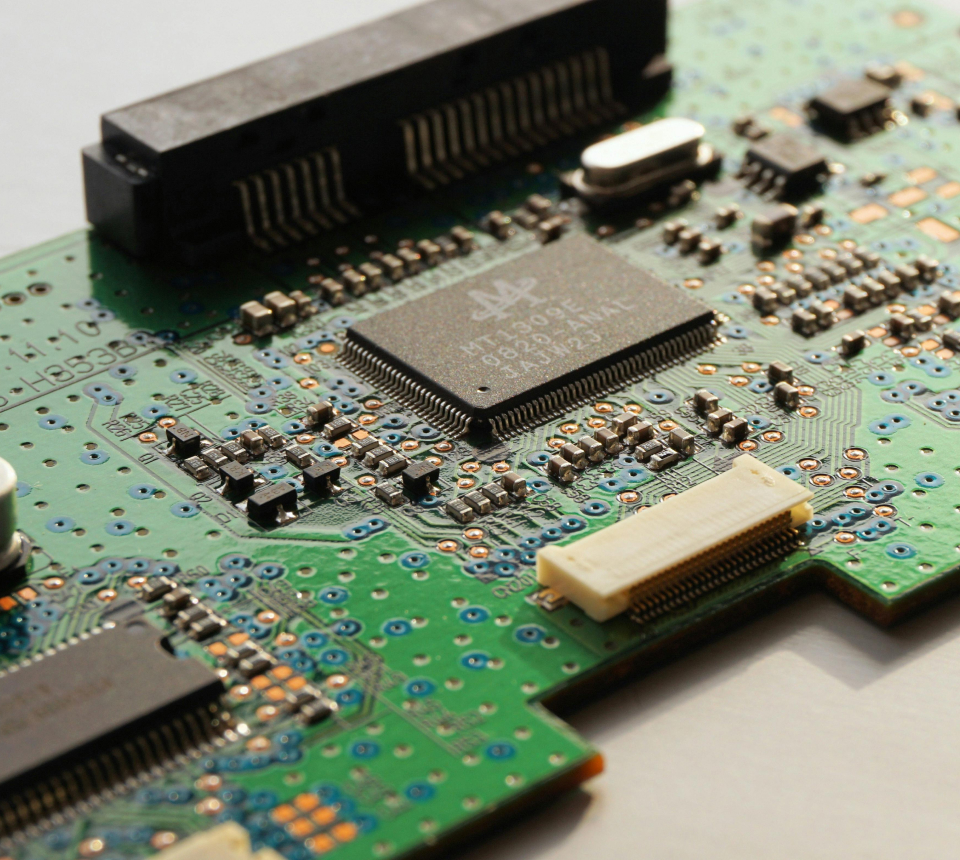
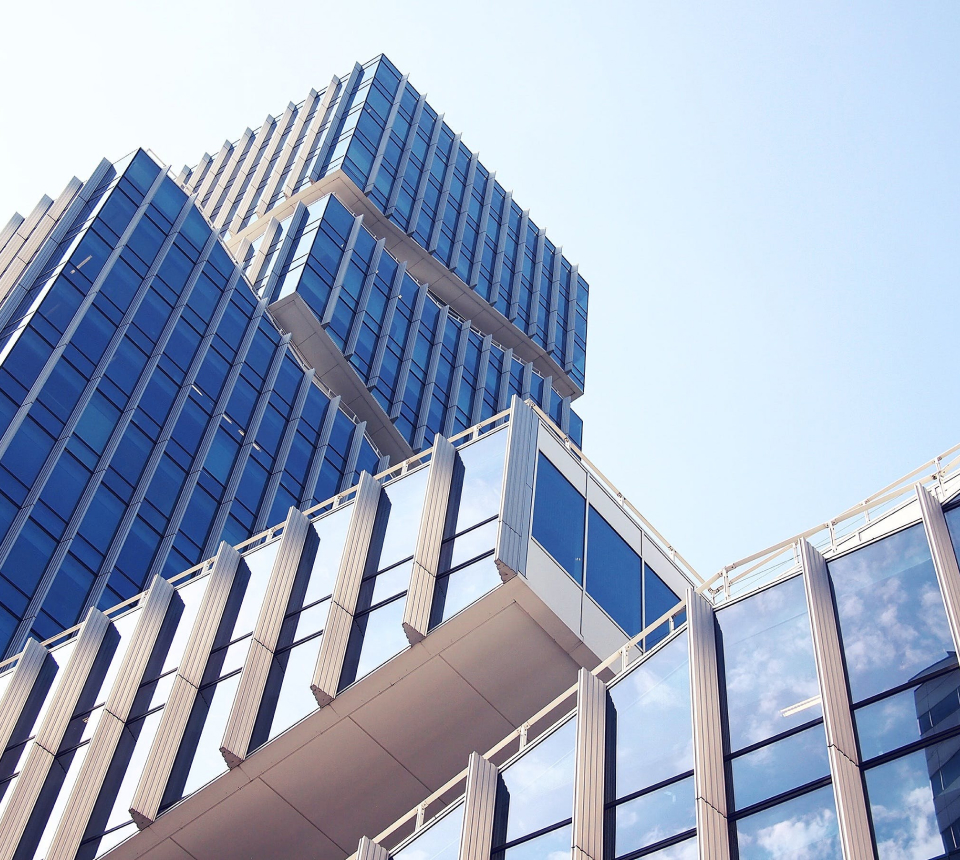
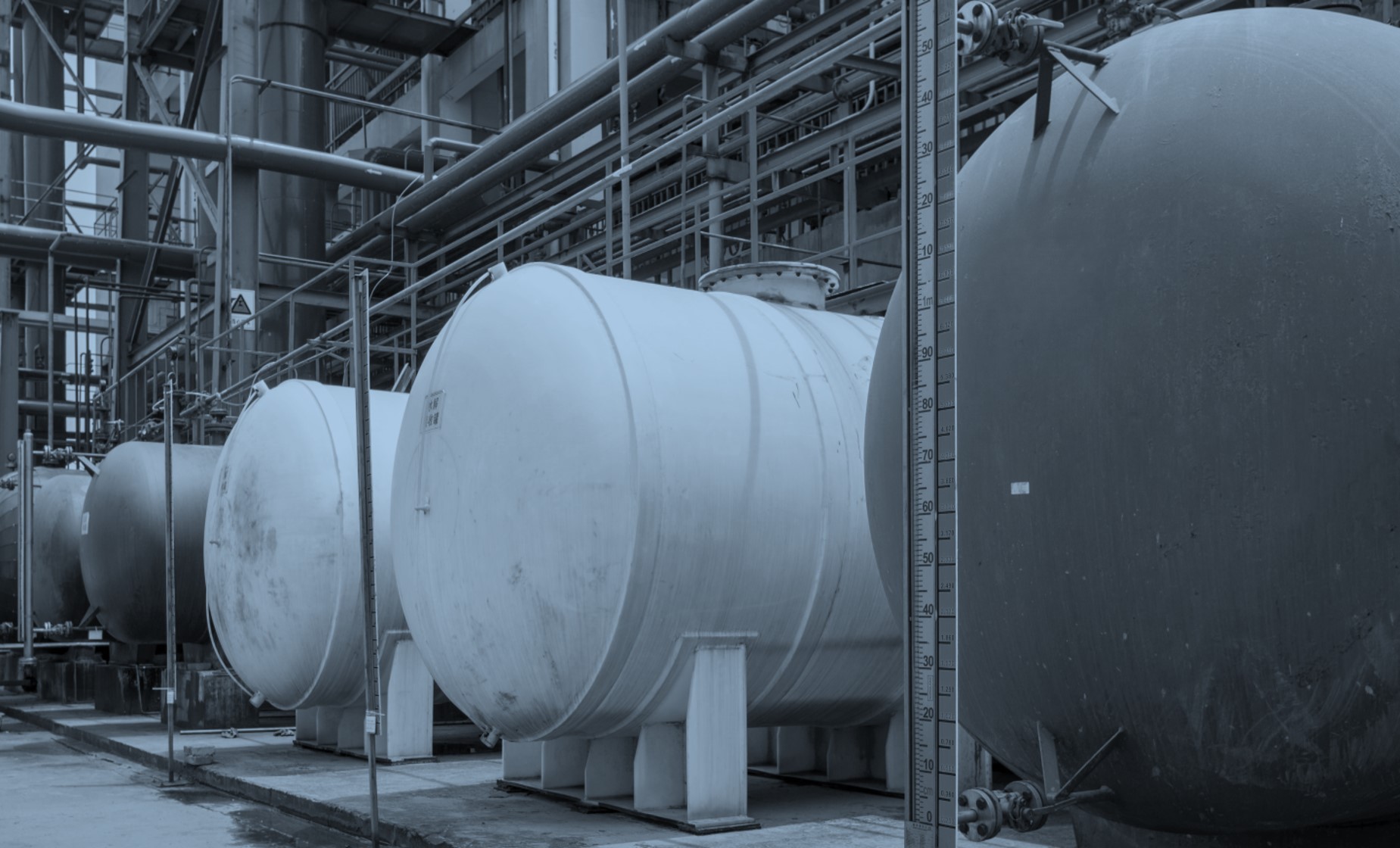
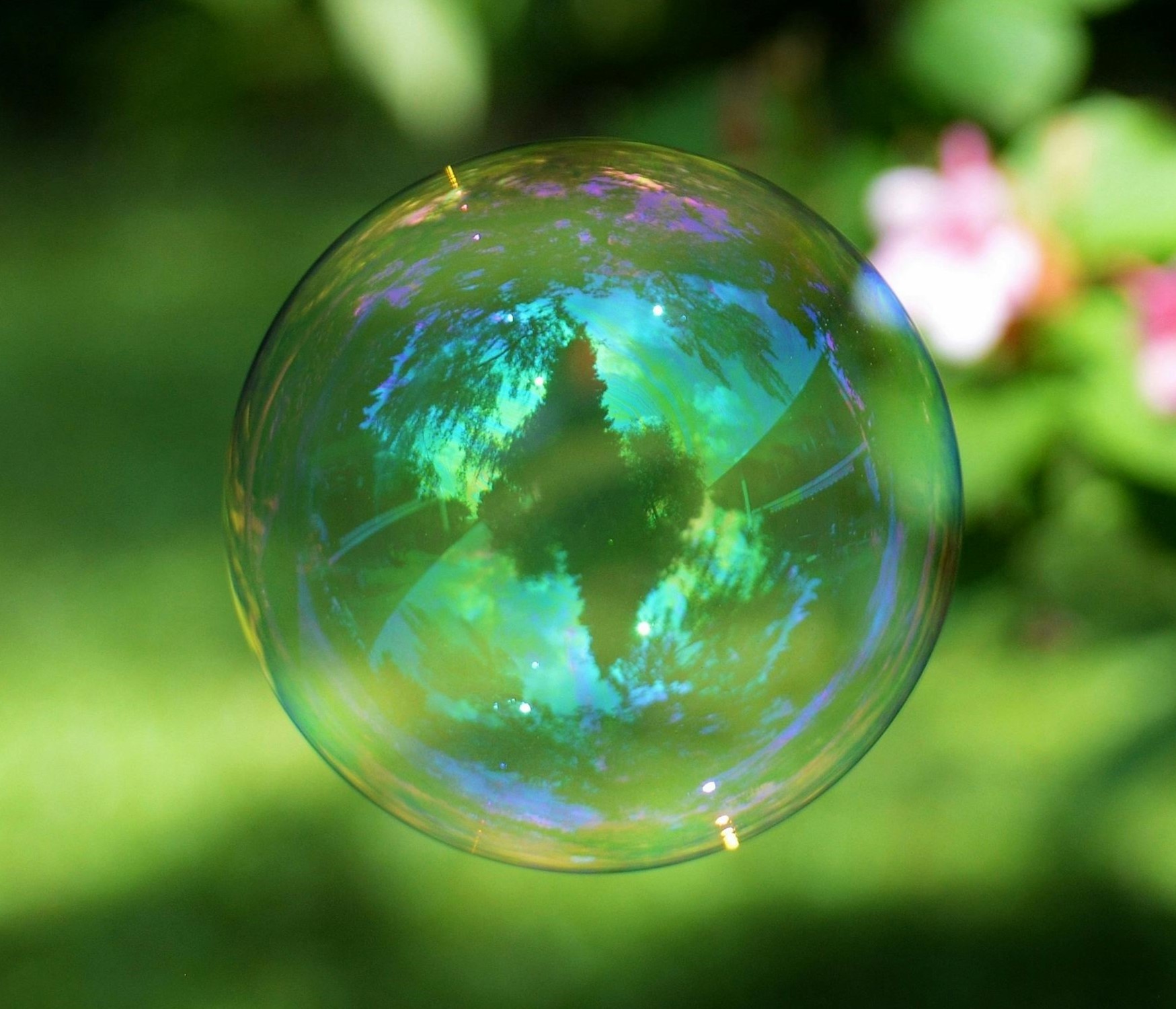
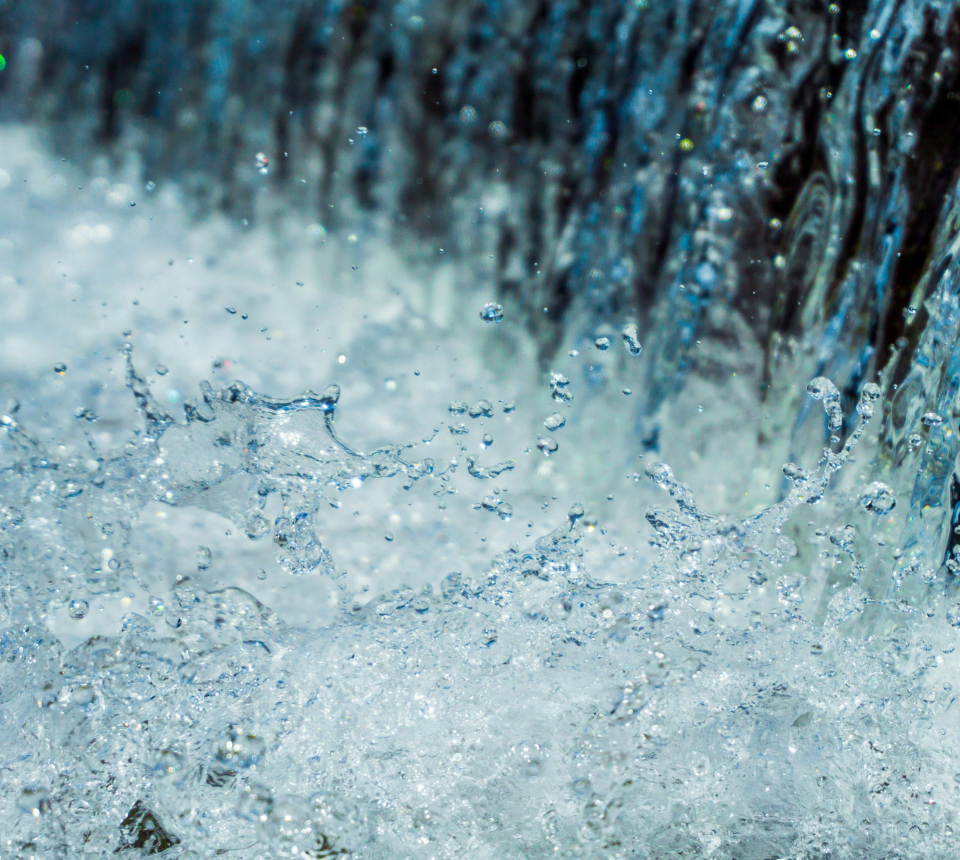
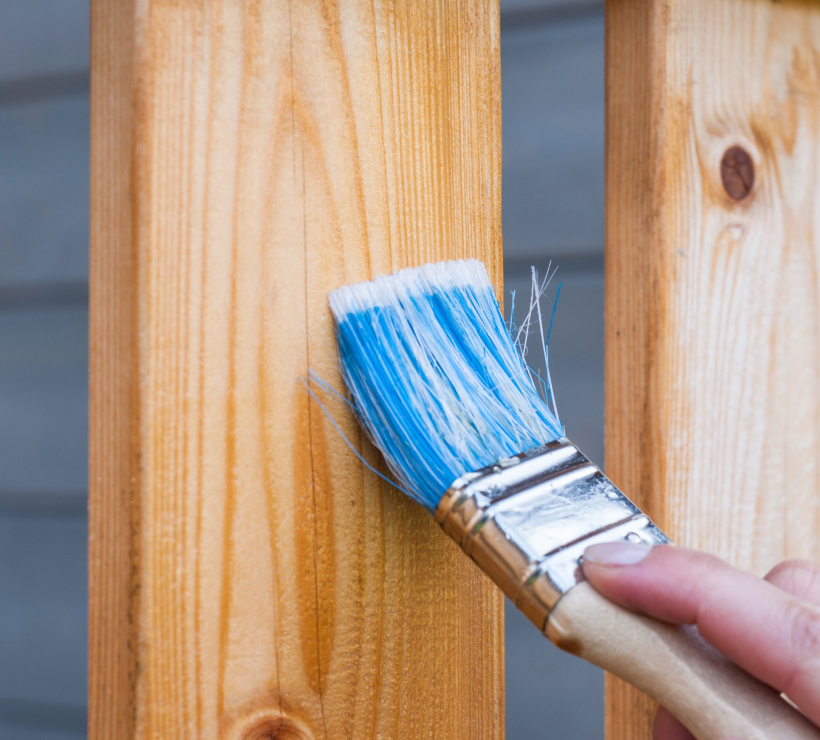

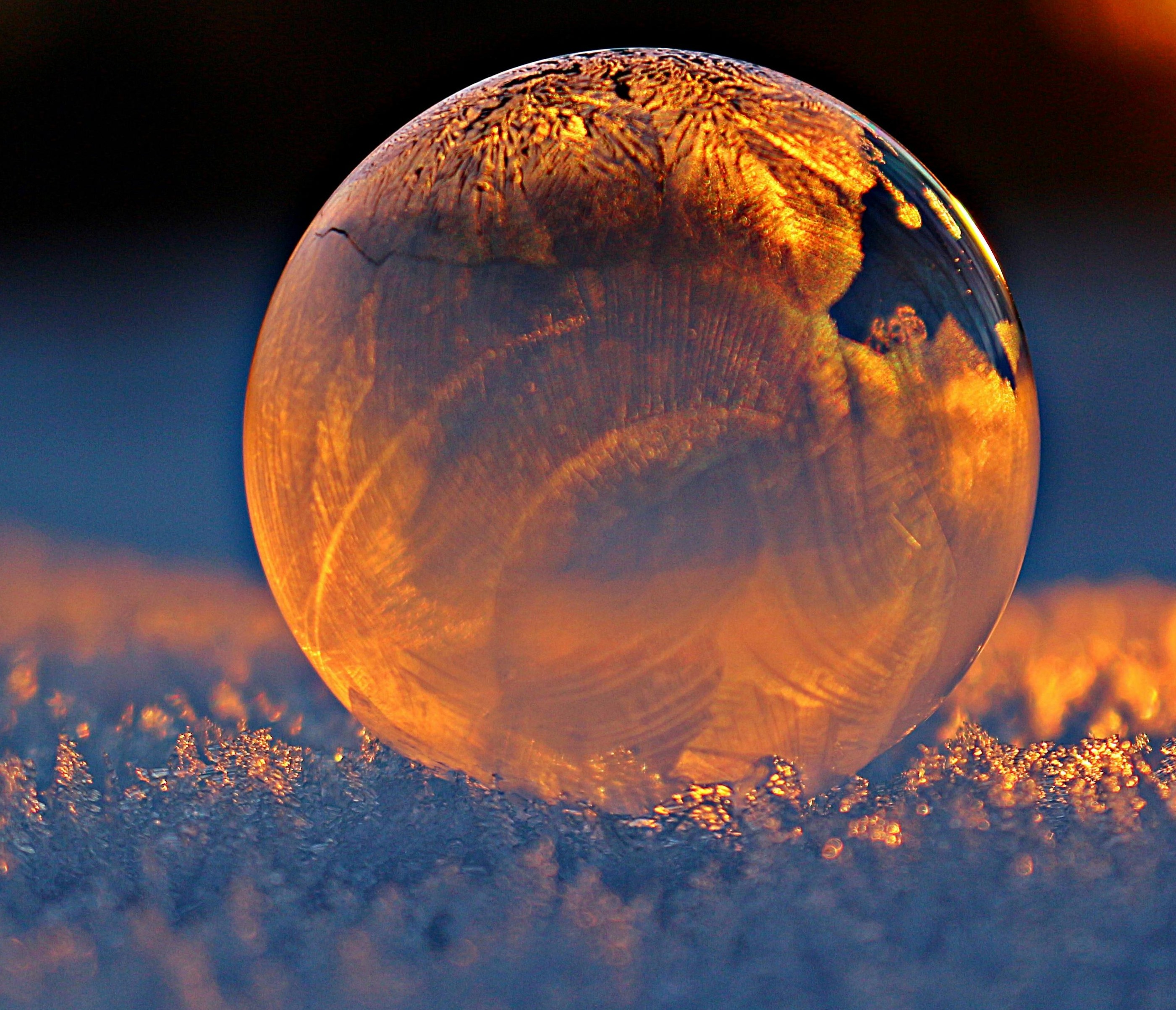
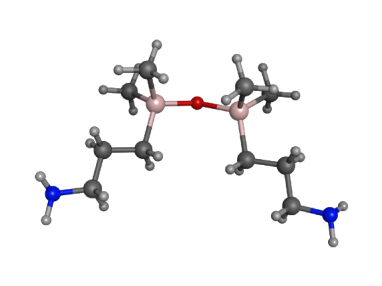
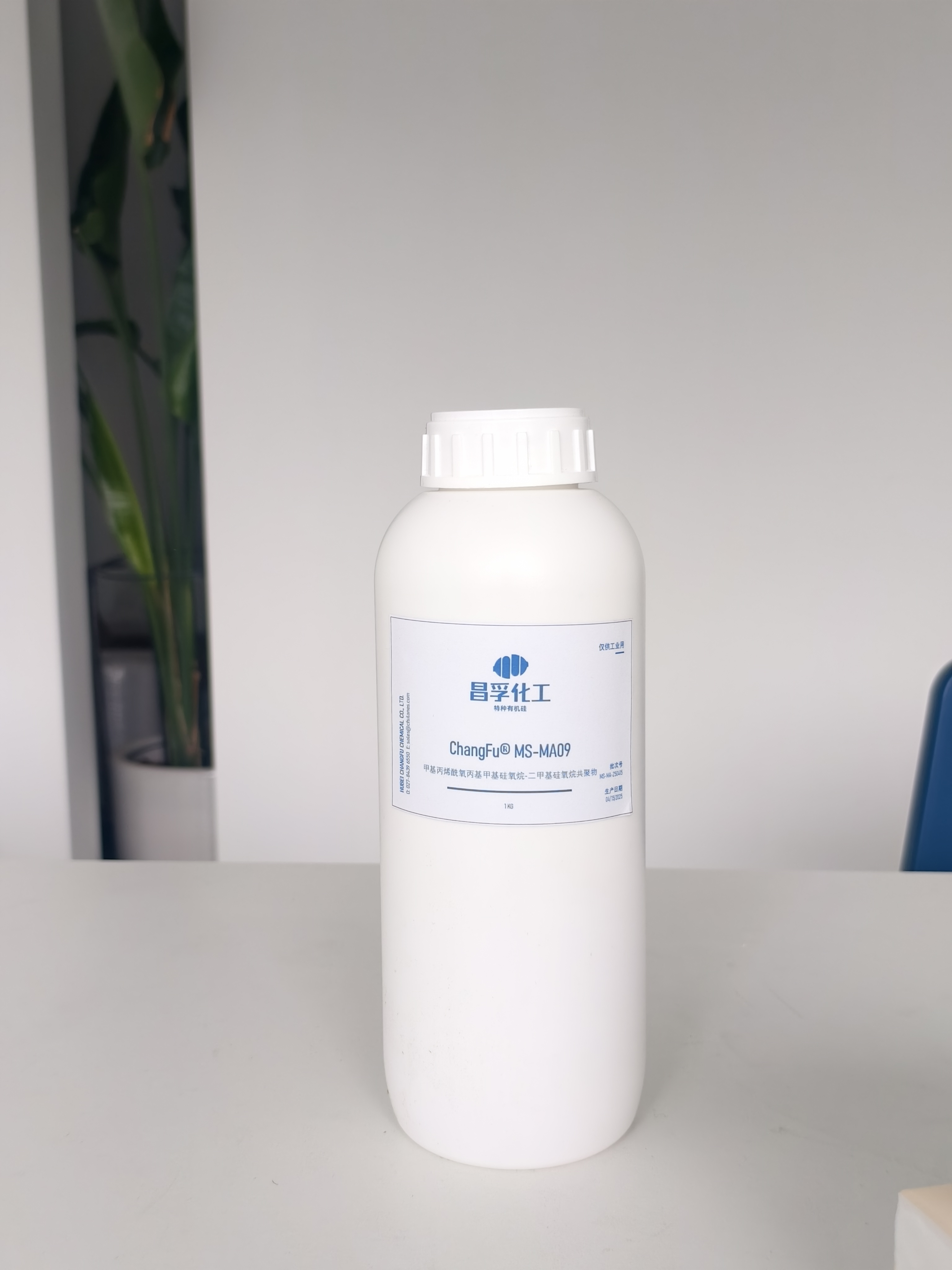
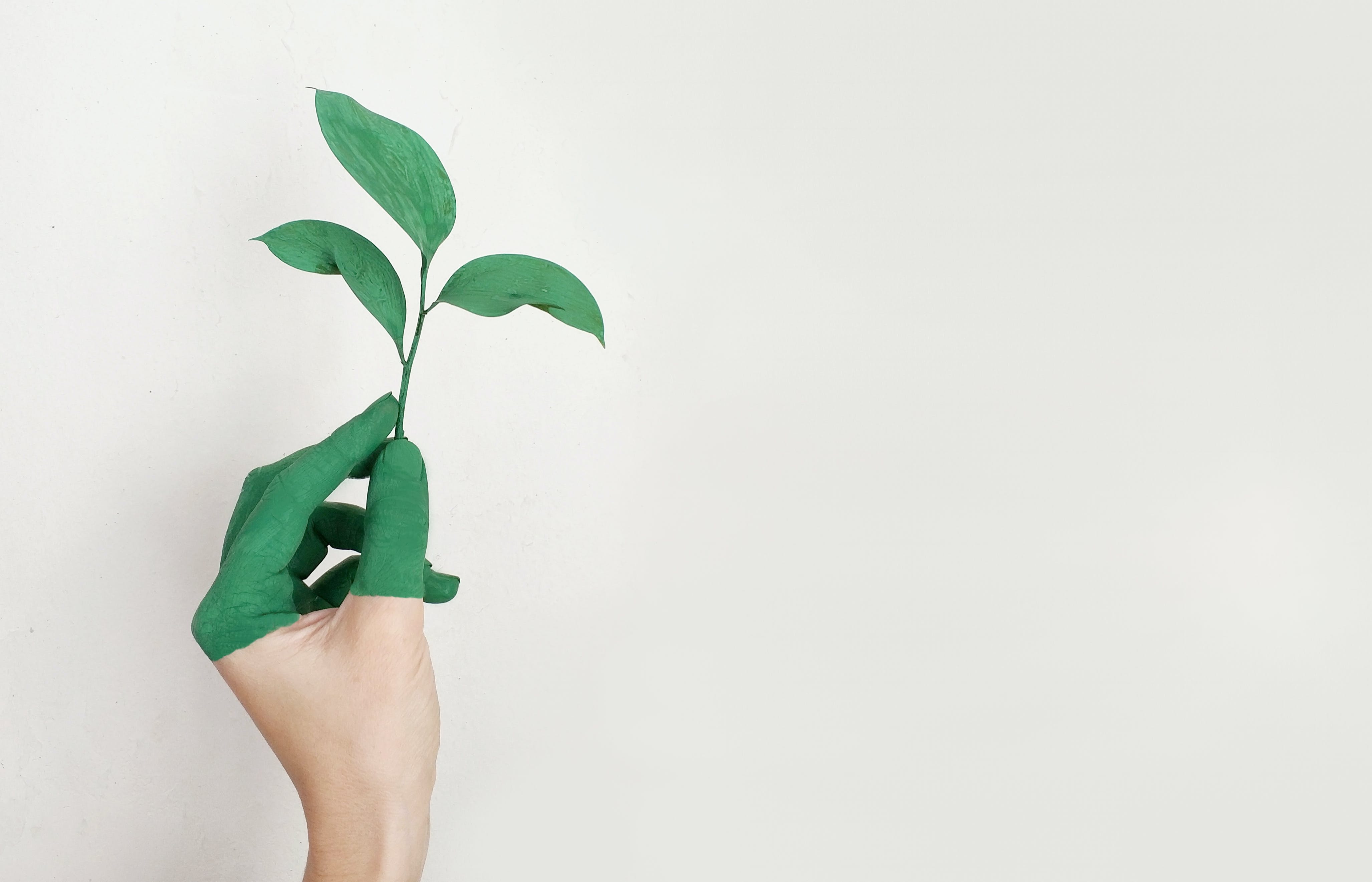
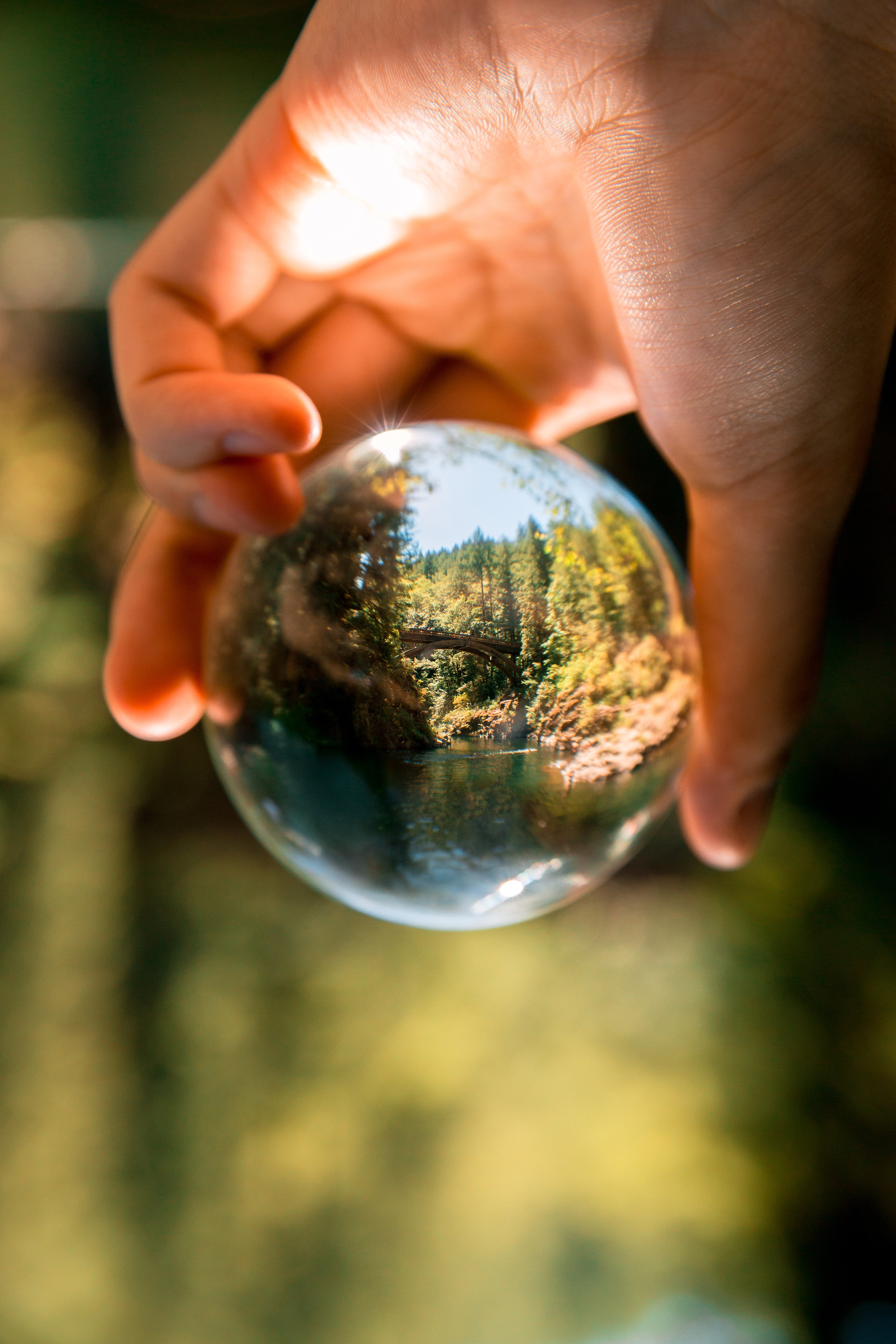
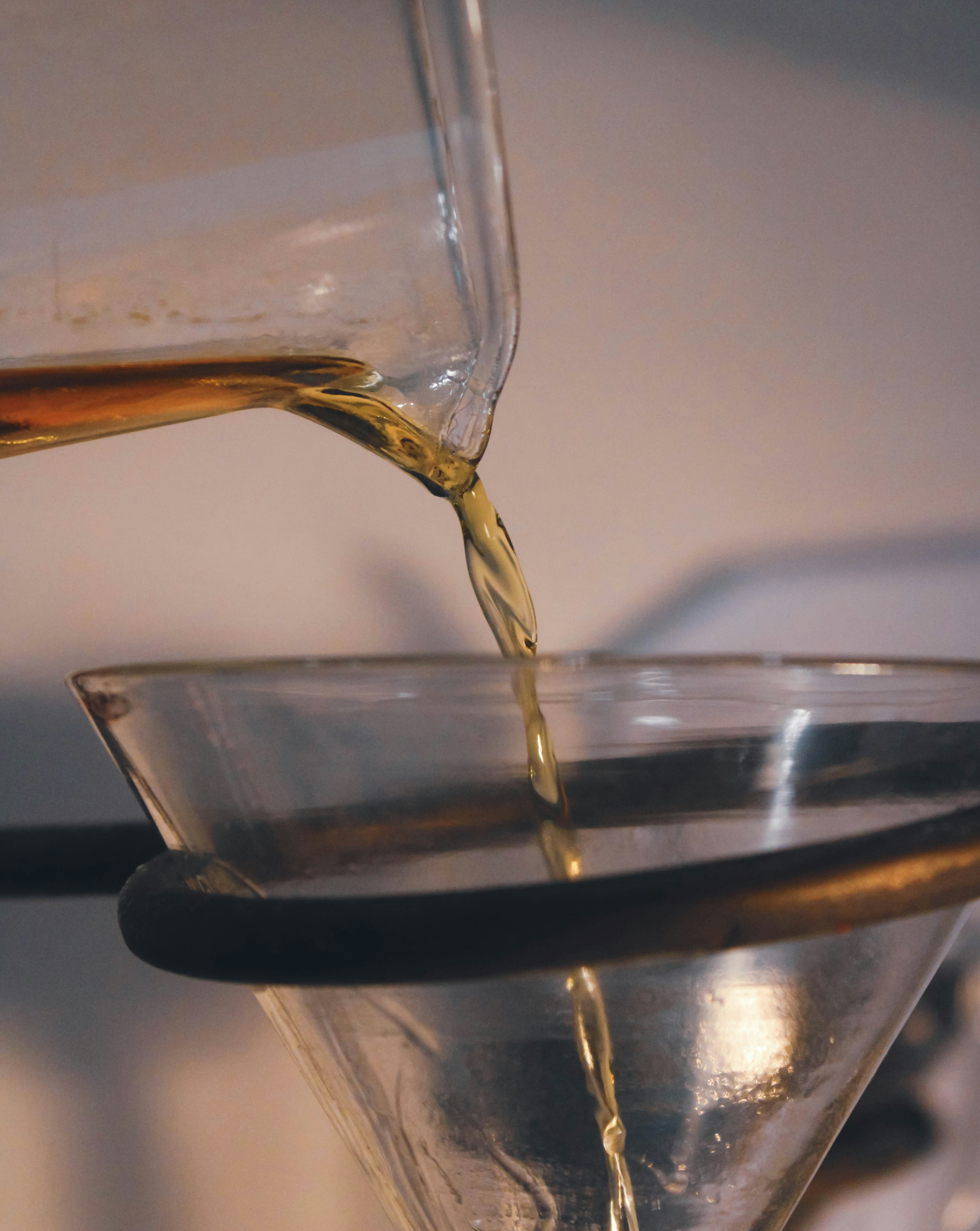
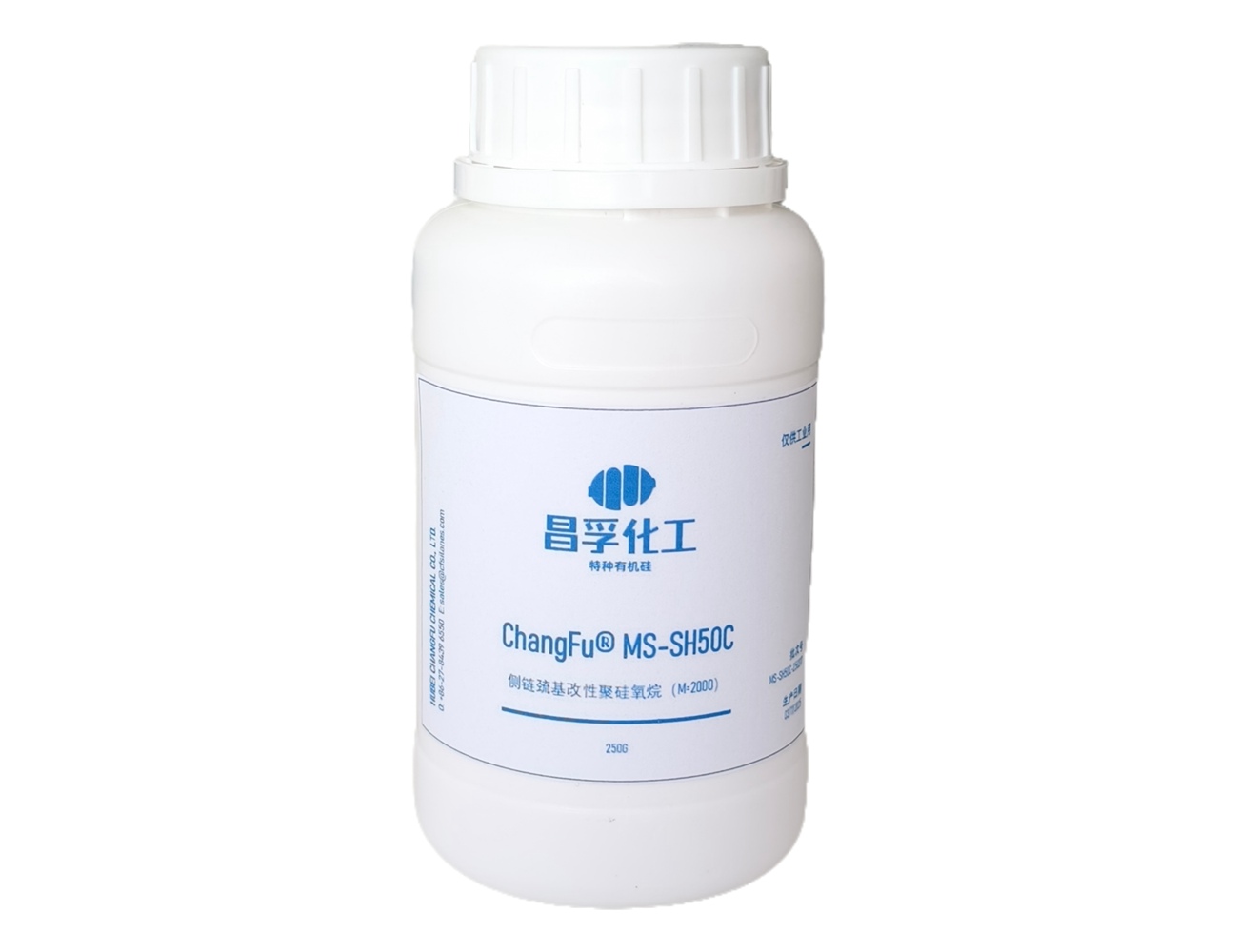
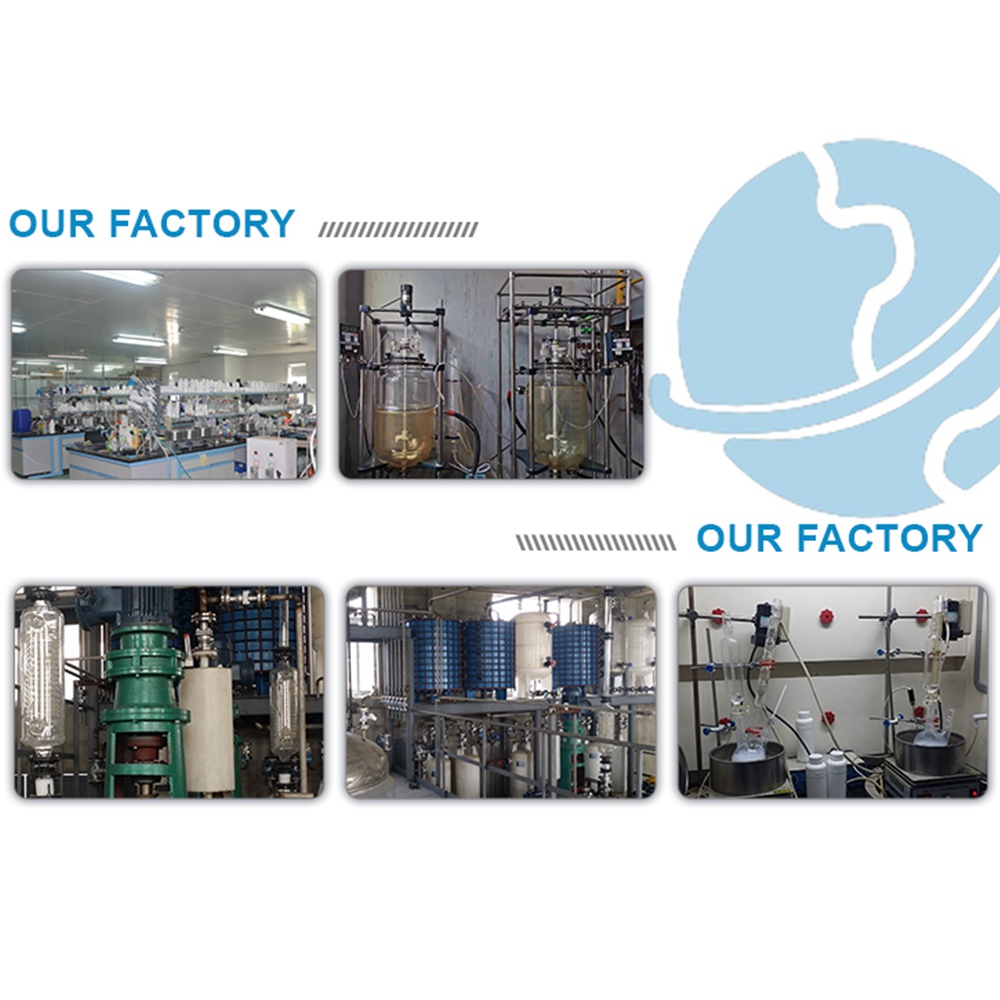
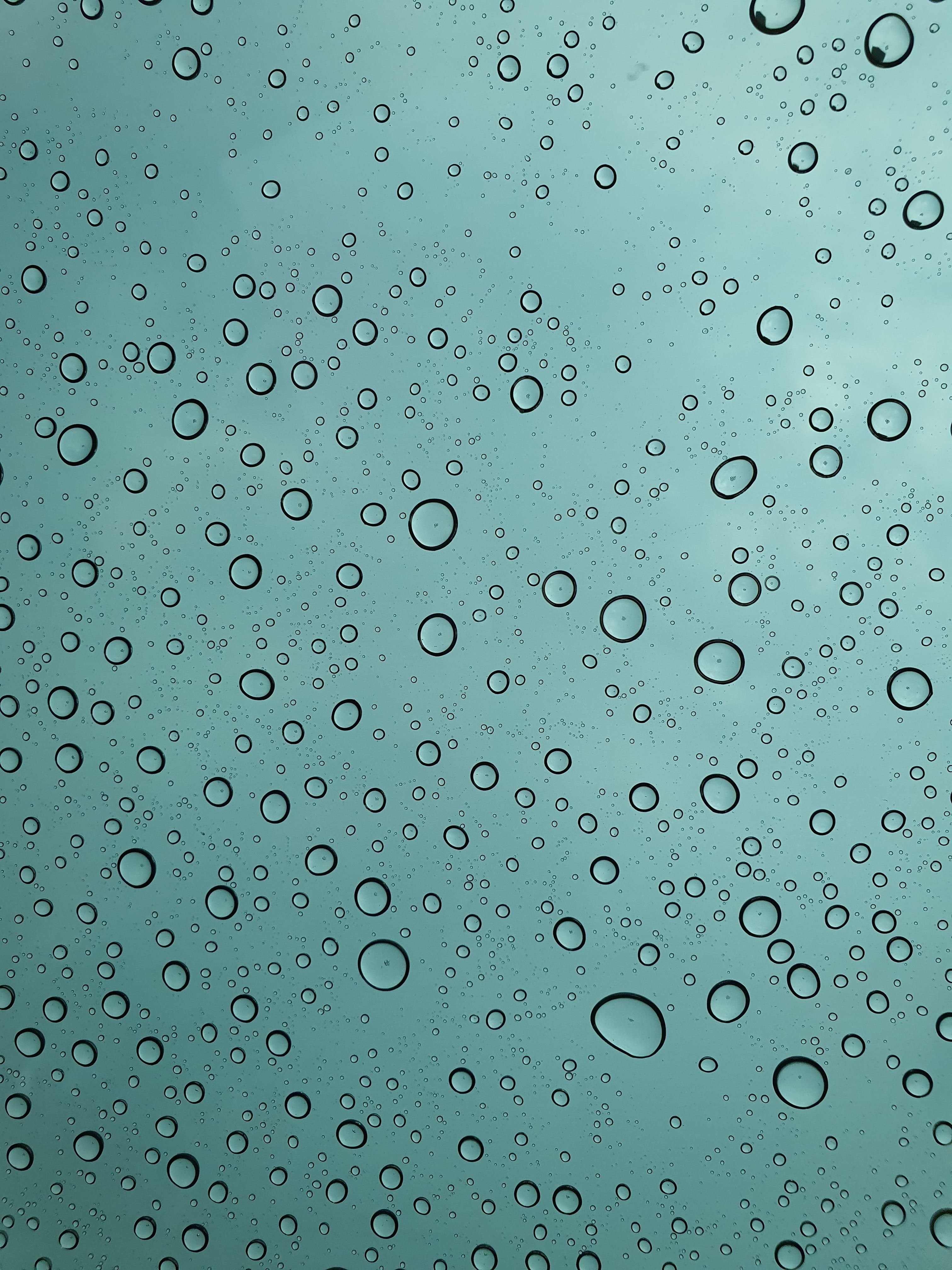
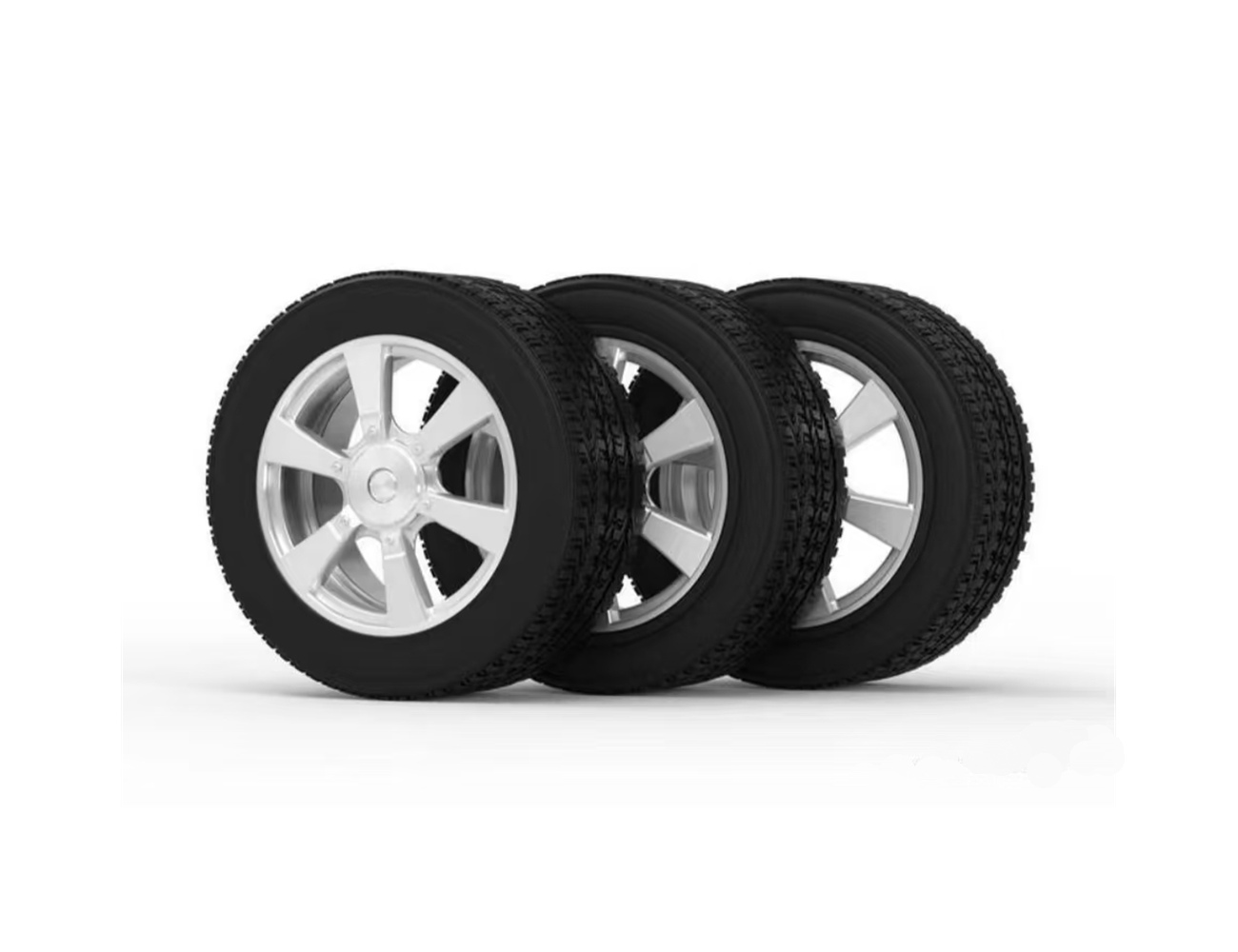
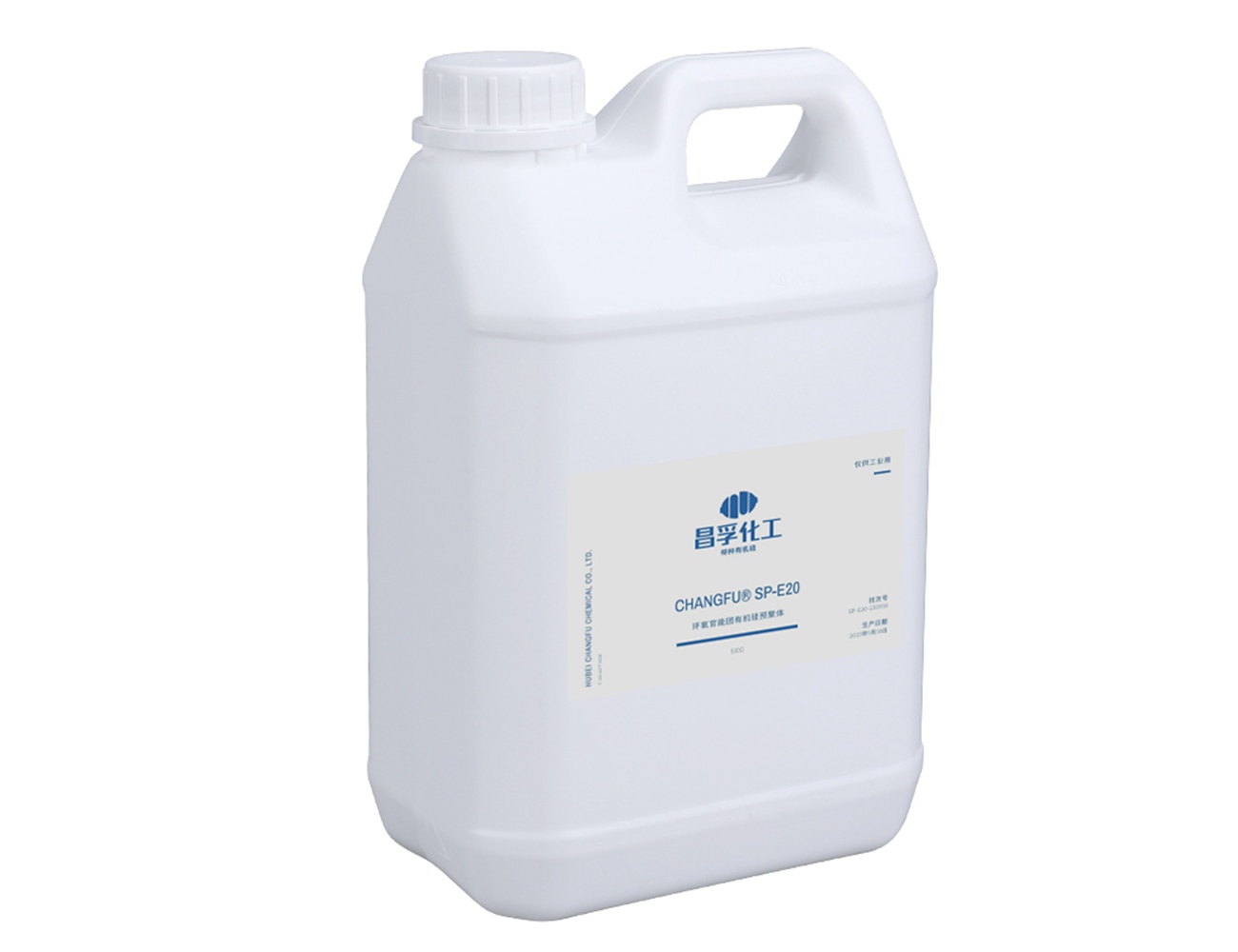
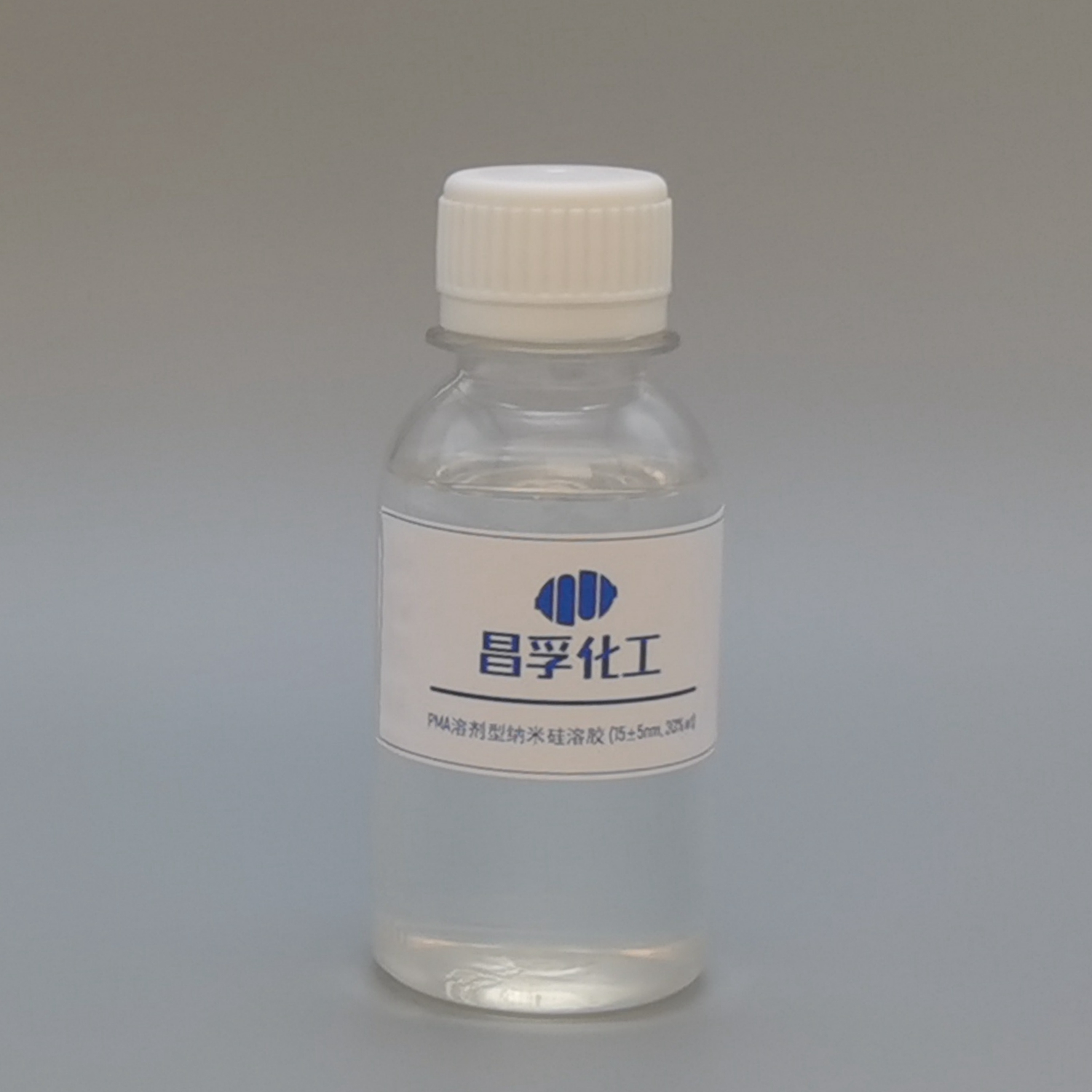
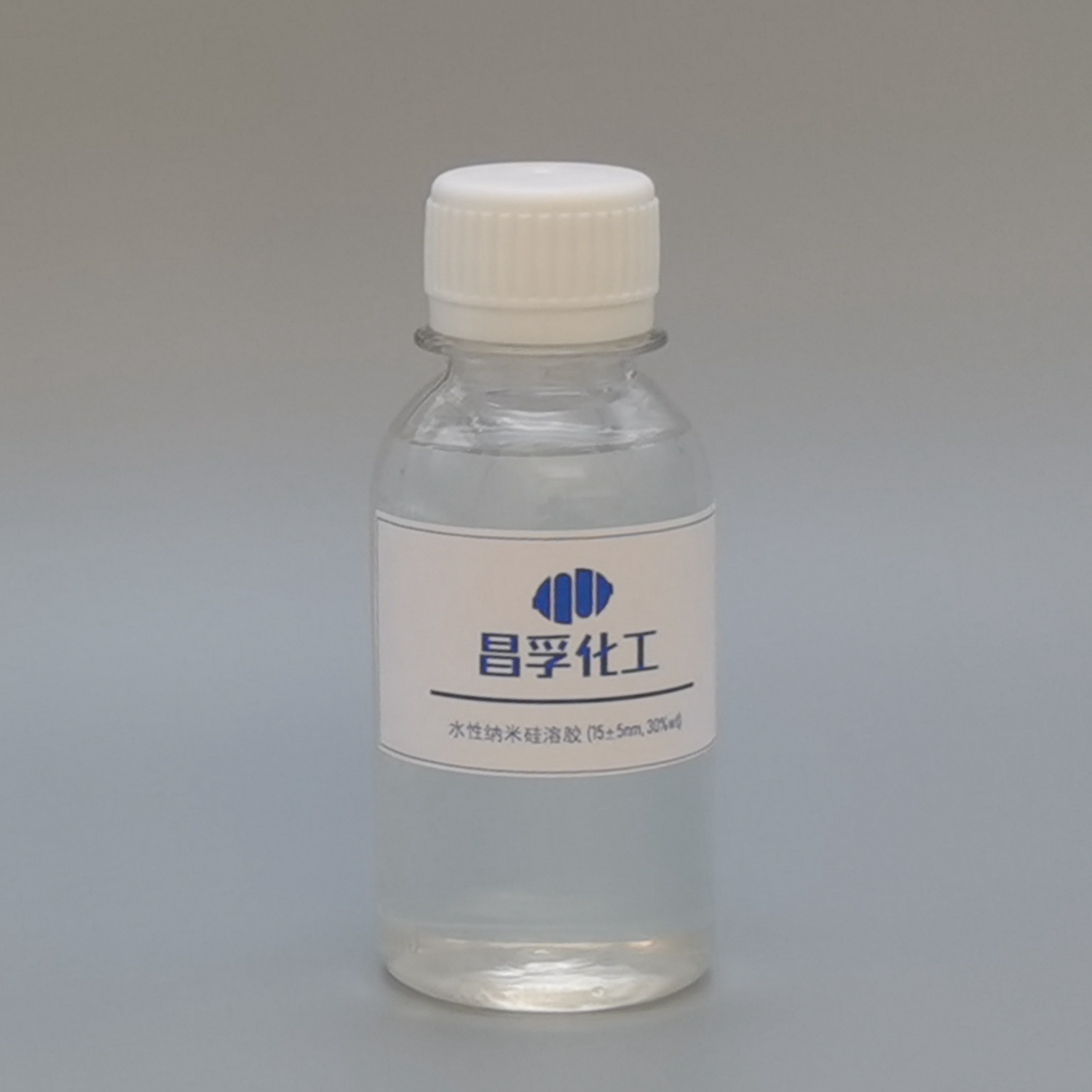
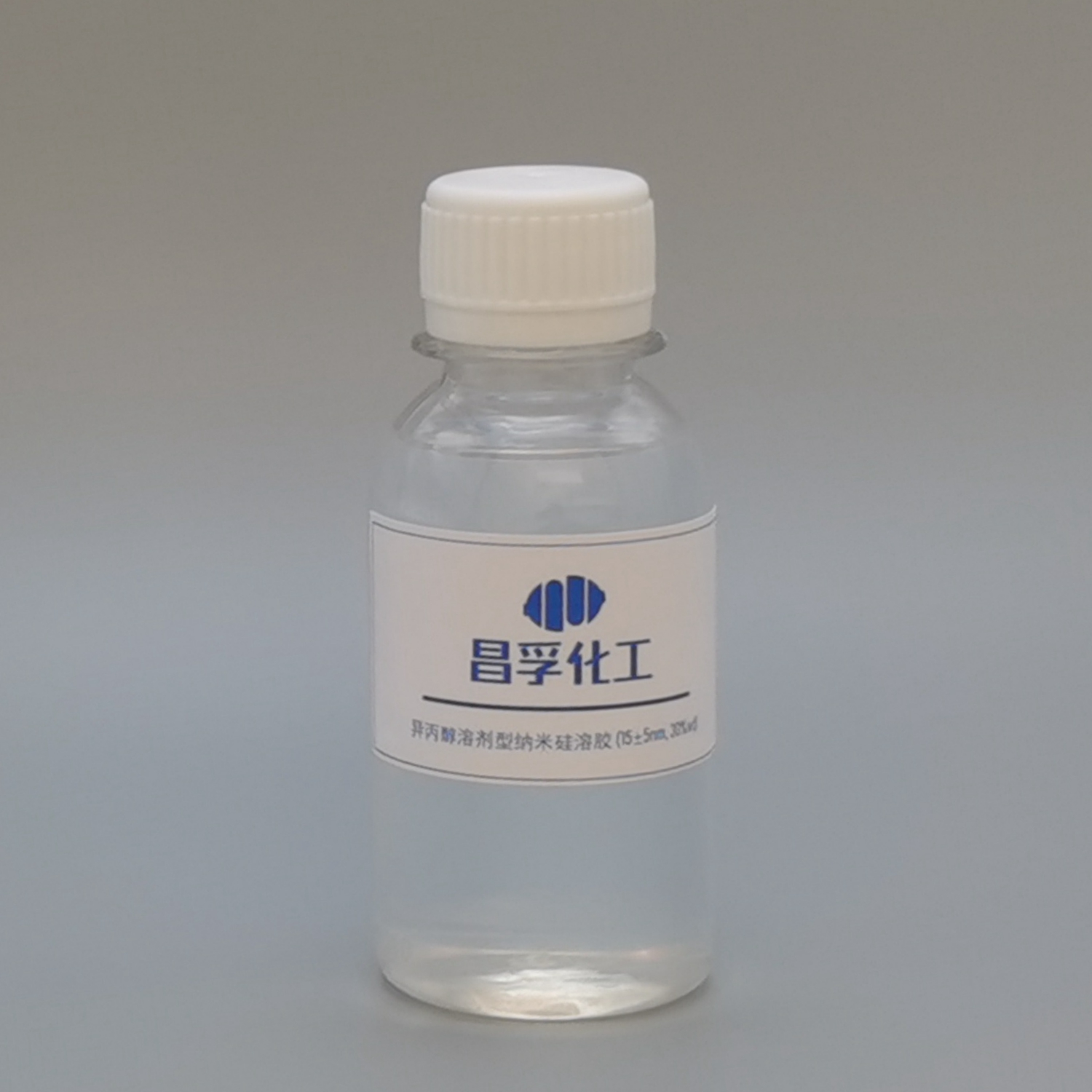
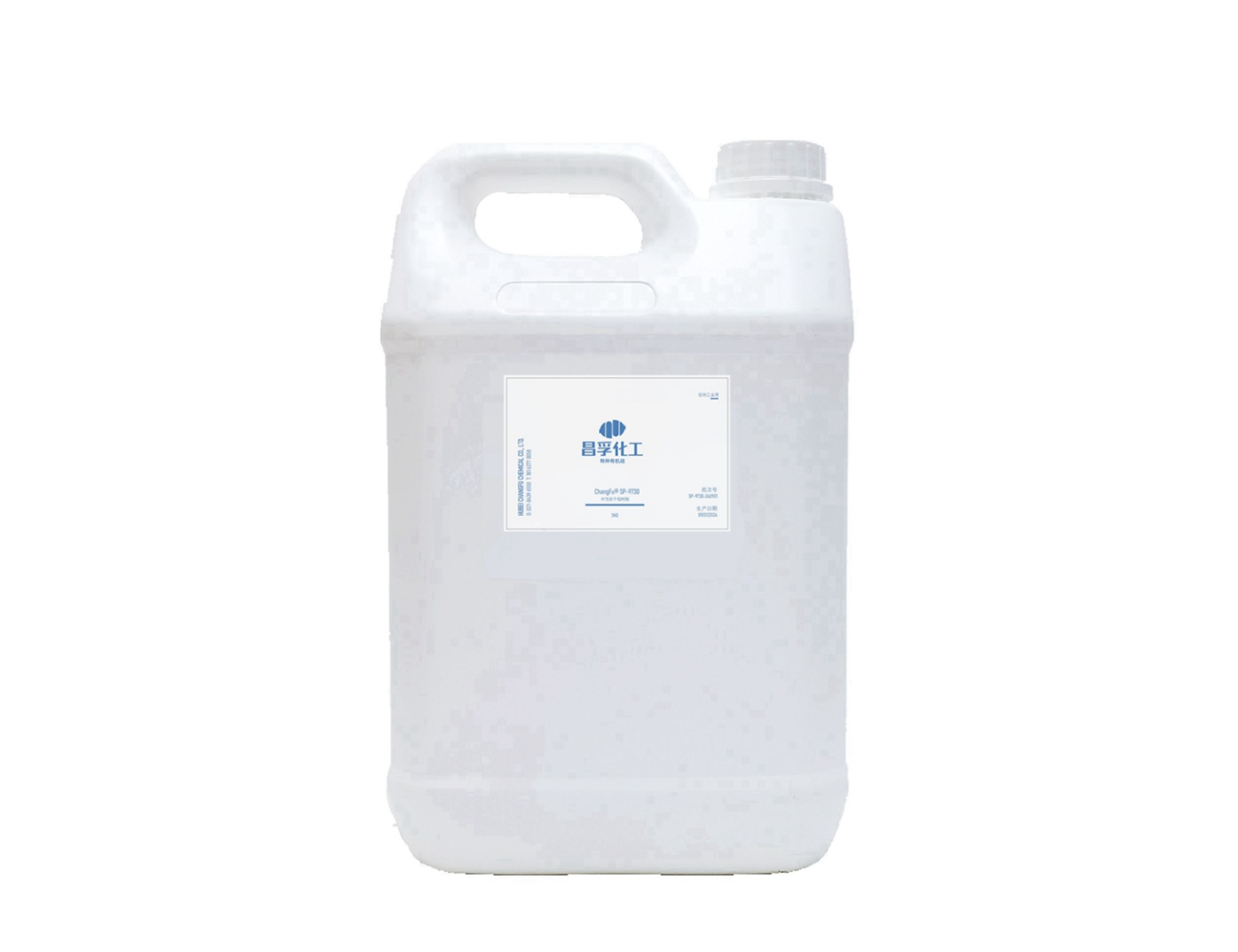
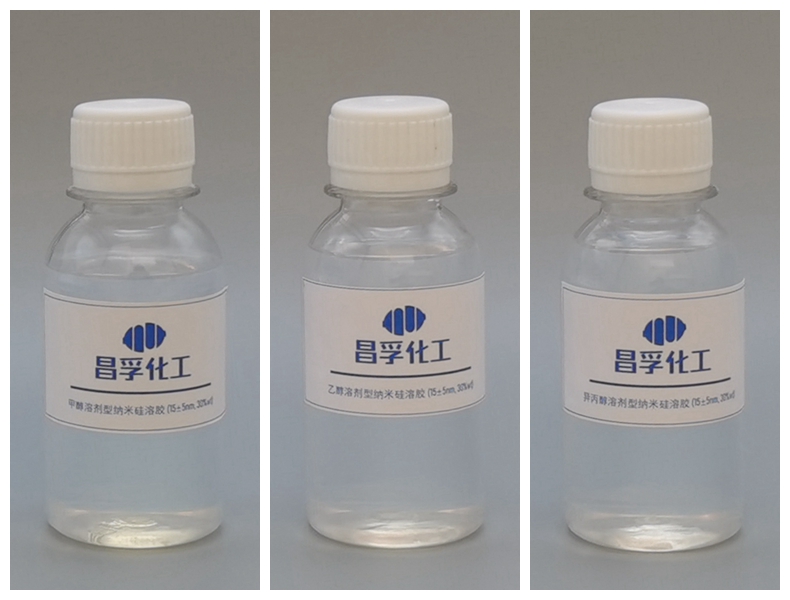
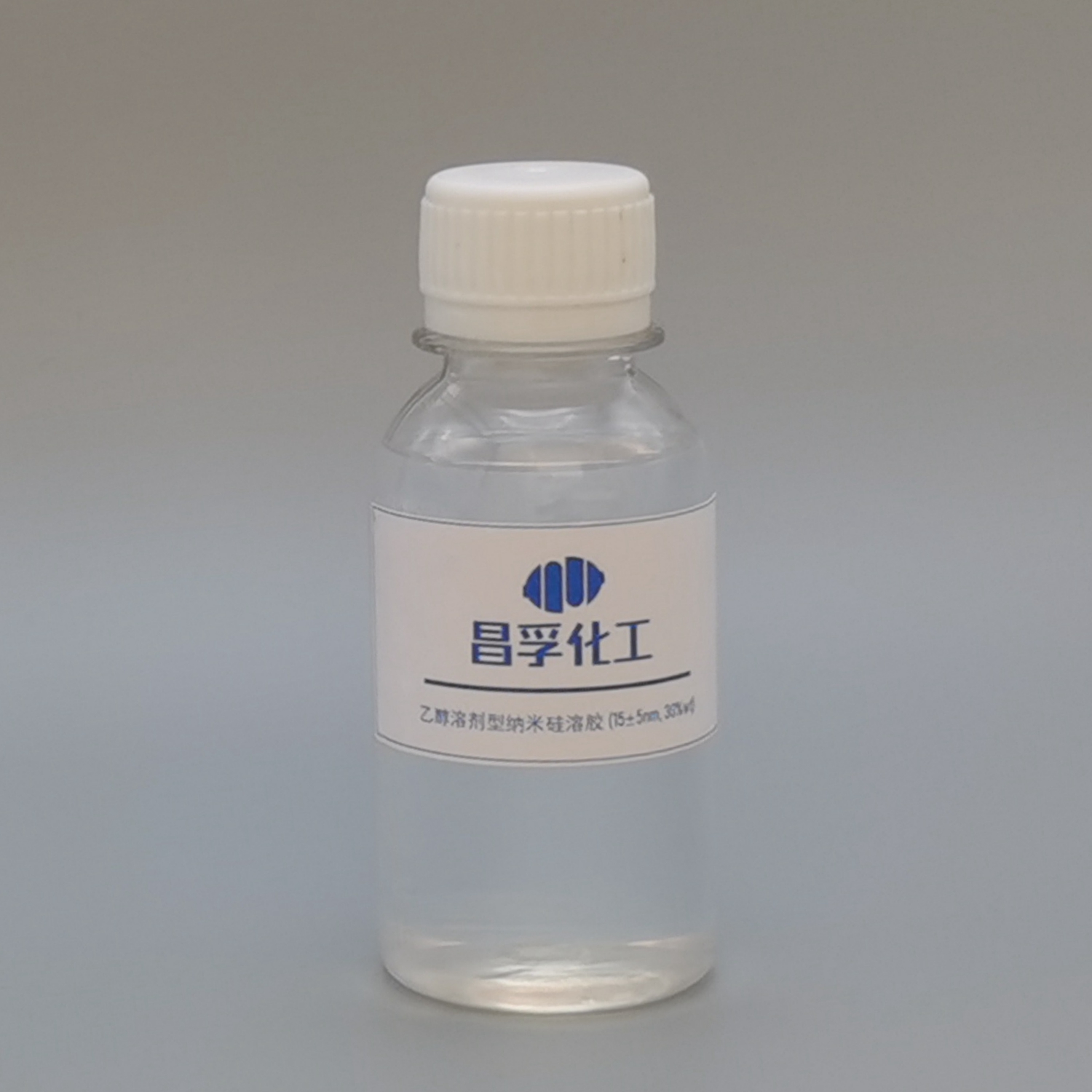
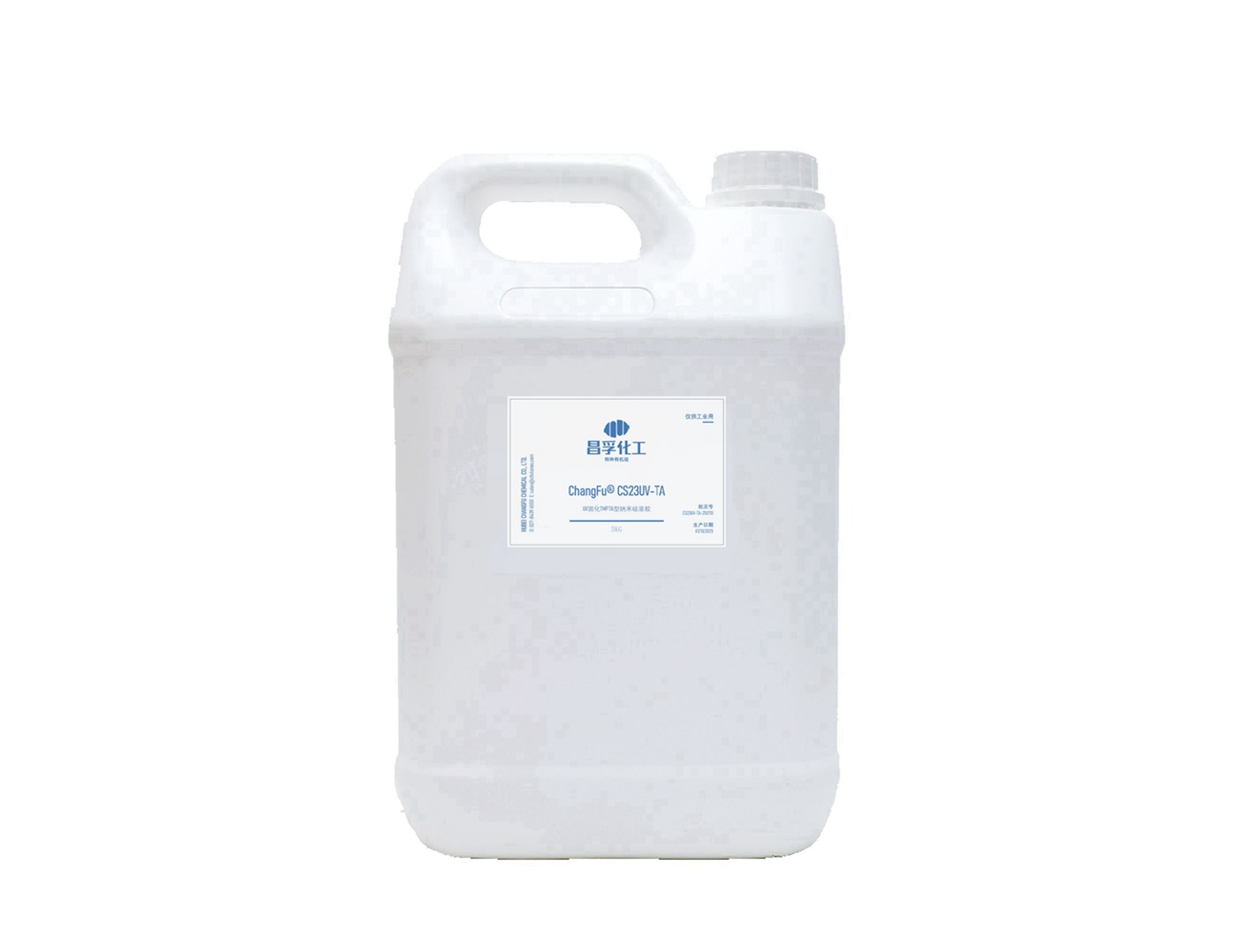
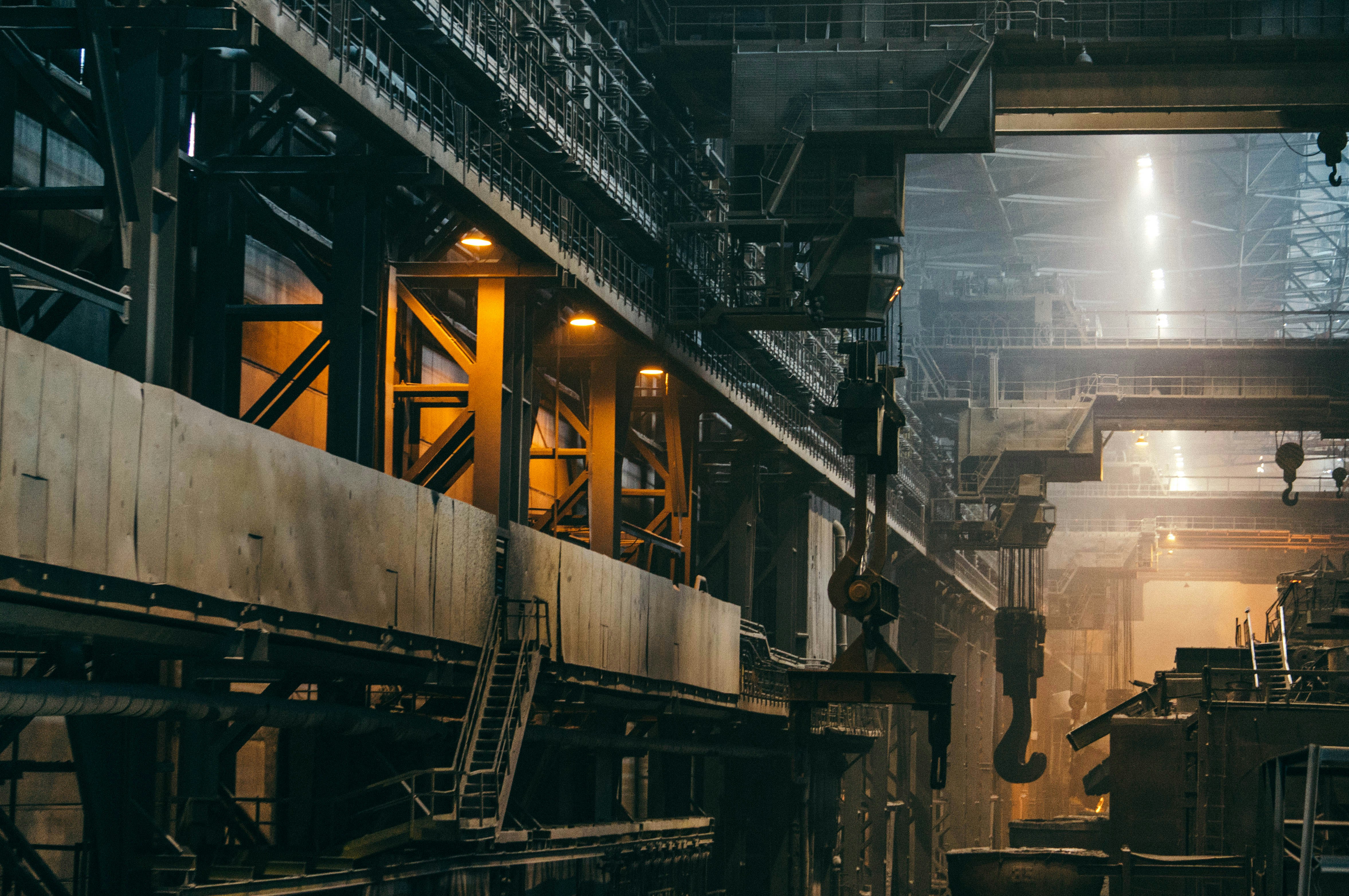
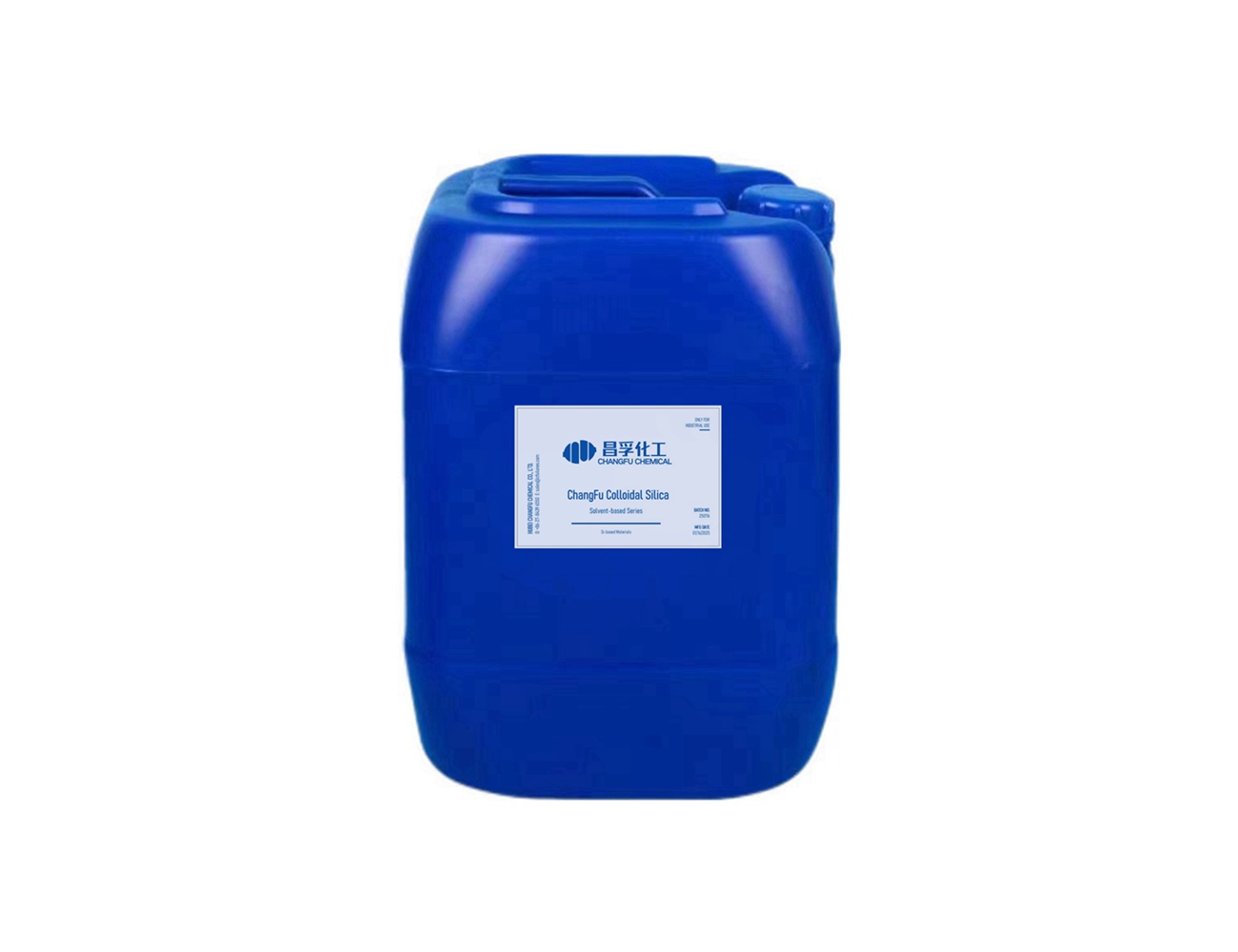
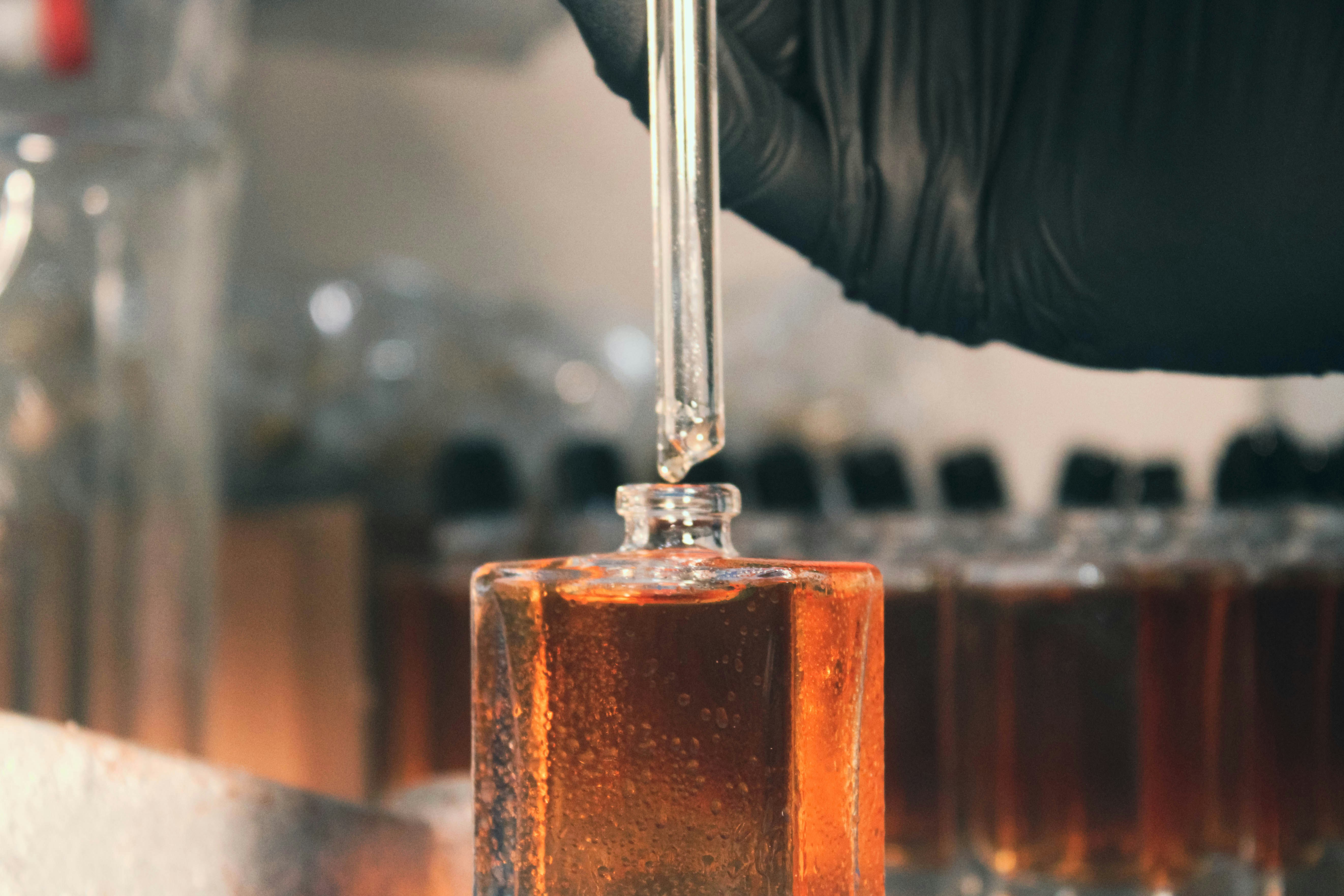
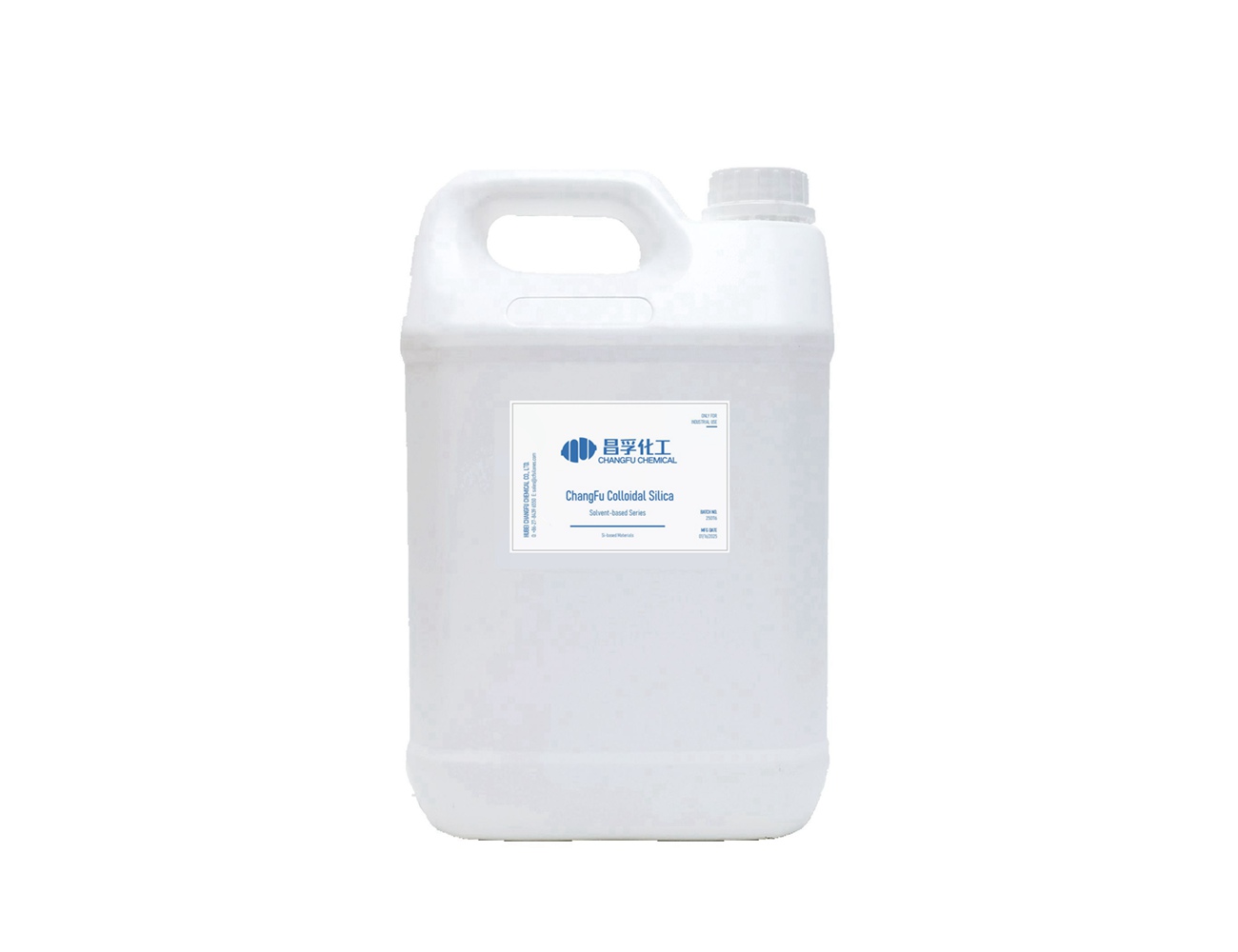
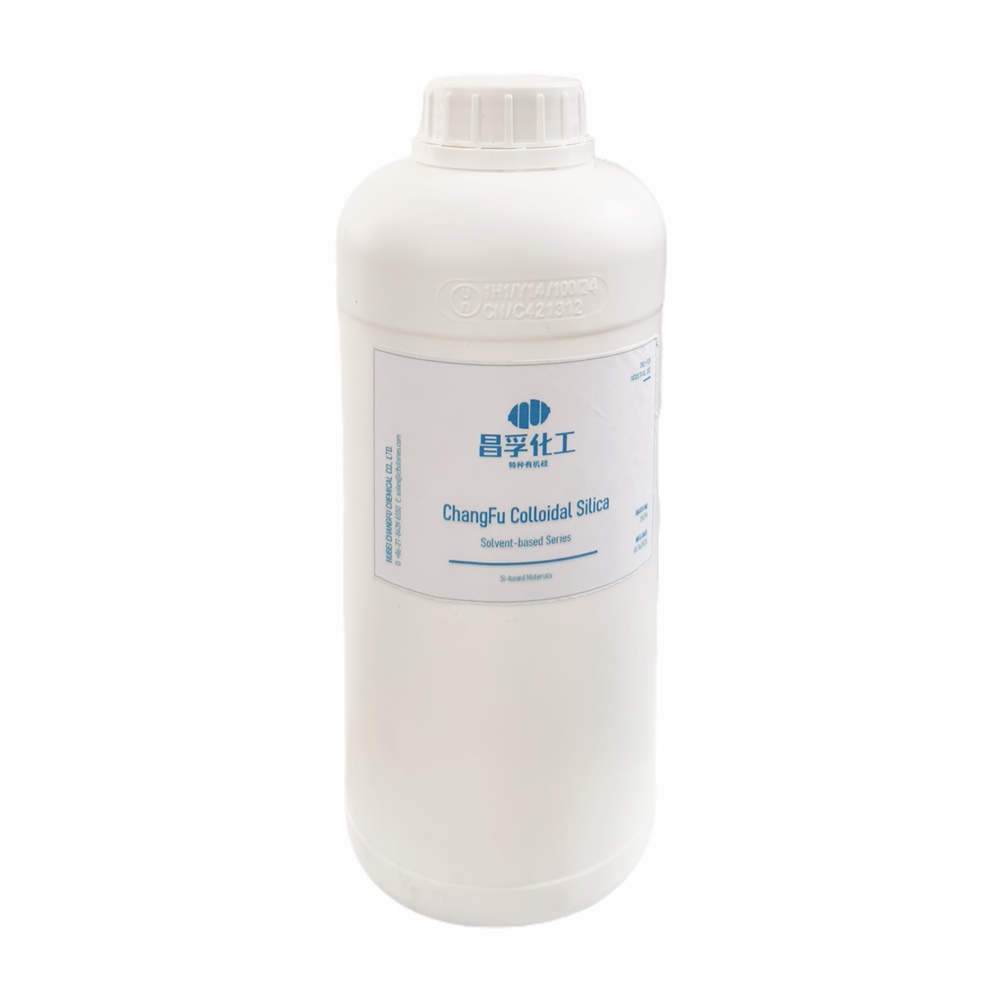
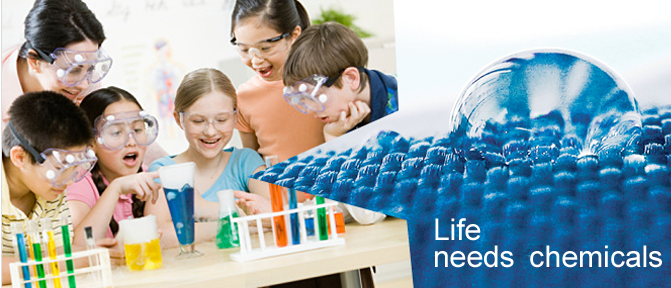


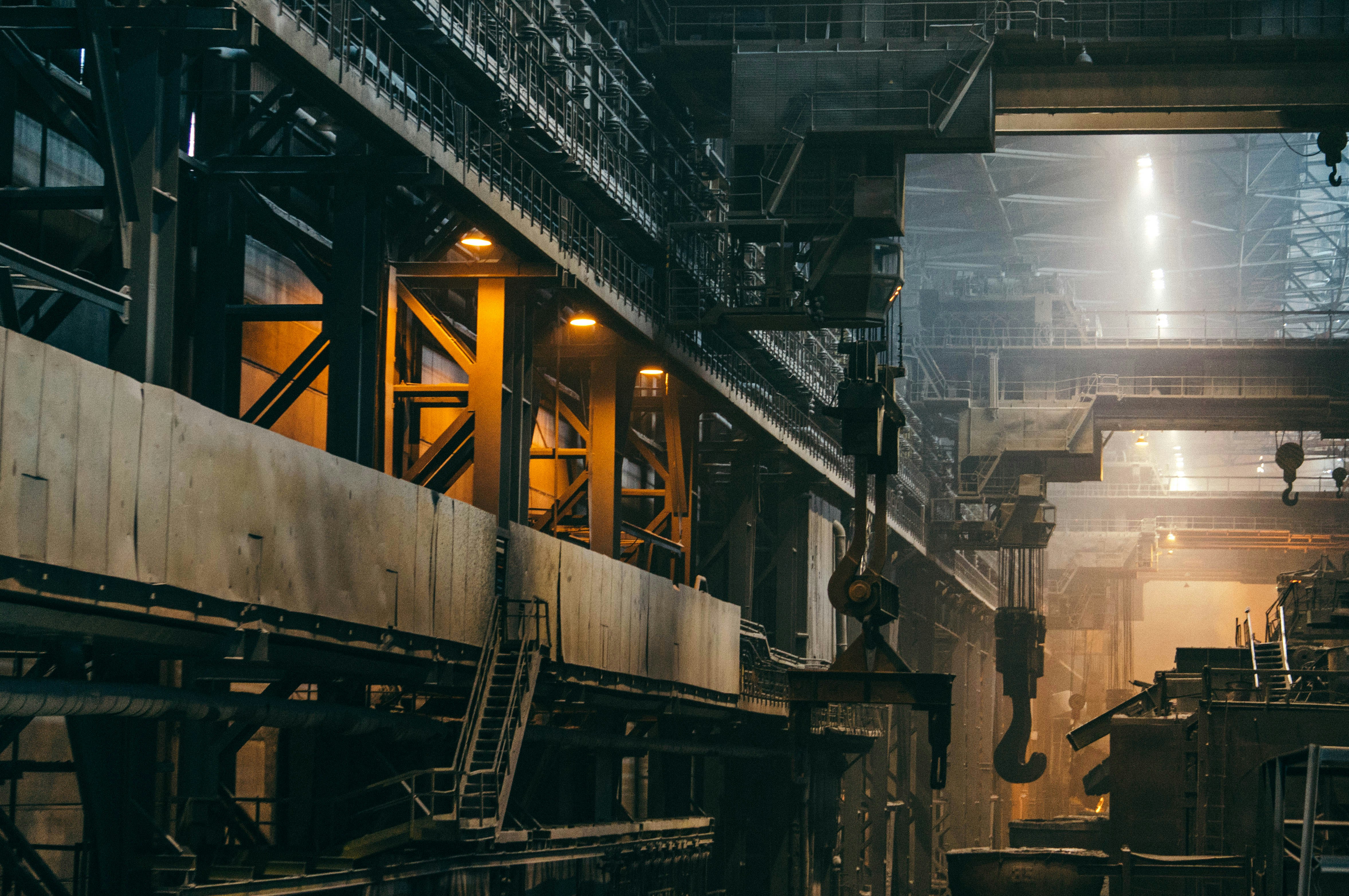
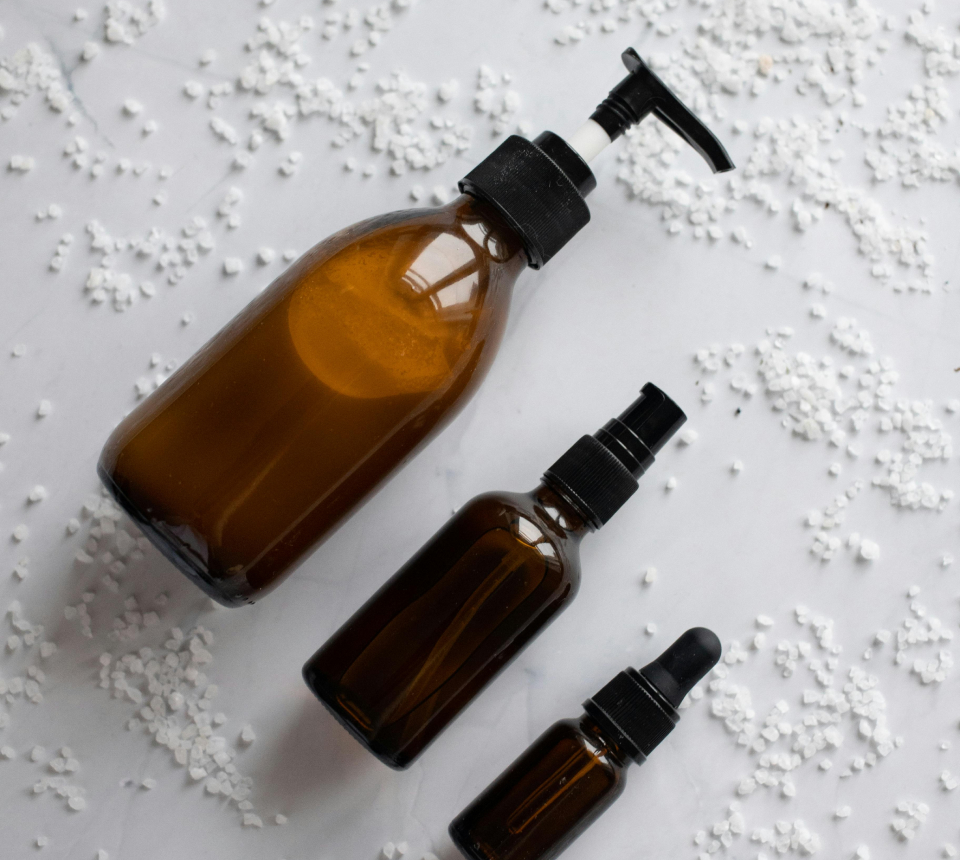
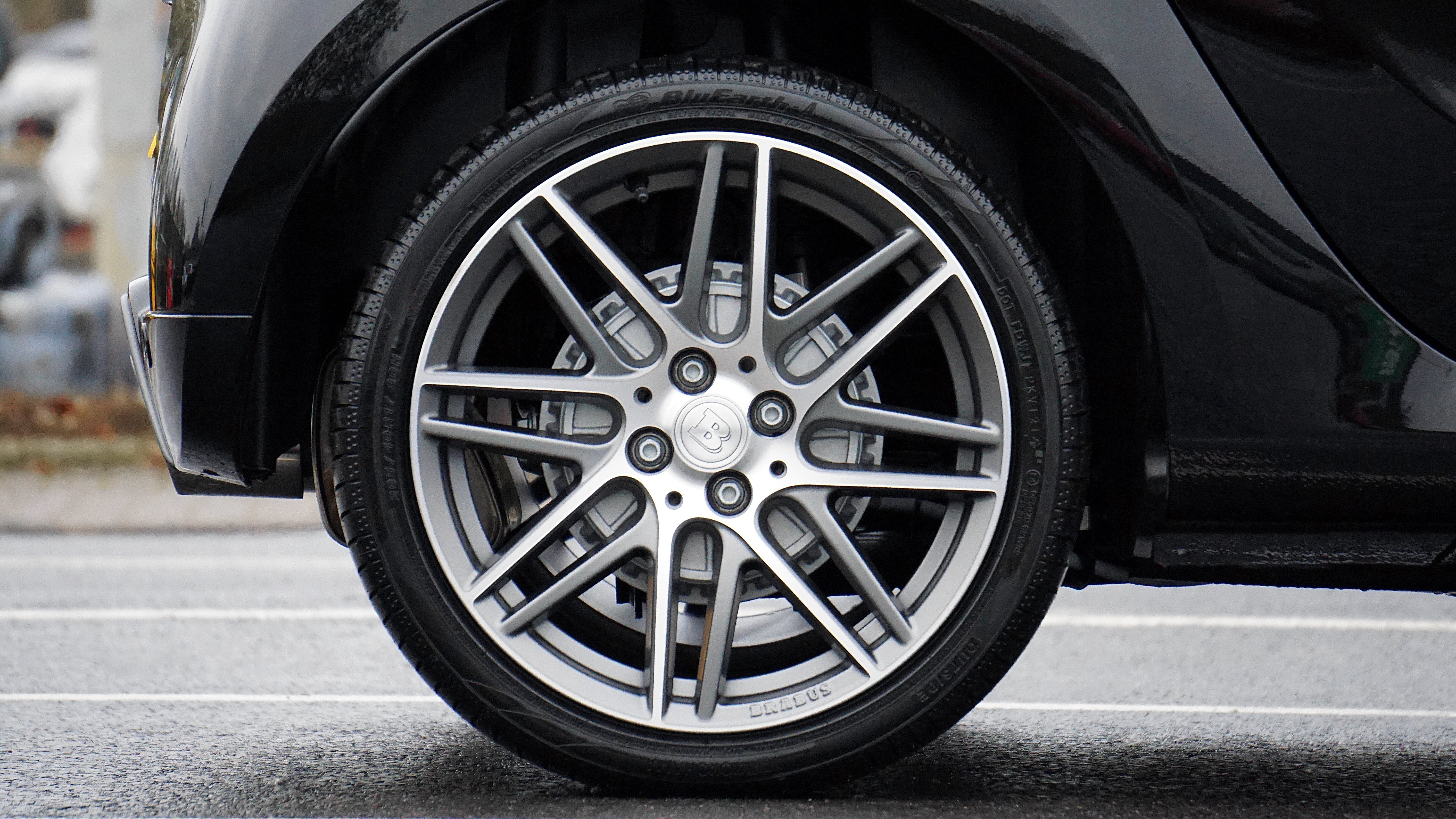
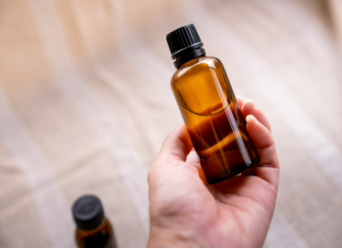
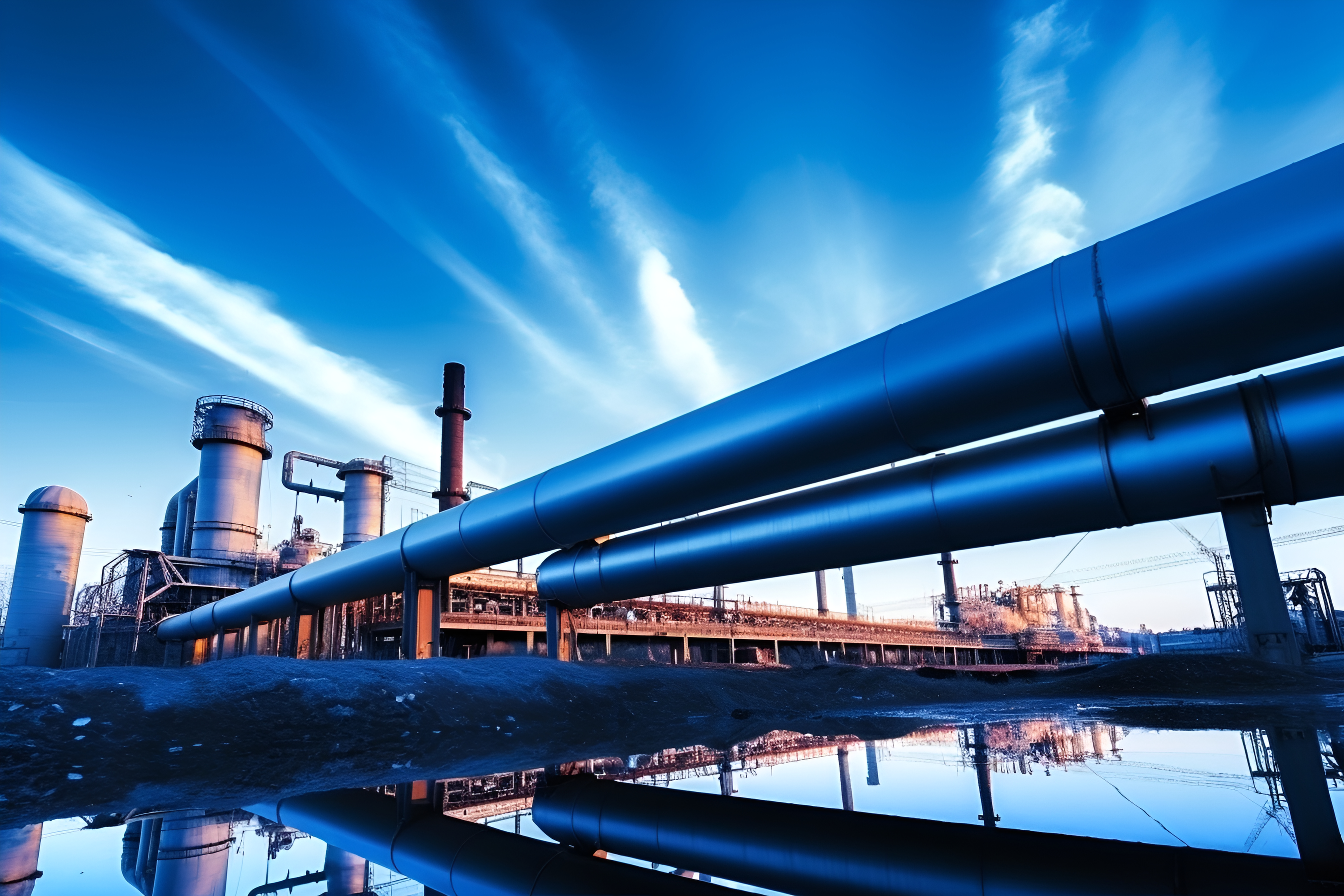

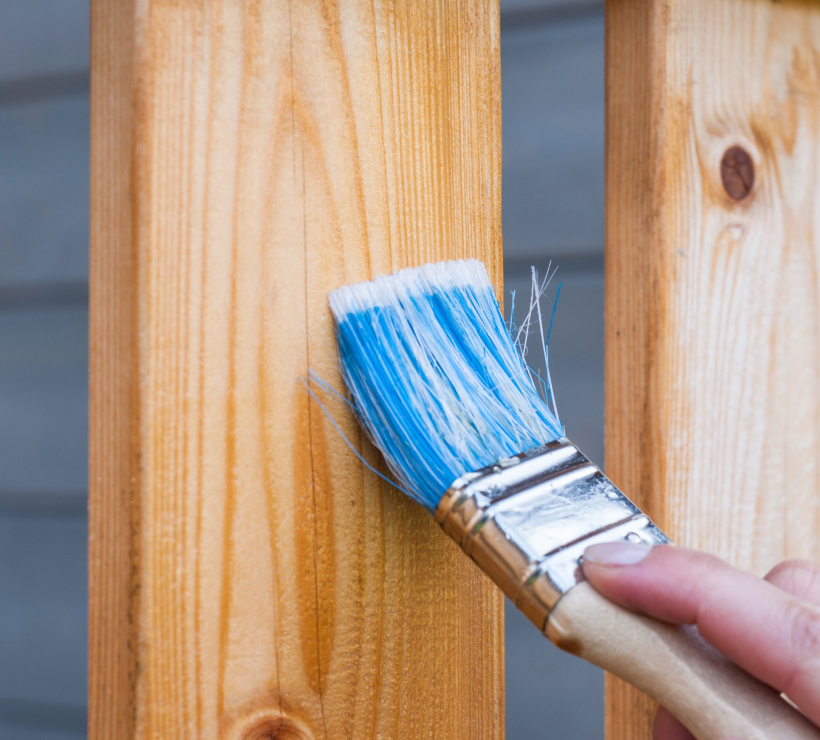
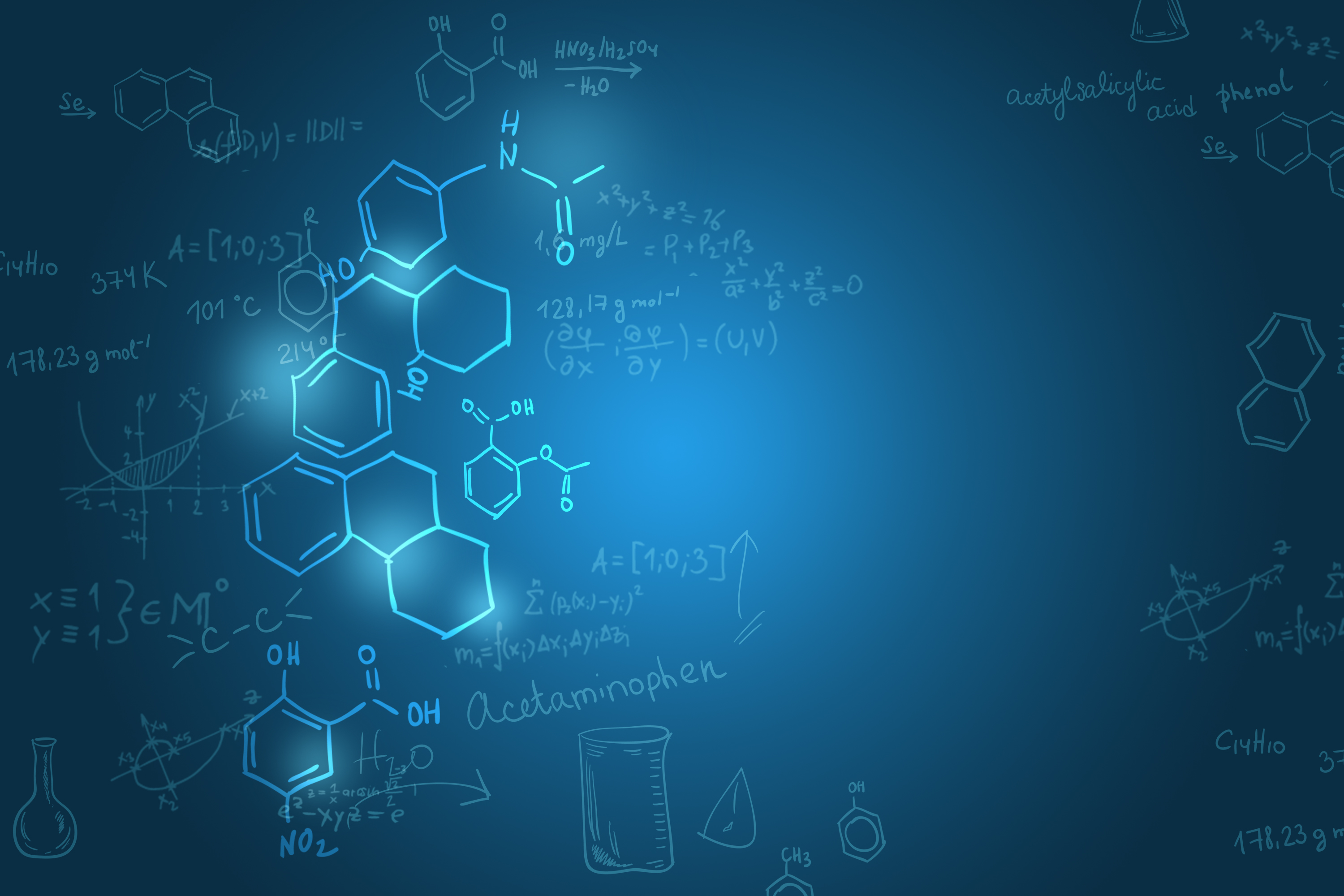
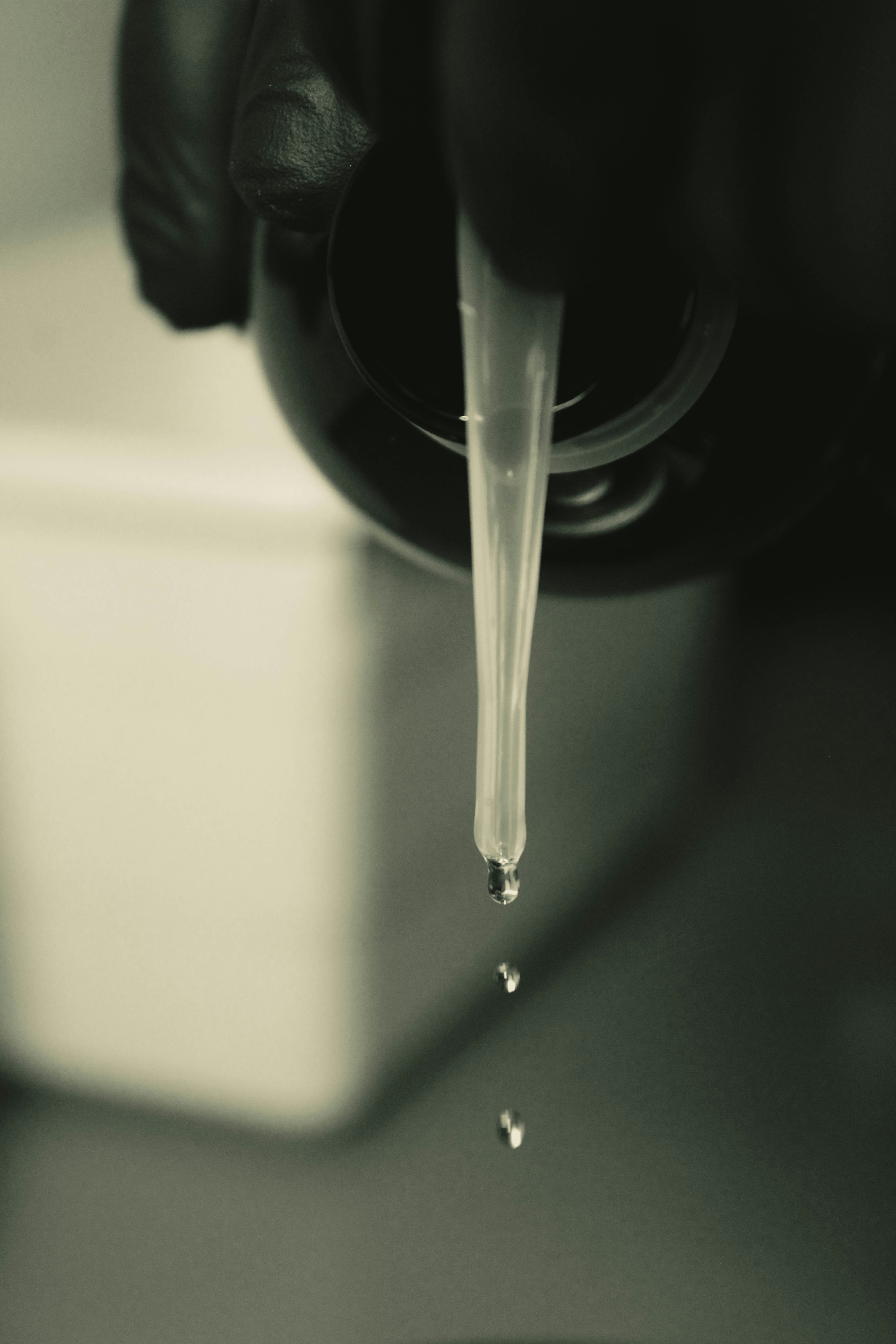
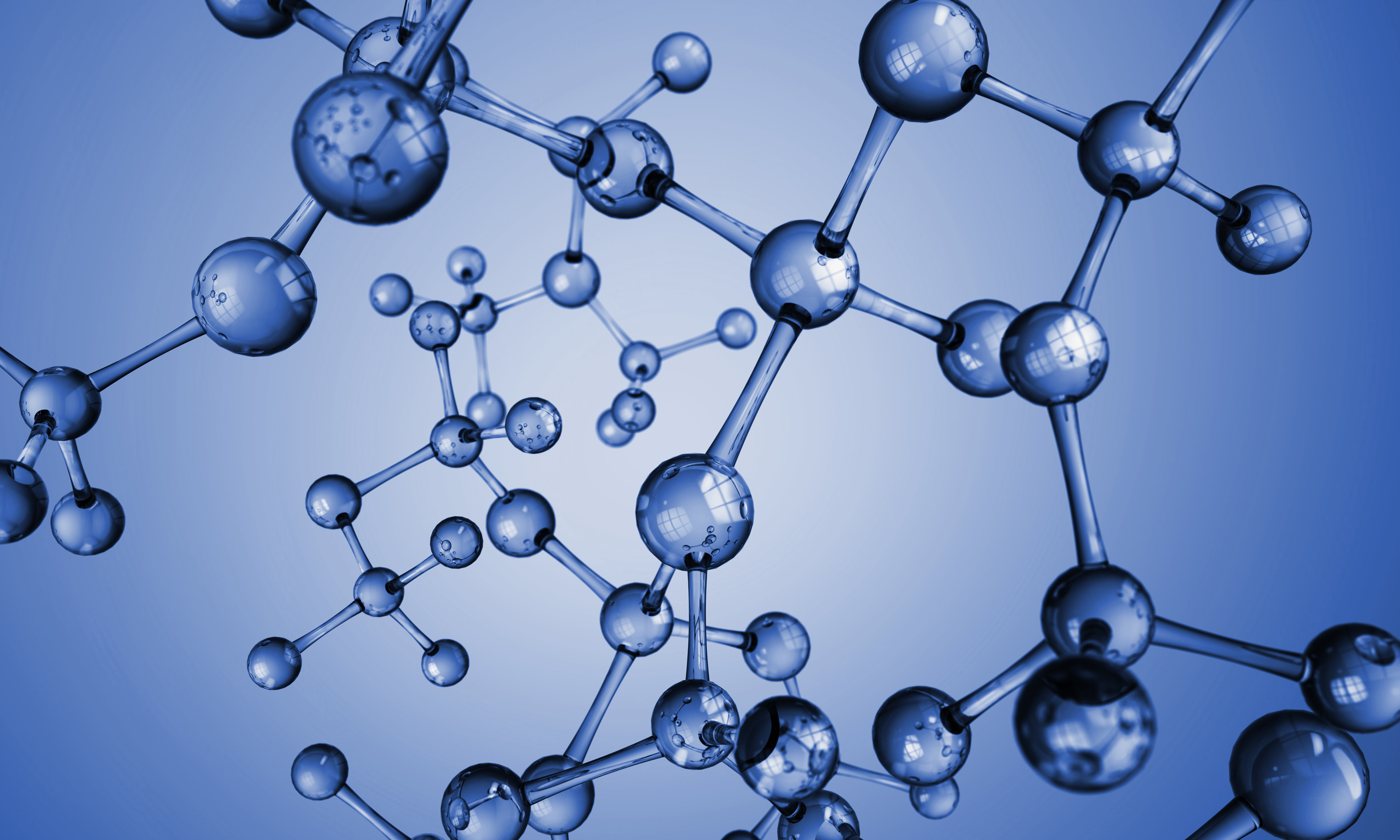
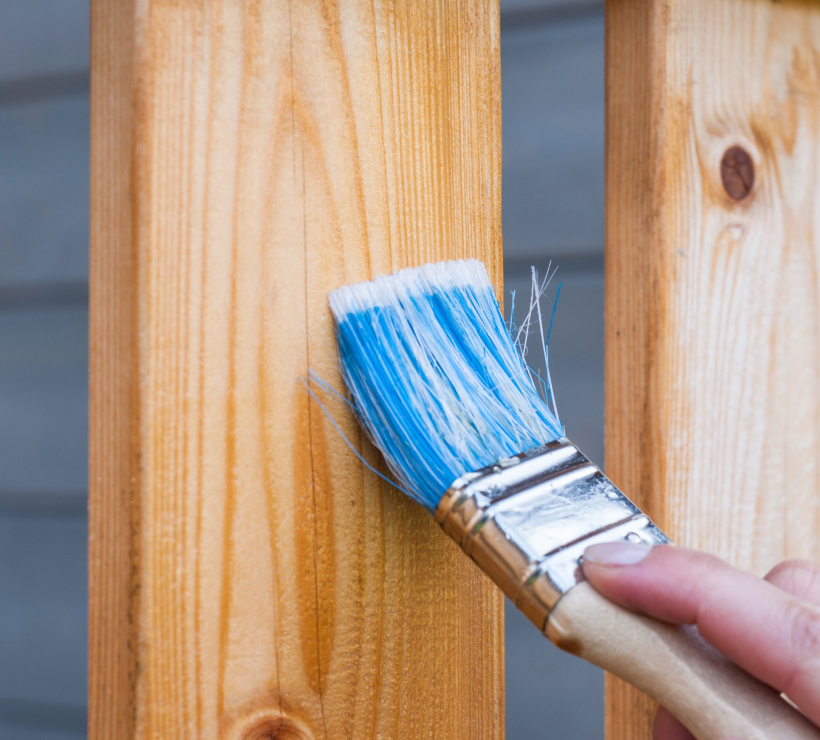

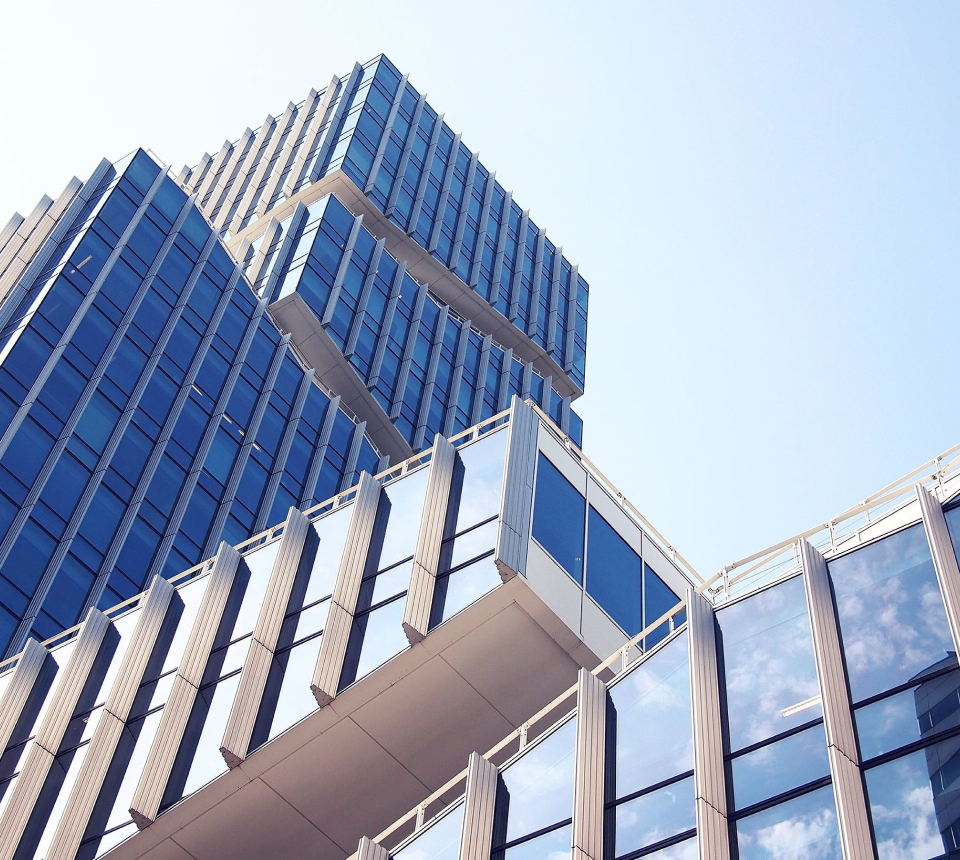
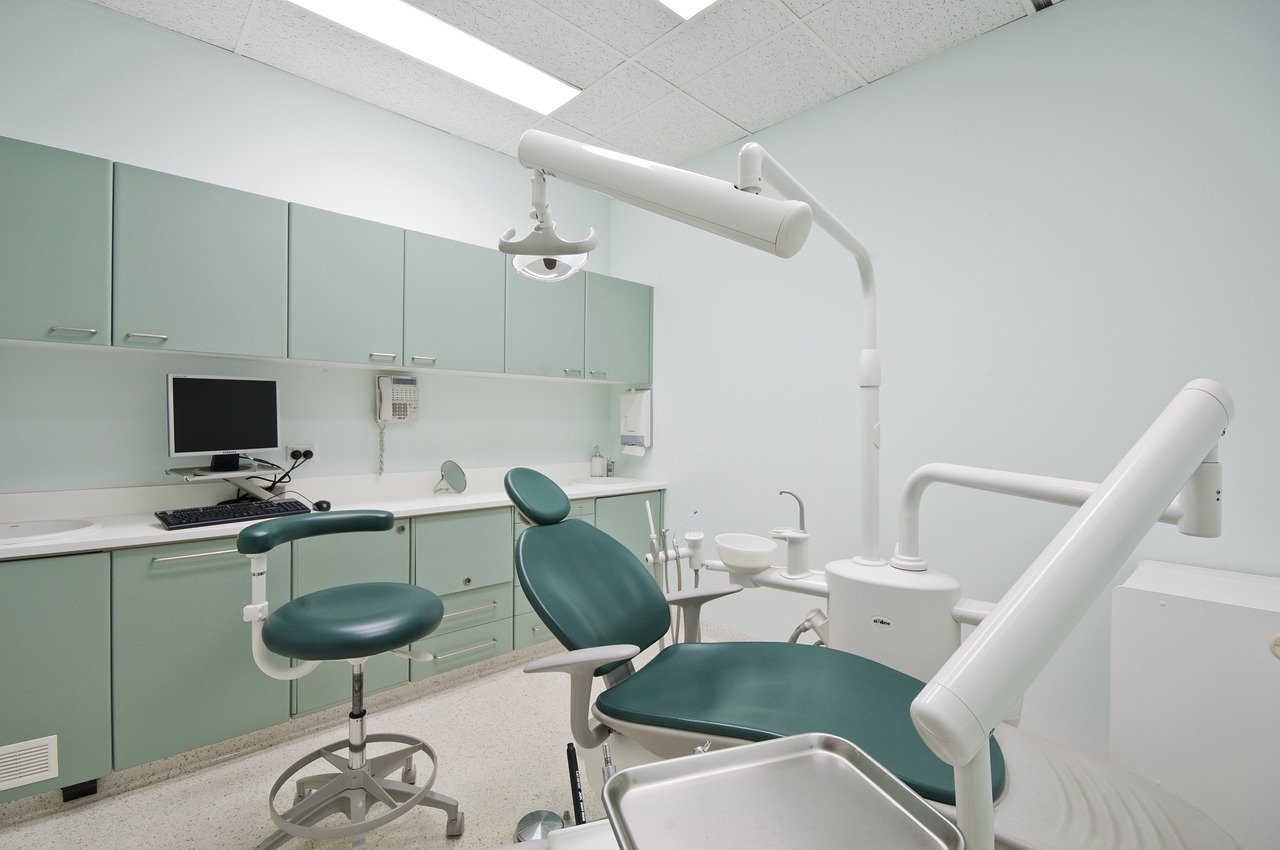
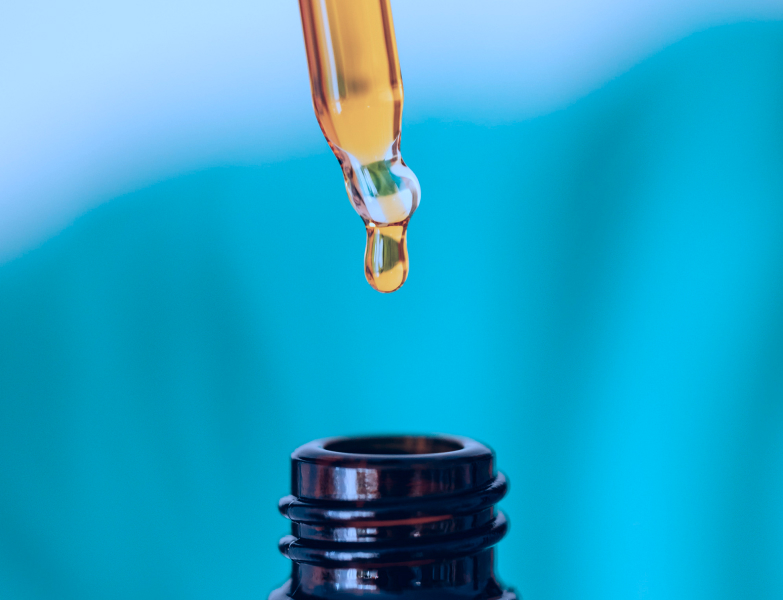
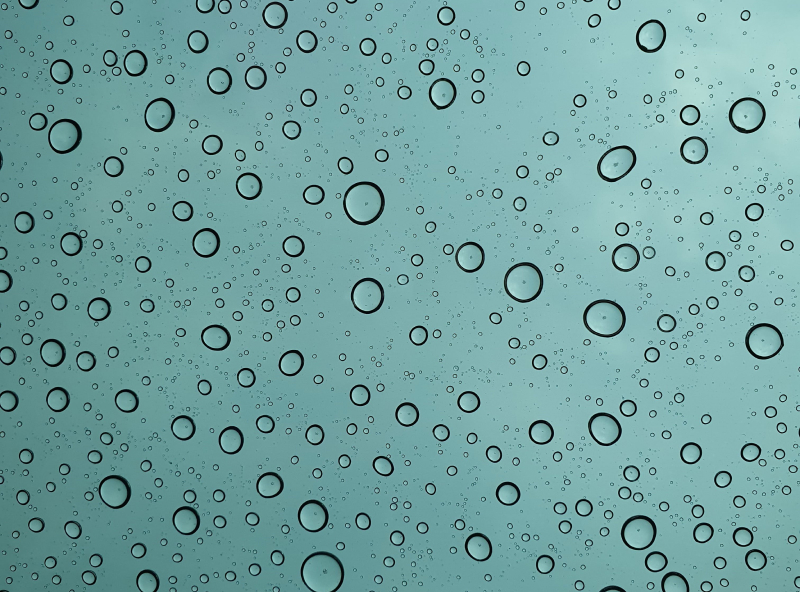
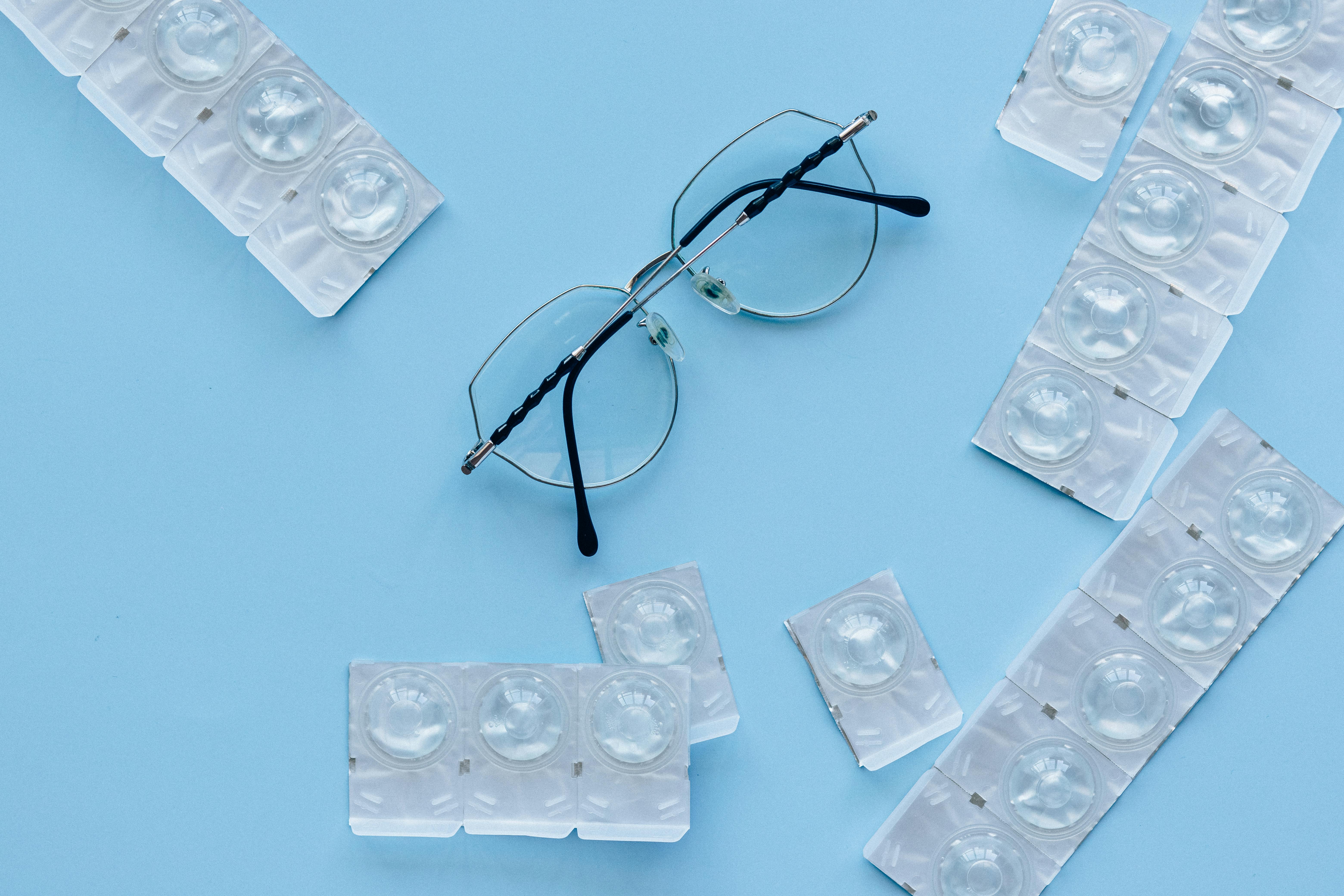
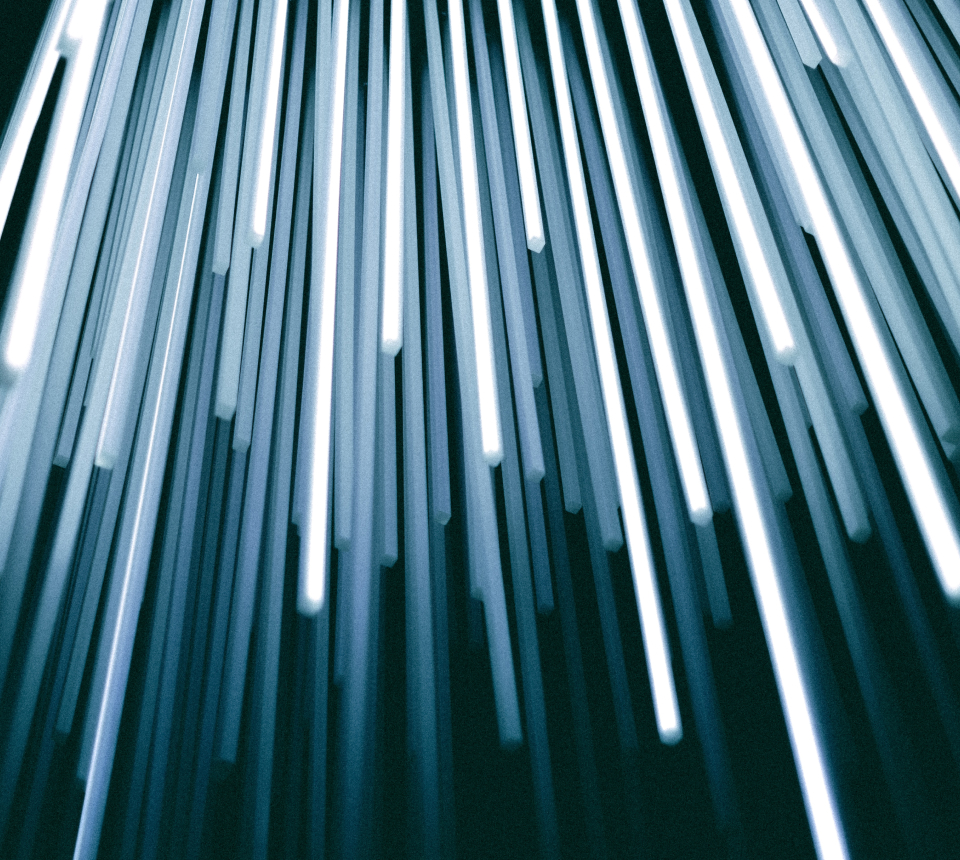
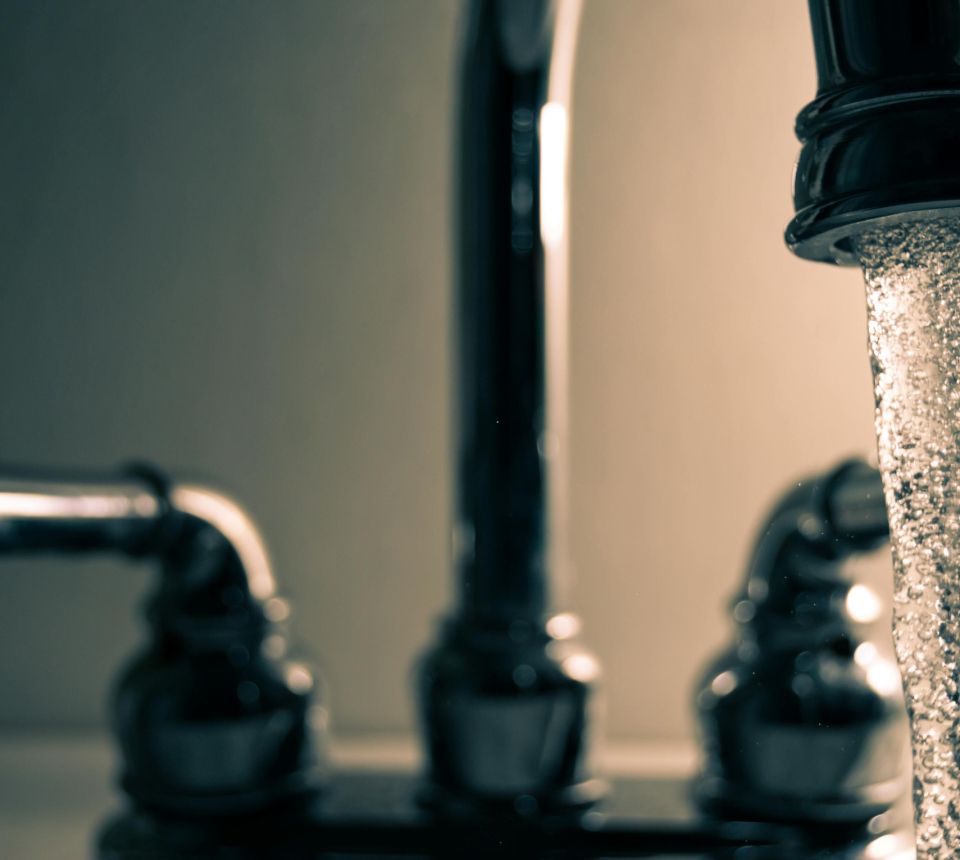
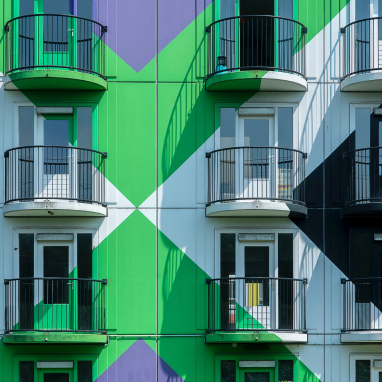
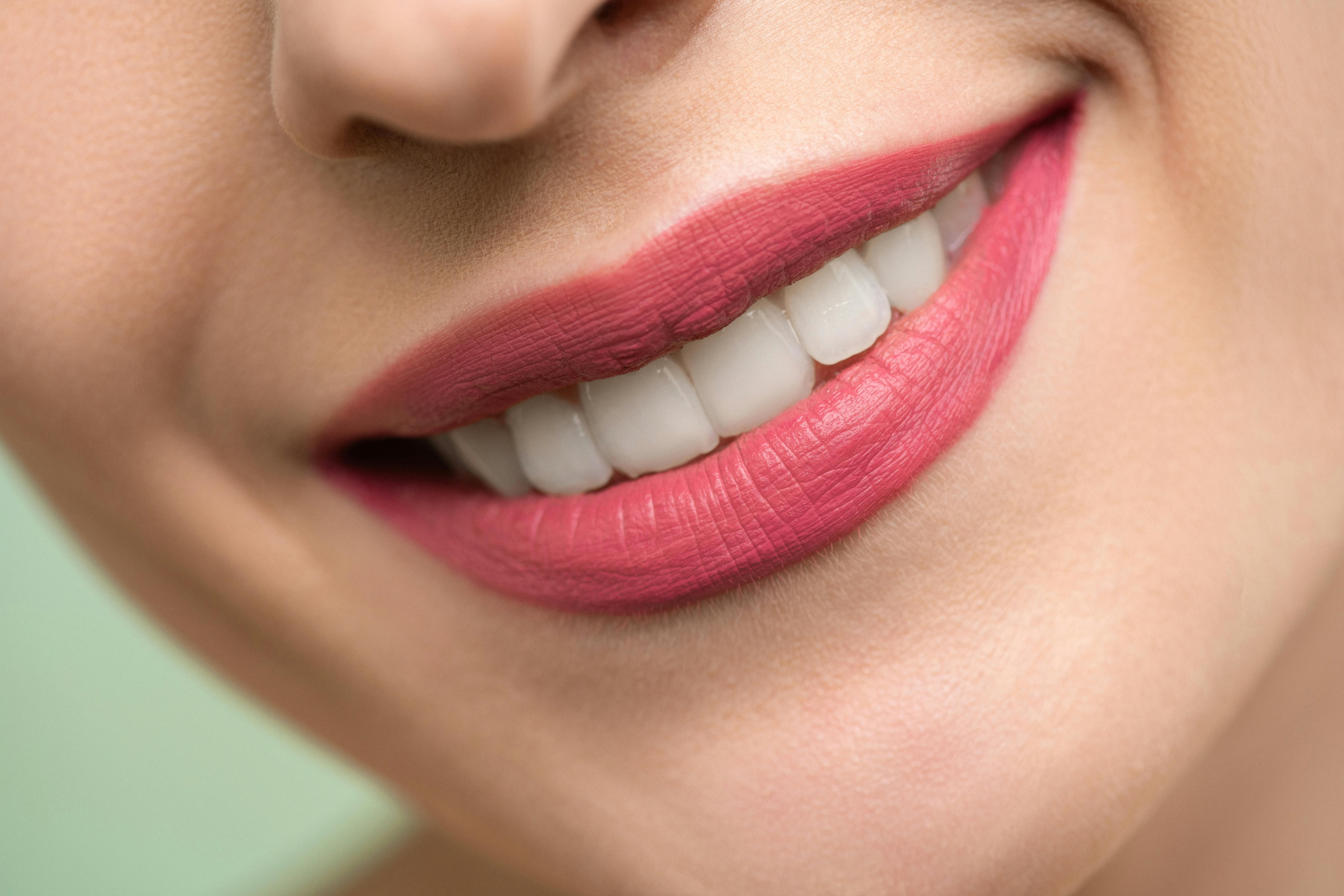
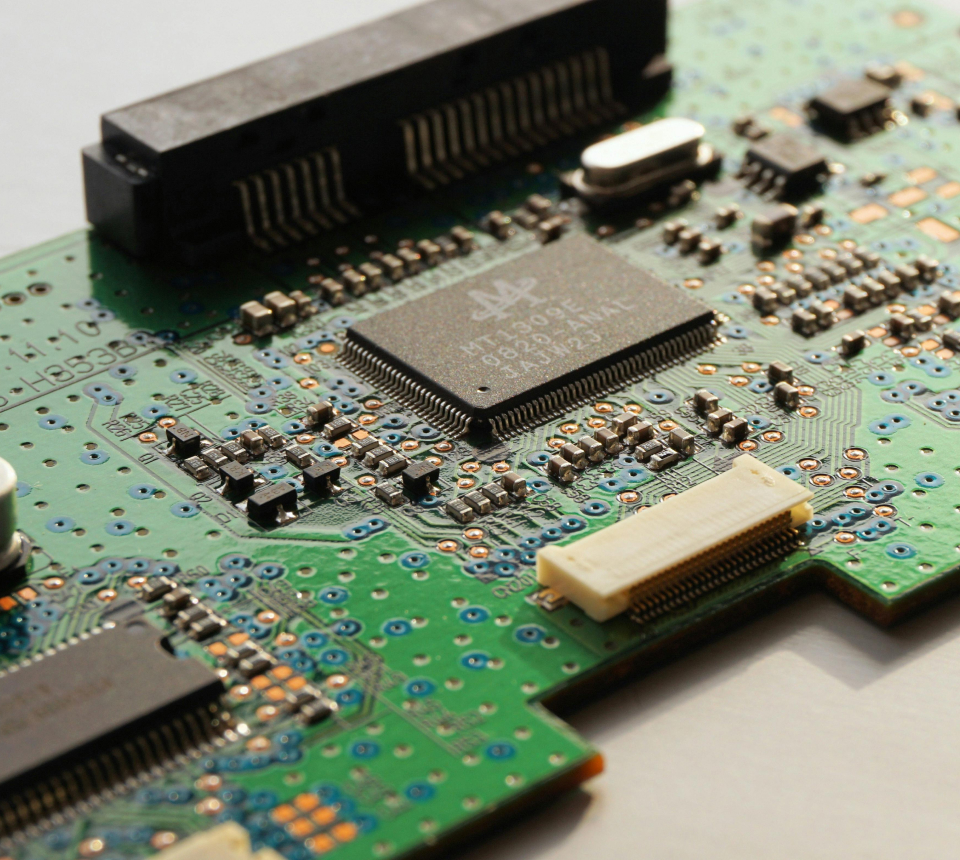
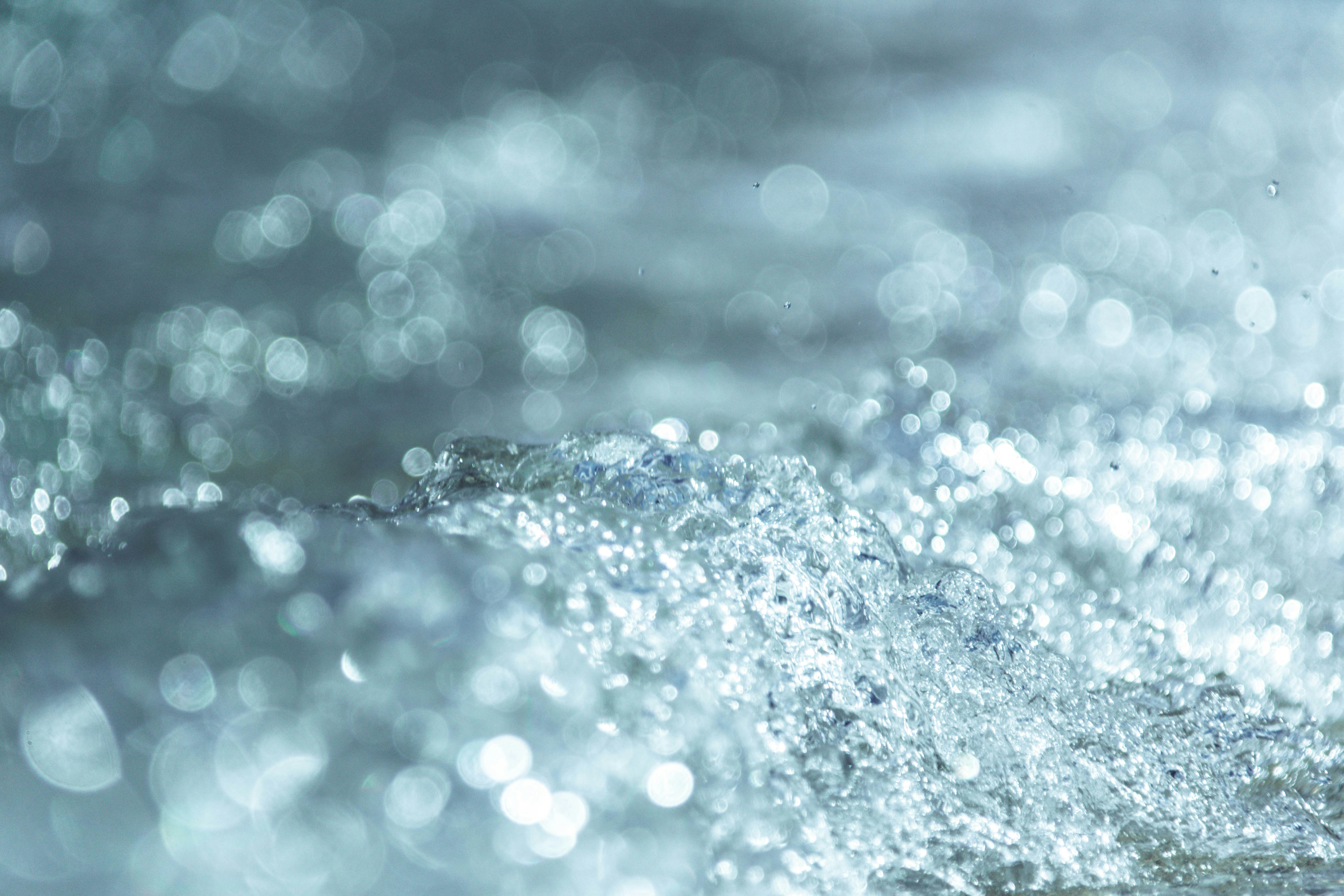
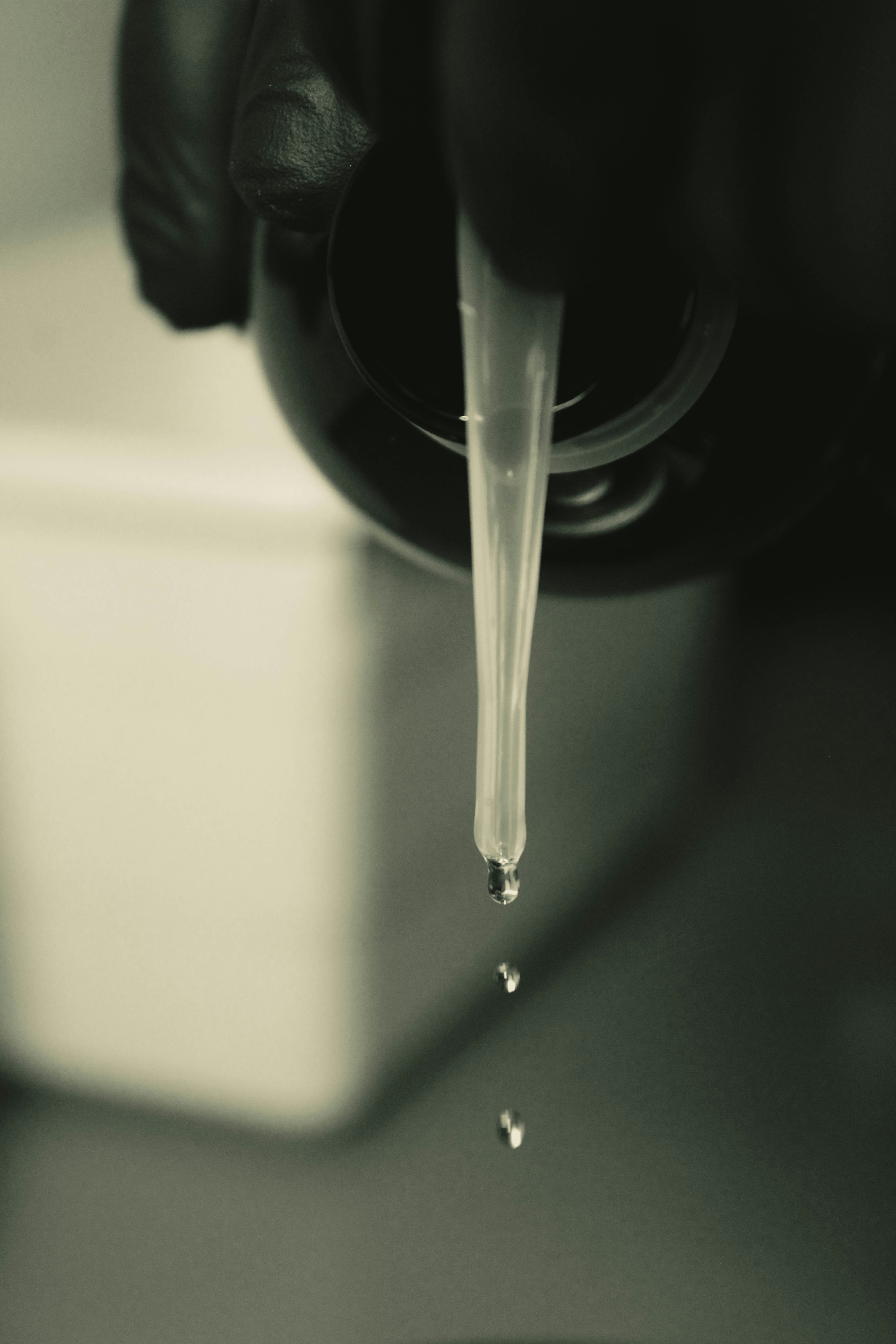
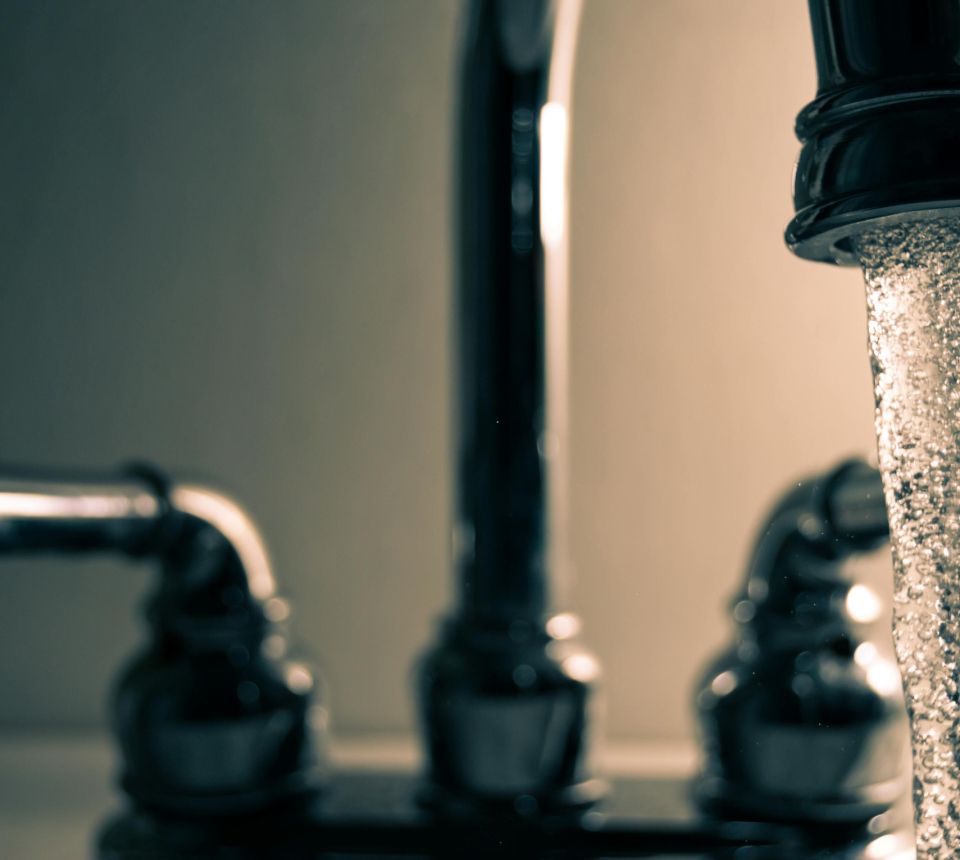
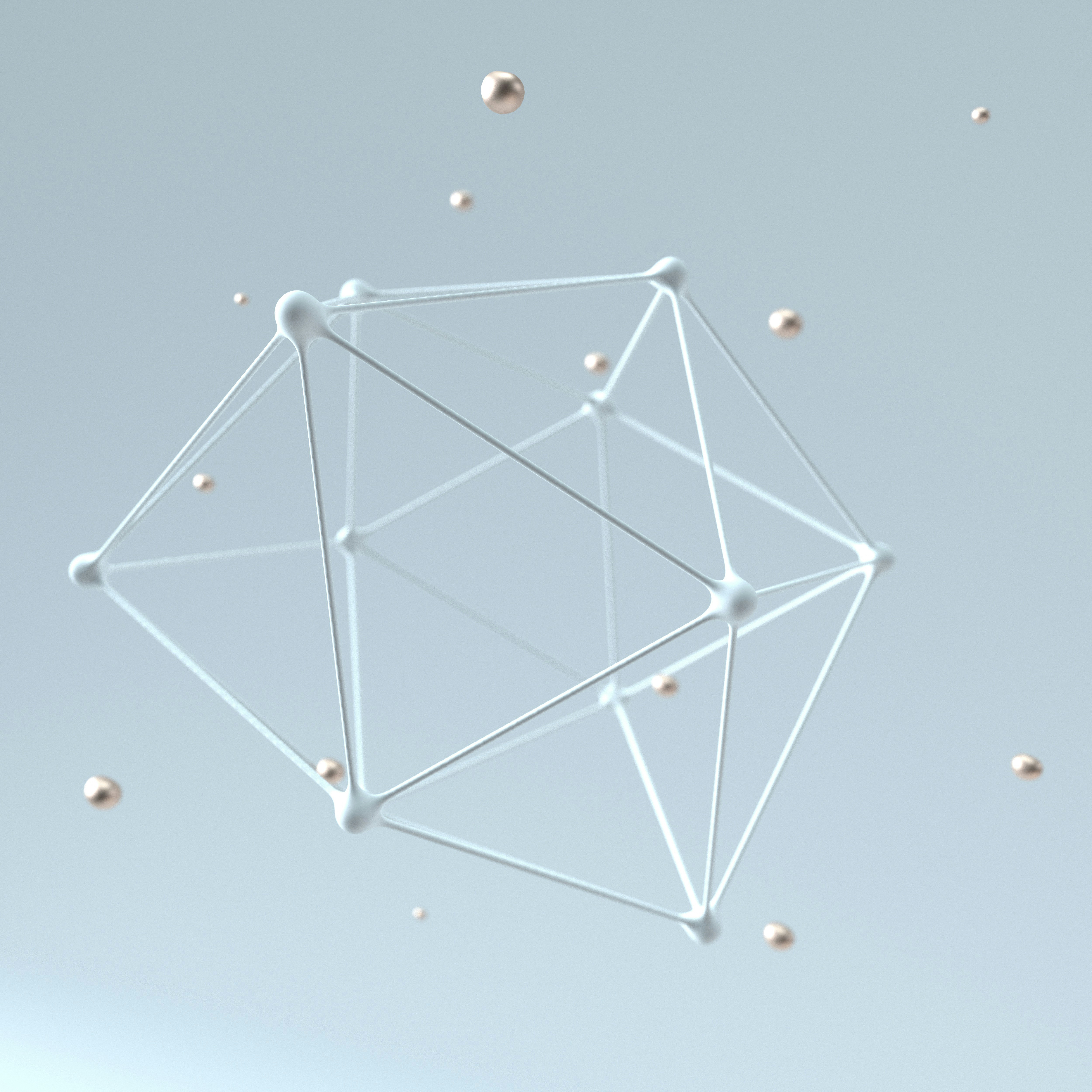
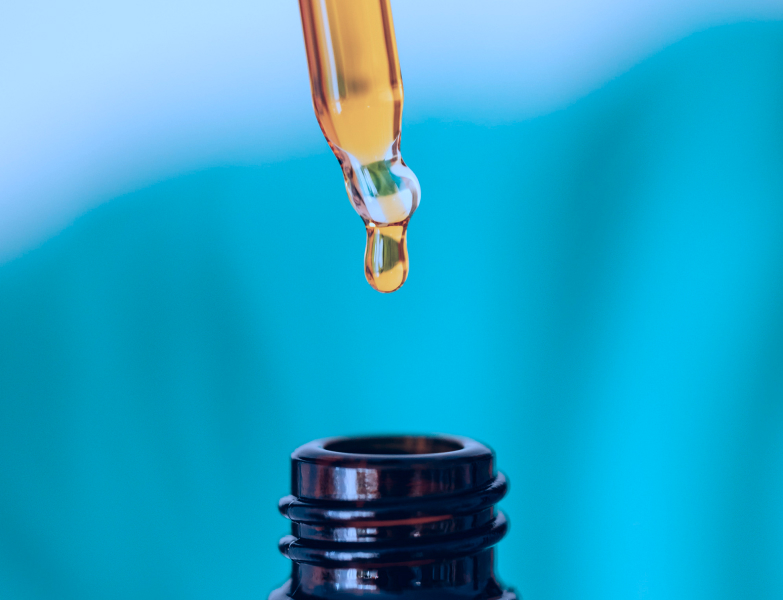
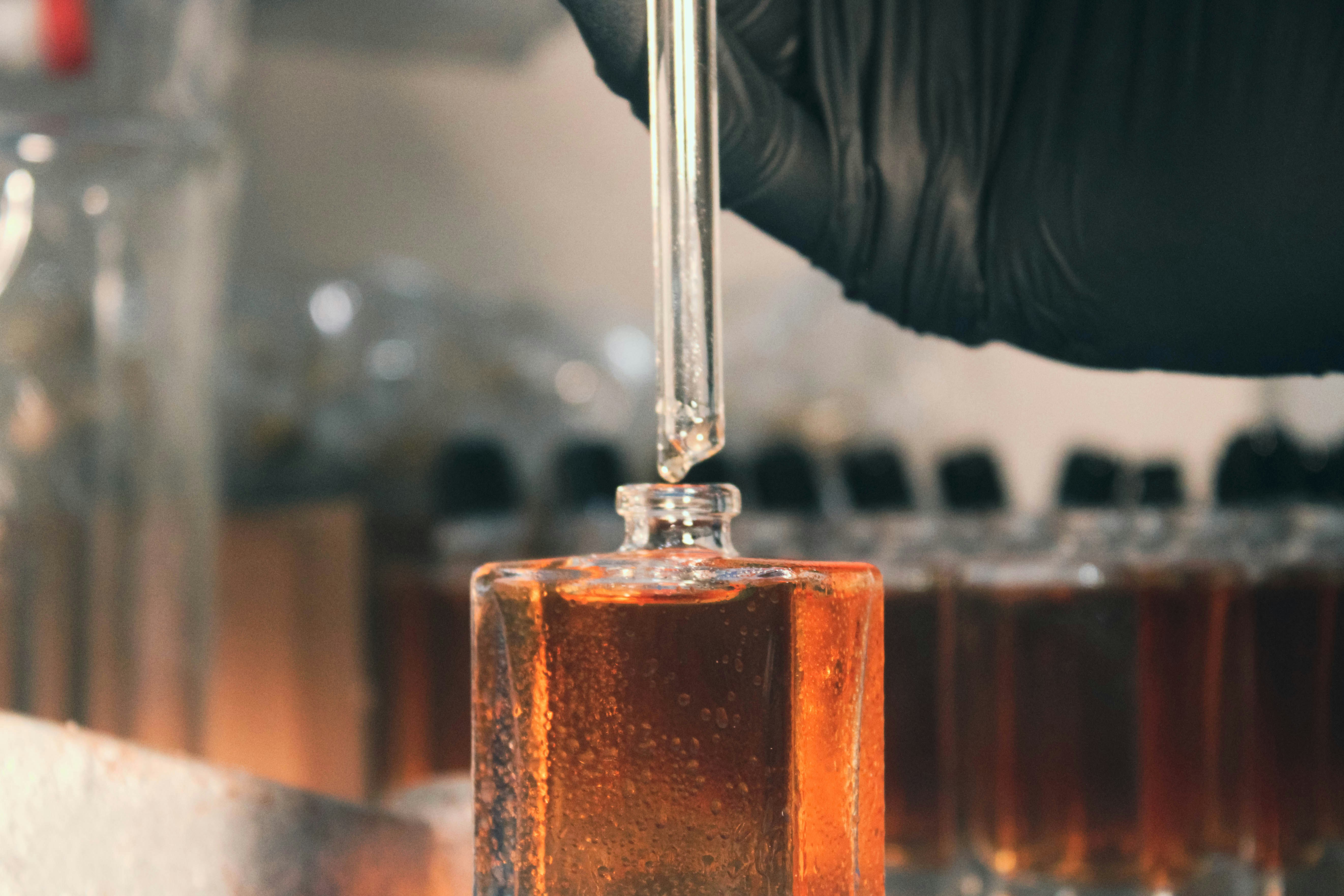
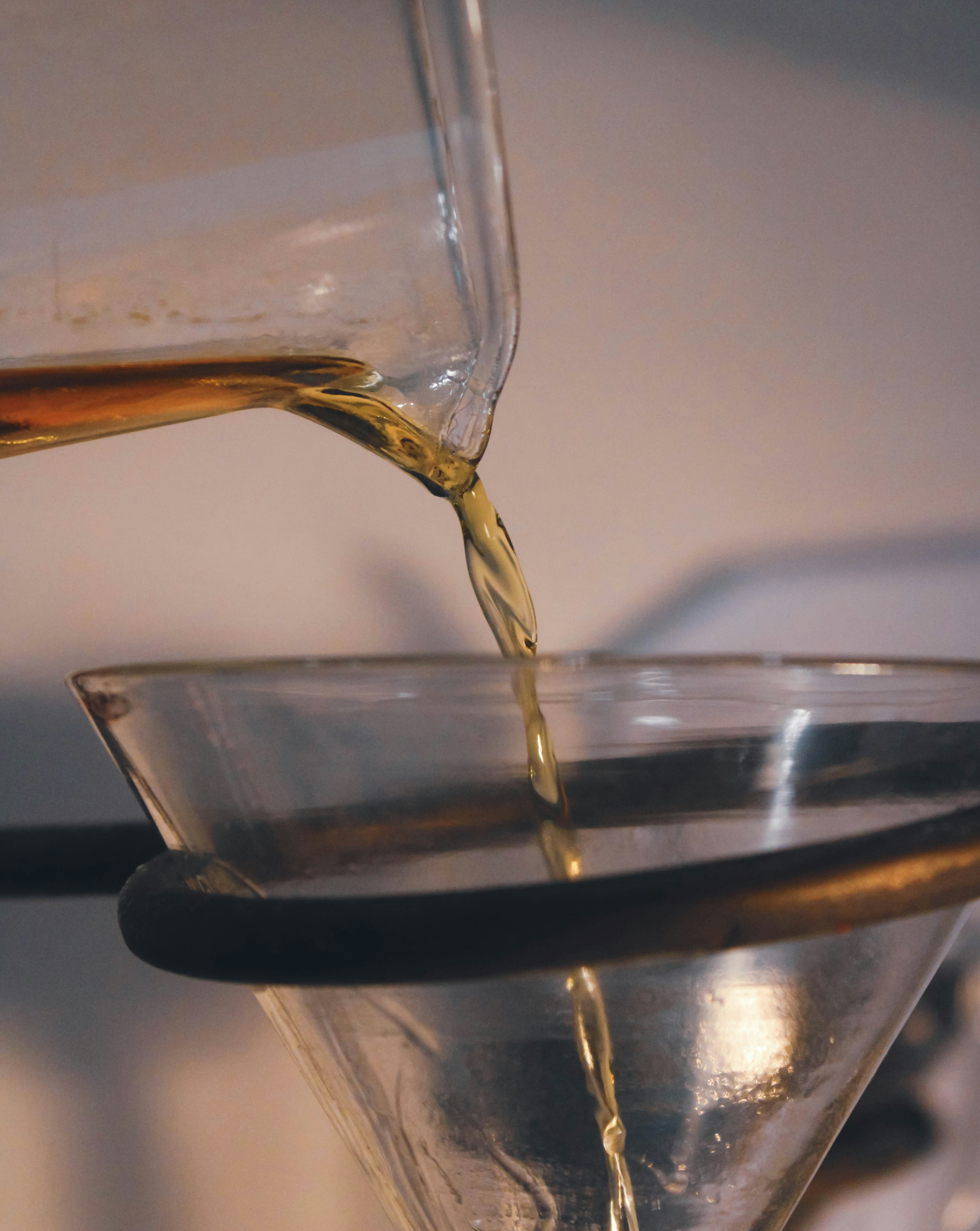
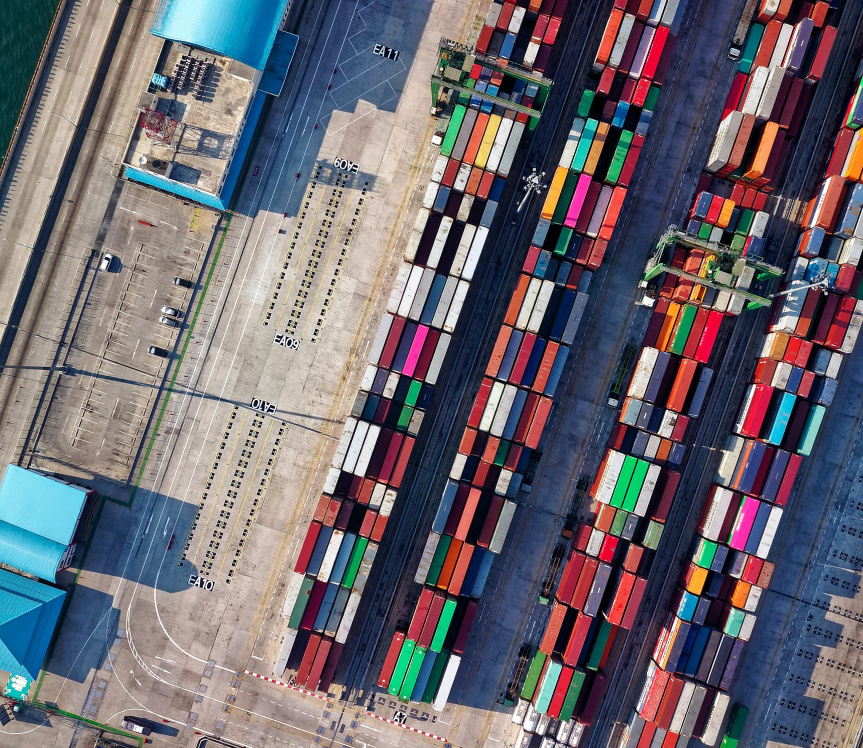
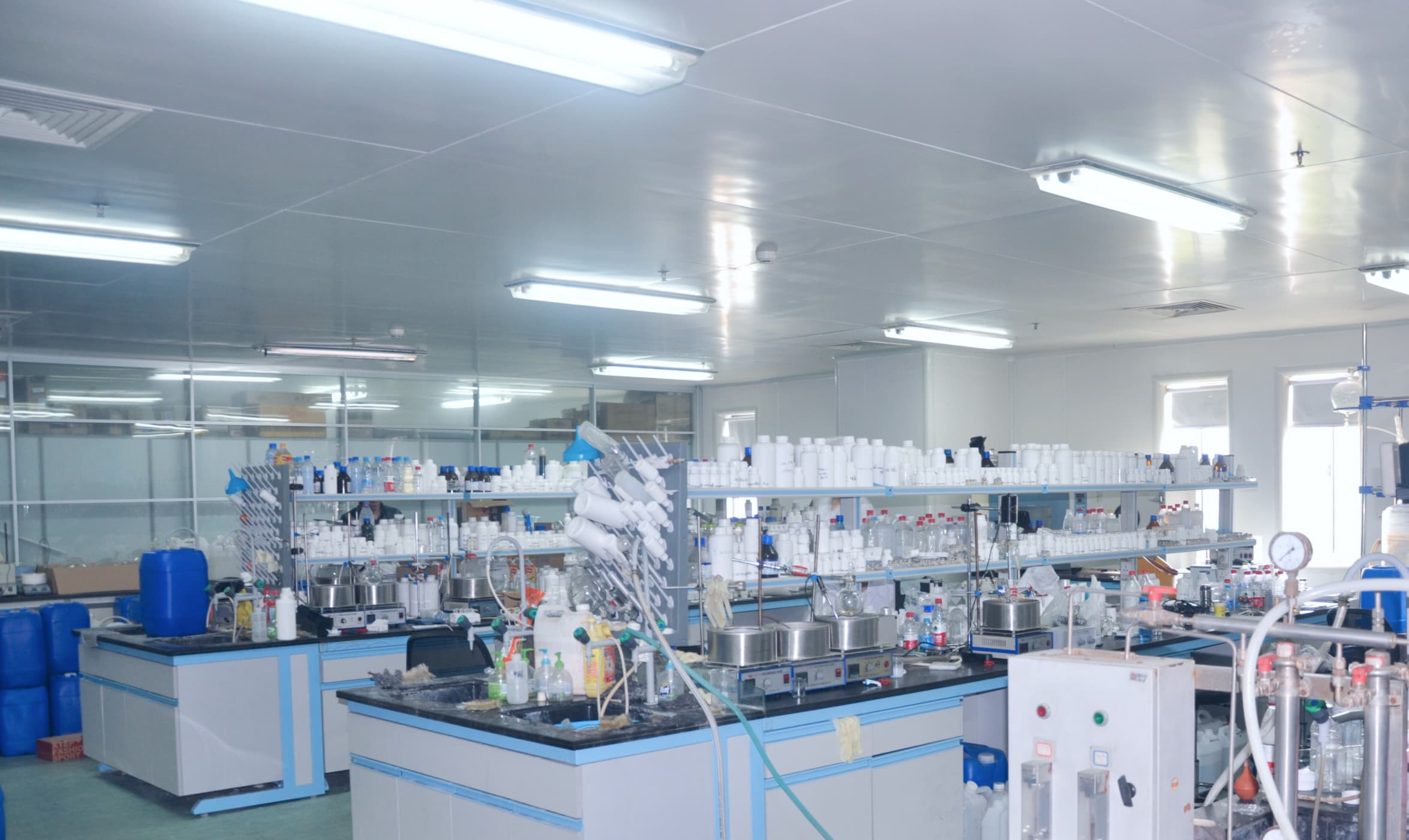
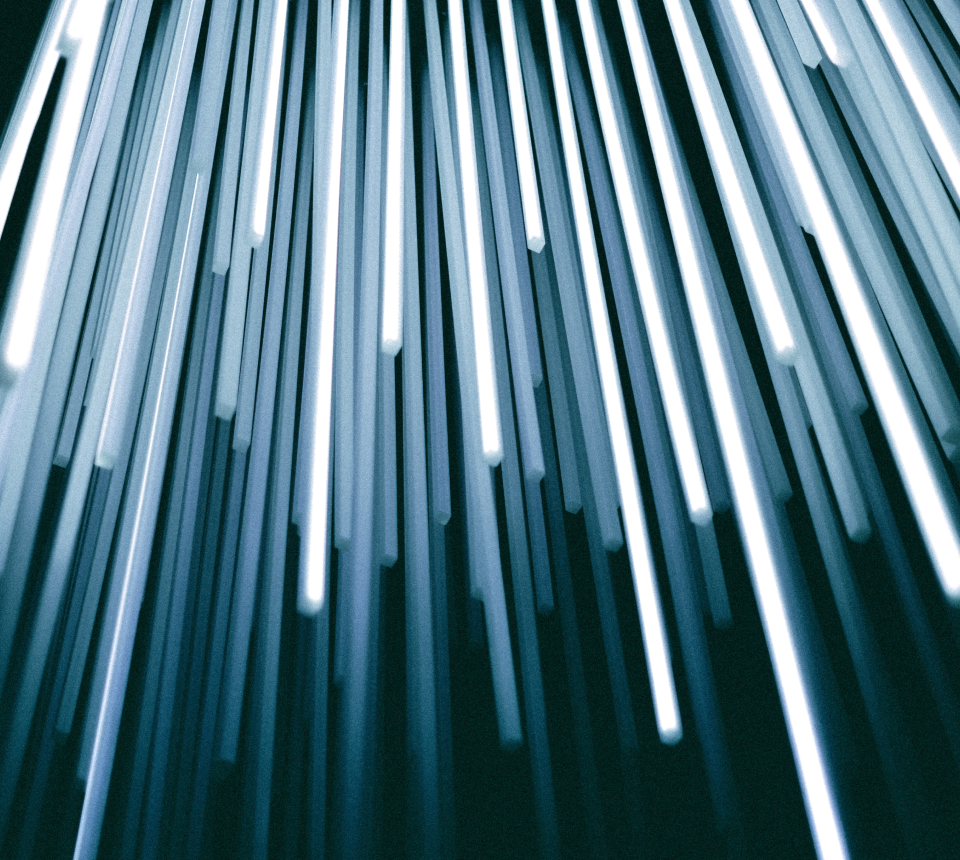
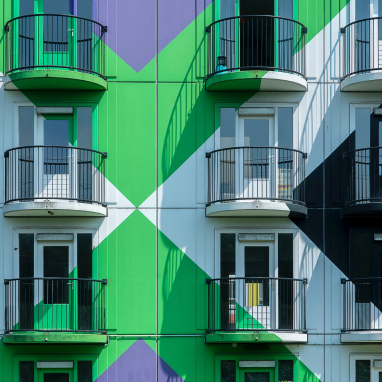
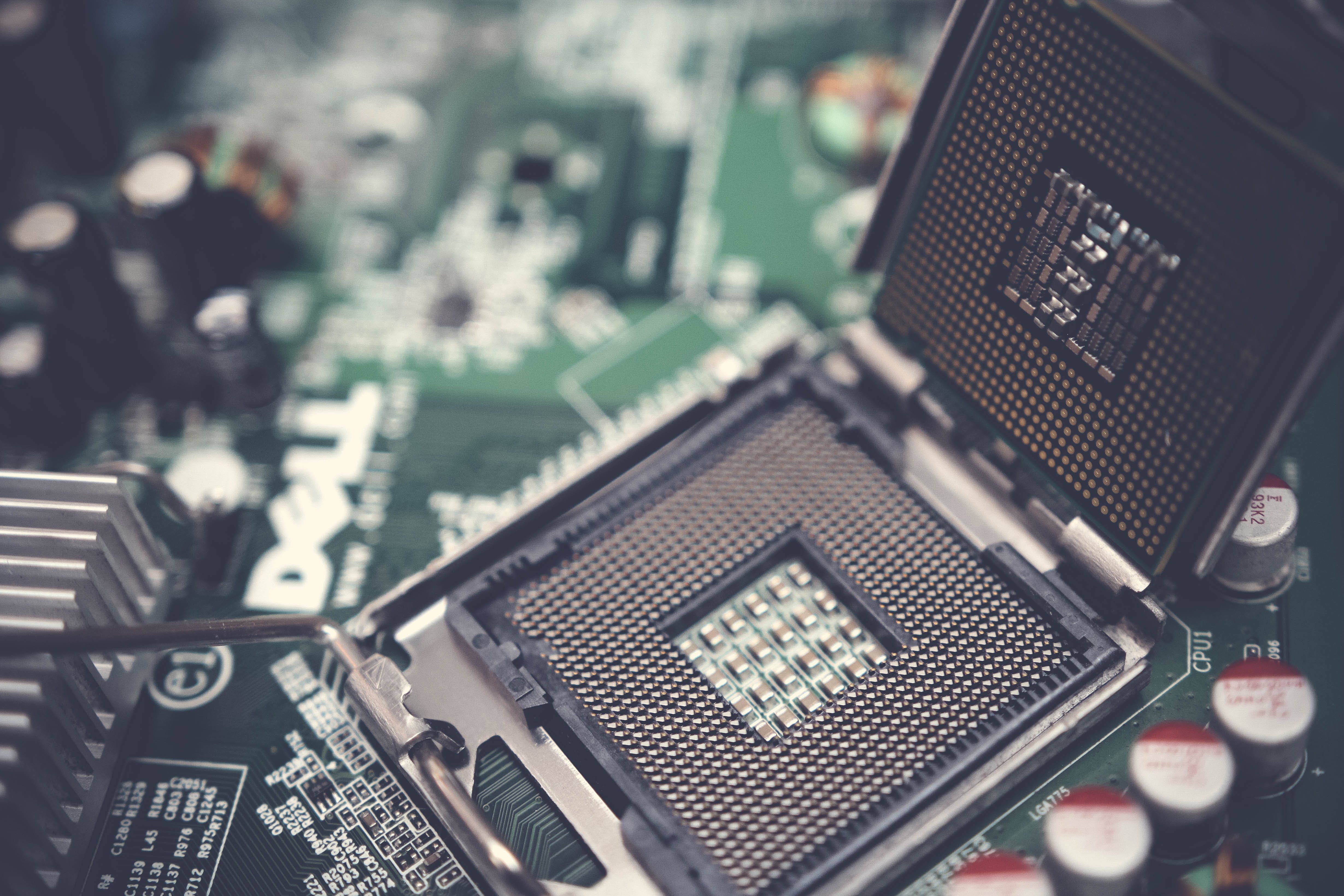
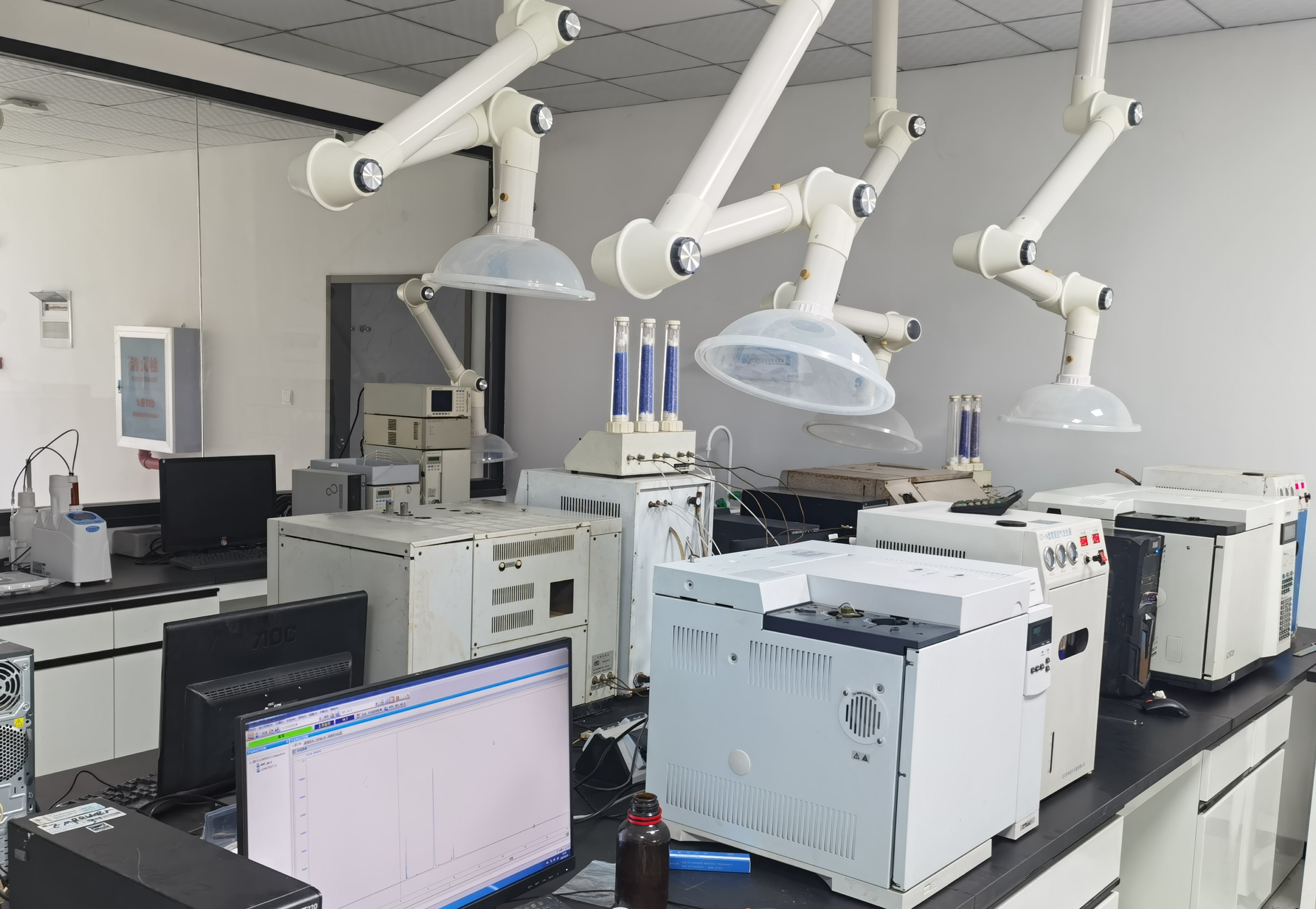
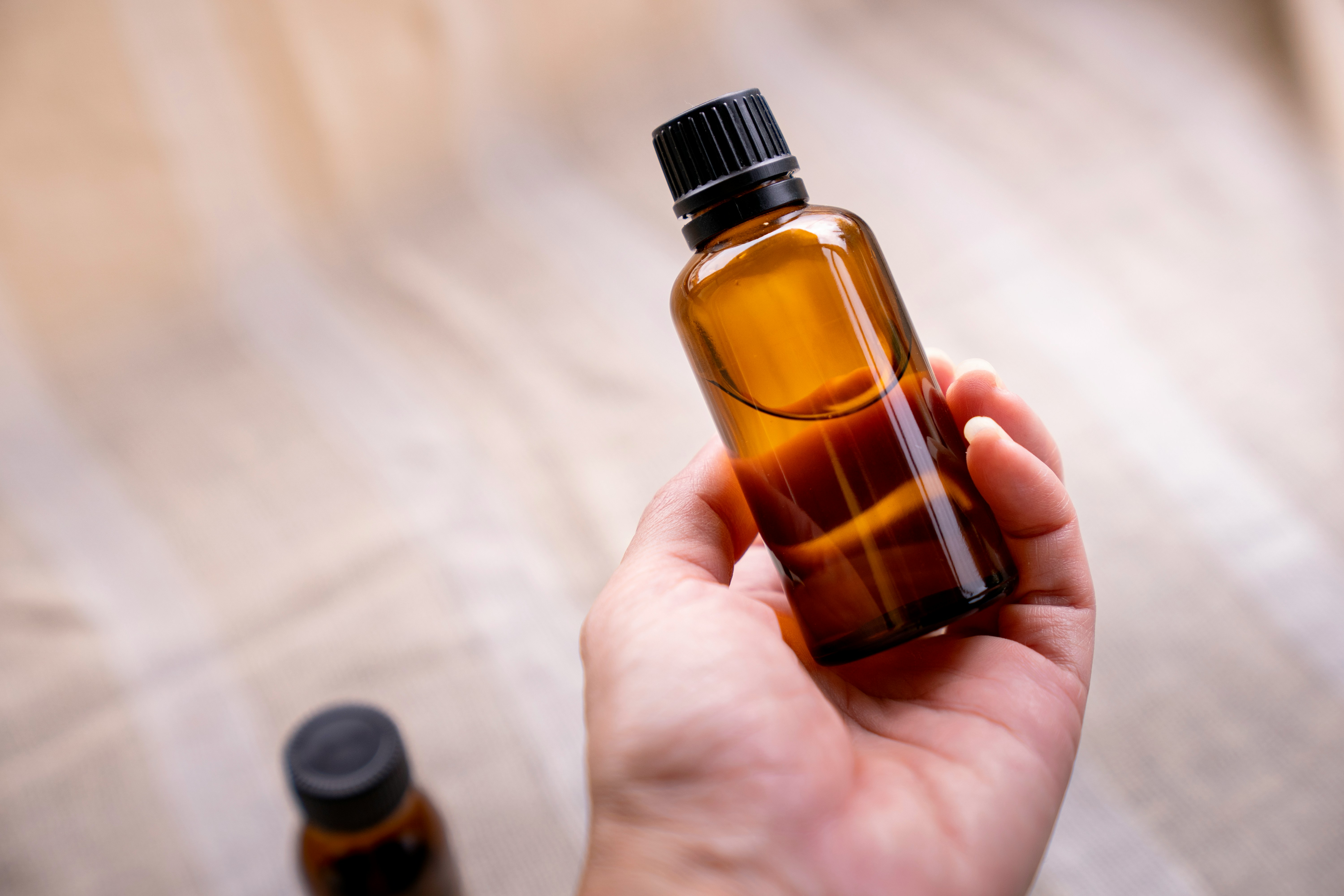
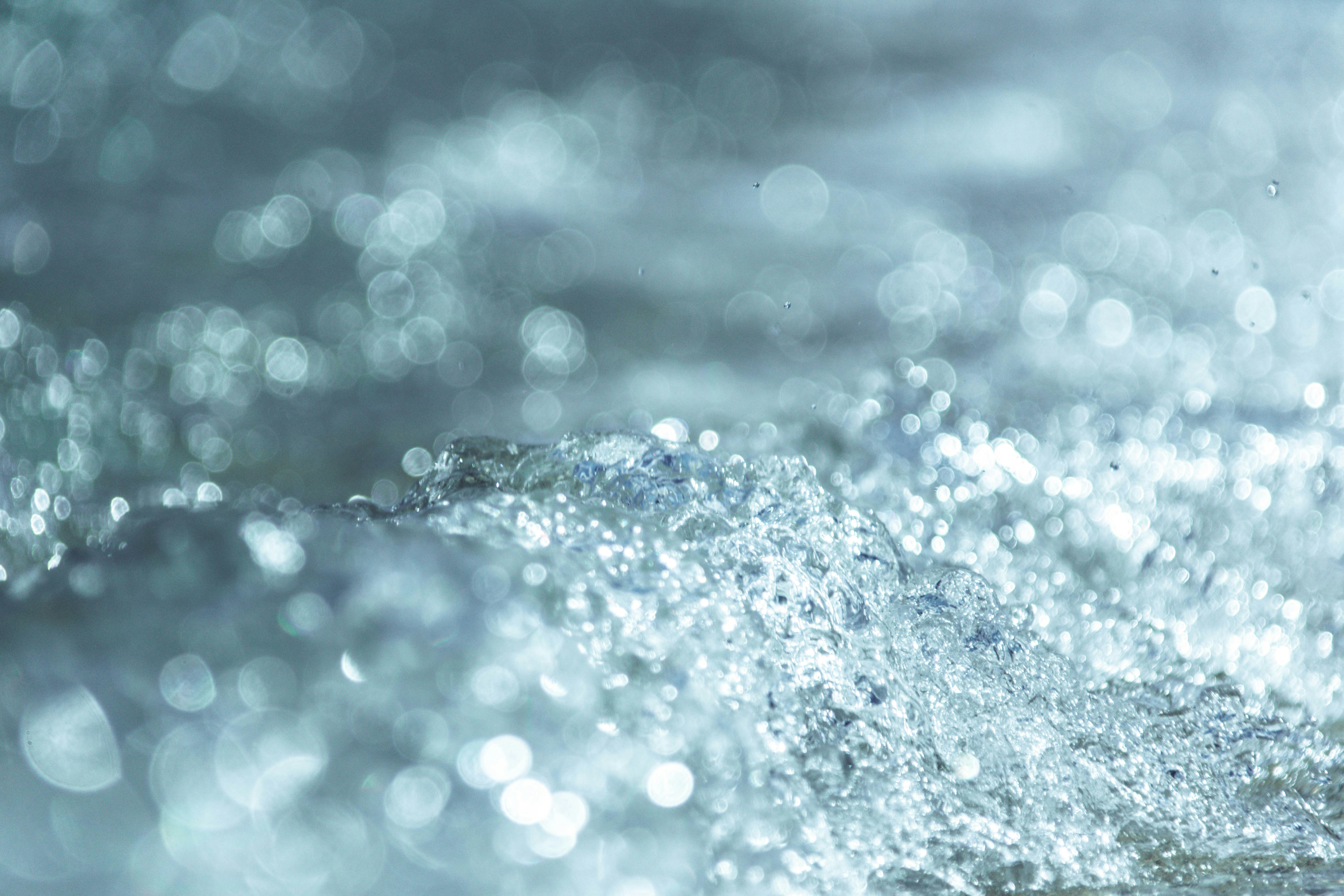
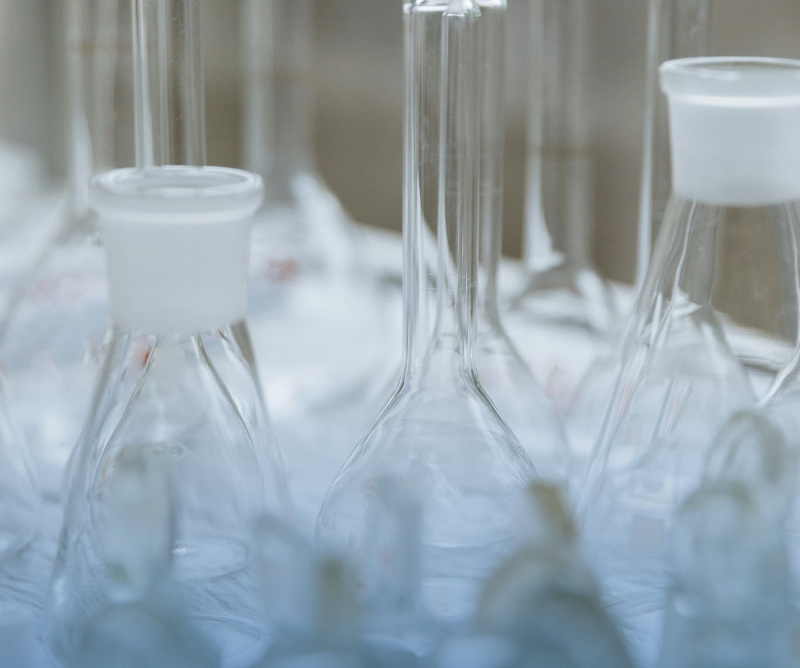
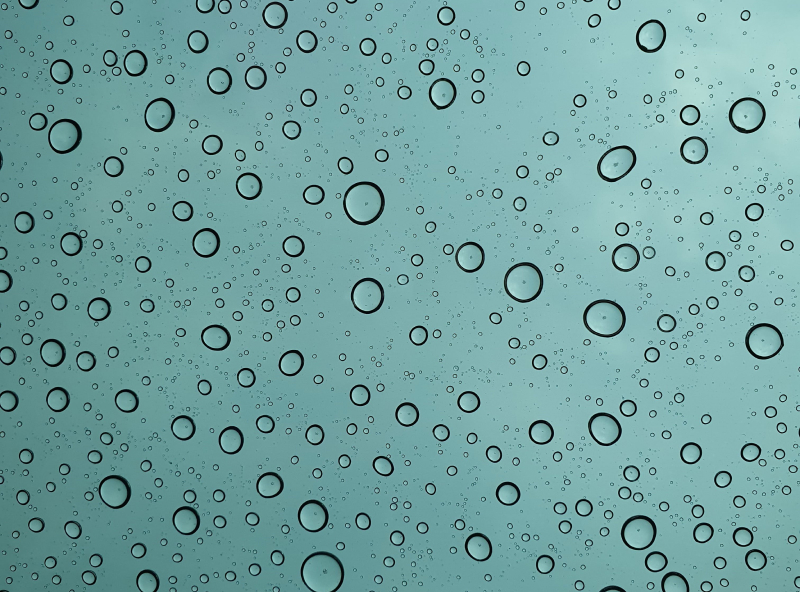
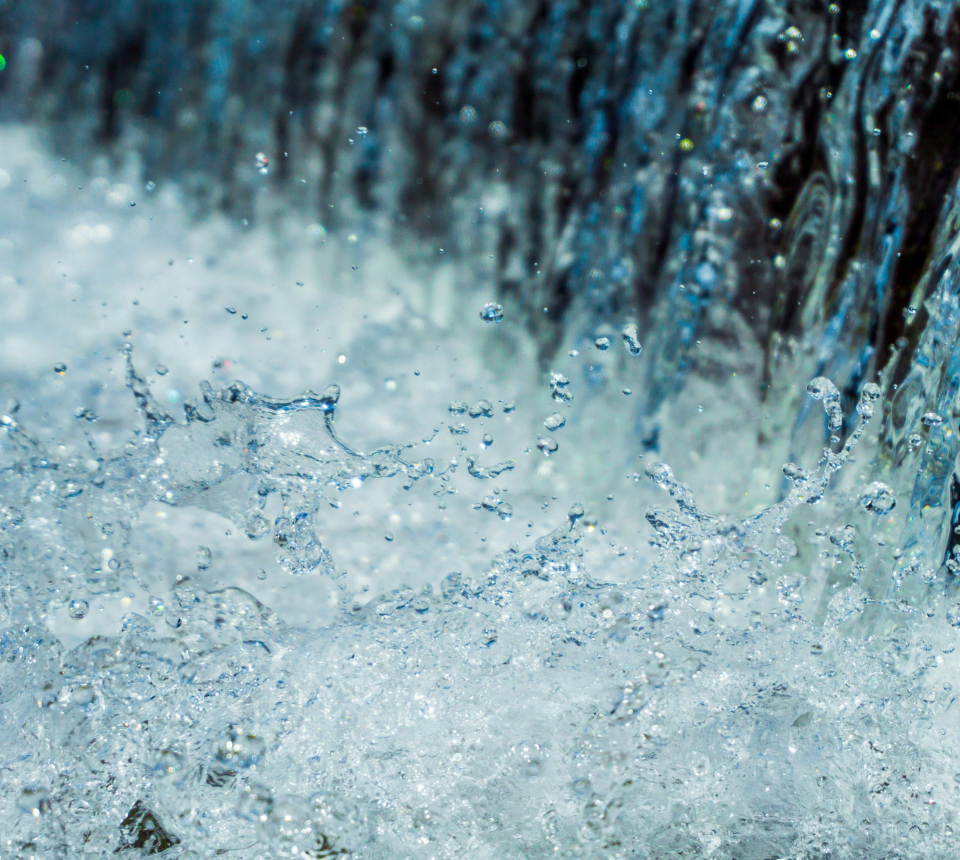
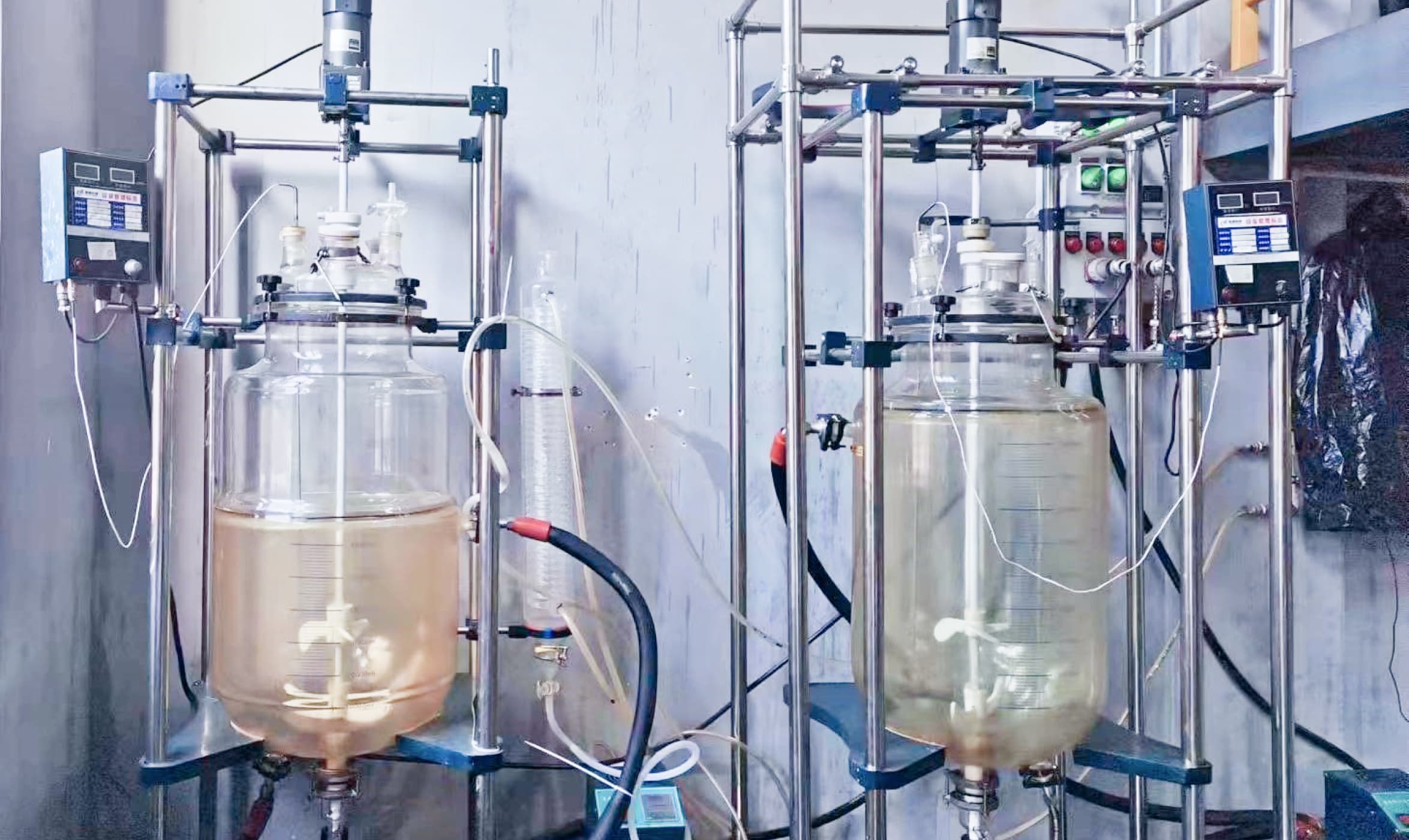
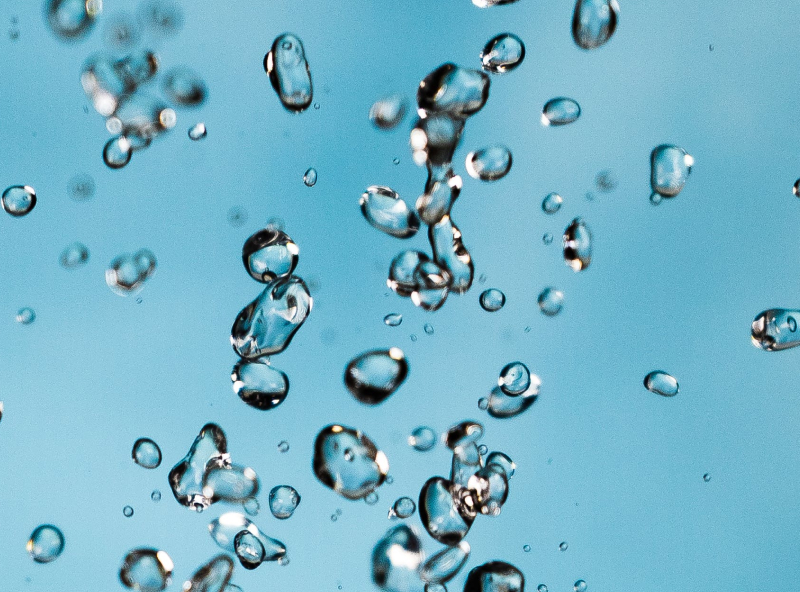
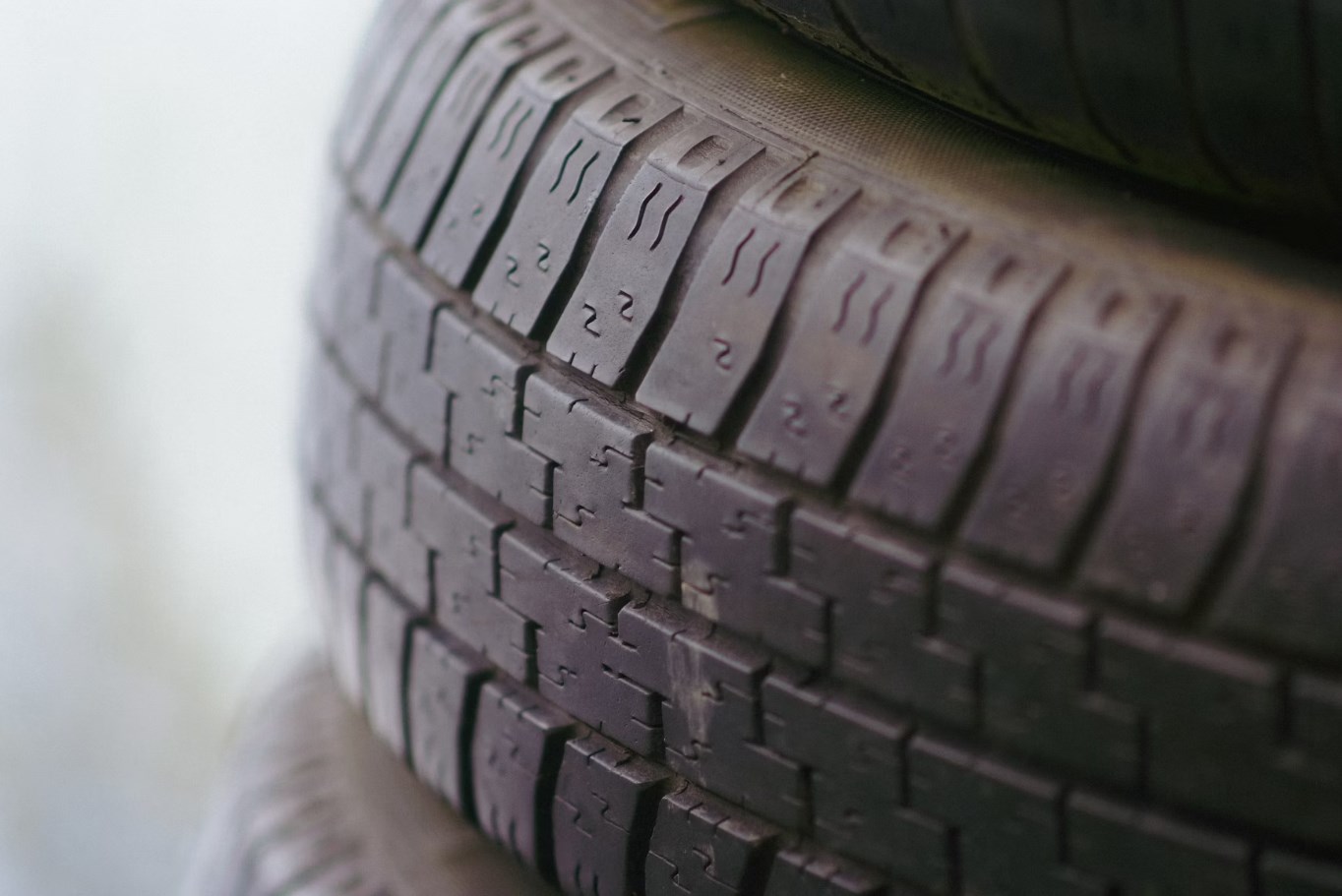
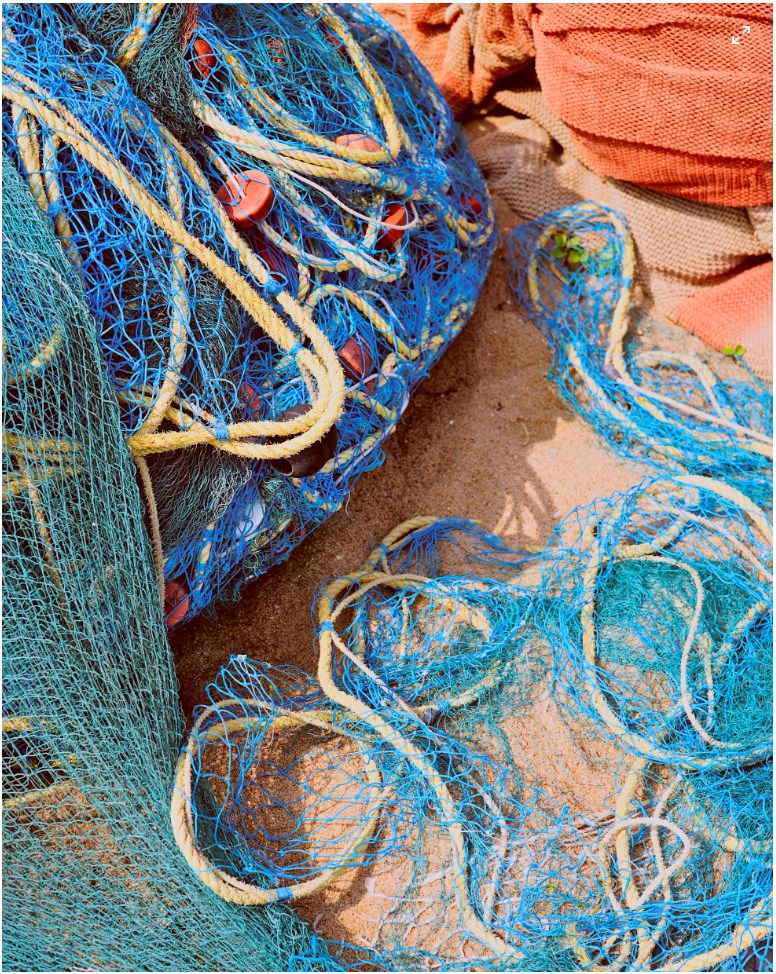
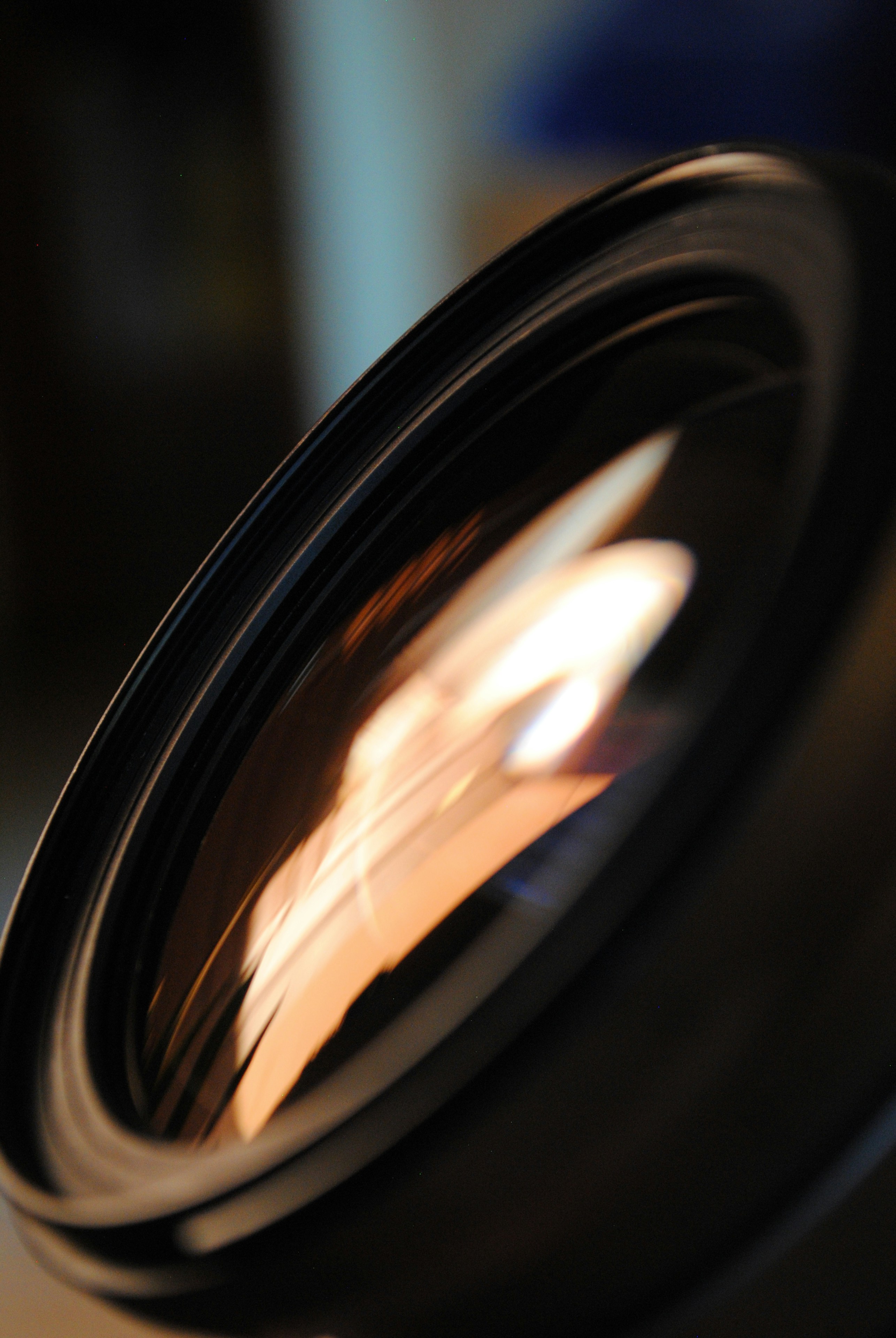
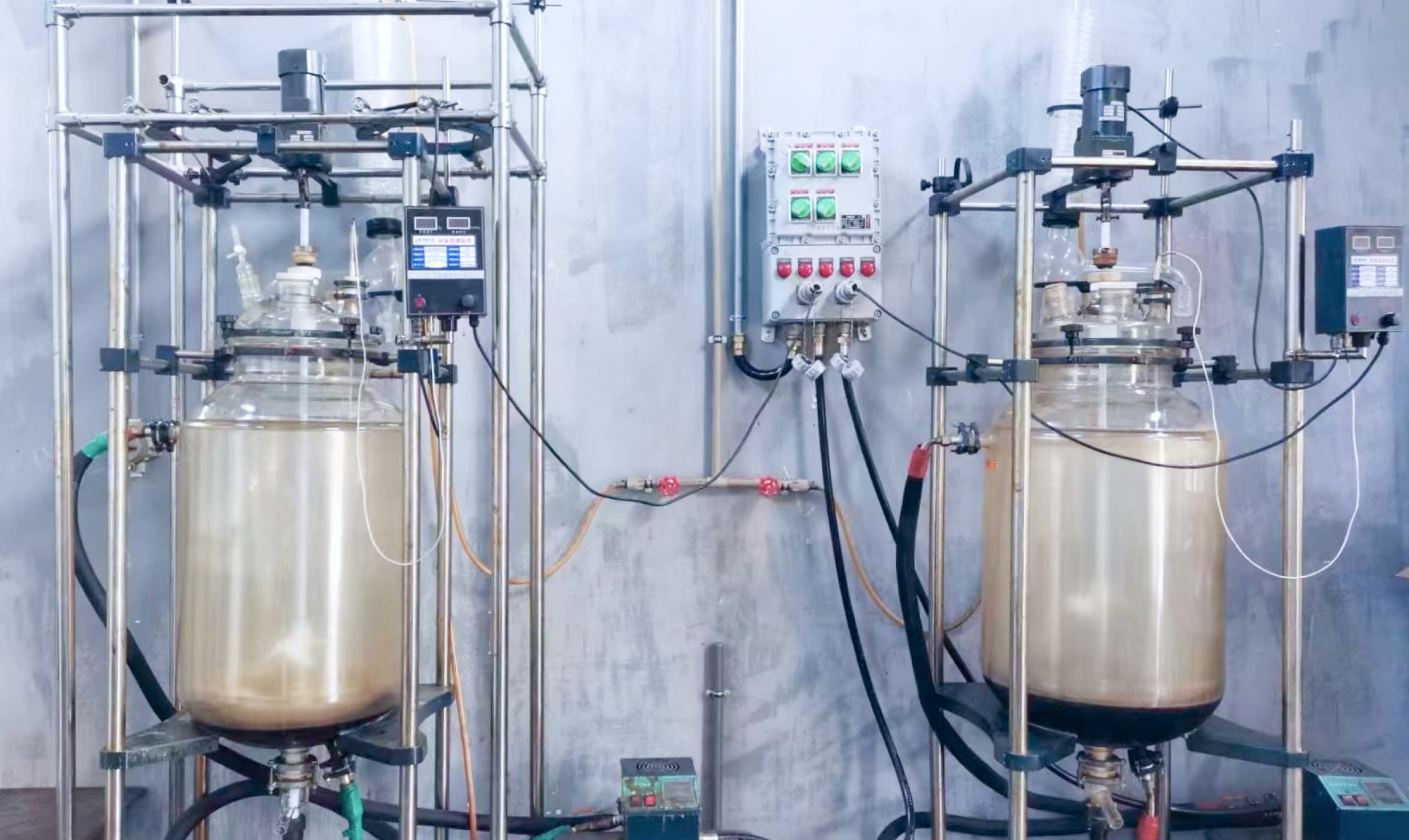
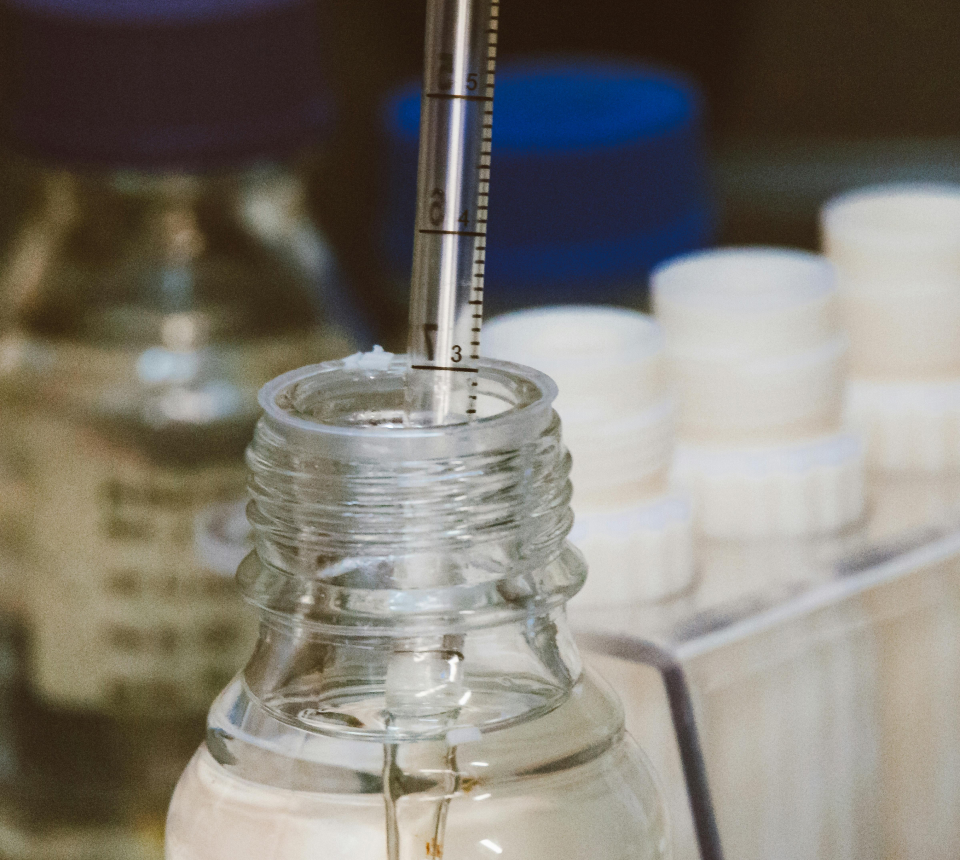
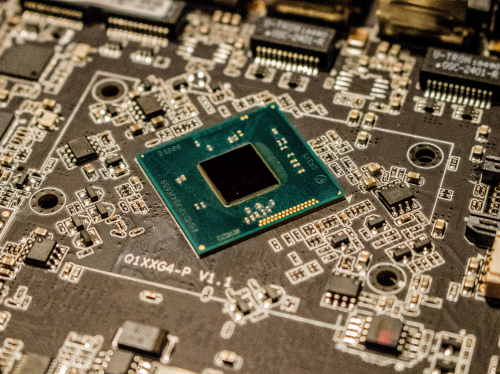
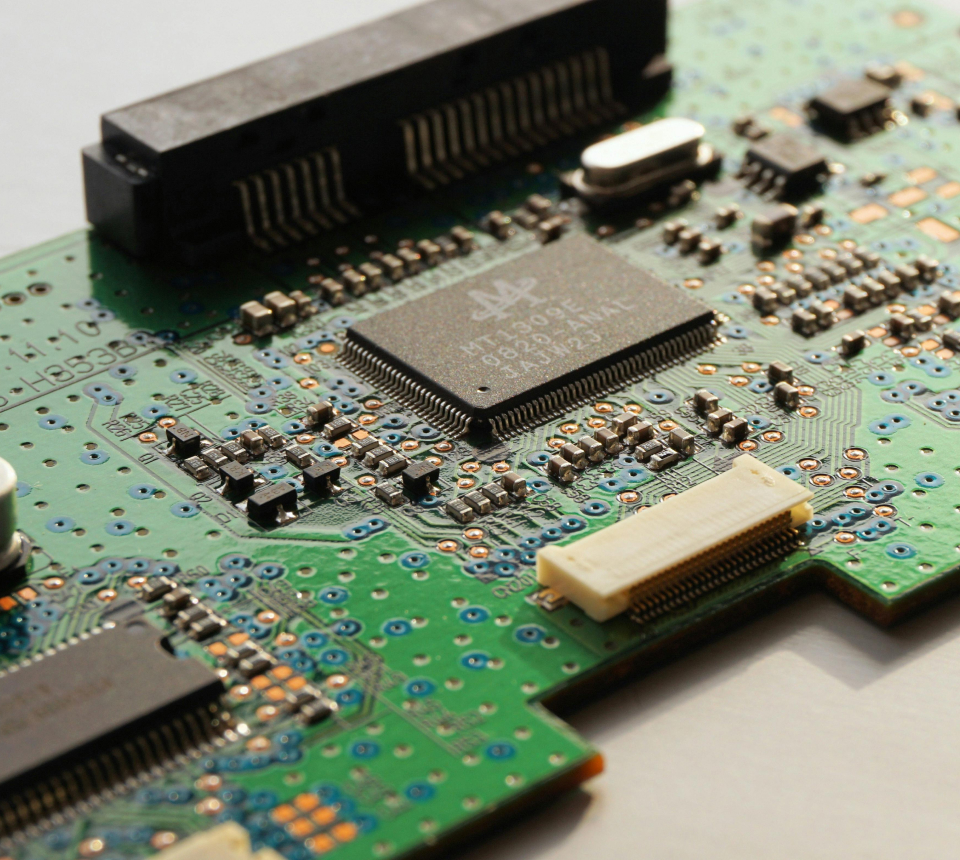
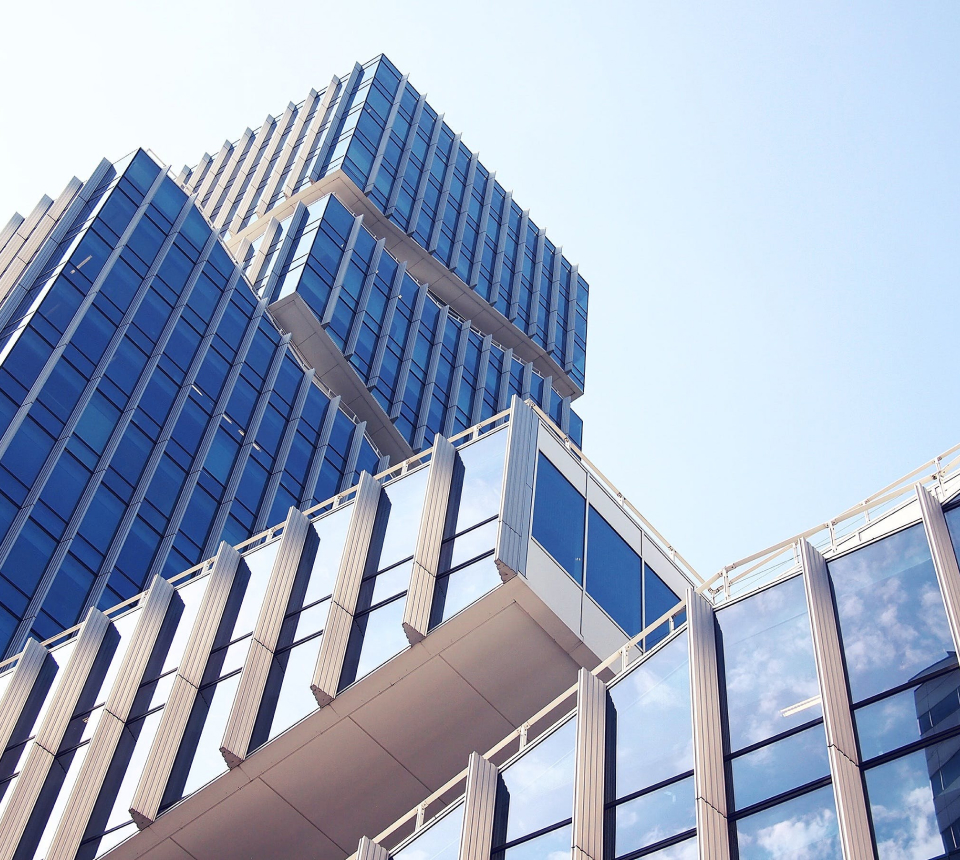
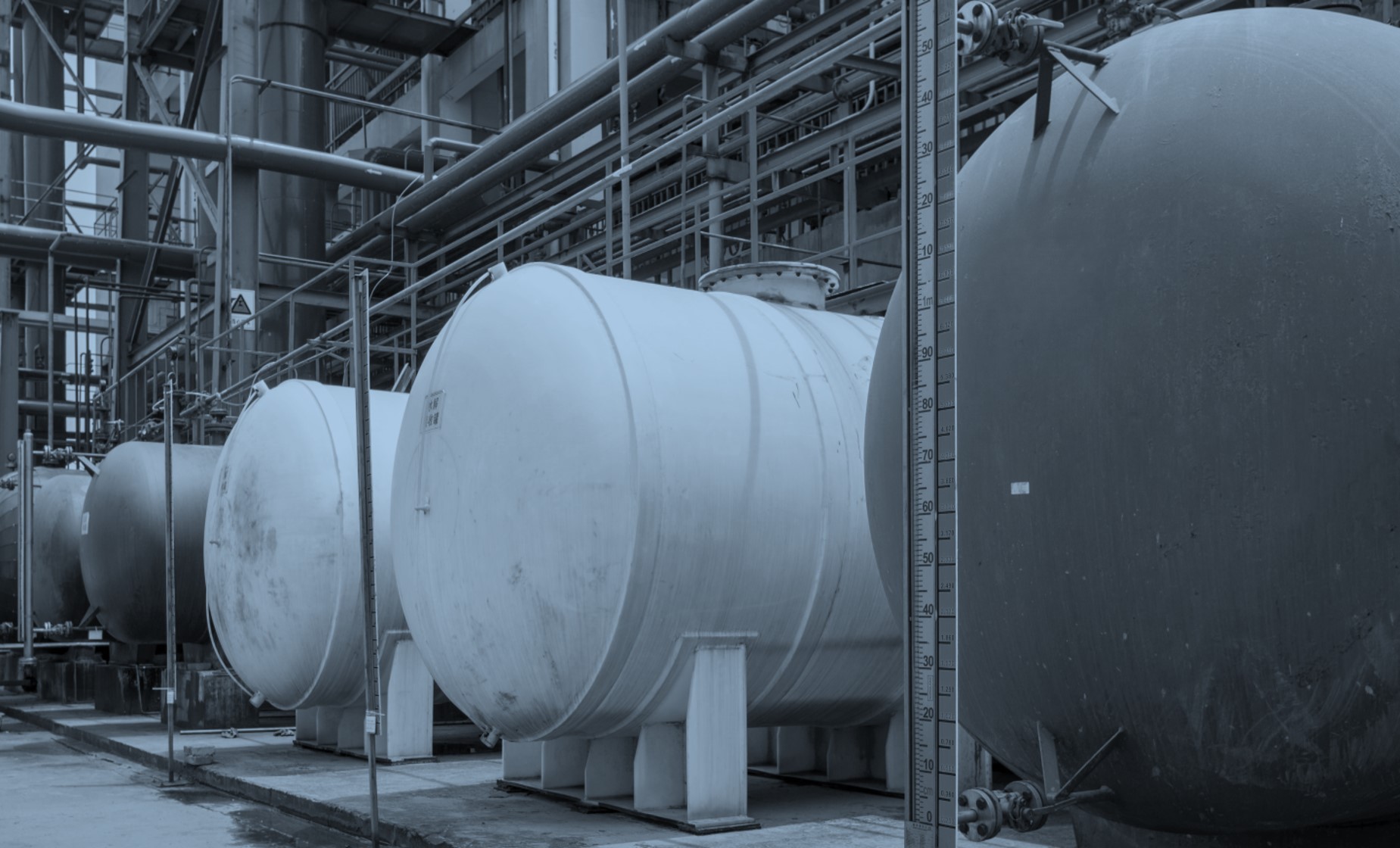
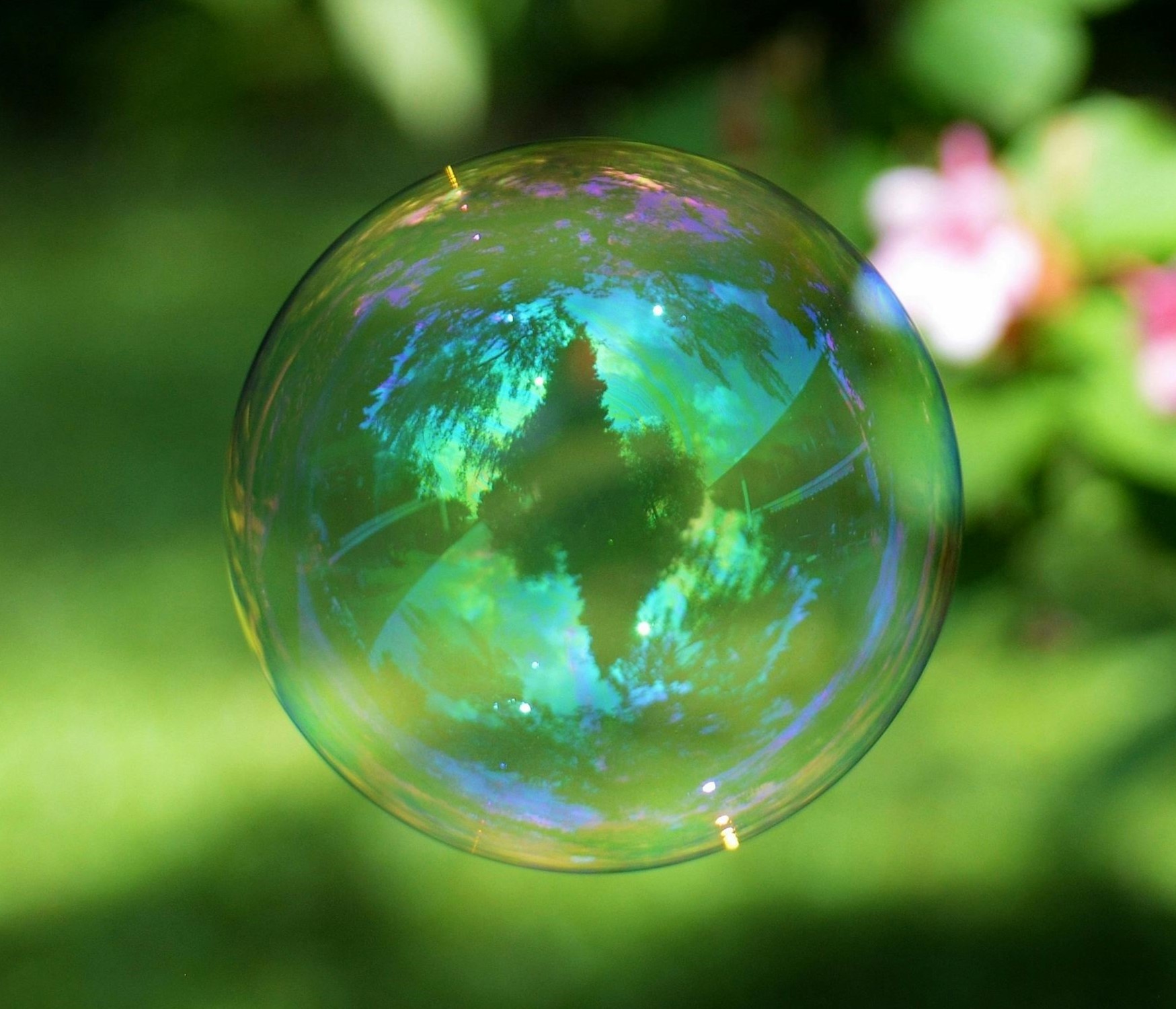
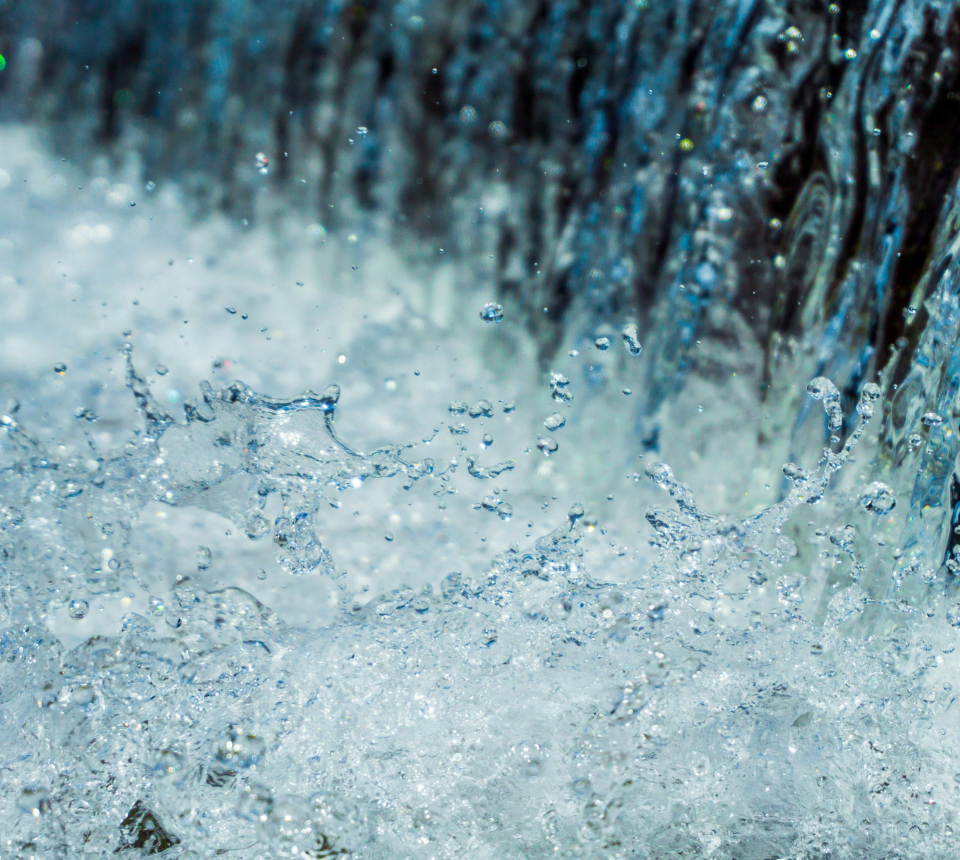
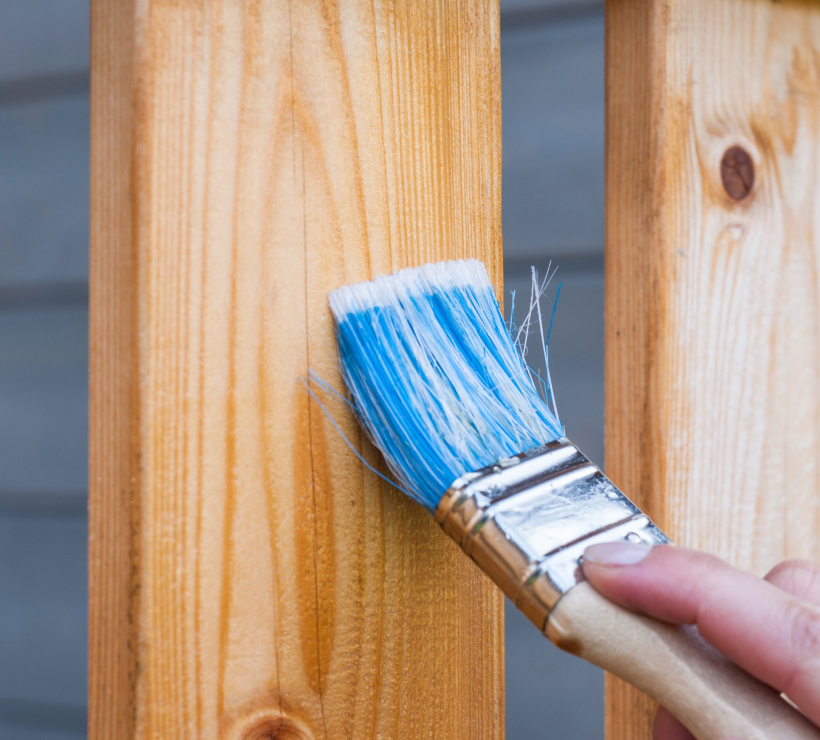

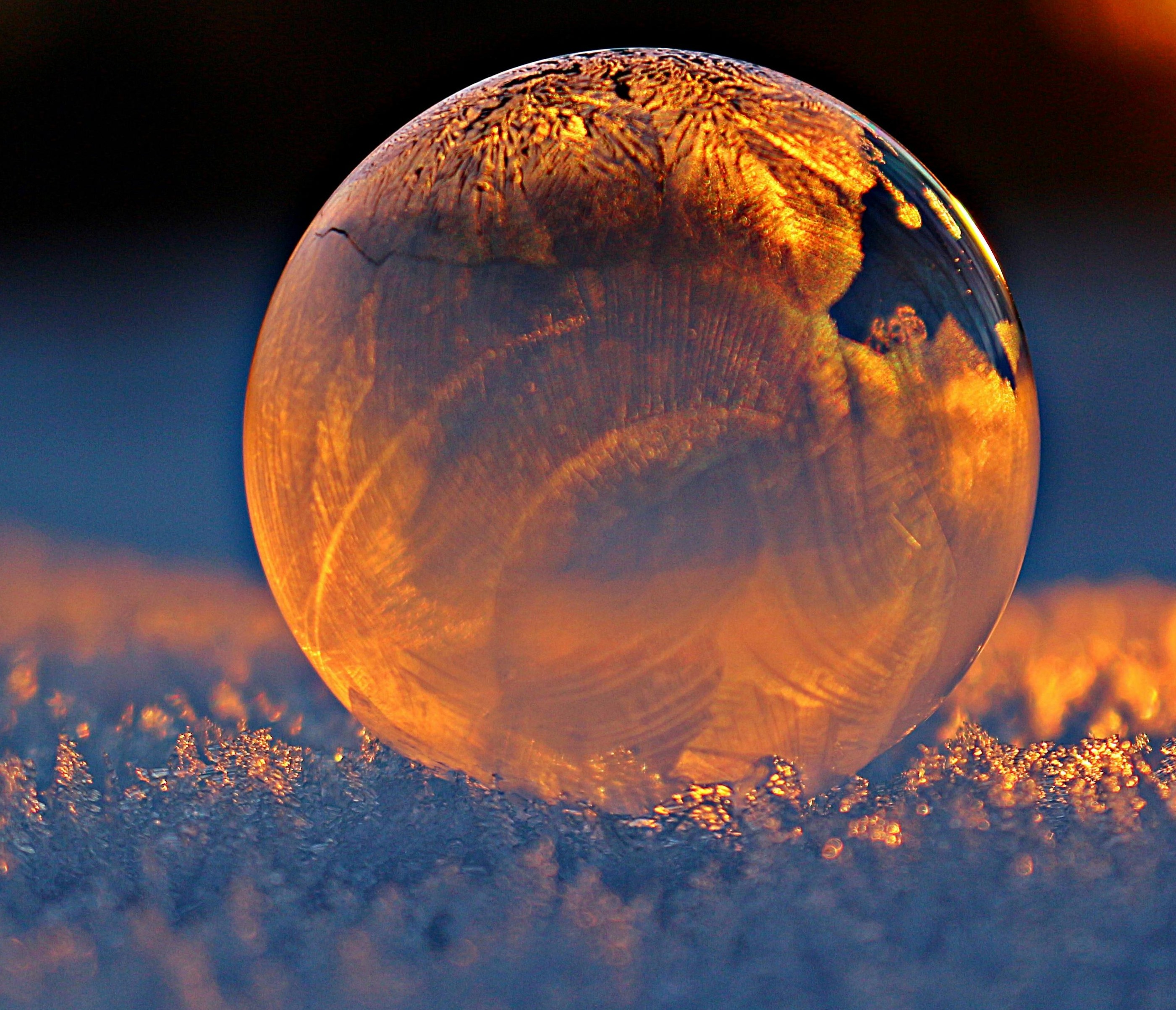
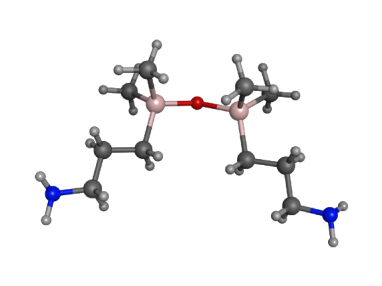
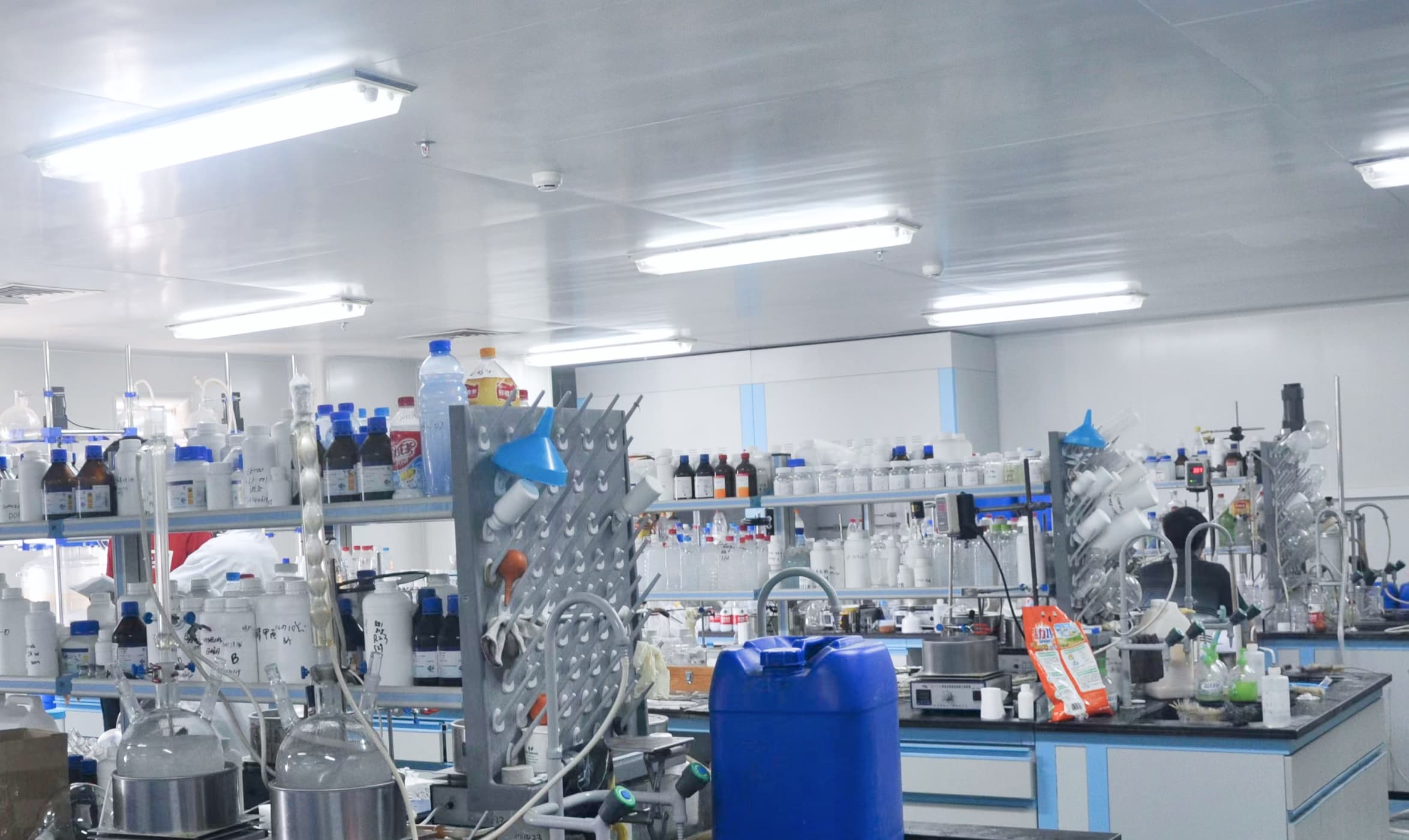
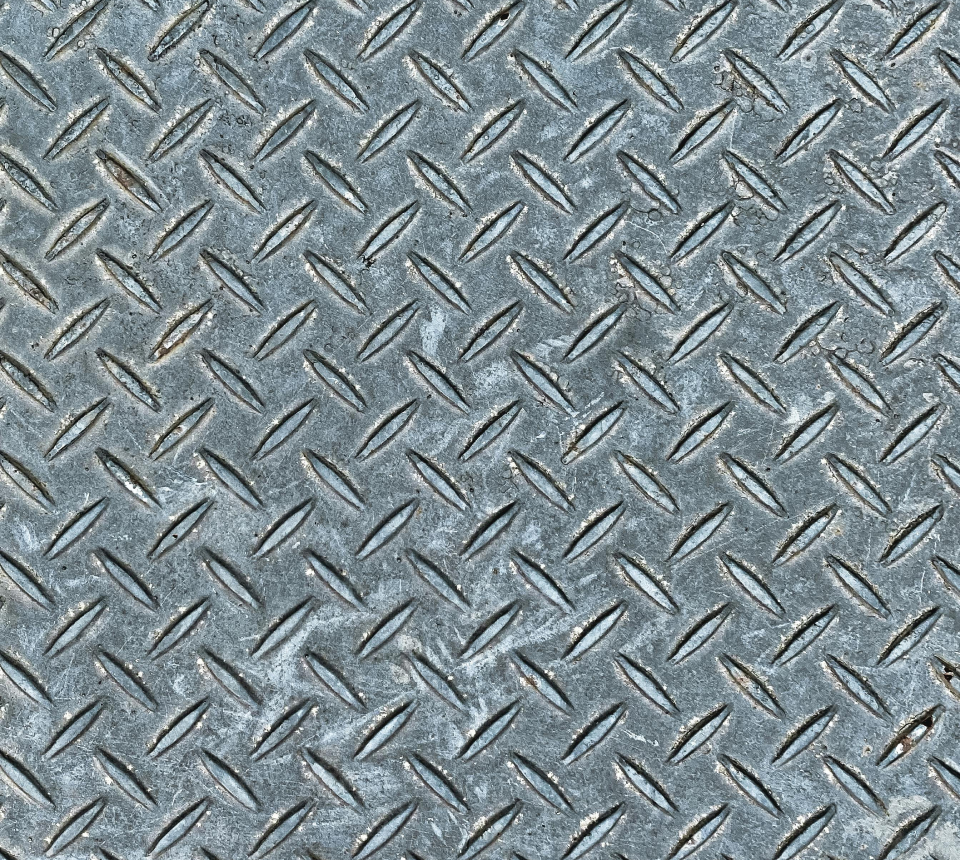
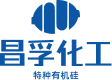
+86 27 8439 6550
+86 181 6277 0058
sales@cfsilanes.com
Optics Valley Bio-City
No. 666, Gaoxin Avenue
Hongshan District, Wuhan City
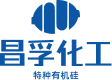
+86 27 8439 6550 | +86 181 6277 0058
sales@cfsilanes.com
Optics Valley Bio-City
No. 666, Gaoxin Avenue
Hongshan District, Wuhan City
Copyright © Hubei ChangFu Chemical Co., Ltd. All Rights