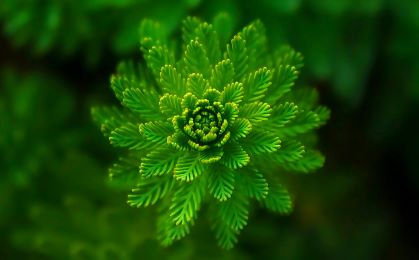
Contact Changfu Chemical Now!
+86 27 8439 6550 | +86 181 6277 0058
Understanding Two Types of Silicone Chemical Compounds: Silicon Coatings, and Silicone Defoamers
Silicone chemicals are a diverse group of synthetic materials made from silicon, oxygen, carbon, and hydrogen. Known for their unique properties, such as heat resistance, water repellence, and flexibility, they have become indispensable in a variety of industrial applications. This blog delves into the world of silicone chemicals, exploring their applications in silicon coatings and silicone defoamers, two critical products that leverage the properties of silicone to enhance performance in various industries.
What is Silicone Chemicals?
Silicone chemicals are a class of synthetic compounds that combine the elemental properties of silicon with organic functional groups. They are incredibly versatile, finding applications in everything from cosmetics to aerospace engineering. The backbone of a silicone chemical is a repeating siloxane unit, consisting of alternating silicon and oxygen atoms, typically modified with organic groups like methyl or vinyl.
1 The Basic Chemistry of Silicone
At the heart of silicone chemistry is the element silicon, which is the second most abundant element in the Earth's crust. Silicon's ability to form strong bonds with oxygen, carbon, and hydrogen makes it a perfect candidate for creating stable, flexible, and resilient materials. The siloxane backbone (Si-O-Si) is the defining feature of silicone chemistry, giving rise to its characteristic properties, such as thermal stability and resistance to environmental degradation.
2 Properties of Silicone Chemicals
Silicone chemicals possess a range of beneficial properties:
- Thermal Stability: They remain stable across a wide temperature range (-60°C to 300°C).
- Water Repellence: Silicones are hydrophobic, making them ideal for waterproofing applications.
- Chemical Inertness: They are resistant to chemical attack, ensuring longevity in harsh environments.
- Flexibility: Silicones retain their elasticity even at extreme temperatures.
- Low Surface Tension: This makes them excellent candidates for spreading and wetting agents.
Silicon Coatings: An Overview
Silicon coatings, which are derived from silicone chemicals, are thin layers applied to surfaces to impart specific properties like water repellence, thermal stability, or electrical insulation. These coatings are extensively used in industries ranging from construction to electronics.
Types of Silicon Coatings
There are several types of silicon-based coatings, each designed for specific applications:
- Silicone Elastomers: These are rubber-like materials used for flexible, durable coatings.
- Silicone Resins: Often used in paints and varnishes, they provide excellent heat resistance and durability.
- Silicone Oils: These are used as lubricants and release agents due to their stability and non-reactivity.
Applications of Silicon Coatings
Silicon coatings are applied in various industries due to their multifunctional properties:
- Construction: Silicon coatings are used to protect building facades, seal joints, and waterproof surfaces. Their UV resistance and durability make them ideal for long-term applications.
- Electronics: In the electronics industry, silicon coatings provide insulation, moisture protection, and thermal management. They are commonly used in circuit boards, sensors, and other sensitive components.
- Automotive: Silicon coatings are applied to engine components, seals, and gaskets to improve durability and performance under extreme conditions.
- Textiles: They are used to create water-repellent fabrics and enhance the durability of outdoor clothing.
Advantages of Using Silicon Coatings
Silicon coatings offer several advantages over traditional coatings:
- Enhanced Durability: Silicon coatings are resistant to weathering, UV radiation, and chemical attack, ensuring a longer lifespan for the coated material.
- Thermal Resistance: These coatings can withstand high temperatures without degrading, making them suitable for high-heat applications.
- Environmental Resistance: Silicon coatings resist oxidation and corrosion, protecting underlying materials from environmental damage.
- Electrical Insulation: They provide excellent insulation, reducing the risk of short circuits and improving the safety of electronic devices.
Silicone Defoamers: Function and Applications
Silicone defoamers are chemical additives used to reduce and prevent foam formation in industrial processes. Foam can be problematic in various applications, leading to inefficiencies, product defects, and equipment malfunctions.
1 What are Silicone Defoamers?
Silicone defoamers are a type of antifoam agent that contain silicone compounds, typically in the form of silicone oils or emulsions. Their low surface tension allows them to spread rapidly across foam surfaces, breaking down bubbles and preventing new ones from forming.
2 How Silicone Defoamers Work
The effectiveness of silicone defoamers lies in their ability to disrupt the stability of foam. When added to a foaming liquid, the silicone defoamer spreads across the liquid’s surface, causing the foam bubbles to thin out and collapse. This is particularly useful in processes where foam can cause problems, such as in water treatment, chemical manufacturing, and food processing.
3 Applications of Silicone Defoamers
Silicone defoamers are used in a wide range of industries:
- Water Treatment: In water treatment plants, foam can hinder the efficiency of filtration systems and lead to overflow. Silicone defoamers quickly reduce foam, ensuring smooth operation.
- Chemical Manufacturing: During chemical reactions, foam can impede the mixing process, leading to incomplete reactions or product contamination. Silicone defoamers help maintain process integrity.
- Food and Beverage Industry: In food processing, excessive foam can affect the quality and appearance of products. Silicone defoamers are used in processes like fermentation and brewing to control foam levels.
- Paper and Pulp Industry: Foam can cause defects in paper products and disrupt manufacturing processes. Silicone defoamers help produce smooth, high-quality paper.
- Oil and Gas Industry: In drilling operations, foam can cause operational delays and equipment damage. Silicone defoamers ensure efficient drilling by controlling foam in drilling fluids.
4 Benefits of Using Silicone Defoamers
The use of silicone defoamers provides several benefits:
- Efficiency: They act quickly to reduce foam, minimizing downtime and improving process efficiency.
- Versatility: Silicone defoamers are effective in a wide range of temperatures and pH levels, making them suitable for diverse applications.
- Non-Toxic: Many silicone defoamers are non-toxic and can be used safely in food and beverage processing.
- Long-Lasting: They provide long-lasting foam control, reducing the need for frequent reapplication and lowering operational costs.
Comparative Analysis: Silicon Coatings vs. Silicone Defoamers
While both silicon coatings and silicone defoamers are derived from silicone chemicals, they serve very different purposes and have unique properties suited to their specific applications.
1 Composition and Functionality
Silicon Coatings: These are solid or semi-solid layers applied to surfaces to provide protection, insulation, or enhancement of specific properties. They are designed to remain on the surface and interact with the environment to protect the substrate.
Silicone Defoamers: These are liquid or semi-liquid additives introduced into a system to reduce or eliminate foam. They work by interacting with the foam at a molecular level to destabilize and collapse bubbles.
2 Applications and Industry Use
Silicon Coatings: Widely used in industries that require long-term surface protection, such as construction, automotive, and electronics. Their role is to enhance the durability and performance of materials by providing a protective barrier.
Silicone Defoamers: Primarily used in process industries, such as chemical manufacturing, food and beverage, and water treatment. Their main function is to improve process efficiency by controlling foam, which can cause operational disruptions.
3 Key Benefits
Silicon Coatings:
Provide long-lasting protection and durability.
Enhance aesthetic appeal and surface quality.
Offer resistance to environmental factors like UV radiation and chemical exposure.
Silicone Defoamers:
Improve process efficiency and product quality.
Reduce downtime and operational costs.
Are effective across a broad range of conditions and applications.
Innovations in Silicone Chemistry
The field of silicone chemistry is continuously evolving, with new innovations and applications emerging across various industries. These advancements are driven by the unique properties of silicone chemicals and the growing demand for materials that can perform under extreme conditions.
1 Advances in Silicon Coatings
Recent innovations in silicon coatings have focused on enhancing their environmental performance and expanding their application range:
- Eco-Friendly Coatings: Development of silicon coatings with reduced VOC (Volatile Organic Compounds) emissions to meet environmental regulations.
- Smart Coatings: Integration of sensors and other technologies into silicon coatings to create "smart" surfaces that can respond to environmental changes, such as temperature or humidity.
- Advanced Protective Coatings: Creation of silicon coatings with enhanced resistance to corrosion, abrasion, and chemical exposure, making them suitable for harsh industrial environments.
2 Breakthroughs in Silicone Defoamers
In the realm of silicone defoamers, innovation is focused on improving efficiency and expanding usability:
- High-Efficiency Defoamers: Development of defoamers with improved spreading properties, allowing for faster and more effective foam control with lower concentrations.
- Biodegradable Defoamers: Creation of defoamers that break down more easily in the environment, reducing their ecological impact.
- Customizable Formulations: Tailoring defoamer formulations to meet the specific needs of different industries, such as food-safe defoamers for the beverage industry or high-temperature defoamers for oil and gas.
The Future of Silicone Chemicals
The future of silicone chemicals looks promising, with ongoing research and development aimed at enhancing their performance and expanding their applications. As industries continue to demand materials that can withstand extreme conditions and deliver superior performance, silicone chemicals will play an increasingly important role.
1 Sustainability in Silicone Chemistry
One of the key trends driving the future of silicone chemicals is sustainability. Manufacturers are increasingly focusing on developing silicone products that are not only high-performing but also environmentally friendly:
Recyclable Silicones: Research is being conducted to create silicones that can be more easily recycled at the end of their life cycle, reducing waste and environmental impact.
Green Manufacturing Processes: Efforts are being made to reduce the environmental footprint of silicone production through the use of renewable energy sources and more efficient manufacturing processes.
Biodegradable Silicones: The development of biodegradable silicones is an area of active research, with the potential to create materials that break down more easily in the environment.
2 Expanding Applications
As the properties of silicone chemicals continue to be explored and optimized, new applications are likely to emerge:
Healthcare: Silicones are already used in medical devices, implants, and wound care products. Future developments may include advanced drug delivery systems and tissue engineering applications.
Renewable Energy: Silicone coatings and defoamers could play a role in the development of renewable energy technologies, such as wind turbines and solar panels, by improving durability and efficiency.
Advanced Electronics: The electronics industry is likely to see increased use of silicone chemicals in the development of flexible, lightweight, and durable components for next-generation devices.
Conclusion
Silicone chemicals, including silicon coatings and silicone defoamers, represent a significant advancement in material science. Their unique properties and versatility make them indispensable in a wide range of industries. As research and innovation continue, we can expect to see even more sophisticated applications and environmentally friendly solutions emerge from this fascinating field of chemistry.
Whether it’s providing durable, weather-resistant coatings for buildings or ensuring the smooth operation of industrial processes by eliminating foam, silicone chemicals are at the forefront of modern industrial advancements. Their role in enhancing efficiency, protecting materials, and contributing to sustainability will only grow as industries continue to push the boundaries of what these remarkable compounds can achieve.
Popular Silicon Compounds
Popular Silicon Compounds
Related News & Blog
Related News & Blog
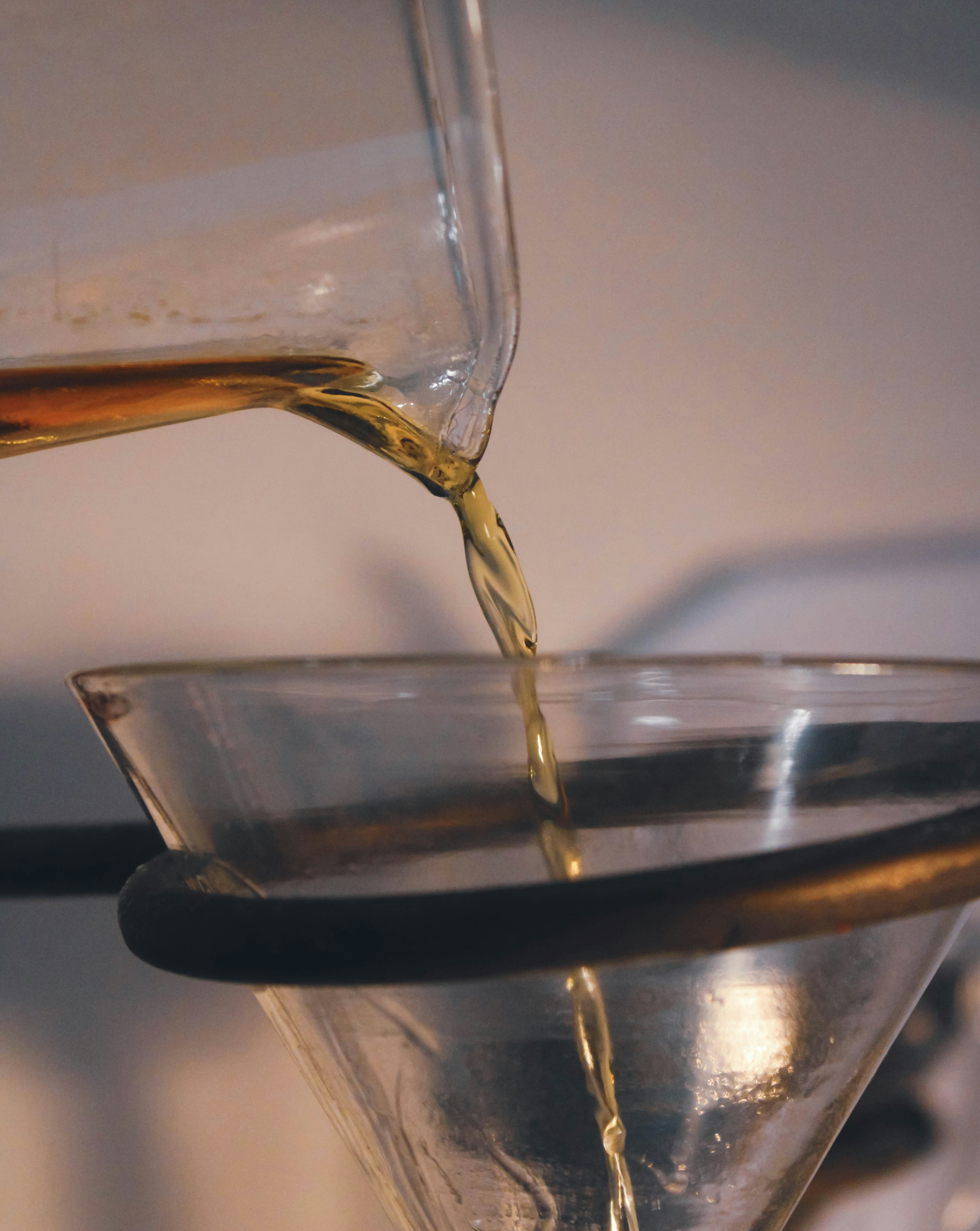
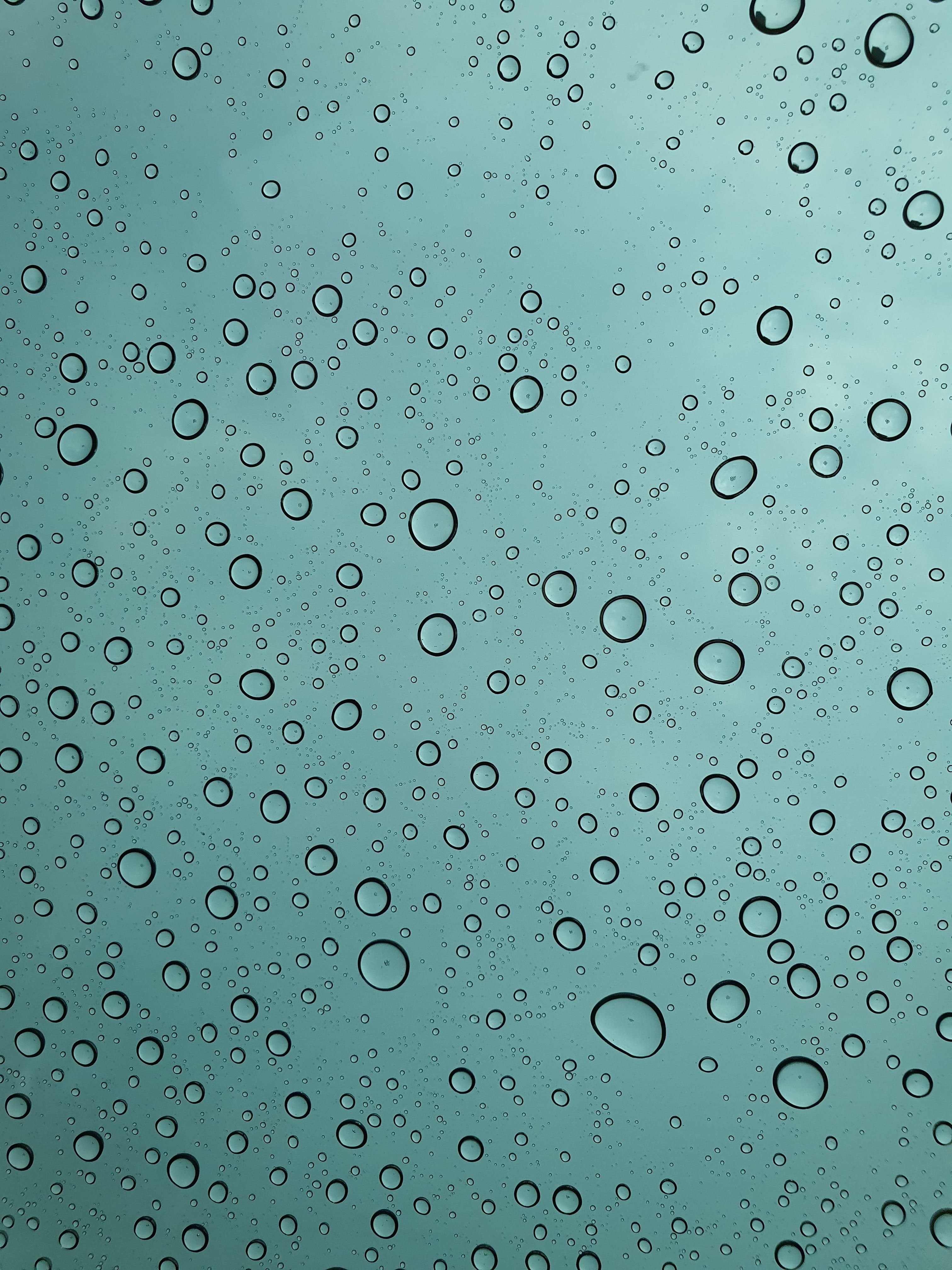
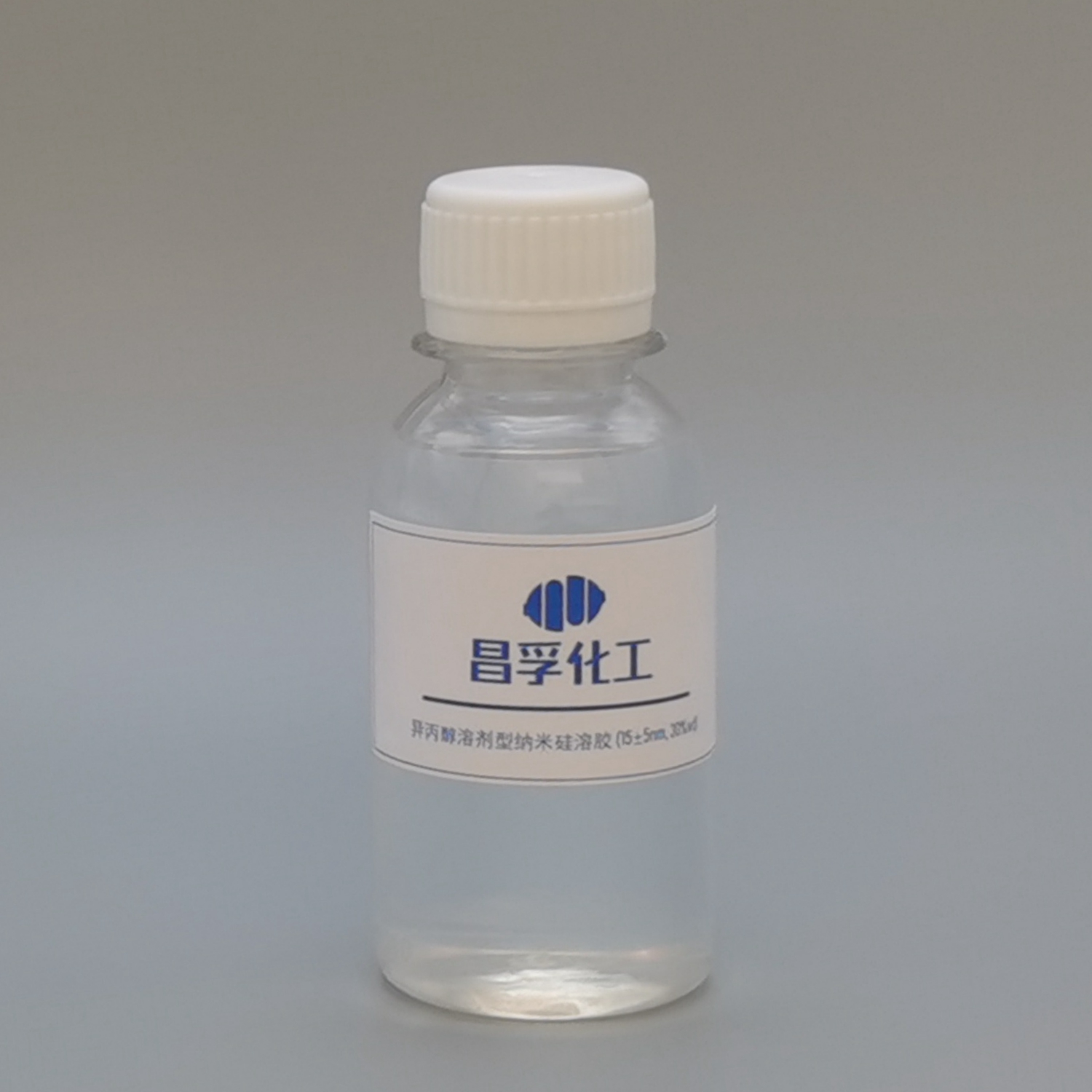
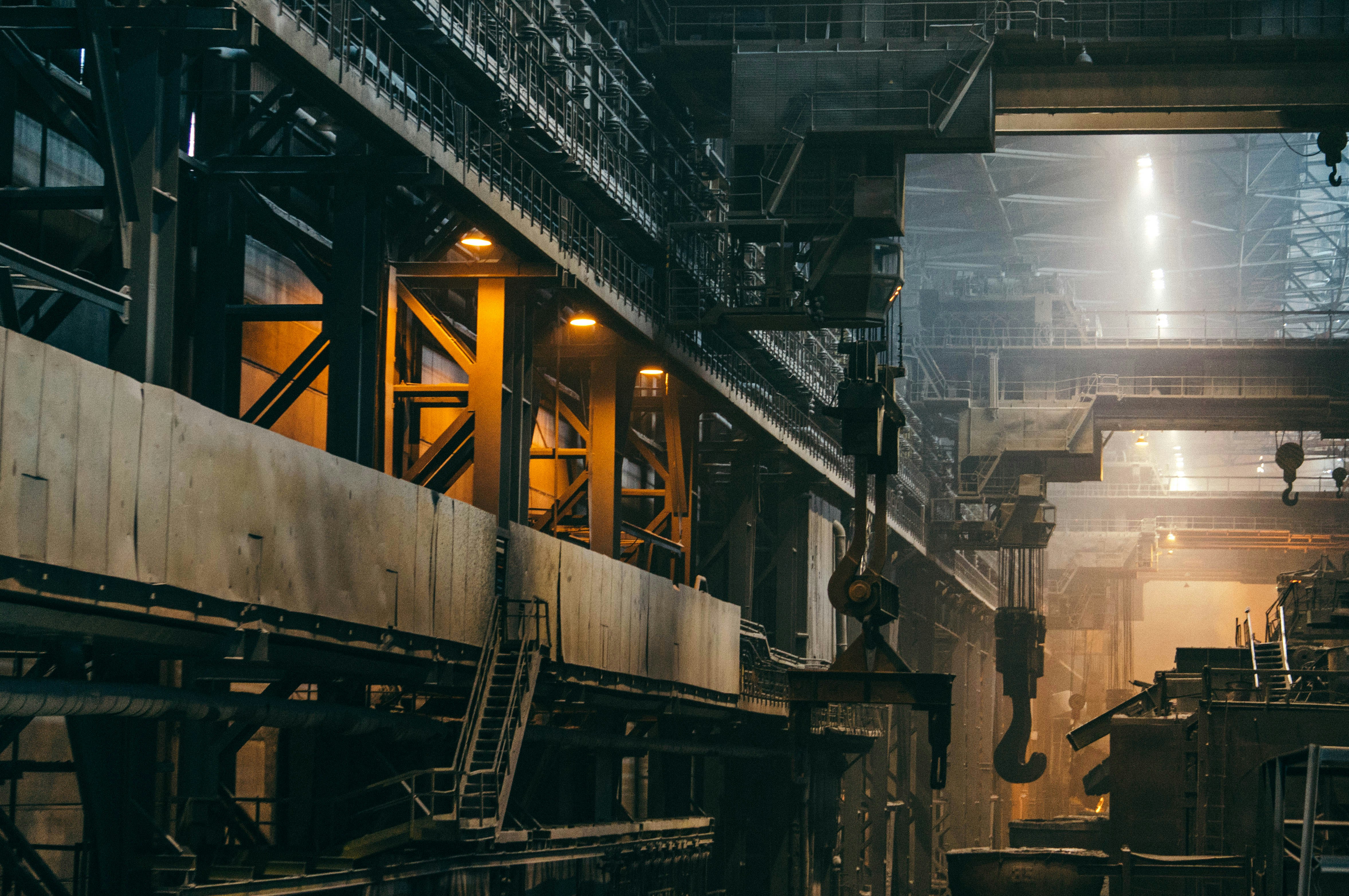
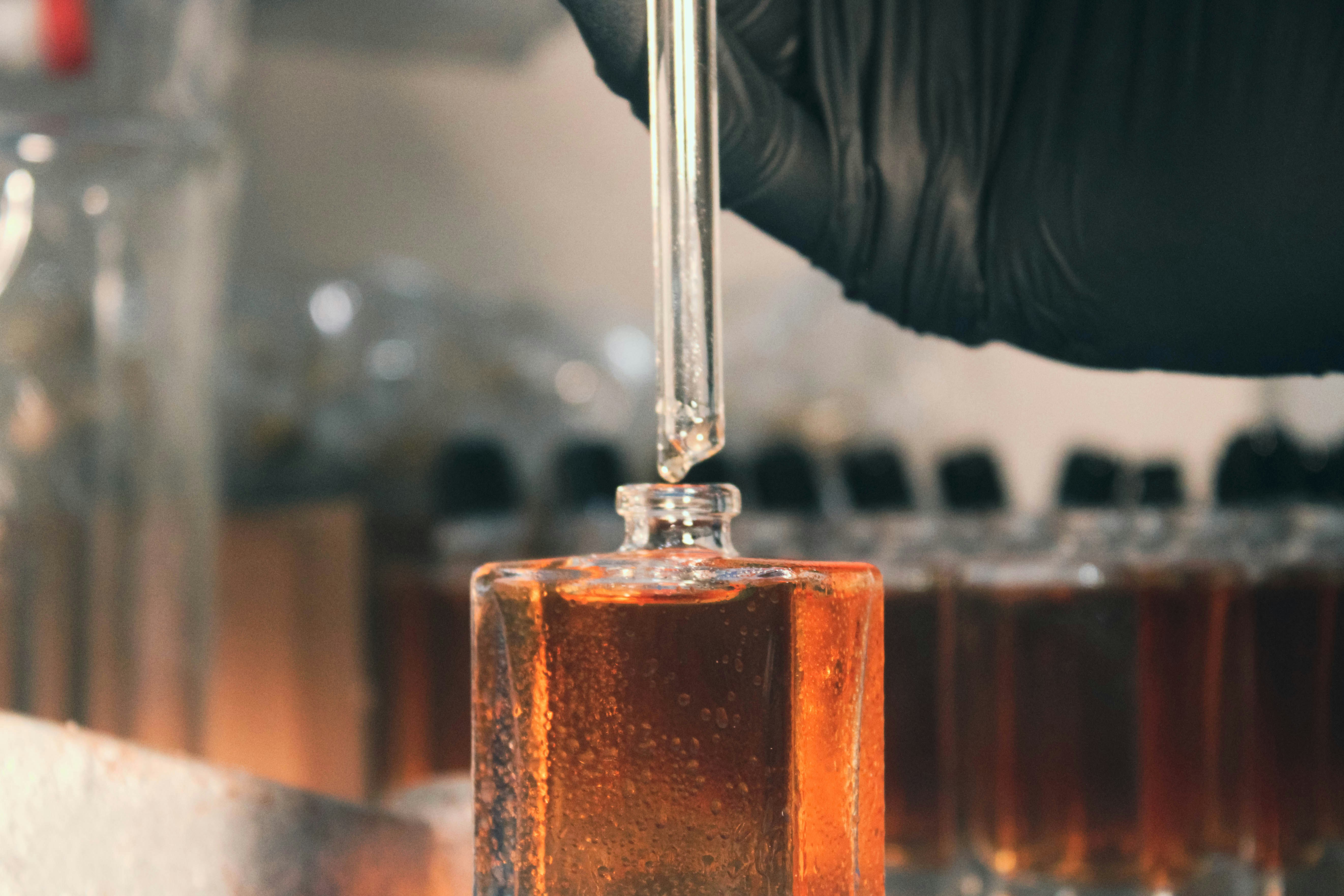
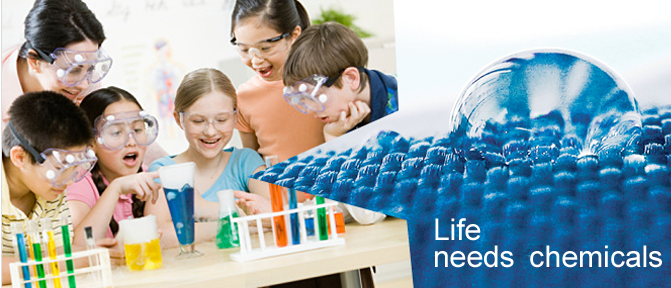

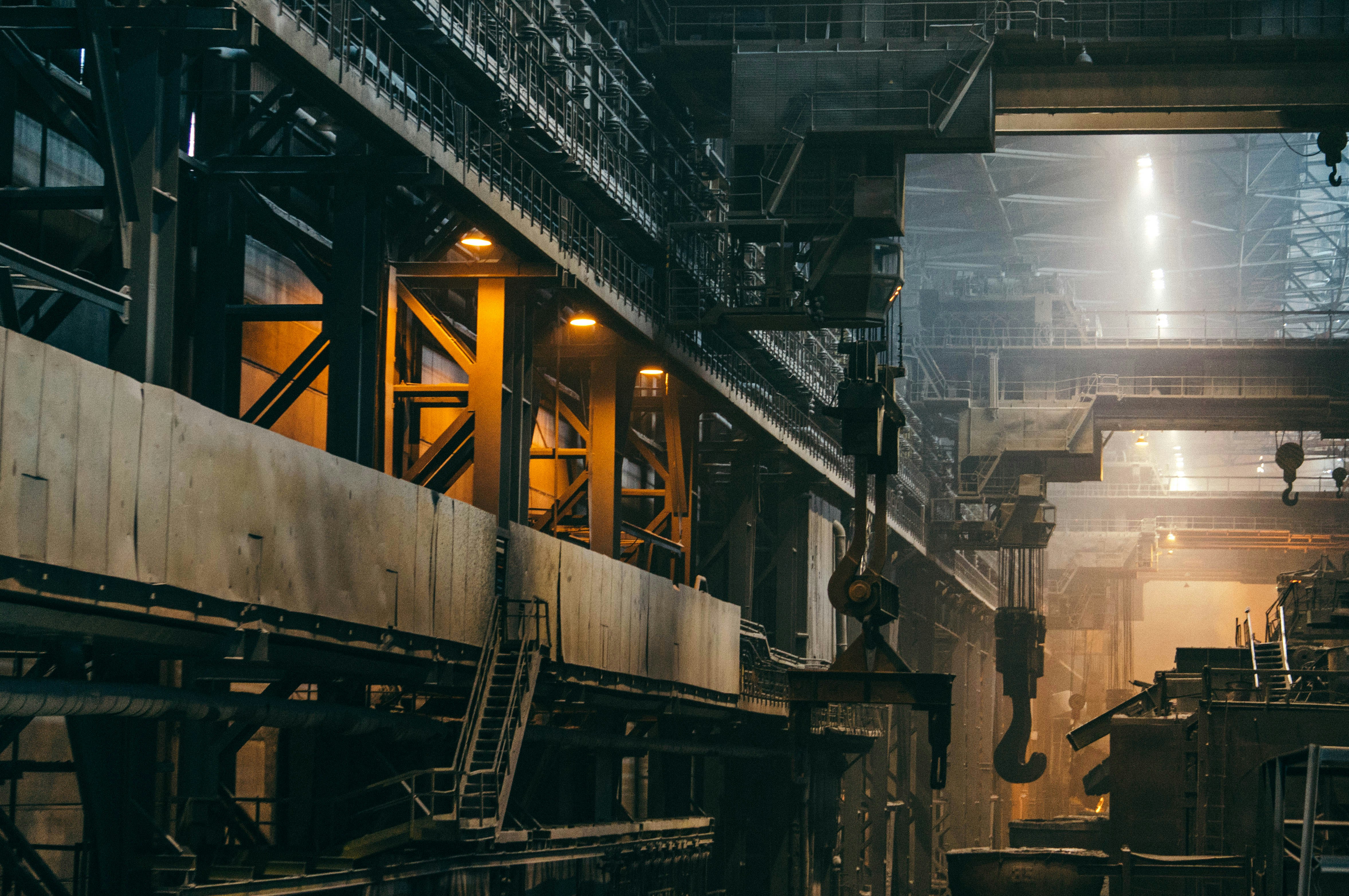
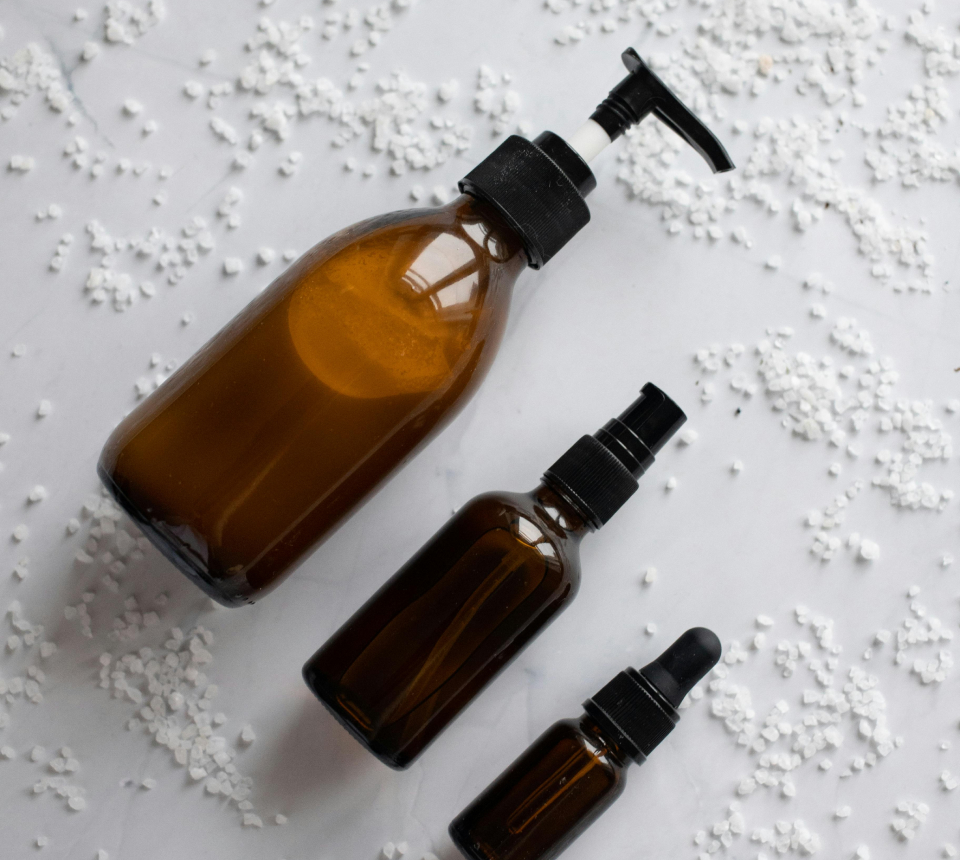
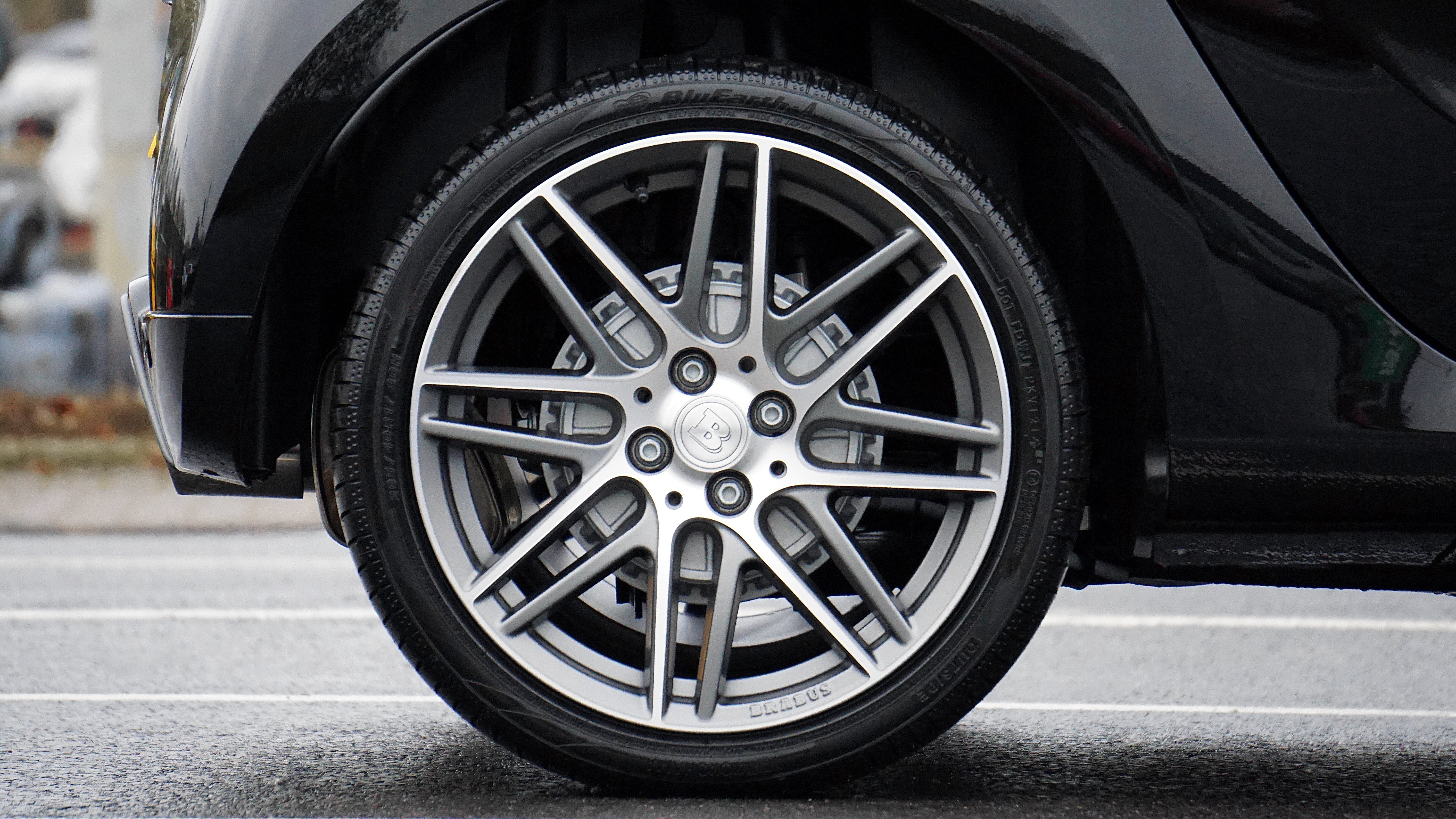
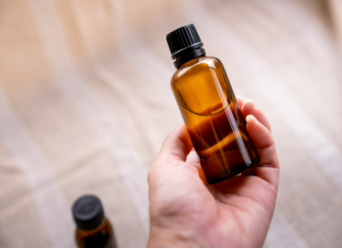
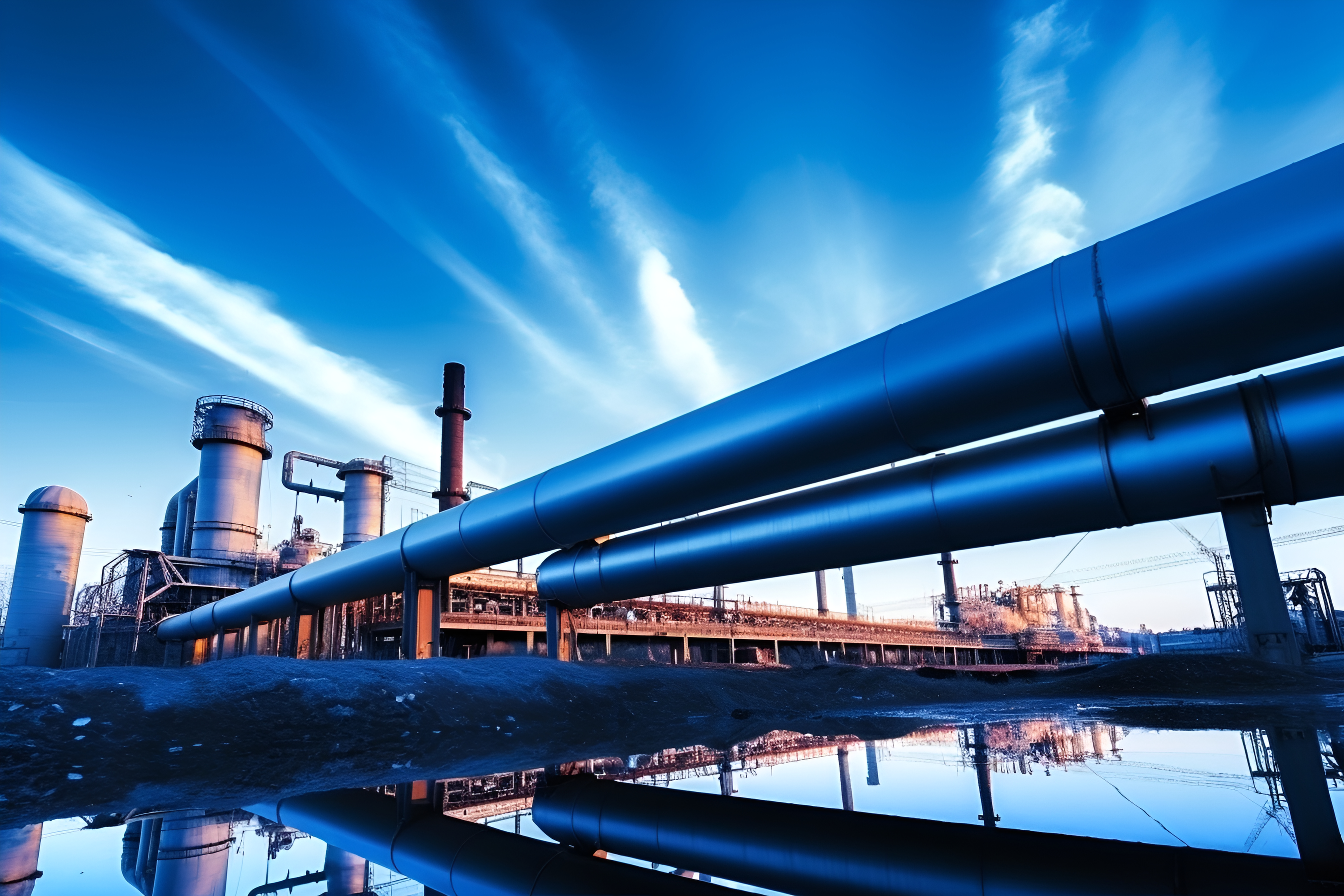

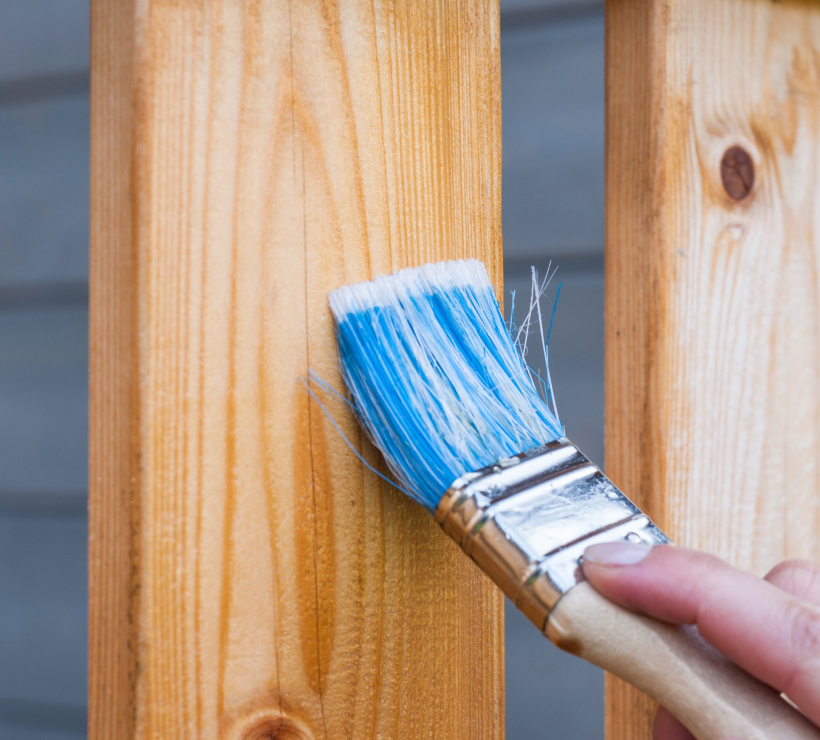
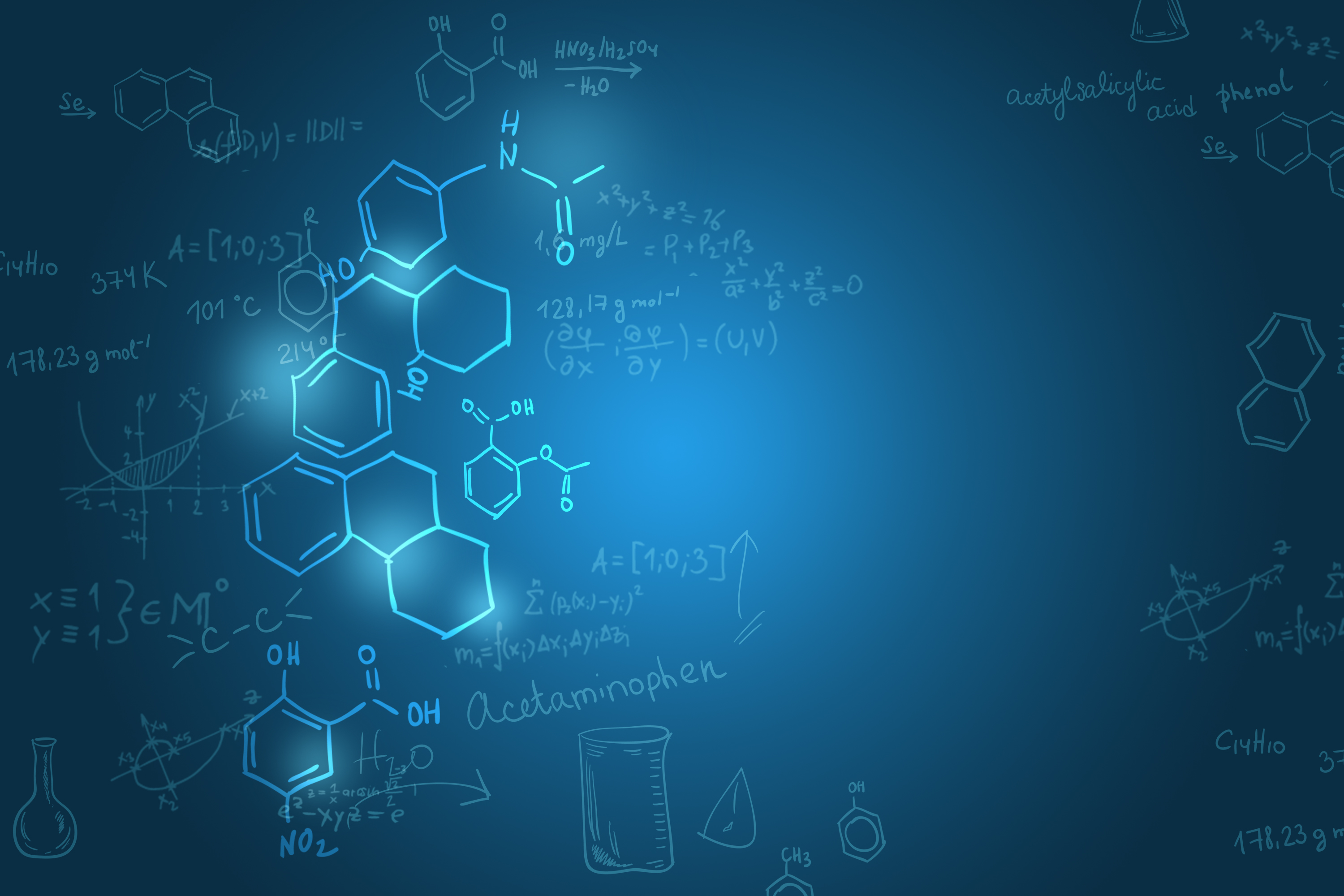
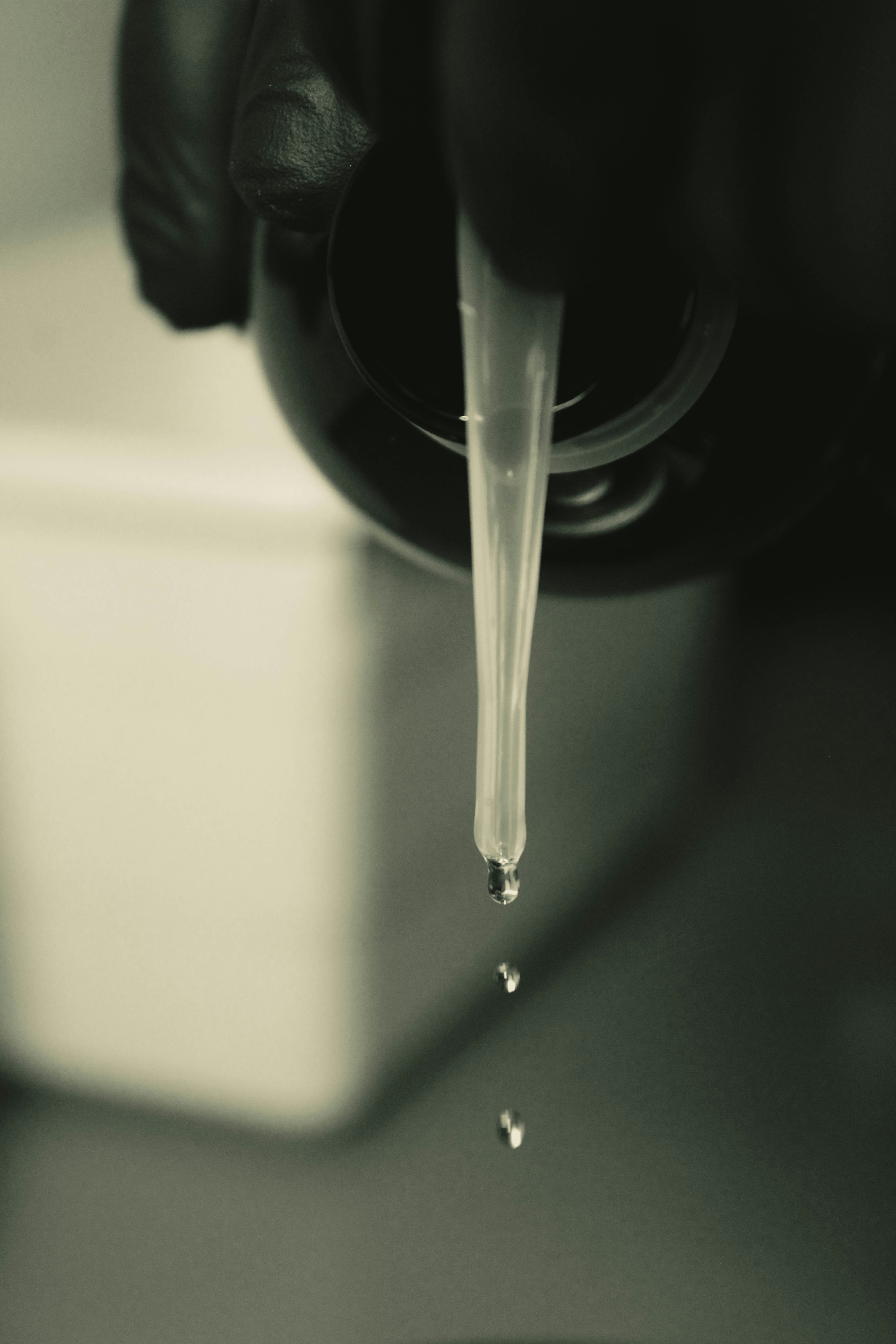
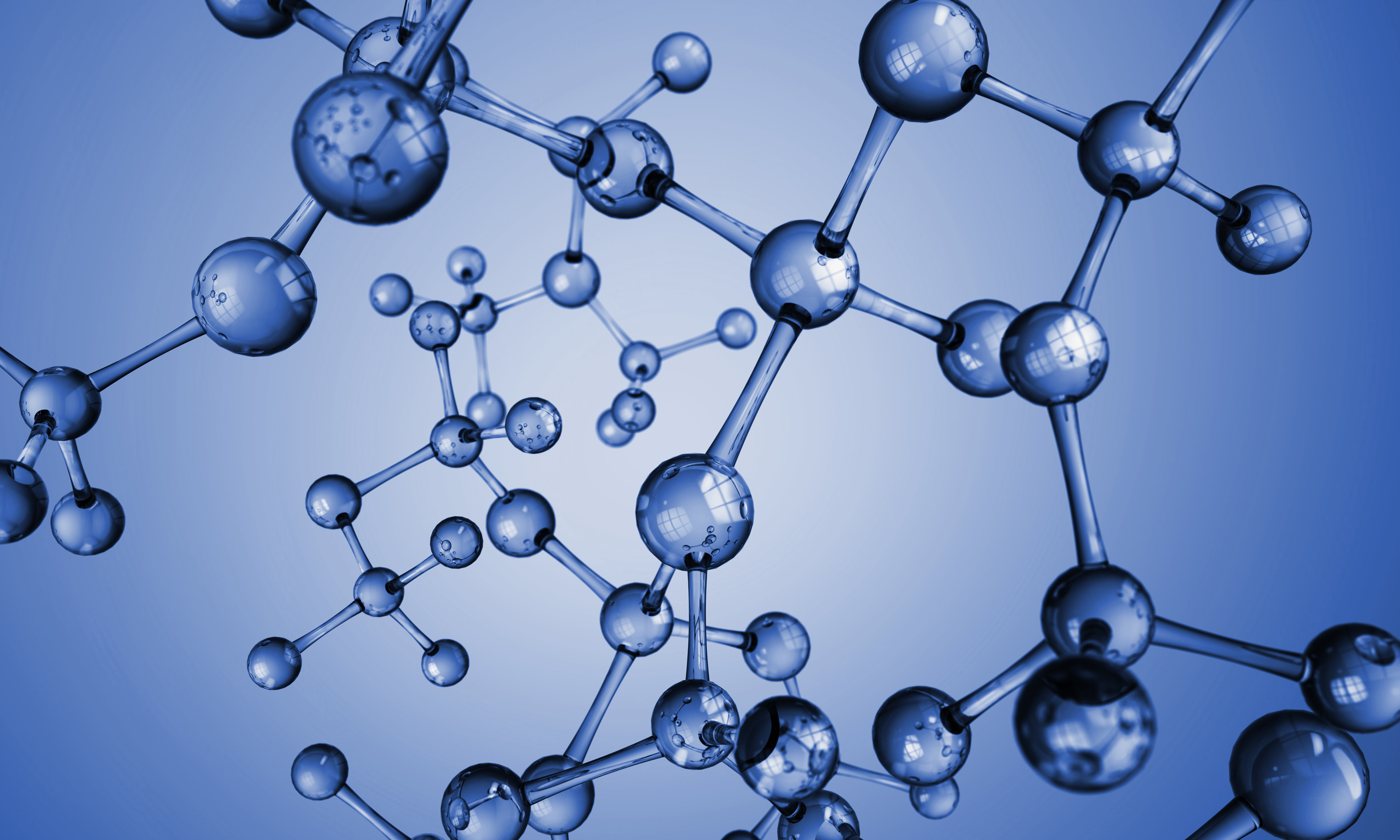
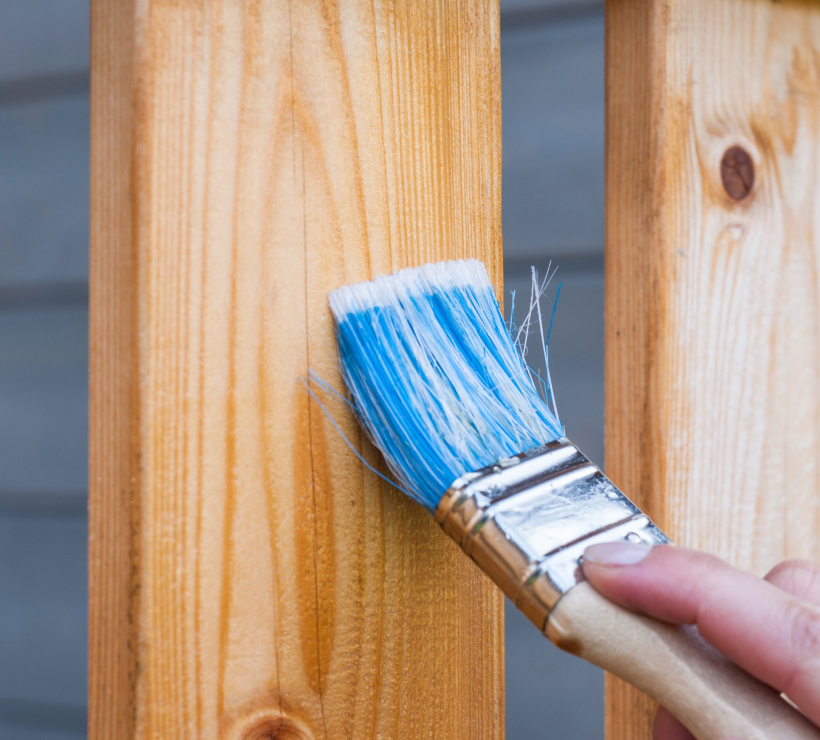

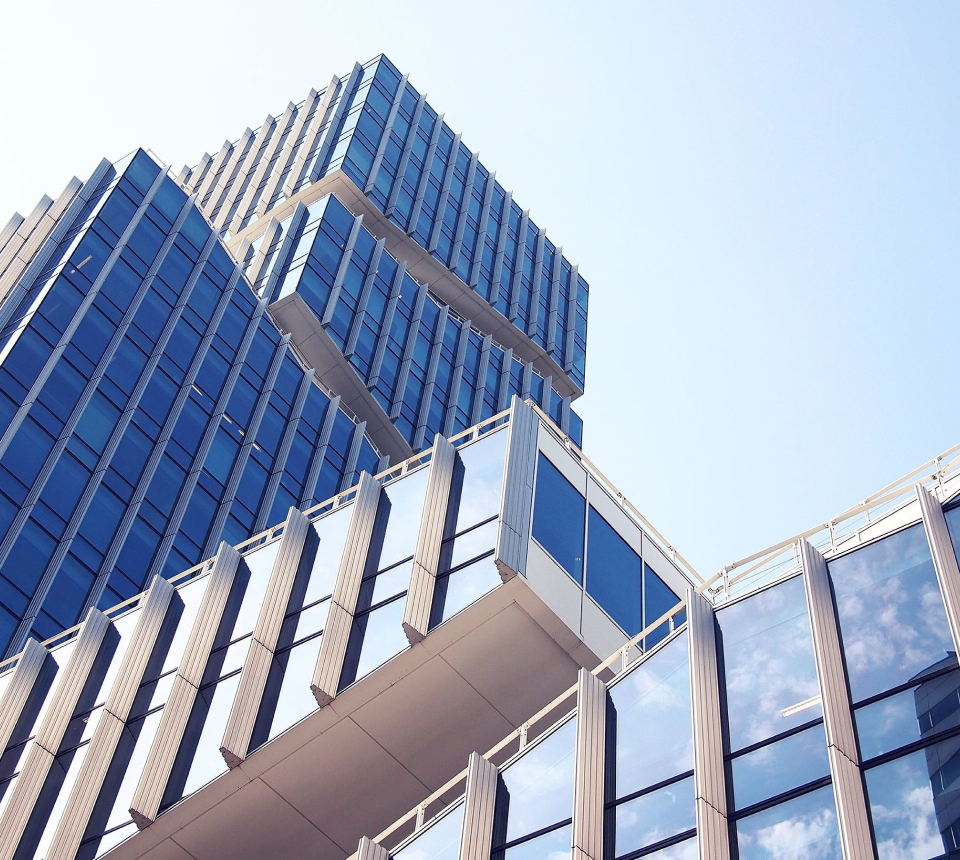
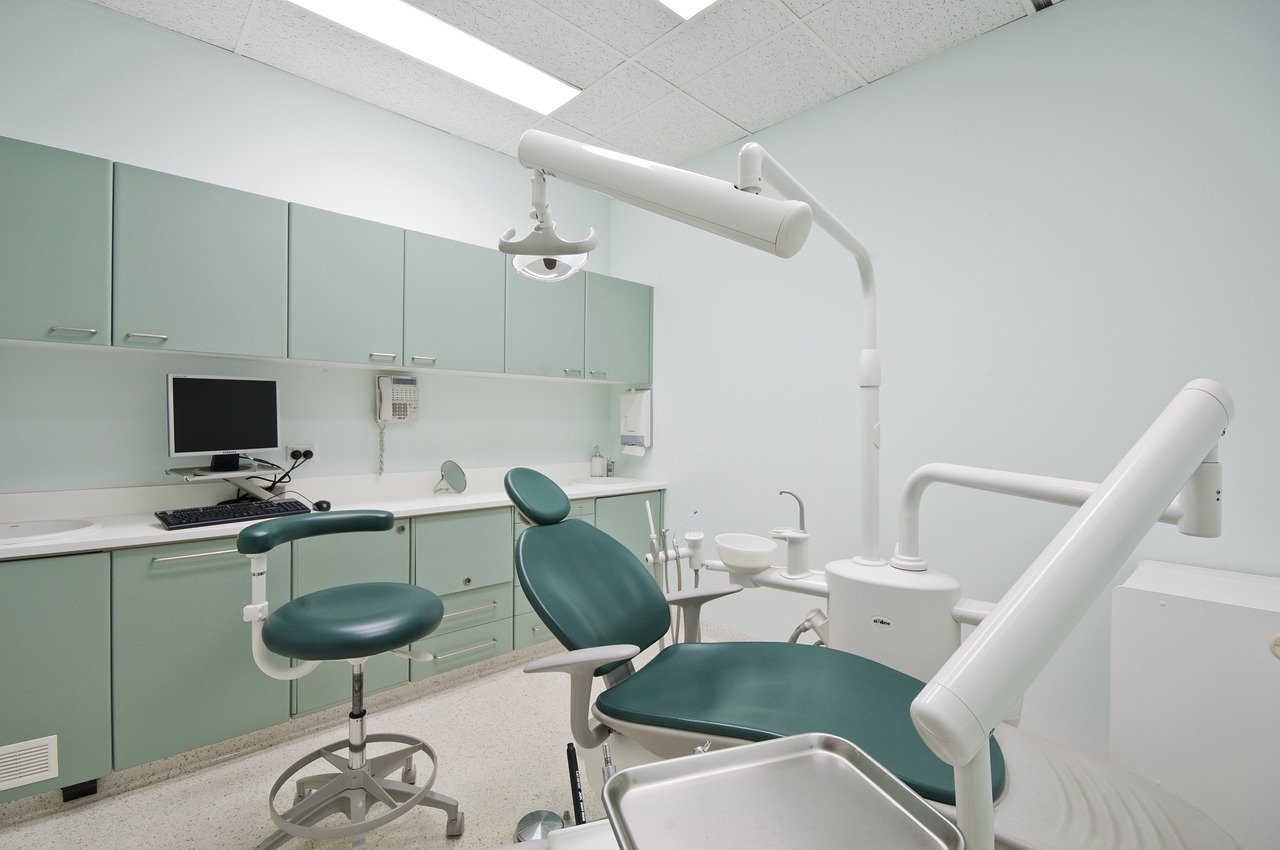
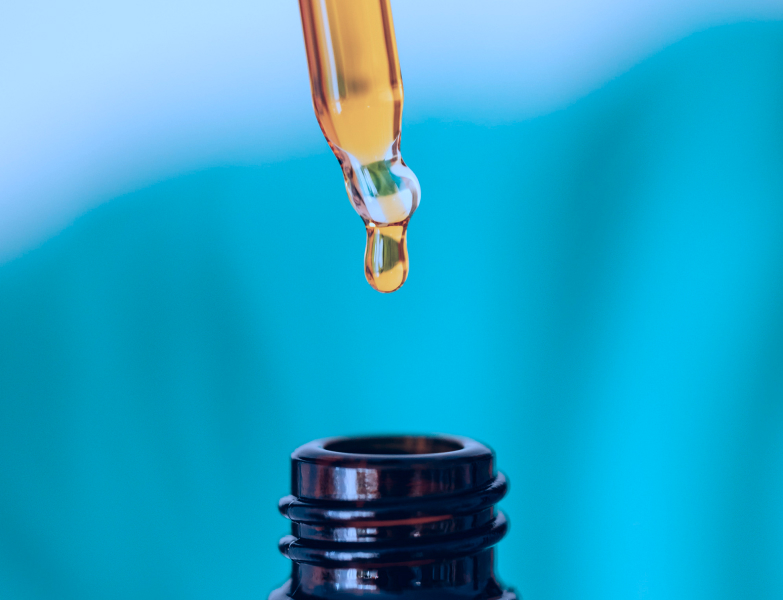
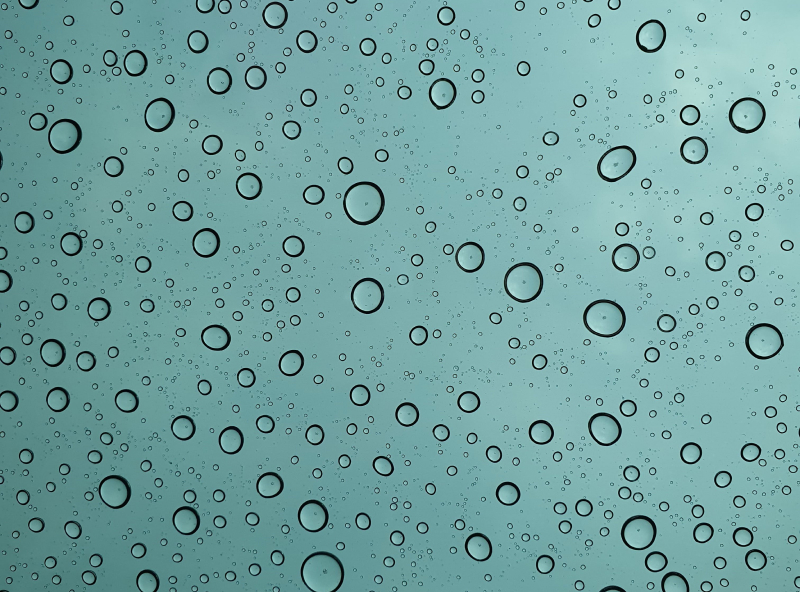
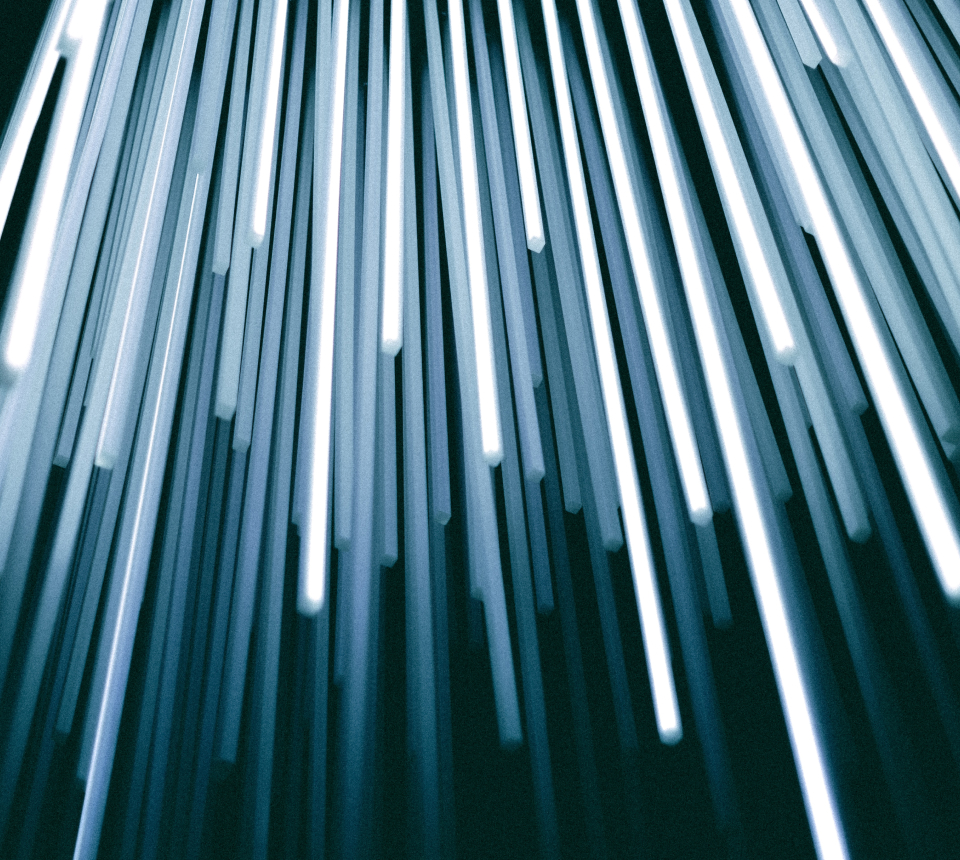
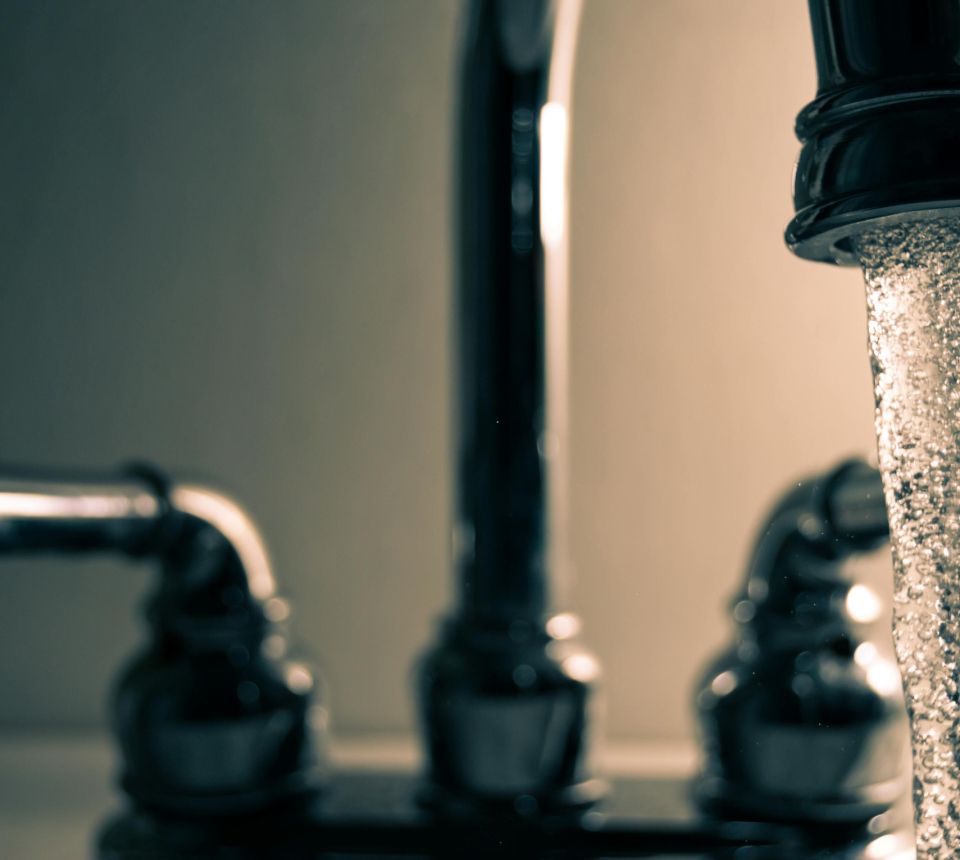
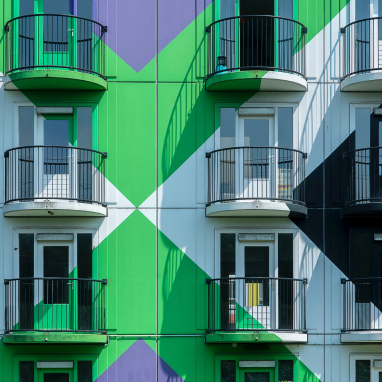
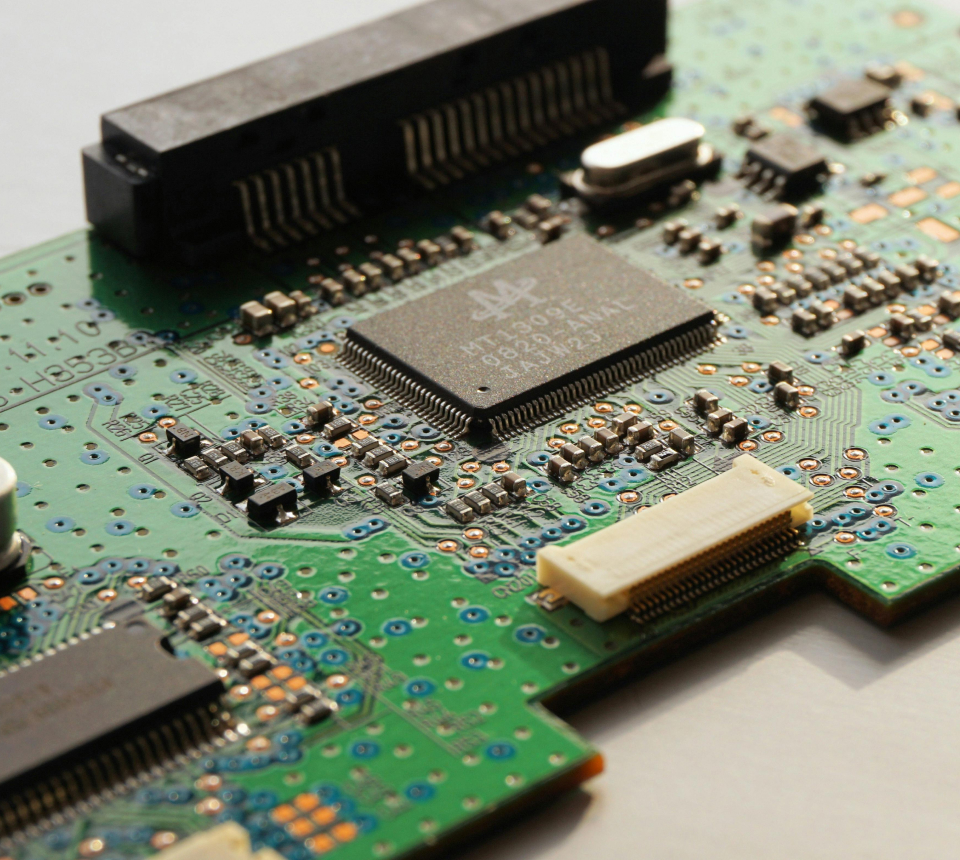
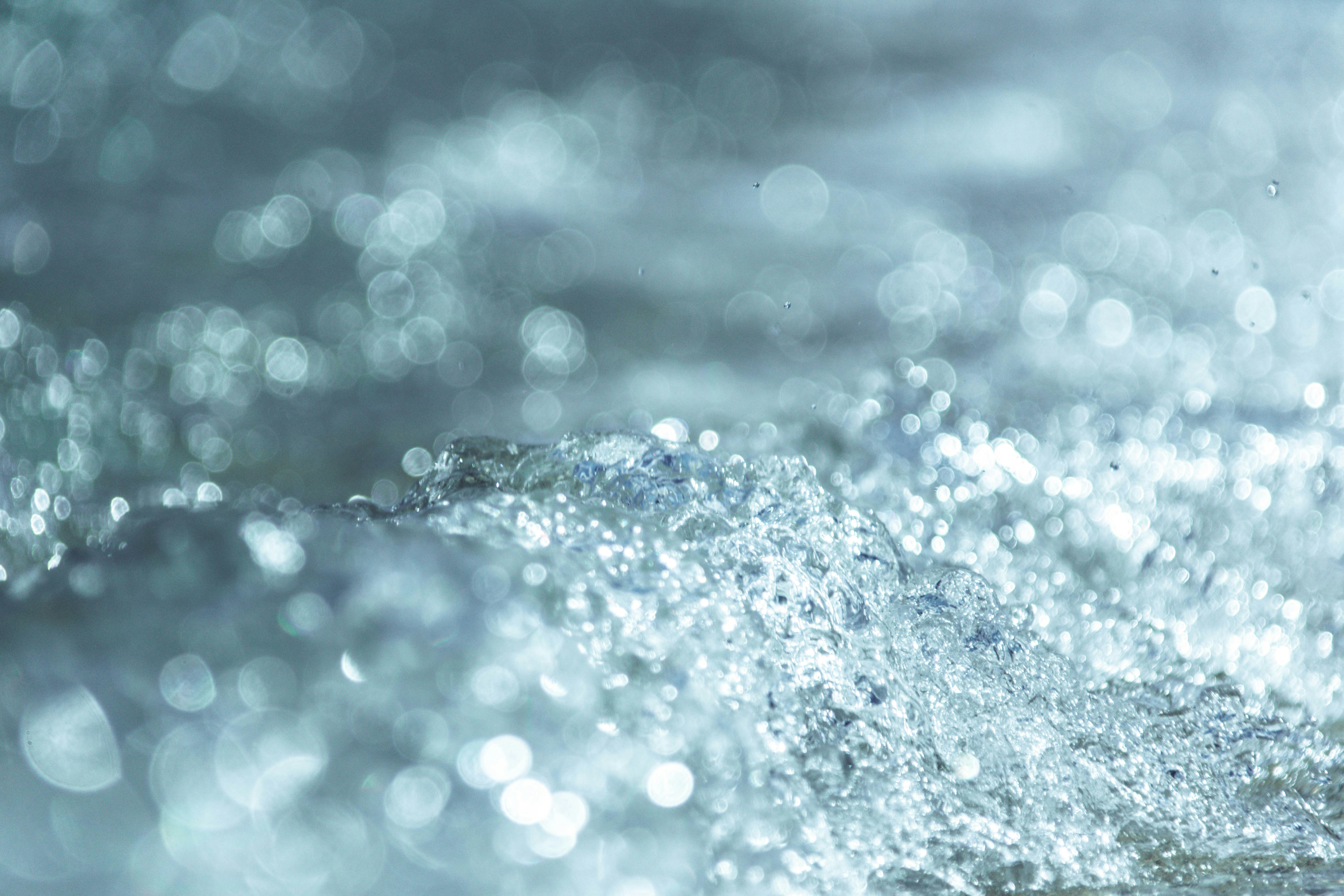
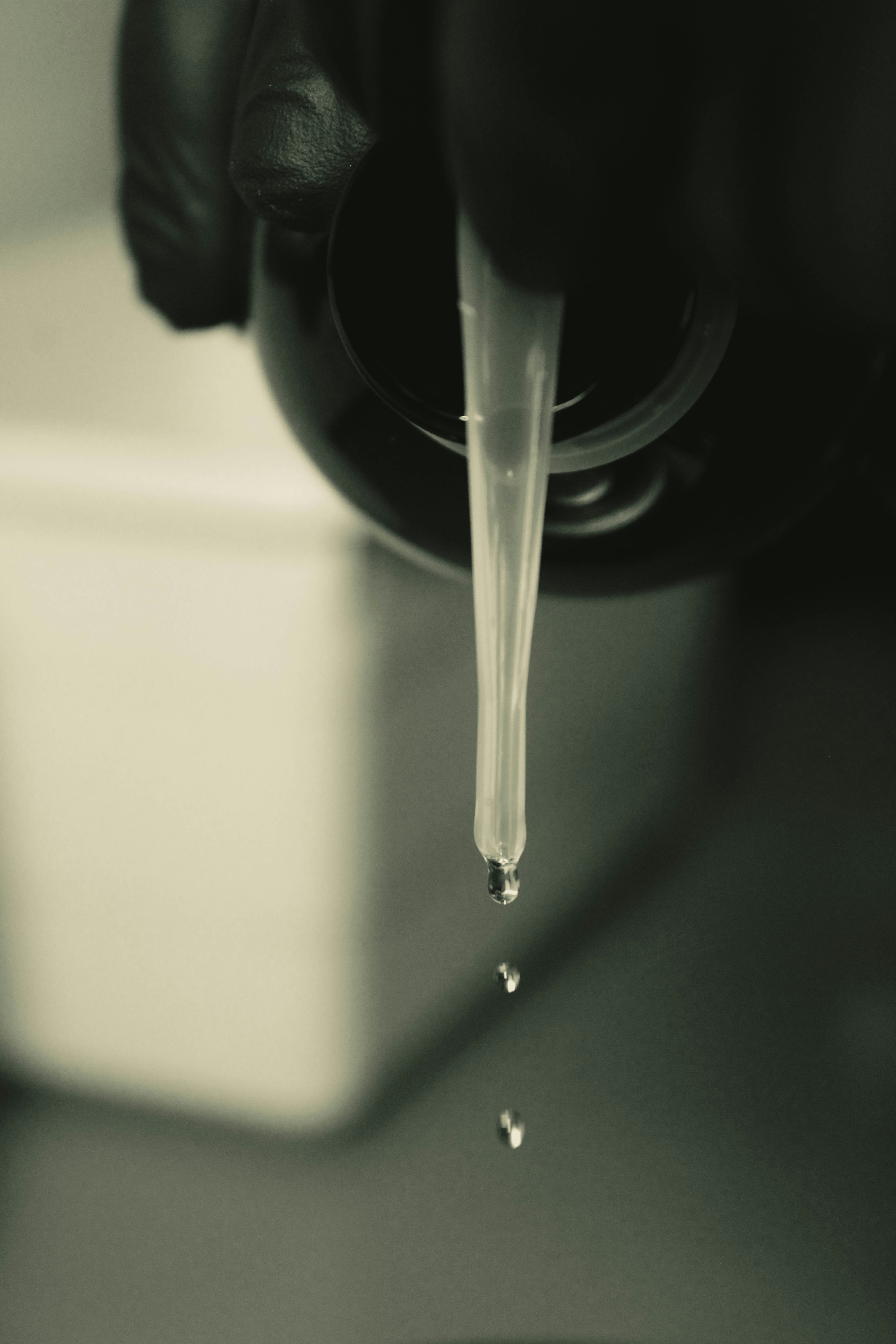
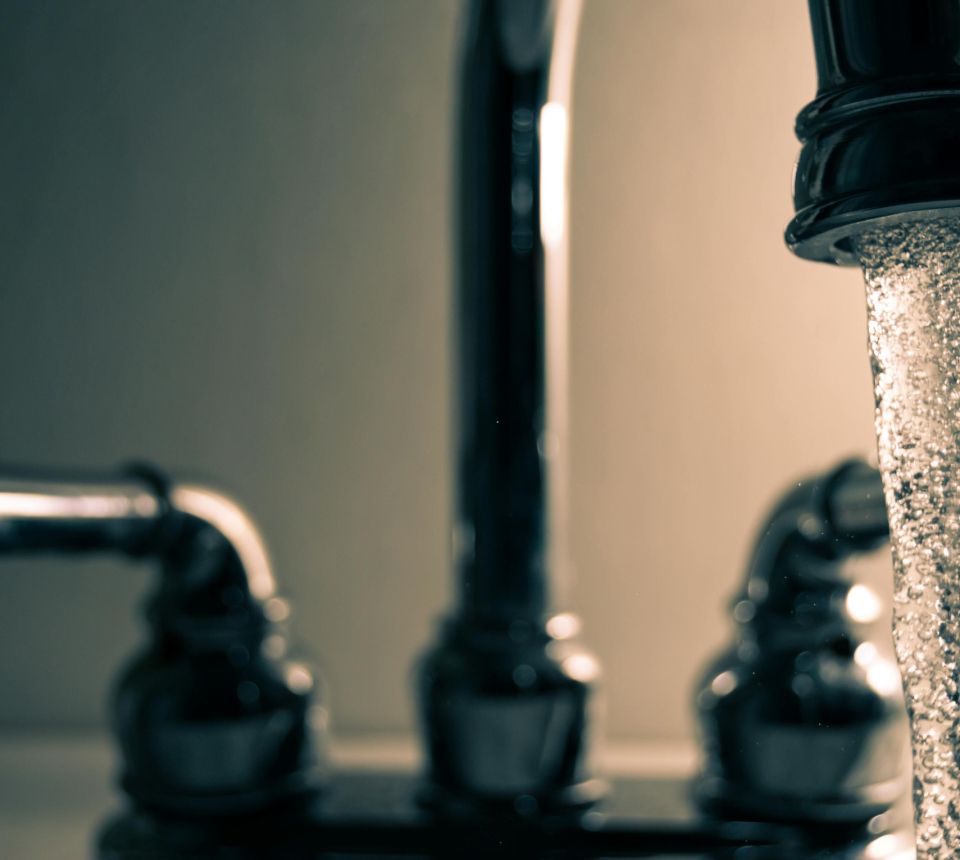
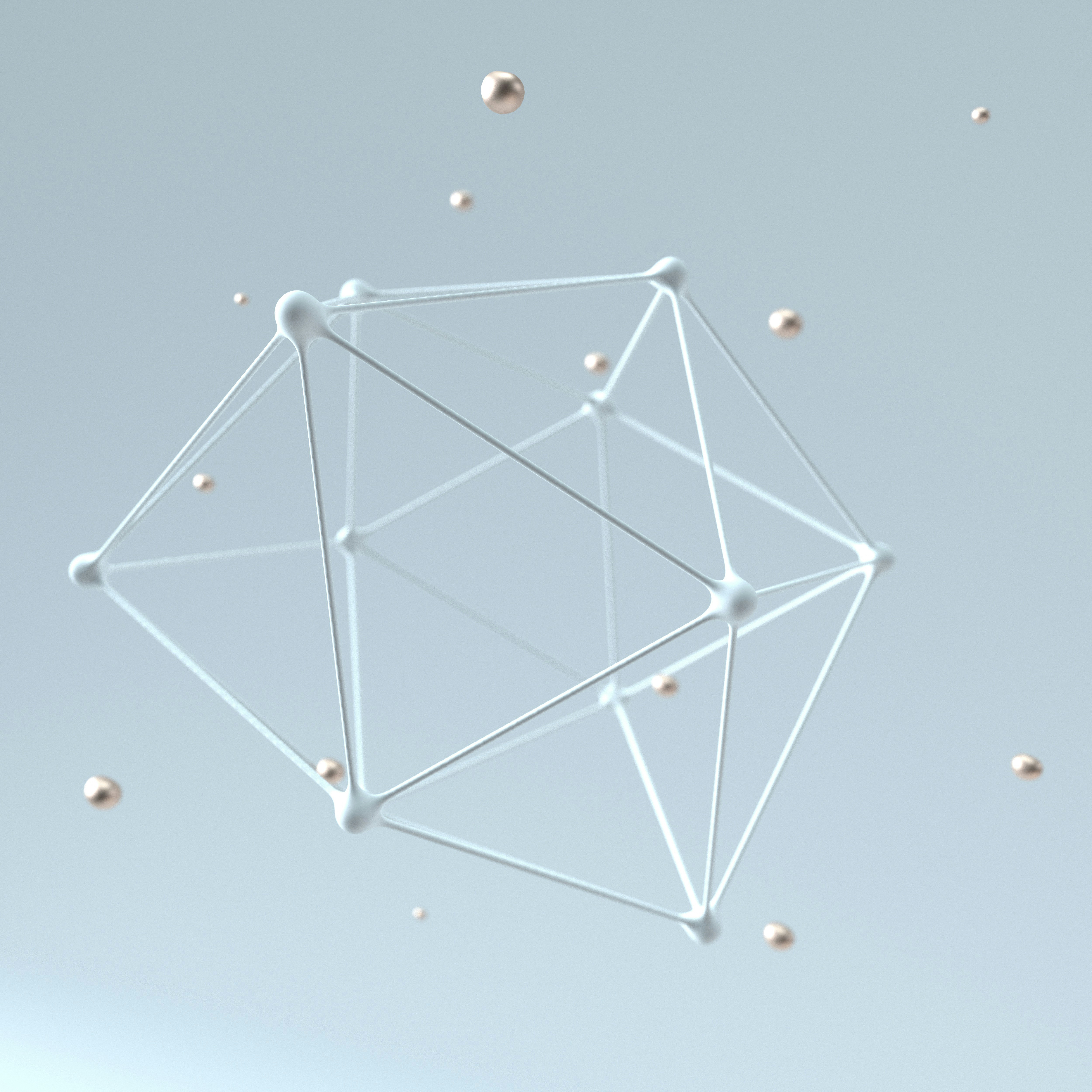
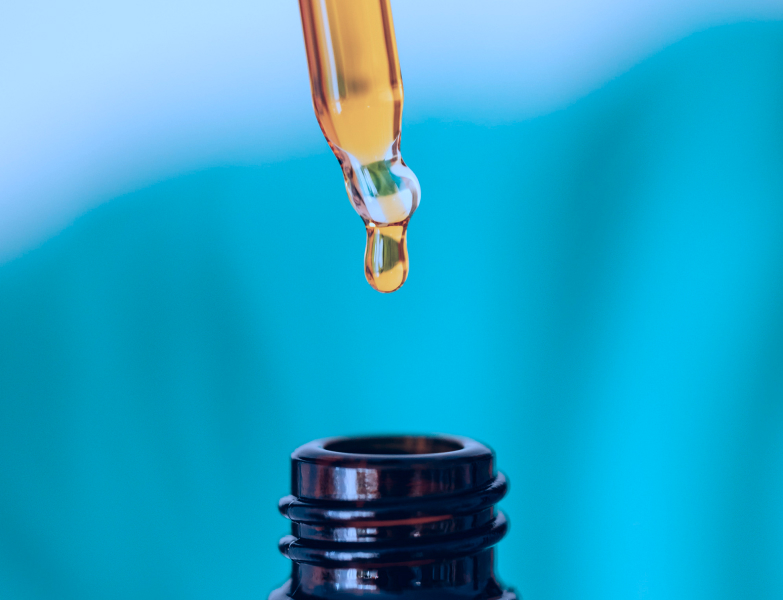
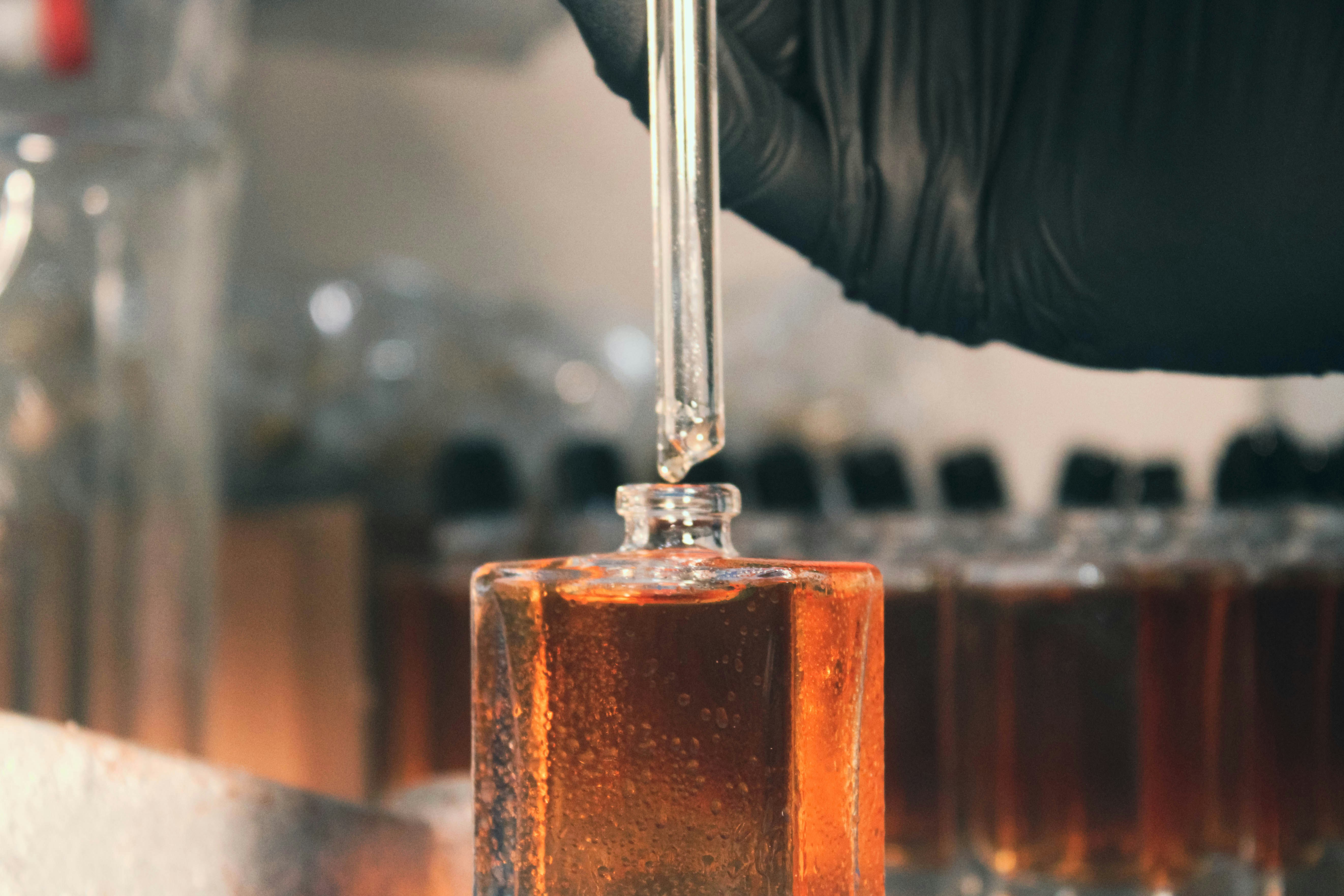
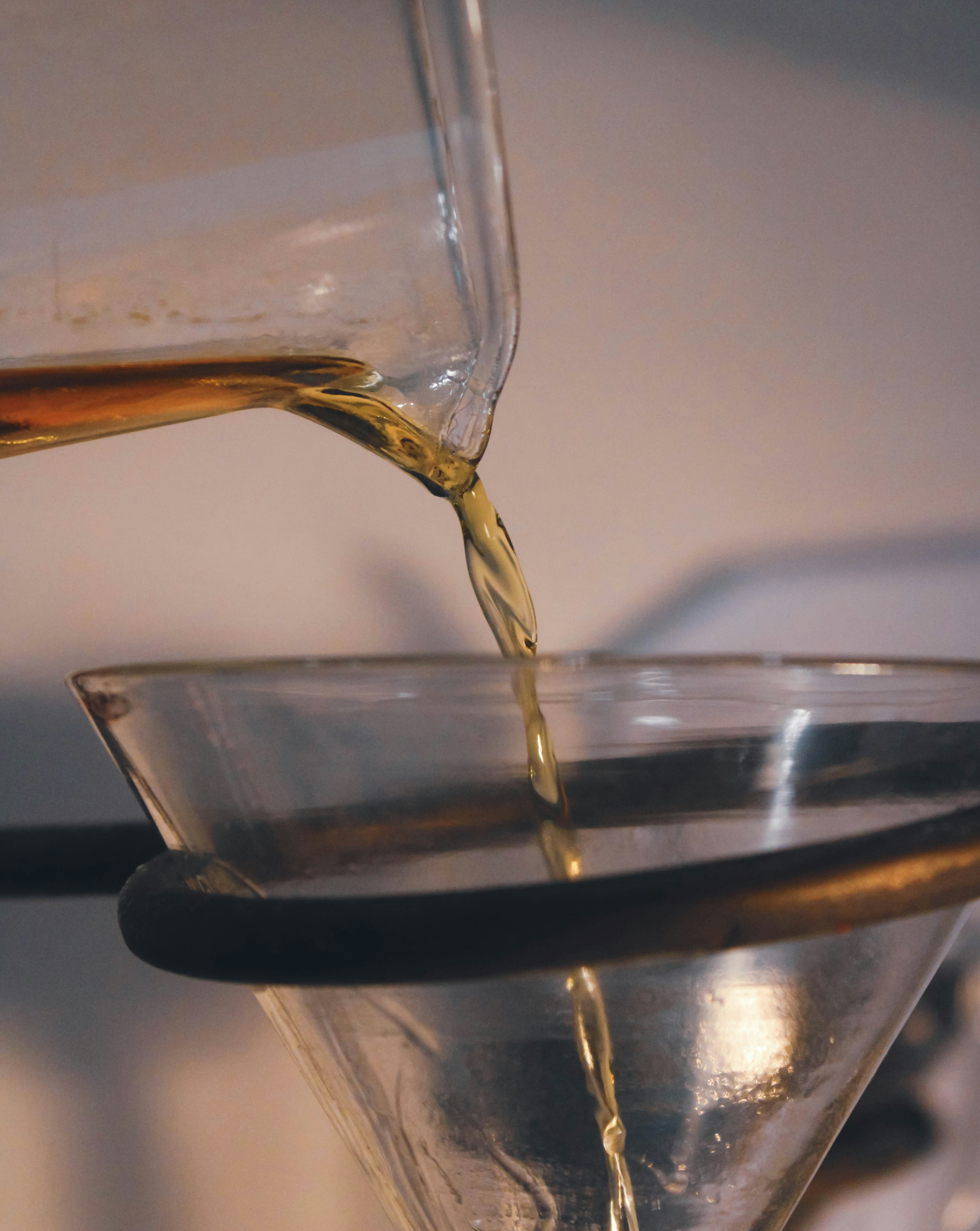
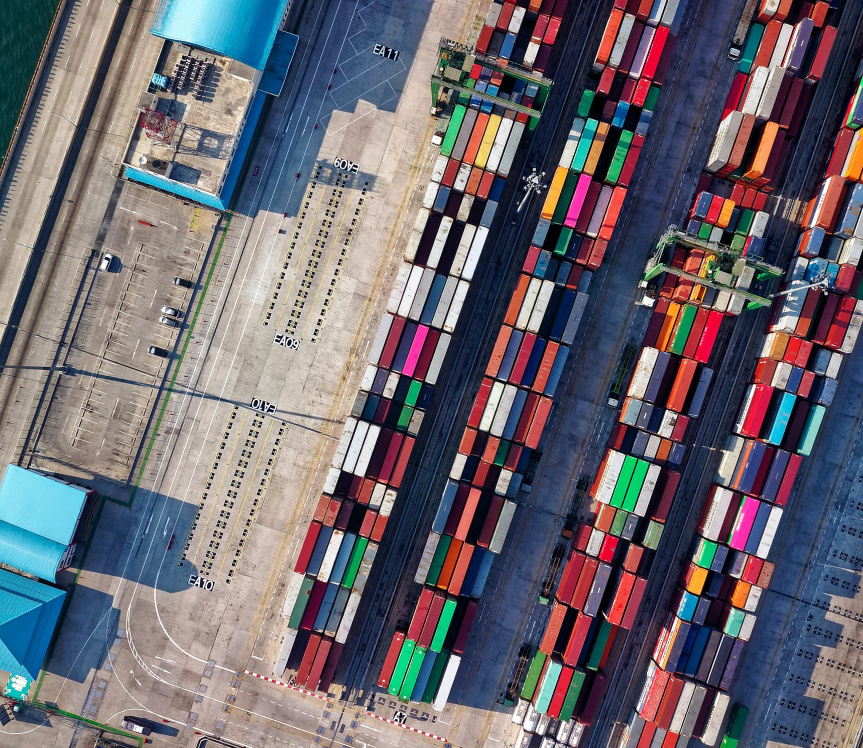
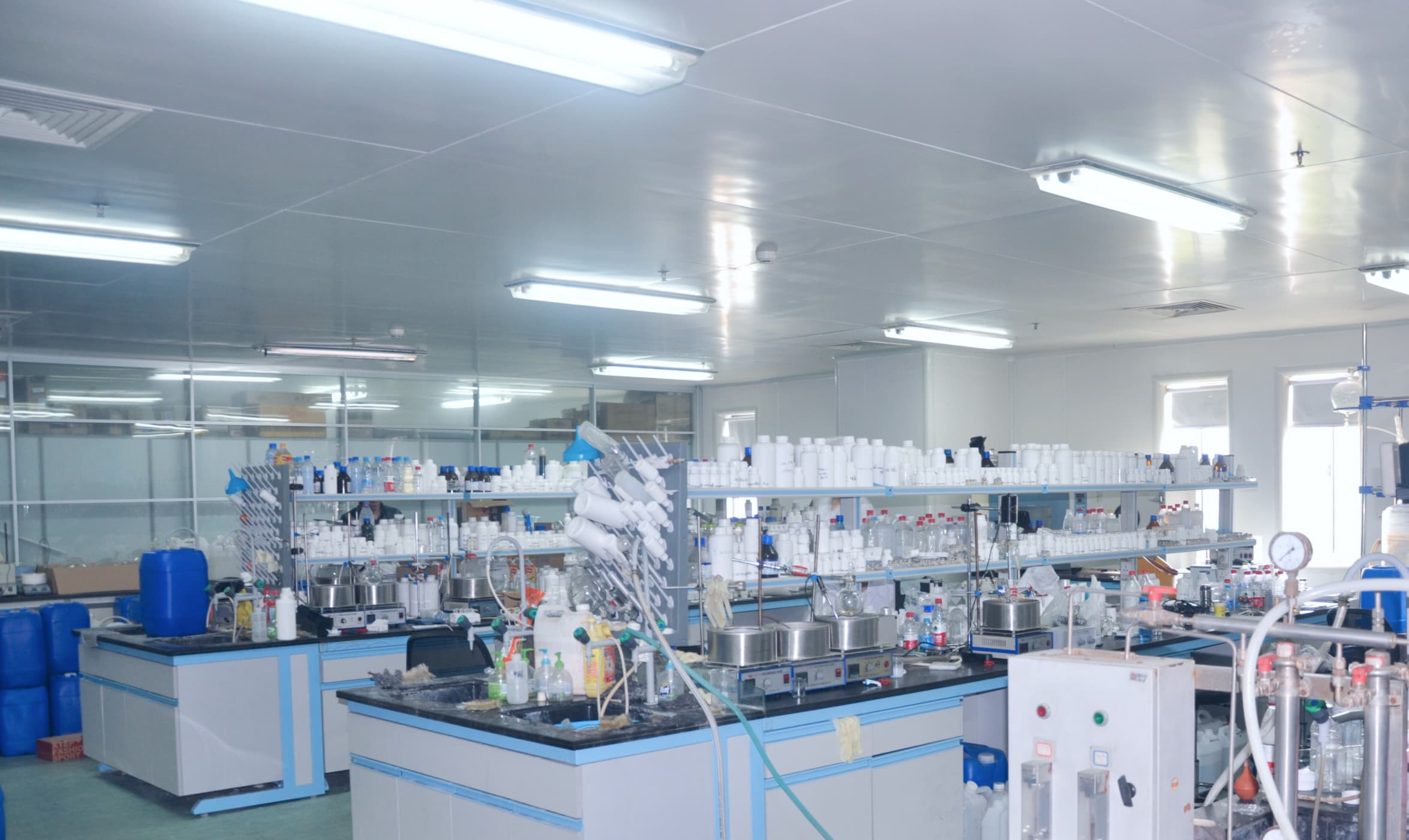
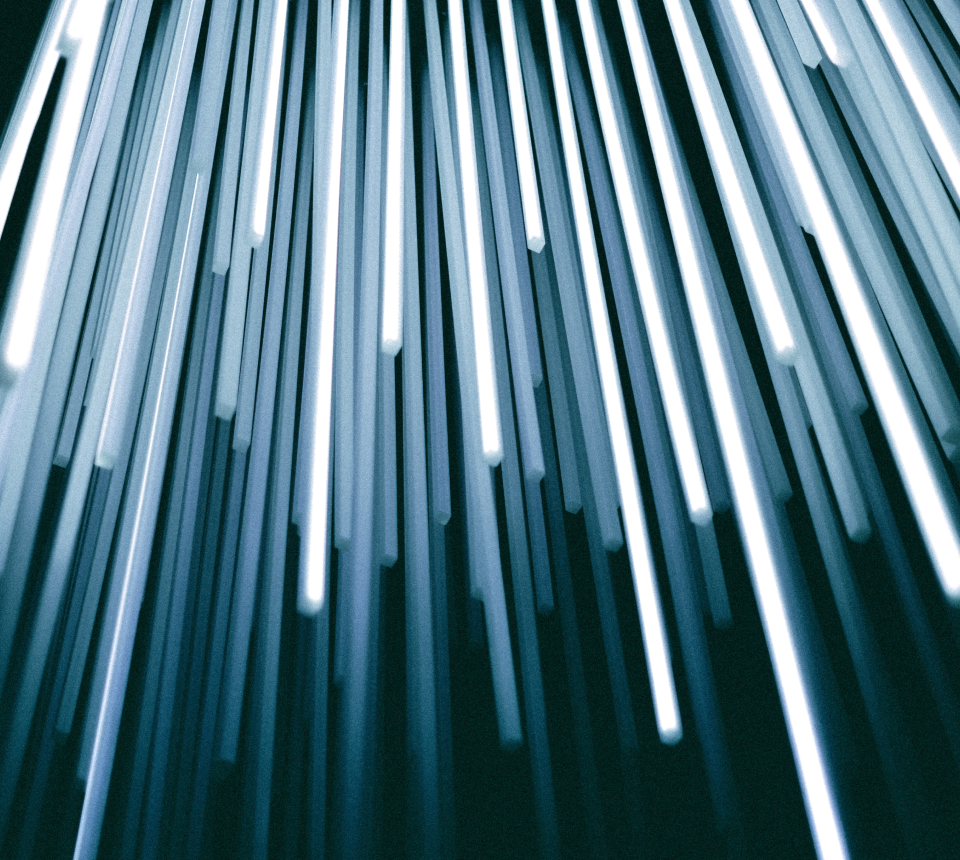
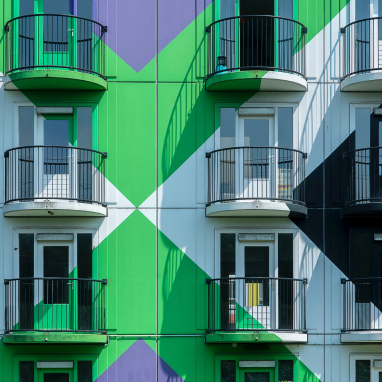
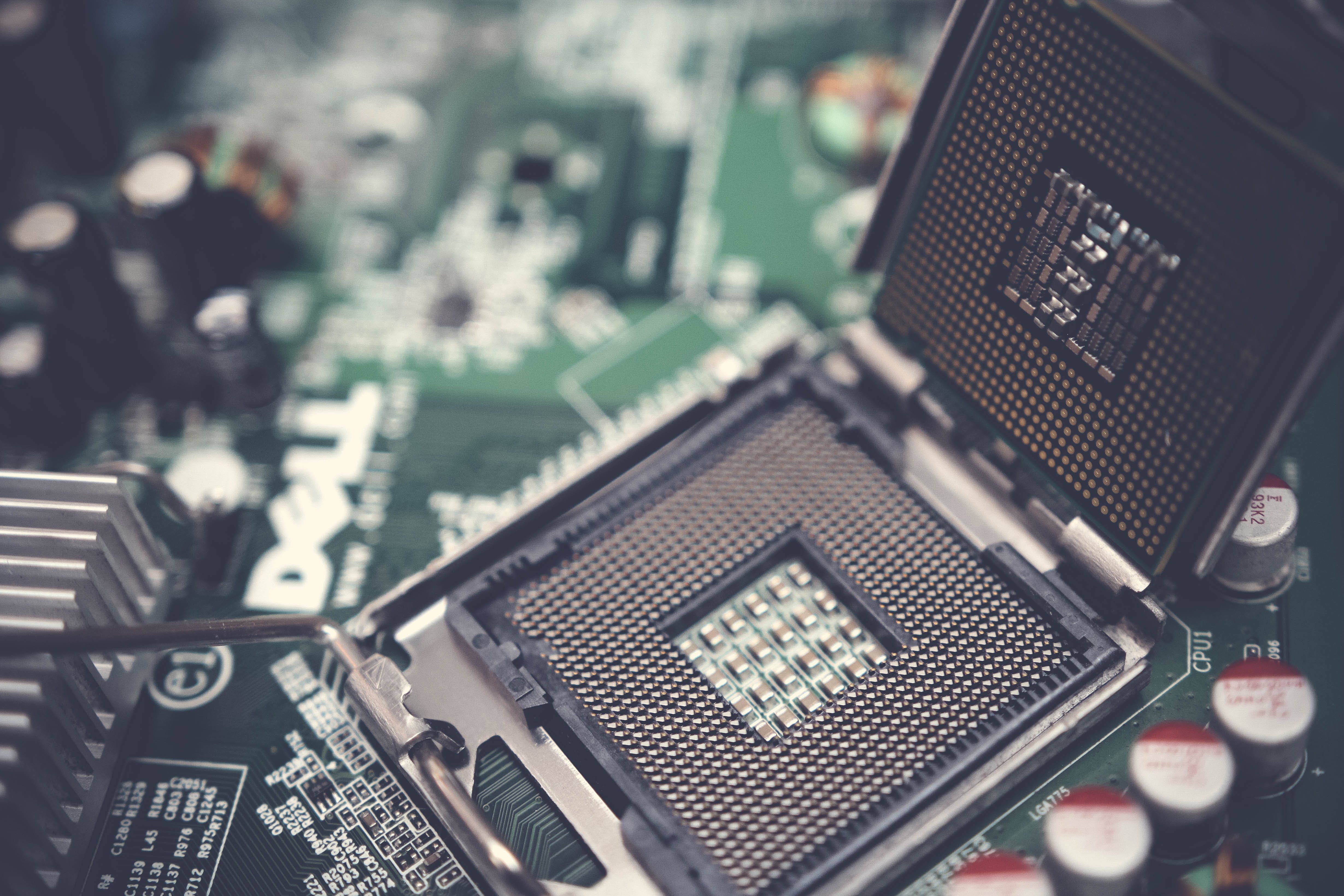
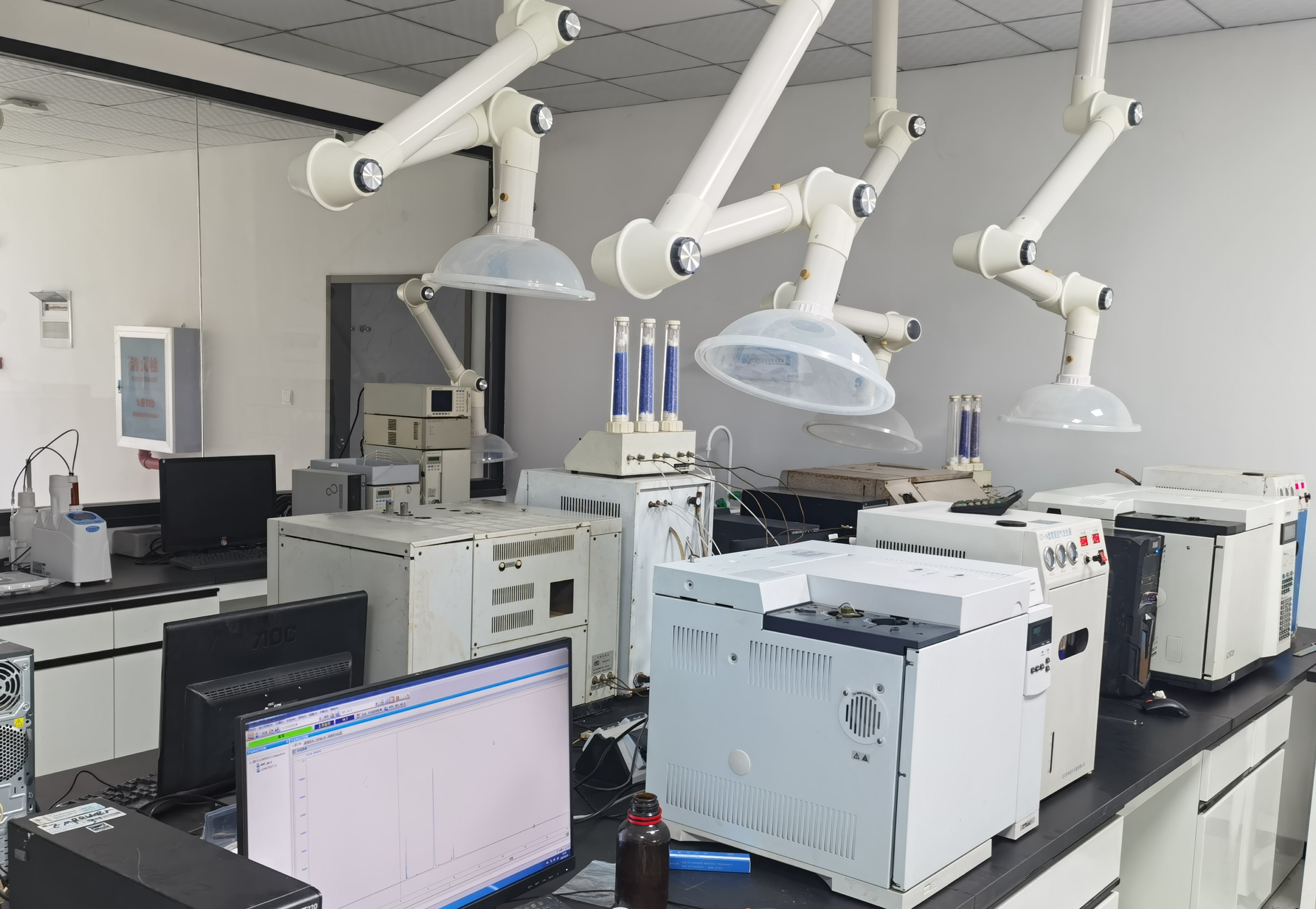
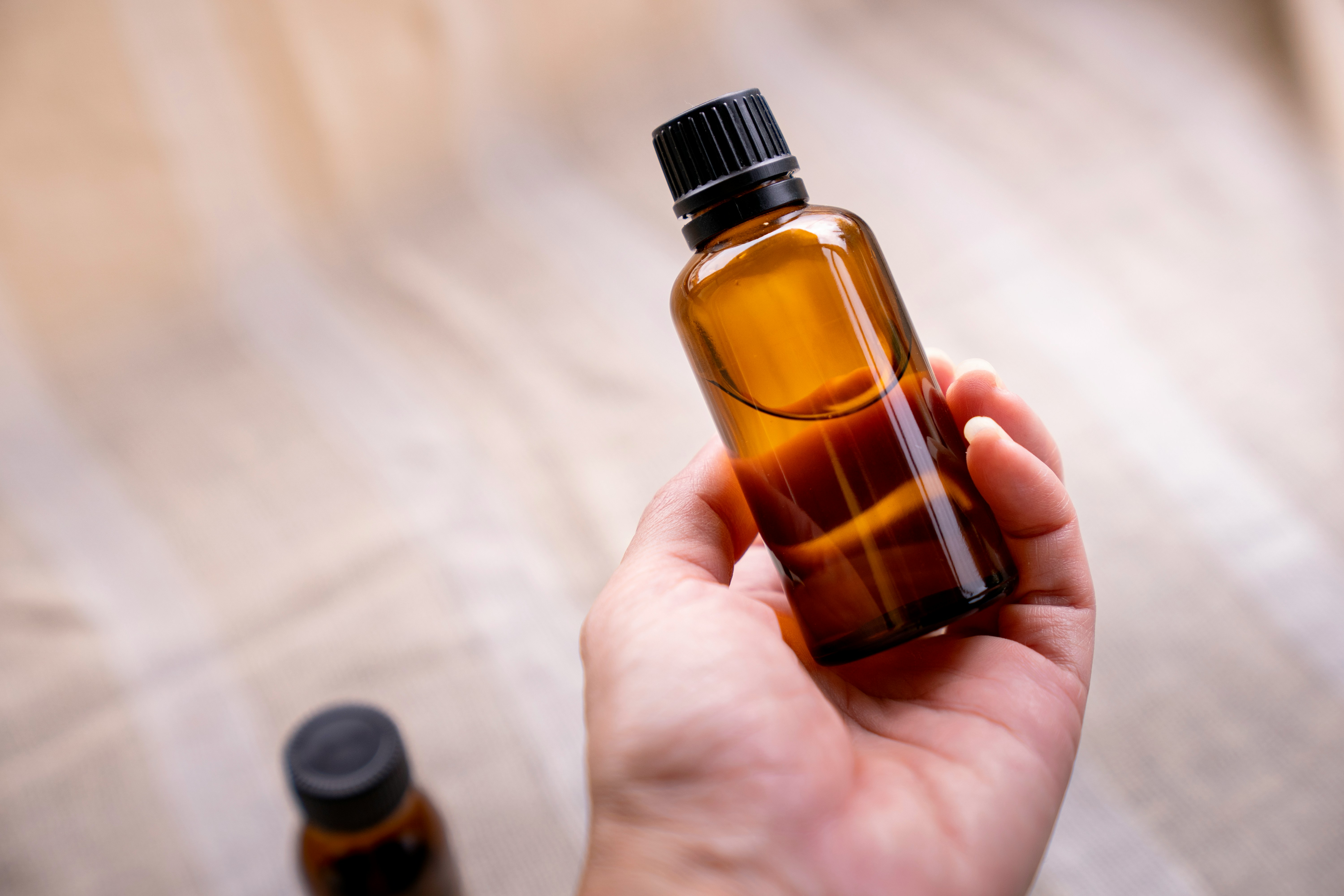
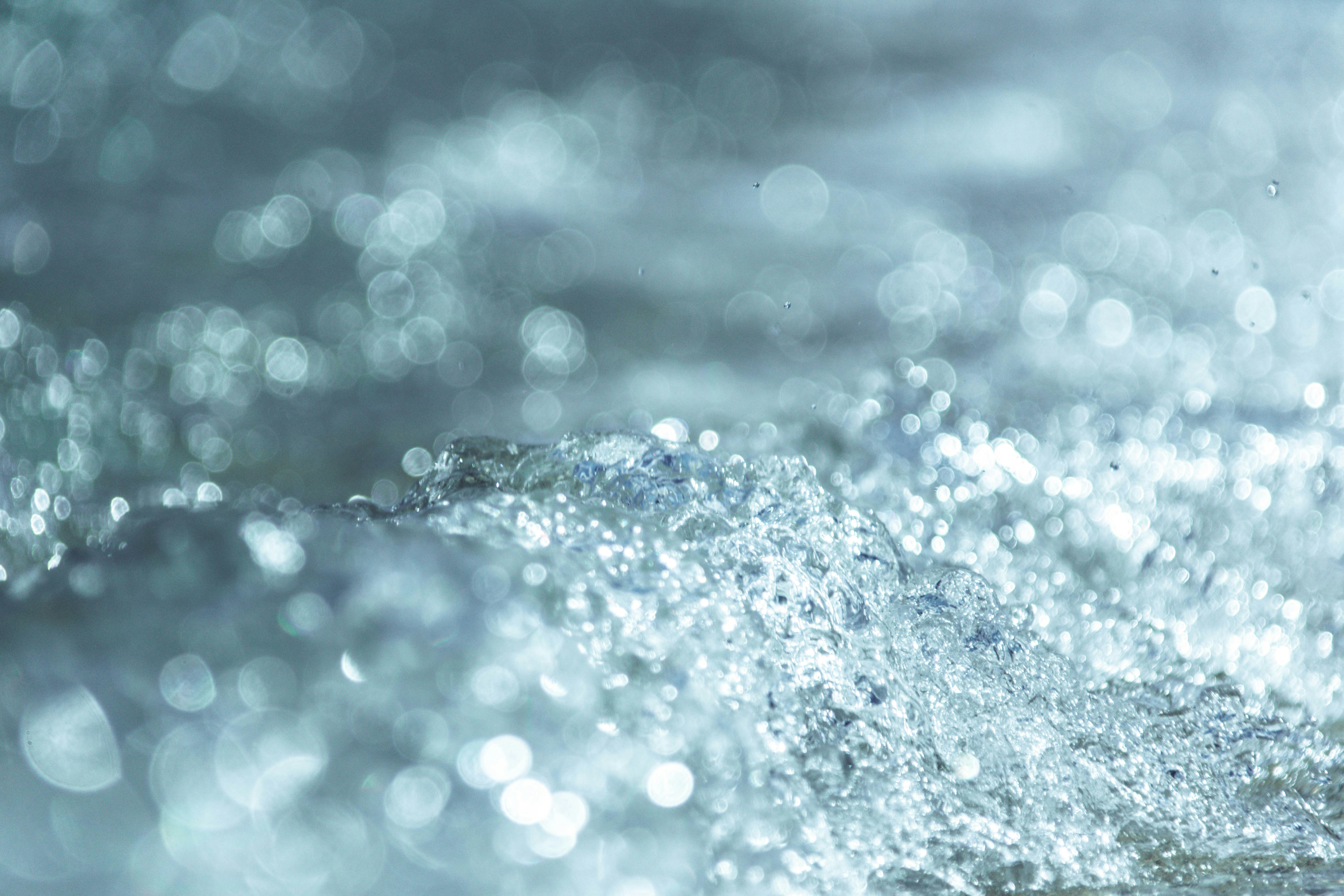
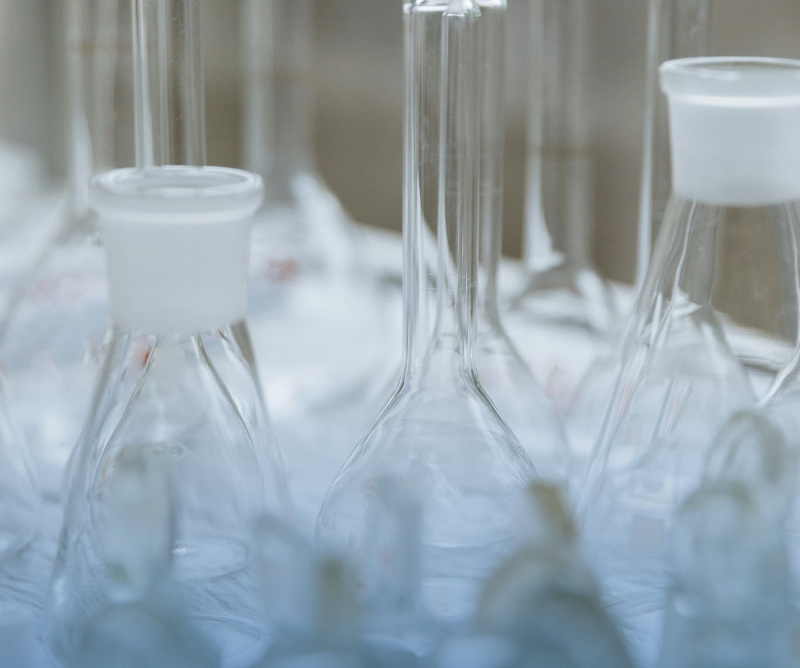
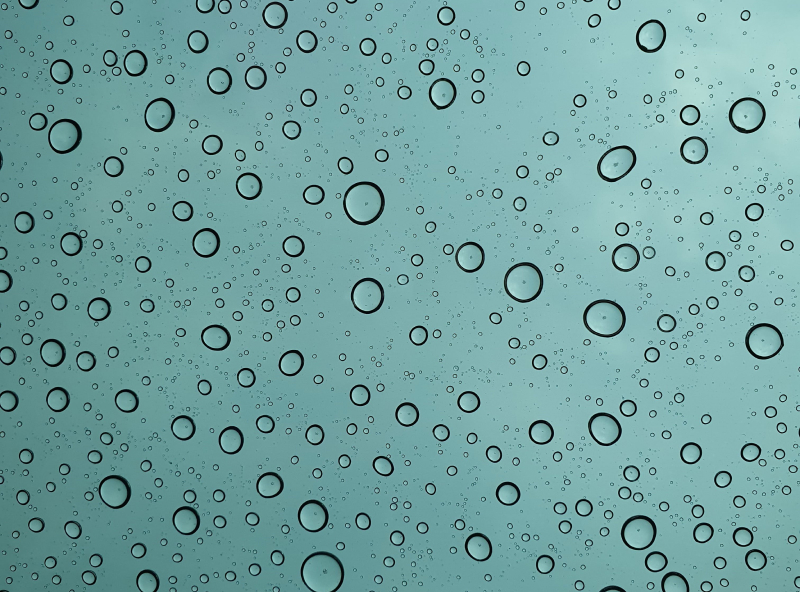
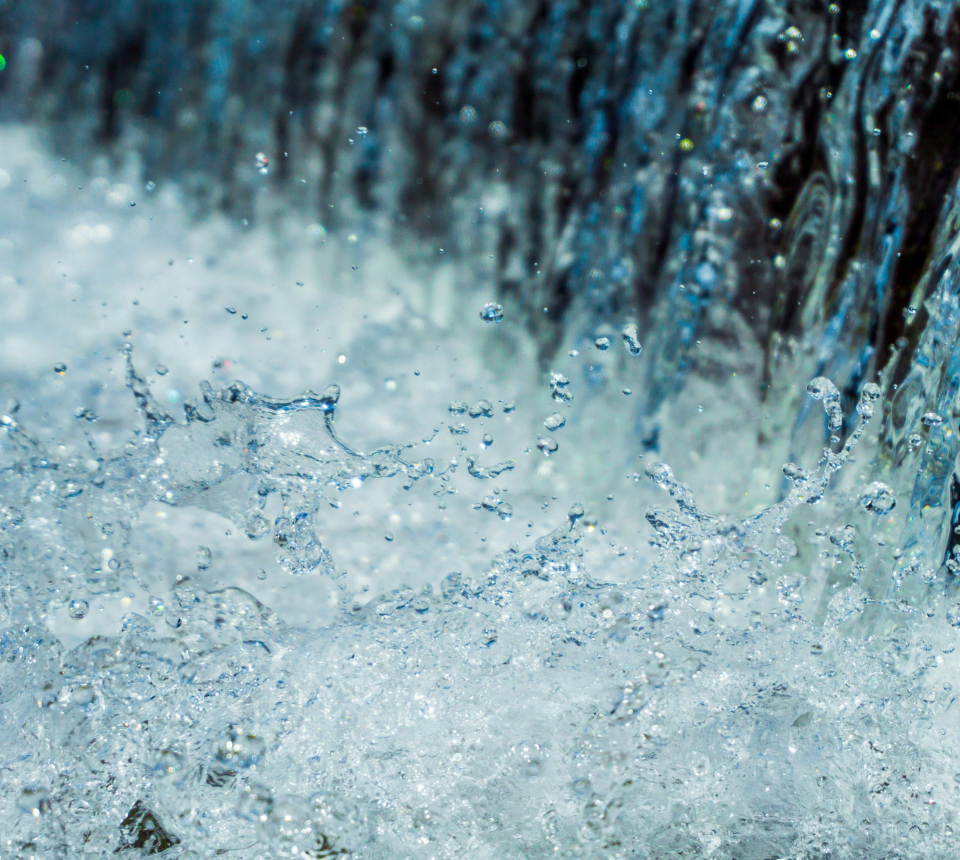
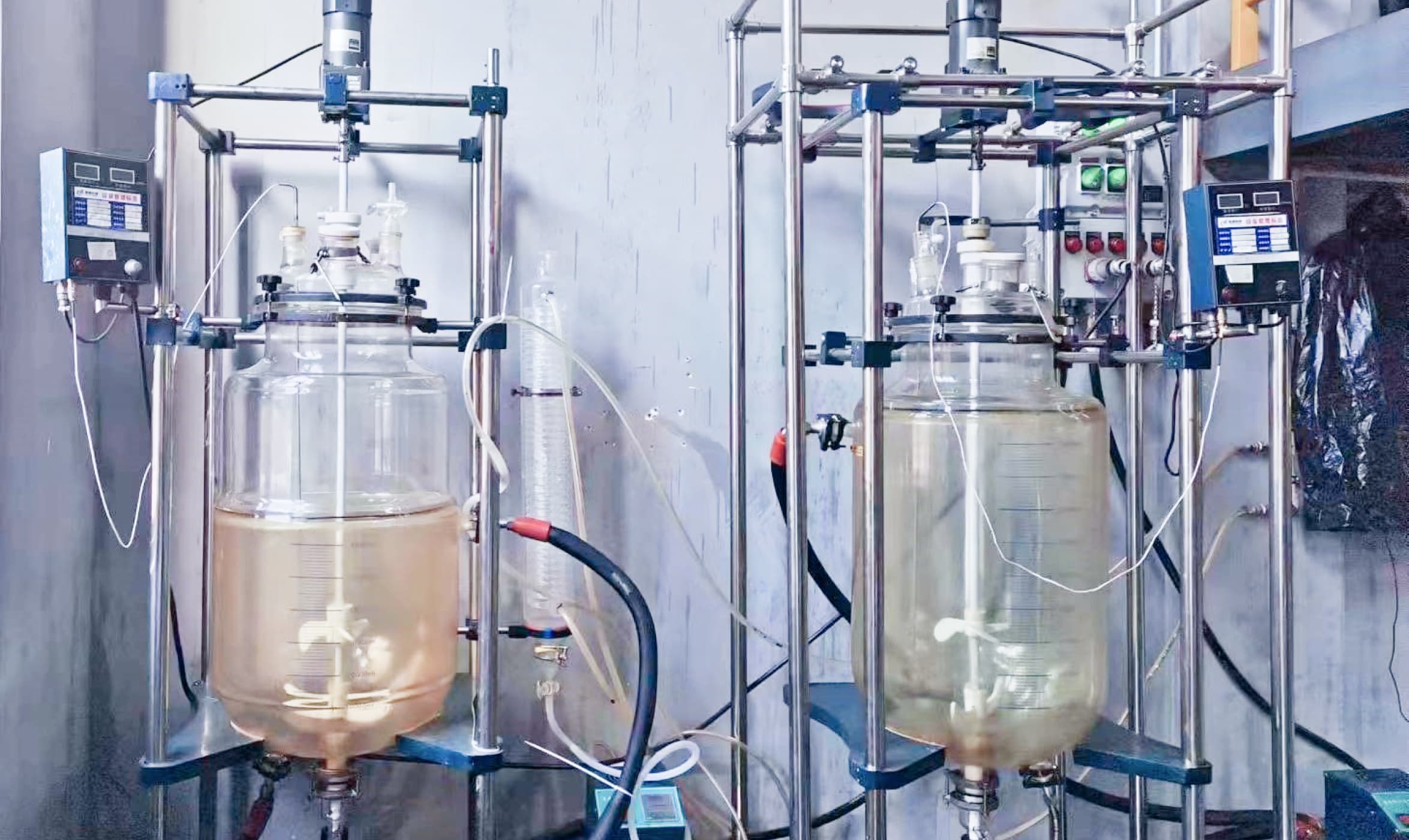
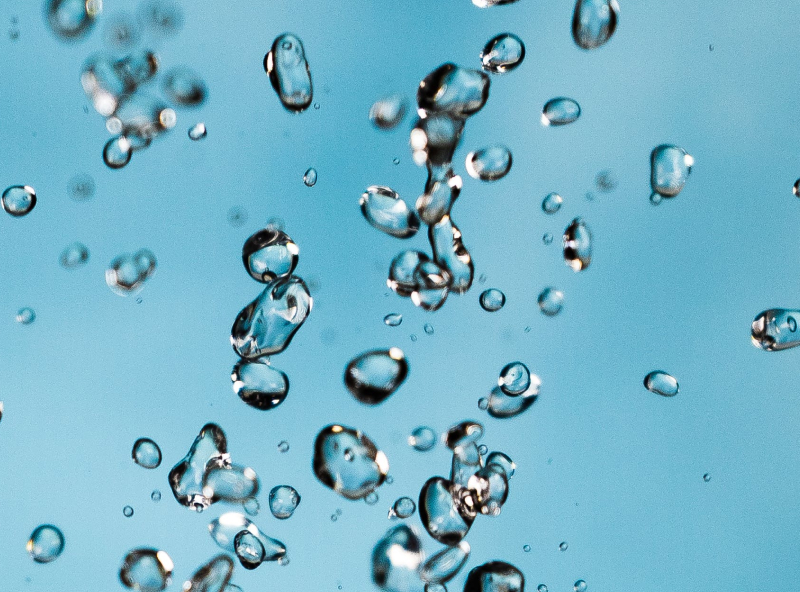
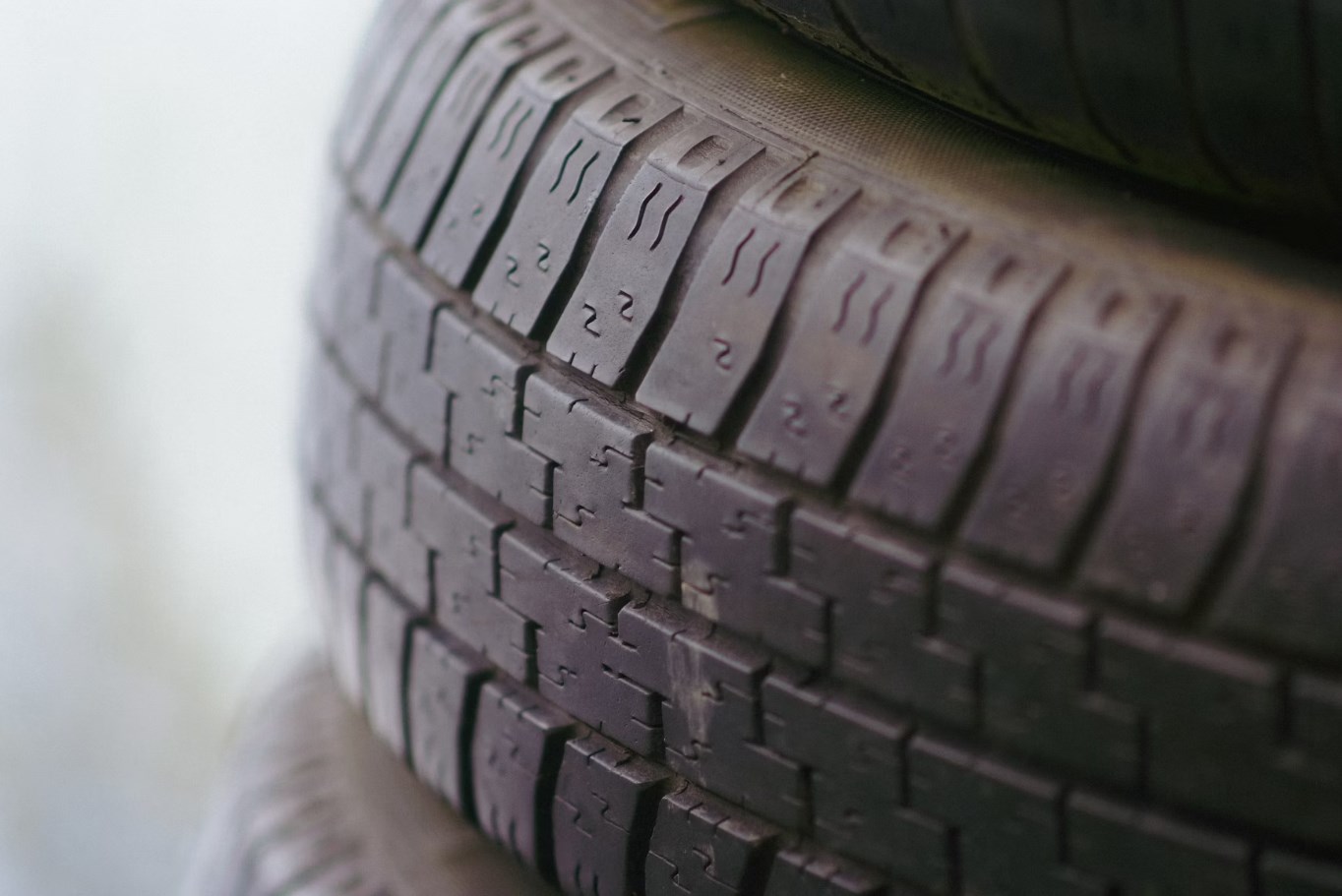
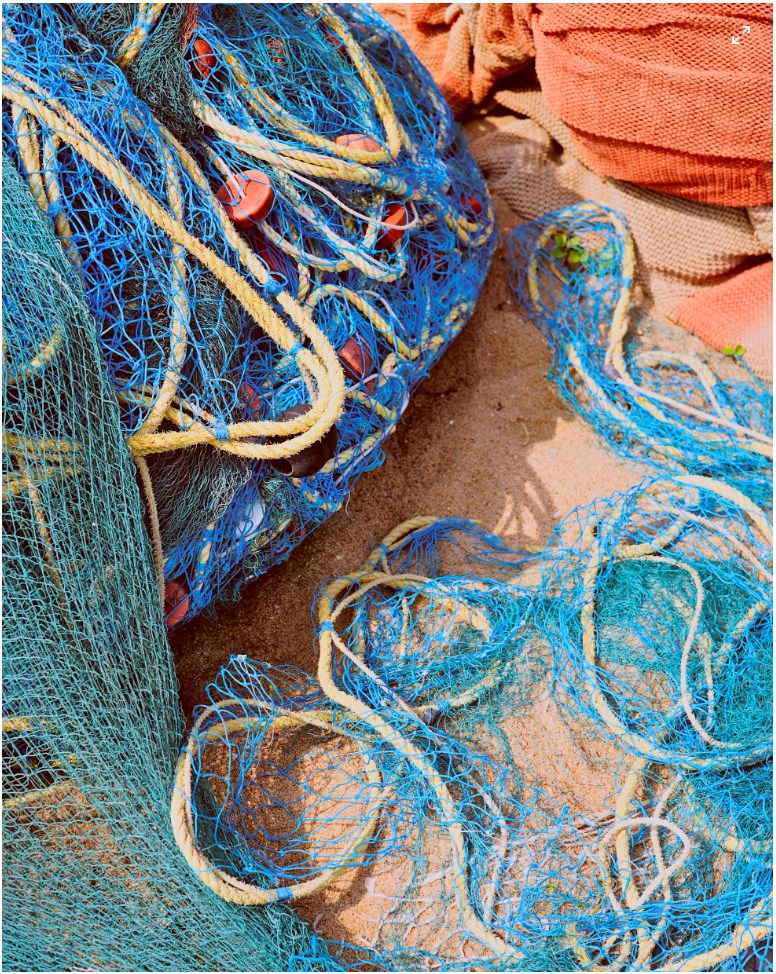
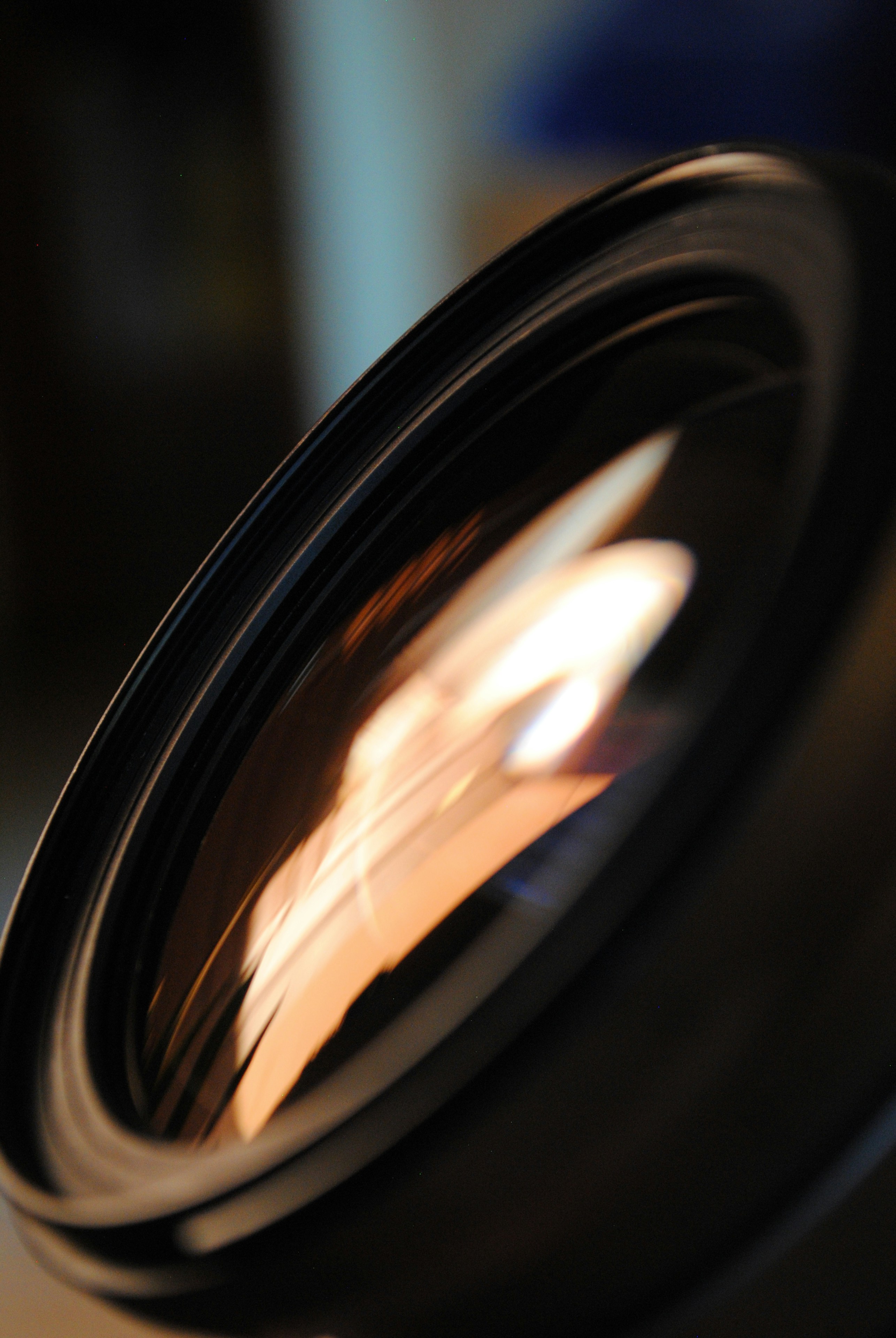
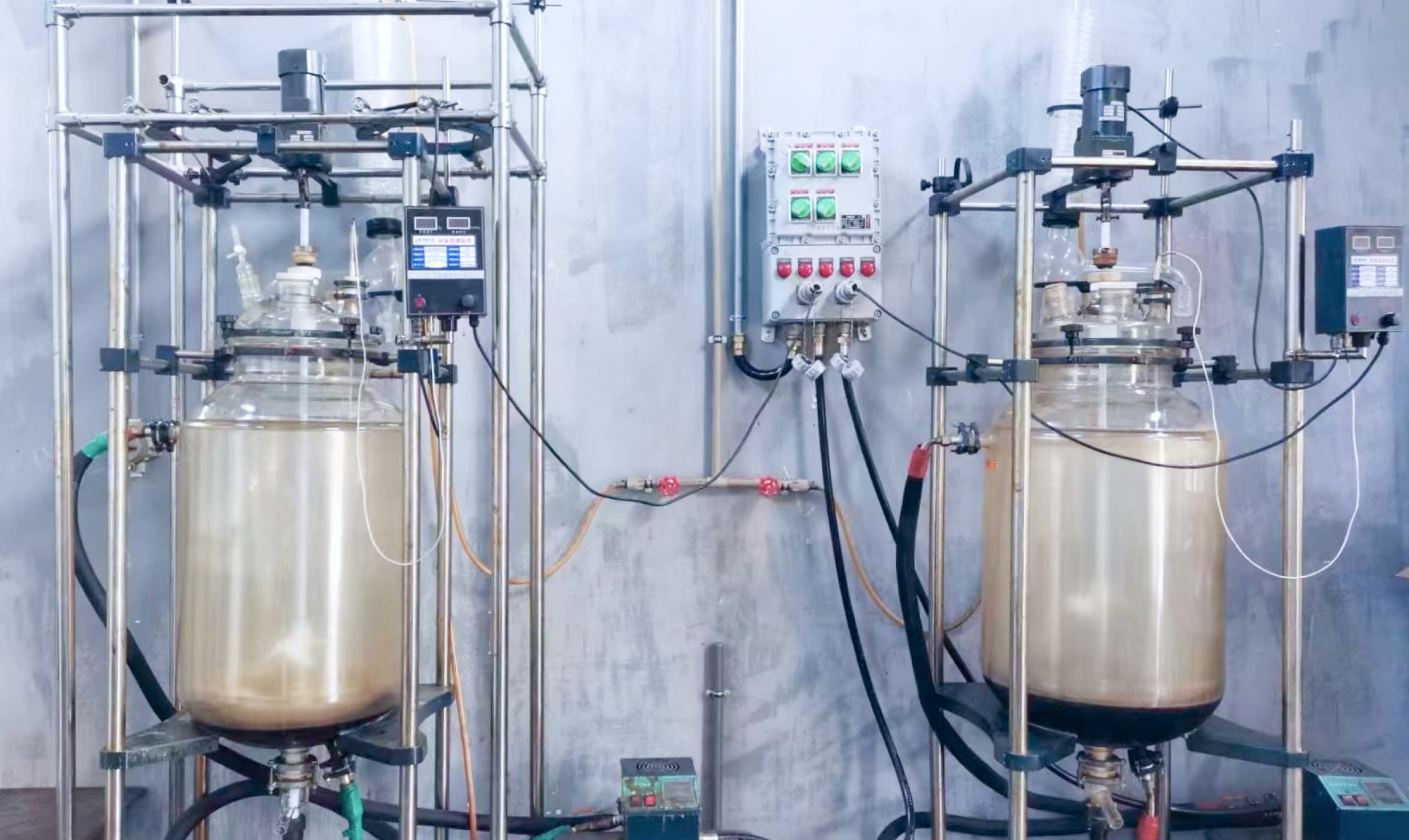
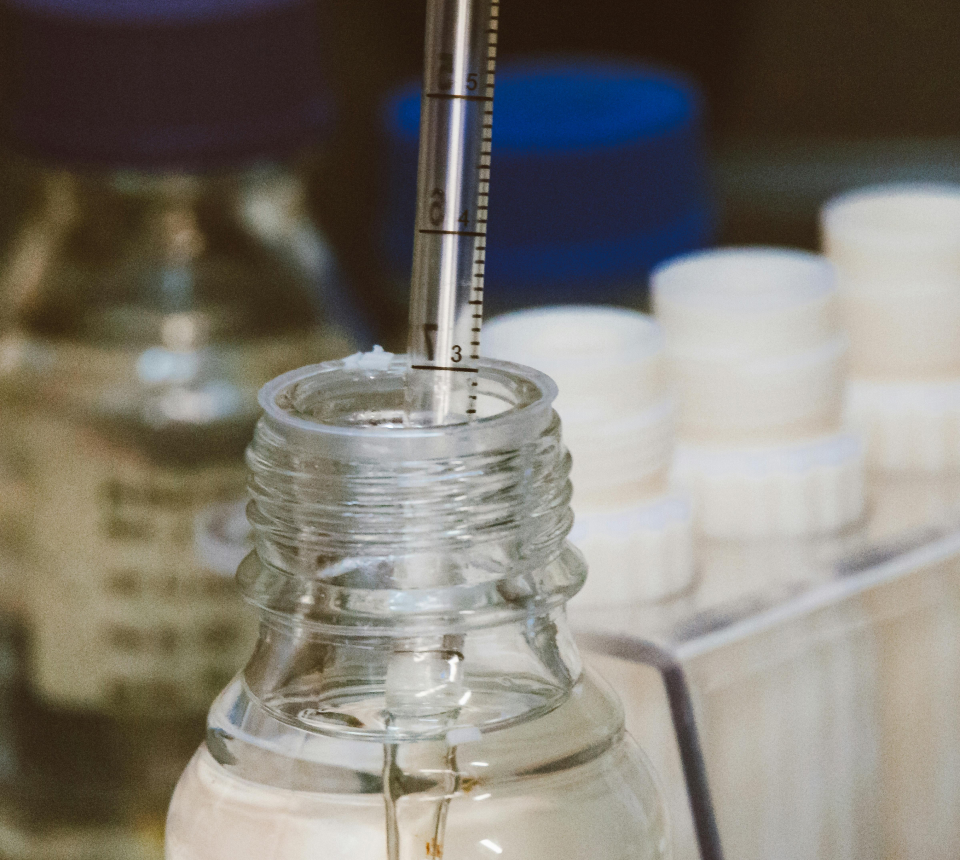
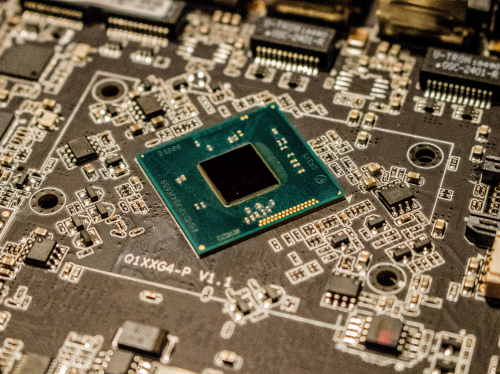
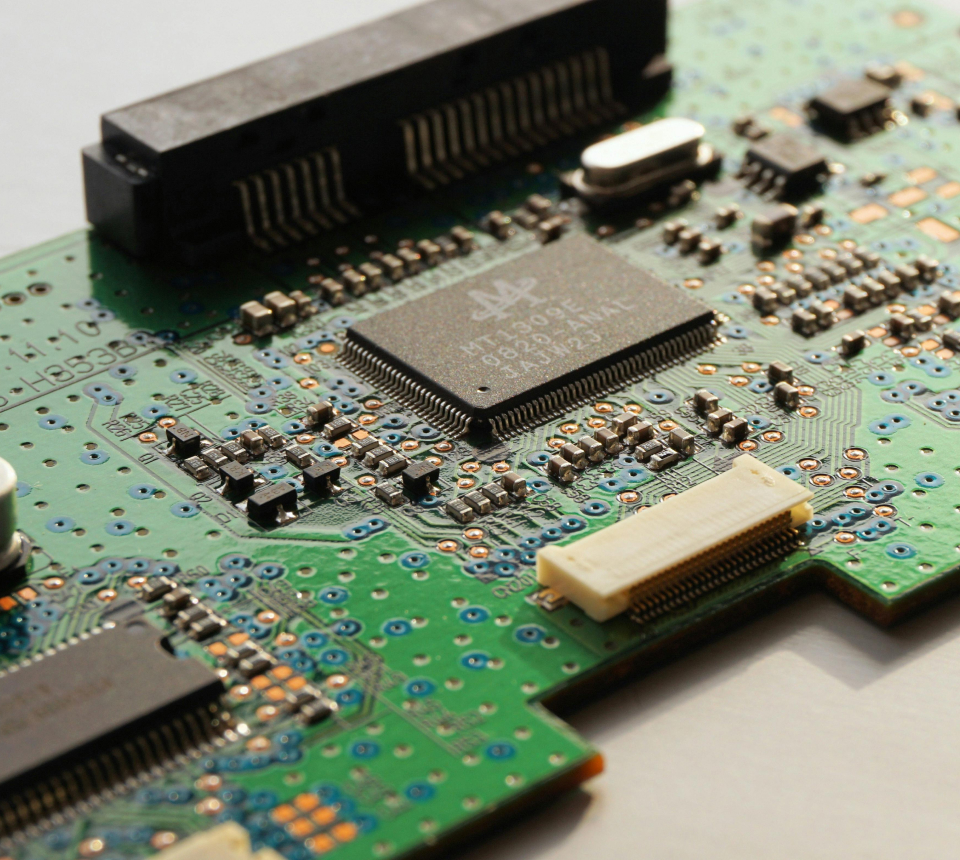
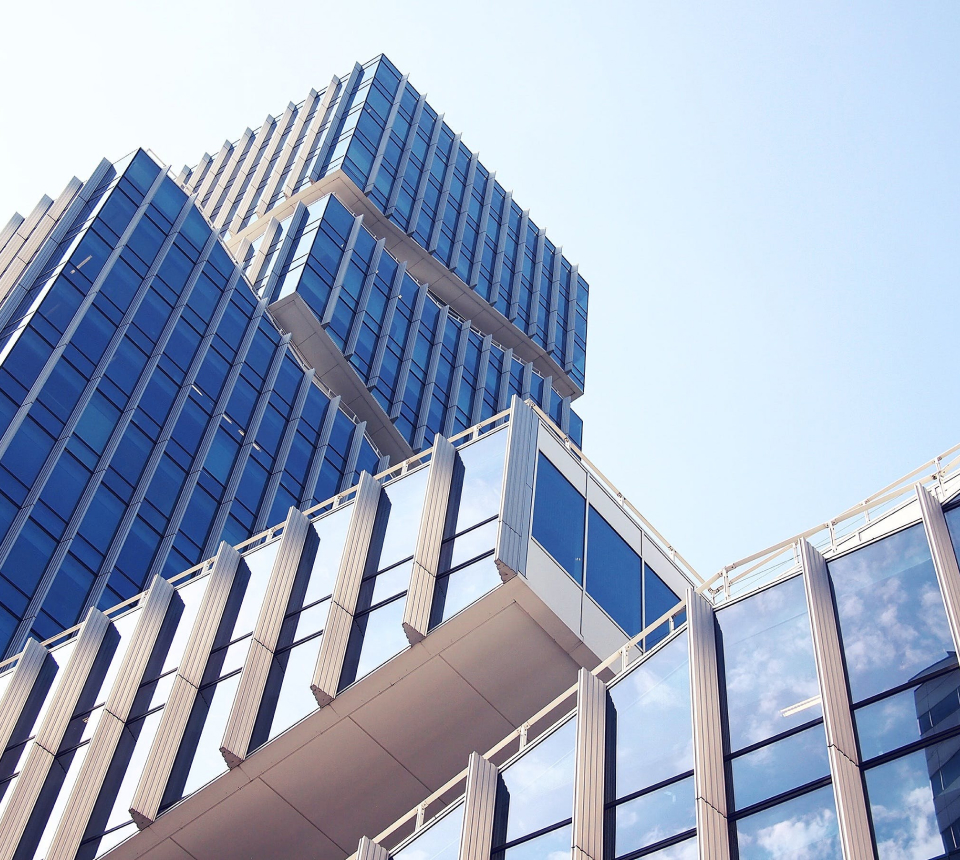
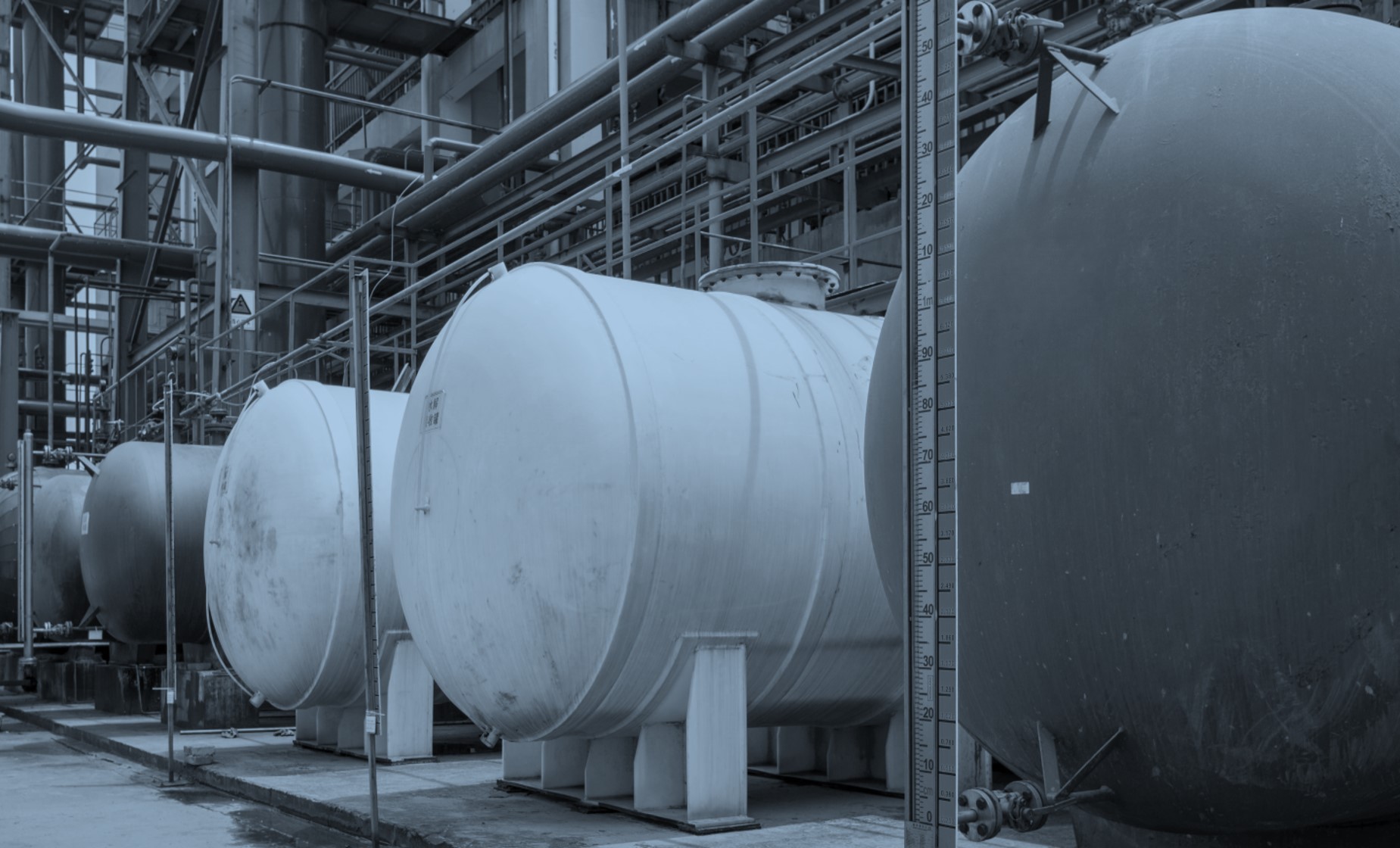
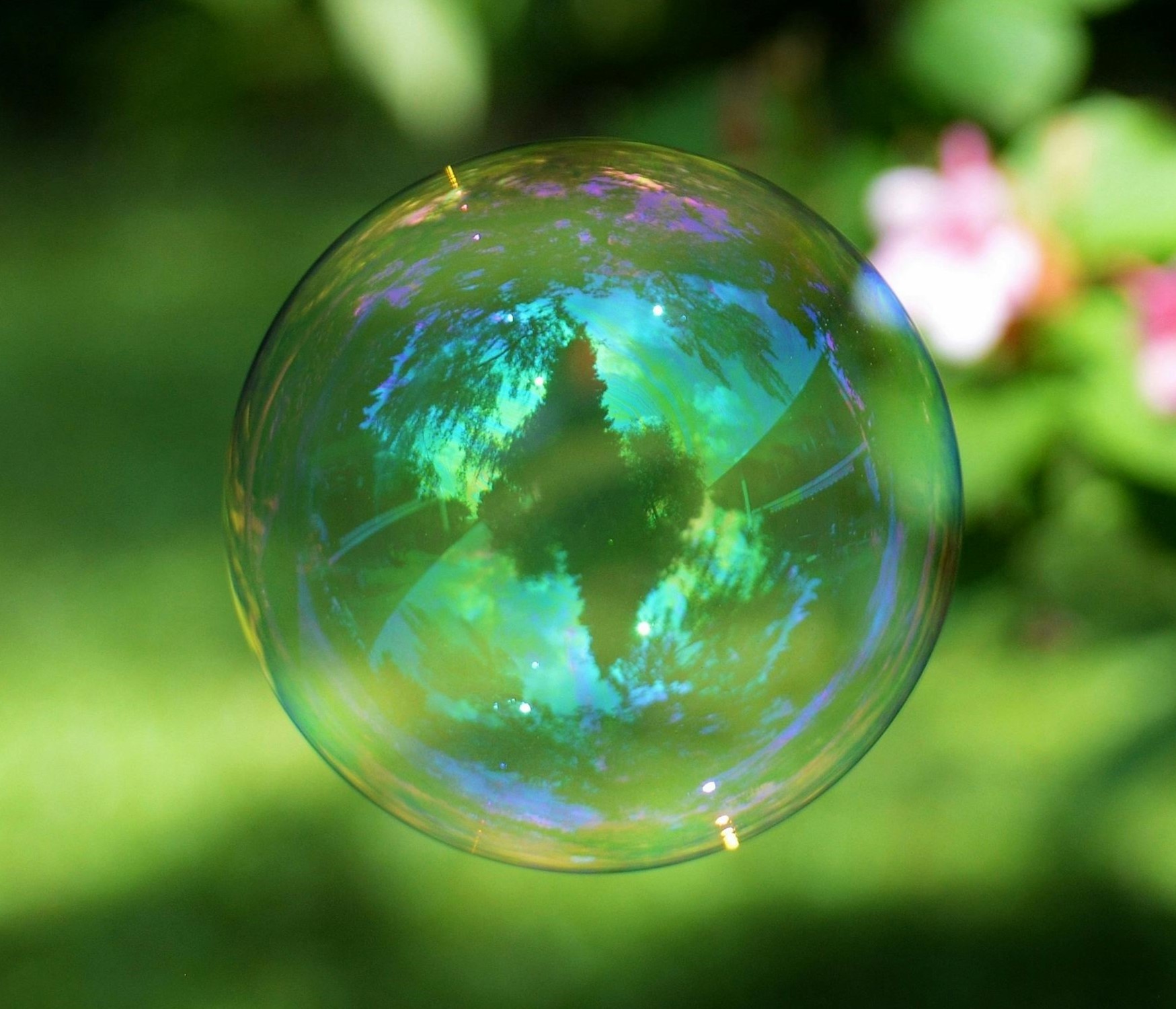
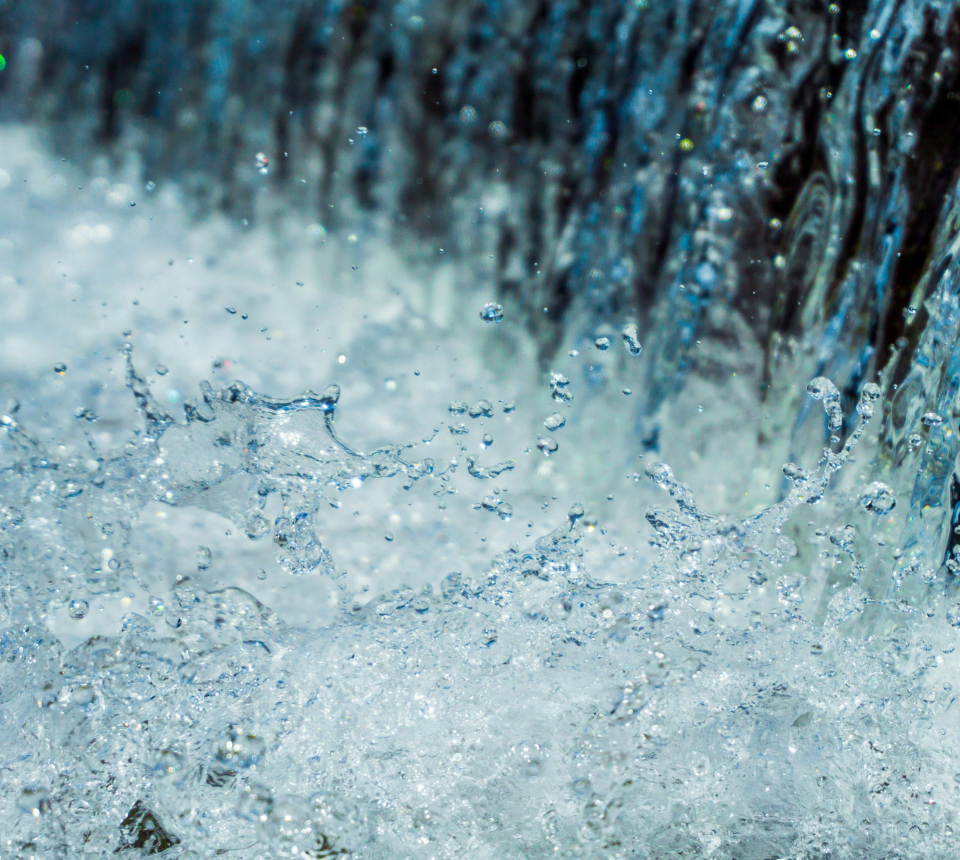
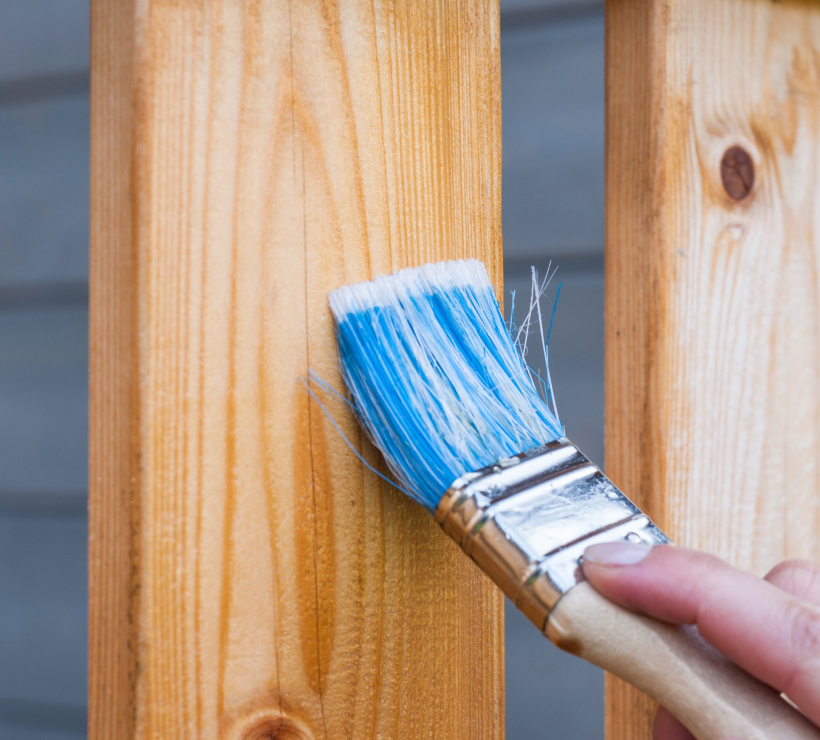

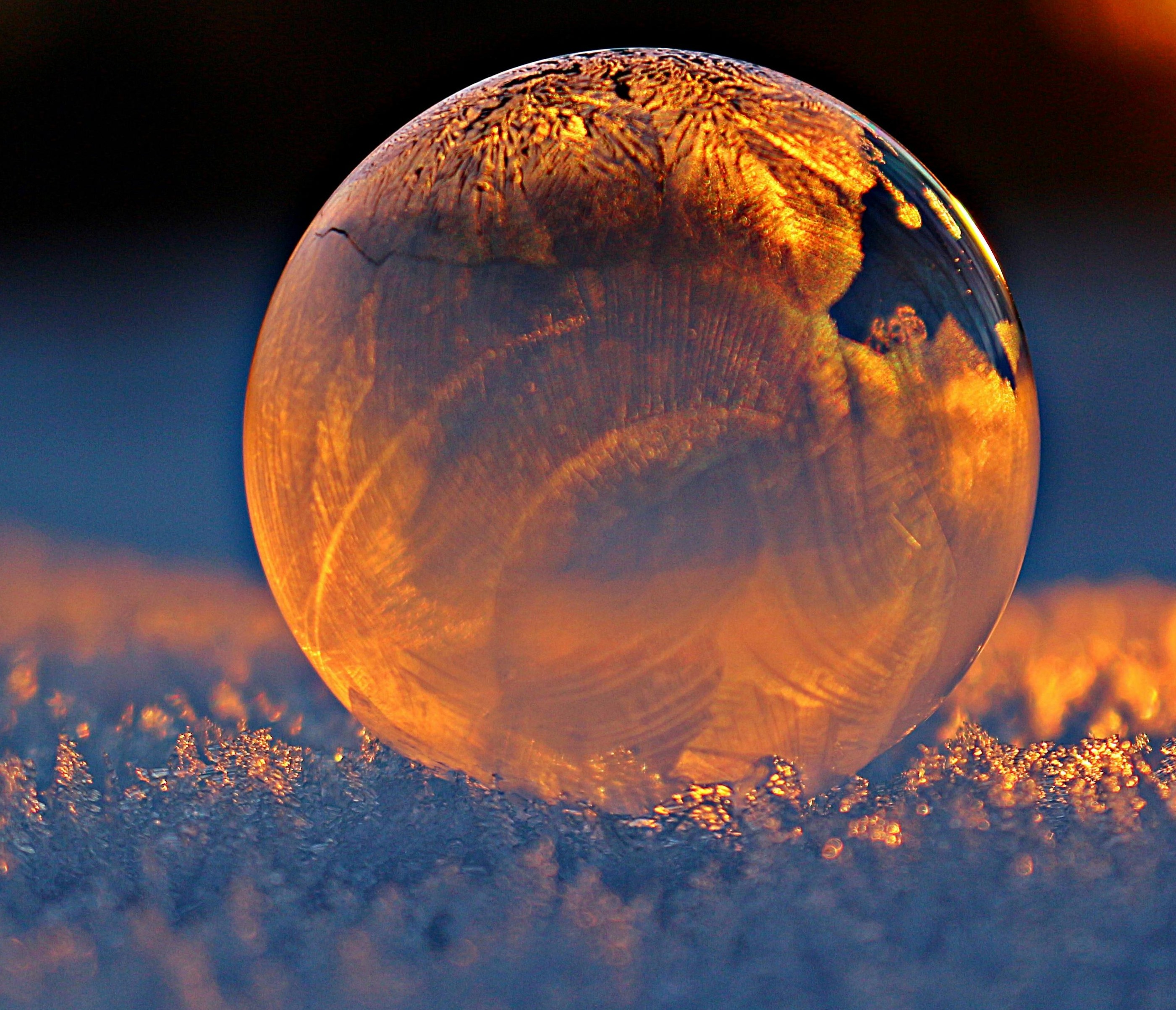
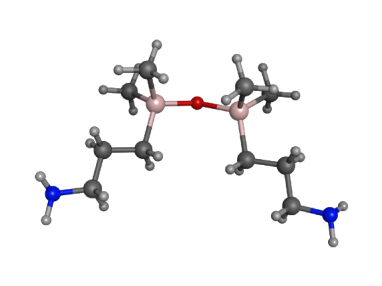
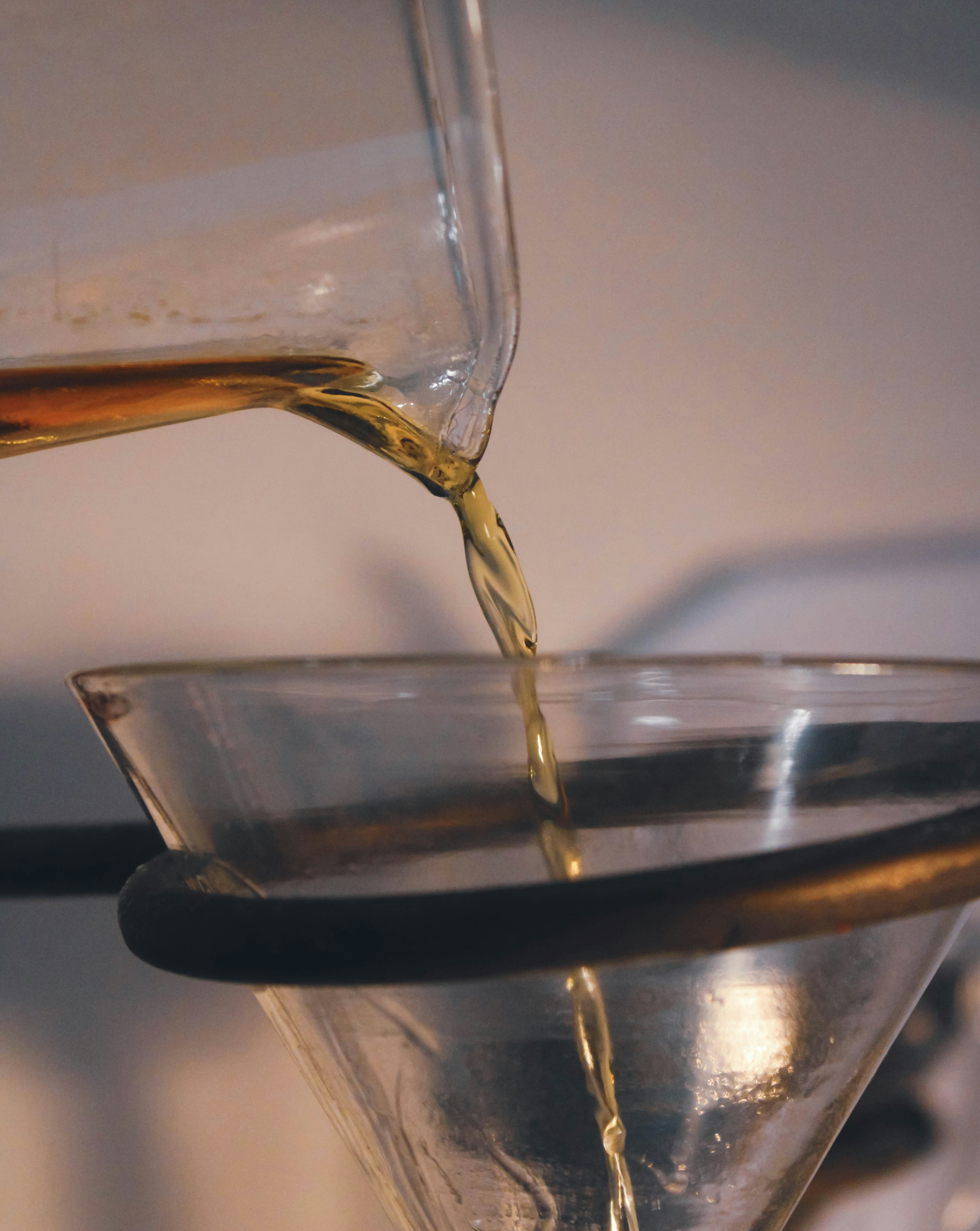
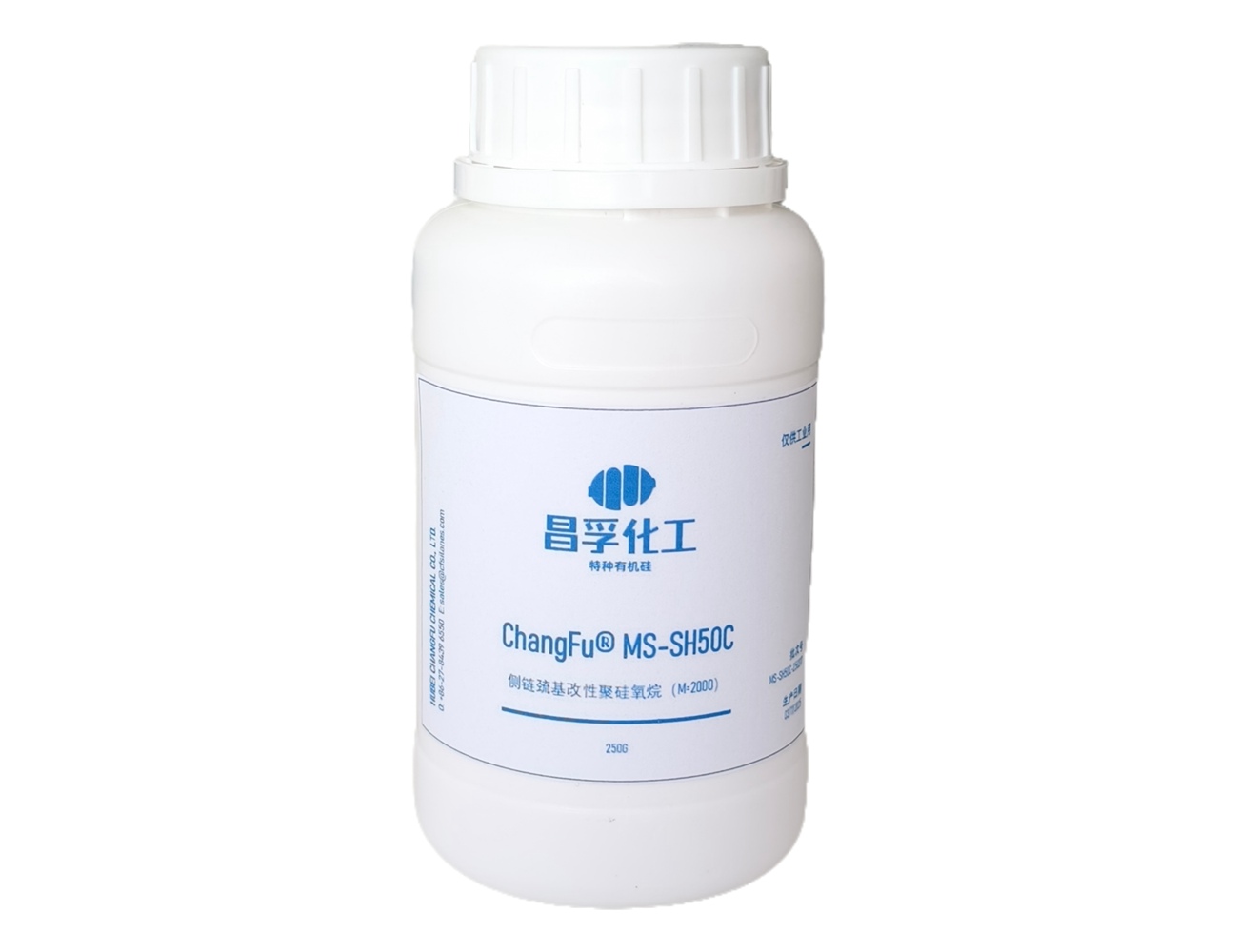
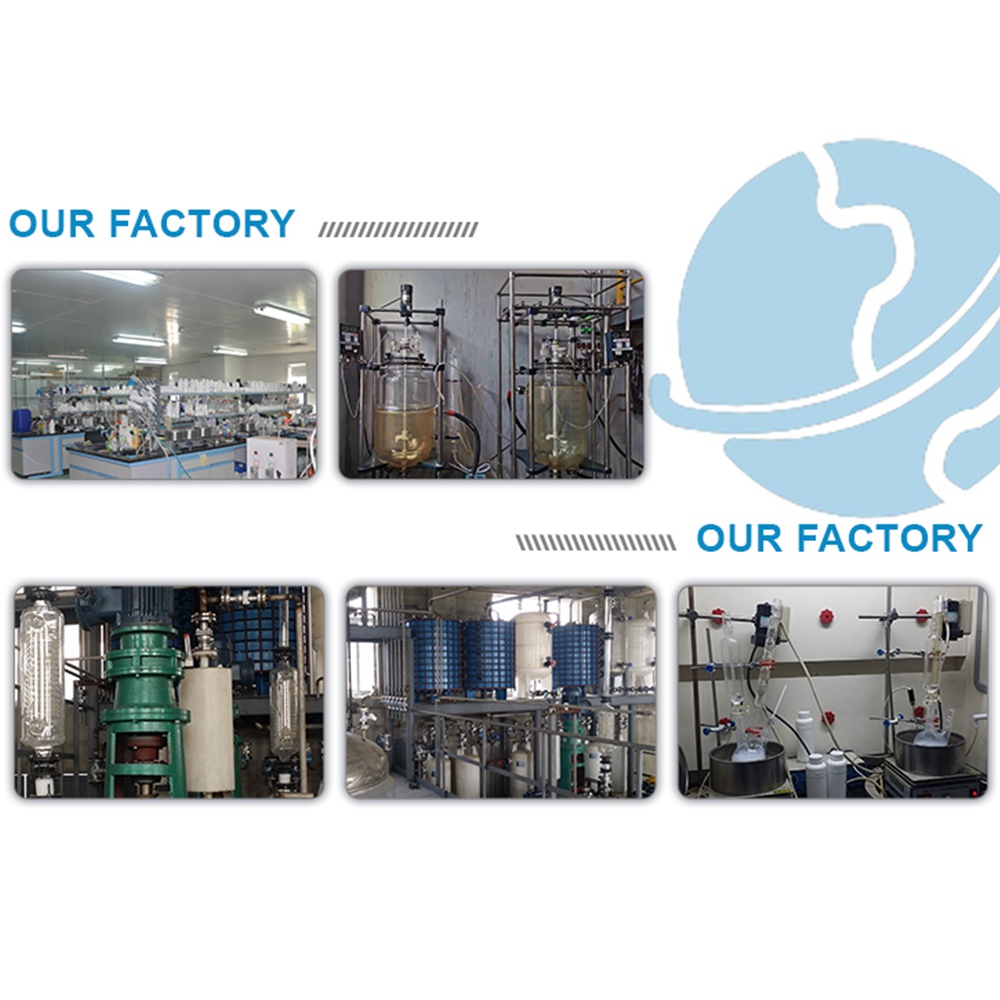
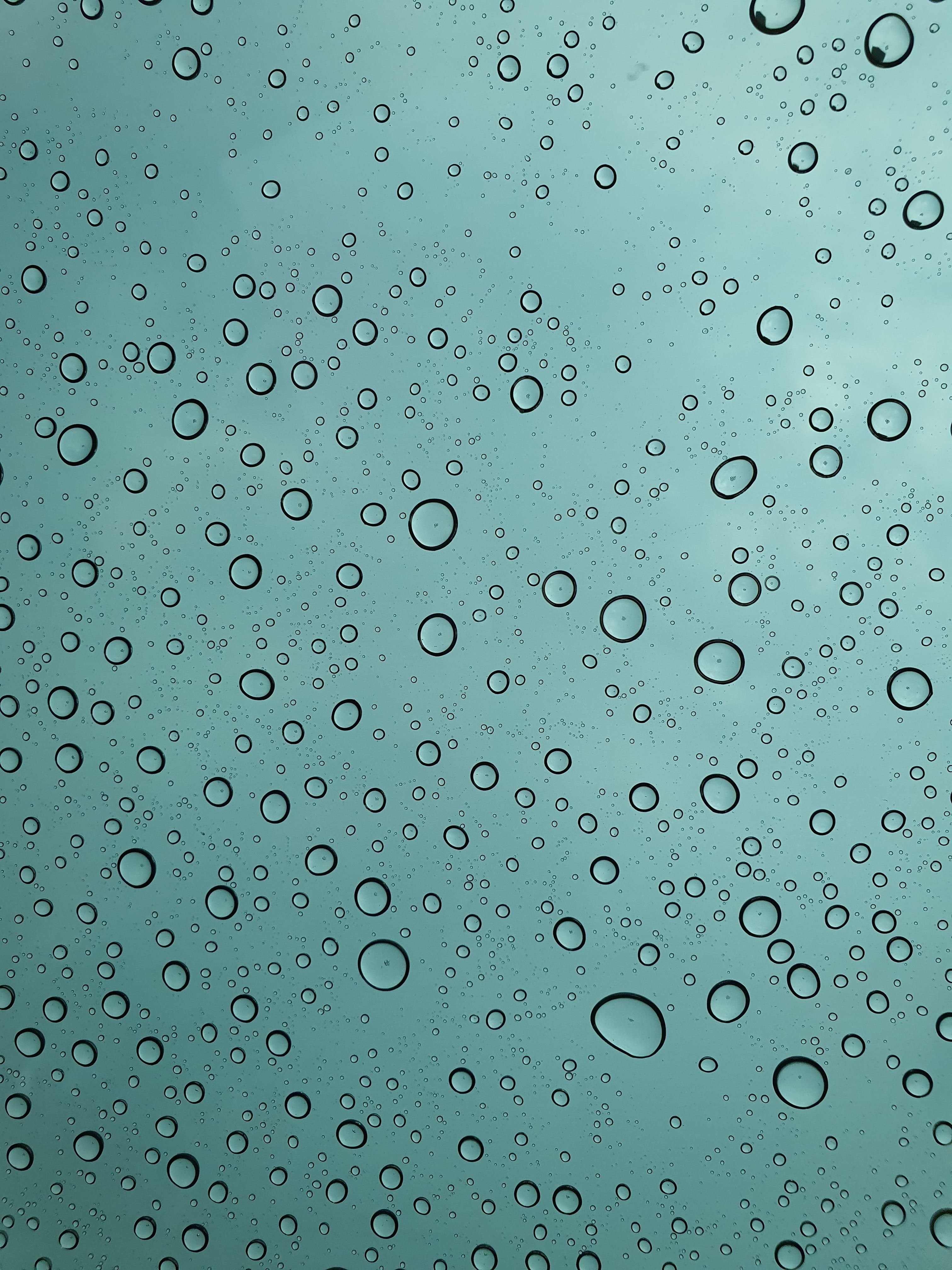
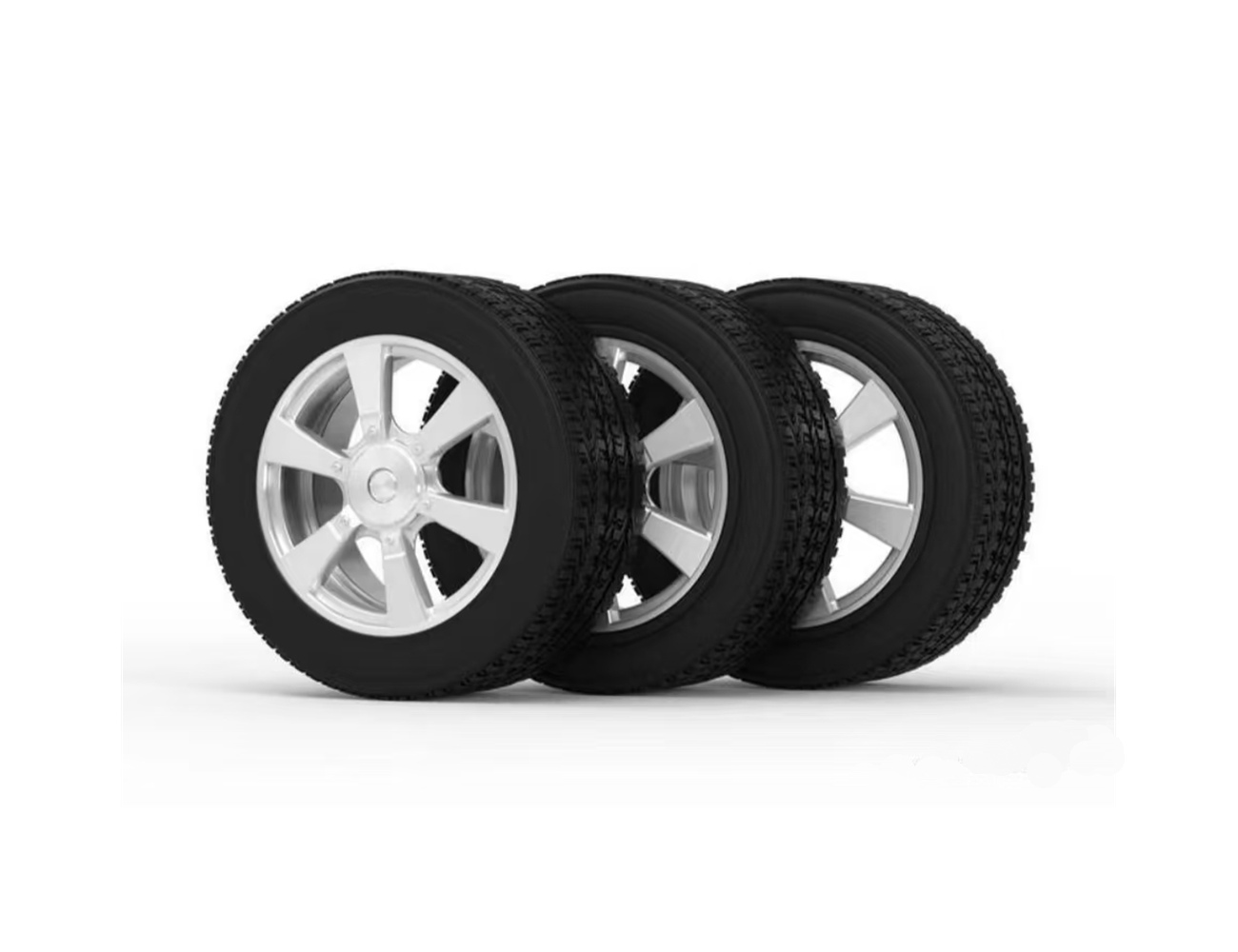
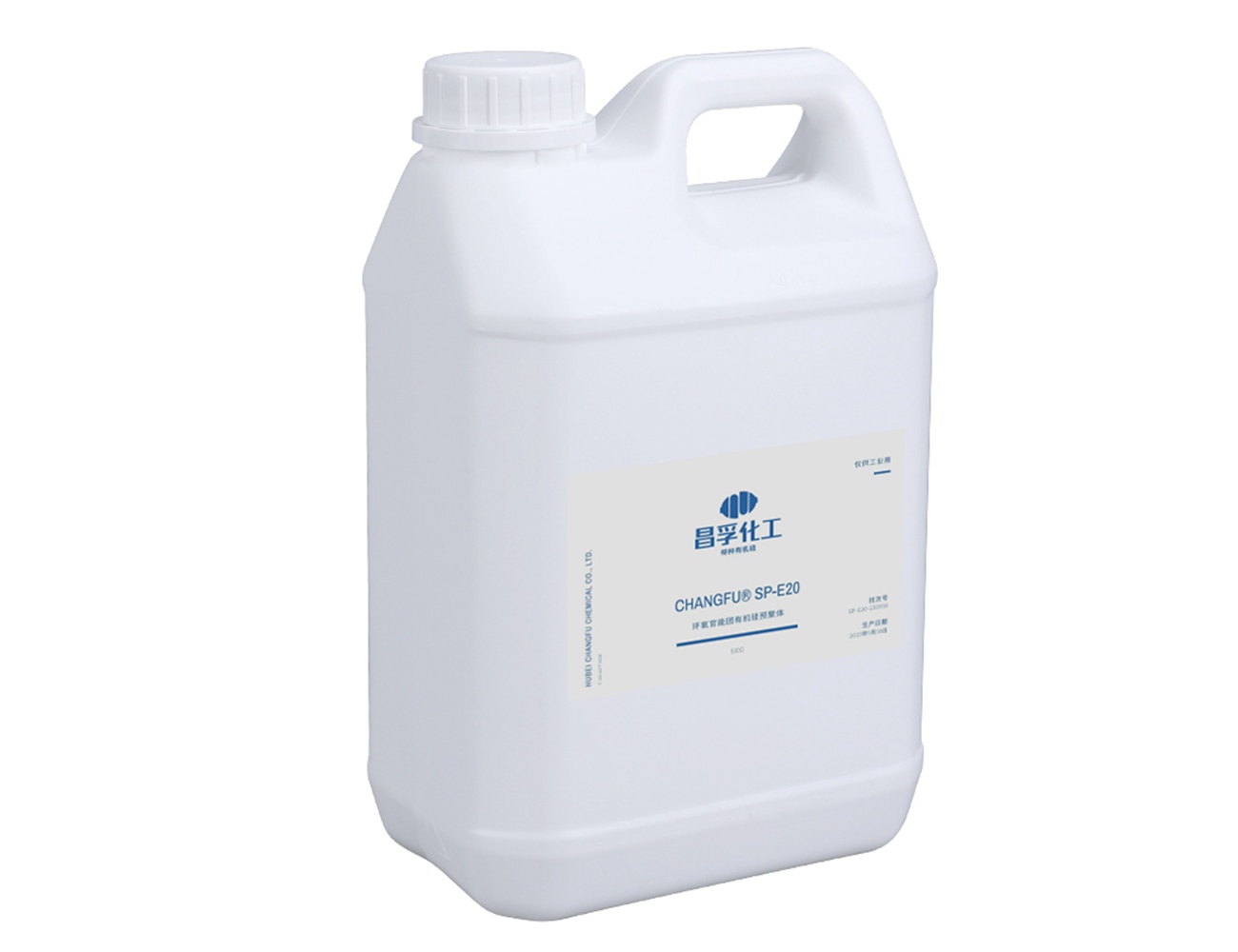
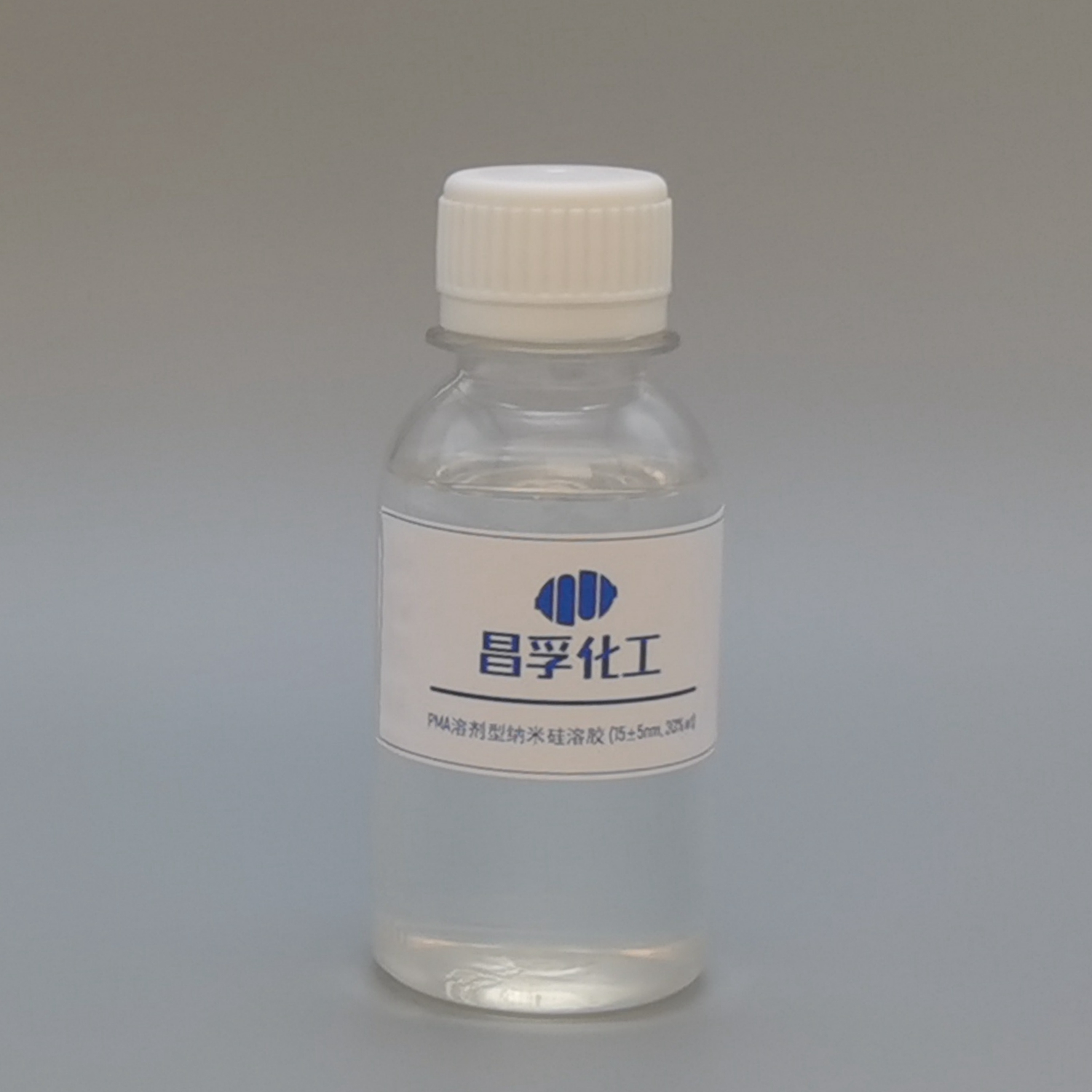
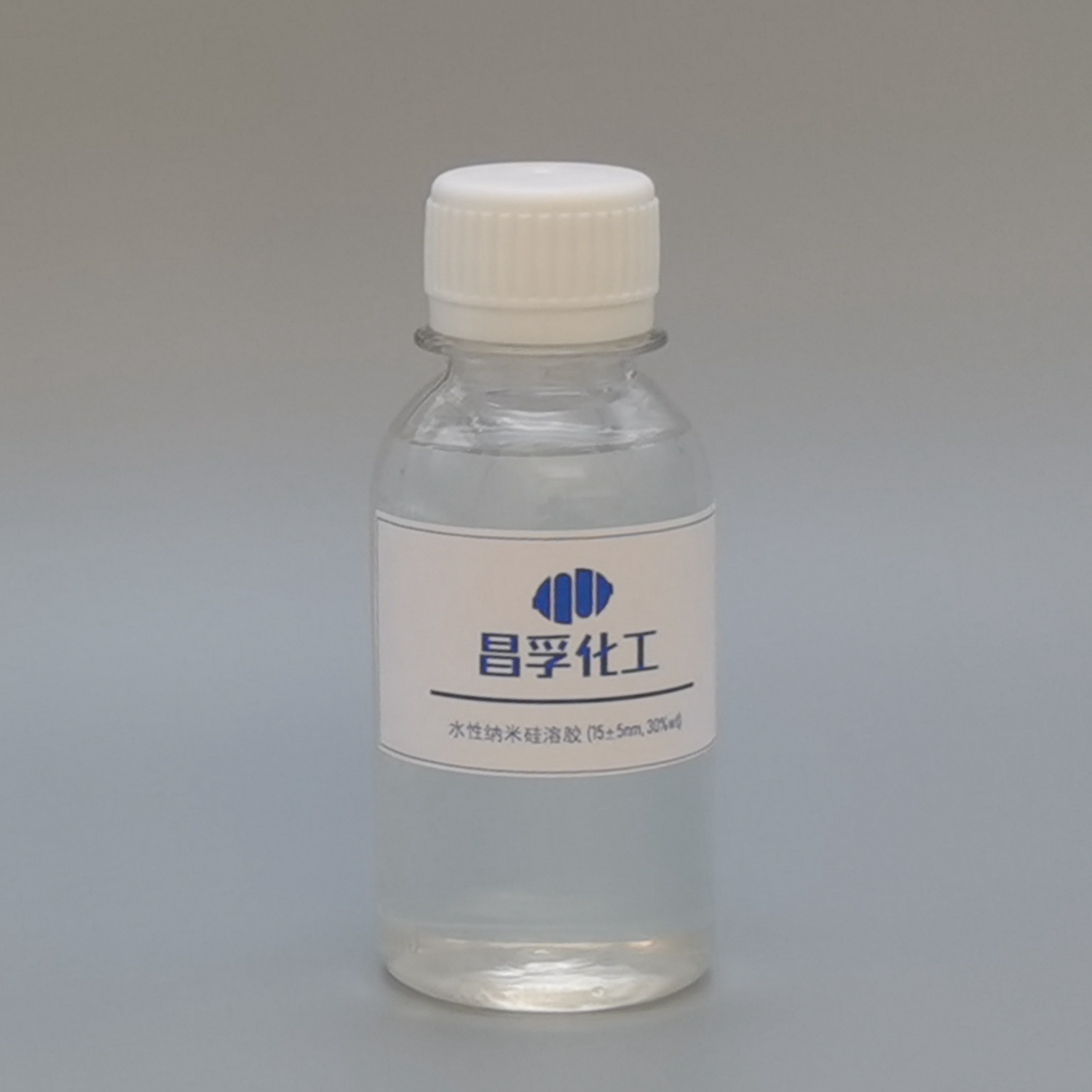
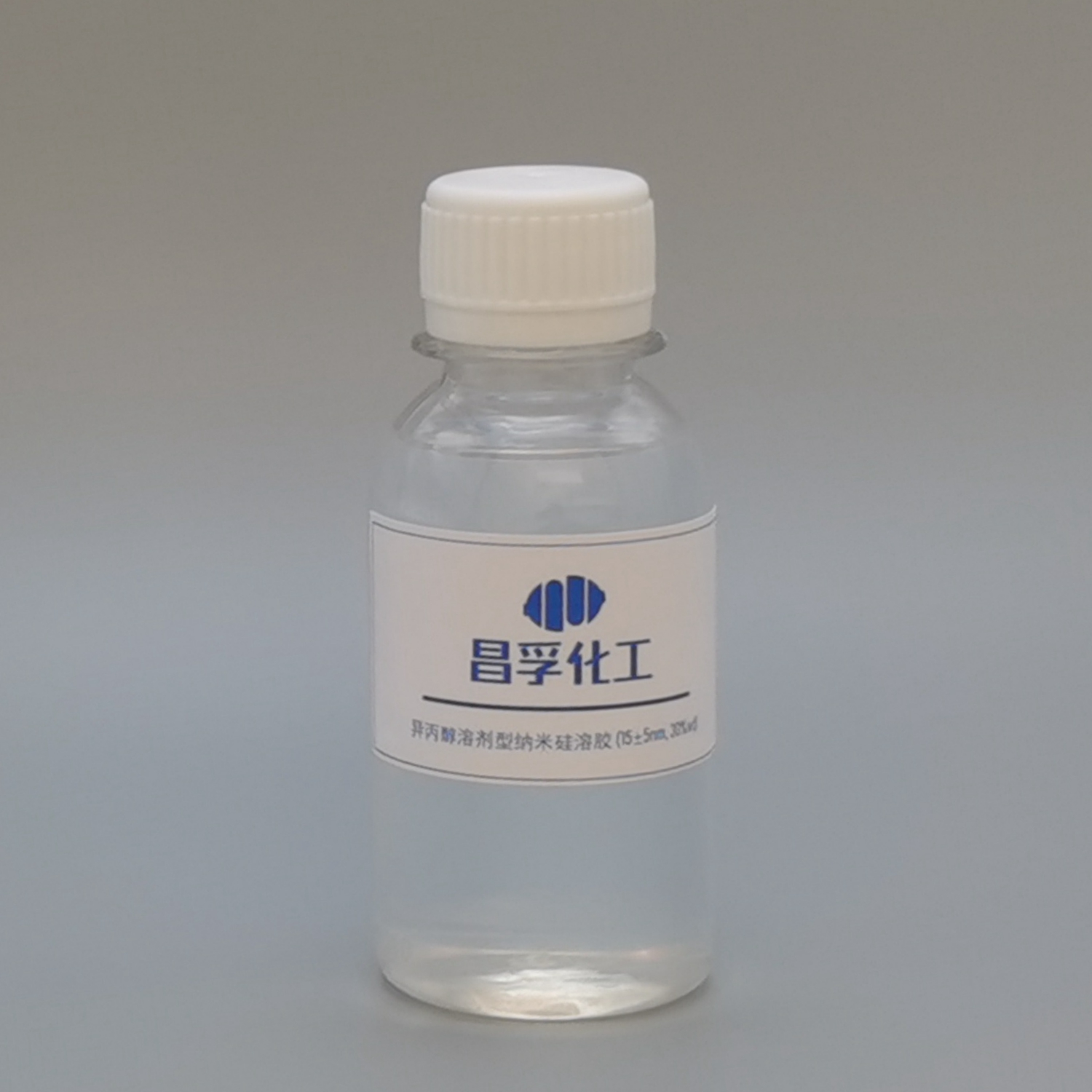
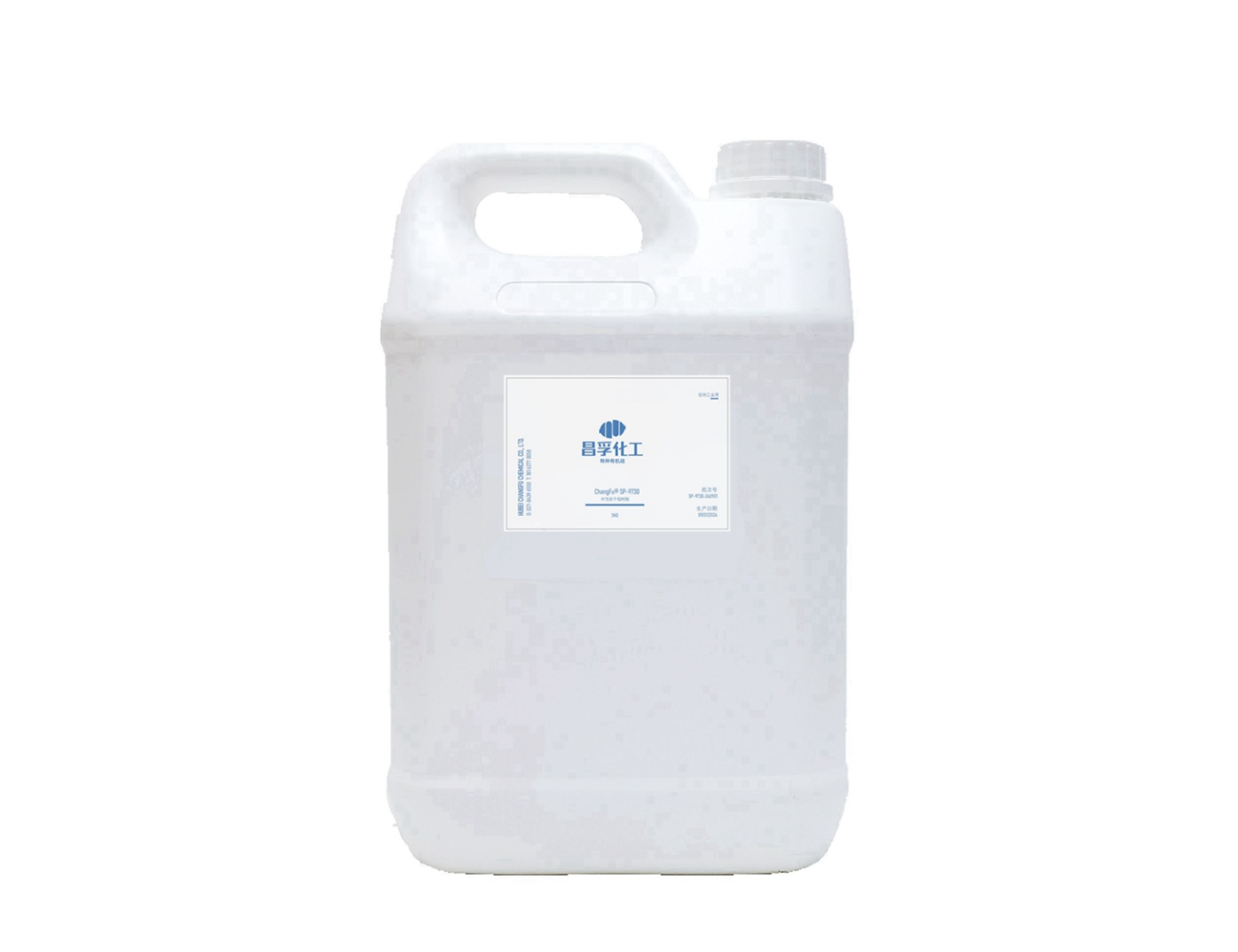
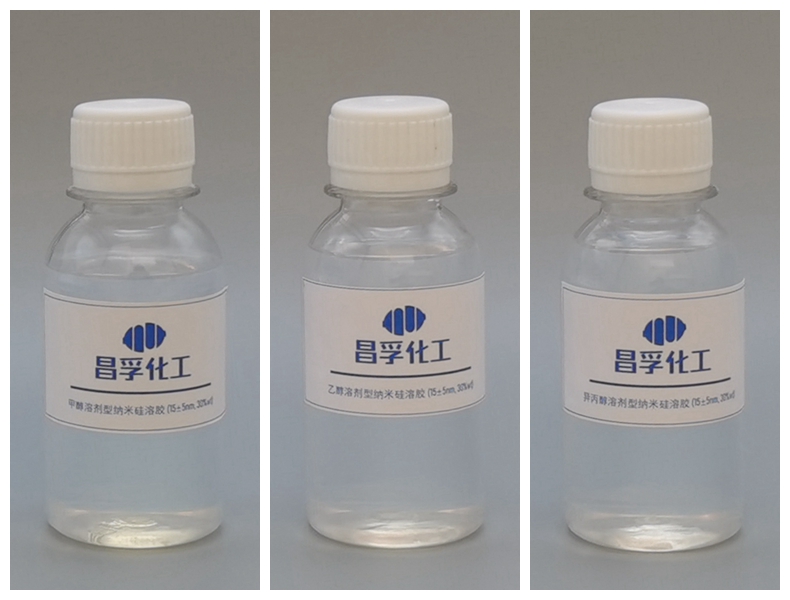
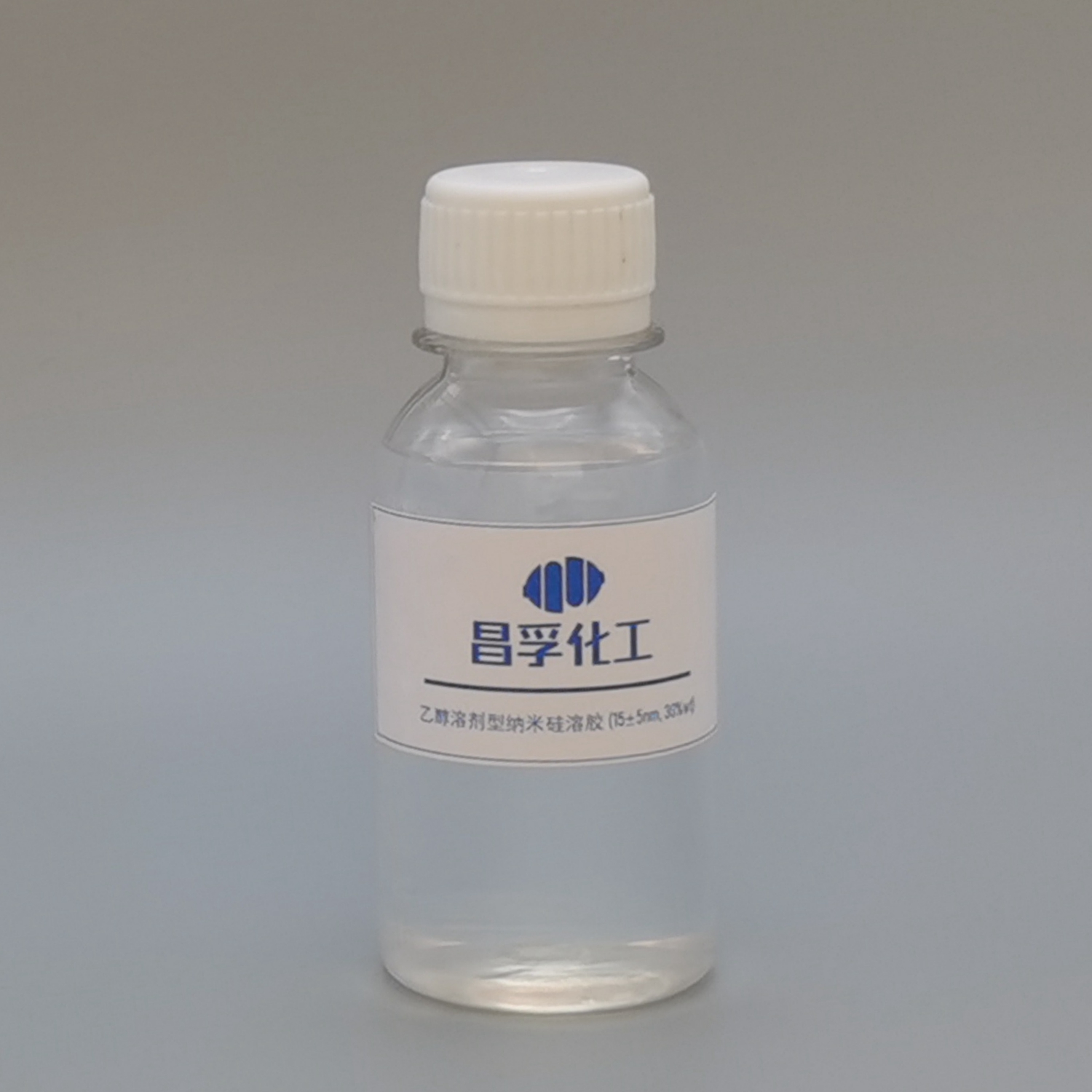
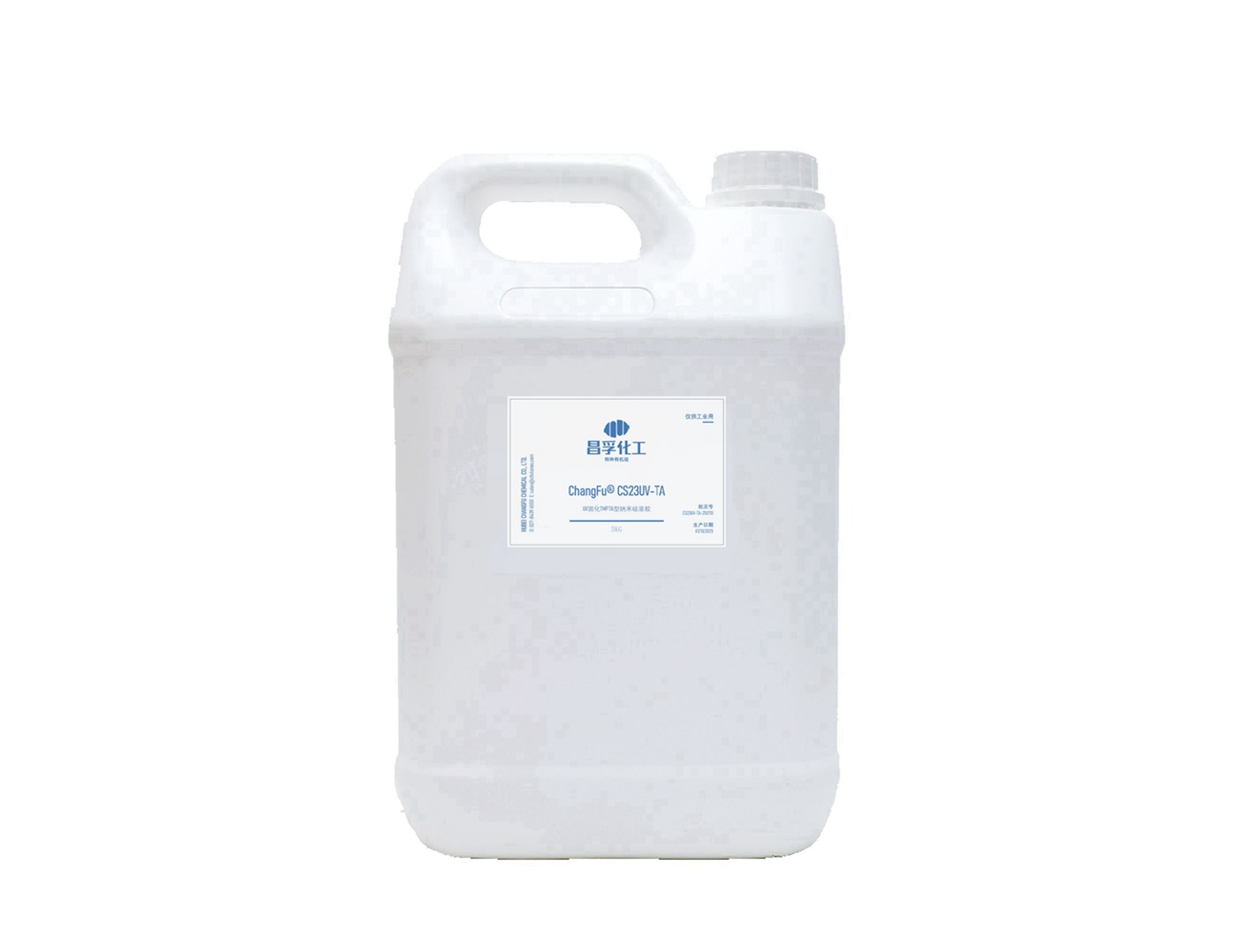
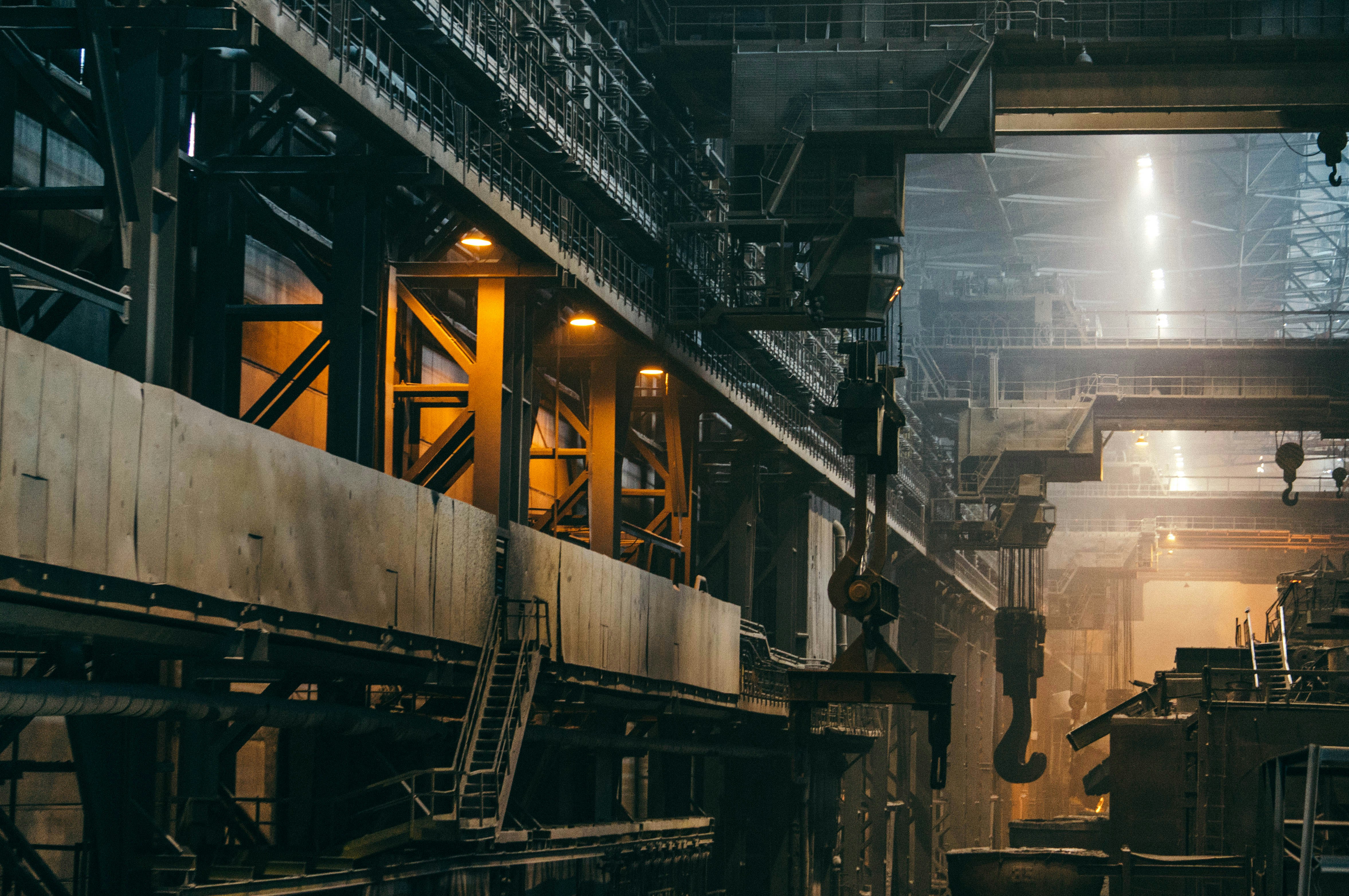
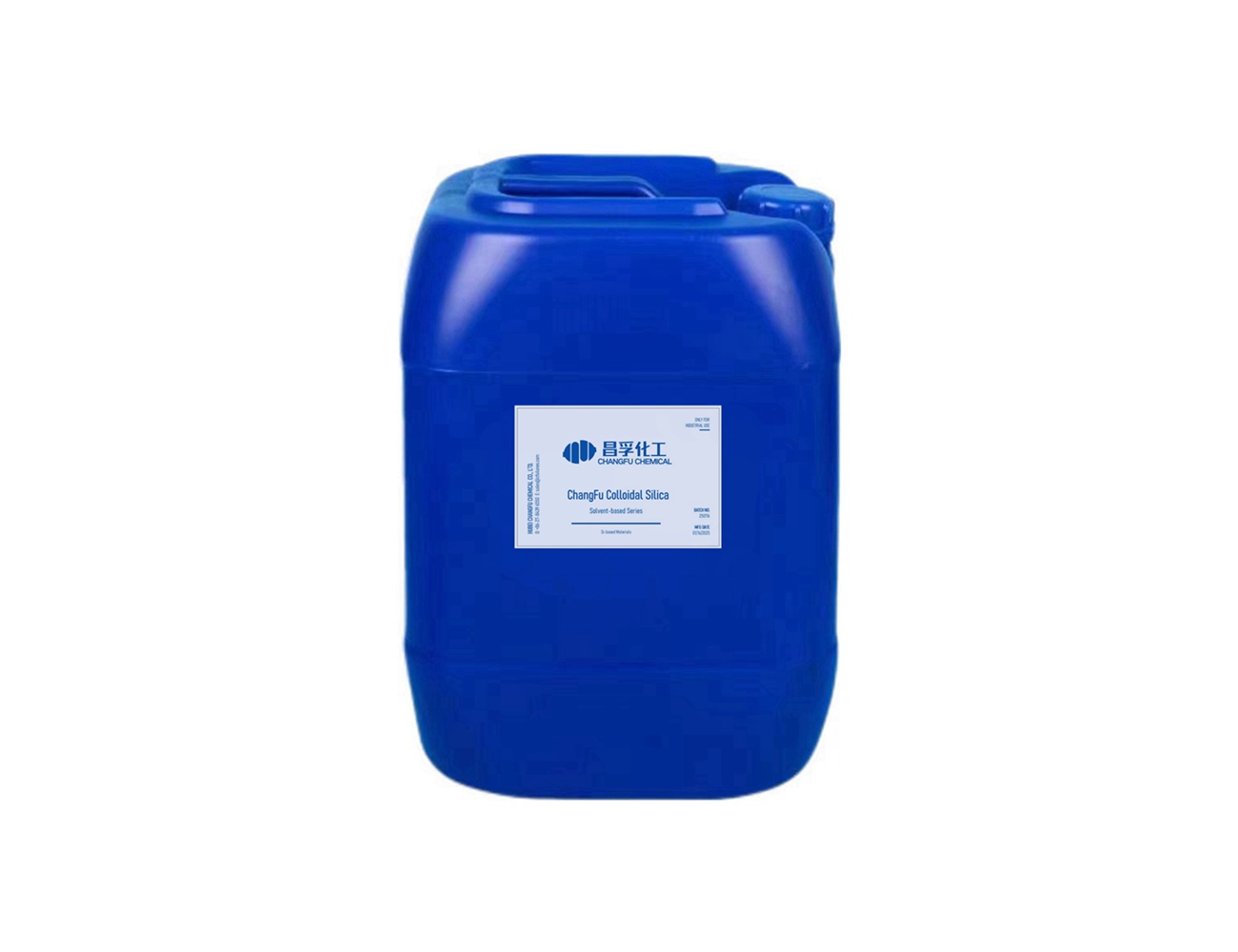
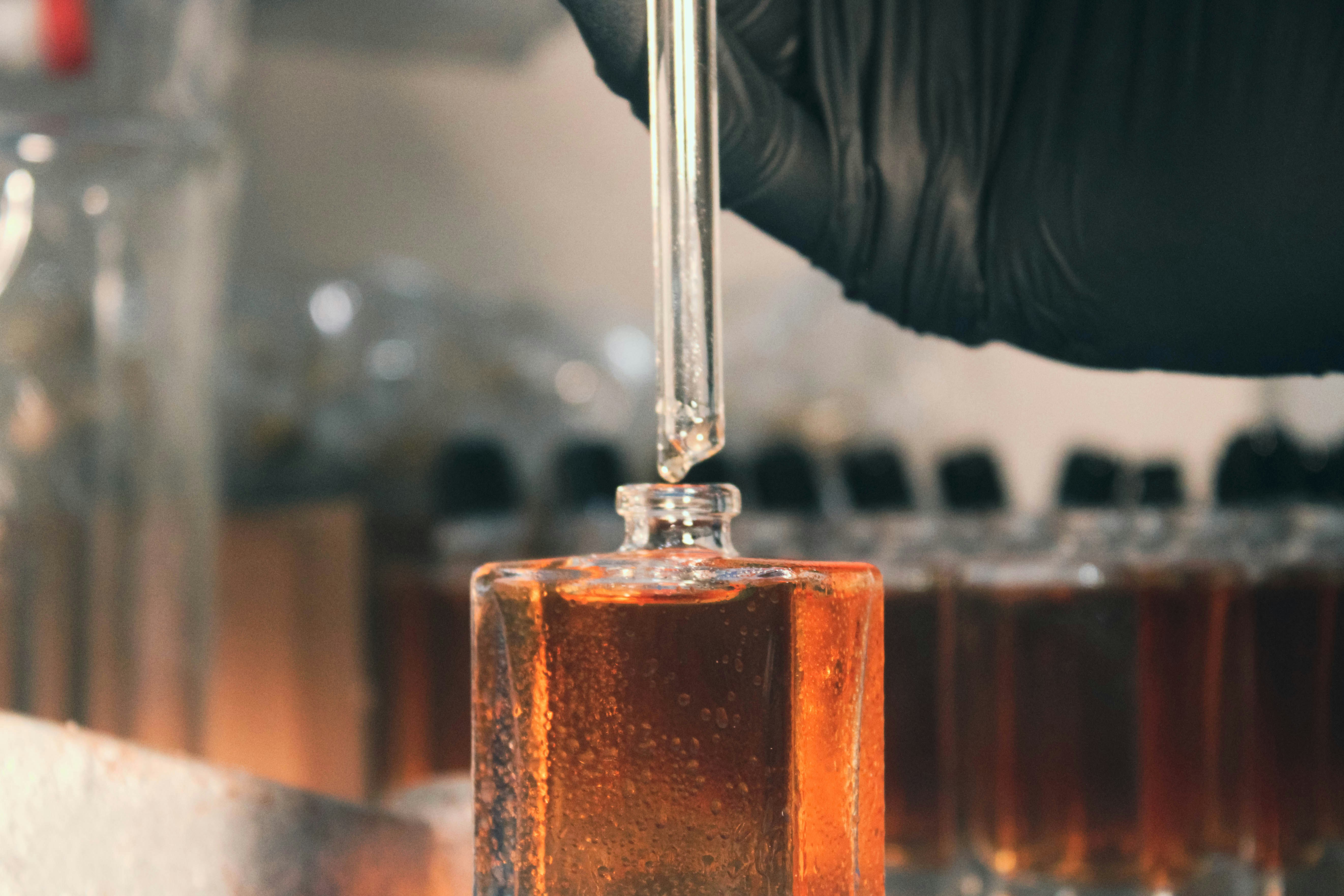
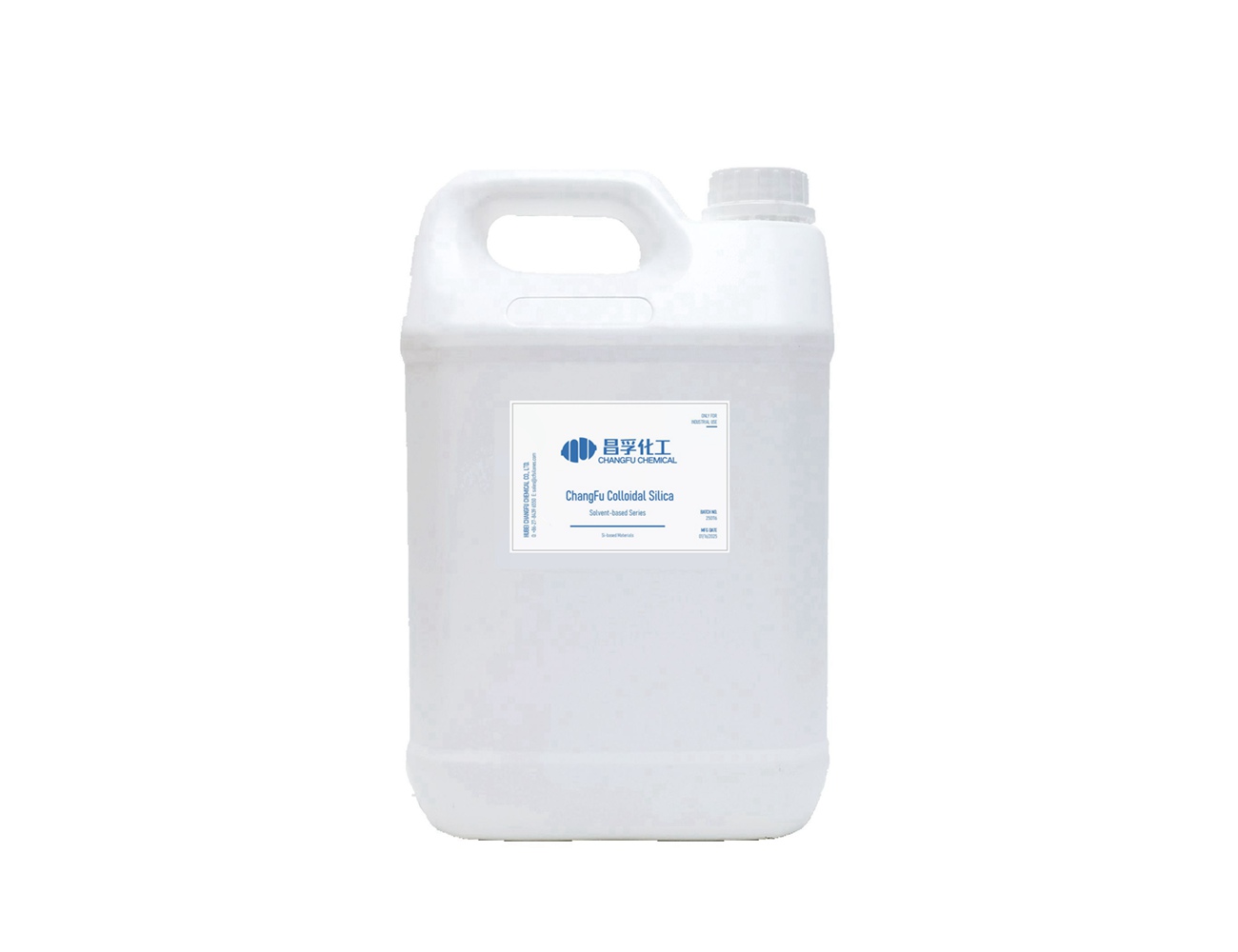
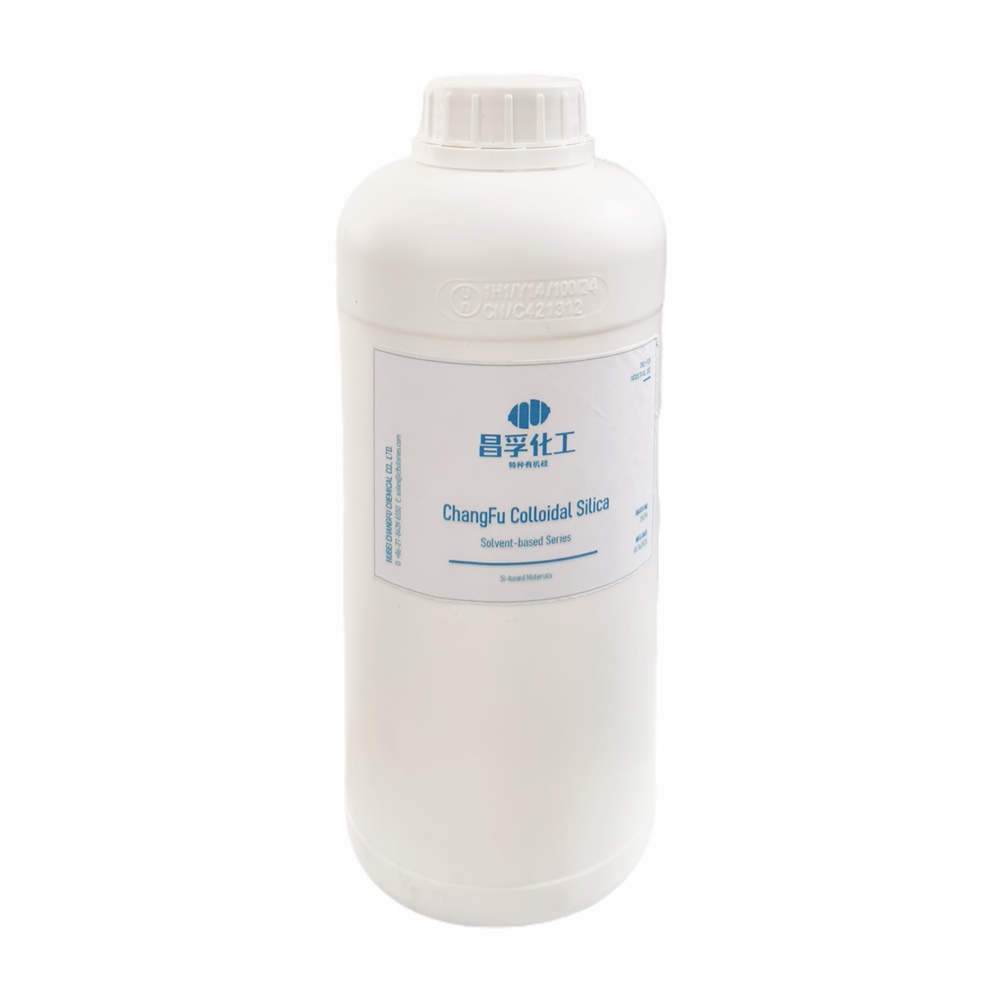
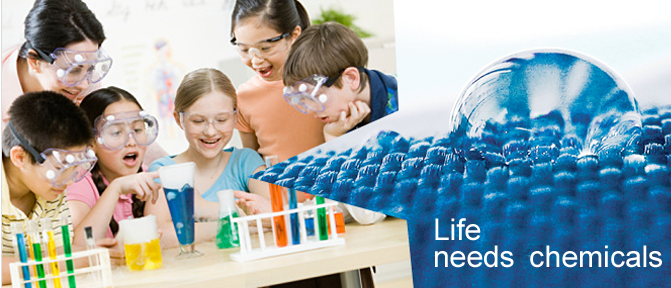


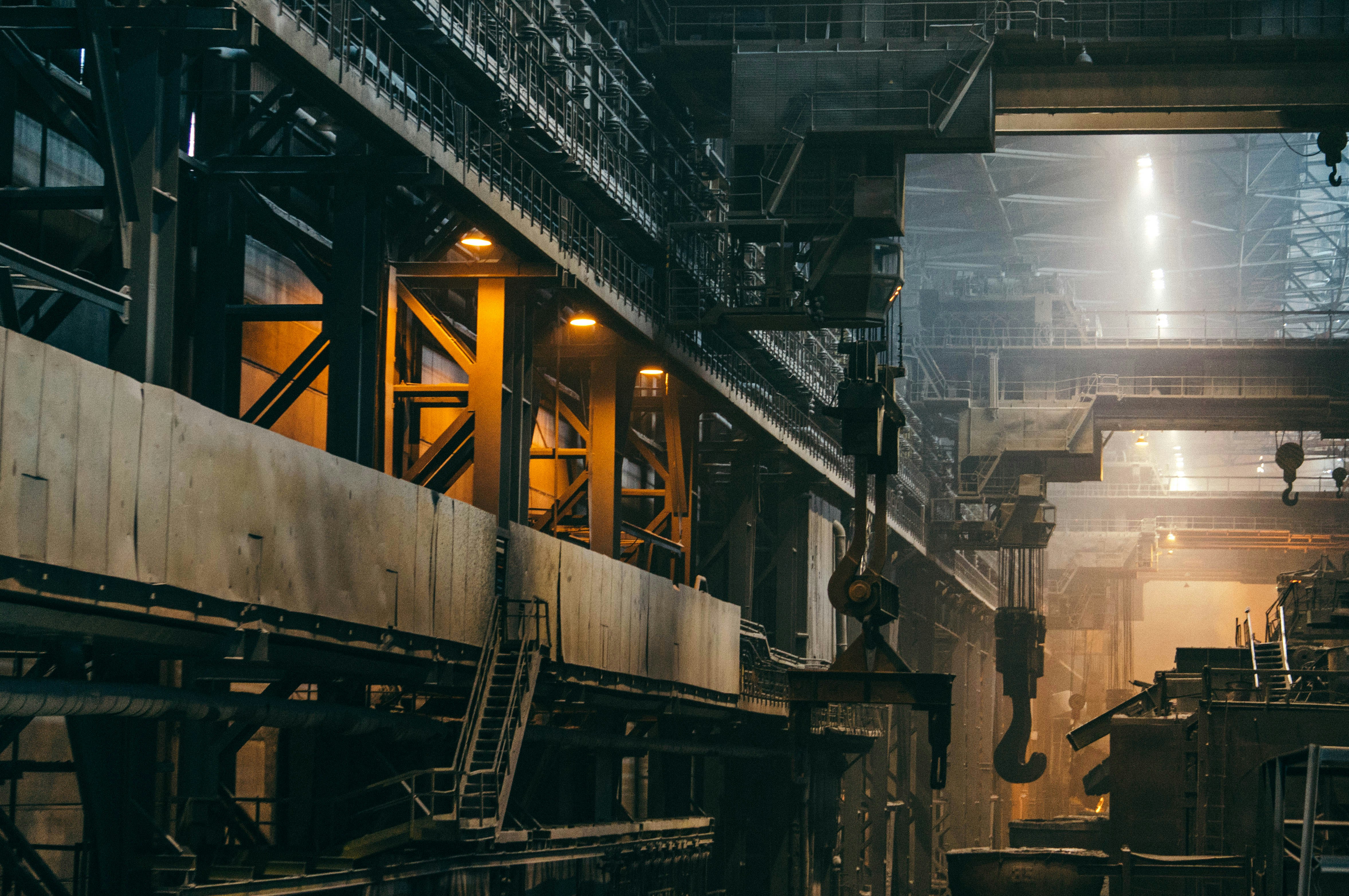
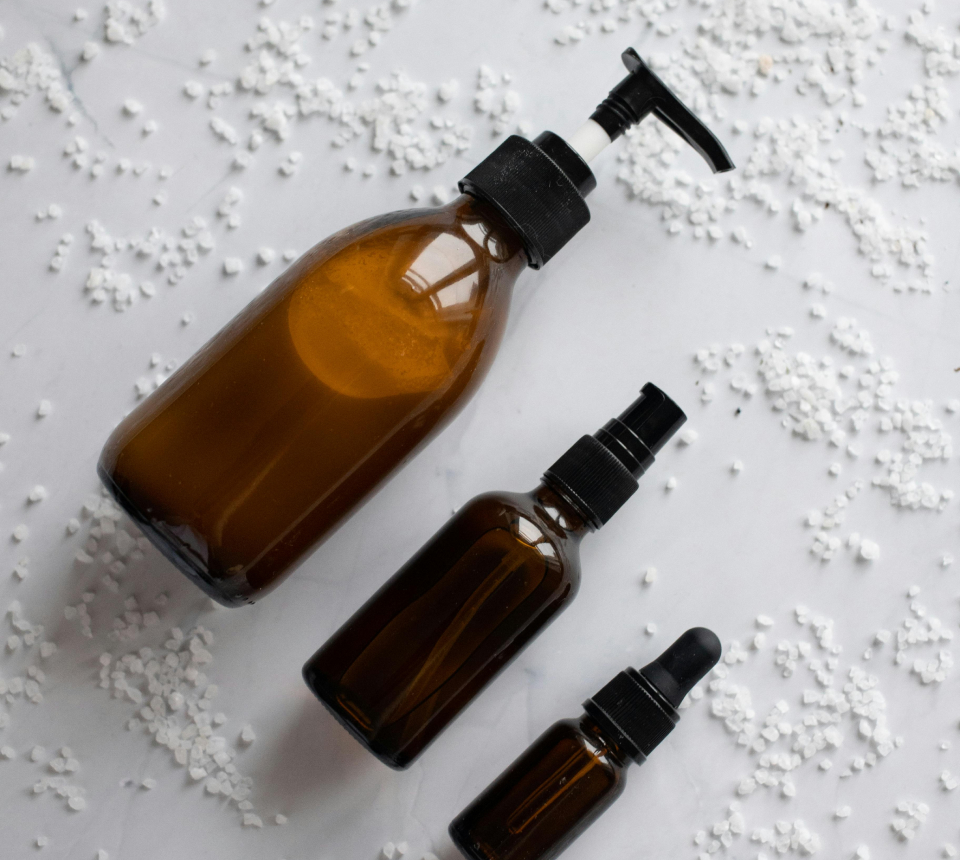
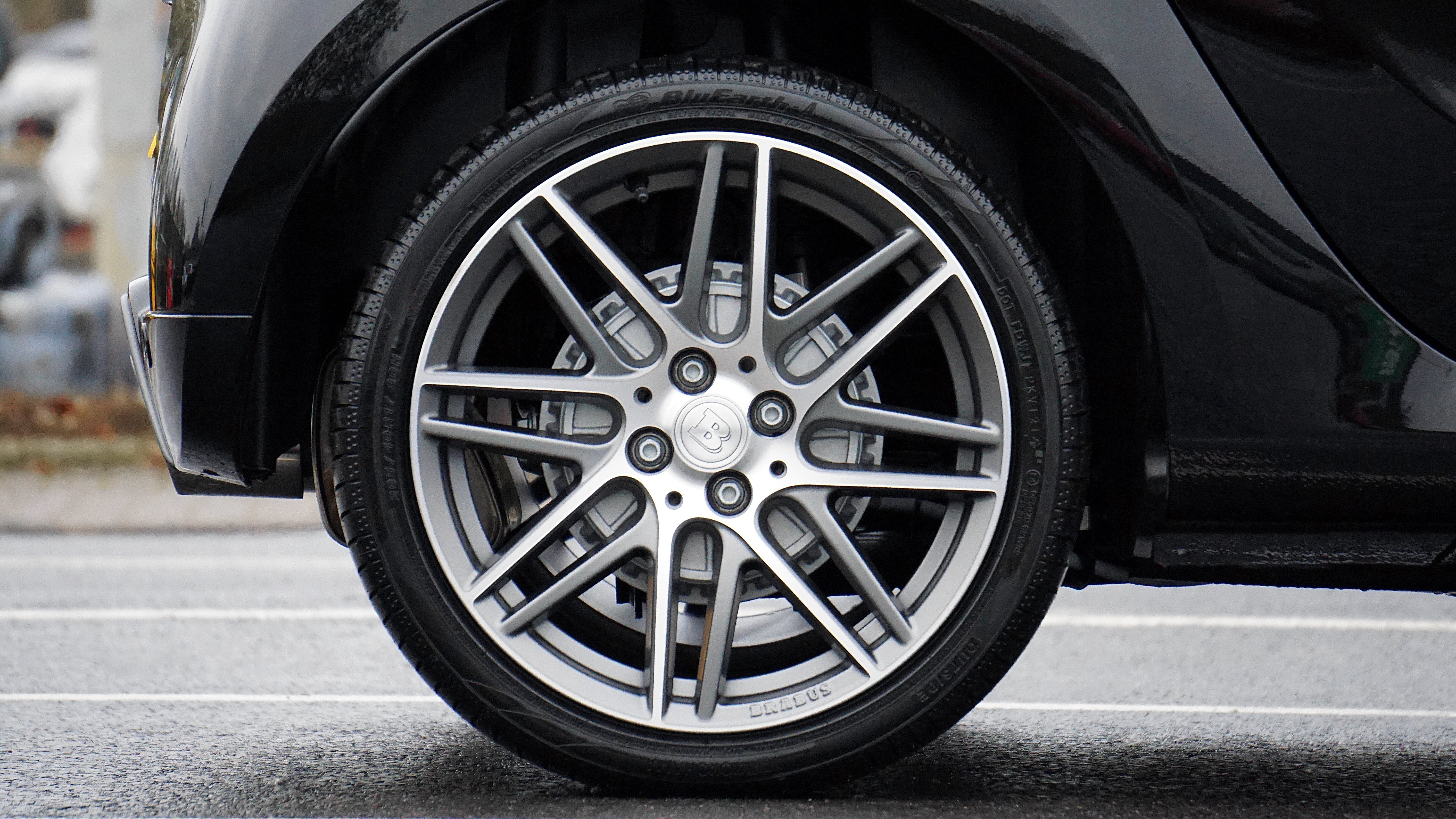
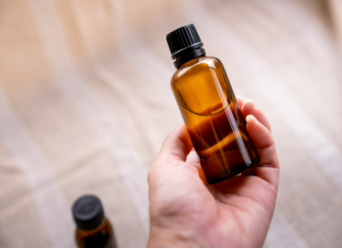
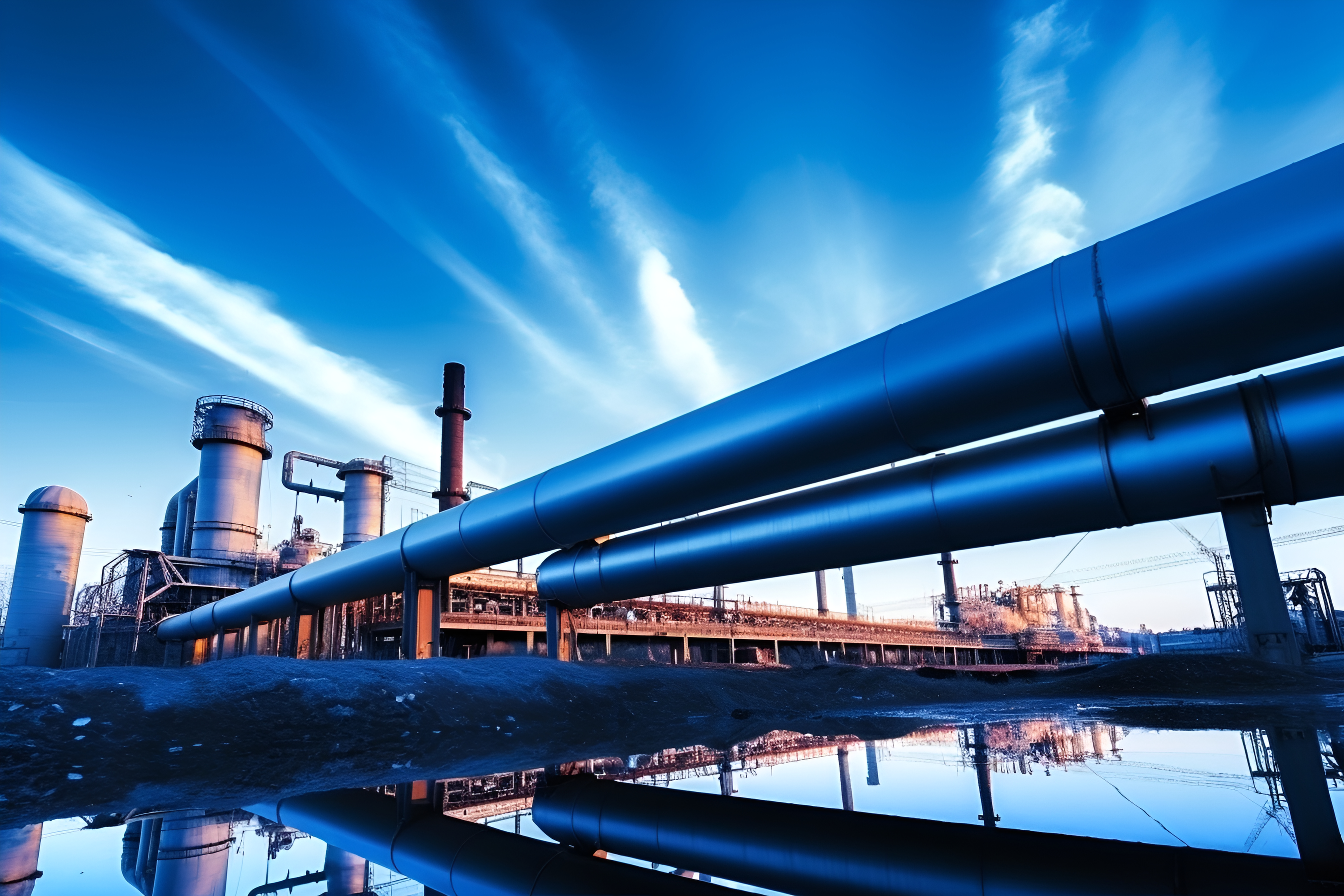

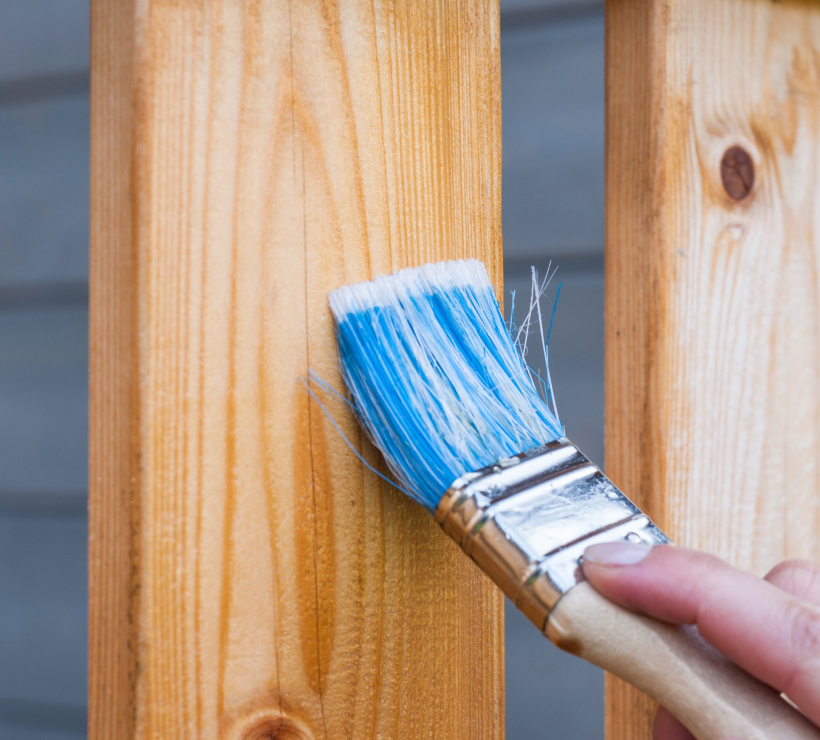
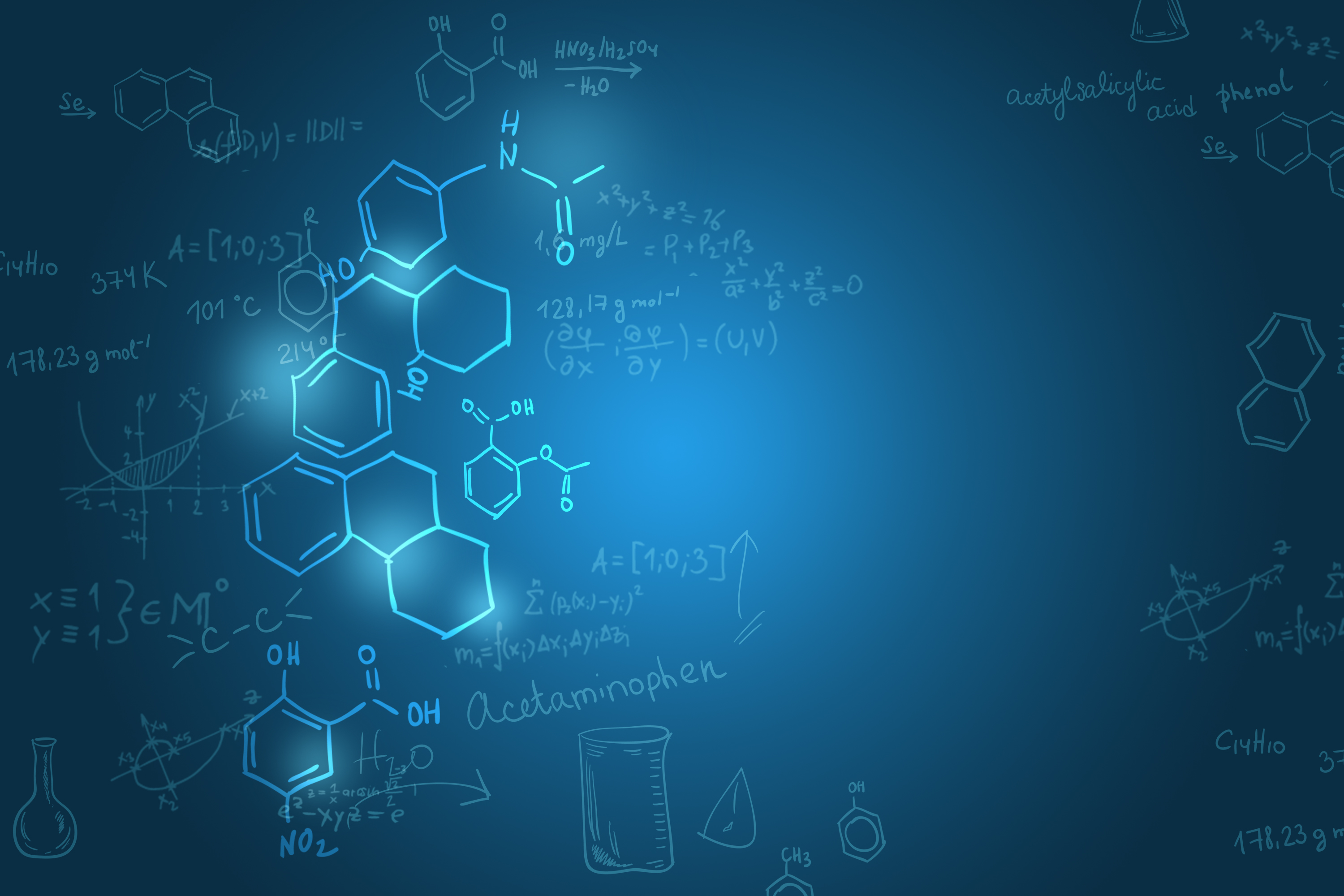
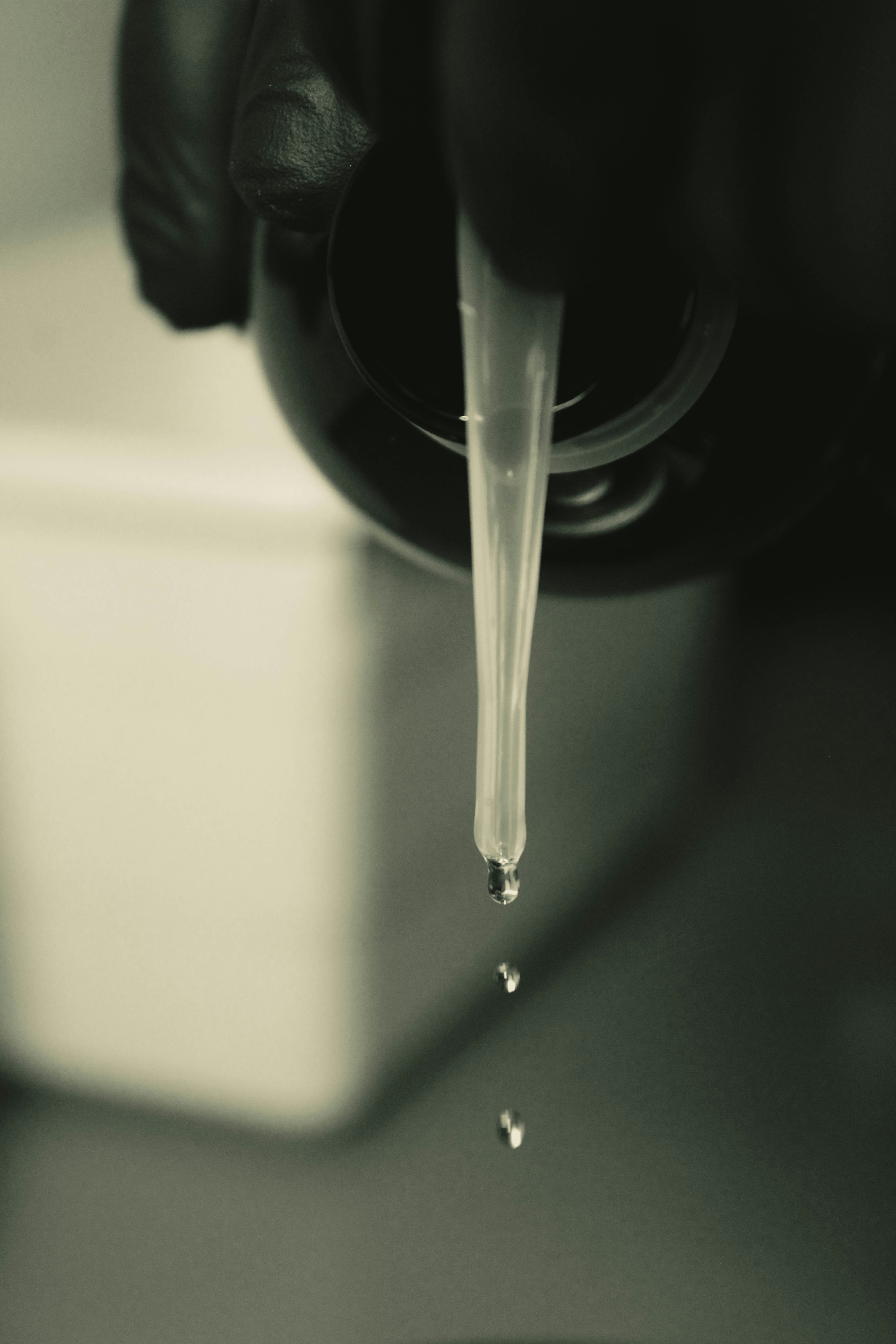
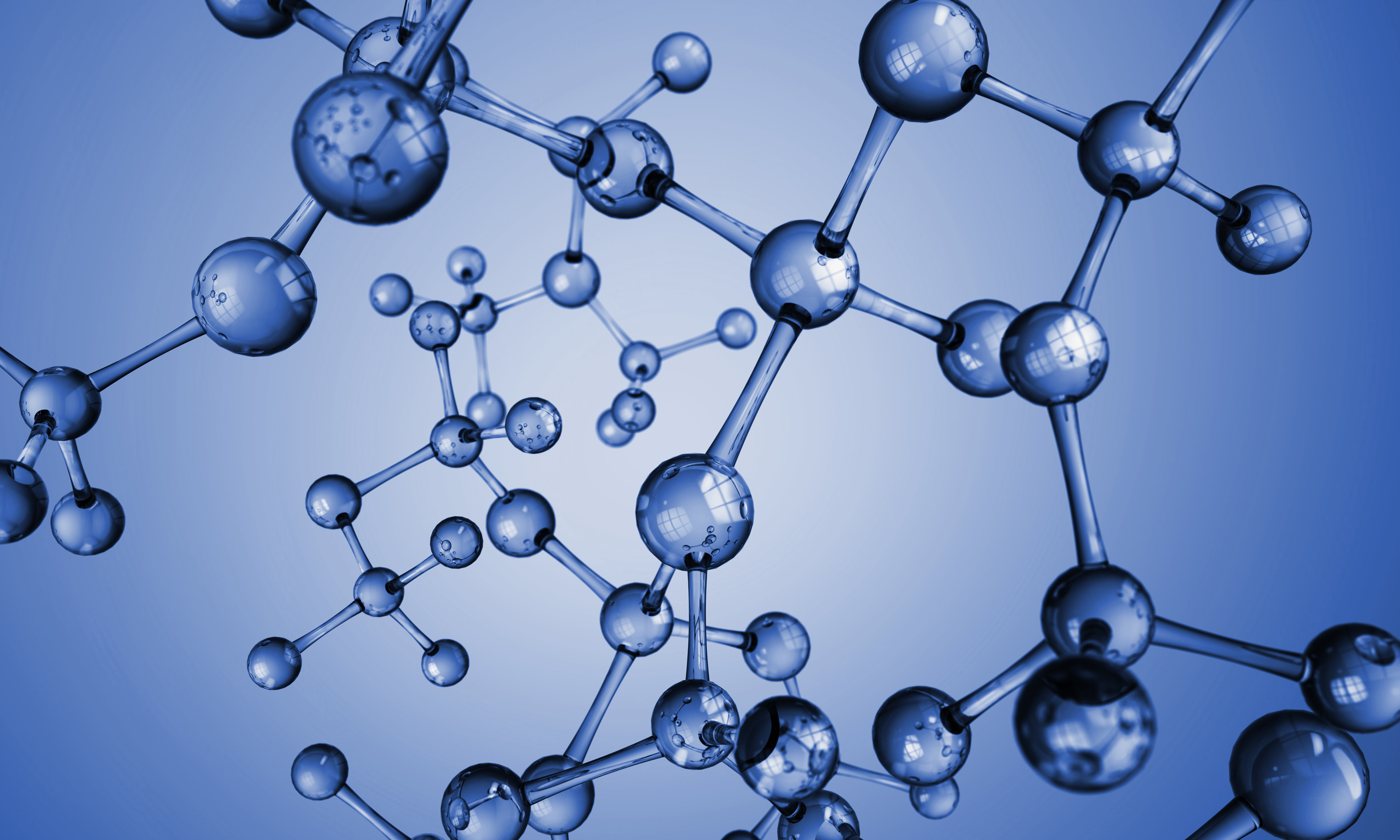
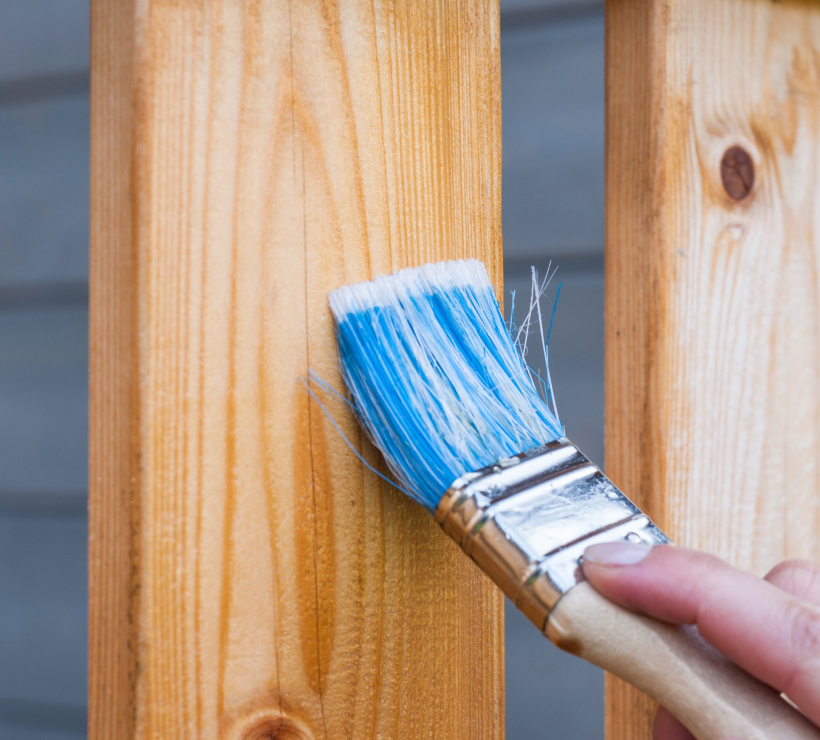

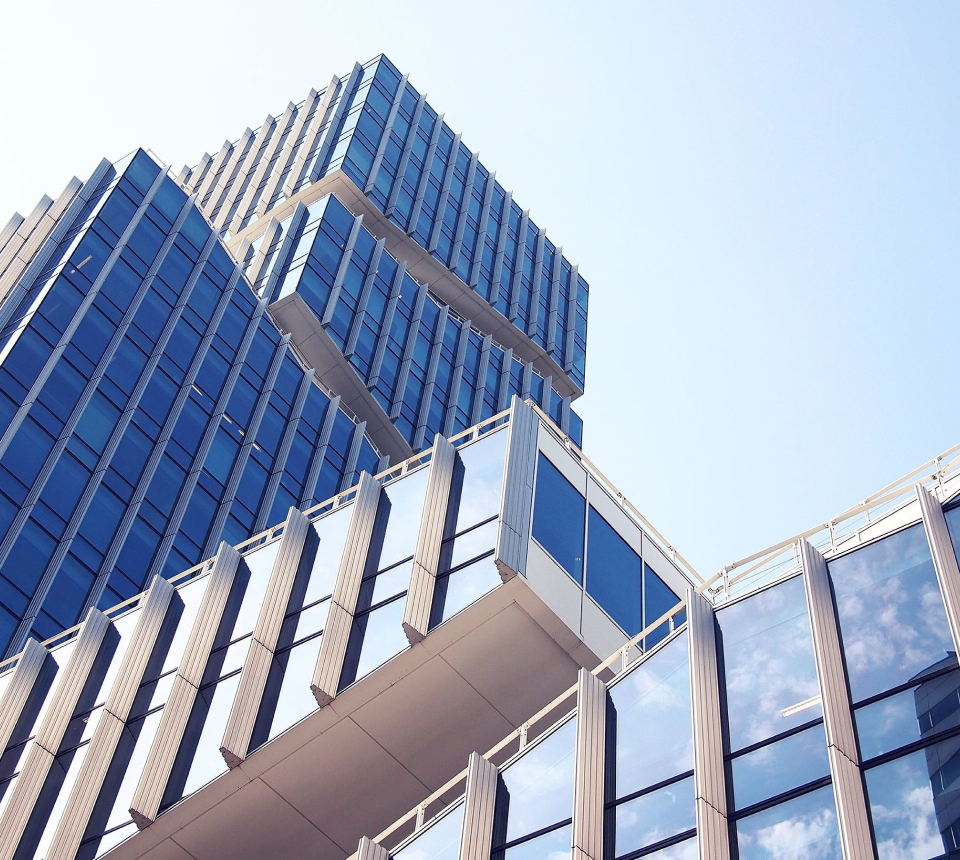
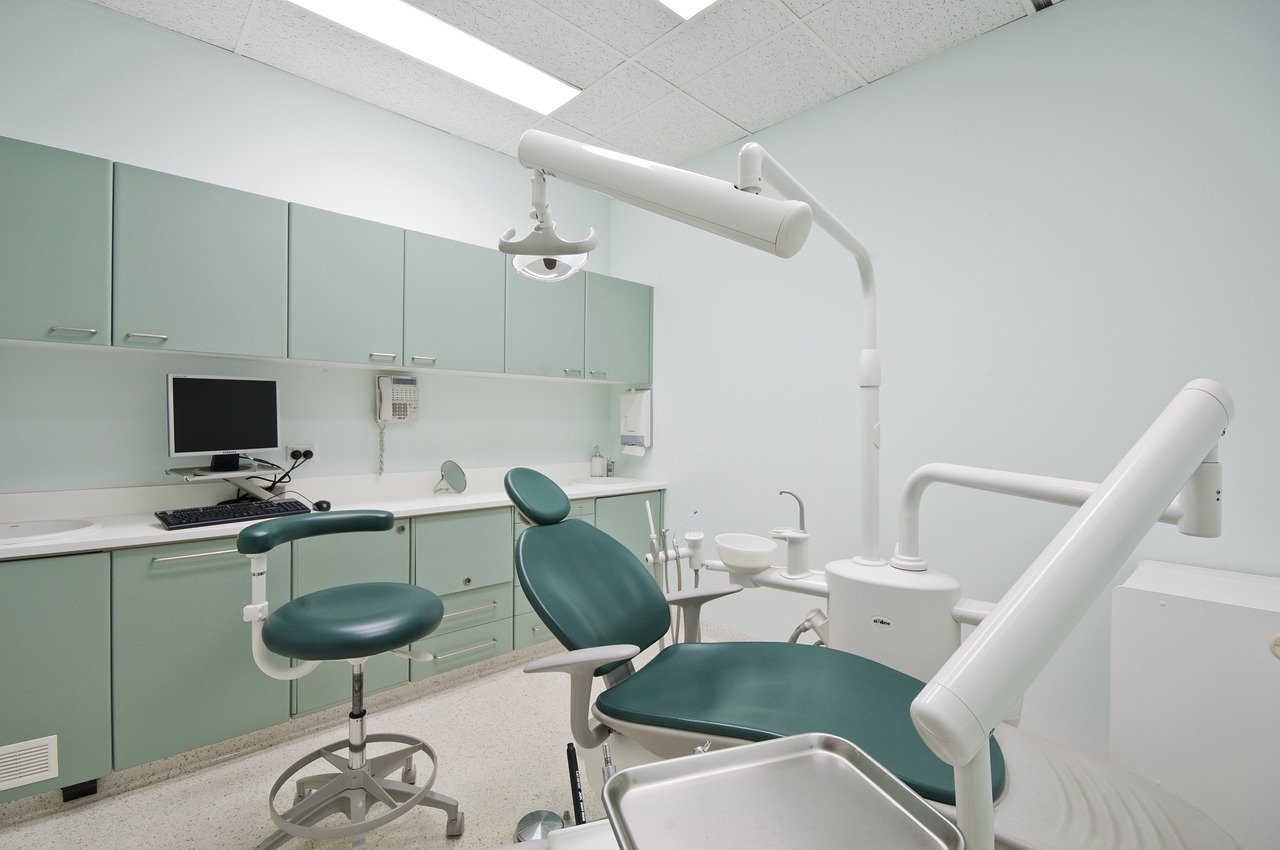
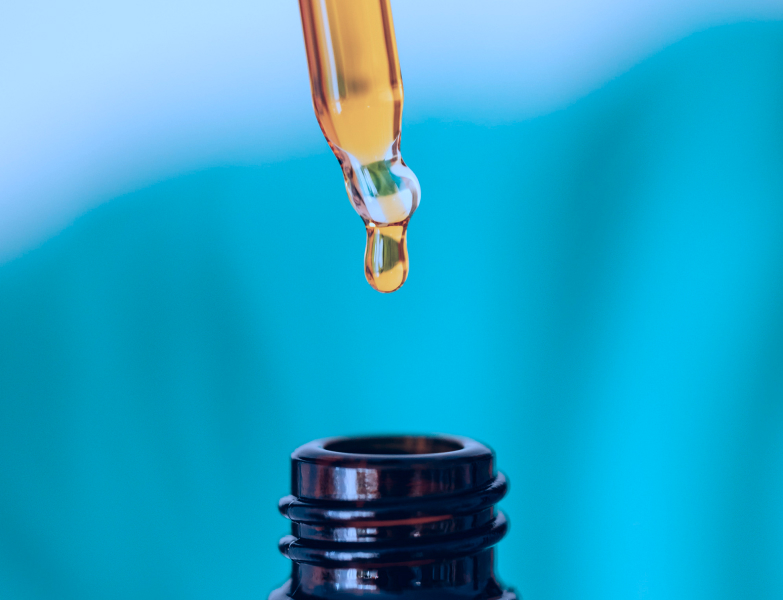
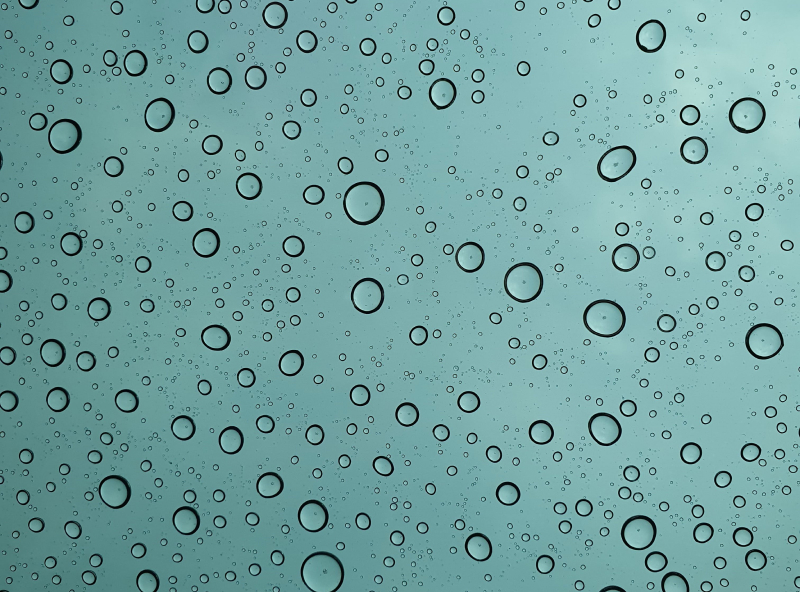
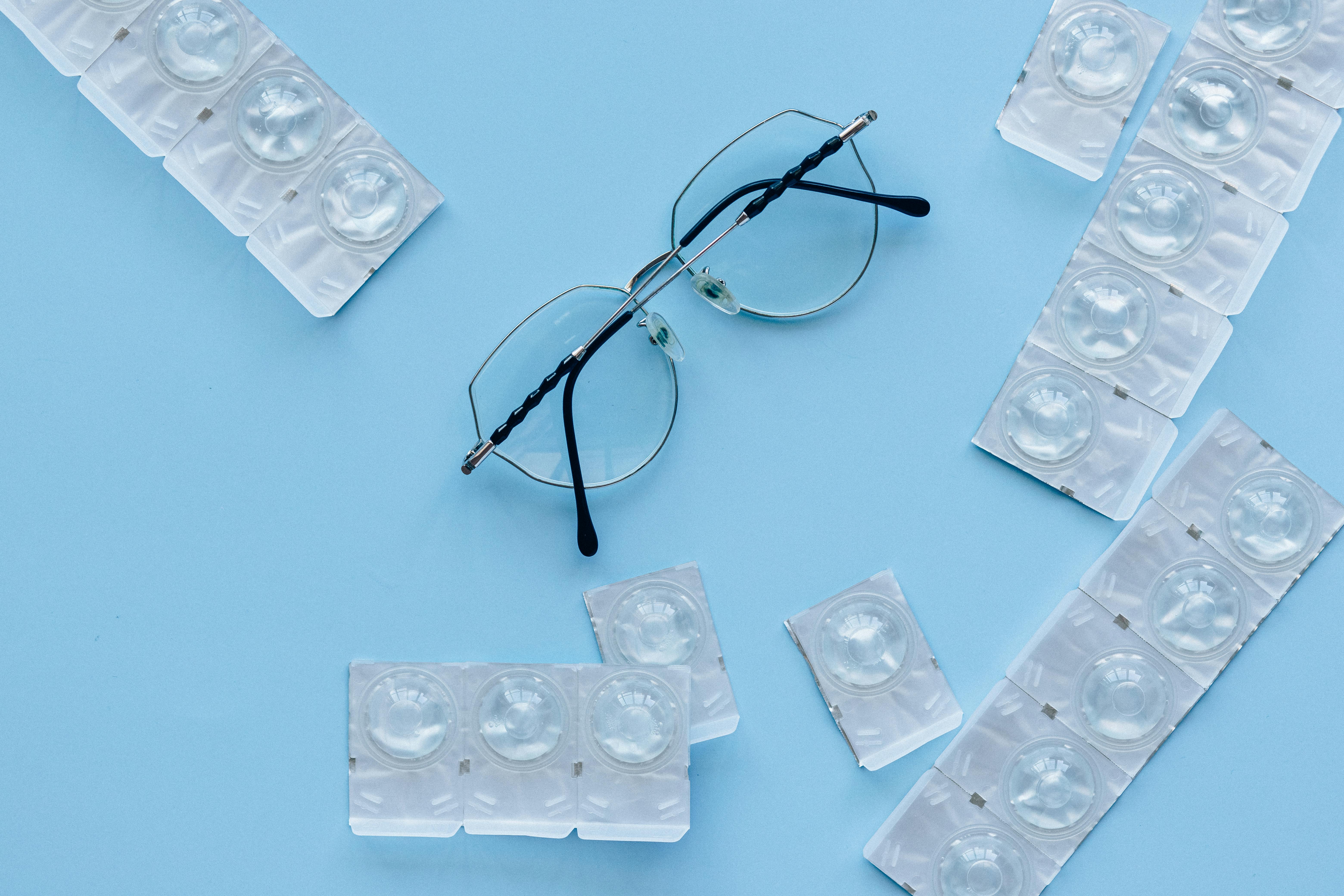
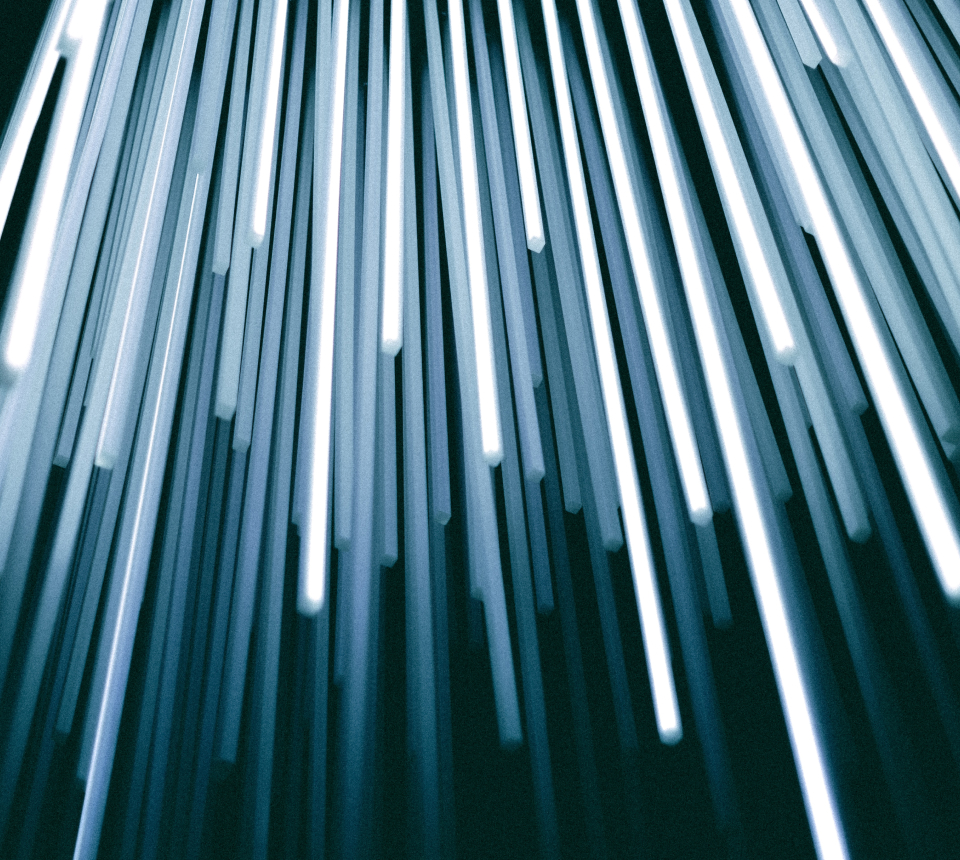
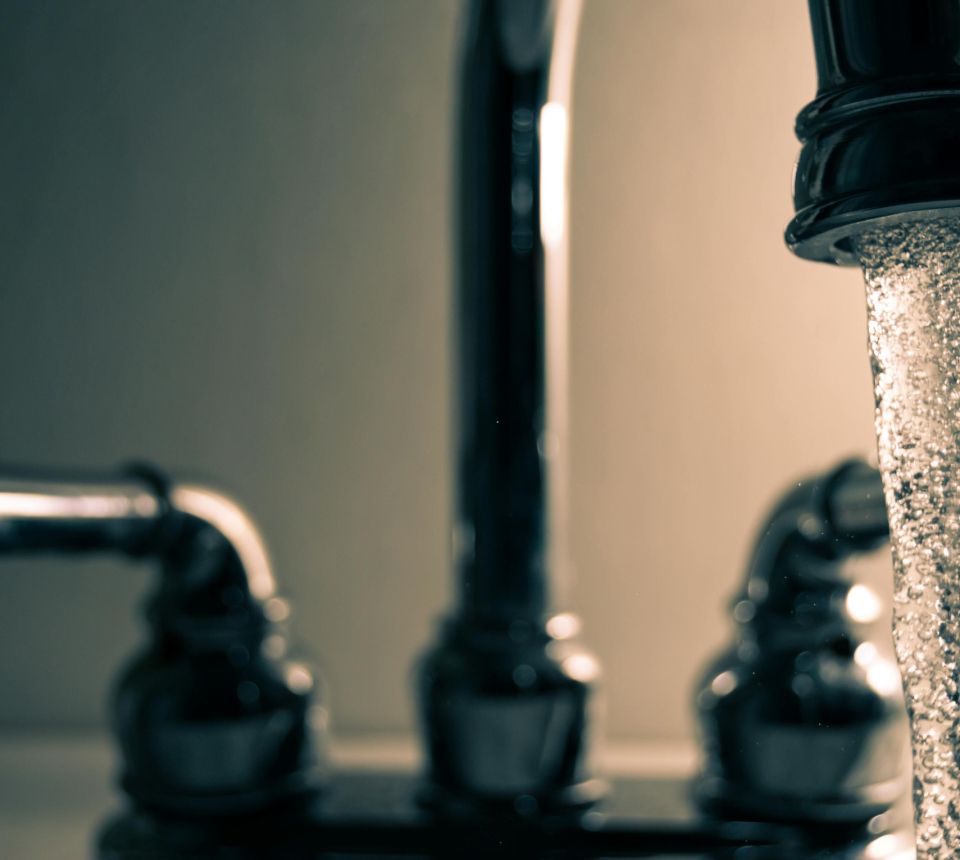
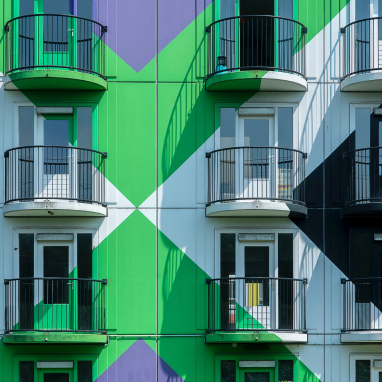
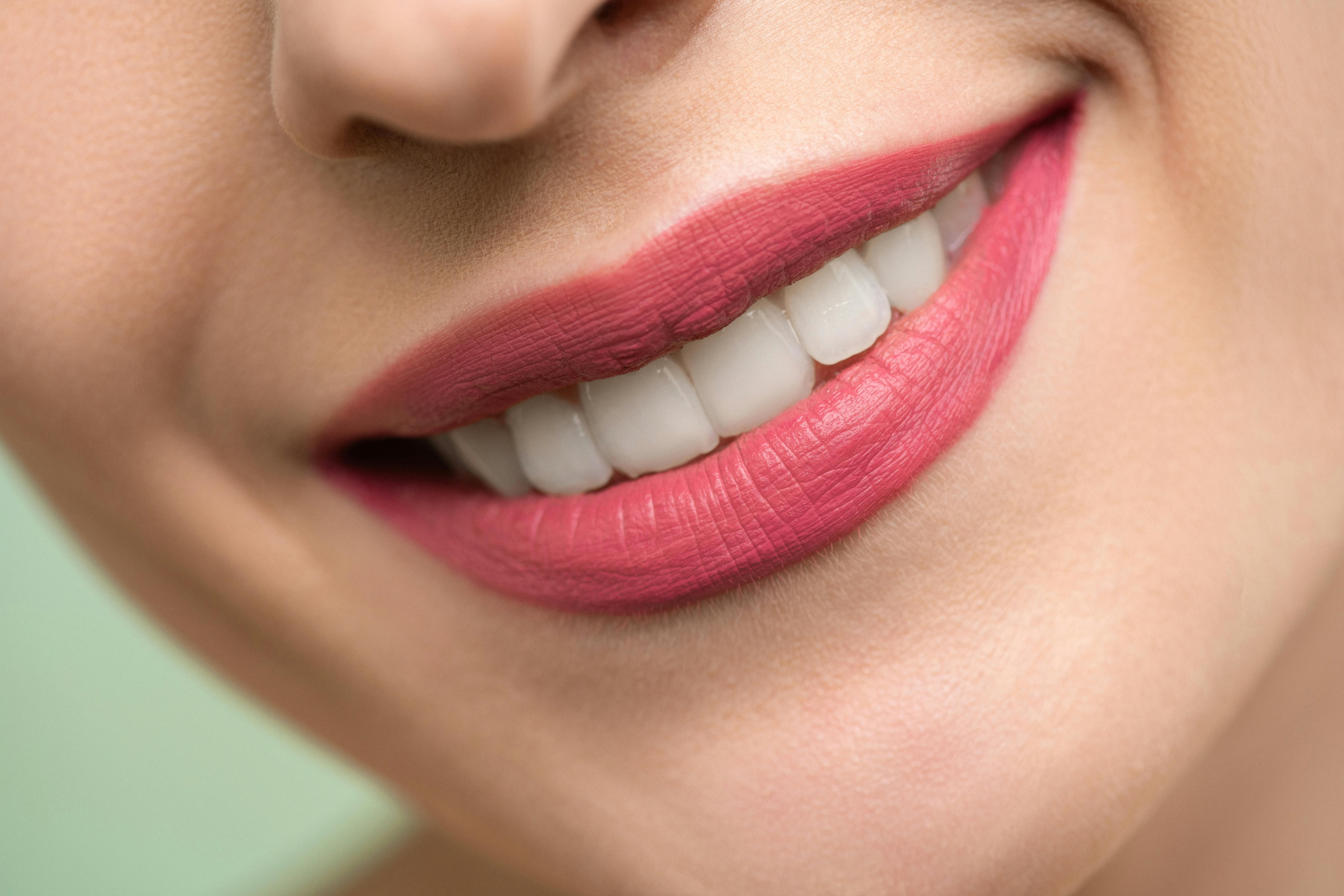
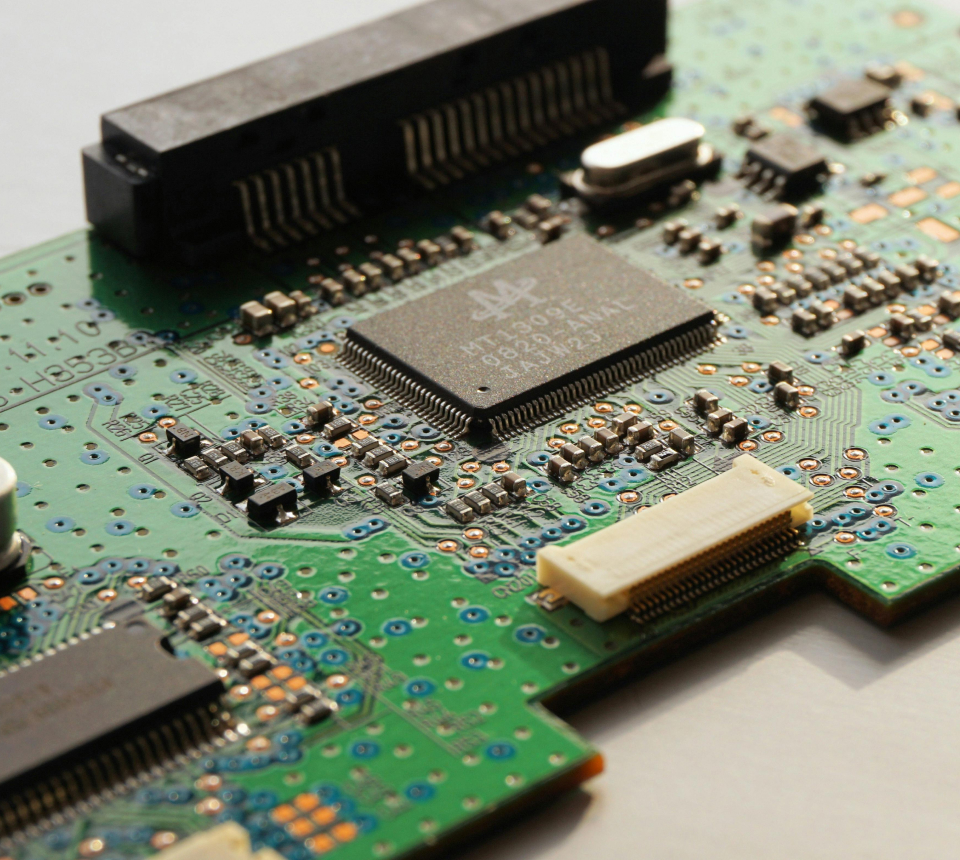
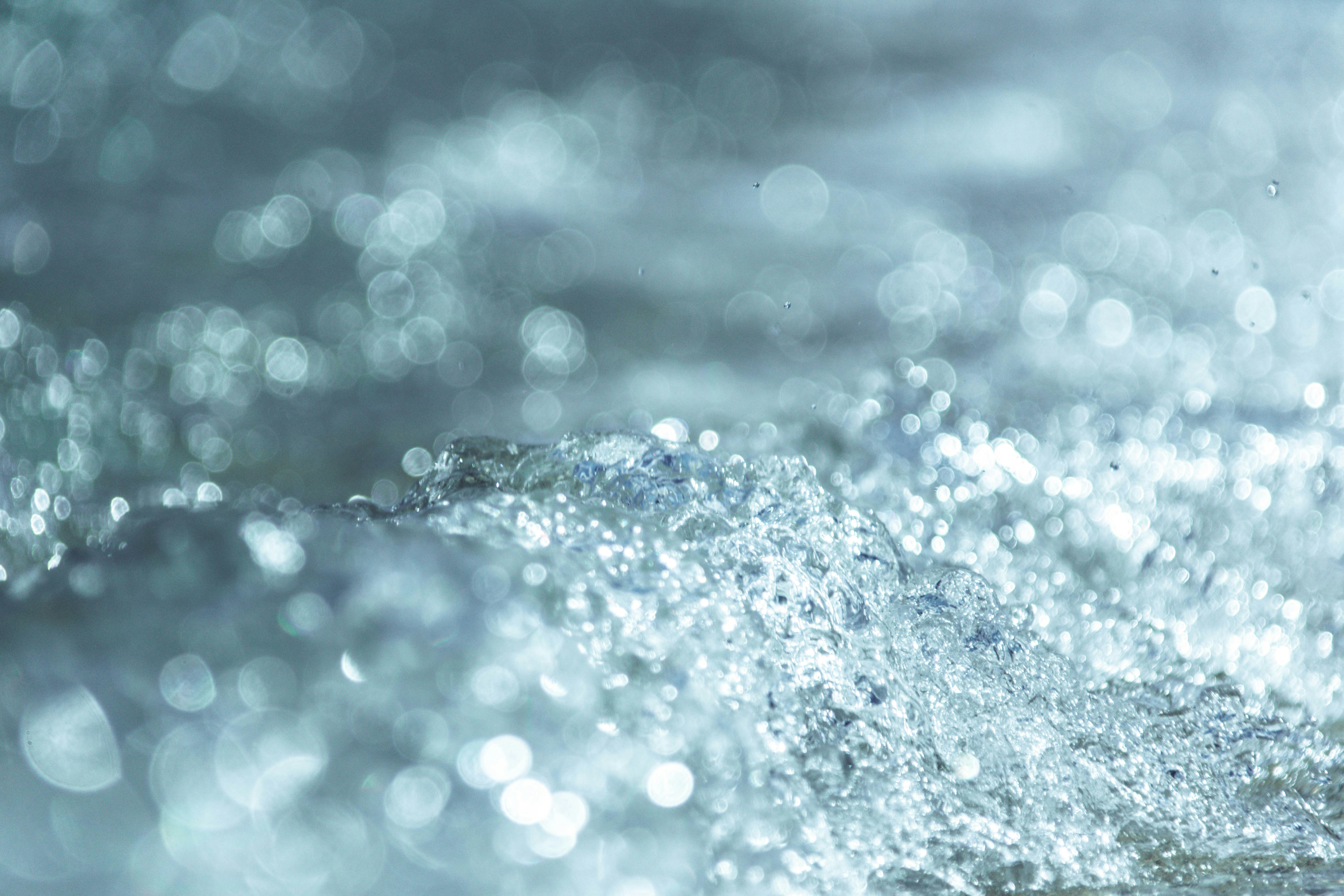
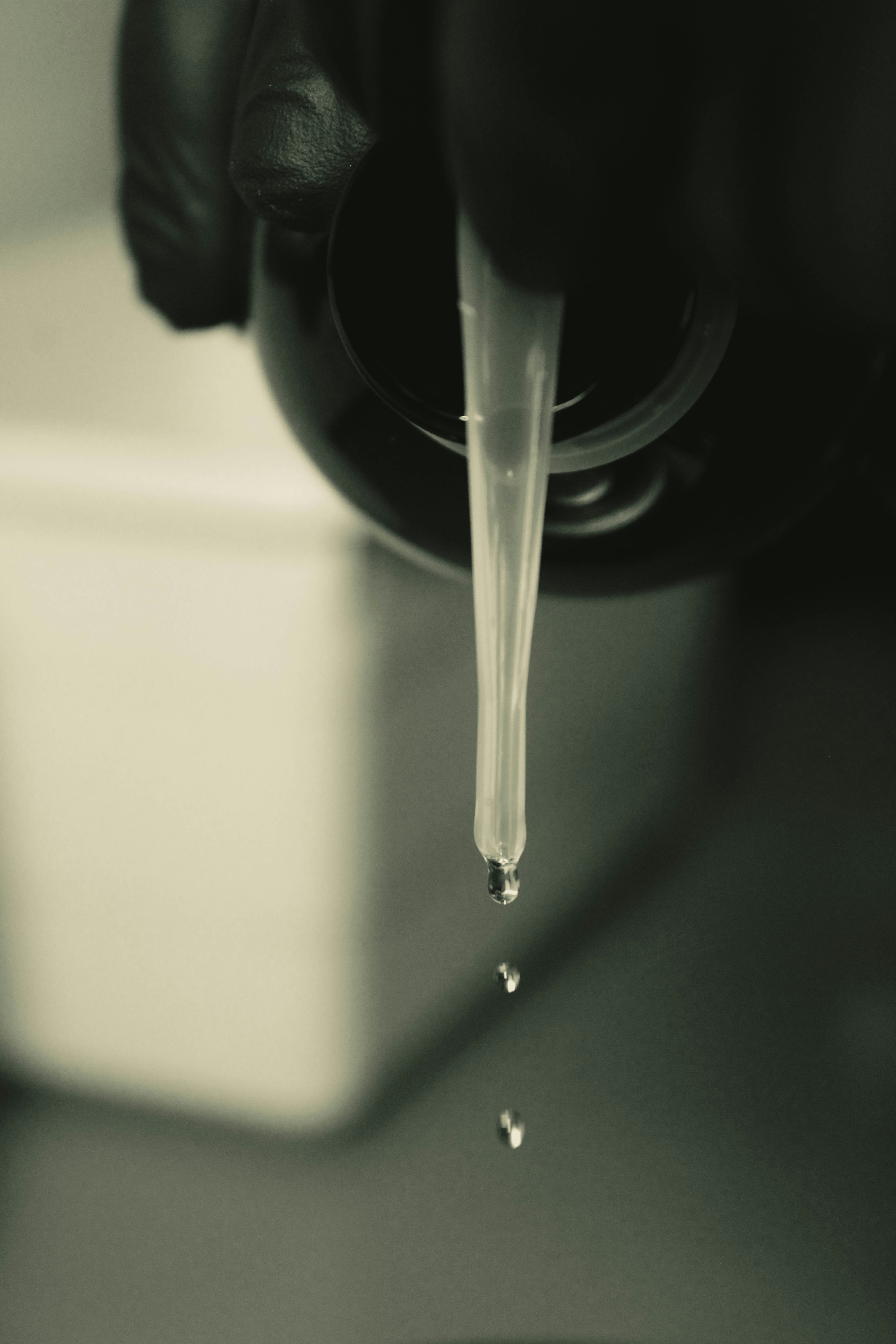
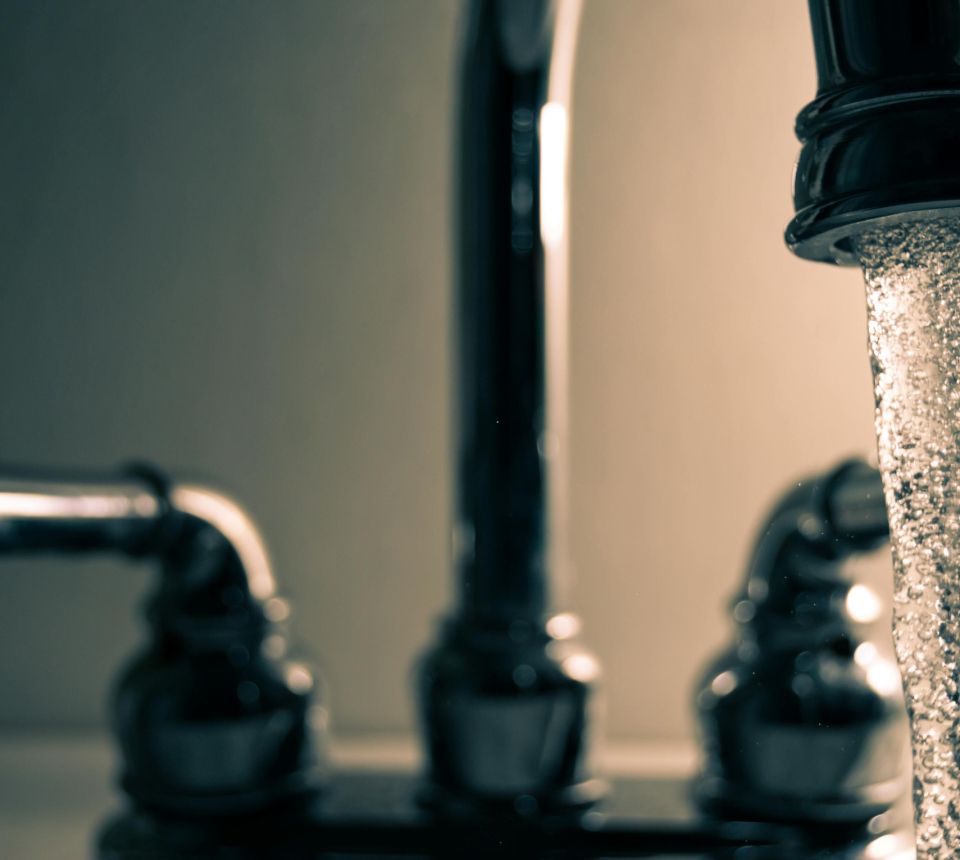
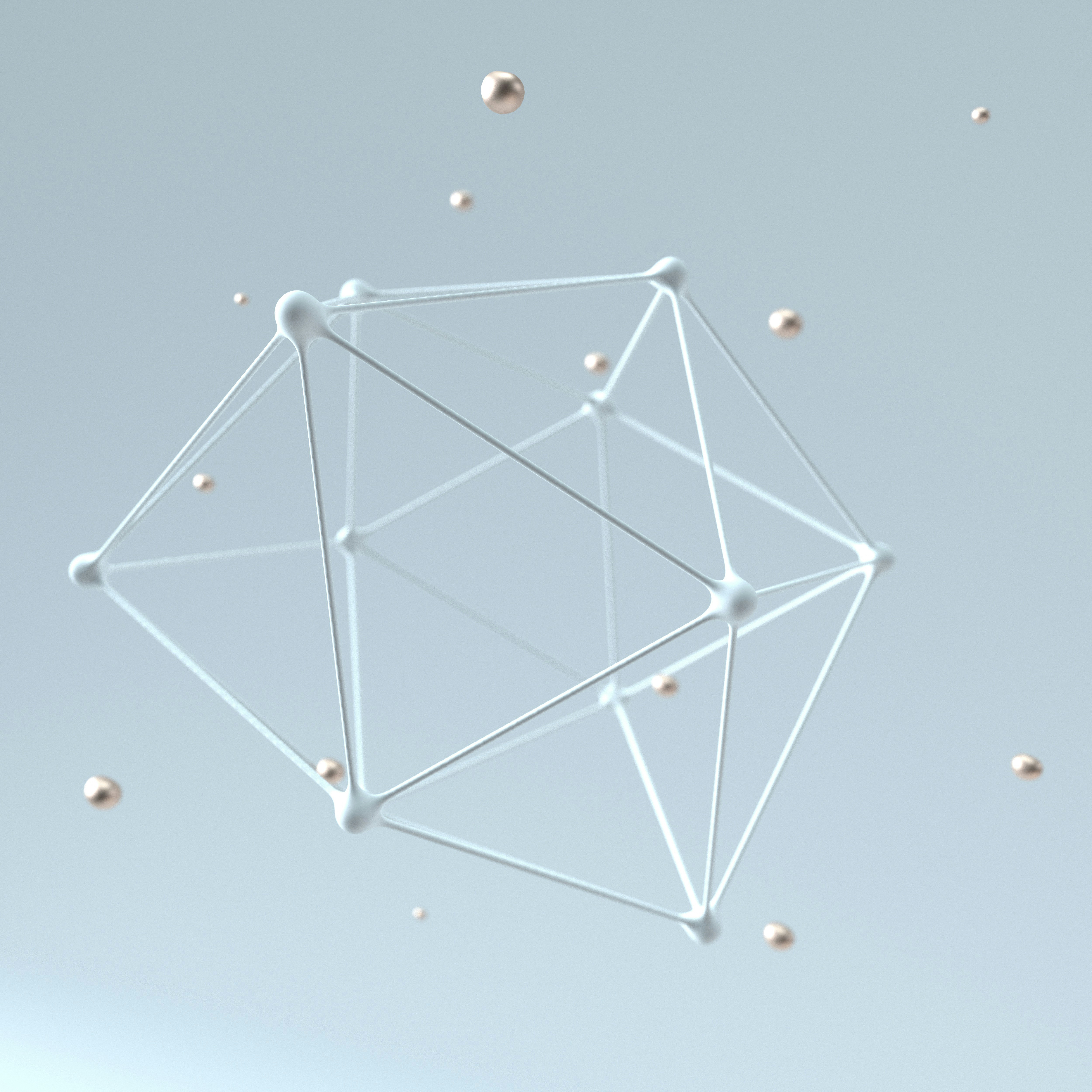
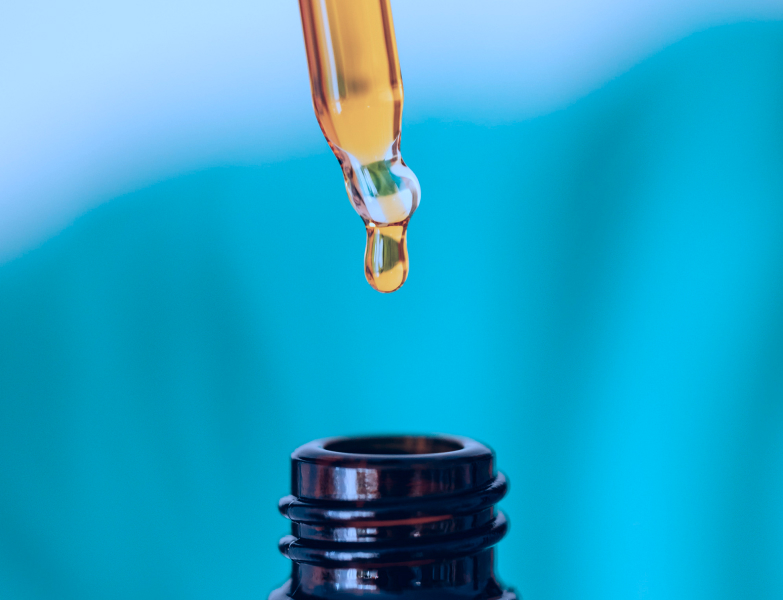
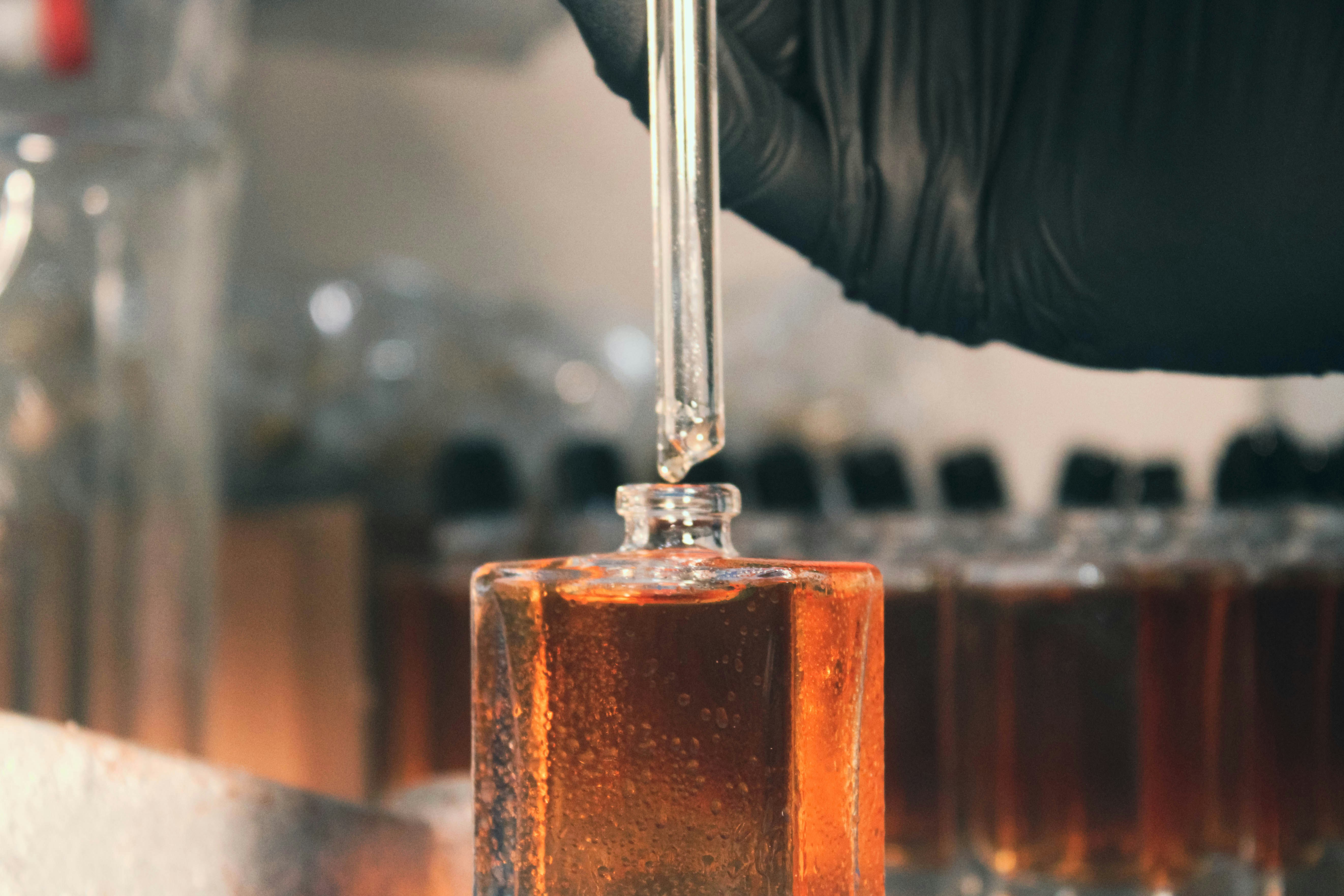
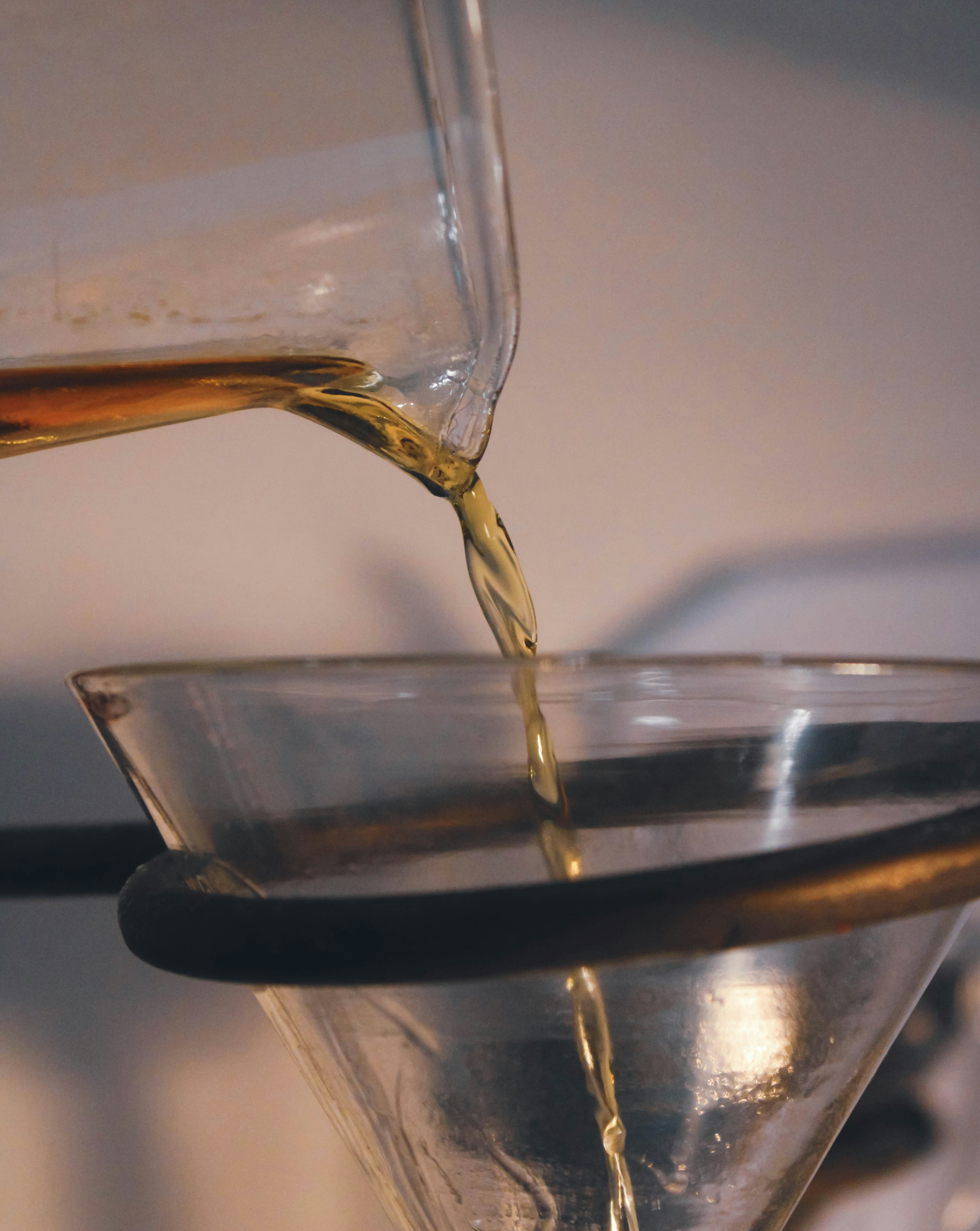
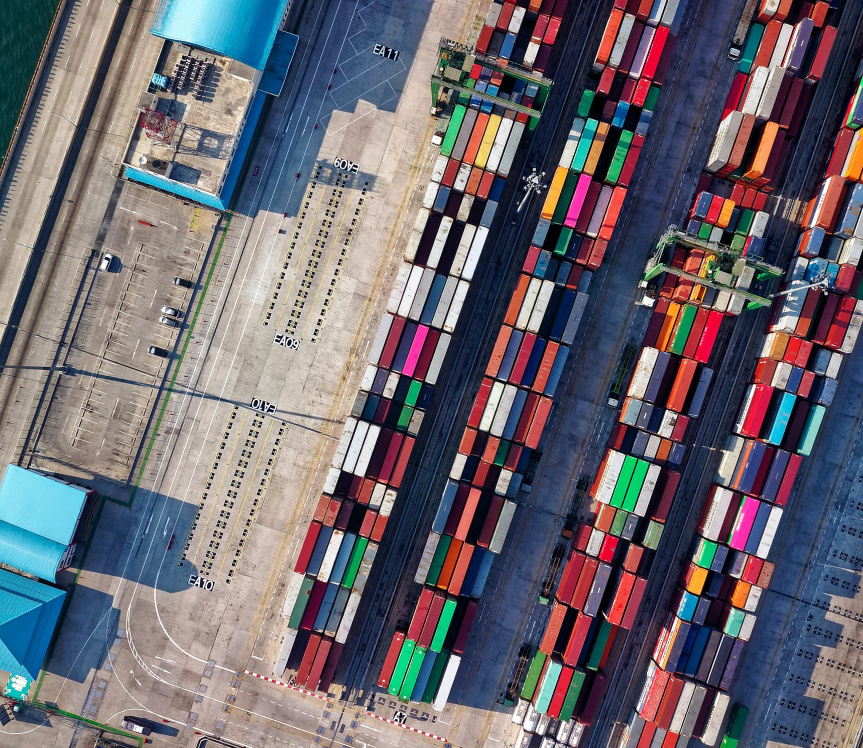
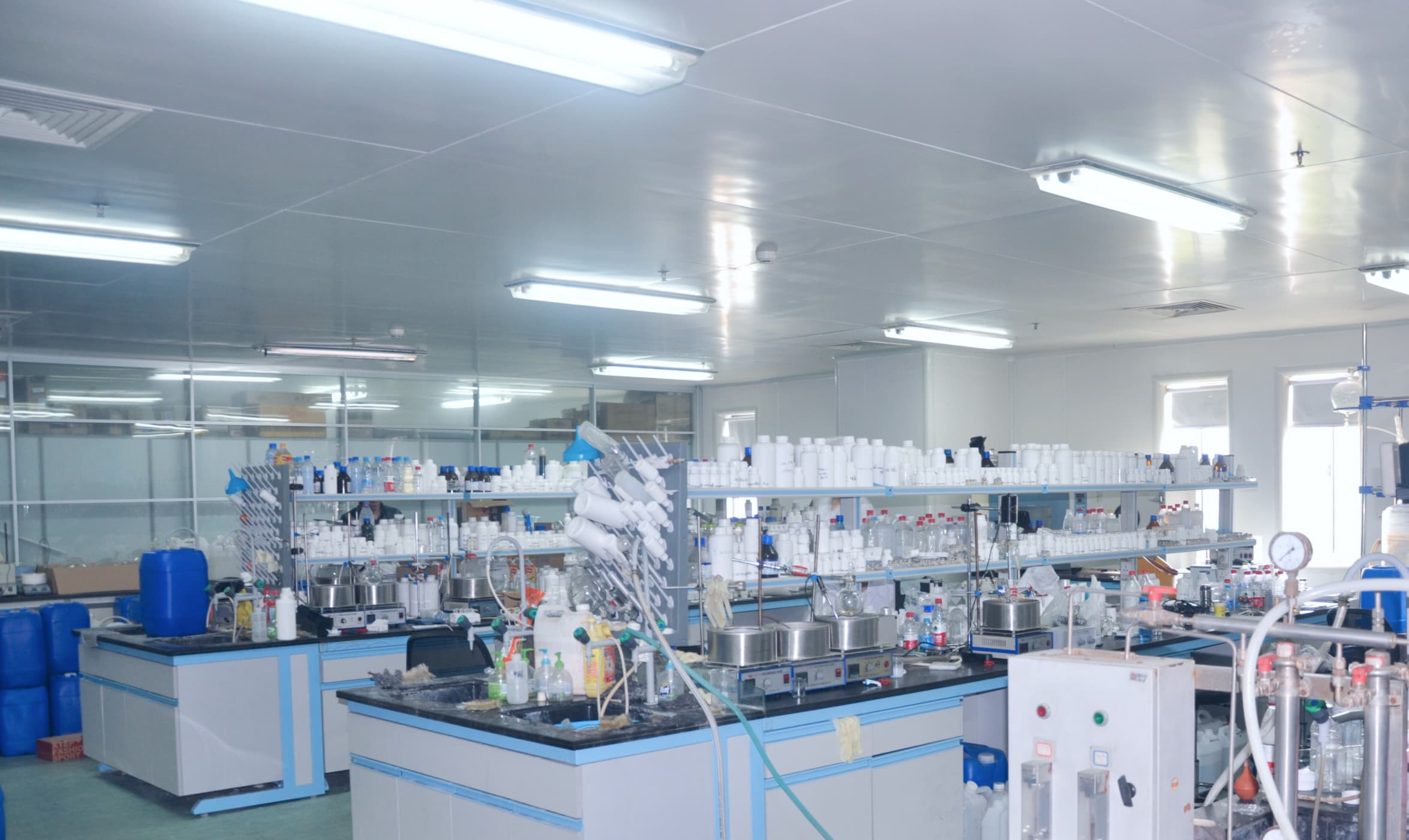
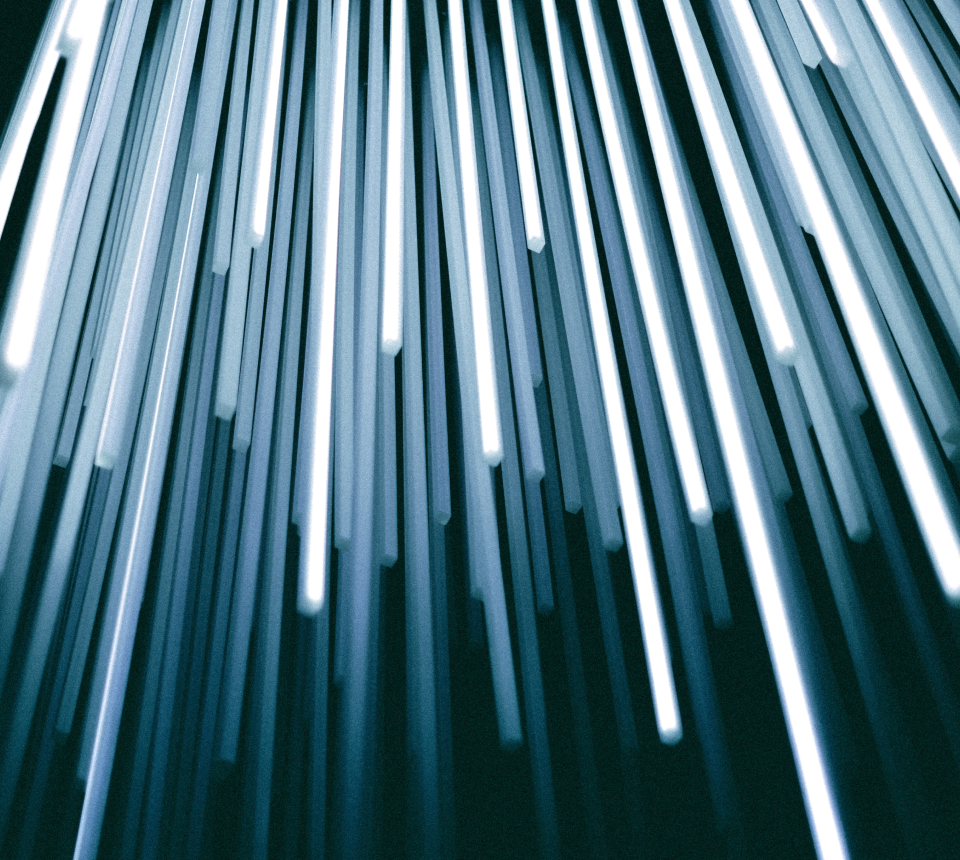
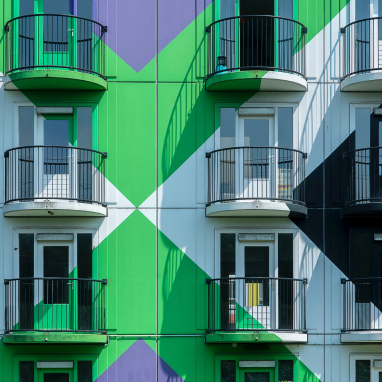
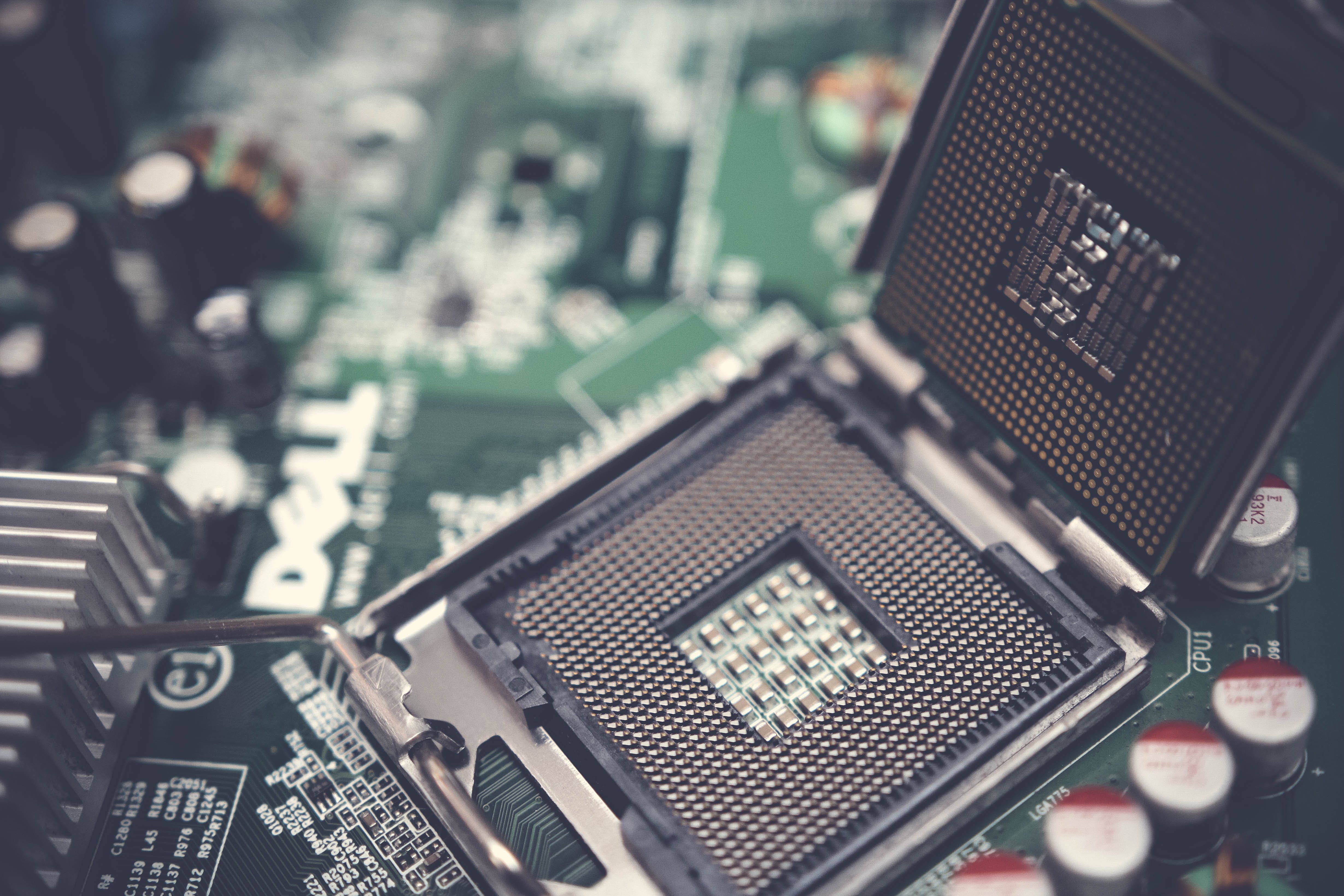
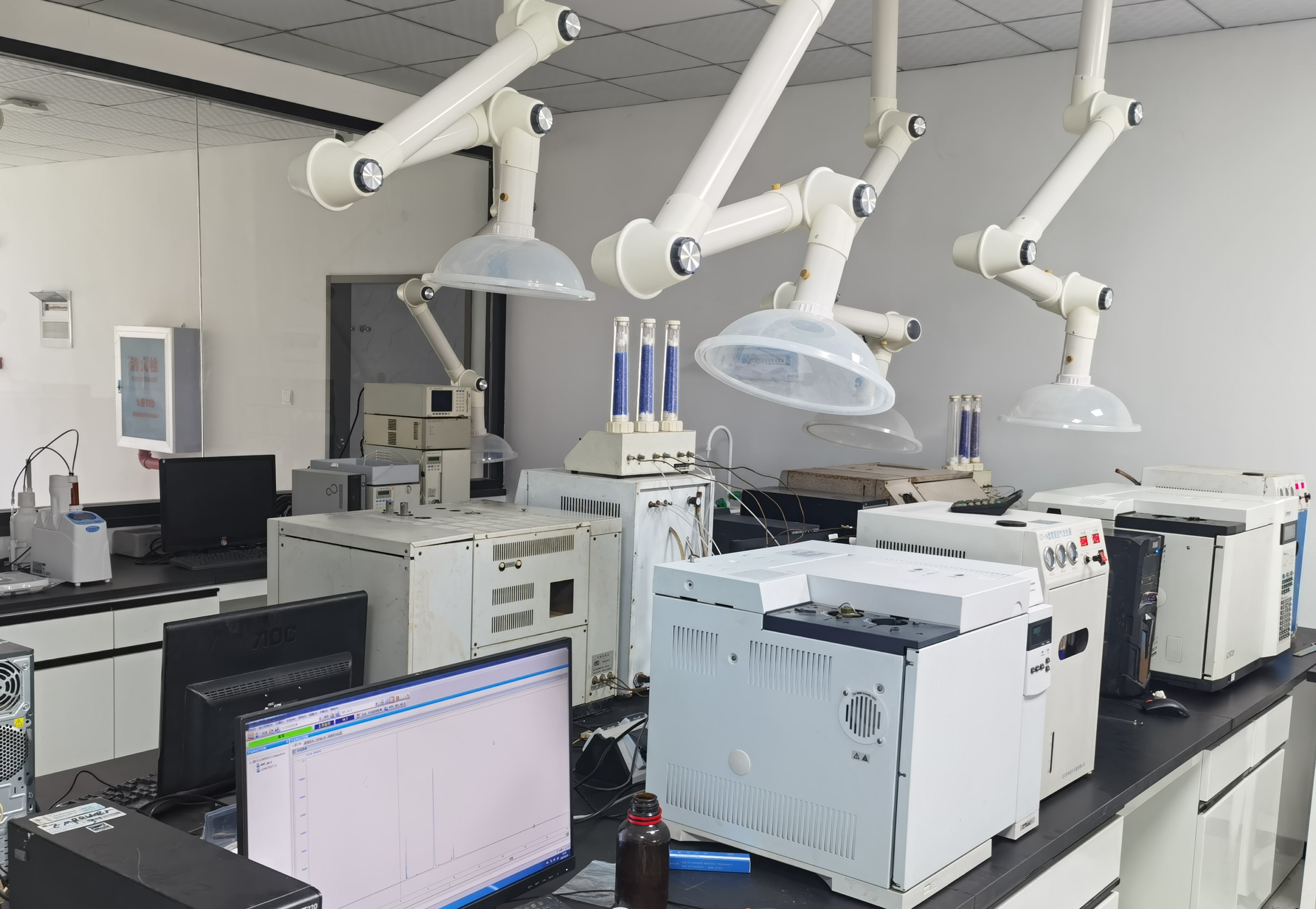
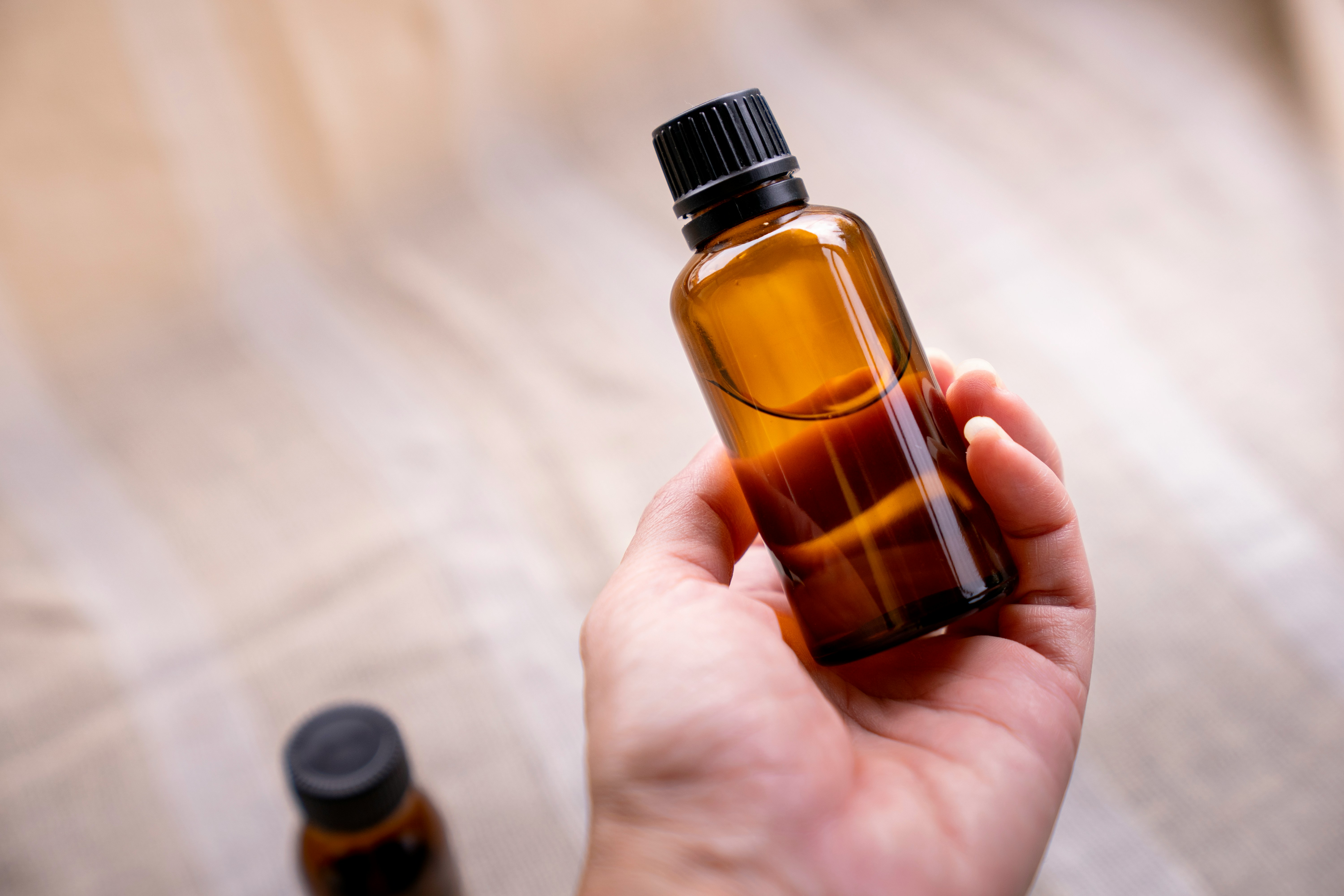
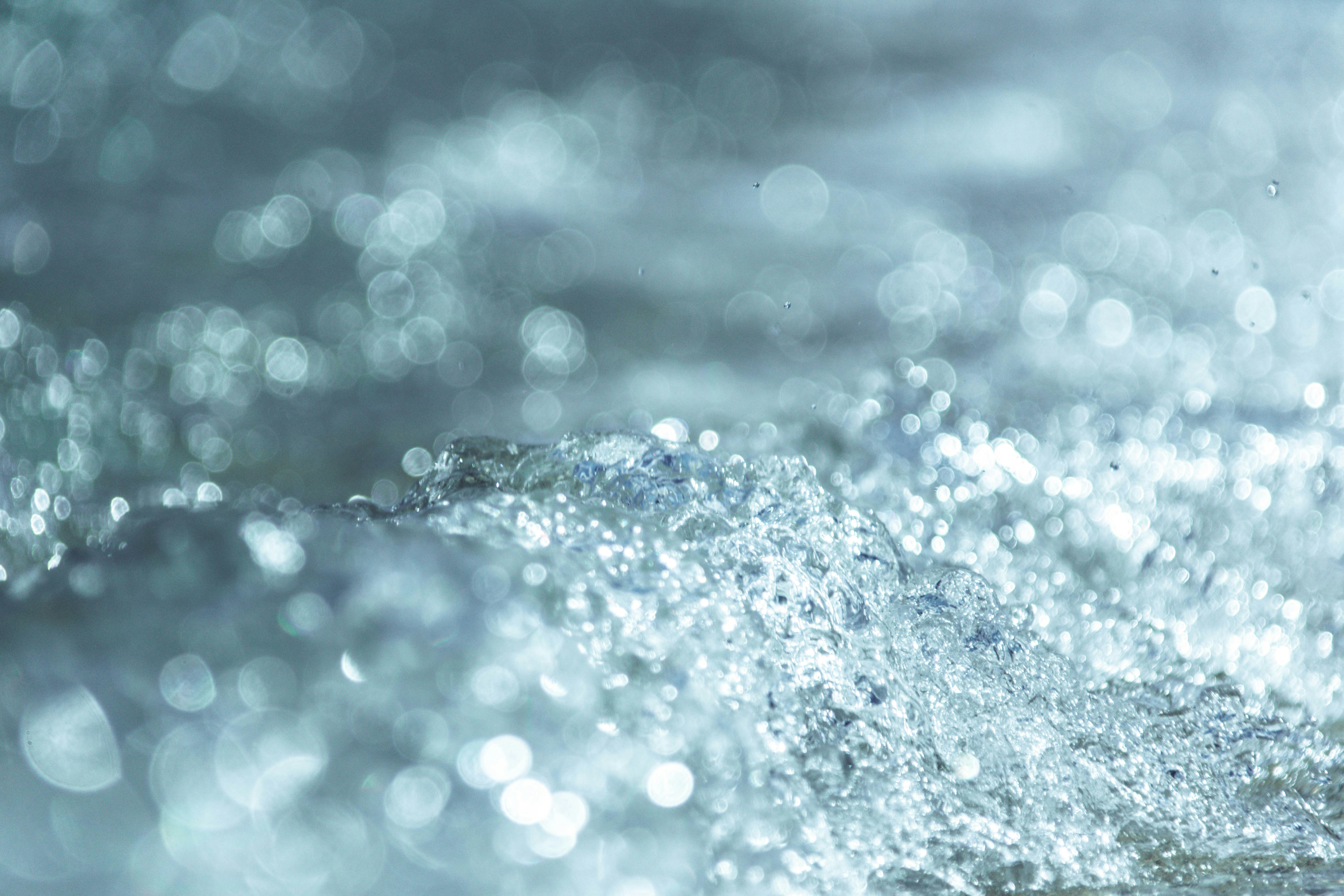
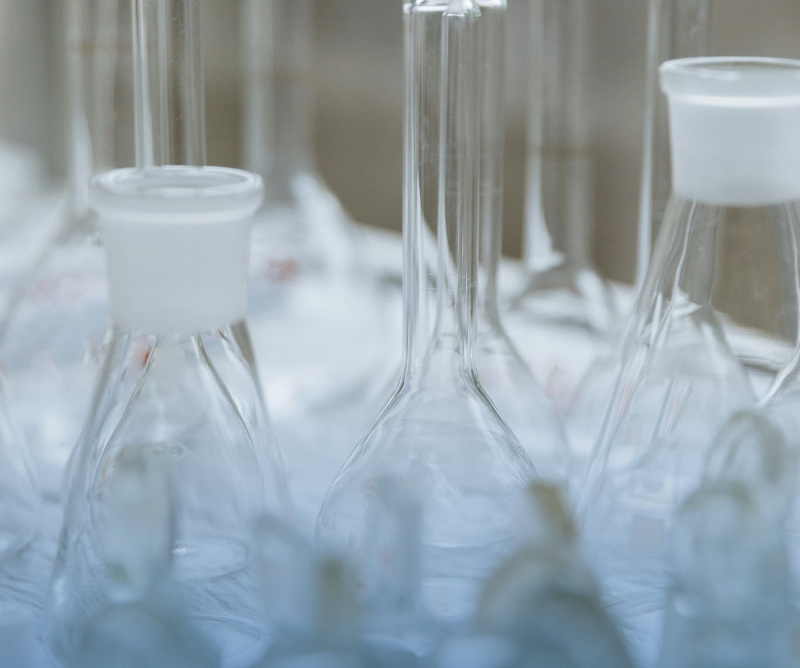
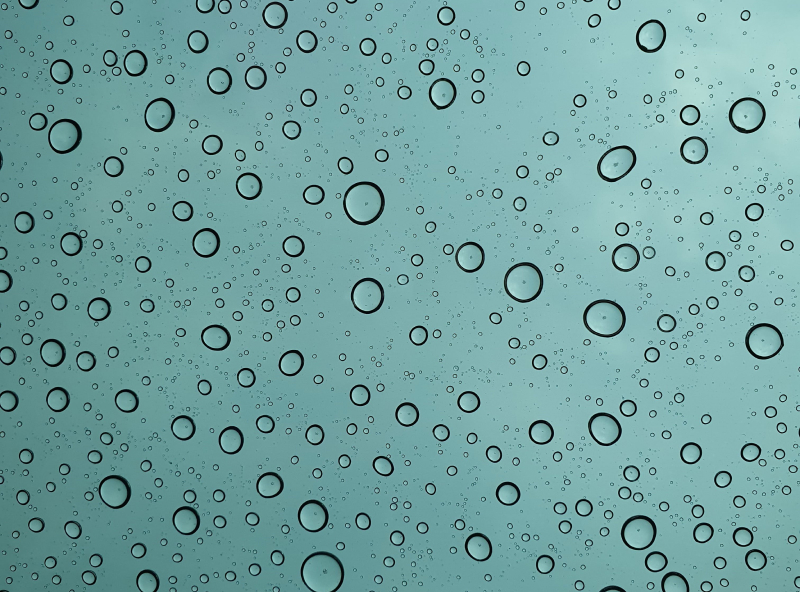
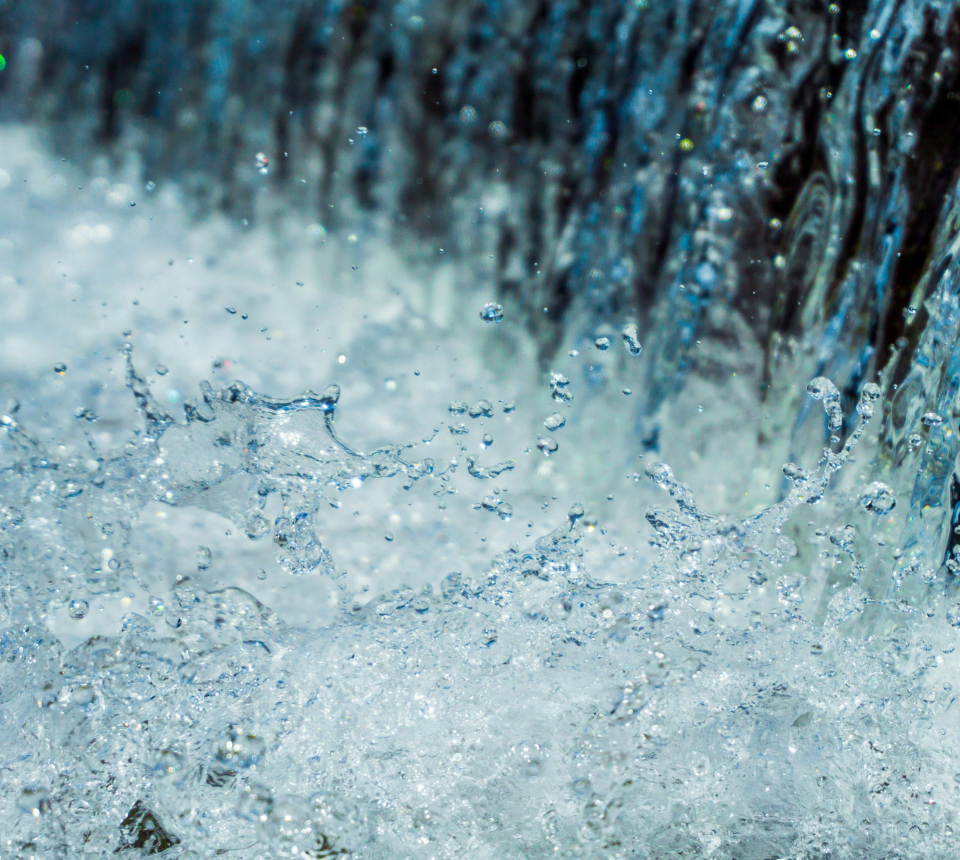
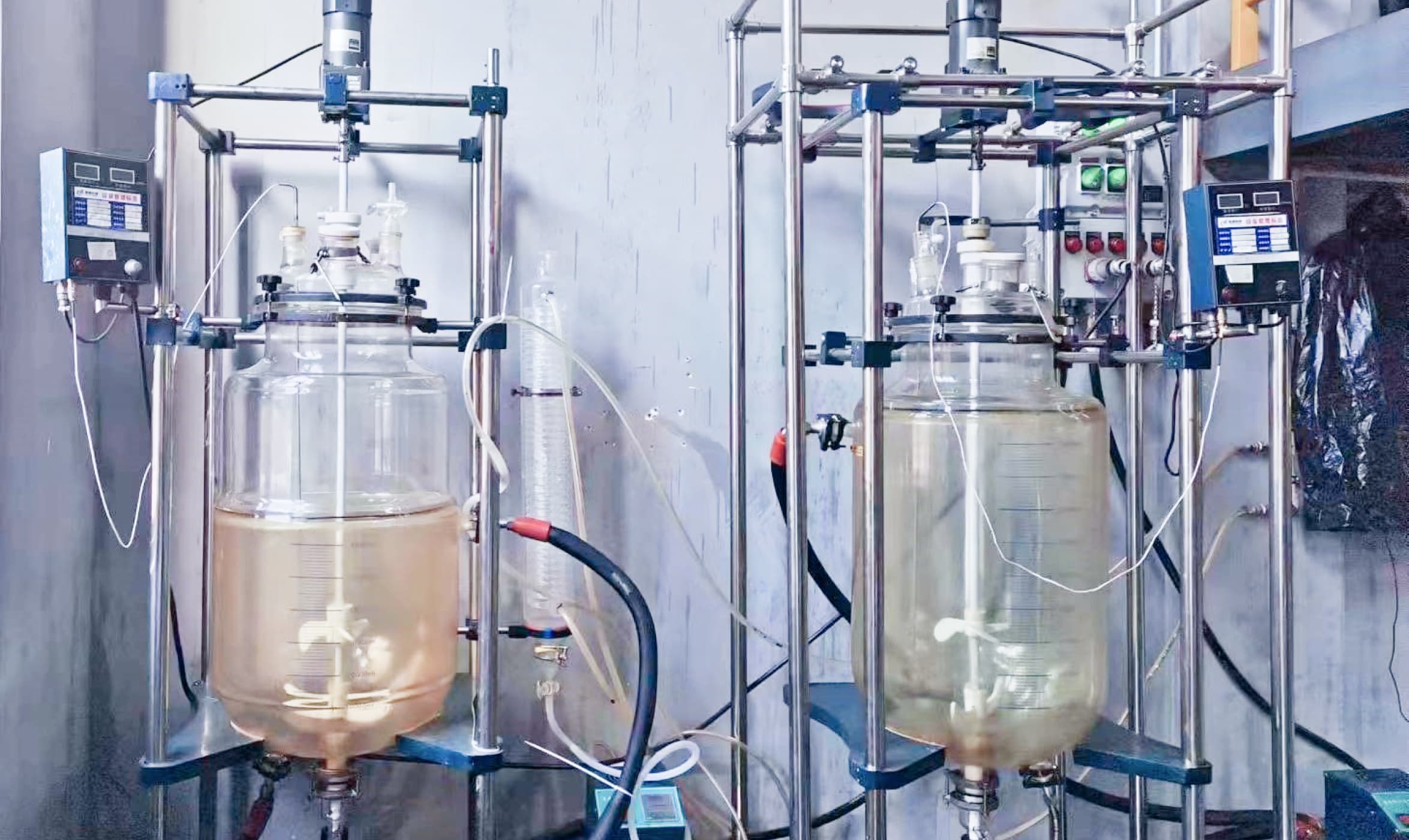
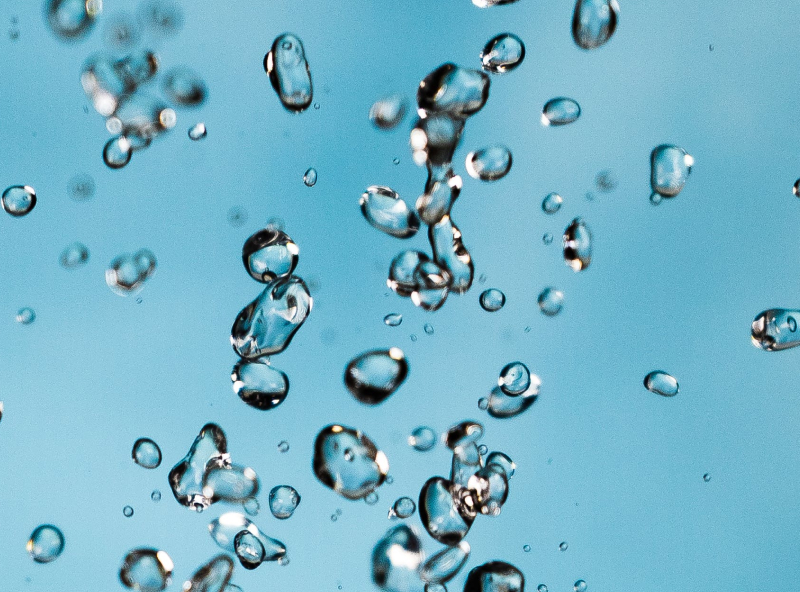
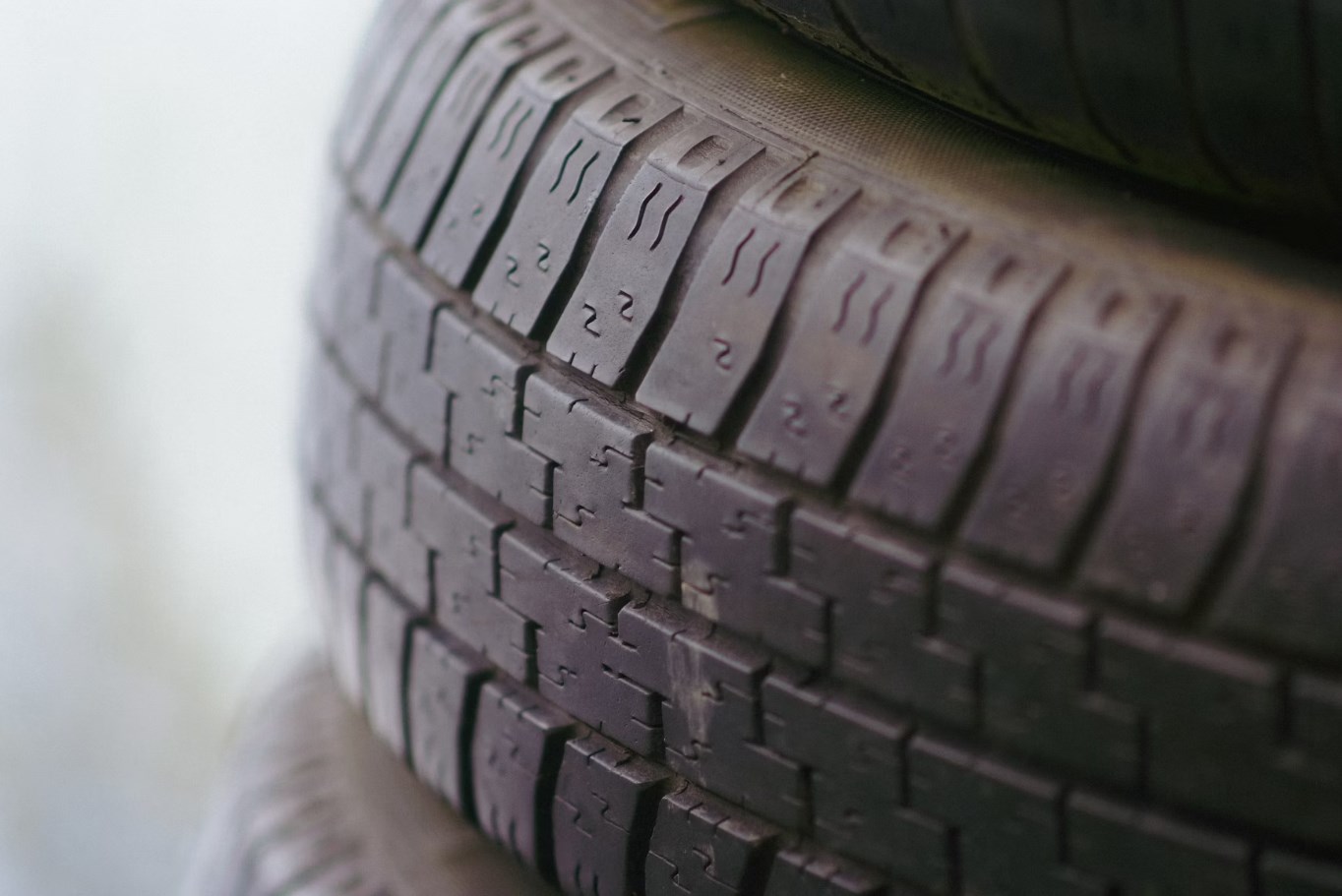
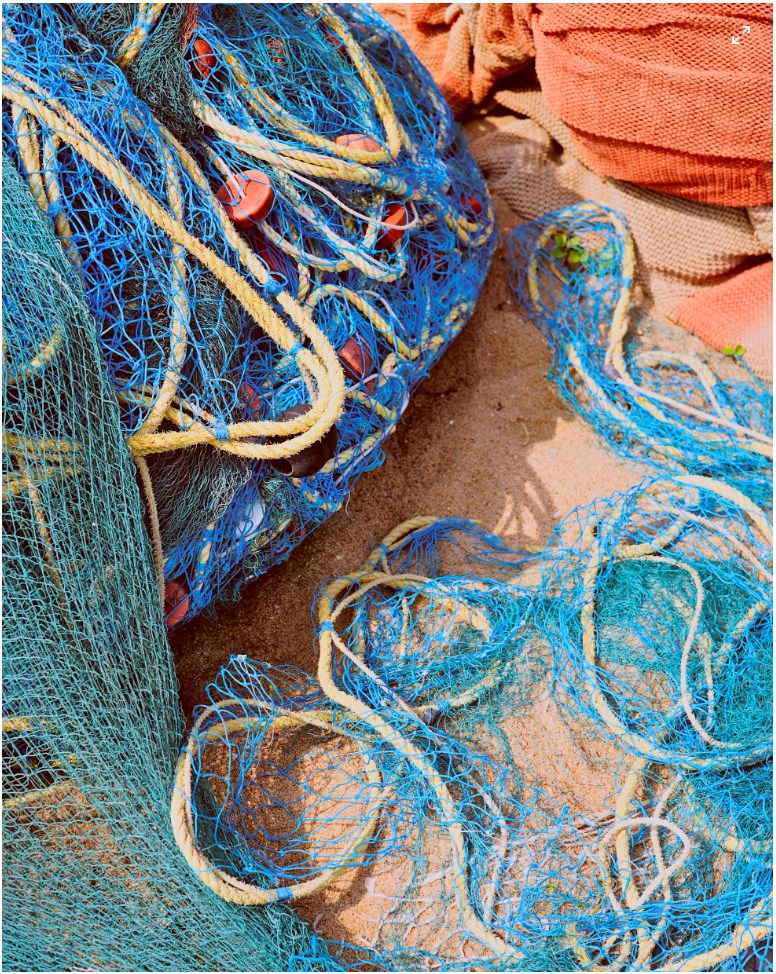
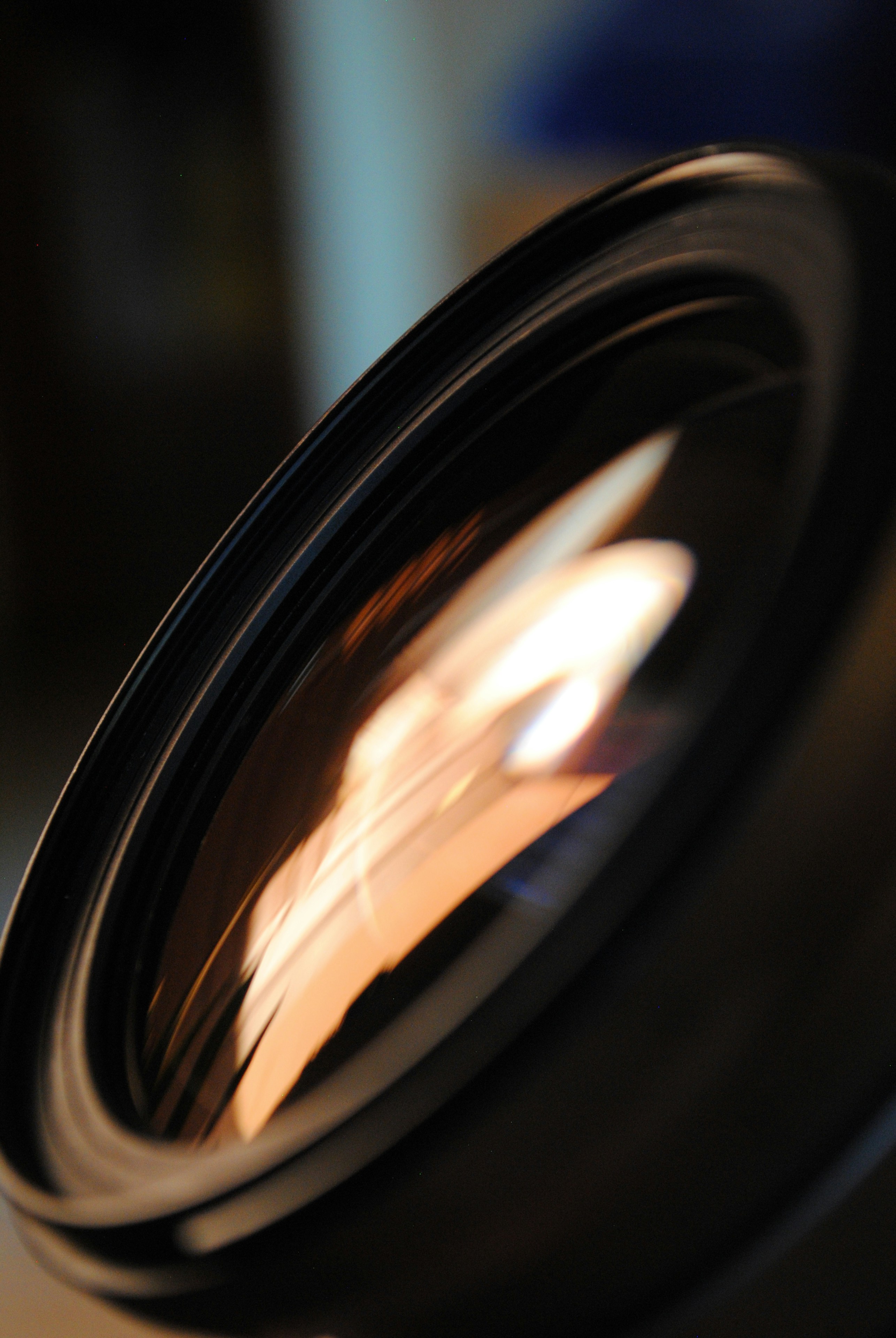
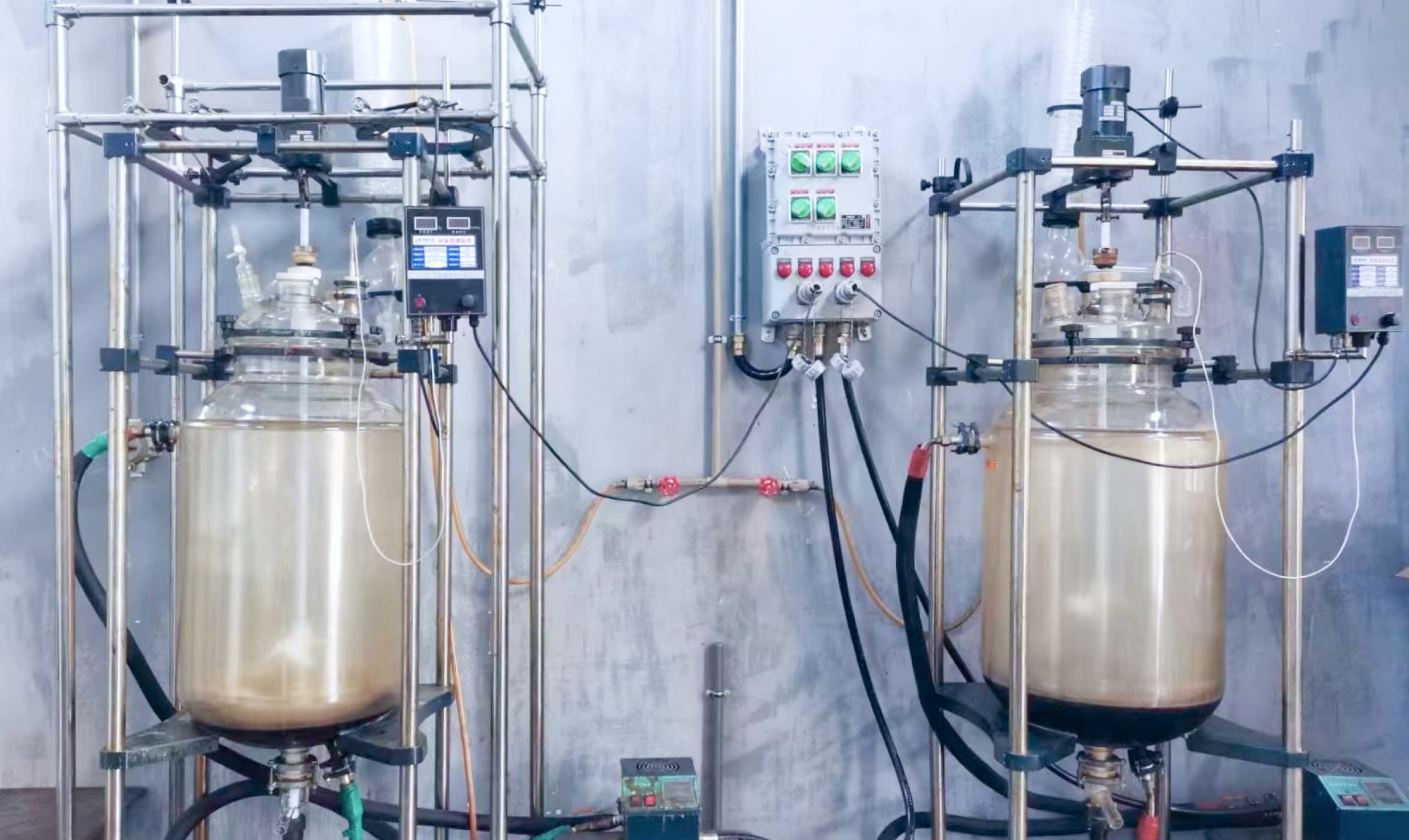
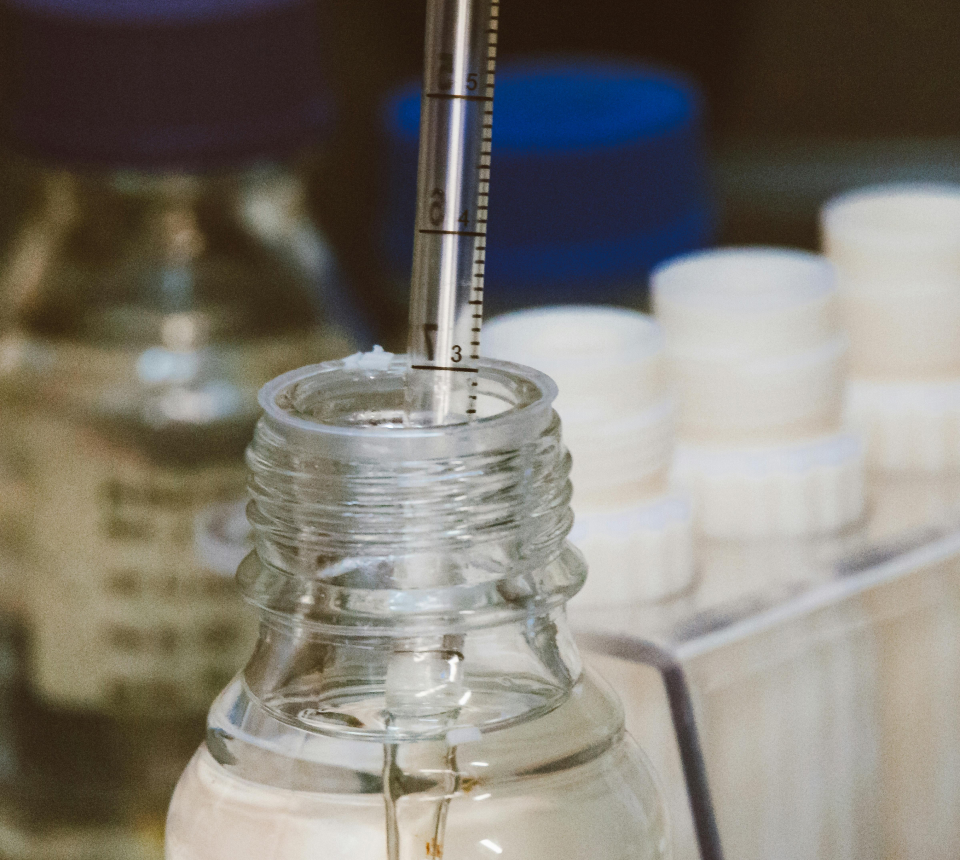
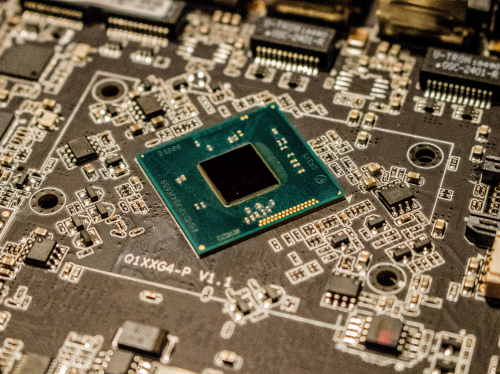
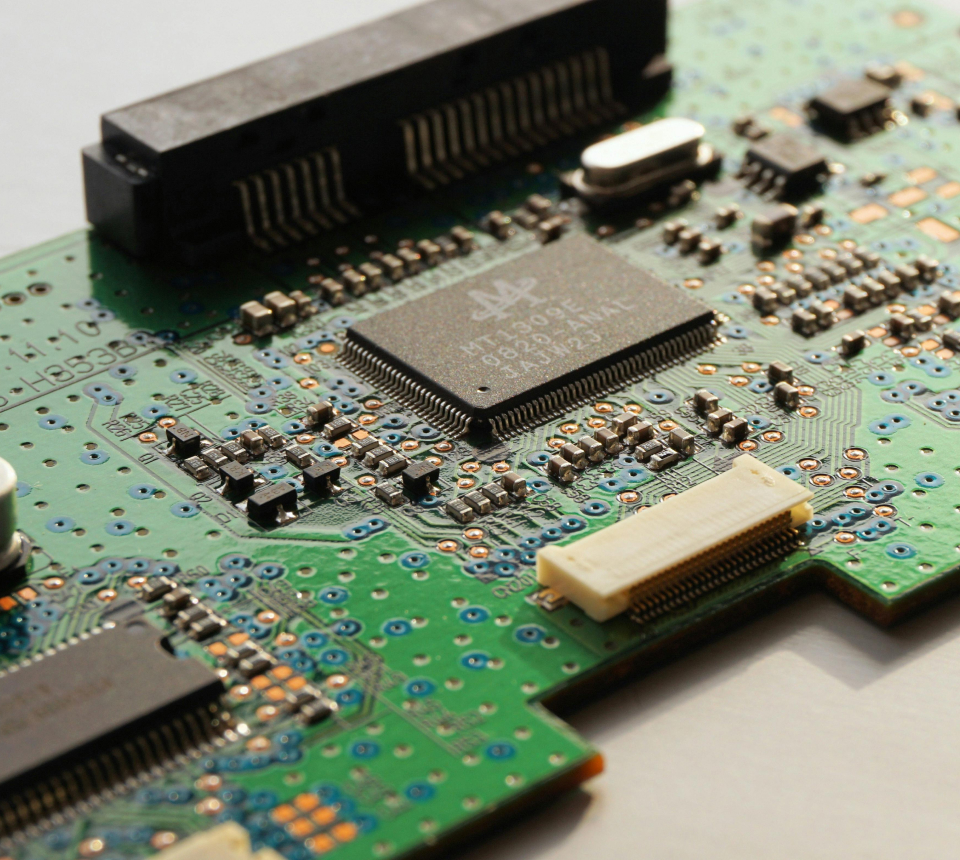
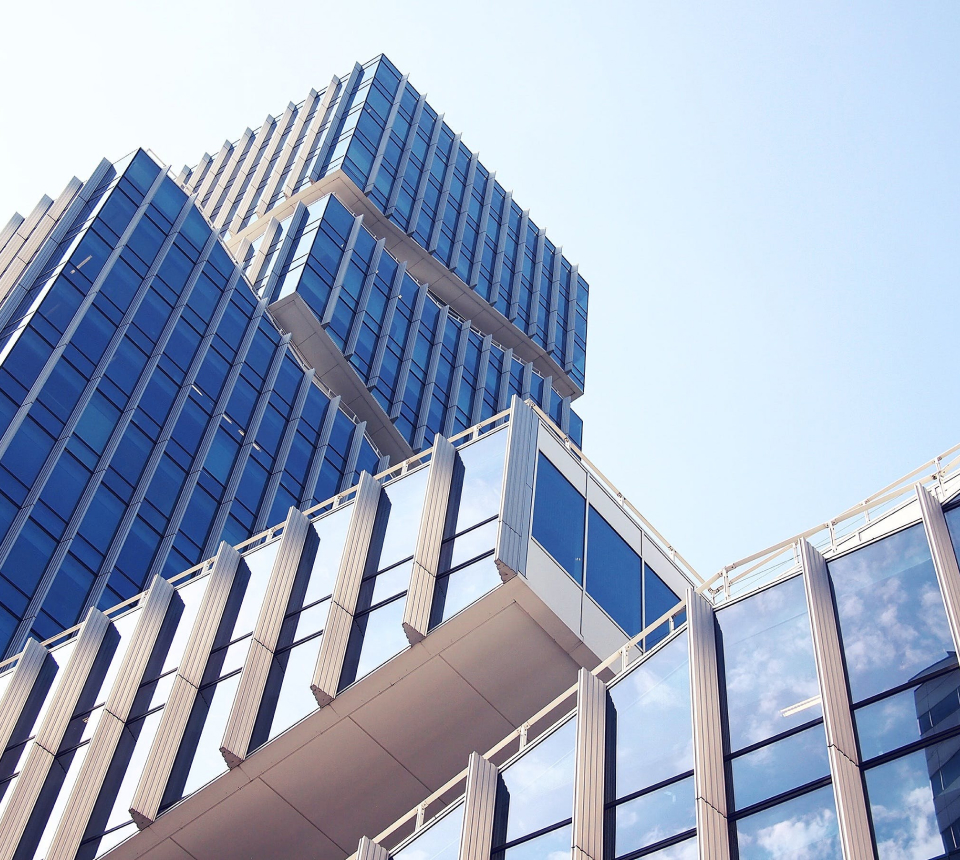
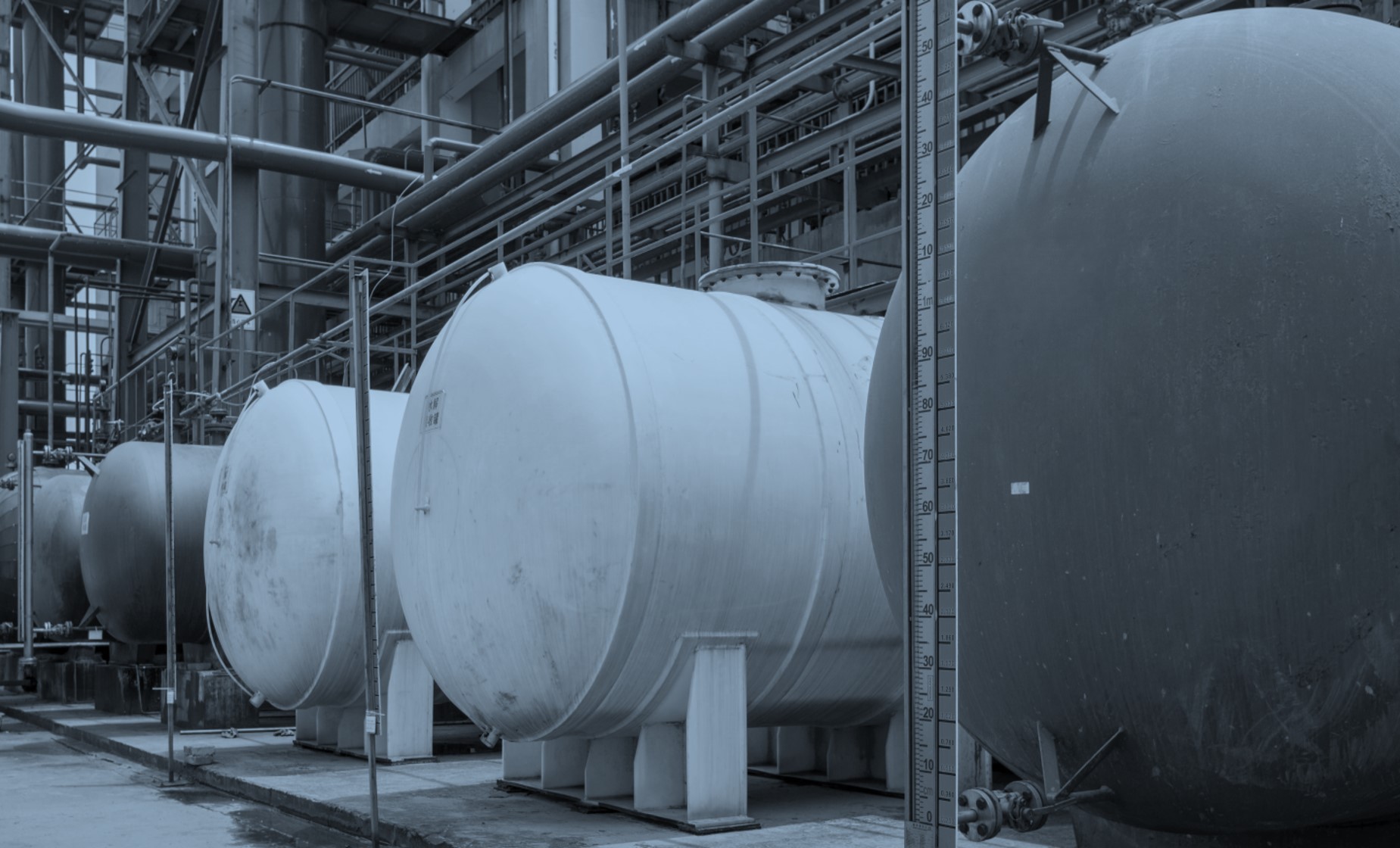
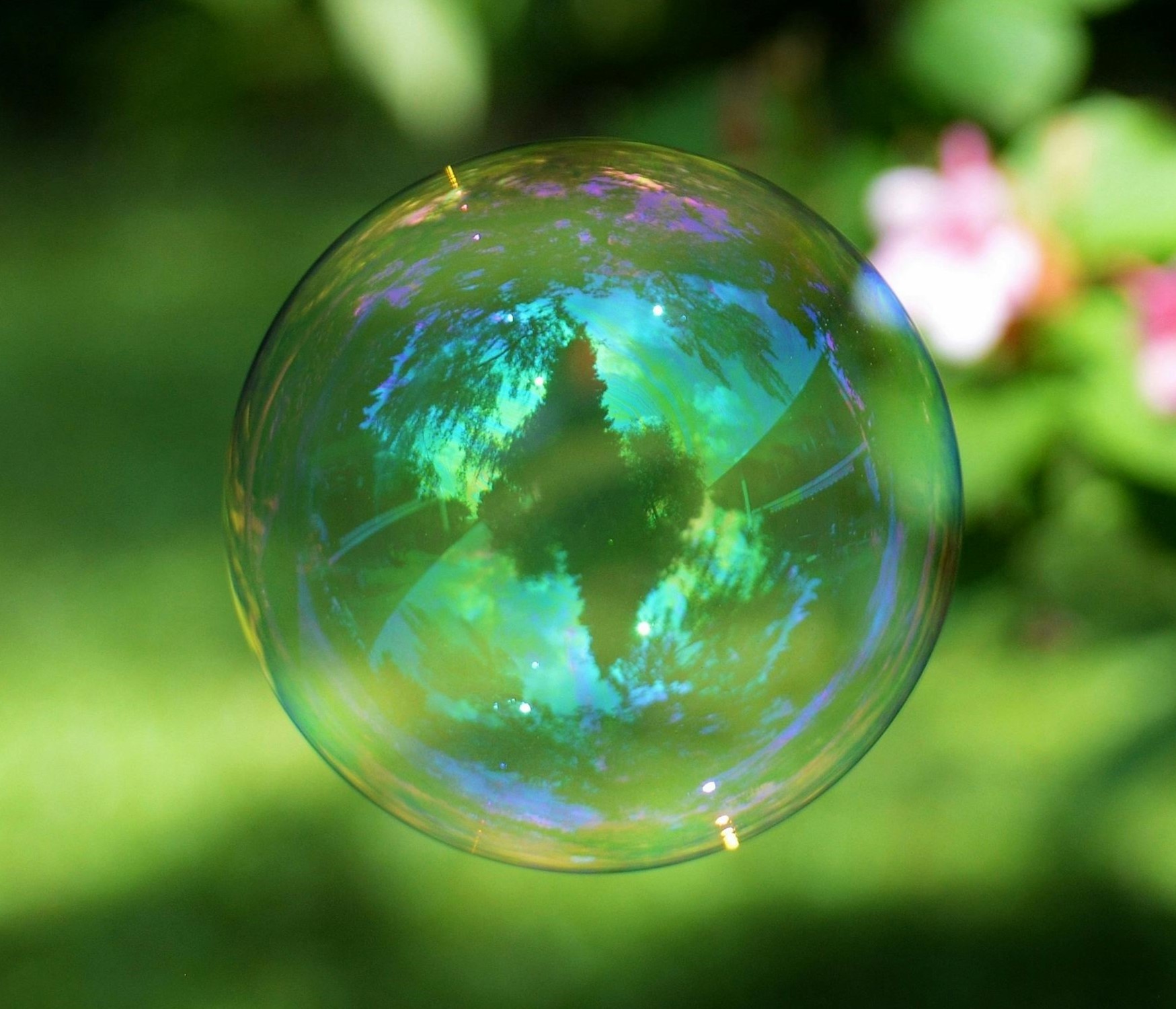
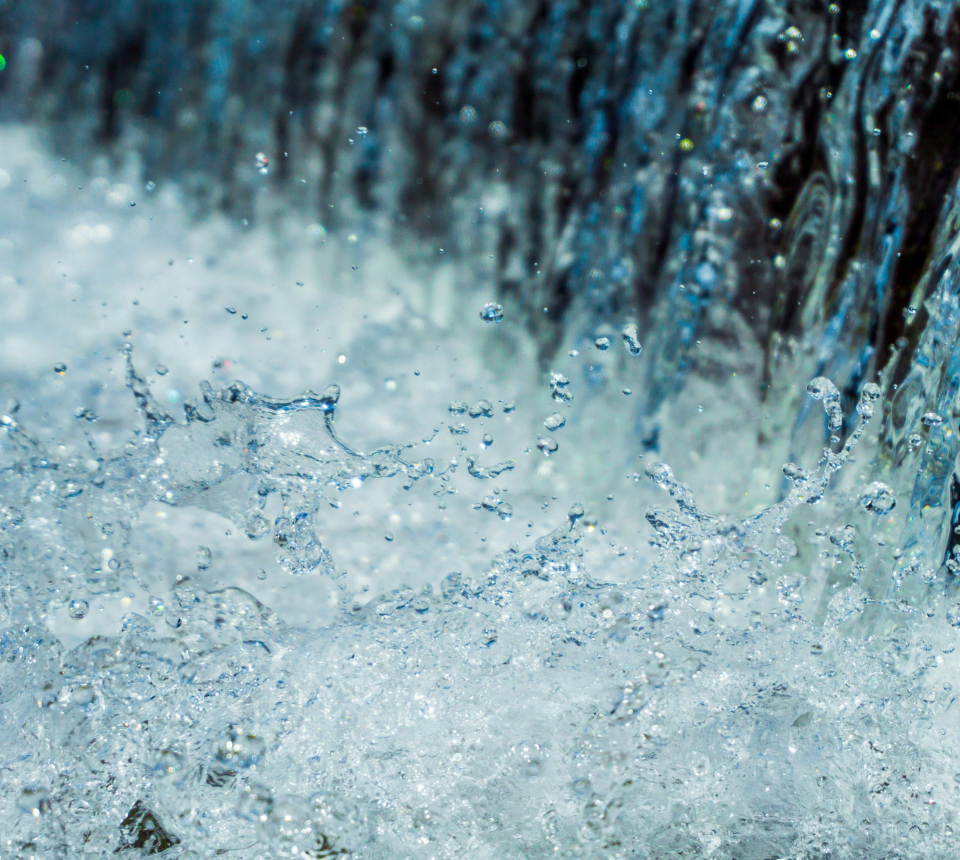
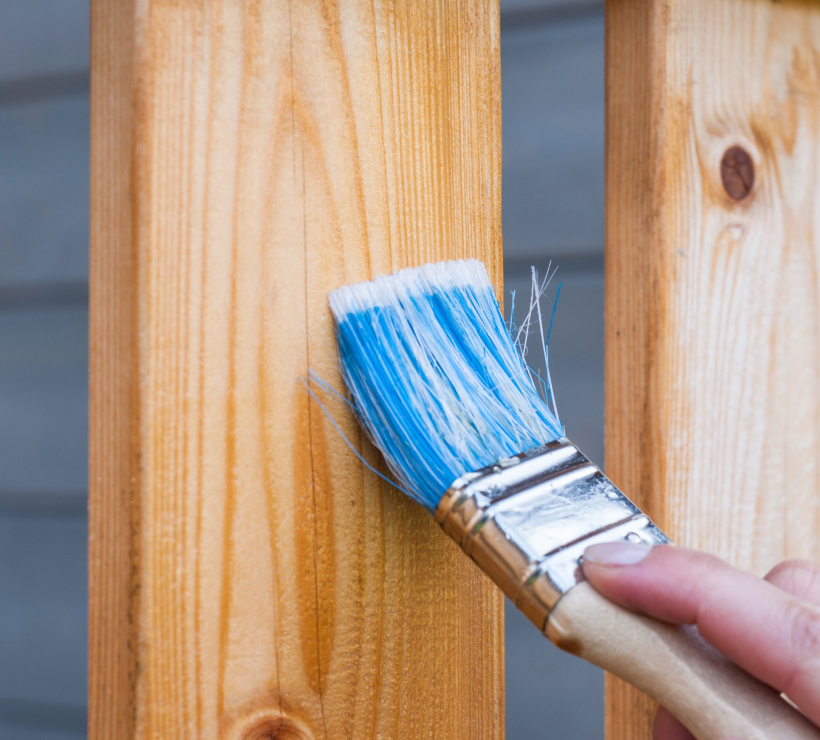

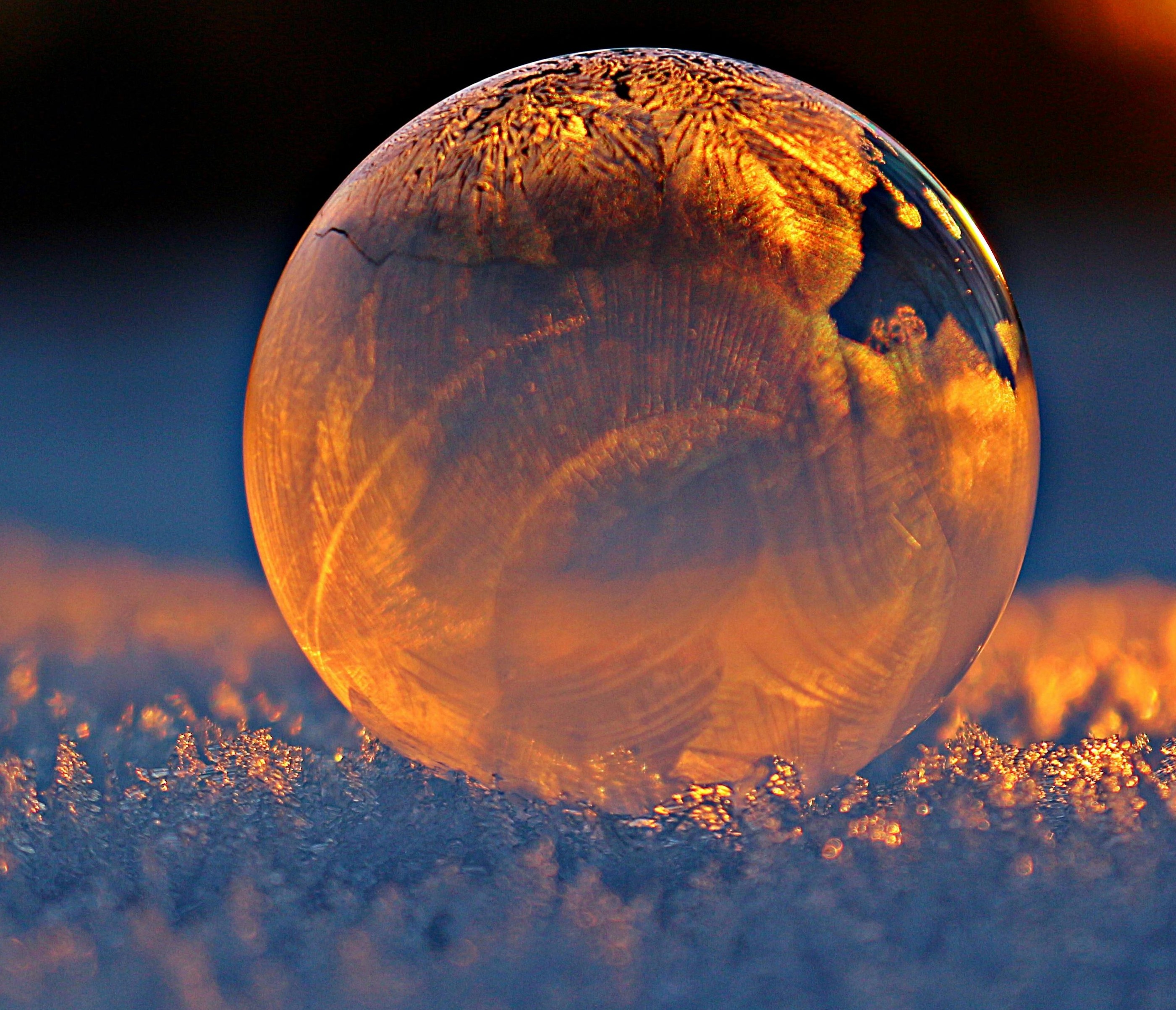
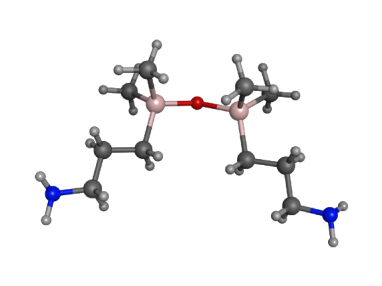
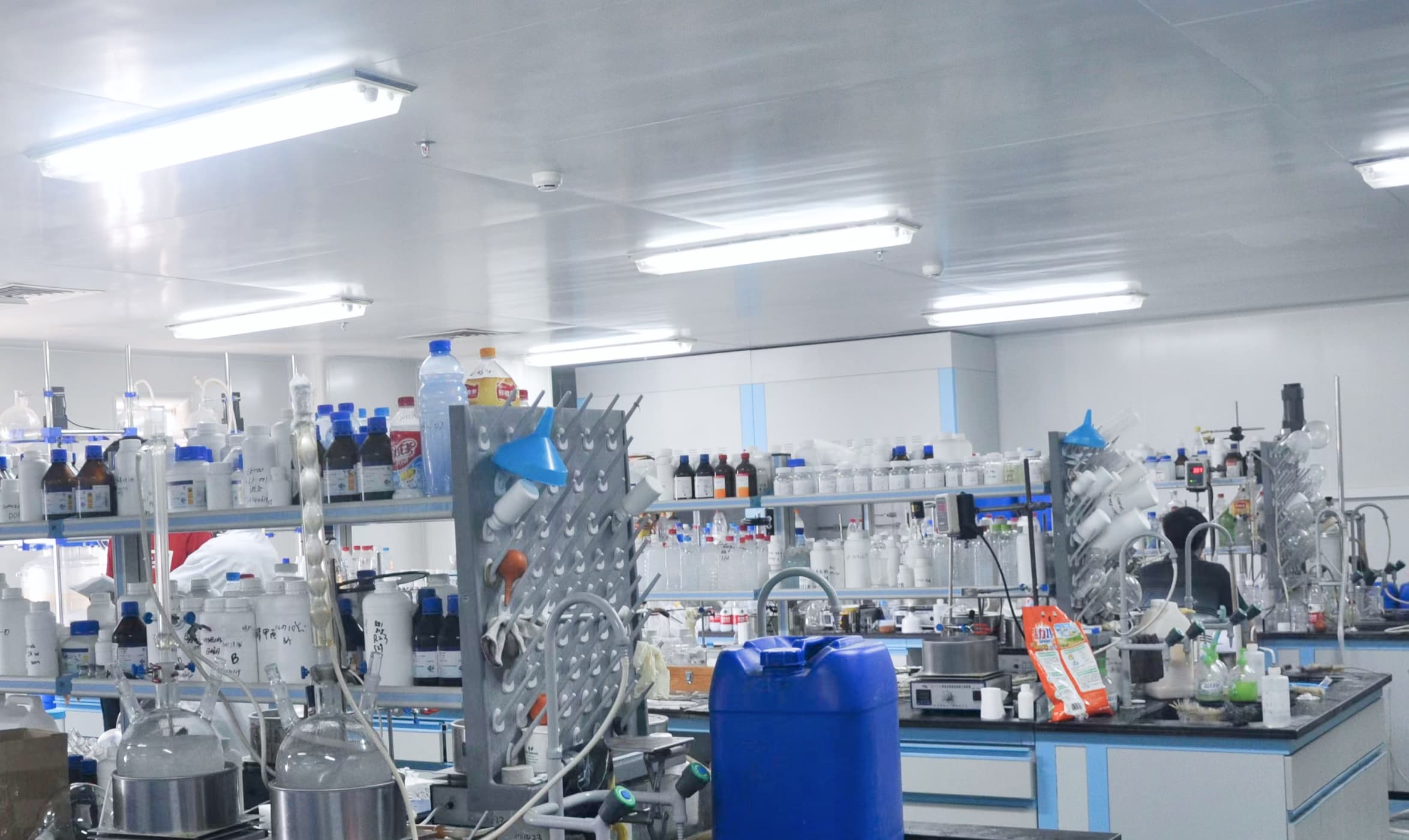
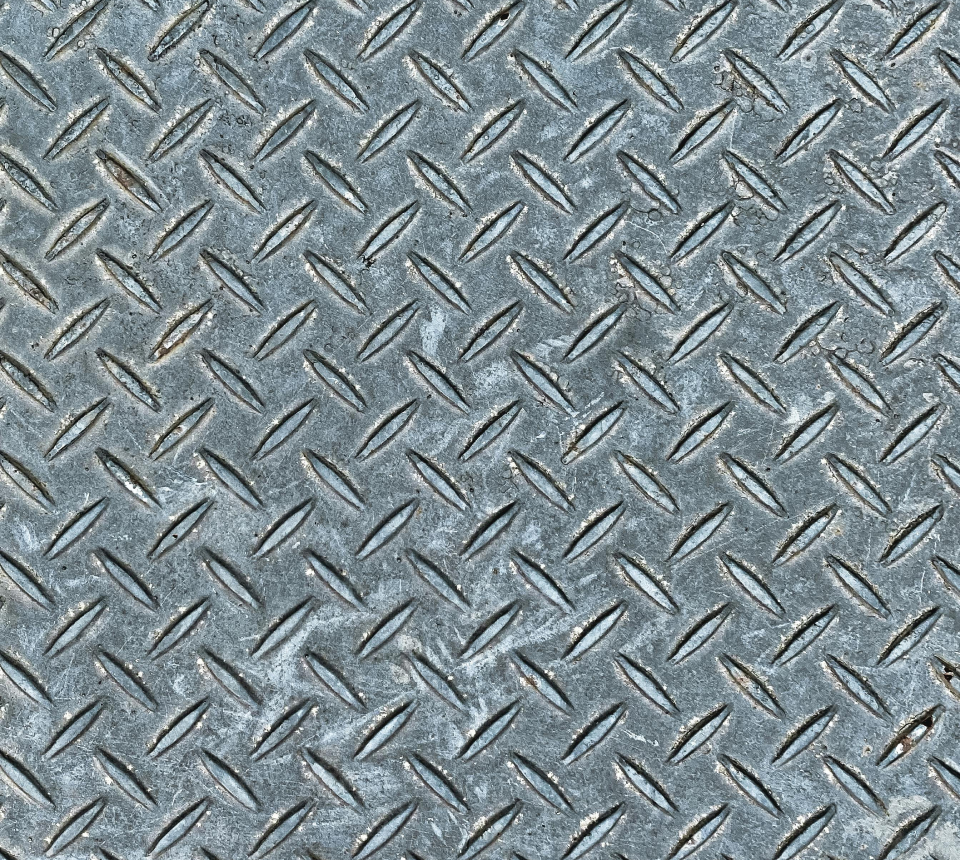
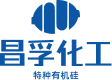
+86 27 8439 6550
+86 181 6277 0058
sales@cfsilanes.com
Optics Valley Bio-City
No. 666, Gaoxin Avenue
Hongshan District, Wuhan City
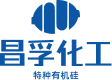
+86 27 8439 6550 | +86 181 6277 0058
sales@cfsilanes.com
Optics Valley Bio-City
No. 666, Gaoxin Avenue
Hongshan District, Wuhan City
Copyright © Hubei ChangFu Chemical Co., Ltd. All Rights