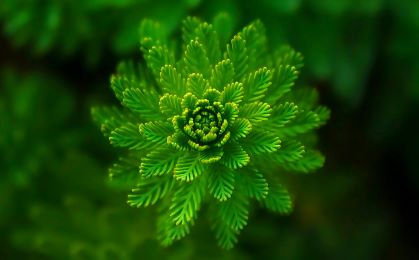
Contact Changfu Chemical Now!
+86 27 8439 6550 | +86 181 6277 0058
Silicone Potting Compound for Electronics: Benefits, Applications, and Selection Tips
As the digital age progresses, the electronics industry continues to demand higher levels of protection and reliability for devices operating in harsh environments. With the rise of smart devices, electric vehicles, industrial automation, and advanced medical equipment, there's an urgent need for dependable encapsulation materials. Enter the silicone potting compound for electronics—a flexible, high-performance material that's become the gold standard for insulating and protecting sensitive electronic components.
In this extended guide, we will explore the science behind silicone compounds, examine their practical benefits, highlight industry-specific applications, and guide you through the process of selecting and applying the right compound for your needs.
Introduction to Potting Compounds
Potting is a process of filling or covering electronic assemblies with a liquid material that hardens to protect against environmental and mechanical damage. This protection is crucial for preventing premature failure of the electronics due to moisture, vibration, dust, chemicals, or temperature extremes.
Potting materials generally fall into three major categories:
- Epoxy-based compounds – Known for rigidity and strong adhesion
- Polyurethane-based compounds – Offering a good balance between flexibility and durability
- Silicone-based compounds – Providing superior thermal and environmental resistance with excellent elasticity
Among these, silicone potting compound for electronics stands out for its long-term stability, adaptability across temperatures, and biocompatibility.
What is Silicone Potting Compound?
Silicone potting compound is a two-component or single-component silicone rubber used to encapsulate and protect electronic assemblies. Composed of silicone polymers, fillers, and curing agents, these compounds form a rubbery, flexible mass upon curing.
The chemistry of silicone makes it uniquely suited for electronics. The polymer chains maintain their flexibility across a wide temperature range and do not degrade easily under UV exposure or chemical attack. Silicone compounds may be tailored for specific needs, such as flame retardance, thermal conductivity, or optical transparency.
These compounds are available in:
- One-part systems (RTV): Convenient and easy to use, cures at room temperature
- Two-part systems: Require mixing but provide greater control over cure speed and material properties
Why Use Silicone Potting Compound for Electronics?
The increasing complexity and miniaturization of electronics have increased vulnerability to failure. Silicone potting offers an effective line of defense for circuit boards, sensors, modules, and other components. Here’s why it’s a preferred choice:
- Moisture and corrosion resistance: Forms a water-tight seal, preventing condensation and corrosion
- Thermal stability: Performs consistently in cold, heat, or cycling environments
- Shock absorption: Protects against drops, vibrations, and mechanical impact
- Electrical insulation: Prevents arcing and electrical shorts
- Longevity: Maintains protective properties over the lifespan of the device
Key Benefits of Silicone-Based Encapsulation
1. Wide Temperature Range
Silicone can withstand temperatures from -55°C to over +200°C without losing elasticity or performance. This is critical for automotive and aerospace electronics subjected to temperature extremes.
2. Exceptional Flexibility
Unlike rigid potting materials like epoxy, silicone remains flexible after curing. This minimizes stress on sensitive solder joints and components, especially when thermal expansion occurs.
3. Excellent Dielectric Properties
Silicone’s dielectric strength often exceeds 20 kV/mm. This high insulation value is essential for high-voltage circuits, power supplies, and transformers.
4. Resistance to UV and Ozone
For outdoor and solar applications, silicone offers unmatched resistance to ultraviolet radiation and ozone. It does not yellow or degrade when exposed to sunlight.
5. Chemical and Moisture Resistance
Silicone resists aggressive chemicals, salt spray, and humid environments. It’s perfect for marine electronics and devices used in industrial plants.
Common Applications
Silicone potting compounds are trusted across multiple industries:
1. Automotive Electronics
Used in engine control modules, battery packs, EV charging units, and LED headlamps. Withstand vibrations, oil exposure, and extreme heat.
2. Consumer Electronics
Smartphones, fitness trackers, and wireless earbuds benefit from the waterproofing and miniaturization support offered by silicone encapsulation.
3. Medical Devices
Biocompatible silicone is used to encapsulate pacemakers, insulin pumps, and diagnostic sensors—ensuring both patient safety and reliability.
4. LED Lighting Systems
Transparent silicone potting compounds protect LED arrays while allowing maximum light output. They also resist yellowing from UV light.
5. Aerospace and Military
Used in avionics, guidance systems, and satellite modules. Silicone’s ability to function in vacuum and radiation-prone environments is unmatched.
Types of Silicone Potting Compounds
1. Room Temperature Vulcanizing (RTV)
Convenient for field repairs or small-scale production. RTV silicones require no special curing equipment.
2. Heat-Curing Silicones
Ideal for high-speed manufacturing. These compounds cure faster under elevated temperatures, improving throughput.
3. Optical-Grade Silicones
Used in photonics and LED applications. Maintains clarity and transmits light efficiently.
4. Flame-Retardant Silicones
Critical in safety-focused applications. Formulated to meet UL94-V0 or similar fire safety standards.
Selection Criteria
Selecting the right silicone potting compound for electronics involves multiple factors:
1. Thermal Conductivity
Choose thermally conductive silicone for power devices to avoid overheating. Values range from 0.5 W/m·K to over 3 W/m·K.
2. Viscosity
Low-viscosity compounds flow into intricate spaces easily. High-viscosity types are better for large gaps or vertical surfaces.
3. Cure Time
Rapid cure times improve productivity. However, slower curing options allow better component alignment.
4. Hardness
Measured on Shore A or D scale. Softer silicones absorb vibration, harder ones provide physical protection.
5. Electrical Properties
High dielectric strength and volume resistivity are critical for high-voltage or sensitive applications.
Application Methods and Best Practices
1. Surface Preparation
Clean all surfaces to remove dust, grease, and oxidation. Use isopropyl alcohol and ensure the area is dry before applying.
2. Mixing and Degassing
For two-part systems, thorough mixing is vital. Degassing under vacuum removes bubbles that could weaken the insulation.
3. Pouring and Curing
Pour slowly and allow the compound to fill gaps. Use molds or dams to guide the flow. Follow recommended cure times and temperatures.
4. Post-Cure Testing
After curing, check for:
- Hardness
- Adhesion
- Insulation resistance
- Thermal conductivity
Environmental Considerations and Safety
1. Low VOC Formulations
Many silicone potting compounds are low in volatile organic compounds, reducing workplace exposure and air pollution.
2. Biocompatibility
Medical-grade silicones meet international standards (e.g., ISO 10993) for safe use in or on the human body.
3. Disposal and Waste Management
Cured silicone is non-hazardous and can be disposed of with standard solid waste. Liquid components must be handled per SDS guidelines.
4. Personal Protection
Always wear gloves and goggles when handling liquid silicone. Ensure good ventilation or use fume extraction.
Conclusion
The evolution of electronics demands materials that can endure and protect in increasingly challenging environments. Silicone potting compound for electronics meets this challenge head-on. Its unmatched flexibility, thermal resistance, and electrical insulation properties make it a superior choice for professionals seeking long-term performance and reliability.
Whether you're designing the next breakthrough medical wearable, an electric vehicle component, or a solar-powered control system, silicone potting compounds can help ensure your product lasts longer, performs better, and withstands whatever the world throws at it.
Read More: A Deep Dive into Reactive Silicones and Specialty Silicones
Popular Silicon Compounds
Popular Silicon Compounds
Related News & Blog
Related News & Blog
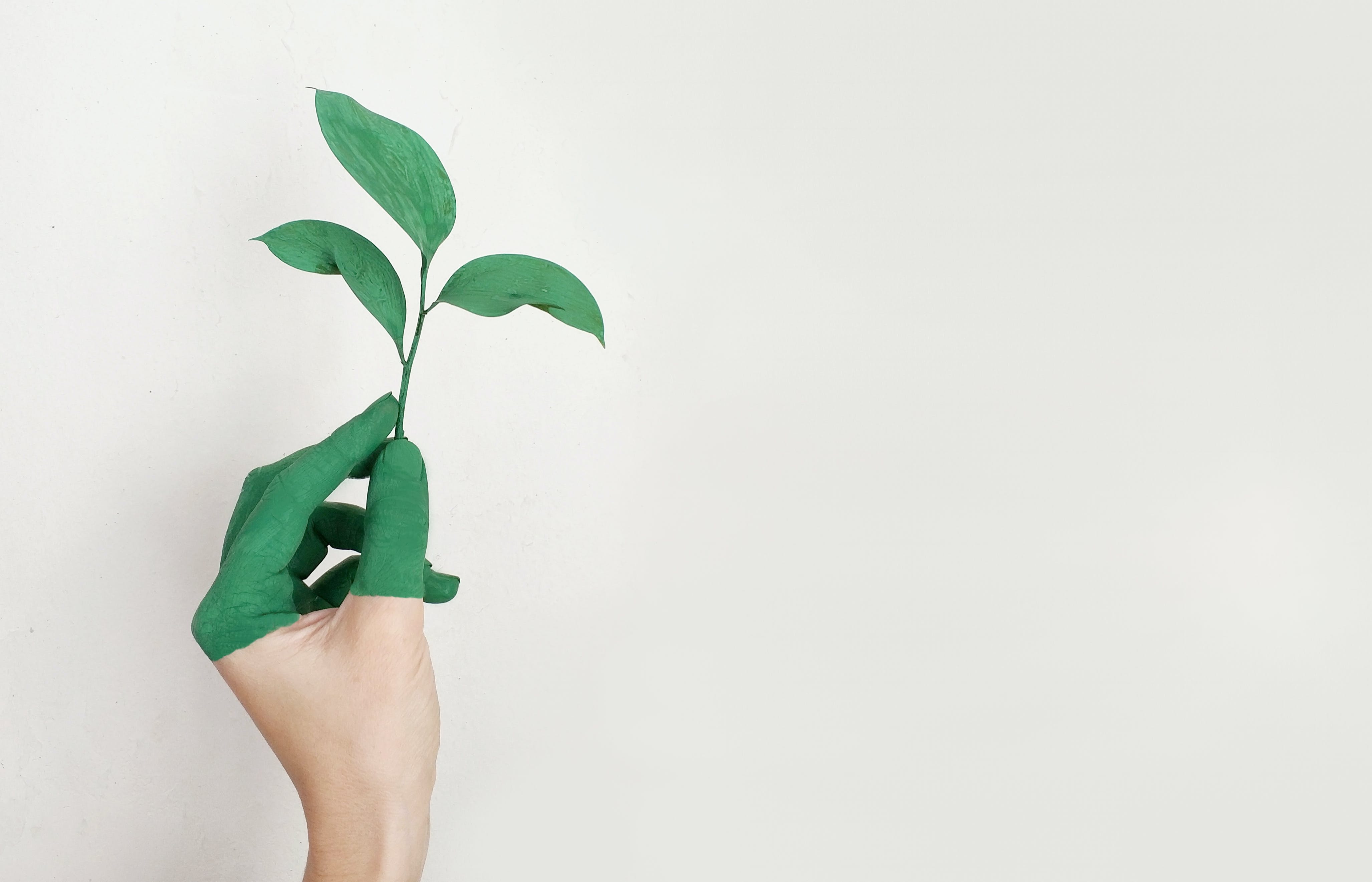
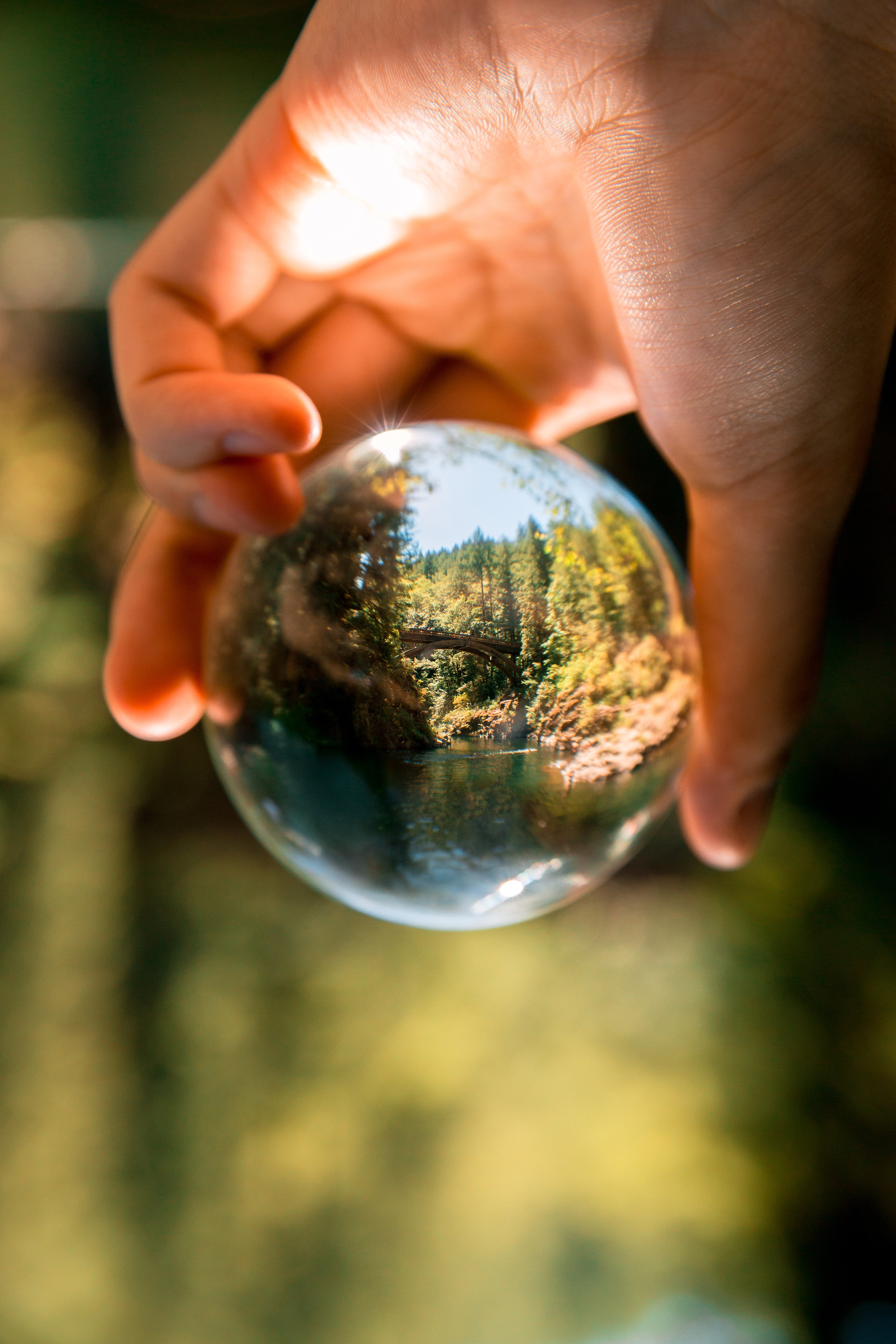
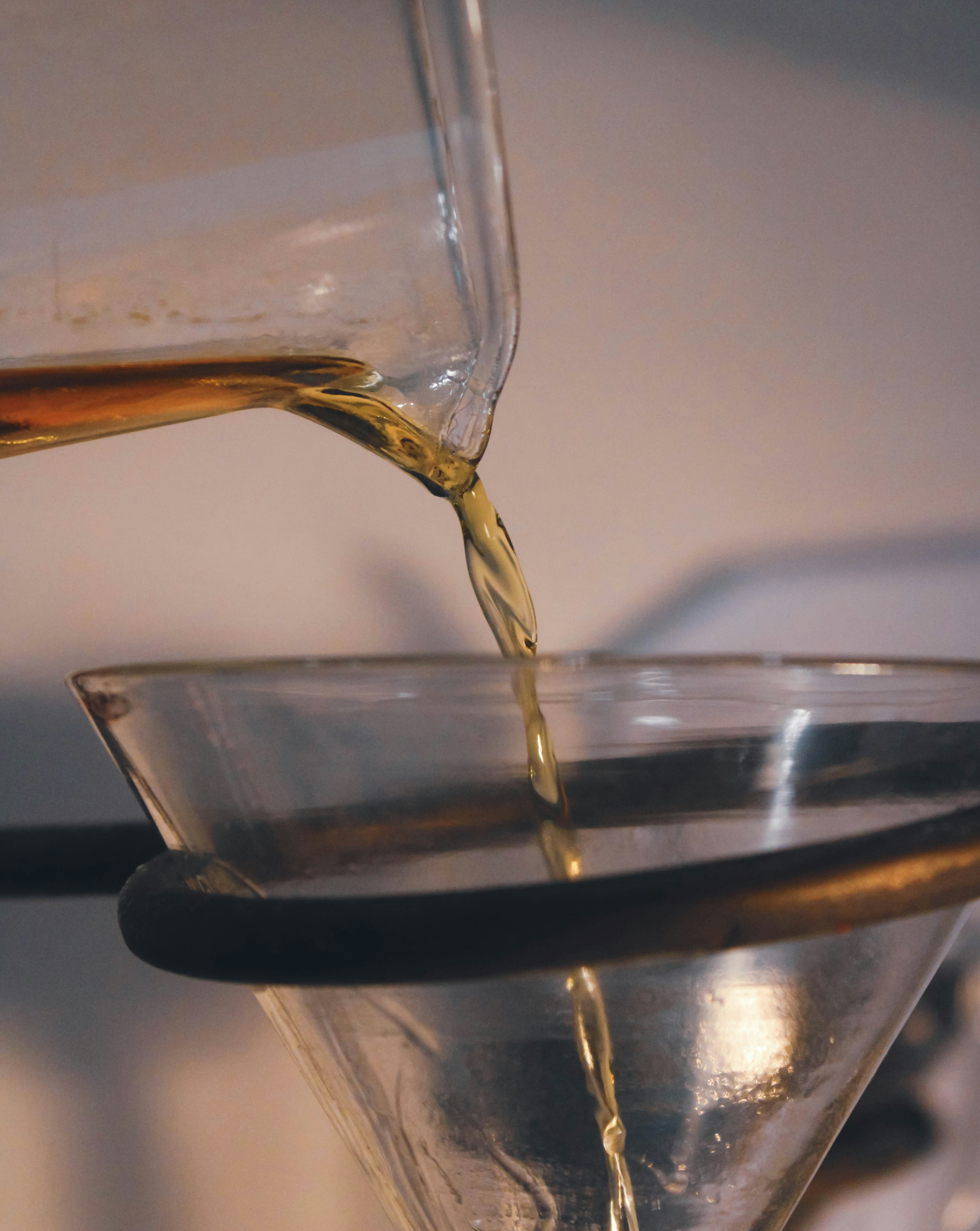
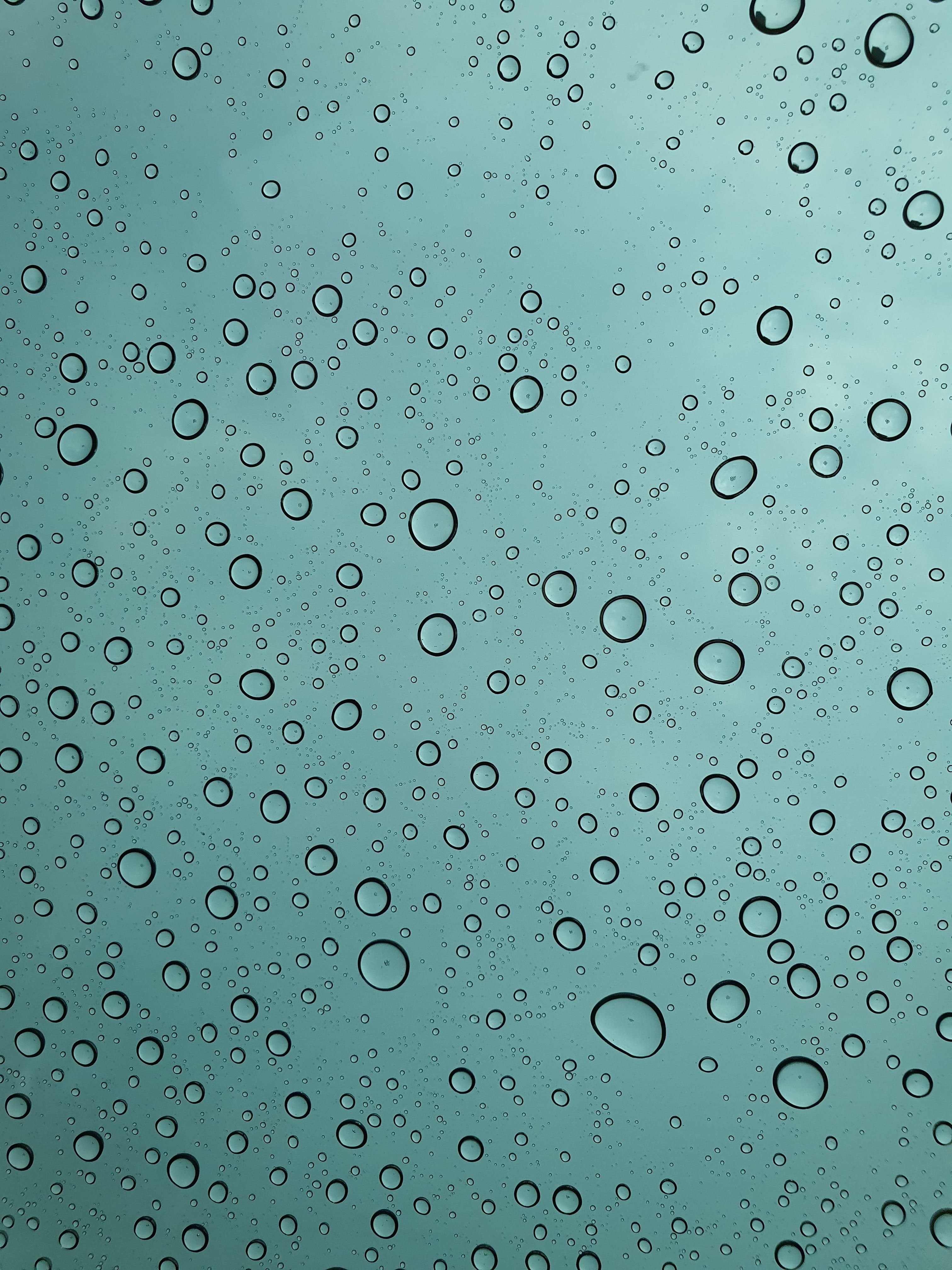
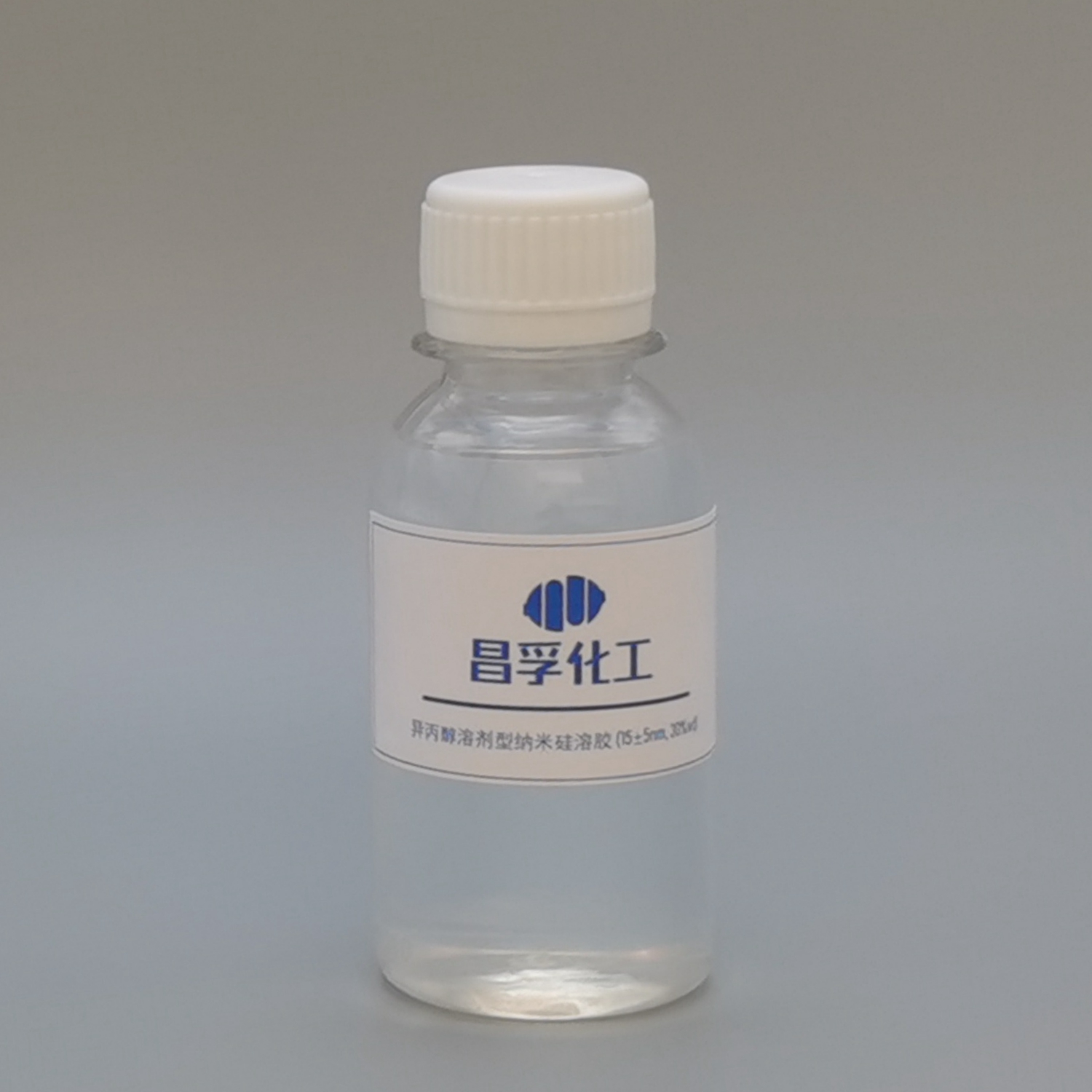
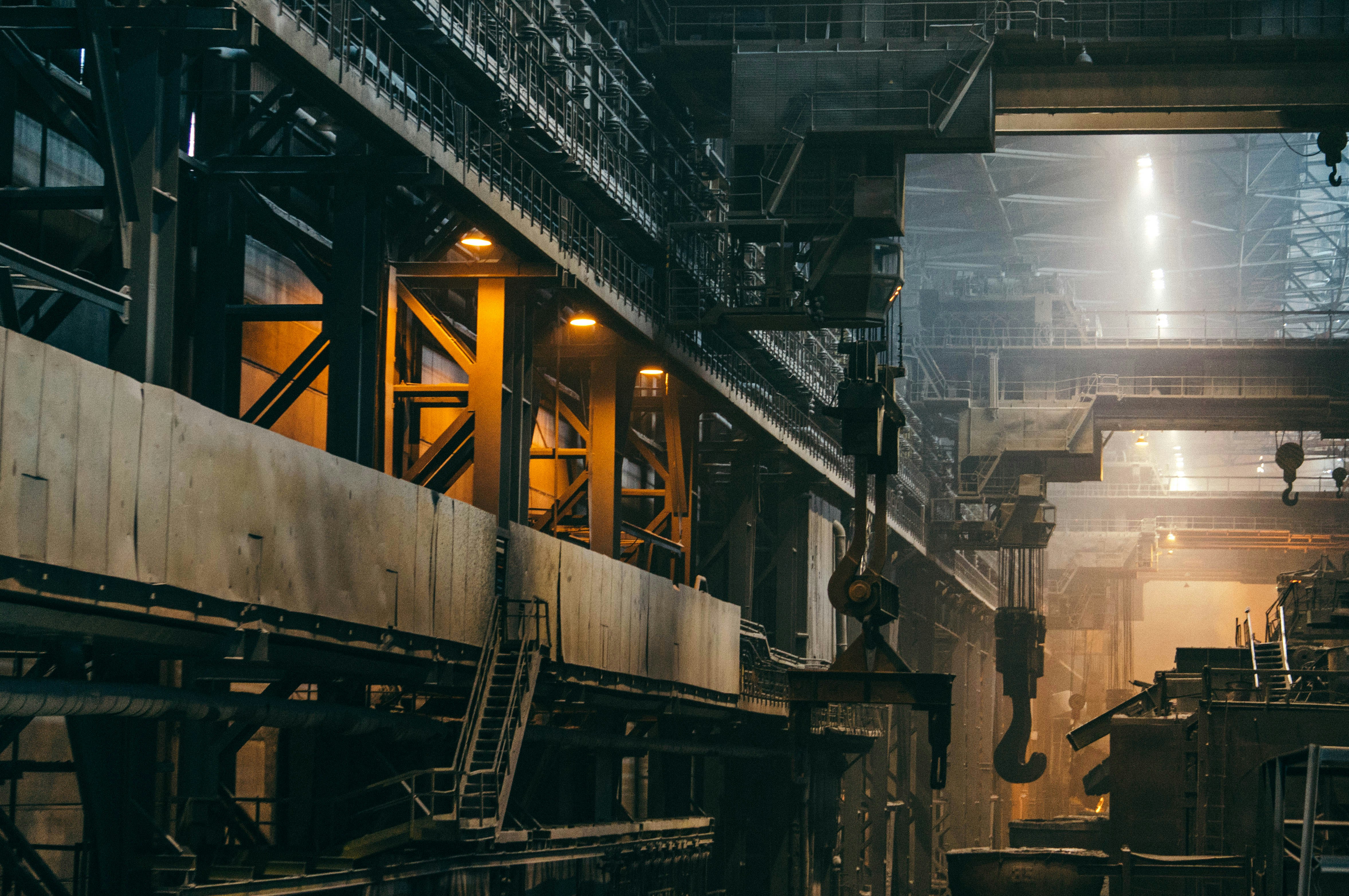
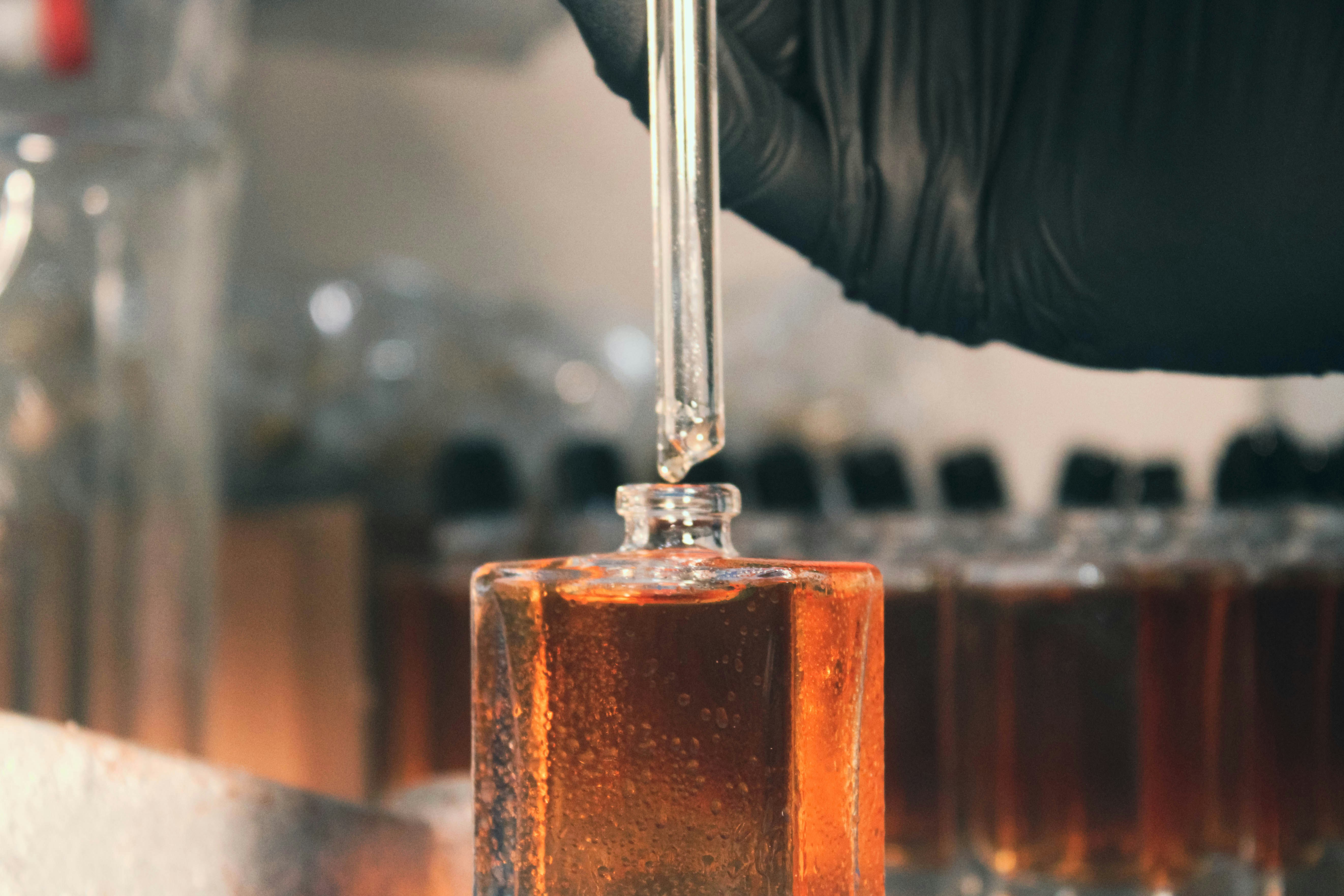
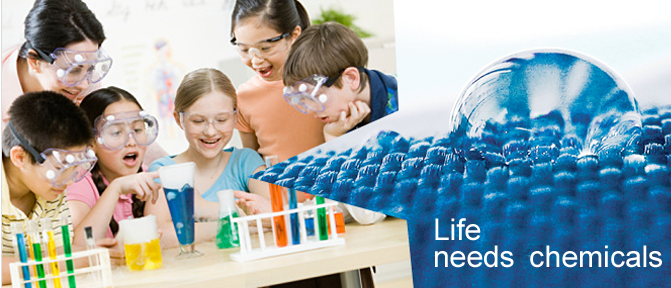

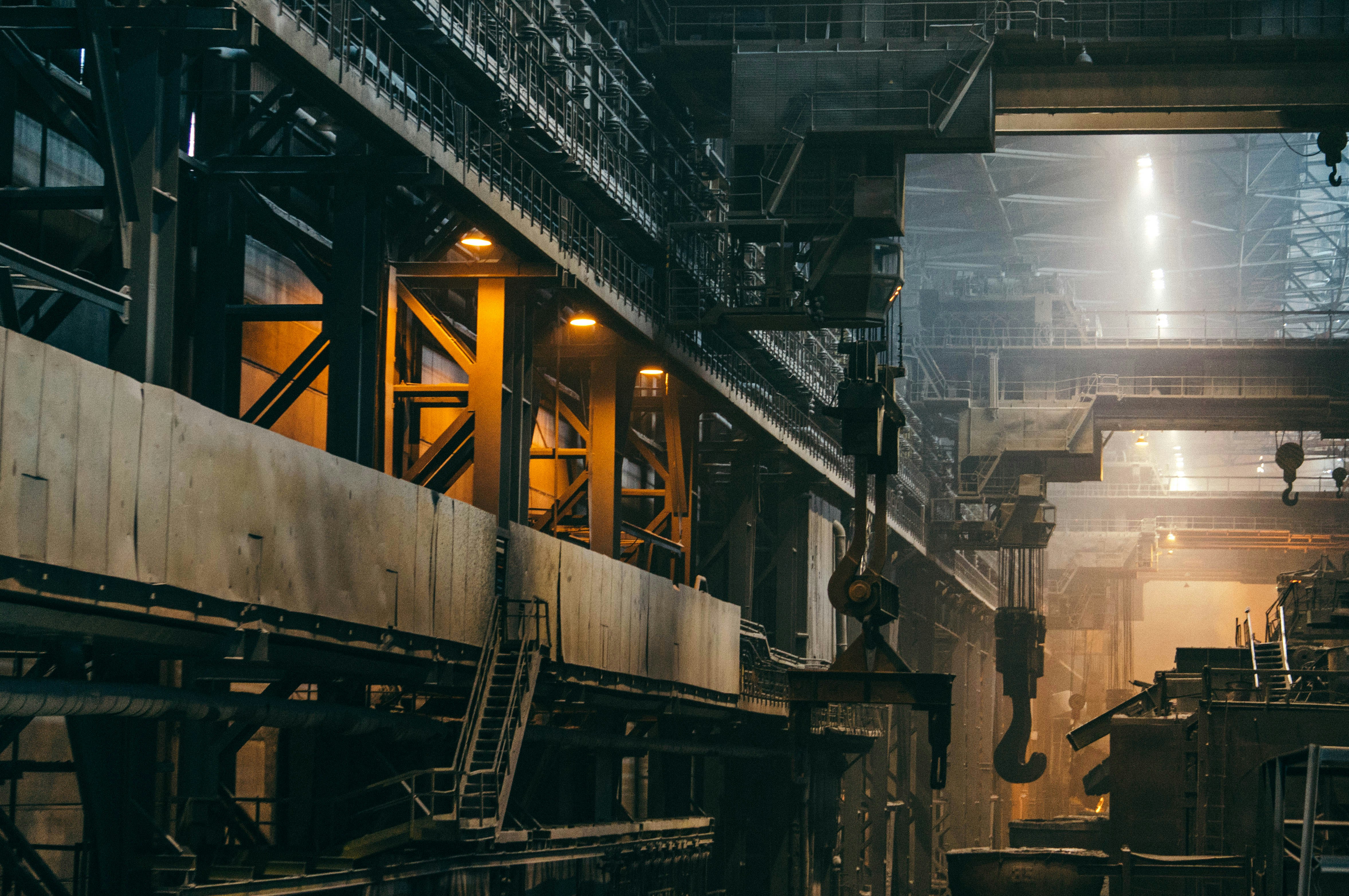
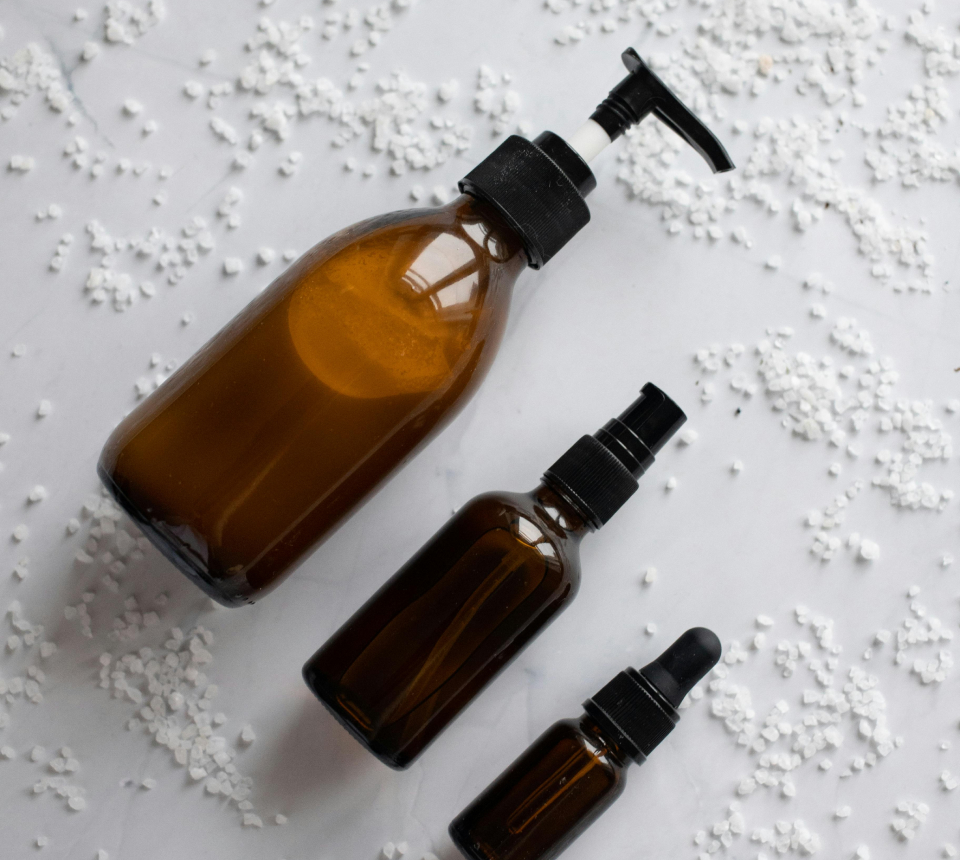
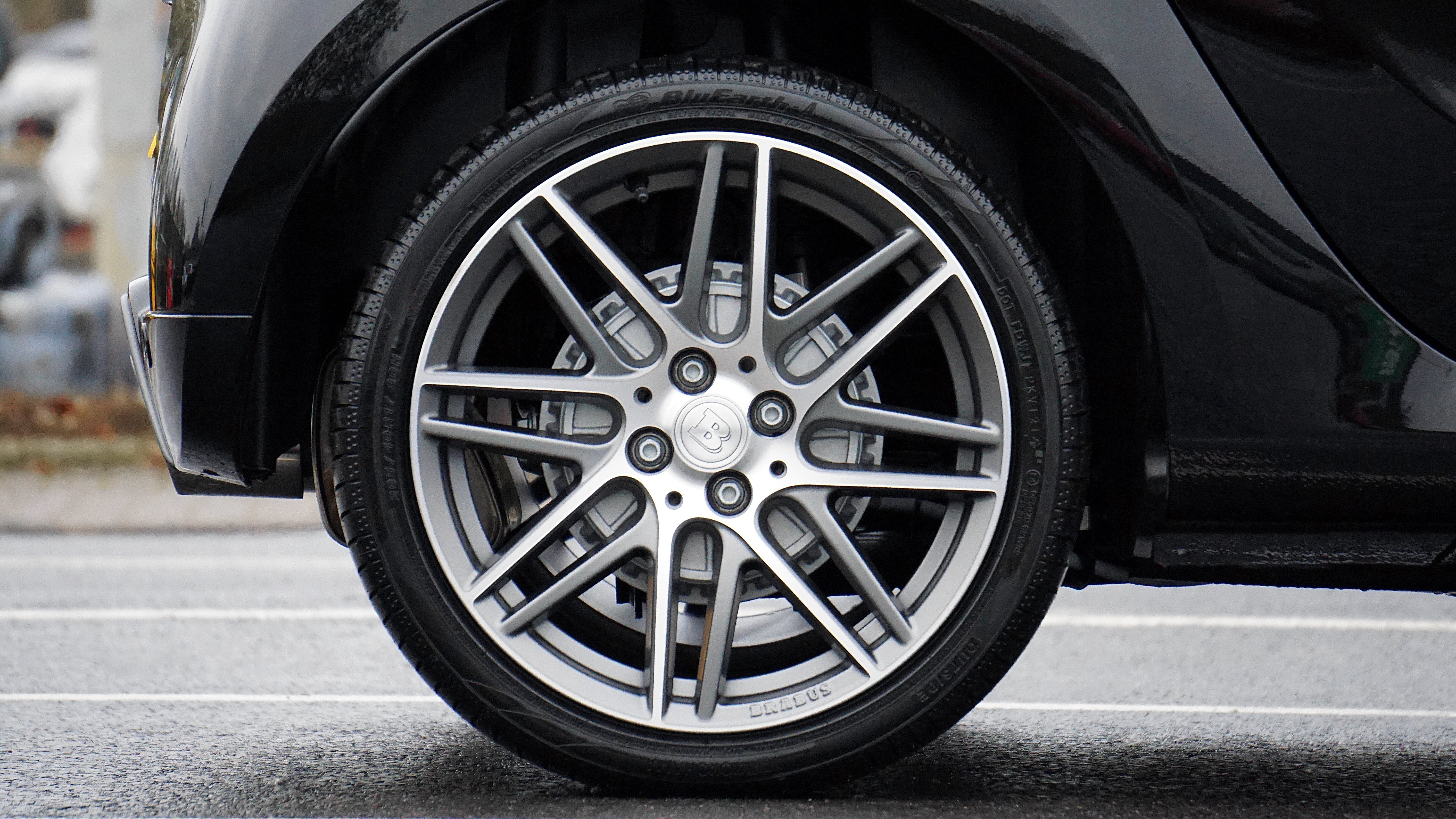
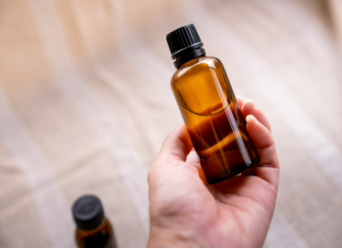
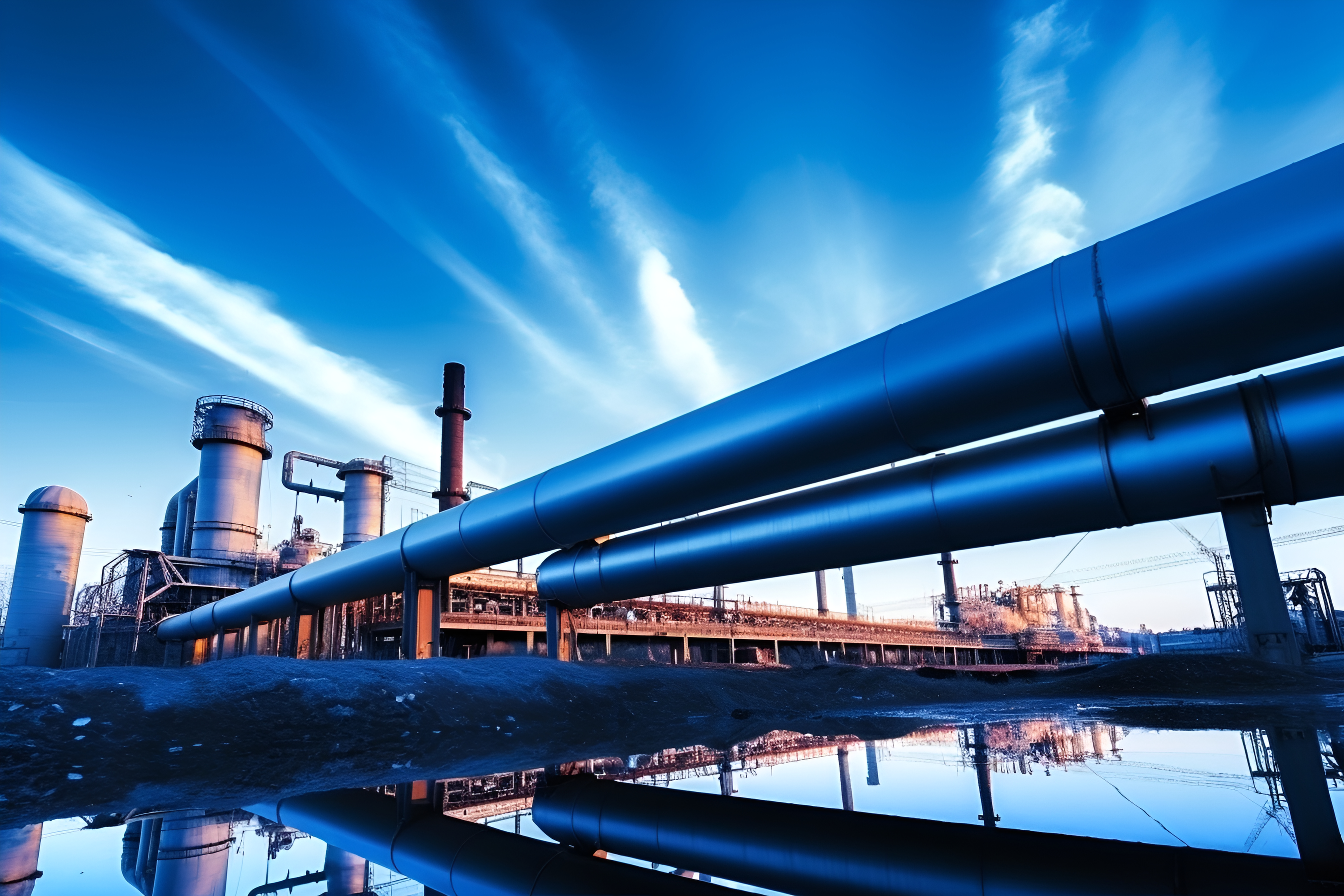

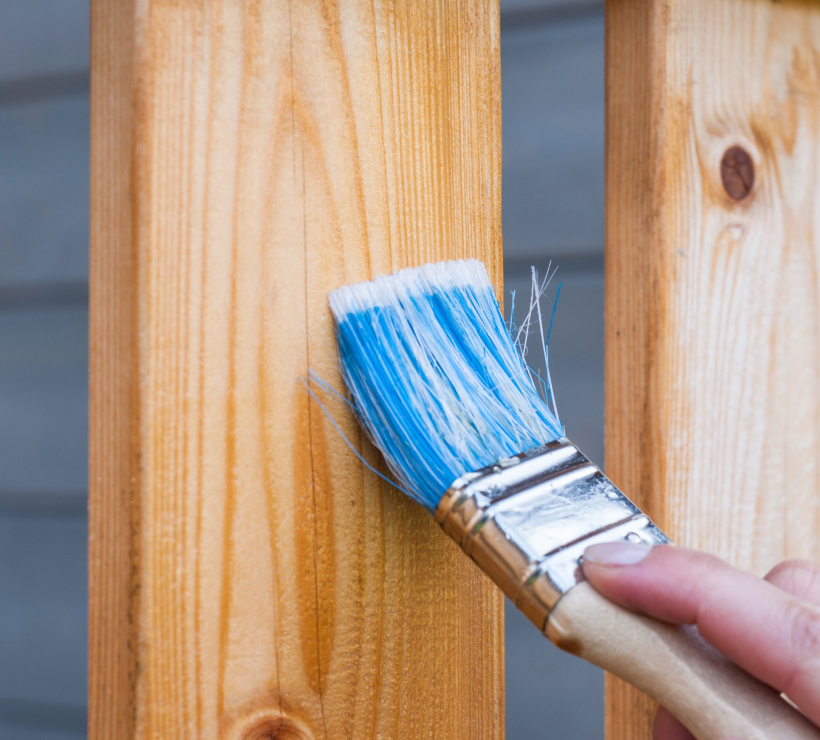
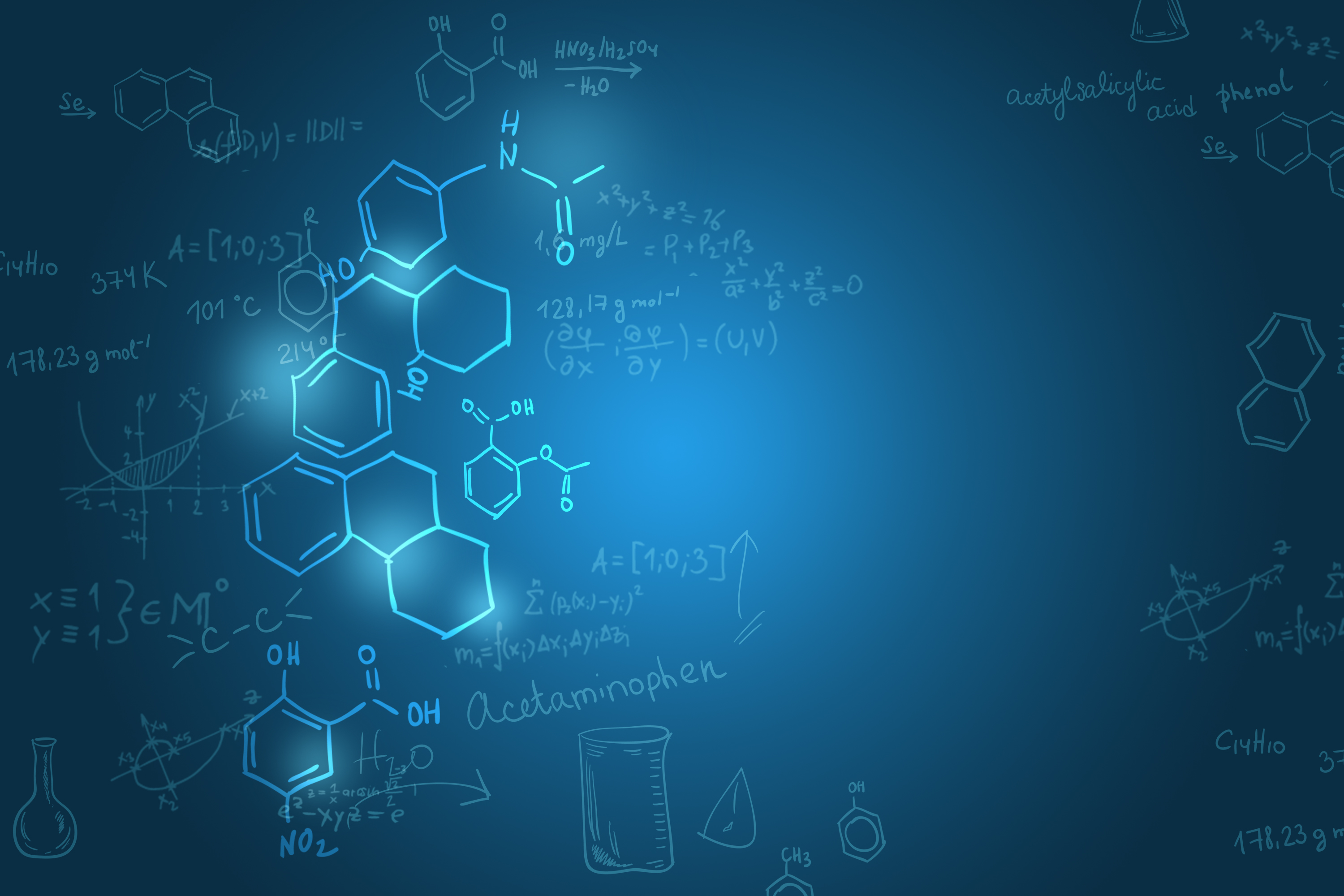
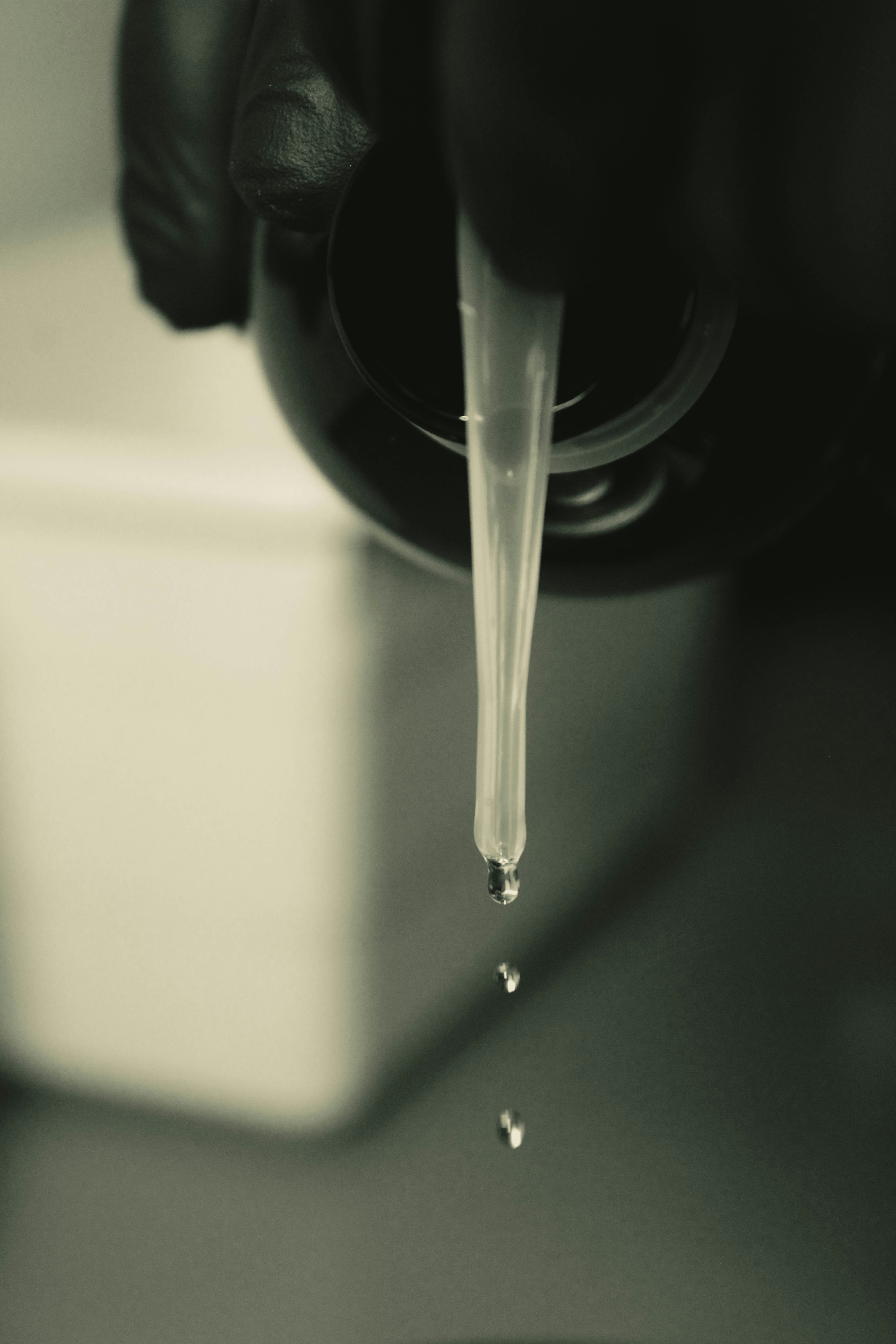
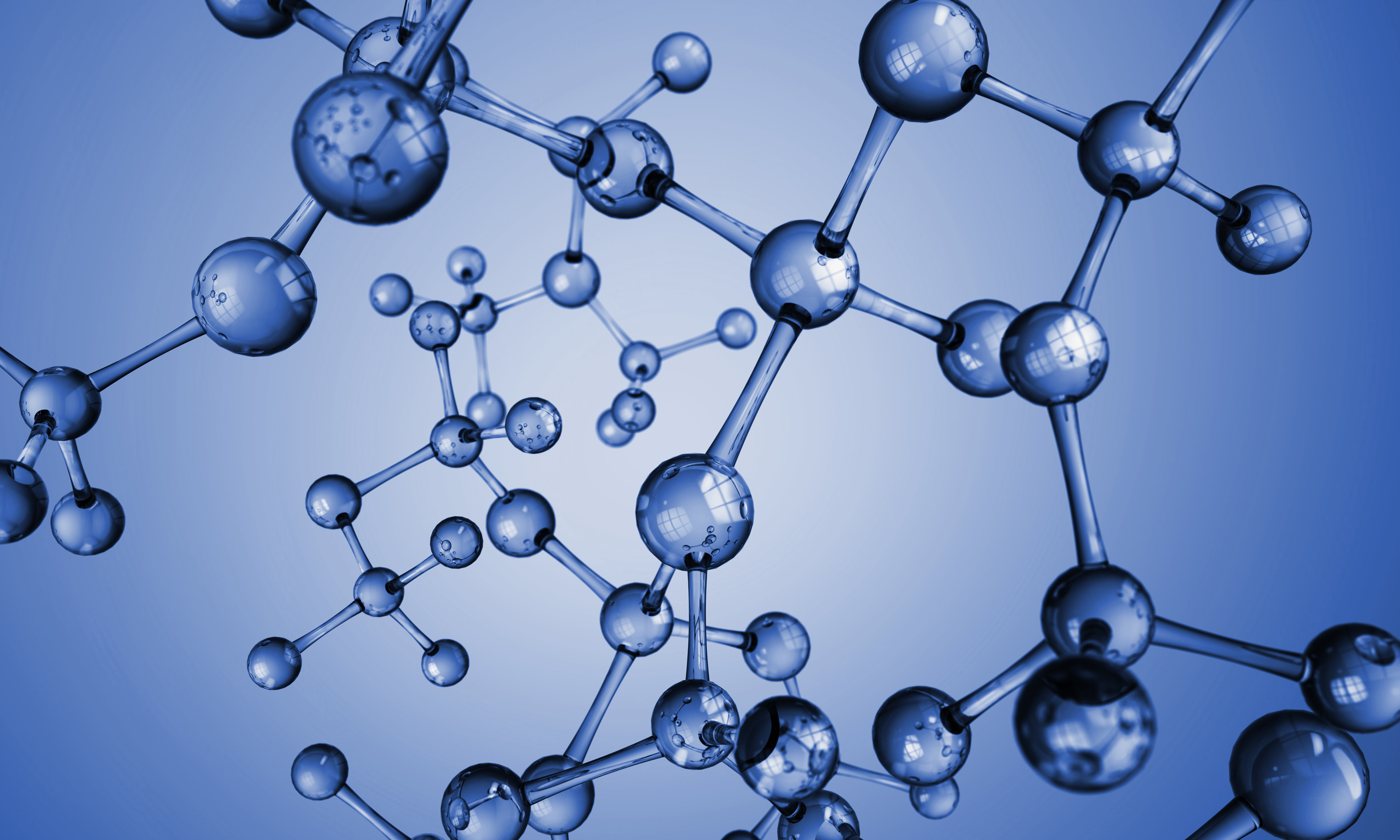
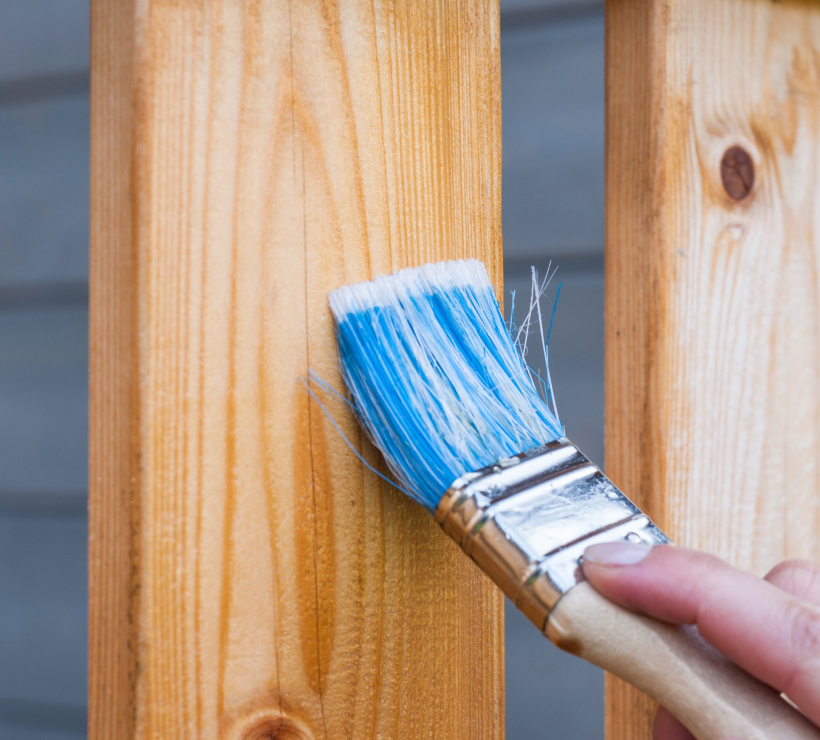

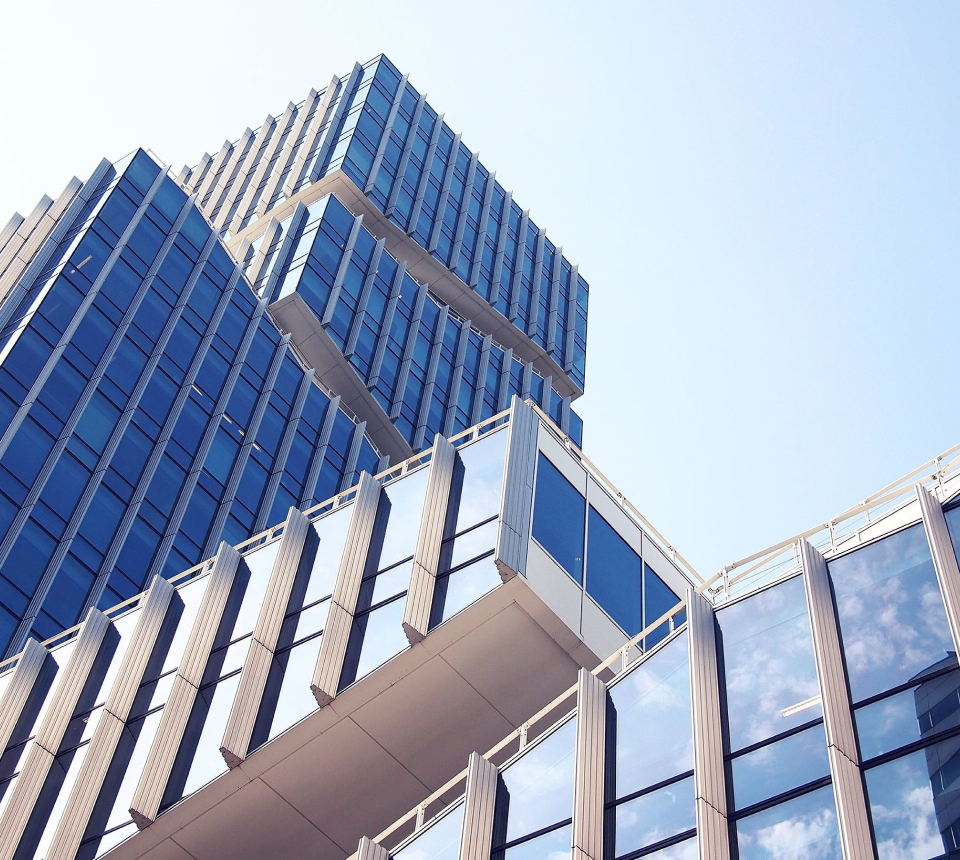
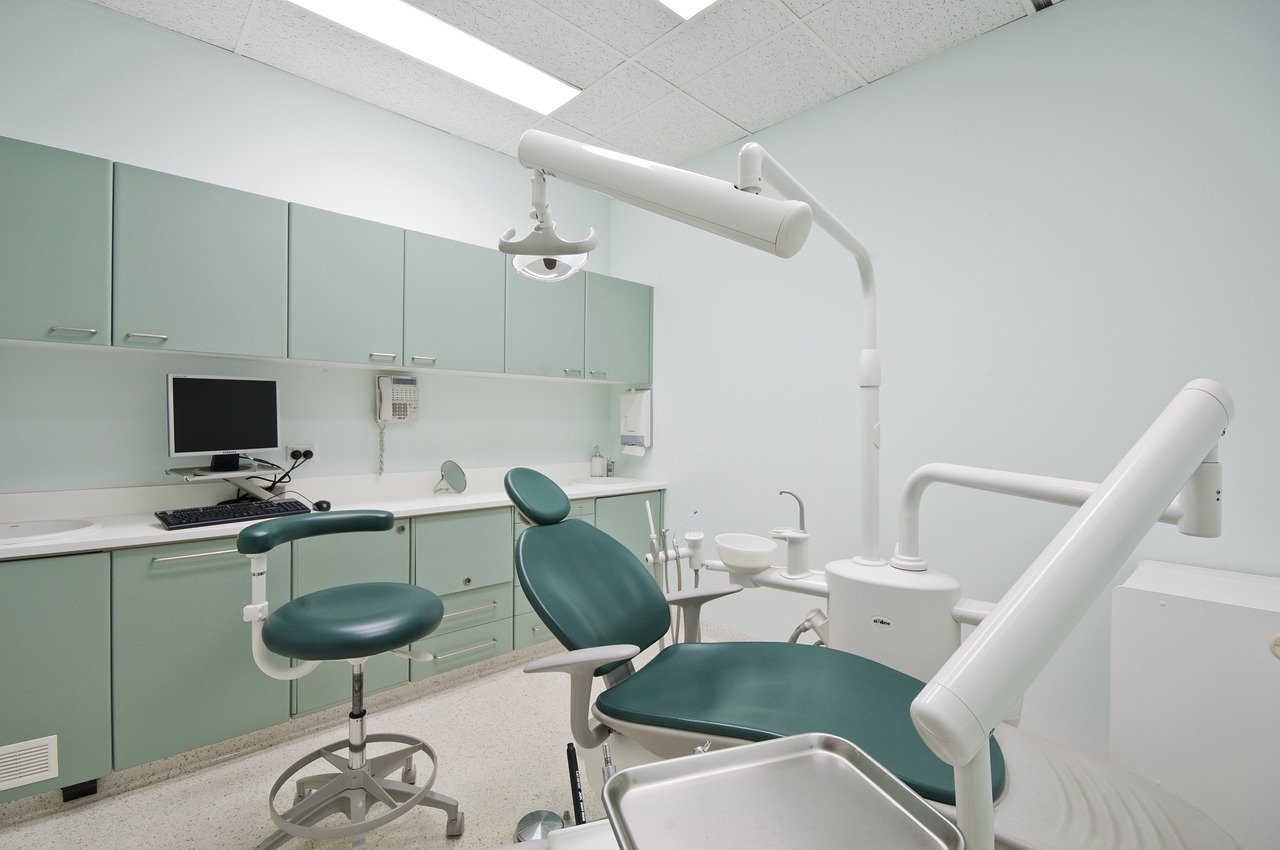
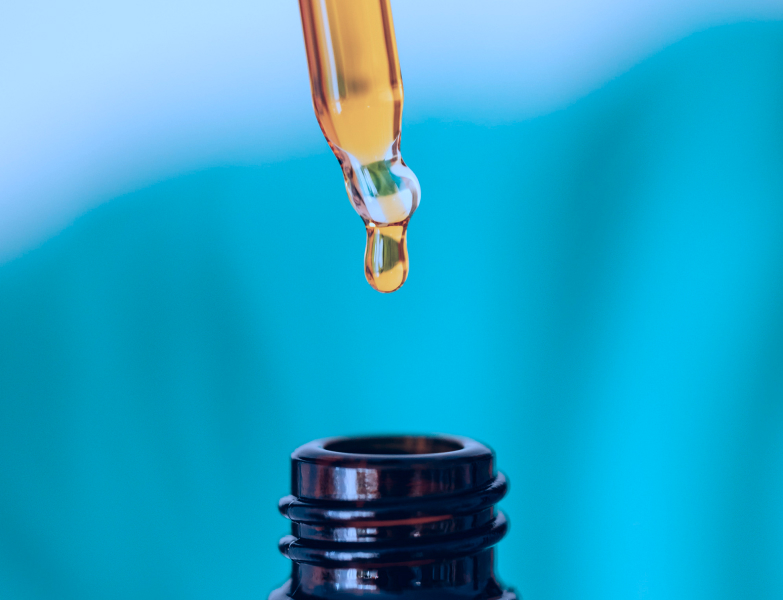
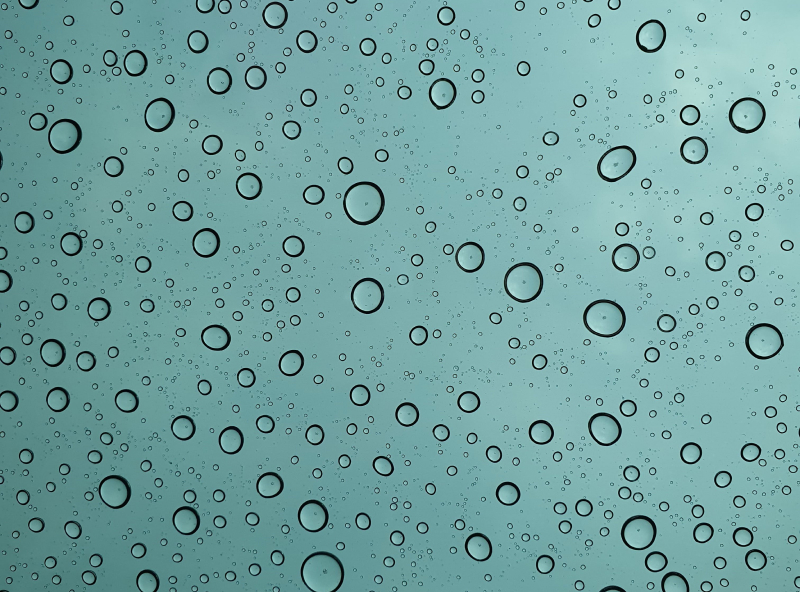
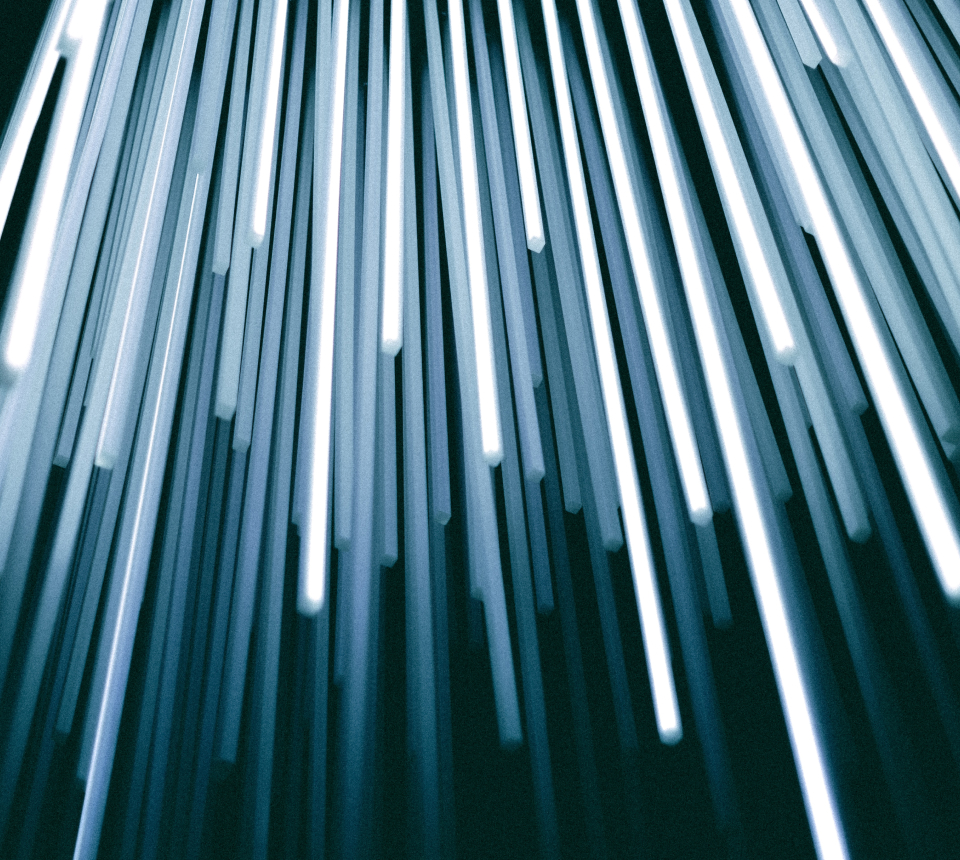
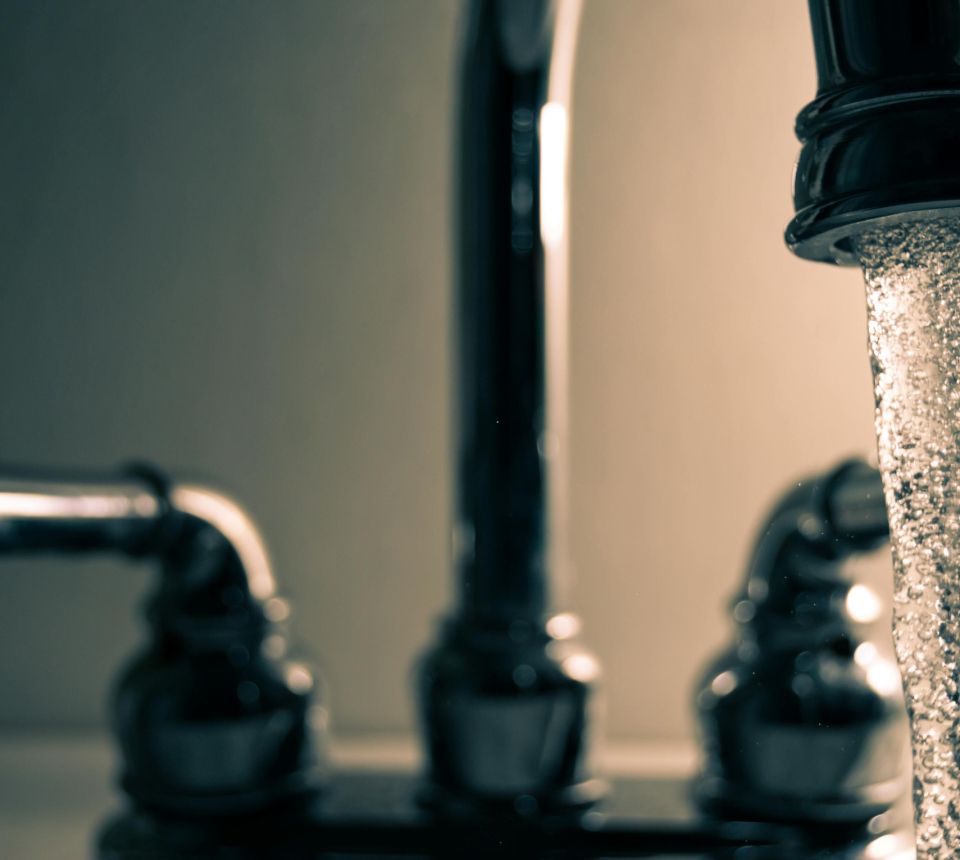
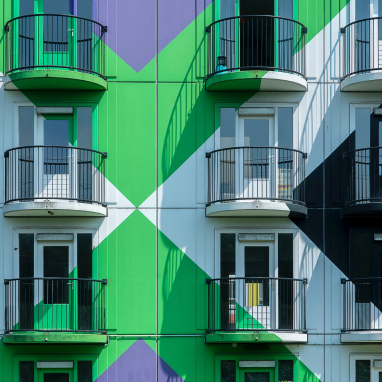
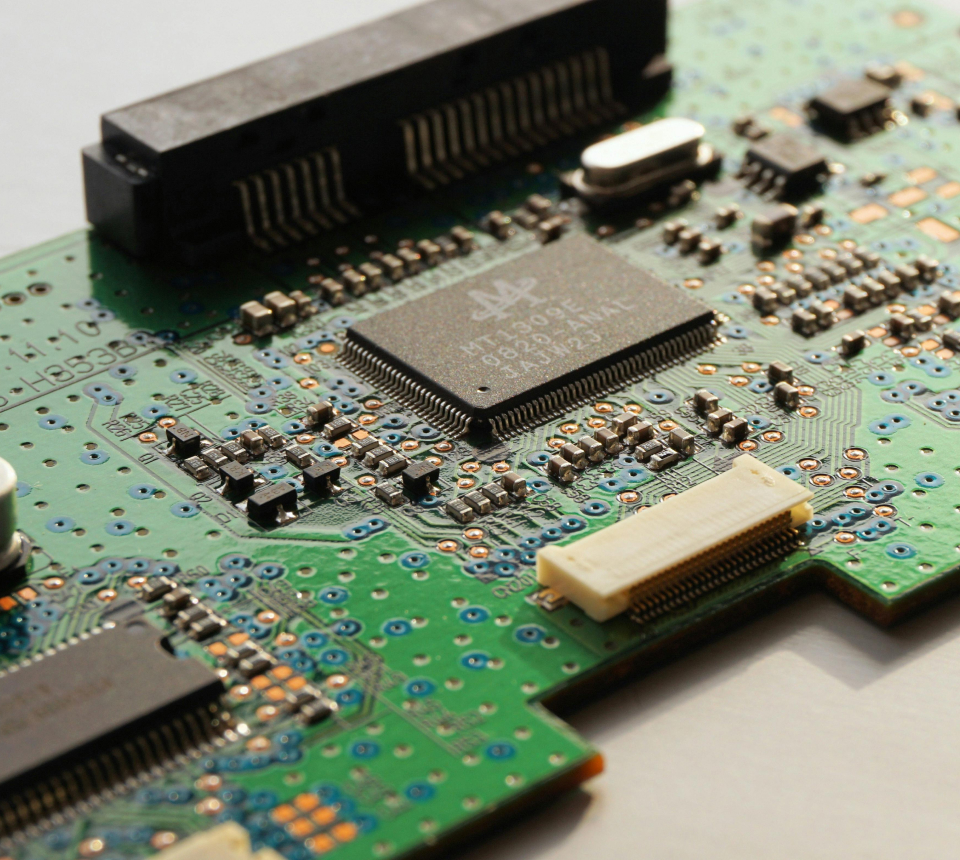
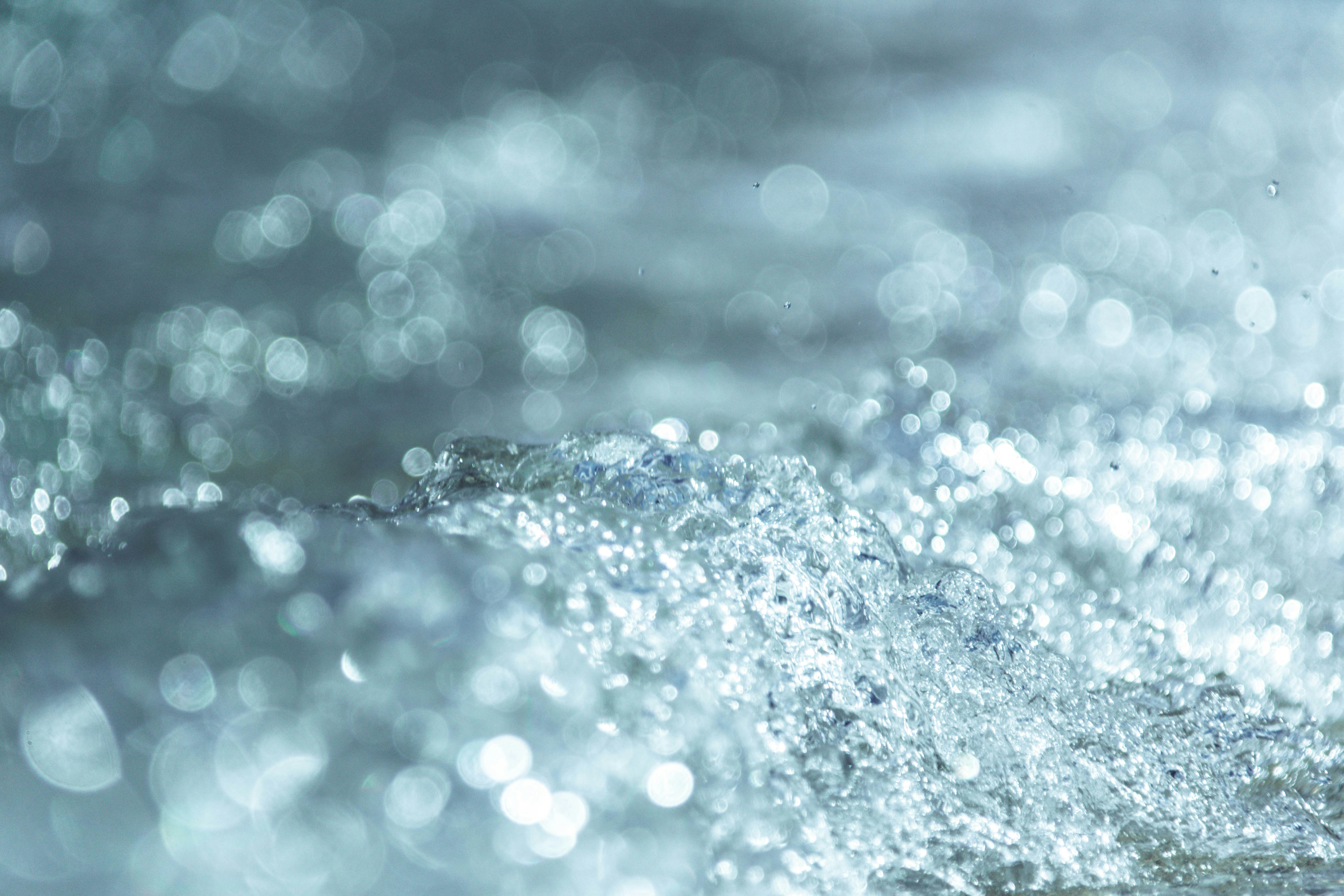
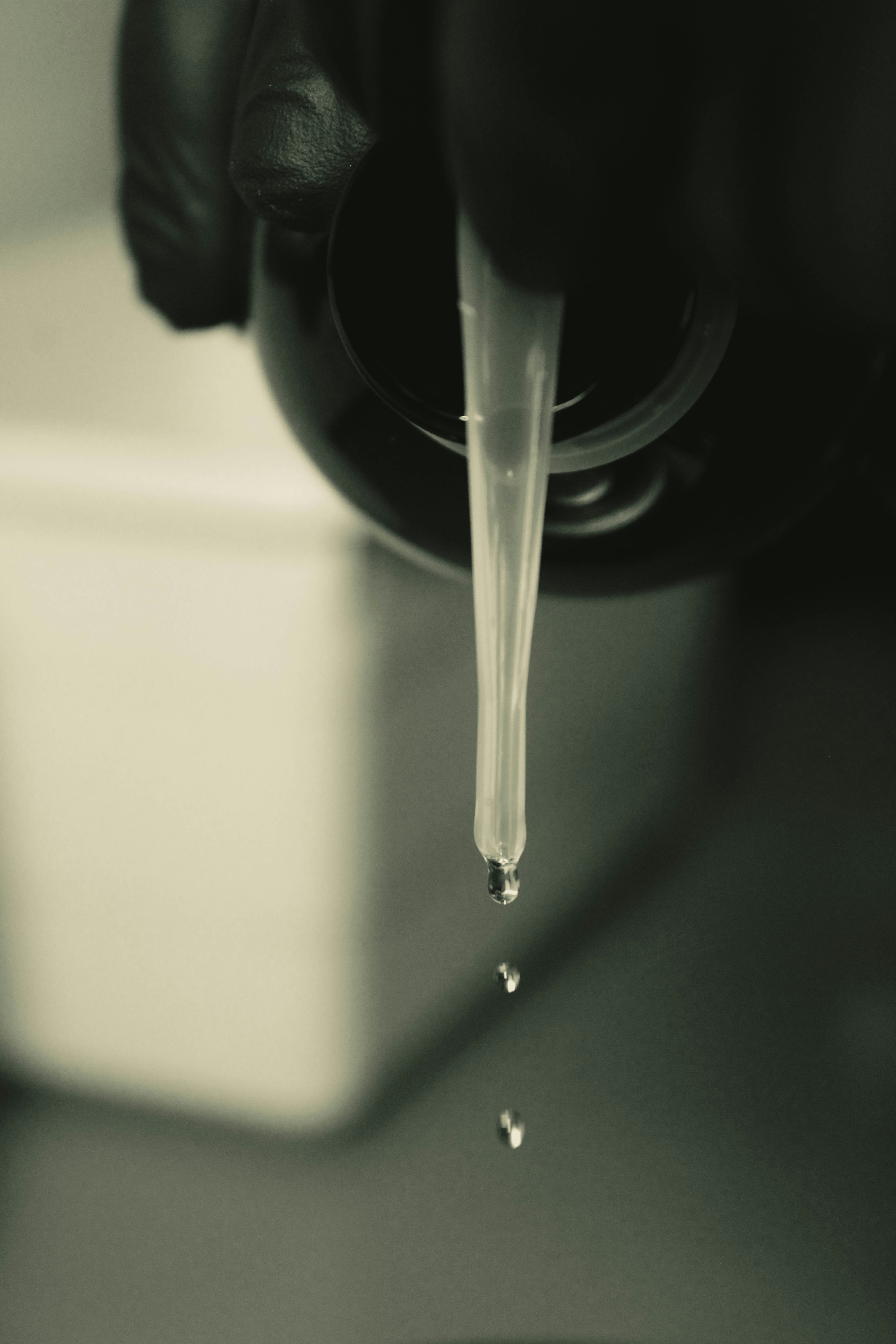
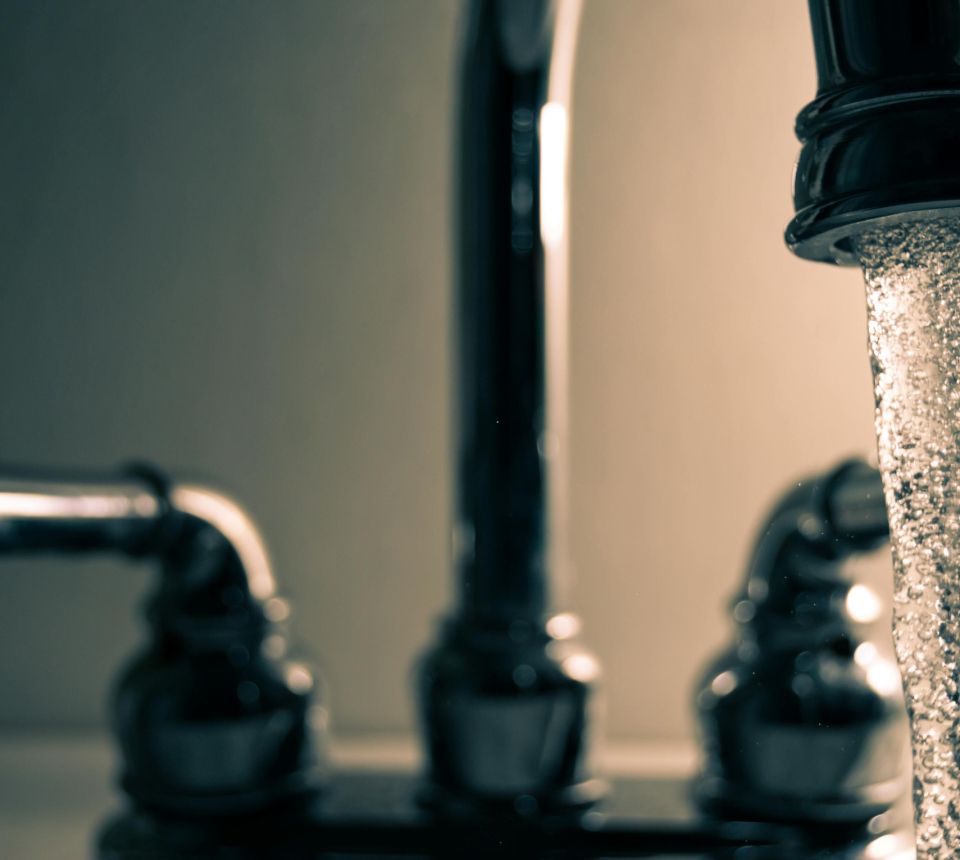
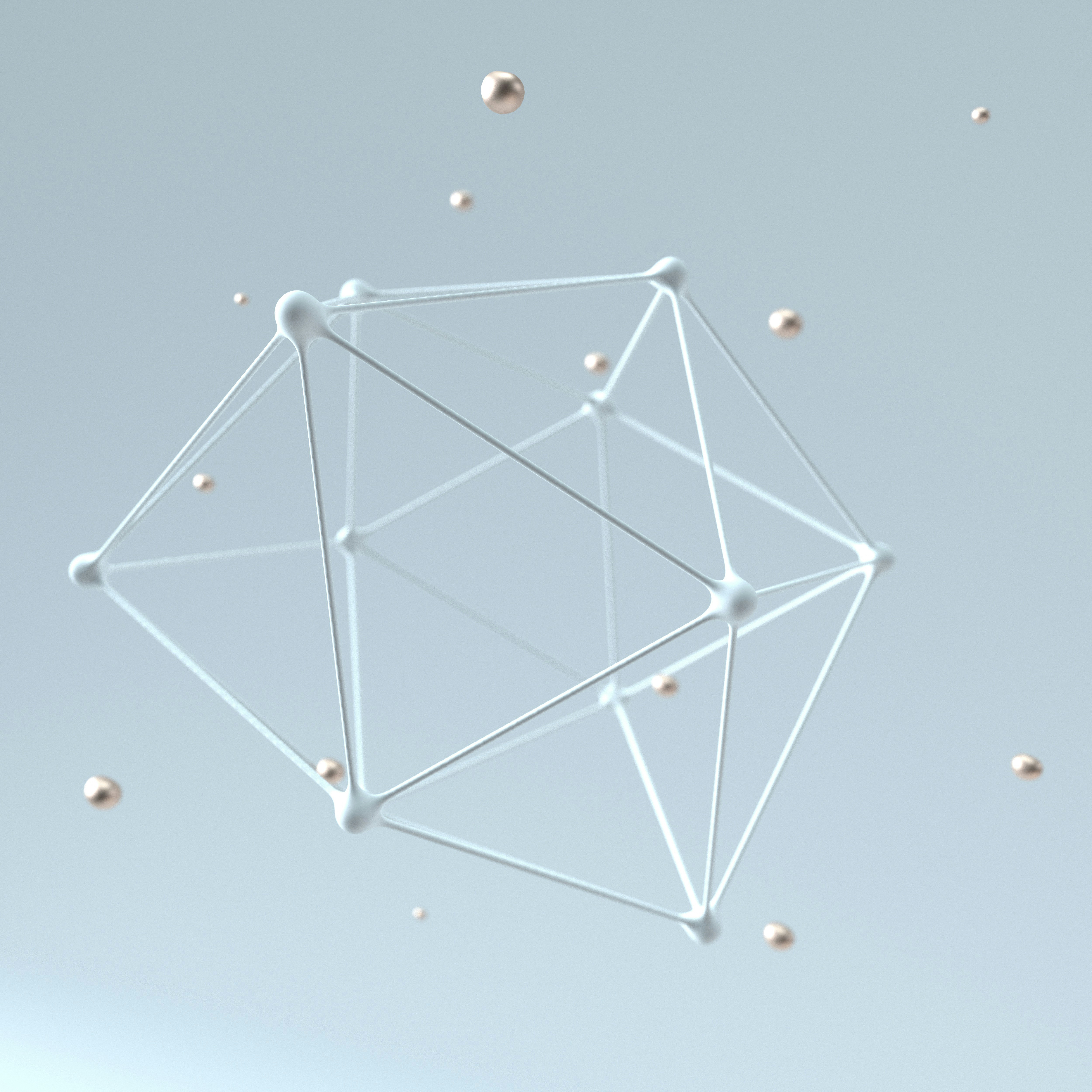
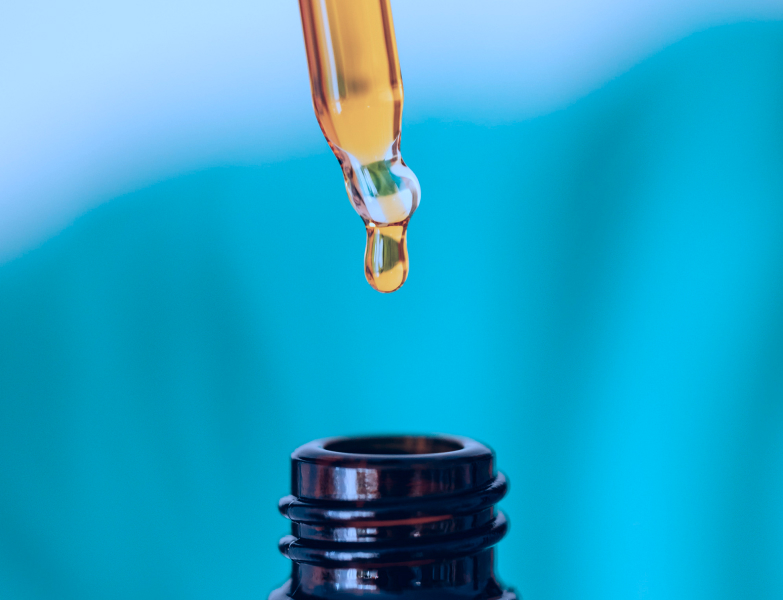
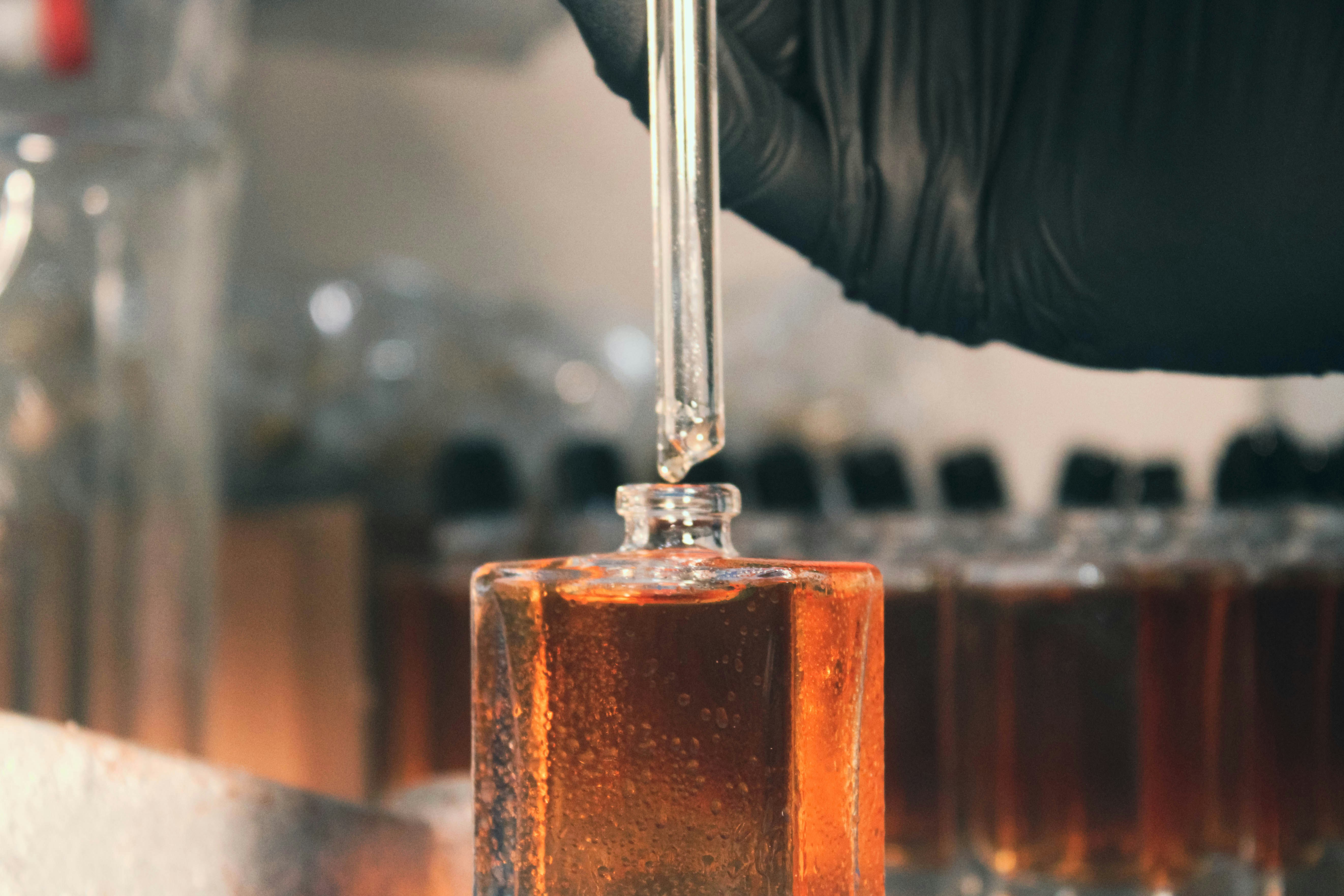
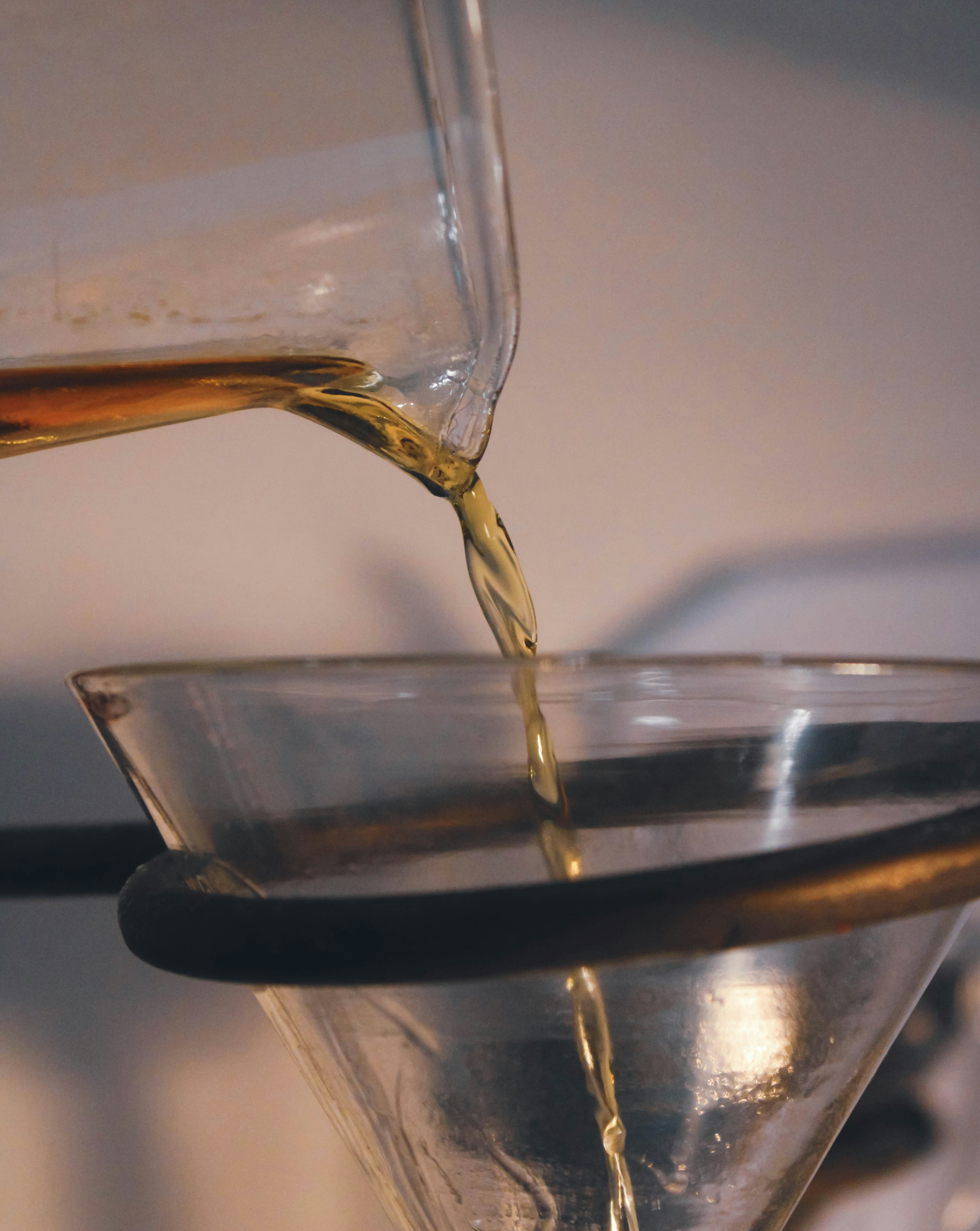
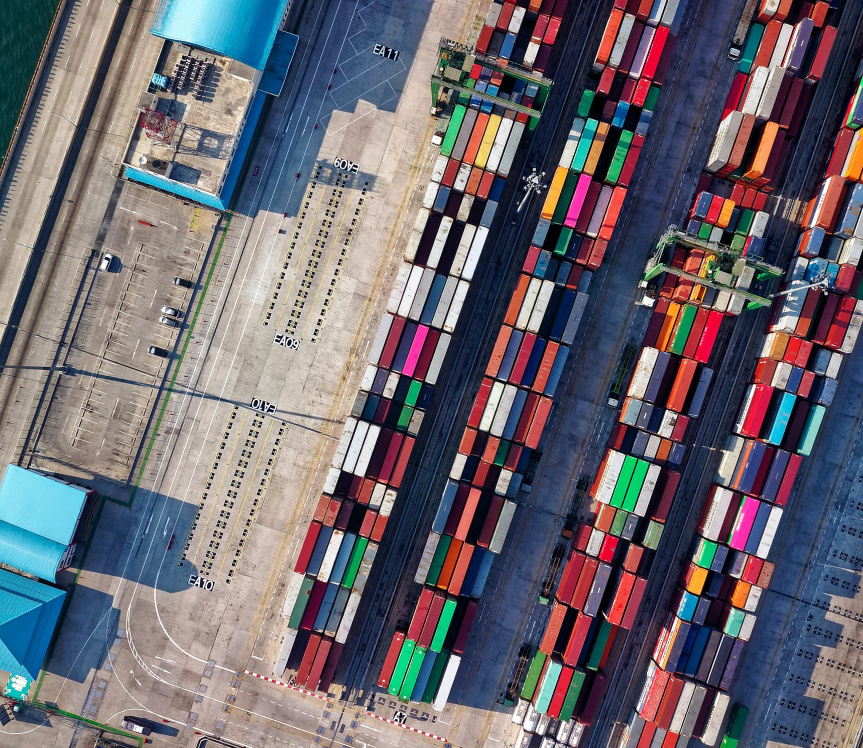
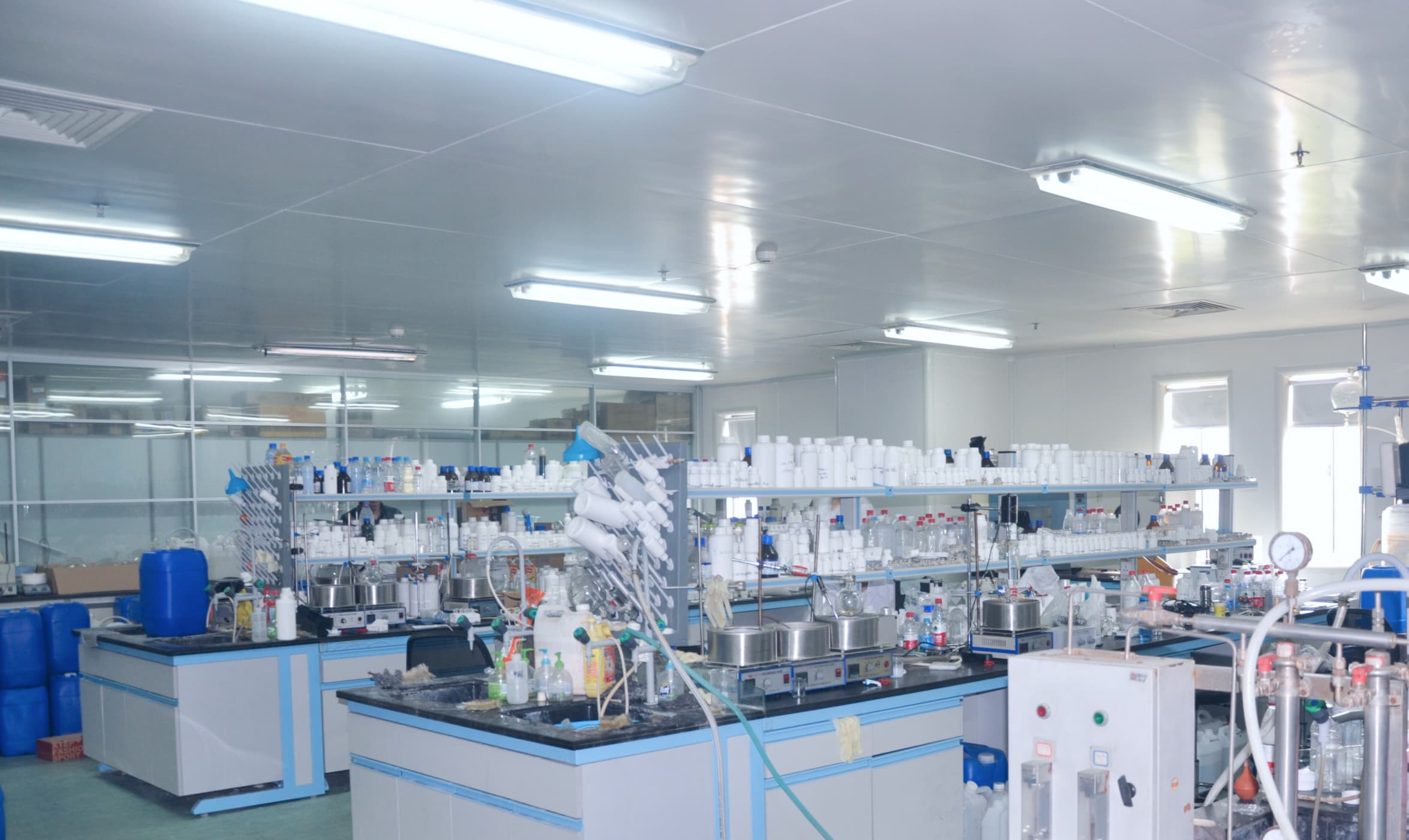
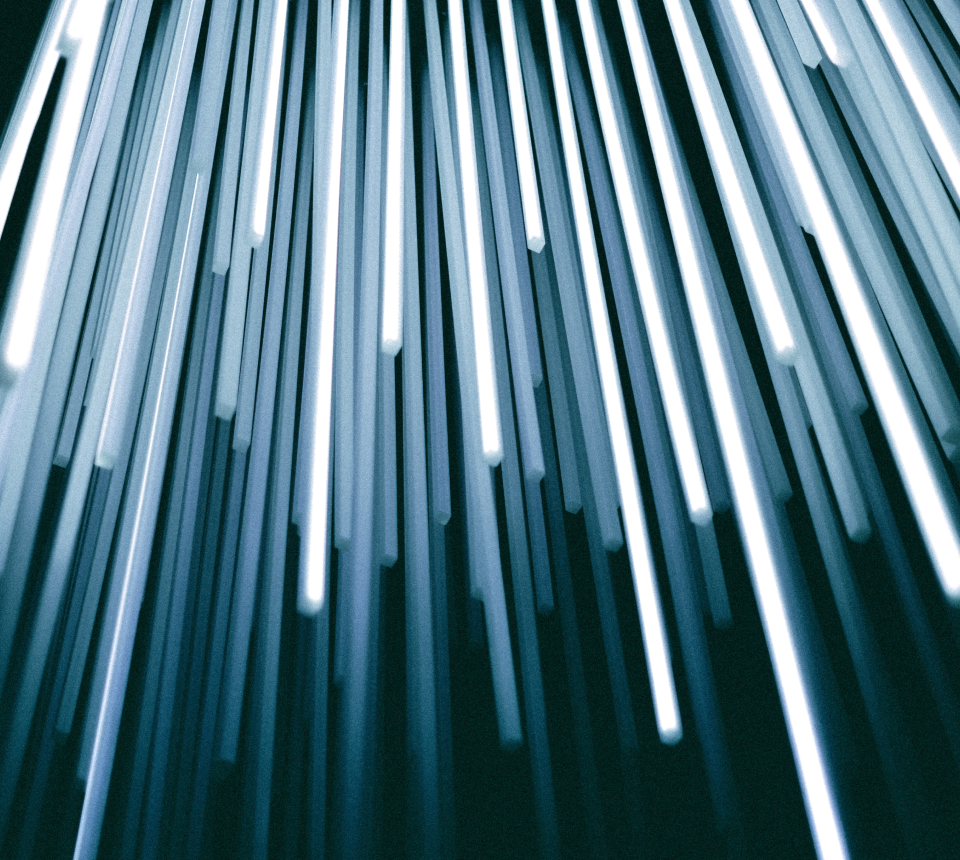
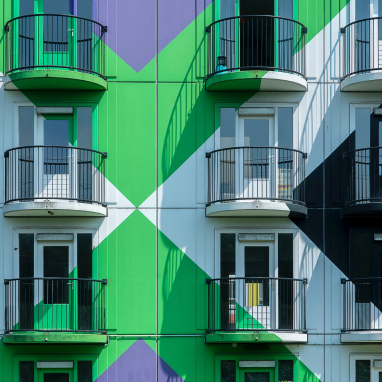
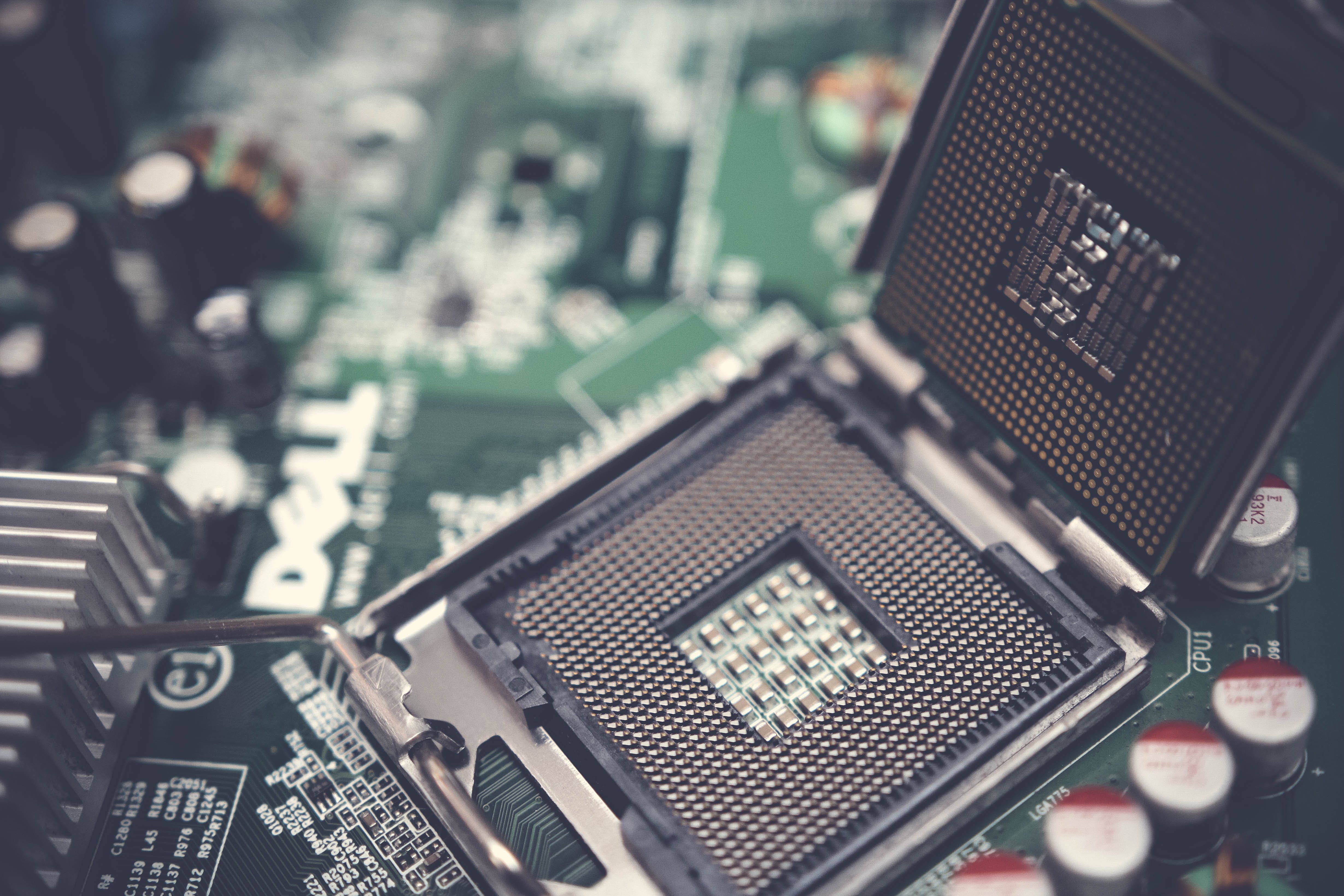
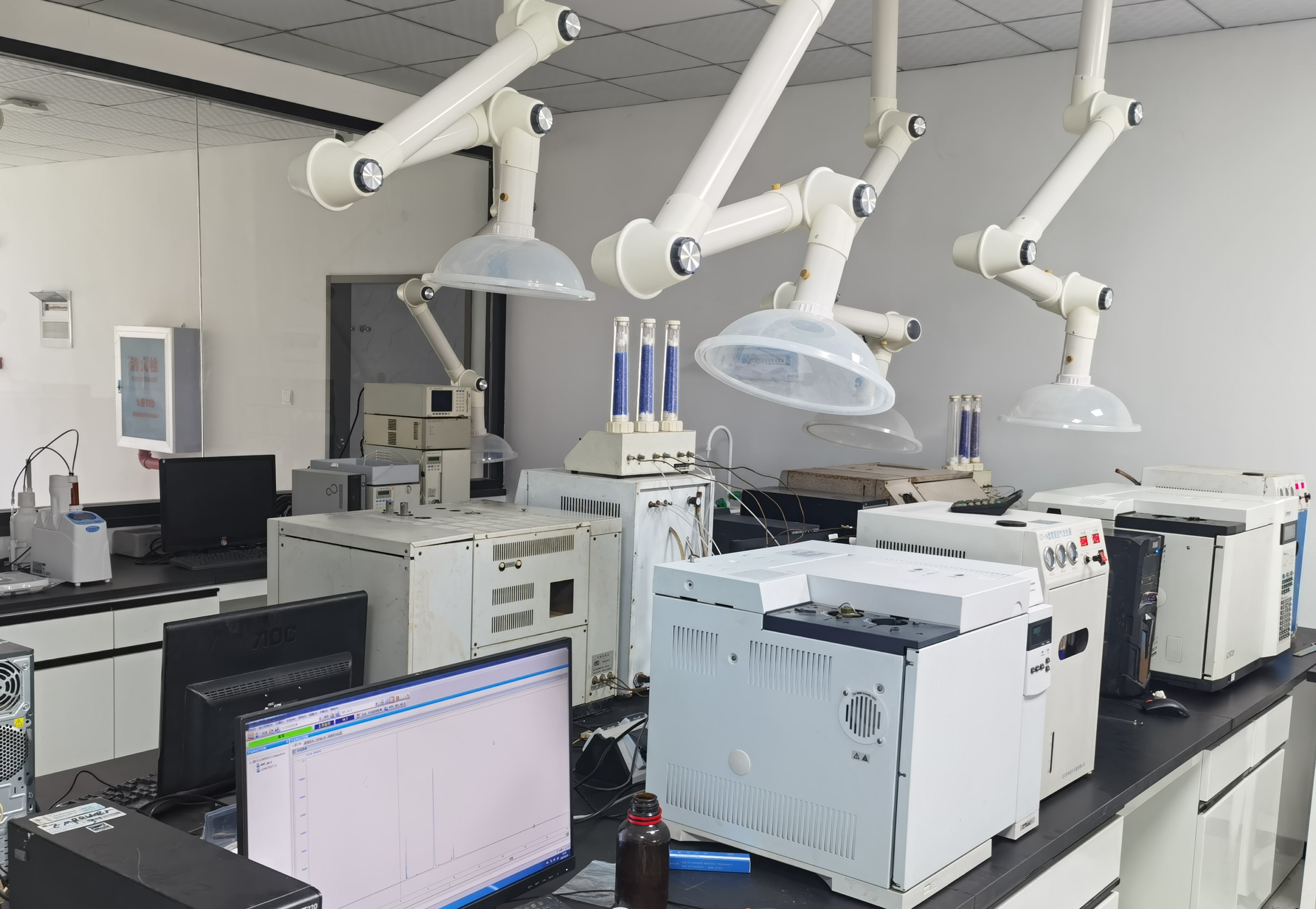
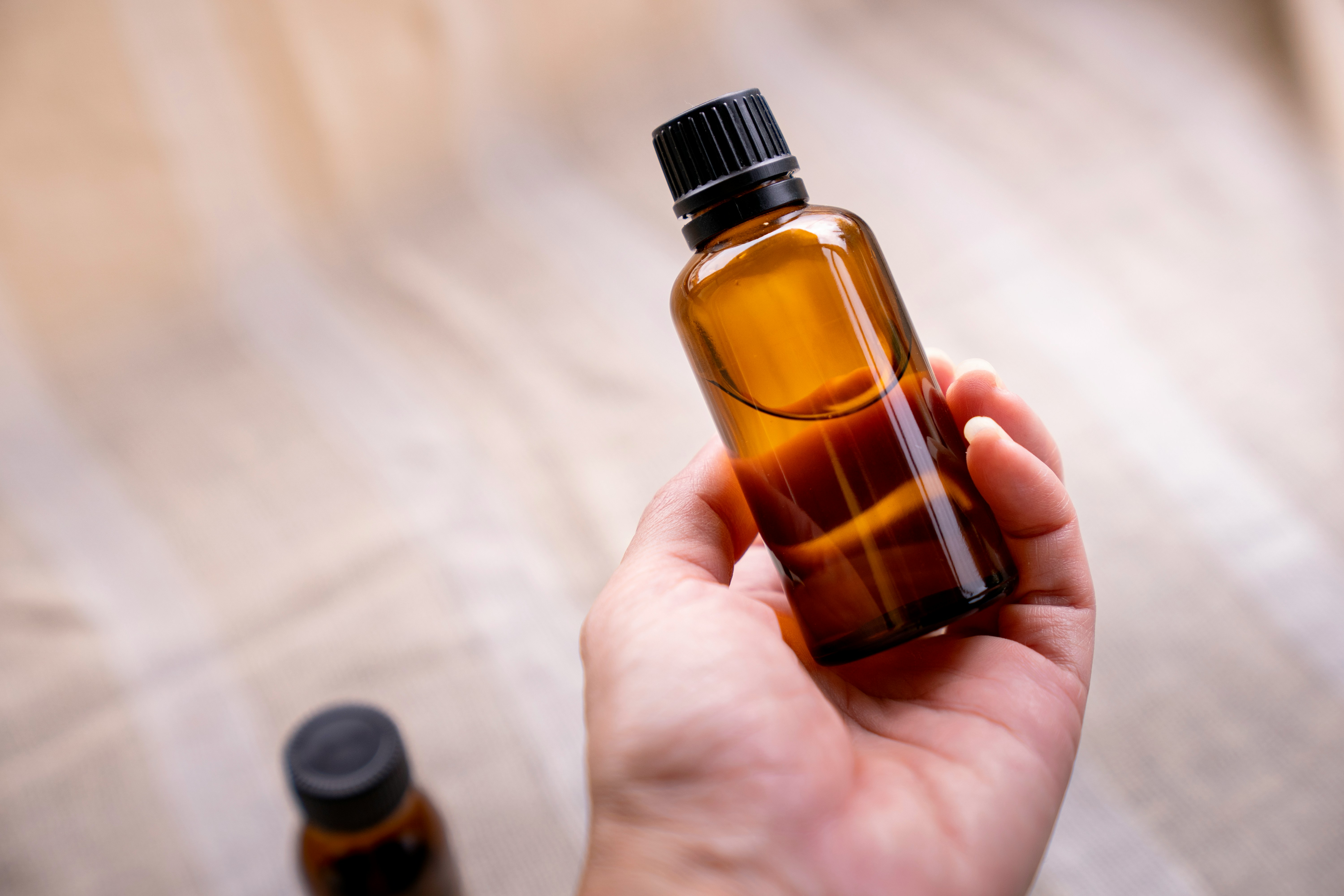
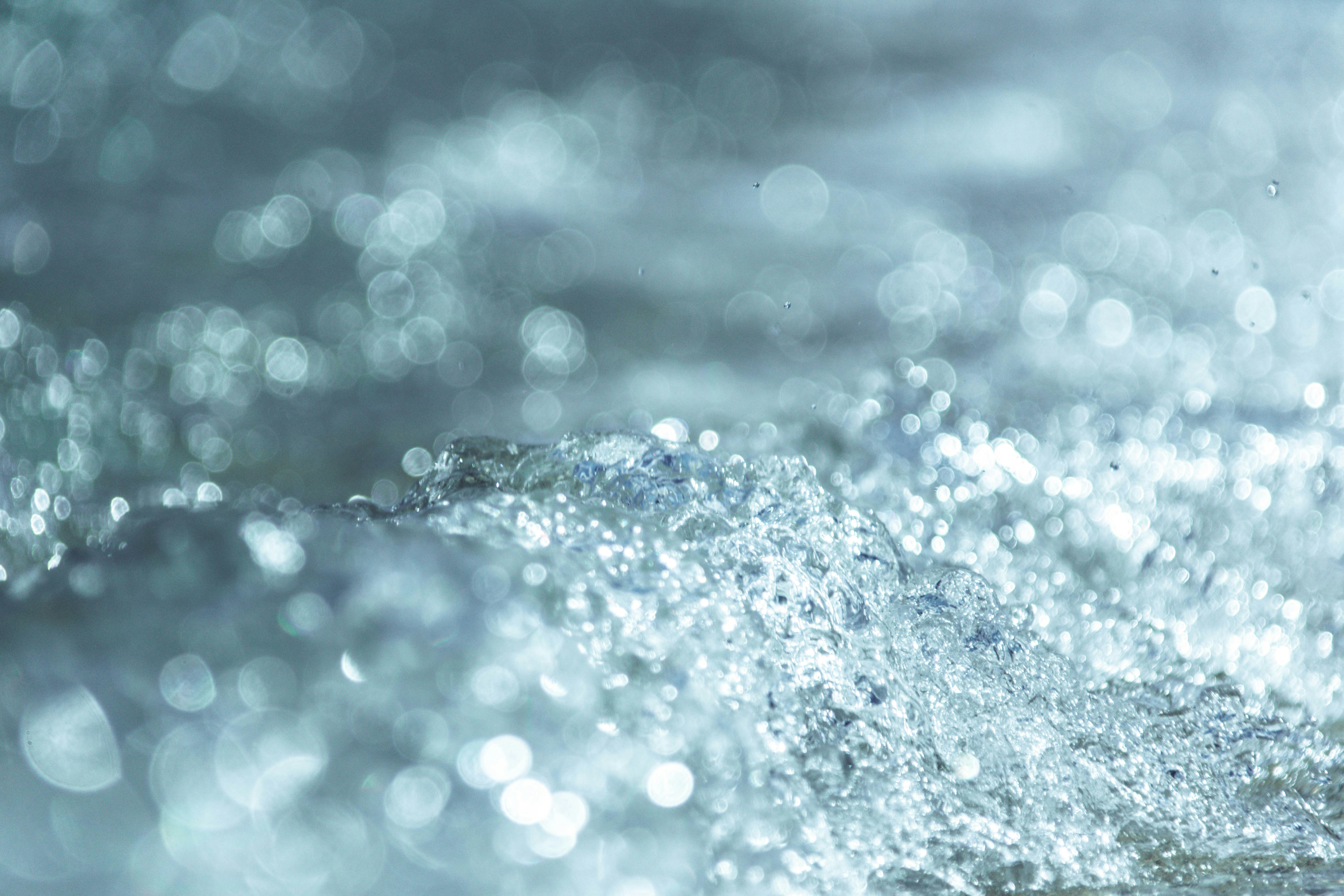
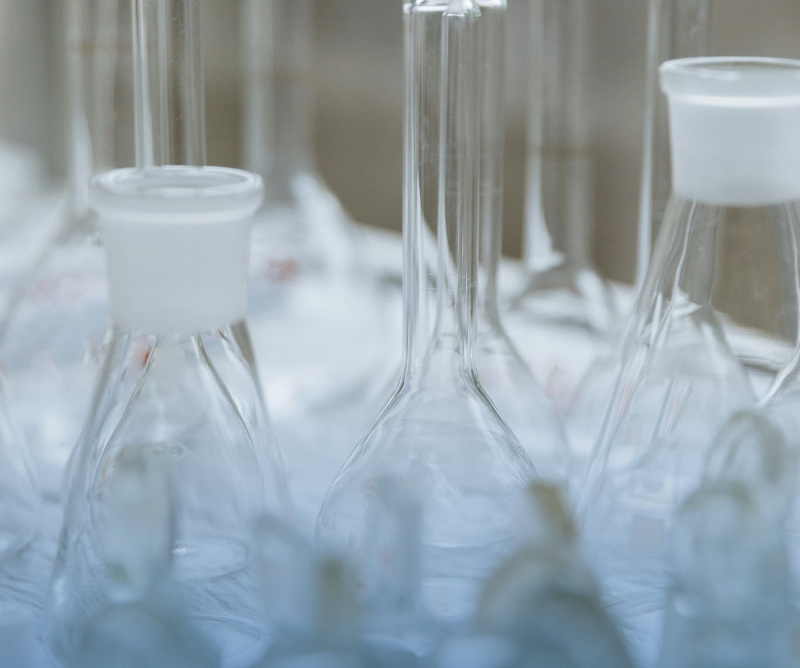
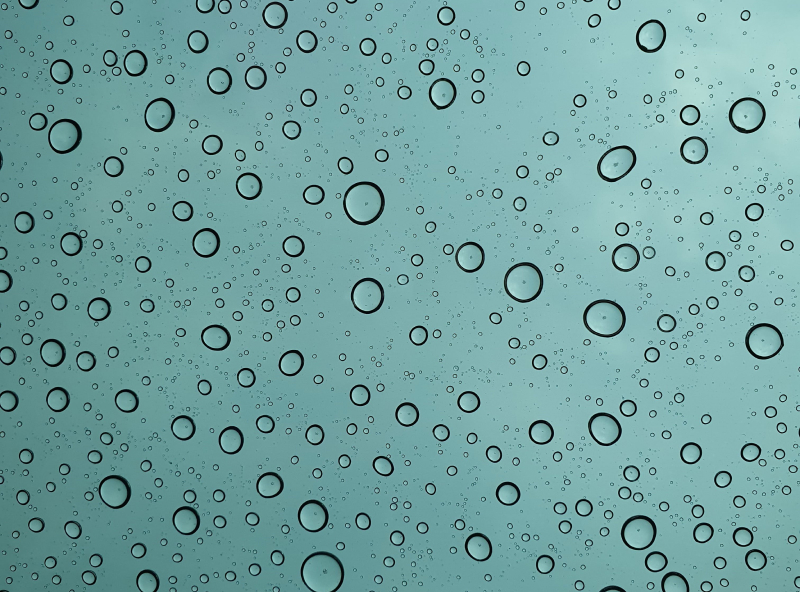
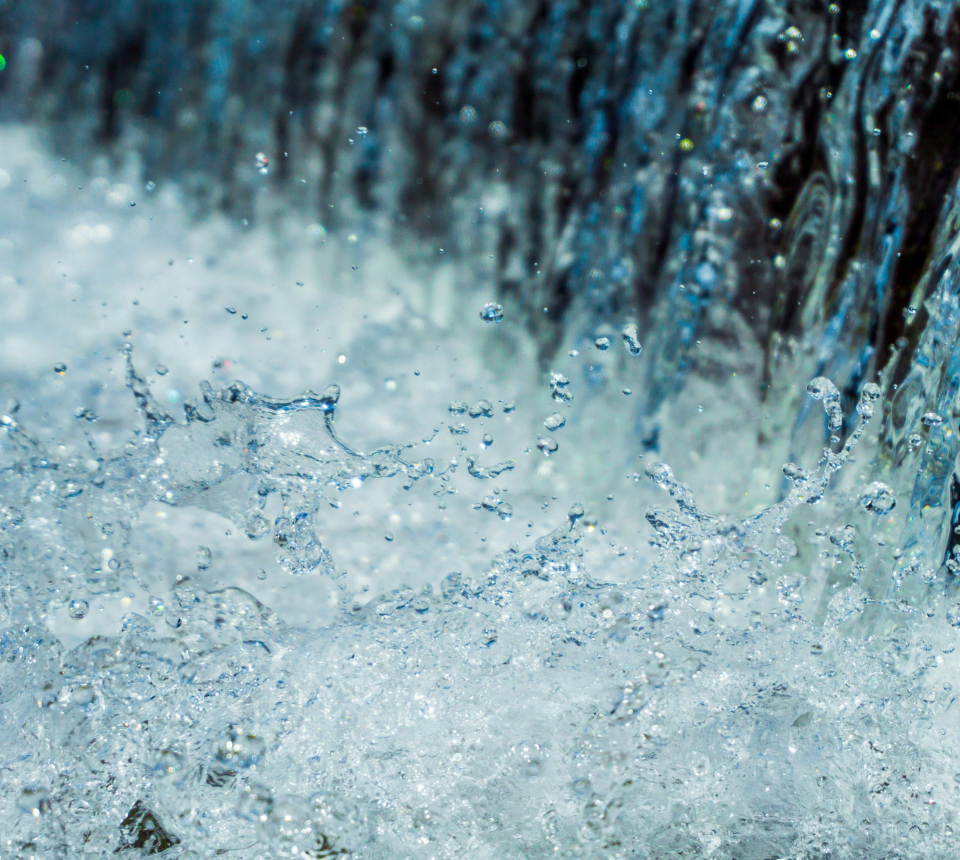
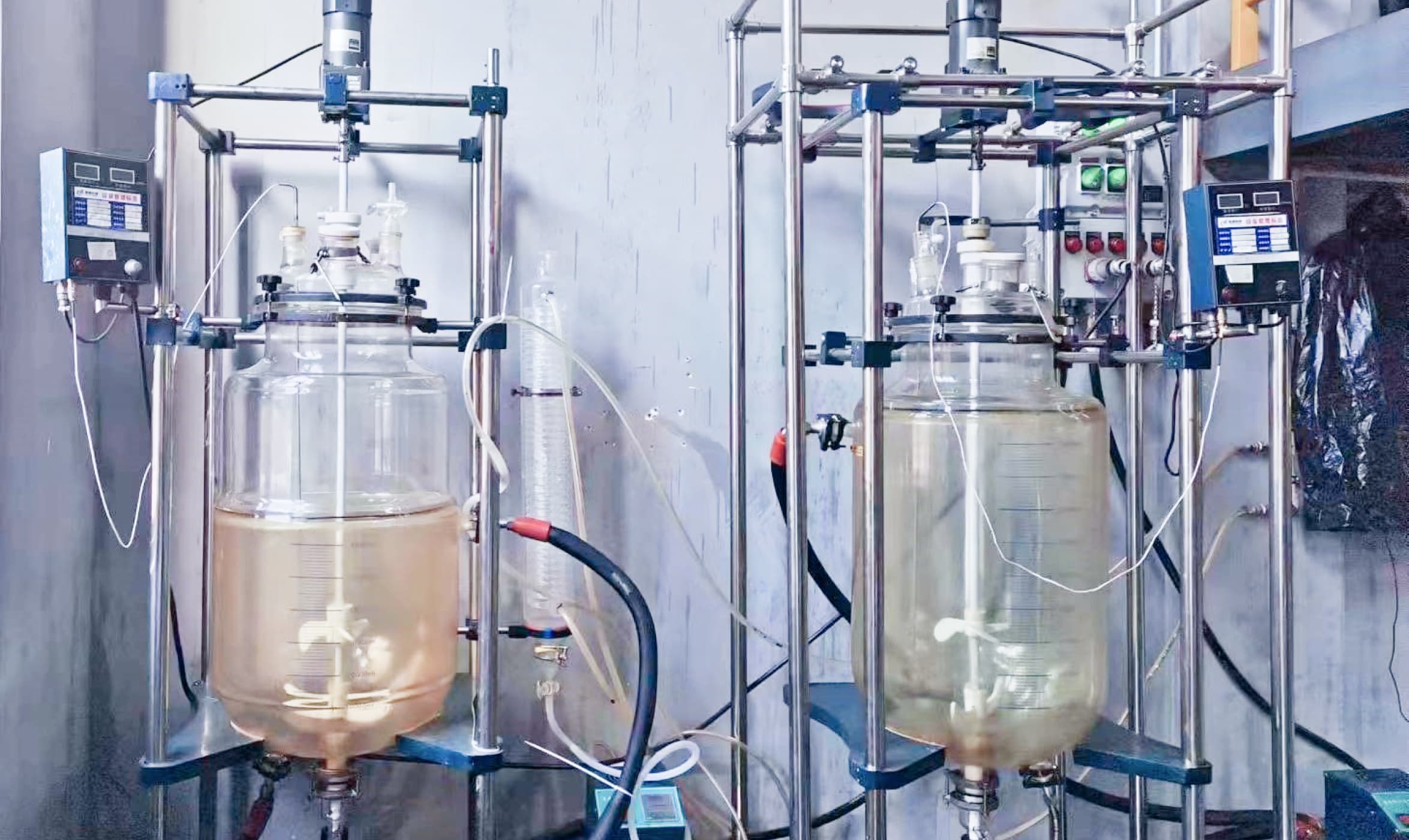
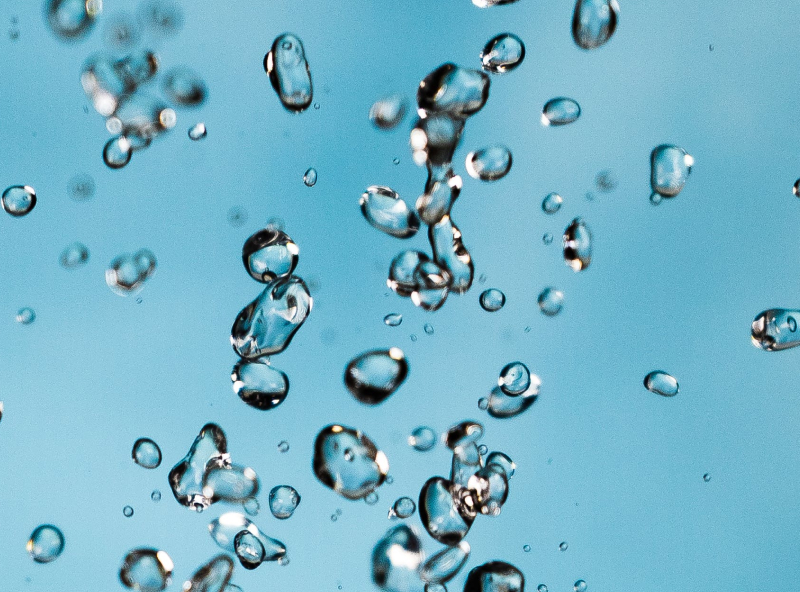
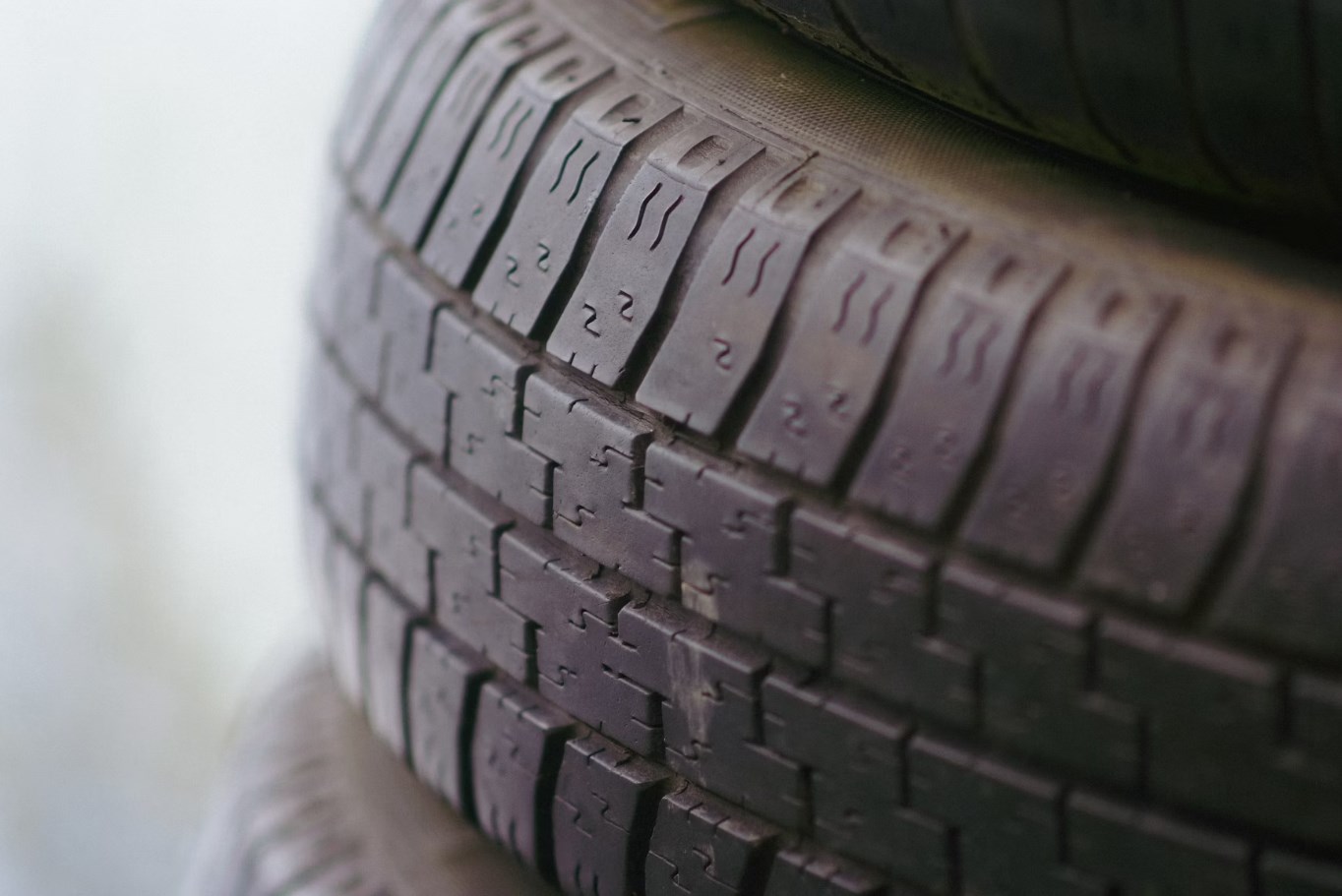
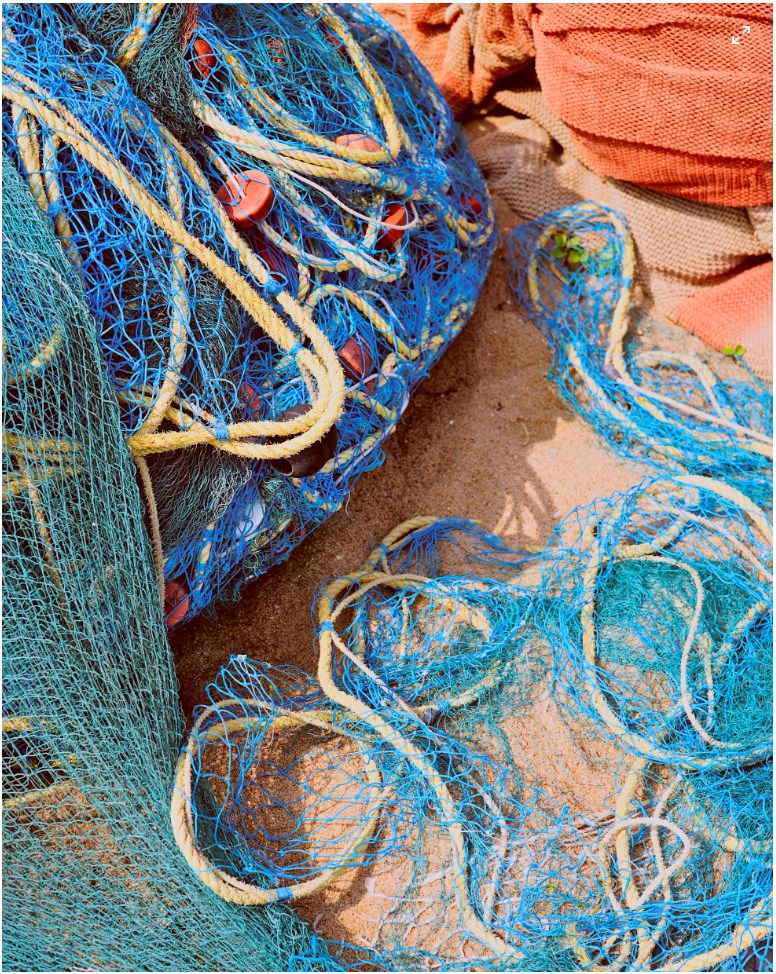
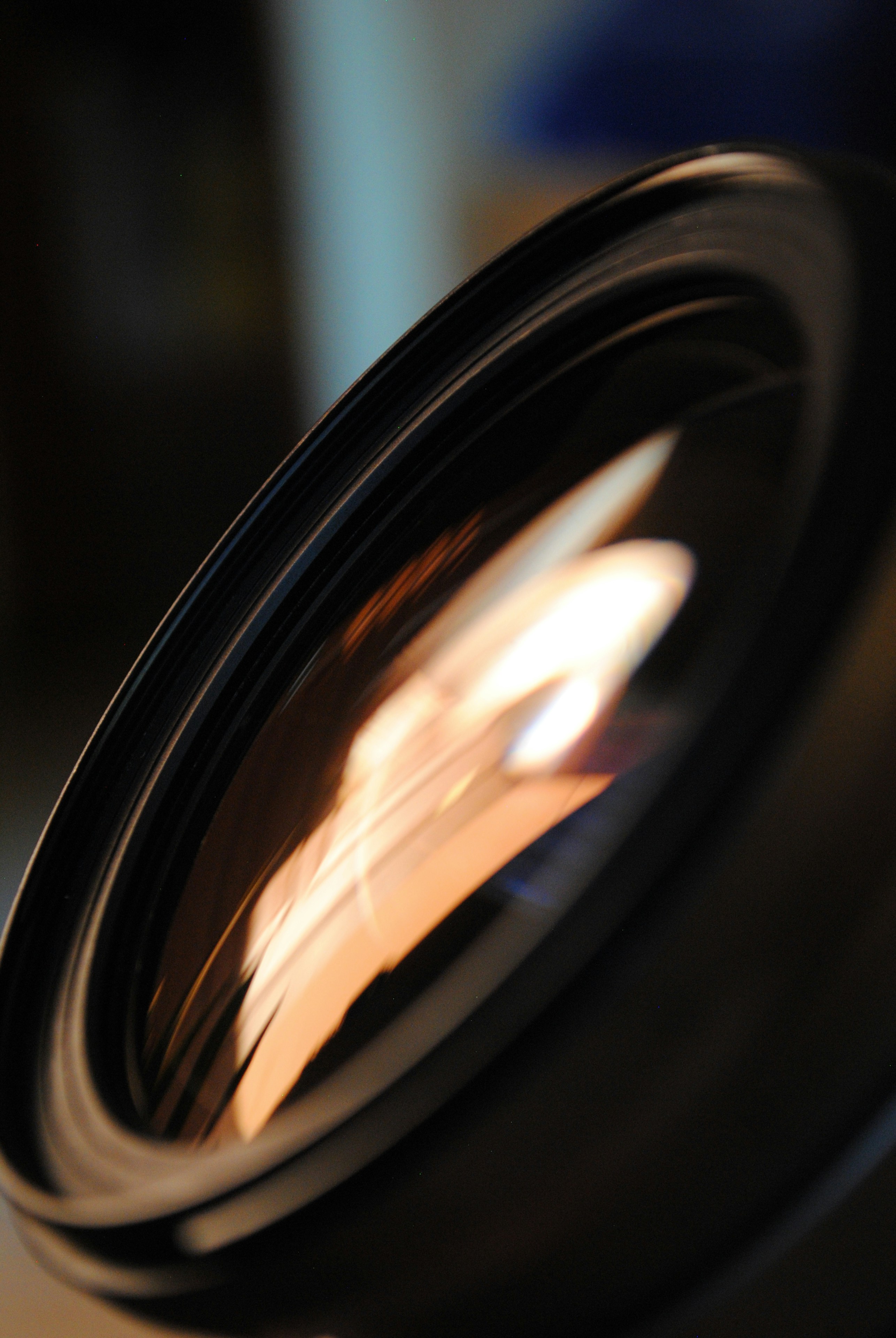
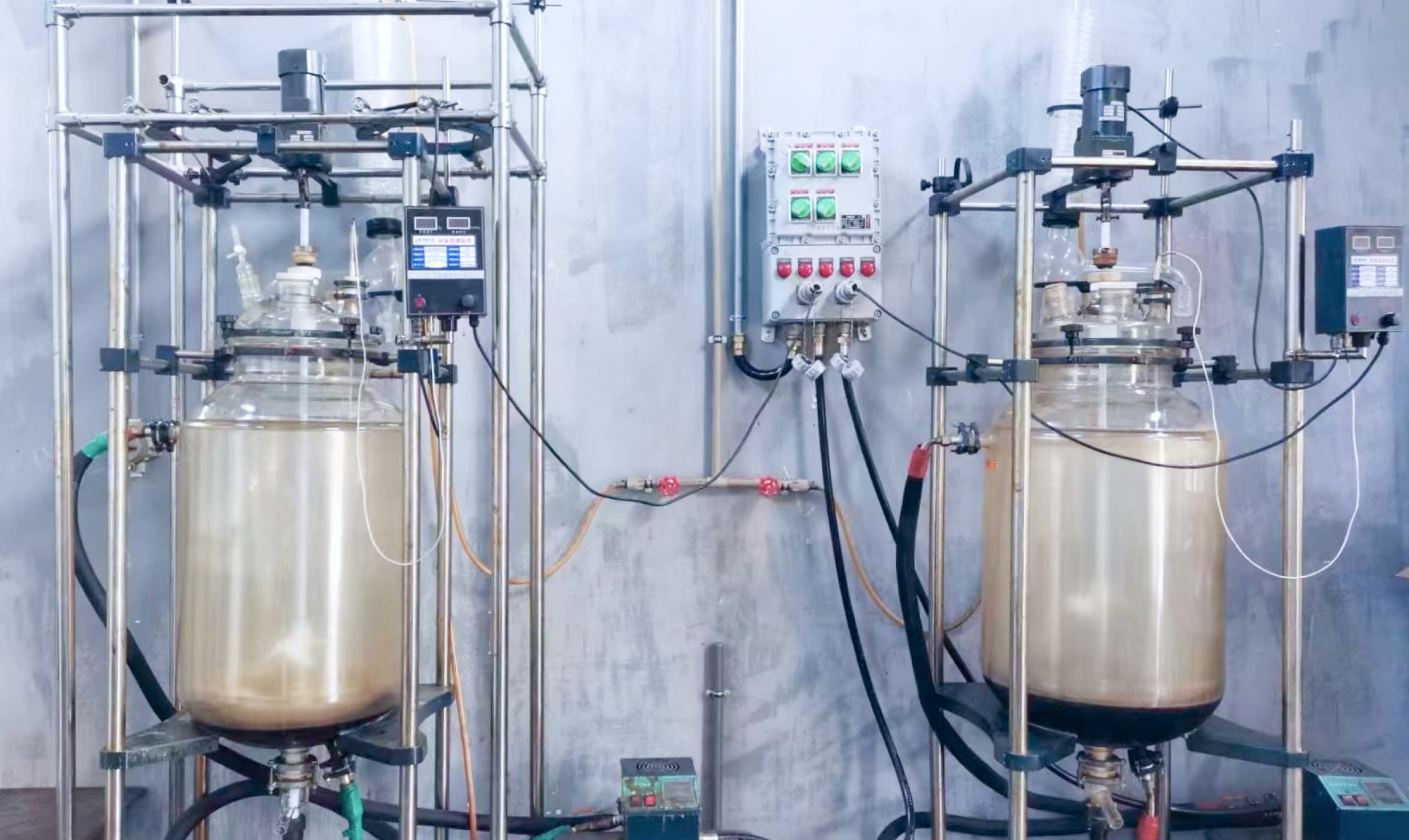
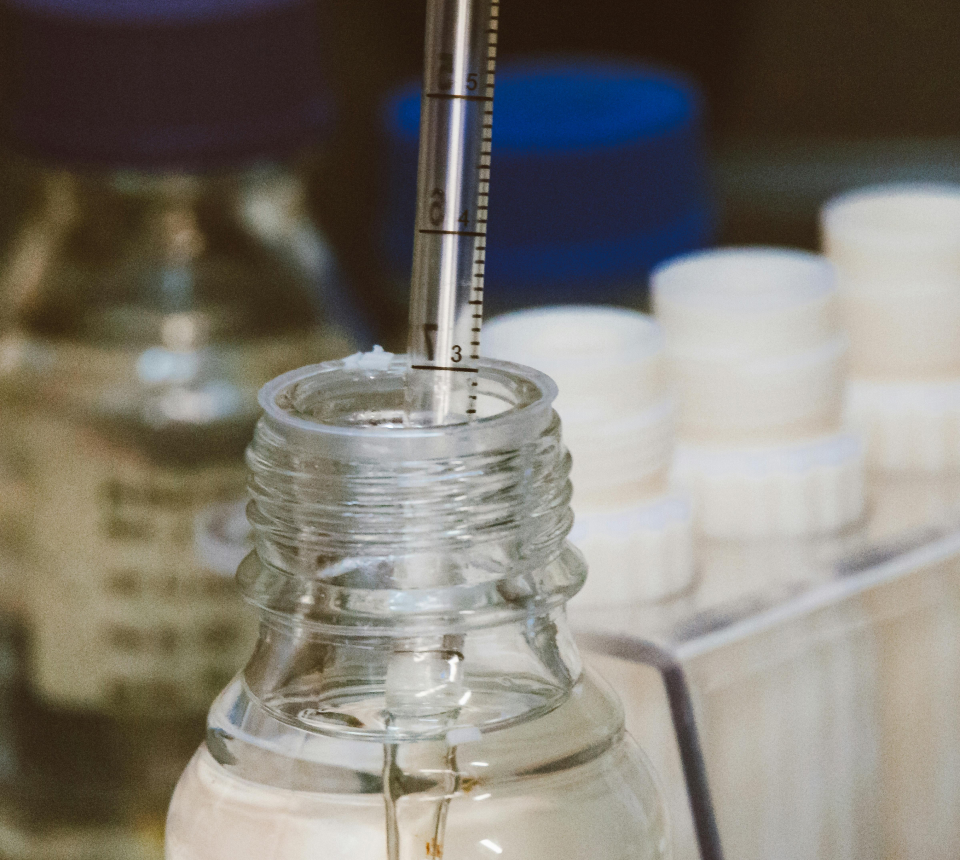
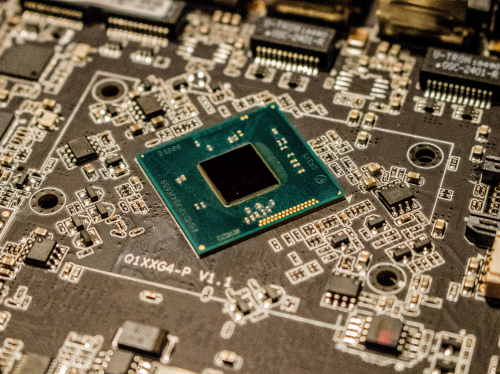
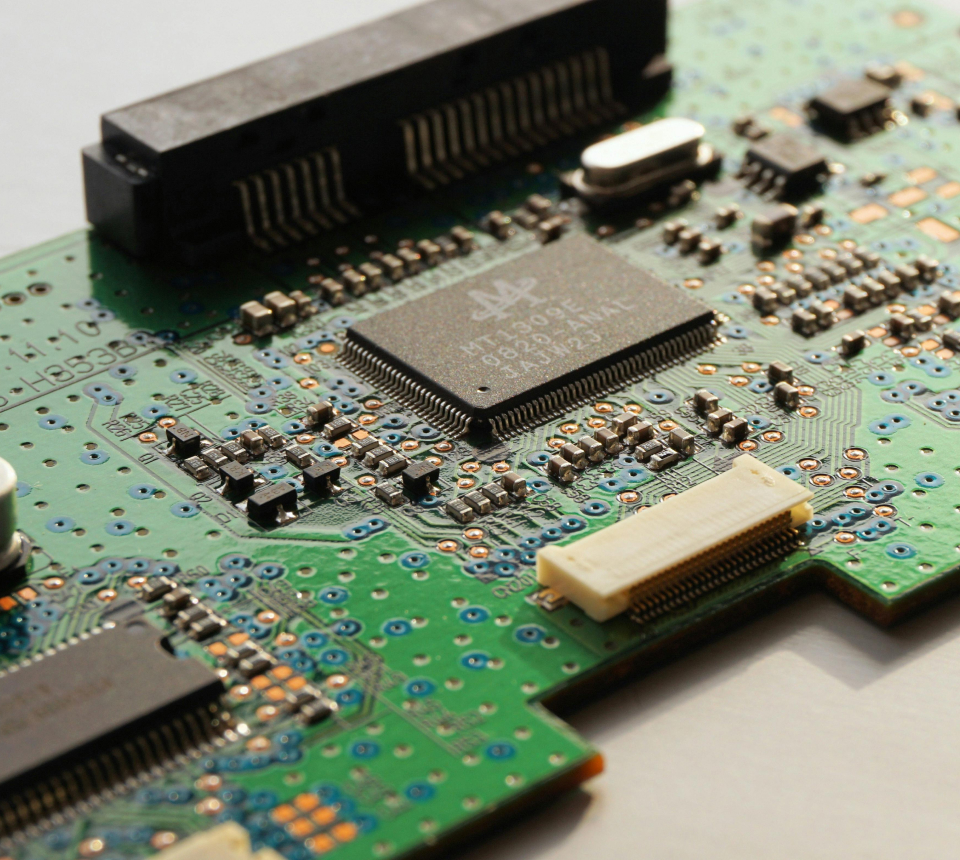
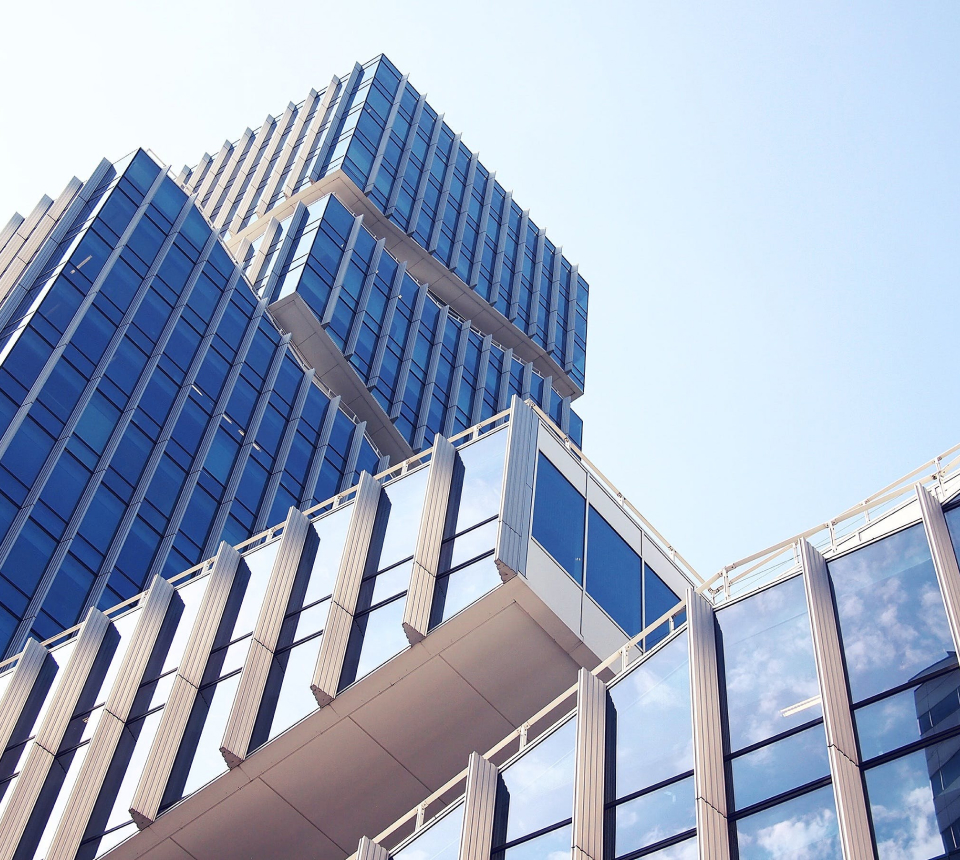
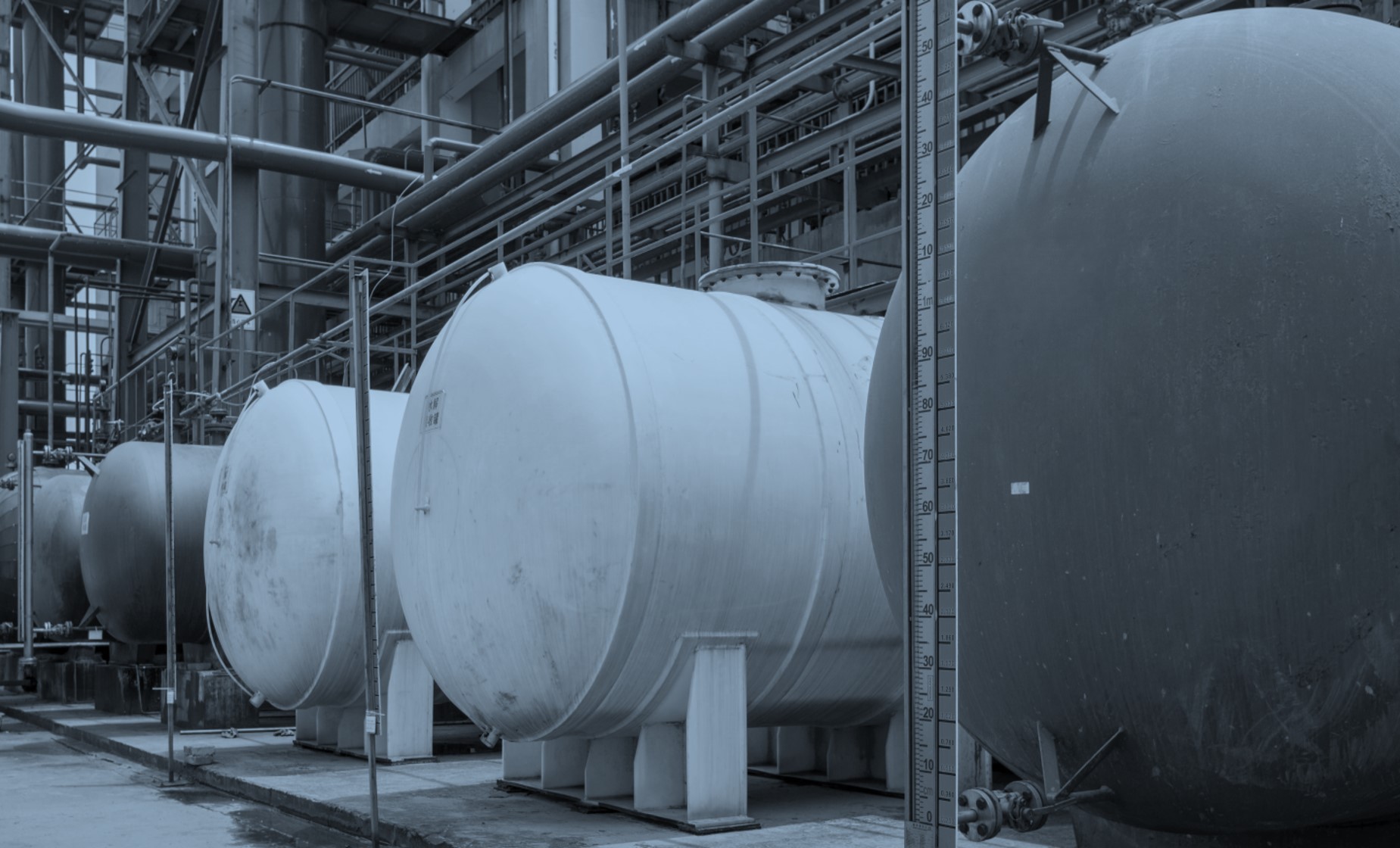
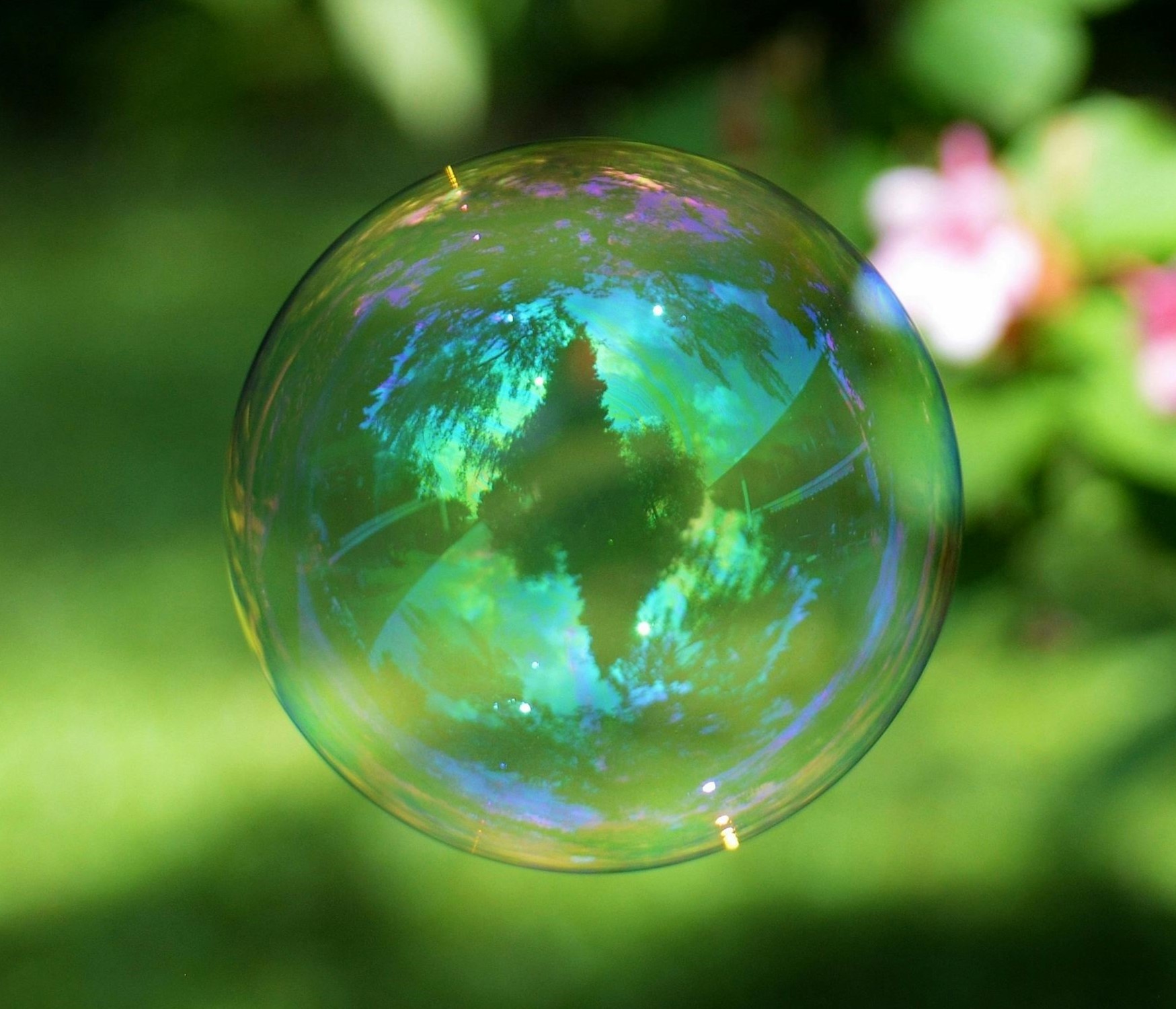
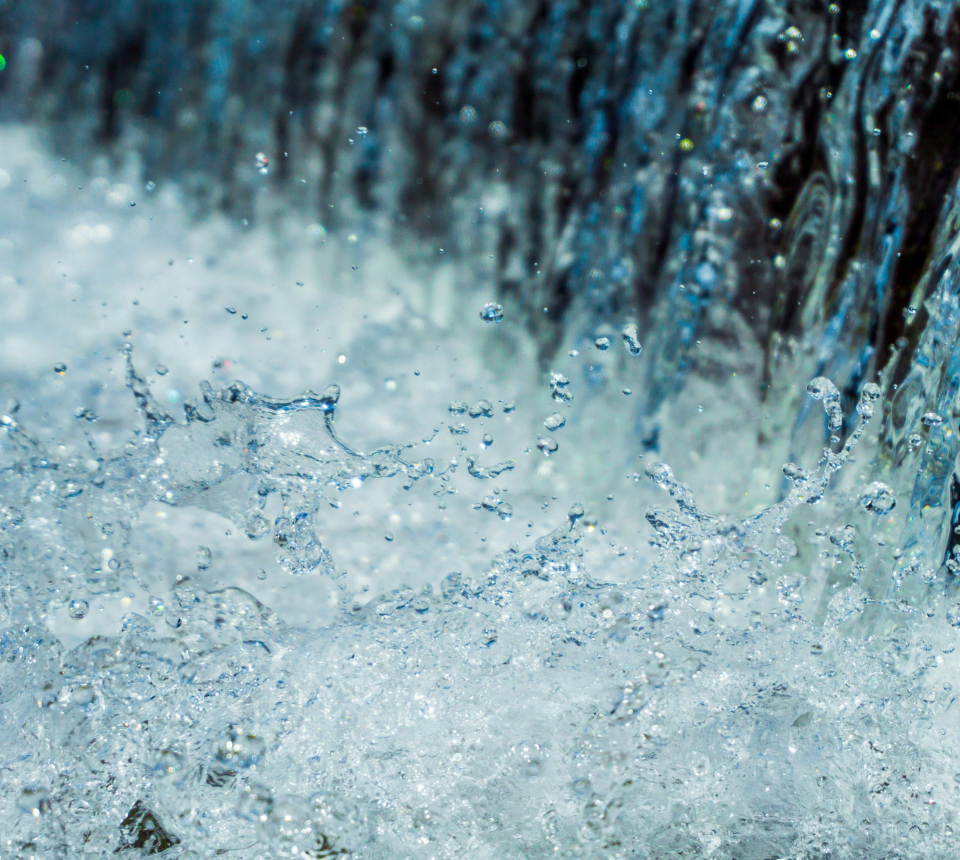
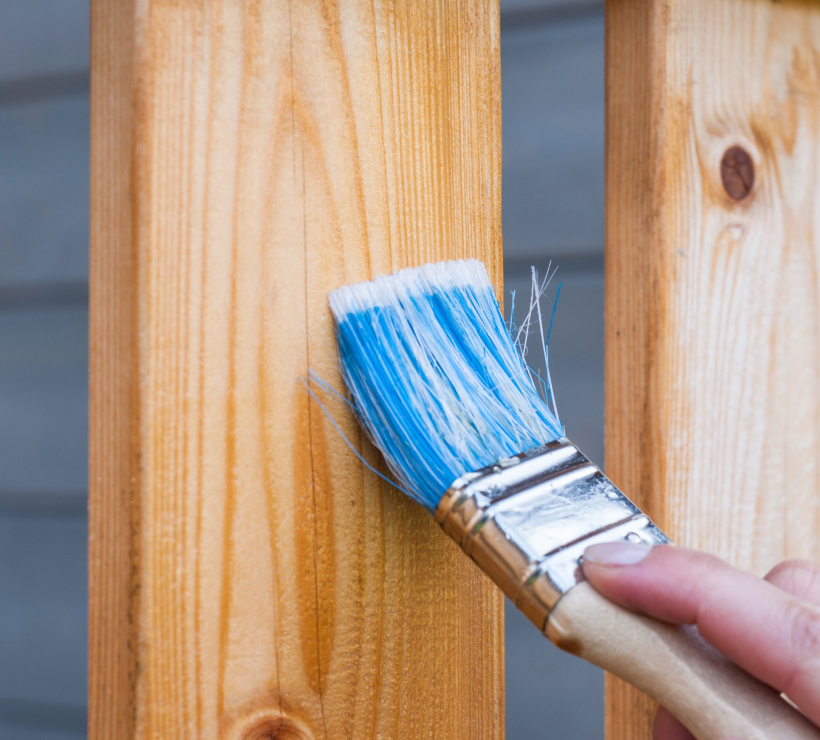

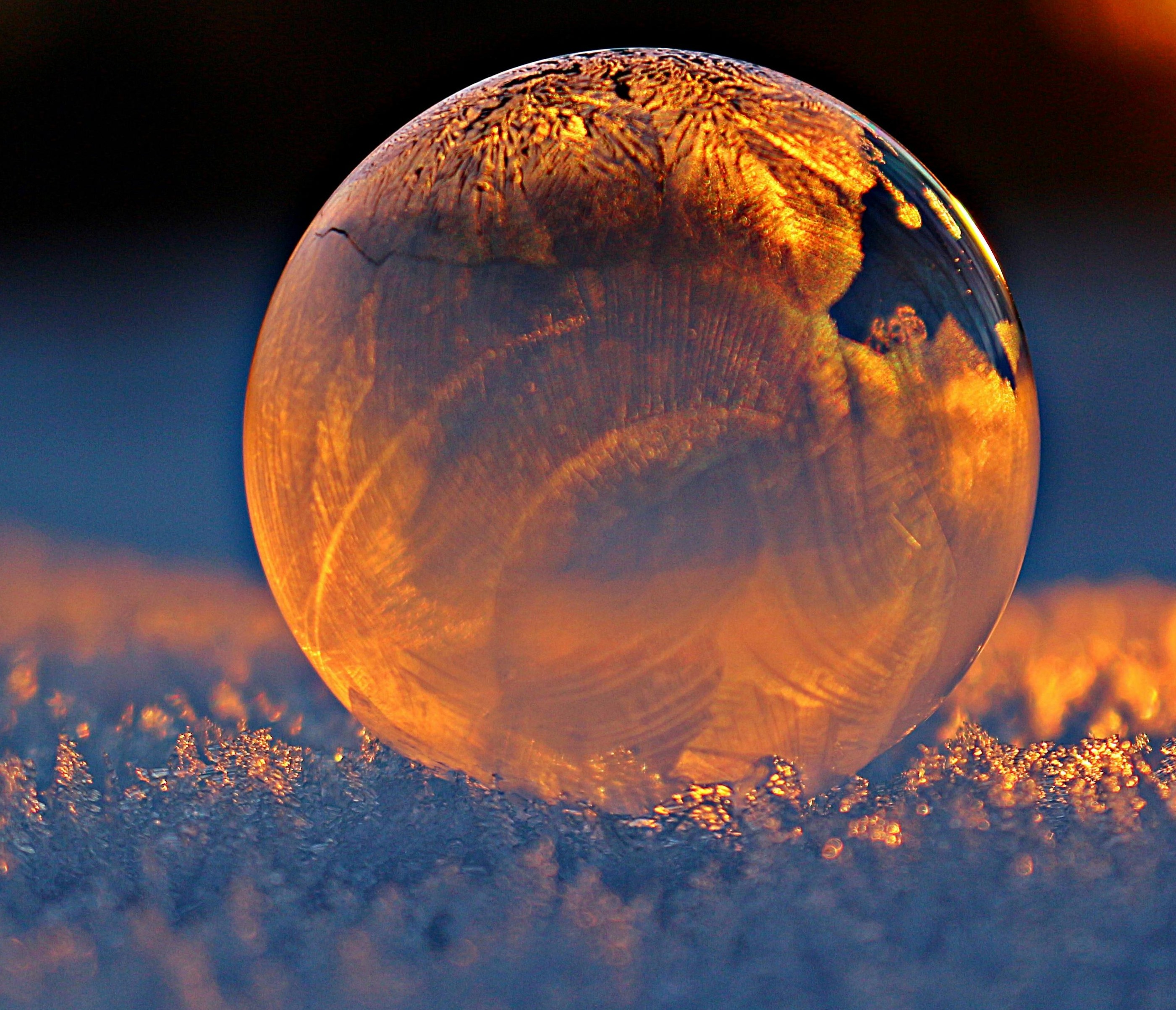
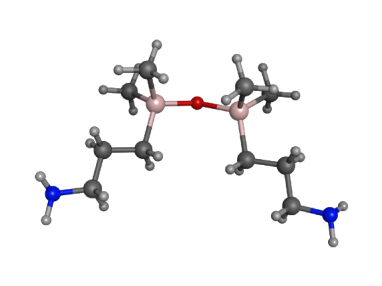
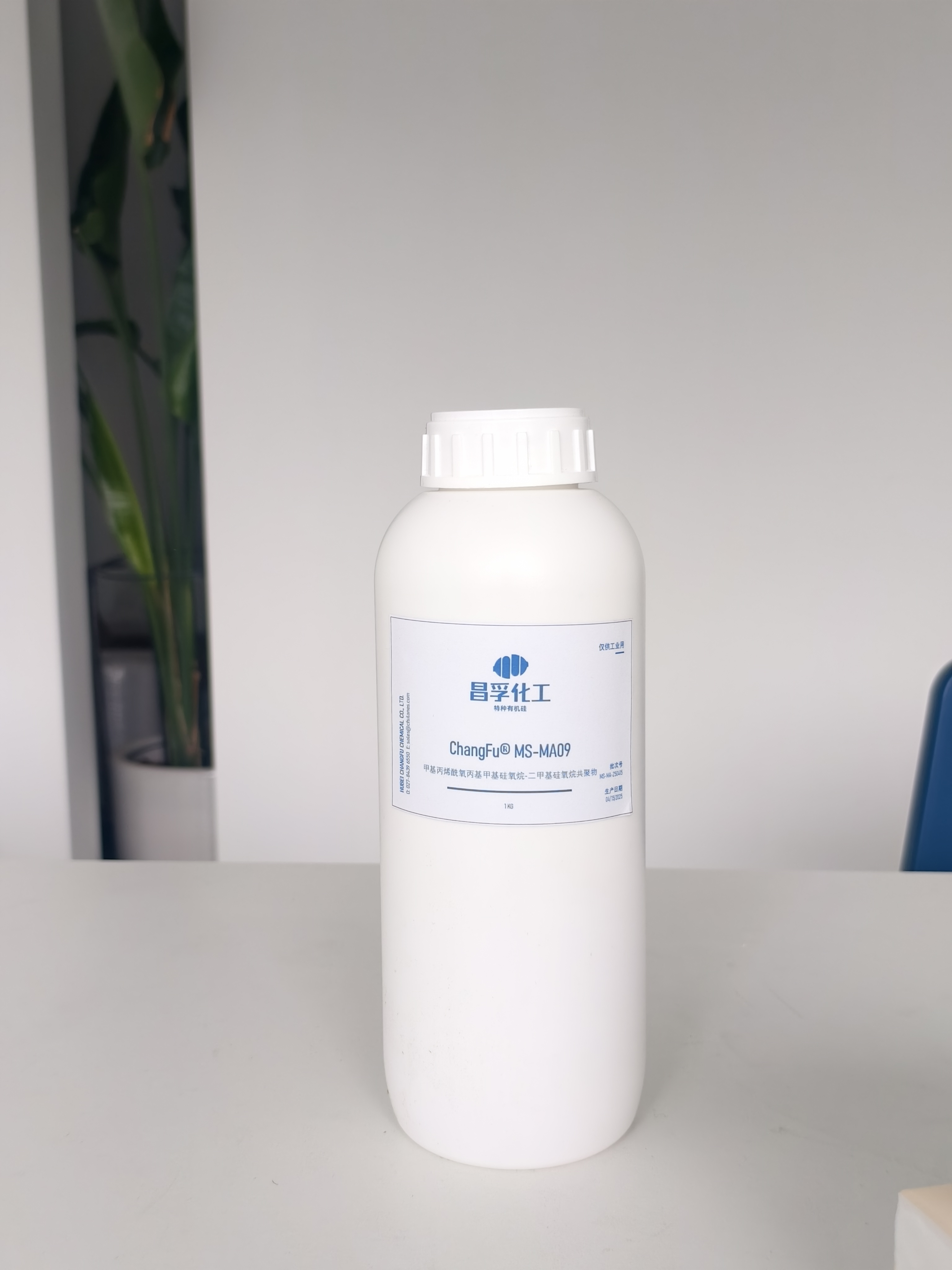
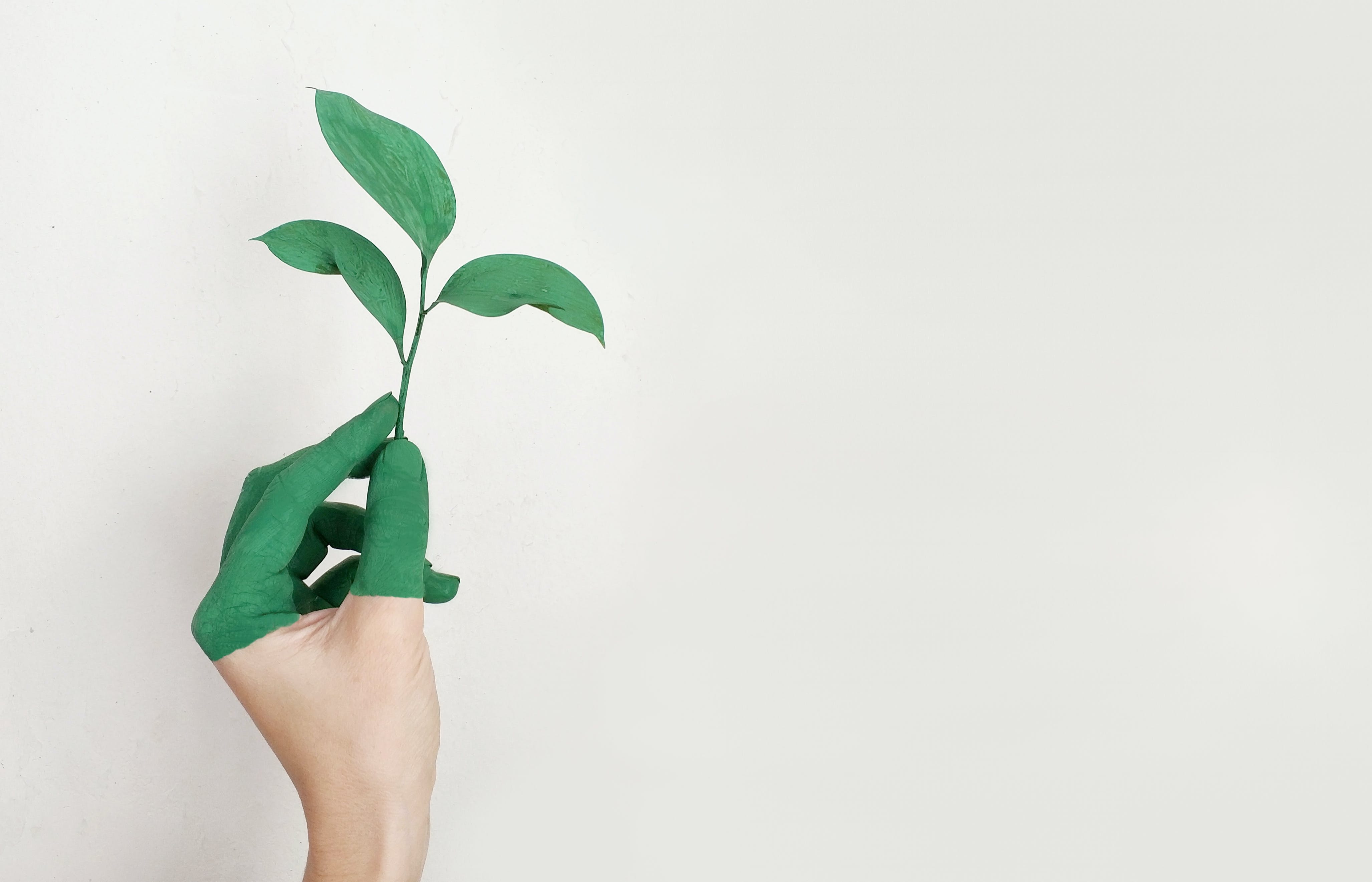
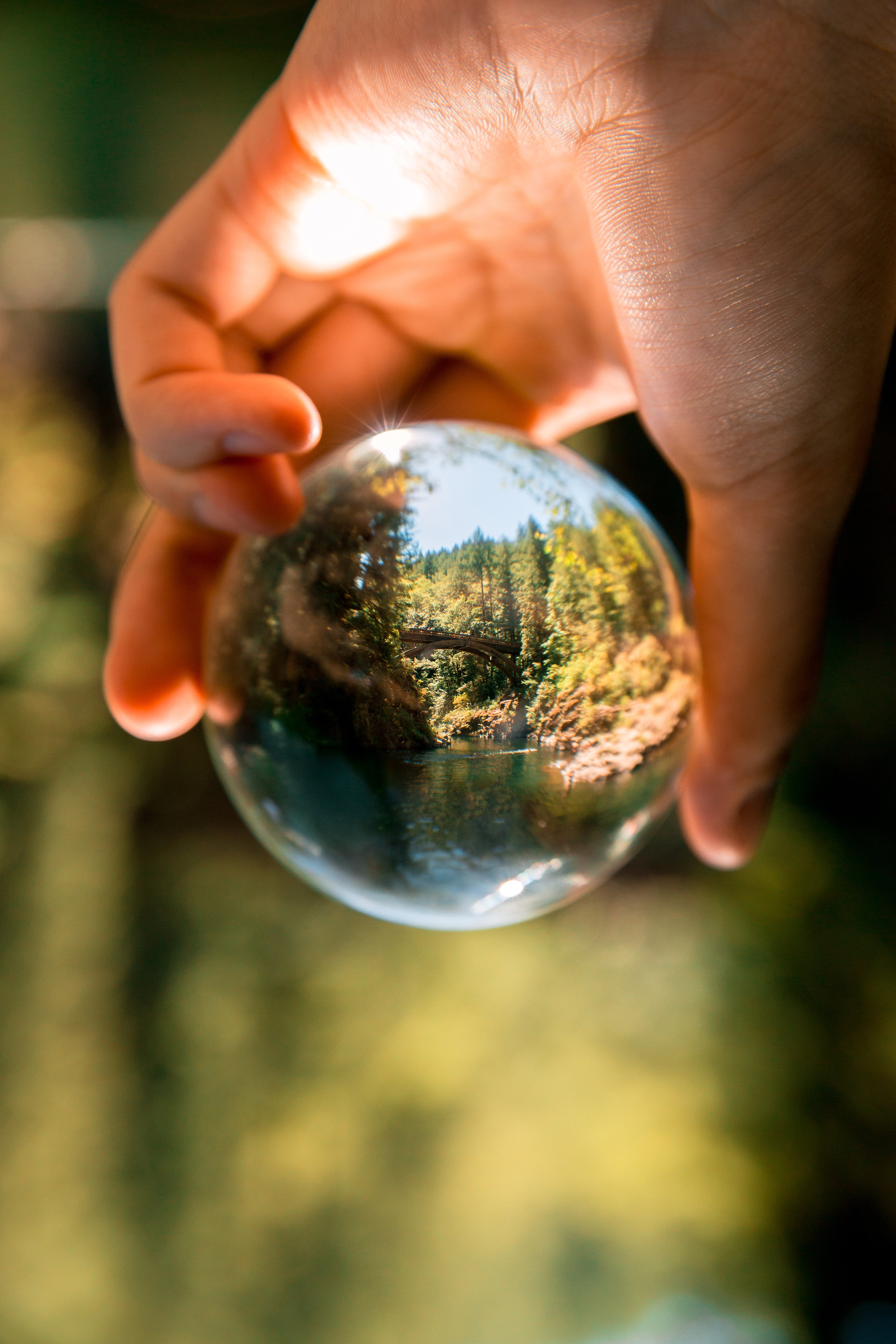
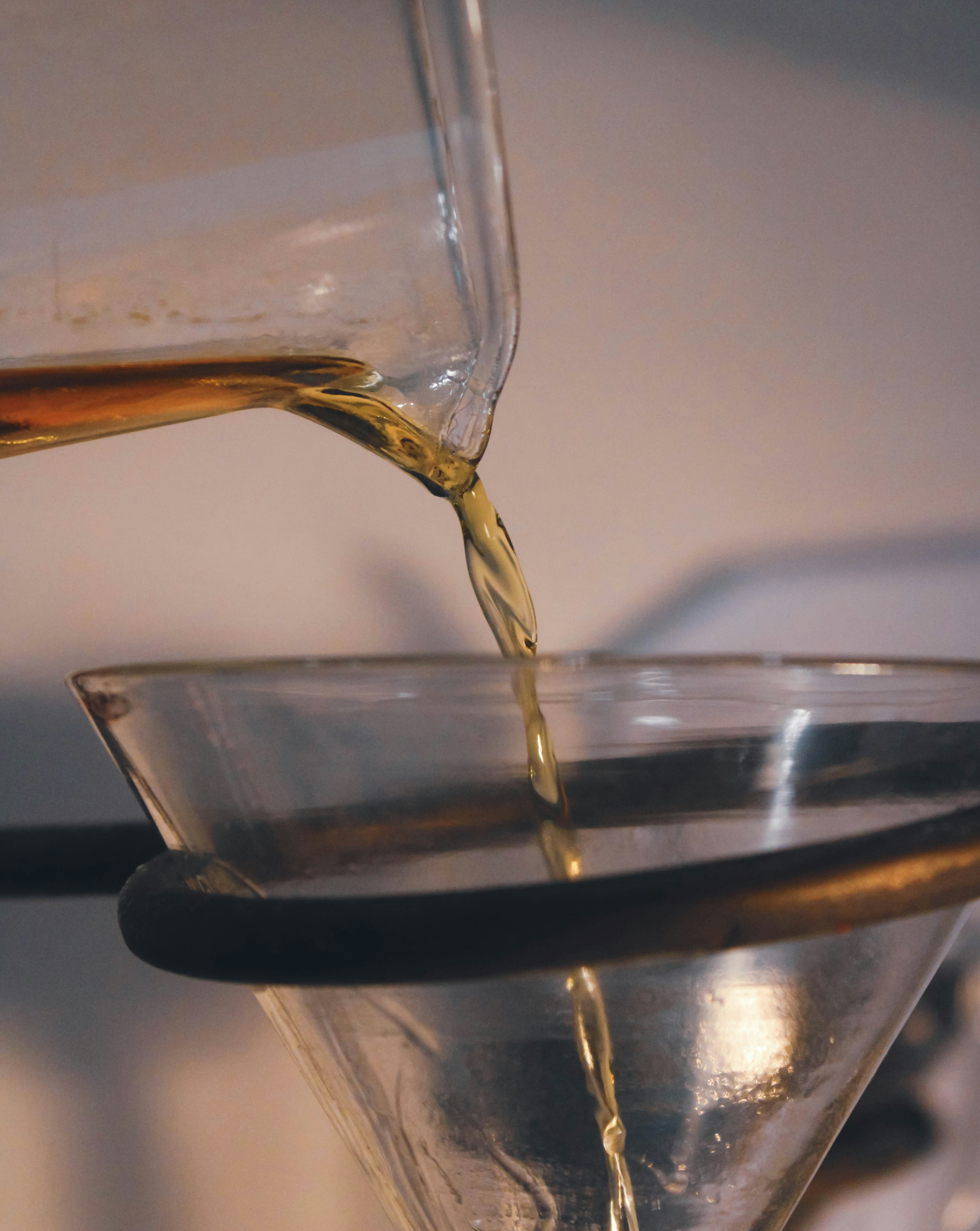
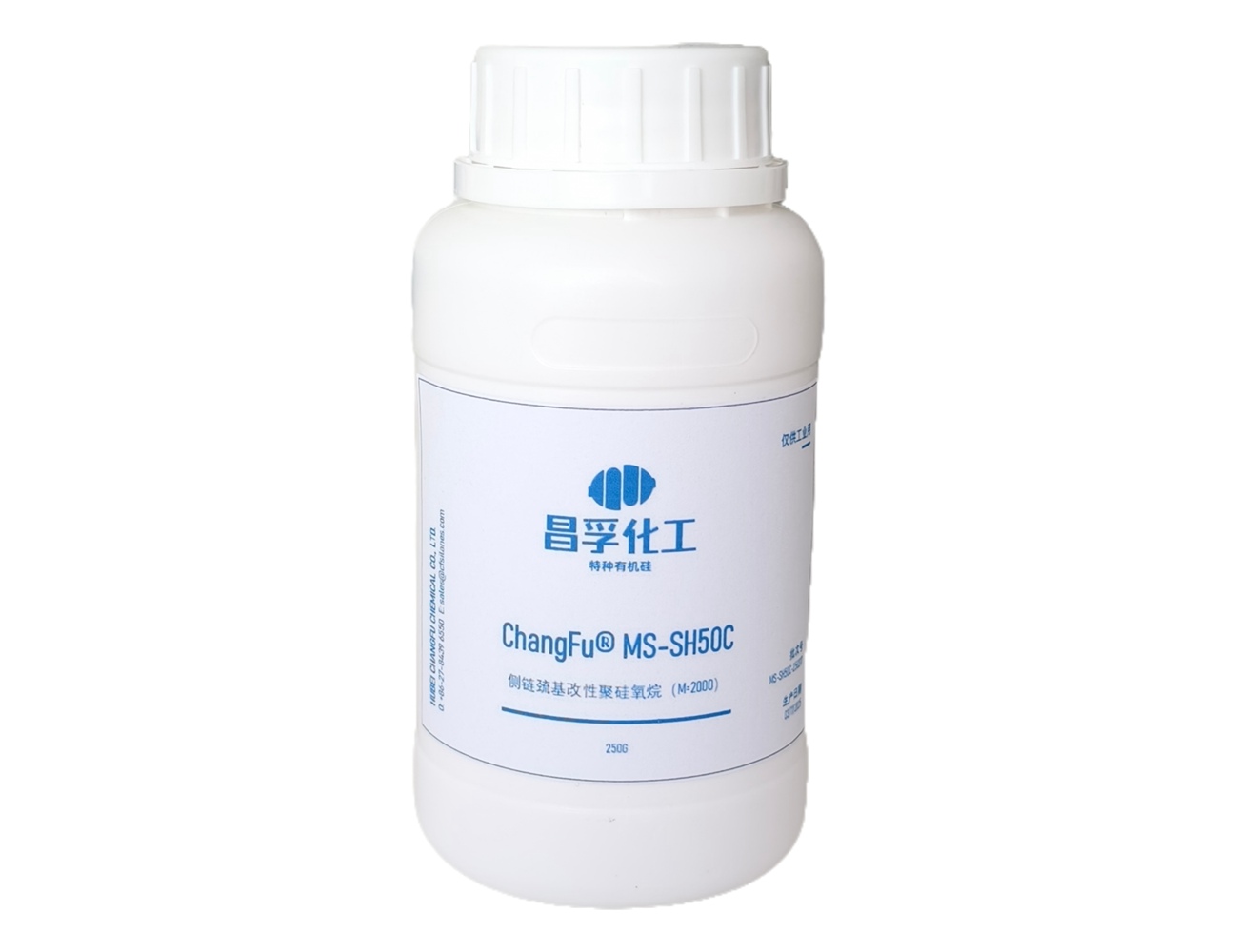
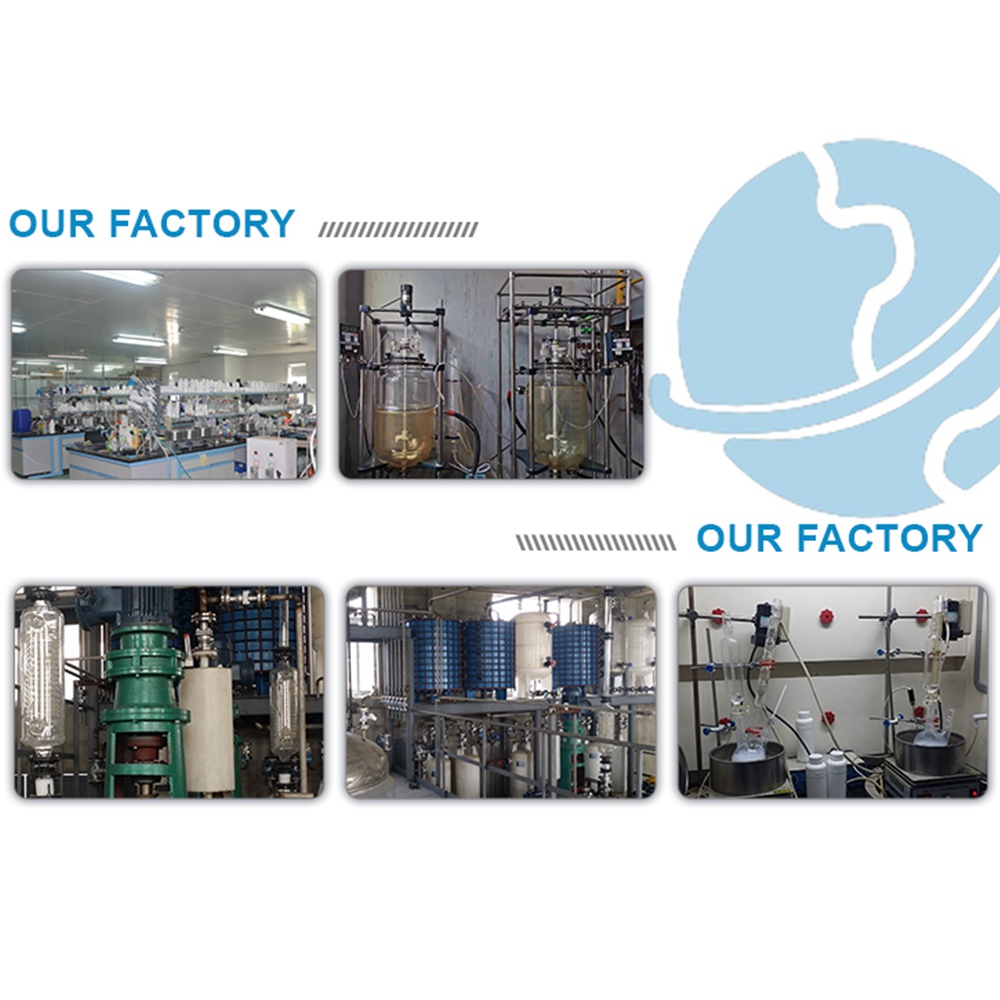
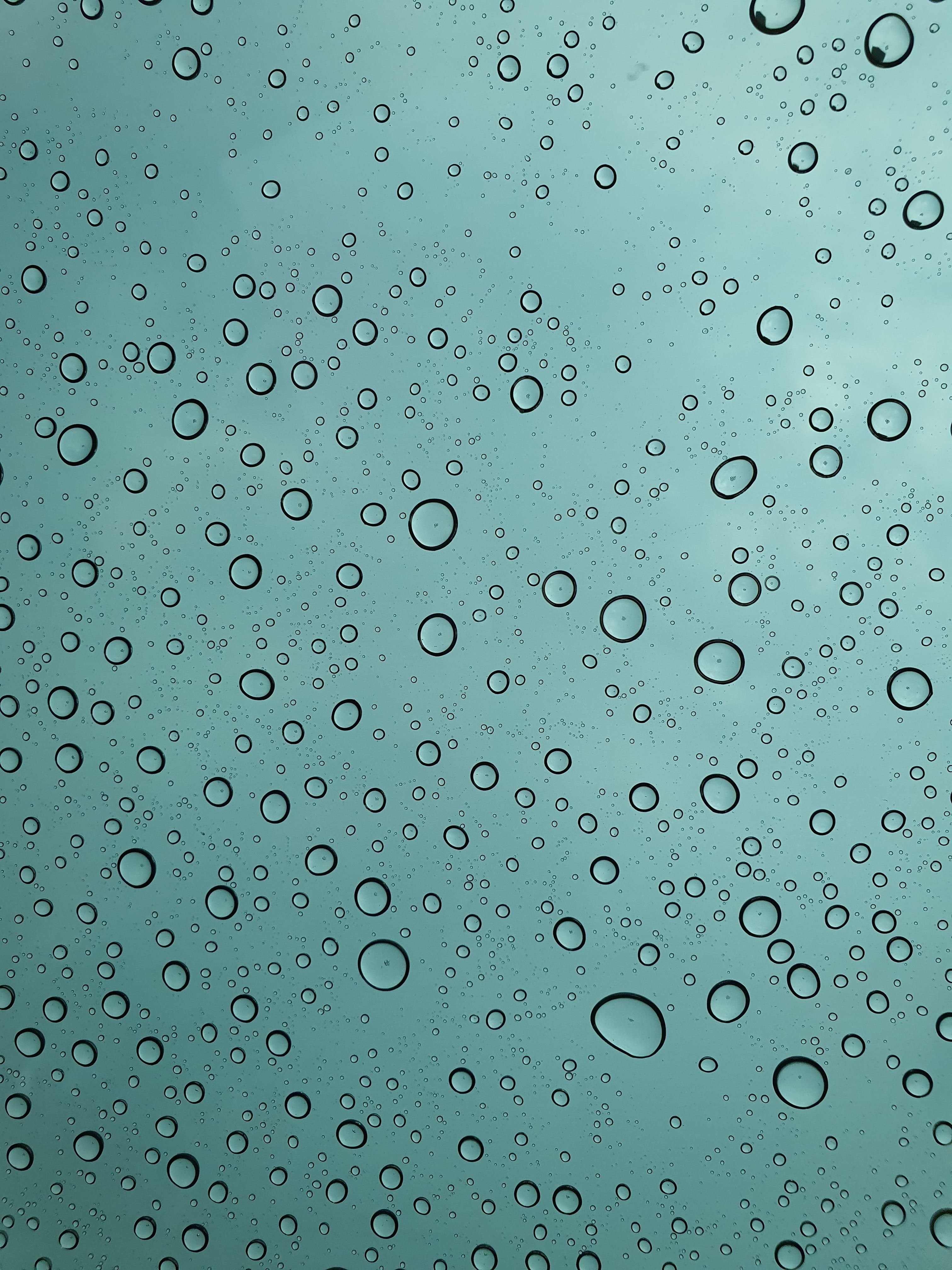
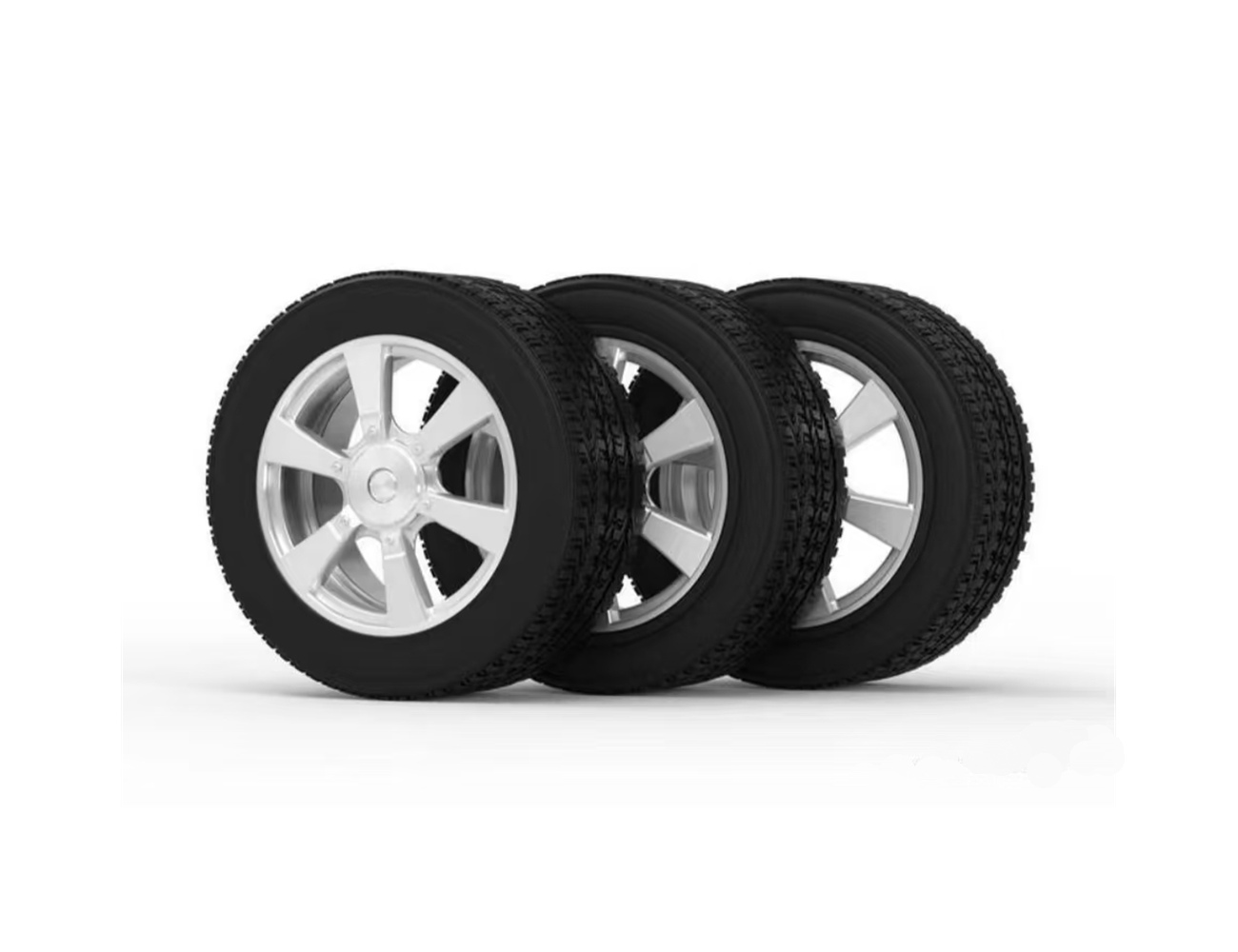
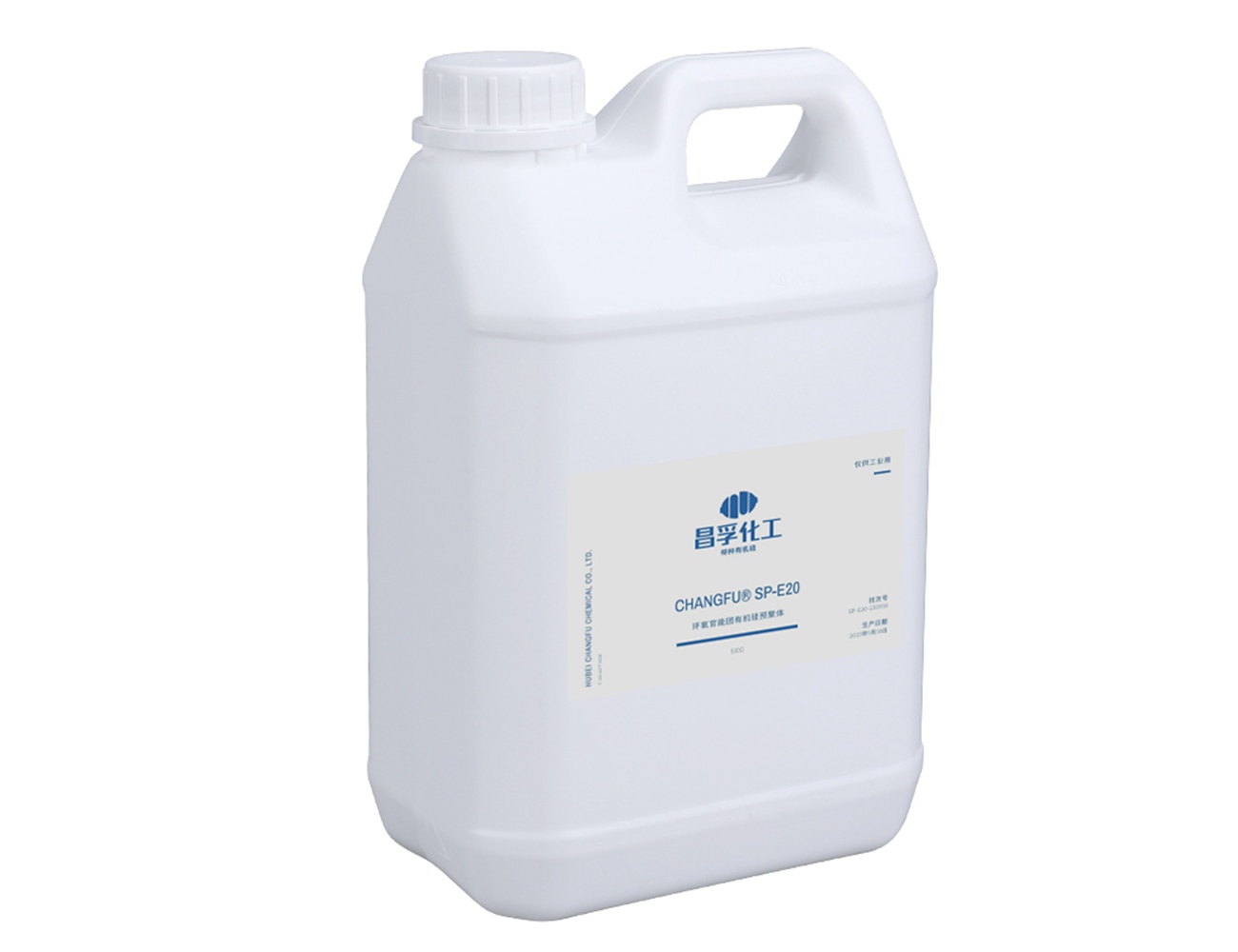
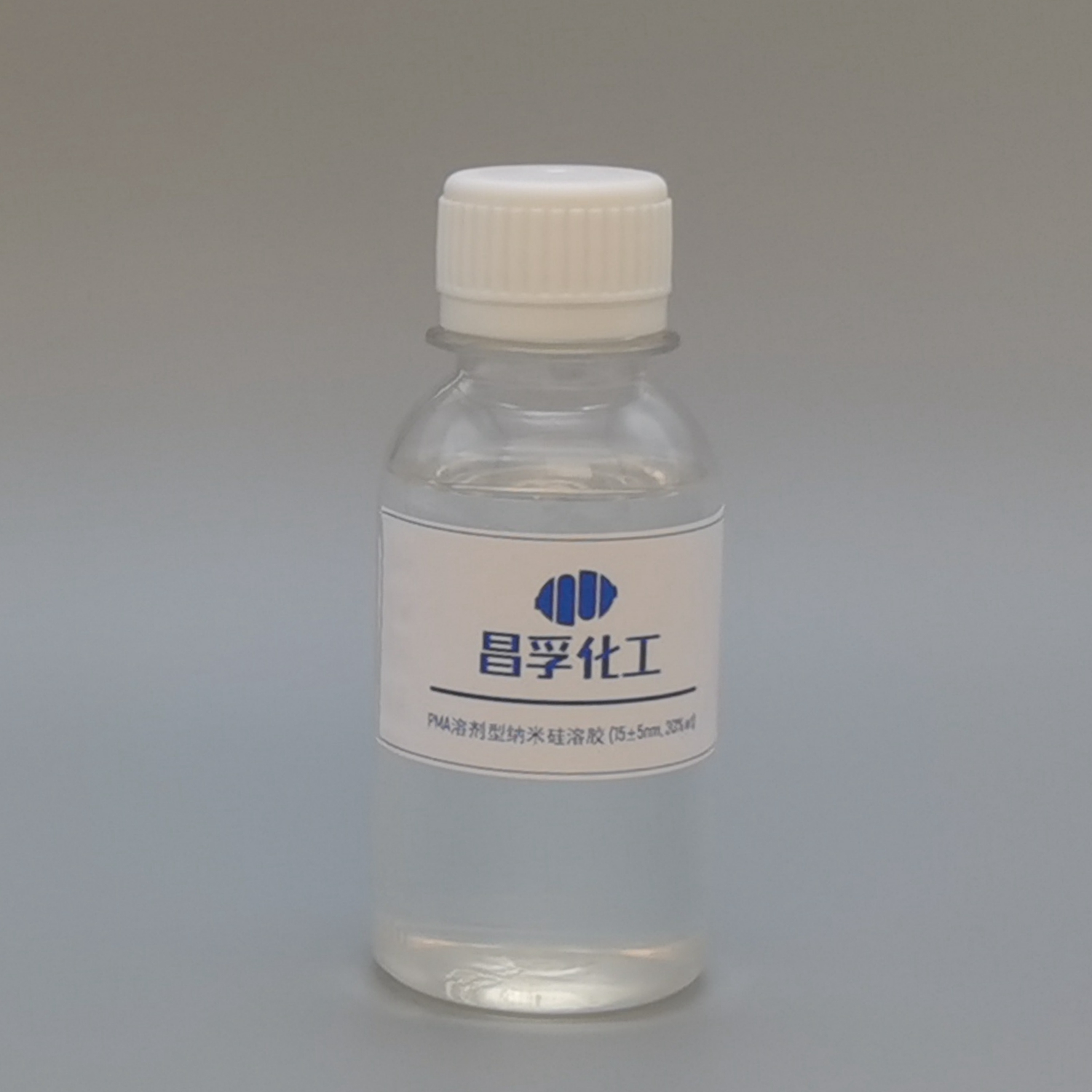
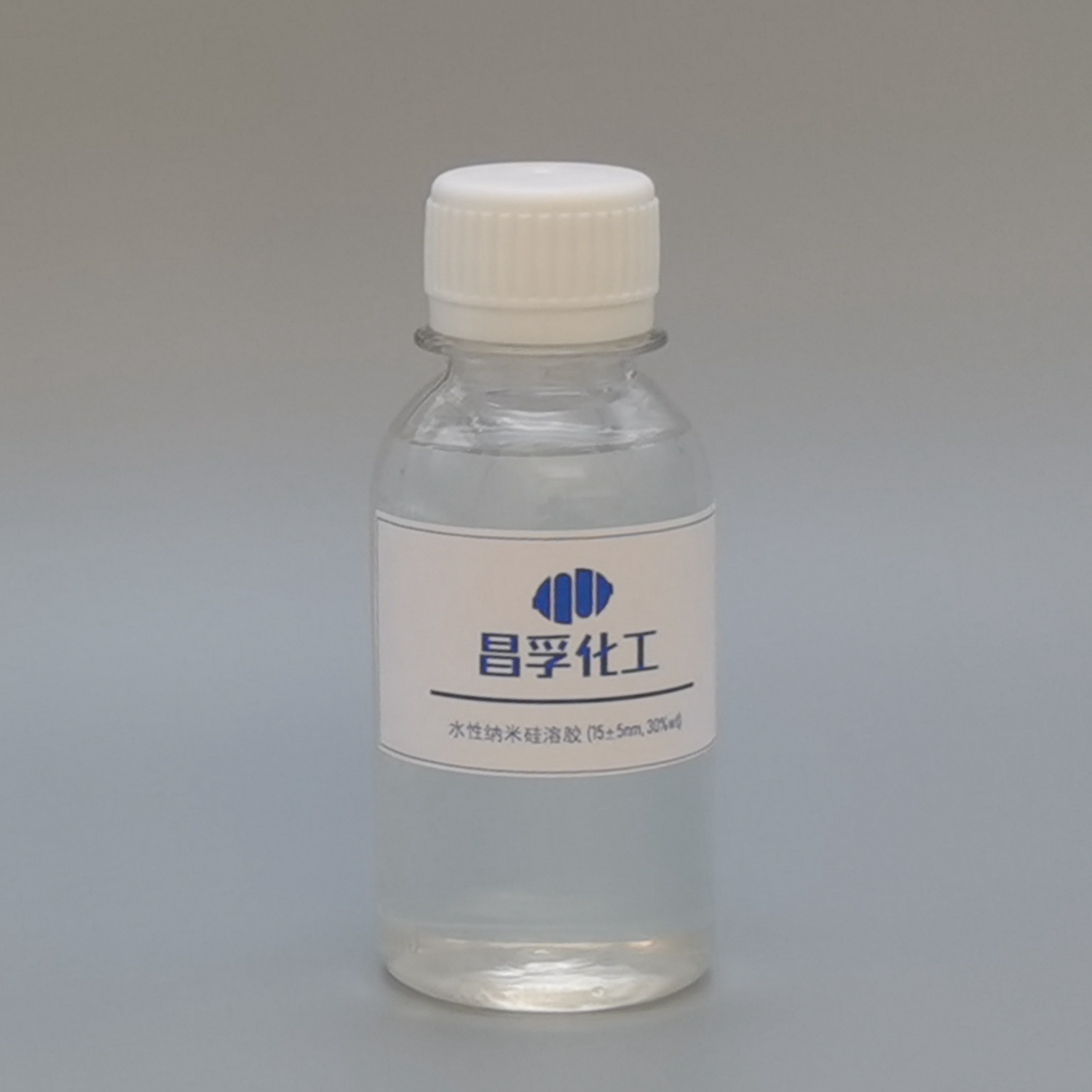
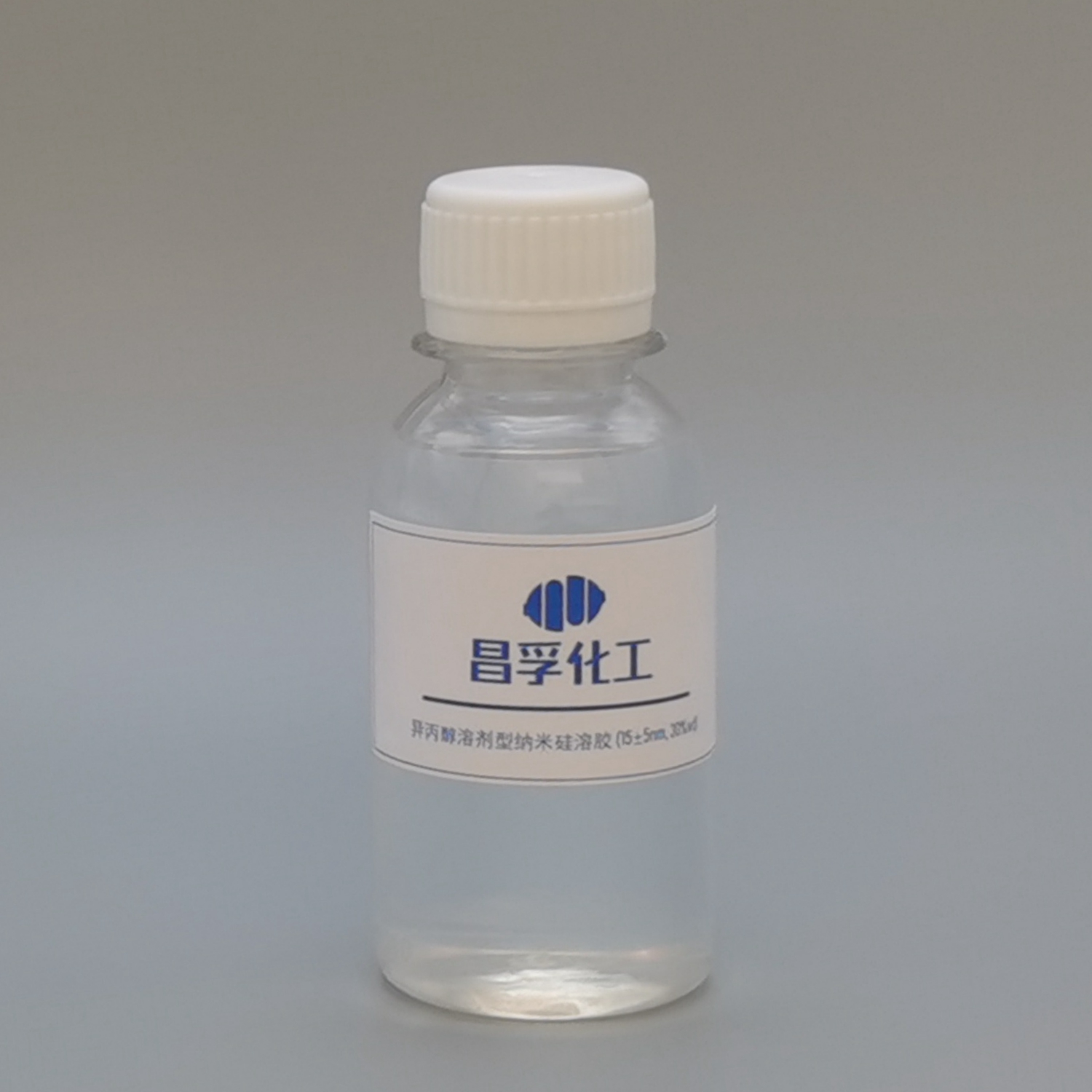
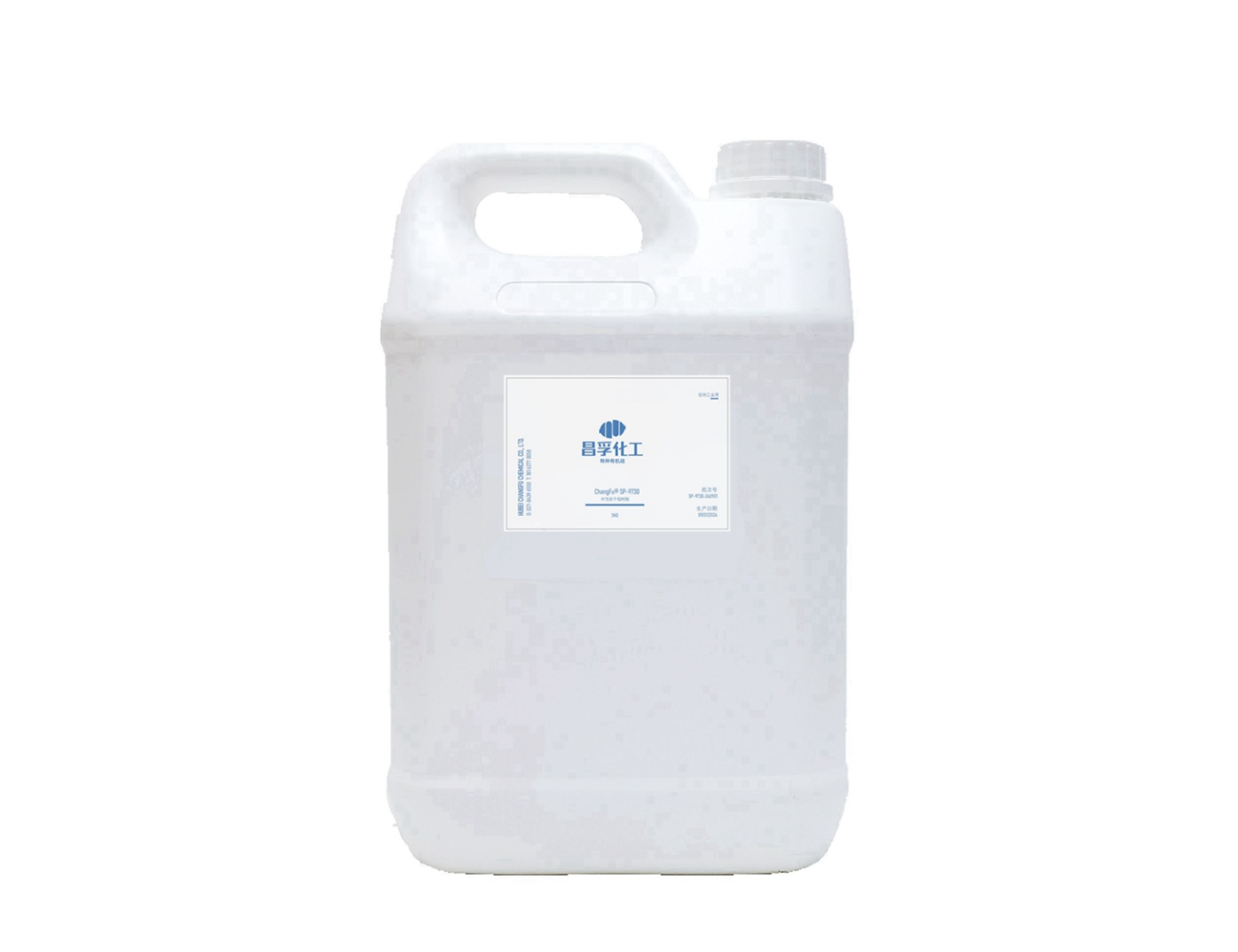
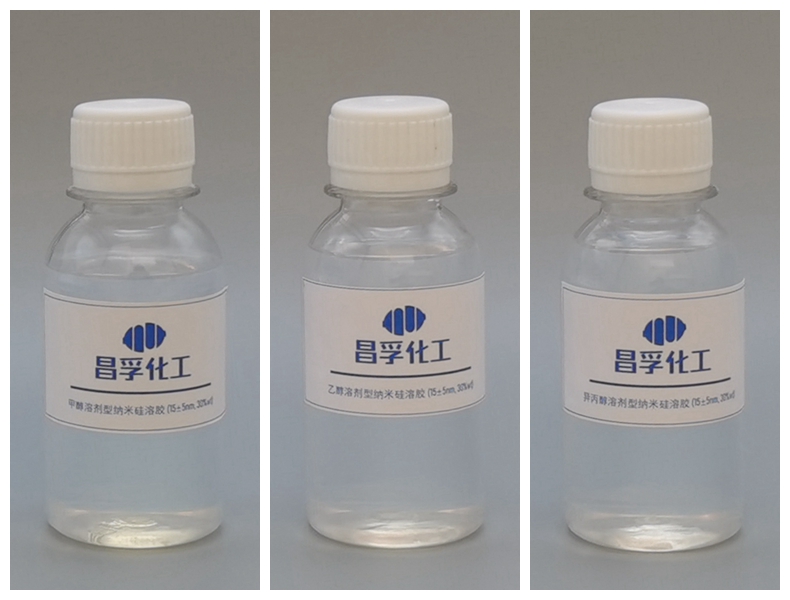
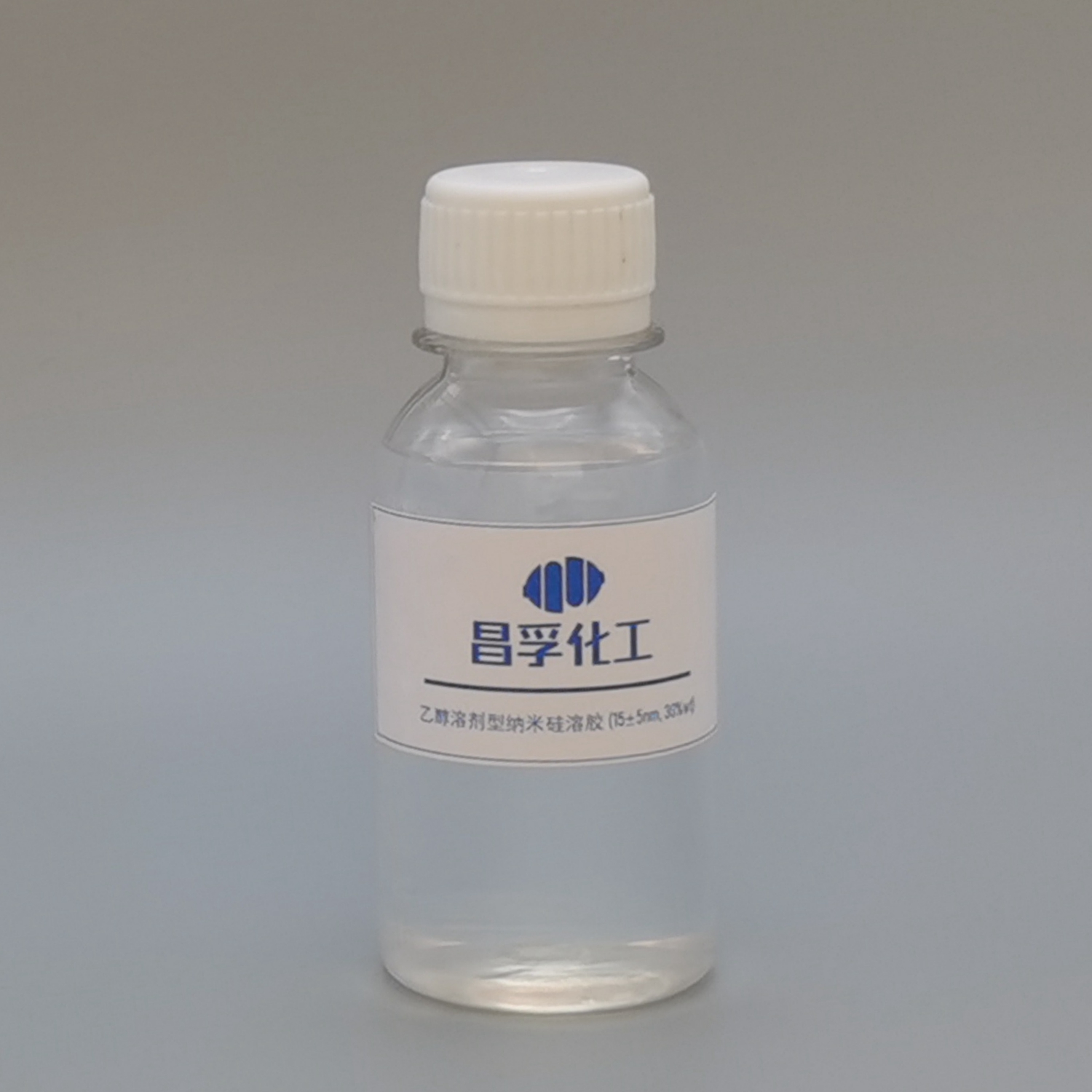
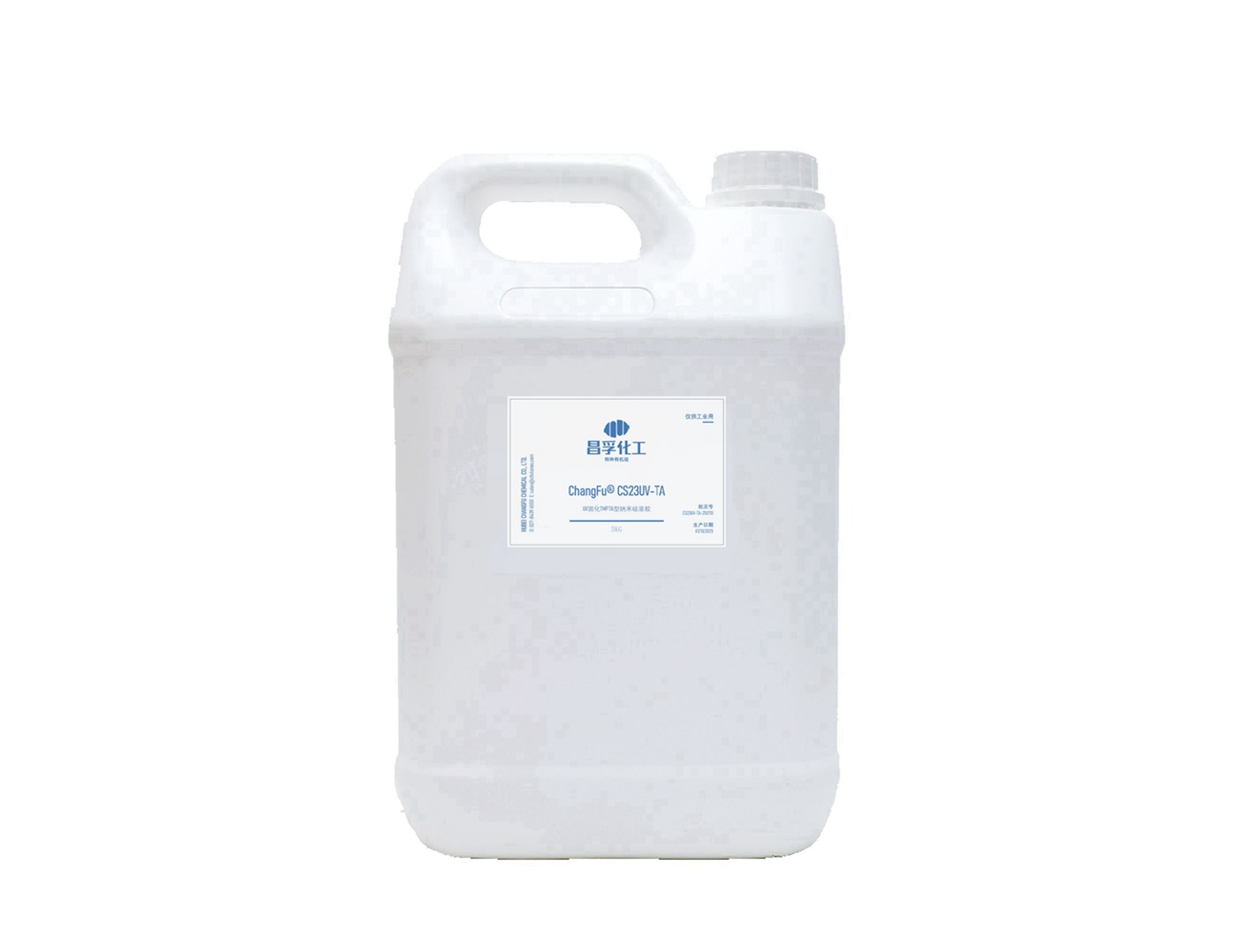
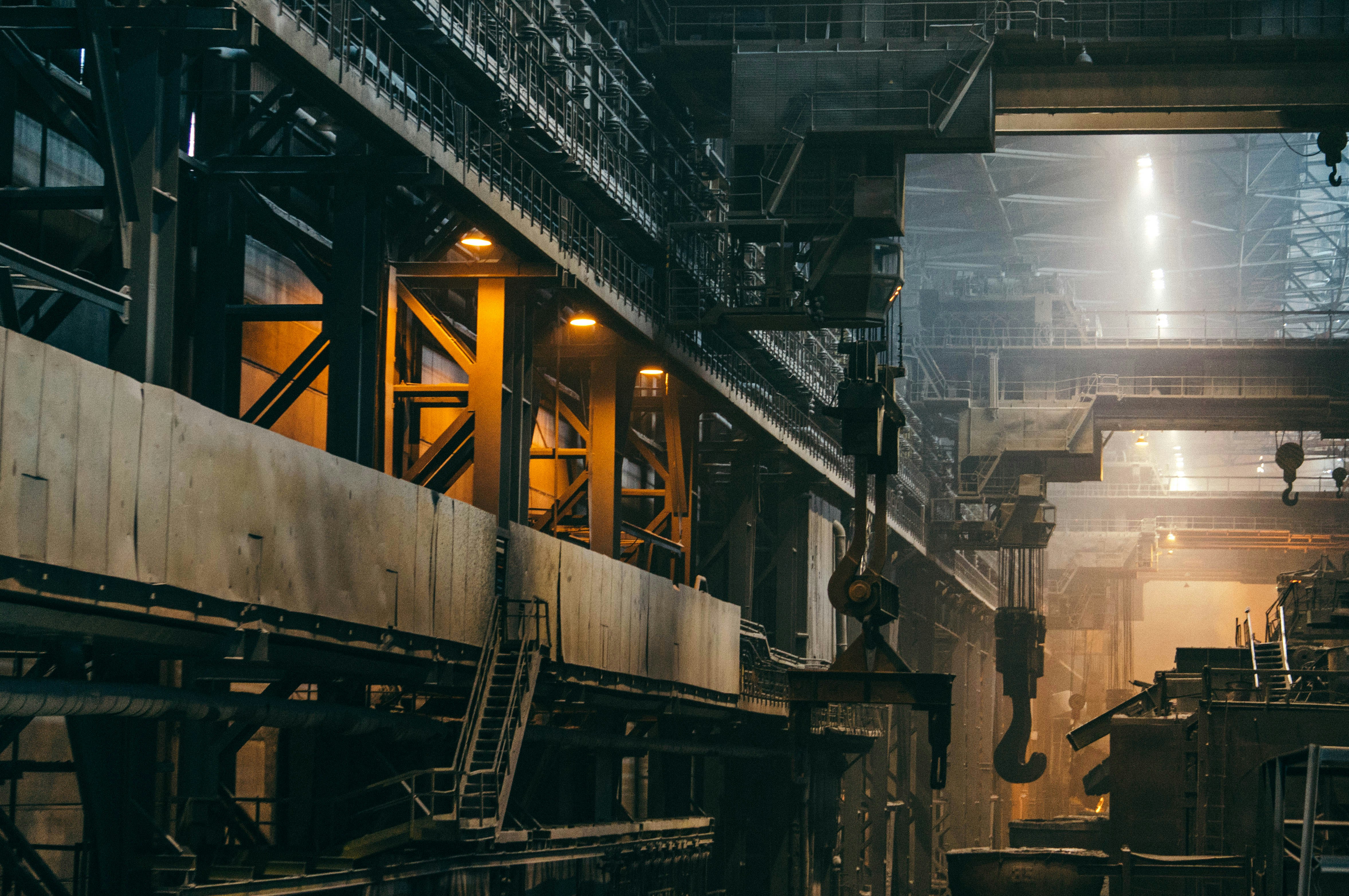
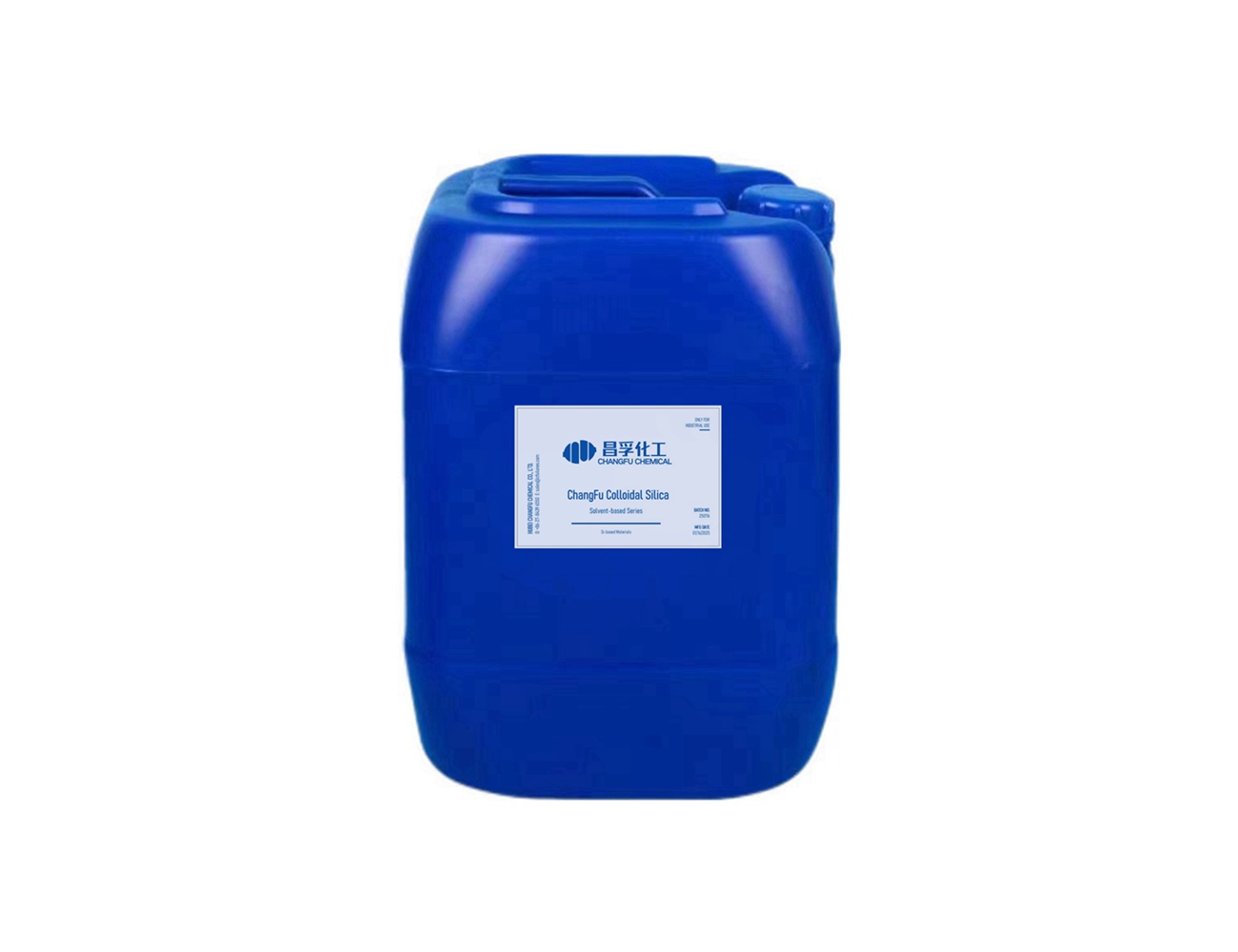
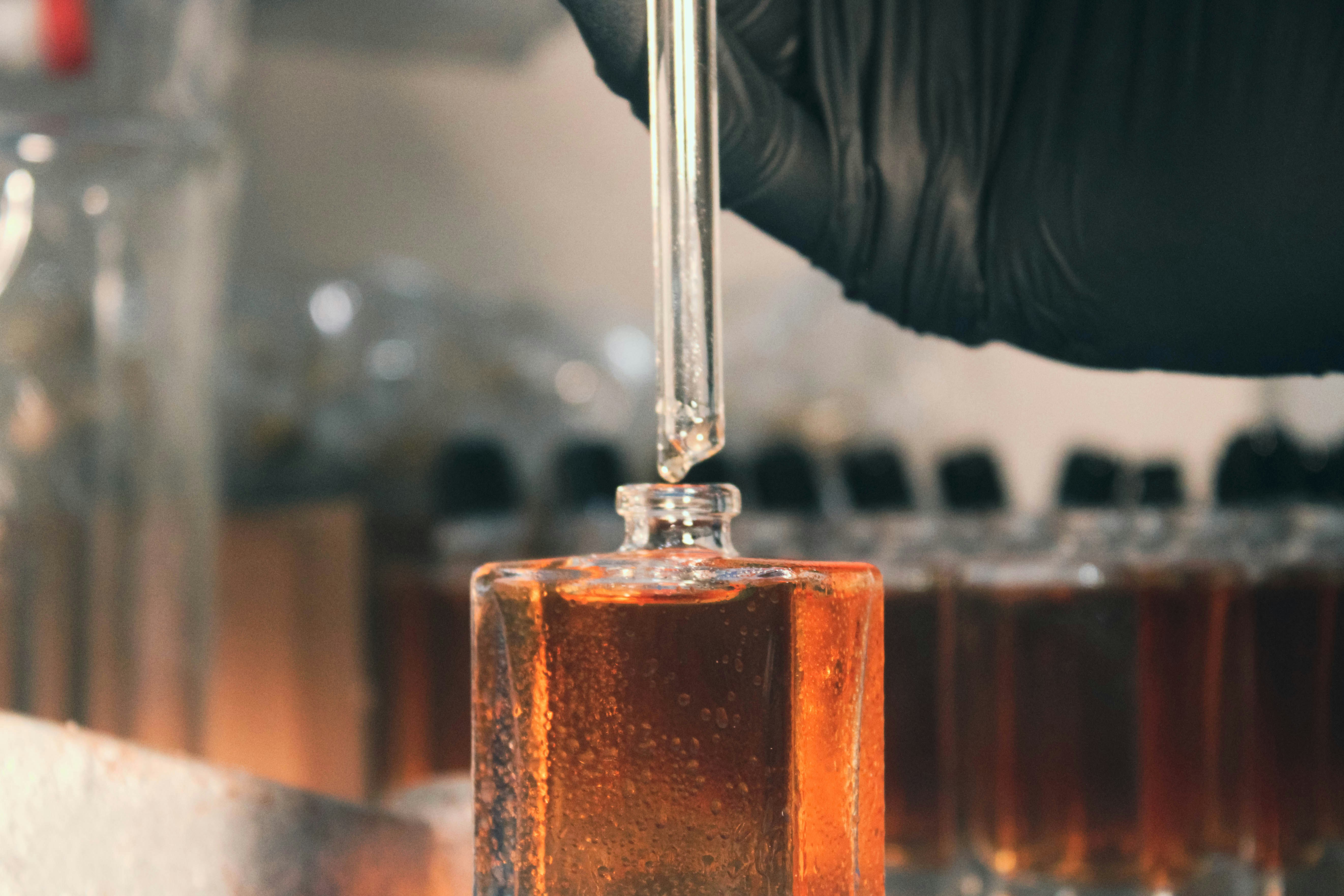
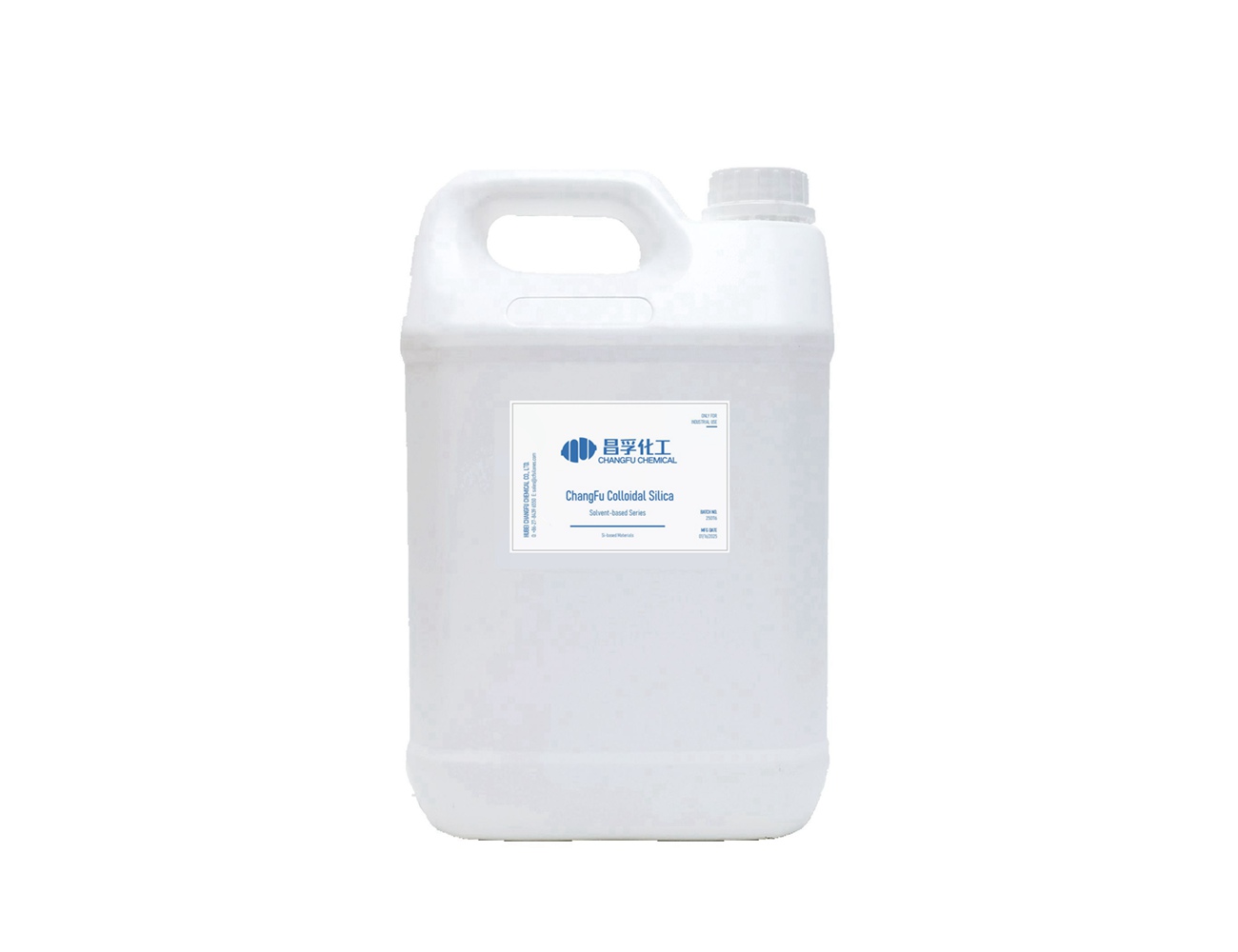
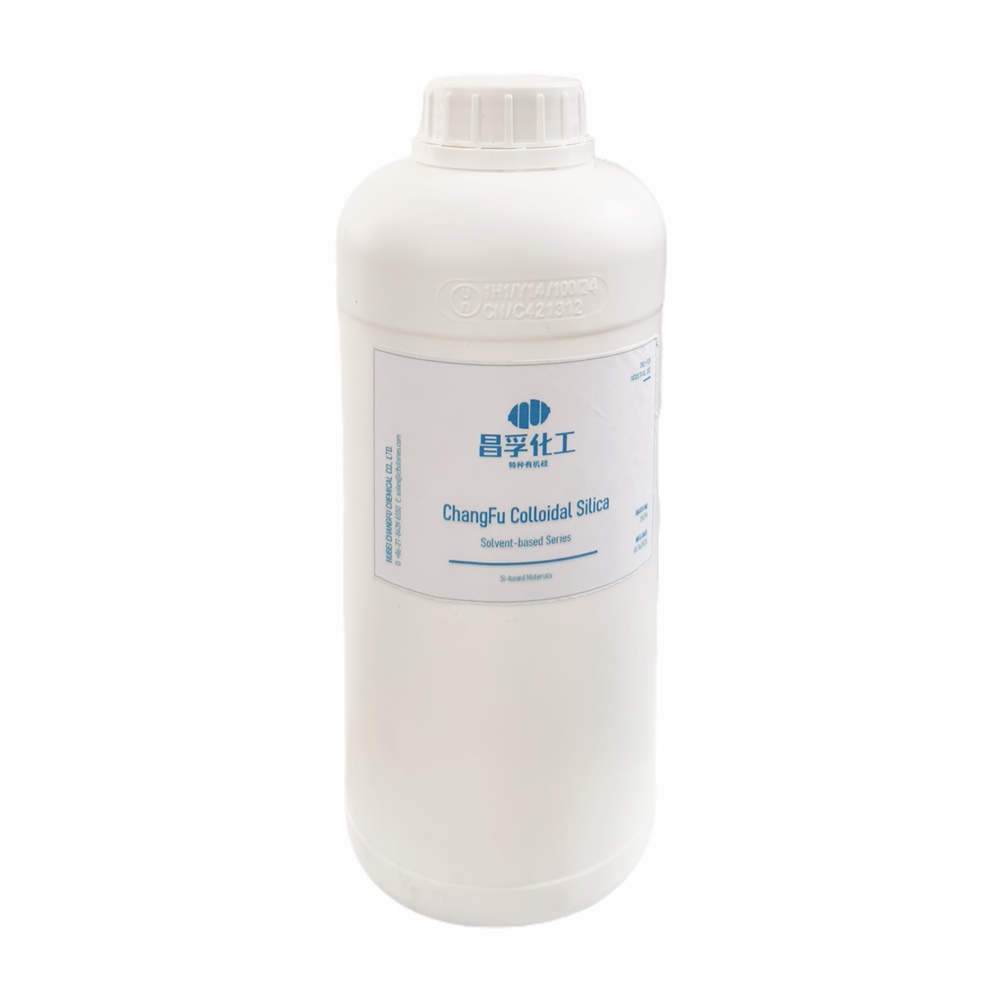
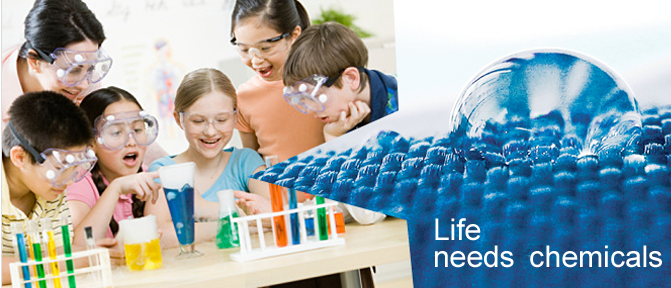


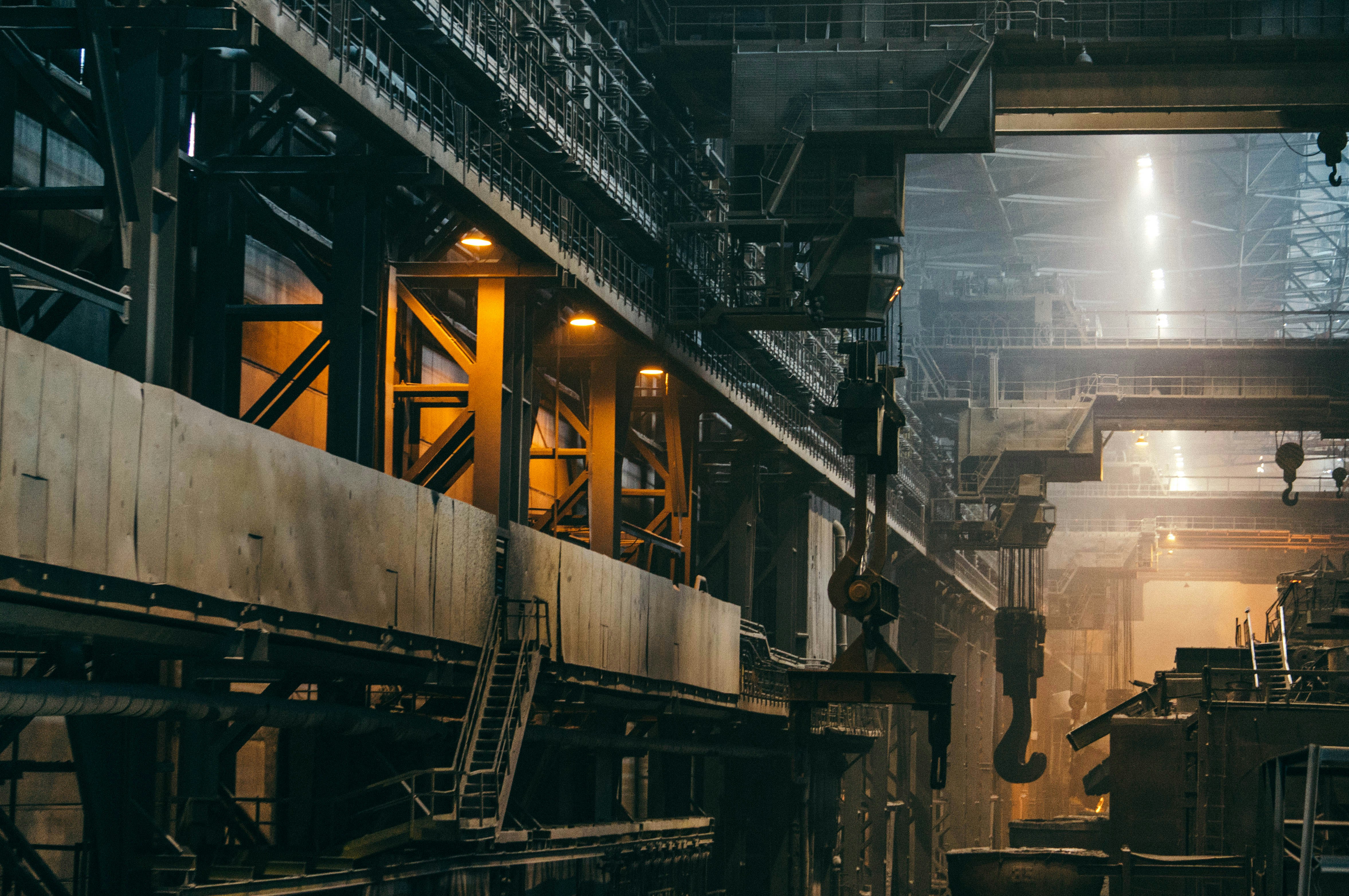
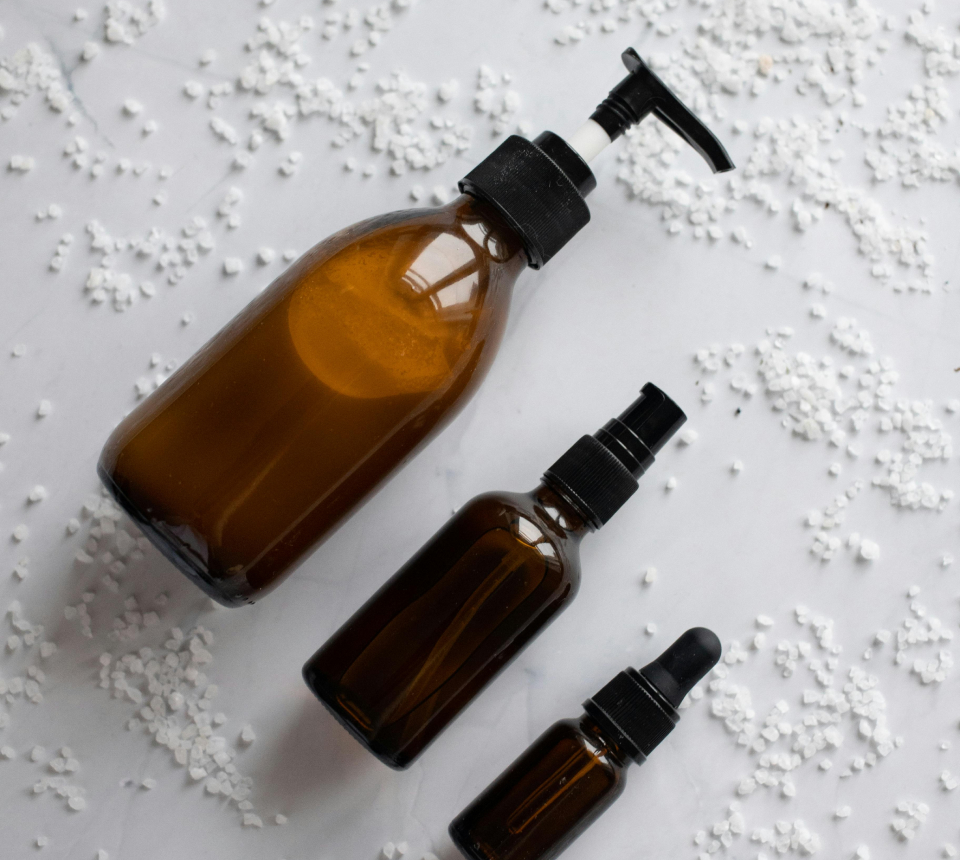
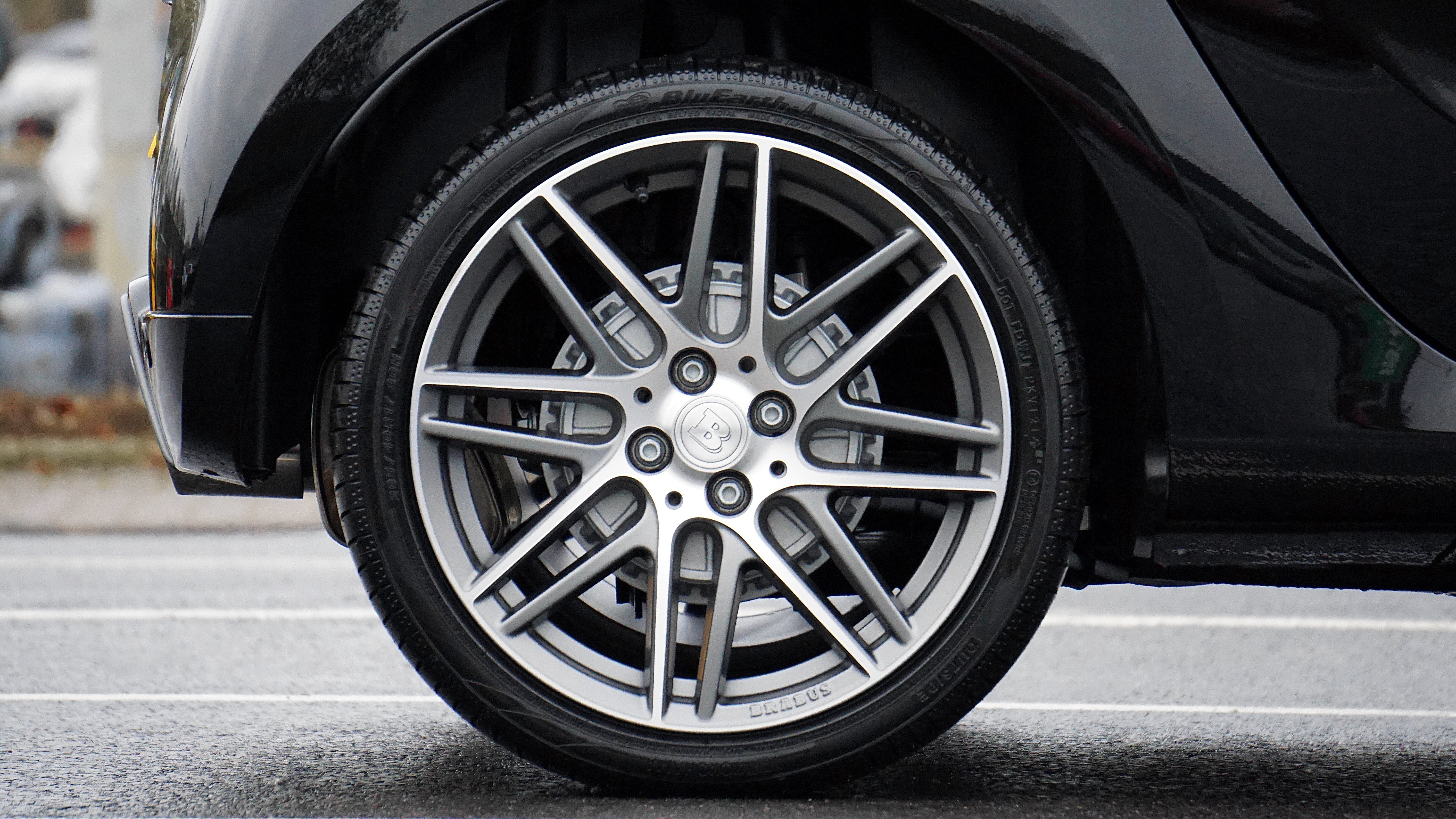
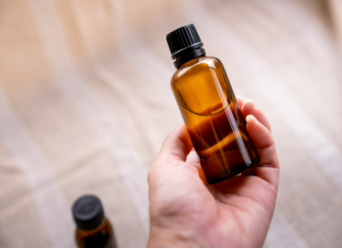
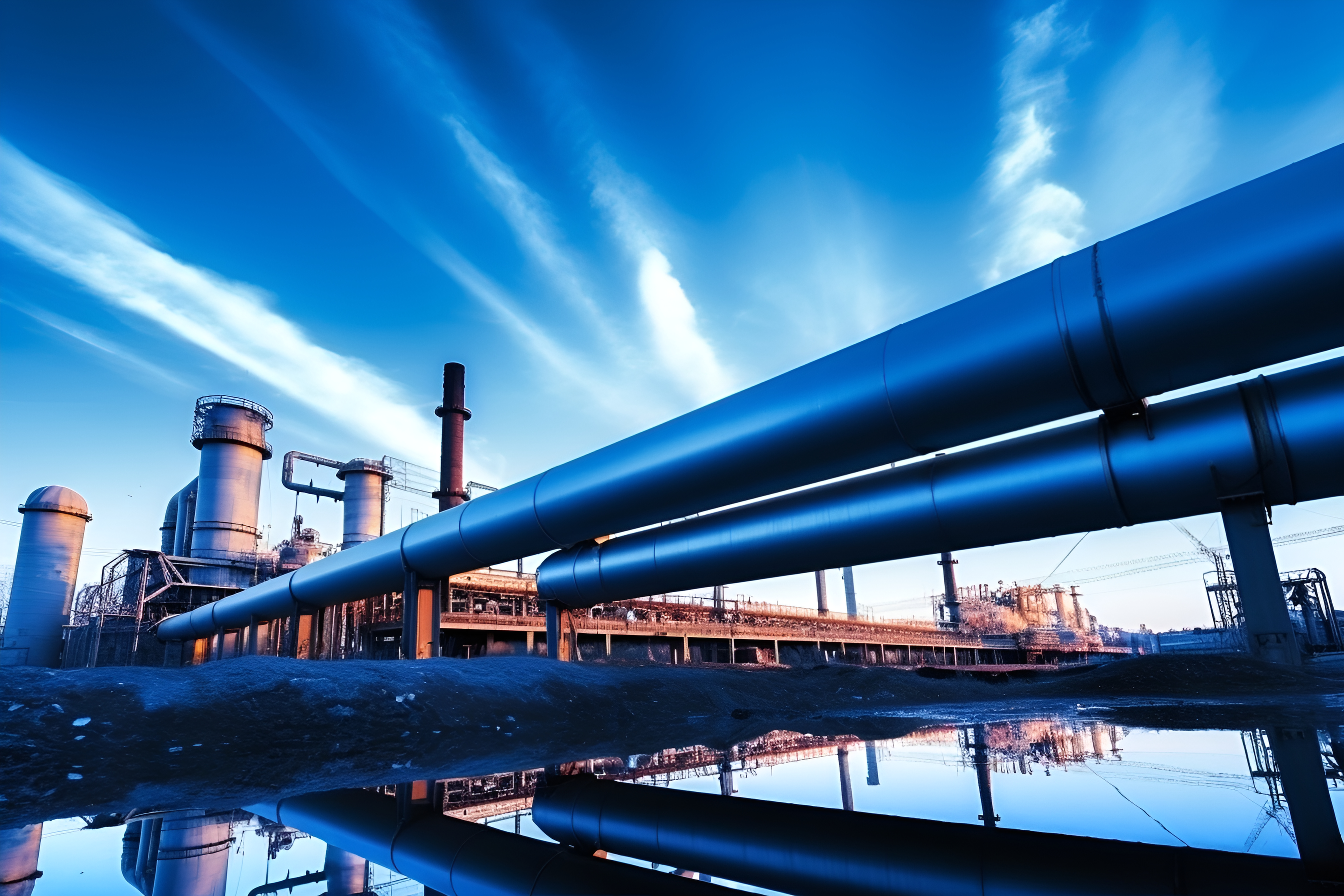

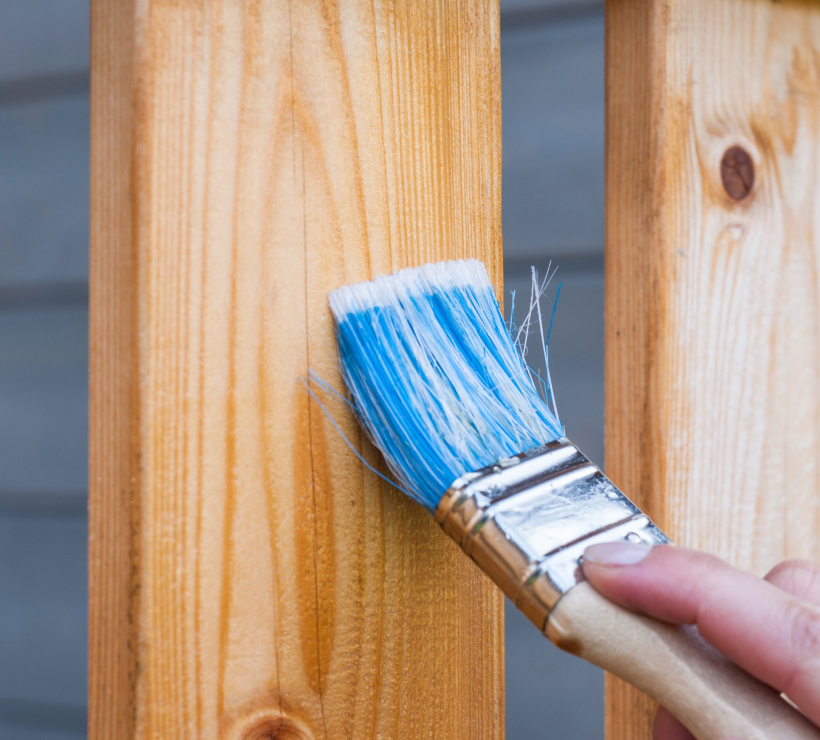
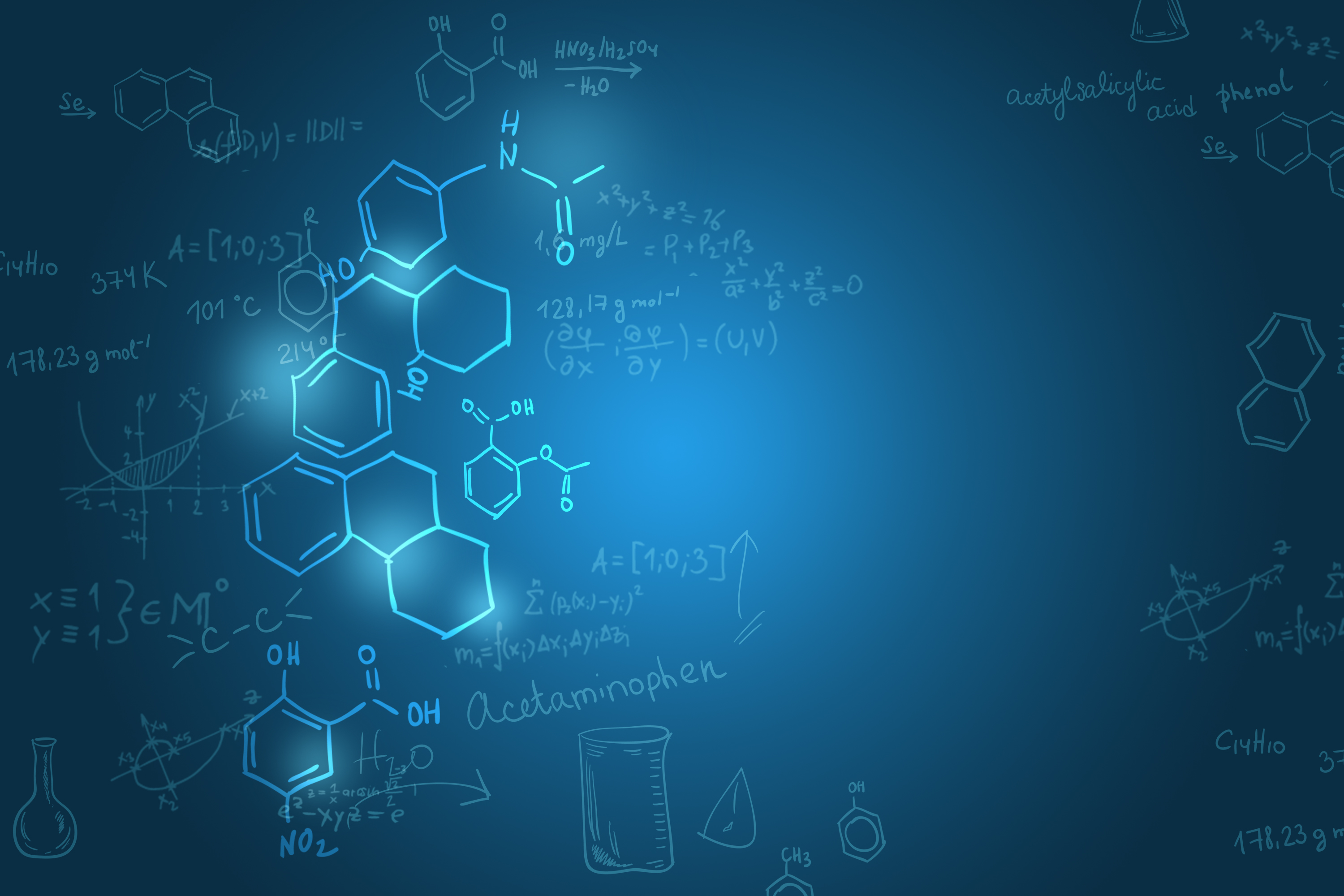
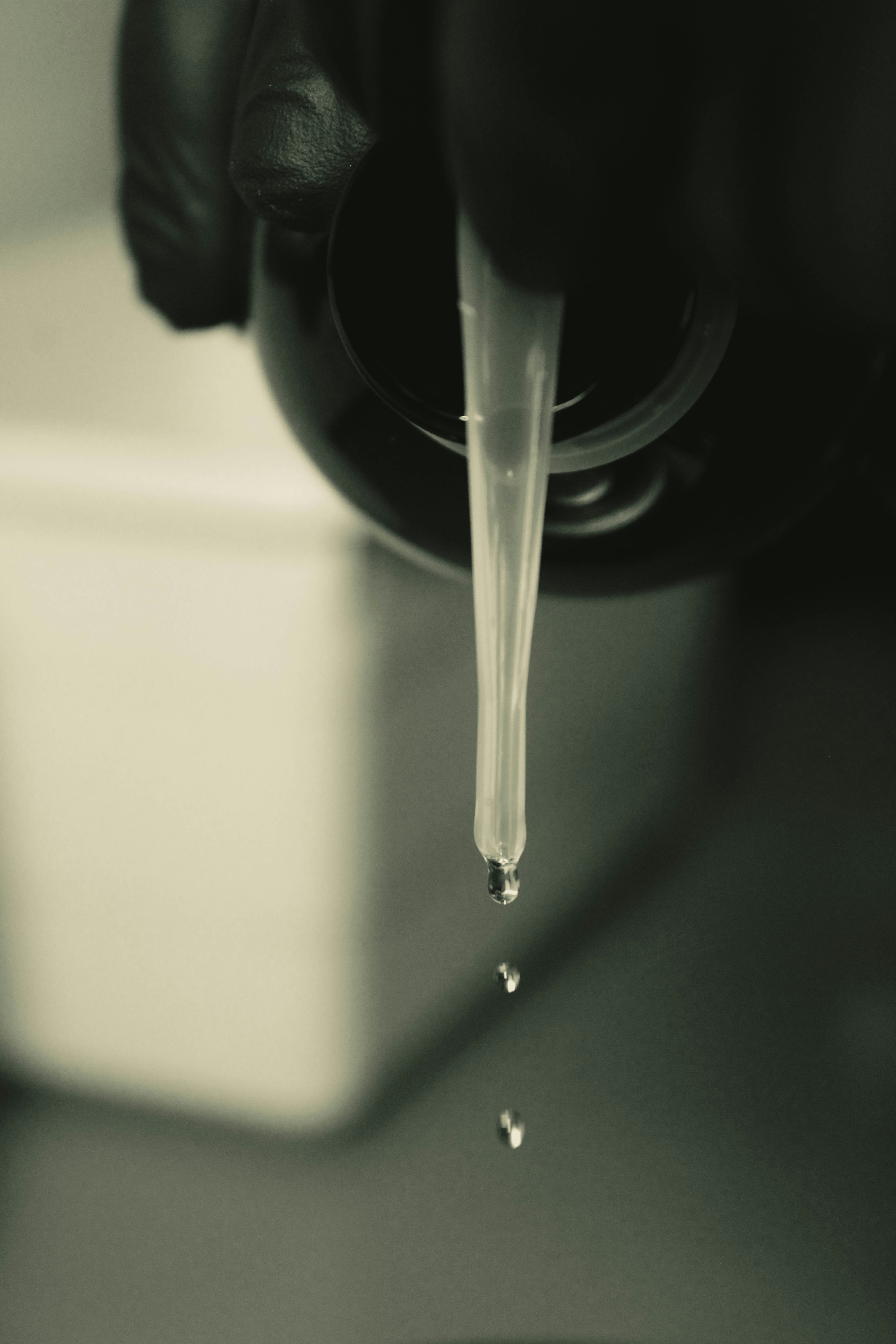
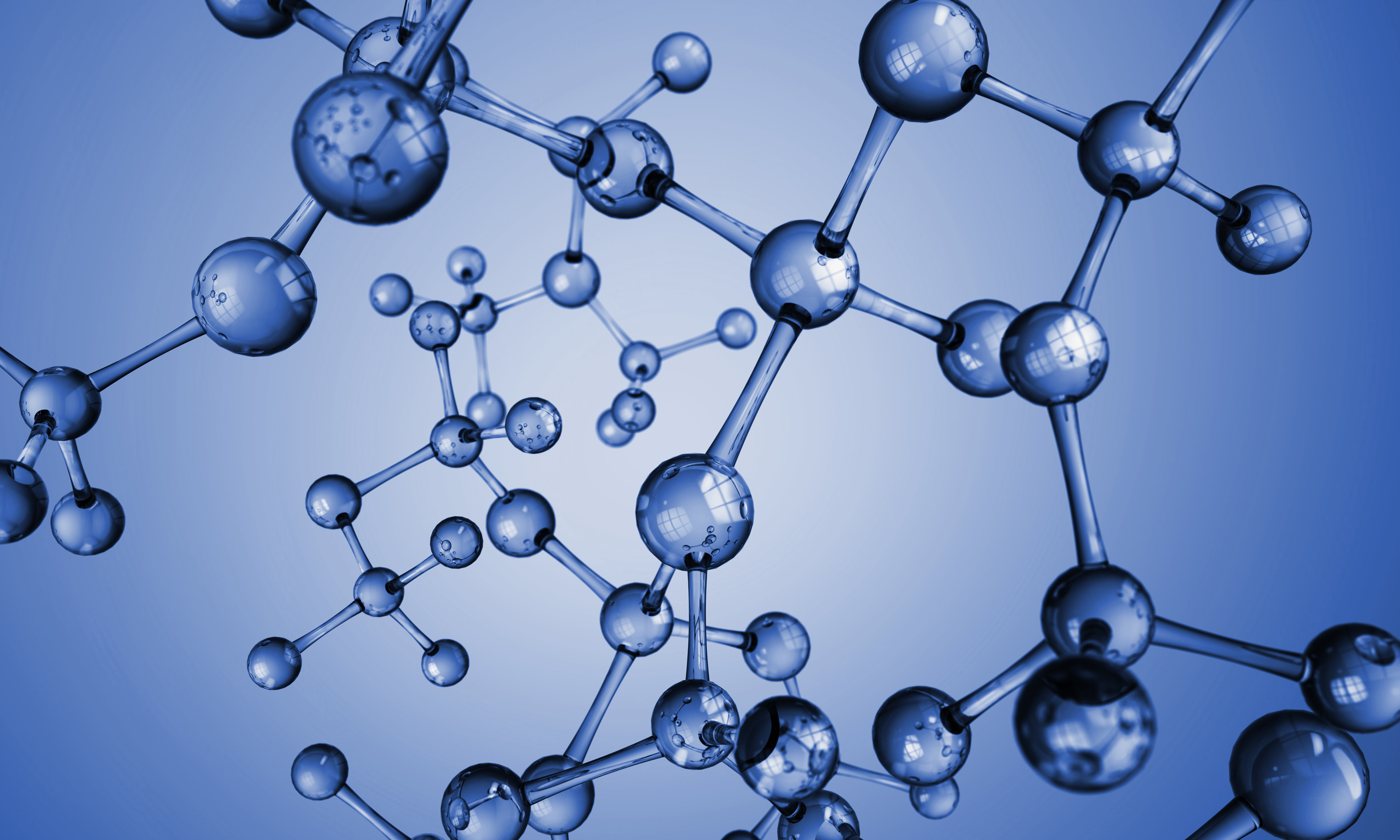
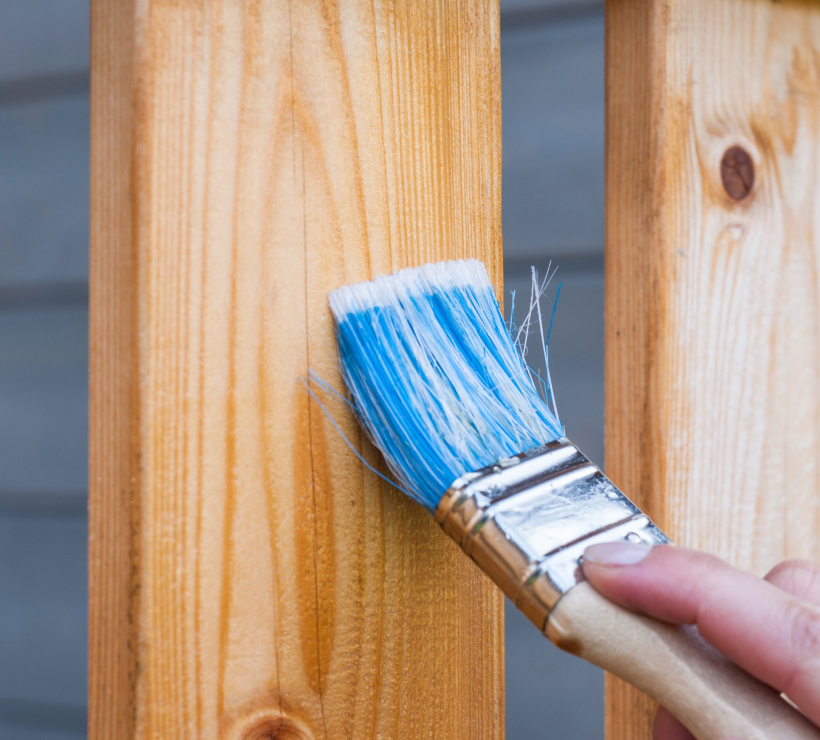

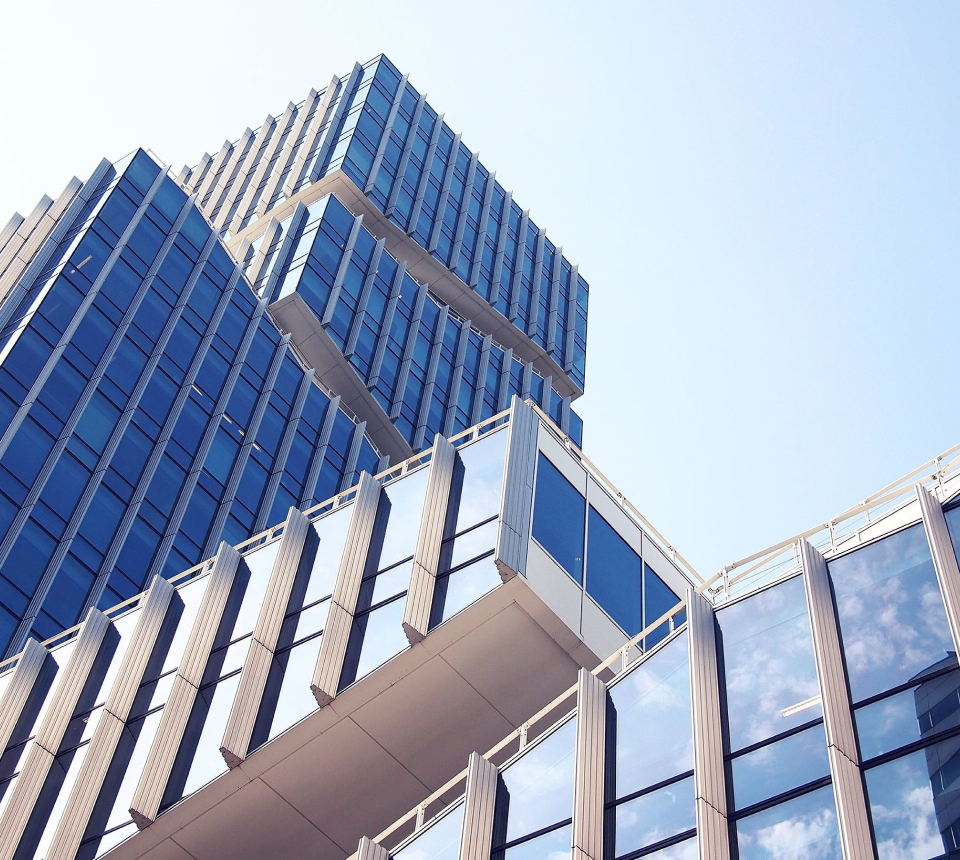
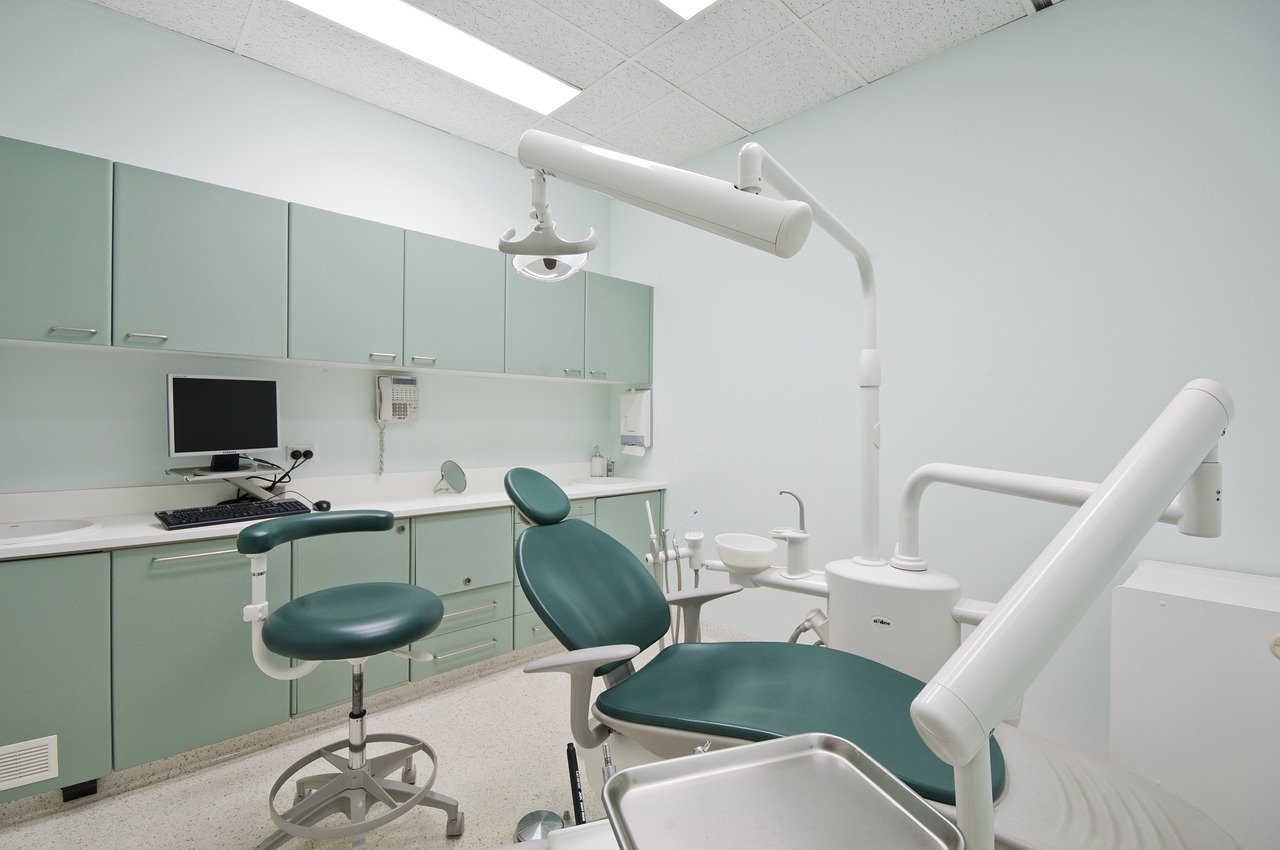
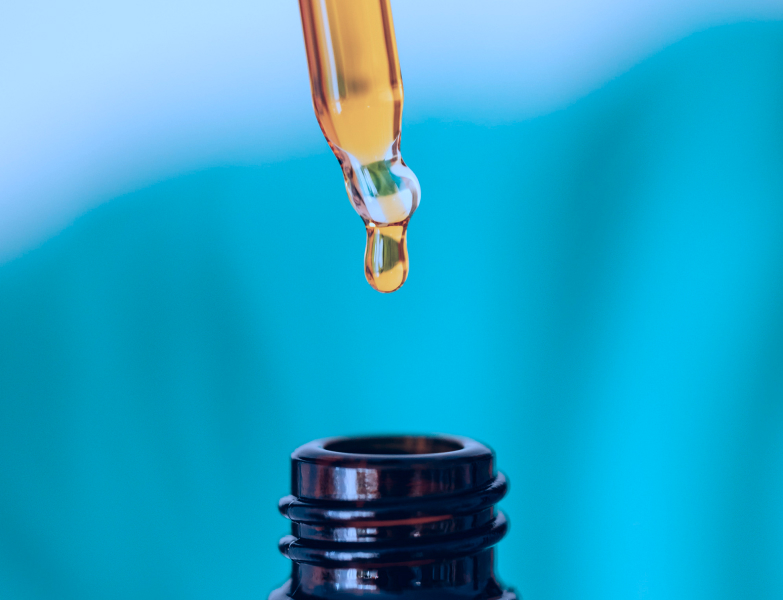
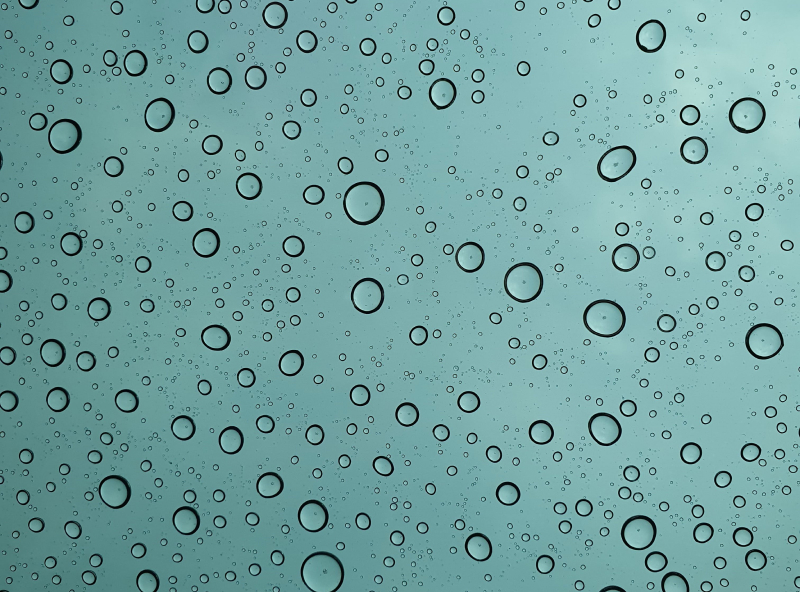
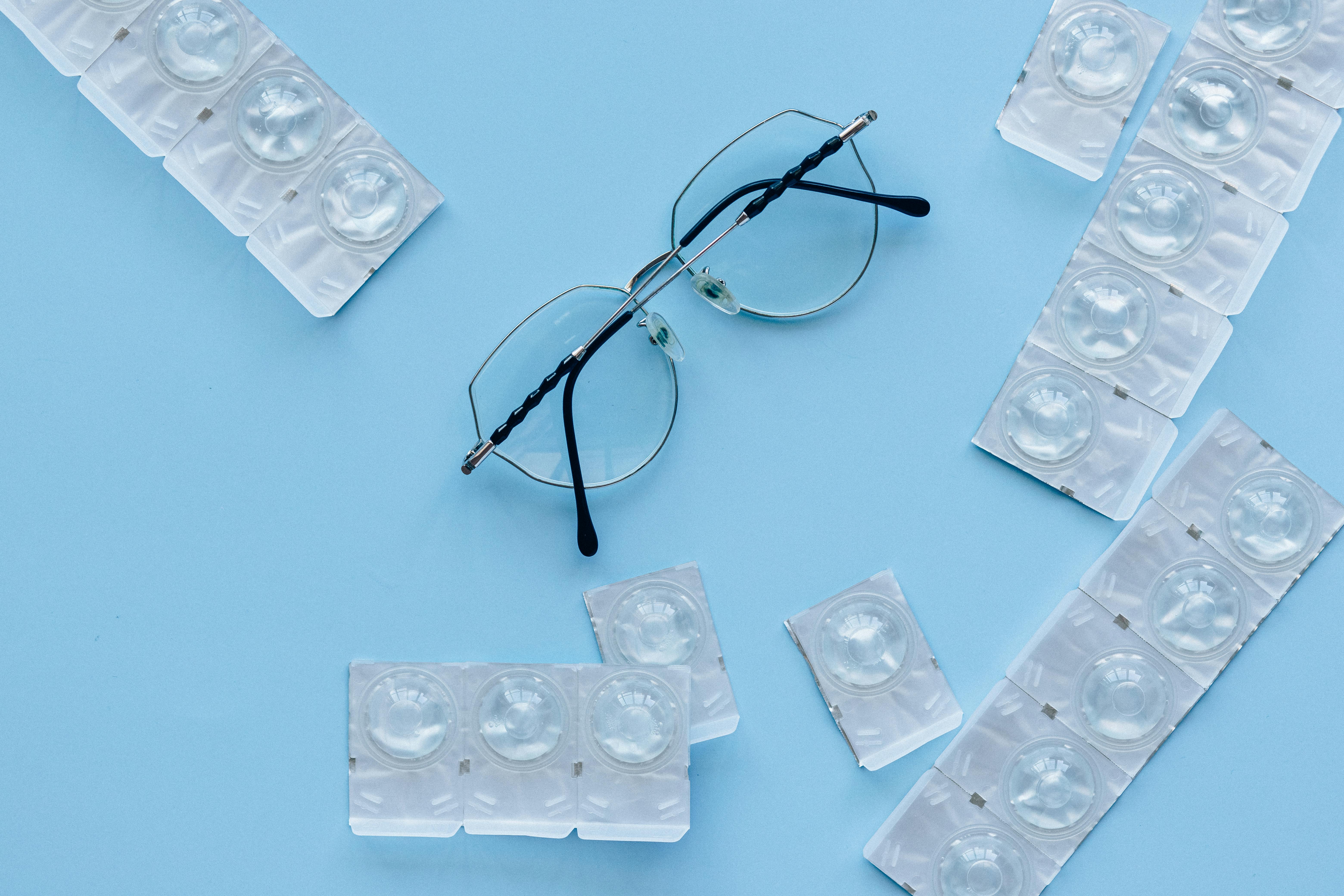
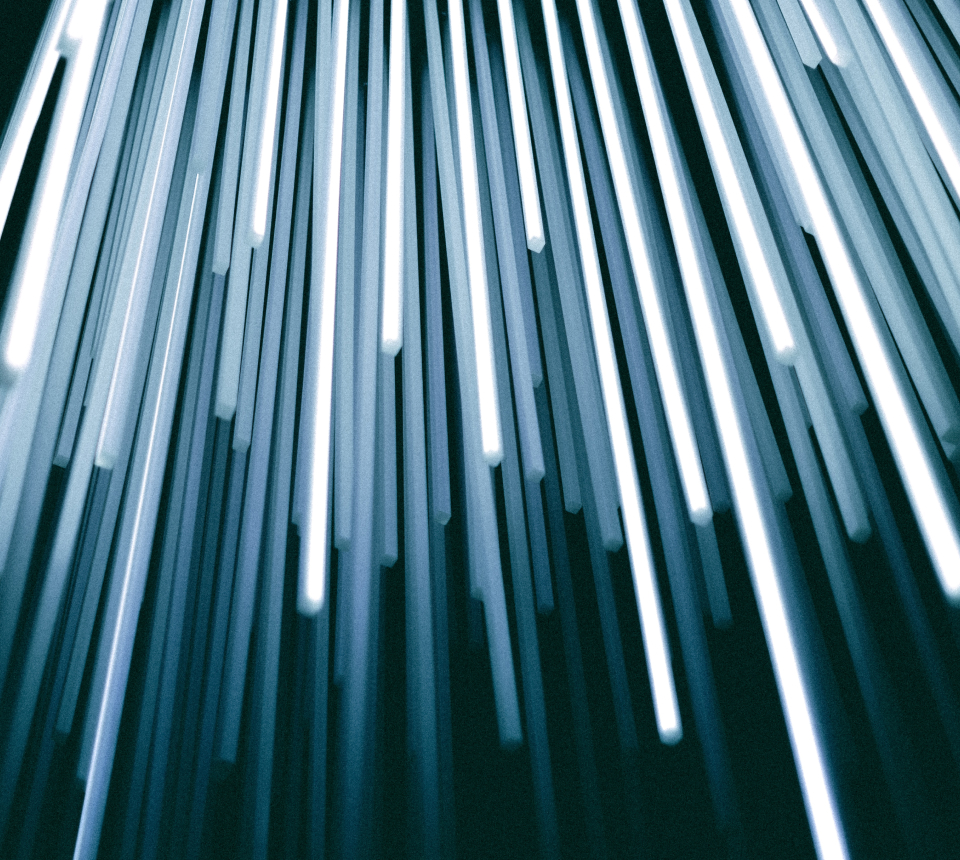
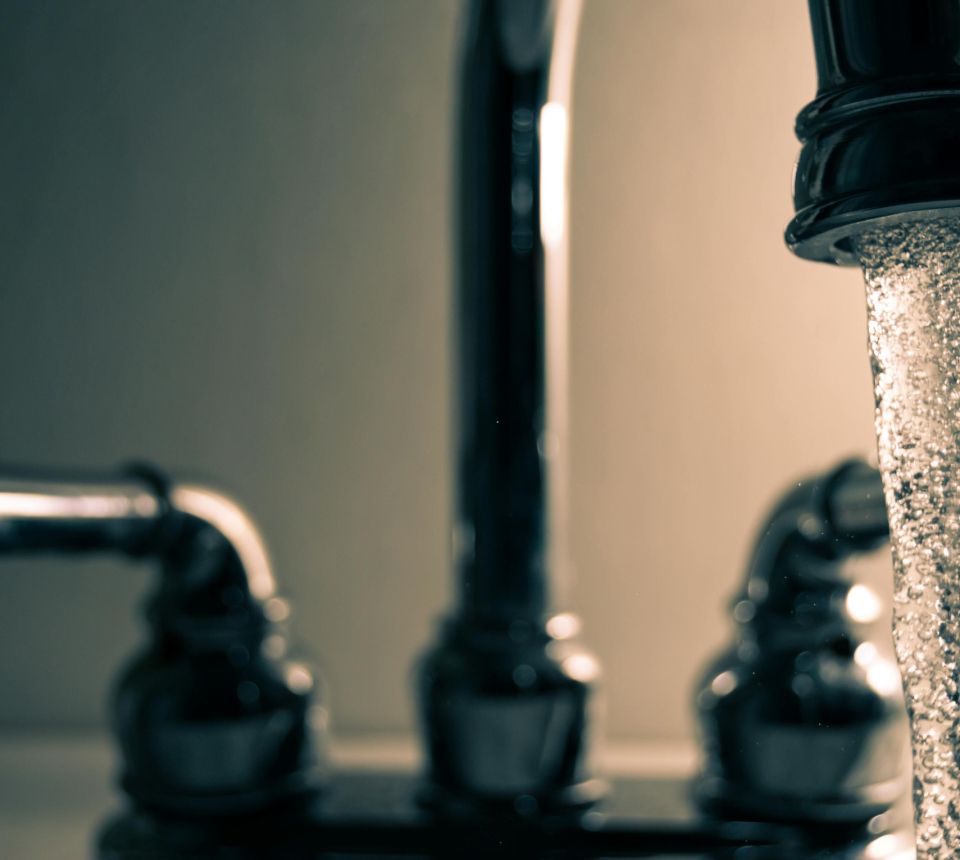
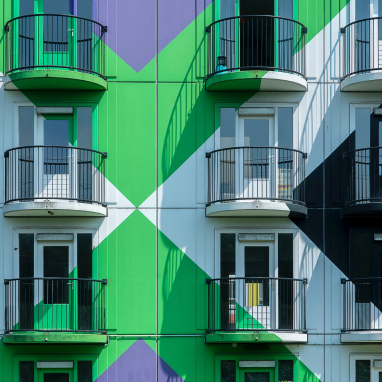
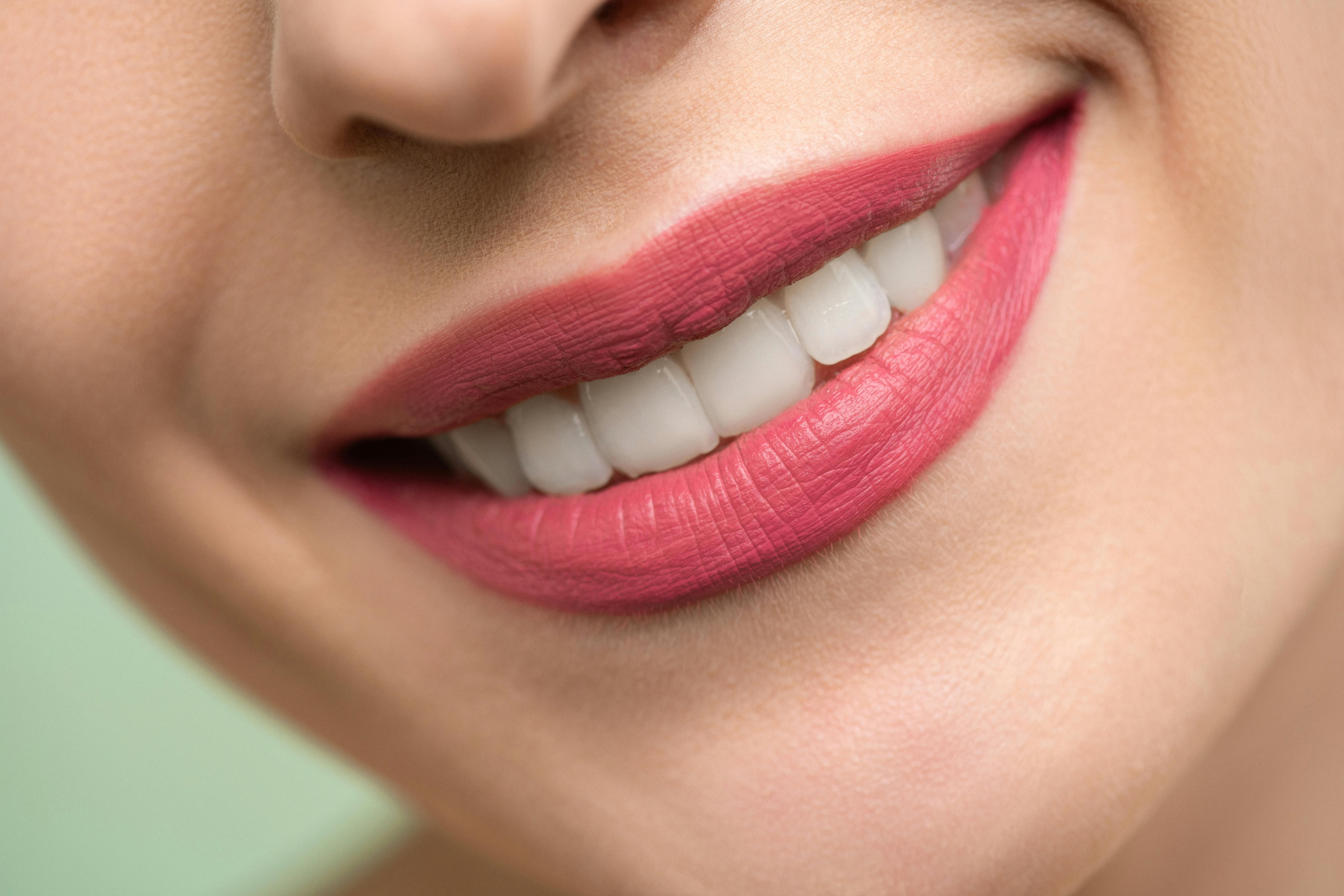
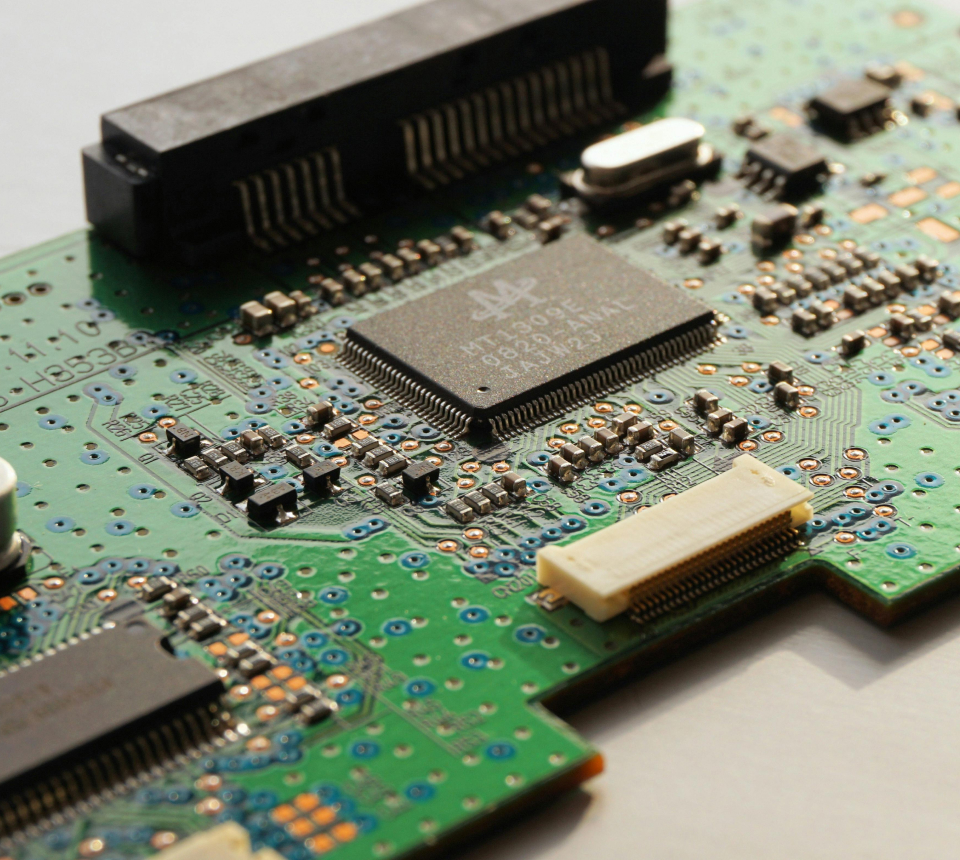
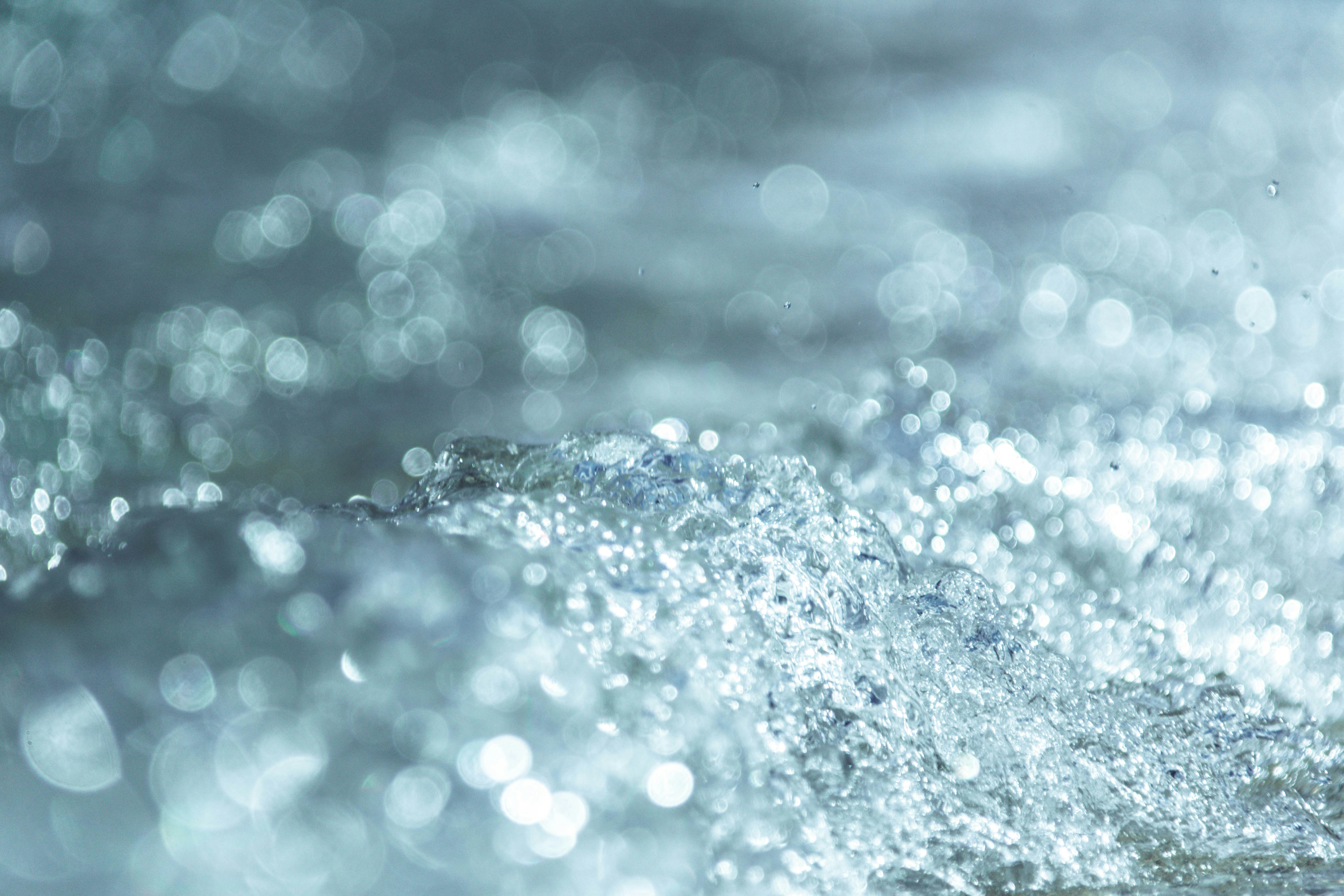
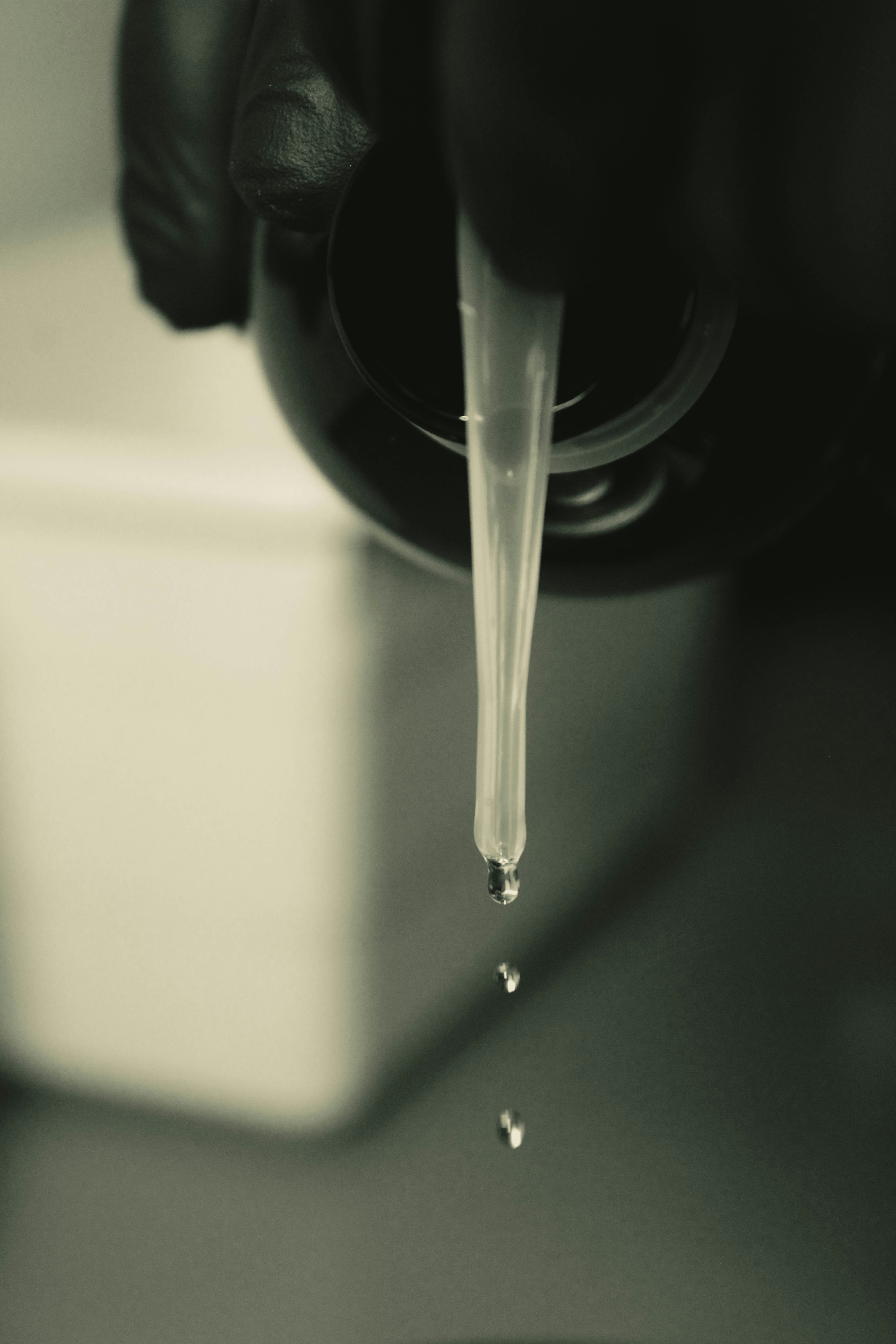
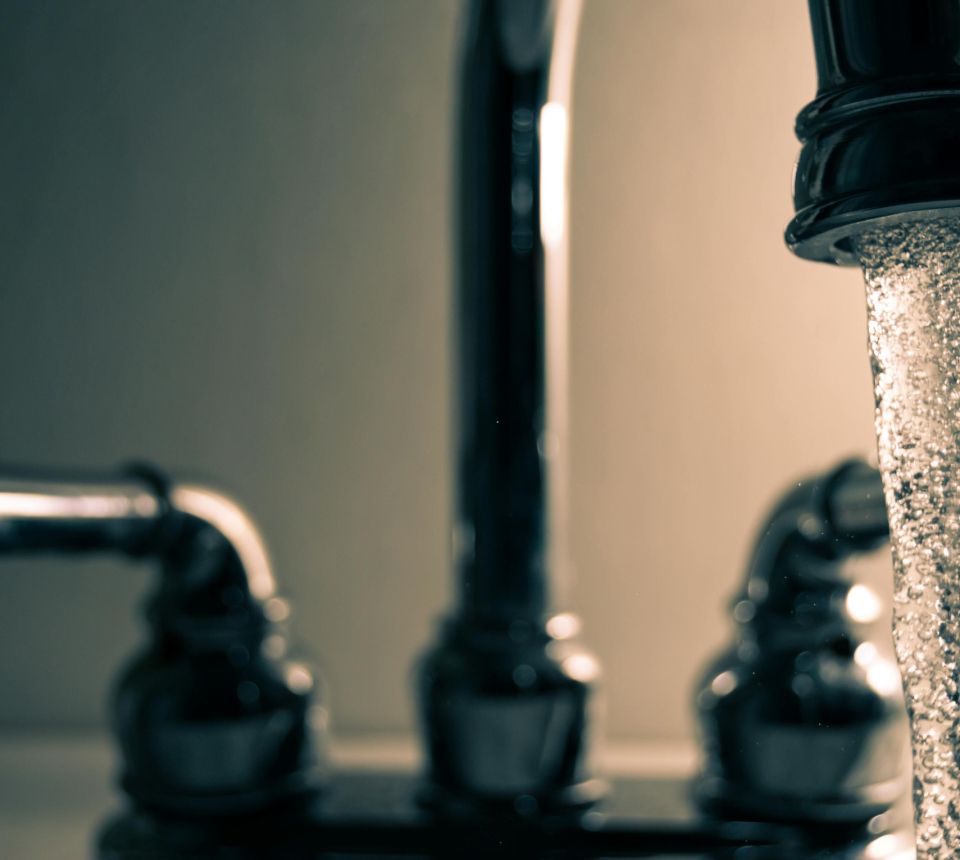
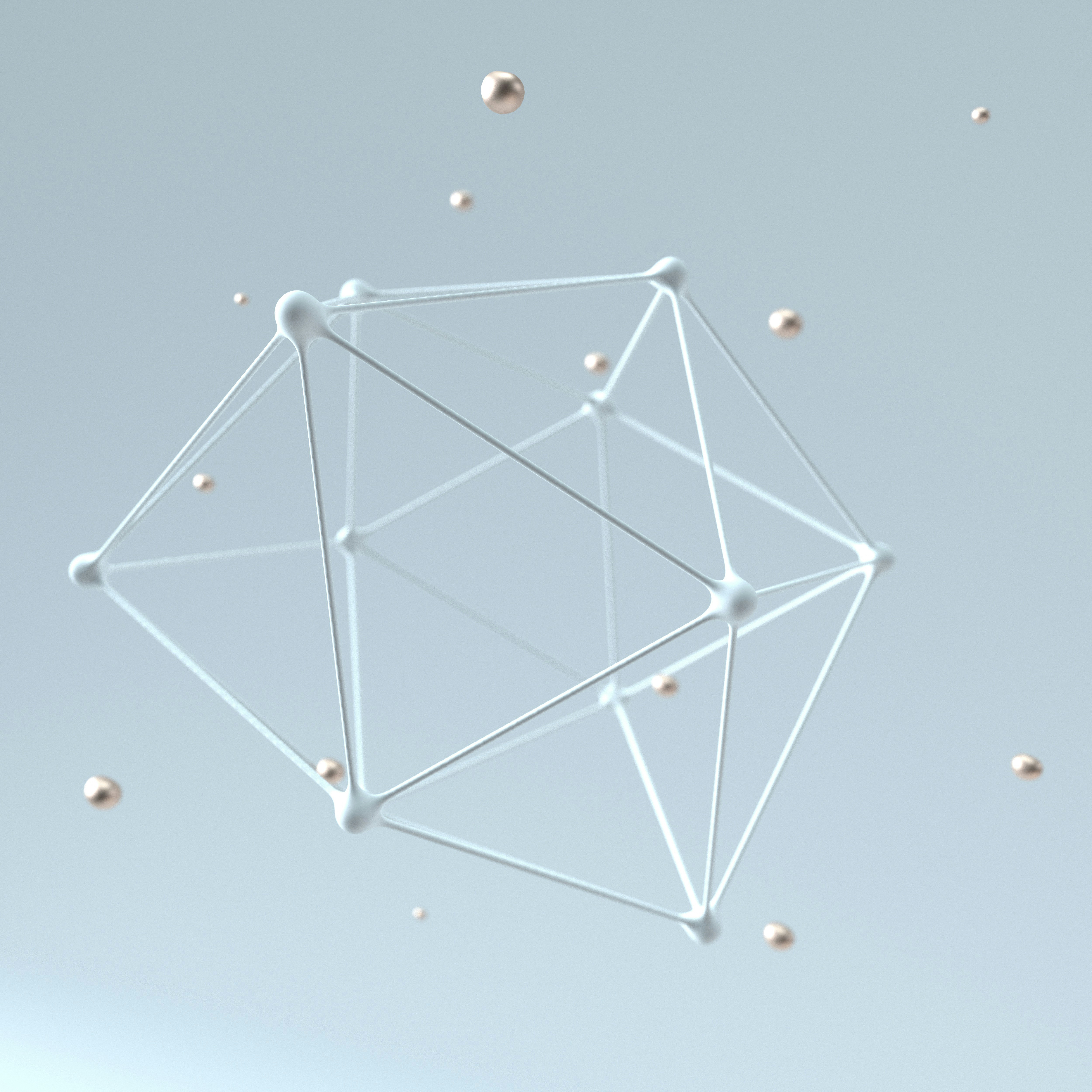
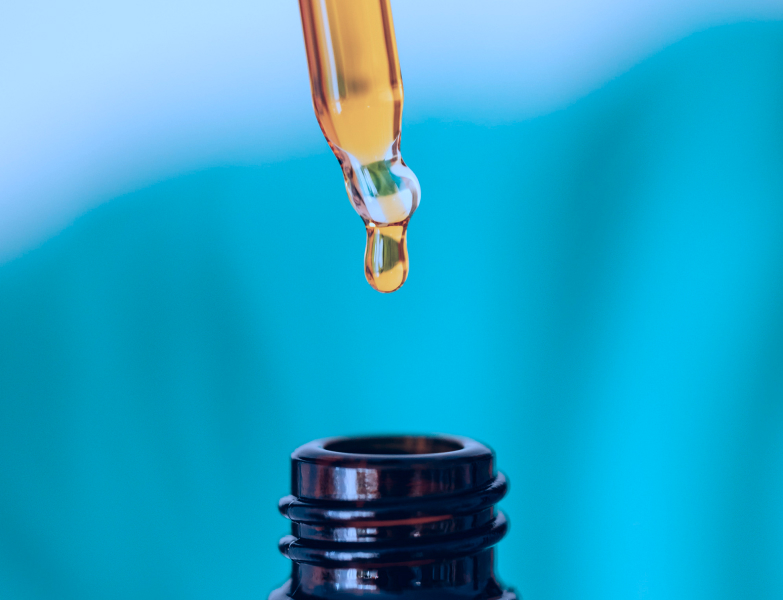
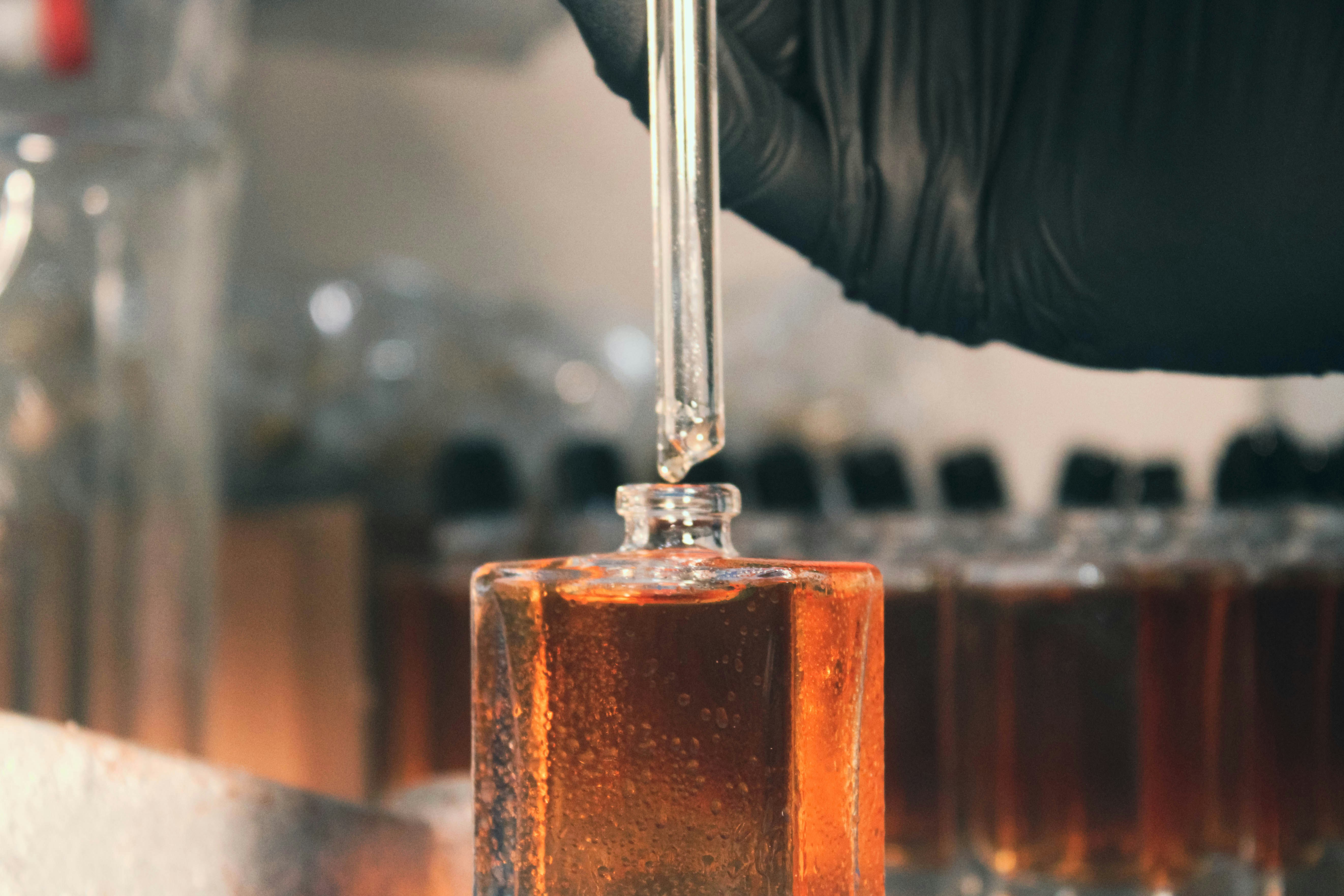
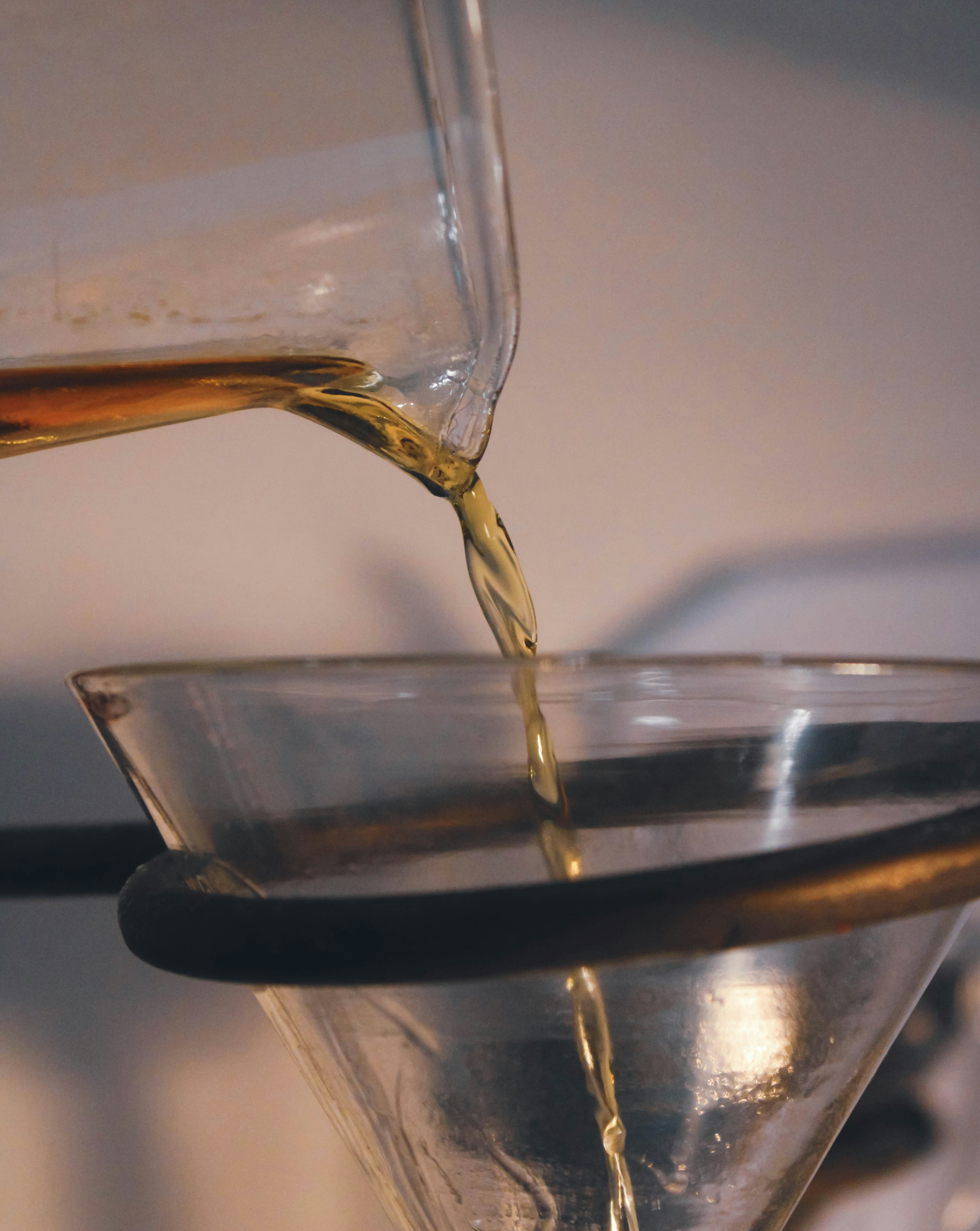
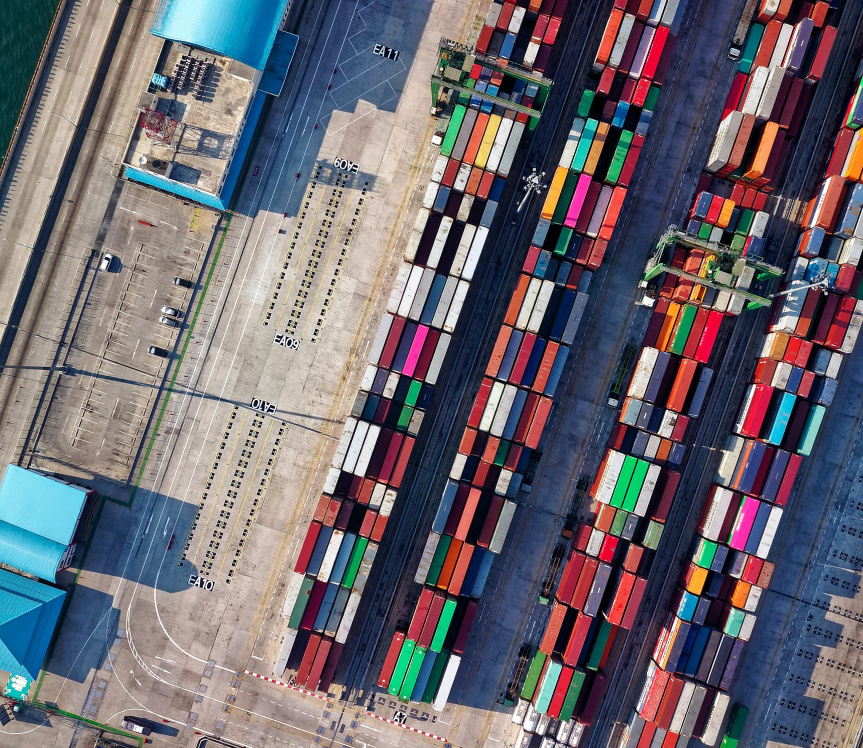
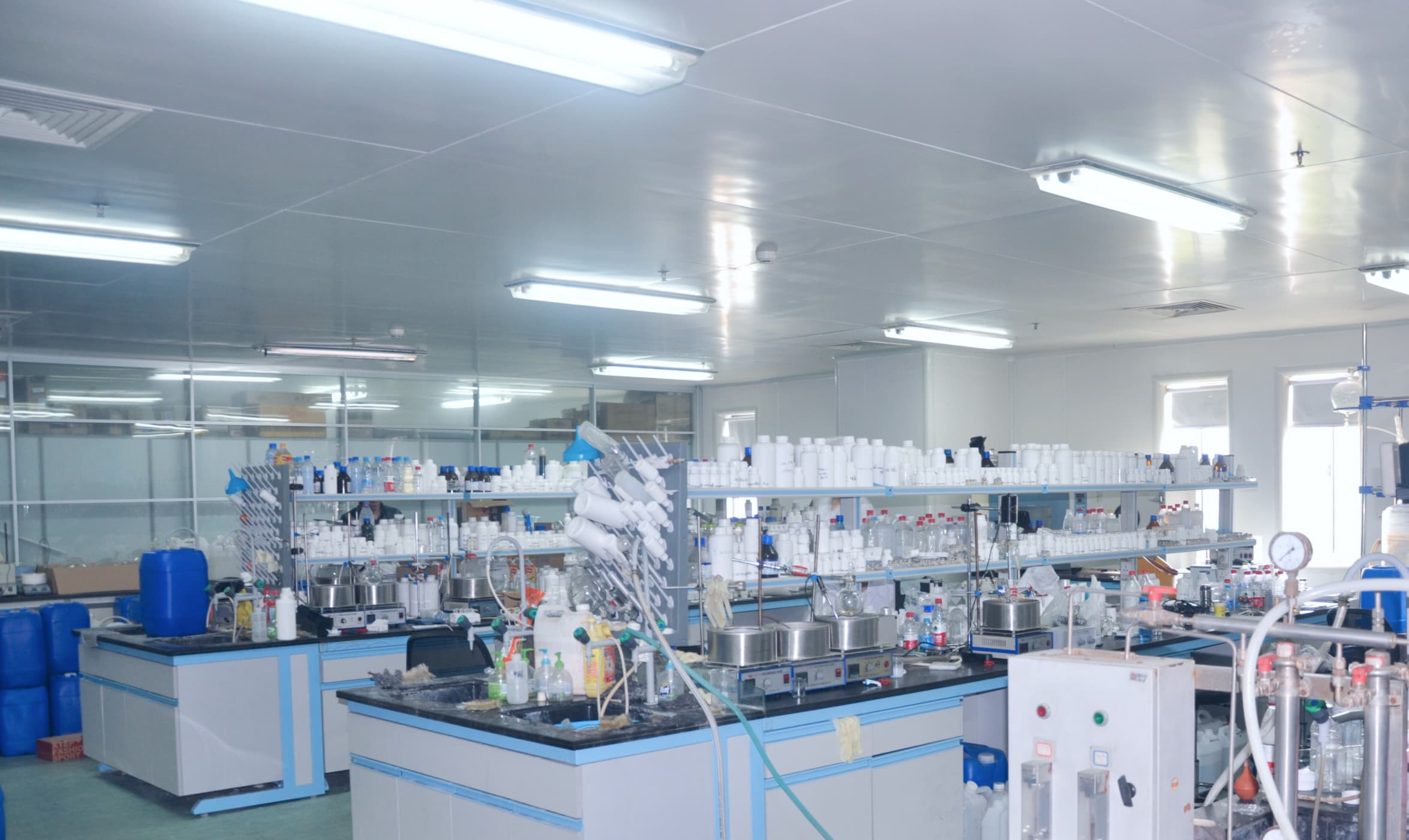
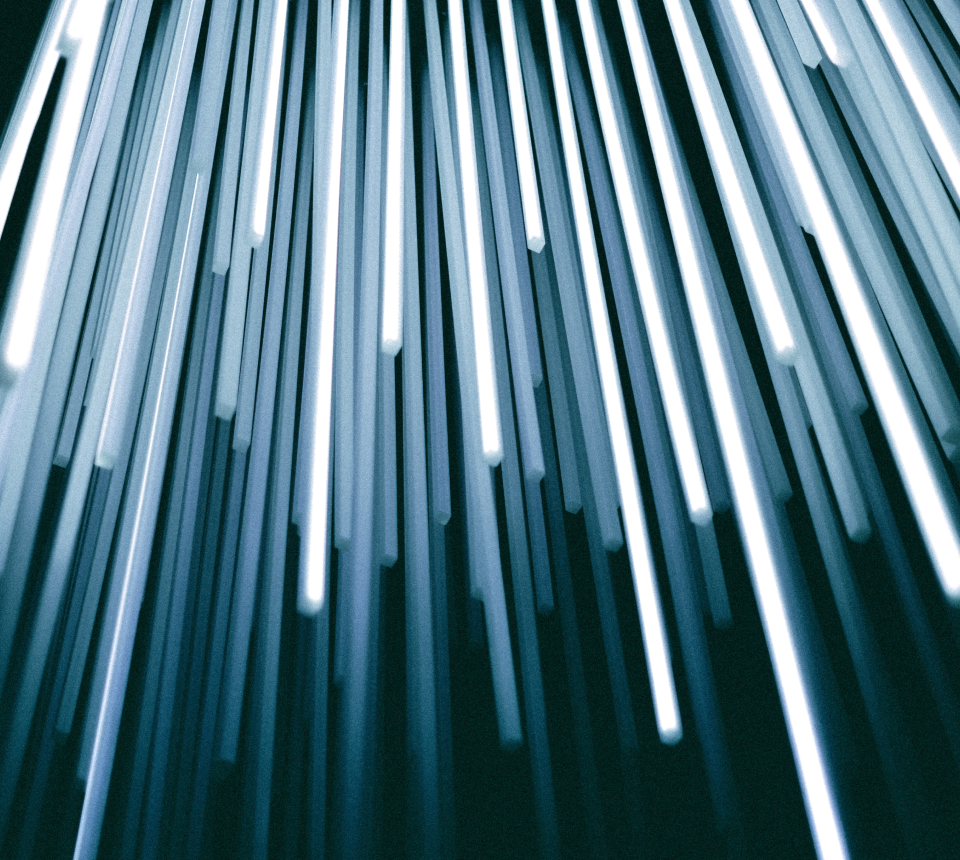
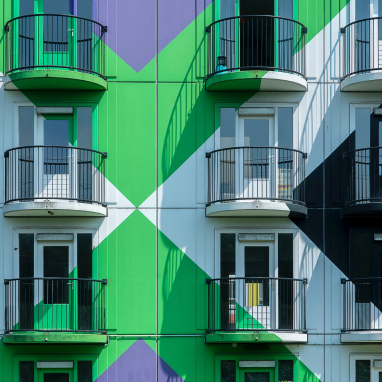
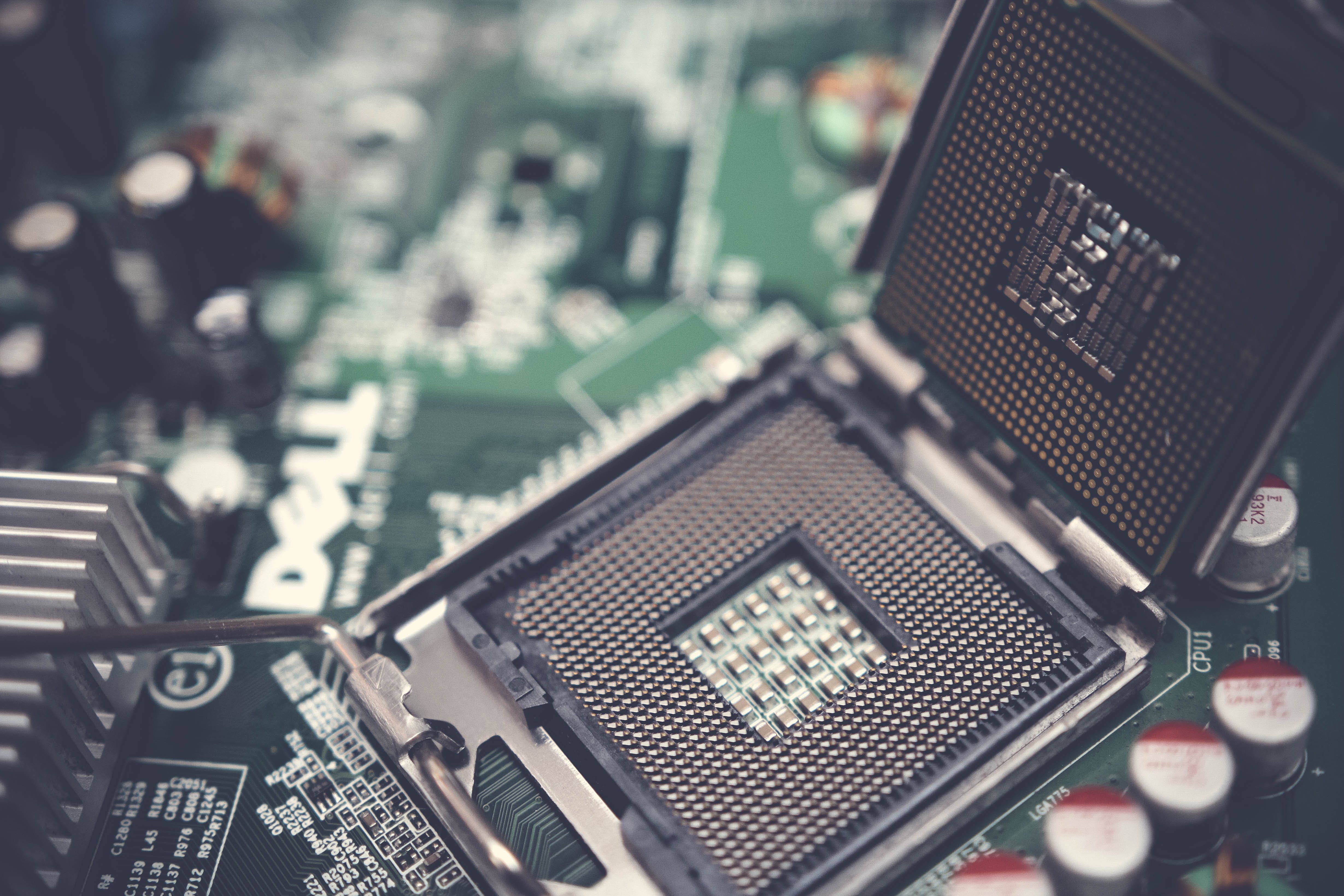
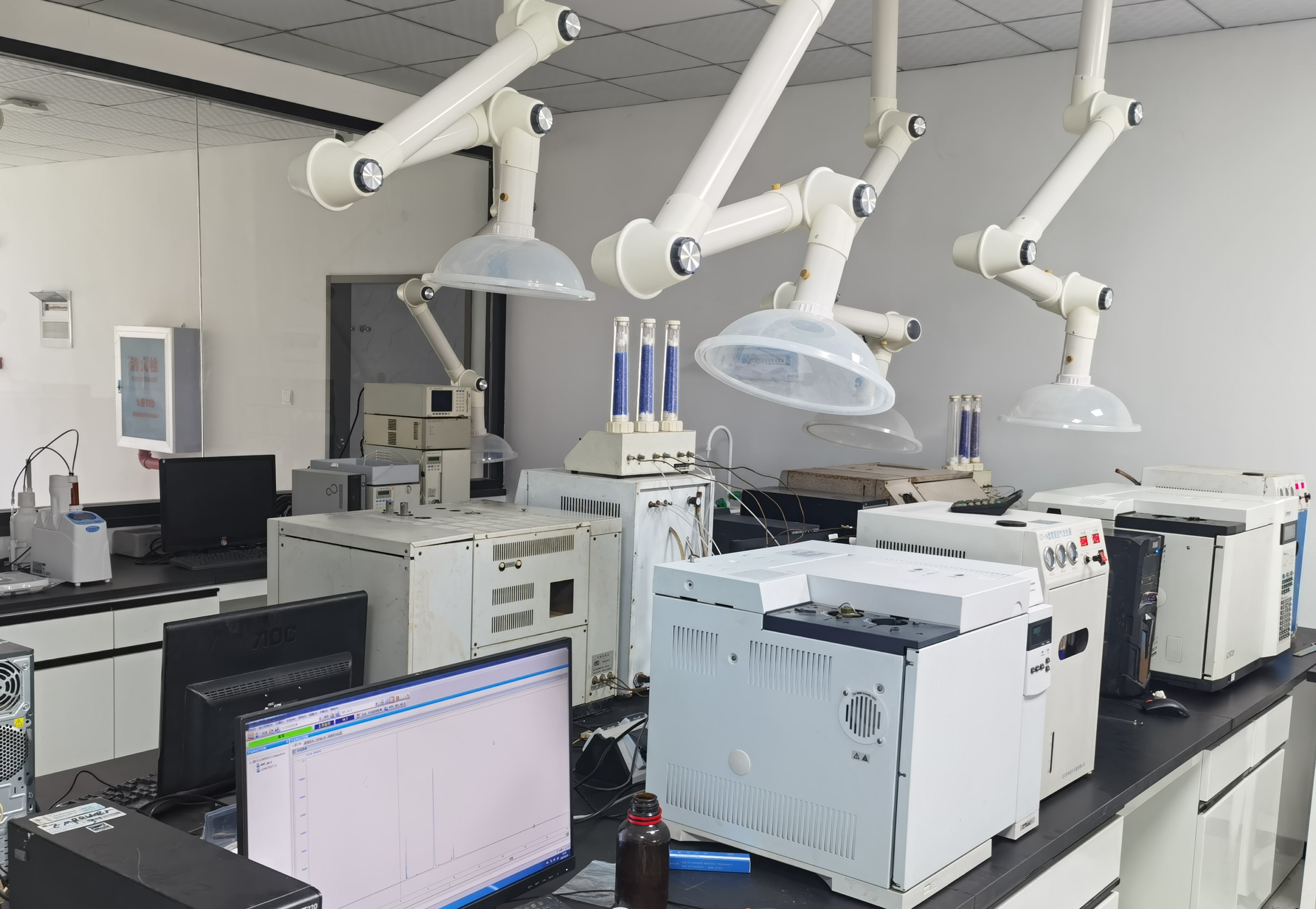
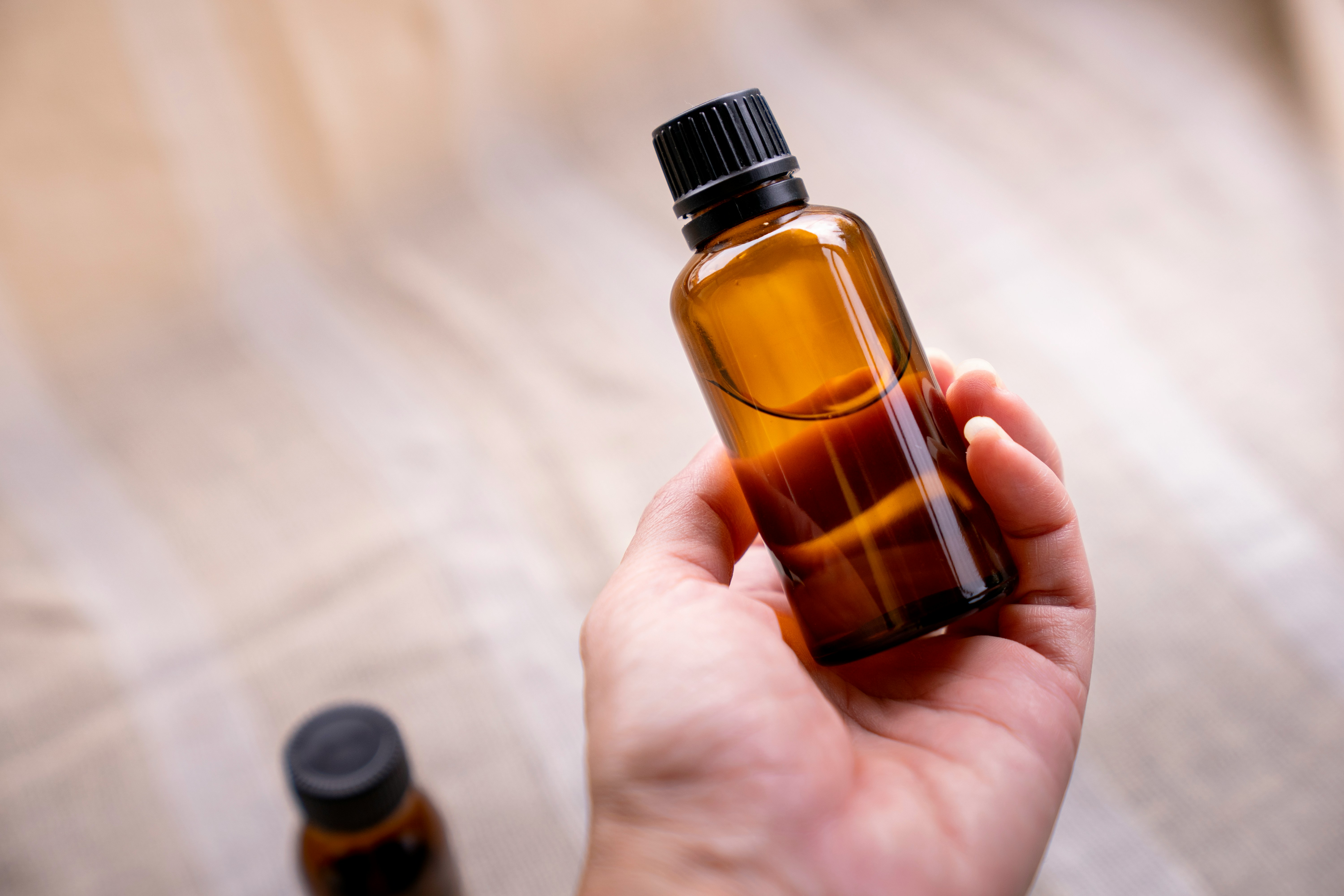
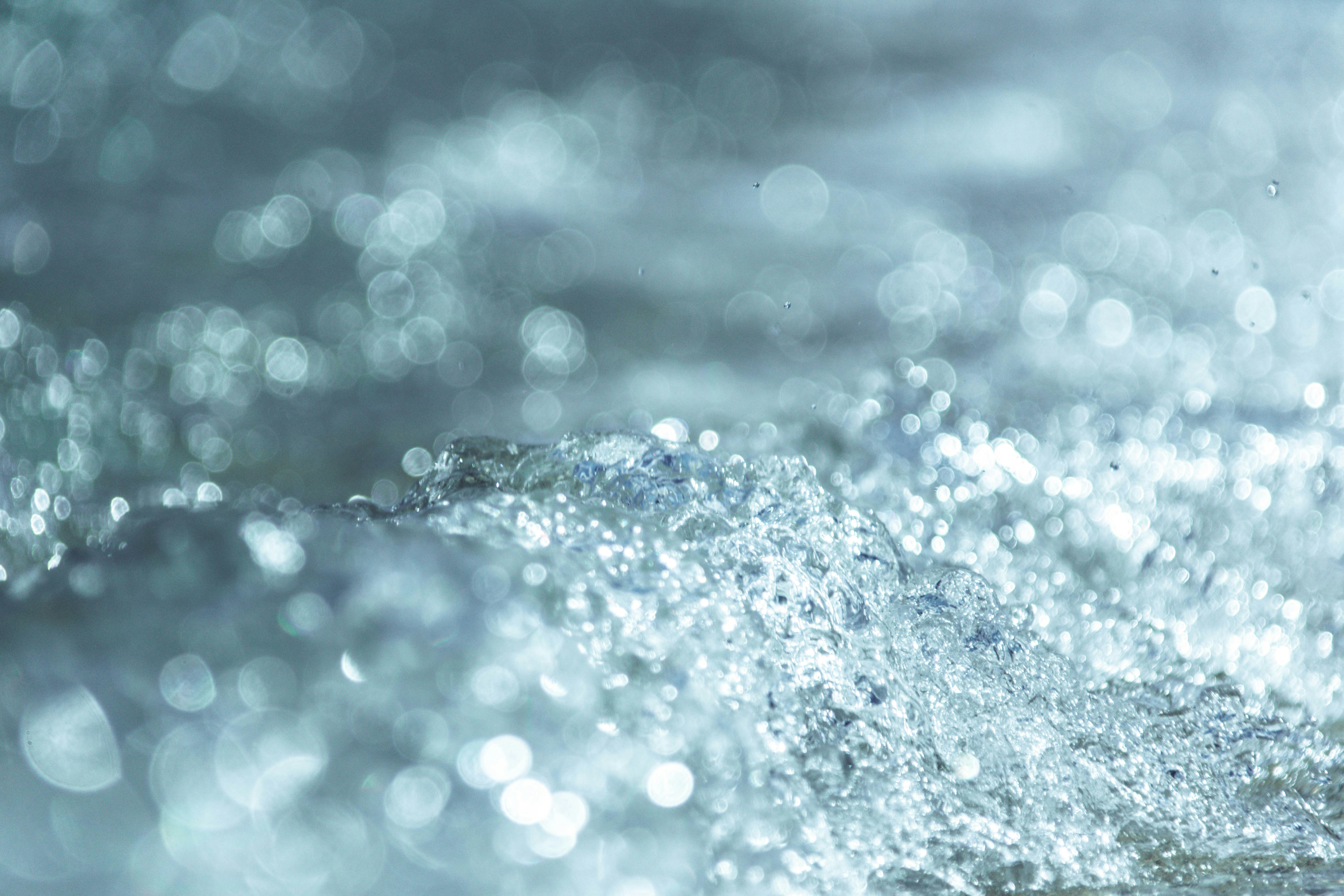
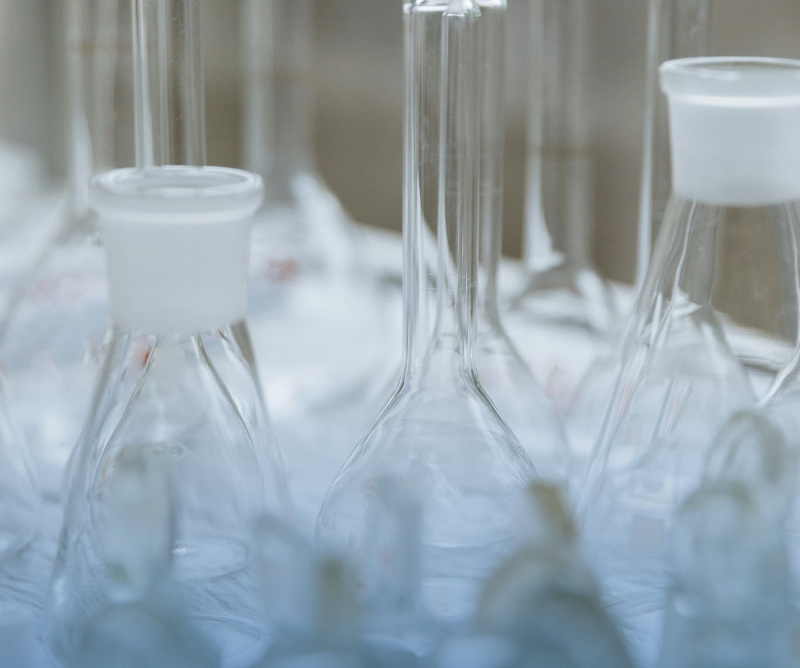
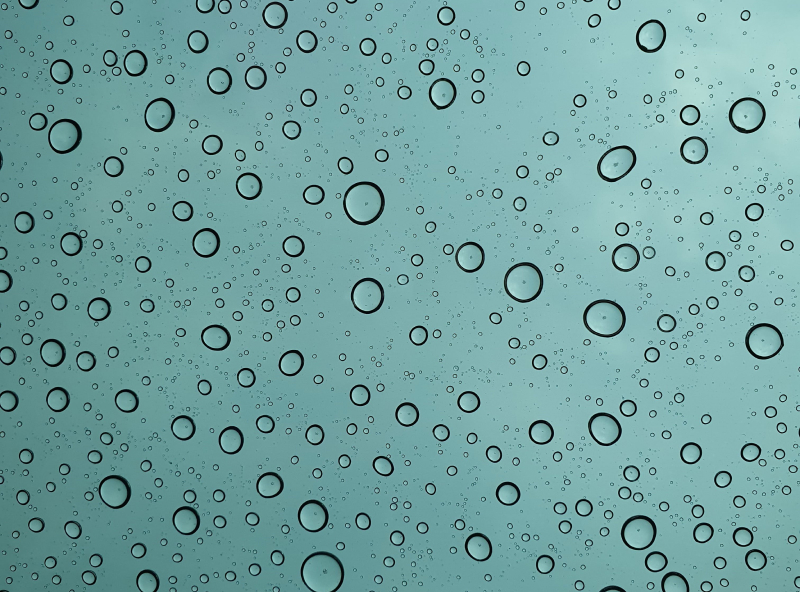
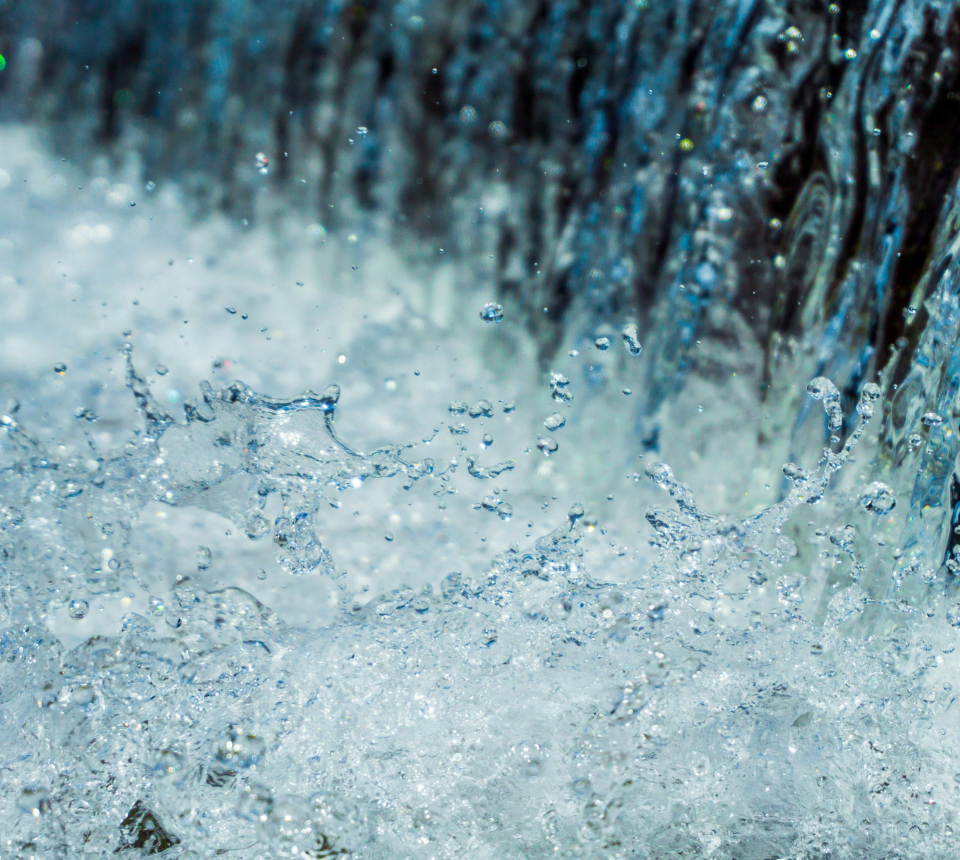
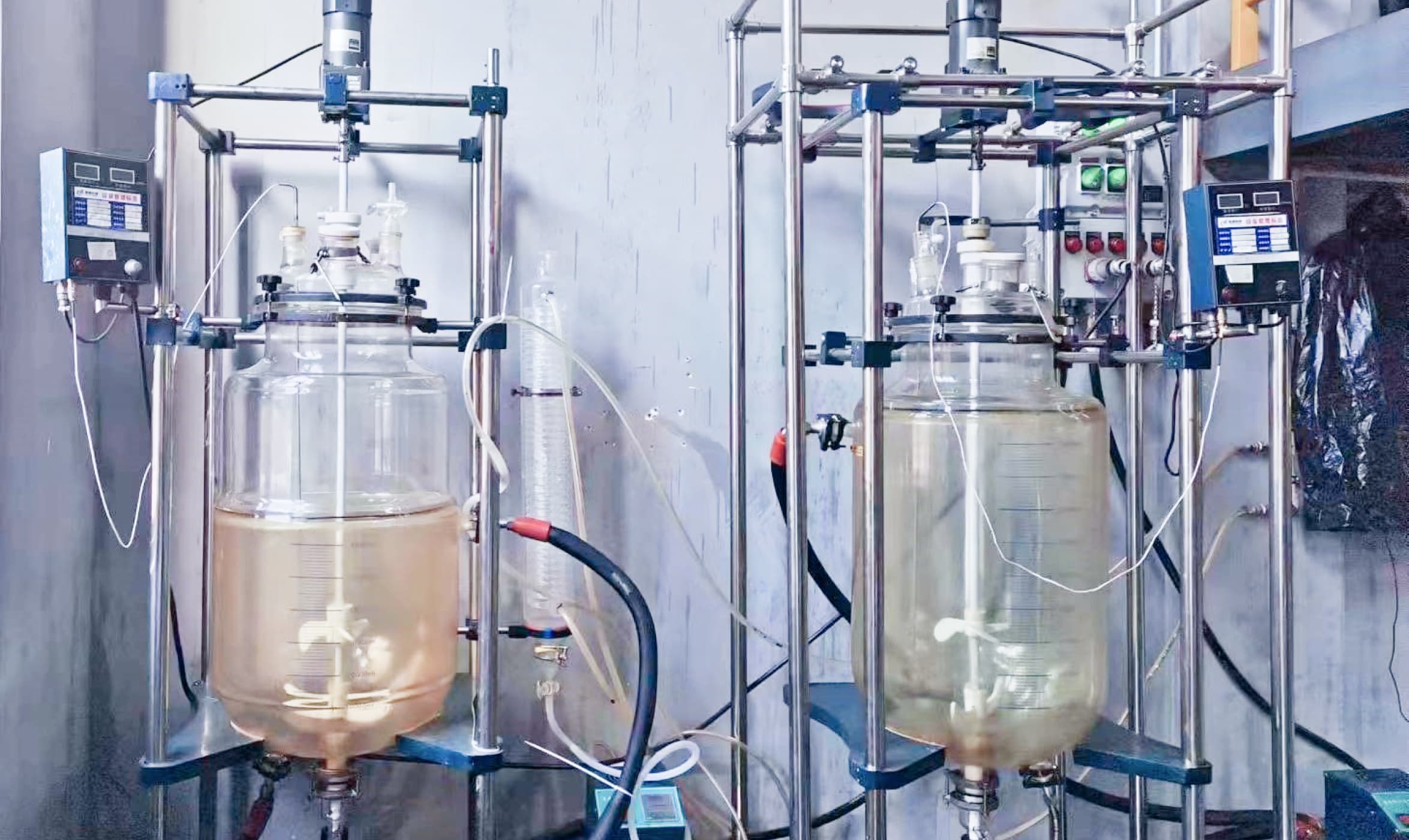
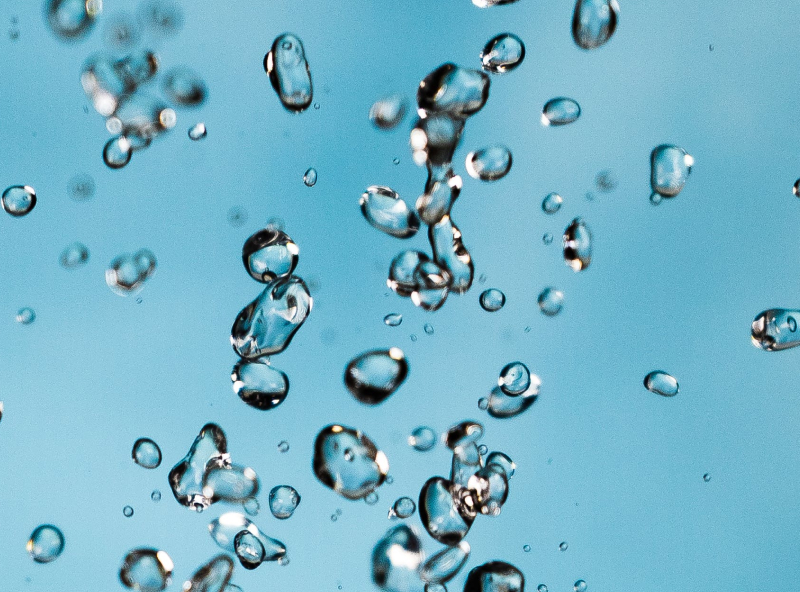
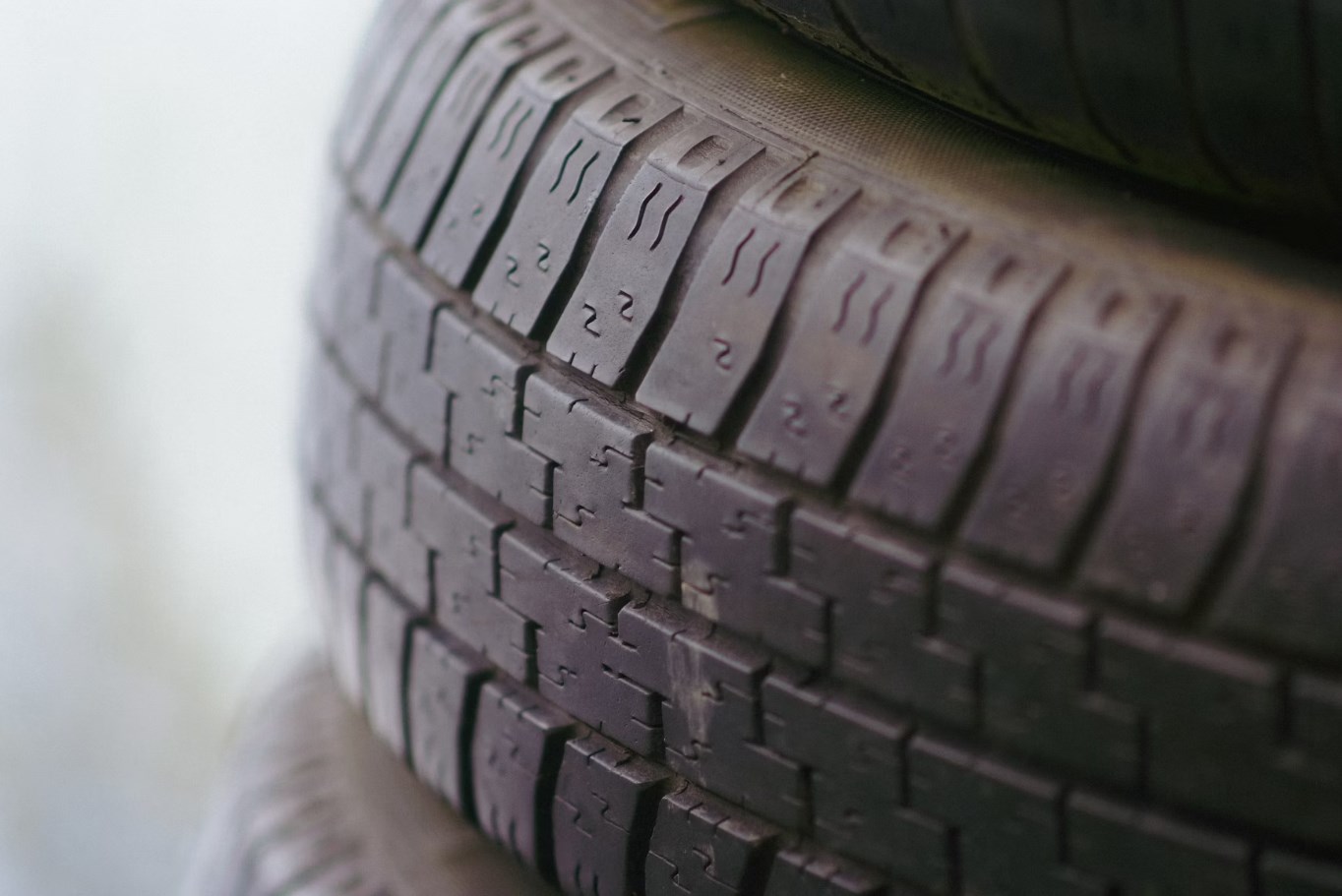
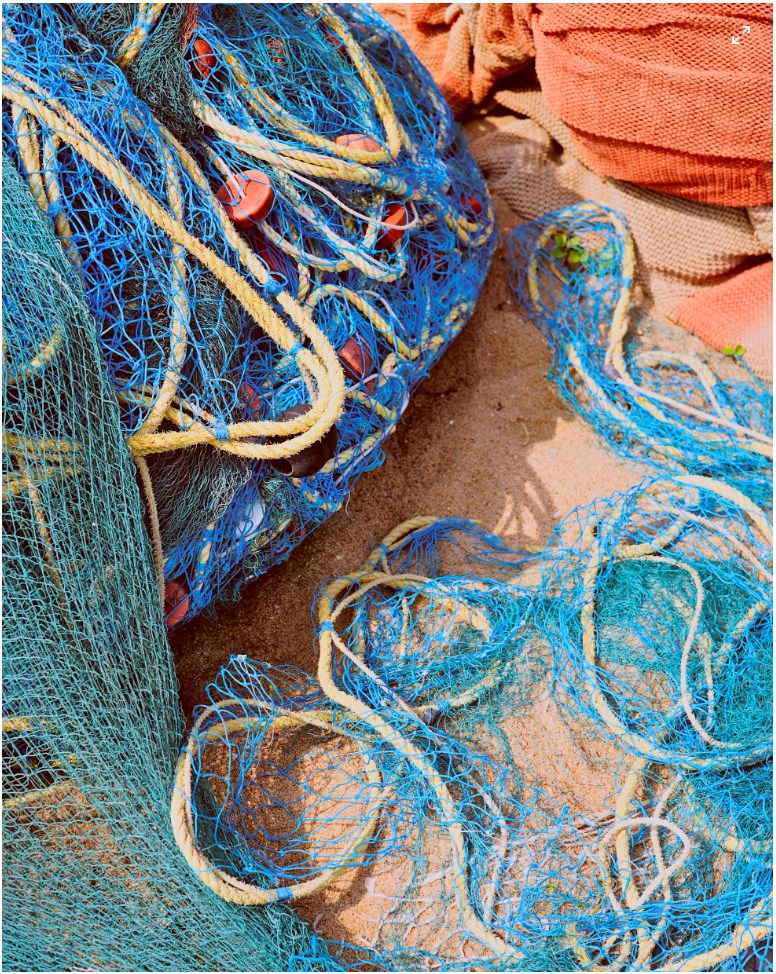
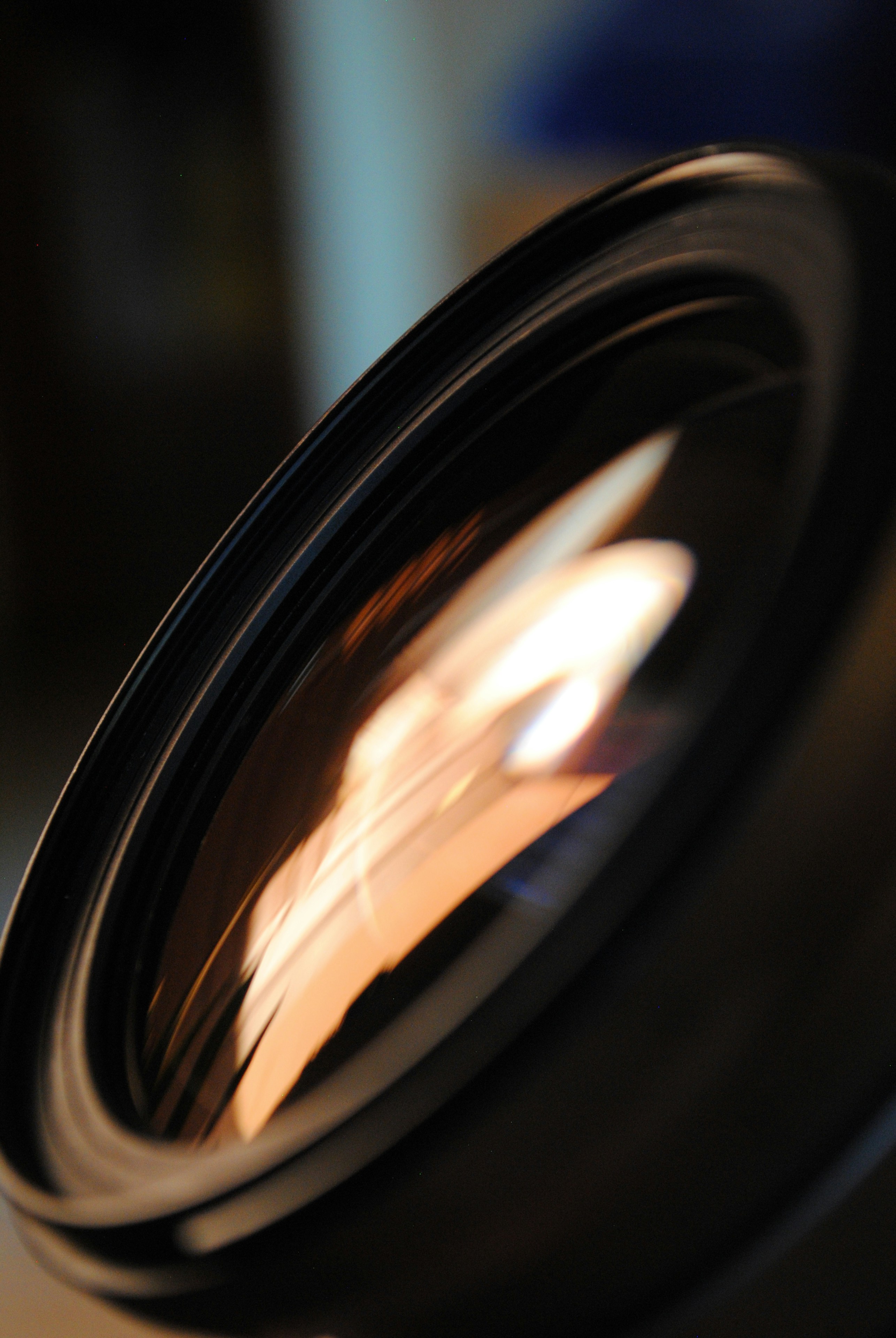
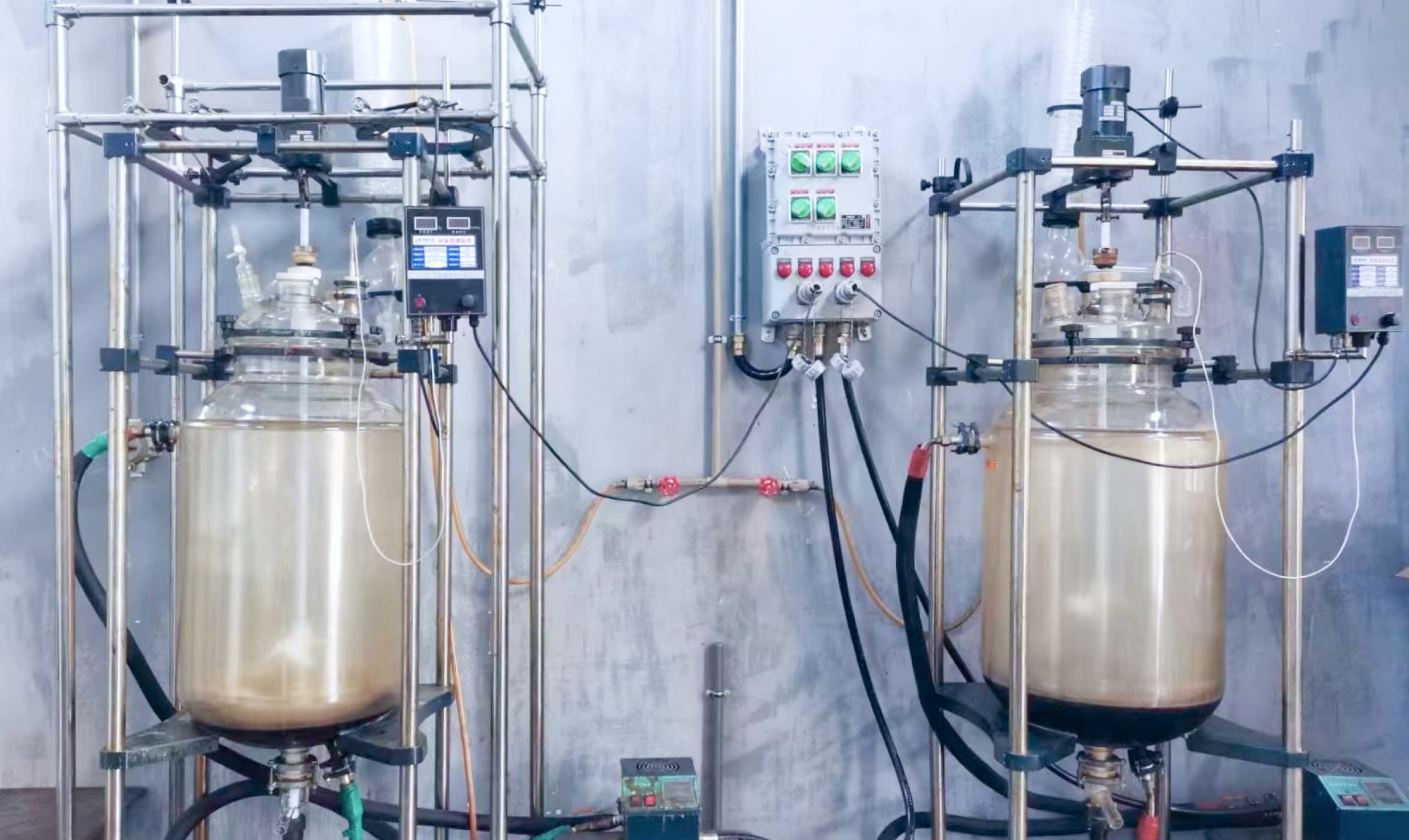
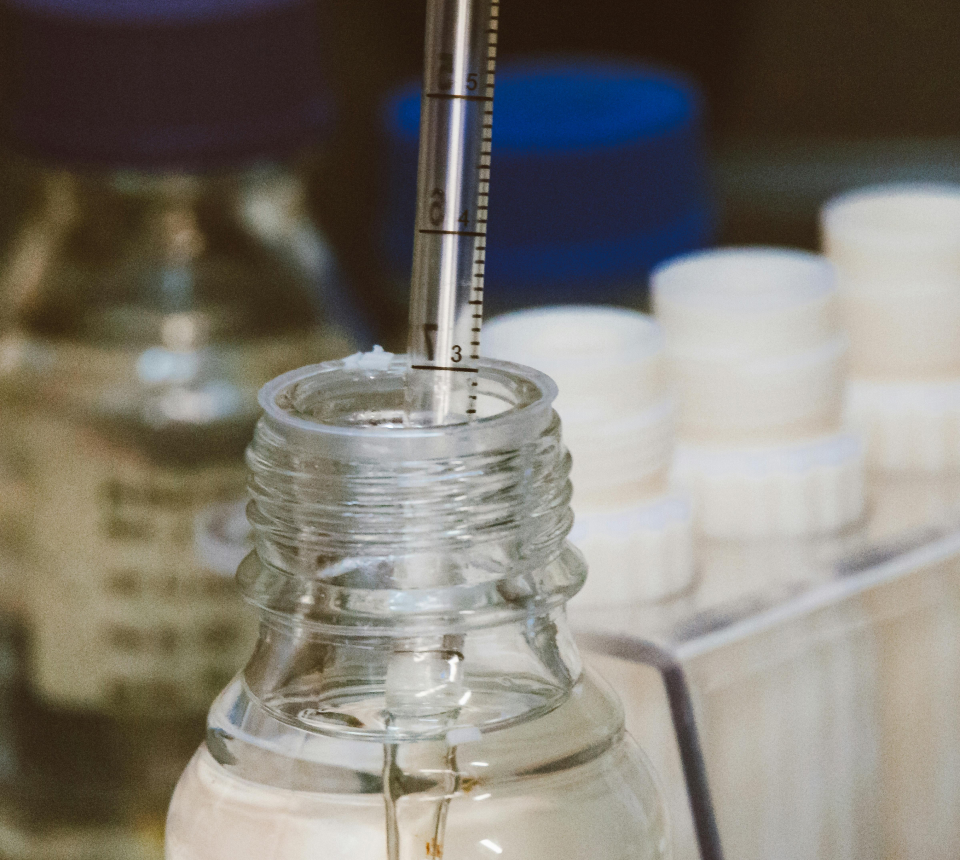
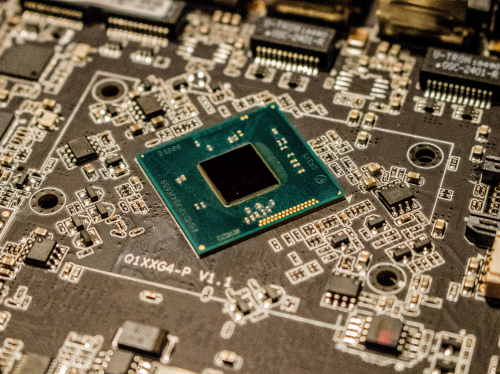
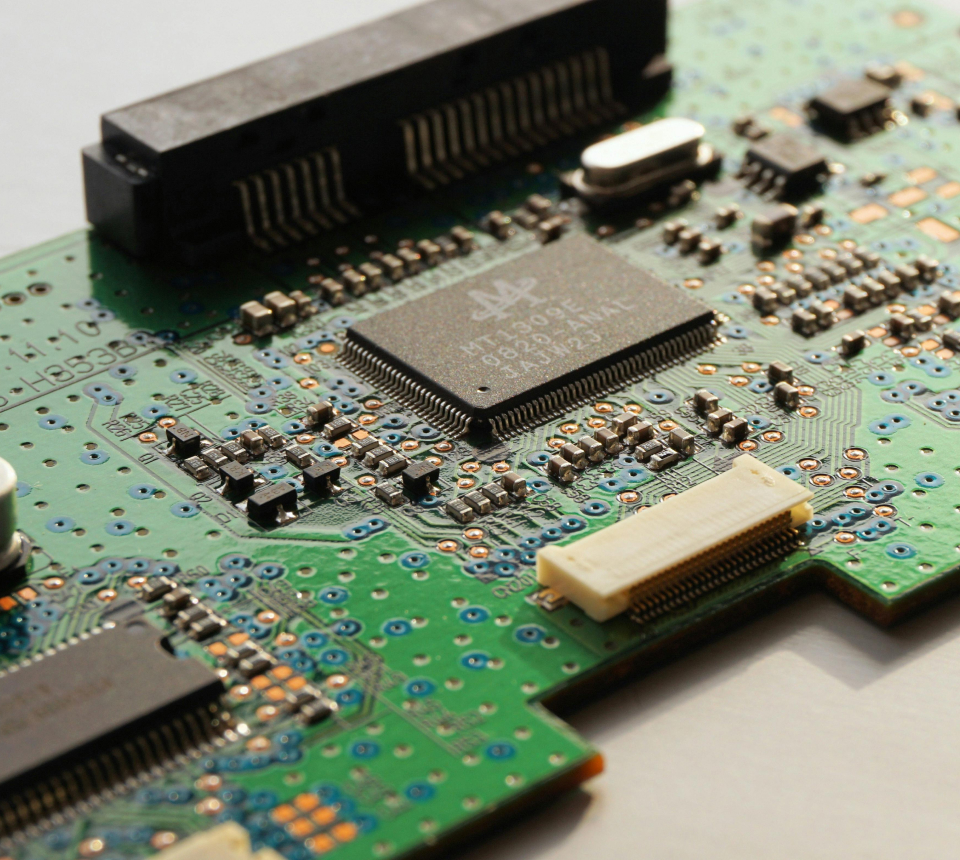
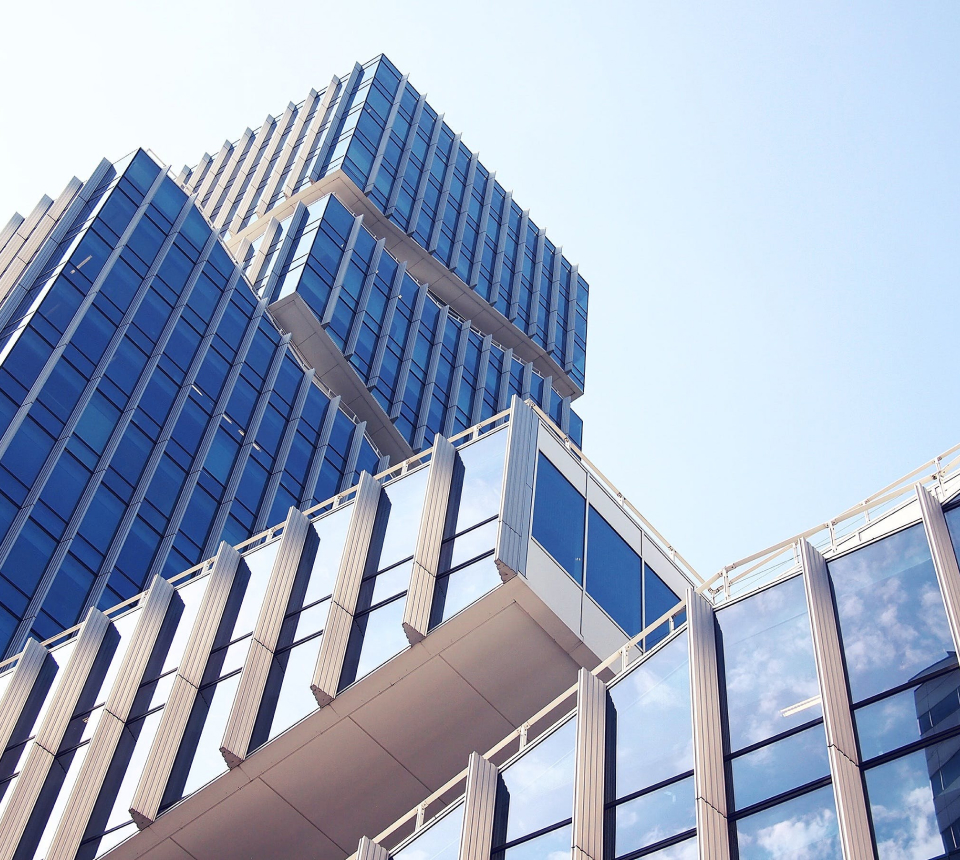
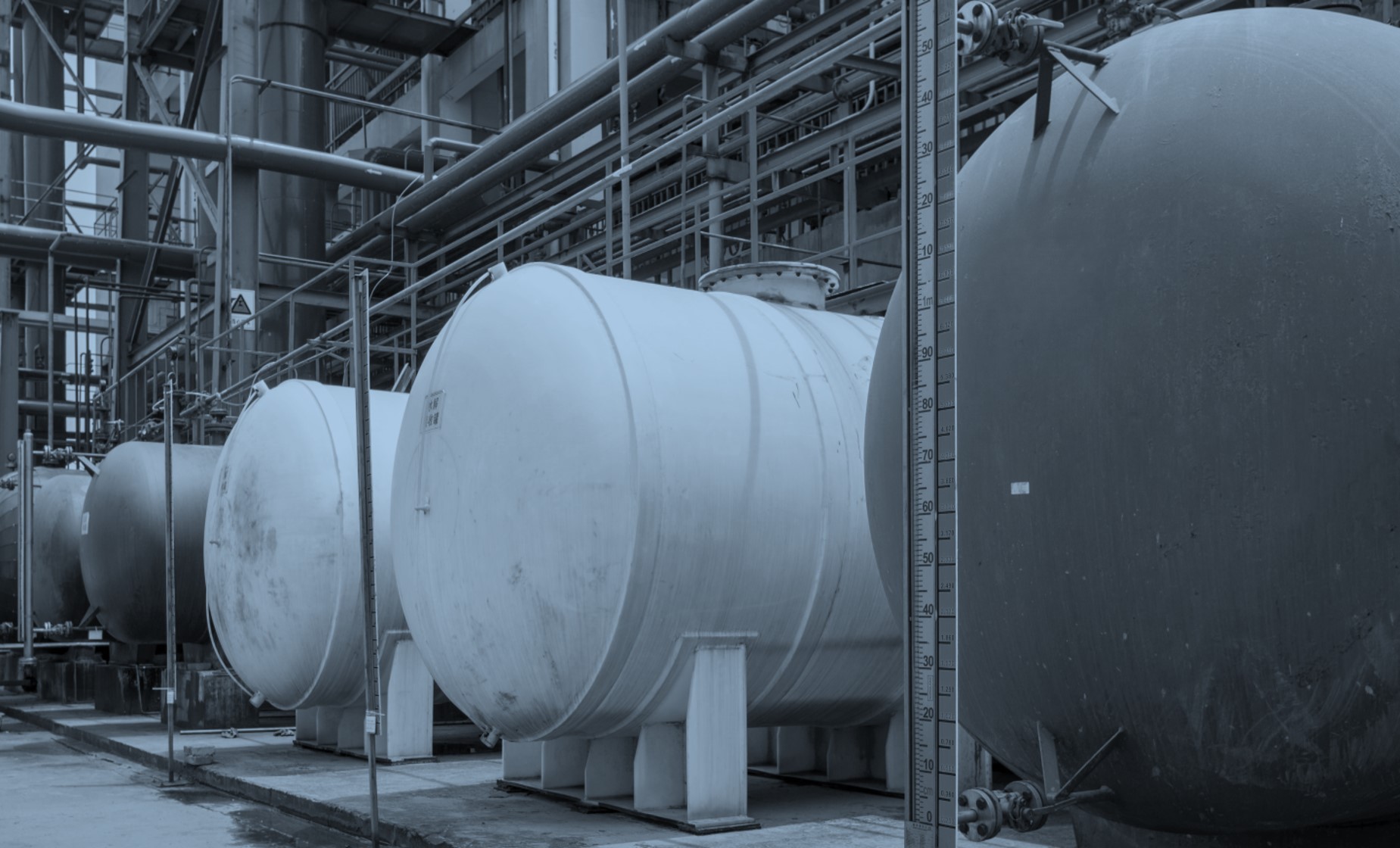
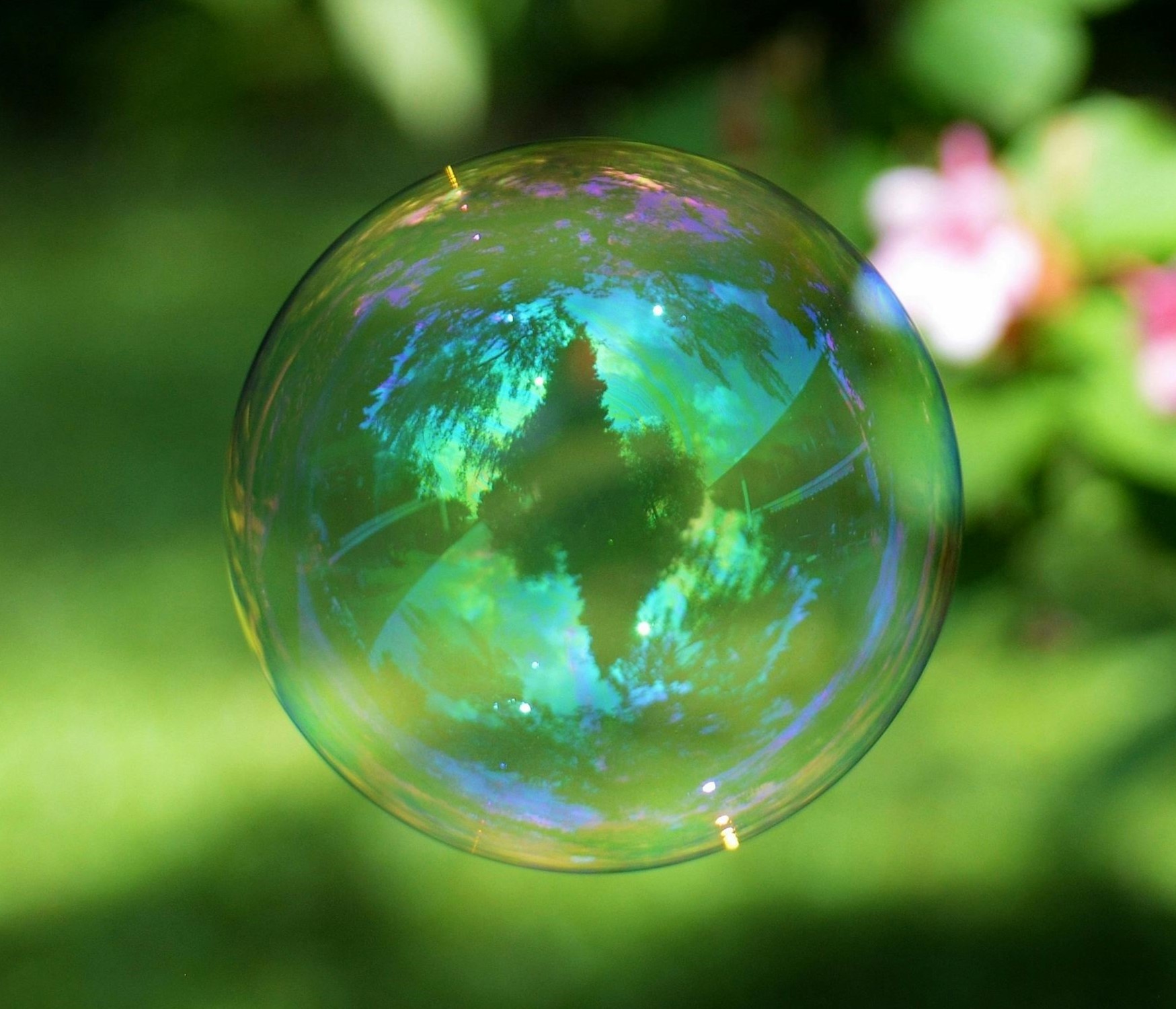
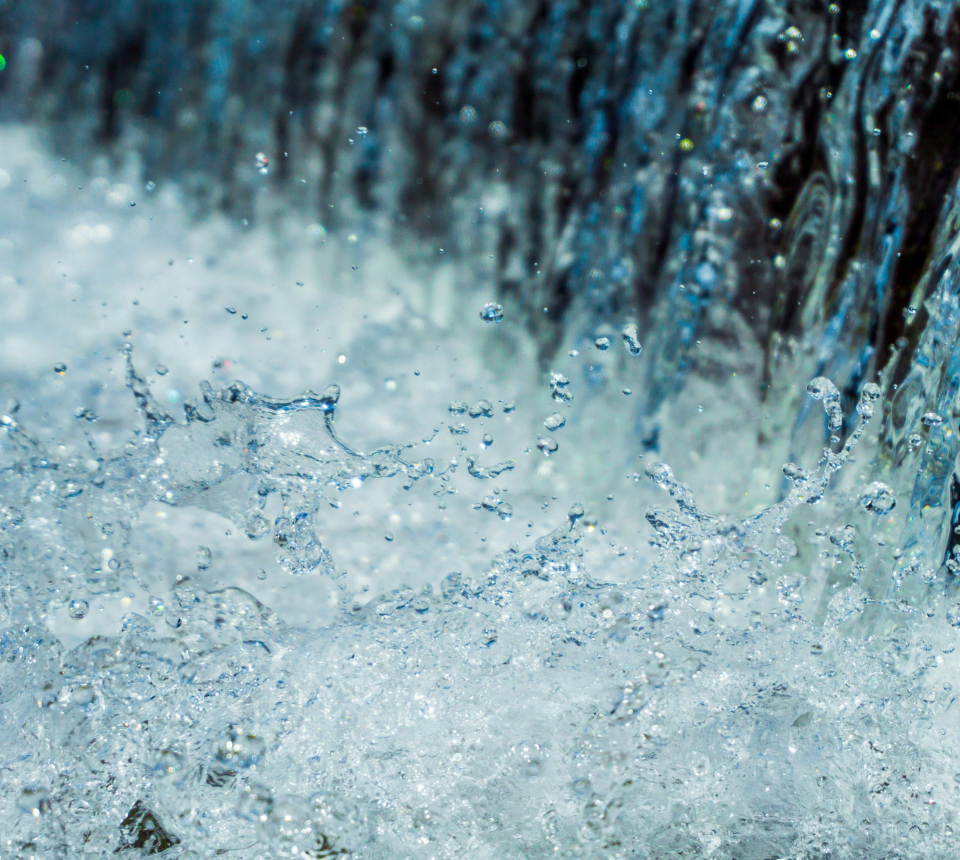
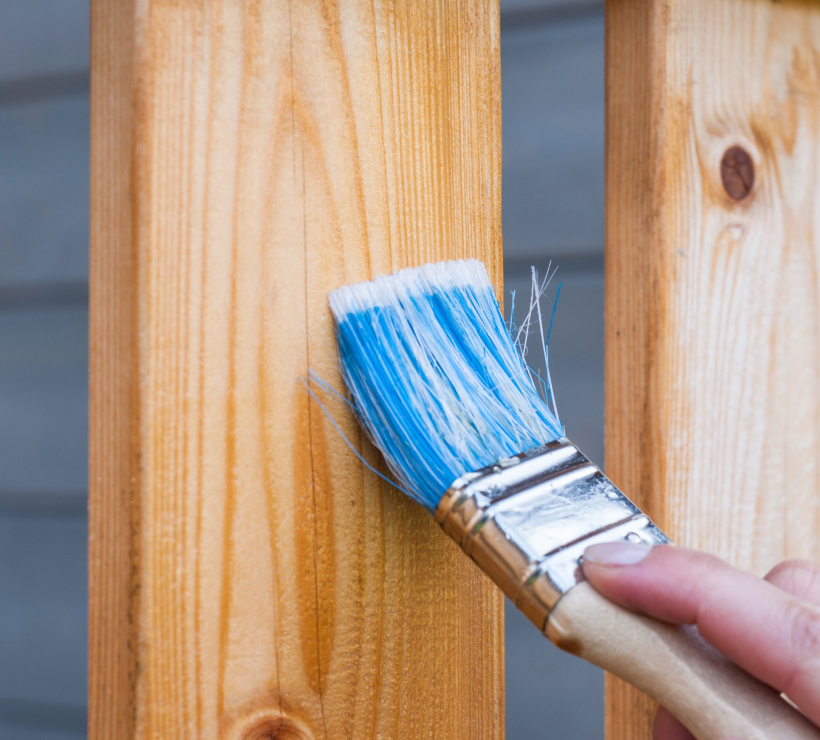

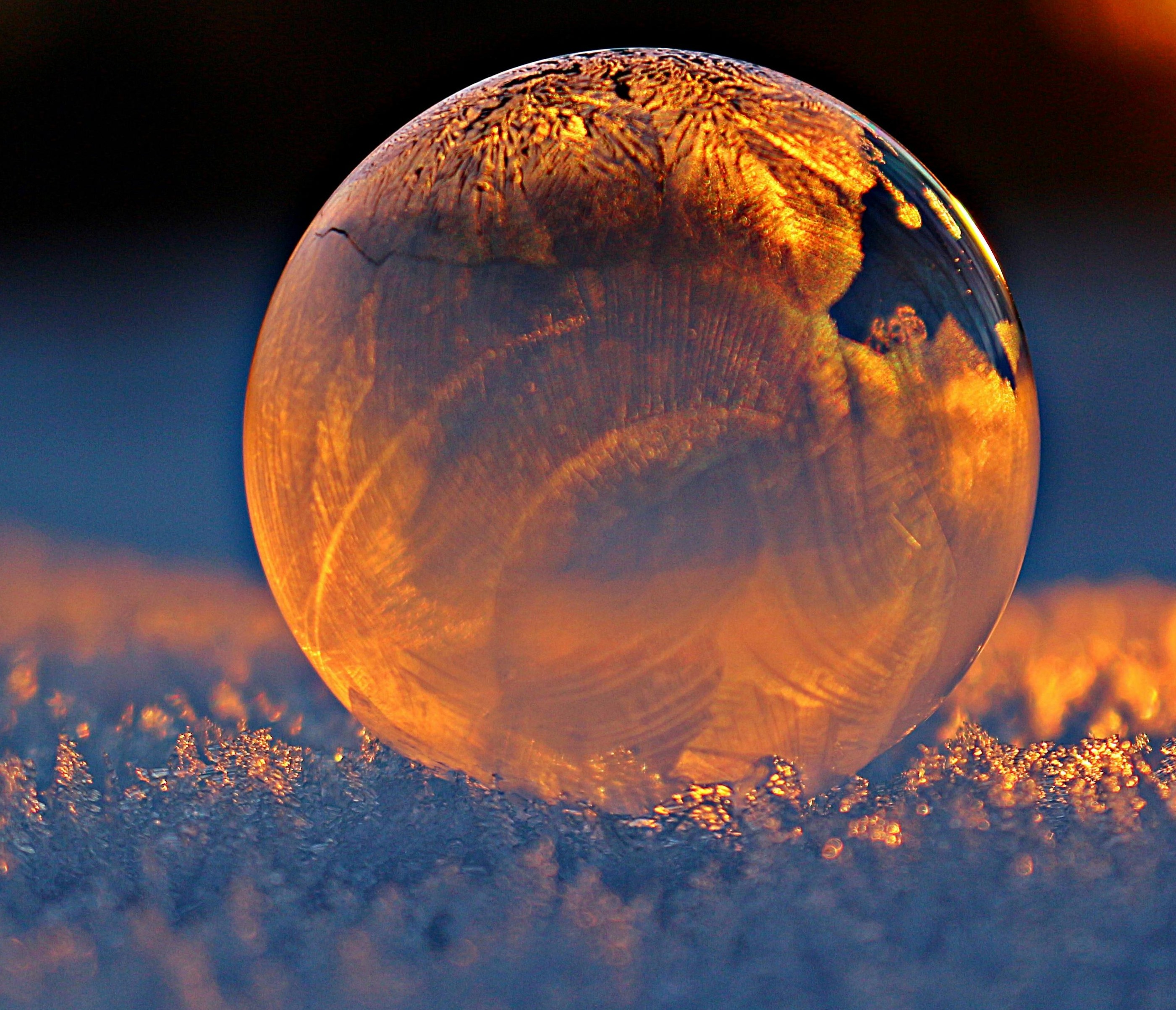
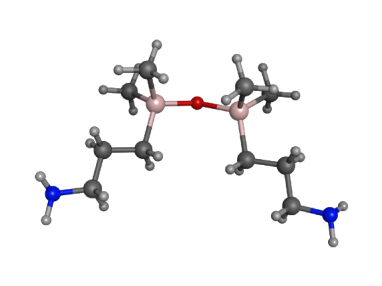
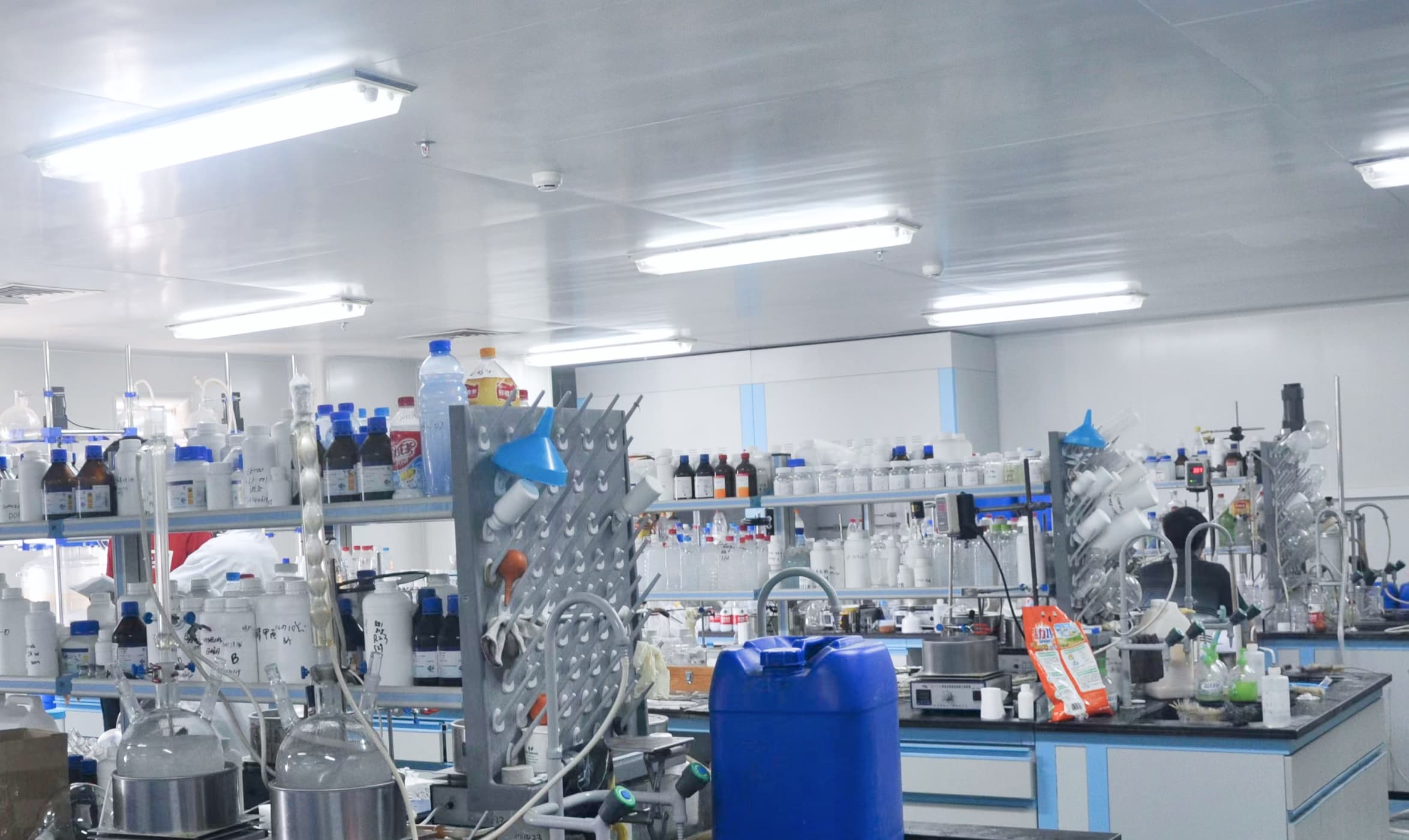
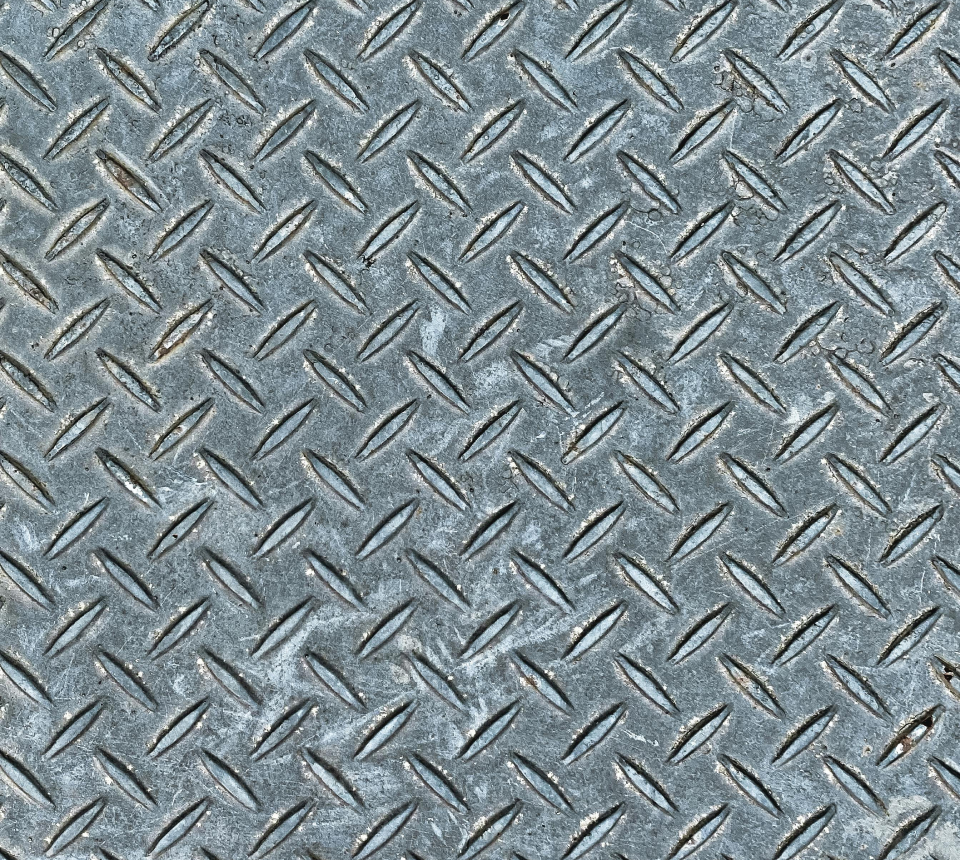
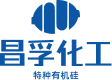
+86 27 8439 6550
+86 181 6277 0058
sales@cfsilanes.com
Optics Valley Bio-City
No. 666, Gaoxin Avenue
Hongshan District, Wuhan City
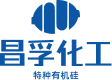
+86 27 8439 6550 | +86 181 6277 0058
sales@cfsilanes.com
Optics Valley Bio-City
No. 666, Gaoxin Avenue
Hongshan District, Wuhan City
Copyright © Hubei ChangFu Chemical Co., Ltd. All Rights